
- •Оглавление
- •Предисловие
- •Глава 1. Общие вопросы заточки режущих инструментов
- •1.3 Заточные станки
- •1.4 Вопросы для контроля
- •Глава 2. Исследование конструкций резцов
- •2.1 Назначение, типы и конструктивные особенности
- •2.2 Конструктивные элементы резца
- •2.3 Геометрические параметры резца
- •2.4. Износ, критерий затупления и число переточек резцов
- •2.6 Вопросы для контроля
- •Глава 3. Исследование конструкций спиральных свёрл
- •3.1 Назначение, типы и конструктивные особенности
- •3.2 Методы заточки спиральных сверл
- •3.4 Вопросы для контроля
- •Глава 4. Исследование конструкций зенкеров
- •4.1 Назначение, типы и конструктивные особенности
- •4.2 Износ и затачивание зенкеров
- •4.4 Вопросы для контроля
- •5.1 Назначение, типы и конструктивные особенности
- •5.2 Выбор основных параметров
- •5.3 Износ и затачивание разверток
- •5.5 Вопросы для контроля
- •Глава 6. Исследование конструкций фрез
- •6.1 Назначение, типы и конструктивные особенности
- •6.2 Износ и восстановление фрез
- •6.3 Лабораторная работа «Конструкция фрез»
- •6.4 Вопросы для контроля
- •6.6 Вопросы для контроля
- •7.1 Исследование конструкций метчиков
- •7.1.1 Назначение, типы и конструктивные особенности
- •7.1.3 Вопросы для контроля
- •7.1.5 Вопросы для контроля
- •7.1.7 Вопросы для контроля
- •7.2 Исследование конструкций резьбонарезных головок
- •7.2.1. Назначение, типы и конструктивные особенности
- •7.2.3 Вопросы для контроля
- •Глава 8. Исследование конструкций зуборезных долбяков
- •8.1 Назначение, типы и конструктивные особенности
- •8.3 Вопросы для контроля
- •8.5 Вопросы для контроля
- •Глава 9. Исследование конструкций червячных фрез
- •9.1 Назначение, типы и конструктивные особенности
- •9.3 Вопросы для контроля
- •9.5 Вопросы для контроля
- •10.1 Назначение, типы и конструктивные особенности
- •10.3 Вопросы для контроля
- •10.5 Вопросы для контроля
- •10.7 Вопросы для контроля
- •10.9 Вопросы для контроля
- •10.11 Вопросы для контроля
- •11.1 Назначение, типы и конструктивные особенности
- •11.2 Алмазные сверла на связке «МонАлиТ»
- •11.3 Состояние рабочей поверхности сверла
- •11.4 Моделирование процесса алмазного сверления
- •11.5 Оценка режущей способности алмазных свёрл
- •11.7 Вопросы для контроля
- •12.1 Назначение и структура САПР
- •12.3 Вопросы для контроля
- •12.5 Вопросы для контроля
- •12.7 Вопросы для контроля
11
Глава 1. Общие вопросы заточки режущих инструментов
1.1 Выбор характеристики шлифовального круга,
режимов заточки и места переточки инструмента на производстве
Повышение качества производимой продукции машиностроительного производства, автоматизация технологических процессов на базе станков с ЧПУ, применение новых высокотвердых и высокопрочных материалов при изготовлении деталей машин, повышенные требования к точности и производительности технологических процессов повысили требования к эксплуатационным свойствам режущих инструментов, которые в значительной степени определяются технологией шлифовально-заточных операций,
правильным выбором современного шлифовального и заточного оборудования.
При разработке технологических процессов заточки режущих инструментов необходимо учитывать особенности шлифования современных инструментальных материалов, производить правильный выбор характеристик шлифовальных кругов, средств и параметров режима их правки и балансировки с учетом предотвращения дефектов шлифования: прижогов и трещин, которые являются причинами повышенного износа инструмента, снижения его стойкости.
Заточка новых режущих инструментов производится на инструментальных заводах, выпускающих соответствующие виды режущих инструментов или в инструментальных цехах, производящих инструмент.
