
- •ВВЕДЕНИЕ
- •2. ОСНОВЫ ЛИТЕЙНОГО ПРОИЗВОДСТВА
- •2.1. Теоретические основы производства отливок
- •2.2. Формовочные материалы
- •2.3. Литье в разовые песчано-глинистые формы
- •2.4. Разработка чертежей отливок
- •2.5. Определение размеров припусков на механическую обработку
- •2.6. Расчет литниковой системы
- •2.7. Литье под давлением
- •2.8. Кокильное литье
- •2.9. Центробежное литье
- •2.12. Литье по газифицируемым моделям
- •2.13. Литье по ледяным моделям
- •2.14. Особенности изготовления отливок из различных сплавов
- •3. ОСНОВЫ ОБРАБОТКИ МАТЕРИАЛОВ ДАВЛЕНИЕМ
- •3.1. Сущность процессов обработки материалов давлением
- •3.2. Процессы прокатки
- •3.3. Прессование металлов
- •3.4. Волочение
- •3.5. Процессы свободной ковки
- •3.6. Процессы точной объемной штамповки
- •3.6.1. Выбор методов и способов производства заготовок объемной штамповкой
- •3.6.2. Разработка технологии открытой объемной штамповки
- •3.6.3. Определение класса точности поковки
- •3.6.4. Определение группы стали
- •3.6.6. Определение исходного индекса
- •3.6.8. Определение допусков на размеры поковки
- •3.6.9. Разработка чертежа холодной поковки
- •3.6.10. Назначение напусков
- •3.6.11. Разработка чертежа горячей поковки
- •3.6.12. Определение размеров исходной заготовки
- •3.7. Горячая раскатка кольцевых заготовок
- •3.8. Штамповка на термических прессах
- •3.9. Процессы листовой штамповки
- •3.10. Штамповка бризантными взрывчатыми веществами
- •3.11. Штамповка горючими газовыми смесями
- •3.12. Магнитно-импульсная обработка металлов
- •3.13. Электрогидроимпульсная штамповка
- •4.1. Классификация металлорежущих станков
- •4.2. Особенности технологии резания материалов
- •4.4. Способы и инструмент обработки отверстий
- •4.5. Способы и инструмент обработки фрезерованием
- •4.6. Способы и инструмент для строгания поверхностей
- •4.7. Способы и инструмент обработки шлифованием
- •4.8. Отделочные методы обработки поверхностей
- •5.1. Сущность процессов сварки
- •5.2. Ручная дуговая сварка стали
- •5.3. Дуговая сварка под флюсом
- •5.4. Дуговая сварка в среде защитных газов
- •5.5. Газовая сварка
- •5.6. Контактная электрическая сварка
- •5.7. Свариваемость сталей
- •5.8. Специальные термические процессы при сварке
- •5.9. Пайка металлов
- •6.1. Общая характеристика неметаллических материалов
- •6.2. Основы технологии производства изделий из пластмасс
- •6.3. Основы технологии производства изделий из резины
- •6.4. Характеристика композиционных материалов
- •6.5. Механизмы упрочнения композиционных материалов
- •6.6. Назначение и характеристика порошковых, дисперсно-упрочненных композиционных материалов
- •6.7. Волокнистые композиционные материалы
- •7. ТЕХНОЛОГИИ И ОСНАСТКА ХОЛОДНОЙ ОБЪЕМНОЙ ШТАМПОВКИ
- •7.1. Особенности холодной объемной штамповки
- •7.3. Способы формообразования, особенности технологии получения изделий стержневого типа, схемы инструмента
- •7.4. Штамповая оснастка для процессов выдавливания
- •7.5. Материалы инструмента для холодного деформирования
- •КОНТРОЛЬНЫЕ ВОПРОСЫ
- •Контрольные вопросы к разделу 1
- •Контрольные вопросы к разделу 2
- •Контрольные вопросы к разделу 3
- •Контрольные вопросы к разделу 4
- •Контрольные вопросы к разделу 5
- •Контрольные вопросы к разделу 6
- •Контрольные вопросы к разделу 7
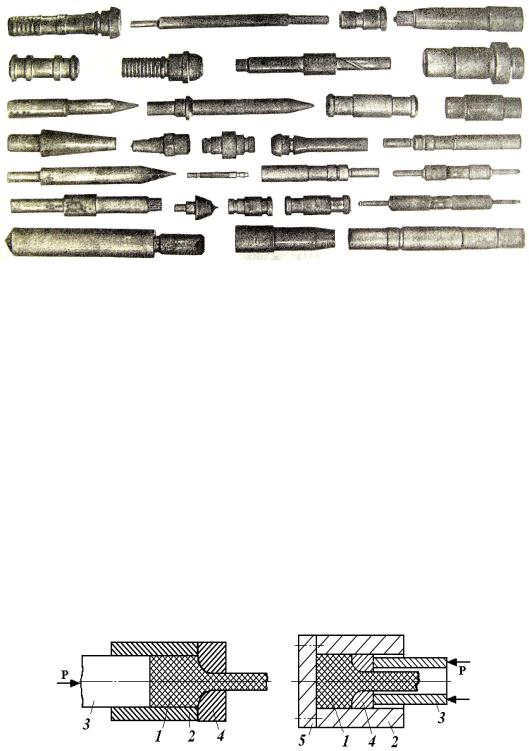
Для профилирования заготовок переменного сечения (рис. 3.22) широко используются станы с инструментами в виде клиньев, расположенных на валках или плоских плитах.
