
- •ВВЕДЕНИЕ
- •1. ОБРАБОТКА РЕЗУЛЬТАТОВ НОРМАТИВНЫХ НАБЛЮДЕНИЙ
- •1.1. Общий порядок организации нормативных наблюдений
- •1.2. Обработка результатов натурных наблюдений. Программа «Natura»
- •1.3. Определение основных характеристик рядов наблюдения. Программа «Sample»
- •2. МНОГОФАКТОРНЫЕ МАТЕМАТИЧЕСКИЕ МОДЕЛИ НА ОСНОВЕ БАЗ ДАННЫХ НАБЛЮДЕНИЙ (ИСПЫТАНИЙ). ПРОГРАММА «MODELL»
- •2.1. Шаговый регрессионный метод
- •2.2. Построение доверительных интервалов. Программа «Diagram»
- •3.1. Формулировка задачи
- •3.2. Примеры формулировок экономических задач и их решений при помощи программ «Simply», «Simplint» и «Rasm»
- •4. ТРАНСПОРТНАЯ ЗАДАЧА. ПРОГРАММА «TRANSY»
- •5. ЗАДАЧА КОММИВОЯЖЕРА. ПРОГРАММА «KOMMY»
- •6. ОПТИМИЗАЦИЯ ПОРТФЕЛЯ ЦЕННЫХ БУМАГ. ПРОГРАММА «MARK»
- •7. СЕТЕВОЙ ГРАФИК. ПРОГРАММА «SETY»
- •8. ВАРИАНТЫ ЗАДАЧ ДЛЯ САМОСТОЯТЕЛЬНОГО РЕШЕНИЯ
- •Задача 1. Провести обработку результатов нормативных наблюдений и рассчитать новую норму времени на выполнение строительного процесса вручную. Результаты ручного расчета проверить с помощью программы «Natura».
- •Задача 3. В таблицах 8.32 и 8.33 приведены данные по 15 субъектам Российской Федерации о денежных доходах и потребительских расходах на душу.
- •Задача 8. Определение оптимального варианта раскроя арматуры. Произвести раскрой арматурных стержней определенной длины и получить заготовки проектных размеров в необходимых количествах с минимальными отходами при раскрое.
- •9. ПРИЛОЖЕНИЯ. ЛИСТИНГИ ПРИКЛАДНЫХ ПРОГРАММ
- •П1. Листинг программы «NATURA»
- •П2. Листинг программы «SAMPLE»
- •П3. Листинг программы «MODELL»
- •П4. Листинг программы «DIAGRAMM»
- •П5. Листинг программы «SIMPLY»
- •П6. Листинг программы «SIMPLINT»
- •П7. Листинг программы «RASM»
- •П8. Листинг программы «TRANSY»
- •П9. Листинг программы «KOMMY»
- •П10. Листинг программы «MARK»
- •П11. Листинг программы «SETY»
- •РЕКОМЕНДУЕМАЯ ЛИТЕРАТУРА
- •Содержание
- •ВВЕДЕНИЕ
- •1.1. Организационно-технологическая надёжность строительства. Её роль в повышении качества производства работ
- •1.2. Критерии оценки организационно-технологической надежности. Методики их определения
- •1.3. Методики и программы расчета технико-экономических показателей систем машин
- •1.4. Работы по формированию рациональных систем машин
- •1.5. Задачи и подходы к оптимизации распределения систем машин по строительным объектам
- •1.6. Методические и программные средства оценки инвестиционных проектов
- •1.7. Цель и задачи исследований
- •2. ТЕОРЕТИЧЕСКИЕ ОСНОВЫ РАБОТЫ СТРОИТЕЛЬНЫХ МАШИН
- •2.1. Критерии оценки состояния организационно-технологической надежности работы машин
- •2.2. Обработка натурных испытаний строительных машин
- •2.3. Модель надежности инвестиционных проектов
- •2.4. Модель надежности календарного планирования
- •2.5. Модель надежности работы гидротранспортных систем
- •2.6. Модель надежности технологических процессов
- •2.7. Выводы
- •3. ПРОГНОЗИРОВАНИЕ И ОЦЕНКА ОРГАНИЗАЦИОННО-ТЕХНОЛОГИЧЕСКОЙ НАДЕЖНОСТИ РАБОТЫ СИСТЕМ МАШИН
- •3.1. Методологические подходы к прогнозированию и оценке систем
- •3.2. Прогнозирование и оценка организационно-технологической надежности инвестиционных проектов
- •3.3. Прогнозирование и оценка организационно-технологической надежности календарных планов строительства
- •3.4. Прогнозирование и оценка организационно-технологической надежности очередности строительства
- •3.5. Прогнозирование и оценка организационно-технологической надежности работы систем машин
- •3.6. Прогнозирование и оценка организационно-технологической надежности работы комплектов машин для производства земляных работ
- •3.7. Прогнозирование и оценка организационно-технологической надежности работы комплектов машин для производства бетонных работ
- •3.8. Моделирование организационно-технологической надежности работы комплектов машин для перевозки грузов
- •3.9. Прогнозирование и оценка организационно-технологической надежности работы монтажных кранов
- •3.10. Выводы
- •4. ОПТИМИЗАЦИЯ СИСТЕМ МАШИН
- •4.1. Оптимизации парка машин
- •4.2. Оптимизация комплекса машин
- •4.3. Оптимизация очередности выполнения строительных работ
- •4.4. Оптимизация распределения машин в строительстве
- •4.5. Выводы
- •5. РЕКОМЕНДАЦИИ ПО ЭФФЕКТИВНОМУ ИСПОЛЬЗОВАНИЮ СИСТЕМ МАШИН
- •5.2. Оценка организационно-технологической надёжности инвестиционных проектов
- •5.3. Оценка организационно-технологической надёжности календарного планирования
