
- •ВВЕДЕНИЕ
- •2. ОСНОВЫ ЛИТЕЙНОГО ПРОИЗВОДСТВА
- •2.1. Теоретические основы производства отливок
- •2.2. Формовочные материалы
- •2.3. Литье в разовые песчано-глинистые формы
- •2.4. Разработка чертежей отливок
- •2.5. Определение размеров припусков на механическую обработку
- •2.6. Расчет литниковой системы
- •2.7. Литье под давлением
- •2.8. Кокильное литье
- •2.9. Центробежное литье
- •2.12. Литье по газифицируемым моделям
- •2.13. Литье по ледяным моделям
- •2.14. Особенности изготовления отливок из различных сплавов
- •3. ОСНОВЫ ОБРАБОТКИ МАТЕРИАЛОВ ДАВЛЕНИЕМ
- •3.1. Сущность процессов обработки материалов давлением
- •3.2. Процессы прокатки
- •3.3. Прессование металлов
- •3.4. Волочение
- •3.5. Процессы свободной ковки
- •3.6. Процессы точной объемной штамповки
- •3.6.1. Выбор методов и способов производства заготовок объемной штамповкой
- •3.6.2. Разработка технологии открытой объемной штамповки
- •3.6.3. Определение класса точности поковки
- •3.6.4. Определение группы стали
- •3.6.6. Определение исходного индекса
- •3.6.8. Определение допусков на размеры поковки
- •3.6.9. Разработка чертежа холодной поковки
- •3.6.10. Назначение напусков
- •3.6.11. Разработка чертежа горячей поковки
- •3.6.12. Определение размеров исходной заготовки
- •3.7. Горячая раскатка кольцевых заготовок
- •3.8. Штамповка на термических прессах
- •3.9. Процессы листовой штамповки
- •3.10. Штамповка бризантными взрывчатыми веществами
- •3.11. Штамповка горючими газовыми смесями
- •3.12. Магнитно-импульсная обработка металлов
- •3.13. Электрогидроимпульсная штамповка
- •4.1. Классификация металлорежущих станков
- •4.2. Особенности технологии резания материалов
- •4.4. Способы и инструмент обработки отверстий
- •4.5. Способы и инструмент обработки фрезерованием
- •4.6. Способы и инструмент для строгания поверхностей
- •4.7. Способы и инструмент обработки шлифованием
- •4.8. Отделочные методы обработки поверхностей
- •5.1. Сущность процессов сварки
- •5.2. Ручная дуговая сварка стали
- •5.3. Дуговая сварка под флюсом
- •5.4. Дуговая сварка в среде защитных газов
- •5.5. Газовая сварка
- •5.6. Контактная электрическая сварка
- •5.7. Свариваемость сталей
- •5.8. Специальные термические процессы при сварке
- •5.9. Пайка металлов
- •6.1. Общая характеристика неметаллических материалов
- •6.2. Основы технологии производства изделий из пластмасс
- •6.3. Основы технологии производства изделий из резины
- •6.4. Характеристика композиционных материалов
- •6.5. Механизмы упрочнения композиционных материалов
- •6.6. Назначение и характеристика порошковых, дисперсно-упрочненных композиционных материалов
- •6.7. Волокнистые композиционные материалы
- •7. ТЕХНОЛОГИИ И ОСНАСТКА ХОЛОДНОЙ ОБЪЕМНОЙ ШТАМПОВКИ
- •7.1. Особенности холодной объемной штамповки
- •7.3. Способы формообразования, особенности технологии получения изделий стержневого типа, схемы инструмента
- •7.4. Штамповая оснастка для процессов выдавливания
- •7.5. Материалы инструмента для холодного деформирования
- •КОНТРОЛЬНЫЕ ВОПРОСЫ
- •Контрольные вопросы к разделу 1
- •Контрольные вопросы к разделу 2
- •Контрольные вопросы к разделу 3
- •Контрольные вопросы к разделу 4
- •Контрольные вопросы к разделу 5
- •Контрольные вопросы к разделу 6
- •Контрольные вопросы к разделу 7
7. ТЕХНОЛОГИИ И ОСНАСТКА ХОЛОДНОЙ ОБЪЕМНОЙ ШТАМПОВКИ
7.1. Особенности холодной объемной штамповки
Технологии холодной объемной штамповки (ХОШ) с полным основанием относятся к малоотходным. Опыт отечественных и зарубежных ф рм показывает, что при изготовлении изделий ХОШ
почти вдвое сокращаются расходы материала и электроэнергии, |
|
внедрение |
|
уменьшается, а ногда полностью исключается доработка резанием. |
|
СВ то же время |
процессов холодного деформирования |
требует относ тельно высоких расходов на опытно-конструкторские
работы |
зготовлен едеформирующегоинструмента. |
|
разработкой |
Перспект вы расширения применения технологий ХОШ |
|
связаны с |
новых способов формообразования фасонных |
изделий, высокостойкого инструмента и смазок. Повышение производ тельности труда и уровня принимаемых решений при проектировании технологическихАпроцессов ХОШ может быть обеспечено за счет накопления данных о приемах формоизменения заготовок; унификации расчетных схем, штамповых блоков и инструмента; внедрения классификаций штампуемых изделий и способовобработки; расширенияпримененияДвычислительнойтехники.
