
Pivovarennaya_inzheneria_ / Глава 7
.pdf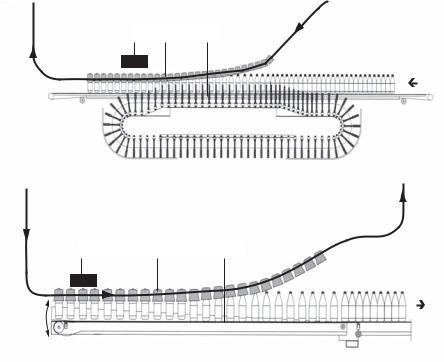
УПАКОВЫВАНИЕ ПИВА И ГАЗИРОВАННЫХ НАПИТКОВ |
827 |
|
|
|
|
а)
1 2 3
б)
4 |
52 |
65 |
Рис. 7.119. Система транспортирования бутылок в машине Spiragrip:
а — загрузка бутылок в машину; б — выгрузка бутылок из машины: 1 — устройство для блокировки бутылок; 2 — устройство несущее; 3 — конвейер загрузочный; 4 — устройство для разблокировки бутылок; 5 — конвейер разгрузочный
7.4.5.2.2. Ополаскивающая машина Spirasept
Новые ПЭТ-бутылки, как и стеклянные, перед наполнением продуктом необходимо подвергнуть ополаскиванию для удаления механических частиц и вредных для пива микроорганизмов. Ополаскивание ПЭТ-бутылок может быть осуществлено в оборудовании двух типов:
•в универсальных машинах роторного типа (см. раздел 7.3.5.4.2.2), предназначенных как для стеклянных, так и для ПЭТ-бутылок;
•в специализированных машинах Spirasept со спиралеобразной траекторией перемещения бутылок в процессе обработки (рис. 7.120).
Конструктивно машины Spirasept фирмы Krones устроены аналогично вышеописанной машине Spiragrip. Отличие машин Spirasept заключается в том, что они имеют меньше стадий обработки бутылок. Бутылки в них обрабатываются только дезинфицирующим раствором и стерильной водой методом погружения и шприцевания.
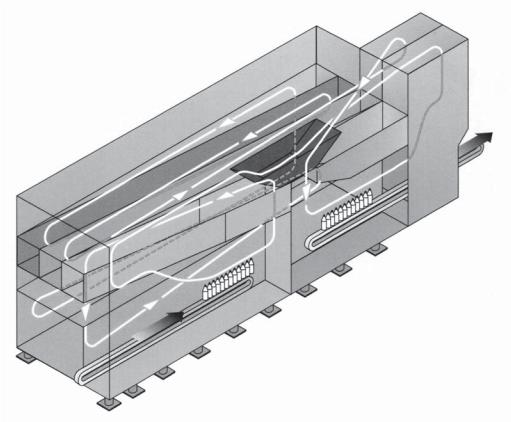
828 |
ПИВОВАРЕННАЯ ИНЖЕНЕРИЯ |
|
|
Рис. 7.120. Принципиальное устройство ополаскивающей машины Spirasept
7.4.5.3. Фасование пива в полимерные бутылки
Для наполнения пивом ПЭТ-бутылок в принципе пригодны все существующие системы. При этом первостепенное значение имеют точность объема и минимизация контакта продукта с кислородом воздуха.
Для фасования в ПЭТ-бутылки в типовых фасовочной и укупорочной машинах требуется лишь небольшая дооснастка.
Для наполнения ПЭТ прекрасно зарекомендовали себя фасовочная система Mecafill VKP-PET с системой вакуумной поддержки (см. раздел 7.3.8), а также система фасования по объему Volumetic VO-DM-L-PET с длинной наполнительной трубкой. Принципиальное устройство этой системы показано на рис. 7.121. Особенно предпочтительны эти системы при фасовании чувствительных к кислороду напитков.
