
- •СОДЕРЖАНИЕ
- •ПРЕДИСЛОВИЕ
- •ВВЕДЕНИЕ
- •ГЛАВА 1. ЭЛЕКТРИЧЕСКОЕ ПОЛЕ
- •§1.1. Определение и изображение электрического поля
- •§ 1.2. Закон кулона. Напряженность электрического поля
- •§ 1.3. Потенциал. Электрическое напряжение
- •§ 1.4. Проводники в электрическом поле. Электростатическая индукция
- •§1.5. Диэлектрики в электрическом поле. Поляризация диэлектрика
- •§ 1.6. Электроизоляционные материалы
- •Газообразные диэлектрики.
- •Жидкие диэлектрики.
- •Твердые диэлектрики.
- •Твердеющие диэлектрики.
- •§ 1.7. Электрическая емкость. Плоский конденсатор
- •§ 1.8. Соединение конденсаторов. Энергия электрического поля
- •Параллельное соединение.
- •Последовательное соединение.
- •ГЛАВА 2 .ЭЛЕКТРИЧЕСКИЕ ЦЕПИ ПОСТОЯННОГО ТОКА
- •§ 2.1. Электрическая цепь
- •§ 2.2. Электрический ток
- •§ 2.3. ЭДС и напряжение
- •§ 2.4. Закон ОМА
- •§ 2.5. Электрическое сопротивление и проводимость
- •§ 2.6. Основные проводниковые материалы и проводниковые изделия
- •§ 2.7. Зависимость сопротивления от температуры
- •§ 2.8. Способы соединения сопротивлений
- •Параллельное соединение.
- •Последовательное соединение.
- •Смешанное соединение.
- •§2.9. Электрическая работа и мощность. Преобразование электрической энергии в тепловую.
- •§ 2.10. Токовая нагрузка проводов и защита их от перегрузок
- •§ 2.11. Потери напряжения в проводах
- •§ 2.12. Два режима работы источника питания
- •§ 2.13. Расчет сложных электрических цепей
- •Метод узловых и контурных уравнений.
- •Метод контурных токов.
- •Метод узлового напряжения.
- •§ 2.14. Нелинейные электрические цепи
- •Последовательное соединение.
- •Параллельное соединение.
- •ГЛАВА 3 ЭЛЕКТРОМАГНЕТИЗМ
- •§ 3.1. Характеристики магнитного поля
- •§ 3.2. Закон полного тока
- •§ 3.3. Магнитное поле прямолинейного тока
- •§3.4. Магнитное поле кольцевой и цилиндрической катушек.
- •§ 3.5. Намагничивание ферромагнитных материалов
- •§ 3.6. Циклическое перемагничивание
- •§ 3.7. Расчет магнитной цепи
- •Первый закон Кирхгофа.
- •Второй закон Кирхгофа.
- •Закон Ома.
- •§ 3.8. Электрон в магнитном поле
- •§3.9. Проводник с током в магнитном поле. Взаимодействие параллельных проводников с током
- •§ 3.10. Закон электромагнитной индукции
- •§ 3.11. ЭДС индукции в контуре
- •§ 3.12. Принцип Ленца
- •§ 3.13. Преобразование механической энергии в электрическую
- •§ 3.14. Преобразование электрической энергии в механическую
- •§3.15. Потокосцепление и индуктивность катушки
- •§ 3.16. ЭДС самоиндукции. Энергия магнитного поля
- •§ 3.17. ЭДС взаимоиндукции. Вихревые токи
- •ГЛАВА 4. ОСНОВНЫЕ ПОНЯТИЯ ПЕРЕМЕННОГО ТОКА
- •§4.1. Определение, получение и изображение переменного тока
- •§ 4.2. Параметры переменного тока
- •§ 4.3. Фаза переменного тока. Сдвиг фаз
- •§ 4.4. Изображение синусоидальных величин с помощью векторов
- •§ 4.5. Сложение и вычитание синусоидальных величин
- •§ 4.6. Поверхностный эффект. Активное сопротивление
- •ГЛАВА 5. ОДНОФАЗНЫЕ ЭЛЕКТРИЧЕСКИЕ ЦЕПИ
- •§ 5.1. Особенность электрических цепей
- •§ 5.2. Цепь с активным сопротивлением
- •Мгновенная мощность.
- •Средняя мощность.