Переточка режущих инструментов после определенного срока эксплуатации осуществляется в цехах машиностроительных предприятий.
Возможные схемы перемещения инструмента представлены на рис.1.1.
Произведенный режущий инструмент на инструментальном заводе (блок 1)
перемещается на участок заточки (блок 2). Готовый заточной инструмент поступает на машиностроительное предприятие (блок 3) на инструментальный склад (блок 4) и после соответствующего контроля и настройки транспортируется в цеха основного производства (блок 5). По достижении критического износа из цехов основного производства изношенный инструмент
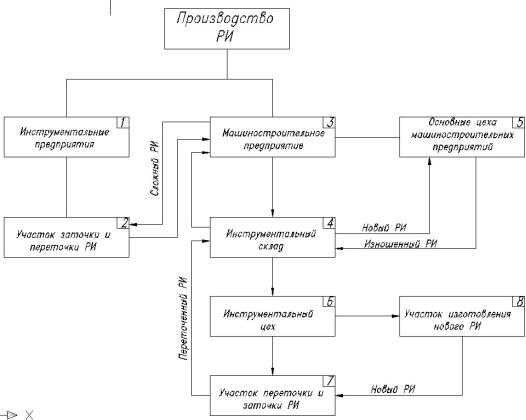
12
поступает на инструментальный склад (блок 4), а затем на участок переточки режущего инструмента (блок 7) инструментального цеха (блок 6). Из инструментального цеха переточенный инструмент транспортируется на инструментальный склад и после соответствующего контроля и настройки поступает в цеха основного производства (блок 5).
Рис. 1.1. Схема перемещения нового и переточенного режущего инструмента
Если машиностроительное предприятие не имеет соответствующего оборудования для переточки сложного режущего инструмента (шеверы,
косозубые долбяки и т.д.) то переточка инструмента осуществляется на инструментальном предприятии на участке заточки инструмента (блок 2).
В случае изготовления режущего инструмента в инструментальном цехе машиностроительного предприятия (блок 8) его заточка производится на участке переточки инструмента (блок 7), после чего он направляется на инструментальный склад с последующей транспортировкой в цехи основного производства (блок 5).
13
Функциональные свойства металлорежущего инструмента (качество и точность получаемых после обработки поверхностей, производительность инструмента и его стойкость) зависят в основном от способности материала режущей части инструмента сопротивляться изнашиванию и разрушению,
соответствия геометрических параметров инструмента условиям его работы, а
также качества и точности поверхностей, образующих режущие кромки инструмента [1].
Способность инструментального материала сопротивляться изнашиванию и разрушению зависит от правильности его выбора, зависящего от условий работы,
а также от правильности выполнения при изготовлении инструмента таких процессов, как термическая обработка, сварка, пайка, упрочнение и т.п.
Работоспособность твердосплавных инструментов с механическим креплением пластинок во многом зависит и от выбранного способа крепления режущих элементов.
Режущие кромки инструмента не только срезают припуск с обрабатываемой заготовки, но и образуют форму ее поверхности. Конфигурация режущих кромок получается в результате пересечения передних и задних поверхностей инструмента и зависит от пространственной формы последних.
Формообразование режущих кромок является одной из основных задач проектирования и изготовления режущих инструментов. Причем для сложных инструментов, имеющих фасонные и винтовые передние и задние поверхности, точное формообразование режущих кромок затруднительно.
Геометрические параметры, точность и качество режущей части инструмента, указанные на чертеже и в технических требованиях,
обеспечиваются при окончательном формообразовании выбором требуемого оборудования, оснастки, характеристик шлифовальных кругов, режимов обработки и установкой инструмента на станке в необходимое положение.
Заточкой обеспечивают не только режущие свойства инструмента, но и запроектированную форму режущей части. Изучение и практическое освоение
14
этого процесса является также эффективным средством для понимания основных принципов конструирования режущих инструментов.
