
Metod_2542
.pdfОсадки, получаемые из холодных сернокислых электролитов, отличаются высокой твердостью и хрупкостью. Наращивание слоя железа в холодных электролитах идет с малой скоростью, примерно 0,001 мм/ч. Эти осадки не пригодны для восстановления изношенных деталей.
Наибольшее распространение в ремонтном производстве получил хлористый электролит — водный раствор хлористого железа, содержащий небольшое количество соляной кислоты и некоторые добавки.
Состав хлористых электролитов и режим работы с их использованием приведены в табл. 3.25.
|
|
|
|
Таблица 3.25 |
|
|
|
|
|
Компоненты |
Концентрация в растворах, г/л |
|||
№ 1 |
|
№ 2 |
№ 3 |
|
|
|
|||
Хлористое железо |
180–200 |
|
350–500 |
700–800 |
Хлористый натрий |
80–100 |
|
80–100 |
— |
Хлористый марганец |
— |
|
10 |
— |
Соляная кислота |
3,0–3,5 |
|
0,5–2,0 |
0,3–0,5 |
|
Режим работы |
|
|
|
Температура, °С |
70–80 |
|
90–95 |
75–80 |
Плотность тока, А/дм2 |
8–10 |
|
5–20 |
10–20 |
Выход по току, % |
75–100 |
|
90–95 |
75–80 |
Из электролитов с низкой концентрацией FeCl2 4H2O (180– 220 г/л) получаются покрытия с высокой твердостью (600–6500 Hv) и малой толщиной (h = 0,3…0,4 мм). Высококонцентрированные электролиты (700–800 г/л) дают осадки большой толщины (h = = 0,8…1,0 мм) и относительно малой твердости (1500–2000 Hv).
При осталивании применяются растворимые аноды (из малоуглеродистой стали марок сталь 08, сталь 10 по ГОСТ 1050–88). При таком процессе убыль ионов железа из электролита компенсируется за счет растворения анодов. При работе на малоконцентрированных (бедных) электролитах CFeCl2 4H2 0 180...220 г/л интенсивность растворения анодов велика, в связи с чем растет концентрация основной соли CFeCl2 4H2 0 300...400 г/л:
Fe 2Cl 4H2O FeCl2 4H2O.
173
На этом уровне концентрация основной соли в электролите стабилизируется. При работе на электролитах высокой концентрации CFeCl2 4H2 0 700...800 г/л имеет место обратное явление.
Поэтому наибольшее распространение получил электролит следующего состава, г/л:
CFeCl2 4H2 0 400 20; CHCl2 2 0,2; CMnCl2 4H2 0 10 2.
Электролит такого состава сохраняет концентрацию основных компонентов длительное время, позволяет получить покрытия требуемой толщины и твердости, обладает высокой рассеивающей способностью, т.е. дает равномерное распределение осадка, характеризуется высоким выходом металла по току.
Наличие в электролите хлористого марганца способствует повышению прочности сцепления железа покрытия с подложкой.
В процессе эксплуатации состав электролита может изменяться, что неизбежно отражается на качестве покрытия, поэтому необходимо постоянно его контролировать и корректировать.
Концентрацию основного компо-
нента FeCl2 4H2O определяют с помо-
щью графика (рис. 3.29), по плотности электролита. Плотность электролита измеряется ареометром.
Содержание в электролите соляной кислоты определяется по показаниям рН-метра, датчик этого прибора постоянно находится в ванне. При этом следует учитывать влияние на рН концентрации основной соли. При одной и той же концентрации кислоты (CHCl const ) величина рН будет уменьшаться с ростом концентра-
ции основной соли. Эта зависимость представлена на рис. 3.30. Растворение соли вызывает усилие диссоциации молекул растворителя, т.е. воды, а следовательно, увеличение концентрации водородных ионов (уменьшение рН).
