
- •ВВЕДЕНИЕ
- •2. ОСНОВЫ ЛИТЕЙНОГО ПРОИЗВОДСТВА
- •2.1. Теоретические основы производства отливок
- •2.2. Формовочные материалы
- •2.3. Литье в разовые песчано-глинистые формы
- •2.4. Разработка чертежей отливок
- •2.5. Определение размеров припусков на механическую обработку
- •2.6. Расчет литниковой системы
- •2.7. Литье под давлением
- •2.8. Кокильное литье
- •2.9. Центробежное литье
- •2.12. Литье по газифицируемым моделям
- •2.13. Литье по ледяным моделям
- •2.14. Особенности изготовления отливок из различных сплавов
- •3. ОСНОВЫ ОБРАБОТКИ МАТЕРИАЛОВ ДАВЛЕНИЕМ
- •3.1. Сущность процессов обработки материалов давлением
- •3.2. Процессы прокатки
- •3.3. Прессование металлов
- •3.4. Волочение
- •3.5. Процессы свободной ковки
- •3.6. Процессы точной объемной штамповки
- •3.6.1. Выбор методов и способов производства заготовок объемной штамповкой
- •3.6.2. Разработка технологии открытой объемной штамповки
- •3.6.3. Определение класса точности поковки
- •3.6.4. Определение группы стали
- •3.6.6. Определение исходного индекса
- •3.6.8. Определение допусков на размеры поковки
- •3.6.9. Разработка чертежа холодной поковки
- •3.6.10. Назначение напусков
- •3.6.11. Разработка чертежа горячей поковки
- •3.6.12. Определение размеров исходной заготовки
- •3.7. Горячая раскатка кольцевых заготовок
- •3.8. Штамповка на термических прессах
- •3.9. Процессы листовой штамповки
- •3.10. Штамповка бризантными взрывчатыми веществами
- •3.11. Штамповка горючими газовыми смесями
- •3.12. Магнитно-импульсная обработка металлов
- •3.13. Электрогидроимпульсная штамповка
- •4.1. Классификация металлорежущих станков
- •4.2. Особенности технологии резания материалов
- •4.4. Способы и инструмент обработки отверстий
- •4.5. Способы и инструмент обработки фрезерованием
- •4.6. Способы и инструмент для строгания поверхностей
- •4.7. Способы и инструмент обработки шлифованием
- •4.8. Отделочные методы обработки поверхностей
- •5.1. Сущность процессов сварки
- •5.2. Ручная дуговая сварка стали
- •5.3. Дуговая сварка под флюсом
- •5.4. Дуговая сварка в среде защитных газов
- •5.5. Газовая сварка
- •5.6. Контактная электрическая сварка
- •5.7. Свариваемость сталей
- •5.8. Специальные термические процессы при сварке
- •5.9. Пайка металлов
- •6.1. Общая характеристика неметаллических материалов
- •6.2. Основы технологии производства изделий из пластмасс
- •6.3. Основы технологии производства изделий из резины
- •6.4. Характеристика композиционных материалов
- •6.5. Механизмы упрочнения композиционных материалов
- •6.6. Назначение и характеристика порошковых, дисперсно-упрочненных композиционных материалов
- •6.7. Волокнистые композиционные материалы
- •7. ТЕХНОЛОГИИ И ОСНАСТКА ХОЛОДНОЙ ОБЪЕМНОЙ ШТАМПОВКИ
- •7.1. Особенности холодной объемной штамповки
- •7.3. Способы формообразования, особенности технологии получения изделий стержневого типа, схемы инструмента
- •7.4. Штамповая оснастка для процессов выдавливания
- •7.5. Материалы инструмента для холодного деформирования
- •КОНТРОЛЬНЫЕ ВОПРОСЫ
- •Контрольные вопросы к разделу 1
- •Контрольные вопросы к разделу 2
- •Контрольные вопросы к разделу 3
- •Контрольные вопросы к разделу 4
- •Контрольные вопросы к разделу 5
- •Контрольные вопросы к разделу 6
- •Контрольные вопросы к разделу 7
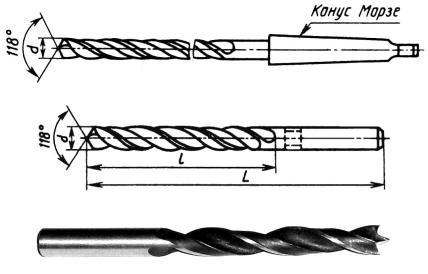
4.4. Способы и инструмент обработки отверстий
Отверстия с различной формой боковой поверхности обрабатывают сверлами, зенкерами, развертками и метчиками.