Определенные требования на разработку технологических процессов ХОШ накладывают особенности поведения металла при холодной пластической деформации: значительное увеличение
механической |
прочности |
при |
одновременном |
снижении |
|
|
|
И |
|
пластических свойств, а также изменение макро- и микроструктуры, |
||||
образование |
текстуры деформации, |
отсутствие |
окалины на |
поверхности, интенсивное схватывание с материалом инструмента. ХОШ характеризуется многообразием вариантов технологических схем пластического деформирования, которые зависят от свойств деформируемого металла, геометрии детали, необходимости обеспечения определенных эксплуатационных характеристик, программы выпуска, типа используемого оборудования.
Методы холодной объемной штамповки используются в основном при крупносерийном и массовом производстве осесимметричных и плоскосимметричных (реже несимметричных) в плане изделий, если они требуют больших затрат труда при
274
изготовлении другими методами [30]. Форма наружных и |
||
внутренних поверхностей изделий должна быть простой, без |
||
выступов и поднутрений, препятствующих формообразованию, без |
||
острых углов при переходе от одного сечения к другому и в местах, |
||
где меняется направление течения металла. Резкие переходы на |
||
С |
|
|
инструменте вызывают концентрацию напряжений, срезают слои |
||
носителя смазки и смазки, способствуют образованию дефектов |
||
структуры |
формы зделия, например, |
трещин, сколов, застойных |
зон и т. д., пр ч ной пониженной стойкости инструмента. |
||
или |
|
|
Одна |
з основных задач проектирования технологий состоит в |
|
выборе способов формообразования, |
выборе последовательности |
совмещен я операций, определении характера формоизменения
за каждый переход. Вы ранная маршрутная схема формоизменения |
|
должна |
обеспеч |
ть наилучшие условия работы инструмента при |
|
минимальном кол честве переходов. |
|
Детали, представленные в «классификаторе» [29, 30, 31], могут |
|
быть |
зготовлены за один или несколько переходов. Количество |
|
А |
переходов определяется конфигурацией детали, степенью пластической деформации, свойствами металла заготовки.