Изменение состава электролита и необходимость его корректировки возникают из-за испарения электролита и расхода кислоты на растворение анодов. Интенсивность испарения зависит
174
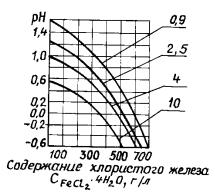
главным образом от рабочей тем- |
|
|
пературы электролита. Расход со- |
|
|
ляной кислоты в процессе элек- |
|
|
тролиза зависит от концентрации |
|
|
основной соли, плотности тока и |
|
|
температуры электролита. При ра- |
|
|
боте на бедных электролитах при |
|
|
понижении плотности тока и по- |
|
|
вышении температуры расход со- |
Рис. 3.30. График зависимости |
|
ляной кислоты увеличивается, т.е. |
между рН и содержанием HCl в |
|
возникают благоприятные условия |
электролитах при различной |
|
для растворения анода. |
концентрации FeCl2 4H2O |
|
Для электролита средней кон- |
(цифры на кривых — |
|
содержание HCl в растворе, г/л) |
||
центрации |
CFeCl2 4H2O 400 ã/ë |
|
при Тэл = 75 °С и Dк = 40…50 А/дм2 удельный расход соляной кислоты можно определить по формуле, г/(л ч):
gHCl 0,08...0,10 100a ,
где а — содержание хлористого водорода в технической соляной кислоте, г/л.
Для указанных выше режимов процесса электролиза за 1,0–1,5 ч уменьшение концентрации соляной кислоты не превысит 0,10– 0,12 г/л и не вызовет разрегулирования процесса.
При |
уменьшении |
содержания |
|
||
свободной |
кислоты |
в |
электролите |
|
|
наблюдается |
гидролиз |
электролита |
|
||
(раствор мутнеет) и появление в осад- |
|
||||
ке железа гидроокиси железа — по- |
|
||||
крытие приобретает хрупкость. |
|
||||
С увеличением концентрации со- |
|
||||
ляной кислоты выход металла по току |
|
||||
резко снижается (рис. 3.31). |
Рис. 3.31. Выход металла |
||||
Вышесказанное |
позволяет сфор- |
по току при осталивании |
|||
мулировать |
вывод о необходимости |
в зависимости от |
|||
корректировки электролита по содер- |
концентрации HCl, г/л |
||||
|
175
жанию соляной кислоты до рабочей отметки в течение смены, между завесами деталей.
При хранении неработающего электролита с открытым зеркалом, а также при эксплуатации электролита на пониженной кис-
лотности CHCl 1,2...1,0 ã/ë в нем накапливаются ионы Fe+++ и образуется гидроокись железа. Раствор мутнеет, приобретает бу-
рый цвет. Для восстановления такого электролита нужно повы-
сить СHCl до 3–5 г/л, установить плотность тока 1–2 А/дм2 и при повышенной температуре поработать до приобретения электроли-
том зеленого оттенка.
Для избежания порчи в неработающий электролит нужно поместить небольшое количество стружки малоуглеродистой стали в мешочке из стеклоткани, а зеркало закрыть поплавками из пенопласта.
Качество железных осадков. При оценке качества электролитических осадков обобщенным показателем является твердость.
Влияние плотности тока и температуры электролита на микро-
твердость Н железных осадков представлено на рис. 3.32. При исследовании этой зависимости концентрация хлористого железа оставалась неизменной: CFeCl2 4H2O 400 ã/ë .
Из графика видно, что при осталивании твердость осадка увеличивается с повышением катодной плотности тока при понижении температуры электролита. Эта закономерность наблюдается при хромировании, цинковании и при других процессах гальваностегии.
Металлографический анализ позволяет объяснить изменение напряженного состояния железа при различных условиях проведения электролиза [24].
Железо покрытия, полученное при пониженной плотности тока в горячем электролите, имеет крупнозернистую структуру. Зерна ориентированы нормально к поверхности подложки, микро- и макротрещины отсутствуют.