Геометрические и точностные параметры у инструментов с многогранными твердосплавными пластинками обеспечиваются за счет формы, точности изготовления и установки пластинок в корпусе инструмента.
В процессе эксплуатации режущие свойства изношенных инструментов восстанавливаются заточкой. Инструменты с многогранными пластинками переточке не подвергаются. Воcстановление режущих свойств этих инструментов осуществляют поворотом или сменой многогранных пластинок.
Окончательное формообразование режущей части инструмента производят на универсально-заточных или специальных станках шлифовальными кругами.
Типы используемых станков приведены в описаниях ниже. Более подробно о моделях и технических характеристиках оборудования см. в [ 2].
Шлифовальные круги, используемые для окончательного формообразования режущих кромок инструментов, характеризуются следующими основными признаками: видом абразивного материала,
зернистостью, типом связки, твердостью, структурой, формой и размерами.
В качестве абразивного материала для заточки и доводки режущих инструментов из углеродистых, легированных и быстрорежущих сталей применяют материалы на основе кристаллической окиси алюминия А12О3:
электрокорунд нормальный (16А...12А), электрокорунд белый (25А...22А),
монокорунд (45А...43А), электрокорунд титанистый (37А), электрокорунд хромистый (34А, ЗЗА, 32А), электрокорунд хромотитанистый (92А, 91А).
Электрокорунд белый рационально применять для чистовой обработки.
Для предварительной черновой заточки твердосплавных инструментов с большими припусками применяют круги из карбида кремния SiC (карбид кремния зеленый – 64С).
Зернистость по ГОСТ 3647–80 определяет размер зерен. Классификация шлифовальных материалов и обозначение зернистости приведены в табл. 1.1.
15
Размеры шлифзерна и шлифпорошков выражаются в сотых долях миллиметра,
микропорошков и тонких микропорошков – в микрометрах.
В зависимости от процентного содержания зерен основной фракции номер зернистости абразивных кругов дополнительно обозначается буквенным индексом. Для заточки применяют круги с индексом П, содержащие 55–50%
зерен основной фракции, и Н, содержащие 45–40 %.
|
Таблица 1.1 |
|
Группа шлифовального |
Обозначение зернистости (номера зернистости) |
|
материала |
||
|
||
Шлифзерно |
200, 160, 125, 100, 80, 63, 50, 40, 32, 25, 20, 16 |
|
Шлифпорошки |
12,10,8,6,5,4,3 |
|
Микропорошки |
М63, М50, М40, М28, М20, М14 |
|
Тонкие микропорошки |
М10, М7, МЗ, М2, M1 |
Для заточки режущего инструмента преимущественно применяют круги следующих зернистостей: для предварительной заточки – 63, 50, 40, для окончательной – 25, 20, 16, для доводки– от12–10 иниже.
Связка является связующим (цементирующим) веществом для
соединения абразивных зерен в одно целое.
Для изготовления абразивных кругов применяют керамическую (К),
бакелитовую (Б), и вулканитовую (В) связки. Для заточки и доводки режущего инструмента главным образом применяют круги на керамической и
бакелитовой связках.
За твердость абразивного инструмента принимают сопротивление связки вырыванию абразивных зерен в процессе его работы. Степени твердости
абразивных инструментов, применяемых при заточке, приведены ниже.
Твердость инструмента |
Степень твердости |
Мягкий |
М1, М2, М3 |
Средне-мягкий |
СМ1, СМ2 |
Средний |
С1, С2 |
Средне-твердый |
СТ1, СТ2, СТ3 |
Твердый |
Т1, Т2 |

16
Структура характеризует соотношение объемов шлифовального материала,
связки и пор в абразивном инструменте. Абразивные круги имеют 12 номеров структуры и делятся на три группы: закрытые или плотные (1 – 4), средние (5 – 8),
и открытые (9–12). Структуры 5 – 7 рекомендуются для заточки инструмента,
изготовленного из стали, структуры 8 – 10 – из твердого сплава.
