
Metod_2542
.pdf2.Перечислите виды загрязнений поверхностей машин, сборочных единиц и деталей.
3.Назовите методы, оборудование и материалы для очистки деталей от старой смазки.
4.Назовите методы, оборудование и материалы для очистки деталей от нагара.
5.Опишите технологический процесс очистки деталей от старой краски и продуктов коррозии.
2.3. Дефектация деталей
Для оценки влияния износа или разрушения рабочих поверхностей на работоспособность деталей, т.е. для выявления и описания дефектов, выполняется комплекс контрольно-измерительных операций — дефектация.
Дефект — несоответствие детали по какому-либо параметру требованиям рабочего чертежа.
Классификация дефектов по различным признакам, описание методов, приборов и технологий их обнаружения являются предметом отдельного учебного пособия, мы рассмотрим лишь некоторые методы контроля деталей, поступающих на дефектацию.
Контроль деталей, поступивших из разборочно-моечного участка, на соответствие их техническим требованиям рабочего или ремонтного чертежа проходит в две стадии: визуальный осмотр и технические измерения. На стадии визуального осмотра выявляются видимые дефекты: остаточные деформации, обломы, макротрещины и др. При наличии выбраковочных дефектов детали уже на этой стадии выбраковываются в утиль.
На стадии технических измерений определяется действительное состояние рабочих поверхностей деталей (размер поверхности, ее геометрическая форма, качество поверхности и др.), взаимное расположение поверхностей (соосность, перпендикулярность, параллельность и т.д.) и соответствие этих параметров техническим требованиям.
Для технических измерений используются универсальные и специальные измерительные инструменты, приборы и измерительные комплексы.
Наиболее ответственные детали проходят трехстадийный контроль: коленчатые валы, шатуны, блоки цилиндров, оси и ва-
33

лы силовой передачи и др. Для этих деталей в дополнение к двум вышеназванным стадиям контроля вводится операция неразрушающего контроля с целью обнаружения скрытых дефектов: микротрещин, пор, раковин и неметаллических включений.
По результатам контроля составляются карты дефектации и назначается технологический маршрут восстановления деталей. При составлении карты дефектации можно использовать данные табл. 2.3. Детали этой группы передаются на склад деталей, ожидающих ремонта (склад ДОР).
Таблица 2.3
|
Карта дефектации |
|
|
||||
|
|
|
|
|
|
|
|
|
Деталь |
|
|
|
|
|
|
|
Муфта включения сцепления |
|
|
||||
|
Номер детали |
|
|
|
|
|
|
|
130-1602051 |
|
|
|
|
|
|
|
Материал |
|
|
Твердость |
|||
|
Чугун СЧ15 |
|
|
НВ 163–229 |
|||
|
|
|
|
|
|
|
|
|
|
Размер, мм |
|
||||
|
Способ установле- |
рабочпо. чертежу |
.допустбез ремонта |
допуст. ремонтадля |
|
||
Возможные |
ния дефекта и изме- |
Заключение |
|||||
|
|
|
|
||||
дефекты |
рительный инстру- |
|
|
|
|
||
|
|
|
|
|
|||
|
мент |
|
|
|
|
|
|
|
|
|
|
|
|
|
|
1. Трещины и |
|
|
|
|
|
|
|
обломы любого |
|
|
|
|
|
|
|
характера и |
|
|
|
|
|
|
|
расположения, |
Осмотр |
— |
— |
— |
