
- •1. ОБЩИЕ СВЕДЕНИЯ О САМОЛЕТЕ Ту-154
- •Геометрические данные
- •Массовые данные самолета
- •Центровка самолета
- •Летные данные
- •Взлетные и посадочные данные
- •2. ПЛАНЕР САМОЛЕТА
- •2.2. ЗАЩИТА ПЛАНЕРА ОТ КОРРОЗИИ
- •2.3. ФЮЗЕЛЯЖ
- •Компоновка фюзеляжа
- •Зона герметизации фюзеляжа
- •Конструкция силовых элементов фюзеляжа
- •Шпангоуты
- •Стрингеры
- •Продольные балки
- •Обшивка
- •Фонарь кабины экипажа
- •Окна пассажирских кабин
- •Система дренажа окон пассажирских кабин
- •Входные двери
- •Система запирания входной двери
- •Замки
- •Тяги
- •Механизм управления замками
- •Механизм автоматического стопорения замков
- •Заборник воздуха
- •Система сигнализации
- •Запасная и служебная двери
- •Аварийные выходы
- •Люки багажных помещений
- •Люк заднего технического отсека
- •Полы кабин и багажных помещений
- •2.4. КРЫЛО
- •Центроплан
- •Кессон
- •Лонжероны
- •Стрингеры
- •Нервюры
- •Обшивка
- •Носовая часть центроплана
- •Первый носок
- •Второй носок
- •Хвостовая часть центроплана
- •Крепление центроплана к фюзеляжу
- •Отъемная часть крыла
- •Кессон
- •Носовая часть
- •Хвостовая часть
- •Концевой обтекатель
- •Стык отъемной части крыла с центропланом
- •Гондола главной ноги шасси
- •Закрылки
- •Средняя часть
- •Дефлектор
- •Хвостик закрылка
- •Шторки
- •Предкрылки
- •Интерцепторы
- •Элероны
- •2.5. ХВОСТОВОЕ ОПЕРЕНИЕ
- •Киль
- •Кессон киля
- •Носок киля
- •Хвостовая часть киля
- •Концевой обтекатель киля
- •Руль направления
- •Стабилизатор
- •Центроплан
- •Консоль стабилизатора
- •Обтекатель стабилизатора
- •Руль высоты
- •2.6. ОСОБЕННОСТИ ТЕХНИЧЕСКОГО ОБСЛУЖИВАНИЯ ПЛАНЕРА
- •Глава 3. Управление самолетом Ту-154
- •3.1 ОБЩИЕ СВЕДЕНИЯ
- •Основные данные системы управления
- •3.2. СИСТЕМА УПРАВЛЕНИЯ РУЛЕМ ВЫСОТЫ
- •Колонка управления
- •Тяги
- •Роликовые направляющие
- •Качалки и поводки
- •Дифференциальная качалка
- •Пружинные тяги
- •Герметический вывод
- •Ограничение отклонения руля высоты
- •Полетный загружатель
- •Механизм включения полетного загружателя
- •Электромеханизм триммерного эффекта
- •Следящая тяга
- •3.3. СИСТЕМА УПРАВЛЕНИЯ РУЛЕМ НАПРАВЛЕНИЯ
- •Педали
- •Механизм регулировки педалей
- •Проводка
- •Тяги
- •Направляющие
- •Качалки и поводки
- •Дифференциальная качалка
- •Герметический вывод
- •Механизм триммерного эффекта
- •Полетный загружатель
- •Механизм включения