- •§ 5.3. Цепь с индуктивностью
- •Мгновенная мощность.
- •Реактивная мощность.
- •§5.4. Цепь с активным сопротивлением и индуктивностью
- •Мгновенная мощность.
- •Средняя мощность.
- •Реактивная мощность.
- •Полная мощность.
- •§5.5. Цепь с емкостью
- •Мгновенная мощность.
- •Реактивная мощность.
- •§ 5.6. Цепь с активным сопротивлением и емкостью
- •Мгновенная мощность.
- •Средняя мощность.
- •Реактивная мощность.
- •§5.7. Цепь с активным сопротивлением, индуктивностью и емкостью
- •§ 5.8. Резонансный режим работы цепи
- •§ 5.9. Резонанс напряжений
- •§ 5.10. Разветвленная цепь. Метод проводимостей
- •§ 5.11. Резонанс токов
- •§ 5.12. Коэффициент мощности.
- •ГЛАВА 6. ТРЕХФАЗНЫЕ ЭЛЕКТРИЧЕСКИЕ ЦЕПИ
- •§6.1. Принцип получения трехфазной ЭДС. Основные схемы соединения трехфазных цепей
- •§6.2. Соединение трехфазной цепи звездой. Четырех и трехпроводная цепи
- •§ 6.3. Cоотношения между фазными и линейными напряжениями и токами при симметричной нагрузке в трехфазной цепи, соединенной звездой
- •§6.4. Назначение нулевого провода в четырехпроводной цепи
- •§6.5. Соединение нагрузки треугольником. Векторные диаграммы, соотношения между фазными и линейными токами и напряжениями
- •§6.6. Активная, реактивная и полная мощности трехфазной цепи. коэффициент мощности
- •§ 6.7. Выбор схем соединения осветительной и силовой нагрузок при включении их в трехфазную сеть
- •ГЛАВА 7. ТРАНСФОРМАТОРЫ
- •§7.1. Назначение трансформаторов и их применение
- •§7.2. Устройство трансформатора
- •§7.3. Формула трансформаторной ЭДС
- •§7.4. Принцип действия однофазного трансформатора. Коэффициент трансформации
- •§7.5. Трехфазные трансформаторы
- •§7.6. Aвтотрансформаторы и измерительные трансформаторы
- •§ 7.7. Cварочные трансформаторы
- •ГЛАВА 8. ЭЛЕКТРИЧЕСКИЕ МАШИНЫ ПЕРЕМЕННОГО ТОКА
- •§8.1. Вращающееся магнитное поле
- •Вращающееся магнитное поле двухфазного тока.
- •Графическое пояснение процесса образования вращающегося магнитного поля.
- •Вращающееся магнитное поле трехфазного тока.
- •§ 8.2. Устройство асинхронного двигателя
- •§ 8.3. Принцип действия асинхронного двигателя. Физические процессы, происходящие при раскручивании ротора
- •§8.4. Скольжение и частота вращения ротора
- •§8.5. Влияние скольжения на ЭДС в обмотке ротора
- •§8.6. Зависимость значения и фазы тока от скольжения и ЭДС ротора
- •§8.7. Вращающий момент асинхронного двигателя
- •§8.8. Влияние активного сопротивления обмотки ротора на форму зависимости вращающего момента от скольжения
- •§ 8.9. Пуск асинхронного двигателя
- •§8.10. Регулирование частоты вращения асинхронного двигателя
- •§8.11. КПД и коэффициент мощности асинхронного двигателя
- •§8.12. Однофазный асинхронный двигатель
- •§8.13. Синхронный генератор
- •§8.14. Синхронный двигатель
- •ГЛАВА 9. ЭЛЕКТРИЧЕСКИЕ МАШИНЫ ПОСТОЯННОГО ТОКА
- •§9.1. Устройство электрических машин постоянного тока. Обратимость машин
- •§9.2. Принцип работы машины постоянного тока
- •Генератор постоянного тока.
- •Двигатель постоянного тока.
- •§9.3. Понятие об обмотке якоря. Коллектор и его назначение
- •§9.4. ЭДС, индуцируемая в обмотке якоря
- •§9.5. Реакция якоря
- •§9.6. Коммутация и способы ее улучшения. Дополнительные полюсы
- •§9.7. Генераторы постоянного тока независимого возбуждения
- •§ 9.8. Генераторы с самовозбуждением
- •Генератор параллельного возбуждения.