Браковать |
||
кроме трещин и |
|||||||
|
|
|
|
|
|
||
обломов ушка |
|
|
|
|
|
|
|
под оттяжную |
|
|
|
|
|
|
|
пружину |
|
|
|
|
|
|
|
2. Трещины и |
|
|
|
|
|
|
|
обломы ушка |
Осмотр |
— |
— |
— |
Восстанавливать |
||
под оттягиваю- |
|
|
|
|
|
наплавкой |
|
щую пружину |
|
|
|
|
|
|
34

|
|
|
|
Окончание табл. 2.3 |
||
|
|
|
|
|
|
|
|
Деталь |
|
|
|
|
|
|
Муфта включения сцепления |
|
|
|||
|
Номер детали |
|
|
|
|
|
|
130-1602051 |
|
|
|
|
|
|
Материал |
|
|
Твердость |
||
|
Чугун СЧ15 |
|
|
НВ 163–229 |
||
|
|
|
|
|
|
|
|
|
Размер, мм |
|
|||
|
Способ уста- |
|
.допустбез ремонта |
допуст. ремонтадля |
|
|
Возможные |
новления де- |
рабочпо. чертежу |
|
|||
фекта и измери- |
Заключение |
|||||
|
|
|
||||
дефекты |
|
|
|
|||
тельный ин- |
|
|
|
|
||
|
|
|
|
|
||
|
струмент |
|
|
|
|
|
|
|
|
|
|
|
|
3. Износ лап по |
Осмотр. Шаб- |
16+0,25 |
16 |
Более |
Восстанавливать |
|
высоте |
лон, 16,0 мм |
|
|
15 |
наплавкой |
|
4. Износ отвер- |
Измерение. |
|
|
|
|
|
стия под крыш- |
Пробка пластин- |
|
|
|
Браковать при |
|
ку подшипника |
чатая 47,9 мм |
47,5+0,04 |
|
|
||
47,9 |
— |
диаметре более |
||||
первичного ва- |
или индикатор- |
|
|
|
47,9 мм |
|
ла коробки пе- |
нутромер 35– |
|
|
|
||
|
|
|
|
|||
редач |
50 мм |
|
|
|
|
|
5. Износ шейки |
Измерение. |
|
|
|
|
|
под подшипник |
Скоба или мик- |
0,021 |
55 |
Менее |
Восстанавливать |
|
выключения |
рометр |
55 0,002 |
55 |
наплавкой |
||
|
||||||
сцепления |
50–70 мм |
|
|
|
|
Детали, параметры которых соответствуют требованиям чертежа, отправляются на сборку через комплектовочное отделение.
Крупные базовые детали (рамы, отвалы, стрелы, рукояти и др.) контролируются на разборочно-моечном участке после выполнения моечной операции.
Гусеничные полотна, радиаторы, баки, сборочные единицы системы смазки, электрооборудования, топливная аппаратура и т.п. дефектуются на рабочих местах, на которых производится ремонт.
На рис. 2.14 представлена типовая схема размещения оборудования на рабочем месте дефектовщика.
35
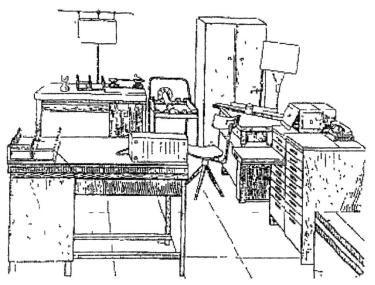
Рис. 2.14. Размещение оборудования на рабочем месте дефектовщика
Для контроля деталей на наличие скрытых дефектов без разрушения целостности их применяются следующие виды неразрушающего контроля:
–магнитный;
–акустический;
–капиллярный;
–оптический;
–радиационный;
–радиоволновый;
–тепловой;
–течеиспусканием (опрессовка);
–электрический;
–вихретоковый.
В машиностроении и в ремонтном производстве широкое распространение получили три первых вида.
Магнитный контроль. Этот вид контроля позволяет выявить в деталях (из ферромагнитных материалов) без их разрушения поверхностные и подповерхностные трещины. Он основан на том, что при намагничивании детали в местах дефекта нарушается равномерность магнитного поля, образуется поток рассеивания магнитных силовых линий, который и регистрируется прибором. Регистрация полей дефектов может производиться различными способами с использованием магнитных порошков, ферромагнитных пленок, феррозондов и индукторов.