- •Штурвал
- •Тяги
- •Качалки и поводки
- •Дифференциальная качалка
- •Пружинные тяги
- •Пружинный загружатель
- •Механизм триммерного эффекта
- •Следящая тяга
- •3.5. СИСТЕМА УПРАВЛЕНИЯ ЭЛЕРОНАМИ-ИНТЕРЦЕПТОРАМИ
- •Дифференциальный механизм
- •Проводка
- •Поводки
- •Пружинная тяга
- •Ограничитель отклонения элерона-интерцептора
- •3.6. СИСТЕМА УПРАВЛЕНИЯ СРЕДНИМИ ИНТЕРЦЕПТОРАМИ
- •Рукоятка управления
- •Проводка управления
- •Тросы
- •Ролики
- •Герметический вывод троса
- •Жесткая проводка
- •3.7. СИСТЕМА УПРАВЛЕНИЯ СТАБИЛИЗАТОРОМ
- •Подъемник стабилизатора
- •Управление стабилизатором
- •3.8. СИСТЕМА УПРАВЛЕНИЯ ЗАКРЫЛКАМИ
- •Система перемещения закрылков СПЗ-1А
- •Трансмиссия закрылков
- •Валы
- •Опоры
- •Герметические выводы
- •Редукторы
- •Подъемники закрылков
- •3.9. СИСТЕМА УПРАВЛЕНИЯ ПРЕДКРЫЛКАМИ
- •Трансмиссия предкрылков
- •Валы
- •Промежуточные опоры,
- •Герметические выводы
- •Редукторы
- •Механизм концевых выключателей МКВ-36
- •Винтовые подъемники предкрылков
- •Система управления и сигнализации
- •Замер люфтов по рулю направления и элеронам
- •Глава 4. Шасси самолета Ту-154
- •4.1. ОБЩИЕ СВЕДЕНИЯ О ШАССИ САМОЛЕТА
- •Основные данные
- •4.2. НАГРУЗКА НА ШАССИ
- •4.3. ПЕРЕДНЯЯ НОГА ШАССИ
- •Амортизационная стойка
- •Зарядный клапан
- •Цилиндр уборки и выпуска шасси
- •Установка оси колес
- •Скалывающийся подкос
- •Механизм распора
- •Замок подвески передней ноги
- •Механизм управления створками люка ниши передней ноги
- •4.4.ГЛАВНЫЕ НОГИ ШАССИ
- •Амортизационная стойка с однокамерным амортизатором
- •Амортизационная стойка с двухкамерным амортизатором
- •Подкос-цилиндр
- •Стабилизирующий амортизатор
- •Масляный зарядный клапан
- •Тележки главных ног шасси
- •Механизм управления створками люков главных ног
- •Ведущий и ведомый редукторы
- •4.5. СИГНАЛИЗАЦИЯ ПОЛОЖЕНИЯ НОГ ШАССИ
- •5.2. СИСТЕМА ДО ПОТРЕБИТЕЛЕЙ ПЕРВОЙ ГИДРАВЛИЧЕСКОЙ СИСТЕМЫ
- •Разъемные клапаны
- •Дроссель постоянного расхода НУ-5810-40М1
- •Обратный клапан ОК6А
- •Холодильник 5601.060
- •Сливной фильтр 5810.020
- •Гаситель пульсаций 5803.040
- •Гидроаккумулятор 5803.030
- •Сигнализатор падения давления МСТ-100
- •Электрический дистанционный манометр ДИМ2-240
- •Дроссель Н5810.820
- •Панель бортового обслуживания первой гидросистемы 5606.410
- •Работа системы до потребителей первой гидросистемы.
