
- •ВВЕДЕНИЕ
- •2. ОСНОВЫ ЛИТЕЙНОГО ПРОИЗВОДСТВА
- •2.1. Теоретические основы производства отливок
- •2.2. Формовочные материалы
- •2.3. Литье в разовые песчано-глинистые формы
- •2.4. Разработка чертежей отливок
- •2.5. Определение размеров припусков на механическую обработку
- •2.6. Расчет литниковой системы
- •2.7. Литье под давлением
- •2.8. Кокильное литье
- •2.9. Центробежное литье
- •2.12. Литье по газифицируемым моделям
- •2.13. Литье по ледяным моделям
- •2.14. Особенности изготовления отливок из различных сплавов
- •3. ОСНОВЫ ОБРАБОТКИ МАТЕРИАЛОВ ДАВЛЕНИЕМ
- •3.1. Сущность процессов обработки материалов давлением
- •3.2. Процессы прокатки
- •3.3. Прессование металлов
- •3.4. Волочение
- •3.5. Процессы свободной ковки
- •3.6. Процессы точной объемной штамповки
- •3.6.1. Выбор методов и способов производства заготовок объемной штамповкой
- •3.6.2. Разработка технологии открытой объемной штамповки
- •3.6.3. Определение класса точности поковки
- •3.6.4. Определение группы стали
- •3.6.6. Определение исходного индекса
- •3.6.8. Определение допусков на размеры поковки
- •3.6.9. Разработка чертежа холодной поковки
- •3.6.10. Назначение напусков
- •3.6.11. Разработка чертежа горячей поковки
- •3.6.12. Определение размеров исходной заготовки
- •3.7. Горячая раскатка кольцевых заготовок
- •3.8. Штамповка на термических прессах
- •3.9. Процессы листовой штамповки
- •3.10. Штамповка бризантными взрывчатыми веществами
- •3.11. Штамповка горючими газовыми смесями
- •3.12. Магнитно-импульсная обработка металлов
- •3.13. Электрогидроимпульсная штамповка
- •4.1. Классификация металлорежущих станков
- •4.2. Особенности технологии резания материалов
- •4.4. Способы и инструмент обработки отверстий
- •4.5. Способы и инструмент обработки фрезерованием
- •4.6. Способы и инструмент для строгания поверхностей
- •4.7. Способы и инструмент обработки шлифованием
- •4.8. Отделочные методы обработки поверхностей
- •5.1. Сущность процессов сварки
- •5.2. Ручная дуговая сварка стали
- •5.3. Дуговая сварка под флюсом
- •5.4. Дуговая сварка в среде защитных газов
- •5.5. Газовая сварка
- •5.6. Контактная электрическая сварка
- •5.7. Свариваемость сталей
- •5.8. Специальные термические процессы при сварке
- •5.9. Пайка металлов
- •6.1. Общая характеристика неметаллических материалов
- •6.2. Основы технологии производства изделий из пластмасс
- •6.3. Основы технологии производства изделий из резины
- •6.4. Характеристика композиционных материалов
- •6.5. Механизмы упрочнения композиционных материалов
- •6.6. Назначение и характеристика порошковых, дисперсно-упрочненных композиционных материалов
- •6.7. Волокнистые композиционные материалы
- •7. ТЕХНОЛОГИИ И ОСНАСТКА ХОЛОДНОЙ ОБЪЕМНОЙ ШТАМПОВКИ
- •7.1. Особенности холодной объемной штамповки
- •7.3. Способы формообразования, особенности технологии получения изделий стержневого типа, схемы инструмента
- •7.4. Штамповая оснастка для процессов выдавливания
- •7.5. Материалы инструмента для холодного деформирования
- •КОНТРОЛЬНЫЕ ВОПРОСЫ
- •Контрольные вопросы к разделу 1
- •Контрольные вопросы к разделу 2
- •Контрольные вопросы к разделу 3
- •Контрольные вопросы к разделу 4
- •Контрольные вопросы к разделу 5
- •Контрольные вопросы к разделу 6
- •Контрольные вопросы к разделу 7
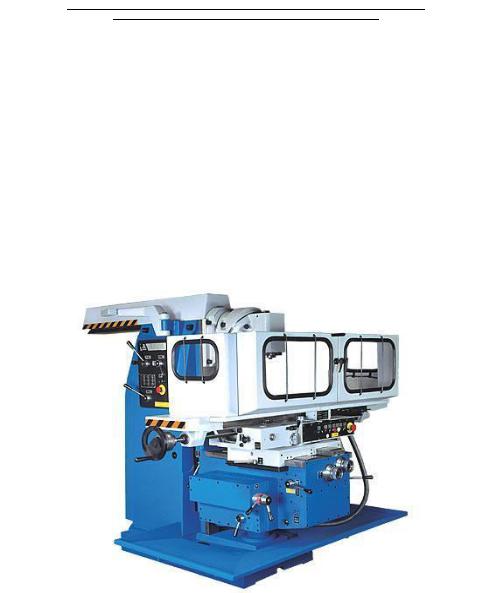
Министерство образования и науки РФ Федеральное государственное бюджетное образовательное учреждение
высшего образования « ибирский государственный автомобильно-дорожный университет (СибАДИ)»
СибАДИВ.В. Евстифеев, .А. Александров
ТЕХНОЛОГИЧЕСКИЕ ПРОЦЕССЫ МАШИНОСТРОИТЕЛЬНЫХ ПРОИЗВОДСТВ
Уче ное пособие
Омск – 2018
УДК |
621.7 |
Согласно 436-ФЗ от 29.12.2010 «О защите |
детей от информации, причиняющей вред |
||
ББК |
34.5 |
их здоровью и развитию» данная продукция |
|
Е26 |
маркировке не подлежит. |
Рецензенты:
д-р техн. наук, проф. С.А. Корнилович (СибГАУ); д-р техн. наук, доц. В.И. Гурдин (СибАДИ)
Работа утверждена редакционно-издательским советом СибАДИ в качестве учебного пособия.
