
- •Н. М. Андрюхов
- •К. М. Кулик
- •Д. Ю.Пьянина
- •МУСОРОВОЗЫ СО СМЕННЫМИ КОНТЕЙНЕРАМИ
- •Т. К. Балгабеков
- •А. Н. Конкыбаева
- •Р. С. Жандильдина
- •ИССЛЕДОВАНИЯ УДАРНОГО ПРОЦЕССА В САМОХОДНЫХ БЕТОНОСМЕСИТЕЛЯХ (СБС)
- •А. И. Демиденко
- •И. С. Кузнецов
- •КИНЕМАТИКА ДВИЖЕНИЯ РЕЗЦОВ ФРЕЗЕРНОГО РАБОЧЕГО ОБОРУДОВАНИЕ ЭКСКАВАТОРА
- •С.Д.Игнатов
- •М. Е. Крамшов
- •ПОВЫШЕНИЕ ПОПЕРЕЧНОЙ УСТОЙЧИВОСТИ СТРОИТЕЛЬНЫХ И ЗЕМЛЕРОЙНЫХ МАШИН ПРИ РАБОТЕ НА СКЛОНАХ
- •С.А. Крохмаль
- •К ВОПРОСУ ИСПОЛЬЗОВАНИЯ СОВРЕМЕННЫХ ТЕХНОЛОГИЙ СВАРКИ ПРИ РЕМОНТЕ НЕФТЯНОГО РЕЗЕРВУАРА
- •А.Б. Летопольский
- •АНАЛИЗ КОНСТРУКЦИИ РЕЖУЩЕЙ ЧАСТИ ПРОХОДЧЕСКОГО ЩИТА С ПРИМЕНЕНИЕМ ПРОГРАММНОГО ПРОДУКТА T-FLEX CAD
- •С. А. Павлов
- •А. М. Погонина
- •Н. М. Андрюхов
- •С. А. Павлов
- •Н. В. Шершнев
- •Н. М. Андрюхов
- •ПРИМЕНЕНИЕ МЕТОДОВ ВОССТАНОВЛЕНИЯ ГРУНТОВ, ЗАГРЯЗНЕННЫХ НЕФТЕПРОДУКТАМИ
- •И. К. Потеряев
- •М. И. Кременецкий
- •СОВЕРШЕНСТВОВАНИЕ РАЗДАЧИ НЕФТЕПРОДУКТОВ ДЛЯ ЭКСПЛУАТАЦИИ ДОРОЖНО-СТРОИТЕЛЬНОЙТЕХНИКИ
- •К.Г. Пугин
- •О.Н. Мехонин
- •ПОВЫШЕНИЕ БЕЗОПАСНОСТИ РАБОТ НА КРАНАХ-МАНИПУЛЯТОРАХ УСТАНОВЛЕННЫХ НА АВТОМОБИЛЬНОМ ШАССИ
- •К. Г. Пугин
- •У.А. Пираматов
- •СОВЕРШЕНСТВОВАНИЕ МЕТОДОВ ДИАГНОСТИРОВАНИЯ ГИДРОСИСТЕМ ГИДРОФИЦИРОВАННЫХ МАШИН
- •С.В. Савельев
- •Г. Г. Бурый
- •З. Р. Аднагулова
- •МЕТОДИКА ОБОСНОВАНИЯ ПАРАМЕТРОВ ВИБРАЦИОННЫХ КАТКОВ ДЛЯ УПЛОТНЕНИЯ ГРУНТОВЫХ НАСЫПЕЙ, УЧИТЫВАЮЩАЯ ЗОНУ АКТИВНОГО ДЕЙСТВИЯ ВИБРАЦИИ
- •В. В. Савинкин
- •ОПТИМИЗАЦИЯ УГЛОВ ПОЗИЦИОНИРОВАНИЯ РАБОЧЕГО ОБОРУДОВАНИЯ ГИДРАВЛИЧЕСКОГО ЭКСКАВАТОРА
- •ПОВЫШЕНИЕ ЭФФЕКТИВНОСТИ АВАРИЙНО-ВОССТАНОВИТЕЛЬНЫХ РАБОТ НА ЛИНЕЙНОЙ ЧАСТИ НЕФТЕПРОВОДОВ
- •ПУТИ СОВЕРШЕНСТВОВАНИЯ РАБОЧЕГО ОРГАНА АВТОГРЕЙДЕРА ДЛЯ РЕКУЛЬТИВАЦИИ ПОЛОСЫ ОТВОДА ПРИ СТРОИТЕЛЬСТВЕ МАГИСТРАЛЬНОГО ТРУБОПРОВОДА
- •АЛГОРИТМ РАСЧЕТА ТРАМБУЮЩЕГО РАБОЧЕГО ОРГАНА
- •И.В. Лазута
- •Е.Ф. Лазута
- •МОДЕЛИРОВАНИЕ И ИНЖЕНЕРНЫЙ АНАЛИЗ ГИДРОСТАТИЧЕСКОЙ ПЕРЕДАЧИ В СРЕДЕ SIMULINK
- •В. В. Голубенко
- •СОВЕРШЕНСТВОВАНИЕ РАБОТЫ АВТОМАТИЧЕСКОЙ СИСТЕМЫ УПРАВЛЕНИЯ РАБОЧЕГО ОРГАНА АСФАЛЬТОУКЛАДЧИКА
- •Ш.К. Мукушев
- •БЕЗОГНЕВАЯ РЕЗКА НЕФТЕГАЗОПРОВОДОВ
- •И.Е. Почекуева
- •В.С. Щербаков
- •МАТЕМАТИЧЕСКОЕ ОПИСАНИЕ АВТОГРЕЙДЕРА, КАК ОБЪЕКТА УПРАВЛЕНИЯ
- •Направление 2. ПРОБЛЕМЫ И ПЕРСПЕКТИВЫ РАЗВИТИЯ ТРАНСПОРТНОГО КОМПЛЕКСА
- •ОПРЕДЕЛЕНИЕ ОПТИМАЛЬНОГО КОМПЛЕКТА ДИАГНОСТИЧЕСКИХ ПАРАМЕТРОВ В РАМКАХ НОВОГО МЕТОДА ДИАГНОСТИРОВАНИЯ ГИДРАВЛИЧЕСКОЙ ТОРМОЗНОЙ СИСТЕМЫ
- •Л.Ю. Волкова
- •Г.С.Коровин
- •А.В.Пузаков
- •ИССЛЕДОВАНИЕ ПАРАМЕТРОВ ТЕПЛОВОЙ МОДЕЛИ АВТОМОБИЛЬНОГО ГЕНЕРАТОРА
- •В. А. Лисин
