
- •1.1. Сучасне металургійне виробництво і його продукція
- •1.2. Матеріали для виробництва металів і сплавів
- •1.3. Виробництво чавуну.
- •1.4. Виплавка чавуну.
- •1.5. Продукти доменної плавки
- •ЛЕКЦІЯ 2
- •2.1. Процеси прямого одержання заліза з руд
- •2.2. Одержання губчатого заліза в шахтних печах.
- •2.3. Відновлення заліза в киплячому шарі.
- •2.4. Одержання губчатого заліза в капсулахатиглях.
- •2.5. Виробництво сталі
- •ЛЕКЦІЯ 3
- •3.1. Виробництво сталі
- •3.2. Розливання сталі
- •3.3. Способи підвищення якості стали
- •3.4. Виробництво кольорових металів>
- •ЛЕКЦІЯ 4
- •4.1. Зварювальне виробництво. Зварювання плавленням
- •4.2. Зварювання плавленням
- •4.3. Плазмове зварювання
- •4.4. Електрошлакове зварювання.
- •4.5. Променеві способи зварювання
- •4.6. Газове зварювання
- •ЛЕКЦІЯ 5
- •5.1. Зварювання тиском
- •5.2. Контактне зварювання
- •5.3. Дифузійне зварювання
- •5.4. Зварювання тертям
- •5.5. Зварювання вибухом
- •5.6. Тип звареного з'єднання
- •5.7. Спеціальні термічні процеси у зварювальнім виробництві
- •5.8. Напилювання
- •5.9. Пайка
- •ЛЕКЦІЯ 6
- •6.1. Заготівельне виробництво
- •6.2. Загальні принципи вибору заготовки
- •6.3. Основні фактори, що впливають на вибір способу одержання заготовки.
- •6.4. Ливарне виробництво
- •6.5. Класифікація литих заготовок.
- •6.6. Ливарні сплави
- •6.7. Ливарні властивості сплавів
- •6.8. Ливарні сплави
- •ЛЕКЦІЯ 7
- •7.1. Виготовлення виливків у піщаних формах
- •7.2. Модельний комплект
- •7.3. Виготовлення ливарних форм
- •7.4. Формування в кесонах.
- •7.5. Машинне формування
- •7.6. Вакуумне формування.
- •7.7. Виготовлення стрижнів
- •ЛЕКЦІЯ 8
- •8.1. Виготовлення виливків у піщаних формах
- •8.2. Спеціальні способи лиття
- •8.3. Виготовлення виливків відцентровим литтям
- •ЛЕКЦІЯ 9
- •9.1. Спеціальні способи лиття
- •9.2. Виготовлення виливків електрошлаковим литтям
- •9.3. Виготовлення виливків безперервним литтям
- •9.4. Особливості виготовлення виливків з різних сплавів
- •9.5. Сталеві виливки
- •9.6. Алюмінієві сплави
- •9.7. Мідні сплави
- •9.8. Титанові сплави
- •9.9. Дефекти виливків і їх виправлення
- •9.10. Методи виявлення дефектів
- •9.11. Методи виправлення дефектів
- •9.12. Техніка безпеки й охорона навколишнього середовища в ливарнім виробництві
- •ЛЕКЦІЯ 10
- •10.1. Технологічність конструкцій литих форм
- •10.2. Основи конструювання литих заготовок
- •10.3. Виливка, виготовлені литтям у піщані форми
- •10.4. Основні положення до вибору способу лиття
- •ЛЕКЦІЯ 11
- •11.1. Класифікація процесів обробки тиском
- •11.2. Схеми напруженого й деформованого станів
- •11.3. Закономірності обробки тиском. Характеристики деформацій
- •11.4. Технологічні властивості
- •11.5. Технологічні випробування
- •ЛЕКЦІЯ 12
- •12.1. Прокат і його виробництво
- •12.2. Способи прокатки
- •12.3. Технологічний процес прокатки
- •12.4. Виправлення прокату
- •12.5. Разрезка й заготівельна обробка прокату
- •ЛЕКЦІЯ 13
- •13.1. Продукція прокатного виробництва
- •13.2. Пресування
- •13.3. Волочіння
- •ЛЕКЦІЯ 14
- •14.1. Кування
- •14.2. Операції кування
- •14.3. Попередні операції
- •14.4. Основні операції
- •14.5. Устаткування для кування
- •14.6. Конструювання кутих заготовок
- •ЛЕКЦІЯ 15
- •15.1. Гаряче об'ємне штампування
- •15.2. Формоутворення при гарячім об'ємнім штампуванні
- •15.3. Креслення кування
- •15.4. Технологічний процес гарячого об'ємного штампування
- •ЛЕКЦІЯ 16
- •16.1. Гаряче об'ємне штампування на молотах
- •16.2. Геометрична точність кувань, отриманих на молотах