Евстифеев, Владислав Викторович.
Е26 Технологические процессы машиностроительных производств
[Электронный ресурс] : учебное пособие / В.В. Евстифеев, А.А. Александров. –
Электрон. дан. – Омск : СибАДИ, 2018. – URL: http://bek.sibadi.org/cgi-bin/ irbis64r_plus/cgiirbis_64_ft.exe. - Режим доступа: для авторизованных пользователей.
Представлены современные методы, обеспечивающие высокое качество продукции, экономию материалов и высокую производительность труда.
Описаны физические основы процессов, их технико-экономические характеристики, области применения, а также технологические и техникоэкономические характеристики типового оборудования, инструмента и приспособлений.
Имеет интерактивное оглавление в виде закладок.
Предназначено для обучающихся всех форм обучения всех технических направлений бакалавриата, магистратуры и всех технических специальностей, изучающих дисциплины «Материаловедение. Технология конструкционных материалов», «Технология автомобиле- и тракторостроения», «Конструкторскотехнологические решения обеспечения безопасности функционирования автотранспортных средств», «Перспективные технологии обработки материалов».
Подготовлено на кафедре «Автомобили, конструкционные материалы и технологии».
Текстовое (символьное) издание (70 МБ)
Системные требования: Intel, 3,4 GHz; 150 Мб; Windows XP/Vista/7; DVD-ROM; 1 Гб свободного места на жестком диске; программа для
чтения pdf-файлов: Adobe Acrobat Reader; Foxit Reader
Редактор И.Г. Кузнецова
Техническая подготовка Н.В. Кенжалинова Издание первое. Дата подписания к использованию 04.06.2018
Издательско-полиграфический комплекс СибАДИ. 644080, г. Омск, пр. Мира,5 РИО ИПК СибАДИ. 644080, г. Омск, ул. 2-я Поселковая, 1
ФГБОУ ВО «СибАДИ», 2018
|
|
ОГЛАВЛЕНИЕ |
|
Введение……………………………………………………………... |
5 |
||
1. Основы технологии порошковой металлургии……………... |
6 |
||
2. Основы литейного производства……………………………… |
19 |
||
2.1. Теоретические основы производства отливок.…………. |
20 |
||
С |
|
|
24 |
2.2. Формовочные материалы………………………………… |
|||
2.3. Литье в разовые песчано-глинистые формы……………. |
25 |
||
2.4. Разработка чертежей отливок……………………………. |
30 |
||
2.5. Определен е размеров припусков………………………. |
34 |
||
2.6. Расчет л тн ковой системы……………………………... |
37 |
||
литье |
39 |
||
2.7. Л тье под давлением ..…………………………………… |
|||
2.8. Кок льное |
...……………………………………….. |
42 |
|
2.9. Центро ежное литье ……………………………………... |
44 |
||
2.10. Л тье по выплавляемым моделям……………………… |
46 |
||
обра |
47 |
||
2.11. Л тье в о олочковые формы…………………………… |
|||
2.12. Л тье по газифицируемым моделям…………………… |
49 |
||
2.13. Л тье по «ледяным моделям»…………………………... |
51 |
||
2.14. Осо енности |
изготовления отливок из различных |
|
|
|
А |
52 |
|
сплавов …………………………………………….………………… |
|||
3. Основы |
отки металлов давлением……………………... |
54 |
|
3.1. Сущность процессов о работки металлов давлением…. |
54 |
||
3.2. Процессы прокатки……………………………………….. |
66 |
||
3.3. Прессование металлов…………………………………… |
74 |
||
3.4. Волочение…………………………………………………. |
82 |
||
3.5. Процессы свободной ковки……………………………… |
85 |
||
3.6. Процессы точной объемной штамповки…...…………… |
88 |
||
3.7. Горячая раскатка кольцевых заготовок…….…………… |
111 |
||
|
|
И |
|
3.8. Штамповка на термических прессах…………………….. |
115 |
||
3.9. Процессы листовой штамповкиД..……………………….. |
117 |
||
3.10. Штамповка бризантными взрывчатыми веществами.... |
132 |
||
3.11. Штамповка горючими газовыми смесями…………….. |
139 |
||
3.12. Магнитно-импульсная обработка металлов……….…... |
140 |
||
3.13. Электрогидроимпульсная штамповка…………………. |
150 |
||
4. Обработка заготовок резанием ………………………………. |
161 |
||
4.1. Классификация металлорежущих станков …………….. |
161 |
||
4.2. Особенности технологии резания материалов ………… |
162 |
||
4.3. Обработка заготовок точением…………………………. |
165 |
||
4.4. Способы и инструмент обработки отверстий………….. |
189 |
||
4.5. Способы и инструмент обработки фрезерованием……. |
199 |
||
