
Metod_2542
.pdfную поверхность. Хорошая очищающая способность достигается высоким ударным импульсом (на расстоянии 20 см от насадки его величина составляет более 70 %), а большая площадь очистки — вращением струи.
Турболазер — насадка, которая изменяет структуру жидкости, поступающей на очищаемую поверхность. Каждая капля воды турболазера в 10 раз крупнее и весит в 1000 раз больше, чем в машинах с обычными насадками. Мелкие капли жидкости теряют свою силу из-за сопротивления воздуха, а крупные — ударяют по очищаемой поверхности со скоростью 600 км/ч. Отсюда возникает мощный ударный импульс, величина которого на расстоянии 20 см от насадки составляет 90 %, в то время как для обычных машин — 5–15 %, а для турбонасадки — 70–75 %.
Наружная мойка машин погружением в ванну (см. рис. 2.7) достаточно широко применяется в ремонтном производстве по причине высокого качества очистки и высокой производительности. Качество очистки и экономическая эффективность этой операции существенно могут быть повышены активацией моющего раствора в ванне. Например, продуванием раствора паром, сжатым воздухом или механическими активаторами.
Очистка и мойка деталей
Очистка деталей от нагара, накипи и продуктов коррозии может производиться химическим, механическим, термохимическим и комбинированным способами. Очистку от нагара стальных и чугунных деталей можно осуществлять химическим способом, основанным на использовании щелочных растворов повышенной концентрации. В табл. 2.1 представлена массовая концентрация компонентов щелочного очистителя в водном растворе для удаления нагара с поверхностей деталей из различных материалов, г/л. Наличие NaOH в растворе приводит к разрушению алюминия:
2Al + 6NaOH = 2Na3AlO3 + 3H2.
Детали из алюминиевых сплавов обрабатывают в растворе, не содержащем каустической соды. Детали загружают в ванну с раствором (см. табл. 2.1) на 3–4 ч при температуре раствора 90–95 °С. Размягченный нагар снимают металлическими щетками, а затем
23
детали промывают в слабом щелочном растворе (0,1 % К2СОз, 0,2 % Na2SiO3). Однако этот способ очистки малопроизводителен.
|
|
Таблица 2.1 |
|
|
|
Компонент раствора |
Черные сплавы |
Алюминиевые сплавы |
Кальцинированная сода (Na2CO3) |
11,4 |
10,0 |
Каустическая сода (NaOH) |
13,5 |
— |
Жидкое стекло (Na2SiO3) |
11,0 |
10,0 |
Хромпик (K2Cr2О7 или Na2Cr2O7) |
0,8 |
1,0 |
Мыло |
— |
10,0 |
Тринатрий фосфат (Na3PO4) |
12,0 |
— |
Активное разрушение большинства загрязнений наблюдается при щелочности, равной рН 11,5–13,0. Источником щелочности в моющих растворах обычно является кальцинированная сода, как доступная и дешевая щелочь. Чаще всего моющий раствор изготавливают из трех-четырех щелочных компонентов.
Тринатрий фосфат, триполифосфат натрия вводятся в
моющий раствор для умягчения воды, одновременно они являются диспергирующими (измельчающими загрязнения) добавками.
Силикаты — метасиликат натрия и жидкое стекло — вы-
полняют роль ингибиторов коррозии, повышают диспергирующие свойства растворов и предотвращают повторное осаждение загрязнений из растворов на очищенную поверхность детали.
Из синтетических моющих средств для машин струйного типа рекомендуются МЛ-51, Лабомид-101 и МС-8. Моющая способность и сроки службы их больше, чем у щелочных растворов, они более экономичны. Растворы СМС не вызывают коррозии черных металлов, не разрушают алюминиевые сплавы, не оказывают вредного влияния на здоровье человека, не требуют последующего ополаскивания деталей.
К недостаткам СМС следует отнести склонность их к повышению пенообразования. В связи с этим в моющие растворы на основе СМС рекомендуется вводить пеногасители (дизельное топливо, керосин или уайт-спирит).
Для выварочных ванн при мойке погружением рекомендуется СМС марок МЛ-52, Лабомид-203 или МС-8. Эти растворы в 3–4 раза эффективнее растворов каустической соды.
24
В табл. 2.2 приведены технологические рекомендации по применению некоторых СМС.
