
- •ВВЕДЕНИЕ
- •2. ОСНОВЫ ЛИТЕЙНОГО ПРОИЗВОДСТВА
- •2.1. Теоретические основы производства отливок
- •2.2. Формовочные материалы
- •2.3. Литье в разовые песчано-глинистые формы
- •2.4. Разработка чертежей отливок
- •2.5. Определение размеров припусков на механическую обработку
- •2.6. Расчет литниковой системы
- •2.7. Литье под давлением
- •2.8. Кокильное литье
- •2.9. Центробежное литье
- •2.12. Литье по газифицируемым моделям
- •2.13. Литье по ледяным моделям
- •2.14. Особенности изготовления отливок из различных сплавов
- •3. ОСНОВЫ ОБРАБОТКИ МАТЕРИАЛОВ ДАВЛЕНИЕМ
- •3.1. Сущность процессов обработки материалов давлением
- •3.2. Процессы прокатки
- •3.3. Прессование металлов
- •3.4. Волочение
- •3.5. Процессы свободной ковки
- •3.6. Процессы точной объемной штамповки
- •3.6.1. Выбор методов и способов производства заготовок объемной штамповкой
- •3.6.2. Разработка технологии открытой объемной штамповки
- •3.6.3. Определение класса точности поковки
- •3.6.4. Определение группы стали
- •3.6.6. Определение исходного индекса
- •3.6.8. Определение допусков на размеры поковки
- •3.6.9. Разработка чертежа холодной поковки
- •3.6.10. Назначение напусков
- •3.6.11. Разработка чертежа горячей поковки
- •3.6.12. Определение размеров исходной заготовки
- •3.7. Горячая раскатка кольцевых заготовок
- •3.8. Штамповка на термических прессах
- •3.9. Процессы листовой штамповки
- •3.10. Штамповка бризантными взрывчатыми веществами
- •3.11. Штамповка горючими газовыми смесями
- •3.12. Магнитно-импульсная обработка металлов
- •3.13. Электрогидроимпульсная штамповка
- •4.1. Классификация металлорежущих станков
- •4.2. Особенности технологии резания материалов
- •4.4. Способы и инструмент обработки отверстий
- •4.5. Способы и инструмент обработки фрезерованием
- •4.6. Способы и инструмент для строгания поверхностей
- •4.7. Способы и инструмент обработки шлифованием
- •4.8. Отделочные методы обработки поверхностей
- •5.1. Сущность процессов сварки
- •5.2. Ручная дуговая сварка стали
- •5.3. Дуговая сварка под флюсом
- •5.4. Дуговая сварка в среде защитных газов
- •5.5. Газовая сварка
- •5.6. Контактная электрическая сварка
- •5.7. Свариваемость сталей
- •5.8. Специальные термические процессы при сварке
- •5.9. Пайка металлов
- •6.1. Общая характеристика неметаллических материалов
- •6.2. Основы технологии производства изделий из пластмасс
- •6.3. Основы технологии производства изделий из резины
- •6.4. Характеристика композиционных материалов
- •6.5. Механизмы упрочнения композиционных материалов
- •6.6. Назначение и характеристика порошковых, дисперсно-упрочненных композиционных материалов
- •6.7. Волокнистые композиционные материалы
- •7. ТЕХНОЛОГИИ И ОСНАСТКА ХОЛОДНОЙ ОБЪЕМНОЙ ШТАМПОВКИ
- •7.1. Особенности холодной объемной штамповки
- •7.3. Способы формообразования, особенности технологии получения изделий стержневого типа, схемы инструмента
- •7.4. Штамповая оснастка для процессов выдавливания
- •7.5. Материалы инструмента для холодного деформирования
- •КОНТРОЛЬНЫЕ ВОПРОСЫ
- •Контрольные вопросы к разделу 1
- •Контрольные вопросы к разделу 2
- •Контрольные вопросы к разделу 3
- •Контрольные вопросы к разделу 4
- •Контрольные вопросы к разделу 5
- •Контрольные вопросы к разделу 6
- •Контрольные вопросы к разделу 7
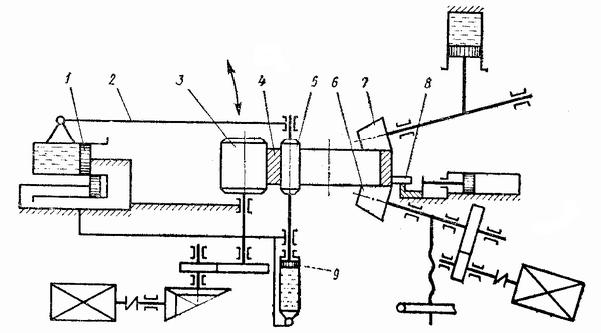
С |
|
|
|
|
|
и |
|
|
|||
Рис. 3.60. Схема кольцераскатной машины для полуоткрытой раскатки типа |
|||||
РАВ: 1 – г дравл ческ й привод нажимного механизма; 2 – накидная опора |
|||||
внутреннего |
валка; |
3 – |
наружный приводной и |
нажимной |
валок; |
4 – раскатываемый полуфа рикат; 5 – внутренний холостой валок; 6 – нижний |
|||||
приводной |
торцовый |
валок; |
7 – верхний нажимной |
торцовый |
валок; |
8 – измерительное и отключающее устройство; 9 – гидропривод осевого |
|||||
перемещения внутреннего валка для загрузки полуфабрикатов |
|
||||
|
3.8. Штамповка на термических прессах |
|
|||
|
бА |
|
|
В технологических процессахДобработки металлов давлением с успехом используются разнообразные физические эффекты. Например, объёмная штамповка крупногабаритныхИотносительно тонких цилиндрических и конических обечаек с внутренним рельефом, фасонных пластин с рёбрами жесткости или узорами и других подобных изделий осуществляется методом теплового прессования на специальных установках – термических прессах (ТП) [15]. На установках можно получать изделия, требующие приложения силы в десятки и сотни тысяч тонн. В настоящее время механических или гидравлических прессов такой мощности нет.