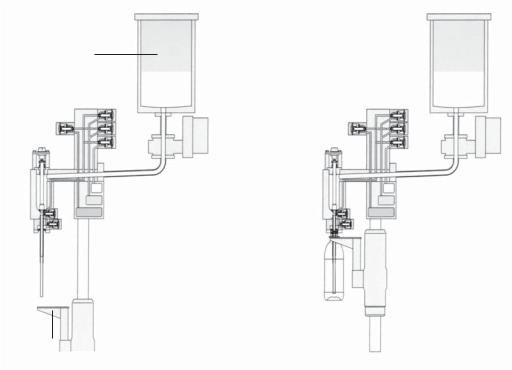
|
УПАКОВЫВАНИЕ ПИВА И ГАЗИРОВАННЫХ НАПИТКОВ |
829 |
|
|
|
|
|
|
а) |
б) |
|
8
7 |
|
|
|
|
|
|
1 |
|
|
1 |
|
4 |
2 |
|
4 |
2 |
|
|
3 |
|
|
3 |
|
|
|
11 |
|
|
|
|
|
|
|
|
|
|
|
12 |
|
|
|
|
|
|
|
|
|
5 |
|
13 |
|
|
5 |
|
|
|
|||
6 |
9 |
|
6 |
10
Рис. 7.121. Принципиальное устройство системы фасования по объему Volumetic VO-DM-L-PET фирмы Krones:
а — исходное положение; б — фаза наполнения: 1 и 2 — газовые клапаны; 3 — разгрузочный клапан; 4 — клапан создания предварительного давления; 5 и 6 — управляющий клапан;
7 — одноступенчатый управляющий пневмоцилиндр; 8 — кольцевой продуктовый канал; 9 — индуктивный расходомер; 10 — подъемный пневматический столик; 11 — канал разгрузочный; 12 — канал соединительный кольцевому продуктовому каналу; 13 — канал чистого СО2
7.4.5.4. Укупоривание полимерных бутылок
Для укупоривания полимерных бутылок с пивом применяют различные виды пробок: кронен-пробки; резьбовые колпачки из пластмассы или алюминия и металлические колпачки с кольцом для открывания.
Стадии укупоривания ПЭТ-бутылок резьбовыми колпачками и кронен-пробками показаны на рис. 7.122.
Действие патронов для резьбовых колпачков основано на принципе накручивания, а патронов для кронен-пробок — на принципе обжима. Для укупоривания ПЭТ-бутылок металлическими пробками с открывающим кольцом используют те же укупорочные патроны, которые применяют для кронен-пробок.
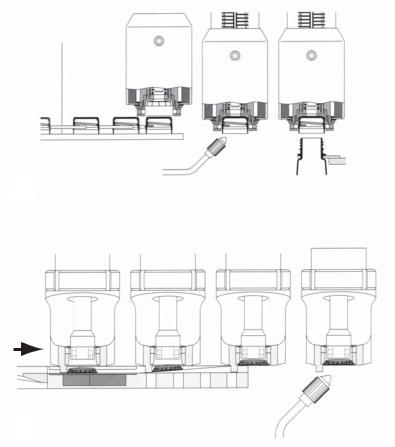
830 |
ПИВОВАРЕННАЯ ИНЖЕНЕРИЯ |
|
|
а)
1
б)
2
Рис. 7.122. Укупоривание ПЭТ-бутылок:
а— резьбовыми колпачками; б — кронен-пробками
7.4.5.5.Пневматические конвейеры
Обычные пластинчатые конвейеры не пригодны для транспортирования очень легких пустых пластиковых бутылок, поскольку из-за своей малой массы они крайне неустойчивы на конвейере в процессе движения.
Всвязи с этим возникла необходимость создания принципиально новых транспортирующих систем — пневматических конвейеров, принципиальное устройство которых показано на рис. 7.123.
Впневматическом конвейере лишь кольцо горлышка бутылки контактирует с направляющими скольжения, и благодаря воздушным потокам, подаваемым под кольцо с разных сторон, легкие пустые бутылки в буквальном смысле слова плывут на воздушной подушке. Так бутылки перемещают от выдувной машины к ополаскивателю и фасовочной машине. При этом на поверхности бутылки не остается никаких повреждений, царапин и пр.,
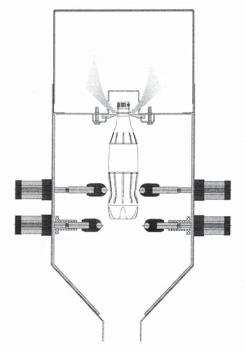
УПАКОВЫВАНИЕ ПИВА И ГАЗИРОВАННЫХ НАПИТКОВ |
831 |
|
|
|
|
Рис. 7.123. Принципиальное устройство пневматического конвейера
поскольку с направляющими транспортирующей системы соприкасается только кольцо горлышка бутылки. Кроме того, при таком способе транспортирования снижается до минимума трение и износ, а также обеспечиваются гигиенические условия.