- •Генератор последовательного возбуждения.
- •Генераторы смешанного возбуждения.
- •§9.9. Двигатели постоянного тока независимого и параллельного возбуждения. Вращающий момент
- •§9.10. Механическая и рабочие характеристики двигателей постоянного тока независимого и параллельного возбуждения
- •§9.11. Регулирование частоты вращения двигателей постоянного тока независимого и параллельного возбуждения
- •§9.12. Двигатели постоянного тока последовательного и смешанного возбуждения
- •ГЛАВА 10. ЭЛЕКТРИЧЕСКИЕ И МАГНИТНЫЕ ЭЛЕМЕНТЫ АВТОМАТИКИ
- •§10.1. Автоматы и автоматика
- •§10.2. Структура системы автоматического регулирования
- •§10.3. Устройства для измерения сигналов в автоматических системах
- •§10.4. Реле
- •§10.5. Магнитные усилители, их назначение и классификация
- •§10.6. Принцип действия дроссельного магнитного усилителя
- •§10.7. Принцип действия трансформаторного магнитного усилителя
- •§10.8. Влияние обратной связи на коэффициент усиления магнитного усилителя
- •§10.9. Дифференциальный магнитный усилитель с обмотками смещения
- •§10.10. Дифференциальный магнитный усилитель с обратной связью
- •§10.11. Магнитный усилитель, собранный по мостовой схеме
- •§10.12. Ферромагнитные стабилизаторы напряжения
- •ГЛАВА 11. ЭЛЕКТРИЧЕСКИЕ ИЗМЕРЕНИЯ И ПРИБОРЫ
- •§11.1. Сущность и значение электрических измерений
- •§11.2. Основные единицы электрических и магнитных величин в международной системе единиц
- •§11.3. Производные и кратные единицы
- •§11.4. Основные методы электрических измерении. Погрешности измерительных приборов
- •§11.6. Электроизмерительные приборы непосредственной оценки
- •§11.7. Приборы магнитоэлектрической системы
- •§11.8. Приборы электромагнитной системы
- •§11.9. Приборы электродинамической системы
- •§11.10. Цифровые приборы
- •§11.12. Расширение пределов измерения приборов непосредственной оценки
- •§11.13. Измерение мощности в трехфазных цепях
- •§11.14. Индукционный счетчик электрической энергии. Учет энергии в однофазных и трехфазных цепях
- •§11.15. Измерение сопротивлений
- •§11.16. Измерение сопротивлений с помощью моста постоянного тока
- •§11.17. Магнитоэлектрический осциллограф
- •ГЛАВА 12. ПЕРЕДАЧА И РАСПРЕДЕЛЕНИЕ ЭЛЕКТРИЧЕСКОЙ ЭНЕРГИИ
- •§12.1. Назначение и классификация электрических сетей, их устройство и графическое изображение
- •§12.2. Провода, кабели, электроизоляционные материалы в сетях напряжением до 1000В
- •§12.3. Электроснабжение промышленных предприятий
- •§12.4. Падение и потеря напряжения в линиях электроснабжения
- •§12.5. Расчет проводов по допустимой потере напряжения в линиях постоянного, однофазного и трехфазного тока
- •§12.6. Сопоставление двухпроводной однофазной системы передачи энергии с трехфазными системами по расходу цветного металла
- •§12.7. Расчет проводов по допустимому нагреву
- •§12.8. Плавкие предохранители
- •§12.9. Выбор плавких вставок
- •§12.10. Выбор площади сечения проводов в зависимости от установленных предохранителей
- •§12.11. Действие электрического тока на организм человека. Понятие о напряжении прикосновения. допустимые значения напряжения прикосновения
- •§12.12. Защитное заземление трехпроводных цепей трехфазного тока
- •§12.13. Защитное заземление четырехпроводных цепей трехфазного тока
- •§12.14. Устройство и простейший расчет заземлителей
- •ГЛАВА 13. ОСНОВЫ ЭЛЕКТРОПРИВОДА
- •§13.1. Понятие об электроприводе
- •§13.2. Нагревание и охлаждение электродвигателей
- •§13.3. Режимы работы электродвигателей. Выбор мощности
- •Длительный режим.
- •Кратковременный режим.