СиР с. 3.22. Издел я, полученные поперечно-клиновой прокаткой
ПрессованиебАможет выполняться двумя методами. При прямом методе (рис. 3.23, а) заготовку 1 выдавливают из контейнера 2 пуансоном 3 через отверстие в матрице 4. При обратном прессовании
3.3. Прессование металлов
Прессование – процесс выдавливания металла из контейнера
через отверстие в матрице [10, 11].
(рис. 3.23, б) давление пресса передаетсяДзаготовке 1 через полый пуансон 3 с смонтированной внутри его матрицей 4. Таким образом, металл заготовки 1 течет навстречу движению пуансона. При обратном прессовании усилие на 25 – 30% меньше, чем при прямом прессовании.
И
а |
б |
Рис. 3.23. Схемы прессования: 1 – заготовка; 2 – контейнер; 3 – пуансон; 4 – матрица; 5 – держатель
74
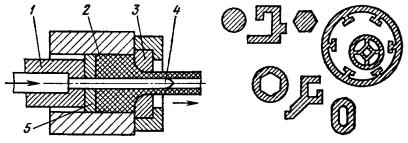
Достоинства процессов прессования (особенности):
- реализуется одна из самых благоприятных схем нагружения, обеспечивающая максимальную пластичность – всестороннее неравномерное сжатие. Это позволяет обрабатывать даже малопластичные материалы. Благодаря этому возможна обработка с высокой степенью деформации: Fзаг/Fпресс. изд = (10 – 50)/1;
- возможность получения профилей сложной формы, в том
числе |
пустотелых, |
что зачастую невозможно при других способах |
|||
обработки пласт ческой деформацией. |
(рис. 3.24, а) при |
||||
|
прессован и |
полых профилей |
|||
движен |
пуансона |
1 |
и пресс-шайбы 5 |
металл заготовки 2 |
|
С |
|
|
|
||
выдавл вается |
з контейнера в зазор между матрицей 3 и иглой 4. |
||||
Прессован |
ем |
зготовляют изделия разнообразного сортамента |
|||
из цветных металлов |
сплавов, в том числе прутки диаметром от 3 |
||||
до 250 мм, |
д аметром от 20 до 400 мм со стенкой толщиной от |
||||
При |
|
||||
1,5 до 12 мм друг е профили (рис. 3.24, б). Из углеродистых сталей |
20, 35, 45, 50, конструкционных 30ХГСА, 40ХН, коррозионно- |
|||
стойких 12Х18Н10Т и других высоколегированных сталей прессуют |
|||
трубы с внутренним диаметром 30 – 160 мм со стенкой толщиной 2 – |
|||
10 мм. |
трубы |
||
А |
|||
|
|||
|
а |
б |
|
|
|
Д |
|
|
|
И |
Рис. 3.24. Схема прессования полого профиля (а) и примеры прессованных профилей (б)
При производстве изделий из труднодеформируемых и малопластичных сплавов довольно широко используются процессы гидропрессования [13, 14].
При прессовании проталкиванию металла препятствуют силы трения, поэтому контактное трение является причиной исключительно высокой энергоёмкости процесса. Более 60% энергии пресса затрачивается на преодоление сил трения.
