
- •1.1. Сучасне металургійне виробництво і його продукція
- •1.2. Матеріали для виробництва металів і сплавів
- •1.3. Виробництво чавуну.
- •1.4. Виплавка чавуну.
- •1.5. Продукти доменної плавки
- •ЛЕКЦІЯ 2
- •2.1. Процеси прямого одержання заліза з руд
- •2.2. Одержання губчатого заліза в шахтних печах.
- •2.3. Відновлення заліза в киплячому шарі.
- •2.4. Одержання губчатого заліза в капсулахатиглях.
- •2.5. Виробництво сталі
- •ЛЕКЦІЯ 3
- •3.1. Виробництво сталі
- •3.2. Розливання сталі
- •3.3. Способи підвищення якості стали
- •3.4. Виробництво кольорових металів>
- •ЛЕКЦІЯ 4
- •4.1. Зварювальне виробництво. Зварювання плавленням
- •4.2. Зварювання плавленням
- •4.3. Плазмове зварювання
- •4.4. Електрошлакове зварювання.
- •4.5. Променеві способи зварювання
- •4.6. Газове зварювання
- •ЛЕКЦІЯ 5
- •5.1. Зварювання тиском
- •5.2. Контактне зварювання
- •5.3. Дифузійне зварювання
- •5.4. Зварювання тертям
- •5.5. Зварювання вибухом
- •5.6. Тип звареного з'єднання
- •5.7. Спеціальні термічні процеси у зварювальнім виробництві
- •5.8. Напилювання
- •5.9. Пайка
- •ЛЕКЦІЯ 6
- •6.1. Заготівельне виробництво
- •6.2. Загальні принципи вибору заготовки
- •6.3. Основні фактори, що впливають на вибір способу одержання заготовки.
- •6.4. Ливарне виробництво
- •6.5. Класифікація литих заготовок.
- •6.6. Ливарні сплави
- •6.7. Ливарні властивості сплавів
- •6.8. Ливарні сплави
- •ЛЕКЦІЯ 7
- •7.1. Виготовлення виливків у піщаних формах
- •7.2. Модельний комплект
- •7.3. Виготовлення ливарних форм
- •7.4. Формування в кесонах.
- •7.5. Машинне формування
- •7.6. Вакуумне формування.
- •7.7. Виготовлення стрижнів
- •ЛЕКЦІЯ 8
- •8.1. Виготовлення виливків у піщаних формах
- •8.2. Спеціальні способи лиття
- •8.3. Виготовлення виливків відцентровим литтям
- •ЛЕКЦІЯ 9
- •9.1. Спеціальні способи лиття
- •9.2. Виготовлення виливків електрошлаковим литтям
- •9.3. Виготовлення виливків безперервним литтям
- •9.4. Особливості виготовлення виливків з різних сплавів
- •9.5. Сталеві виливки
- •9.6. Алюмінієві сплави
- •9.7. Мідні сплави
- •9.8. Титанові сплави
- •9.9. Дефекти виливків і їх виправлення
- •9.10. Методи виявлення дефектів
- •9.11. Методи виправлення дефектів
- •9.12. Техніка безпеки й охорона навколишнього середовища в ливарнім виробництві
- •ЛЕКЦІЯ 10
- •10.1. Технологічність конструкцій литих форм
- •10.2. Основи конструювання литих заготовок
- •10.3. Виливка, виготовлені литтям у піщані форми
- •10.4. Основні положення до вибору способу лиття
- •ЛЕКЦІЯ 11
- •11.1. Класифікація процесів обробки тиском
- •11.2. Схеми напруженого й деформованого станів
- •11.3. Закономірності обробки тиском. Характеристики деформацій
- •11.4. Технологічні властивості