Формы и размеры абразивных кругов, рекомендуемые для заточки основных видов инструментов, по ГОСТ 2424–83, приведены в табл. 1.2.
Таблица 1.2
|
Круг |
Эскиз |
Размер круга, мм |
Основное |
|||
|
|
Диаметр |
Высота |
Диаметр |
|||
Тип |
Наименование |
назначение |
|||||
|
круга D |
Н |
отверстия d |
||||
|
|
|
|
||||
|
|
|
|
|
|
Для обработки |
|
|
|
|
100 |
50 |
20 |
задних |
|
|
|
|
поверхностей |
||||
|
Чашечный |
|
125 |
63 |
32;51 |
острозаточенных |
|
ЧЦ |
|
150 |
80 |
32;51 |
фрез, разверток, |
||
цилиндрический |
|
||||||
|
|
|
200 |
63 |
32;51 |
зенкеров; |
|
|
|
|
250 |
100 |
76;127;150 |
передних и задних |
|
|
|
|
поверхностей |
||||
|
|
|
|
|
|
||
|
|
|
|
|
|
резцов |
|
|
Чашечный |
|
100 |
25;40 |
20 |
|
|
ЧК |
|
125 |
40;45 |
32 |
То же |
||
конический |
|
||||||
|
|
150 |
40;50 |
32 |
|
||
|
|
|
|
||||
|
|
|
|
|
|
|
|
|
|
|
100 |
10 |
20 |
Для обработки |
|
Т, |
|
|
125 |
13 |
32 |
передних |
|
1Т, |
Тарельчатый |
|
150 |
16 |
32 |
поверхностей |
|
|
фрез, разверток, |
||||||
4Т |
|
|
100 |
10 |
20 |
||
|
|
метчиков, |
|||||
|
|
|
150 |
16 |
32 |
протяжек |
|
|
|
|
|
|
|
Для обработки |
|
|
С коническим |
|
100 |
6 |
20 |
передних |
|
3П |
|
125 |
8 |
32 |
поверхностей |
||
профилем |
|
инструментов с |
|||||
|
|
150 |
8 |
32 |
|||
|
|
|
винтовыми |
||||
|
|
|
|
|
|
канавками и др. |
|
|
|
|
|
|
|
|
|
|
|
|
150 |
25;32 |
32 |
Для заточки |
|
ПВ |
С выточкой |
|
200 |
40;63 |
76 |
||
|
сверл, резцов |
||||||
|
|
|
300 |
40;50;63 |
127 |
||
|
|
|
|
||||
|
|
|
|
|
|
|
|
|
|
|
|
|
|
Для заточки |
|
|
|
|
125 |
20 |
32 |
резцов, протяжек, |
|
ПП |
Прямого |
|
150 |
20;25 |
32 |
затылования |
|
|
метчиков, |
||||||
профиля |
|
175 |
25;32 |
32 |
|||
|
|
шлифования |
|||||
|
|
|
200 |
25;32;40 |
32 |
поверхностей |
|
|
|
|
|
|
|
долбяков и др. |
17
Выбор характеристик кругов приведен в табл. 1.3.