75
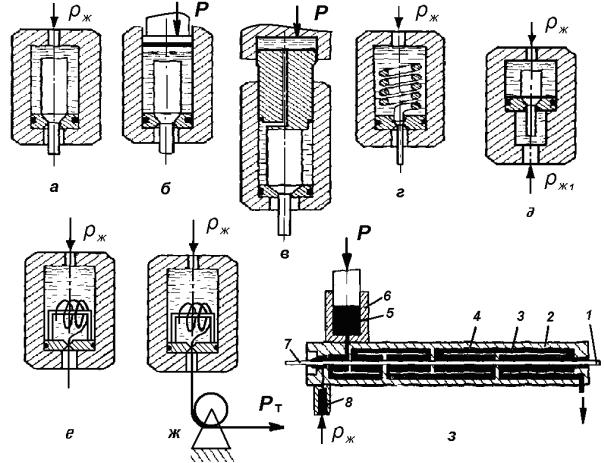
Силы трения можно снизить принудительной подачей смазки в матрицу и контейнер или заполнением зазоров между заготовкой, контейнером и матрицей газами, жидкостями или квазижидкими средами. На рис. 3.25 приведены схемы установок различных типов для прессования прутков и проволоки, а также для непрерывного
Спрессования проволоки.
и бА Д
Рис. 3.25. Основные схемы гидропрессования сплошныхИметаллических заготовок: а – компрессорное гидростатическое прессование;
б – бескомпрессорное (прямое) гидропрессование; в – гидромеханическое прессование; г – гидропрессование длинной заготовки; д – гидростатическое прессование с противодавлением; е – гидропрессование проволокой заготовки
сбобины; ж – гидропрессование проволоки с натяжением;
з– непрерывное прессование : 1 – пруток; 2 – контейнер; 3 – возвратные каналы; 4 – «проталкивающая» жидкость; 5 – камера; 6 – установка сжатия
«проталкивающей» жидкости; 7 – изделие; 8 – источник высокого давления «формующей» жидкости
76
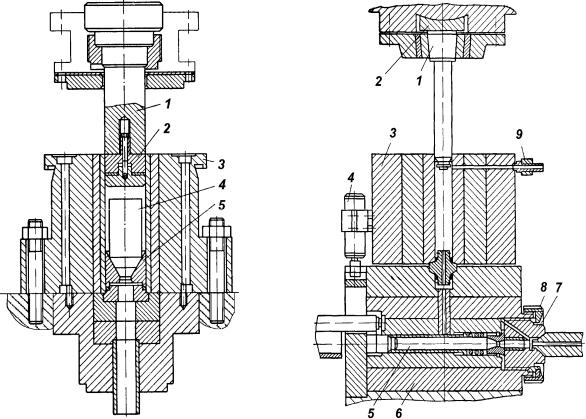
В установке, схема которой приведена на рис. 3.25, з, для |
||||
достижения непрерывности процесса используется активный |
||||
характер вязкого трения жидкости. Проволочная заготовка |
||||
непрерывно поступает в контейнер 2. Контейнер разбит на ряд зон, в |
||||
которых создан направленный поток «проталкивающей» жидкости. |
||||
С |
|
|
|
|
Вязкость жидкости подбирают так, чтобы продольное усилие вязкого |
||||
трения, возникающее при обтекании прутка, было достаточным для |
||||
проталк ван я заготовки в формующую зону. Для успешного |
||||
протекан я |
процесса необходимо |
определенное превышение |
||
воронки |
|
|
||
давлен я «формующей» жидкости над осевыми напряжениями. |
||||
Поэтому ж дкость |
дополнительно |
подают в область матричной |
||
от |
сточн ка 8 (вынесенного или прямого действия). |
|||
Установки прямого гидропрессования проектируются в двух |
||||
бА |
||||
вариантах (р |
с. 3.26 |
3.27). |
|
|
|
|
|
Д |
|
Рис. 3.26. |
|
|
И |
|
|
|
Рис. 3.27. Установка с |
||
Гидроэкструзионная |
независимой камерой сжатия: |
|||
установка прямого действия: |
|
1 – плунжер; 2 – опора; |
||
1 – пресс-штемпель; 2 – пресс- |
|
3 – контейнер; 4 – затвор; |
||
шайба с уплотнительным |
5 – заготовка; 6 – рабочий |
|||
узлом; 3 – контейнер; |
цилиндр; 7 – калиброванное |
|||
4 – заготовка; |
|
кольцо; 8 – запор матрицы; |
||
5 – матричный узел |
9 – подводящая магистраль |
|||
|
|
|
77 |
|
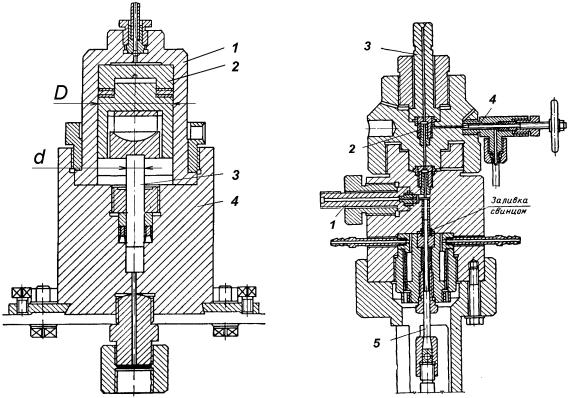
В установки (см. рис. 3.25, а, б, г, д, е, ж) жидкость высокого давления подается от мультипликаторов или гидрокомпрессоров
(рис. 3.28 и 3.29).
