
Metod_2542
.pdf1.2.5. Осповидный износ
Осповидный износ наиболее отчетливо наблюдается при трении качения на рабочих поверхностях подшипников и зубчатых колес.
Трение качения реальных тел (деталей) является процессом более сложным и менее изученным, чем трение скольжения. Однако достоверно установлено [14], что трение качения сопровождается упругими и пластическими деформациями материалов в зоне контакта, скольжением трущихся поверхностей.
Пластическое деформирование материалов вызывает упрочнение его на рабочих поверхностях, причем упрочненные объемы располагаются на некоторой глубине от поверхности трения, что сопровождается локальными объемными изменениями, т.е. является причиной зарождения усталостных трещин.
Сочетание повторно-переменного нагружения, упругих и пластических деформаций вызывает усталостное разрушение, т.е. образование усталостных трещин, которые, развиваясь, выходят на поверхность трения и приводят к выкрашиванию материала, образованию осповидных углублений на рабочей поверхности детали.
Дальнейшему разрушению рабочих поверхностей способствует сопутствующий окислительный износ, т.е. образование и разрушение окисных пленок на открывающихся чистых поверхностях материала.
Из сказанного следует, что повышение стойкости материала против осповидного износа может быть достигнуто за счет повышения предела его усталости: оптимизацией химического состава, термической обработкой, включением упрочняющих операций (накатка роликом, дробеструйная обработка и т.п.) на финише технологического процесса восстановления детали.
1.2.6. Современные представления об износе материалов
Развитие физико-химической механики материалов привело к формированию новых направлений в науке о трении и износе: трибохимии, трибофизики и трибомеханики.
Трибохимия — это область химии, которая занимается химическими и физико-химическими изменениями твердого тела под влиянием механической энергии трения.
13
Трибофизика — это ветвь физики, рассматривающая механические взаимодействия между твердыми телами при трении.
Трибомеханика — это наука о трении и износе. Трибохимическими исследованиями установлено, что одной
из особенностей химических реакций, протекающих на поверхностях трения, является их высокая скорость по сравнению со скоростью тех же реакций на неподвижных контактирующих поверхностях.
Ускорение химических реакций происходит в результате физических и механических явлений, возникающих в месте контакта или деформаций: давление и температура, скорость перемещения, каталитическое воздействие окисных пленок на смазку, разупрочненное состояние сплава или искаженное состояние кристаллической решетки и т.д.
Перечисленные и другие явления, в совокупности с теми или иными режимами трения, сочетаниями материалов, свойств смазки, могут приводить к различной износостойкости материалов. Так, например, самопроизвольное окисление смазки в процессе длительного трения медного сплава со сталью при небольшом объеме смазки приводит граничное трение к избирательному переносу. Такой процесс наблюдается в редукторах с бронзовыми колесами и стальными червяками при редкой замене смазки.
В количественном плане скорость химических реакций может возрастать на четыре порядка при механическом воздействии трения.
Триботехнические исследования позволяют объяснить и установить закономерности избирательного переноса, повысить износостойкость деталей сопряжений, повысить долговечность сборочных единиц изделия и изделия в целом.
1.3. Разрушение рабочих поверхностей деталей
Кроме износа, проявляющегося при трении, рабочие поверхности подвержены и другим видам разрушения: усталостному, коррозионному, эрозионному и др. Некоторые исследователи считают [16], что образование накипи или нагара также является процессом разрушения рабочих поверхностей деталей.
14
1.3.1. Усталостное разрушение
Усталостное разрушение проявляется в виде отдельных трещин или скопления их на рабочих поверхностях, а также в виде разрушения деталей под действием длительного циклического или знакопеременного нагружения.
Усталостному разрушению чаще подвержены валы, оси, шатуны, шатунные болты, зубчатые колеса и др.
При восстановлении названных и некоторых других деталей можно существенно повысить сопротивление усталостному разрушению путем введения в технологический процесс упрочняющих операций (дробеструйной обработки, накатки роликом, чеканки молотком), повышения требований к шероховатости галтелей и других переходных поверхностей.
Обязательным должен быть контроль ответственных деталей с целью обнаружения начальных усталостных трещин перед восстановлением.
1.3.2. Коррозия
Коррозия — это поверхностное разрушение металла под действием окислительных процессов.
Окислительные процессы протекают самопроизвольно и являются следствием химического или электрохимического взаимодействия металла с окружающей средой.