- •§13.4. Релейно-контакторное управление электродвигателями
- •Назначение релейно-контакторного управления.
- •Изображение схем релейно-контакторного управления.
- •Схема управления и защиты асинхронного двигателя с помощью реверсивного магнитного пускателя.
- •Схема автоматического пуска асинхронного двигателя с контактными кольцами.
- •§14.1. Общие сведения
- •§ 14.2. Электронная эмиссия
- •§14.3. Катоды электронных ламп
- •§14.4. Движение электронов в электрическом и магнитном полях
- •§14.5. Диоды
- •Параметры диодов.
- •Типы ламповых баллонов и система обозначений электронных ламп.
- •§14.6. Триоды
- •Устройство и принцип работы.
- •Характеристики триодов.
- •Параметры триодов.
- •Понятие о динамическом режиме работы триода.
- •Недостатки триода.
- •§14.7. Тетроды
- •§14.8. Пентоды. Лучевые тетроды
- •§14.9. Многоэлектродные и комбинированные лампы
- •ГЛАВА 15. ГАЗОРАЗРЯДНЫЕ ПРИБОРЫ
- •§15.1. Основные разновидности электрических разрядов в газе
- •§ 15.2. Газотрон
- •§ 15.3. Тиратрон
- •§15.4. Стабилитрон
- •§15.5. Газосветные сигнальные лампы и индикаторы
- •§15.6. Условные обозначения и маркировка газоразрядных приборов
- •ГЛАВА 16. ПОЛУПРОВОДНИКОВЫЕ ПРИБОРЫ
- •§16.1. Атомы
- •§16.2. Энергетические уровни и зоны
- •§16.3. Проводники, изоляторы и полупроводники
- •§16.4. Электропроводность полупроводников
- •§16.5. Электронно-дырочный переход
- •§16.6. Полупроводниковые диоды
- •§16.7. Биполярный транзистор
- •§16.8. Полевые транзисторы
- •№ 16.9. Тиристоры
- •§16.10. Области применения транзисторов и тиристоров
- •ГЛАВА 17. ФОТОЭЛЕКТРИЧЕСКИЕ ПРИБОРЫ
- •§17.1. Основные понятия и определения
- •§17.2. Электронные фотоэлементы с внешним фотоэффектом
- •§17.3. Фотоэлектронные умножители
- •§17.4. Фоторезисторы
- •§ 17.5. Фотодиоды
- •§17.6. Фототранзисторы
- •ГЛАВА 18ЭЛЕКТРОННЫЕ ВЫПРЯМИТЕЛИ
- •§18.1. Основные сведения о выпрямителях
- •§18.2. Однополупериодный выпрямитель
- •§18.3. Двухполупериодный выпрямитель
- •§18.4. Трехфазный выпрямитель
- •§18.5. Выпрямитель на тиристоре. Стабилизатор напряжения
- •§18.6. Сглаживающие фильтры. выпрямление с умножением напряжения
- •§19.1. Общие сведения
- •Классификация усилителей.
- •Основные технические характеристики усилителей.
- •§19.2. Предварительный каскад УНЧ
- •§19.3. Выходной каскад УНЧ
- •§19.4. Обратная связь в усилителях
- •§19.5. Межкаскадные связи. усилители постоянного тока
- •§19.6. Импульсные и избирательные усилители
- •ГЛАВА 20. ЭЛЕКТРОННЫЕ ГЕНЕРАТОРЫ И ИЗМЕРИТЕЛЬНЫЕ ПРИБОРЫ
- •§20.1. Общие сведения
- •§20.2. Транзисторный автогенератор типа
- •§20.3. Транзисторный автогенератор типа
- •§20.4. Генераторы линейно изменяющегося напряжения
- •§20.5. Мультивибратор
- •§20.6. Электронно-лучевые трубки
- •ЭЛТ с электростатическим управлением.
- •ЭЛТ с электромагнитным управлением.