Таблица 2.2
|
|
|
|
|
Режим очистки |
1 т , кг |
|||
Наименование моющихсредств |
|
|
|
|
|
|
|
|
|
Состояние поставки |
Назначение |
|
Концентрация, г/л |
|
Температура раствора, |
Давление, МПа |
Продолжительность очистки, мин |
препаратаРасход на очищаемыхизделий |
|
|
|
|
Тип удаляемых |
|
|
С |
|
|
|
|
|
|
|
|
|
° |
|
|
|
|
|
|
загрязнений |
|
|
|
|
|
|
|
|
|
|
|
|
|
|
|
|
|
|
Очистка |
|
|
|
|
|
|
|
|
|
машин, |
Горючесмазоч- |
|
|
|
|
|
|
|
|
сборочных |
|
|
|
|
|
|
|
|
|
ные материалы |
|
|
|
|
|
|
|
|
|
единиц и |
|
|
|
0,25–0,6 |
|
|
|
МЛ-51 |
Порошок |
(ГСМ), про- |
10–20 |
|
80–85 |
10–15 |
1,5–5,5 |
||
черных и |
|
||||||||
цвета |
ления и терми- |
|
|||||||
|
белого |
деталей из |
дукты их окис- |
|
|
|
|
|
|
|
|
|
|
|
|
|
|
||
|
|
цветных |
ческого разло- |
|
|
|
|
|
|
|
|
сплавов в |
|
|
|
|
|
|
|
|
|
жения |
|
|
|
|
|
|
|
|
|
струйных |
|
|
|
|
|
|
|
|
|
|
|
|
|
|
|
|
|
|
|
машинах |
|
|
|
|
|
|
|
Лабомид-101 |
То же |
То же |
То же |
10–20 |
|
70–85 |
0,25–0,5 |
10–30 |
1,5–6 |
|
|
|
|
|
|
|
|||
|
|
|
|
|
|
|
|
|
|
|
|
Очистка |
|
|
|
|
|
|
|
|
|
деталей из |
ГСМ, продук- |
|
|
|
|
|
|
МЛ-52 |
– // – |
черных и |
ты их окисле- |
20–30 |
|
80–95 |
— |
1,0–3,0 |
2,0–2,5 |
сплавов в |
ния, лаковые |
|
|||||||
|
цветных |
ния и разложе- |
|
|
|
|
|
|
|
|
|
ваннах |
пленки |
|
|
|
|
|
|
|
|
(вываркой) |
|
|
|
|
|
|
|
Лабомид-203 |
|
|
Смолистые от- |
20–30 |
|
80–100 |
— |
1,5–3,0 |
— |
– // – |
То же |
ложения, лако- |
|
||||||
|
|
|
|
|
|
|
|||
|
|
|
вые пленки |
|
|
|
|
|
|
|
|
|
|
|
|
|
|
|
|
|
|
|
|
|
|
|
|
|
25 |
Окончание табл. 2.2
|
|
|
|
|
Режим очистки |
1 т , кг |
|||
Наименование моющихсредств |
|
|
|
|
|
|
|
|
|
Состояние поставки |
Назначение |
|
Концентрация, г/л |
|
Температура раствора, |
Давление, МПа |
Продолжительность очистки, мин |
препаратаРасход на очищаемыхизделий |
|
|
|
|
Тип удаляемых |
|
|
С |
|
|
|
|
|
|
|
|
|
° |
|
|
|
|
|
|
загрязнений |
|
|
|
|
|
|
|
|
|
|
|
|
|
|
|
|
|
|
Для струй- |
|
|
|
|
|
|
|
МС-8 |
Порошок |
ной очист- |
Смолистые от- |
10–20 |
|
75–85 |
0,25–0,6 |
10–20 |
1,0–2,0 |
сборочных |
|
||||||||
цвета |
вые пленки |
|
|||||||
|
белого |
ки машин, |
ложения, лако- |
|
|
|
|
|
|
|
|
|
|
|
|
|
|
||
|
|
единиц, де- |
|
|
|
|
|
|
|
|
|
талей |
|
|
|
|
|
|
|
|
Жидкость |
Очистка де- |
Продукты |
|
|
|
|
|
|
АМ-15 |
окисления и |
100 |
|
20–30 |
— |
20–40 |
3,0–5,0 |
||
коричнево- |
в ваннах |
разложения |
|
||||||
|
светло- |
талей ДВС |
термического |
|
|
|
|
|
|
|
|
|
|
|
|
|
|
|
|
|
го цвета |
(вываркой) |
ГСМ |
|
|
|
|
|
|
|
|
|
|
|
|
|
|
|
Более совершенным является механический способ удаления нагара косточковой или капроновой крошкой, стеклянными шариками, гранулами сухого льда и т.д. (рис. 2.8). Наибольшее распространение получила очистка от нагара косточковой крошкой (дробленая скорлупа фруктовых косточек). Косточковая крошка подается потоком сжатого воздуха, движущегося с высокой скоростью, на поверхность с нагаром под давлением 0,3–0,6 МПа. Частицы, с силой ударяясь о поверхность детали, разрушают и удаляют нагар и другие загрязнения, при этом не нарушая шероховатости поверхности детали. Это особенно важно для деталей, изготовленных из алюминиевых сплавов, а также ответственных деталей и сборочных единиц двигателей (коленчатые валы, шатуны, головки блоков, выпускные коллекторы и др.). Очистка поверхностей деталей косточковой крошкой выполняется в специальных установках. Перед обработкой косточковой крошкой поверхности с нагаром предварительно с нее должны быть удалены масляные и асфальтосмолистые загрязнения. Для удаления с деталей нагара применяются металлический песок и гидропескоструйная очистка.
