
- •Оглавление
- •Предисловие
- •Глава 1. Общие вопросы заточки режущих инструментов
- •1.3 Заточные станки
- •1.4 Вопросы для контроля
- •Глава 2. Исследование конструкций резцов
- •2.1 Назначение, типы и конструктивные особенности
- •2.2 Конструктивные элементы резца
- •2.3 Геометрические параметры резца
- •2.4. Износ, критерий затупления и число переточек резцов
- •2.6 Вопросы для контроля
- •Глава 3. Исследование конструкций спиральных свёрл
- •3.1 Назначение, типы и конструктивные особенности
- •3.2 Методы заточки спиральных сверл
- •3.4 Вопросы для контроля
- •Глава 4. Исследование конструкций зенкеров
- •4.1 Назначение, типы и конструктивные особенности
- •4.2 Износ и затачивание зенкеров
- •4.4 Вопросы для контроля
- •5.1 Назначение, типы и конструктивные особенности
- •5.2 Выбор основных параметров
- •5.3 Износ и затачивание разверток
- •5.5 Вопросы для контроля
- •Глава 6. Исследование конструкций фрез
- •6.1 Назначение, типы и конструктивные особенности
- •6.2 Износ и восстановление фрез
- •6.3 Лабораторная работа «Конструкция фрез»
- •6.4 Вопросы для контроля
- •6.6 Вопросы для контроля
- •7.1 Исследование конструкций метчиков
- •7.1.1 Назначение, типы и конструктивные особенности
- •7.1.3 Вопросы для контроля
- •7.1.5 Вопросы для контроля
- •7.1.7 Вопросы для контроля
- •7.2 Исследование конструкций резьбонарезных головок
- •7.2.1. Назначение, типы и конструктивные особенности
- •7.2.3 Вопросы для контроля
- •Глава 8. Исследование конструкций зуборезных долбяков
- •8.1 Назначение, типы и конструктивные особенности
- •8.3 Вопросы для контроля
- •8.5 Вопросы для контроля
- •Глава 9. Исследование конструкций червячных фрез
- •9.1 Назначение, типы и конструктивные особенности
- •9.3 Вопросы для контроля
- •9.5 Вопросы для контроля
- •10.1 Назначение, типы и конструктивные особенности
- •10.3 Вопросы для контроля
- •10.5 Вопросы для контроля
- •10.7 Вопросы для контроля
- •10.9 Вопросы для контроля
- •10.11 Вопросы для контроля
- •11.1 Назначение, типы и конструктивные особенности
- •11.2 Алмазные сверла на связке «МонАлиТ»
- •11.3 Состояние рабочей поверхности сверла
- •11.4 Моделирование процесса алмазного сверления
- •11.5 Оценка режущей способности алмазных свёрл
- •11.7 Вопросы для контроля
- •12.1 Назначение и структура САПР
- •12.3 Вопросы для контроля
- •12.5 Вопросы для контроля
- •12.7 Вопросы для контроля
75
и фаской не только увеличивает прочность режущей кромки, но и облегчает
деформацию стружки и ее отвод.
Таблица 2.3 Рекомендуемые значения параметров заточки твердосплавных резцов в
зависимости от предела прочности обрабатываемой стали.
σВ, |
|
Размеры, мм |
|
|
Углы, º |
|
|
Н/мм2 |
|
|
|
|
|
|
|
A |
f |
h |
r |
γ |
α |
γф |
|
|
|
|
|
|
|
|
|
< 850 |
3,5 |
0,2…0,3 |
1…2 |
6 |
16 |
8 |
-3 |
|
|
|
|
|
|
|
|
700…1000 |
|
0,1…0,3 |
|
10 |
12 |
|
0…-5 |
|
4 |
|
2…3 |
|
|
10 |
|
До 1200 |
0,15…0,4 |
6 |
3…5 |
0…-5 |
|||
|
|
|
|
|
|||
До1300 |
|
|
|
|
8…10 |
|
|
|
|
|
|
|
|
|
|
Формы заточки передних поверхностей резцов с напайными пластинками твердого сплава приведены в таблице 2.2, рекомендуемые значения параметров заточки в таблице 2.3.