1. верла по конструкции и назначению подразделяют на |
|||||
С |
|
центровочные |
(рис. 4.31) |
и |
|
спиральные |
(рис. 4.30), |
||||
специальные |
|
|
|
|
|
(рис. 4.32). На более распространенный для сверления и |
|||||
рассверл ван я |
|
нструмент – |
спиральное сверло, состоящее |
из |
|
различают |
|
|
|
||
рабочей части, шейки (с проточкой или без проточки), хвостовика и |
|||||
лапки (оформленной в виде лыски). На рабочей части сверла |
|||||
режущую коническую (с определенным углом заточки) |
|||||
или режущую фасонную часть (исключающую вырыв материала и |
обработке специальных конструкцийА(рис. 4.32), исключающие скол кромок
деформац ю заготовки) и направляющую часть с винтовыми канавками. Сверло сп ральное служит для сверления отверстий в сплошном матер але рассверливания уже имеющихся отверстий.
При некоторых материалов применяются сверла
отверстий.
Центровочные сверла предназначены для обработки центровых отверстий с предохранительной фаской (рис. 4.31, в) и без фаски
(рис. 4.31, а, б, г). |
|
Д |
|
а |
И |
|
б
в
Рис. 4.30. Конструкции сверл: а – спиральное с коническим хвостовиком (для металла); б – спиральное с цилиндрическим хвостовиком (для металла); в – спиральное с цилиндрическим хвостовиком для сверления дерева
189
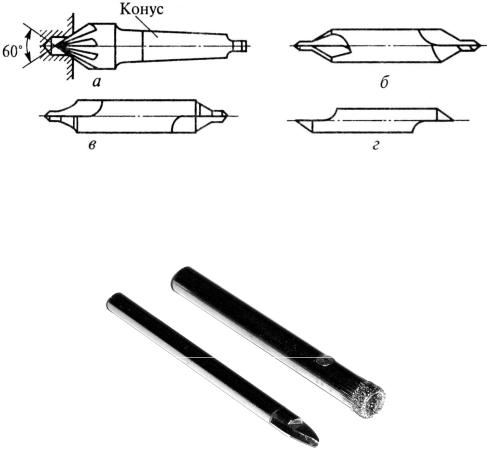
СР с. 4.31. Центровочные сверла: а – многозубая зенковка; иб – комб н рованное сверло; в – комбинированное сверло
с предохран тельной фаской; г – однозубая зенковка
бАРис. 4.32. Конструкции сверл: клинообразное и трубчатое (с напыленнойДалмазной крошкой)
для сверления керамики и стекла И
Рис. 4.33. Зенкер: а – элементы: l – рабочая часть; l1 – режущая часть; l2 – калибрующая часть;
l3 – шейка; l4 – хвостовик; e – лапка
190
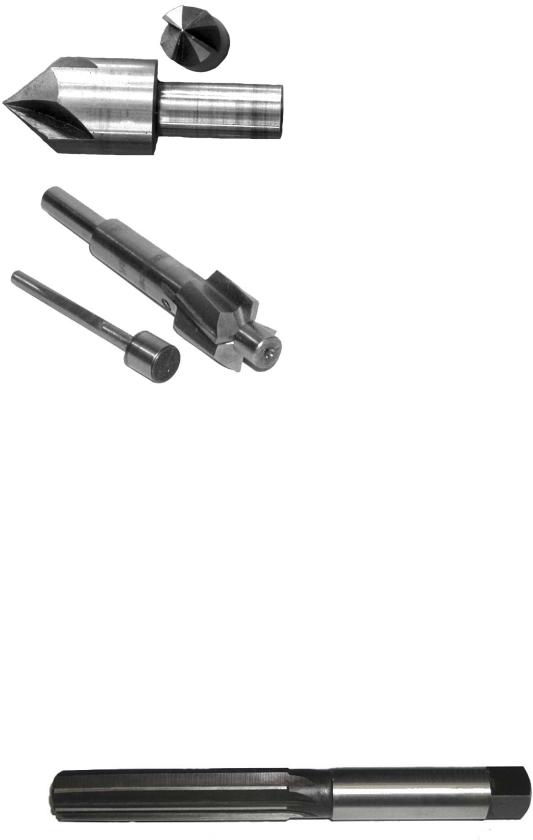
|
|
|
2. |
Зенкерами |
и |
|||
|
|
|
зенковками |
обрабатывают |
||||
С |
|
|
отверстия |
в |
литых |
или |
||
|
|
штампованных |
заготовках, |
|||||
|
|
предварительно просверленные |
||||||
|
|
|
||||||
|
|
|
отверстия. |
Отличие |
зенкера |
|||
и |
|
(рис. 4.33) от сверла состоит в |
||||||
|
том, |
что у него отсутствует |
||||||
|
поперечная режу-щая кромка и |