36
При магнитопорошковом способе неразрушающего контроля
используется ферромагнитный порошок окиси железа (крокус) или суспензия с указанным порошком. Порошок под действием магнитного поля дефекта концентрируется вблизи дефекта, копируя его форму и размеры. Способ характеризуется высокой чувствительностью. Могут быть обнаружены поверхностные и подповерхностные дефекты, например, трещины шириной 1 мкм при длине и глубине до 10 мкм.
Магнитографический способ. При этом способе магнитные поля дефектов фиксируются магнитными пленками, которые накладываются на поверхность намагниченной детали. Полученный «отпечаток» считывается с пленки прибором с магнитной головкой и фиксируется индикатором.
Феррозондовый способ основан на том, что магнитное поле дефекта преобразуется в электрические сигналы с помощью специальных индикаторов — феррозондов. Способ характеризуется высокой чувствительностью. Феррозондовым способом могут быть выявлены поверхностные трещины глубиной до 0,1 мм, а также подповерхностные трещины, залегающие на глубине до 10 мм.
Индукционный способ. Магнитное поле дефекта фиксируется с помощью индуктивной катушки, в которой наводится ЭДС, зависящая от параметров магнитного поля рассеивания. По конструкции прибор проще, чем феррозондовый, но менее чувствительный.
Акустический (ультразвуковой) контроль. Сущность уль-
тразвукового контроля, предложенного проф. С.Я. Соколовым в 1929 г., заключается в том, что упругие механические колебания ультразвуковой частоты, направленные в деталь, способны отражаться от трещин, раковин и др. дефектов. Для возбуждения и приема колебаний используются различного рода электромеханические преобразователи, наибольшее распространение получили пьезоэлектрические преобразователи. По времени распространения прямой и отраженной волн устанавливается глубина залегания дефекта. Ультразвуковой способ позволяет контролировать детали, изготовленные из различных материалов: черных и цветных сплавов, пластмасс, резины и др. К достоинствам этого способа следует также отнести возможность обнаружения дефектов, залегающих на глубине до 2600 мм, т.е. практически все крупные
37
детали и заготовки можно контролировать этим способом на наличие скрытых дефектов.
Капиллярный контроль. Этот способ контроля основан на использовании явления проникновения специальных жидкостей в полости поверхностных трещин. Эти жидкости (их называют индикаторными или пенетрантами) после очистки поверхности деталей остаются в полостях трещин, остатки пенетрантов легко могут быть обнаружены при облучении детали ультрафиолетовыми лучами или с помощью «проявляющихся» порошков или жидкостей. По способу проявления пенетрантов в капиллярном контроле можно выделить люминесцентный и цветной способы дефектоскопии.
Люминесцентная дефектоскопия. При этом способе на по-
верхность детали наносят пенетранты, способные светиться после облучения ультрафиолетовыми лучами, — люминофоры. В состав люминофора входят: керосин, трансформаторное масло и порошковый дефоктоль.
Керосин, обладая высокой смачивающей способностью, обеспечивает заполнение полости трещины пенетрантом.
Так же как акустический способ, люминесцентная дефектоскопия позволяет выявлять поверхностные дефекты, например, трещины в деталях, изготовленных из различных конструкционных материалов.
Цветная дефектоскопия. Здесь в состав пенетранта наряду с трансформаторным маслом и керосином вводится краситель, например, ярко-красная краска «Судан-3». Обнаружение остатков пенетрантов в трещинах производится с помощью «проявляющих» порошков: талька, мела или силикагеля (SiO2), которые наносятся на контролируемую поверхность детали. При наличии трещины на белом фоне порошка проявляется красный «отпечаток», который позволяет определить место залегания, форму и размеры трещины.
Достоинством капиллярного контроля является его высокая чувствительность. Минимальные размеры обнаруживаемых трещин достигают 1 мкм ширины, 10 мкм глубины и 100 мкм длины.
