
Metod_2542
.pdf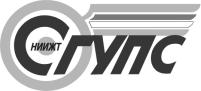
621
Б125
СИБИРСКИЙ ГОСУДАРСТВЕННЫЙ УНИВЕРСИТЕТ ПУТЕЙ СООБЩЕНИЯ
А.В. Бабич, А.Л. Манаков, С.В. Щелоков
РЕМОНТ МАШИН
Учебное пособие
Новосибирск
2012
3
УДК 629.4.004 ББК 30.83 Б125
Бабич, А.В.
Б125 Ремонт машин: Учеб. пособие / А.В. Бабич, А.Л. Манаков,
С.В. Щелоков. – Новосибирск: Изд-во СГУПСа, 2012. – 238 с. ISBN 978-5-93461-546-9
Рассматриваются вопросы проектирования технологических процессов ремонта агрегатов и деталей путевых, строительных, дорожных машин и автомобилей, содержатся рекомендации по реализации отдельных этапов процесса ремонта.
Учебное пособие предназначено для студентов, изучающих дисциплину «Ремонт машин», при подготовке к лекциям, практическим занятиям и выполнении курсового и дипломного проектирования.
УДК 629.4.004 ББК 30.83
Утверждено редакционно-издательским советом университета в качестве учебного пособия.
О т в е т с т в е н н ы й р е д а к т о р канд. техн. наук, проф. Л.Б. Тихомирова
Р е ц е н з е н т ы:
кафедра «Механизация путевых, погрузочно-разгрузочных и строительных работ» ФГБОУ ВПО «Сибирский государственный университет путей сообщения» (завкафедрой д-р техн. наук, проф. Б.Н. Смоля-
ницкий)
завкафедрой «Технология машиностроения» ФГБОУ ВПО «Новосибирский государственный аграрный университет» канд. техн. наук,
доц. В.В. Коноводов
ISBN 978-5-93461-546-9
©Бабич А.В., Манаков А.Л.,
Щелоков С.В., 2012
©Сибирский государственный
университет путей сообщения, 2012
4
ГЛАВА 1. НЕИСПРАВНОСТИ И ОТКАЗЫ МАШИН, СБОРОЧНЫХ ЕДИНИЦ И ДЕТАЛЕЙ
1.1. Некоторые сведения о надежности машин
Эффективность использования машины во многом зависит от ее надежности, от надежности сборочных единиц и деталей.
Надежность — это свойство машины или ее сборочных единиц, деталей выполнять заданные функции, сохраняя свои эксплуатационные показатели в заданных пределах в течение установленного промежутка времени или требуемой наработки.
Таким образом, надежной можно считать машину, которая способна не только выполнять технологические функции (копать грунт, поднимать или транспортировать груз, укладывать рельсошпальную решетку в путь и т.д.), но и сохранять при этом техни- ко-экономические характеристики в пределах, установленных нор- мативно-технической документацией (тяговое усилие на крюке — для тягача; мощность, крутящий момент на валу, расход топлива — для двигателя внутреннего сгорания; грузоподъемность, скорость подъема и перемещения груза — для мостового крана и др.).
Надежность — это комплексное свойство, характеризующееся безотказностью, ремонтопригодностью, сохраняемостью и долговечностью.
Безотказность — свойство машины сохранять работоспособность в течение некоторой наработки без вынужденных перерывов на устранение отказов.
Показателем безотказности могут служить, например, наработка на отказ или вероятность безотказной работы в заданный момент времени.
Работоспособность есть состояние машины, при котором она способна выполнять заданные функции с параметрами, установленными технической документацией. Например, если трактор развивает тяговое усилие на крюке на всех передачах в соответствии с тяговой характеристикой, то такое состояние тягача следует считать работоспособным.
Отказ — событие, вызвавшее нарушение работоспособности. Долговечность — свойство машины сохранять работоспособ-
ность до предельного состояния с необходимыми перерывами для
5
технического обслуживания и ремонта. Долговечность может быть оценена ресурсом или сроком службы.