- •5.3. СИСТЕМА ДО ПОТРЕБИТЕЛЕЙ ВТОРОЙ ГИДРАВЛИЧЕСКЮИ СИСТЕМЫ
- •Панель бортового обслуживания второй гидросистемы 5606.410
- •5.4. СИСТЕМА ДО ПОТРЕБИТЕЛЕЙ ТРЕТЬЕЙ ГИДРАВЛИЧЕСКОЙ СИСТЕМЫ
- •Панель бортового обслуживания третьей гидросистемы 5606.400
- •5.5. ГИДРОСИСТЕМА ОСНОВНОГО ТОРМОЖЕНИЯ КОЛЕС ШАССИ
- •Обратный клапан ОК8А
- •5.6. ГИДРОСИСТЕМА АВАРИЙНОГО ТОРМОЖЕНИЯ КОЛЕС ШАССИ
- •Обратный клапан ОК6А
- •Сигнализатор падения давления ЭС-200
- •5.7. ГИДРОСИСТЕМА ШАССИ (ОСНОВНОЕ УПРАВЛЕНИЕ)
- •Цилиндр замка подвески главной ноги шасси
- •Цилиндр-подкос
- •Золотниковый распределитель 5810.000
- •Цилиндр створок
- •Цилиндр механизма распора
- •Клапан отключения 5810.050
- •Обратные клапаны ОК10А, ОК14А, ОК6А
- •Гаситель пульсаций
- •5.8. ГИДРОСИСТЕМА АВАРИЙНОГО ВЫПУСКА ШАССИ
- •Кран аварийного выпуска 5855.000
- •Пружинная тяга
- •Пружинный цилиндр
- •5.10. ГИДРОСИСТЕМА УПРАВЛЕНИЯ ВНУТРЕННИМИ ИНТЕРЦЕПТОРАМИ
- •Работа на прямом ходе
- •Гидравлический цилиндр 5801.100
- •Обратный клапан ОК12А
- •5.11. ГИДРОСИСТЕМА УПРАВЛЕНИЯ СРЕДНИМИ ИНТЕРЦЕПТОРАМИ
- •Обратные клапаны ОК6А и ОК8А
- •Редуктор ГА-213
- •5.13. ГИДРОСИСТЕМА УПРАВЛЕНИЯ ЗАКРЫЛКАМИ
- •5.14. СИСТЕМА НАДДУВА И ДРЕНАЖА ГИДРОБАКОВ
- •Обратный клапан 5810.270
- •Воздушный баллон 5810.300
- •Дренажный бак 5602.350
- •Регулятор давления 5810.180
- •Предохранительный клапан 5810.250
- •Клапан сброса давления наддува 3501с51
- •Запорный кран 219К
- •Бортовой зарядный штуцер 3509с50
- •5.15. ОСОБЕННОСТИ ТЕХНИЧЕСКОГО ОБСЛУЖИВАНИЯ ГИДРОСИСТЕМЫ
позволит рабочей жидкости открыть клапаны 52 и за полнить через отверстия л полость Ш, а через отверстия у и р полость К. Поршень 54 сожмет пружину 57 и поднимется в крайнее верхнее положение, а плавающий поршень 59 начнет опускаться вниз и будет продолжать сжимать азот в полости М.
Одновременно повышенное избыточное давление будет проталкивать рабочую жидкость через кольцевой зазор д в полость Е, а затем и в полость Д. Так будет продолжаться до тех пор, пока не будет поглощена вся энергия удара и давления в верхней и нижней камере не стабилизируются.
При втором этапе работы во время обжатия амортизатора на амортизационную стойку действуют усилия вследствие сжатия азота в верхней и нижней пневматических камерах полостей Д и М и в результате дросселирования жидкости через кольцевой зазор д и отверстия р и у в клапанах 52.
III. Обжатие после удара или медленное обжатие стойки.
Ход штока 23 (см. рис. 4.25) при ударе после посадки и поглощения энергии должен прекратиться, а давление во всех полостях должно выравниться.
Пружина 36 переместит поршень 35 вверх до упора, а пружина 53 — поршень 54 в крайнее нижнее положение. В этом случае полость И через отверстие г, полость Ж и отверстия е и а будет сообщаться с полостью Д, а с другой стороны через отверстие у с полостью К. Рабочая жидкость при этом будет перетекать из одной полости в другую без дросселирования, что дает хорошую амортизацию самолета три разбеге, пробеге, рулении и наезде колес на неровную поверхность аэродрома, так как работает только пневматическая амортизация.
Такая же картина наблюдается и при медленном обжатии стойки, потому что исключается дросселирование рабочей жидкости при ее перетекании из полости И в полости К и Д. Усилие в этом случае определяется только степенью сжатия азота.
Работа амортизатора при обратном ходе штока.
I. Первый этап — обратный ход.
После поглощения энергии удара азот начинает выталкивать шток 23 (см. рис. 4.25). Тарелка клапана 40 под воздействием пружины 41 закроется и масло АМГ-10 будет перетекать из полости Д в полость Е, а затем в полость И через отверстие б, полость Я, дроссельное отверстие в в поршне 35 и кольцевой зазор д. Из полости К в это время масло перетекает в полость И через дроссельные отверстия р клапанов 52.