7.4.5.6. Блок выдувной машины и фасовочно-укупорочного агрегата
Прогрессивным техническим решением при организации поточных линий упаковывания напитков в ПЭТ-бутылки является образование блока выдувной машины и фасовочноукупорочного агрегата. В этом случае существенно сокращается путь от операции выдува ПЭТ-бутылок до операции фасования и отпадает необходимость в пневматическом конвейере и ополаскивающей машине, требуется меньшая производственная площадь. Но поскольку бутылки из выдувной машины поступают не остывшими и, следовательно, еще весьма пластичными, то для незамедлительного наполнения их напитком они не пригодны — донышки могут деформироваться под гидродинамическим напором струи наполнительного устройства.
Поэтому на участке между выдувной машиной и фасовочно-укупорочным агрегатом размещают устройство (см. рис. 7.115, б) для охлаждения донышек бутылок водой. Через это устройство проходит относительно короткий конвейер, на горизонтальной цепи которого с одинаковым интервалом размещены механические захваты, фиксирующие ПЭТ-бутылки под упорное кольцо на горлышке и перемещающие их в рабочем положении (т. е. горлышком вверх).
832 |
ПИВОВАРЕННАЯ ИНЖЕНЕРИЯ |
|
|
Охлаждающее устройство и фасовочно-укупорочный агрегат, как правило, отделяют от пространства цеха прозрачными панелями, создавая тем самым более благоприятные санитарно-гигиенические условия для фасования напитков.
7.4.5.7. Специальные концепции фасования напитков
Фасование пива, газированных прохладительных напитков, вин, шампанского требует соблюдения определенных санитарно-гигиенических условий, обеспечивающих сокращение возможностей контакта продукта с посторонней микрофлорой. Основные требования к таким условиям были упомянуты выше в соответствующих разделах.
Но в последние годы многократно вырос масштаб фасования и существенно расширился ассортимент напитков, обладающих повышенной чувствительностью к посторонней микрофлоре, например таких, как фруктовые и овощные соки, холодный чай, молочные напитки, питьевая вода, негазированные прохладительные напитки и пр. Такие напитки требуют применения более жестких санитарно-гигиенических требований к процессам упаковывания. В связи с этим появились и все активнее начинают распространяться специальные концепции фасования напитков, обеспечивающие повышенные требования к асептике процесса, в частности, включающие горячее и асептическое фасование.
Впоточных линиях для стеклянных бутылок применяют:
• горячее фасование;
• холодное фасование с предохранением от посторонней микрофлоры;
• холодное фасование и последующую тепловую обработку в туннельном пастеризаторе.
Впоточных линиях для ПЭТ бутылок применяют:
•горячее фасование;
•холодное фасование с предохранением от посторонней микрофлоры;
•асептическое (холодное) фасование.
7.4.5.7.1. Горячее фасование напитков
Горячее фасование напитков осуществляют в стеклянные и полимерные бутылки при температуре 80–95 °С.
Отличительной особенностью поточных линий для горячего розлива напитков является то, что, помимо типичной комплектации, в их состав дополнительно входит устройство для поворота бутылок из вертикального в горизонтальное положение и обратно, а также туннельный охладитель.
Горячее фасование осуществляют следующим образом: напиток с начальной температурой 12–20 °С предварительно нагревают в теплообменнике до 55–60 °С, при которой происходят деаэрация и гомогенизация продукта. После этого напиток в другом (последующем) теплообменнике дополнительно нагревают до 100 °С (а иногда и более), выдерживают при этой температуре в специальном выдерживателе около 30 с, после чего охлаждают в рекуперационной секции второго (по ходу технологического потока) теплообменника обычно до 85–95 °С и при этой достаточно высокой температуре осуществляют фасование напитка.