Принцип действия ТП основан на взаимодействии заготовки (заготовок) 2 и инструментов 1 и 3, один из которых расширяется при нагревании (рис. 3.61). Если нагревать инструмент 3 и заготовки 2 (контейнер 1 уже нагрет до температуры штамповки), то они
115
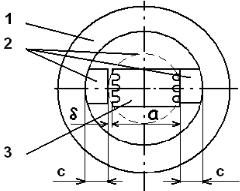
расширяются, а их суммарная длина b = а + 2·c |
изменяется на |
|||||||||
величину |
= α·в·ΔТ, где α – коэффициент линейного |
расширения; |
||||||||
Т |
– превышение |
температуры |
по |
сравнению |
с |
исходной; |
||||
а – исходный размер |
деформирующего инструмента. Когда в > δ |
|||||||||
(технологический зазор), происходит сборка с натягом (затекание |
||||||||||
С |
|
|
|
|
|
|
|
|
||
металла заготовки в полости инструмента 3). |
|
|
|
|
||||||
|
На практике используются ТП двух |
видов: тепловые установки |
||||||||
с |
незав с мым |
нд видуальным |
устройством |
для |
нагрева |
и |
||||
охлажден я деформ рующего инструмента, тепловые установки с |
||||||||||
и |
|
|
|
|
|
|
||||
подводом тепла в печах. |
|
|
|
|
|
|
||||
|
|
|
|
|
Рис. 3.61. Принципиальная схема |
|||||
|
|
|
|
|
теплового пресса: 1 – контейнер; |
|||||
|
|
|
|
|
2 – заготовки; 3 – инструмент |
|
||||
|
Независимая тепловая установка (рис. 3.62, а) состоит из |
|||||||||
массивного контейнера 1 с нагревательным элементом 5, оправки с |
||||||||||
|
|
|
|
Д |
|
|||||
рельефом требуемого профиля 2, устройства 3 |
для подъёма и |
|||||||||
опускания |
бАоправки [15]. В теплоизолированном |
|
контейнере |
|||||||
поддерживается постоянная температура, необходимая для |
||||||||||
деформации заготовки. Исходная заготовка (сплошная или сварная |
||||||||||
из |
листа) |
плотно |
надевается на холодную оправку |
и |
вводится |
в |
нагретый контейнер. После этого включаютсяИнагреватели 4 оправки, последняя увеличивается в размерах и давит на заготовку, зажатую между ней и контейнером.
К моменту выравнивания температур между оправкой и контейнером развивается контактное давление, обеспечивающее заполнение рельефа оправки материалом заготовки. После заполнения рельефа обогрев оправки отключается и начинается ее охлаждение водой через каналы 6. Сначала это обеспечивает уменьшение натяга до нуля, а затем создает некоторый зазор, что позволяет беспрепятственно извлечь из контейнера оправку с отформованным на ней изделием.
116

Упрощенная тепловая установка (рис. 3.62, б) состоит из контейнера кольцевой формы 1 и разборной оправки 2. Отверстия 3 предназначены для охлаждения.
СРис. 3.62. Тепловые установки независимые ( ) и упрощенныеб( ); о ечайка, изготавливаемая на ТПа (в)
Заготовка надеваетсяАна оправку так же, как и у независимой тепловой установки. Контейнер, нагретый в печи до температуры деформации материала о ечайки или несколько выше, надевается на холодную оправку с заготовкой. После некоторой выдержки между контейнером и надетой на оправку заготовкой возникает сцепление, так как из-за подстывания Дконтейнера и прогрева оправки появляются натяг и соответствующее контактное давление. Весь пакет (контейнер, оправка и заготовка) загружается в печь, нагревается и выдерживается в ней при температуре, не превышающей температуру деформации материалаИобечайки. После этого пакет извлекают из печи и подают на охлаждение оправки. Затем разбирают оправку и снимают обечайку. На рис. 3.62, в приведен пример обечайки, штампуемой на ТП.