Предельное состояние машины есть такое состояние, при ко-
тором ее дальнейшая эксплуатация становится неэффективной или невозможной с точки зрения безопасности выполнения работ.
Ресурс — наработка машины до предельного состояния, оговоренного в технической документации. Ресурс может измеряться
вчасах, в метрах кубических вынутого грунта, в килограммах израсходованного топлива и т.д.
Срок службы — календарная продолжительность работы машины до предельного состояния, оговоренного в технической документации, или списания.
Ремонтопригодность — свойство машины, заключающееся
вее приспособленности к предупреждению и устранению отказов и неисправностей вследствие проведения технических воздействий (технических обслуживаний и ремонтов).
Показателями ремонтопригодности могут быть:
среднее время на устранение отказа;
вероятность выполнения технического обслуживания или ремонта в заданное время и др.
Из сказанного следует, что переход машины из исправного и работоспособного состояния в неисправное или предельное может произойти вследствие отказа или израсходования ресурса.
Так как всякая машина представляет собой совокупность сборочных единиц и сопряжений, то неисправность машины будет определяться неисправностью ее сборочных единиц и сопряжений.
Неисправность сопряжений проявляется в нарушении расчетной посадки, т.е. в увеличении зазора в подвижных или уменьшении натяга в неподвижных сопряжениях. Так, уменьшение мощности дизельного двигателя может стать следствием увеличения зазора в сопряжении плунжер — гильза топливного насоса высокого давления.
Нарушение посадки сопряжения обусловлено изменениями формы и размеров рабочих поверхностей деталей. Эти изменения могут произойти по многим причинам, среди которых особо нужно выделить изнашивание деталей.
6
Связь надежности машин с износом деталей можно установить сопоставлением кривых изменения зазоров в сопряжениях (рис. 1.1) и графика изменения интенсивности потока отказов в зависимости от времени работы машины (рис. 1.2).
Рис. 1.1. Изменение зазора в сопряжении |
Рис. 1.2. Зависимость плотности |
с подвижной посадкой |
потока отказов от времени работы |
|
машины |
Общим для этих графиков является наличие трех явно выраженных участков:
участок I характеризует увеличение зазоров в сопряжениях до начального значения Sнач и резкое уменьшение потока отказов
в период приработки;
участок II прямолинейный и соответствует времени нор-
мальной работы сопряжения 1 с установившимися износом и потоком отказов (время работы сопряжения и машины 1 в этом режиме можно считать сроком их службы);
участок III соответствует предельному состоянию деталей, сопряжений, сборочных единиц и машин в целом. Величины за-
зоров превышают максимально допустимые значения Smax, появляются дополнительные динамические нагрузки на детали, нарушается режим трения, в результате быстро растет износ деталей, поток отказов резко нарастает.
Таким образом, можно считать, что надежность машин в целом и безотказность, в частности, зависят от величины износа деталей и сопряжений.
1.2. Износ и виды износа деталей
Изнашиванием называется процесс изменения размеров, формы и взаимного расположения рабочих поверхностей деталей в процессе работы сопряжений.
7
Износ деталей — результат изнашивания, т.е. работы силы трения.
Существует несколько точек зрения на процесс изнашивания, и предложены варианты классификаций износов деталей [2, 8, 14, 15]. Большинство же исследователей принимают классификацию износов, разработанную Б.И. Костецким, который выделяет следующие виды износа:
схватыванием;
окислительный;
тепловой;
абразивный;
осповидный.
1.2.1. Износ схватыванием
Износ схватыванием возникает в |
|
сопряжении деталей, имеющих следы |
|
предшествующей механической об- |
|
работки и перемещающихся относи- |
|
тельно друг друга со скоростью около |
|
1,0 м/с, при отсутствии смазки и |
|
больших давлениях в местах контакта |
|
(рис. 1.3). |
Рис. 1.3. Схема процесса |
На рис. 1.3 деталь А перемещает- |
изнашивания схватыванием |
ся относительно детали Б со скоро-
стью v, м/с, при давлении Р, Па. Контактирование деталей происходит в точках 1, 2, 3. Фактическое давление в точках контакта деталей превосходит расчетное на несколько порядков, в результате происходит холодное пластическое деформирование материалов деталей А и Б. Процесс деформирования сопровождается разрушением окисных, жировых и других пленок, наблюдается контактирование абсолютно чистых (ювенильных) металлов, т.е. создаются условия для образования атомных (металлических) связей материалов. Образованию металлических связей способствует тепло, выделяющееся при пластическом деформировании.