7.2. Спосо ы формоо разования, конструирование инструмента, построение процессов ХОШ полых изделий
При выдавливании изделий типа «стакан» основными способами (операциями) являются: обратное выдавливание, когда
металл |
заготовки выталкивается в |
зазор между пуансоном и |
|||
матрицей |
|
|
И |
||
(рис. 7.1, а); прямое выдавливание |
(рис. 7.1, |
б); |
|||
выдавливание по способу КуногиД(рис.7.1,в); дифференцированное |
|||||
обратное |
выдавливание с |
поднимающейся |
принудительно |
||
матрицей (рис. 7.2, а) [30]; |
обратное выдавливание с наложением |
||||
растяжения (модификация дифференцированного выдавливания, рис. |
|||||
7.2, б); |
дифференцированное |
обратное |
выдавливание |
с |
|
опускающимся принудительно выталкивателем (рис. 7.2, в) [30]. |
|
275
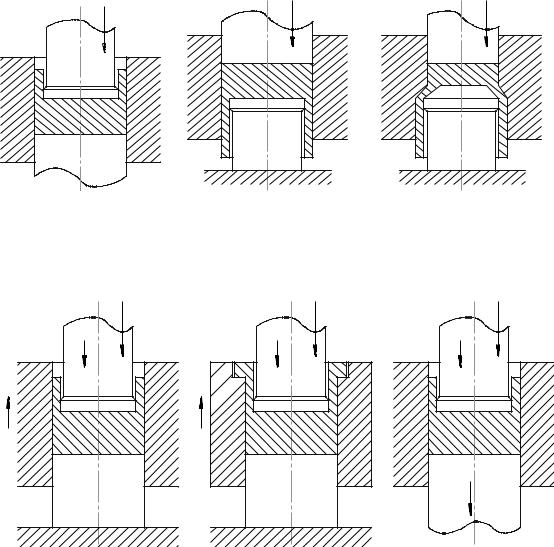
|
P |
|
|
P |
P |
|
|
|
|
|
|
|
а |
|
|
б |
в |
Рис. 7.1. |
пособы выдавл вания полых изделий: а – обратное выдавливание; |
||||
С |
|
; в – выдавливание по способу Куноги |
|||
б – прямое выдавл |
|||||
|
P |
|
|
P |
P |
|
V0 |
|
|
V0 |
V0 |
вание |
|
|
|||
V1 |
|
|
V1 |
|
|
|
бА |
V1 |
|||
|
в |
||||
|
а |
|
|
б |
|
Рис. 7.2. Способы дифференцированного обратного выдавливания полых |
|||||
|
|
|
|
изделий |
|
|
|
|
|
Д |
|
Эти основные операции применяются в том случае, когда |
|||||
расчетная степень инструмента и деформации меньше или равна |
|||||
предельной ( расч |
εпред) и, кроме того, если выполняется условие |
||||
соответствия отношения lп/dп удельным усилиям p (табл. 7.1). Такие |
|||||
нормы должны выполняться и для любых другихИпроцессов ХОШ. |
|||||
Удельные усилия выдавливания изделий с многогранной |
|||||
наружной или внутренней поверхностями зависят от ε и количества |
|||||
граней. Увеличение периметра (уменьшение числа сторон) приводит |
|||||
к повышению удельных усилий на 10 – 15% [29]. |
|
276
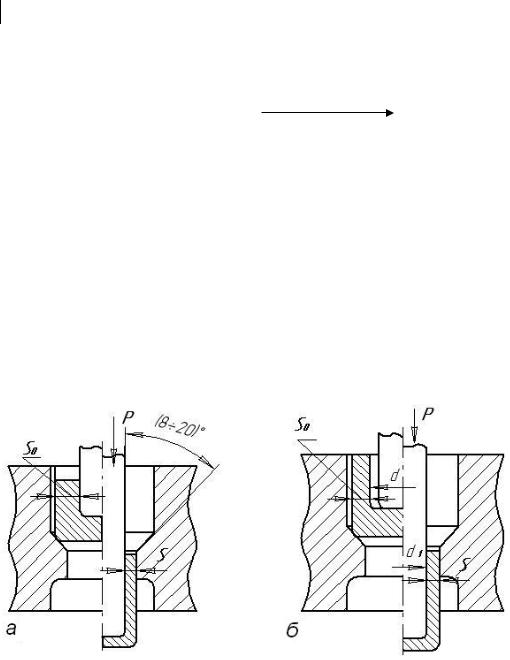
Таблица 7 .1
Рекомендованные lп/dп при деформировании различных материалов
|
р, |
|
600 |
|
800 |
|
1000 |
|
1400 |
|
1800 |
|
|
2000 |
2200 |
2400 |
||
|
МПа |
|
|
|
|
|
|
|
||||||||||
|
|
|
|
|
|
|
|
|
|
|
|
|
|
|
|
|
|
|
|
lп/dп |
|
≤ 8,0 |
|
|
≤ 6,0 |
|
≤ 4,0 |
|
≤ 3,0 |
|
≤ 2,5 |
|
≤ 2,0 |
≤ 1,5 |
|
≤ 1,0 |
|
С |
|
|
|
|
|
|
|
|
|
|
|
|
||||||
|
|
|
|
Al (чистый) |
|
|
|
|
|
|
|
|
|
|
||||
|
|
|
|
|
|
|
|
Медь, Al (сплавы) |
|
|
|
|
|
|||||
|
|
|
|
|
|
|
|
|
|
латунь |
|
|
|
|
|
|||
|
|
|
|
|
|
|
|
|
|
|
|
Сталь |
|
|
|
|
||
|
технологии |
|
|
|
|
|
|
|
|
|
||||||||
|
Увеличен е прочности материала |
|
|
|
|
|
|
|
|
|
||||||||
|
|
В случаях, когда εрасч > εпред; при необходимости калибровки |
||||||||||||||||
|