- •11.5. Технологічні випробування
- •ЛЕКЦІЯ 12
- •12.1. Прокат і його виробництво
- •12.2. Способи прокатки
- •12.3. Технологічний процес прокатки
- •12.4. Виправлення прокату
- •12.5. Разрезка й заготівельна обробка прокату
- •ЛЕКЦІЯ 13
- •13.1. Продукція прокатного виробництва
- •13.2. Пресування
- •13.3. Волочіння
- •ЛЕКЦІЯ 14
- •14.1. Кування
- •14.2. Операції кування
- •14.3. Попередні операції
- •14.4. Основні операції
- •14.5. Устаткування для кування
- •14.6. Конструювання кутих заготовок
- •ЛЕКЦІЯ 15
- •15.1. Гаряче об'ємне штампування
- •15.2. Формоутворення при гарячім об'ємнім штампуванні
- •15.3. Креслення кування
- •15.4. Технологічний процес гарячого об'ємного штампування
- •ЛЕКЦІЯ 16
- •16.1. Гаряче об'ємне штампування на молотах
- •16.2. Геометрична точність кувань, отриманих на молотах
- •16.3. Гаряче об'ємне штампування на пресах
- •16.5. Ротаційні способи виготовлення кувань
- •16.6. Штампування рідкого металу
- •ЛЕКЦІЯ 17
- •17.1. Холодне штампування
- •17.2. Об'ємне холодне штампування
- •17.3. Листове штампування
- •17.4. Операції листового штампування
- •ЛЕКЦІЯ 18
- •18.1. Листове штампування
- •18.2. Високошвидкісні методи штампування
- •18.3. Формоутворення заготовок з порошкових матеріалів
- •ЛЕКЦІЯ 19
- •19.1. Загальна характеристика розмірної обробки
- •19.2. Режими різання, шорсткість поверхні
- •19.3. Верстати для обробки різанням
- •19.4. Технологічні можливості способів різання
- •19.5. Свердління
- •19.6. Протягання
- •ЛЕКЦІЯ 20
- •20.1. Фрезерування
- •20.2. Шліфування
- •20.3. Технологічні методи оздоблювальної (фінішної) обробки поверхонь деталей машин
- •20.4. Хонингование
- •20.5. Суперфінішування
- •20.6. Полірування
- •ЛЕКЦІЯ 21
- •21.1. Характеристика електрофізичних і електрохімічних методів обробки
- •21.2. Електроерозійні методи обробки
- •21.3. Електроіскрова обробка
- •21.4. Электроимпульсная обробка
- •21.5. Електрохімічна обробка
- •21.6. Електрохімічна розмірна обробка
- •21.7. Комбіновані методи обробки
- •21.9. Променеві методи обробки
- •21.10. Плазмова обробка
- •21.11. Плазмове напилювання.
- •ЛІТЕРАТУРА
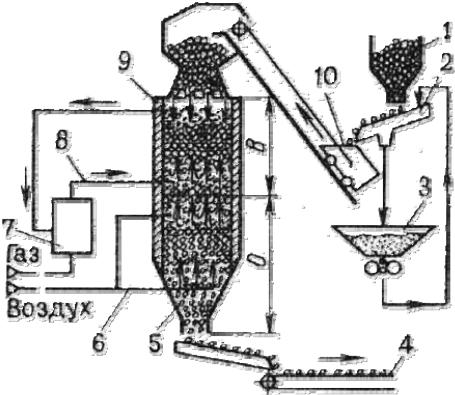
13
ЛЕКЦІЯ 2
Процеси прямого одержання заліза з руд. Виробництво стали.
2.1. Процеси прямого одержання заліза з руд
Під процесами прямого одержання заліза розуміють такі хімічні, електрохімічні або хіміко-термічні процеси, які дають можливість одержувати безпосередньо з руди, минаючи доменну піч, металеве залізо у вигляді губки, криці або рідкого металу.
Такі процеси ведуться, не витрачаючи металургійний кокс, флюси, електроенергію (на підготовку стисненого повітря), а також дозволяють одержати дуже чистий метал.