26

Однако при такой очистке на поверхностях деталей могут появляться риски и царапины, которые являются очагами более интенсивного повторного образования нагара.
Рис. 2.8. Схема установки для очистки деталей косточковой крошкой: 1 — смеситель; 2 — клапан; 3 — шланг; 4 — поворотный стол;
5 — наконечник; 6 — корпус; 7 и 8 — краны; 9 — бункер; 10 — циклон; 11 — вентилятор
Хорошие результаты дает очистка деталей от нагара термохимическим способом в расплаве солей и щелочей. Наиболее распространенный состав расплава содержит 65 % NaOH, 30 % Na3PO4 и 5 % NaCl.
Температура расплава составляет (400 ± 20) °С. Для очистки деталей от нагара (а также от накипи и ржавчины) используют специальную установку (рис. 2.9), состоящую из четырех ванн. В первой ванне с щелочным расплавом детали выдерживают 5-10 мин. При этом происходит разрушение загрязнений. Затем детали переносят во вторую ванну с проточной водой, где резкий перепад температур вызывает бурное парообразование, что способствует разрыхлению остатков нагара (накипи, ржавчины) и растворению остатков расплава. В третьей ванне производится кислотная обработка (травление) с целью осветления поверхности деталей и нейтрализации остатков щелочи. При одновременной очистке поверхности детали из черных и алюминиевых сплавов травление ведут раствором фосфорной кислоты (85 кг/м3) с добавлением хромового ангидрида (125 кг/м3) при температуре (30 ± 5) °С. Окончательно детали промывают горячей водой в четвертой ванне. Общее время обработки 20–25 мин.
27

Рис. 2.9. Схема установки для очистки деталей от нагара и накипи в расплаве солей и щелочей:
1 — ванна с расплавом; 2 — первая промывочная ванна; 3 — ванна с кислотным раствором; 4 — электротельфер
для загрузки и выгрузки деталей; 5 — вторая промывочная ванна
Очистку от накипи внутренних полостей двигателя и деталей системы охлаждения, как правило, проводят щелочными растворами. Карбонаты кальция, магния, содержащиеся в накипи, хорошо растворяются в соляной кислоте, а силикаты и сульфаты кальция и магния хорошо разрыхляются в щелочных растворах. Разрыхленный слой накипи легко смывается струей воды. Накипь с внутренних поверхностей трубок радиаторов удаляют 3–5 %-м раствором каустической соды с последующей промывкой проточной водой. После этого трубки в течение 5–10 мин обрабатывают 5–8 %-м водным раствором соляной кислоты при температуре 50–60 °С. В качестве ингибитора коррозии в раствор добавляют 3–4 г уротропина на 1 л раствора. Для нейтрализации кислоты проводят окончательную промывку радиатора 15–20 %-м раствором углекислой соды, а затем горячей водой. Для удаления накипи с поверхностей деталей из алюминиевых сплавов применяют растворы фосфорной и молочной кислот.