- •К ВОПРОСУ ОБ ЭКСПЛУАТАЦИОННОЙ НАДЕЖНОСТИ ШАРОВЫХ ОПОР АВТОМОБИЛЯ ПРИ УСЛОВИИ ЭКСПЛУАТАЦИИ В РФ
- •И.В. Приходько
- •А.Н. Кошко
- •ОЦЕНКА ВЛИЯНИЯ КЛИМАТИЧЕСКИХ ПАРАМЕТРОВ НА РАБОТОСПОСОБНОСТЬ УСТРОЙСТВ И ОБОРУДОВАНИЯ
- •А. В. Пузаков
- •МОДЕЛИРОВАНИЕ НЕИСПРАВНОСТЕЙ ЭЛЕКТРОМАГНИТНОЙ ТОПЛИВНОЙ ФОРСУНКИ АВТОМОБИЛЬНОГО ДВИГАТЕЛЯ
- •Д.А. Смирнов
- •А. В. Пузаков
- •ИССЛЕДОВАНИЕ ПАРАМЕТРОВ СТАРТЕРНОЙ АККУМУЛЯТОРНОЙ БАТАРЕИ С РАЗНЫМ СОСТОЯНИЕМ ЗАРЯЖЕННОСТИ
- •М. А. Танская
- •В. А. Лисин
- •АНАЛИЗ ЭКСПЛУАТАЦИОННЫХ ОТКАЗОВ ГРУЗОВЫХ АВТОМОБИЛЕЙ В СЛОЖНЫХ КЛИМАТИЧЕСКИХ УСЛОВИЯХ
- •А.В. Трофимов
- •А. В. Чурсин
- •К ВОПРОСУ ОРГАНИЗАЦИИ МЕТРОЛОГИЧЕСКОЙ ПОВЕРКИ АВТОМОБИЛЬНЫХ ТАХОГРАФОВ ПРИ ОБСЛУЖИВАНИИ В СПЕЦИАЛИЗИРОВАННОЙ МАСТЕРСКОЙ
- •О ПОЭЛЕМЕНТНОМ ФОРМИРОВАНИИ ПРОЦЕССА ЭКСПЛУАТАЦИИ АВТОМОБИЛЬНЫХ ТАХОГРАФОВ НА ПРЕДПРИЯТИИ С УЧЕТОМ НОРМАТИВНЫХ ТРЕБОВАНИЙ
- •С.В. Ушнурцев
- •А.В. Келлер
- •А.В. Шевелев
- •АНАЛИЗ ПУТЕЙ СОВЕРШЕНСТВОВАНИЯ МЕХАНИЗМА ПРЕОБРАЗОВАНИЯ ДВИЖЕНИЯ ПОРШНЯ ВО ВРАЩАТЕЛЬНОЕ ДВИЖЕНИЕ КОЛЕНЧАТОГО ВАЛА
- •Д.О. Бородович
- •ОСОБЕННОСТИ ПЛАНИРОВАНИЯ ГОРОДСКОЙ АВТОБУСНОЙ ЭКСКУРСИИ, СВЯЗАННЫЕ С ОРГАНИЗАЦИИ ТРАНСПОРТНОГО ПРОЦЕССА
- •С.С. Войтенков
- •РАЗВИТИЕ СИСТЕМЫ ОБЩЕСТВЕННОГО ТРАНСПОРТА ГОРОДА НУР-СУЛТАН
- •ОБЗОР ТЕОРИИ ПЕРЕВОЗОК ГРУЗОВ В СМЕШАННОМ СООБЩЕНИИ
- •Е.С. Галактионова
- •НЕКОТОРЫЕ РЕЗУЛЬТАТЫ ОБЗОРА ТЕОРИИ ОПИСАНИЯ ГРУЗОВЫХ ПЕРЕВОЗОК ПРИМЕНИТЕЛЬНО К «ГРУЗОВОМУ ТАКСИ»
- •М.Н. Латышева
- •ТРАНСПОРТНАЯ ЛОГИСТИКА ЕВРАЗИЙСКОГО ЭКОНОМИЧЕСКОГО СОЮЗА
- •Б. Ю.Калмыков
- •Ю. Б. Гармидер
- •АНАЛИЗ СОСТОЯНИЯ МАРШРУТНОЙ СЕТИ ПАССАЖИРСКОГО АВТОМОБИЛЬНОГО ТРАНСПОРТА НА ТЕРРИТОРИИ ГОРОДА ЭЛИСТЫ
- •Д.В. Капский
- •С.С. Семченков
- •Д.В. Капский
- •С.С. Семченков
- •ОСОБЕННОСТИ ОБЕСПЕЧЕНИЯ БЕЗОПАСНОСТИ ДОРОЖНОГО ДВИЖЕНИЯ И ПЕРЕВОЗОК НА ДЕЖУРНЫХ МАРШРУТАХ, ПРЕДНАЗНАЧЕННЫХ ДЛЯ ПЕРЕВОЗОК ВОДИТЕЛЕЙ ГОРОДСКОГО ПАССАЖИРСКОГО ТРАНСПОРТА, КАК ВАЖНЕЙШИЙ ФАКТОР ФУНКЦИОНИРОВАНИЯ ТРАНСПОРТНОЙ СИСТЕМЫ
- •А. В. Кирьянов
- •Н. А. Филиппова
- •Т. Н. Пашкова
- •ТРАНЗИТНЫЙ ПОТЕНЦИАЛ РОССИИ
- •И.С. Курушин
- •Д.В.Шаповал
- •ПЛАНИРОВАНИЕ МАРШРУТА ПЕРЕВОЗКИ КРУПНОГАБАРИТНОГО ГРУЗ В МЕЖДУГОРОДНОМ СООБЩЕНИИ
- •ИССЛЕДОВАНИЕ ПРИВЛЕКАТЕЛЬНОСТИ ВИДОВ ТРАНСПОРТА НА ОСНОВЕ КРИТЕРИЕВ ПРЕДПОЧТЕНИЯ КЛИЕНТОВ
- •В.В. Лыкова
- •РЕЗУЛЬТАТЫ ПЛАНИРОВАНИЯ ПЕРЕВОЗОК ГРУЗОВ АВТОМОБИЛЬНЫМ ТРАНСПОРТОМ ДЛЯ ВЫПОЛНЕНИЯ ДОРОЖНО-РЕМОНТНЫХ РАБОТ В ОМСКОЙ ОБЛАСТИ
- •М.Т.Насковец
- •М.М.Цмак
- •Н.И.Занько
- •А.В. Пахомова
- •Р.Р. Баширзаде
- •ТРАНСПОРТНОЕ ОБЕСПЕЧЕНИЕ СИТИ-ЛОГИСТИКИ
- •ПРАКТИКА ПЕРЕВОЗОК ПАССАЖИРОВ В ОМСКОЙ ОБЛАСТИ
- •Ф.И. Садыков
- •Н.В. Ловыгина
- •СОВЕРШЕНСТВОВАНИЕ СХЕМЫ ОРГАНИЗАЦИИ ПЕРЕВОЗОК НА ПРЕДПРИЯТИИ ООО «РАНГОУТ»