Методи прямого одержання заліза відомі давно. Випробуване більш 70 різних способів, але лише деякі здійснені й притім у невеликому промисловому масштабі.
В останні роки інтерес до цієї проблеми виріс, що зв'язане, крім заміни коксу іншим паливом, з розвитком способів глибокого збагачення руд, що забезпечують не тільки високого змісту заліза в концентратах (70…72%), але й майже повне звільнення його від сірки й фосфору.
2.2. Одержання губчатого заліза в шахтних печах.
Схема процесу представлена на Рис. 2.1.
Рис. 2.1. Схема установки для прямого відновлення заліза з руд і одержання металізованих окатишів.
14
При одержанні губчатого заліза добуту руду збагачують і одержують окатиші. Окатиші з бункера 1 по грохоту 2 поступают в короб 10 шихто завальної машини і потім в шахтну піч 9, яка працює по принципу противотока. Просип від окатишів попадає в бункер 3 с брикетировочним пресом и в вигляді окатишів знов поступає на грохот 2. Для відновлення заліза з окатышив у пічь по трубопроводу 8 подають суміш природного и доменного газів, подвергнуту у устутковання 7 конверсії, в результаті якій суміш
розчинюється на водород |
и оксид углерода CO |
. В відновлюючій зоні печи. В ній |
создається температура 1000…1100 0C, при якій |
і відновляють зелізную руду в |
окатышах до твердого губчастого зеліза. Склад зеліза в окатишах буде 90…95%.
2.3. Відновлення заліза в киплячому шарі.
Дрібнозернисту руду або концентрат поміщають на ґрати, через які подають водень або інший відбудовний газ під тиском 1,5 МПа. Під тиском водню частки руди перебувають у зваженому стані, роблячи безперервний рух і утворюючи «киплячий», «псевдосжиженый» шар. У киплячому шарі забезпечується гарний контакт газуивосстановителя із частками оксидів заліза. На одну тонну відновленого порошку витрата водню становить 600…650 м3.
2.4. Одержання губчатого заліза в капсулахатиглях.
Використовують карбидокремниевые капсули діаметром 500 мм і висотою 1500 мм. Шихта завантажується концентричними шарами. Внутрішня частина капсули заповнена восстановителем – здрібненим твердим паливом і вапняком (10…15%) для видалення сірки. Другий шар – відновлювана измельч¨нная руда або концентрат, окалина, потім ще один концентричний шар – восстановителя й вапняку. Установлені на вагонетки капсули повільно переміщаються в тунельній печі довжиною до 140 м, де відбувається нагрівання, витримка при 1200 0C і охолодження протягом 100 годин.
Відновлене залізо одержують у вигляді товстостінних труб, їх чистять, дроблять і подрібнюють, одержуючи залізний порошок зі змістом заліза до 99 %, вуглецю –
0,1…0,2%.
2.5. Виробництво сталі
Сутність процесу
Стали – залізовуглецеві сплави, що містять практично до 1,5% вуглецю, при більшому його змісті значно збільшуються твердість і крихкість сталей і вони не знаходять широкого застосування.
Основними вихідними матеріалами для виробництва стали є передільний чавун і сталевий лом (скрап).
Зміст вуглецю й домішок у сталі значно нижче, чим у чавуні. Тому сутність будьякого металургійного переділу чавуну в сталь – зниження змісту вуглецю й домішок шляхом їхнього вибіркового окиснення й перекладу в шлаки й гази в процесі плавки.
Залізо окисниться в першу чергу при взаємодії чавуну з киснем у сталеплавильних печах:
2Fe + O2 = 2Feo + Q
15
Одночасно із залізом окисняться кремній, фосфор, марганець і вуглець. оксид, що утворюється, заліза при високих температурах віддає свій кисень більш активним домішкам у чавуні, окиснюючи їх.
Процеси виплавки стали здійснюють у три етапи.
