
- •Раздел 1. Теоретические основы технологии производства летательных аппаратов. Глава 1. Особенности самолетостроения. §1. Особенности летательного аппарата как объекта производства.
- •§2. Структура предприятия, его производственный процесс, объем и программа выпуска самолетов.
- •§3. Понятие о технологии самолетостроения и технологическом процессе.
- •§4. Типы производства.
- •Глава 2. Технологические методы обеспечения качества самолета как объекта производства и эксплуатации. §1. Понятие и эволюция «качества продукции». Управление качеством.
- •§2. Показатели качества.
- •§3. Структура процесса формирования качества изделия.
- •Стоимость устранения несоответствия
- •Эксплуатация изделия.
- •Утилизация изделия. §4. Источники получения корректирующей информации.
- •§5. Технологические методы обеспечения заданного ресурса.
- •§6. Технологические методы создания конструкций минимальной массы.
- •§7. Общие принципы обеспечения заданной точности изготовления и сборки изделий. Взаимозаменяемость и точность изготовления как показатели качества.
- •Точность увязки размеров между собой.
- •Методы увязки размеров.
- •Базы изделий и их роль в обеспечении заданной точности.
- •Группы размеров ла, требующих согласования (которые необходимо увязывать)
- •§8. Плазово-шаблонный метод увязки (пшм) заготовительной и сборочной оснастки.
- •Теоретические плазы.
- •Основные шаблоны и конструктивные плазы.
- •Производственные шаблоны
- •§9. Основные методы технического контроля качества. Значение технического контроля в обеспечении высокого качества.
- •Виды технического контроля.
- •Ким (Контрольно-Измерительные Машины)
- •Глава 3. Экономическая эффективность технологических процессов.
- •§1. Технологические методы повышения производительности труда.
- •Условия обеспечения максимальной производительности труда.
- •§2. Технологические методы снижения себестоимости продукции.
- •Технологическая себестоимость
- •Технологические методы снижения технологической себестоимости.
- •Глава 4. Основные направление механизации и автоматизации технологических процессов.
- •§1. Системы организации производства.
- •§2. Автоматизированное производство.
- •§2. Используемые сплавы. Алюминиевые сплавы
- •Титановые сплавы
- •Высокопрочные сплавы
- •Интерметаллидные сплавы
- •Композиционные материалы
- •Покрытия
- •§3. Характерные полуфабрикаты и заготовки, используемые при изготовлении деталей ла.
- •§4. Классификация технологических процессов. Заготовительно-обработочные процессы.
- •Глава 6. Процессы формообразования разделением полуфабриката а удалением лишнего материала. §1. Классификация процессов и припуски на обработку.
- •§2. Механические процессы.
- •Резка ножницами и штампами.
- •Обработка резанием.
- •1) Корпус хона; 2) абразивный брусок; 3) деталь.
- •§3. Электрические процессы.
- •§4. Электрохимические процессы.
- •§5. Химические процессы.
- •§6. Акустические процессы.
- •Глава 7. Процессы формообразования холодным деформированием.
- •§1. Листовая штамповка.
- •Обтяжка
- •Вытяжка
- •Рельефная формовка
- •Глава 8. Технологическая оснастка для изготовления деталей.
- •Базирующие элементы:
- •§1. Методика проектирования технологических процессов.
- •§2. Проектирование специальных станочных приспособлений.
- •§3. Проектирование заготовительно-штамповочной оснастки.
- •§4. Проектирование технологических процессов.
- •§5. Современные тенденции в области проектирования процессов изготовления деталей.
- •§6. Комплексный метод проектирования технологических процессов.
- •Раздел 3. Сборочные процессы. Глава 9. Основные понятия технологии сборки летательных аппаратов.
- •§1. Технологическая характеристика процессов сборки
- •§2. Требования к точности обводов агрегатов и их взаимному положению.
- •§3. Схемы сборочных процессов.
- •§4. Взаимосвязь конструкции и технологии.
- •§5. Пути повышения эффективности сборочных процессов
- •§6. Методы сборки и сборочные базы.
- •Сборочные базы при сборке в приспособлениях.
- •Сборка по базе «поверхность каркаса».
- •Сборка в приспособлении с базой «наружная поверхность обшивки».
- •Сборка в приспособлении с базой «внутренняя поверхность обшивки».
- •Сборка с базированием по координатно-фиксирующим отверстиям (кфо).
- •Сборка с пригонкой по месту.
- •Современные технологии агрегатно-сборочного производства.
- •Сущность метода бесплазовой увязки размеров.
- •Электронное описание – основа бесплазовой увязки размеров.
- •Преимущества и недостатки различных методов сборки.
- •Глава 10. Конструктивно-технологическая характеристика соединений, применяемых в конструкциях самолетов. Виды и технологические характеристики соединений
- •Обобщенная схема технологических процессов выполнения соединения.
- •Силовые схемы соединений.
- •Показатели качества соединений.
- •Технологические методы соединения болтовых высокоресурсных соединений
- •Технологический процесс клепки.
- •Технология выполнения высокоресурсных клеевых и клеесварных соединений.
- •Изготовление конструкций с сотовым заполнителем.
- •Изготовление сотового заполнителя.
- •Контроль качества сотовых агрегатов.
- •Изготовление узлов с заполнителем в виде пенопласта.
- •Процессы выполнения комбинированных соединений.
- •Точность и технико-экономические показатели различных методов базирования.
- •Раздел 4. Теория и практика разработки автоматизированных систем технологической обработки. Глава 11.
- •§1. Понятие о системах сао/сам/сае (сквозные сапр).
- •§2. Анализ современных подходов к разработке сапр-тп. Обзор разработок алгоритмического комплекса сапр-тп.
- •§3. Автоматизированная технологическая подготовки производства в авиастроении.
- •§4. Организационное обеспечение сапр
- •§5. Разработка сапр-тп на базе идей типизации
- •§6. Стратегия, концепция, принципы cals
- •§7. Этапы жизненного цикла изделий и развитие cals.
- •§8. Причины появления и принципы cals.
- •Глава 12. Автоматизация подготовки производства в концепции cals-технологий. §1. Основные принципы.
- •§2. Реализация процессов в системе pdm.
- •Основные характеристики
- •§3. Постановка задачи классификации объектов.
- •§4. Алгоритмы формирования классификационных группировок.
- •Глава 13. Задачи оптимального проектирования в сапр технологического назначения.
- •§1. Математические модели оптимального проектирования.
- •§2. Методы решения задач оптимального проектирования. Методы классического анализа.
- •Метод множителей Лагранжа.
- •Динамическое программирование.
- •Линейное программирование.
- •Затраты времени на обработку одного изделия для каждого из типов оборудования
- •Метод ветвей и границ.
- •Глава 14. Проектирование оптимальных технологических процессов для гибкого автоматизированного производства.
- •Глава 15. Автоматизация проектирования процессов сборки. Математическая модель сборки и ее свойства.
- •Список литературы
Условия обеспечения максимальной производительности труда.
Для обеспечения максимальной производительности технолог должен выполнять следующее условия:
Выбирать рациональную структуру технологического процесса и наиболее прогрессивные процессы обработки и сборки. Нужно обращать внимание на объемы производства. Нужно думать, чтобы затраты окупились.
Применять наиболее высокопроизводительное и автоматизированное оборудование и оснастку. Необходимо всегда помнить об объеме производства.
Максимально использовать технические возможности оборудования и оснастки, обеспечивая их полную загрузку по мощности и во времени. Неоднозначный тезис.
Наиболее рационально использовать квалификацию и время рабочего, применяя многостаночное обслуживание, и, где это возможно, самостоятельную наладку оборудования рабочим. (Использовать по той квалификации, которую имеет рабочий. Нельзя ставить высококвалифицированного рабочего на легкую работу.)
Пути (возможности) сокращения основного времени обработки:
Сокращение количества проходов (i). Желательно за 1 проход делать.
Повышение скорости обработки.
Увеличение подачи.
Сокращение врезания и перебега режущего инструмента.