Перетекание происходит до момента, пока грибок иглы 24 не упрется в буртик поршня 35.
II . Второй этап — конец обратного хода.
В конце обратного хода штока 23 (см. рис. 4.25) грибок иглы упрется в буртик поршня 35 и отверстия е будут перекрыты. Игла 24 потянет поршень 35 вниз, а жидкость из полости Ж будет поступать через кольцевой зазор с в полость И, а из полости Д — в полость Е через отверстие б, полость П и дроссельное отверстие в.
Такое дросселирование обеспечивает плавный безударный подход штока к упорной втулке 22 (см. рис. 4.24).
Подкос-цилиндр уборки и выпуска главных ног — гидравлический механизм двустороннего действия. Это силовой и кинематический элемент, который служит для выпуска, уборки и удержания в выпущенном положении основных ног шасси на стоянке, а также при передвижении самолета по аэродрому.
При выпущенном положении главной ноги шток убран и стоит на цанговом замке. Стабилизирующий амортизатор — это пневматическая пружина, работающая на растяжение и сжатие. Он служит для установки тележки в определенное положение после выпуска ноги и гашения колебания тележки при движении самолета по неровной поверхности аэродрома, а также работает как жесткая тяга в механизме опрокидывания
тележки.
166
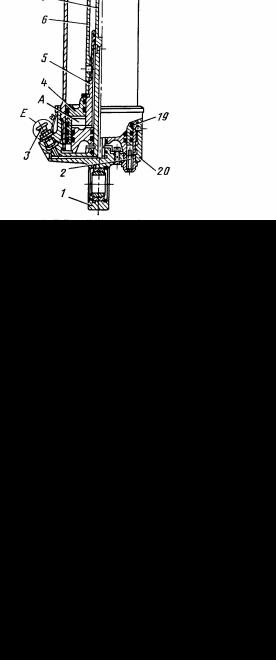
Одним концом амортизатор крепится к уху 19 на балке 3 (см. рис. 4.28), а другим
— к качалке 1 (см. рис. 4.20).
Стабилизирующий амортизатор состоит из следующих узлов и деталей: цилиндра 8 (рис 4.26) с головкой 1 и иглой 7, штока 13 с ухом 14, внутреннего штока 5 с распорной втулкой 6, поршня 4, буксы 11 с уплотнительными кольцами 17, зарядного клапана 10, масляных зарядных клапанов 3, указателя 2 и других деталей. Указатель имеет гнездо 20 и пружину.
Рис. 4.26. Стабилизирующий амортизатор:
1—головка; 2—указатель; 3— масляный зарядный клапан; 4—поршень; 5—внутренний шток; 6—распорная втулка; 7—игла; 3—цилиндр; 9, 18— гайки; 10—зарядный клапан; 11—буксы; 12—гайка; 13— шток; 14—ухо; 15—штифт; 16, 17, 19—уплотнительные кольца; 20—гнездо; 21—направляющая втулка; 22—пружина; 23—клапан; 24—кольцо; 25—шайба; 26—корпус; 27— колпачок; А, Г—верхняя и нижняя масляные полости; Б, В—
верхняя и нижняя пневматические полости; Д— полость
167
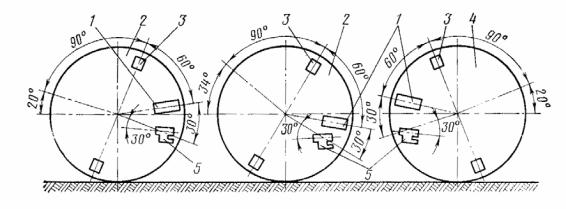
Основными силовыми и кинематическими элементами являются цилиндр и штоки амортизатора.
При обжатии амортизатора шток двигателя вниз, уменьшая объемы полостей Б и Д, т. е. совершает работу, увеличивая степень сжатия азота до величиныП1 =1,52+−00,,0402 . Полный
ход сжатия стабилизирующего амортизатора равен 183 мм.
