
- •BUSINESSES IN THE BOOK
- •Preface
- •Brief Contents
- •CONTENTS
- •Why Study Strategy?
- •Why Economics?
- •The Need for Principles
- •So What’s the Problem?
- •Firms or Markets?
- •A Framework for Strategy
- •Boundaries of the Firm
- •Market and Competitive Analysis
- •Positioning and Dynamics
- •Internal Organization
- •The Book
- •Endnotes
- •Costs
- •Cost Functions
- •Total Cost Functions
- •Fixed and Variable Costs
- •Average and Marginal Cost Functions
- •The Importance of the Time Period: Long-Run versus Short-Run Cost Functions
- •Sunk versus Avoidable Costs
- •Economic Costs and Profitability
- •Economic versus Accounting Costs
- •Economic Profit versus Accounting Profit
- •Demand and Revenues
- •Demand Curve
- •The Price Elasticity of Demand
- •Brand-Level versus Industry-Level Elasticities
- •Total Revenue and Marginal Revenue Functions
- •Theory of the Firm: Pricing and Output Decisions
- •Perfect Competition
- •Game Theory
- •Games in Matrix Form and the Concept of Nash Equilibrium
- •Game Trees and Subgame Perfection
- •Chapter Summary
- •Questions
- •Endnotes
- •Doing Business in 1840
- •Transportation
- •Communications
- •Finance
- •Production Technology
- •Government
- •Doing Business in 1910
- •Business Conditions in 1910: A “Modern” Infrastructure
- •Production Technology
- •Transportation
- •Communications
- •Finance
- •Government
- •Doing Business Today
- •Modern Infrastructure
- •Transportation
- •Communications
- •Finance
- •Production Technology
- •Government
- •Infrastructure in Emerging Markets
- •Three Different Worlds: Consistent Principles, Changing Conditions, and Adaptive Strategies
- •Chapter Summary
- •Questions
- •Endnotes
- •Definitions
- •Definition of Economies of Scale
- •Definition of Economies of Scope
- •Economies of Scale Due to Spreading of Product-Specific Fixed Costs
- •Economies of Scale Due to Trade-offs among Alternative Technologies
- •“The Division of Labor Is Limited by the Extent of the Market”
- •Special Sources of Economies of Scale and Scope
- •Density
- •Purchasing
- •Advertising
- •Costs of Sending Messages per Potential Consumer
- •Advertising Reach and Umbrella Branding
- •Research and Development
- •Physical Properties of Production
- •Inventories
- •Complementarities and Strategic Fit
- •Sources of Diseconomies of Scale
- •Labor Costs and Firm Size
- •Spreading Specialized Resources Too Thin
- •Bureaucracy
- •Economies of Scale: A Summary
- •The Learning Curve
- •The Concept of the Learning Curve
- •Expanding Output to Obtain a Cost Advantage
- •Learning and Organization
- •The Learning Curve versus Economies of Scale
- •Diversification
- •Why Do Firms Diversify?
- •Efficiency-Based Reasons for Diversification
- •Scope Economies
- •Internal Capital Markets
- •Problematic Justifications for Diversification
- •Diversifying Shareholders’ Portfolios
- •Identifying Undervalued Firms
- •Reasons Not to Diversify
- •Managerial Reasons for Diversification
- •Benefits to Managers from Acquisitions
- •Problems of Corporate Governance
- •The Market for Corporate Control and Recent Changes in Corporate Governance
- •Performance of Diversified Firms
- •Chapter Summary
- •Questions
- •Endnotes
- •Make versus Buy
- •Upstream, Downstream
- •Defining Boundaries
- •Some Make-or-Buy Fallacies
- •Avoiding Peak Prices
- •Tying Up Channels: Vertical Foreclosure
- •Reasons to “Buy”
- •Exploiting Scale and Learning Economies
- •Bureaucracy Effects: Avoiding Agency and Influence Costs
- •Agency Costs
- •Influence Costs
- •Organizational Design
- •Reasons to “Make”
- •The Economic Foundations of Contracts
- •Complete versus Incomplete Contracting
- •Bounded Rationality
- •Difficulties Specifying or Measuring Performance
- •Asymmetric Information
- •The Role of Contract Law
- •Coordination of Production Flows through the Vertical Chain
- •Leakage of Private Information
- •Transactions Costs
- •Relationship-Specific Assets
- •Forms of Asset Specificity
- •The Fundamental Transformation
- •Rents and Quasi-Rents
- •The Holdup Problem
- •Holdup and Ex Post Cooperation
- •The Holdup Problem and Transactions Costs
- •Contract Negotiation and Renegotiation
- •Investments to Improve Ex Post Bargaining Positions
- •Distrust
- •Reduced Investment
- •Recap: From Relationship-Specific Assets to Transactions Costs
- •Chapter Summary
- •Questions
- •Endnotes
- •What Does It Mean to Be “Integrated?”