Химическая коррозия есть результат взаимодействия металла с газами, растворами кислот, щелочей, солей, которые всегда присутствуют в окружающей среде.
Продуктом химической коррозии являются рыхлый и хрупкий слои окислов на поверхности деталей.
Электрохимическая коррозия является результатом процесса электролиза, при котором идет растворение (разрушение) одного из электродов — анода. Процесс электролиза возможен при наличии электролита, двух электродов и разности потенциалов между ними.
Электролит, т.е. токопроводящий раствор кислот, солей и щелочей, практически всегда присутствует на поверхностях деталей. Гальваническая пара образуется при контакте двух металлов, занимающих различное положение в электрохимическом ряду,
15
причем анодом будет являться более активный металл, т.е. занимающий левое положение в электрохимическом ряду.
В качестве электродов гальванической пары могут быть различные структурные составляющие: чистые металлы, твердые растворы, химические соединения или механические смеси, неметаллические включения.
Известно, что равновесные структурные составляющие и фазы характеризуются более высокой электрохимической активностью, чем те элементы структуры, которые имеют искаженную (напряженную) кристаллическую решетку, поэтому правильные и химически чистые кристаллы чаще являются анодом, т.е. разрушающимся электродом гальванической пары. Таким образом, деформация отдельных участков детали или конструкции, образование скоплений загрязнений на поверхности детали, эксплуатация изделий в электростатическом или электромагнитном поле резко повышают разность потенциалов между отдельными участками поверхности детали, т.е. повышают склонность металла к электрохимической коррозии.
Известные способы защиты металлов от коррозии (антикоррозионное легирование, покрытие коррозионно-стойкими металлами и лакокрасочными материалами и др.) лишь частично решают проблему, которая до сих пор не получила комплексного решения.
1.3.3. Эрозионное разрушение
Эрозионное разрушение характеризуется зарождением и быстрым развитием каверн (кратеров) на рабочих поверхностях деталей.
Каверны образуются при неблагоприятном обтекании деталей быстротекущей жидкостью, воздухом или газом. Это явление получило название кавитации, а процесс разрушения рабочих поверхностей деталей стали называть кавитационно-эрозионным [5]. Разрушение происходит в результате усталости материала в ограниченных макрообъемах, где наблюдаются частые и сильные гидравлические удары.
Кавитационно-эрозионному разрушению подвергаются детали гидродвигателей, гидронасосов, жесткие трубопроводы гидросистем строительных машин, летательных аппаратов, металлоре-
16
жущих станков и детали систем охлаждения двигателей внутреннего сгорания (ДВС).
Электроэрозионное разрушение наблюдается на деталях со-
пряжений или соединений, где возможно образование искровых разрядов (прерыватели магнето, распределители, коллекторы генераторов и стартеров, контактные соединения сильно- и слаботочных цепей и т.п.). Детали таких сопряжений, как правило, несут большие заряды электростатического электричества. При определенных зазорах в сопряжении происходит разряд в виде кратковременного мощного импульса (10–4 … 10–7 с) — искровой разряд. Он характеризуется микроскопической площадью, поэтому температура анода на этих микроплощадках достигает высоких значений, материал анода плавится и выбрасывается в межэлектродное пространство, идет формирование каверн.
Скорость разрушения при этом зависит от многих факторов, главные из них — свойства материалов и величина тока в цепи разряда. Эрозия металла составляет: для закаленной стали — 17,8 г/ч; меди — 18; алюминия — 38; для латуни — 18 г/ч, т.е. практически не зависит от его твердости и прочности.
Представленный теоретический материал дает некоторое представление о разрушениях поверхностей деталей. Разрушения же самих деталей (образование трещин различной природы, разрушения и деформации деталей) достаточно полно описаны в дисциплинах общепрофессионального цикла, поэтому в дальнейшем эти разрушения будут рассматриваться в технологических процессах как устранимые или неустранимые дефекты.
Вопросы для самоконтроля
1.Сформулируйте определение понятия «технологический процесс ремонта машин».
2.Перечислите составляющие структуры технологического процесса капитального ремонта машин.
3.Определите основные этапы технологического процесса капитального ремонта машин.
4.Охарактеризуйте виды ремонта строительных, транспортных и транспортно-технологических машин и оборудования.
17
5. Определите влияние уровня разработки технологического процесса ремонта машин на качество ремонта, производительность труда и обеспечение безопасности выполнения операций.
