
Metod_2542
.pdfВ справочной литературе рекомендуются припуски на механическую обработку деталей, определенные статистическим методом. При этом учитываются тип обрабатываемой поверхности, вид обработки, величина размера, обрабатываемый материал и другие факторы. Табличные значения припусков широко используются при разработке технологических процессов. Однако надо помнить, что статистический метод дает завышенные значения припусков, в результате трудоемкость механической обработки деталей возрастает.
Таблица 3.35
|
|
Наибольший |
Погрешность |
||
|
|
размер |
установки, мкм |
||
Тип |
Установочная |
детали, или |
|
|
|
приспособления |
база |
диаметр |
радиальная |
осевая |
|
|
|
поверхности, |
|||
|
|
мм |
|
|
|
|
Шлифованная |
6–50 |
20 |
10 |
|
|
50–120 |
30 |
15 |
||
|
поверхность |
||||
|
120–260 |
40 |
25 |
||
|
|
||||
|
Чисто обрабо- |
6–50 |
50 |
30 |
|
|
танная поверх- |
50–120 |
80 |
50 |
|
|
ность |
120–260 |
100 |
80 |
|
Трехкулачковый |
Предварительно |
5–120 |
150 |
80 |
|
обработанная |
|||||
самоцентрирующийся |
120–260 |
200 |
100 |
||
поверхность |
|||||
патрон |
|
|
|
||
Пруток горяче- |
10–50 |
200–280 |
90–130 |
||
|
|||||
|
250– |
||||
|
катаный |
50–120 |
400–500 |
||
|
350 |
||||
|
|
|
|
||
|
Литая, штампо- |
|
|
|
|
|
ванная или |
50–120 |
300 |
100 |
|
|
наплавленная |
120–260 |
400 |
120 |
|
|
заготовка |
|
|
|
|
Цанговый патрон |
Шлифованная |
15–50 |
20–50 |
— |
|
поверхность |
50–80 |
30–75 |
— |
||
|
|||||
|
Точно обрабо- |
|
В пределах |
|
|
Оправка жесткая |
— |
допуска на |
10 |
||
танное отверстие |
|||||
|
|
зазор |
|
||
|
|
|
|
||
Оправка разжимная |
То же |
До 50 |
10–35 |
20 |
|
50–200 |
20–60 |
50 |
|||
|
|
213
|
|
|
Таблица 3.36 |
|
|
|
|
|
|
|
Погрешность установки, мм, |
|||
Метод выверки |
|
для деталей |
||
|
мелких |
средних |
|
крупных |
1. Разметкой иглой по необработанной |
|
|
|
|
или предварительно обработанной по- |
0,5–1,0 |
1,0–1,5 |
|
2,0–3,0 |
верхности |
|
|
|
|
2. По предварительно обработанной |
0,02–0,04 |
0,03–0,05 |
|
0,05–0,12 |
поверхности индикатором |
|
|||
|
|
|
|
|
|
|
|
|
|
В тех случаях, когда механическая обработка восстанавливаемой поверхности осуществляется несколькими операциями, возникает необходимость в расчете операционных (промежуточных) размеров (рис. 3.46).
Рис. 3.46. Схема расчета операционных размеров при обработке шейки вала:
dнаим; d1наим; d2наим; dзаг. наим — наименьший предельный размер, соответственно, готовой детали, заготовки после чистовой обработки, после черно-
вой обработки и заготовки после ее изготовления или восстановления;
dнаиб; d1наиб; d2наиб; dзаг. наиб — наибольший предельный размер готовой детали и заготовки на разных этапах технологического процесса;
Td; Td1; Td2; Tdзаг — допуск на финишную и предшествующие операции, а также допуск на заготовку;
Z1; Z2; Z3 — минимальный расчетный припуск на выполнение трех операций технологического маршрута обработки шейки вала.