У резцов из твердых сплавов отрицательная фаска и двойной передний угол служат для усиления режущей кромки и облегчения процесса заточки и особенно доводки, так как всю остальную переднюю поверхность не доводят.
Лунка вдоль режущей кромки создает лучшие условия для завивания и ломания стружки.
2.4. Износ, критерий затупления и число переточек резцов
Износ и последующее затупление режущих инструментов происходят вследствие трения стружки и обрабатываемой детали по контактным площадкам передней и задней поверхностей, пластического деформирования материала инструмента под влиянием теплоты резания и давления стружки,
вырывания или выкрашивания мельчайших частиц. Выкрашивание режущей части инструмента рассматривается как его поломка [2].
Схема износа и переточки резцов приведена на рис. 2.5. В зависимости от материала детали, условий резания и материала инструмента отчетливо видимый износ происходит по задней (рис. 2.5, а) или передней (рис. 2.5, в)
поверхности, или по обеим одновременно (рис. 2.5, б). Наиболее часто

76
наблюдается износ по обеим поверхностям как у инструмента из стали, так и у инструмента твердого сплава. В этом случае к моменту затупления на задней поверхности образуется фаска износа h3 c углом αn=0º, а на передней поверхности – лунка глубиной hл и шириной В. Моменту полного затупления резца соответствует разрушение полочки f. Изнашивается вся режущая часть резца, участвующая в работе (главная режущая кромка, вершина и вспомогательная кромка), но с разной интенсивностью. В наибольшей степени изнашивается главная задняя поверхность около вершины резца.
I |
II |
III |
а) |
б) |
в) |
|
Рис. 2.5. Схемы износа и переточки резцов |
|
Экономически целесообразный допустимый износ резцов из быстрорежущей стали и оснащенных напайными пластинками твердого сплава приведен в таблицах 2.4 и 2.5.
Величина стачивания за одну переточку токарных резцов определяется исходя из:
–величин износа h3 и hл;
–геометрии режущей части;
–расположения пластины режущей части;
–дополнительной величины стачивания после удаления следов износа равной 0,1 – 0,2мм;
77
– схемы затачивания.
Таблица 2.4 Допустимый износ h3 резцов из быстрорежущих сталей, мм [6]
|
Обрабатываемый материал |
|
||
Тип резца |
Сталь, стальное литье, чугун ковкий при |
|
||
работе |
|
Серый чугун |
||
|
|
|||
|
с охлаждением |
|
без охлаждения |
|
Токарный проходной, |
|
|
|
|
подрезной или |
1,5 – 2,0 |
|
0,3 – 0,5 |
2,0 – 3,0 |
расточной |
|
|
|
|
Токарный прорезной и |
0,8 – 1,0 |
|
0,3 – 0,5 |
1,5 – 2,0 |
отрезной |
|
|||
|
|
|
|
|
|
|
|
|
|
Таблица 2.5 |
|
|
Допустимый износ h3 твердосплавных резцов, мм [6] |
||||||
|
|
|
Обрабатываемый материал |
|
|
||
|
|
Сталь, стальное литье, |
|
|
|
||
Тип резца |
Характер |
цветные металлы, |
Чугун |
|
|||
легированные сплавы |
|
|
|
||||
обработки |
|
|
|
||||
|
Марки |
|
|
Марки |
|
|
|
|
|
|
|
|
|
||
|
|
материала |
|
h3 |
материала |
h3 |
|
|
|
инструмента |
|
|
инструмента |
|
|
|
Черновая |
Т 15 К 6 |
|
1,5 – 2,0 |
ВК 6 |
0,8 – 1,0 |
|
Токарный |
Т 5 К 10 |
|
0,8 – 1,0 |
ВК 8 |
1,4 – 1,7 |
|
|
проходной, |
|
ВК 8 |
|
0,8 – 1,0 |
ВК 4 |
0,6 – 0,7 |
|
подрезной или |
|
Т 15 К 6 |
|
|
ВК 6 |
|
|
расточной |
Чистовая |
Т 5 К 10 |
|
0,4 – 0,6 |
ВК 8 |
0,6 – 0,7 |
|
|
|
ВК 8 |
|
|
ВК 4 |
|
|
Токарный |
– |
Т 5 К 10 |
|
0,8 – 1,0 |
ВК 6 |
0,8 – 1,0 |
|
прорезной и |
Т 15 К 6 |
|
ВК 8 |
|
|||
отрезной |
|
|
|
|
|
||
|
|
|
|
|
|
|
При переточке резца по передней поверхности (рис. 2.6) величина стачивания за одну переточку равна [1]:
h1 = hл + a (мм), (2.1)
где h1 – величина стачивания за одну переточку по передней поверхности в мм; hл – величина износа по передней поверхности в мм;
а – дополнительная величина на удаление следов износа в мм.