изделия по д аметру; для дополнительного повышения стойкости |
|||||||||||||||||
|
|
|
бА |
|
|
|
||||||||||||
|
инструмента (с учетом того, что при |
ε = 40 – 45% удельные усилия |
||||||||||||||||
|
основной операц м нимальны); при штамповке изделий с длиной |
|||||||||||||||||
|
до 10 д аметров в |
|
|
|
вводятся дополнительные переходы |
|||||||||||||
|
штамповки с операц ями вытяжки с утонением стенки (рис. 7.3) |
|||||||||||||||||
[29], |
|
дорнован я, |
ротационного |
выдавливания, |
совмещения |
обратного выдавливания и вытяжки с утонением стенки. Вытяжка с утонением стенки производится через конические матрицы с углом наклона образующей к оси от 8 до 20º.
Д И
Рис. 7.3. Способы вытяжки с утонением стенки: а – с уменьшением S; б – с уменьшением S и d
При выдавливании изделий типа «стакан со ступенчатой полостью» используются те же операции, что и при выдавливании
277
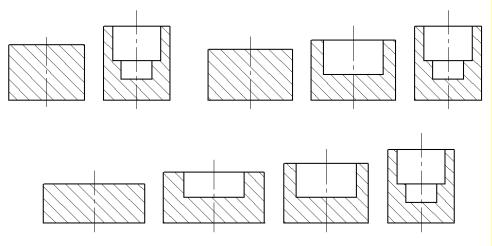
стаканов. Однако есть особенности, которые определяются соотношениями размеров ступеней.
Например, при попытке выдавливания изделия за один переход |
||
(рис. 7.4, а) ступенчатым пуансоном, когда отношение диаметров |
||
полостей больше 1,3 – 1,5, наблюдается дефект в виде складок на |
||
С |
|
|
стенках. Для получения качественного изделия выполняют |
||
последовательно две операции обратного выдавливания (рис. 7.4, б). |
||
Если расчетная степень деформации на первом переходе превышает |
||
допуст мую, то увел ч |
вают диаметр заготовки и вводят переход, на |
|
полости |
||
котором стенка полуфабриката утоняется. Тогда технологическая |
||
схема штамповки выглядит, как на рис. 7.4, в. Если глубина нижней |
||
меньше 0,3 dn, |
а отношение диаметров полостей меньше |
|
1,3, то выдавл ван е можно производить за один переход. |
||
|
бАб |
|
|
спользован ем операций прямого, обратного и |
|
комбин рованного выдавливания, вытяжки с утонением стенки |
||
изготавл вают здел я |
типа «стакан со сплошным или полым |
|
отростком», втулок с наружным или внутренним фланцем [29]. |
||
а |
|
Д |
|
|
в
Рис.7.4. Выдавливание стаканов со ступенчатой полостью: а – за один переход; |
|
б – за два перехода; в – с введением перехода «вытяжка с утонением стенки» |
|
Например, |
при изготовлении изделийИтипа «стакан с |
наружным отростком» возможны такие варианты технологий: |
|
- если диаметр полости больше диаметра отростка, то |
|
возможно комбинированное выдавливание детали из сплошной |
|
заготовки |
(рис. 7.5, а). Если при этом отросток получится |
короче, чем требуется, то следует производить последовательное
278
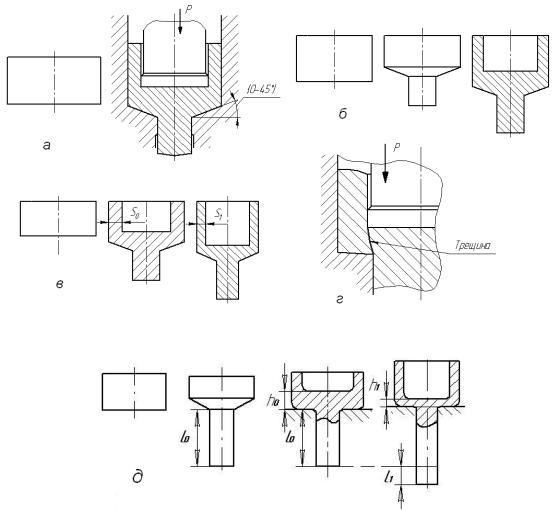
формирование (рис. 7.5,б) сначала стержня, а затем полой части.