4.6. Способы и инструмент для строгания поверхностей….. |
210 |
3
4.7. Способы и инструмент обработки шлифованием……... |
218 |
||
4.8. Отделочные методы обработки поверхностей………… |
227 |
||
5. Процессы сварочного производства…………………………. |
232 |
||
5.1. Сущность процессов сварки……………………………. |
232 |
||
5.2. Ручная дуговая сварка стали……………………………. |
234 |
||
5.3. Дуговая сварка под флюсом……………………………. |
238 |
||
Свар |
|
|
239 |
5.4. Дуговая сварка в среде защитных газов……………….. |
|||
5.5. Газовая сварка…………………………………………… |
243 |
||
5.6. Контактная электрическая сварка……………………… |
244 |
||
5.7. |
ваемость сталей…………………………………… |
248 |
|
5.8. Спец альные термические процессы при сварке……… |
249 |
||
технологии |
|
251 |
|
5.9. Пайка металлов..…………………………………………. |
|||
6. Основы |
|
производства изделий из |
|
неметалл ческ х композиционных материалов……………. |
253 |
||
6.1. |
характеристика неметаллических материалов…. |
253 |
6.2. Основы |
производства |
изделий из |
|
пластмасс…………………………………………………………….. |
255 |
||
6.3. Основы технологии производства изделий из резины… |
259 |
||
6.4. Характер стика композиционных материалов………… |
261 |
||
6.5. Механизмы упрочнения композиционных материалов |
267 |
||
6.6.ОбщаяНазначение и характеристика |
порошковых, |
|
|
дисперсионно-упрочненных композиционных материалов ..……. |
268 |
||
6.7. Волокнистые композиционные материалы…………..…. |
271 |
||
|
Д |
274 |
|
7. Технологии и оснастка холодной объемной штамповки…... |
|||
7.1. ОсобенностиАхолодной объемной штамповки…………… |
274 |
||
7.2. Способы |
формообразования, |
конструирование |
|
инструмента, построение процессов ХОШ полых изделий…….. |
275 |
||
7.3. Способы формообразования, особенности технологии |
|
||
|
И |
||
получения изделий стержневого типа, схемы инструмента……… |
284 |
||
7.4. Штамповая оснастка для процессов выдавливания………... |
290 |
||
7.5. Материалы инструмента для холодного деформирования |
297 |
||
Контрольные вопросы ……………………………………………. |
298 |
||
Библиографический список …………………………………….... |
303 |
||
|
|
|
4
ВВЕДЕНИЕ
Технологические процессы машиностроительных производств
являются |
основополагающими |
для |
специальностей |
машиностроительного профиля и служат базой для изучения |
|||
С |
|
использования |
|
специальных |
технологических дисциплин. Цель |
учебного пособия – дать будущим специалистам знания по выбору и применен ю технолог ческих методов получения и обработки заготовок деталей машин, обеспечивающих высокое качество продукц , эконом ю материалов и высокую производительность
труда. Основные задачи – изучение физических основ процессов, их |
||
технико-эконом ческ |
х характеристик, области применения, а также |
|
технолог ческ |
х технико-экономических характеристик типового |
|
бА |
||
оборудован я, |
нструмента и приспособлений. |
|
В учебном посо |
и представлены основные фундаментальные |
|
методыобработкиконструкционных материалов: литья, обработки |
давлен ем, сварки, о ра отки резанием, порошковой металлургии. Эти методы в современной технологии конструкционных материалов характеризуются многоо разием традиционных и новых технологических процессов.
Детали машин и при оров по форме и назначению весьма разнообразны, для их изготовления необходимы материалы с самыми
Д машин и приборов, были и остаются Иметаллы. Однако доля
различными свойствами.
Свойства конструкционных материалов во многом определяют
технологию изготовления изделий из них.
Основными материалами, из которых изготовляются детали
неметаллических материалов, применяемых в различных отраслях техники, постоянно возрастает. Некоторые свойства неметаллов,
такие как низкая плотность при достаточной прочности, эластичность, химическая стойкость и другие, во многих случаях делают их незаменимыми при производстве авиационной и автомобильной техники.
Впроизводстве все шире используют порошковые, полимерные
идругие материалы, позволяющие резко повысить технический уровень и надежность изделий.