- •§20.7. Электронный осциллограф
- •§20.8. Аналоговый электронный вольтметр
- •§20.9. Цифровой электронный вольтметр
- •§21.1. Общие сведения
- •§21.2. Гибридные интегральные микросхемы
- •§21.3. толстопленочные микросхемы
- •§21.4. Тонкопленочные микросхемы
- •§21.5. Фотолитография
- •§21.6. Полупроводниковые интегральные микросхемы
- •§21.7. Планарно-эпитаксиальная технология изготовления ИМС
- •§21.8. Элементы полупроводниковых микросхем и их соединение
- •§21.9. Применение интегральных микросхем
- •ГЛАВА 22. ЦИФРОВЫЕ ЭЛЕКТРОННЫЕ ВЫЧИСЛИТЕЛЬНЫЕ МАШИНЫ. МИКРОПРОЦЕССОРЫ И МИКРОЭВМ
- •§22.1. Системы счисления
- •§22.2. Перевод чисел из одной системы в другую
- •§22.3. Арифметические операции с двоичными числами
- •§22.4. Структурная схема цифровой электронной вычислительной машины
- •§22.5. Принцип действия ЦЭВМ
- •§22.6. Триггеры
- •§22.7. Логические элементы
- •§22.8. Счетчики импульсов
- •§22.9. Регистры
- •§22.10. Сумматор
- •§22.11. Арифметическое устройство
- •§22.12. Оперативное запоминающее устройство
- •§22.13. Внешние запоминающие устройства
- •§22.14. Устройство управления
- •§22.15. Устройство ввода информации
- •§22.17. Понятие о программировании
- •§22.18. Технические характеристики и применение ЦЭВМ
- •§22.19. Микропроцессоры
- •§22.20. Микрокалькуляторы
- •§22.21. Микроэвм
- •§22.22. Робототехника
- •КОНСУЛЬТАЦИИ
- •Консультации к главе 1
- •Консультации к главе 2
- •Консультации к главе 3
- •Консультации к главе 4
- •Консультации к главе 5
- •Консультации к главе 6
- •Консультации к главе 7
- •Консультации к главе 8
- •Консультации к главе 9
- •Консультации к главе 10
- •Консультации к главе 11
- •Консультации к главе 12
- •Консультации к главе 13
- •Консультации к главе 14
- •Консультации к главе 15
- •Консультации к главе 16
- •Консультации к главе 17
- •Консультации к главе 18
- •Консультации к главе 19
- •Консультации к главе 20
- •Консультации к главе 21
- •Консультации к главе 22
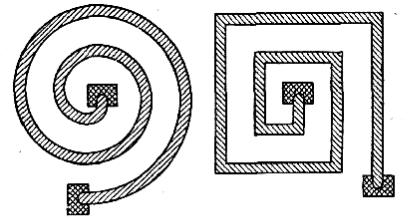
Карточка № 21.3 (302).
Толстопленочные микросхемы
Укажите: а) толщину подложки; |
б) толщину пленки |
а) 1мм; б) от 0,001 до 0,2 мм |
37 |
|||
тостопленочных микросхем |
|
|
|
|
|
|
|
|
а) 1 мкм; б) свыше 1 мкм |
|
67 |
||
|
|
|
|
|||
|
|
|
а) 1 мм; б) 150— 200 мкм |
|
97 |
|
|
|
|
|
|
||
Из какого материала изготовляются подложки |
Керамика |
|
|
127 |
||
пленочных микросхем? |
|
|
|
|
|
|
|
|
Кварц |
|
|
8 |
|
|
|
|
|
|
|
|
|
|
|
Стекло |
|
|
38 |
|
|
|
Из всех перечисленных |
|
98 |
|
Какие компоненты включаются в пасты, используемые |
Смесь |
порошков |
драгоценных |
128 |
||
для нанесения проводящих и резистивных |
толстых |
металлов со стеклом |
|
|
||
пленок? |
|
|
Порошок титаната бария |
|
9 |
|
|
|
|
|
|
||
|
|
|
Порошок из сегнетоке-рамики |
39 |
||
|
|
|
|
|
|
|
Каким образом обеспечивается |
высокая |
точность |
Подбором состава песеты |
|
69 |
|
параметров элементов толстопленочных схем? |
|
|
|
|
||
|
Изменением размеров |
|
99 |
|||
|
|
|
|
|
||
|
|
|
Термической обработкой при 1000К |
129 |
||
|
|
|
|
|||
Что не характерно для толстопленочных микросхем? |
Надежность |
|
68 |
|||
|
|
|
|
|
|
|
|
|
|
Экономичность |
|
10 |
|
|
|
|
|
|
|
|
|
|
|
Стабильность параметров |
|
70 |
|
|
|
|
|
|
||
|
|
|
Отсутствие навесных элементов |
40 |
||
|
|
|
|
|
|
|
§21.4. Тонкопленочные микросхемы
К тонким относят пленки, толщина которых составляет десятые и сотые доли микрометра. При изготовлении ИМС по тонкопленочной технологии для токопроводящих линий, с
помощью которых соединяются пленочные элементы микросхемы, и контактных площадок для подсоединения навесных элементов применяют различные металлы, имеющие высокую электропроводность: алюминий, медь, серебро, золото, никель, хром, олово, их соли и сплавы.