При ужесточении режимов электролиза (повышении плотности тока и снижении температуры электроли-
176
та) размеры зерен железа уменьшаются. При твердости Н 3000 МПа трещины в структуре осадка не наблюдаются, это свидетельствует о том, что величина внутренних напряжений не превышает предела прочности железа на разрыв.
Осадки, полученные при особо жестких режимах, имеют макротвердость Н 5000–6000 МПа, мелкозернистую напряженную структуру. О высоком уровне растягивающих напряжений в осажденном железе свидетельствует большое количество микротрещин.
Известно, что твердость материала оказывает заметное влияние на износостойкость детали. Однако следует сказать, что однозначной взаимосвязи между твердостью и износостойкостью покрытий не существует. На износостойкость покрытия, в том числе и железного, оказывают влияние многие факторы, среди которых не только его твердость, но и микроструктура, пористость и шероховатость осадка, величина и характер нагрузки, условия смазки сопряжения, материал сопряженной детали и др.
Технологический процесс включает в себя следующие операции: механическую обработку восстанавливаемой поверхности; очистку деталей и промывку их органическими растворителями; монтаж детали на подвесные приспособления и защиту мест, не подлежащих покрытию, обезжириванию; анодную обработку; наращивание покрытия (электролиз); мойку в холодной и горячей воде; демонтаж детали с приспособления; удаление защитных пленок, сушку и термообработку; механическую обработку поверхности в соответствии с требованиями чертежа.
Предварительная механическая обработка восстанавливае-
мой поверхности выполняется с целью восстановления ее геометрической формы и расположения относительно конструкторских или технологических баз. Кроме этого, механической обработкой устраняются следы износа, поверхностные дефекты материала и обеспечивается максимально высокое качество. Поэтому предварительную обработку чаще всего выполняют шлифованием, в отдельных случаях ее дополняют полированием.
Припуски на шлифование, режущий инструмент и режимы резания рассчитываются или принимаются согласно общим рекомендациям для обработки соответствующих материалов.
177
Очистка деталей проводится с целью удаления с их поверхности продуктов коррозии, масляных и других загрязнителей. Эта операция выполняется на этапе разборно-моечных работ на соответствующем участке ремонтного предприятия. Моющие растворы, режимы выполнения моечных операций, оборудование описаны в специальной литературе [4, 24].
Монтаж деталей на подвеске. При монтаже необходимо обеспечить надежный контакт на участке электрической цепи деталь — подвеска — штанга.
В состав этой операции входит «оживление» (зачистка) восстанавливаемой поверхности детали шлифовальной шкуркой зернистостью 63–32.
Защита поверхностей, не подлежащих наращиванию, производится нанесением нескольких слоев цапон-лака (обычно в смеси с нитроэмалью в соотношении 1:2,5), приклеиванием полихлорвиниловой пленки толщиной 0,2–0,3 мм, применением различных колпаков, футляров, экранов, изготовленных из диэлектрических химстойких материалов.
Обезжиривание проводится с целью окончательной очистки поверхностей, подлежащих наращиванию, от жировых пленок. Сцепляемость покрытий с материалом подложки достигается лишь при условии, что поверхность детали свободна от какихлибо пленок толщиной более 0,005 мкм. При этих условиях сцепляемость обеспечивается силами металлических (атомных) связей материалов покрытия и детали.
В гальваностегии получило широкое распространение электрохимическое обезжиривание в щелочных электролитах.
Электрохимическое обезжиривание может проводиться на постоянном и переменном токе. При обезжиривании на постоянном токе детали завешиваются на катоде (катодное обезжиривание), разрушение жировой пленки происходит под действием выделяющегося водорода. Бурное выделение водорода на катоде делает процесс обезжиривания высокопроизводительным. Оторванные фрагменты жировой пленки омыливаются щелочью — образуется эмульсия.
Одновременно подложка насыщается водородом, что повышает ее хрупкость. Во избежание наводораживания поверхности детали в конце операции обезжиривания полярность меняется на обратную, и в течение короткого времени (0,20–0,25 длительности
178
обработки на катоде) деталь обрабатывают на аноде. При этом происходит растворение поверхностного слоя металла анода вместе с твердым раствором водорода в решетке железа.
