
- •Раздел 1. Теоретические основы технологии производства летательных аппаратов. Глава 1. Особенности самолетостроения. §1. Особенности летательного аппарата как объекта производства.
- •§2. Структура предприятия, его производственный процесс, объем и программа выпуска самолетов.
- •§3. Понятие о технологии самолетостроения и технологическом процессе.
- •§4. Типы производства.
- •Глава 2. Технологические методы обеспечения качества самолета как объекта производства и эксплуатации. §1. Понятие и эволюция «качества продукции». Управление качеством.
- •§2. Показатели качества.
- •§3. Структура процесса формирования качества изделия.
- •Стоимость устранения несоответствия
- •Эксплуатация изделия.
- •Утилизация изделия. §4. Источники получения корректирующей информации.
- •§5. Технологические методы обеспечения заданного ресурса.
- •§6. Технологические методы создания конструкций минимальной массы.
- •§7. Общие принципы обеспечения заданной точности изготовления и сборки изделий. Взаимозаменяемость и точность изготовления как показатели качества.
- •Точность увязки размеров между собой.
- •Методы увязки размеров.
- •Базы изделий и их роль в обеспечении заданной точности.
- •Группы размеров ла, требующих согласования (которые необходимо увязывать)
- •§8. Плазово-шаблонный метод увязки (пшм) заготовительной и сборочной оснастки.
- •Теоретические плазы.
- •Основные шаблоны и конструктивные плазы.
- •Производственные шаблоны
- •§9. Основные методы технического контроля качества. Значение технического контроля в обеспечении высокого качества.
- •Виды технического контроля.
- •Ким (Контрольно-Измерительные Машины)
- •Глава 3. Экономическая эффективность технологических процессов.
- •§1. Технологические методы повышения производительности труда.
- •Условия обеспечения максимальной производительности труда.
- •§2. Технологические методы снижения себестоимости продукции.
- •Технологическая себестоимость
- •Технологические методы снижения технологической себестоимости.
- •Глава 4. Основные направление механизации и автоматизации технологических процессов.
- •§1. Системы организации производства.
- •§2. Автоматизированное производство.
- •§2. Используемые сплавы. Алюминиевые сплавы
- •Титановые сплавы
- •Высокопрочные сплавы
- •Интерметаллидные сплавы
- •Композиционные материалы
- •Покрытия
- •§3. Характерные полуфабрикаты и заготовки, используемые при изготовлении деталей ла.
- •§4. Классификация технологических процессов. Заготовительно-обработочные процессы.
- •Глава 6. Процессы формообразования разделением полуфабриката а удалением лишнего материала. §1. Классификация процессов и припуски на обработку.
- •§2. Механические процессы.
- •Резка ножницами и штампами.
- •Обработка резанием.
- •1) Корпус хона; 2) абразивный брусок; 3) деталь.
- •§3. Электрические процессы.
- •§4. Электрохимические процессы.
- •§5. Химические процессы.
- •§6. Акустические процессы.
- •Глава 7. Процессы формообразования холодным деформированием.
- •§1. Листовая штамповка.
- •Обтяжка
- •Вытяжка
- •Рельефная формовка
- •Глава 8. Технологическая оснастка для изготовления деталей.
- •Базирующие элементы:
- •§1. Методика проектирования технологических процессов.
- •§2. Проектирование специальных станочных приспособлений.
- •§3. Проектирование заготовительно-штамповочной оснастки.
- •§4. Проектирование технологических процессов.
- •§5. Современные тенденции в области проектирования процессов изготовления деталей.
- •§6. Комплексный метод проектирования технологических процессов.
- •Раздел 3. Сборочные процессы. Глава 9. Основные понятия технологии сборки летательных аппаратов.
- •§1. Технологическая характеристика процессов сборки
- •§2. Требования к точности обводов агрегатов и их взаимному положению.
- •§3. Схемы сборочных процессов.
- •§4. Взаимосвязь конструкции и технологии.
- •§5. Пути повышения эффективности сборочных процессов
- •§6. Методы сборки и сборочные базы.
- •Сборочные базы при сборке в приспособлениях.
- •Сборка по базе «поверхность каркаса».
- •Сборка в приспособлении с базой «наружная поверхность обшивки».
- •Сборка в приспособлении с базой «внутренняя поверхность обшивки».
- •Сборка с базированием по координатно-фиксирующим отверстиям (кфо).
- •Сборка с пригонкой по месту.
- •Современные технологии агрегатно-сборочного производства.
- •Сущность метода бесплазовой увязки размеров.
- •Электронное описание – основа бесплазовой увязки размеров.
- •Преимущества и недостатки различных методов сборки.
- •Глава 10. Конструктивно-технологическая характеристика соединений, применяемых в конструкциях самолетов. Виды и технологические характеристики соединений
- •Обобщенная схема технологических процессов выполнения соединения.
- •Силовые схемы соединений.
- •Показатели качества соединений.
- •Технологические методы соединения болтовых высокоресурсных соединений
- •Технологический процесс клепки.
- •Технология выполнения высокоресурсных клеевых и клеесварных соединений.
- •Изготовление конструкций с сотовым заполнителем.
- •Изготовление сотового заполнителя.
- •Контроль качества сотовых агрегатов.
- •Изготовление узлов с заполнителем в виде пенопласта.
- •Процессы выполнения комбинированных соединений.
- •Точность и технико-экономические показатели различных методов базирования.
- •Раздел 4. Теория и практика разработки автоматизированных систем технологической обработки. Глава 11.
- •§1. Понятие о системах сао/сам/сае (сквозные сапр).
- •§2. Анализ современных подходов к разработке сапр-тп. Обзор разработок алгоритмического комплекса сапр-тп.
- •§3. Автоматизированная технологическая подготовки производства в авиастроении.
- •§4. Организационное обеспечение сапр
- •§5. Разработка сапр-тп на базе идей типизации
- •§6. Стратегия, концепция, принципы cals
- •§7. Этапы жизненного цикла изделий и развитие cals.
- •§8. Причины появления и принципы cals.
- •Глава 12. Автоматизация подготовки производства в концепции cals-технологий. §1. Основные принципы.
- •§2. Реализация процессов в системе pdm.
- •Основные характеристики
- •§3. Постановка задачи классификации объектов.
- •§4. Алгоритмы формирования классификационных группировок.
- •Глава 13. Задачи оптимального проектирования в сапр технологического назначения.
- •§1. Математические модели оптимального проектирования.
- •§2. Методы решения задач оптимального проектирования. Методы классического анализа.
- •Метод множителей Лагранжа.
- •Динамическое программирование.
- •Линейное программирование.
- •Затраты времени на обработку одного изделия для каждого из типов оборудования
- •Метод ветвей и границ.
- •Глава 14. Проектирование оптимальных технологических процессов для гибкого автоматизированного производства.
- •Глава 15. Автоматизация проектирования процессов сборки. Математическая модель сборки и ее свойства.
- •Список литературы
§3. Структура процесса формирования качества изделия.
Заданный уровень качества закладывается при проектировании изделия, реализуется при его изготовлении и поддерживается различными методами на всех этапах жизни изделия:
Разработка технического задания (ТЗ), в котором определяются основные тактико-технические требования. ТЗ разрабатывают организации, наиболее полно изучающие и обобщающие требования заказчика. Маркетинговые изделия определяют потребность какого-либо летательного аппарата. ТЗ разрабатывают различные институты, которые моделируют различные ситуации, в которых применяются различные летательные аппараты. Определяют состав и требования к летательному аппарату.
Как раньше было:






Проектирование
ЦК КПСС
ТЗ
Производство
Эксплуатация



Оформляется кредит в банке
Поиск возможных потребителей
Тактико-технические требования
Как сейчас:

Маркетинг




Эксплуатация
Производство
Проектирование
ТЗ
Разработка проекта изделия на основе требования ТЗ. Законченный проект представляет собой совокупность информации, полностью определяющей конструкцию будущего изделия и зафиксированная на различных носителей.
Технологическая подготовка производства летательного аппарата. На этом этапе реализуется (формируется) программа материализации изделия, которая оформляется в форме различной документации на изготовление изделия.
10000
Стоимость устранения несоответствия
Производство изделия. Задача состоит в точном воспроизведении летательного аппарата в соответствии с программой и информацией, предусмотренными технологической информацией.
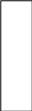
1000

100

10

1





Технологическая подготовка производства
Производство
Эксплуатация
Этапы жизненного цикла изделия
Проектирование
ТЗ
Рис. 2.5. График зависимости стоимости устранения несоответствия стандартам качества от этапа жизненного цикла изделия.
Испытания. Проверка реализации конструкции летательного аппарата и его технических возможностей.
Эксплуатация изделия.
Утилизация изделия. §4. Источники получения корректирующей информации.
Эксплуатация изделий лидером – форсированная эксплуатация.