- •5.4. Оценка организационно-технологической надёжности строительного производства на примере земляных работ
- •5.5. Управление организационно-технической надежностью работы строительно-дорожных машин
- •5.6. Выводы
- •ЗАКЛЮЧЕНИЕ
- •СПИСОК ИСПОЛЬЗОВАННОЙ ЛИТЕРАТУРЫ
- •Содержание
- •ВВЕДЕНИЕ
- •1. ТЕОРЕТИЧЕСКИЕ ОСНОВЫ ФОРМИРОВАНИЯ ПАРКОВ МАШИН
- •1.3. Оценка надежности инвестиционных проектов
- •1.4. Оценка надежности календарного планирования
- •1.5. Оценка надежности проектных показателей работы машин
- •1.6. Оценка надежности технологических процессов
- •2.1. Методологические подходы к моделированию
- •2.2. Моделирование организационно-технологической надежности инвестиционных проектов
- •2.3. Моделирование организационно-технологической надежности календарных планов строительства
- •2.4. Моделирование организационно-технологической надежности очередности строительства
- •2.5. Моделирование организационно-технологической надежности работы парков машин
- •2.6. Моделирование организационно-технологической надежности работы комплектов машин для производства земляных работ
- •2.7. Моделирование организационно-технологической надежности работы комплектов машин для производства бетонных работ
- •2.8. Моделирование организационно-технологической надежности работы комплектов машин для перевозки грузов
- •2.9. Моделирование организационно-технологической надежности работы монтажных кранов
- •3. ОПТИМИЗАЦИЯ КОЛИЧЕСТВА И ТИПОВ МАШИН, СОСТАВЛЯЮЩИХ ПАРК МАШИН
- •3.1. Методика оптимизации составов парка машин
- •3.2. Оптимизация комплекса машин
- •3.3. Формирование ресурсосберегающего комплекса машин
- •3.4. Оптимизация очередности выполнения механизированных объёмов на строительных объектах
- •3.5. Оптимальное распределение машин в строительстве
- •4.1. Возможности методического и программного обеспечения
- •4.2. Модели организационно-технологической надёжности инвестиционных проектов
- •4.3. Модели организационно-технологической надёжности календарного планирования
- •4.4. Модели организационно-технологической надёжности строительного производства на примере земляных работ
- •4.5. Управление организационно-технической надежностью работы строительно-дорожных машин
- •4.6. Рекомендации по определению эффективности применения новых строительных машин и механизмов
- •ЗАКЛЮЧЕНИЕ
- •Содержание
- •ВВЕДЕНИЕ
- •1.1. Оценка надежности работы строительных машин
- •1.2. Оценка организационно-технологической надежности работы строительных машин
- •1.3. Действующие методики расчета технико-экономических показателей проектных решений
- •1.5. Защита свай от коррозии
- •2. ОБОСНОВАНИЕ СПОСОБОВ ПОГРУЖЕНИЯ СВАЙ
- •2.1. Моделирование погружения свай
- •2.2. Модели способов погружения свай
- •2.3. Влияние условий производства работ на экономическую эффективность свайно-бурового производства
- •2.4. Анализ показателей производства свайных работ
- •3. ОБОСНОВАНИЕ КОМПЛЕКСА МАШИН ДЛЯ ПОГРУЖЕНИЯ СВАЙ
- •3.1. Автоматизация проектирования технологических процессов
- •3.2. Алгоритм обоснования способов погружения свай
- •3.3. Выводы
- •4. ФОРМИРОВАНИЕ РЕСУРСОСБЕРЕГАЮЩИХ ПАРКОВ, КОМПЛЕКСОВ И КОМПЛЕКТОВ СТРОИТЕЛЬНЫХ МАШИН
- •4.1. Общий подход
- •4.2. База технических и экономических показателей строительных машин и механизмов
- •4.3. База данных по организационно-технологической надёжности
- •4.4. База справочной информации для организационно-технологических расчётов
- •4.5. Выводы
- •5. ОЦЕНКА ТЕХНИЧЕСКОЙ НАДЕЖНОСТИ РАБОТЫ БУРОВЫХ СТАНКОВ
- •6. МОДЕЛИРОВАНИЕ НАДЕЖНОСТИ РАБОТЫ БУРОВЫХ СТАНКОВ
- •ЗАКЛЮЧЕНИЕ
- •СПИСОК ИСПОЛЬЗОВАННОЙ ЛИТЕРАТУРЫ
- •Содержание
- •ВВЕДЕНИЕ
- •1. ОСНОВНЫЕ ПОНЯТИЯ И ОПРЕДЕЛЕНИЯ
- •1.1. Строительство как отрасль материального производства
- •1.2. Трудовые ресурсы отрасли (строительные организации и фирмы)
- •1.3. Возникновение и развитие науки «Организация, планирование и управление строительством»
- •2. НАУЧНЫЕ ОСНОВЫ ОРГАНИЗАЦИИ СТРОИТЕЛЬСТВА
- •2.1. Основные термины и понятия организации строительства
- •2.3. Понятие «инвестиционный проект» и управление проектом
- •3. ПОДГОТОВКА СТРОИТЕЛЬНОГО ПРОИЗВОДСТВА
- •3.1. Организационно-техническая подготовка к строительству
- •3.2. Организация проектно-изыскательских работ для строительства
- •4. МОДЕЛИРОВАНИЕ ОРГАНИЗАЦИИ СТРОИТЕЛЬНОГО ПРОИЗВОДСТВА
- •4.1. Понятие и виды организационно-технологических моделей строительства
- •4.2. Моделирование поточного строительства
- •4.2.1. Сущность поточной организации строительства