|||||||
|
а |
|
||||||
|
|
|
он имеет не две, а три или |
|||||
|
|
|
четыре режущие кромки (зуба). |
|||||
|
|
|
Это обеспе-чивает получение |
|||||
бА |
|
высо-кой |
||||||
|
|
|
более |
|
|
|
||
|
|
|
производительности и чистоты |
|||||
|
|
|
по |
|
сравнению |
|
с |
|
|
|
|
рассверливанием. |
Режущие |
||||
|
|
|
кроки |
выполняют |
основную |
|||
|
|
|
работу резания. |
|
|
|||
|
|
|
Зенковки |
(рис. |
4.34) |
|||
Рис. 4.34. Зенковки: а – конические; |
предназначены |
для обработки |
||||||
б – торцовые |
|
конических и цилиндрических |
||||||
|
|
Д |
|
|||||
|
|
|
отверстий |
|
под |
головки |
стержневых деталей.
3. Развертками (рис. 4.35, 4.36) окончательно обрабатывают отверстия после сверления или зенкерования. По форме обрабатываемого отверстия различают сплошные цилиндрические и конические развертки, а также развертки со вставными режущими пластинами. Развертки имеют до 12 режущих кромок, расположенных на режущей части с направляющим конусом (рис.
4.35). Калибрующая часть |
направляет развертку в отверстии и |
обеспечивает высокую точность размера и малую шероховатость |
|
поверхности. |
И |
Рис. 4.35. Развертка цилиндрическая
191

4. Метчики применяют для нарезания внутренних резьб. Метчик (рис. 4.37) представляет из себя винт с заходным конусом (с углом при вершине 2 ) и прорезанными прямыми или винтовыми канавками, образующими режущие кромки. Рабочая часть метчика l
имеет режущую l1 и калибрующую l2 |
части. Профиль резьбы |
|
С |
|
|
метчика должен соответствовать профилю нарезаемой резьбы. |
||
и |
|
|
бА |
||
|
а |
|
б |
Д |
|
|
в |
|
Рис. 4.36. Развертки: а – ручная разжимная; б – коническая; в – машинная |
||
|
|
И |
насадная со вставными ножами из быстрорежущей стали
Рис. 4.37. Метчик для нарезания внутренней резьбы: 1 – центровое отверстие; 2 – канавки; 3 – сердцевина; 4 – зуб
192
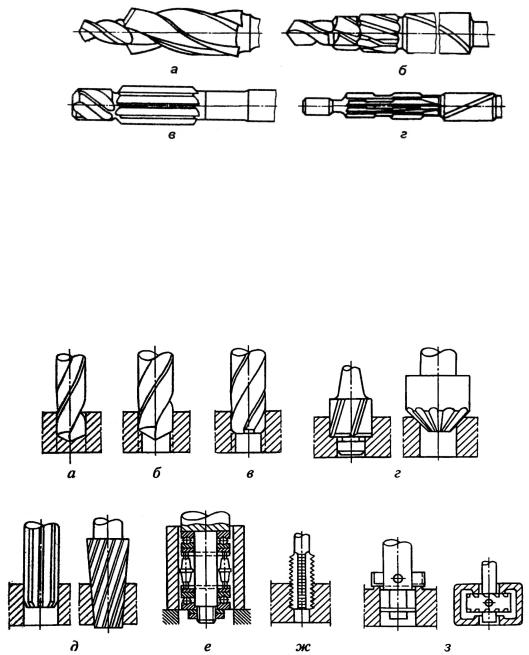
5. Цековками обрабатывают торцовые поверхности отверстия для достижения перпендикулярности к оси отверстия.
6. Комбинированным инструментом (рис. 4.38) за один проход сверлят, рассверливают, зенкеруют, развертывают отверстия (в различной последовательности) [26].