Очистку поверхностей деталей от коррозии (продукты коррозии FeО, Fе3О4, Fе2О3) можно осуществлять механической, химической или абразивно-жидкостной обработкой. Механическую обработку осуществляют металлическими щетками или металлическим песком. Металлическим песком, подаваемым на очищае-
28
мую поверхность деталей сжатым воздухом, можно очищать массивные детали достаточной толщины. Мелкие детали (шестерни, пружины и др.) очищают от коррозии (окалины, загрязнений) аб- разивно-жидкостной обработкой в галтовочных барабанах с фарфоровой крошкой. Барабан с загруженными деталями и фарфоровой крошкой вращается с частотой 16–20 об./мин в ванне с водным раствором кальцинированной соды и хозяйственного мыла при температуре 60–70 °С в течение 1,5–2 ч. После такой обработки детали промывают водой. Химический способ очистки от коррозии заключается в травлении пораженных коррозией поверхностей растворами серной, соляной, фосфорной и других кислот, а также пастами. Очистка поверхностей деталей от коррозии может осуществляться термохимическим способом в расплаве солей, так же как и при удалении нагара.
Очистку поверхностей деталей от старых лакокрасочных покрытий проводят при подготовке поверхности к очередной окраске. Лакокрасочные покрытия могут быть удалены частично или полностью. Выбор способа и режима очистки зависит от марки старого нанесенного лакокрасочного покрытия, материала детали, на которую было нанесено это покрытие, и режима нанесения.
Удаление лакокрасочных покрытий осуществляется применением растворителей, смывок, растворов щелочей и специального инструмента, а также путем обработки открытым пламенем. Наибольшее распространение нашел способ обработки деталей из черных металлов и их сплавов в ванне с водным раствором каустической соды концентрацией 50–100 г/л при температуре раствора 85 °С. Для ускорения процесса снятия лакокрасочного покрытия (в 2–3 раза) в раствор вводят ускорители — трипропиленгликоль или смесь триэтаноламина с монофениловым эфиром этиленгликоля (1–10 % массы каустической соды). По окончании обработки деталей в щелочной ванне их промывают в воде при температуре 50–60 °С и нейтрализуют 10 %-м водным раствором ортофосфорной кислоты. После такой обработки на поверхности деталей образуется пленка фосфатов, временно защищающая от коррозии и являющаяся грунтом для последующего лакокрасочного покрытия.
Когда удаление лакокрасочного покрытия в щелочных растворах невозможно или нецелесообразно технологически или конструктивно, то его удаляют растворителями (№ 646, 647, 648,
29
651 и Р-10), смывками (СД(СП), СД(ОБ) и АФТ-1) и специальным инструментом. Смывки наносят на поверхность распылением или кистью. Скорость действия смывок: СД(СП) — 5 мин, СД(ОБ) — 30 мин и АФТ-1 — 20 мин; расход соответственно 0,17; 0,15; 0,25 кг/м2. После выдержки смывки на крашеной поверхности детали в зависимости от марки смывки лакокрасочное покрытие снимают скребками с последующей протиркой очищенной поверхности ветошью, смоченной уайт-спиритом или раствором CMC.
В некоторых случаях старое лакокрасочное покрытие снимают механическим способом, используя металлические проволочные щетки — дисковые, кольцевые, торцевые (чашечные) и др. Работу выполняют вручную или с помощью механизированного инструмента. В отдельных случаях при очистке поверхностей от старой краски используют пламенный метод. Очищаемую поверхность нагревают кислородно-ацетиленовым пламенем или горячим воздухом, а продукты горения удаляют с помощью щеток.
Очистку поверхностей деталей от консервационных смазочных материалов производят в растворах CMC (например, Ла- бомид-101) с концентрацией 10 кг/м2 при температуре 90–100 °С.
Очистку деталей от технологических загрязнений (пыли, стружки, смазочных эмульсий) проводят в машинах струйного типа под давлением 0,4–0,6 МПа раствором тринатрийфосфата или нитрита натрия (3–5 кг/м3) при температуре 75–85 °С.