Из рис. 3.46 видно, что каждый операционный размер получается путем суммирования наименьшего предельного размера детали по чертежу и припусков всех предшествующих переходов. Это
214

позволяет сделать вывод, что задача по определению промежуточных припусков и размеров в ремонтном производстве решается так же, как и при проектировании технологического процесса механической обработки деталей в машиностроении [4, 13, 25].
3.5.3.6. Расчет и выбор параметров режима резания
Режим резания при механической обработке определяется следующими параметрами:
глубиной резания t, мм;
подачей S, мм/об.;
скоростью резания v, м/мин.
При расчете и выборе параметров резания следует исходить из того, что операция должна обеспечивать выполнение технологических требований на обработку поверхности детали (точность и шероховатость), осуществляться с наименьшей трудоемкостью. При этом нужно стремиться к наиболее полному использованию режущих свойств инструмента и техникоэксплуатационных данных станка. Определение режима резания позволяет выбрать тип и размеры режущего инструмента, а также геометрические параметры режущей его части.
Но кроме наименьшей себестоимости при расчете и выборе параметров режима резания необходимо учитывать жесткость и прочность системы «Станок – Приспособление – Инструмент – Деталь» (СПИД).
Расчетные значения параметров режима резания корректируются по паспортным данным станка. Расчетную мощность резания Nрез сравнивают с мощностью электродвигателя Nэ станка:
Ný Nðåç ,
где — КПД передачи привода шпинделя ( = 0,7…0,8). Изношенная деталь, как правило, имеет неравномерный из-
нос, следовательно, при механической обработке величина припуска и глубина резания — величины переменные. Процесс резания при этом сопровождается изменением нагрузки на инструмент, механизмы станка и приспособление. Кроме этого, обрабатываемая поверхность может иметь твердость, отличную от тре-
215
буемой по рабочему чертежу детали. Меньшая твердость получается в случае износа поверхностного упрочненного слоя, а большая — в результате наклепа материала. Поэтому при расчете и выборе режимов резания для черновых видов обработки расчетную скорость резания следует уменьшить на 10–20 %.
Методика расчета режимов резания рассматривается в соответствующих разделах курса «Резание металлов».
3.5.3.7. Выбор станков, инструментов и приспособлений
Группа станка выбирается в зависимости от принятого метода обработки поверхности или совокупности поверхностей на данной операции. Поэтому название операции происходит от наименования группы станка, например: обтачивание на станках токарной группы требует названия операции — токарная. То же можно сказать о фрезерных, сверлильных, протяжных и других операциях.
Тип станка выбирается в зависимости от вида обработки детали (черновой, чистовой и т.д.) с учетом конструкции и размеров заготовки, а также по принципу достижения наименьшей себестоимости обработки.
Сравнение и выбор экономически целесообразного варианта производится по величине приведенных затрат Зпр:
Зпр = СтN + EнК,
где Ст — себестоимость операции, выполняемой на данном станке, р.; N — годовая программа выпуска деталей, шт.; Ен — нормативный коэффициент экономической эффективности (Ен = 0,25 р. на рубль капитальных вложений); К — капитальные вложения на
осуществление данного варианта технологического процесса (К ≈ Sст, где Sст — стоимость станка).
Cò Cç.ï Cî Cïð Cèí ñòð Hö ,
где Сз.п — заработная плата станочника; Со — затраты на эксплуатацию оборудования (станка); Cпр — затраты на эксплуатацию приспособления; Синстр — затраты на эксплуатацию инструментов; Нц — накладные цеховые расходы.
Cç.ï CTøò. ê K ,
216
где С — часовая тарифная ставка данного разряда (принимается по действующей на ремонтном заводе тарифной сетке); Тшт.-к — штучно-калькуляционное время на выполнение операции, ч; К — коэффициент, учитывающий доплаты (К = 1,14…1,50).
Cî |
|
Sñò |
, |
|
n |
||
|
100 Ni |
|
|
|
|
i 1 |
|
где Ni — годовая программа деталей i-й номенклатуры.