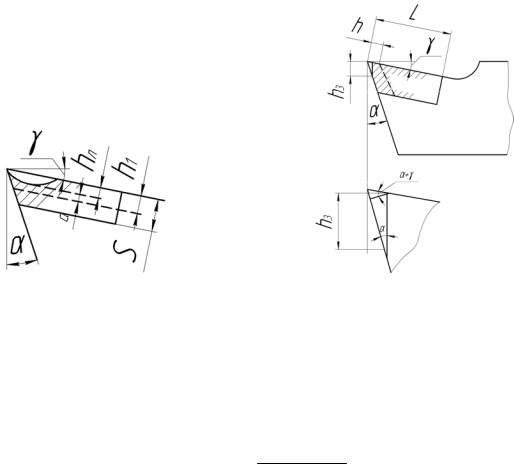
78
Рис. 2.6. Схема переточки резцов при износе |
Рис. 2.7. Схема переточки резцов при износе |
по передней поверхности |
по задней поверхности |
При переточке резца по задней поверхности (рис. 2.7) величины стачивания определяются зависимостью [1]:
sin
h h3 a, (2.2) cos
где h – величина стачивания за одну переточку по задней поверхности в мм; α и γ – задний и передний углы (°);
h3 – величина износа по задней поверхности в мм.
Более прогрессивной является схема переточек по передней и задней поверхностям.
Число возможных переточек резца лимитирует:
–при износе резца по передней поверхности – толщина пластинки «S»;
–при износе по задней поверхности – длина пластинки «l»;
–при износе по передней и задней поверхности - длина пластинки «l».
Количество переточек до полного износа резцов рассчитывается по
формулам:
n |
M |
или |
n1 |
|
M1 |
, |
(2.3) |
|
|
h1 |
|||||||
h |
||||||||
|
|
|
79
где М и М1 – предельные величины стачивания лимитирующих величин, для резцов принимают:
M 0,7l , а M1 0,5S ,
где n и n1 – количество переточек, соответственно, по задней и передней поверхностям.
2.5 Лабораторная работа
«Изучение формообразования и исследование геометрических параметров цельных и составных резцов»
Цель и задачи работы. Цель работы – изучение конструктивных особенностей цельных и составных резцов, их геометрических параметров и приемов их формообразования.
В задачи работы входят практическое освоение методов, средств формирования и контроля заданных геометрических параметров режущей части цельных и составных резцов, определение периодов стойкости и составление заключения о соответствии лабораторного образца заданным требованиям.
Необходимое оборудование, инструменты и приборы. Практическую часть лабораторной работы выполняют на универсально-заточном станке модели 3Д642Е или аналогичном из имеющихся в лаборатории.
В качестве объекта исследования используют проходные токарные резцы.
Для снижения трудоемкости механической обработки рекомендуется применять макет державки из легкообрабатываемого материала (алюминия,
дерева).
Формообразование основных элементов режущей части резца выполняют в двух или трех поворотных тисках.
