
- •Preface
- •About the Author
- •About the Book
- •Acknowledgment
- •Contents
- •1.1 Industry Overview
- •1.2 Incentives for Renewables
- •1.3 Utility Perspective
- •1.3.1 Modularity
- •1.3.2 Emission-Free
- •References
- •2.1 Wind in the World
- •2.3 Europe
- •2.4 India
- •2.5 Mexico
- •2.6 Ongoing Research and Development
- •References
- •3.1 Present Status
- •3.2 Building Integrated pv Systems
- •3.3 pv Cell Technologies
- •3.3.2 Polycrystalline and Semicrystalline
- •3.3.3 Thin Films
- •3.3.4 Amorphous Silicon
- •3.3.5 Spheral
- •3.3.6 Concentrated Cells
- •3.4 pv Energy Maps
- •References
- •5.1 System Components
- •5.1.1 Tower
- •5.1.2 Turbine Blades
- •5.1.3 Yaw Control
- •5.1.4 Speed Control
- •5.2 Turbine Rating
- •5.3 Electrical Load Matching
- •5.5 System Design Features
- •5.5.1 Number of Blades
- •5.5.2 Rotor Upwind or Downwind
- •5.5.3 Horizontal Axis Versus Vertical Axis
- •5.5.4 Spacing of the Towers
- •5.6 Maximum Power Operation
- •5.6.2 Peak Power Tracking Scheme
- •5.7 System Control Requirements
- •5.7.1 Speed Control
- •5.7.2 Rate Control
- •5.8 Environmental Aspects
- •5.8.1 Audible Noise
- •5.8.2 Electromagnetic Interference (EMI)
- •References
- •6.1 Electromechanical Energy Conversion
- •6.1.1 DC Machine
- •6.1.2 Synchronous Machine
- •6.1.3 Induction Machine
- •6.2 Induction Generator
- •6.2.1 Construction
- •6.2.2 Working Principle
- •6.2.3 Rotor Speed and Slip
- •6.2.4 Equivalent Circuit for Performance Calculations
- •6.2.8 Transients
- •References
- •7.1 Speed Control Regions
- •7.2 Generator Drives
- •7.3 Drive Selection
- •References
- •8.1 The pv Cell
- •8.2 Module and Array
- •8.3 Equivalent Electrical Circuit
- •8.4 Open Circuit Voltage and Short Circuit Current
- •8.6 Array Design
- •8.6.1 Sun Intensity
- •8.6.2 Sun Angle
- •8.6.3 Shadow Effect
- •8.6.4 Temperature Effect
- •8.6.5 Effect of Climate
- •8.6.6 Electrical Load Matching
- •8.6.7 Sun Tracking
- •8.7 Peak Power Point Operation
- •8.8 pv System Components
- •References
- •9.1 Energy Collection
- •9.1.1 Parabolic Trough
- •9.1.2 Central Receiver
- •9.1.3 Parabolic Dish
- •9.2 Solar II Power Plant
- •9.3 Synchronous Generator
- •9.3.1 Equivalent Electrical Circuit
- •9.3.2 Excitation Methods
- •9.3.3 Electrical Power Output
- •9.3.4 Transient Stability Limit
- •9.4 Commercial Power Plants
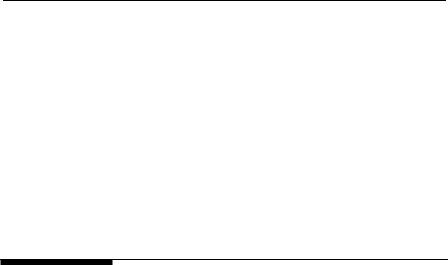
TABLE 9-1
Comparison of Alternative Solar Thermal Power System Technologies
|
Solar Concentration |
Operating Temperature |
Thermodynamic |
Technology |
(x Suns) |
on the Hot Side |
Cycle Efficiency |
|
|
|
|
Parabolic Trough |
100 |
300–500°C |
Low |
Receiver |
|
|
|
Central Receiver |
1000 |
500–1000°C |
Moderate |
Power Tower |
|
|
|
Dish Receiver with |
3000 |
800–1200°C |
High |
Engine |
|
|
|
|
|
|
|
the dish collectors. Because of their small size, it is more modular than other solar thermal power systems, and can be assembled in a few hundred kW to few MW capacities. This technology is particularly attractive for small stand-alone remote applications.
The three alternative solar thermal technologies are compared in Table 9-1.
9.2Solar II Power Plant
The central receiver technology with power tower is getting new development thrust in the U.S.A. as having a higher potential of generating lower cost electricity at large scale. An experimental 10 MWe power plant using this technology has been built and commissioned in 1996 by the Department of Energy in partnership with the Solar II Consortium of private investors led by the Southern California Edison, the second largest electrical utility company in the U.S.A. It is connected to the grid, and has enough capacity to power 10,000 homes. The plant is designed to operate commercially for 25 to 30 years. Figure 9-3 is the site photograph of this plant located east of Barstow, California. It uses some components of Solar I plant, which was built and operated at the site using the central receiver power tower technology. The Solar I plant, however, generated steam directly to drive the generator without the thermal storage feature of the Solar II plant.
Solar II central receiver (Figure 9-4) was developed by the Sandia National Laboratory. It raises the salt temperature to 1,050°F. The most important feature of the Solar II design is its innovative energy collection and the storage system. It uses a salt that has excellent heat retention and heat transfer properties. The heated salt can be used immediately to generate steam and electric power. Or, it can be stored for use during cloudy periods or after the sun goes down to meet the evening load demand on the utility grid. Because of this unique energy storage feature, the power generation is decoupled from the energy collection. For electrical utility, this storage capability is crucial in that the energy is collected when available, and is used to generate high-value electricity when it is most needed. The salt selected by
© 1999 by CRC Press LLC