ГЛАВА 2. ТЕХНОЛОГИЧЕСКИЙ ПРОЦЕСС РЕМОНТА МАШИН
2.1. Общие сведения
Технологический процесс является основой для организации современного ремонтного производства и представляет собой совокупность операций, выполненных в определенной последовательности с целью восстановления исправности и ресурса или поддержания работоспособности машин.
Технологический процесс должен обеспечить выполнение технических условий на ремонт машин с минимальными затратами труда и издержками производства.
В технологическом процессе дается подробное описание операций с необходимыми техническими и экономическими расчетами.
Разработанный или принятый технологический процесс позволяет установить виды и объемы работ, трудоемкость ремонта машины, номенклатуру и количество ремонтного оборудования и технологической оснастки, типы и количество транспортного оборудования и др.
На рис. 2.1 представлена схема технологического процесса капитального ремонта автомобиля на авторемонтном заводе, согласно которой весь технологический процесс можно разделить на несколько блоков операций:
–разборочно-моечные работы;
–контрольно-сортировочные работы (дефектация деталей);
–комплектование и сборка сборочных единиц и машин;
–приработка и испытание сборочных единиц и машин;
–окрасочные работы.
18
Всостав машин входит ряд неразборных элементов (сварных, изготовленных клепкой и пайкой, склеиванием и др). Примерами таких элементов могут служить баки для топлива и рабочей жидкости, радиаторы, рамы и др. Для подобных сборочных единиц в технологическом процессе не предусматривается разборка на детали. В технологический процесс закладывается ремонт их сваркой, правкой, заменой дефектных частей и др.
Вмашине можно выделить ряд элементов и сборочных единиц, не требующих испытания и приработки, для таких элементов и сборочных единиц в технологическом процессе контроль- но-испытательные операции не предусматриваются. Это кузова автомобилей, рамы, кабины, облицовки и др.
Комплектующие таких систем, как электрооборудование, гидрооборудование, система питания и др., не проходят по типовому технологическому маршруту и ремонтируются комплектно на специализированных участках, где выполняются разборочные, моечные, сборочные, испытательные и др. операции.
Отдельный блок операций технологического процесса ремонта составляет восстановление изношенных деталей. Оно осуществляется для деталей, имеющих достаточно большой остаточный ресурс, восстановление которых технологически и экономически целесообразно.
2.2. Разборочно-моечные работы при ремонте машин
На данном этапе технологического процесса осуществляется очистка от загрязнений и мойка машин, сборочных единиц и деталей.
Разборочные работы выполняются в несколько стадий:
–разборка машины;
–подразборка сборочных единиц;
–разборка сборочных единиц высшего уровня на простейшие;
–разборка простейших сборочных единиц на детали и нор-
мали.
Между указанными разборочными операциями ведется мойка отдельных сборочных единиц. Таким образом реализуется многостадийная мойка в технологическом процессе ремонта (рис. 2.2).
19
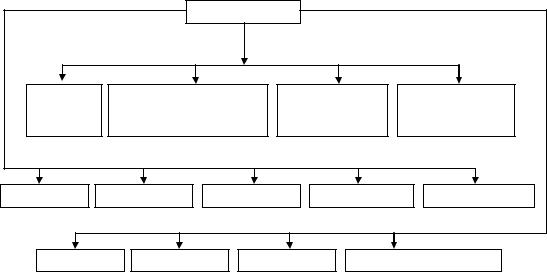
Представленная на рис. 2.2 организация моечных работ дает возможность повысить качество ремонта, его экономическую эффективность, сократить выход деталей в утиль. Одной из стадий моечно-очистительных работ является наружная мойка машин.
Наружная мойка машины производится в сборе или после предварительной подразборки. Во втором случае перед моечной операцией с машины демонтируется рабочее оборудование, а также кожухи и др. Такое построение операций позволяет повысить качество моечно-очистительных работ.
Загрязнения машин, агрегатов и их деталей по их составу делят на следующие виды: частицы и комья пыли и земли, масла и жиры, смолы, накипи, продукты коррозии, старые лакокрасочные и металлические покрытия.