Перший етап – розплавлювання шихти й нагрівання ванни рідкого металу. Температура металу порівняно невисока, інтенсивно відбувається окиснення заліза,
утвір оксиду заліза й окиснення домішок: кремнію, марганцю й фосфору.
Найбільш важливе завдання етапу – видалення фосфору. Для цього бажане проведення плавки в основній печі, де шлаки містить Cao. Фосфорний ангідрид P2O5 утворює з оксидом заліза нестійке з'єднання (Feo)3 x P2O5. Оксид кальцію Cao– більш сильна підстава, чому оксид заліза, тому при невисоких температурах P2O5 зв'язує й переводить його в шлаки:
2P + 5Feo + 4Cao = (Cao)4 x P2O5 + 5Fe.
Для видалення фосфору необхідні невисокі температура ванни металу й шлаків, достатній зміст у шлаках Feo. Для підвищення змісту Feo у шлаках і прискорення окиснення домішок у піч додають залізну руду й окалину, наводячи залізистий шлаки. У міру видалення фосфору з металу в шлаки, зміст фосфору в шлаках збільшується. Тому необхідно забрати цей шлаки із дзеркала металу й замінити його новим зі свіжими добавками Cao.
Другий етап – кипіння металевої ванни – починається в міру прогріву до більш високих температур.
При підвищенні температури більш інтенсивно протікає реакція окиснення вуглецю, що відбувається з поглинанням теплоти:
Feo + C = CO + Fe – Q
Для окиснення вуглецю в метал уводять незначна кількість руди, окалини або вдмухують кисень.
При реакції оксиду заліза з вуглецем, пухирці оксиду вуглецю CO виділяються з рідкого металу, викликаючи «кипіння ванни». При «кипінні» зменшується зміст вуглецю в металі до необхідного, вирівнюється температура за обсягом ванни, частково віддаляються неметалічні включення, що прилипають до спливаючих пухирців CO, а також гази, що проникають у пухирці CO. Усе це сприяє підвищенню якості металу. Отже, цей етап - основної в процесі виплавки стали.
Також створюються умови для видалення сірки. Сірка в сталі перебуває у вигляді сульфіду (Fes), який розчиняється також в основному шлаках. Чим вище температура, тем більша кількість сульфіду заліза Fes розчиняється в шлаках і взаємодіє з оксидом кальцію
Cao:
Fes + Cao = Cas + Feo
з'єднання, що утворюється, Cas розчиняється в шлаках, але не розчиняється в залозі, тому сірка віддаляється в шлаки.
Третій етап – розкислення стали полягає у відновленні оксиду заліза, розчиненого в рідкому металі.
При плавці підвищення змісту кисню в металі необхідно для окиснення домішок, але в готовій сталі кисень – шкідлива домішка, тому що знижує механічні властивості стали, особливо при високих температурах.
Сталь раскисляют двома способами: осаджуючим і дифузійним.
16
Осаджуюче розкислення здійснюється введенням у рідку сталь розчинних раскислителей (феромарганцю, феросиліцію, алюмінію) елементи, що містять, які мають більшу спорідненість до кисню, чому залізо.
У результаті розкислення відновлюється залізо й утворюються оксиди: Mno, Sio2, Al2O3, які мають меншу щільність, чому сталь, і віддаляються в шлаки.
Дифузійне розкислення здійснюється розкисленням шлаків. Феромарганець, феросиліцій і алюміній у здрібненому виді завантажують на поверхню шлаків. Раскислители, відновлюючи оксид заліза, зменшують його зміст у шлаках. Отже, оксид заліза, розчинений у сталі переходить у шлаки. оксиди, що утворюються при цьому процесі, залишаються в шлаках, а відновлене залізо переходить у сталь, при цьому в сталі знижується зміст неметалічних включень і підвищується її якість .
Залежно від ступеня розкислення виплавляють сталі: а) спокійні, б) киплячі,
в) напівспокійні.
