
- •Preface
- •About the Author
- •About the Book
- •Acknowledgment
- •Contents
- •1.1 Industry Overview
- •1.2 Incentives for Renewables
- •1.3 Utility Perspective
- •1.3.1 Modularity
- •1.3.2 Emission-Free
- •References
- •2.1 Wind in the World
- •2.3 Europe
- •2.4 India
- •2.5 Mexico
- •2.6 Ongoing Research and Development
- •References
- •3.1 Present Status
- •3.2 Building Integrated pv Systems
- •3.3 pv Cell Technologies
- •3.3.2 Polycrystalline and Semicrystalline
- •3.3.3 Thin Films
- •3.3.4 Amorphous Silicon
- •3.3.5 Spheral
- •3.3.6 Concentrated Cells
- •3.4 pv Energy Maps
- •References
- •5.1 System Components
- •5.1.1 Tower
- •5.1.2 Turbine Blades
- •5.1.3 Yaw Control
- •5.1.4 Speed Control
- •5.2 Turbine Rating
- •5.3 Electrical Load Matching
- •5.5 System Design Features
- •5.5.1 Number of Blades
- •5.5.2 Rotor Upwind or Downwind
- •5.5.3 Horizontal Axis Versus Vertical Axis
- •5.5.4 Spacing of the Towers
- •5.6 Maximum Power Operation
- •5.6.2 Peak Power Tracking Scheme
- •5.7 System Control Requirements
- •5.7.1 Speed Control
- •5.7.2 Rate Control
- •5.8 Environmental Aspects
- •5.8.1 Audible Noise
- •5.8.2 Electromagnetic Interference (EMI)
- •References
- •6.1 Electromechanical Energy Conversion
- •6.1.1 DC Machine
- •6.1.2 Synchronous Machine
- •6.1.3 Induction Machine
- •6.2 Induction Generator
- •6.2.1 Construction
- •6.2.2 Working Principle
- •6.2.3 Rotor Speed and Slip
- •6.2.4 Equivalent Circuit for Performance Calculations
- •6.2.8 Transients
- •References
- •7.1 Speed Control Regions
- •7.2 Generator Drives
- •7.3 Drive Selection
- •References
- •8.1 The pv Cell
- •8.2 Module and Array
- •8.3 Equivalent Electrical Circuit
- •8.4 Open Circuit Voltage and Short Circuit Current
- •8.6 Array Design
- •8.6.1 Sun Intensity
- •8.6.2 Sun Angle
- •8.6.3 Shadow Effect
- •8.6.4 Temperature Effect
- •8.6.5 Effect of Climate
- •8.6.6 Electrical Load Matching
- •8.6.7 Sun Tracking
- •8.7 Peak Power Point Operation
- •8.8 pv System Components
- •References
- •9.1 Energy Collection
- •9.1.1 Parabolic Trough
- •9.1.2 Central Receiver
- •9.1.3 Parabolic Dish
- •9.2 Solar II Power Plant
- •9.3 Synchronous Generator
- •9.3.1 Equivalent Electrical Circuit
- •9.3.2 Excitation Methods
- •9.3.3 Electrical Power Output
- •9.3.4 Transient Stability Limit
- •9.4 Commercial Power Plants
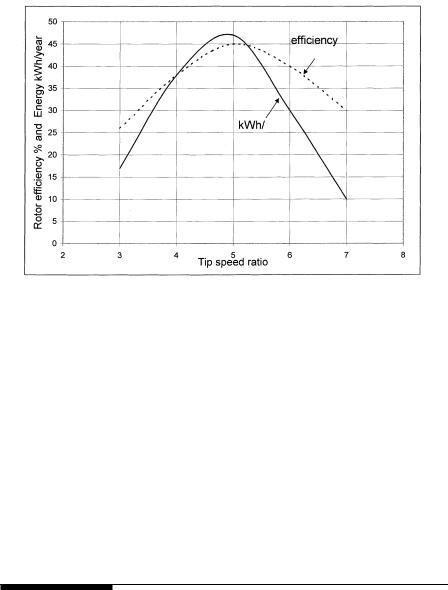
FIGURE 5-11
Rotor efficiency and annual energy production versus rotor tip-speed ratio.
coefficient Cp. The theory and field experience indicates that the variablespeed operation yields 20 to 30 percent more energy than with the fixedspeed operation. Nevertheless, cost of the variable-speed control is added. In the system design, this trade-off between the energy increase and the cost increase has to be optimized. In the past, the added costs of designing the variable-pitch rotor, or the speed control with power electronics, outweighed the benefit of the increased energy capture. However, falling prices of the power electronics for speed control, and availability of high-strength fiber composites for constructing high-speed rotors, have made it economical to capture more energy when the speed is high. In the fixed-speed operation, on the other hand, the rotor is shut off during high-wind speeds, losing significant energy. The pros and cons of the variable and the fixed-speed operations are listed in Table 5-1.