- •4.2.2. Классификация строительных потоков
- •4.2.3. Параметры строительных потоков
- •4.2.4. Моделирование ритмичных строительных потоков
- •4.2.5. Моделирование неритмичных строительных потоков
- •4.2.6. Установление оптимальной очередности возведения объектов
- •4.3. Моделирование строительства на основе системы сетевого планирования и управления строительством
- •4.3.2. Основные понятия метода СПУ и элементы сетевых моделей
- •4.3.3. Классификация сетевых графиков
- •4.3.4. Правила построения сетевых моделей
- •4.3.5. Расчетные параметры сетевых графиков и формулы их определения
- •4.3.6. Расчет сетевых графиков и построение их в масштабе времени
- •4.3.7. Корректировка и оптимизация сетевых графиков
- •5. ПРОЕКТИРОВАНИЕ ОРГАНИЗАЦИИ СТРОИТЕЛЬСТВА
- •5.1. Разработка проекта организации строительства (ПОС)
- •5.1.1. Характеристика исходных данных
- •5.1.3. Определение потребности в материально-технических, трудовых и водо-энергетических ресурсах
- •5.1.3.1. Расчет потребности в строительных материалах, конструкциях и полуфабрикатах
- •5.1.3.2. Расчет потребности в водо-энергетических ресурсах
- •5.1.3.3. Определение затрат труда
- •5.1.4. Выбор организационно-технологических схем возведения зданий
- •5.1.5. Выбор методов организации работ
- •5.1.6. Составление сводного календарного плана строительства (СКПС). Составление календарного плана подготовительного периода
- •5.1.6.2. Расчет параметров комплексного потока строительства промышленного предприятия
- •5.1.7. Разработка стройгенпланов на основной и подготовительный периоды строительства с расчетом строительного хозяйства
- •5.1.8. Охрана труда и противопожарные мероприятия
- •5.1.9. Технико-экономическая оценка ПОС
- •6. РАЗРАБОТКА ПРОЕКТА ПРОИЗВОДСТВА РАБОТ (ППР) НА ОБЪЕКТЕ
- •6.1. Характеристика исходных данных и объекта строительства
- •6.2. Подсчет объемов работ
- •6.3. Выбор методов производства работ, основных строительных машин и механизмов
- •6.3.1. Земляные работы.
- •6.3.2. Возведение подземной и надземной частей здания
- •6.4. Определение трудоемкости работ
- •6.5. Календарное планирование
- •6.5.1. Проектирование линейного графика
- •6.5.2. Проектирование циклограммы
- •6.5.3. Проектирование сетевого графика
- •6.6. Проектирование стройгенплана объекта с расчетом строительного хозяйства
- •6.6.1. Потребность во временных зданиях и сооружениях
- •6.6.2. Определение площадей складов
- •6.6.3. Водоснабжение строительной площадки
- •6.6.4. Электроснабжение строительной площадки
- •6.6.5. Снабжение строительства сжатым воздухом
- •6.7. Мероприятия по охране труда и противопожарной безопасности
- •6.8. Технико-экономическая оценка ППР
- •7. ОРГАНИЗАЦИЯ МАТЕРИАЛЬНО-ТЕХНИЧЕСКОГО ОБЕСПЕЧЕНИЯ СТРОИТЕЛЬСТВА
- •7.1. Понятие и масштабы материально-технической базы строительства.
- •7.2. Организация и источники поставок материально-технических ресурсов
- •7.3. Понятие логистики
- •7.4. Учет и контроль расхода материалов
- •7.5. Организация производственно-технологической комплектации строящихся объектов
- •8. ОРГАНИЗАЦИЯ И ЭКСПЛУАТАЦИЯ СТРОИТЕЛЬНЫХ МАШИН
- •8.1. Основные положения и понятия
- •8.2. Организационные формы эксплуатации парка строительных машин
- •9. ОРГАНИЗАЦИЯ ТРАНСПОРТА НА СТРОИТЕЛЬСТВЕ
- •9.1. Общие положения
- •9.2. Организация автотранспорта на строительстве
- •Библиографический указатель
- •ВВЕДЕНИЕ
- •1. СУЩНОСТЬ УПРАВЛЕНИЯ СТРОИТЕЛЬНЫМ ПРОИЗВОДСТВОМ
- •1.1. Сущность понятия «управление строительством»
- •1.2. Строительство как производственная система
- •1.3. Управляющая и управляемая подсистемы
- •2.1. Закономерности управления
- •2.2. Принципы управления
- •3. ОРГАНИЗАЦИЯ УПРАВЛЕНИЯ
- •3.1. Процесс управления
- •3.2. Функции управления
- •4. ОРГАНИЗАЦИЯ СИСТЕМ УПРАВЛЕНИЯ
- •4.1. Требования к системам управления
- •4.2. Типы организационных структур управления
- •4.3. Организационные формы и структура управления отраслью
- •4.4. Виды подрядных строительно-монтажных организаций
- •4.5. Организационная структура аппарата управления строительных организаций
- •5. ТЕХНОЛОГИЯ И ТЕХНИКА УПРАВЛЕНИЯ
- •5.1. Управленческая информация ее виды
- •5.2. Техника управления
- •6. УПРАВЛЕНЧЕСКИЕ РЕШЕНИЯ
- •6.1. Роль управленческих решений в процессе управления
- •6.3. Субъективные недостатки решений и пути их устранения
- •6.4. Организация принятия и реализации управленческих решений
- •7. МЕТОДЫ ПРИНЯТИЯ УПРАВЛЕНЧЕСКИХ РЕШЕНИЙ