- •В.А. Титов
- •Н.В. Ловыгина
- •ПЕРЕВОЗКА ПАССАЖИРОВ РАЗЛИЧНЫМИ ВИДАМИ ТРАНСПОРТА И ЕЁ РЕНТАБЕЛЬНОСТЬ В СОВРЕМЕННЫХ ГОРОДСКИХ УСЛОВИЯХ
- •В.В.Томм
- •Д. В.Шаповал
- •ПРАКТИКА ПЕРЕВОЗКИ МОЛОКА В ЦИСТЕРНАХ ПРИ ЕГО СБОРЕ У НАСЕЛЕНИЯ
- •В.В. Холоша
- •Л.С. Трофимова
- •ПЛАНИРОВАНИЕ РАБОТЫ ПОДВИЖНОГО СОСТАВА В АГРОПРОМЫШЛЕННОМ КОМПЛЕКСЕ
- •БАЗА ДАННЫХ РЫНКА МЕЖДУГОРОДНИХ ПАССАЖИРСКИХ ПЕРЕВОЗОК
- •И.Б. Ахунова
- •С.Е. Бебинов
- •О.Н. Кривощекова
- •ФОРМИРОВАНИЕ НАВЫКОВ ВОЖДЕНИЯ АВТОМОБИЛЯ С УЧЕТОМ ХАРАКТЕРИСТИК ТРАНСПОРТНОГО ПОТОКА
- •Г.Н. Климова
- •В.А. Зеликов
- •М.Н. Казачек
- •ВЛИЯНИЕ ПСИХОЛОГИЧЕСКОГО СОСТОЯНИЯ ВОДИТЕЛЕЙ НА БЕЗОПАСНОСТЬ ДОРОЖНОГО ДВИЖЕНИЯ
- •ЭКОЛОГИЧЕСКИЙ УЩЕРБ ОТ ЗАГРЯЗНЕНИЯ ВОЗДУХА ТРАНСПОРТНЫМИ ПОТОКАМИ НА ПРИМЕРЕ УЧАСТКА УЛ. 7-Я СЕВЕРНАЯ Г. ОМСКА
- •В.Д. Шепелев
- •Н.С. Абрамов
- •СОВРЕМЕННЫЕ ТЕХНОЛОГИИ В ЗАДАЧАХ ПОВЫШЕНИЯ СРЕДНЕЙ СКОРОСТИ ДВИЖЕНИЯ ОБЩЕСТВЕННОГО ТРАНСПОРТА В ГОРОДЕ ЧЕЛЯБИНСК
- •Секция 2.4. ОСНОВНЫЕ ПРОБЛЕМЫ РАЗВИТИЯ ТРАНСПОРТА В УСЛОВИЯХ ФОРМИРОВАНИЯ ЦИФРОВОЙ ЭКОНОМИКИ
- •Е.В. Авдейчикова
- •УПРАВЛЕНИЕ ЛОГИСТИЧЕСКИМИ ОПЕРАЦИЯМИ В ПРОЦЕССЕ ТРАНСПОРТИРОВАНИЯ ТВЕРДЫХ КОММУНАЛЬНЫХ ОТХОДОВ
- •А.Г. Болтовский
- •ФОРМИРОВАНИЕ ЭФФЕКТИВНОГО МЕХАНИЗМА ВЗАИМОДЕЙСТВИЯ ТУРИСТИЧЕСКОЙ ОТРАСЛИ И ТРАНСПОРТА ДЛЯ МАЛОМОБИЛЬНЫХ ГРУПП НАСЕЛЕНИЯ
- •Г.В. Горнасталёв
- •Д.И. Заруднев
- •ИНСТРУМЕНТАЛЬНЫЕ СРЕДСТВА ИМИТАЦИОННОГО МОДЕЛИРОВАНИЯ В ЛОГИСТИКЕ
- •Р.В.Горшков
- •И.А. Горшкова
- •ОСОБЕННОСТИ ПРИМЕНЕНИЯ СИСТЕМЫ МЕНЕДЖМЕНТА КАЧЕСТВА В СФЕРЕ УСЛУГ
- •В.Е. Граматчикова
- •РАДИОЧАСТОТНАЯ ИДЕНТИФИКАЦИЯ КАК СПОСОБ ЗАЩИТЫ ОТ КОНТРАФАКТА В АВТОМОБИЛЬНОЙ ПРОМЫШЛЕННОСТИ
- •Н.В. Стефанович
- •ВРЕМЯ ЛОГИСТИЧЕСКОГО ПРОЦЕССА И ЕГО ВЛИЯНИЕ НА ЭФФЕКТИВНОСТЬ ПОСТАВКИ ПРОДУКЦИИ
- •Д.А. Дубровский
- •ОБЗОР МЕТОДОВ И МОДЕЛЕЙ ОЦЕНКИ КАЧЕСТВА ТРАНСПОРТНОГО ОБСЛУЖИВАНИЯ В ЛОГИСТИКЕ
- •М.О.Каюмова
- •ПРОБЛЕМЫ ВНЕДРЕНИЯ СИСТЕМЫ ХАССП НА РОССИЙСКИХ ПРЕДПРИЯТИЯХ
- •В. М. Курганов
- •М. В. Грязнов
- •В. Н. Мукаев
- •ОНТОЛОГИЯ ТРАНСПОРТНОГО ПРОЦЕССА В ИНФОРМАЦИОННЫХ СИСТЕМАХ УПРАВЛЕНИЯ
- •Е.А. Байда
- •ОСОБЕННОСТИ ПРОЕКТИРОВАНИЯ ИНТЕГРИРОВАННЫХ СИСТЕМ МЕНЕДЖМЕНТА ОРГАНИЗАЦИЙ
- •Е.И. Плаксина
- •Е.В. Романенко
- •НАЛОГОВЫЙ МЕХАНИЗМ КАК ФАКТОР РАЗВИТИЯ БИЗНЕС-СРЕДЫ В УСЛОВИЯХ ЦИФРОВИЗАЦИИ ЭКОНОМИКИ
- •Е. Э. Попова
- •ИССЛЕДОВАНИЕ ВЛИЯНИЯ НЕРАВНОМЕРНОСТИ МАТЕРИАЛЬНОГО ПОТОКА НА ТРАНСПОРТНО-СКЛАДСКИЕ ПРОЦЕССЫ
- •С.В. Сухарева
- •М.С. Высоцкая
- •АЛГОРИТМ РАЗРАБОТКИ ИННОВАЦИОННОГО РЕЖИМА ТРАНСПОРТНОГО ПРЕДПРИЯТИЯ
- •С. В. Сухарева
- •Н. В. Рыбина
- •ПЛАНИРОВАНИЕ ПРИМЕНЕНИЯ БЕСПИЛОТНЫХ АВТОМОБИЛЕЙ В СОВРЕМЕННЫХ УСЛОВИЯХ