При растяжении амортизатора шток выходит из цилиндра и тянет за собой через распорную втулку внутренний шток и плунжер. В этом случае уменьшается объем полости В, но объем масляной полости А остается неизменным.
Амортизатор при растяжении тоже совершает работу, увеличивая степень сжатия до величины П2 =1,14+0,02 . Полный ход штока при растяжении равен 68 мм.
Давление в полостях В и Б выравнивается при перетекании воздуха через отверстие в штоке.
Работа, совершаемая амортизатором, затрачивается на стабилизацию положения тележки путем прижатия колес к земле при движении самолета по неровной поверхности аэродрома.
Масляный зарядный клапан предназначен для набивки полостей А и Г смазкой ЦИАТИМ-203 по мере ее расходования. Смазка в полость Г поступает сразу через отверстие в цилиндре, а в полость А — по сверлениям в головке 1, игле 7, через кольцевую полость между иглой и внутренним штоком 5, а также по радиальному сверлению в нем.
Масляный зарядный клапан (см. рис. 4.26, узел Е) состоит из корпуса 26 со штуцером, клапана 23 с привулканизированной резиновой шайбой 25, направляющей втулки 21, возвратной пружины 22, резинового уплотнительного кольца 24 и предохранительного колпачка 27.
Работа клапана заключается в следующем. При подаче смазки через штуцер корпуса клапан 23 сожмет пружину и смазка будет заполнять полости А или Г. Когда подача смазки прекращается, пружина распрямится и прижмет клапан к седлу корпуса.
Тележки главных ног шасси по конструкции одинаковы. Различие тележек связано лишь с установкой дисковых тормозов колес КТ-141А относительно их осей и применением двух сборок колес (КТ-141А000-1; КТ-141А000-2), которые являются по отношению друг к другу отраженными видами.
Рис. 4.27. Положение правых (внешних) колес КТ-141А000-1 и КТ-141А000-2 правой главной ноги (вид изнутри тележки):
1—антиюзовый автомат типа УА-51А; 2—колеса КТ-141А000-1; 3—воздушный клапан; 4—колесо КТ-141А000-2; 5—челночный клапан
На рис. 4.27 показано положение сборок колес и их дисковых тормозов относительно осей для правых (внешних) колес правой тележки.
Положение левых (внутренних) колес правой тележки является отраженным видом правых внешних колес этой тележки.
168
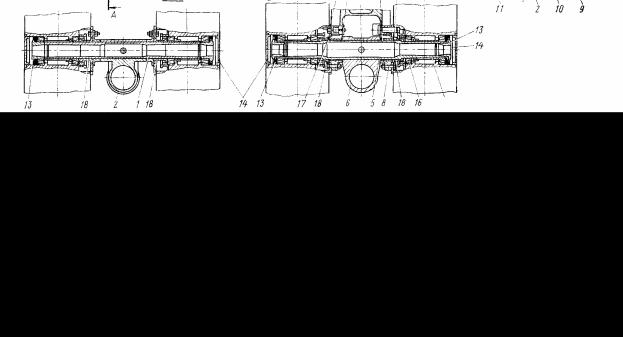
Тележки служат для передвижения самолета по аэродрому и позволяют частично с помощью пневматиков поглощать энергию удара.
Основными узлами и деталями тележек (рис. 4.28) являются балка 3, шесть тормозных колес КТ-141А 7, центральная 5 и две крайние 1 оси, гайка 13, болты 8, 10, 12.
Балка представляет собой пустотелую трубу. На концах балки приварены головки 2, к которым болтами 10 крепятся оси, а к фланцам головок болтами 8 — колеса К.Т- 141А. На балке по центру приварено основание 6. В основании болтом 12 крепится центральная ось.