- •7.1. Системный подход
- •7.2. Моделирование систем
- •7.3. Системный анализ
- •7.4. Экспертные методы принятия решения
- •7.5. Логические и логико-математические методы принятия решений
- •8. СТИЛИ И МЕТОДЫ УПРАВЛЕНИЯ
- •8.1. Социально-психологические аспекты управления
- •8.2. Стили управления
- •8.3. Типичные недостатки работников сферы управления
- •8.4. Методы управления
- •9. ОПЕРАТИВНОЕ УПРАВЛЕНИЕ СТРОИТЕЛЬНЫМ ПРОИЗВОДСТВОМ
- •9.1. Общие положения
- •9.2. Разработка месячных оперативных планов
- •9.3. Недельно-суточное оперативное планирование
- •9.4. Диспетчерское управление в строительстве
- •10.1. Научные основы управления качеством строительства
- •10.2. Система контроля качества в строительстве
- •10.3. Организация приемки объектов в эксплуатацию
- •Библиографический указатель
- •Содержание
pн и pк |
– минимальная и максимальная плотность бетонной смеси, |
|
т/м3; |
|
|
Пн и Пк |
– минимальная и максимальная пористость бетонной смеси, |
|
%; |
|
|
pон и pок |
– минимальное и максимальное атмосферное давление на |
|
смесь, МПа; |
||
γбсн |
и γбск |
– минимальное и максимальное статическое давление на |
смесь, МПа; |
||
tвибн |
и tвибк |
– минимальная и максимальная продолжительность вибри- |
рования, с;
tперн и tперк – минимальная и максимальная продолжительность перестановки вибратора, с.
С помощью выражения Eр = f (R в) строится график. При этом E принимается для пористости П = 0,04. Предельный радиус действия внутреннего вибратора rо будет соответствовать на полученной кривой
точке Eр = Eр,min.
Проведенные соискателем исследования позволили выявить основные факторы, влияющие на ОТН работы глубинных вибраторов
(таблица 3.39).
Таблица 3.39. Факторы, влияющие на ОТН работы глубинных вибраторов
Показатель |
Обозначение |
Поле |
Продолжительность смены, ч |
Tс |
Ts |
Коэффициент использования по времени |
Kв |
Kv |
Толщина прорабатываемого слоя, мм |
h |
H |
Плотность бетонной смеси, т/м3 |
p |
Pbs |
Пористость бетонной смеси |
П |
Pr |
Атмосферное давление на смесь, МПа |
P0 |
Pa |
Давление на смесь от пригруза, МПа |
pст |
Ps |
Продолжительность вибрирования, с |
tвиб |
Tv |
Продолжительность переустановки вибратора, с |
tпер |
Tp |
3.8. Моделирование организационно-технологической надежности работы комплектов машин для перевозки грузов
Весь транспорт, обеспечивающий доставку грузов от поставщиков непосредственно на строительные площадки, является технологическим. По своей роли этот транспорт уже не ограничивается механическим перемещением грузов в обслуживаемом строительном производстве. Он приобретает характер одного из организующих факторов и, в первую очередь, обеспечивает ритмичность производства строительно-монтажных работ и ввода объектов в эксплуатацию [72,
129
231, 239]. Выбор способа организации технологических перевозок комплектов материалов и изделий полностью зависит от принятого способа выполнения строительно-монтажных работ.
В настоящее время актуальна проблема согласованной работы автомобильного транспорта с обслуживаемым строительным производством, поэтому важное значение приобретает разработка транспортного процесса путём его моделирования. Формализация транспортного процесса в строительстве обычно начинается с изучения его структуры, в результате чего появится содержательное описание процесса. Последнее является исходным материалом при последующих этапах формализации: построения формализованной схемы и математической модели, а также программного обеспечения
[165, 166].
Характерный пример моделирования транспортного процесса изложен ниже. Рассматривая АТП, которое имеет ограниченный парк машин, обслуживающих строительную организацию. Требуется минимизировать суммарные затраты на доставку грузов при перевозке материалов и конструкций. Задача может быть решена несколькими методами линейного и нелинейного программирования с теми или иными допущениями и ограничениями [279–282].
1.С помощью транспортной задачи.
2.Симплекс-методом.
3.Перебором всех возможных вариантов.
4.С помощью задачи о назначении.
5.С помощью теории игр.
6.Методом Монте-Карло и т. д.
Требуется, из перечисленных выше методов, выбрать наиболее подходящий метод решения подобного типа задач. К сожалению, нет абсолютной уверенности, что разрабатываемый метод окажется самым оптимальным. Задача эта сложная. Не исключена возможность разработки алгоритмов и программ для решения данной задачи методом Монте-Карло и с помощью теории игр.