- •С. В. Сухарева
- •Н.В. Рыбина
- •ОСНОВНЫЕ ПРОБЛЕМЫ ЦИФРОВИЗАЦИИ ТРАНСПОРТА В УСЛОВИЯХ СОВРЕМЕННОЙ ЭКОНОМИКИ
- •С.А. Теслова
- •М. В. Николаенко
- •АНАЛИЗ УСЛОВИЙ И НАПРАВЛЕНИЙ РАЗВИТИЯ БИЗНЕСА В ИННОВАЦИОННОЙ СРЕДЕ
- •Б. Г. Хаиров
- •ОБЗОР ТЕХНОЛОГИЙ ИДЕНТИФИКАЦИИ ТОВАРОВ И ЗАЩИТЫ ИХ ОТ ПОДДЕЛОК ПРИ ОРГАНИЗАЦИИ МЕЖДУНАРОДНЫХ ЦЕПЕЙ ПОСТАВОК
- •С. М. Хаирова
- •АНАЛИЗ ОТЕЧЕСТВЕННОГО И ЗАРУБЕЖНОГО ОПЫТА ОРГАНИЗАЦИИ КОНТРОЛЯ КАЧЕСТВА ТОВАРОВ ПРИ ТРАНСПОРТИРОВКЕ В ЦЕПИ ПОСТАВОК
- •Е.А. Байда
- •РАЗРАБОТКА МОДЕЛИ СИСТЕМЫ МЕНЕДЖМЕНТА КАЧЕСТВА ПРОИЗВОДСТВА СТРОИТЕЛЬНЫХ КОНСТРУКЦИЙ
- •Д.С. Алешков
- •О.В. Владимова
- •ОЦЕНКА ПРОФЕССИОНАЛЬНЫХ РИСКОВ ПРИ СХОДЕ ЛЕДОВЫХ ОБРАЗОВАНИЙ С КРЫШ ЗДАНИЙ И СООРУЖЕНИЙ
- •Д.С. Алешков
- •М.В. Суковин
- •ИДЕНТИФИКАЦИЯ ОПАСНОСТЕЙ ПРИ ОЦЕНКЕ ПРОФЕССИОНАЛЬНЫХ РИСКОВ НА РАБОЧЕМ МЕСТЕ ВОДИТЕЛЯ ТРАНСПОРТНОГО СРЕДСТВА
- •А.П. Бархатова
- •О.В.Плешакова
- •ПРОБЛЕМЫ УТИЛИЗАЦИИ СНЕЖНЫХ МАСС В ЗИМНИЙ ПЕРИОД В ОМСКЕ
- •В.М. Брянцева
- •АНАЛИЗ КОЛИЧЕСТВЕННЫХ ПОКАЗАТЕЛЕЙ ТРАВМАТИЗМА И ЗАБОЛЕВАЕМОСТИ ВОЕННОСЛУЖАЩИХ
- •А.В.Пуговкин
- •РАЗРАБОТКА СИСТЕМЫ КОНТРОЛЯ И УПРАВЛЕНИЯ МИКРОКЛИМАТОМ ПОМЕЩЕНИЯ «УМНАЯ ЛАБОРАТОРИЯ»
- •Л.В. Ровкин
- •МУСОРНАЯ РЕФОРМА В КРУТИНСКОМ РАЙОНЕ ОМСКОЙ ОБЛАСТИ
- •В.А. Хомич
- •К.А. Алексеенко
- •ПЕРСПЕКТИВА ПРОЕКТИРОВАНИЯ ЭКОДУКА ЧЕРЕЗ АВТОМОБИЛЬНУЮ ДОРОГУР-402 В ОМСКОЙ ОБЛАСТИ
- •В.А. Хомич
- •ОЦЕНКА ВЛИЯНИЯ ДОБАВОК АНТИПИРЕНОВ НА ГОРЮЧЕСТЬ РЕЗИН
Направление 2. ПРОБЛЕМЫ И ПЕРСПЕКТИВЫ РАЗВИТИЯ ТРАНСПОРТНОГО КОМПЛЕКСА
Секция 2.1. НОВЫЕ ТЕХНОЛОГИИ, УСТРОЙСТВА
ИМАТЕРИАЛЫ ПРИ ПРОИЗВОДСТВЕ
ИЭКСПЛУАТАЦИИ АВТОТРАНСПОРТНЫХ СРЕДСТВ
ВСЛОЖНЫХ КЛИМАТИЧЕСКИХ УСЛОВИЯХ
ОБРАЗОВАНИЕ. ТРАНСПОРТ. ИННОВАЦИИ. СТРОИТЕЛЬСТВО
Сборник материалов III Национальной научно-практической конференции
_______________________________________________________________________________________
УДК 629.113
ОПРЕДЕЛЕНИЕ ОПТИМАЛЬНОГО КОМПЛЕКТА ДИАГНОСТИЧЕСКИХ ПАРАМЕТРОВ В РАМКАХ НОВОГО МЕТОДА ДИАГНОСТИРОВАНИЯ ГИДРАВЛИЧЕСКОЙ ТОРМОЗНОЙ СИСТЕМЫ
А. Л. Бородин, старший преподаватель; А.В. Шарыпов,кандидат технических наук, доцент
Федеральное государственное бюджетное образовательное учреждение высшего образования «Курганский государственный университет», Курган, Россия
Аннотация.В статье рассматривается применение математического моделирования для поэлементного диагностирования главного, двухконтурного тормозного цилиндра гидравлической тормозной системы автотранспортного средства с использованием метода диагностирования по силе сопротивления воздействия на тормозную педаль в зависимости от темпа нажатия.