- •16.3. Гаряче об'ємне штампування на пресах
- •16.5. Ротаційні способи виготовлення кувань
- •16.6. Штампування рідкого металу
- •ЛЕКЦІЯ 17
- •17.1. Холодне штампування
- •17.2. Об'ємне холодне штампування
- •17.3. Листове штампування
- •17.4. Операції листового штампування
- •ЛЕКЦІЯ 18
- •18.1. Листове штампування
- •18.2. Високошвидкісні методи штампування
- •18.3. Формоутворення заготовок з порошкових матеріалів
- •ЛЕКЦІЯ 19
- •19.1. Загальна характеристика розмірної обробки
- •19.2. Режими різання, шорсткість поверхні
- •19.3. Верстати для обробки різанням
- •19.4. Технологічні можливості способів різання
- •19.5. Свердління
- •19.6. Протягання
- •ЛЕКЦІЯ 20
- •20.1. Фрезерування
- •20.2. Шліфування
- •20.3. Технологічні методи оздоблювальної (фінішної) обробки поверхонь деталей машин
- •20.4. Хонингование
- •20.5. Суперфінішування
- •20.6. Полірування
- •ЛЕКЦІЯ 21
- •21.1. Характеристика електрофізичних і електрохімічних методів обробки
- •21.2. Електроерозійні методи обробки
- •21.3. Електроіскрова обробка
- •21.4. Электроимпульсная обробка
- •21.5. Електрохімічна обробка
- •21.6. Електрохімічна розмірна обробка
- •21.7. Комбіновані методи обробки
- •21.9. Променеві методи обробки
- •21.10. Плазмова обробка
- •21.11. Плазмове напилювання.
- •ЛІТЕРАТУРА
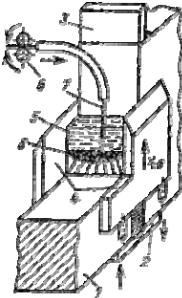
33
то забезпечується підвищена якість зварених швів. Це дозволяє виконувати мікроплазмове зварювання металу товщиною 0,025…0,8 мм.
Недолік плазмового зварювання – недовговічність пальників.
4.4. Електрошлакове зварювання.
Сутність процесу полягає в тому, що теплову енергію, необхідну для розплавлювання основного й присадочного металу, дає теплота, виділювана в обсязі жужільної ванни при проходженні через неї струму (мал. 4.4).
Мал.4.4. Схема електрошлакового зварювання
заготовки, що зварюються, 1 установлюють у вертикальнім положенні. У замкнений простір між водоохлаждаемыми мідними повзунами 4 і вертикально встановленими крайками виробів засинають флюс і подають електродний дріт 7 за допомогою спеціального механізму подачі 6.
На початку процесу збуджують дугу, флюс плавиться й утворюється електропровідний шлаки 5. Шлаки шунтирует дугу, вона гасне, вихідний ланцюг джерела живлення замикається через шлаки. Струм, проходячи через шлаки, розігріває його, це приводить до раславлению крайок основного металу й електрода. Розплав стікає вниз і утворює зварювальну ванну 8, вичавлюючи шлаки нагору, і затвердевает.
У початковому й кінцевому ділянках шва утворюються дефекти: на початку шва – непровар крайок, наприкінці шва – усадочна раковина й неметалічні включення. Тому зварювання починають і закінчують на спеціальних планках 2 і 3, які потім видаляють газовим різанням.
Переваги: можливе зварювання металу будь-якої товщини (з 16 мм). Заготовки з товщиною до 150 мм можна зварювати одним електродом, що роблять поперечне коливання в площині стику, при товщині більш 150 мм використовуються декількох дротів. Є досвід зварювання товщиною до 2 м.
Недолік способу – утвір крупного зерна у шві й околошовной зоні внаслідок уповільненого нагрівання й охолодження. Необхідне проведення термічної обробки: нормалізації або отжига для здрібнювання зерна.
Електрошлакове зварювання широко застосовують у важкім машинобудуванні для виготовлення кованесзварених і литих-зварених конструкцій; станини й деталі потужних пресів і верстатів, колінчаті вали суднових дизелів, ротори й вали гідротурбін, казани високого тиску й т.п.