СиР с. 4.38. Ком инированные инструменты: абА– сверло – зенкер; – сверло–зенкер – развертка; в – зенкер – развертка; г – развертка – развертка
Сверлен е, рассверливание, зенкерование, развертывание, цекован е, зенкован е, нарезание резьбы (рис. 4.39) выполняют на сверлильных (рис. 4.40, а, , 4.41), расточных (рис. 4.40, в, г), агрегатных (рис. 4.42), фрезерных, токарных и др. станках.
Д И
Рис. 4.39. Виды обработки отверстий в заготовках: а – сверление;
б– рассверливание; в – зенкерование; г – зенкование;
д– развертывание; е – раскатывание; ж – нарезание резьбы;
з– подрезание (цекование) торцов
193
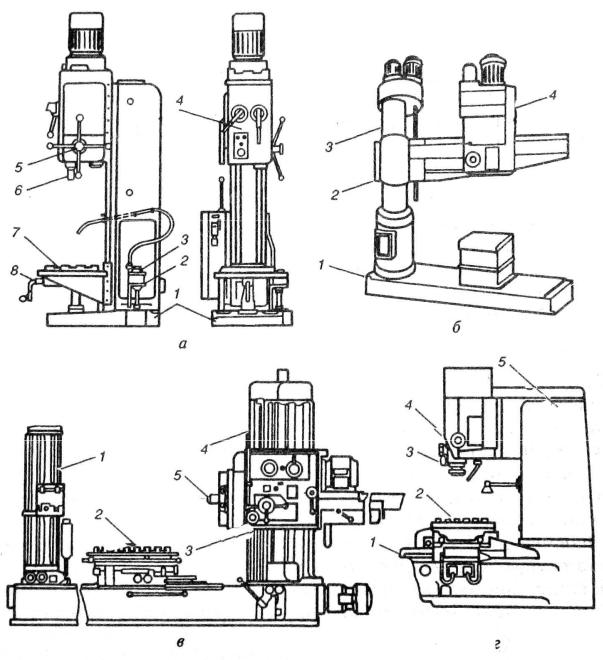
Приспособления для закрепления инструментов на сверлильных станках показаны на рис. 4.43.
Си бА Д
Рис. 4.40. Станки сверлильно-расточной группы: аИ– вертикально-сверлильный (1 – станина; 2 – насос; 3 – фильтр; 4 – головка сверлильная; 5 – рукоятка; 6 – шпиндель; 7 – стол; 8 – привод подъема стола); б – радиально-сверлильный (1 – станина; 2 – траверса поворотная; 3 – колонна; 4 – головка сверлильная); в – горизонтально-расточной (2 – суппорт с поворотным столом; 3 – бабка шпиндельная; 4 – стойка; 5 – шпиндель расточной); г – координатно-расточной (1 – крестовый стол; 2 – стол; 3 – контрольное устройство; 4 – головка шпиндельная; 5 – станина)
194
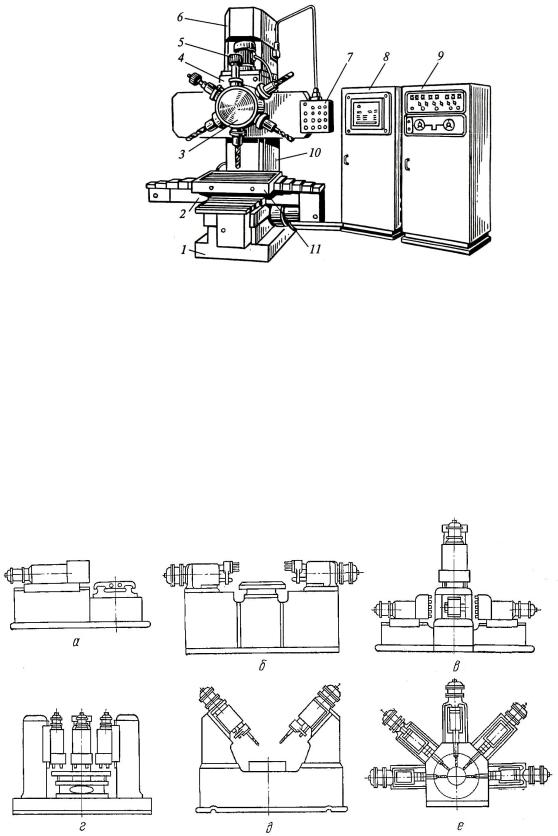
С |
|
|
|
|
||
орудования |
|
|
|
|||
Р с. 4.41. Станок вертикально-сверлильный с ЧПУ: 1 – основание; |
||||||
|
б |
|
||||
2 – стол крестовый; 3 |
– головка револьверная; 4 – суппорт; 5 – инструмент; |
|||||
6 – электродв |
гатель поворота револьверной головки; 7 – пульт управления; |
|||||
8 – шкаф электроо |
|
; 9 – шкаф с ЧПУ; 10 – стойка; 11– стол |
||||
Для |
|
одновременного |
|
(параллельного) |
выполнения |
|
|
|
А |
|
|||
многошпиндельной и многосторонней обработки с несколькими |
||||||
технологическими переходами |
предназначены агрегатные станки, |
создаваемые на азе стандартных узлов: станин, стоек, кронштейнов, делительных столов, коро ок скоростей, силовых головок и других элементов станков различных типовД.