- •The Property Rights Theory of the Firm
- •Alternative Forms of Organizing Transactions
- •Governance
- •Delegation
- •Recapping PRT
- •Path Dependence
- •Making the Integration Decision
- •Technical Efficiency versus Agency Efficiency
- •The Technical Efficiency/Agency Efficiency Trade-off
- •Real-World Evidence
- •Double Marginalization: A Final Integration Consideration
- •Alternatives to Vertical Integration
- •Tapered Integration: Make and Buy
- •Franchising
- •Strategic Alliances and Joint Ventures
- •Implicit Contracts and Long-Term Relationships
- •Business Groups
- •Keiretsu
- •Chaebol
- •Business Groups in Emerging Markets
- •Chapter Summary
- •Questions
- •Endnotes
- •Competitor Identification and Market Definition
- •The Basics of Competitor Identification
- •Example 5.1 The SSNIP in Action: Defining Hospital Markets
- •Putting Competitor Identification into Practice
- •Empirical Approaches to Competitor Identification
- •Geographic Competitor Identification
- •Measuring Market Structure
- •Market Structure and Competition
- •Perfect Competition
- •Many Sellers
- •Homogeneous Products
- •Excess Capacity
- •Monopoly
- •Monopolistic Competition
- •Demand for Differentiated Goods
- •Entry into Monopolistically Competitive Markets
- •Oligopoly
- •Cournot Quantity Competition
- •The Revenue Destruction Effect
- •Cournot’s Model in Practice
- •Bertrand Price Competition
- •Why Are Cournot and Bertrand Different?
- •Evidence on Market Structure and Performance
- •Price and Concentration
- •Chapter Summary
- •Questions
- •Endnotes
- •6: Entry and Exit
- •Some Facts about Entry and Exit
- •Entry and Exit Decisions: Basic Concepts
- •Barriers to Entry
- •Bain’s Typology of Entry Conditions
- •Analyzing Entry Conditions: The Asymmetry Requirement
- •Structural Entry Barriers
- •Control of Essential Resources
- •Economies of Scale and Scope
- •Marketing Advantages of Incumbency
- •Barriers to Exit
- •Entry-Deterring Strategies
- •Limit Pricing
- •Is Strategic Limit Pricing Rational?
- •Predatory Pricing
- •The Chain-Store Paradox
- •Rescuing Limit Pricing and Predation: The Importance of Uncertainty and Reputation
- •Wars of Attrition
- •Predation and Capacity Expansion
- •Strategic Bundling
- •“Judo Economics”
- •Evidence on Entry-Deterring Behavior
- •Contestable Markets
- •An Entry Deterrence Checklist
- •Entering a New Market
- •Preemptive Entry and Rent Seeking Behavior
- •Chapter Summary
- •Questions
- •Endnotes
- •Microdynamics
- •Strategic Commitment
- •Strategic Substitutes and Strategic Complements
- •The Strategic Effect of Commitments
- •Tough and Soft Commitments
- •A Taxonomy of Commitment Strategies
- •The Informational Benefits of Flexibility
- •Real Options
- •Competitive Discipline
- •Dynamic Pricing Rivalry and Tit-for-Tat Pricing
- •Why Is Tit-for-Tat So Compelling?