3.9. Процессы листовой штамповки
Для листовой штамповки в качестве исходной заготовки используется металлический лист, полоса или лента с толщиной не более 10 мм (в редких случаях – до 20 мм). Получаемое изделие – плоское или объемное полое (трансформаторное железо, детали кузовов автомобилей, ложки, вилки, детали самолетов и т.д.). Детали
117
из заготовок толщиной более 20 мм штампуют с нагревом (горячая листовая штамповка). Холодная листовая штамповка получила более широкое применение, чем горячая.
Толщина стенок деталей, получаемых листовой штамповкой, |
|||||||
незначительно отличается от толщины исходной заготовки. При |
|||||||
С |
|
|
|
|
|
||
изготовлении листовой штамповкой пространственных деталей |
|||||||
заготовка обычно испытывает значительные местные пластические |
|||||||
деформац |
|
. Это |
вынуждает |
предъявлять к материалу |
заготовки |
||
достаточно высок |
е требования по пластичности. |
|
|
||||
жесткости |
|
|
|
|
|||
К пре муществам листовой штамповки относятся: возможность |
|||||||
получен я деталей м н мальной массы при заданной их прочности и |
|||||||
|
; |
сравн тельная |
простота |
автоматизации |
процессов |
||
штамповки, обеспеч вающая высокую производительность; хорошая |
|||||||
|
бА |
|
|
||||
приспособляемость к масшта ам производства, при которой |
|||||||
листовая штамповка может ыть экономически целесообразной и в |
|||||||
массовом, |
|
в |
мелкосерийном |
производстве; |
возможность |
||
использован я для деформирования материалов жестких и |
|||||||
эластичных инструментов, жидкости и газов. |
|
|
|||||
Различают разделительные операции, в которых этап |
|||||||
пластического |
деформирования |
обязательно |
завершается |
||||
разрушением заготовки в заданном месте (на заданном контуре), и |
|||||||
формоизменяющие операции |
листовой штамповки, при которых |
||||||
заготовка не должна разрушаться при локальном и общем |
|||||||
растяжении-сжатии. |
|
|
|
|
|||
Основными |
формоизменяющими инструментами |
являются |
|||||
матрицы и |
пуансоны, чаще |
всего жесткие (металлические или |
пластмассовые). |
Изготовление |
И |
||
листовых |
деталей |
может |
||
производиться и с использованиемДтолько одного из инструментов, |
||||
когда деформирование производится жидкостью, газом, воздухом, |
||||
магнитным полем, |
ударной волной |
после детонации взрывчатых |
веществ (бризантных и порохов) и горючих газов.
На рис. 3.63 представлены схемы разделительных операций, с использованием которых [16]:
-отделяют одну часть заготовки от другой по незамкнутому контуру (рис. 3.63, а);
-разделяют полуфабрикат на две детали удалением перемычки
(рис. 3.63, б);
118
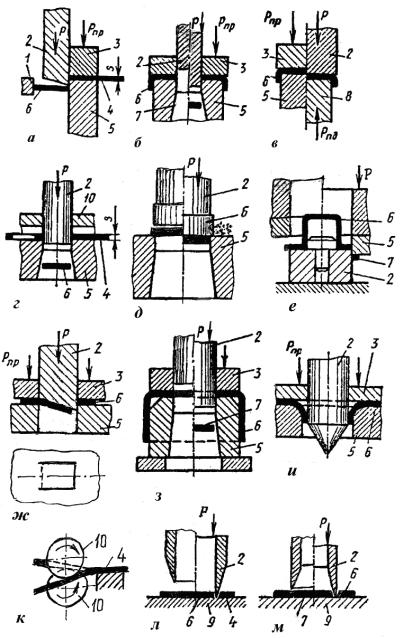
- разделяют штампованную заготовку на две симметричные (или несимметричные) детали (рис. 3.63, в);
Си бА Д
Рис. 3.63. Операции разделительные: а – отрезкаИ; б – разрезка с удалением перемычки; в – разрезка; г – вырубка; д – надрезка; е – отбортовка; ж – пробивка отверстий в деталях; з – зачистка; и – обрезка; к – высечка; л – просечка; 1 – упор; 2 – пуансон (нож); 3 – прижим; 4 – лист; 5 – матрица; 6 – деталь; 7 – отход;
8 – выталкиватель; 9 – плита; 10 – съемник
119
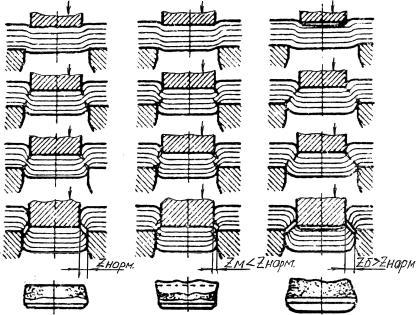
- производят вырубку детали из полосы (рис. 3.63, г), зачистку боковой поверхности, проталкивая вырубленную деталь через матрицу меньших размеров (рис. 3.63, д);
- обрезают деталь по наружному контуру, если на предыдущих переходах получили форму или размеры, не соответствующие
требуемым по чертежу (рис. 3.63, е); |
|
||
- оформляют |
«язычок», |
надрезая отверстие с трех |
сторон |
(рис. 3.63, ж); |
|
|
|
- проб вают отверстия в деталях (рис. 3.63, з); |
|
||
- осуществляют совмещение операции пробивки отверстия |
|||
коническ м пуансоном и отбортовки (рис. 3.63, и). |
|
||
С |
|
|
|
К раздел тельным относятся и такие операции, как разрезание |
|||
матер ала (в том числе непрерывного) на полосы |
|||
многод сковыми |
ножницами |
(рис. 3.63, к), высечка |
деталей |
листового (рис. 3.63, лбА) просечка отверстий (рис. 3.63, м).