Особое место среди конструкционных материалов занимают композиционные материалы – искусственно созданные материалы,
5
состоящие из двух и более компонентов различного химического |
||||||||
состава, объединенных в монолит. Свойства композиционного |
||||||||
материала, как правило, отличны от свойств его компонентов, взятых |
||||||||
в отдельности (например, может быть значительно повышена |
||||||||
прочность, жесткость композита). В качестве компонентов в |
||||||||
С |
|
|
|
|
|
|
|
|
композитах используются как металлы, так и неметаллы. |
|
|||||||
1. О НОВЫ ТЕХНОЛОГИИ ПОРОШКОВОЙ МЕТАЛЛУРГИИ |
||||||||
порошками |
– отрасль науки и техники, |
|||||||
Порошковая |
металлургия |
|||||||
охватывающая область производства металлических порошков, а |
||||||||
также здел й |
з н х |
(или их |
|
смесей) с |
неметаллическими |
|||
. |
|
|
|
|
|
|
|
|
бА |
|
|
||||||
Возможности порошковой металлургии для изготовления |
||||||||
машиностро тельных |
материалов |
|
с различными |
свойствами |
||||
практически не ограничены. Методом порошковой металлургии |
||||||||
изготавл ваются |
зделия |
из композиций металлов |
с |
различными |
||||
неметаллическими материалами, из растворимых друг в друге |
||||||||
металлов, из осо о |
тугоплавких |
металлов, |
из |
материалов с |
контролируемой пористостью, в том числе многослойные [1, 2, 3, 4]. Методами порошковой металлургии изготовляют изделия, имеющие специальные свойства: антифрикционные детали узлов приборов и машин (втулки, вкладышиД, опорные шайбы и т.д.), конструкционные детали (шестерни, кулачки и др.), фрикционные детали (диски, колодки и др.), инструментальные материалы (резцы, пластины резцов и фрез, сверла и др.), электротехнические детали
-высокий коэффициент использованияИметалла (К М) – до 96–98% за счет сокращения отходов при обработке, энергосбережение;
-дальнейшая механическая обработка отсутствует или уменьшена;
-можно получать изделия с уникальными свойствами, сложной формы;
6
- возможность |
передела отходов |
в исходный |
материал |
|
(порошок). |
|
|
|
|
Основные этапы порошковой металлургии: получение |
||||
порошков, приготовление смесей (композиций), формообразование |
||||
полуфабрикатов, спекание изделий. |
|
|
||
С |
|
|
|
|
Металлические порошки получают различными способами [2, |
||||
3, 4]: |
|
|
|
|
1) |
змельчен ем в механических |
мельницах |
(щековых, |
|
валковых, |
конусных |
др.) стружки, скрапа и других отходов до |
||
грануляция |
|
|
||
1–10 мм, а затем размолом в шаровых вращающихся, вибрационных |
||||
или планетарных центробежных, вихревых и молотковых мельницах; |
2) распылен ем жидкого металла струей воды или газа (под
давлен ем 50 – 100 МПа), так дешевле всего получать алюминий, |
|
бА |
|
железо, сталь, медь, ц нк, никель. |
|
Распылен е |
жидких металлов является наиболее |
простым дешевым спосо ом изготовления порошков металлов c температурой плавлен я до 1600 °С: алюминия, железа, сталей, меди, цинка, свинца, никеля и других металлов и сплавов.
Сущность измельчения расплава состоит в дроблении струи расплава либо газом, ли о жидкостью, либо механическими распылителями, ли о сливанием струи расплава в жидкую среду (например, воду). Распыление воздухом – самый экономичный способ изготовления порошков;
3) восстановлением окалины, оксидов металлов водородом, углеродом и т.д. (получают порошки молибдена, титана, циркония, тантала, ниобия, легированных сталей и сплавов).
|
И |
Окислы железа восстанавливаются твердым углеродом или |
|
газом. |
Д |
Медные, никелевые и кобальтовые порошки легко получают восстановлением окислов этих металлов, так как они обладают низким сродством к кислороду. Сырьем для производства порошков этих металлов служат либо окись меди Cu2O, CuO, закись никеля NiO, окись – закись кобальта Co2O3, Co3O4, либо окалина от проката проволоки, листов и т.д. Восстановление проводят в муфельных или в трубчатых печах водородом, диссоциированным аммиаком или конвертированным природным газом. Температура восстановления сравнительно низка: меди – 400 – 500 °С, никеля – 700 – 750 °С, кобальта – 520 – 570 °С. Длительность процесса восстановления
7
составляет 1 – 3 ч при толщине слоя окисла 20 – 25 мм. После восстановления получают губку, которая легко растирается в порошок.
Порошок вольфрама получают из вольфрамового ангидрида |
||||||
или паравольфрамата аммония. Восстановление проводят либо |
||||||
С |
|
|
|
|
||
водородом при температуре 850 – 900 °С, либо углеродом при |
||||||
температуре 1350 – 1550 °С в электропечах; |
|
|||||
4) терм ческой диссоциацией карбонилов (соединений типа |
||||||
Меx(CO). |
получают порошки железа, никеля, кобальта, хрома, |
|||||
производстве |
|
|
||||
молибдена, вольфрама; |
|
|
|
|||
5) |
электрол зом |
(этот |
способ наиболее экономичен |
при |
||
|
|
х м чески чистых порошков меди). |
|
|||
В зав |
мости от метода изготовления порошка получают |
|||||
|
губчатую |
|
||||
соответствующую форму частиц: сферическую – при карбонильном |
||||||
способе, |
|
|
– |
при |
восстановлении, осколочную – |
при |
измельчен |
в |
шаровых |
мельницах, тарельчатую – |
при |
||
измельчен |
в в хревых мельницах, дендритную – при электролизе, |
|||||
|
|
|
А |
|
||
каплевидную – при распылении. |
|
|||||
К технологическим свойствам порошков относятся [2, 4]: |
|
|||||
- насыпная масса (масса единицы объема свободно |
||||||
насыпанного порошка); |
|
|
|
|||
- текучесть (способность порошка заполнять форму), которая |
||||||
имеет большое значение при автоматическом прессовании; |
|
|||||
- прессуемость (характеризуется способностью порошка |
||||||
уплотняться |
под |
действием |
внешней нагрузки и прочностью |
- спекаемость (прочность сцепленияДчастиц после спекания); - пирофорность (способность порошка самовозгораться при
сцепления частиц после прессования); И
соприкосновении с воздухом);
- токсичность (ядовитость порошков, которые в атмосфере помещений образуют аэрозоли, способные вызывать болезненное
состояние).