Сменная производительность автотранспорта
|
P |
n |
m T K |
|
K |
|
|
|
|
||||
Пс = |
ат |
∑ |
с |
|
|
|
г |
|
|
в , |
|
(3.33) |
|
n |
|
t |
|
|
|
|
|
||||||
|
= |
|
ат |
|
|
|
|
|
|
|
|||
|
|
i 1 |
|
|
|
|
|
|
|
|
|
|
|
|
tат = tпогр + |
|
Lгруж |
+tразгр + |
Lпор |
, |
|||||||
|
|
|
|
||||||||||
|
|
|
|
|
Vгруж |
|
|
Vпор |
|||||
|
|
|
|
N ≥ Nсут , |
|
|
|
||||||
|
|
|
Lн |
≤ L |
|
|
≤ Lк |
, |
|
|
|||
|
|
|
груж |
|
|
|
груж |
груж |
|
|
|
||
|
|
|
|
|
|
130 |
|
|
|
|
|
|
Lнпор ≤ Lпор ≤ Lкпор ,
Vгружн ≤Vгруж ≤Vгружк ,
Vпорн ≤Vпор ≤Vпорк ,
Tсн ≤ Tс ≤ Tск ,
Kгн ≤ Kн ≤ Kгк ,
Kвн ≤ Kв ≤ Kвк , tпогрн ≤ tпогр ≤ tпогрк ,
tразгрн ≤ tразгр ≤ tразгрк ,
где Pат – грузоподъемность автотранспорта, т; n – количество проектировок;
tат – время цикла транспортного процесса, ч;
N – необходимое количество автотранспорта, исходя из условия обеспечения непрерывной работы и дальности возки груза;
равномерно распределенные случайные величины:
Tc – продолжительность смены, ч;
Kв – коэффициент использования машины по времени, учитывающий
неизбежные внутрисменные простои, вызванные технологией и организацией работы машин;
Kг – коэффициент использования автотранспорта по грузоподъемно-
сти;
tпогр – время погрузки автотранспорта с учетом установки машины под
погрузку, с;
Lгруж, Lпор – расчетное расстояние перемещения грунта и длина пути
порожнего хода автотранспорта, м;
Vгруж, Vпор – скорость движения груженого и порожнего автотранспор-
та, м/с;
tразгр – время разгрузки автотранспорта с учетом установки машины под
разгрузку, с;
диапазоны изменения случайных величин:
Lнгруж и Lкгруж – минимальное и максимальное расстояние перемещения грунта автомобилем-самосвалом, км;
Lнпор и Lкпор – минимальная и максимальная длина пути порожнего хода автотранспорта, км;
Vгружн и Vгружк – минимальная и максимальная скорость движения груженого автотранспорта, км/ч;
131
Vпорн и Vпорк – минимальная и максимальная скорость движения порожнего автотранспорта, км/ч;
Tсн и Tск – минимальная и максимальная продолжительность смены, ч;
Kгн и Kгк – минимальный и максимальный коэффициент использования автотранспорта по грузоподъемности;
Kвн и Kвк – минимальный и максимальный коэффициент использования машины по времени;
tпогрн и tпогрк – минимальное и максимальное время погрузки автотранспорта, ч;
tразгн и tразгк – минимальная и максимальная продолжительность разгруз-
ки автотранспорта, ч.
Проведенные соискателем исследования позволили выявить основные факторы, влияющие на ОТН работы автотранспорта (таблица
3.40).
Таблица 4.40. Факторы, влияющие на ОТН работы автотранспорта
Показатель |
Обозначение |
Поле |
|
|
|
Число ковшей грунта, загружаемых в кузов машины |
m |
Nk |
Коэффициент наполнения ковша |
Kн |
Kn |
Коэффициент использования по времени |
Kв |
Kv |
Продолжительность смены, ч |
Tс |
Ts |
Время установки автотранспорта под погрузку, с |
tуст |
Tus |
Количество автотранспорта, шт. |
N |
Nat |
Время выгрузки, с |
tразгр |
Trg |
Дальность возки грунта, м |
Lгруж |
Lg |
Длина пути порожнего хода автотранспорта, м |
Lпор |
Lp |
Средняя скорость возки грунта, км/ч |
Vгруж |
Vg |
Средняя скорость порожнего автотранспорта, км/ч |
Vпор |
Vp |
3.9. Прогнозирование и оценка организационно-технологической надежности работы монтажных кранов
Выбор комплектов монтажных кранов для возведения объектов является центральным звеном обоснования организационно- технологических схем строительства отдельных зданий, сооружений и их комплексов при разработке проектов организации строительства и при выборе наиболее рациональных методов производства строитель- но-монтажных работ во время разработки проектов производства работ на отдельном здании.
132
Для автоматизации выбора комплекта монтажных кранов для строительства зданий и сооружений создана база данных по автомобильным, башенным, гусеничным и пневмоколесным кранам и разработана экономико-математическая модель формирования комплектов кранов из база данных. С помощью этой модели из базы данных выбирается необходимый в конкретных условиях комплект монтажных кранов для производства строительно-монтажных работ с минимальными затратами [87, 164, 317].
Общая схема автоматизированного выбора монтажных кранов для строительства зданий и сооружений представлена на рисунке 3.9. Процесс формирования комплекта строительных кранов позволяет по единой методике оценить эффективность как отдельной машины, так и любого комплекта, показатели которых хранятся в базе данных [163].
Для уменьшения объема информации, необходимой для подбора марки монтажного крана, и упрощения поиска табличная информация аппроксимирована с помощью полиномов второй степени. Применение математических моделей для подбора марки крана позволило повысить эффективность использования ЭВМ за счет сокращения объема информации, упрощения поиска и уменьшения времени счета при стандартной ошибке не более одного процента.