Возможно |
комбинированное выдавливание с последующей |
вытяжкой с утонением стенки (рис. 7.5, в). Удельное усилие на |
|
основном переходе меньше на 20–30%, чем при «простых» |
|
операциях; |
|
С |
|
- если диаметр полости примерно равен диаметру отростка, то |
|
возможен чистый сдвиг в донной части (рис. 7.5, г). В этом случае |
|
следует раздельно формировать отросток и полую часть (рис. 7.5, д). |
« таканы с полым отростком» выдавливают по комбинированной
стечение |
|
схеме з кольцевых заготовок (рис. 7.6, а), если при этом получаются |
|
соответствующ е чертежу размеры стакана и отростка. В противном |
|
случае огран ч вают |
металла вверх (рис. 7.6, б). |
бА |
|
|
Д |
|
И |
Рис.7.5. Варианты технологий выдавливания изделия «стакан с наружным отростком»
279
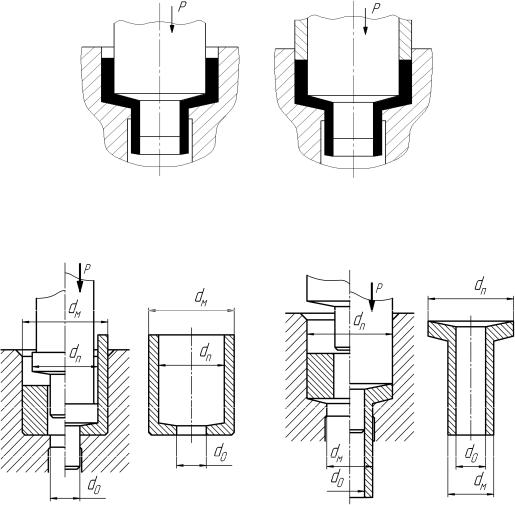
Типовые схемы штамповки «стаканов» с отверстием в дне и трубок с фланцем представлены на рис.7.7, а, б.
С |
|
б |
Р с. 7.6. |
|
схем выдавливания «стаканов» |
|
с полым отростком |
|
Варианты |
|
|
бА |
||
а |
|
б |
Рис. 7.7. Схемы выдавливания «стакана» с отверстием в дне (а) |
||
|
и трубки с фланцем (б) |
|
|
|
Д |
На рис. 7.8 представлены варианты технологийИвыдавливания детали со сферической полостью из стали 35. Варианты а, в и г требуют больших удельных усилий. При комбинированном выдавливании удельные усилия значительно меньше, стойкость инструмента выше, но существует сложность в подборе размеров заготовки (рис. 7.8, б). Если же оптимальные соотношения размеров определены, то получается поковка (рис. 7.9), требующая только расточки отверстия и оформления фасок. Заготовка изготовлена из трубы 48 с толщиной стенки 6 мм [29].