Продолжительность наполнения бутылки, в зависимости от ее вместимости, составляет 2–6 с. После наполнения бутылки укупоривают продезинфицированными пробками и выдерживают в вертикальном положении около 60 с. Затем бутылки поворачивают в горизонтальное положение и выдерживают около 30 с, при этом горячий напиток с температурой 85–95 °С начинает контактировать с внутренней поверхностью горлышка бутылки и пробки. Таким образом осуществляется обеззараживание всей внутренней полости бутылки.
УПАКОВЫВАНИЕ ПИВА И ГАЗИРОВАННЫХ НАПИТКОВ |
833 |
|
|
|
|
После этих манипуляций бутылки возвращают в вертикальное положение, контролируют уровень заполнения в инспекционном устройстве и направляют в туннельный охладитель, который по конструктивному устройству напоминает туннельный пастеризатор — в нем тепловые режимы обеспечивают благодаря орошению наполненных и укупоренных бутылок водой с различной температурой. В его первой секции осуществляется выдерживание упакованного напитка при повышенной температуре, т. е. действительно продолжается тепловая обработка продукта (пастеризация), а в последующих секциях, количество которых может составлять от 2 до 8, осуществляется постепенное охлаждение продукта в течение примерно 120 с до конечной температуры примерно 30 °С.
Стеклянные бутылки, будучи по своей природе более жесткими, в процессе горячего фасования напитков не вызывают особых проблем. В то время как полимерные бутылки при изменяющихся условиях рабочего цикла деформируются — при фасовании и последующем выдерживании они растягиваются вследствие теплового расширения материала бутылки и повышенного давления в ней после укупоривания, а при охлаждении — сжимаются вследствие вакууммирования, вызванного конденсацией паров внутри сосуда.
Поэтому к полимерным бутылкам для горячего фасования предъявляют особые требования — они должны иметь более жесткую структуру и обеспечивать наилучшее сохранение формы при повышенной температуре, внутреннем избыточном давлении и вакууме. Полимерные бутылки для горячего фасования отличаются от обычных ПЭТ-бутылок специальными свойствами некоторых критических (с точки зрения условий процесса) поверхностей, а именно:
•горлышко бутылки у них более тяжелое, а полимер, образующий его, имеет высокую степень кристалличности, что позволяет выдерживать повышенную термическую нагрузку на площадь поверхности горлышка;
•корпус бутылок изготавливают с так называемыми вакуумными панелями, обеспечивающими их защиту от гидростатического давления в процессе наполнения и компенсацию деформаций при вакууме;
•они имеют более высокую кристалличность стенок, что способствует повышению теплового сопротивления корпуса бутылок;
•их ребристые донышки содержат большую порцию аморфного материала для обеспечения их жесткости;
•высокая степень растяженияматериалаплечиковбутылки(переходнойучастокот корпуса к горлышку) обеспечивает жесткость; также возможно изготавливать их ребристыми.
Охлаждение внутренней полости при изготовлении ПЭТ-бутылок для горячего фасования осуществляют непосредственно в пресс-формах благодаря высокоскоростным воздушным потокам, нагнетаемым из отверстий полых вытягивающих штоков выдувной машины.
7.4.5.7.2.Асептическое фасование напитков
Всоответствии с концепцией асептического фасования напитков обеззараживание бутылок, фасование продукта и укупорка наполненных бутылок должны осуществляться изолированно от других стадий технологического потока в асептических условиях, в так называемой локальной чистой зоне. Помимо бутылок в эту зону должны поступать: на стадию фасования — продукт после тепловой обработки (пастеризованный или стерилизованный), а на стадию укупоривания — обеззараженные пробки.
834 |
ПИВОВАРЕННАЯ ИНЖЕНЕРИЯ |
|
|
Локальная чистая зона — своеобразный «изолятор», отделяющий прозрачными боковыми панелями и потолком внутреннее изолированное пространство, в котором установлено соответствующее технологическое оборудование, от атмосферы окружающего помещения. Внутри этой зоны поддерживают небольшое избыточное давление за счет нагнетания в нее стерильного воздуха.
При организации чистой зоны необходимо стремиться к минимизации ее внутреннего пространства, поэтому оборудование для асептического фасования напитков стараются специально конструировать более компактным. При этом стремятся по возможности уменьшить количество подвижных механических частей внутри чистой зоны, особенно располагаемых выше бутылок, а приводы, распределительные пневматические и электрические устройства и т. п. разместить вне этой зоны.
