
- •1.1. Сучасне металургійне виробництво і його продукція
- •1.2. Матеріали для виробництва металів і сплавів
- •1.3. Виробництво чавуну.
- •1.4. Виплавка чавуну.
- •1.5. Продукти доменної плавки
- •ЛЕКЦІЯ 2
- •2.1. Процеси прямого одержання заліза з руд
- •2.2. Одержання губчатого заліза в шахтних печах.
- •2.3. Відновлення заліза в киплячому шарі.
- •2.4. Одержання губчатого заліза в капсулахатиглях.
- •2.5. Виробництво сталі
- •ЛЕКЦІЯ 3
- •3.1. Виробництво сталі
- •3.2. Розливання сталі
- •3.3. Способи підвищення якості стали
- •3.4. Виробництво кольорових металів>
- •ЛЕКЦІЯ 4
- •4.1. Зварювальне виробництво. Зварювання плавленням
- •4.2. Зварювання плавленням
- •4.3. Плазмове зварювання
- •4.4. Електрошлакове зварювання.
- •4.5. Променеві способи зварювання
- •4.6. Газове зварювання
- •ЛЕКЦІЯ 5
- •5.1. Зварювання тиском
- •5.2. Контактне зварювання
- •5.3. Дифузійне зварювання
- •5.4. Зварювання тертям
- •5.5. Зварювання вибухом
- •5.6. Тип звареного з'єднання
- •5.7. Спеціальні термічні процеси у зварювальнім виробництві
- •5.8. Напилювання
- •5.9. Пайка
- •ЛЕКЦІЯ 6
- •6.1. Заготівельне виробництво
- •6.2. Загальні принципи вибору заготовки
- •6.3. Основні фактори, що впливають на вибір способу одержання заготовки.
- •6.4. Ливарне виробництво
- •6.5. Класифікація литих заготовок.
- •6.6. Ливарні сплави
- •6.7. Ливарні властивості сплавів
- •6.8. Ливарні сплави
- •ЛЕКЦІЯ 7
- •7.1. Виготовлення виливків у піщаних формах
- •7.2. Модельний комплект
- •7.3. Виготовлення ливарних форм
- •7.4. Формування в кесонах.
- •7.5. Машинне формування
- •7.6. Вакуумне формування.
- •7.7. Виготовлення стрижнів
- •ЛЕКЦІЯ 8
- •8.1. Виготовлення виливків у піщаних формах
- •8.2. Спеціальні способи лиття
- •8.3. Виготовлення виливків відцентровим литтям
- •ЛЕКЦІЯ 9
- •9.1. Спеціальні способи лиття
- •9.2. Виготовлення виливків електрошлаковим литтям
- •9.3. Виготовлення виливків безперервним литтям
- •9.4. Особливості виготовлення виливків з різних сплавів
- •9.5. Сталеві виливки
- •9.6. Алюмінієві сплави
- •9.7. Мідні сплави
- •9.8. Титанові сплави
- •9.9. Дефекти виливків і їх виправлення
- •9.10. Методи виявлення дефектів
- •9.11. Методи виправлення дефектів
- •9.12. Техніка безпеки й охорона навколишнього середовища в ливарнім виробництві
- •ЛЕКЦІЯ 10
- •10.1. Технологічність конструкцій литих форм
- •10.2. Основи конструювання литих заготовок
- •10.3. Виливка, виготовлені литтям у піщані форми
- •10.4. Основні положення до вибору способу лиття
- •ЛЕКЦІЯ 11
- •11.1. Класифікація процесів обробки тиском
- •11.2. Схеми напруженого й деформованого станів
- •11.3. Закономірності обробки тиском. Характеристики деформацій
- •11.4. Технологічні властивості
- •11.5. Технологічні випробування
- •ЛЕКЦІЯ 12
- •12.1. Прокат і його виробництво
- •12.2. Способи прокатки
- •12.3. Технологічний процес прокатки
- •12.4. Виправлення прокату
- •12.5. Разрезка й заготівельна обробка прокату
- •ЛЕКЦІЯ 13
- •13.1. Продукція прокатного виробництва
- •13.2. Пресування
- •13.3. Волочіння
- •ЛЕКЦІЯ 14
- •14.1. Кування
- •14.2. Операції кування
- •14.3. Попередні операції
- •14.4. Основні операції
- •14.5. Устаткування для кування
- •14.6. Конструювання кутих заготовок
- •ЛЕКЦІЯ 15
- •15.1. Гаряче об'ємне штампування
- •15.2. Формоутворення при гарячім об'ємнім штампуванні
- •15.3. Креслення кування
- •15.4. Технологічний процес гарячого об'ємного штампування
- •ЛЕКЦІЯ 16
- •16.1. Гаряче об'ємне штампування на молотах
- •16.2. Геометрична точність кувань, отриманих на молотах
- •16.3. Гаряче об'ємне штампування на пресах
- •16.5. Ротаційні способи виготовлення кувань
- •16.6. Штампування рідкого металу
- •ЛЕКЦІЯ 17
- •17.1. Холодне штампування
- •17.2. Об'ємне холодне штампування
- •17.3. Листове штампування
- •17.4. Операції листового штампування
- •ЛЕКЦІЯ 18
- •18.1. Листове штампування
- •18.2. Високошвидкісні методи штампування
- •18.3. Формоутворення заготовок з порошкових матеріалів
- •ЛЕКЦІЯ 19
- •19.1. Загальна характеристика розмірної обробки
- •19.2. Режими різання, шорсткість поверхні
- •19.3. Верстати для обробки різанням
- •19.4. Технологічні можливості способів різання
- •19.5. Свердління
- •19.6. Протягання
- •ЛЕКЦІЯ 20
- •20.1. Фрезерування
- •20.2. Шліфування
- •20.3. Технологічні методи оздоблювальної (фінішної) обробки поверхонь деталей машин
- •20.4. Хонингование
- •20.5. Суперфінішування
- •20.6. Полірування
- •ЛЕКЦІЯ 21
- •21.1. Характеристика електрофізичних і електрохімічних методів обробки
- •21.2. Електроерозійні методи обробки
- •21.3. Електроіскрова обробка
- •21.4. Электроимпульсная обробка
- •21.5. Електрохімічна обробка
- •21.6. Електрохімічна розмірна обробка
- •21.7. Комбіновані методи обробки
- •21.9. Променеві методи обробки
- •21.10. Плазмова обробка
- •21.11. Плазмове напилювання.