И
Рис. 4.42. Схемы компоновки агрегатных станков
195
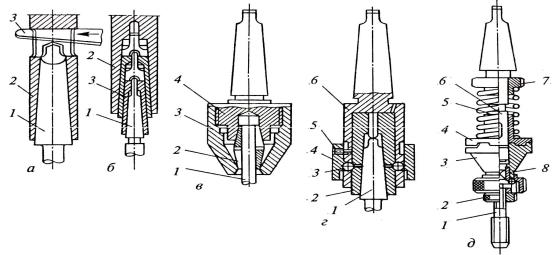
Возможности |
агрегатных |
станков |
обусловлены |
их |
компоновкой, предусматривающей размещение силовых головок с |
||||
индивидуальными |
приводами |
вокруг |
стационарных |
или |
вращающихся столов. Силовые головки могут быть одноили |
||||
многошпиндельными, т.е. производить одновременно несколько |
||||
С |
|
|
|
|
операций; наличие поворотных столов с позициями загрузки позволяет совмещать вспомогательное время на снятие и установку заготовок с маш нным временем.
На агрегатных станках производятся операции сверления, зенкерован я, развертывания, растачивания отверстий, точения
гладких |
ступенчатых |
поверхностей, |
нарезания наружных и |
|
внутренн |
х резьб, фрезерования лысок, пазов и т.д. |
|||
Компоновка агрегатных станков зависит от габаритов |
||||
обрабатываемой детали, |
|
выполняемых |
операций, требуемой |
|
|
тельности технико-экономических показателей. |
|||
производ |
|
|
||
|
бА |
|||
|
|
|
Д |
|
Рис. 4.43. Приспособления для закрепления на сверлильных станках: |
||||
а, б – инструментов с коническим хвостовиком (1 – инструмент; 2 – шпиндель; |
3 – клин); в – инструментов с цилиндрическим хвостовикомИ(1 – инструмент; 2 – цанга; 3 – гайка; 4 – корпус); г – быстросменный патрон (1 – инструмент; 2 – втулка; 3 – шарики; 4 – кольцо; 5 – винт стопорный; 6 – корпус);
д – реверсивный патрон (1 – инструмент; 2 – гайка; 3, 4 – полумуфты; 5 – пружина; 6 – оправка; 7 – гайка); 8 – шпонка
При назначении режима сверления отверстий в сплошном материале за глубину резания t (мм) принимают половину диаметра сверла:
T = D/2,
196
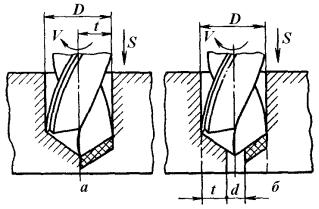
а при рассверливании
t = (D – d)/2,
где d – диаметр обрабатываемого отверстия, мм (рис. 4.44).