Образование соединений деталей А и Б в точках 1, 2, 3 назы-
вают схватыванием или холодной сваркой.
В зоне фрикционного контакта происходят изменения физикомеханических свойств трущихся материалов. Это явление обнаружено
8
академиком П.А. Ребиндером и является предметом изучения специального направления науки — физико-химической механики [8].
Явление, открытое Ребиндером, называется адсорбционным эффектом понижения прочности трущегося материала, когда в результате адсорбции поверхностно-активное вещество покрывает твердое тело слоем толщиной хотя бы в одну молекулу.
Это открытие позволило пересмотреть роль смазки в процессе трения. До этого считалось, что действие смазки при граничном трении заключается лишь в том, что она разъединяет трущиеся материалы. Исследования Ребиндера и его учеников показали, что активные смазки облегчают пластическое течение тонких поверхностных слоев материалов при трении с высоким давлением. Это облегчает процесс приработки деталей, предотвращает задиры на рабочих поверхностях.
При перемещении детали происходит разрушение мостиков схватывания по менее прочному материалу. Например, при схватывании деталей сопряжения вал–подшипник скольжения разрушение происходит по антифрикционному сплаву подшипника, так как его прочность и твердость намного меньше тех же характеристик стального закаленного вала. В результате такого процесса изнашивания на рабочей поверхности подшипника появляются грубые риски, царапины, а на цапфе или шейке вала — следы прочно закрепленного антифрикционного сплава подшипника. Размеры рабочих поверхностей деталей изменяются, шероховатость их перестает удовлетворять требованиям рабочих чертежей — сопряжение становится неработоспособным.
Меры, снижающие вероятность появления процесса схватывания, можно разделить на:
конструкторские (наличие в машине или механизме системы, обеспечивающей надежную смазку трущихся поверхностей деталей, и др.);
технологические (формирование оптимальной шероховатости рабочих поверхностей деталей на финишных операциях механической обработки, обеспечение заданной точности размеров деталей и зазоров в сопряжениях и т.д.);
эксплуатационные (соблюдение режимов обкатки в начальный период эксплуатации после изготовления или ремонта изде-
9
лия, соблюдение расчетного режима эксплуатации, проведение технических воздействий для поддержания исправности и работоспособности изделий).
1.2.2. Окислительный процесс
Окислительный процесс характеризуется микропластическими деформациями и диффузией кислорода, одновременно протекающими в тонких слоях трущихся поверхностей деталей. Следует отметить, что химическая гипотеза износа была выдвинута еще в 1930 г. немецким ученым М. Финком, который обнаружил повышенную окисляемость медных сплавов при сухом трении и последующее отшелушивание пленок окислов.
Окислительное изнашивание протекает в два этапа.
На первом этапе поверхностный слой металла детали постепенно насыщается кислородом, образуется твердый раствор кислорода в металле, пластичность последнего резко повышается, идет перетекание микрослоя по поверхности детали, разрыв его и унос продуктов разрушения подвижного пластичного микрослоя из зоны трения — формируется износ.
Второй этап характеризуется образованием химических соединений кислорода с металлом, для железа это FeO, Fe2O3, Fe2O4. Известно, что окислы железа характеризуются высокой твердостью и хрупкостью, поэтому износ на втором этапе формируется за счет хрупкого разрушения окисных слоев (пленок), толщина которых заметно меньше толщины высокопластического слоя, образующегося на первом этапе. Следовательно, можно ожидать, что износ на втором этапе будет меньше, чем на первом.