Процесс разделения материала на части начинается с его
пластической деформации в зоне разделения, а завершается разрушением от развивающихся от кромок пуансона и матрицы трещин (рис. 3.64). Качество поверхности среза зависит от зазора между инструментами.
Д И
а б в
Рис. 3.64. Схема отделения детали от листового материала при различныхзазорах между матрицей и пуансоном:
а – оптимальных; б – малых; в – больших
120
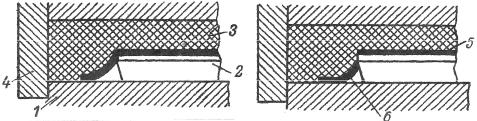
При деформации при нормальном зазоре Zнорм трещины совпадают, что способствует образованию поверхностей разделения
без рванин и заусенцев (рис. 3.64, а). При малом зазоре Zм |
||
скалывающие трещины от пуансона и матрицы идут параллельно на |
||
некотором расстоянии друг от друга. На заключительной стадии |
||
С |
|
|
металл разрывается, что приводит к образованию второго |
||
блестящего пояска и затянутого заусенца (рис. 3.64, б). В случае |
||
больш х зазоров Zб происходит разрыв и втягивание материала в |
||
зазор между нструментами с образованием заусенца. Нижняя |
||
кромка с льно закругляется (рис. 3.64, в). |
||
На практ ке зазор между матрицей и пуансоном (для толщины |
||
матер ала до 12 мм) вы ирается в пределах от 4 до 15% толщины |
||
матер ала. |
бА |
|
|
||
Разделять заготовки толщиной до 1,5 мм на части можно |
||
эластичной средой (резиной, полиуретаном). Механизм разделения |
||
показанВиднона р с. 3.65. , что сначала резина 3, заключенная в |
||
контейнер 4, отг |
ает свисающие края 6 заготовки, а затем отрывает |
|
их от детали 5, |
которая прижата к шаблону 2. Высота шаблона |
|
(пуансона) зависит от толщины материала и составляет от 6 до 12 |
мм. По его контуру оставляют режущий поясок высотой 1,0 – 1,5 мм.