Контроль полученных геометрических параметров режущей части выполняется с помощью настольного угломера для контроля углов резца в плане, настольного или инклинометрического угломера конструкции ВНИИ.
80
Методика выполнения работы
1.В соответствии с заданными условиями обработки и материала режущей части по табл. 2.1; 2.2; 2.3 выбирают форму заточки передней поверхности и геометрические параметры резца, а по табл. 2.4 и 2.5 величины допустимого износа.
2.Восстановление режущей способности у цельных и составных резцов при их затуплении производится затачиванием, которое обеспечивает также и формообразование режущей части инструментов. В зависимости от величины и характера износа по формулам (2.1; 2.2) рассчитывают величины стачивания за одну переточку, а затем по формуле (2.3) определяют количество переточек, допустимое прочностью головки резца. Для составных инструментов определяют предельные величины стачивания по размерам пластинок, которые выбираются по справочной литературе [6].
3.Для выполнения операций затачивания в зависимости от марки инструментального материала и конструктивных элементов на головке резца необходимо выбрать характеристику шлифовального круга и режимы затачивания (табл. 2.6).
4.Практическая часть работы выполняется на универсально-заточном станке.
После выбора и закрепления шлифовального круга на стол станка устанавливаются трехповоротные тиски (рис. 2.8) и через основание 1
закрепляются болтами в Т-образных пазах стола станка.
Нижняя поворотная часть имеет внутри вертикальную ось поворота относительно основания, а в верхней своей части – горизонтальную ось,
соединенную со средней частью. В средней поворотной части имеется еще и вертикальная ось, соединенная с поворотными тисками.
Для затачивания передней и задней поверхностей резца необходимо определять углы поворота отдельных частей приспособления (пользуясь шкалами) таким образом, чтобы после поворотов затачиваемые поверхности
(как бы уже готового резца) расположились бы в вертикальной плоскости параллельной плоскости вращения торца шлифовального круга.
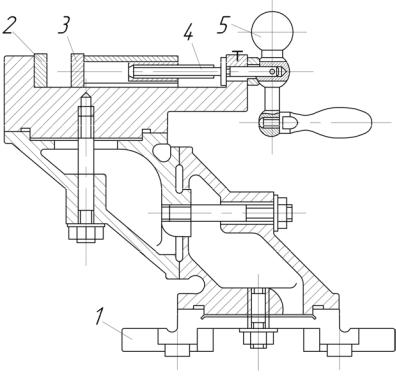
81
Рис. 2.8. Универсальные трехповоротные тиски:
1-основание; 2-неподвижная губка; 3-подвижная губка; 4-ходовой винт; 5-рукоятка
Для затачивания передней и задней поверхностей резца необходимо определять углы поворота отдельных частей приспособления (пользуясь шкалами) таким образом, чтобы после поворотов затачиваемые поверхности
(как бы уже готового резца) расположились бы в вертикальной плоскости параллельной плоскости вращения торца шлифовального круга.
Начальное положение отдельных частей тисков соответствует положению поворотных шкал на «0º». Настройка тисков для затачивания передней поверхности.
При заточке главной передней поверхности резца необходимо выдержать заданные по чертежу величины: главный передний угол γN, измеренный в сечении, нормальном к главной режущей кромке; главный угол в плане φ и
угол λ наклона главной режущей кромки.
Схемы настройки тисков при формообразовании передней поверхности показаны на рис. 2.9.