Классификация способов очистки и мойки, в зависимости от степени механизации, вида применяемой энергии и моющих средств, приведена на рис. 2.3.
|
|
Способы мойки |
|
|
|
|
|
|
По степени |
механизации |
|
|
|
Ручной |
С использованием ручного |
|
Механизированный |
Автоматизированный |
||
|
механизированного инструмента |
|
|
|
||
|
|
По виду применяемой энергии |
|
|
||
Механический |
Химический |
Термический |
|
Ультразвуковой |
Комбинированный |
|
|
|
По виду моющих средств |
|
|
||
Вода, пар |
Щелочь |
Гидроабразив |
Косточковая крошка |
Рис. 2.3. Классификация способов мойки машин, их агрегатов и деталей
Наружная мойка машин выполняется погружным, струйным и струйно-щеточным способами. На ремонтных предприятиях преимущественно применяются стационарные многоструйные и струйно-щеточные установки. При этом для мойки машин сложной геометрической формы (краны, экскаваторы и т.п.) более предпочтительны струйные установки, а для мойки машин относительно простой формы (автобусы, легковые автомобили и т.п.) —
20

струйно-щеточные установки. Конструкции передвижных и стационарных моечных машин показаны на рис. 2.4–2.7.
Моющая способность установок зависит от расхода, давления и температуры воды, формы струи, крупности капель и состава применяемых моющих средств. Развитие конструкции моечных установок характеризуется следующими тенденциями: рост давления воды до величины, обеспечивающей сохранность машины и лакокрасочных покрытий (10 и
более МПа); подогрев воды; применение пара и воздуха для распыления воды; применение турболазеров для укрупнения и увеличения силы удара водяных капель; закручивание струи воды; совершенствование конструкции щеток, повышение долговечности и очищающей способности их ворса; автоматическое управление режимом мойки (подача, давление, температура, обороты, траектория и сила прижатия щетки и т.д.); уменьшение габаритов и массы; применение оборотного водоснабжения; обеспечение безопасности эксплуатации; защита окружающей среды.
Рис. 2.5. Схема передвижной моечной установки с подогревом воды: 1 — поплавковая камера; 2 — подвод воды; 3 — топливный бак; 4 — водяной насос; 5 — топливный насос; 6 — трансформатор;
7 — форсунка; 8 — свеча зажигания; 9 — теплообменник; 10 — змеевик теплообменника; 11 — пистолет-распылитель;
12 — бак для моющих средств; 13 — вентилятор; 14 — электродвигатель
21
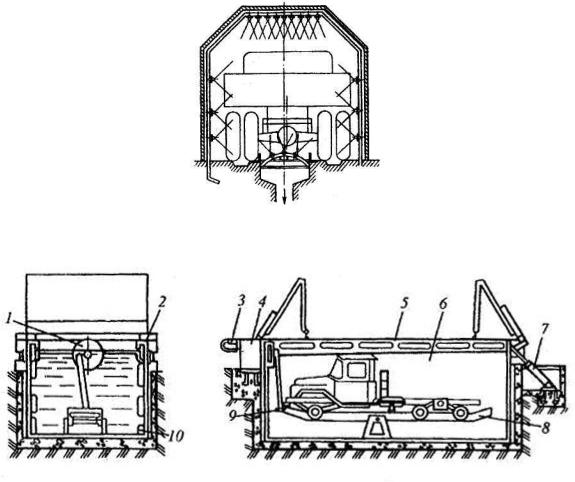
|
Рис. 2.6. Стационарная струйная моечная установка |
а) |
б) |
Рис. 2.7. Стационарная моечная установка погружного типа: поперечный (а) и продольный (б) разрезы;
1 — кривошип; 2 — маслообменник; 3 — электродвигатель; 4 — редуктор; 5 — крышка; 6 — ванна; 7 — гидроцилиндр; 8 — платформа; 9 — шатун; 10 — нагреватель
Для повышения качества очистки и облегчения труда мойщиков используются насадки высокого давления, турбонасадки и турболазеры. Насадки высокого давления определяют форму и площадь следа струи на очищаемой поверхности. Они имеют постоянный (0, 15, 25, 30, 40 и 60°) или переменный (от 0 до 90°) угол распыла, регулируемый в процессе очистки от минимального до максимального значений. При угле распыла 0° струя сосредоточенная, с большим ударным импульсом, но площадь очистки небольшая. Увеличение угла распыла приводит к расширению струи — струя становится плоской, веерной и широкозахватной, но ударный импульс резко снижается.
Турбонасадки формируют сосредоточенную струю жидкости, которая, вращаясь со скоростью 4000 об./мин, описывает конус-
22