- •Coordinating on the Right Price
- •Impediments to Coordination
- •The Misread Problem
- •Lumpiness of Orders
- •Information about the Sales Transaction
- •Volatility of Demand Conditions
- •Facilitating Practices
- •Price Leadership
- •Advance Announcement of Price Changes
- •Most Favored Customer Clauses
- •Uniform Delivered Prices
- •Where Does Market Structure Come From?
- •Sutton’s Endogenous Sunk Costs
- •Innovation and Market Evolution
- •Learning and Industry Dynamics
- •Chapter Summary
- •Questions
- •Endnotes
- •8: Industry Analysis
- •Performing a Five-Forces Analysis
- •Internal Rivalry
- •Entry
- •Substitutes and Complements
- •Supplier Power and Buyer Power
- •Strategies for Coping with the Five Forces
- •Coopetition and the Value Net
- •Applying the Five Forces: Some Industry Analyses
- •Chicago Hospital Markets Then and Now
- •Market Definition
- •Internal Rivalry
- •Entry
- •Substitutes and Complements
- •Supplier Power
- •Buyer Power
- •Commercial Airframe Manufacturing
- •Market Definition
- •Internal Rivalry
- •Barriers to Entry
- •Substitutes and Complements
- •Supplier Power
- •Buyer Power
- •Professional Sports
- •Market Definition
- •Internal Rivalry
- •Entry
- •Substitutes and Complements
- •Supplier Power
- •Buyer Power
- •Conclusion
- •Professional Search Firms
- •Market Definition
- •Internal Rivalry
- •Entry
- •Substitutes and Complements
- •Supplier Power
- •Buyer Power
- •Conclusion
- •Chapter Summary
- •Questions
- •Endnotes
- •Competitive Advantage Defined
- •Maximum Willingness-to-Pay and Consumer Surplus
- •From Maximum Willingness-to-Pay to Consumer Surplus
- •Value-Created
- •Value Creation and “Win–Win” Business Opportunities
- •Value Creation and Competitive Advantage
- •Analyzing Value Creation
- •Value Creation and the Value Chain
- •Value Creation, Resources, and Capabilities
- •Generic Strategies
- •The Strategic Logic of Cost Leadership
- •The Strategic Logic of Benefit Leadership
- •Extracting Profits from Cost and Benefit Advantage
- •Comparing Cost and Benefit Advantages
- •“Stuck in the Middle”
- •Diagnosing Cost and Benefit Drivers
- •Cost Drivers
- •Cost Drivers Related to Firm Size, Scope, and Cumulative Experience
- •Cost Drivers Independent of Firm Size, Scope, or Cumulative Experience
- •Cost Drivers Related to Organization of the Transactions
- •Benefit Drivers
- •Methods for Estimating and Characterizing Costs and Perceived Benefits
- •Estimating Costs
- •Estimating Benefits
- •Strategic Positioning: Broad Coverage versus Focus Strategies
- •Segmenting an Industry
- •Broad Coverage Strategies
- •Focus Strategies
- •Chapter Summary
- •Questions
- •Endnotes
- •The “Shopping Problem”
- •Unraveling
- •Alternatives to Disclosure
- •Nonprofit Firms
- •Report Cards
- •Multitasking: Teaching to the Test
- •What to Measure
- •Risk Adjustment
- •Presenting Report Card Results
- •Gaming Report Cards
- •The Certifier Market
- •Certification Bias
- •Matchmaking
- •When Sellers Search for Buyers
- •Chapter Summary
- •Questions
- •Endnotes
- •Market Structure and Threats to Sustainability
- •Threats to Sustainability in Competitive and Monopolistically Competitive Markets
- •Threats to Sustainability under All Market Structures
- •Evidence: The Persistence of Profitability