С |
|
и |
|
бА |
|
Рис. 3.28. Устройство |
Рис. 3.29. Устройство |
мультипликатора |
гидрокомпрессора |
Устройство и принцип работы мультипликатора видны из рис. |
||
3.28. При подаче масла в цилиндр низкого давления 1 происходит |
||
И |
||
перемещение поршня 2, который толкает плунжер |
3. |
При |
перемещении плунжера давлениеДжидкости в цилиндре 4 |
и в |
связанной с ним системе возрастает. Вследствие разности диаметров поршня низкого давления D и плунжера d давление в цилиндре высокого давления будет в D2/d2 раз выше, чем в цилиндре низкого давления (рж до 800 – 1500 МПа).
Несмотря на возможность повышать давление многократно, установки с мультипликатором отличаются низкой производительностью, процесс подготовки установок весьма трудоемок.
Для создания давления в контейнере может быть применена система, состоящая из газового аккумулятора, гидрокомпрессора и
78
ресивера. Жидкостно-газовый аккумулятор подает рабочую жидкость в гидрокомпрессор под давлением 10 МПа. Из гидрокомпрессора жидкость поступает в ресивер – сосуд высокого давления. Ресивер служит для накопления в большом объеме (по сравнению с объемом
контейнера) жидкости высокого давления (рж до 2000 – 3500 |
|||||
С |
|
|
|
|
|
МПа).Разрез рабочей головки гидрокомпрессора показан на рис. |
|||||
3.29. Давление создается плунжером 5, который приводится в |
|||||
движен е от кр вош пно-шатунного механизма. Рабочая жидкость |
|||||
забирается |
з аккумулятора через штуцер 1. Штуцер 3 соединен с |
||||
ями |
4 осуществляются заполнение всей |
||||
ресивером. |
Через вентиль |
||||
системы |
сброс давления. При перемещении плунжера 5 жидкость |
||||
небольш |
порц |
нагнетается в ресивер. Обратный поток |
|||
жидкости удерж вается клапаном 2. |
|
|
|||
|
более |
внедрении |
технологий |
||
Знач тельные |
трудности при |
||||
гидропрессован |
возникают из-за того, что давления жидкости |
||||
составляют |
1000 МПа. Поэтому |
уплотнения |
выдерживают |
небольшое кол чество циклов: 2 – 3 при давлении 1500 – 2000 МПа, 10 – 15 при давленииА1000 – 1500 МПа. Поэтому их
конструированию и размещению в установке уделяют особое внимание. Уплотняющие элементы могут быть подвижными (крепятся на пуансоне) и неподвижными. Передающие среды должны удовлетворять требованиям: иметь минимальную
могут быть твёрдыми (свинец иДего сплавы, фторопласт, материалы на основе графита или дисульфита молибдена), жидкими, порошкообразными.
сжимаемость, сохранять свойства при различных температурах, не взаимодействовать с материалом заготовки, иметь низкую теплопроводность и теплоёмкость, сохранять химический состав, не быть токсичными, огне- и взрывоопасными, быть пластичными. Они
Следует учитывать, что вязкость жидкостей возрастает с увеличением давления. Например, при 400 МПа вязкость воды
И
увеличивается в 1,35 раза, керосина – в 50 раз, масла трансформаторного – в 4500 раз. Масло «замерзает» при 1000 МПа. При горячем выдавливании вязкость снижается.