Неразрушающий контроль течеиспусканием. Этот способ контроля (опрессовка) основан на регистрации утечки жидкостей или газов через сквозные трещины. Такие жидкости или газы называются индикаторными. Опрессовкой контролируют кор-
38
пусные детали (головки и блоки цилиндров), впускные и выпускные коллекторы, радиаторы, ресиверы и др. Утечка индикаторного тела может быть обнаружена по падению давления либо по появлению жидкости вне детали в зоне дефекта.
Вопросы для самоконтроля
1.Определить место в технологическом процессе ремонта машин операции дефектации деталей.
2.Назовите три этапа контрольно-сортировочных работ при ремонте.
3.Определите место технических измерений деталей при дефектации.
4.Сформулируйте физическую сущность, область применения и технические возможности магнитного контроля.
5.Опишите физическую сущность, применение и технологический процесс акустического вида контроля.
6.Охарактеризуйте два способа дефектоскопии в капиллярном контроле, сформулируйте их технические возможности.
2.4.Сборка при ремонте
2.4.1. Основные понятия, термины и определения
Сборка — образование соединений составных частей изделия. Изделие представляет собой предмет или набор предметов производства, подлежащих изготовлению на предприятии.
Установлены следующие виды изделий: детали, сборочные единицы, комплексы, комплекты.
Деталь — изделие, изготовленное из однородного по наименованию и марке материала без применения сборочных операций.
Сборочная единица — изделие, составные части которого подлежат соединению между собой на предприятии-изготовителе сборочными операциями (свинчиванием, сочленением, клепкой, сваркой, пайкой, опрессовкой, развальцовкой, склеиванием, укладкой и т.п.).
Комплекс — два и более специфицированных изделия, не соединенных на предприятии-изготовителе сборочными операциями, но предназначенных для выполнения взаимосвязанных эксплуатационных функций (например, бурильная установка и т.п.).
39
Комплект — два и более изделия, не соединенных на пред- приятии-изготовителе сборочными операциями и представляющих собой набор изделий, имеющих общее эксплуатационное назначение вспомогательного характера, например, комплект запасных частей, комплект инструмента и принадлежностей и т.п.
К неспецифицированным относятся изделия, не имеющие составных частей (детали), а к специфицированным — состоящие из двух и более составных частей (сборочные единицы, комплексы, комплекты).
Вкачестве составных частей собираемого изделия могут быть детали, сборочные единицы (соединения, узлы, агрегаты) и комплектующие изделия.
Впроцессе сборки происходит соединение составных частей изделия по сопрягаемым поверхностям. Соединение при сборке —
сопряжение составных частей изделия или заготовок, определяемое заданными в конструкторской документации их относительным положением и видом связи между ними, лишающей эти части определенного числа степеней свободы. Сопряжение при сборке — относительное положение составных частей изделия при сборке, характеризуемое соприкосновением их поверхностей и (или) зазором между ними, заданными в конструкторской документации. Деталь, имеющая сопряжения с другими деталями, называется сопрягаемой деталью. Она имеет сопрягаемую (сопрягаемые) поверхность (поверхности), образующую (образующие) сопряжения при сборке. Деталь (сборочная единица), с которой начинают сборку изделия, присоединяя к ней детали или другие сборочные единицы, называется базовой деталью (сборочной единицей).
При выполнении сборки должна достигаться необходимая точность сборки изделия, под которой понимается свойство процесса сборки изделия обеспечивать соответствие значений параметров изделия заданным в конструкторской документации. Необходимая точность сборки достигается применением соответствующего метода сборки изделия — совокупности правил достижения заданной точности замыкающего звена размерной цепи при сборке.
Различают следующие методы сборки сборочных единиц и изделий:
–метод полной (абсолютной) взаимозаменяемости;
–метод неполной (ограниченной) взаимозаменяемости;
40
–метод групповой (селективной) сборки;
–метод сборки с регулировкой.