При выполнении очистных операций используют мониторные, струйные, погружные, комбинированные специальные моечные машины, автоматизированные линии, а также специальные установки для механического и термохимического способов очистки поверхностей деталей.
Мониторные (гидромониторные) моечные машины обеспечи-
вают гидродинамическую очистку. На очищаемую поверхность подается водяная струя под давлением 5–15 МПа при температуре 20–30 °С. Эффективное удаление загрязнений обеспечивается комплексным воздействием динамического напора струи, высокой температуры и моющих средств. В гидромониторных установках применяют специальные насадки, которые обеспечивают эффективную гидродинамическую очистку. В зависимости от вида изделий и загрязнений через различные по конструкции насадки мони-
30
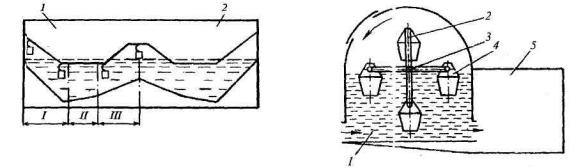
торной установки могут подаваться вода, вода с паром, различные щелочные растворы или растворы CMC.
Струйные моечные машины используют для общей очистки поверхностей деталей. Основными составными частями этих машин являются моечная камера, насосный агрегат, система гидрантов с насадками, баки для очищающей среды и транспортирующее устройство. В моечной камере размещены гидранты. Нагревают моющий раствор обычно в баках с помощью горячей воды, электрической энергии, жидкого топлива или газа. Нагревающими элементами являются трубчатые змеевики при нагревании водой, жаровые трубы при нагревании жидким топливом и газом и теплоэлектронагреватели. Гидранты с помощью различного числа насадок образуют струи раствора и обеспечивают направление струи на очищаемую поверхность. Давление жидкости в гидрантах 0,2–0,6 МПа при диаметре отверстия насадки 4–6 мм.
Погружные моечные машины могут быть проходными (рис. 2.10) и тупиковыми (рис. 2.10–2.13), стационарными (рис. 2.10, 2.11) и переставными (рис. 2.12, 2.13).
Транспортирование деталей в процессе мойки внутри стационарных машин может осуществляться транспортерами (см. рис. 2.10 — для проходных) или роторами (см. рис. 2.11). Перемещение деталей внутри переставных машин может отсутствовать (см. рис 2.12), производиться роторами или вибрирующими платформами путем встряхивания (см. рис. 2.13).
Рис. 2.10. Схема моечной установки |
Рис. 2.11. Схема моечной |
конвейерного типа: |
установки роторного типа: |
1 — камера мойки; |
1 — ванна; 2 — крестовина; |
2 — камера ополаскивания; |
3 — вал; 4 — корзина; |
I, II, III — зоны нагрева, |
5 — очистное отделение |
колебаний и обмыва |
|
31

Рис. 2.12. Переставная |
Рис. 2.13. Ванна с вибрирующей |
моечная установка |
платформой: |
|
1 — ванна; 2 — вибрирующая платформа; |
|
3 — кассета для деталей; 4 — пневмоцилиндр; |
|
5 — стойка; 6 — нагревательные элементы; |
|
7 — крышка ванны; 8 — рольганг; |
|
9 — кран управления; 10 — упоры вибрирую- |
|
щей платформы; 11 — люк для очистки ванны |
Интенсификация процесса мойки достигается путем повышения температуры моющего раствора, концентрации моющих средств, перемещения деталей, циркуляции раствора и создания в ванне ультразвуковых колебаний. Удаление загрязнений в стационарных моечных машинах механизировано путем применения скребковых или винтовых транспортеров, а в переставных производится вручную либо гидравлически, путем слива и транспортирования потоком воды в установленную поблизости емкость.
Комбинированные моечные машины сочетают различные способы очистки, что способствует повышению ее качества.
Специальные моечные машины предназначены для очистки поверхностей деталей, которую описанными выше способами качественно выполнить невозможно. Например, полная очистка масляных каналов в коленчатых валах, блоках цилиндров, очистка фильтров, прецизионных деталей и др. обеспечиваются только в специальных моечных машинах.
Вопросы для самоконтроля
1. Охарактеризуйте влияние качества очистки и мойки на качество ремонта, ресурс машин после ремонта и безопасность технологического процесса.
32