При холодном гидропрессовании используют керосин, масло касторовое или веретенное (до 500 МПа), глицерин, этиленгликоль с глицерином, изопентан с бензином, бензин Б70, воду (при
79
р = 1000 МПа); при горячем гидропрессовании – битум, битум с графитом, стекла, расплавы солей, графит.
Значительные трудности при внедрении технологий |
|||
гидропрессования возникают из-за того, что давление жидкости |
|||
составляет более 1000 МПа; уплотнения выдерживают небольшое |
|||
С |
|
|
|
количество циклов: 2 – 3 при давлении 1500 – 2000 МПа, 10 – 15 при |
|||
давлении 1000 – 1500 МПа. Поэтому их конструированию и |
|||
размещен ю в установке уделяют особое внимание. |
|||
Уплотняющ е элементы могут быть подвижными (крепятся на |
|||
значительно |
|
||
пуансоне) |
неподв жными. Запирающее действие первых зависит |
||
от качества |
зготовления полости контейнера на всей длине, даже |
||
небольш е р ски пр водят к утечке жидкости; у вторых стойкость |
|||
|
выше. |
|
|
либо |
высокими давлениями в |
||
Уплотнен |
еспечивается |
||
контактных зонах, |
о самоуплотняющейся системой, в которой |
||
уплотнен е улучшается по мере увеличения давления жидкости. |
|||
Выбор способа уплотнения зависит от типа установки и диапазона |
|||
|
|
А |
|
давления жидкой среды. |
|
||
Наиболее распространенным и |
эффективным является |
уплотнение, предложенное Бриджменом и основанное на использовании принципа так называемой некомпенсированной площади. Этот тип подвижного уплотнения показан на рис. 3.30, а, б, в. В пуансоне 1 имеется глухое отверстие, в которое плотно входит стержень грибка 5. Между грибком и пуансоном устанавливают набор шайб. Шайбы 2 и 4 изготовлены из меди М3, шайба 3 – из фторопласта 4. Во время работы установки давление на шайбы
всегда больше давления жидкостиДв контейнере. Шайбы, деформируясь, заполняют зазор между пуансоном и контейнером. Уплотнение может надежно работать и при отсутствии фторопластового кольца (рис. 3.30, в).
Надежное уплотнение получается при запрессовке в контейнер
И
7 медного кольца по схеме, представленной на рис. 3.30, г. Недостаток такого уплотнения – необходимость изготовления большого количества медных колец 6 (повторное использование кольца невозможно), а также трудность последующего извлечения кольца из контейнера. Второй недостаток свойственен и уплотнениям грибкового типа при выполнении их по схеме, представленной на рис. 3.30, а, б, в: грибок с уплотнительными
80
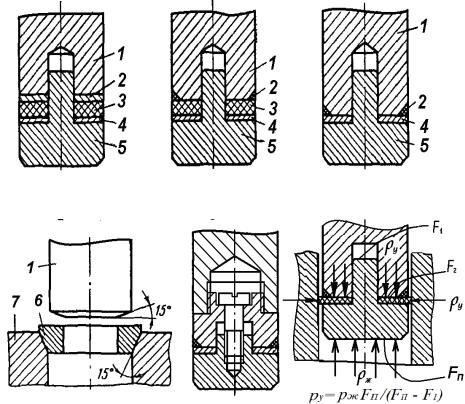
шайбами, как правило, остается в контейнере и для их извлечения приходится разбирать всю установку.
Са |
в |
и |
|
б |
|
А |
е |
г д |
|
Д |
Рис. 3.30. Основные способы уплотнения пуансона
При давлениях жидкости до 3000 МПа для пуансона может использоваться неподвижная конструкция уплотнения сальникового типа (рис. 3.31, а), исключающая необходимость точной подгонки плунжера к внутреннему диаметру контейнераИ. При этом диаметр нажимного кольца 1 из закаленной стали ШХ15 точно подгоняли по размеру плунжера и его гнезду. Подпорные кольца 2, 3 и 5 изготавливали из бронзы, а уплотняющее кольцо 4 – из фторопласта и вставляли в гнездо с натягом.
Матрицы (рис. 3.31, б) в контейнере уплотнялись с помощью только двух колец; опорное кольцо 6 из бронзы или латуни устанавливали с небольшим зазором, а фторопластовое кольцо 7 – между матрицей 8 и контейнером – с натягом.
На рис. 3.32 показано неподвижная конструкция уплотнения матрицы при гидростатическом прессовании, которое представляет
81