Рис. 3.2. Врезание и перебег инструмента.
Использовать специальные многоместные приспособления, устанавливается несколько деталей. Фрезерует последовательно несколько штук.
Когда заканчивается фрезерование одной детали, она начинает фрезеровать следующую. Длина врезания и перебега будет в 3 раза меньше. Эффективно в том случае, если близко находятся детали. Если их раздвинуть, то не будет никакого эффекта.
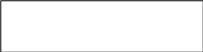




Призма
Фреза
S



Рис. 3.3. Вид сверху.
-
длина
перебега.
Многоинструментальная обработка:







Сверло

Резец
Рис.3.4. Многоинструментальная обработка.
Обработать панельки и просверлить отверстия. Делать это одновременно.
Уменьшение вспомогательного времени:
Сократить время на установку и закрепление детали. Применение механизированных и автоматизированных устройств (электрические пневматические зажимы).
Сокращение времени на управление оборудованием:
Сокращение количества ручек управление.
Концентрация органов управления в одной зоне (на пульте).
Переход от «ручек» к кнопкам.
Сокращать время на смену режущего оборудования: револьверные головки – приспособление у станка.
Сокращение времени на измерение. Применять станки настроечного типа.
Зона обработки
Совмещение вспомогательного времени с основным.
Зона смены обработки



Перемещается
Рис. 3.5. Схема совмещения вспомогательного и основного времен.
Сокращение времени на обслуживание рабочего места:
Сокращение времени на смену затупившегося режущего инструмента (применение высоко стойких режущих инструментов и быстродействующих зажимных устройств).
Сокращение подготовительно-заключительного времени (повышение качества изделий в партии).
Использование методов групповой технологии.
Сокращение подготовительно-заключительного времени. Чем больше количество изделий в партии, тем меньше время. Количество определяется запросов (сколько нужно). Как повысить размер партии? Делать наладки не на одну деталь, а на партию. Т.е. использовать методы групповой технологии деталей, которые обладают конструктивно-технологическими общностями.