82
|
|
|
|
|
Рекомендуемые характеристики шлифовальных |
|
Таблица 2.6 |
|||||||||||||
|
|
|
|
|
|
|
|
|||||||||||||
|
|
|
|
|
|
кругов и режимы затачивания [5] |
|
|
|
|
|
|||||||||
|
|
|
Заточка предварительная |
|
|
|
|
Заточка |
|
|
|
Доводка |
|
|||||||
|
|
|
|
|
окончательная |
|
|
|
||||||||||||
|
|
|
|
|
|
|
|
|
|
|
|
|
|
|
|
|||||
Основныеданные |
Быстрорежущая |
Твердый сплав |
сплавТвердый, керамика, |
сверхтвердыематериалы |
|
|
|
сплавТвердый, керамика, сверхтвердыематериалы |
|
|
|
|
|
сплавТвердый, керамика, сверхтвердыематериалы |
||||||
удовлетворительнойс шлифуемостью: Р18, 5М6Р12,Ри др. |
|
пониженнойс |
шлифуемостью: Р9К5, 5М6Р3,Ф12РК5 и др. |
Быстрорежущаясталь |
|
|
|
|
|
|
||||||||||
|
удовлетворительнойс шлифуемостью: ВК8, 10К5Т6,ВКи др. |
пониженнойс шлифуемостью: ВК3, К14Т6,К15Т8 и др. |
|
|
|
|
|
|
||||||||||||
|
|
сталь |
|
|
|
|
|
|
|
|
|
|
|
|
|
|
|
|
||
|
|
|
|
|
|
|
|
|
|
|
|
|
|
|
Быстрорежущая сталь |
|
||||
|
|
|
|
|
|
|
|
|
|
|
|
|
|
|
|
|
|
|
||
Абразивный |
материал |
Электрокорунд белый 24А, 25А |
|
Электрокорунд |
хромистый 33А, монокорунд 44А, 45А |
Карбид кремния |
зеленый 63С, 64С |
Синтетический алмаз |
АС6, АС4 |
Эльбор ЛО |
|
Синтетический алмаз |
АС2 |
Эльбор ЛО |
Карбид кремния 63С |
|
Синтетический алмаз |
АСМ |
||
|
|
|
|
|
|
|
|
|
|
|
|
|
|
|
|
|
|
|
||
Зернистость |
40…25 |
|
40…25 |
40…25 |
40…25 |
125/100… |
100/80 |
100/80… |
80/63 |
80/63… |
50/40 |
50/40… |
40/28 |
6 – 5 |
|
40/28 – 28/20 |
||||
|
|
|
|
|
|
|
|
|
|
|
|
|
||||||||
|
|
|
|
|
|
|
|
|
|
|
|
|
|
|
|
|
|
|
||
Тв-ть |
СМ1… |
|
М3… |
СМ1… |
М2… |
|
– |
2С1…С керамическойдля( |
100%)связки |
– |
|
– |
|
М3… |
|
– |
– |
|||
Номер илиструктуры концентрация |
СМ2 |
|