Cïð |
Sïð |
|
1 |
|
|
q |
|
, |
|
|
|
|
|
|
|||
n |
P |
100 |
||||||
|
Ni |
|
|
|
|
|||
|
i 1 |
|
|
|
|
|
|
|
где Sпр — стоимость приспособления, р.; Р — срок эксплуатации приспособления (2–5 лет); q — процент расходов на ремонт и техническое обслуживание приспособления (q = 10…20).
C |
|
Sèíñò ð zCперет |
t K |
|
, |
èí ñòð |
|
T Z 1 |
0 |
óá |
|
|
|
|
где Sинстр — стоимость инструмента, р.; z — количество допустимых переточек инструмента (принимается по нормативнотехнической документации); Сперет — стоимость одной переточки инструмента, р.; Т — стойкость инструмента, ч; t0 — основное время на данной операции, ч; Куб — коэффициент, учитывающий вероятность поломки инструментов.
Накладные цеховые расходы начисляются в процентах от заработной платы производственных рабочих. Они зависят от типа производства, степени автоматизации производственного процесса в цехе, принимаются от 150 до 800 % от заработной платы производственных рабочих.
3.5.3.8. Техническое нормирование станочных работ
Норма времени на обработку одной детали из партии описывается штучно-калькуляционным временем Тшт.-к:
Тшт.-к t0 tâ.ó tâ.ï tî.ð.ì |
|
tï. ç |
, |
|
|||
|
|
Ni |
217

где t0 — основное (машинное) время, т.е. время работы инструмента на данной операции; tв.у — вспомогательное время на установку и снятие детали; tв.п — вспомогательное время, связанное с переходом; tо.р.м — время на обслуживание рабочего места; tп.-з — подготовительно-заключительное время.
Основное (машинное) время для всех видов и методов обработки рассчитывается по формуле
t0 lnSy i ,
где l — длина обрабатываемой поверхности, мм; у — величина врезания и выхода инструмента, мм; n — частота вращения заготовки, об./мин; S — подача инструмента, мм/об.; i — число подходов.
Величина врезания и выхода резца при токарных и расточ-
ных работах определяется по формуле y y1 y2 y3,
где y1 — величина врезания инструмента, равная tgt , мм, t —
глубина резания, мм, — главный угол в плане, град; у2 — величина выхода (перебега) резца (у2 = 2…3 мм); у3 — величина врезания, необходимая для снятия пробной стружки (у3 = 2…5 мм).
Величина врезания и выхода инструмента при сверлении, зенкеровании или развертывании отверстия находится по формуле
y y1 y2 ,
где y1 — величина врезания инструмента, мм; у2 — выход инструмента при обработке сквозного отверстия (у2 = 3…5 мм).
Величина врезания сверла, мм,
y1 d2 ctg 2 ,
где d — диаметр сверла, мм; угол заточки сверла, град.
Для стали и чугуна средней твердости = 116…120°. С увеличением твердости угол заточки увеличивается до 140°.
Величина врезания зенкера и развертки
218
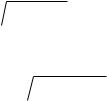
y1 d d1 ctg 90 , 2
где d и d1 — диаметр отверстия до и после обработки соответственно, мм; — угол наклона режущей кромки приемной части инструмента, град:
–для зенкеров = 30…60°;
–для развертки при обработке стали = 12…15°, при обработке чугуна = 4…5°.
Тогда величина врезания будет:
– при зенкеровании для = 30° |
у1 = 0,87 (d – d1); |
– при развертывании стали для = 15° |
у1 = 1,86 (d – d1); |
– при развертывании чугуна для = 5° |
у1 = 5,72 (d – d1). |
Величина врезания и перебега фрезы — |
|
у = у1 + у2,
где у1 — величина врезания, мм; у2 — величина перебега фрезы,
мм, у2 = (0,03…0,05) D (D — диаметр фрезы, мм).