Средняя пара колес болтами 8 крепится к фланцам на головке штока 4. Таким образом осуществляется шарнирная подвеска тележки колес. Спереди перед основанием 6 приварена проушина 19 крепления стабилизирующего амортизатора. На головках 2 имеются проушины 9 для установки домкратов при замене колес и буксировки самолета по аэродрому. На балке устанавливают хомуты для крепления маслопроводов, идущих к тормозам колес. К заднему хомуту прикреплена метелка заземления 11, отводящая заряды статического электричества на землю.
Рис. 4.28. Тележка шасси (показана правая тележка шасси):
1, 5—оси; 2—головка балки; 3—балка; 4—шток амортизационной стойки; 6— основание; 7—колесо КТ-141А; 8, 10, 12—болты; 9, 19—проушины; 11—метелка заземления; 13—гайка; 14, 17—шайбы; 15, 18—распорные втулки; 16—роликовый подшипник; В, Г, Д, Е—зазоры
В убранном положении балка 3 упирается в головку 58 штока (см. рис. 4.22). Колеса КТ-141 служат для передвижения самолета по земле, торможения при
посадке и рулении самолета.
Каждое колесо состоит из следующих основных деталей (рис. 4.29); барабана 19 со съемной ребордой 22 и стопорным кольцом 23, пневматика 20, дискового тормоза с антиюзовым автоматом типа УА-51А 10 и челночным клапаном 11, распорной втулки 38, роликовых подшипников 37 и обойм 12, 35.
Барабан колеса изготовлен из магниевого сплава.
Обод барабана имеет два борта — один съемный, называемый ребордой, а другой несъемный.
Реборда служит для упрощения монтажа и демонтажа пневматика. На барабане она удерживается стопорным кольцом. Барабан колеса устанавливается на оси на двух
169
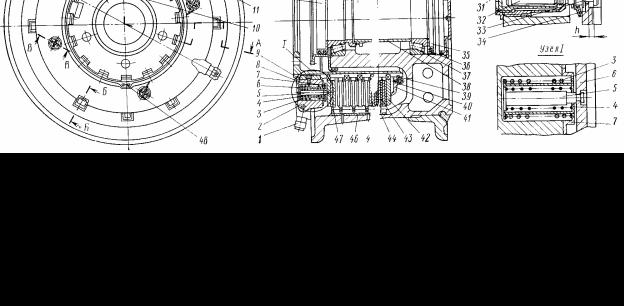
конических радиально-упорных подшипниках, которые воспринимают большие осевые нагрузки. Внутренние кольца подшипников надеваются на оси колес, а наружные — размещаются в барабане.
Рис. 4.29. Тормозное колесо КТ-141А000-1 (колесо КТ-141А000-2 — отраженный вид): 1—клапан; 2—блок цилиндров; 3, 4—пружины; 5—стержень; 6—стакан; 7, 29—крышки; 8, 23, 28, 35—стопорные кольца; 9—стопорное полукольцо; 10—антиюзовый автомат; 11—челночный клапан; 12, 35—обоймы; 13, 36—манжеты; 14—заглушка; 15—шестерня; 16, 40—кольца; 17-гильза; 18—поршень; 19— барабан; 20—шина; 21—вентиль; 42— реборда; 23—стопорное кольцо; 24—указатель износа; 25—шайба; 26—гайка; 27— колпачок; 30—цанга; 31—режим; 32—упор; 33—специальный винт; 34—тарельчатые пружины; ,37—роликовый подшипник; 38—распорная втулка; 41—фланец; 42—опорный диск; 43—корпус писка; 44—металлокерамический диск; 45—промежуточный диск; 46— направляющая; 47—нажимной диск; 48—винт; Б—суммарный зазор после растормаживания; В—направление вращения колеса; Г—размер, указывающий на максимальное обжатие пружины узла растормаживания; h—зазор между тарельчатой пружиной и нажимным диском
Дисковый тормоз установлен во внутренней полости обода барабана и имеет с ним сцепление посредством металлокерамических дисков 44, которые установлены в направляющих обода барабана, поэтому при вращении колеса металлокерамические диски тоже вращаются.
Между несъемной и съемной 22 ребордами барабана находится пневматик с вентилем 21. Конец вентиля в гнезде закреплен гайкой 26 с шайбой 25 и защищен от загрязнения предохранительным колпачком 27.