Таблица 1.3
|
Затачиваемые |
Материал |
|
Характеристика круга |
|
|||
|
|
|
|
|
|
|||
Инструмент |
|
Марка шли- |
|
Степень |
|
|||
поверхности |
инструмента |
|
|
|
||||
Тип |
фовального |
Зернистость |
Связка |
|||||
|
|
|
твердости |
|||||
|
|
|
|
материала |
|
|
|
|
|
Передние и |
Быстрорежущая |
ЧК |
16А– 12А |
63-40 |
С1-СМ2 |
К |
|
Резец |
сталь |
25А-22А |
||||||
|
|
|
|
|||||
задние |
|
|
|
|
|
|
||
|
Твердый сплав |
ЧЦ |
64С–62С |
40–25 |
МЗ-М2 |
К, Б |
||
|
|
|||||||
|
|
|
|
|
|
|
|
|
|
|
Быстрорежущая и |
|
16 А– 12А |
|
|
|
|
Сверло |
Задние |
инструментальная |
ПВ |
40-25 |
СМ1-СМ2 |
К |
||
25А–23А |
||||||||
|
|
стали |
|
|
|
|
||
|
|
|
|
|
|
|
||
|
|
|
|
|
|
|
|
|
Зенкер, |
|
Быстрорежущая и |
ЧК |
|
|
|
|
|
развертка, |
Задние |
инструментальная |
24А–23А |
40–25 |
СМ1-СМ2 |
К |
||
ЧЦ |
||||||||
фреза |
|
стали |
|
|
|
|
||
|
|
|
|
|
|
|||
|
|
|
|
|
|
|
|
|
Развертка, |
|
Быстрорежущая и |
|
|
|
|
|
|
фреза, |
|
4Т, |
16А–14А |
|
|
|
||
Передние |
инструментальная |
40-25 |
СМ1–СМ2 |
К |
||||
метчик, |
|
стали |
1T |
24А-23А |
|
|
|
|
протяжка |
|
|
|
|
|
|
||
|
|
|
|
|
|
|
||
Червячная |
Передние |
Быстрорежущая |
Т, |
16А–14А |
25 |
С1-СМ1 |
К |
|
фреза |
сталь |
1T |
24А-23А |
|||||
|
|
|
|
|||||
|
|
|
|
|
|
|
|
|
|
Задние |
Быстрорежущая и |
|
16А-14А |
|
|
|
|
Метчики |
легированная |
ПП |
25–16 |
С1-СМ2 |
К |
|||
(затылованные) |
24А–23А |
|||||||
|
|
стали |
|
|
|
|
|
При маркировке на поверхность абразивного круга несмываемой краской наносят: марку завода-изготовителя, абразивный материал, зернистость, индекс,
указывающий содержание зерен основной фракции, твердость круга, связку,
структуру, форму круга, наружный диаметр, высоту, диаметр посадочного отверстия, максимальную окружную скорость при работе круга. Например,
ЧА3 24А 25 Н СМ2 К5 ПП 90х16х20 35м/с.
Для чистовой заточки и доводки твердосплавных инструментов, а также заточки твердосплавных инструментов, имеющих малые припуски на заточку,
рекомендуется использовать алмазные круги.
Рекомендации по выбору форм алмазных кругов для заточки и доводки твердосплавных инструментов приведены в табл. 1.4.
Рекомендации по выбору зернистости и связки алмазных кругов в зависимости от требований к параметрам шероховатости обработанной поверхности при заточке твердосплавного инструмента даны в табл. 1.5.
18
Таблица 1.4
|
Форма круга |
|
|
Круг |
|
Область применения |
|
|
||||||
|
|
|
|
|
|
|
Заточка |
и |
|
доводка |
передней |
|
||
|
1А1 |
|
Плоский прямого профиля |
поверхности |
|
у резцов. |
Круглое |
|
||||||
|
|
наружное |
|
|
|
шлифование |
|
|||||||
|
|
|
|
|
|
|
|
|
|
|
||||
|
|
|
|
|
|
|
инструментов |
|
|
|
|
|||
|
А8 |
Плоский прямого профиля без корпуса |
Обработка |
цилиндрических |
и |
|
||||||||
|
плоских поверхностей |
|
|
|
||||||||||
|
6А2 |
|
Плоский с выточкой |
|
Заточка |
и |
доводка |
резцов |
на |
|
||||
|
|
|
|
|
|