133
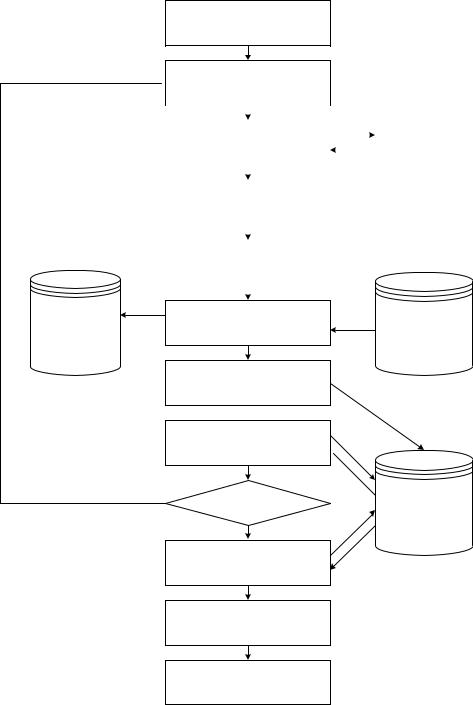
Ввод исходных данных для формирования комплектов монтажных кранов
Создание модели технологии монтажа сооружения
|
|
|
|
|
Формирование |
|
|
||||
Формирование расчётной |
|
|
|
комбинаций |
|
схемы технологии монтажа |
|
|
|
возможных |
|
сооружения |
|
|
|
загружений |
|
|
|
|
|||
|
|
|
|
|
крана |
|
|
||||
|
|
|
|
|
|
Подготовка данных для расчёта |
|
|
|
|
|
параметров монтажных кранов |
|
|
|
|
|
|
|
|
|
|
|
|
|
|
|
|
|
|
|
|
|
|
|
Формирование возможных |
|
|
|
|
|
вариантов комплектов |
|
|
|
|
|
монтажных кранов |
|
|
|
|
|
|
|
|
|
|
|
|
|
|
|
|
|
База справочной информации
Выбор из базы данных монтажных кранов для формирования комплектов
Формирование выборки монтажных кранов под первое загружение
База данных по автомобильным, пневмоколёсным,
гусеничным и башенным кранам
Формирование выборки кранов, удовлетворяющих всем возможным загружениям
Нет |
Краны подобраны? |
|
Расчёт значений целевой функции для выборки монтажных кранов
Выбор лучшего варианта монтажных кранов для строительства сооружения
Создание технологических схем, карт и проектов производства работ
Выборка по монтажным кранам
Рисунок 3.9. Схема автоматизированного выбора монтажных кранов для строительства зданий и сооружений
134

Модель подбора монтажных кранов объединяет в себе две модели. Во-первых, модель подбора кранов по техническим параметрам. Во- вторых, имитационную модель экономического обоснования выбора кранов с учетом ОТН их работы. На рисунке 3.10 приведена расчетная схема монтажа конструкций стреловыми кранами на гусеничном, пневмоколесном и автомобильном ходу.
Рисунок 3.10. Схема для определения требуемых параметров стреловых кранов
Стреловые краны подбираются по следующим параметрам:
–требуемая грузоподъемность − масса самого тяжелого элемента с учетом стропующих устройств, т;
–требуемая высота подъема крюка Hкр – расстояние от уровня стоянки крана до крюка при стянутом полиспасте на определенном вылете крюка, м;
–требуемый вылет крюка Lкр − расстояние между вертикальной осью вращения крана и вертикальной осью, проходящей через центр крюка, м;
–требуемая длина стрелы Lстр − расстояние от пяты стрелы до оси головного блока, м.
Требуемые характеристики крана определяются по следующим формулам:
Qкр =1,1 Pм + Pс , |
(3.34) |
Hкр = Hо + H з + Hэл + Hс , |
(3.35) |
L = (b + d) (Hо + H з + Hэл + Hс + Hп − Hш ) + e , (3.36)
кр |
Hп + Hс |
|
|
|
135 |
b − расстояние от центра строповки поднимаемого элемента до ближайшего к стреле крана края элемента, м;
d − расстояние между геометрической осью стрелы и элементом, м; Hп − минимальная длина полиспаста, м;
Hш − высота от уровня стоянки крана до шарнира пяты стрелы, м;
e − расстояние от шарнира стрелы до оси вращения крана, м;
Ниже приведена имитационная модель работы монтажных кранов с учетом ОТН их работы.