При фрезеровании цилиндрической фрезой величину врезания находят по формуле
y1 Dt t2 .
При фрезеровании торцовой фрезой
y1 0,5 D D2 B2 ,
где t — глубина резания, мм; В — ширина фрезерования, мм. Вспомогательное время на установку и снятие заготовки,
вспомогательное время, связанное с переходом, а также время на обслуживание рабочего места и подготовительно-заключительное время принимают из таблиц нормативно-технической документации станочных работ.
Вспомогательное время на установку и снятие детали tв.у, например при обработке на токарных станках, выбирается в зависимости от типа приспособления, способа установки и массы заготовки (табл. 3.37).
219
Таблица 3.37
Способ установки |
|
Вспомогательное время, мин |
|
||||||
|
|
при массе детали, кг |
|
|
|||||
детали вручную |
|
|
|
|
|||||
0,5 |
1,0 |
|
3,0 |
5,0 |
8,0 |
|
12,0 |
20,0 |
|
|
|
|
|||||||
В трехкулачковом патроне с |
|
|
|
|
|
|
|
|
|
ручным зажимом |
|
|
|
|
|
|
|
|
|
– без выверки |
0,22 |
0,25 |
|
0,29 |
0,34 |
0,38 |
|
0,46 |
0,56 |
– с выверкой по мелку |
0,42 |
0,45 |
|
0,54 |
0,64 |
0,72 |
|
0,84 |
1,00 |
– с выверкой индикатором |
1,15 |
1,25 |
|
1,29 |
1,44 |
1,68 |
|
1,96 |
2,36 |
То же, с пневматическим за- |
|
|
|
|
|
|
|
|
|
жимом |
|
|
|
|
|
|
|
|
|
– без выверки |
0,11 |
0,12 |
|
0,13 |
0,14 |
0,16 |
|
0,19 |
0,24 |
– с выверкой по мелку |
0,32 |
0,34 |
|
0,38 |
0,44 |
0,50 |
|
0,57 |
0,70 |
В табл. 3.38 приведены нормы вспомогательного времени, связанного с переходом, при продольном обтачивании и растачивании на токарных станках.
Таблица 3.38
|
|
|
Вспомогательное вре- |
||||
|
Измерительный инструмент |
Обрабатываемый мм,диаметр |
|
мя, мин |
|
||
|
|
|
при высоте центра |
||||
Характер |
|
|
|
станка, мм |
|
||
|
|
до 200 |
|
до 300 |
|||
обработки |
|
|
|
||||
|
|
Длина обрабатывае- |
|||||
|
|
|
|||||
|
|
|
мой поверхности, мм |
||||
|
|
|
до |
до |
до |
до |
|
|
|
|
200 |
500 |
200 |
500 |
|
Обтачивание или раста- |
Штангенциркуль |
до 100 |
0,38 |
0,40 |
0,44 |
0,48 |
|
чивание по 9–8 квали- |
|
200–300 |
0,41 |
0,43 |
0,47 |
0,51 |
|
тету со взятием проб- |
Скоба или |
до 100 |
0,34 |
0,36 |
0,40 |
0,44 |
|
ной стружки |
штихмас |
100–300 |
0,37 |
0,39 |
0,43 |
0,47 |
Из табл. 3.38 видно, что затраты времени на обслуживание перехода зависят от точности обработки поверхности, метода измерения, типоразмера станка и размеров обрабатываемой поверхности. Это время расходуется на измерение, переключение механизмов станка, подвод и отвод инструмента от обрабатываемой поверхности и другие действия станочника.
Вспомогательное время, связанное с переходом, для других операций принимается по табл. 3.39–3.40, справочным материалам.