Металлы должны быть устойчивы к химическим воздействиям и иметь хорошую адгезию к подложке.
Для изготовления обкладок конденсаторов чаще всего применяют алюминий и медь; индуктивные элементы (рис. 21.6) изготовляют из никеля, серебра или хрома.
Рис. 21.6. Пленочные индуктивные катушки
Для получения резистивных элементов используют тантал, титан, никель, хром и их сплавы, а также углерод и кремний.
Изолирующие диэлектрические пленки получают окислением внешних слоев металлических пленок или нанесением покрытий из диэлектрических материалов.
Для нанесения тонких пленок на подложку применяют различные методы: вакуумное напыление, катодное распыление, химическое осаждение и электролитическое анодирование.
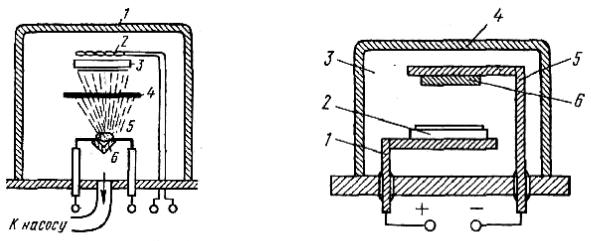
Метод вакуумного напыления иллюстрируется рис. 21.7. Материал для изготовления пленки помещают в тугоплавкий тигель из платины или вольфрама. Эту систему плотно закрывают колпаком, давление под которым понижают до 10-3 Па, затем тигель нагревают до температуры примерно 1000К. Материал начинает интенсивно испаряться, осаждаясь на более холодной подложке. Осажденная пленка должна быть однородной и плотно соединяться с подложкой, для чего ее поверхность должна быть хорошо очищена от посторонних примесей. Для этого подложку подогревают. Между испарителем и подложкой устанавливают экран, который поглощает молекулы, не попадающие на нее. Осаждающиеся на экране дорогостоящие металлы в дальнейшем смывают и используют вторично.
Для создания композитных пленок в камере размещают несколько испарителей.
Если в рассмотренной схеме нагрев испарителей осуществляется электрическим током, то для создания пленок из тугоплавких материалов, например вольфрама, титана, молибдена, нагрев производят электронным лучом, направленным непосредственно на испаряющуюся поверхность.
Рис. 21.7. Схема вакуумного напыления: 1 — колпак; 2 — |
Рис. 21.8. Схема катодного распыления: |
подогреватель подложки; 3 — подложка; 4 — экран; 5 — |
1 — анод; 2 — подложка; 3 — объем, заполненный газом; |
испаряющий материал; 6 — подогреватель |
4 — колпак; 5 — катод; 6 — распыляющийся материал |
Вакуумное напыление можно использовать во всех случаях, однако испарение материалов с высокой температурой кипения — достаточно трудная задача. Поэтому широкое применение находит также метод катодного распыления (рис. 21.8).
При катодном распылении рабочий объем камеры заполняют инертным газом при давлении около 1 Па, а к электродам подводят постоянное напряжение в несколько тысяч вольт. Газ в камере ионизируется, и положительные ионы газа, устремляясь к катоду, выбивают из распыляемого материала молекулы, которые осаждаются на подложке, образуя пленку. Так как разгон ионов осуществляется электрическим полем, процесс распыления может идти при относительно низких температурах распыляемого материала. Метод катодного распыления применяют для создания пленок из таких материалов, как тантал, титан, молибден, вольфрам, платина.
При химическом осаждении в камеру, где помещается подложка, по различным трубопроводам подают газообразные реагенты. В результате химической реакции выделяются молекулы металла или его солей, которые и осаждаются на подложке. Ненужные продукты реакции откачиваются.