Рис. 3.65. Схема отделения детали от листового материала эластичной средой: 1 – плита; 2 – шаблон (пуансон); 3 – эластичная среда (матрица); 4 – контейнер; 5 – деталь; 6 – отход
На рис. 3.66 представлены схемы формоизменяющих операций,
Д И
сиспользованием которых:
-формируют углы между отдельными частями заготовки при увеличении кривизны пластически деформируемого участка (рис. 3.66, а);
-превращают плоскую заготовку в полое изделие (рис. 3.66, б);
121
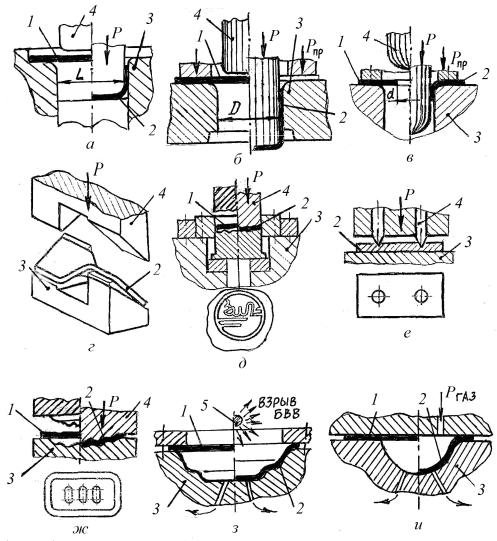
- формируют борта на месте предварительно пробитого отверстия (рис. 3.66, в);
- поворачивают одну часть заготовки относительно другой на заданный угол (например, в штампе, рис. 3.66, г);
- производят оттиск рельефа на одной или двух сторонах Сплоской заготовки (например, чеканка монет, медалей, значков,
рис. 3.66, д); - про зводят накернивание отметок для сверления отверстий
(рис. 3.66, е) вместо разметки штангенциркулем и ручного кернения;
и бА Д И
Рис. 3.66. Операции формоизменяющие: а – гибка П-образная; б – вытяжка-свертка; в – отбортовка с предварительно пробитым
отверстием; г – скручивание; д – чеканка; е – кернение; ж – формовка; з – формовка взрывом; и – формовка газом; 5 – заряд бризантного взрывчатого вещества; стрелками указан отвод воздуха
122
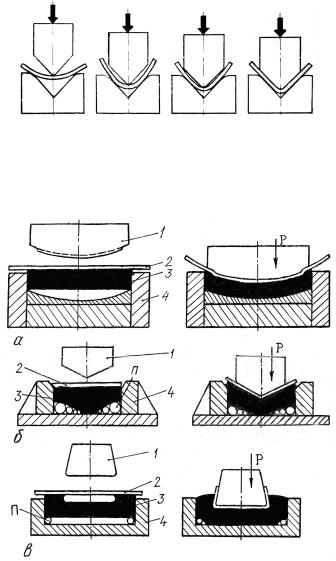
- производят формовку вогнуто-выпуклых изделий жестким инструментом (рис. 3.66, ж), взрывной волной детонации бризантных взрывчатых веществ или газовых смесей (рис. 3.66, з) в
случае изготовления крупногабаритных |
деталей, давлением газов |
|
(рис. 3.66, и) при изготовлении деталей из тонких материалов. |
||
С |
|
|
Картина изменения кривизны деформируемой заготовки в |
||
процессе одноугловой гибки представлена на рис. 3.67. |
||
При мелкосер йном производстве в качестве матрицы |
||
используют эласт чную среду (рис. 3.68). |
|
|
бА |
||
иа |
в |
г |
Р с. 3.67. Последовательность деформирования заготовки при одноугловой гибке
Д И
Рис. 3.68. Схемы использования полиуретановых матриц в гибочных штампах: 1 – пуансон; 2 – заготовка;
3 – резина; 4 – контейнер; П – прокладки
123
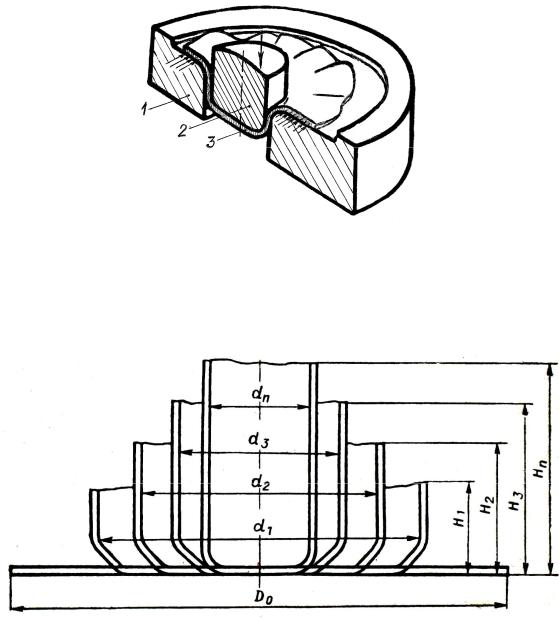
В процессе втягивания заготовки в матрицу под действием пуансона во фланце заготовки возникают радиально-растягивающие и тангенциально-сжимающие напряжения (рис. 3.69) [16]. Последние у наружной кромки достигают максимальной величины и при некоторых отношениях диаметра пуансона (dп) к диаметру заготовки
С(Dо) вызывают образование складок. Поэтому при малых отношениях dп/Dо полое изделие формируют постепенно (за несколько переходов), рис. 3.70 [16].