280

С |
а |
б |
и |
||
Р с. 7.8. Вар анты технологий выдавливания изделия |
||
|
|
со сферической полостью |
бА |
||
|
в |
г |
Рис. 7.8. Варианты технологий выдавливания изделия |
||
|
|
Д |
|
|
со сферической полостью |
|
|
И |
Рис. 7.9. Технология выдавливания детали «вкладыш»
281
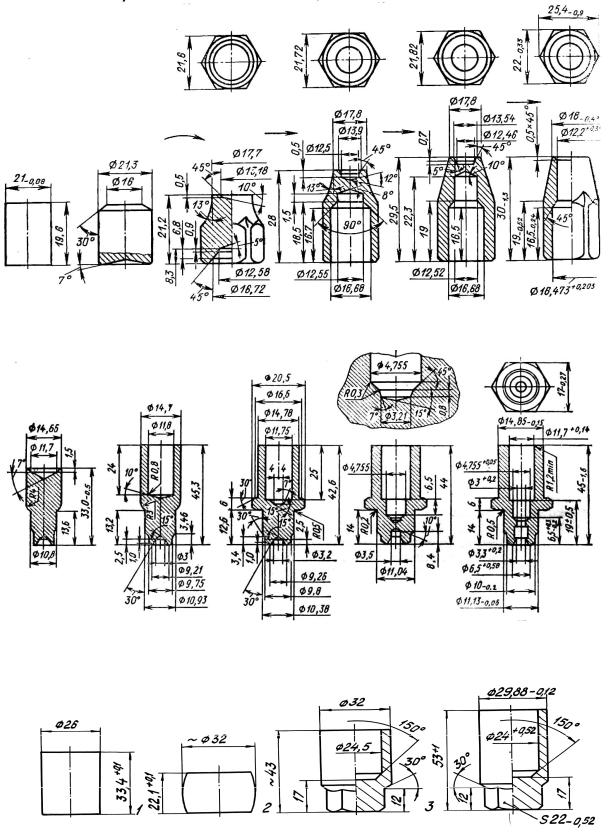
На рис. 7.10 – 7.15 показаны технологические переходы выдавливания деталей сложной формы.
Си Р с. 7.10.бАПереходы холодного выдавливания детали «штуцер» [31]
Д
Рис. 7.11. Переходы холодного выдавливания деталиИ«корпус свечи» [31]
Рис. 7.12. Технологические переходы выдавливания детали «крышка»
282
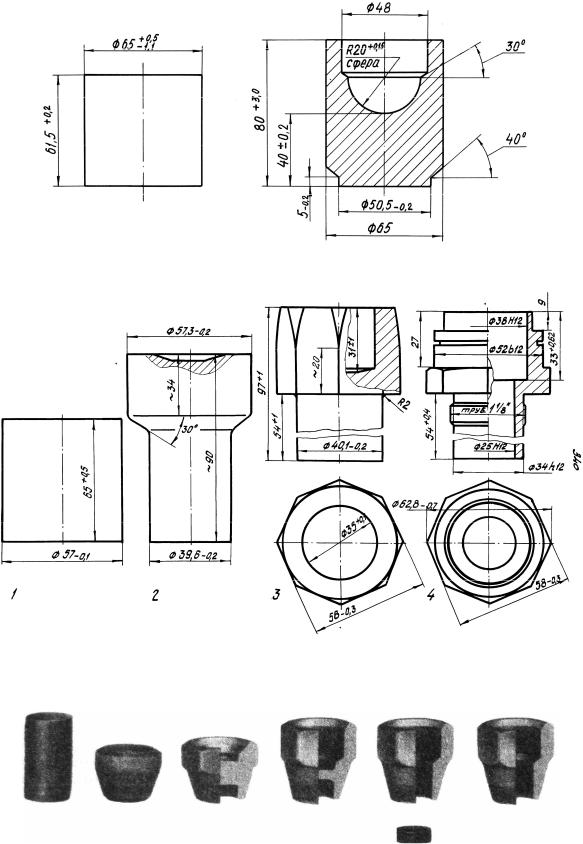
С |
|
Технология |
|
Р с. 7.13. |
выдавливания детали «головка плунжера» |
бА |
|
|
Д |
|
И |
Рис. 7.14. Технологические переходы выдавливания детали «корпус» [29]
Рис. 7.15. Технологические переходы выдавливания детали «корпус» [31]
283