Важная характеристика порошков – гранулометрический состав, под которым понимается соотношение количества частиц различных размеров (фракций), выраженное в процентах. Размеры
частиц порошка обычно составляют 0,1–100 мкм. Фракции порошков размерами более 100 мкм называют гранулами, менее 0,1 мкм – пудрой.
8

Формообразование заготовок. Формование изделий из
порошков осуществляется |
воздействием не только жесткого |
инструмента, но также жидкости, газа, энергии взрывчатых веществ, |
|
магнитного поля [1, 2], электрического разряда в жидкости и др. |
|
уществующие методы прессования можно подразделить по способу |
|
С |
|
подачи шихты – на прерывистые (в пресс-формы) и непрерывные |
|
(прокатной); по способу |
приложения давления – с постепенно |
возрастающ м давлен ем (статические), мгновенно возрастающим давлен ем ( мпульсные) и без давления (литьё, осаждение).
и бА Д
Рис. 1.1. Классификация порошковыхИдеталей
По сложности конфигурации детали, изготавливаемые из порошковых материалов, можно разделить на семь групп (рис. 1.1) [2]:
1) изделия без отверстий с постоянным сечением по высоте, ограниченные параллельными горизонтальными плоскостями;
9
2) изделия с постоянным сечением по высоте, ограниченные параллельными плоскостями, с одним или несколькими отверстиями в направлении прессования и с отношением высоты изделия к минимальной толщине стенки: h/ min 8;
3) изделия, относящиеся ко второй группе, но с отношением
высоты |
к толщине стенки: h/ min 8; |
|
4) |
изделия, близкие по форме деталям второй группы, но с |
|
небольш м ч слом переходов по сечению и общим отношением |
||
высоты к толщ не стенки: h/ min 6; |
||
стенки |
||
5) |
здел я, относящиеся к четвертой группе, но с отношением |
|
Свысоты к толщ не |
: h/ min 6; |
|
6) |
здел я |
ез отверстий, имеющие по высоте несколько |
переходов; |
|
|
7) |
бА |
|
здел я с отверстиями, имеющие несколько наружных или |
||
внутренн х переходов в направлении прессования, а также детали, |
ограниченные непараллельными плоскостями или криволинейными поверхностями, пересекающими ось направления прессования.
Прессование может ыть односторонним (рис. 1.2, а) и двухсторонним (рис. 1.2, ). Односторонним прессованием получают заготовки простой формы с отношением высоты к диаметру меньше единицы и заготовки типа втулок с отношением наружного диаметра
к толщине стенки меньше Дтрех. вухстороннее прессование
применяют для формообразования заготовок сложной формы и большей высоты. В этом случае требуемое давление для получения
равномерной плотности снижается на 30 – 40%.
Давление прессования зависит от требуемой плотности, формы прессуемой заготовки, вида прессуемого порошкаИи других факторов.
Использование вибрационного прессования позволяет в десятки раз уменьшить необходимое давление.
В процессе прессования увеличивается контакт между частицами, уменьшается пористость, деформируются или разрушаются отдельные частицы. Прочность получаемой заготовки обеспечивается в основном силами механического сцепления частиц порошка. С увеличением давления прессования прочность заготовки возрастает. В процессе прессования частицы порошка подвергаются упругим и пластическим деформациям, в результате чего в заготовке накапливаются значительные напряжения. После извлечения из
10
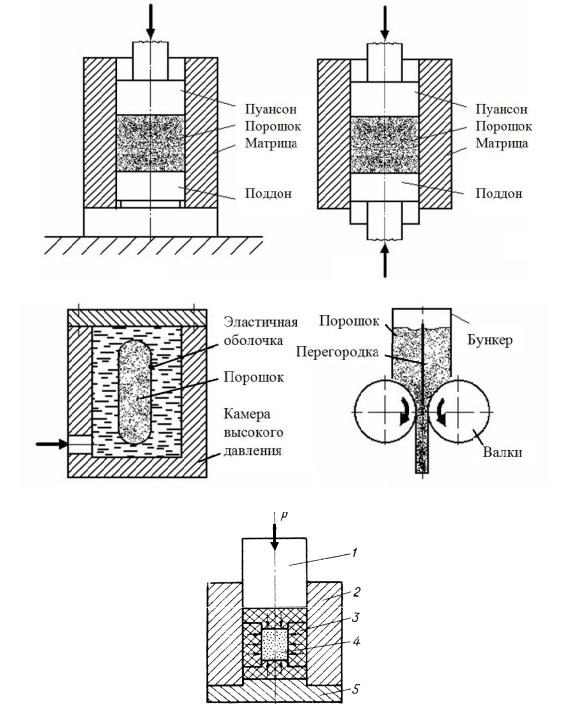
пресс-формы заготовки размеры ее изменяются за счет упругого последействия.