Спокійна сталь виходить при повному розкисленні в печі й ковші.
Кипляча сталь раскислена в печі неповністю. Її розкислення триває в изложнице при затвердінні злитка, завдяки взаємодії оксиду заліза й вуглецю: Feo + C = Fe + CO,
оксид, що утворюється, вуглецю CO виділяється зі сталі, сприяючи видаленню зі сталі азоту й водню, гази виділяються у вигляді пухирців, викликаючи її кипіння. Кипляча сталь не містить неметалічних включень, тому має гарну пластичність.
Напівспокійна сталь має проміжну раскисленность між спокійної й киплячою. Частково вона раскисляется в печі й у ковші, а частково – в изложнице, завдяки взаємодії оксиду заліза й вуглецю, що втримуються в сталі.
Легування стали здійснюється введенням феросплавів або чистих металів у необхідній кількості в розплав. Легуючі елементи, у яких спорідненість до кисню менше, чим у заліза (Ni, Co, Mo, Cu), при плавці й розливанню не окисняться, тому їх уводять у будь-який час плавки. Легуючі елементи, у яких спорідненість до кисню більше, чим у заліза (Si, Mn, Al, Cr, V, Ti), уводять у метал після розкислення або одночасно з ним наприкінці плавки, а іноді в ківш.
Способи виплавки стали
Чавун переробляється в сталь у різні за принципом дії металургійних агрегатах: мартенівських печах, кисневих конвертерах, електричних печах.
Виробництво стали в мартенівських печах
Мартенівський процес (1864-1865, Франція). У період до сімдесятих років був основним способом виробництва стали. Спосіб характеризується порівняно невеликою продуктивністю, можливістю використання вторинного металу – сталевого скрапу. Місткість печі становить 200…900 т. Спосіб дозволяє одержувати якісну сталь.
Мартенівська піч (Рис. 2.2.) по пристрою й принципу роботи є полум'яною відбивною регенеративною піччю. У плавильному просторі спалюється газоподібне
паливо або мазут. Висока температура для одержання стали в розплавленому стані забезпечується регенерацією тепла грубних газів.
Сучасна мартенівська піч являє собою витягнуту в горизонтальному напрямку камеру, складену з вогнетривкої цегли. Робочий плавильний простір обмежений знизу подиною 12, зверху зводом 11, а з боків передньої 5 і задньої 10 стінками. Подина має форму ванни з укосами в напрямку до стінок печі. У передній стінці є завантажувальні вікна 4 для подачі шихти й флюсу, а в задній – отвір 9 для випуску готової сталі.
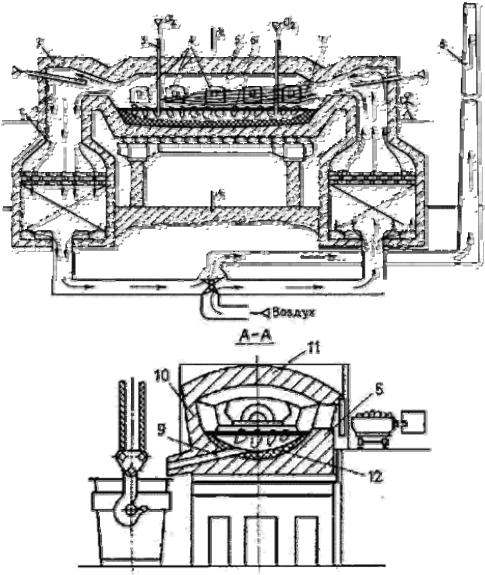
17
Рис. 2.2. Схема мартенівської печі
Характеристикою робочого простору є площа поду печі, яку підраховують на рівні порогів завантажувальних вікон. З обох торців плавильного простору розташовані головки печі 2, які служать для змішування палива з повітрям і подачі цієї суміші в плавильний простір. У якості палива використовують природний газ, мазут.