Вращение колес осуществляется на роликовых подшипниках 37, наружные кольца которых запрессованы в гнездо ступиц барабанов.
Для обеспечения эксплуатационного зазора в подшипниках установлена распорная втулка 38. Подшипники защищены от засорения и вытекания из них смазки обоймами 12, 35 с манжетами 13, 36. Кроме этого, с внешних сторон колес для этих целей установлена крышка 29 с резиновыми стопорными кольцами 28.
Для передачи вращения колеса антиюзовому автомату 10 на ступице барабана имеется шестерня 15.
Дисковый тормоз состоит из корпуса 43, фланца 41, блока цилиндров 2, трех промежуточных дисков 45, четырех металлокерамических дисков 44, опорного диска 42, нажимного диска 47, двенадцати рабочих цилиндров (см. сеч. Б—Б), восьми узлов
170
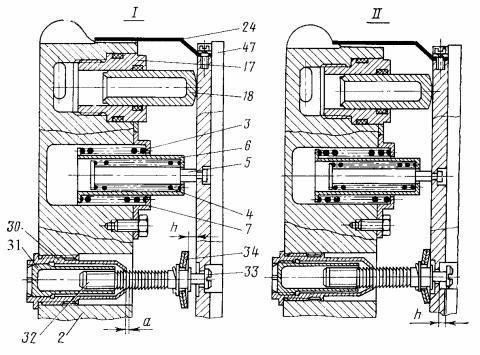
растормаживания (см. узел I), четырех регуляторов зазора (см. сеч. В—В) и других деталей.
Металлокерамические диски установлены между промежуточными дисками. Фланец удерживается от смещения вдоль оси корпуса 43 стопорным кольцом 39 и
кольцом 40, который крепится к фланцу винтом.
Рис. 4.30. Схема работы гидравлического дискового тормоза (номера позиций соответствуют рис. 4.29):
1—положение деталей тормозного диска при полном износе дисков (заторможенное состояние); 11—положение нажимного диска при полном износе металлокерамических дисков (расторможенное состояние); а—расстояние от торца цанги до ближайшего гребня разжима
Нажимной диск соединен с блоком цилиндров через узлы растормаживания (см. узел I) и регуляторы зазора (см. сеч. В—В).
Блок цилиндров крепится к корпусу двумя стопорными полукольцами 9 и кольцом 8 с помощью винтов 48. В блок цилиндров ввернуты гильзы 17 с уплотнительными кольцами, соединенные между собой кольцевым каналом.
Узлы растормаживания и регуляторов зазоров размещены в колодцах блока цилиндров.
Узел растормаживания состоит из стержня 5, пружин 3, 4, стакана 6, крышки 7. Он предназначен для возврата нажимного диска 47 в исходное положение при растормаживании колеса.
Регулятор зазора состоит из упора 32, разжима 31, цанги 30, тарельчатых пружин 34, специального винта 33 и других деталей крепления.
Тарельчатые пружины предохраняют цангу и упор от поломки при обратном ударе во время растормаживания диска. Специальный винт 33 крепит тарельчатые пружины на разжиме и позволяет регулировать зазор h между дисками.
Чтобы подключить дисковый тормоз к гидравлической системе, имеется челночный клапан 11.
Замер давления и прокачка системы тормозов для удаления воздушных полостей производится через клапан 1.
Для контроля за износом дисков имеется указатель износа 24, закрепленный винтом на нажимном диске.
171
Антиюзовый автомат УА-51А прямого действия. Шестерня автомата входит в зацепления с шестерней 15 барабана. Для защиты шестеренчатого привода от засорения продуктами износа дисков имеются кольца 16.
Работа дискового тормоза. Подведенное к блоку цилиндров масло по сверлениям в блоке 2 (рис. 4.30) поступает к поршням 18 и они с нажимным диском 47 переместятся в осевом направлении, устраняя начальный зазор между промежуточными и металлокерамическими дисками.