С |
|
|
|
|
и |
|
|
|
|
|
|
|
||
|
|
|
||
бА |
||||
|
а |
|
б |
|
|
|
|
|
|
|
|
Д |
в г д И
Рис. 1.2. Схемы формообразования заготовок из металлических порошков:
а– одностороннее прессование; б – двухстороннее прессование;
в– изостатическое (гидростатическое) прессование; г – прокатка;
д – одностороннее гидростатическое прессование
11
В последнее время широкое распространение получил метод
изостатического (всестороннего, |
гидростатического) |
прессования |
||||
(рис. 1.2, в) [2]. Изостатическое прессование, в основе которого |
||||||
лежит известный закон Паскаля, позволяет поместить материал в |
||||||
жидкую или газообразную среду, на которую действует |
||||||
С |
|
|
|
|
|
|
определенное давление, которое распределяется равномерно по всей |
||||||
поверхности материала. Таким образом, материал подвергается |
||||||
сжатию по мног м направлениям, образуя прессовку, которая |
||||||
обладает формой, аналогичной заготовке, но меньших размеров в |
||||||
зависимости от прессуемого материала, а также от применяемого |
||||||
давлен я. Эта технология позволяет получать материалы с |
||||||
гомогенной мелкозерн стой структурой, без сегрегаций, с высокими |
||||||
прочностными |
пластическими |
характеристиками. |
Во |
многих |
||
бА |
|
|
|
|||
случаях эти характеристики значительно превышают уровень, |
||||||
достигаемый при горячей деформации соответствующих компактных |
||||||
матерНедостаткиалов. |
гидростатического |
прессования: |
||||
невозможность получения прессованных деталей с заданными |
||||||
размерами, |
нео ходимость |
механической |
доработки |
при |
||
изготовлении |
изделий точной |
формы и размеров, а |
также малая |
производительность процесса.
Одним из наи олее производительных и перспективных способов переработки порошковых материалов является прокатка. Порошок непрерывно поступаетДиз бункера в зазор между валками. При вращении валков происходят обжатие и вытяжка порошка в ленту или полосу определенной толщины (рис. 1.2, г). Процесс прокатки может быть совмещен со спеканием и окончательной обработкой получаемых заготовок. В этомИслучае лента проходит через печь для спекания, а затем снова подвергается прокатке с целью придания ей заданных размеров. В бункере может присутствовать перегородка для изготовления двухслойных лент.
Самым простым и универсальным способом изготовления изделий из порошковых материалов является эластостатическое прессование (ЭлП) [2] в толстостенных эластичных оболочках (рис. 1.2, д). Применение эластомеров позволяет реализовать практически любую схему напряженно-деформированного состояния
впрессуемом материале.
Вмассовом производстве изделий типа профилей, труб и т.д. используется технология мундштучного прессования – формование
12
заготовок из смеси порошка с пластификатором путем продавливания ее чеpeз отверстие в матрице (мундштук). В качестве пластификатора применяют парафин, крахмал, поливиниловый спирт, бакелит. Этим методом получают трубы, прутки, уголки и
другие изделия большой длины. |
|
|
|
|
С |
|
|
|
|
Мундштучным формованием получают длинномерные изделия |
||||
с равномерной |
плотностью из |
плохо |
прессуемых |
материалов |
(тугоплавк е металлы и соединения, твердые сплавы, керметы на |
||||
основе окс дов |
др.). |
|
|
|
сечения |
|
|
|
|
На р с. 1.3, а показана пресс-форма для прессования труб на |
||||
гидравл ческом |
прессе. В обойме |
1 с |
мундштуком |
переменного |
2 установлена звездочка 4 с ввинченной иглой 3. Над
обоймой наход |
тся матрица 6, соединенная с ней гайкой 5. |
||
бА |
заготовку |
||
Предвар тельно |
спрессованную |
цилиндрическую |
вставляют в матр цу выдавливают пуансоном 7 через зазор между иглой звездочки мундштуком.
Стержни получают в такой же пресс-форме, но без звездочки с иглой. Например, пресс-форма (рис. 1.3, б) для выдавливания заготовок сверл состоит из пуансона 1, матричной воронки 2 с запрессованной в нее матрицей 3 с резьбовой полостью, изготовленной из твердого сплава. Контейнер составной – корпус 5, гильза 6 и гайка – опора 4.