- •The Resource-Based Theory of the Firm
- •Imperfect Mobility and Cospecialization
- •Isolating Mechanisms
- •Impediments to Imitation
- •Legal Restrictions
- •Superior Access to Inputs or Customers
- •The Winner’s Curse
- •Market Size and Scale Economies
- •Intangible Barriers to Imitation
- •Causal Ambiguity
- •Dependence on Historical Circumstances
- •Social Complexity
- •Early-Mover Advantages
- •Learning Curve
- •Reputation and Buyer Uncertainty
- •Buyer Switching Costs
- •Network Effects
- •Networks and Standards
- •Competing “For the Market” versus “In the Market”
- •Knocking off a Dominant Standard
- •Early-Mover Disadvantages
- •Imperfect Imitability and Industry Equilibrium
- •Creating Advantage and Creative Destruction
- •Disruptive Technologies
- •The Productivity Effect
- •The Sunk Cost Effect
- •The Replacement Effect
- •The Efficiency Effect
- •Disruption versus the Resource-Based Theory of the Firm
- •Innovation and the Market for Ideas
- •The Environment
- •Factor Conditions
- •Demand Conditions
- •Related Supplier or Support Industries
- •Strategy, Structure, and Rivalry
- •Chapter Summary
- •Questions
- •Endnotes
- •The Principal–Agent Relationship
- •Combating Agency Problems
- •Performance-Based Incentives
- •Problems with Performance-Based Incentives
- •Preferences over Risky Outcomes
- •Risk Sharing
- •Risk and Incentives
- •Selecting Performance Measures: Managing Trade-offs between Costs
- •Do Pay-for-Performance Incentives Work?
- •Implicit Incentive Contracts
- •Subjective Performance Evaluation
- •Promotion Tournaments
- •Efficiency Wages and the Threat of Termination
- •Incentives in Teams
- •Chapter Summary
- •Questions
- •Endnotes
- •13: Strategy and Structure
- •An Introduction to Structure
- •Individuals, Teams, and Hierarchies
- •Complex Hierarchy
- •Departmentalization
- •Coordination and Control
- •Approaches to Coordination
- •Types of Organizational Structures
- •Functional Structure (U-form)
- •Multidivisional Structure (M-form)
- •Matrix Structure
- •Matrix or Division? A Model of Optimal Structure
- •Network Structure
- •Why Are There So Few Structural Types?
- •Structure—Environment Coherence
- •Technology and Task Interdependence
- •Efficient Information Processing
- •Structure Follows Strategy
- •Strategy, Structure, and the Multinational Firm
- •Chapter Summary
- •Questions
- •Endnotes
- •The Social Context of Firm Behavior
- •Internal Context
- •Power
- •The Sources of Power
- •Structural Views of Power
- •Do Successful Organizations Need Powerful Managers?
- •The Decision to Allocate Formal Power to Individuals
- •Culture
- •Culture Complements Formal Controls
- •Culture Facilitates Cooperation and Reduces Bargaining Costs
- •Culture, Inertia, and Performance
- •A Word of Caution about Culture
- •External Context, Institutions, and Strategies
- •Institutions and Regulation
- •Interfirm Resource Dependence Relationships
- •Industry Logics: Beliefs, Values, and Behavioral Norms
- •Chapter Summary
- •Questions
- •Endnotes
- •Glossary
- •Name Index
- •Subject Index
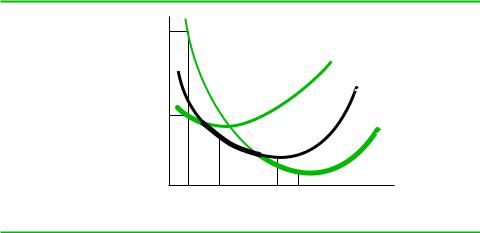
16 • Economics Primer: Basic Principles
•When average cost is an increasing function of output, marginal cost is greater than average cost.