2.4.2. Виды сборки
Под видом сборки изделия понимается категория сборки, выделяемая по одному из ее признаков. Существует большое число видов сборки, которые можно выделить по: объекту сборки; стадии процесса; методу образования соединения; организации производства; перемещению собираемого изделия; механизации и автоматизации процесса; методу обеспечения точности замыкающего звена; последовательности сборки; расположению оси сборки в пространстве; виду сборочного движения; числу одновременно собираемых соединений; способу совмещения осей сопрягаемых поверхностей собираемых компонентов; переналаживаемости процессов сборки; виду теплового воздействия на собираемые компоненты; виду покрытий сопрягаемых поверхностей и веществ, вводимых в зону сопряжения.
По объекту сборки сборка изделия подразделяется на узловую, объектом которой является составная часть изделия (узел), и общую, объектом которой является изделие в целом. Объект сборки — это собираемые в процессе сборки составные части изделия или изделие в целом.
По стадии процесса сборка делится на предварительную, промежуточную и окончательную, а также сборку под сварку, пайку, склеивание. При предварительной сборке производится сборка заготовок, составных частей или изделия в целом, которые в последующем подлежат разборке. При промежуточной сборке выполняется сборка заготовок с целью дальнейшей их совместной обработки. При окончательной сборке осуществляется сборка изделия, после которой не предусмотрена его последующая разборка.
По методу образования соединения сборка подразделяется на слесарную сборку, монтаж, электромонтаж, сварку, пайку, клепку, склеивание. При слесарной сборке производится сборка изделия или его составной части при помощи слесарно-сборочных операций. Монтаж — установка изделия или его составных частей на месте использования. Электромонтаж — монтаж электроизделий или их составных частей, имеющих токоведущие элементы.
41
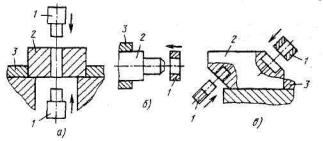
По последовательности сборки сборка подразделяется на по-
следовательную, параллельную и последовательно-параллельную сборку изделия или его составных частей. При последовательной сборке сборочные операции выполняются одна за другой, при
параллельной сборке — одновременно, при параллельно-
последовательной — одна за другой и одновременно.
По расположению оси сборки в пространстве сборка под-
разделяется на вертикальную, горизонтальную и наклонную (рис. 2.15). При вертикальной (см. рис. 2.15, а) и наклонной (см. рис. 2.15, в) сборке подача присоединяемых компонентов на базовый может осуществляться сверху вниз и снизу вверх. Для деталей небольшой массы и размеров наиболее предпочтительной является вертикальная сборка (сверху вниз). Для деталей значительной массы и длины часто целесообразно применение горизонтальной сборки (см. рис. 2.15, б). Применение наклонной сборки обычно обусловлено конструктивными особенностями базового компонента, т.е. наличием сопрягаемых поверхностей, расположенных под углом к его основной базовой поверхности.
а) |
|
б) |
в) |
|
|
|
|
|
|
|
|
|
|
|
|
|
|
|
|
|
|
|
|
|
|
|
|
|
|
Рис. 2.15. Вертикальная (а), горизонтальная (б)
инаклонная (в) сборка:
1 и 2 — присоединяемый и базовый компоненты;
3 — установочное приспособление
Сопряжение и (или) закрепление собираемых компонентов при сборке может обеспечиваться различными видами сборочного движения: прямолинейным, вращательным, винтовым, криволинейным плоским, криволинейным пространственным и комбинированным (например, прямолинейно-вращательным, вращатель- но-криволинейным и др.) (рис. 2.16). При этом сборочные движения могут быть реализованы вследствие: движения присоединяемого компонента; движения базового компонента; движения сбо-
42