Высокое качество очистки, отсутствие наводораживания и ускорение процесса достигаются при электрохимическом обезжиривании переменным током (U = 12…15 B).
В табл. 3.26 приведены составы щелочных электролитов и режимы процесса электрохимического обезжиривания постоянным и переменным током.
|
|
Таблица 3.26 |
|
|
|
|
|
Компоненты раствора |
Концентрация, г/л, и значения |
||
параметров процесса |
|||
и параметры |
|||
на постоянном |
на переменном |
||
режима обезжиривания |
|||
токе |
токе |
||
|
|||
Каустическая сода NaOH |
10 |
10 |
|
Сода кальцинированная Na2CO3 |
25 |
25 |
|
Тринатрий фосфат Na3PO4 |
25 |
25 |
|
Жидкое стекло Na2SiO3 |
3 |
— |
|
Эмульгатор ОП-7 |
— |
3–5 |
|
Температура раствора, °С |
70–80 |
70 |
|
Плотность тока, А/дм2 |
5–10 |
10 |
|
Длительность обработки, мин |
1–2 |
0,5–2,0 |
Из химических технологий обезжиривания высокое качество дает лишь обработка поверхностей деталей кашеобразной «венской известью» (смесь окиси кальция и окиси магния).
После обезжиривания деталь промывается сначала теплой (60 °С), затем холодной проточной водой. Мойка детали преследует цель удалить с нее щелочной электролит и проверить качество обезжиривания. Сплошная (без разрывов) пленка воды на обезжиренной поверхности свидетельствует о высоком качестве очистки.
Анодная обработка является одной из важнейших операций технологического процесса осталивания и предназначена для удаления (растворения) окисной пленки на восстанавливаемой поверхности детали. Качество выполнения анодной обработки определяет прочность сцепления покрытия с подложкой.
Анодное травление выполняется в специальных ваннах на аноде. В табл. 3.27 приведены электролиты для анодной обработки.
179
|
|
|
Таблица 3.27 |
||
|
|
|
|
|
|
Компоненты раствора и |
Концентрация, г/л, и значения |
||||
параметров для электролитов |
|||||
параметры режима травления |
|||||
1 |
2 |
3 |
4 |
||
|
|||||
Серная кислота H2SO4 |
360 |
350 |
700–800 |
360–400 |
|
Железный купорос FeSO4 7H2O |
10 |
— |
— |
10–20 |
|
Тринатрий фосфат Na3PO4 |
— |
1180 |
— |
— |
|
Хромпик K2Cr2O7 |
— |
— |
20–30 |
— |
|
Плотность электролита, г/мл |
1,22 |
1,74 |
— |
— |
|
Температура, °С |
15–20 |
— |
18–25 |
15–20 |
|
Плотность тока, А/дм2 |
25–35 |
— |
5–10 |
25–30 |
|
Продолжительность травления, с |
30–45 |
— |
5–10 |
60–100 |
Прошедшие анодное травление детали в сборе с подвеской промывают и тем самым подогревают до 50–60 °С в ванне с горячей проточной водой.
Осталивание. Подвеска с деталями завешивается на катод в ванну осталивания и выдерживается в электролите без включения тока в течение 0,5–1,5 мин. За это время детали нагреваются до температуры электролита.
По истечении указанного времени включается ток малой плотности Dк = 1…5 А/дм2, и на таком режиме процесс ведется 2–5 мин. За это время восстанавливается пассивная (окисная) пленка, образовавшаяся в промежутке между операциями анодного травления и осталивания на поверхности детали. Восстановление происходит за счет выделения водорода на катоде при разряде его ионов:
H e H; H H H2 .
Атомы водорода взаимодействуют с окислами железа и оказывают восстанавливающее действие:
Fe2O3 6H 2Fe 3H2O.