Динамическое (импульсное) прессование – это процессы прессования с использованием импульсных нагрузок. Отличительной
чертой является скорость |
приложения нагрузки. |
сточниками |
энергии могут быть: взрыв заряда взрывчатого вещества, энергия |
||
|
И |
|
электрического разряда в жидкости, импульсное магнитное поле, |
||
сжатый газ, вибрация. |
Д |
Например, применение вибрации при прессовании позволяет снизить величину прилагаемого давления примерно в 100 раз. Для этой цели используются механические вибраторы частотой 233 Гц и амплитудой 0,03 мм (см. рис. 1.3, а) [2]. Вибратор соединен гибким валом с булавой, расположенной под пресс-формой на пружинах. Время вибрационного прессования составляет: 4 – 10 с – для смесей твердых сплавов, 5 – 15 с – для порошков жаропрочных соединений, 10 – 60 с – для порошка меди. Плотность получаемых прессовок может достигать 90% теоретического значения.
13
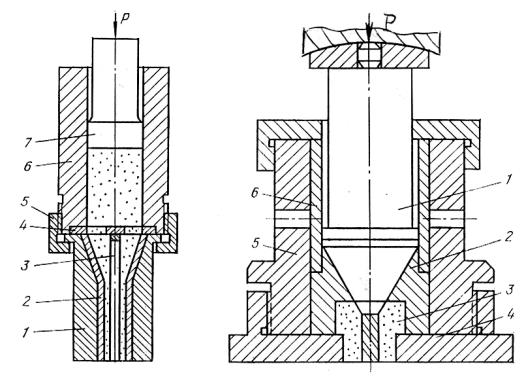
Си бАа б
Рис. 1.3. Пресс-формы для мундштучного прессования [2]
Тонкие порошковые детали типа шайб или пластин любой
конфигурации в плане можно изготавливать методом пакетного прессования в закрытых пресс-формах с применением промежуточных проставок. Такая технология позволяет выталкивать прессовки без разрушения и добиваться почти одинаковой плотности
всех прессовок. Стальные прокладки используются неоднократно
(рис. 1.4).
Спекание заготовок проводится в электропечах сопротивления |
|
или индукционных печах, |
Д |
но чаще в вакуумной или |
|
восстановительной атмосфере, |
что способствует удалению оксидов. |
Температура спекания составляет 0,6 – 0,9 температуры плавления
основного материала порошка. Время выдержки 30 |
– 90 мин. В |
|||
процессе спекания происходит рост контактов между отдельными |
||||
|
|
|
И |
|
частицами порошка вследствие восстановления оксидов, диффузии, |
||||
рекристаллизации. Прочность изделия повышается. |
|
|||
Наибольшую |
активность |
при |
спекании |
проявляют |
мелкодисперсные порошки неравноосной формы. |
|
14
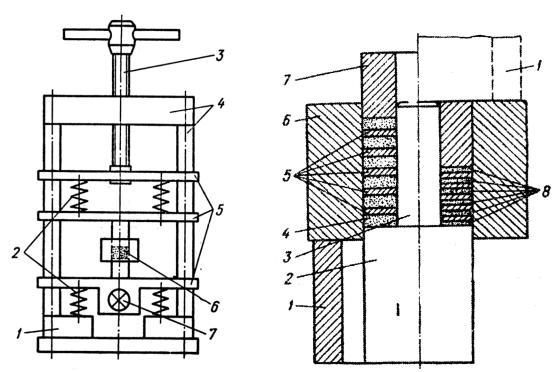
С |
|
и |
|
б |
б |
а |
|
А |
|
Рис. 1.4. Пресс для ви рационного прессования (а): 1 – основание; |
|
2 – пружины; 3 – нагрузочный винт; 4 – станина; 5 – промежуточные |
|
плиты; 6 – пресс-форма; 7 – вибратор. Пресс-форма для пакетного |
|
прессования тонких деталей ( ): 1 – подставка; 2 – нижний пуансон; |
|
3 – стержень; 4 – порошок; 5 – промежуточные стальные проставки; |
|
Д |
|
6 – матрица; 7 – верхний пуансон; 8 |
– спрессованные изделия |
Спеченные материалы можно подвергать ковке, прокатке, штамповке при повышенных температурах. Обработка давлением
позволяет снизить пористость материалов и повысить их |
|
пластичность [3]. |
И |
|
Усадка при спекании может проявляться в изменении размеров и объема, поэтому различают линейную и объемную усадку. Обычно усадка в направлении прессования больше, чем в поперечном направлении. Порошки с развитой поверхностью уплотняются при спекании с наибольшей скоростью, как обладающие большим запасом поверхностной энергии.
При увеличении плотности прессовок усадка при спекании уменьшается.
При прессовании твердосплавных изделий в качестве пластификаторов предпочтительно использовать раствор синтетического каучука в бензине. Прочность кромок спрессованных
15
изделий, равномерность распределения плотности и легкость удаления – таковы его преимущества. Недостатком этого пластификатора (он вводится в количестве около 1,0%) является неполная отгонка, содержание углерода увеличивается на 0,1 – 0,2%. Важно обеспечить равномерное смешивание порошка с пластификатором, иначе возможно появление зон графитовых включений. Давление прессования в твердосплавном производстве невелико – 60 – 150 МПа, так как нет необходимости в получении при
прессован |
высокоплотных изделий. Пористость заготовок – около |
50%. Как показывает практика, пористость спрессованных твердых |
|
сплавов практ чески не влияет на прочность спеченных изделий. |
|
С |
|
Прессован е в жестких пресс-формах является наиболее |
|
распространенным при производстве деталей практически всех |
|
групп |
. При этом вы ираются конструкции пресс-форм, в |
сложности которых вбАмакс мальной степени устраняется неравномерное
распределен е плотности прессовок, вызываемое действием сил трения на контакте прессовок и инструмента и сложной формой изделия [4].