и
бАРис. 3.69. Схема втягивания материала в матрицу при вытяжке: 1 – матрица; 2 – пуансон; 3 – заготовка;
стрелками показано действие сжимающих напряжений Д И
Рис. 3.70. Схема к расчету количества операций вытяжки стакана из плоской заготовки
124
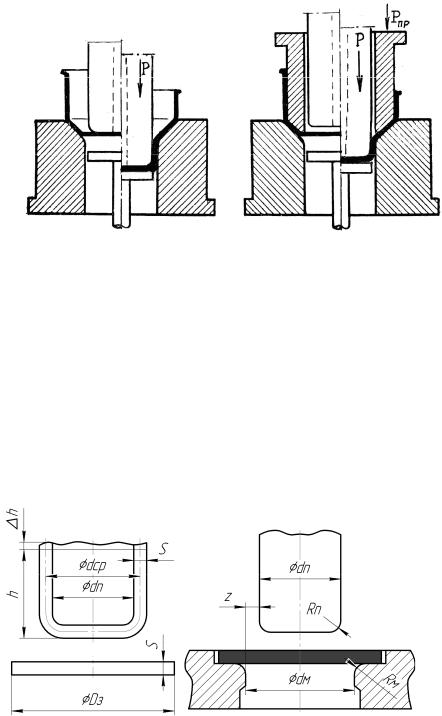
Схемы вторых и последующих переходов показаны на рис. 3.71, а, б. Отношение диаметров пуансонов к диаметрам полуфабрикатов, полученных на предыдущем переходе, должно в этом случае составлять от 0,7 до 0,8.
С |
|
|
и |
|
|
без |
б |
|
а |
|
|
Рис. 3.71. Схемы наладок инструментов для вытяжки деталей на втором |
||
последующ х переходах: а – |
прижима; б – с прижимом |
|
А |
||
Чтобы определить количество переходов штамповки-вытяжки |
||
детали типа «стакан», нео ходимое для получения детали с |
||
заданными соотношениями размеров, нужно рассчитать диаметр |
||
Д |
||
исходной заготовки Dз (рис. 3.72, |
а). Предварительно назначается |
припуск h на высоту детали (в зависимости от отношения h/dср), поскольку после штамповки торец всегда неровный.
|
И |
а |
б |
Рис. 3.72. Схемы: а – |
к определению размеров исходной заготовки |
операции «вытяжка»; б – соотношения размеров инструментов
125
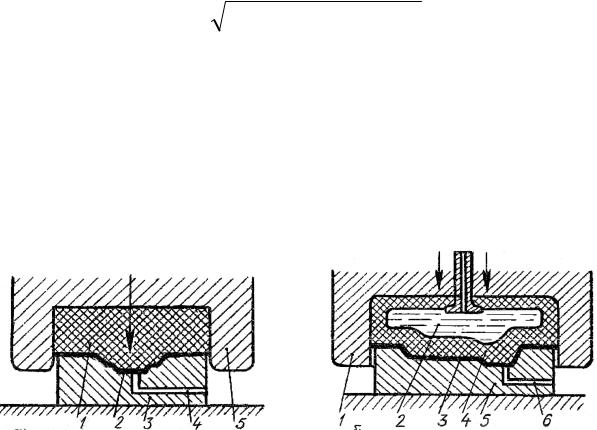
Размер заготовки определяется по методу равенства поверхностей детали и заготовки
Dз = d ср2 4d ср (h h) , |
|
С |
+ S (1 + c); |
где dср – средний диаметр тела детали, мм, dср = dп |
|
с ≈ (0,15 – 0,3)S – коэффициент, учитывающий увеличение толщины |
|
матер ала под действ ем тангенциальных напряжений в той части |
|
эластичным |
|
заготовки, которая ещё не вошла в матрицу. |
|
На р . 3.73 показаны схемы формовки листового материала |
|
пуансоном и эластично-жидкостным |
пуансоном |
(гидроэласт чной средой). |
|
бА |
|
а |
б |
Рис. 3.73. Схемы формовки деталей эластичной (а) и гидроэластичной (б) средой |
|
Для уменьшения поперечных размеров краевой части трубной |
|
|
И |
заготовки в конической или сферической матрице применяется |
|
операция «обжим» (рис. 3.74), аДдля увеличения размеров краевой |
|
части заготовки коническим (сферическим) пуансоном – операция |
|
«раздача» [16]. При выполнении этих |
технологических операций |
возможно появление дефектов (рис. 3.75).
Часто в производстве необходимо произвести правку материала. Плоские листовые заготовки правят осадкой между плоскими плитами (рис. 3.76, а), но если такая правка не удается, то правят осадкой между рифлеными (рис. 3.76, б) или плитами с полостями (рис. 3.76, в). Проволоку или прутки правят протяжкой через ролики (рис. 3.76, г, д) или растяжением.