Для підігріву повітря й газу при роботі на низькокалорійному газі пекти має два регенератори 1.
Регенератор – камера, у якій розміщена насадка – вогнетривка цегла, выложенный у клітку, призначений для нагрівання повітря й газів.
гази, що відходять від печі, мають температуру 1500…1600 0C. Потрапляючи в регенератор, гази нагрівають насадку до температури 1250 0C. Через один з регенераторів подають повітря, яке проходячи через насадку нагрівається до 1200 0C і надходить у головку печі, де змішується з паливом, на виході з головки утворюється факел 7, спрямований на шихту 6.
гази, що відходять, проходять через протилежну головку (ліву), очисні пристрої (шлаковики), службовці для відділення від газу часток шлаків і пили й направляються в другий регенератор.
Охолоджені гази залишають пекти через димар 8.
18
Після охолодження насадки правого регенератора перемикають клапани, і потік газів у печі змінює напрямок.
Температура факела полум'я досягає 1800 0C. Факел нагріває робочий простір печі й шихту. Факел сприяє окисненню домішок шихти при плавці.
Тривалість плавки становить 3…6 годин, для великих печей – до 12 годин. Готову плавку випускають через отвір, розташоване в задній стінці на нижньому рівні поду. Отвір щільний забивають малоспекающимися вогнетривкими матеріалами, які при випуску плавки вибивають. Печі працюють безупинно, до зупинки на капітальний ремонт –
400…600 плавок.
Залежно від состава шихти, використовуваної при плавці, розрізняють різновиди мартенівського процесу:
–скрап-процес, при якім шихта складається зі сталевого лома (скрапу) і 25…45 % чушкового передільного чавуну, процес застосовують на заводах, де немає доменних печей, але багато металобрухту.
–скрапррудний процес, при якім шихта складається з рідкого чавуну (55…75 %), скрапу й залізної руди, процес застосовують на металургійних заводах доменні печі, що мають.
Футеровка печі може бути основний і кислої. Якщо в процесі плавки стали, у шлаках переважають основні оксиди, то процес називають основним мартенівським процесом, а якщо кислі – кислим.
Найбільша кількість стали, роблять скрапррудним процесом у мартенівських печах з основний футеровкой.
У піч завантажують залізну руду й вапняк, а після підігріву подають скрап. Після розігріву скрапу в піч заливають рідкий чавун. У період плавлення за рахунок оксидів руди й скрапу інтенсивно окисняться домішки чавуну: кремній, фосфор, марганець і, частково, вуглець. Оксиди утворюють шлаки з високим змістом оксидів заліза й марганцю (залізистий шлаки). Після цього проводять період «кипіння» ванни: у піч завантажують залізну руду й продувають ванну подаваним по трубах 3 киснем. У цей час відключають подачу в піч палива й повітря й видаляють шлаки.
Для видалення сірки наводять новий шлаки, подаючи на дзеркало металу вапно з додаванням бокситу для зменшення в'язкості шлаків. Зміст Cao у шлаках зростає, а Feo зменшується.
У період «кипіння» вуглець інтенсивно окисниться, тому шихта повинна містити надлишок вуглецю. На даному етапі метал доводить до заданого хімічного складу, з нього віддаляються гази й неметалічні включення.
Потім проводять розкислення металу у два етапи. Спочатку розкислення йде шляхом окиснення вуглецю металу, при одночасній подачі у ванну раскислителей – феромарганцю, феросиліцію, алюмінію. Остаточне розкислення алюмінієм і феросиліцієм здійснюється в ковші, при випуску стали з печі. Після відбору контрольних проб сталь випускають у ківш.
В основних мартенівських печах виплавляють сталі углеродистые конструкційні, низько- і среднелегированные (марганцовистые, хромисті), крім високолегованих сталей і сплавів, які одержують у плавильних електропечах.
У кислих мартенівських печах виплавляють якісні сталі. Застосовують шихту з низьким змістом сірки й фосфору.