These relationships follow from the mathematical properties of average and marginal cost, but they are also intuitive. If the average of a group of things (costs of manufacturing cellular phones, test scores, or whatever) increases when one more thing (one more phone, one more test) is added to the group, then it must be because the value of the most recently added thing—the “marginal”—is greater than the average. Conversely, if the average falls, it must be because the marginal is less than the average.
The Importance of the Time Period: Long-Run versus Short-Run Cost Functions
We emphasized the importance of the time horizon when discussing fixed versus variable costs. In this section, we develop this point further and consider some of its implications.
Figure P.6 illustrates the case of a firm whose production can take place in a facility that comes in three different sizes: small, medium, and large. Once the firm commits to a production facility of a particular size, it can vary output only by varying the quantities of inputs other than the plant size (e.g., by hiring another shift of workers). The period of time in which the firm cannot adjust the size of its production facilities is known as the short run. For each plant size, there is an associated short-run average cost function, denoted by SAC. These average cost functions include the annual costs of all relevant variable inputs (labor, materials) as well as the fixed cost (appropriately annualized) of the plant itself.
If the firm knows how much output it plans to produce before building a plant, then to minimize its costs, it should choose the plant size that results in the lowest
FIGURE P.6
Short-Run and Long-Run Average Cost Functions
Average cost
SACL(Q1)
SACS(Q1)
SACS(Q)
SACM(Q)
SACL(Q)
Q1 Q2 |
Q3 Q4 |
|
Q Output |
The curves labeled SACS(Q), SACM(Q), and SACL(Q) are the short-run average cost functions associated with small, medium, and large plants, respectively. For any level of output, the optimal plant size is the one with the lowest average cost. For example, at output Q1, the small plant is best. At output Q2, the medium plant is best. At output Q3, the large plant is best. The long-run average cost function is the “lower envelope” of the short-run average cost functions, represented by the bold line. This curve shows the lowest attainable average cost for any output when the firm is free to adjust its plant size optimally.

Costs • 17
short-run average cost for that desired output level. For example, for output Q1, the optimal plant is a small one; for output Q2, the optimal plant is a medium one; for output Q3, the optimal plant is a large one. Figure P.6 illustrates that for larger outputs, the larger plant is best; for medium-output levels, the medium plant is best; and for small-output levels, the small plant is best. For example, when output is Q1, the reduction in average cost that results from switching from a large plant to a small plant is SACL(Q1) 2 SACS(Q1). This saving not only arises from reductions in the fixed costs of the plant, but also because the firm can more efficiently tailor the rest of its operations to its plant size. When the firm produces Q1 in the large plant, it may need to utilize more labor to assure steady materials flows within the large facility. The small plant may allow flows to be streamlined, making such labor unnecessary.
The long-run average cost function is the lower envelope of the short-run average cost functions and is depicted by the bold line in Figure P.6. It shows the lowest attainable average cost for any particular level of output when the firm can adjust its plant size optimally. This is the average cost function the firm faces before it has committed to a particular plant size.
In this example, the long-run average cost function exhibits economies of scale. By operating with larger plant sizes, the firm can lower its average costs. This raises a deceptively simple but extremely significant point. To realize the lower average costs, the firm must not only build a large plant but must also achieve sufficient output, so that the large plant is indeed the optimal one. It would be disastrous for the firm to build a large plant if it only achieved an output of, say, Q1. The firm would be saddled with an expensive underutilized facility. If we were to observe a firm in this situation, we might be tempted to conclude that the scale economies inherent in the production process were limited or nonexistent. This would be incorrect. Scale economies exist, but the firm is not selling enough output needed to exploit them. These concepts are closely tied to the concept of throughput that we introduce in Chapter 1. Essentially, firms cannot fully exploit economies of scale unless they have sufficient inputs for production and distribution to get their products to market. Without such throughput, strategies that hinge on scale economies are doomed to fail.