Известно [8, 15], что при трении деталей, изготовленных из материалов с невысокой твердостью, преобладающим является изнашивание с образованием твердых растворов кислорода и пластичных микрослоев; для деталей с высокой твердостью рабочих поверхностей ведущим является процесс образования и разрушения пленок окислов, т.е. наибольшему окислительному износу подвержены мягкие стали.
Окислительный износ часто встречается на деталях криво- шипно-шатунного механизма двигателя внутреннего сгорания: на коренных и шатунных шейках коленчатого вала, на зеркале цилиндра, на рабочей поверхности поршневого пальца и др.
10
Для уменьшения величины окислительного износа можно рекомендовать способы восстановления, в которых имеются операции повышения твердости рабочих поверхностей деталей (закалка, азотирование, цианирование и др.) или операции нанесения покрытий, препятствующих проникновению кислорода в материал подложки детали.
1.2.3. Тепловой износ
Тепловой износ наблюдается чаще всего у деталей, работающих при больших давлениях и скоростях скольжения трущихся поверхностей, а также в среде с высокой температурой теплоносителя.
Возникающее в этих условиях работы тепло нагревает рабочие поверхности деталей и вызывает термические процессы в микрообъемах материала: отпуск, нормализацию и даже оплавление. Эти структурные превращения, как правило, снижают твердость, повышают пластичность, т.е. повышают склонность материалов к схватыванию.
Различие условий работы сопряжений, физико-механических свойств трущихся материалов, многообразие структурных превращений при нагреве материалов делают тепловой износ весьма различным по величине и глубине проникновения от поверхности. Однако присутствие указанных и других различий не скрывает характерных признаков процесса теплового изнашивания: изменение микроструктуры сплава в поверхностных слоях, снижение твердости и прочности материала, наличие следов схватывания в этих микрообъемах.
Интенсивность теплового изнашивания во много раз больше интенсивности окислительного изнашивания. О подавляющем преобладании теплового изнашивания в материалах над окислительным свидетельствует отсутствие окислов в продуктах теплового износа. Б.И. Костецкий объясняет это тем, что вышеназванные термические процессы способствуют полному или частичному
восстановлению искаженной кристаллической решетки Fe, это, в свою очередь, уменьшает растворимость кислорода.
Из описания сущности теплового изнашивания следует, что для уменьшения износа кулачков распределительного вала, гнезда сёдел клапанов, толкателей и других подобных деталей следует
11
рекомендовать их изготовление из жаропрочных легированных сталей.
Для других же деталей, например гильз, цилиндров, необходимы мероприятия, гарантирующие расчетный тепловой режим работы детали: предупреждение образования накипи и нагара на стенках гильзы, обеспечение нормированного расхода и температуры охлаждающей жидкости в рубашке блока цилиндров и т.д.
1.2.4. Абразивный износ
Разрушение поверхностных слоев трущихся деталей при абразивном изнашивании связано с микропластическими деформациями и срезанием микрообъемов металла твердыми абразивными частицами.
Абразивный материал может быть рабочей средой, в которой работает деталь, например грунт для рабочих органов землеройных машин или ходовых аппаратов гусеничных машин. Абразивный материал на рабочие поверхности деталей может попадать вместе с недостаточно очищенным топливом, воздухом или маслом, через неисправные уплотнительные узлы сборочных единиц. Наконец, в качестве абразивного материала могут выступать продукты изнашивания деталей — обломки окислов, упрочненные частицы металла и т.д.
Исследования М.М. Хрущова и др. [31] показывают, что закономерности абразивного изнашивания и абразивного резания общие, но полной аналогии между этими процессами нет, поскольку абразивная обработка (шлифование) ведется с большой скоростью и вызывает значительный нагрев обрабатываемого материала, уменьшение сопротивления пластическому деформированию, чего нет при абразивном износе. Следовательно, интенсивность съема металла при абразивном резании во много раз выше интенсивности абразивного изнашивания.
Из технологических способов повышения стойкости деталей машин против абразивного изнашивания следует отметить такой способ, как повышение твердости материалов, из которых они изготовляются.
12