126
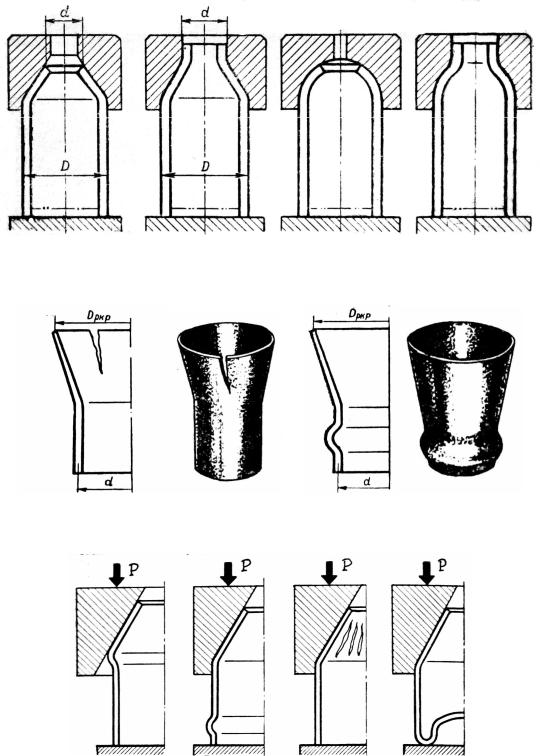
С |
|
|
и |
|
|
Р с. 3.74. Возможные схемы процесса обжима |
||
бА |
б |
|
а |
|
|
|
Д |
|
в |
И |
|
г д е |
Рис. 3.75. Возможные дефекты, образующиеся при раздаче трубных заготовок: а – образование трещин,
б– потеря устойчивости; и при обжиме трубной заготовки в, г, е – потеря устойчивости; д – складкообразование
127
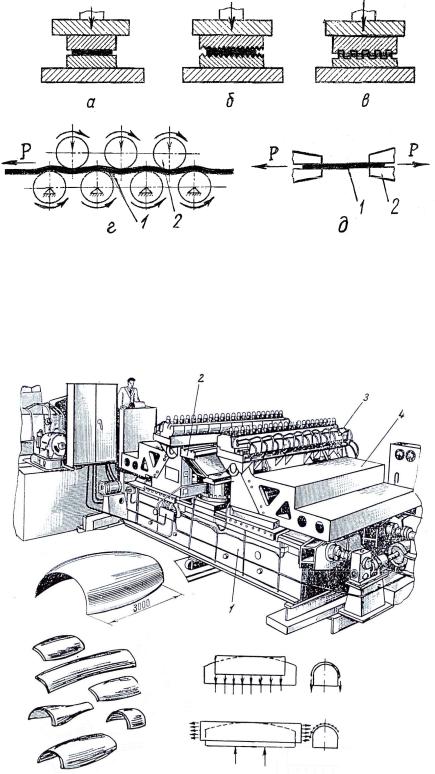
Спосоы. 3.76. правки листового ( – ) и пруткового ( ) материалов
д
–
г
д
а
РисКрупныебдетали с поверхностями двоякой кривизны формуют на спец альных маш нах – о тяжных прессах (рис. 3.77).
А Д И
Рис. 3.77. Обтяжной пресс, схемы нагружения заготовок, образцы изделий
Сложные по форме сечений профили, представленные на рис. 3.78, изготавливаются на многороликовых станах (рис. 3.79).
128
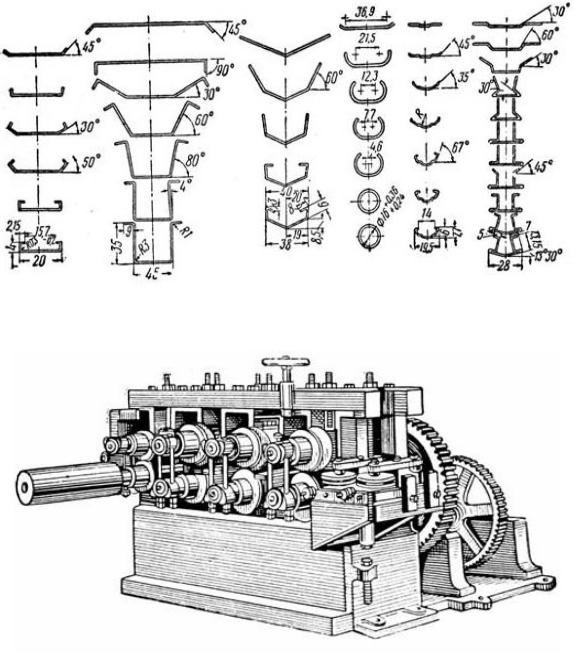
С |
|
ги |
|
бА |
|
Р с. 3.78. Пр меры |
ки профилей на роликовой машине |
|
Д |
|
И |
Рис. 3.79. Профилировочная многороликовая машина |
|
Самыми сложными в |
отладке являются процессы гибки |
«широких» деталей (см. рис. 3.80) или вытяжки панелей двоякой кривизны с выступами или впадинами. При «свободном» деформировании (рис. 3.80, а, б) не удается оформить деталь по пуансону, приходится перетягивать металл через пороги (рис. 3.81) с тем, чтобы вся заготовка подверглась пластической деформации. Поэтому формовку деталей автомобильных кузовов производят на прессах двойного действия в специальных штампах (рис. 3.82).