- •ЛІТЕРАТУРА
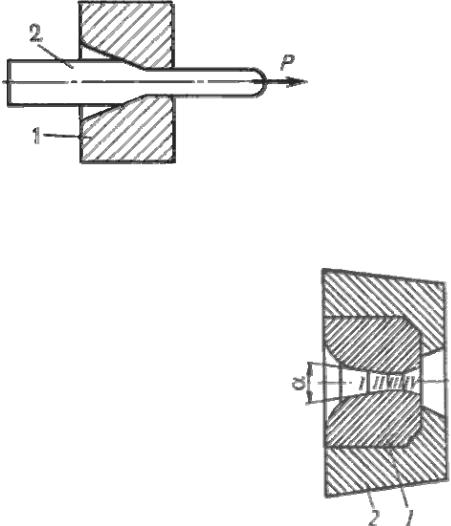
96
Недоліки процесу :
•підвищена витрата металу на одиницю виробу через втрати у вигляді пресзалишку;
•поява в деяких випадках помітної нерівномірності механічних властивостей по довжині й поперечному перерізу виробу;
•висока вартість і низька стійкість пресового інструмента;
•висока енергоємність.
13.3.Волочіння
Сутність процесу волочіння полягає в протяганні заготовок через сужающееся отвір (фильеру) в інструменті, називаному волокой. Конфігурація отвору визначає форму одержуваного профілю. Схема волочіння представлена на мал.13.7.
Мал.13.7. Схема волочіння
Волочінням одержують дріт діаметром 0,002…4 мм, прутки й профілі фасонного перетину, тонкостінні труби, у тому числі й капілярні. Волочіння застосовують також для калібрування перетину й підвищення якості поверхні оброблюваних виробів. Волочіння частіше виконують при кімнатній температурі, коли пластичну деформацію супроводжує наклеп, це використовують для підвищення механічних характеристик металу, наприклад, межа міцності зростає в 1,5… 2 рази.
Вихідним матеріалом може бути гарячекатаний пруток, сортовий прокат, дріт, труби. Волочінням обробляють сталі різного хімічного складу, кольорові метали й сплави, у тому числі й дорогоцінні.
Основний інструмент при волочінні – волоки різної конструкції. Волока працює в складних умовах: велика напруга сполучається зі зношуванням при протяганні, тому їх виготовляють із твердих сплавів. Для одержання особливо точних профілів волоки виготовляють із алмаза. Конструкція інструмента представлена на мал. 13.8.
Мал.13.8. Загальний вид волоки
Волока 1 закріплюється в обоймі 2. Волоки мають складну конфігурацію, її складовими частинами є: забірна частина I, що включає вхідний конус і мастильну частину; деформуюча частина II з кутом у вершині (6…18 0 – для прутків, 10…24 0 – для труб); циліндричний пасок, що калібрує, III довжиною 0,4…1 мм; вихідний конус IV.
97
Технологічний процес волочіння включає операції:
•попередній отжиг заготовок для одержання дрібнозернистої структури металу й підвищення його пластичності;
•травлення заготовок у підігрітому розчині сірчаної кислоти для видалення окалини з наступним промиванням, після видалення окалини на поверхню наносять подсмазочный шар шляхом омеднения, фосфотирования, вапнування, до шару добре прилипає змащення й коефіцієнт тертя значно знижується;
•волочіння, заготовку послідовно простягають через ряд поступово зменшуваних отворів;
•отжиг для усунення наклепу: після 70…85 % обтиснення для сталі й 99 % обтиснення для кольорових металів ;
•обробка готової продукції (обрізка кінців, виправлення, різання на мірні довжини й ін.)
Технологічний процес волочіння здійснюється на спеціальних волочильних станах. Залежно від типу тягнучого пристрою розрізняють стани: із прямолінійним рухом металу, що простягається (ланцюговий, рейковий); з намотуванням оброблюваного металу на барабан (барабанний). Стани барабанного типу звичайно застосовуються для одержання дроту. Число барабанів може доходити до двадцяти. Швидкість волочіння досягає 50 м/с.
Процес волочіння характеризується параметрами: коефіцієнтом витяжки й ступенем деформації.
Коефіцієнт витяжки визначається відношенням кінцевої й початкової довжини або початкової й кінцевої площі поперечного переріза:
λ = l1/lo = Fo/F1
Ступінь деформації визначається по формулі:
ε = (Fo – F1)/Fo x 100%
Звичайно за один прохід коефіцієнт витяжки λ не перевищує 1,3, а ступінь деформації ε – 30 %. При необхідності одержати більшу величину деформації роблять багаторазове волочіння.