Экстренное вмешательство оператора в технологический процесс со стороны цеха возможно только с помощью специальных герметичных рукавов-перчаток, расположенных внутри чистой зоны и закрепленных на прозрачных боковых панелях «изолятора». Мойку и дезинфекцию оборудования в чистой зоне осуществляют автоматизировано.
Бутылки обеззараживают, обычно, смесью пара и надуксусной кислоты. При этом необходимо обеспечить полный контакт с поверхностью бутылки, осуществив при этом одновременное обеззараживание внутренней и наружной поверхности бутылок. Остатки дезинфицирующего раствора удаляют из полости бутылки при ополаскивании ее стерильной водой, подаваемой вместе со стерильным воздухом. Остаточная концентрация надуксусной кислоты (или перекиси водорода) не должна превышать 0,1 ppm.
Обеззараживание пробок осуществляют в ванне с надуксусной кислотой в течение не менее 60 с.
7.5.ЛИНИИ УПАКОВЫВАНИЯ ПИВА И НАПИТКОВ
ВМЕТАЛЛИЧЕСКИЕ БАНКИ
Вметаллические банки упаковывают значительную часть пива и газированных безалкогольных напитков.
7.5.1.Типы и основные параметры линий для упаковывания напитков
вметаллические банки
По структуре и организации работы все баночные линии однотипны и различаются лишь производительностью. Максимальная производительность баночных линий может достигать 150 000 банок/ч.
7.5.2.Инженерные задачи при упаковывании напитков в металлические банки
Косновным и обязательным инженерным задачам при машинном упаковывании на-
питков в металлические банки относят:
• ополаскивание банок;
• фасование напитков;
• закатывание банок;
• межоперационное транспортирование банок.
Помимо этого, в комплексных поточных линиях упаковывания напитков в банки приходится решать и некоторые другие инженерные задачи, например, обеспечить:
УПАКОВЫВАНИЕ ПИВА И ГАЗИРОВАННЫХ НАПИТКОВ |
835 |
|
|
|
|
•подачу крышек;
•контроль пустых банок;
•контроль уровня напитка;
•упаковку банок в термоусадочную пленку;
•палетизацию упаковок с банками.
Несмотря на все предосторожности, предпринимаемые при транспортировке и погрузке/разгрузке металлических банок, они все же могут быть повреждены или загрязнены. Простого визуального контроля металлических банок, при котором выявляют лишь грубое изменение формы банки (овальность), зачастую оказывается недостаточно. Очень важно выявить и прочие механические повреждения банок, поскольку вмятины на стенках приводят к нарушению слоя лака на внутренней поверхности банки. Кроме этого, важно выявить загрязнения, которые не могут быть удалены в ополаскивающей машине.
Контроль пустых банок осуществляют с помощью таких же инспекционных устройств, какие применяют при контроле пустых бутылок.
7.5.3. Организация поточных линий упаковывания напитков в металлические банки
Автоматические линии упаковывания пива и газированных напитков в металлические банки во многом схожи с линиями, применяемыми для упаковывания напитков в стеклянные и пластиковые бутылки. Они также состоят из нескольких машин, расположенных в порядке последовательности выполнения технологических операций и связанных между собой конвейерами для межоперационного транспортирования банок.
От линий упаковывания в стеклянные и полимерные бутылки эти линии отличаются специфическими технологическими операциями и, следовательно, составом оборудования.
Ктаким аппаратурно-технологическим отличиям этих линий относят:
•оснащение их машин для расформирования пакетов с банками — сталкивателей банок;
•использование в них исключительно ополаскивающих машин;
•применение специальных фасовочных машин;
•применение закаточных машин.
Существенным отличием в организации поточных линий для упаковывания напитков в металлические банки является то, что в качестве ведущего оборудования линии, определяющего ее требуемую производительность, принимают пастеризатор, а производительность остальных машин, входящих в состав линии, выбирают с некоторым запасом.
Это обусловлено тем, что критической операцией в линии является пастеризация, поскольку пастеризатор кратковременно останавливать в ходе работы нельзя во избежание перегрева и снижения качества пива.