Ключевые слова: Главный тормозной цилиндр, математическая модель, гидравлическая тормозная система, метод диагностирования по силе противления нажатия на тормозную педаль, темп нажатия.
DETERMINATION OF THE OPTIMAL SET OF DIAGNOSTIC PARAMETERS IN THE FRAMEWORK OF A NEW METHOD FOR DIAGNOSING THE HYDRAULIC BRAKE SYSTEM
A. L. Borodin, senior teacher;
A.V. Sharypov,candidate of technical Sciences, associate Professor
Federal State Budget Educational Institution of Higher Education
"The Kurgan State University", Kurgan, Russia
Abstract.The article deals with the application of mathematical modeling for piecemeal diagnostics of the main, two-circuit brake cylinder of the hydraulic brake system of a vehicle using the method for diagnosing the strength of the resistance of the impact on the brake pedal, depending on the rate of pressing.
Keywords: Master brake cylinder, mathematical model, hydraulic brake system, method of diagnostics by the force of resistance to pressing the brake pedal, the rate of pressing.
Гидравлический тормозной приводполучил большое распространение в тормозных системахавтотранспортных средств. Он состоит из следующих основных элементов: педаль тормоза; вакуумный или электрический усилитель тормозов; главный тормозной цилиндр; трубопроводы; модуль ABS/ESC; тормозные механизмы передних и задних колес.
Органами управления тормозной системой являются главный тормозной цилиндр и модуль ABS/ESC. Модуль ABS/ESC необходим для регулирования давления в контурах колес и поддержания колес автотранспортного средства в не заблокированном состоянии, за счет перераспределения тормозного усилия на колесах. Данный эффект на современных транспортных средствах достигается работой электронного клапана и насоса. ABS срабатывает при соблюдении условий: проскальзывание колес и нажатие на педаль тормоза. Если проскальзывания колес не наблюдается, то система работает в штатном режиме (без модуля ABS). При наличии неисправностей в главном тормозном цилиндре электронные системы могут не сработать или работать в режиме, не соответствующем фактическому режиму торможения, что в свою очередь может привести к дорожнотранспортному происшествию [1].
Главным органом управления в гидравлических тормозных системах можно считать двухконтурный главный тормозной цилиндр (типа тандем), его в настоящее время используют практически все автопроизводители, за счет простоты конструкции и надежности данного узла.
Выявления неисправностей в работе главного тормозного цилиндра является трудоемкой задачей и очень часто сопровождается предварительной заменой узлов и деталей исправных или имеющих большой ресурс наработки на отказ, что в свою очередь увеличивает трудоемкость ремонта, простои
117

Направление 2. Проблемы и перспективы развития транспортного комплекса
_______________________________________________________________________________________
автомобилей в ремонте и расходы на запасные части. Снятие-установка узлов и деталей приводит к снижению их ресурса.
Применение нового метода диагностирования тормозной системы по силе сопротивленияусилию нажатия на педаль тормоза поможет снизить трудоемкость и повысить достоверность при диагностировании гидравлических тормозных систем в условиях эксплуатации.
Гипотеза разработки нового метода: проведениедиагностирования в зоне нечувствительности тормозного приводапри различных режимах воздействия на педаль тормозапозволит определить неисправности элементов главного тормозного цилиндра по расхождению силы сопротивления нажатию с нормативными значениями.
При разработке любого метода диагностирования [2] необходимо провести оценку свойств диагностических параметров – косвенных величин, так или иначе связанных со структурными параметрамии несущими достаточную информацию о техническом состоянии объекта.Для анализа необходимо проведение большого количества экспериментальных исследований, что в свою очередь требует больших затрат труда и времени, в некоторых случаях, не оправданных степенью точности результатов эксперимента. В этом случае можно воспользоваться компьютерным моделированием, что поможет свести к минимуму объем экспериментальных исследований.
В процессе проведения исследования, было выявлено, что процессы, протекающие в гидравлическом тормозном приводе в момент запаздывания, согласно тормозной диаграммы, изучены мало. Диаграммы зависимостей усилия нажатия на тормозную педаль или замедления автомобиля от времени приводятся в литературе [7, 11 и др.] некорректны, в связи с тем, что исследования приводились в восьмидесятые годы и компьютерное оснащение исследователей по сравнению с нынешним было на низком уровне. Но изболее поздних работ [5] можно заметить нелинейное изменение силы нажатия на педаль тормоза при срабатывании тормозной системы. Что в свою очередь должно оказывать непосредственное влияние на силу сопротивленияусилиювоздействия на педаль тормоза. Конечно сила воздействия задана «Техническим регламентом» [12], но сила сопротивления должна отражать изменение всех силовых характеристик работы ГТЦ в динамике и показывать закономерности изменения этих параметров в зависимости от изменения технического состояния элементов системы в эксплуатации.
Для доказательства сформулированной гипотезы был проведен комплекс постановочных экспериментов. Согласно утверждения «сила действия равна силе противодействия», датчик, измеряющий усилие нажатия на педаль тормоза, фиксирует силу сопротивленияусилию нажатия на педаль тормоза. В результате была получена кривая зависимости силы сопротивленияот времени при помощи экспериментального комплекса [6], которая приведена на рисунке 1. Исследование проводили только на участке нарастания усилия на педали тормоза. На данном участке имеются две характерных точки, отображающие момент страгивания с места и остановки второго поршня ГТЦ. В процессе изменении эксплуатационных характеристик элементов ГТЦ происходит смещение точек 1 и 2 как по времени, так и по усилию.
Рисунок 1 – Зависимость силы противления нажатию на педаль тормоза от времени
Динамические процессы работы гидравлической тормозной системы, состоящей из подсистем, наиболее точно описываются системой линейных и нелинейных, алгебраических и дифференциальных уравнений, функционально связанных между собой. Каждая подсистема описывается соответствующим дифференциальным или алгебраическим уравнением. При
118
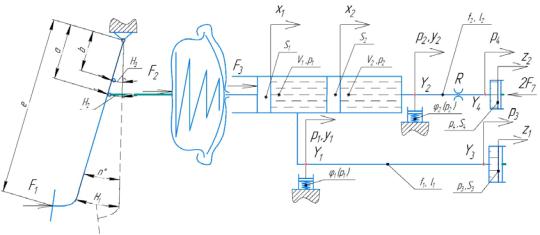
ОБРАЗОВАНИЕ. ТРАНСПОРТ. ИННОВАЦИИ. СТРОИТЕЛЬСТВО
Сборник материалов III Национальной научно-практической конференции
_______________________________________________________________________________________
моделировании система уравнений составлялась согласно схеме гидравлической цепи тормозной системы автомобиля ВАЗ-21213, состоящей из двух контуров, переднего и заднего. Тормозные цилиндры переднего контура – суппорта, состоящие из двух цилиндров и поршней. Задние тормозные цилиндры — это гидроцилиндры двухстороннего действия, рисунок 2. Главный тормозной цилиндр – двухконтурный, типа «тандем» с фиксированием плавающего поршня предварительно сжатой пружиной. Математическая модель позволяет при тестовом режиме диагностирования отображать технические характеристики отдельных элементов главного тормозного цилиндра.