Пакет дисков сжимается и между дисками возникают силы трения, создающие тормозной момент. При этом пружины 3, 4 узла растормаживания сжимаются и после устранения зазора к нажимной диск переместит упор 32 относительно цанги 30.
По мере износа фрикционных пар нажимной диск относительно блока цилиндров перемещается на величину, равную величине износа.
При сбросе давления пружины перемещают диск 47 и поршни на величину к (зазор между тарельчатыми пружинами 34 и нажимным диском 47), а также на величину а (расстояние от торца цанги до ближайшего гребня упора).
После сброса давления все узлы займут положения, указанные на рис. 4.29 или на рис. 4.30. Так автоматически поддерживается постоянный зазор в пределах h + а между дисками и поршнями.
Если тормозной момент будет больше крутящего момента колеса, то колесо будет давать юз. В этом случае в работу вступит антиюзовый автомат У4А51А, который перекроет линию подачи масла в блок цилиндров и соединит линию тормозов с гидробаком. Колесо, имеющее юз, растормозится.
Тормозные колеса позволяют осуществлять опробование двигателей на стоянке без колодок под колесами.
172
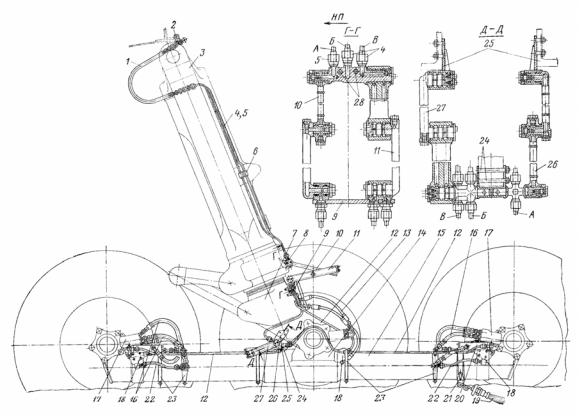
Трубопроводы системы торможения колес, расположенные на главной ноге.
Трубопроводы подачи масла к тормозам колес (рис. 4.31) размещены на стойках и балках главных ног шасси. Они крепятся к элементам шасси с помощью рамок. Верхняя шарнирная рамка служит для выбора хода штока амортизационной стойки при ее обжатии и разжатии, а нижняя — для выбора хода при качании тележки относительно центральной оси.
Верхние звенья 10 шарнирной рамки крепятся к цилиндру-траверсе при помощи двух болтов 28, а нижние 11 — к головке штока 7 кронштейном 9.
Нижние звенья 26 рамки крепятся к прилизу на балке 15, а верхние 27 — к кронштейну 25 на головке штока.
Все звенья рамок имеют сверления, по которым масло поступает в трубопроводы и шланги. Причем имеются две магистрали трубопроводов 4 — трубопроводы основного торможения и слива, а также третья — трубопроводы 5 аварийного торможения.
Замок подвески главных ног. Замок (рис. 4.32) запирает и удерживает ногу шасси в убранном положении и обеспечивает очередность работы агрегатов гидросистемы. Каждый замок укреплен болтами на корпусах редукторов механизмов управления задними створками люков.
Замок состоит из механической и гидравлической частей. В механическую часть замка входят детали, смонтированные в корпусе замка 8, а в гидравлическую — золотниковый цилиндр, служащий для нормального открытия замка, и поршневой — для аварийного. Оба цилиндра смонтированы в одном корпусе, который закреплен на корпусе замка болтами 9.
Рис. 4.31. Трубопроводы системы торможения колес на главной ноге шасси:
1, 13, 16—шланги; 2—штуцер; 3—амортизационная стойка; 4, 5, 12, 22—трубопроводы; 6—скоба крепления; 7—головка штока; 8, 9, 24, 25—кронштейны; 10, 11, 26, 27—звенья; 14—основание балки; 15— балка тележки; 17—антиюзовый автомат УА-51А; 18—чел- ночный клапан; 19—метелка заземления; 20—модулятор ГА-121-2; 21, 23-хомуты; 24, 28—болты; А—линия аварийного торможения; Б—линия слива; В—линия основного торможения
173