Молекулярный (газообразный) водород разрыхляет и разрушает пленку окислов, удаляет ее с поверхности детали — обнажается кристаллическая структура подложки.
После завершения начального периода ванна плавно (за 5– 10 мин) «разгоняется», т.е. происходит медленное увеличение плотности тока до величины, установленной технологической документацией.
180
Далее процесс ведется на расчетных параметрах режима осталивания.
Горячие электролиты для осталивания — весьма агрессивные среды, поэтому ванны облицовываются кислотоупорными материалами: углеграфитовыми плитками, эмалью, полихлорвиниловым пластиком или пихтовой древесиной (рис. 3.33).
Рис. 3.33. Ванна для осталивания:
1 — бортовой отсос паров электролита; 2 — кислотоупорная облицовка; 3 — анод стальной со стеклотканевым мешком; 4 — деталь (катод);
5 — электролит; 6 — электронагреватель; 7 — корпус ванны; 8 — теплоизоляция; 9 — бак для масла; 10 — теплоноситель (масло);
11 — прокладка уплотнительная; 12 — штанги катода и анода
Распространены ванны, изготовленные из кислотоупорного бетона.
Промывка в горячей воде проводится в отдельных ваннах с целью удаления основной части кислого электролита с поверхности детали.
Нейтрализацию остатков электролита проводят в 5–10- процентном растворе каустической соды в течение 5–10 мин. Для этого в технологической линии также предусматривается ванна. Температура раствора 70–80 °С.
Окончательная мойка осуществляется в теплой (50–60 °С) проточной воде. Затем следует разборка подвесок, удаление изоляции и сушка в древесных опилках, в сушильных шкафах или обдувкой сжатым воздухом.
Термообработка выполняется с целью снижения хрупкости слоя покрытия.
Термообработка по своему содержанию соответствует низкому отпуску, т.е. проводятся нагрев в масляной ванне до температуры 180–200 °С и выдержка в течение 1–2 ч.
181
Механическая обработка проводится с целью выполнения требований рабочего (ремонтного) чертежа. Заданную точность размера восстанавливаемой поверхности, точность геометрической формы и расположения деталей чаще обеспечивают шлифованием.
Режимы резания и характеристики шлифовальных кругов, рекомендуемые для обработки деталей с гальваническими покрытиями, приведены в табл. 3.28.
|
|
Таблица 3.28 |
|
|
|
|
|
Параметр |
Вид железных покрытий |
||
Твердые |
Мягкие |
||
|
Н 5000 МПа |
Н = 3000…4500 МПа |
|
|
Электрокорунд |
Электрокорунд |
|
Абразивный материал |
белый или |
||
белый |
|||
|
нормальный |
||
|
|
||
Зернистость |
25 |
25 |
|
Твердость |
СМ2 |
С1–С2 |
|
Связка |
Керамическая |
Керамическая |
|
Режимы резания: |
|
|
|
скорость резания, м/с |
30–35 |
30 |
|
скорость вращения детали, |
|
|
|
м/мин |
20–25 |
20–25 |
|
Подача: |
|
|
|
продольная, мм/об. |
1,0–1,5 |
1,0–1,5 |
|
поперечная, мм/дв. ход |
0,01–0,02 |
0,01–0,02 |
Для обработки гальванических железных покрытий лезвийным инструментом применяются резцы с пластинками из твердого сплава Т30К4 с геометрическими параметрами:
= 0°; = 5°; = +15°; = 60°; ' = 30°; r = 1,5 мм — для мягких покрытий;
= 0°; = 5°; = +15°; = 45°; ' = 30°; r = 1,0 мм — для твер-
дых покрытий.
Перспективным направлением совершенствования технологии восстановления деталей является вневанное проточное осталивание. Многочисленные исследования, выполненные М.П. Мелковым, Ю.Н. Петровым, В.П. Ревякиным и др., показывают, что при таком ведении процесса электролиза создаются благоприятные условия для управления как самим процессом, так и качеством железных осадков.
182