Рисунок 2 – Упрощённая динамическая система гидроцепи тормозной системы
Взоне нечувствительности тормозного привода (время запаздывания) есть возможность проследить эффективность работы основных элементов главного тормозного цилиндра, в большей степени влияющих на работоспособность последнего.
Методики и рекомендации по определению неисправностей и математическому моделированию динамических процессов в главном тормозном цилиндре, предложенные в настоящее время [3, 4, 5],
вряде случаев затрудняют их использование для проведения поэлементного диагностирования главного тормозного цилиндра (ГТЦ). Поэтому некоторые формулы были приведены к виду, позволяющему раскрыть зависимость диагностических параметровот технического состояния отдельных элементов ГТЦ.
Задачей математического моделирования в процессе теоретического исследования являлся выбор комплекса диагностических параметров, с достаточной степенью вероятности указывающихна неисправность.В основном неисправности главного тормозного цилиндра определяют по косвенным признакам, имеющих низкий уровень достоверности. Косвенные признаки не дают точно определить неисправность, а указывают на несколько причин. Основные неисправности ГТЦ [4, 7]: завоздушивание; повреждение или износ уплотнительного кольца высокого давления первого поршня; повреждение или износ уплотнительного кольца высокого давления второго поршня; повреждение или износ уплотнительного кольца разделения контуров; заклинивание первого поршня
вГТЦ; заклинивание второго поршня в ГТЦ; засорено компенсационное 1-е отверстие в главном тормозном цилиндре; засорено компенсационное 2-е отверстие в главном тормозном цилиндре; разбухание резиновых деталей из-за использования тормозной жидкости не рекомендованного вида или замене рем комплекта не надлежащего качества; сломанараспорная пружина в первой полости; сломана распорная пружина во второй полости.
Некоторые указанные неисправности имеют явные признаки и определяются диагностом органолептическим методом, такие как поломка распорных пружин, заклинивание поршней в контурах. Есть неисправности которые проявляются на больших пробегах, и частота их проявления незначительна, менее 0,5% от общих [4]. Вследствие выше приведенных аргументов, рассматривать будем только часто встречающиеся неисправности, которые наиболее трудоемки в определении без применения диагностического аппарата.
Всоответствии с задачами данного исследования были приняты следующие допущения: исполнительные механизмы, тормозные шланги и трубопроводы – исправны; податливостью в исполнительных механизмах пренебрегаем, рабочие цилиндры передних и задних тормозных механизмов приводим к одному цилиндру с увеличенным вдвое диаметром; расчет приведённой массы жидкости к поршню управляющего и исполнительного механизмов производим по усредненной длине трубопроводов; волновые процессы в гидромагистралях вследствие сравнительно малой длины их не влияют на переходной процесс: вязкость, плотность, температура тормозной жидкости и количество нерастворенного воздуха не изменяются в течение переходного процесса; отсутствуют
119
Направление 2. Проблемы и перспективы развития транспортного комплекса
_______________________________________________________________________________________
утечки рабочей жидкости; тормозную педаль в движение приводит автоматическое устройство, обеспечивающее точность входных параметров.
Работу гидравлической системы необходимо рассматривать на различных режимах ее работы [9]. Это дает нам возможность выявить различные неисправности с большей долей вероятности, так как одни неисправности не видны на одном режиме, а прослеживаются на других.В исследовании рассматривается четыре режима нажатия на педаль тормоза: T1 – время нажатия на педаль тормоза составляет 0,2 с; T2 – 0,7 с; T3 – 1,0 с; T4 – 1,4 с. Темпы воздействия на орган управления выбраны согласно экспериментальных исследований.
Как свидетельствуют результаты многочисленных исследований контрольные точки (рисунок 1), при различных неисправностях ГТЦ, перемещаются не только отначала координатна различное расстояние. Всестороннее рассмотрение рабочих процессов, протекающих в ГТЦ поможет определить диагностические параметры, обладающие достоверностью, однозначностью, стабильностью и информативностью. Воспользуемся следующими диагностическими параметрами: S1 – время t1 от начала нажатия на педаль тормоза до точки 1 начала движения второго поршня ГТЦ; S2 – время t2 от начала нажатия на педаль тормоза до точки 2 окончания движения второго поршня ГТЦ; S3 – время t1-t2 между точками 1 и 2 или время движения второго поршня ГТЦ; S4 – усилие F1 на педали тормоза в момент 1 начала движения второго поршня ГТЦ; S5 – усилие F2 на педали тормоза в момент 2 окончания движения второго поршня ГТЦ и S6 – разность усилий F1-F2.
Выберем диапазоны основных структурных параметров и критерия состояния тормозной жидкости: К1 – содержание воздуха в тормозной жидкости.
Диапазон изменения составляет от 0 до 20%. Пропуски в местах соединения тормозных трубок, шлангов, крепления заливного бачка и недостаточный уровень жидкости в гидроприводе способствуют проникновению воздуха в систему привода. Увеличение количества воздуха больше 20% приводит к явному проявлению неисправности, проваливание педали и плохое оттормаживание, что без труда определяется органолептическим методом мастером диагностом.
X2, X3 – изменение жесткости возвратной пружины первого и второго контура.
Примем изменение от 1888 Н/м до 1188 Н/м, на 20%. Изменение жесткости пружин в диапазоне от 0 до 20 % выбрано согласно экспериментальных исследований, проводимых на кафедре «Автомобильный транспорт», КГУ в рамках работы над диссертацией.
X4, X5 – износ уплотнительного кольца первого и второго контура. Износ кольца происходит от состояния «нового кольца» 4,7 мм до 4,4 мм, на 6,3%. Дальнейший износ не влияет на работу ГТЦ в связи с тем, что сила трения станет равна нулю, зазор между цилиндром и уплотнительным кольцом станет меньше зазора между установочным кольцом и поршнем. Давление создаваться не будет, вся тормозная жидкость из полости контура будет перепускаться в заливной бачек.