5.5System Design Features
The following additional design trade-offs are available to the system engineer:
5.5.1Number of Blades
This is the first determination the design engineer must make. Wind machines have been built with the number of blades ranging from 2 to 40
© 1999 by CRC Press LLC

TABLE 5-1
Advantages of Fixed and Variable Speed Systems
Fixed-Speed System |
Variable-Speed System |
|
|
Simple and inexpensive electrical system |
Higher rotor efficiency, hence, higher energy capture |
|
per year |
Fewer parts, hence higher reliability |
Low transient torque |
Lower probability of excitation of |
Fewer gear steps, hence inexpensive gear box |
mechanical resonance of the structure |
|
No frequency conversion, hence, no |
Mechanical damping system not needed, the electrical |
current harmonics present in the |
system could provide damping if required |
electrical system |
|
Lower capital cost |
No synchronization problems |
|
Stiff electrical controls can reduce system voltage sags |
|
|
or more. The high number of blades was used in old low, tip-speed ratio rotors for water pumping, the application which needs high starting torque. The modern high, tip-speeds ratio rotors for generating electrical power have two or three blades, many of them with just two. The major factors involved in deciding the number of blades are as follows:
•the effect on power coefficient.
•the design tip-speeds ratio.
•the cost.
•the nacelle weight.
•the structural dynamics.
•the means of limiting yaw rate to reduce gyroscopic fatigue.
Compared to the two-blade design, the three-blade machine has smoother power output and balanced gyroscopic force. There is no need to teeter the rotor, allowing the use of simple rigid hub. Three blades are more common in Europe, where large machines up to 1 MW are being developed using the three-blade configuration. The American practice, however, has been in the two blade designs. Adding the third blade increases the power coefficient only by about 5 percent, thus giving a diminished rate of return for the 50 percent more weight and cost. The two-blade rotor is also simpler to erect, since it can be assembled on the ground and lifted to the shaft without complicated maneuvers during the lift. The number of blades is often viewed as the blade solidity. Higher solidity ratio gives higher starting torque and operates at low speed. For electrical power generation, the turbine must run at high speed since the electrical generator weighs less and operates more efficiently at high speed. That is why all large-scale wind turbines have low solidity ratio, with just two or three blades.
© 1999 by CRC Press LLC
5.5.2Rotor Upwind or Downwind
Operating the rotor upwind of the tower produces higher power as it eliminates the tower shadow on the blades. This also results in lower noise, lower blade fatigue, and smoother power output. The downwind blades, on the other hand, allow the use of free yaw system. It also allows the blades to deflect away from the tower when loaded. Both types are used at present with no clear trend.
5.5.3Horizontal Axis Versus Vertical Axis
Most wind turbines built at present have a horizontal axis. The vertical axis Darrieus machine has several advantages. First of all, it is omnidirectional and requires no yaw mechanism to continuously orient itself toward the wind direction. Secondly, its vertical drive shaft simplifies the installation of the gearbox and the electrical generator on the ground, making the structure much simpler. On the negative side, it normally requires guy wires attached to the top for support. This could limit its applications, particularly for the offshore sites. Overall, the vertical axis machine has not been widely used because its output power cannot be easily controlled in high winds simply by changing the blade pitch. With modern low-cost, variable-speed power electronics emerging in the wind power industry, the Darrieus configuration may revive, particularly for large capacity applications.
5.5.4Spacing of the Towers
When installing a cluster of machines in a wind farm, certain spacing between the wind towers must be maintained to optimize the power cropping. The spacing depends on the terrain, the wind direction, the speed, and the turbine size. The optimum spacing is found in rows 8 to 12-rotor diameters apart in the wind direction, and 1.5 to 3-rotor diameters apart in the crosswind direction (Figure 5-12). A wind farm consisting of 20 towers rated at 500 kW each need 1 to 2 square kilometers of land area. Of this, only a couple of percent would actually occupy the tower and the access roads. The remaining land could continue its original use (Figure 5-13). The average number of machines in wind farms varies greatly, ranging from several to hundreds depending on the required power capacity.
When the land area is limited or is at a premium price, one optimization study that must be conducted in an early stage of the wind farm design is to determine the number of turbines, their size, and the spacing for extracting the maximum energy from the farm. The trades in such a study are as follows:
© 1999 by CRC Press LLC