На рис. 1.5 показана пресс-форма [2] для формовки втулки 2 в матрице 3. Засыпка порошка производится тогда, когда стержень 4 и матрица подняты выталкивателем пресса вверх относительно контрпуансона 5, установленного на плите 6 (положение б). Прессование осуществляется пуансоном 1 (положение в). При опускании выталкивателя матрица стягивается с изделия и устанавливается так, что ее торец оказывается на одном уровне с торцами стержня и
контрпуансона. |
Изделие сталкивается ползушкой засыпного |
|
аппарата. |
|
И |
В практике |
порошковой |
Дметаллургии все чаще используют |
пресс-формы, в которых усилие пресса через стальной пуансон передается на контейнер из эластомера, в результате чего осевое давление преобразуется эластичной средой во всестороннее сжатие для интенсивного уплотнения порошка [4].
Эластомер должен обеспечивать близкое к гидростатическому давление на порошок. Наибольшее распространение получили полиуретаны марок СКУ-7Л, СКУ-ПФЛ, позволяющие изготовлять литьем эластичные контейнеры сложной формы. Более равномерное по высоте распределение деформаций в заготовке происходит при двухстороннем прессовании.
16
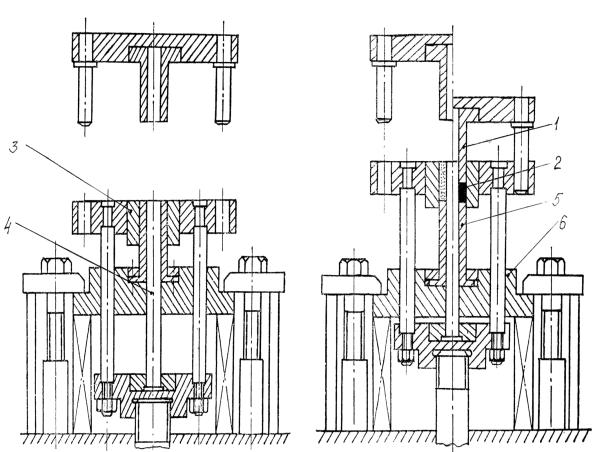
С |
|
|
и |
|
|
а |
б |
в |
Рис. 1.5. Пресс-форма для формовки деталей типа «втулка» |
||
Д |
||
В таблбА. 1.2 представлена классификация основных схем |
||
эластостатического прессования |
трубных деталей |
[1]. В основу |
классификации положены такие технологические критерии, как схема прессования и направление движения инструмента. Среди схем с односторонним движением инструментаИвыделены схемы прессования с применением конусного инструмента.
Метод дает возможность применять как простые схемы прессования (раздача или обжим), так и комбинированные (осевое прессование с раздачей). Эти схемы позволяют осуществлять прессование втулок в направлении наименьшей толщины материала, что обеспечивает получение изделий высокой плотности при минимальных энергетических затратах.
Практика показала, что плотность деталей, деформируемых по любой из схем эластичного прессования, выше, чем при формовке в жесткой пресс-форме.
17
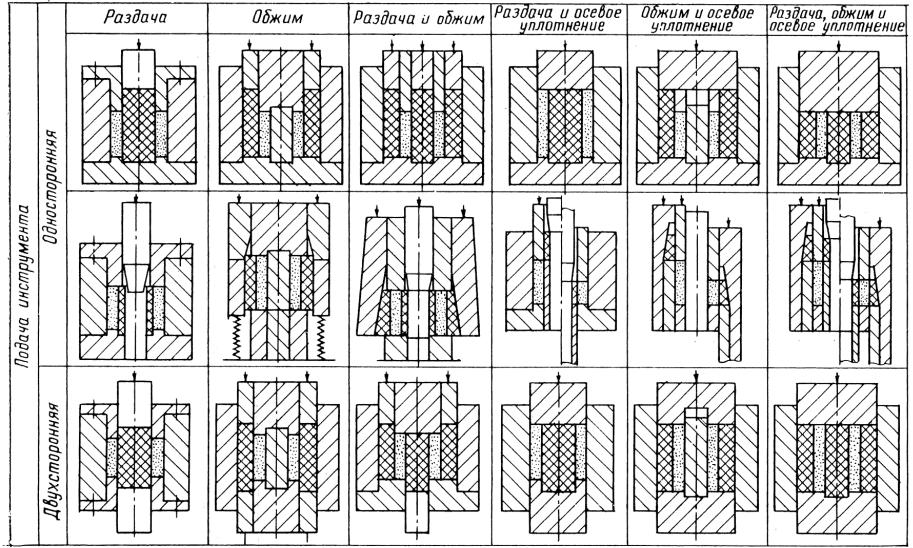
С |
Таблица 1.2 |
Класс ф кац я схем эластостатического прессования |
|
и |
|
б |
|
А |
|
Д |
|
И |
|
18