X6, X7 – увеличение (разбухание) уплотнительного кольца первого контура, изменяется от 4,7 мм до 5,1 мм, на 8,5%. Допускается нормативами изготовителей уплотнительных колец и тормозных жидкостей разбухание до 10% [10, 14]. При дальнейшем разбухании сила трения уплотнительного кольца о стенки цилиндра увеличивается вплоть до заклинивания поршня ГТЦ.
Управление тормозной системой происходит за счет давления жидкости создаваемого главным тормозным цилиндром от перемещения поршней в нем. В этом случае штоку первого поршня приложено входное усилие, которое является функцией от времени.
Была разработана математическая модель гидроцепи, с двумя отдельно сосредоточенными объемами жидкости,описывающаядинамические процессы, происходящие в такой цепи при известном режиме нажатия на педаль тормоза. Данную модель описывает система, состоящая из следующих нелинейных дифференциальных уравнений [5, 3]:
1 Уравнение движения первого поршня.
2 Уравнение движения второго поршня.
3 Уравнение движения поршня суппорта.
4 Уравнение движения поршня заднего тормозного цилиндра.
5 Уравнение баланса давлений первого контура.
6 Уравнение баланса давлений второго контура.
7 Уравнение мгновенных объемных расходов первого контура.
8 Уравнение мгновенных объемных расходов второго контура.
При рассмотрении динамических процессов брались в учет податливость гидропривода в сосредоточенных объемах жидкости, согласно схемы 2.
Детерминированная математическая модель не может быть решена аналитическим методом в общем случае. Исследовали ее числено, проводя компьютерный эксперимент [13]. Согласно особенностей решаемой задачи был разработан алгоритм решения системы алгебраических и дифференциальных уравнений с введением уже выбранных изменений структурных параметров.
Алгоритм работы составлялся с учетом возможности его реализации на ЭВМ в диалоговом режиме работы. Для обеспечения допустимого уровня точности дифференциальные уравнения
120
ОБРАЗОВАНИЕ. ТРАНСПОРТ. ИННОВАЦИИ. СТРОИТЕЛЬСТВО
Сборник материалов III Национальной научно-практической конференции
_______________________________________________________________________________________
решаются с помощью метода Рунге – Кутты 4 порядка. Этот метод имеет четвёртый порядок
точности.
Работа программы разбита на несколько расчётных блоков.
Вблоке 1 производится ввод исходных данных, необходимых для проведения расчетов. Идентификаторы, наименование и числовые значения переменных, используемых в качестве исходных данных. Значения переменных, характеризующих конструкцию автомобиля, брались характерными для автомобиля ВАЗ 21213 [4].
Во втором блоке производим ввод начальных условий для расчета, необходимых для запуска расчета численным методом. После ввода всех данных производится расчет постоянных величин и начальных условий для моделирования. К недостающим начальным условиям относятся площади и объёмы полостей главного и рабочих тормозных цилиндров, трубок, шлангов. На данном этапе производится ввод структурных параметров, с помощью диалогового окна, и вывод начальных условий расчета в таблицу.
После введения и внесения всех необходимых данных для проведения расчета, переходим к телу основной программы, в которой осуществляется цикл до конечного условия, по времени окончания процесса. Все характеристики вычисляются отдельно, с помощью подпрограмм. В основной программе указывается только порядок расчета и условия ограничивающие расчетные параметры.
Рассмотрим расчет основных характеристик. Блок 4. В данном блоке происходит формирование условия воздействия на педаль тормоза. Исходя из заданного оператором условия (время воздействия на педаль тормоза), программа выбирает уравнения расчета ускорения и усилия прилагаемого к органу управления тормозной системой.
Далее в блоке 5 происходит перерасчет динамических и силовых характеристик, с учетом воздействия вакуумного усилителя и системы рычагов, от предали тормоза к штоку ГТЦ.
С расчета шестого блока уже используются значения скоростей первого и второго поршня, расчетные значения, меняющиеся с каждым шагом цикла, в зависимости от расчета системы дифференциальных уравнений. Тут производится определение инерциальных масс гидравлической системы, приведённых к первому и второму поршню управляющего устройства гидравлической тормозной системы.
Вседьмом блоке производится расчет сил трения уплотнительных колец главного и рабочих цилиндров тормозной системы. Расчет производится с поправками на силу терния покоя, силу трения скольжения и расчетное давление в контурах гидроцилиндров. Сила трения в примененном варианте разделяется на две составляющие: сила трения от сжатия уплотнительного кольца, и сила трения от воздействия давления на уплотнительное кольцо. Расчет сил терния применяется при расчете структурных параметров X4, X5, X6, X7. В случае первых двух сила трения уменьшается от снижения давления сжатия уплотнительного кольца, за счет уменьшения размеров (износ). Во втором же, наоборот увеличение размеров, увеличение силы трения вплоть до заклинивания поршней ГТЦ.
Восьмой блок характеризует процессы, происходящие при увеличении зазоров между уплотнительными кольцами и стенками цилиндров – диагностический параметр износ колец X4, X5. От увеличении зазора увеличивается расход жидкости через образовавшуюся щель и снижается сила демпфирования.
Девятый блок уравнений задает время начала движения поршней ГТЦ с фиксированием плавающего поршня предварительно сжатой пружиной. Это определяется балансом сил, воздействующих на поршень и его реакцию на опору, как реакция опоры становится ровна нуля поршень начинает движение. В тандеме с расчетом реакций опор идет расчет сил от воздействия пружин тормозных контуров, подпружинивающих поршни главного цилиндра. Снижение жесткости этих пружин в процессе эксплуатации оказывает влияние на исправную работу тормозной системы и,
внашем случае, оценивается структурными параметрами X2 и X3.
После подготовки всех необходимых данных для расчета системы дифференциальных и алгебраических уравнений подходим к блоку 10. Здесь происходит решение системы уравнений, которая разделяется ограничивающими условиями на несколько этапов: движение первого поршня до начала движения всех остальных элементов тормозной системы; начало движения и движение поршней суппортов после преодоления сил трения; начало движения и движение поршня второго тормозного контура; начало движения и движение поршней задних тормозных механизмов; остановка поршней задних тормозных механизмов и второго поршня ГТЦ; остановка поршней суппортов и поршня первого тормозного контура и нарастание тормозной силы на тормозных механизмах, зависящего от нарастания усилия воздействия на педаль тормоза. На различных режимах влияние структурных параметров проявляется по-разному, но К1 (завоздушенность тормозной жидкости) оказывает воздействие на всех режимах. Воздействие этого параметра оценивается функцией, влияющей на давления в системе.