It is often useful to express short-run average costs as the sum of average fixed costs (AFC) and average variable costs (AVC):
SAC(Q) 5 AFC(Q) 1 AVC(Q)
Average fixed costs are the firm’s fixed costs (i.e., the annualized cost of the firm’s plant plus expenses, such as insurance and property taxes, that do not vary with the volume of output) expressed on a per-unit-of-output basis. Average variable costs are the firm’s variable costs (e.g., labor and materials) expressed on a per-unit-of-output basis. For example, suppose the firm’s plant has an annualized cost of $9 million and other annual fixed expenses total $1 million. Moreover, suppose the firm’s variable costs vary with output according to the formula 4Q2. Then we would have
AFC(Q) 5 10Q
AFC(Q) 5 4Q
AFC(Q) 5 10Q 1 4Q
Note that as the volume of output increases, average fixed costs become smaller, which tends to pull down SAC. Average fixed costs decline because total fixed costs are being
18 • Economics Primer: Basic Principles
spread over an ever-larger production volume. Offsetting this (in this example) is the fact that average variable costs rise with output, which pulls SAC upward. The net effect of these offsetting forces creates the U-shaped SAC curves in Figure P.6.
Sunk versus Avoidable Costs
When assessing the costs of a decision, the manager should consider only those costs that the decision actually affects. Some costs must be incurred no matter what the decision is and thus cannot be avoided. These are called sunk costs. The opposite of sunk costs is avoidable costs. These costs can be avoided if certain choices are made. When weighing the costs of a decision, the decision maker should ignore sunk costs and consider only avoidable costs.
To illustrate the concept of sunk costs, take the case of an online merchandiser of laser printers. The merchandiser traditionally purchased large quantities of printers from the manufacturer, so that it could satisfy rush orders. Increasingly, though, the merchandiser was carrying high inventories, including some lines that the manufacturer no longer produced and would not repurchase. A natural response to this problem would be to put the discontinued lines on sale and reduce inventory. However, the firm’s managers were reluctant to do this. They felt that even in the best of times the margins on their products barely covered their overhead, and by cutting the price, they would be unable to cover their cost of the goods they sold.
This argument is wrong. The cost incurred to purchase the laser printers is a sunk cost as far as pricing is concerned. Whether or not the merchandiser cuts price, it cannot avoid these costs. If it believes that a seller should never price below average cost, the merchandiser will end up with large losses. Instead, it should accept that it cannot undo past decisions (and their associated sunk costs) and strive to minimize its losses.
It is important to emphasize that whether a cost is sunk depends on the decision being made and the options at hand. In the example just given, the cost of the discontinued lines of printers is a sunk cost with respect to the pricing decision today. But before the printers were ordered, their cost would not have been sunk. By not ordering them, the merchandiser would have avoided the purchase and storage costs.
Students often confuse sunk costs with fixed costs. The two concepts are not the same. In particular, some fixed costs need not be sunk. For example, a railroad serving Sydney to Adelaide needs a locomotive and a crew whether it hauls 1 carload of freight or 20. The cost of the locomotive is thus a fixed cost. However, it is not necessarily sunk. If the railroad abandons its Sydney to Adelaide line, it can sell the locomotive to another railroad or redeploy it to another route.
Sunk costs are important for the study of strategy, particularly in analyzing rivalry among firms, entry and exit decisions from markets, and decisions to adopt new technologies. For example, the concept of sunk costs helps explain why established American steel firms were unwilling to invest continuous casting technology, even as new Japanese firms building “greenfield” facilities did adopt the new technology. The new technology had higher fixed costs, but lower variable operating costs. Established American firms viewed the fixed cost of their old technologies as sunk. Thus, they compared the savings in operating costs against the fixed cost of the new technology. The Japanese firms, in contrast, compared the savings in operating costs against the difference between the fixed costs of the new and old technologies. American firms thus required a larger cost savings than the Japanese firms to induce them to adopt the new technology. Despite criticism in the popular business press, the American firms’