220
Время на обслуживание рабочего места tо.р.м |
принимается в |
||
процентах от оперативного времени (табл. 3.39). |
Таблица 3.39 |
||
|
|
||
|
|
|
|
|
Высота центров |
||
Составляющие затрат времени, % от опер. врем. |
|
станка, мм |
|
|
до 200 |
до 300 |
|
Организационное и техническое обслуживание ра- |
|
6 |
7 |
бочего места и естественные надобности станочника |
|
||
|
|
|
|
Физкультурные паузы |
|
3 |
3 |
Примечание. Оперативное время tоп определяется суммированием t0 и общего вспомогательного времени tв.
Подготовительно-заключительное время tп.-з. предназначено для подготовки рабочего места к обработке партии деталей: для знакомства с рабочим чертежом, получения и монтажа приспособлений на станке, настройки станка и т.д. Подготовительнозаключительное время при обработке деталей на токарных станках, мин, представлено в табл. 3.40.
Таблица 3.40
|
Высота центров станка, мм |
|||||||||
Способ установки детали |
|
до 200 |
|
|
до 300 |
|
||||
Количество устанавливаемых |
||||||||||
|
|
|
инструментов |
|
||||||
|
2 |
|
4 |
|
6 |
2 |
|
4 |
|
6 |
В центрах или на оправке на наладку станка, |
7 |
|
9 |
|
12 |
8 |
|
10 |
|
14 |
инструментов и приспособлений, мин |
|
|
|
|
|
|
|
|
|
|
В патроне самоцентрирующемся, цанговом |
8 |
|
10 |
|
12 |
12 |
|
14 |
|
16 |
или пневматическом, мин |
|
|
|
|
||||||
|
|
|
|
|
|
|
|
|
|
|
На дополнительные виды работ, мин |
|
|
|
|
|
|
||||
Установка упора |
|
1,5 |
|
|
|
2,0 |
|
|
||
Установка и регулировка люнета |
|
2,7 |
|
|
|
3,8 |
|
|
||
Смещение задней бабки для обточки конуса |
|
2,5 |
|
|
|
3,0 |
|
|
||
Получение инструментов и приспособлений |
|
|
|
|
|
|
|
|
|
|
станочником до начала работ и сдача после |
|
8 |
|
|
|
0 |
|
|
||
их окончания |
|
|
|
|
|
|
|
|
|
|
Подобные структурные составляющие подготовительнозаключительного времени можно взять в нормативно-технических документах по обработке на других группах и типах станков.
Разработка технологического процесса при восстановлении изношенных деталей в ремонтном производстве и машиностро-
221
ении имеет общую базу, являющуюся результатом исследований многих отечественных и зарубежных ученых и практиков.
Вопросы для самоконтроля
1.Назовите области применения механической обработки при восстановлении деталей.
2.Изложите методику расчета величины и количества ремонтных размеров деталей.
3.Изложите сущность метода восстановления постановкой дополнительных деталей.
4.Укажите этапы проектирования технологического процесса механической обработки деталей при восстановлении и охарактеризуйте содержание работ по ним.
5.Сформулируйте особенности выбора баз, расчета режимов резания, припусков, построения технологических маршрутов
иопераций проектирования технологического процесса механической обработки при восстановлении.
6.Изложите методику расчета технических норм времени при механической обработке.
3.6.Устранение дефектов пластическим деформированием
Этот способ восстановления может быть рекомендован для деталей, изготовленных из пластичных материалов, — стали, латуни и др. Он основан на изменении размеров и формы деталей за счет перераспределения металла самой детали. Пластическое деформирование может производиться с целью восстановления размеров изношенных поверхностей, формы и механических свойств детали.
3.6.1. Физические основы пластического деформирования металлов
В твердых телах атомы, молекулы или ионы расположены в строго определенном порядке, образуя кристаллическую решетку того или иного типа. Связь между указанными элементарными частицами в кристаллической решетке может быть различной.
Для минеральных веществ характерна ионная связь, т.е. электростатические силы удерживают положительно и отрицательно заряженные ионы, расположенные в узлах кристаллической решетки.
222