В 11 блоке производится нахождение силы противления нажатия на педаль тормоза в зависимости от времени. Находится усилие из разности управлявшего воздействия на органе
121

Направление 2. Проблемы и перспективы развития транспортного комплекса
_______________________________________________________________________________________
управления тормозной системой и баланса всех сил на шток главного тормозного цилиндра. В дальнейшем силовая характеристика преобразуется через группу уравнений в силу противления.
После расчета всех характеристик производится вывод данных расчета не рабочий лист Excel, блок 12. По данным моделирования строятся зависимости, затем оценивается воздействия изменений структурных параметров на диагностические.
После проведения цикла расчетов, время Т причащается на величину dt и сравнивается с максимальным значением, если Т меньше минимального значения, то программа переходит к следующему циклу расчетов, а при превышении значения оканчивает работу.
Расчет всех характеристик производится после преобразования формул к виду среды программирования VBA, встроенную в программный продукт MicrosoftOffice профессиональный плюс
2013, Excel [8]. Моделирование проводится на ПЭВМ Intel (R) Core ™ i3-4130 CPU@ 3.40 GHz/2х4Gb DDR3/ ASUSHD7750 Series.
На рисунке 3 приведено диалоговое окно программы моделирования. В данном окне производится ввод неисправностей в рабочие процессы главного тормозного цилиндра.
В соответствии с задачами данного исследования, входными параметрами модели являлись: -сила и ускорение воздействия на педаль тормоза; -состояние тормозной жидкости (процент содержания воздуха); -жесткость пружин ГТЦ; -состояние уплотнительных колец ГТЦ.
Рисунок 3 – Диалоговое окно программы моделирования см
В процессе компьютерного моделирования определялись динамические и силовые характеристики элементов гидравлической тормозной системы, управляющиммеханизмом которой является двухконтурный тормозной цилиндр с фиксированием плавающего поршня предварительно сжатой пружиной.Обработка и анализ результатов моделирования проводились с использованием
Excel 2013 и Statistica 13 Trial 64-bit.
Сравнение экспериментальных данных с теоритическими показало, что средняя погрешность составляет 1,42%. Из чего можно заключить, что математическая модель – адекватна и может использоваться при дальнейших исследованиях.
После проведения математическогомоделирования с оценкой чувствительности, выбранных диагностических параметров, и обоснованием их сочетания для постановки диагноза был произведен выбор оптимального комплекта диагностических параметров и режимов воздействия на педаль тормоза. Отклонения в работе ГТЦ можно выявить однозначно по изменению определенных диагностических параметров на определенных режимах.
Проведенное исследование показывает, что новый метод диагностирования имеет право на существование. Использование его возможно с применением штатного тормозного стенда без внедрения дополнительного оборудования, только с доработкой программного обеспечения, так же возможно применение встроенной диагностики. Своевременное определение конкретной неисправности в главном тормозном цилиндре облегчит труд автослесарей, снизит простои автомобилей в ремонте и, самое главное, поможет частично предотвратить внезапные отказы тормозной системы в эксплуатации. Что в свою очередь снизит количество дорожно-транспортных происшествий, спасет жизни водителей и пассажиров, а также избавит их от травм.
122
ОБРАЗОВАНИЕ. ТРАНСПОРТ. ИННОВАЦИИ. СТРОИТЕЛЬСТВО
Сборник материалов III Национальной научно-практической конференции
_______________________________________________________________________________________
Библиографический список
1.Сведения о показателях состояния дорожного движения // ГИБДД: официальный сайт. – URL:http://stat.gibdd.ru/(дата обращения: 22.03.2020).
2.Мирошников, Л.В. Диагностирование технического состояния автомобилей на автотранспортных предприятиях /Л.В. Мирошников, А.П. Болдин, В.И. Пал. – Москва: Транспорт, 1977. – 263с.
3.Шуклинов, С.Г. Теоретические основы адаптивного управления торможением колесных машин: дис. … доктора техн. наук: 05.22.02 / С. Н. Шуклинов; науч. рук. А. Н. Туренко; ХНАДУ, ХНАДУ.– Харьков: ХНАДУ, 2013. – 428с.
4.ВАЗ-21213 (Нива вседорожник) – руководство по техническому обслуживанию и ремонту // sinref.ru -
библиотека онлайн: - URL: https://sinref.ru/avtomobili/VAZ/015_vaz_21213_niva_vsedorojnik/000.html (дата обращения: 22.03.2020).
5.Метлюк, Н.Ф. Динамика пневматических и гидравлических приводов автомобилей / Н.Ф. Метлюк, В.П. Автушенко. – Москва: Машиностроение, 1980. – 231 с.
6.Бородин, А. Л. Разработка метода диагностирования гидравлических тормозных систем автотранспортных средств на режимах служебного торможения / А. Л. Бородин, В. И. Васильев, А. В. Шарыпов, А. П. Черепанов // Вестник Курганской ГСХА: Технические науки. – №4 (16) . – Курган, 2015.– С. 29-32.
7.Говорущенко, Н. Я. Диагностирование технического состояния автомобилей / Н. Я. Говорущенко. - Москва: Транспорт, 1970. – 256 с.
8.Уокенбах, Дж. Excel 2013: профессиональное программирование на VBA / Дж. Уокенбах– Москва: Диалектика, 2017. – 960 с.
9.Техническая диагностика гидравлических приводов / Т. В. Алексеева, В. Д. Бабанская, Т. М. Баштам[и др.]; ред. Т. М. Башта. - Москва: Машиностроение, 1989.– 264 с.
10.Руководство по кольцам круглого сечения. – Москва: ParkerHannifin LLC. EngineeredMaterialsGroupEurope, 2016. – 165 с.
11.Петин, Ю. П. Исследование возможности диагностирования тормозных систем автомобилей в дорожных условиях по изменению статистической информации о перемещении педали тормоза и приводном усилии: авторефератдис. ... канд. техн. наук: 05.22.11 / Ю. П. Петин; науч. рук. Л. В. Мирошников.–Москва, 1974. – 22 с.
12.ТР ТС 018/2011.Технический регламент таможенного союза "О безопасности колесных транспортных средств" № №877: [принят 9 декабря 2011г.]: Собрание актов Президента и Правительства Российской Федерации. – 2011. – 319 с.
13.Математическое и компьютерное моделирование. Вводный курс: Учебное пособие. – Изд. 4-е испр. - Москва: Едиториал УРСС, 2004. – 152 с.
14.BOSCH. Automotive handbook. - 5th edition изд. –Москва: ЗАО "КЖИ "Зарулем", 2004. – 992 с.
123