СМ1 |
СМ2 |
М3 |
|
|
|
|
|
|
СМ1 |
|
|
|
|||||
|
|
|
|
|
|
|
|
|
|
|
|
|
|
|
||||||
|
|
6…7 |
|
7…8 |
5…6 |
6…7 |
100% |
|
|
|
100% |
50% |
5…6 |
|
– |
50% |
||||
|
|
|
|
|
|
|
|
|
|
|
|
|
|
|
|
|
|
|
||
Связка |
Керамическая |
Керамическая К |
Металлическая |
–1М01 |
БакелитоваяВ2 – керамическая01, |
10С |
БакелитоваяВ2 – |
01 |
БакелитоваяВ2 – |
01 |
БакелитоваяБ |
|
БакелитоваяВ2 – 01 |
БакелитоваяВ2 – 01 |
||||||
|
|
|
|
|
|
|
|
|
|
|
|
|
|
|
||||||
|
|
К8, 51б |
|
|
|
|
|
|
|
|
|
|
|
|
|
|
||||
|
|
|
|
|
|
|
|
|
|
|
|
|
|
|
|
|
|
|||
|
|
|
|
|
|
|
|
|
|
|
|
|
|
|
|
|
||||
Скор. |
ШК, м/с |
20…25 |
|
|
16…18 |
12…15 |
10…12 |
16…18 |
25…30 |
|
25…30 |
18…20 |
|
25…30 |
25…30 |
|||||
|
|
|
|
|
|
|
|
|
|
|
|
|
|
|
|
|||||
Скорость продольной |
подачи, м/мин |
3…6 |
|
|
3…6 |
5…8 |
5…8 |
1…2 |
1…2 |
|
1…2 |
0,1…0,3 |
|
0,1…0,3 |
0,1…0,3 |
|||||
|
|
|
|
|
|
|
|
|
|
|
|
|
|
|
|
|
|
|
|
|
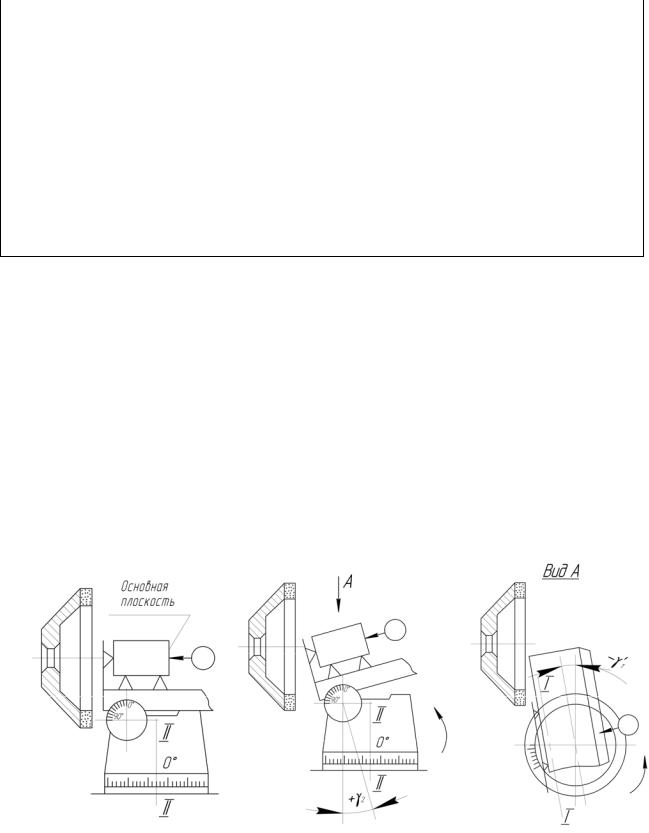
83
Подача на глубину шлифования, мм |
0,04…0,06 |
0,02…0,04 |
0,08…0,12 |
|
0,06…0,08 |
0,02…0,03 |
0,02…0,03 |
|
0,01…0,02 |
0,005…0,01 |
0,01…0,02 |
0,005…0,01 |
0,005…0,01 |
|
|
|
|
|
|
|
|
|
|
|
|
|
|
Охлаждение |
|
|
|
8 л/мин |
С охлаждением |
|
5 л/мин |
|
|
|
|
||
|
|
|
Без охлаждения |
|
|
Без |
|
|
|
|
|||
|
|
|
или с подачей |
|
охлаждения |
|
|
|
|
||||
|
С охлаждением |
СОЖ не менее |
|
или с подачей |
|
Без охлаждения |
|
||||||
|
|
|
|
СОЖ не менее |
|
|
|
|
|||||
|
|
|
|
|
|
|
|
|
|
|
|||
|
|
|
|
|
|
|
|
|
|
|
|
|
|
Примечание. При работе периферией круга или при замене круга на керамической связке кругом на бакелитовой связке, а также при ручной заточке использовать круги твердостью на одну степень выше, а скорость круга увеличить на 25%.