Электролитическое анодирование производят в жидком электролите, куда помещают подложку и материал пленки, растворяющийся в электролите. Подложку (анод) подсоединяют к плюсу источника постоянного тока, а материал пленки (катод) — к минусу.
Так как при изготовлении микросхемы нанесение пленок на подложку производят многократно, для получения определенной строго рассчитанной конфигурации каждого слоя применяют фотолитографию.
Карточка № 21.4 (131).
Тонкопленочные микросхемы
Какие |
материалы |
применяют |
|
для |
Алюминий, медь, серебро, золото |
100 |
||
изготовления тонких пленок? |
|
|
|
|
||||
|
|
Тантал, титан, никель, углерод |
130 |
|||||
|
|
|
|
|
|
|
|
|
|
|
|
|
|
|
|
Вольфрам, молибден |
11 |
|
|
|
|
|
|
|
Все перечисленные |
41 |
|
|
|
|
|
|
|
||
Какой |
метод |
не |
используется |
при |
Вакуумное напыление |
71 |
||
изготовление |
тонких |
пленок |
|
для |
|
|
||
|
Химическое осаждение |
101 |
||||||
микросхем? |
|
|
|
|
|
|
|
|
|
|
|
|
|
Электролитическое осаждение |
131 |
||
|
|
|
|
|
|
|
||
|
|
|
|
|
|
|
|
|
|
|
|
|
|
|
|
Трафаретная печать |
12 |
Каким |
образом |
защищают |
подложку |
от |
Глубоким вакуумом |
42 |
||
загрязнения при |
вакуумном напылении |
|
|
|||||
Экраном |
72 |
|||||||
тонкой пленки? |
|
|
|
|
|
|
|
|
|
|
|
|
|
Подогревом |
102 |
||
|
|
|
|
|
|
|
||
В каких случаях целесообразно применять |
При создании проводящих пленок |
132 |
||||||
метод катодного распыления? |
|
|
При создании резистивных пленок |
13 |
||||
|
|
|
|
|
|
|
|
|
|
|
|
|
|
|
|
При создании тугоплавких пленок. |
43 |
|
|
|
|
|
|
|
||
Как |
образуются |
молекулы |
|
для |
Выбиваются электронным лучом |
73 |
||
формирования |
пленки |
при |
методе |
|
|
|||
Выбиваются положительными ионами |
103 |
|||||||
химического осаждения? |
|
|
|
|
|
|||
|
|
|
Выделяются при химической реакции газов |
133 |
||||
|
|
|
|
|
|
|
||
|
|
|
|
|
|
|
|
|
§21.5. Фотолитография
Процесс фотолитографии начинается с изготовления негатива. На двухслойной пленке с прозрачной основой и зачерненной поверхностью вычерчивают необходимый рисунок. Делается это с помощью ручного или автоматического координатографа, который снимает непрозрачный слой в местах, где должны быть «белые» контуры. С негатива размером 1 м2 делают уменьшенный отпечаток с помощью специальной камеры. Обычно уменьшение производится в две-три ступени, пока отпечаток не достигнет нужных размеров. Окончательный отпечаток делают на фотопластинке и называют фотошаблоном. Стеклянная основа фотошаблона должна быть идеально чистой и плоскопараллельной.
Следующий этап фотолитографии состоит в нанесении фоторезиста на подложку микросхемы или на напыленную ранее пленку. Фоторезистами называют вещества (обычно эмульсии на основе высокомолекулярных соединений), имеющие свойство после облучения менять способность к растворению в специально подобранных средах.
Фоторезисты делятся на негативные и позитивные. В первых под действием облучения образуются нерастворимые, а во вторых, наоборот, растворимые участки. Фоторезист можно наносить окунанием подложки в эмульсию, с помощью пульверизатора или центрифугированием. В последнем случае получают наиболее однородную и прочную пленку фоторезиста.
При центрифугировании на подложку наносят каплю фоторезиста и помещают в центрифугу. Под действием центробежной силы фоторезист равномерно и плотно (без пузырьков и щелей) распределяется по всей поверхности.
Нанесенный фоторезист просушивают сначала при температуре окружающей среды, а затем в сушильном шкафу при 400 К.