Массовая эксплуатация


Проектирование
Производство

Эксплуатация лидером
Рис. 2.6. Схема получения корректирующей информации.
Натурные (летные испытания) – жестко соответствуя программам полета.
Стендовые испытания – на различных стендах испытываются различные части ЛА
Информационное и математическое моделирование – использование различные средств (проектирование, отражения) на которых определяются несоответствия.
§5. Технологические методы обеспечения заданного ресурса.
Под ресурсом понимаемся число часов полета до предельного состояния, оговоренного в технической документации.
Величина ресурса в основном определяется усталостной прочностью конструкции.
Технология изготовления деталей и сборки узлов, агрегатов и систем самолетов оказывают важное, а часто и решающее влияние на усталостную прочность. Это влияние реализуется через изменение свойств и напряженно-деформированного состояния материала элементов конструкции, происходящее при их изготовлении, с помощью различных технологических процессов или при изменении режимов выполнения одного и того же технологического процесса.
При изготовлении деталей с помощью разных способов резания в местах обработки образуется поверхностный слой, отличный по своим свойствам от основного металла.
Глубина
этого слоя зависит от свойств материала,
вида и режимов обработки и колеблется
от 0,05 мм до 0,6 мм, а иногда и больше (
м и
м соответственно).
Состояние поверхностного слоя характеризуется величиной и направлением неровностей, величиной и глубиной наклепа величиной, знаком и глубиной залегания остаточных напряжений химическим составом и структурой металла
Практика показывает, что при хорошем качестве основного металла (отсутствие пустот, внутренних трещин и др.) усталостное разрушение металлических конструкций начинается с поверхностных слоев металла.
Поэтому состояние поверхностного слоя прямо влияет на усталостную прочность конструкции.
Неровность поверхности деталей характеризуется волнистостью и шероховатостью.
Волнистость препятствует плотному прилеганию соединяемых элементов конструкции друг к другу. В местах контакта происходит интенсивное истирание (износ) материала, вследствие чего именно с этих мест начинаются усталостные разрушения.
Шероховатость характеризует микрогеометрию поверхности и образуется как результат взаимодействия инструмента и обрабатываемого материала. Величина шероховатости определяется видом (точение, фрезерование, шлифование и др.) и режимами (скорость, глубина резания и величина подачи) обработки и зависит существенно от жесткости системы станок – приспособление – инструмент – деталь (СПИД).
Особенно опасными с точки зрения усталостной прочности являются следы обработки, расположенные перпендикулярно направлению действия внешних усилий. В этом случае риска от обработки является концентратором напряжений, может стать местом возникновения трещины, приводящей к преждевременному разрушению конструкции.
Повышение чистоты поверхности, как правило, существенно увеличивает усталостную прочность конструкции. Особенно тщательно следует обрабатывать поверхности деталей из высокопрочных материалов (В95, ЗОХГСНА и др.),
Упрочнение (наклеп) поверхностного слоя является следствием совместного воздействия упругопластических деформаций и местного нагрева, возникающих в зоне резания.
Механические характеристики (пределы упругости, текучести, прочности и твердости) наклепанного слоя выше, чем основного металла. Вместе с тем уменьшается его пластичность, повышается хрупкость.
Меняются и физические свойства металла поверхностного слоя по сравнению с основной его массой: увеличивается электрическое сопротивление, уменьшается магнитная проницаемость.
Наклеп
поверхностного слоя характеризуется
его величиной
,
степенью
и глубиной
.
При обычных режимах резания глубина наклепа при обработке среднепрочных сталей и алюминиевых сплавов не превышает 0,1. ..0.2 мм. При большей глубине резания и больших подачах глубина наклепа достигает 0, 5... 1,0 мм.
Степень наклепа определяется как отношение наибольшей величины наклепа поверхностного слоя к твердости основной массы металла:
Для
обычных условий резания
Чрезмерная величина наклепа может привести к разрушению поверхностного слоя, которое может послужить местом возникновения усталостной трещины.
Упрочнение поверхностного слоя, при котором сохраняются его пластические свойства, способствует повышению усталостной прочности конструкции.
Остаточные
напряжения
,
которые образуются в поверхностном
слое, оказывают очень большое влияние
на усталостную прочность.
Так, при внешних растягивающих нагрузках остаточные напряжения сжатия снижают суммарные напряжения в конструкции и тем повышают ее усталостную прочность.
Различают три рода остаточных напряжений: напряжения первого рода или микронапряжения, охватывающие области, соизмеримые по объему с размерами детали; напряжения второго рода или микронапряжения, распределяющиеся в объемах одного или нескольких зерен металла; напряжения третьего рода или субмикроскопические напряжения, проявляющие свои влияния в пределах атомной решетки.
Наибольшее влияние на усталостную прочность оказывают напряжения первого рода. Вместе с тем выбор варианта и режимов обработки оказывает наибольшее влияние на характер и величину именно микронапряжений.
На образование , существенно влияют режимы обработки и геометрии инструмента, а также условия охлаждения при резании.
Величина остаточных напряжений часто соизмерима, а иногда и превосходит напряжения от внешних нагрузок, достигая напряжений предела прочности материала.
Так,
при точении среднепрочной легированной
стали они достигают 500...600 Па (50...60
),
алюминиевых сплавов-150...200 Па (15...20
).
Существенное влияние на измерение ресурса оказывают также режимы и виды процессов термической обработки, образования защитных покрытий, выполнения соединений, сборки узловой агрегатов.