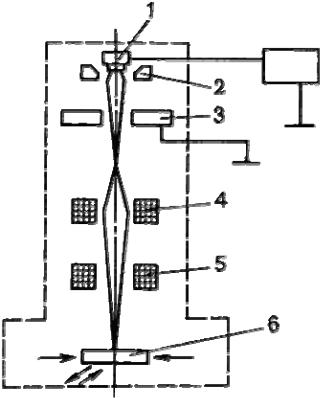
34
4.5. Променеві способи зварювання
Електронно-променеве зварювання.
Сутність процесу полягає в тому, що деталі, що зварюються, зібрані без зазору, поміщають у вакуумну камеру й подають на них електродний промінь – пучок електронів, що рухаються з великою швидкістю. При зіткненні з виробом електрони гальмуються, їхня кінетична енергія переходить у теплову енергію й розплавляє метал. Температура в місці зіткнення досягає 5000…6000 0С. Переміщаючи електронний промінь уздовж стику, одержують зварений шов.
Схема установка для електронно-променевого зварювання представлена на мал. 4.5.
Рис.4.5. Схема установки для електронно-дугового зварювання
Електрони, що випускаються катодом 1 електронної гармати, формуються в пучок електродом 2, розташованим безпосередньо за катодом, прискорюються під дією різниці потенціалів між катодом і анодом 3, що становить 20…150 КВ і вище, потім фокусируются у вигляді променя й направляються спеціальною відхиляючої магнітною системою 5 на оброблюваний виріб 6. На формуючий електрод 2 подається негативний або нульовий стосовно катода потенціал. Фокусуванням досягається висока питома потужність променя. Струм електронного променя невеликий – від декількох міліамперів до одиниць амперів.
Процесу електронно-променевого зварювання властиві дві характерні риси:
•зварювання протікає у вакуумі, забезпечується одержання дзеркально чистої поверхні й дегазація розплавленого металу;
•інтенсивність нагрівання дуже велика, що забезпечує швидке плавлення й затвердіння металу. Шов виходить дрібнозернистий з високими механічними властивостями, з мінімальною шириною, що дозволяє зварювати сплави, чутливі до нагрівання.
Електронно-променевим зварюванням виготовляють деталі з тугоплавких, хімічно активних металів і їх сплавів (вольфрамових, танталових, молібденових, ниобиевых,
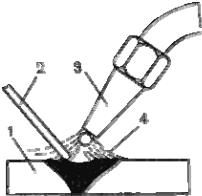
35
цирконієвих), а також алюмінієвих і титанових сплавів і високолегованих сталей. Метали й сплави можна зварювати в однорідних і різнорідних комбінаціях, зі значною різницею толщин, температур плавлення. Мінімальна товщина заготовок, що зварюються, становить 0,02 мм, максимальна – до 100 мм.
Лазерне зварювання.
Лазерне зварювання – спосіб зварювання плавленням, при яких метал нагрівають випромінюванням лазера.
Лазерний промінь являє собою змушене монохроматичне випромінювання, довжина хвилі якого залежить від природи робочого тіла лазера-випромінювача. Воно виникає в результаті змушених стрибкоподібних переходів збуджених атомів робочих тіл на більш низькі енергетичні рівні.
Основними параметрами режимів лазерної обробки є потужність випромінювання, діаметр плями фокусування, швидкість переміщення оброблюваного матеріалу відносно променя.
Перевагою лазерного зварювання є швидке крапкове нагрівання металу до плавлення. Інтенсивне зосереджене нагрівання обумовлює й надзвичайно більшу швидкість охолодження після припинення впливу променя. Це дозволяє звести до мінімуму ширину околошовной зони, зварювальні напруги й деформації.
Механізм процесів при лазернім зварюванні схожий з електронно-променевим зварюванням, але не обов'язково вакуумировать виріб.
Лазером зварюють переважно товщини до 1 мм, тому що коефіцієнт корисної дії перетворення енергії в лазерне випромінювання досить низький.
4.6. Газове зварювання
При газовім зварюванні заготовки 1 і присадочный матеріал 2 у вигляді прутка або дроту розплавляють високотемпературним полум'ям 4 газового пальника 3 (мал. 4.6).
Мал. 4.6. Схема газового зварювання
Газове полум'я одержують при згорянні горючого газу в атмосфері технічно чистого кисню. Потужність полум'я регулюють зміною наконечників пальника.
Нагрівання заготовки здійснюється більш плавно, ніж при дуговім зварюванні, тому газове зварювання застосовують для зварювання металу малої товщини (0,2…3 мм), легкоплавких кольорових металів і сплавів; металів і сплавів, що вимагають поступового нагрівання й охолодження (інструментальні сталі, латуні); для подварки дефектів у чавунних і бронзових виливках. При збільшенні товщини металу знижується продуктивність і збільшується деформація.