Стали містять менше водню й кисню, неметалічних включень. Отже, кисла сталь має більш високі механічні властивості, особливо ударну в'язкість і пластичність, її використовують для особливо відповідальних деталей: колінчатих валів великих двигунів, роторів потужних турбін, шарикопідшипників.
Основними техніко-економічними показниками виробництва стали в мартенівських печах є:

19
•продуктивність печі – знімання стали з 1м2 площі поду в добу (т/м2 у добу),
усередньому становить 10 т/м2; р
•витрата палива на 1т виплавлюваній сталі, у середньому становить 80 кг/т.
Зукрупненням печей збільшується їхня економічна ефективність.
Виробництво стали в кисневих конвертерах.
Киснево-конвертерний процес – виплавка сталі з рідкого чавуну в конвертері з основний футеровкой і продувкою киснем через водоохлаждаемую фурму.
Перші досвіди в 1933-1934 – Мозковий.
У промислових масштабах – в 1952-1953 на заводах у Линце й Донавице (Австрія) – одержав назву ЛД - процес. У цей час спосіб є основним у масовім виробництві стали.
Кисневий конвертер – посудина грушоподібної форми зі сталевого аркуша, футерованный основною цеглою.
Місткість конвертера – 130…350 т рідкого чавуну. У процесі роботи конвертер може повертатися на 360 0 для завантаження скрапу, заливання чавуну, зливу стали й шлаків.
Шихтовими матеріалами киснево-конвертерного процесу є рідкий передільний чавун, сталевий лом (не більш 30%), вапно для наведення шлаків, залізна руда, а також боксит /і плавиковий шпат / для розрідження шлаків.
Послідовність технологічних операцій при виплавці стали в кисневих конвертерах представлена на Рис. 2.3.
Рис. 2.3. Послідовність технологічних операцій при виплавці стали в кисневих конвертерах
Після чергової плавки стали випускний отвір зашпаровують вогнетривкою масою й оглядають футеровку, ремонтують.
Перед плавкою конвертер нахиляють, за допомогою завалочних машин завантажують скрап мал. (2.3.а), заливають чавун при температурі 1250…1400 0C (мал. 2.3.б).
20
Після цього конвертер повертають у робоче положення (мал. 2.3.в), усередину вводять охолоджувану фурму й через не¨ подають кисень під тиском 0,9…1,4 МПа. Одночасно з початком продувки завантажують вапно, боксит, залізну руду. Кисень проникає в метал, викликає його циркуляцію в конвертері й перемішування зі шлаками. Під фурмою розвивається температура 2400 0C. У зоні контакту кисневого струменя з металом окисниться залізо. Оксид заліза розчиняється в шлаках і металі, збагачуючи метал киснем. Розчинений кисень окиснить кремній, марганець, вуглець у металі, і їх зміст падає. Відбувається розігрів металу теплотою, що виділяється при окисненні.
Фосфор віддаляється на початку продувки ванни киснем, коли її температура невисока (зміст фосфору в чавуні не повинне перевищувати 0,15 %). При підвищеному вмісті фосфору для його видалення необхідно зливати шлаки й наводити новий, що знижує продуктивність конвертера.
Сірка віддаляється протягом усієї плавки (зміст сірки в чавуні повинне бути до 0,07
%).
Подачу кисню закінчують, коли зміст вуглецю в металі відповідає заданому. Після цього конвертер повертають і випускають сталь у ківш (мал. 2.3.г), де раскисляют осаджуючим методом феромарганцем, феросиліцієм і алюмінієм, потім зливають шлаки
(мал. 2.3.д).
У кисневих конвертерах виплавляють сталі з різним змістом вуглецю, що киплять і спокійні, а також низьколеговані сталі. Легуючі елементи в розплавленому виді вводять у ківш перед випуском у нього стали.
Плавка в конвертерах місткістю 130…300 т закінчується через 25…30 хвилин.