129
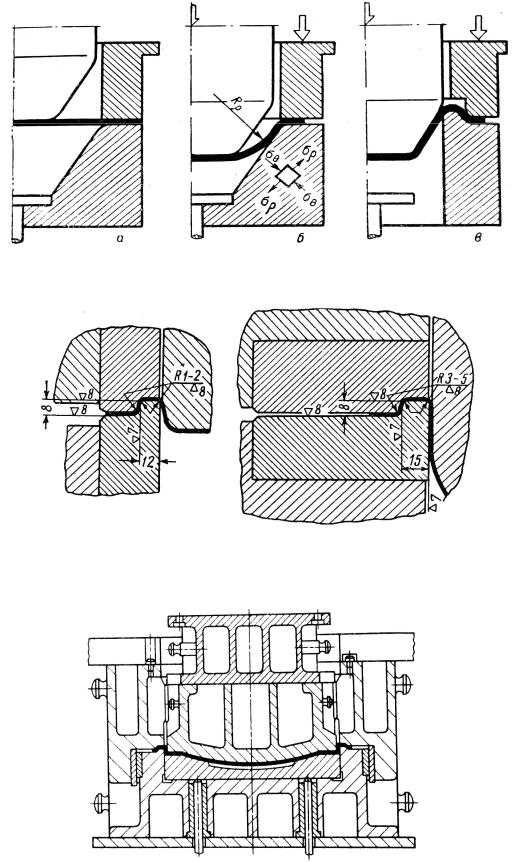
С |
|
и |
|
Р с. 3.80. Разл чные схемы вытяжки конической детали |
|
бА |
|
а |
Д |
б |
|
Рис. 3.81. Конструкции порогов в вытяжных штампах |
|
|
И |
Рис. 3.82. Штамп с перетяжными ребрами
130
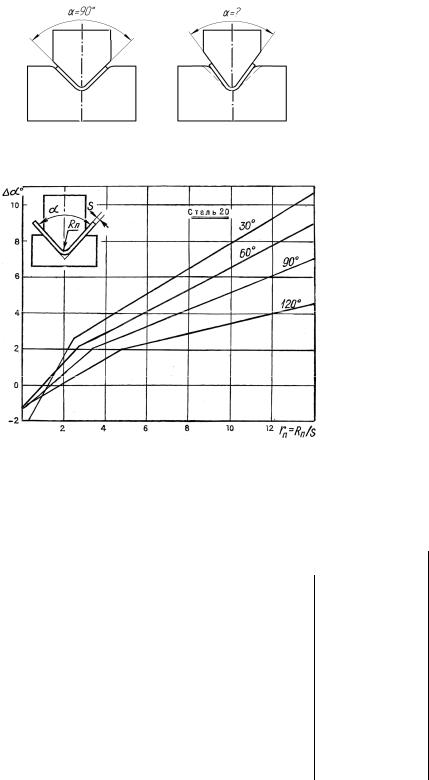
|
При этом |
приходится еще |
учитывать пружинение металла |
||||||
(рис. 3.83). Для большинства конструкционных материалов |
|||||||||
пружинение можно определить по экспериментальным графикам |
|||||||||
(рис. 3.84) или табличным значениям (табл. 3.9), которые приводятся |
|||||||||
в специальной литературе. |
|
|
|
|
|
||||
С |
|
|
|
|
|
|
|
||
и |
|
б |
|
|
|||||
|
|
|
а |
|
|
|
|||
|
Р с. 3.83. Сечен я штампов для оценки углов пружинения |
||||||||
|
бА |
|
|
||||||
|
Рис. 3.84. Графики изменения углов пружинения |
||||||||
|
в зависимости от относительного радиуса изгиба Rп |
||||||||
|
|
|
|
|
|
|
|
Таблица 3.9 |
|
|
|
Величины угловДпружинения ∆α, град |
|||||||
|
Металл |
|
Толщина |
|
Относительный радиус изгиба Rп |
|
|||
|
|
материала S |
|
|
|
|
|
|
|
|
|
|
менее 1 |
|
от 1 до 5 |
более 5 |
|
||
|
|
|
|
|
|
||||
|
Сталь мягкая, |
|
До 0,8 |
|
4 |
|
5 |
6 |
|
|
латунь, |
|
От 0,8 до 2,0 |
|
2 |
|
3 |
4 |
|
|
алюминий |
|
Свыше 2,0 |
|
0 |
|
И1 2 |
||
|
Сталь средней |
|
До 0,8 |
|
5 |
|
6 |
8 |
|
|
твердости, |
|
От 0,8 до 2,0 |
|
2 |
|
3 |
5 |
|
|
латунь |
|
Свыше 2,0 |
|
0 |
|
1 |
3 |
|
|
|
|
До 0,8 |
|
7 |
|
9 |
12 |
|
|
Сталь твердая |
|
От 0,8 до 2,0 |
|
4 |
|
5 |
7 |
|
|
|
|
Свыше 2,0 |
|
2 |
|
3 |
5 |
|
131