|
|
|
По = |
60 Q Kв , |
|
|
|
|
|
|
(3.37) |
|
|
|
|
|
||||||||||||
|
|
|
|
|
|
|
|
|
Tц |
|
|
|
|
|
|
|
|
|
|
|
|
|
|
|
||||
|
|
|
|
|
|
|
|
n |
|
|
|
|
|
|
|
|
|
|
|
|
|
|
|
|
|
|
|
|
|
|
|
|
Q = |
∑(1,1 Pмi + Pсi ) Ni |
|
|
|
|
|
||||||||||||||||||
|
|
|
|
i=1 |
|
|
|
|
|
|
|
|
|
|
|
|
, |
|
|
|
|
|
|
|||||
|
|
|
|
|
|
|
|
|
n |
|
|
|
|
|
|
|
|
|
|
|
|
|||||||
|
|
|
|
|
|
|
|
|
|
|
|
|
∑Ni |
|
|
|
|
|
|
|
|
|
|
|
|
|
||
|
|
|
|
|
|
|
|
|
|
|
|
|
i=1 |
|
|
|
|
|
|
|
|
|
|
|
|
|
|
|
|
|
|
|
|
|
|
Tц |
= Tмаш +Tруч , |
|
|
|
|
|
|
|
|
|
|
||||||||||
|
|
n |
2 |
H |
пi |
|
|
|
|
2 α |
i |
|
|
S |
тi |
|
|
|
|
S |
дi |
|
|
|
||||
|
|
|
|
|
|
|
|
|
|
|
|
|
|
|
|
|
|
|
|
|
|
|
||||||
|
|
∑ |
|
|
|
|
|
+ |
|
|
|
|
+ |
|
|
|
|
Kс + |
|
|
|
|
Ni |
|||||
|
|
Vп |
|
|
|
|
360 ω |
|
Vт |
|
Vд |
|||||||||||||||||
|
|
i=1 |
|
|
|
|
|
|
|
|
|
|
|
|
|
|
|
|
||||||||||
T |
= |
|
|
|
|
|
|
|
|
|
|
|
|
|
|
|
|
|
|
|
|
|
|
|
|
|
, |
|
|
|
|
|
|
|
|
|
|
|
|
|
n |
|
|
|
|
|
|
|
|
|
|
|
|
|
|||
маш |
|
|
|
|
|
|
|
|
|
|
|
|
|
|
|
|
|
|
|
|
|
|
|
|
|
|
|
|
|
|
|
|
|
|
|
|
|
|
|
|
|
∑Ni |
|
|
|
|
|
|
|
|
|
|
|
||||
|
|
|
|
|
|
|
|
|
|
|
|
|
|
i=1 |
|
|
|
|
|
|
|
|
|
|
|
|
|
|
|
|
|
|
|
|
|
|
|
|
|
|
|
n |
|
|
|
|
|
|
|
|
|
|
|
|
|
|
|
|
|
|
|
|
T |
|
|
|
|
|
|
∑Tручi |
Ni |
|
|
|
|
|
|
|
|
|
|
|||||
|
|
|
|
|
|
|
|
= |
i=1 |
|
|
|
|
|
|
, |
|
|
|
|
|
|
|
|
||||
|
|
|
|
|
|
|
|
|
n |
|
|
|
|
|
|
|
|
|
|
|
|
|
||||||
|
|
|
|
|
|
руч |
|
|
|
|
|
|
|
|
|
|
|
|
|
|
|
|
|
|
||||
|
|
|
|
|
|
|
|
|
|
|
|
|
∑Ni |
|
|
|
|
|
|
|
|
|
|
|
i=1
Hпi = Hоi + Hз + H элi + Hсi ,
Tсн ≤ Tс ≤Tск ,
Kвн ≤ Kв ≤ Kвк , Hпнi ≤ Hвi ≤ Hвкi , Vпн ≤Vп ≤Vпк ,
αiн ≤αi ≤ αiк ,
ωн ≤ ω ≤ ωк ,
Sтнi ≤ Sтi ≤ Sткi ,
Vтн ≤Vт ≤Vтк ,
Sднi ≤ Sдi ≤ Sдкi ,
Vдн ≤Vд ≤Vдк ,
136
Hонi ≤ Hоi ≤ Hокi ,
где n – количество проектировок;
Q − средняя масса элементов, монтируемых краном, т;
Тц − средняя продолжительность рабочего цикла (складывающаяся из времени, затрачиваемого на строповку груза, на перемещение груза к месту монтажа, на его удержание при временном закреплении, на его расстроповку и возвращение грузозахватного органа в исходное положение), мин;
Труч − среднее время ручных операций (строповка элементов, установка, временное крепление, выверка и расстроповка), мин;
Тмаш − среднее время машинных операций, включающее подъем крюка с грузом и опускание свободного крюка, поворот стрелы вокруг вертикальной оси при подаче элемента от площадки складирования к месту его установки, передвижку крана вдоль фронта работ, мин;
Pмi − масса i-го элемента, поднимаемого краном, т;
Pсi − масса строповочных устройств и монтажной оснастки для i-го элемента, т;
Hз − запас по технике безопасности между опорой и элементом при его перемещении к месту установки, м;
Hэлi − высота монтируемого i-го элемента, м;
Hсi − монтажная высота строповочных приспособлений для монтажа i- го элемента, м;
Ni − количество i-х элементов, шт.;
равномерно распределенные случайные величины:
Tc – продолжительность смены, ч;
Кв − коэффициент использования крана по времени;
Нпi − средняя высота подъема и опускания крюка крана при монтаже i- го элемента, принимается ориентировочно по монтажному разрезу, м;
Vп − средняя скорость перемещения крюка по вертикали, м/мин; αi − средний угол поворота крана при монтаже i-го элемента, град; ω − скорость вращения крана (число оборотов стрелы), об./мин;
Sтi − расстояние перемещения элемента по горизонтали за счет перемещения грузовой каретки башенных кранов с балочной стрелой при монтаже i-го элемента, м;
Vт − скорость перемещения грузовой каретки, м/мин;
Sдi − средняя длина продольной передвижки крана при монтаже i-го элемента, м;
Vд − скорость перемещения крана, м/мин;
137
Кс − коэффициент совмещения операций;
Hоi − средняя отметка, на которую устанавливают i-й элемент (от уровня стоянки крана до опоры), м;
Тручi − время ручных операций при монтаже i-го элемента, мин;
диапазоны изменения случайных величин:
Tсн и Tск – минимальная и максимальная продолжительность смены, ч;
Kвн и Kвк – минимальный и максимальный коэффициент использования машины по времени;
Hпнi и Hпкi – минимальная и максимальная высота подъема и опускания крюка крана при монтаже i-го элемента, м;
Vпн и Vпк – минимальная и максимальная скорость перемещения крюка по вертикали, м/мин;
ωн и ωк – минимальная и максимальная скорость вращения крана, об./мин;
αiн и αiк – минимальный и максимальный угол поворота крана при монтаже i-го элемента, град;
Sтнi и Sткi – минимальное и максимальное расстояние перемещения
элемента по горизонтали за счет перемещения грузовой каретки башенных кранов с балочной стрелой при монтаже i-го элемента, м;
Vтн и Vтк – минимальная и максимальная скорость перемещения грузовой каретки, м/мин;
Sднi и Sдкi – минимальная и максимальная длина продольной передвижки крана при монтаже i-го элемента, м;
Vдн и Vдк – минимальная и максимальная скорость перемещения крана, м/мин;
Kсн и Kск – минимальный и максимальный коэффициент совмещения операций;
Hонi и Hокi – минимальная и максимальная средняя отметка, на которую устанавливают i-й элемент, м;
T н |
и T к |
− минимальное и максимальное время ручных операций |
ручi |
ручi |
|
при монтаже i-го элемента, мин.