Углы поворота тисков при обработке передней поверхности (углы γ2 и γ1')
[3]:
tg 2 |
tg sin tg cos , |
(2.4) |
||||||||
tg |
/ |
|
sin |
2 / |
ctg , |
(2.5) |
||||
1 |
|
|
/ |
|
|
|||||
|
|
|
|
cos |
|
|
||||
где |
|
|
|
|
|
|
|
|
|
|
|
|
|
tg / |
|
tg |
|
|
|
||
|
|
|
cos , |
|
(2.5) |
|||||
|
|
|
|
|
|
а) |
б) |
в) |
Рис. 2.9. Настройка тисков для заточки передней поверхности резца:
а – начальное положение; б – поворот на угол γ2; в – поворот на угол γ1'
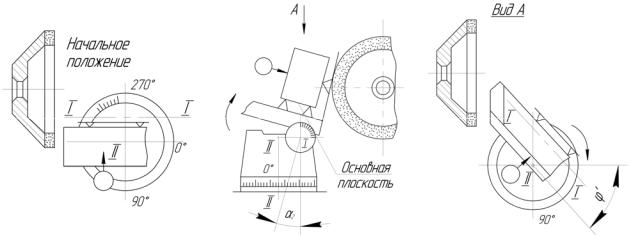
84
4.1.Настройка тисков для затачивания главной задней поверхности.
При заточке главной задней поверхности резца необходимо выдержать следующие геометрические параметры режущей части (заданные по чертежу):
главный задний угол αN измеренный в сечении, нормальном к режущей кромке,
главный угол в плане φ и угол наклона главной режущей кромки λ.
Схемы настройки тисков при формообразовании главной задней поверхности показаны на рис. 2.10.
Углы поворота элементов тисков при обработке главной задней поверхности (углы α2 и φ') [3]:
ctg 2 ctg sin tg cos , |
(2.7) |
|||
tg / |
tg cos / |
|
|
|
cos( / 2 ) . |
(2.8) |
|||
|
а) |
б) |
в) |
Рис. 2.10. Настройка тисков для заточки главной задней поверхности резца:
а– начальное положение; б – поворот на угол α2; в – поворот на угол φ'
4.2.Настройка тисков для вспомогательной задней поверхности.
При заточке вспомогательной задней поверхности резца необходимо выдержать следующие геометрические параметры режущей части (заданные по условию задания), вспомогательный угол в плане φ1, вспомогательный задний угол α1N измеренный в сечении нормальном к вспомогательной режущей кромке.
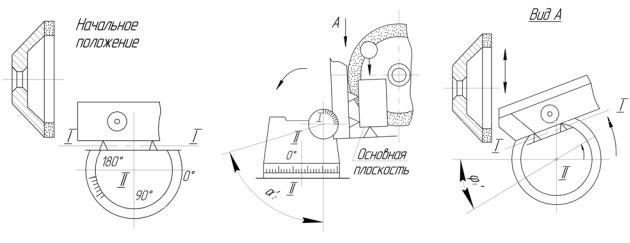
85
Углы поворота частей тисков при формообразовании вспомогательной задней поверхности (углы α2' и φ1') [3]:
ctg |
/ |
ctg |
1 |
sin tg |
cos |
, |
(2.9) |
|||||||||||
|
2 |
|
|
|
|
|
|
|
1 |
|
|
1 |
1 |
|
|
|||
|
|
/ |
|
|
|
tg |
1 |
cos / |
|
|
|
|
|
|||||
|
|
tg 1 |
|
|
|
|
|
|
|
|
1 |
|
, |
|
(2.10) |
|||
|
|
|
cos( |
/ |
|
/ |
) |
|
||||||||||
|
|
|
|
|
|
2 |
|
|
|
|
||||||||
|
|
|
|
|
|
|
|
|
1 |
|
|
|
|
|
|
|
|
|
где |
|
|
|
|
|
|
|
|
|
|
|
|
|
|
|
|
|
|
|
|
|
tg 1/ |
|
|
tg 1 |
|
, |
|
|
|
|
(2.11) |
|||||
|
|
|
|
cos |
|
|
|
|
||||||||||
|
|
|
|
|
|
|
|
|
|
|
|
|
|
|||||
|
|
|
|
|
|
|
|
|
|
|
1 |
|
|
|
|
|
|
|
tg 1 tg sin 1 tg cos 1 , |
(2.12) |
Схемы настройки тисков при обработке вспомогательной задней поверхности показаны на рис. 2.11.