После этого на поверхность, покрытую пленкой фоторезиста, накладывают фотошаблон и экспонируют в ультрафиолетовом свете. В пленке из негативного фоторезиста при облучении образуются нерастворимые участки, которые после проявления остаются на подложке и экранируют ее от напыления. В позитивном фоторезисте облучение формирует растворимые участки, на месте которых после проявления образуются окна. Через эти окна напыляемый материал достигает подложки и оседает на ней.
После напыления проводящей или резистивной пленки фоторезист смывают и на поверхности остаются необходимые элементы тонкопленочной схемы.
Для получения микросхем высокого качества последовательно применяют два вида фоторезистов. Это позволяет получить хорошее совмещение пассивных элементов схемы, контактных площадок и токо-проводящих дорожек.
Карточка № 21.5 (245).
Фотолитография
Что такое фотошаблон? |
|
Пленка с рисунком, вычерченным |
с |
14 |
|||
|
|
помощью координатографа |
|
|
|
||
|
|
|
|
|
|
|
|
|
|
Отпечаток |
|
на |
стеклянной |
44 |
|
|
|
фотопластинке |
|
|
|
|
|
|
|
|
|
|
|
||
Какой метод не применяется для |
нанесения |
Вакуумное напыление |
|
|
74 |
||
негативного фоторезиста? |
|
|
|
|
|
||
|
Окунание |
в |
фоторезистивнуго |
104 |
|||
|
|
эмульсию |
|
|
|
|
|
|
|
|
|
||||
|
|
Опыление обложки из пульверизатора |
134 |
||||
|
|
|
|
|
|
||
|
|
Центрифугирование |
|
|
15 |
||
Какой фоторезист надо применить, чтобы сохранить |
Позитивный |
|
|
|
|
45 |
|
участки фоторезистивиой пленки под затененными |
|
|
|
|
|
|
|
Негативный |
|
|
|
|
75 |
||
участками фотошаблона? |
|
|
|
|
|
|
|
|
Можно тот и другой |
|
|
105 |
|||
|
|
|
|
||||
Когда смывают фоторезист? |
|
После облучения |
|
|
|
135 |
|
|
|
После проявления |
|
|
16 |
||
|
|
После напыления тонкой пленки |
|
46 |
|||
Какие элементы микросхемы требуют |
строгого |
Резисторы и контактные проволочки |
|
76 |
|||
совмещения друг с другом? |
|
|
|
|
|
|
|
|
Резисторы и конденсаторы |
|
|
106 |
|||
|
|
|
|
||||
|
|
|
|
|
|
|
|
|
|
Контактные |
|
площадки |
и |
136 |
|
|
|
токопроводящие дорожки |
|
|
|
||
|
|
|
|
|
|
|
|
§21.6. Полупроводниковые интегральные микросхемы
Полупроводниковые интегральные микросхемы изготовляют на одном кристалле введением легирующих примесей в определенные микрообласти. Современные технологии
позволяют создавать в приповерхностном объеме кристалла весь набор активных и пассивных элементов, а также межэлементные соединения в соответствии с топологией схемы.
В качестве активных элементов ИМС наряду с биполярными широко применяются транзисторы типа МДП. МДП-транзисторы проще в изготовлении, дают больший процент выхода годных изделий, позволяют получить более высокую плотность размещения приборов, потребляют меньшую мощность, дешевле биполярных.
Однако у микросхем на основе МДП-транзисторов есть существенный недостаток — сравнительно высокая инерционность. Поэтому там, где требуется высокое быстродействие, в частности в электронных вычислительных машинах, предпочтение отдают ИМС на биполярных транзисторах.
Один из важных критериев оценки ИМС, характеризующий уровень интеграции,— это отношение числа р-n-р-переходов к числу внешних выводов (вентиль/контакт). Чем больше это отношение и чем меньше потребляемая мощность (лучше условия теплоотдачи), тем надежнее электронные блоки на базе микросхем (сравнивать следует блоки одинаковой функциональной сложности). У простых логических схем это отношение меньше единицы. С повышением сложности ИМС отношение вентиль/контакт достигает десяти и более.
Основой полупроводниковых интегральных микросхем чаще всего служит кремний. На одной пластинке кремния диаметром 75 мм и толщиной 0,2 мм можно сформировать до 10 000 полупроводниковых ИМС.
Широкое применение кремния для производства полупроводниковых ИМС обусловлено прежде всего способностью кремния сохранять полупроводниковые свойства при относительно высоких температурах
(до 400 К).