Повышенная производительность остальных машин относительно пастеризатора позволяет обеспечить запас производительности и при необходимости быстро наверстать упущенное в результате вынужденных непродолжительных остановок при сбое в работе отдельных машин линии.
7.5.4. Строение поточных линий упаковывания напитков в металлические банки
Компоновочные решения линий упаковывания пива и других прохладительных напитков в металлические банки аналогичны решениям, применяемым при проектировании линий, предназначенных для стеклянных бутылок (см. раздел 7.3.4).
Вариант типичной структурной схемы технологической линии упаковывания пива в металлические банки приведен на рис. 7.124.
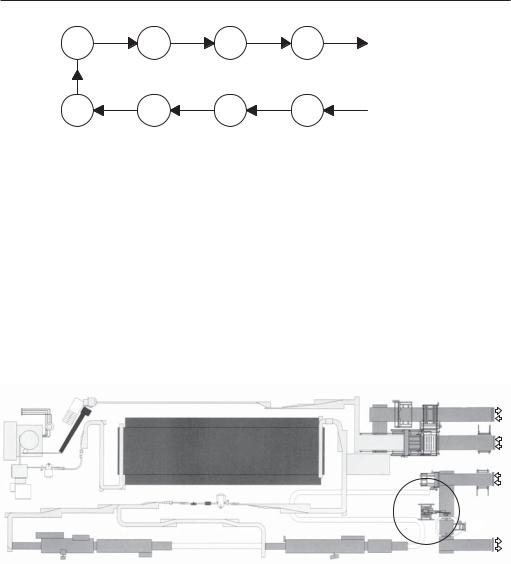
836 |
|
ПИВОВАРЕННАЯ ИНЖЕНЕРИЯ |
|
||
5 |
6 |
7 |
8 |
Отвод упакованной |
|
готовой продукции |
|||||
|
|
|
|
4 |
3 |
2 |
1 |
Подача банок |
Рис. 7.124. Типичная структурная схема технологической линии упаковывания пива в металлические банки:
1 — машина для расформирования пакетов (сталкиватель банок); 2, 3, 4, 5, 7 и 8 — машины ополаскивающая, фасовочная, закаточная, инспекционная, упаковочная
и пакетоформирующая; 6 — пастеризатор туннельный
При упаковывании напитков в банки в поточной автоматизированной линии процессы осуществляются во многом так же, как в линиях, предназначенных для стеклянных бутылок.
Банки послойно снимаются с поддона и последовательно (одна за другой) подаются в ополаскивающую машину. Они перемещаются по системе вертикальных и горизонтальных конвейеров, в результате чего исключается необходимость в устройствах для их переворачивания. После мойки банки поступают к фасовочной машине для наполнения. При наполнении банки напитком применяют прогрессивный метод предварительного вакуумирования, обеспечивающий высокое качество фасования. После наполнения банки поступают к закаточной машине, установленной непосредственно рядом с фасовочной машиной.
Дальнейшие операции по упаковыванию банок в коробки и укладке их на поддоны выполняются упаковочной и пакетоформирующей машинами.