За скорость резания при сверлении принимают окружную
С |
|
|
|
|
|
|
скорость точки режущей кромки, наиболее удаленной от оси сверла. |
||||||
корость резания связана с диаметром сверла и частотой его |
||||||
вращен я зав с мостью |
V= D n / 1000, |
|
|
|||
при |
|
V C |
S y Tm |
K , |
||
где D – наружный д аметр сверла, мм; n |
– частота вращения сверла, |
|||||
об/мин. |
|
|
|
|
|
|
корость резан я |
сверлении назначается по эмпирической |
|||||
|
|
зависимости |
|
|
||
бА |
Dq |
|
||||
|
|
|
|
|
||
|
|
где С – коэффициент, |
||||
|
|
учитывающий |
условия |
|||
|
|
обработки |
(обрабатываемый |
|||
|
|
материал, вид обработки и т. |
||||
|
|
д.); T – стойкость сверла, мин; |
||||
Рис. 4.44. Схемы сверления (а) |
коэффициент |
К определяется |
||||
по формуле К= К1 К2 К3, где |
||||||
и рассверливания (б) |
||||||
К1 |
учитывает |
качество |
||||
|
|
|||||
обрабатываемого материала; К2 учитывает вид инструментального |
материала; |
К3 учитывает |
глубину |
сверления. |
Значения |
коэффициентов K, C, и показателей степени q, y, m приводятся в |
||||
справочниках. |
|
Д |
||
При рассверливании, а также зенкеровании и развертывании |
||||
скорость резания назначается по формуле, |
в которой учитывается |
глубина резания:
V C |
Dq |
K . |
|
tx S y Tm |
|||
|
И |
При сверлении подачу на оборот назначают в зависимости от диаметра сверла и диаметра обрабатываемого отверстия D:
S=0,02 D.
197
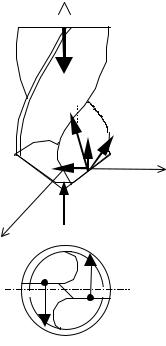
Подача на зуб определяется по формуле
Sz= S / z,
где z – число зубьев сверла.
Проверка элементов режима резания по мощности электродвигателя станка производится следующим образом. Равнодействующую силы резания, действующую на каждое режущее лезвие сверла, можно разложить на три составляющие (рис. 4.45).
умма указанных сил, действующих вдоль оси сверла,
называется осевой с лой Pо. Радиальные силы Py, действующие на |
|||||||||||||||
силы |
|
|
|
|
|
|
|
|
|
|
|
||||
два лезв я сверла, вза мно уравновешивают друг друга, поскольку |
|||||||||||||||
Сони равны по вел чине и противоположны по направлению. |
|||||||||||||||
Крутящ й момент Мк, |
преодолеваемый шпинделем станка, |
создается |
|||||||||||||
тангенц альной с лой Pz, |
а вернее, парой сил, |
действующих на две |
|||||||||||||
|
бА |
|
|
|
|
|
|
|
|
||||||
режущ е кромки сверла. |
Pо (Н) и крутящего |
|
|
|
|
|
x |
|
|
|
|||||
Значен е осевой |
|
|
|
|
|
|
|
|
|
|
|||||
момента Мк (Нм) определяют по эмпирическим |
|
|
|
|
|
Pо |
|||||||||
формулам: |
|
|
|
|
|
|
|
|
|
|
|
|
|
|
|
|
|
Po Cp Dx S y Kp ; |
|
|
|
|
|
|
P |
Px Pz |
|||||
|
|
MK Cм Dx S y Kм , |
|
|
|
|
Py |
|
|||||||
|
|
|
|
|
|
|
|
|
|
|
|
|
y |
||
|
|
|
|
|
Д |
||||||||||
где Сp, См – постоянные коэффициенты, |
|
|
|
|
|
|
|
|
|
||||||
характеризующие обрабатываемый материал и |
|
|
|
|
|
Pп |
|||||||||
условия |
|
резания; |
x, |
y – показатели |
z |
|
|
|
|
|
|
|
|
||
степеней; |
|
|
|
|
|
|
|
|
|
|
|
|
Pz |
||
Кp, Км – |
|
поправочные |
коэффициенты |
на |
|
|
|
|
|
|
|
|
|
||
|
|
|
|
|
|
|
|
|
|
|
|
||||
|
|
|
|
|
|
И |
|||||||||
измененные |
условия |
резания |
(отличные |
от |
|
|
|
|
|
|
|
|
|
||
Pz |
|
|
|
||||||||||||
табличных). Все показатели и коэффициенты |
|
|
|
||||||||||||
|
|
|
|
|
|
|
|
|
|||||||
определяются из справочников. |
|
|
|
Рис. 4.45. Силы, |
|||||||||||
Крутящий момент, кроме того, позволяет |
|
|
|
|
действующие |
||||||||||
определить |
эффективную |
мощность, |
|
|
|
|
на сверло |
затрачиваемую на резание при сверлении
Ne= Мк n / (60 . 103).
Нормирование сверлильной операции производится аналогично токарной операции и по тем же формулам.
198