а) |
б) |
в) |
Рис. 2.11. Настройка тисков для заточки вспомогательной задней поверхности резца:
а– начальное положение; б – поворот на угол α2'; в – поворот на угол φ1'
5.После наладки приспособления и установки лабораторного образца инструмента производят поэтапно затачивание передней, главной и вспомогательной задней поверхностей режущей части резца в соответствии с приведенными выше общими рекомендациям.
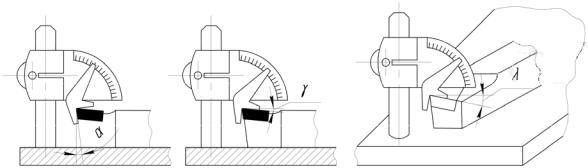
86
При выполнении операций затачивания скорость круга не должна превышать 20м/с; поперечная подача Sпоп = 0,02…0,5мм/дв.ход; продольная подача Sпрод = 2…5м/мин.
6. С целью исследования точности формообразования геометрических параметров режущей части резца для подтверждения выполненных расчетов по настройке приспособления определяют значение переднего угла (γN), главного
(φ) и вспомогательного (φ1) углов в плане, угла наклона главной режущей кромки (λ), главного (αN) и вспомогательного(α1N) задних углов.
Измерение этих углов производится в направлении и в плоскости указанных в определениях этих углов (см. 2.3).
Измерение переднего, задних и угла наклона главной режущей кромки может быть произведено с помощью угломера на стойке (рис. 2.12).
а) |
б) |
в) |
Рис. 2.12. Настольный угломер для измерения углов:
а – заднего α; б – переднего γ; в – наклона режущей кромки λ
Измерение переднего и заднего углов и угла наклона главной режущей кромки может быть произведено также с помощью инклинометрического угломера, действующего на принципе отвеса (рис. 2.13). При измерении инклинометром необходимо следить, чтобы в момент измерения измеряющий прибор занимал положение в вертикальной плоскости и чтобы плоскость измерения была, по возможности, перпендикулярна проекции режущей кромки на основную плоскость. Точное измерение, в силу наличия указанных погрешностей, невозможно. При измерении угла λ наклона главной режущей кромки инклинометрический угломер должен быть установлен также в
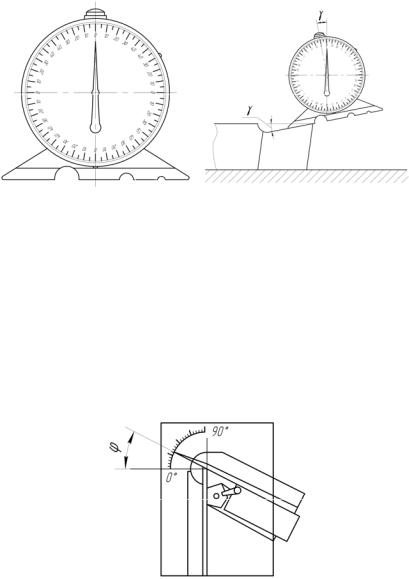
87
вертикальной плоскости, на передней поверхности резца, вдоль (параллельно)
главной режущей кромки.
Рис. 2.13. Инклинометрический угломер
Для измерения резцы устанавливаются на плите, точно установленной в горизонтальной плоскости, с помощью того же инклинометра.
В процессе измерения, при наложении ребра линейки на соответствующую поверхность резца, нажимают на тормозную кнопку угломера и, после окончания колебаний стрелки, фиксируют отчет углов,
освобождая при этом тормозную кнопку.
Рис. 2.14. Схема контроля углов φ и φ1 у резцов
Измерение углов в плане φ и φ1 на этих приборах затруднено тем, что главная и вспомогательная режущие кромки не лежат в плоскости параллельной основной плоскости за счет наличия углов λ и γ. Эти углы должны быть измерены в соответствии с определениями по стандарту, как углы между проекциями режущих кромок на плоскость параллельную основной плоскости и направлением подачи. Для этих целей используют специальный угломер. Схема контроля углов φ и φ1 показана на рис. 2.14.
Прибор состоит из плиты и двух угольников, один из которых подвижный и имеет указательную стрелку перемещающуюся по