Общая трудоемкость работ на объекте определяется по формуле
Qобщ = Tм Nр + ∑Qвсп , |
(3.38) |
а суммарная трудоемкость вспомогательных работ – по формуле
∑Qвсп = Qтр +Qм.д. +Qр +Qпр , |
(3.39) |
где Тм − продолжительность работы крана на объекте, смен;
138
Nр − состав звена монтажников, включая машиниста крана, чел.; ΣQвсп − суммарная трудоемкость вспомогательных работ, чел.-смен; Qтр − трудоемкость транспортирования крана, чел.-смен;
Qм. д. − трудоемкость монтажа, демонтажа, чел.-смен; Qр − трудоемкость текущего ремонта, чел.-смен;
Qпр − трудоемкость прочих подготовительных и заключительных работ (устройство и разборка подкрановых путей), чел.-смен.
В ряде случаев при расчете эксплуатационной производительности крана учитывают также возможное снижение производительности в зависимости от технического состояния машины, квалификации машиниста, комфортности управления машиной при помощи коэффициента Км = 0,85.
Проведенные исследования позволили выявить основные факторы, влияющие на ОТН работы монтажных кранов (таблицы 3.41–3.43).
Таблица 3.41. Факторы, влияющие на ОТН работы монтажных кранов
Показатель |
Обозначе- |
Значимость |
|
ние |
фактора, % |
|
|
|
Средневзвешенная масса монтируемых элементов, т |
Pс |
32,74 |
Коэффициент использования по времени |
Kв |
32,69 |
Время ручных операций при монтаже i-го элемента, мин |
Тручi |
31,14 |
Коэффициент совмещения операций |
Кс |
1,73 |
Средняя высота подъема и опускания крюка крана при |
Нп |
0,60 |
монтаже элементов, м |
|
|
Средний угол поворота крана при монтаже элементов, |
α |
1,09 |
град |
|
|
|
|
Таблица 3.42. Модель сменной производительности стреловых
|
кранов |
Модель |
Значимость переменной, % |
|
|
Пс = + 4,5025 |
|
+ 24,126 * Pс |
32,74 |
+ 90,172 * Kв |
32,69 |
– 4,5449 * Труч |
31,14 |
– 5,1013 * Кс |
1,73 |
– 0,0192 * α |
1,09 |
|
|
– 0,1109 * Нп |
0,60 |
Таблица 3.43. Характеристика модели сменной производительности стреловых кранов
Показатель |
Величина |
Доля объясненной вариации, % |
99,29044 |
Коэффициент множественной корреляции |
0,99645 |
Средний отклик |
72,59910 |
139

Стандартная ошибка в % от среднего отклика |
1,14 |
Стандартная ошибка |
0,83118 |
Общий F – критерий регрессии |
2135105,08 |
Табличное значение общего F – критерия |
3,84 |
Модель подбора башенных кранов
Расчетная схема выбора башенного крана приведена на рисунке 3.11.
Рисунок 3.11. Схема для определения требуемых параметров башенных кранов
Башенные краны подбираются следующим образом:
–определяется требуемая грузоподъемность.
–определяется требуемая высота подъема крюка.
–определяется требуемый вылет крюка для башенных кранов определяется с учетом максимального приближения крана к строящемуся зданию по формуле
Lкр = Rх + d + B , |
(3.40) |
B − ширина здания, включая толщину стен, м;
d − расстояние между поворотной платформой и стеной здания (или выступающими ее частями;
Rx − радиус хвостовой части для кранов с нижним противовесом, у которых габарит поворотной платформы выступает за крановый путь или для кранов с верхним противовесом половина ширины подкранового пути, м.
140

Для автоматизации расчета ОТН использования комплектов и отдельных машин с помощью имитационных моделей разработано соответствующее программное обеспечение. Последнее позволяет для любой имитационной модели работы строительных машин методом Монте-Карло сформировать выборку заданного объема и определить её принадлежность закону нормального. Далее с заданным уровнем ОТН определяется производительность, себестоимость и другие показатели работы машин. Ниже приведен пример расчета стоимости, продолжительности и ОТН работы гусеничного крана СКГ-25–36 (рисунок 3.12).
Разработанные в СГУПС имитационные модели оценки организа- ционно-технологической надежности использования машин и механизмов позволяют по единой методике оценивать надежность работы строительных кранов [14, 16]. Предложенный универсальный алгоритм формирования комплектов машин, показатели которых хранятся в базе данных. Алгоритм создания комплектов может быть применен при производстве земляных работ, монтаже зданий и так далее. С помощью этого алгоритма можно оценивать эффективность приобретения новой техники с учётом имеющихся в парке номенклатуры машин. Для этого достаточно, чтобы показатели всех рассматриваемых машин хранились в базе данных.
Предложен метод оценки организационно-технологической надёжности работы строительных машин, который позволяет прогнозировать показатели их работы последних. Этот метод может быть использован для оценки надежности работы любых парков, комплексов, комплектов и отдельных строительных машин.
141