|
|
|
|
|
|
|
|
|
|
|
|
|
|
|
|
|
|
|
|
|
|
|
|
|
|
|
|
|
|
|
|
|
|
|
|
|
|
|
13 |
|
|
|
|
|
|
|
|
|
|
|
|
|
|
||||||||||||
|
|
|
|
|
|
2 |
|
|
|
|
|
|
|
|
|
|
|
19 |
|
|||||||||||||
|
|
|
|
|
|
|
|
|
|
|
|
|
|
|
|
|
|
|
|
|
|
|
|
|
|
|
|
22 |
||||
|
|
|
|
|
|
|
|
|
|
|
|
|
|
|
|
|
|
|
|
|
|
|
|
|
|
|
|
|
|
|
|
|
|
|
|
|
|
|
|
|
|
|
|
|
|
|
|
|
|
|
|
|
|
|
|
|
|
|
|
|
|
|
|
|
|
|
|
|
|
|
|
|
|
|
|
|
|
|
|
|
|
|
|
|
|
|
|
|
|
|
|
|
|
|
|
|
|
|
|
|
|
|
|
|
3 |
|
|
|
|
|
|
|
|
|
|
|
|
|
|
|
|
|
|
|
|
|
|||||
|
|
|
|
|
|
|
|
|
|
|
|
|
|
|
|
|
|
|
|
17 |
|
|
|
|
|
|
|
|
|
|
||
|
|
|
|
|
|
|
|
|
|
|
|
|
|
|
|
|
|
|
|
|
|
|
||||||||||
|
4 |
|
|
|
|
|
|
|
|
|
|
|
|
|
|
|
|
|
|
|
|
|
|
|
|
|
|
|
|
|
|
|
|
|
|
|
|
|
|
|
|
|
|
|
|
|
|
|
|
|
|
|
|
|
|
|
|
|
|
|
|
|
|
|
|
|
|
|
|
|
|
|
|
|
|
|
|
|
|
|
|
|
7 |
|
|
|
|
|
|
|
1 |
|
|
|
|
|
|
|
|
|
|
|
|
|
|
|
|
|
|
|
|
|
|
|
|
|
|
|
|
|
|
|
|
|
|
|
|
|
|
|
|
5 |
|
|
|
|
|
|
|
|
|
|
|
|
|
|
|
|
|
|
|
|
|
|
|
|
|
|||||||
|
|
|
|
|
|
|
|
|
|
|
|
|
|
|
|
|
|
|
|
|
|
|
|
|
|
|
|
|
|
|
||
|
|
|
|
|
|
|
|
|
|
|
|
|
|
|
|
|
|
|
|
|
|
|
|
|
21 |
|
|
|
||||
|
|
|
|
|
|
|
|
|
|
|
|
|
|
|
|
|
|
|
|
|
|
|
|
|
|
|
|
|
|
|||
|
|
|
|
|
|
6 |
|
|
|
|
|
|
|
|
|
|
|
|
|
|
|
|
|
|
|
|
|
|
|
|
|
|
|
|
|
|
|
|
|
|
|
|
|
|
|
|
|
|
|
|
|
|
|
|
|
|
|
|
|
|
|
|
|
|
|
|
|
|
|
|
|
|
|
|
|
|
|
|
|
9 |
8 |
|
|
|
|
|
|
|
|
|
|
|
|
|||||
|
|
|
|
|
|
|
|
|
|
|
|
|
|
|
|
|
|
|
|
|
14 |
|
|
|
12 |
|
|
|
||||
|
|
|
|
|
|
|
15 |
|
|
|
|
|
|
|
|
|
|
|
|
|
|
|||||||||||
|
|
|
20 |
|
|
|
|
|
|
|
|
|
|
|
|
|
|
|
|
|
|
|
|
|||||||||
|
|
|
|
|
|
|
|
|
|
|
|
|
|
|
|
|
|
|
||||||||||||||
|
|
|
|
|
|
|
|
|
|
|
|
|
|
|
|
|
|
|
|
|
|
|
||||||||||
|
|
|
|
|
|
|
|
|
|
|
|
|
|
|
|
|
|
|
|
|
|
|
|
|||||||||
|
|
|
|
|
|
|
|
|
|
|
|
|
|
|
|
|
|
|
|
|
|
|
|
|
|
|
|
|
|
|
|
|
18
|
|
|
|
|
|
10 |
|
|
|
16 |
|
111 |
|||||
|
|
|
|||
|
|||||
|
|
|
|
|
Рис. 7.125. Вариант компоновки линии производительностью 30 000 бут./ч для упаковывания пива в металлические банки:
1 — сталкиватель банок с транспортных поддонов; 2 — конвейер банок; 3 — ополаскаватель банок; 4 и 5 — машины фасовочная и укупорочная; 6 и 8 — устройства для контроля уровня; 7 — пастеризатор туннельный; 9 — устройство для нанесения даты; 10 и 11 — машины упаковочные: упаковка по шесть банок и упаковка в картонные короба; 12 — робот для формирования пакетов упаковок; 13 — устройство вывода бракованных банок; 14, 15 и 16 — конвейеры упаковок, банок и пакетов на поддонах; 17 — устройство обдува; 18 — упаковщик транспортных поддонов; 19 — магазин пустых транспортных поддонов; 20 — стол подъемный; 21 — устройство поворачивающее;
22 — конвейер поддонов