|
специальных станках для заточки |
|
||||||
|
9А3 |
|
Плоский с двухсторонней выточкой |
|||||||||||
|
|
резцов |
|
|
|
|
|
|
|
|||||
|
|
|
|
|
|
|
Заточка и доводка передних и |
|
||||||
|
|
|
|
|
|
|
задних |
поверхностей |
резцов, |
|
||||
|
12А2 с углом 45˚ |
|
Чашечный конический с уклоном 45˚ |
задних |
поверхностей |
сверл, |
|
|||||||
|
|
зенкеров, |
разверток, |
концевых, |
|
|||||||||
|
|
|
|
|
|
|
цилиндрических, торцевых, фрез и |
|
||||||
|
|
|
|
|
|
|
т.п. |
|
|
|
|
|
|
|
|
12А2 с углом 20˚ |
|
Тарельчатый конический с углом 20˚ |
Заточка |
и |
|
доводка |
передней |
|
|||||
|
|
|
|
|
|
|
поверхности фрез, разверток, |
|
||||||
|
12R4 |
|
|
Тарельчатый |
|
|||||||||
|
|
|
|
зенкеров, протяжек и т.п. |
|
|
|
|||||||
|
|
|
|
|
|
|
Заточка и доводка передней и |
|
||||||
|
|
|
|
|
|
|
задней |
|
|
|
поверхности |
|
||
|
12V5 с углом 20˚ |
|
Тарельчатый с углом 20˚ |
|
многолезвийного инструмента |
с |
|
|||||||
|
|
|
винтовым зубом – концевых и |
|
||||||||||
|
|
|
|
|
|
|
|
|||||||
|
|
|
|
|
|
|
цилиндрических фрез, зенкеров и |
|
||||||
|
|
|
|
|
|
|
т.д. |
|
|
|
|
|
|
|
|
12D9 |
|
|
Тарельчатый |
|
Заточка и доводка червячных фрез |
|
|||||||
|
Круги на |
органической связке применяют 50 |
и 100%-ой концентрации, |
|
||||||||||
|
круги на металлической связке – 100%-ой концентрации. |
|
|
|
|
|
|
|
||||||
|
|
|
|
|
|
|
|
|
|
Таблица 1.5 |
||||
|
|
|
|
Параметр |
|
|
|
|
|
|
|
|
|
|
|
Обработка |
|
шероховатости |
|
Связка |
|
|
Зернистость |
||||||
|
|
|
|
Ra, мкм |
|
|
|
|
|
|
|
|
|
|
|
Заточка твердосплавных |
0,32–0,63 |
|
Металлическая М1, |
|
АС4, АС6, |
|
|
||||||
|
|
М5, МО13, МВ1 |
|
|
200/160 - 100/80 |
|
||||||||
|
|
|
|
|
|
|||||||||
|
пластинок |
|
0,16-0,32 |
|
Органическая Б1, |
|
АС2 160/125- |
|||||||
|
|
|
|
|
Б156, ТО2 |
|
|
|
63/50 |
|
|
|||
|
|
|
|
|
|
|
|
|
|
|
||||
|
Заточка твердосплавных |
0,63-1,25 |
|
Керамическая К1 |
|
АС4 250/200- |
||||||||
|
пластинок совместно с державкой |
|
|
125/100 |
|
|
||||||||
|
|
|
|
|
|
|
|
|
||||||
|
Образование стружколомающих |
0,08-0,16 |
|
Металлическая М1, |
|
|
АС6 |
|
|
|||||
|
лунок, порожков, канавок |
|
М5, МВ1 |
|
|
М60/40 – М14/10 |
||||||||
|
|
|
|
|
||||||||||
|
Доводка твердосплавных |
0,08-0,16 |
|
Органическая |
|
|
АС2 63/50 – |
|||||||
|
пластинок |
|
|
Б1, КБ |
|
|
АСМ 60/40 |
|
|
|||||
|
|
|
|
|
|
|
|
При маркировке на корпусе алмазного круга с наружным диаметром 60мм и более наносятся: товарный знак предприятия-изготовителя, обозначение круга
(форма и габаритные размеры), марка и зернистость алмазного порошка,
концентрация алмазов в алмазном слое, марка связки, номер круга по системе
19
нумерации предприятия-изготовителя. Например, ТЗАИ АЧК 125х10х3х32 АС2 100/63 Б1 100% 1200.
На корпусах кругов с наружным диаметром до 60мм проставляется только номер круга и товарный знак завода-изготовителя. Полностью маркируют эти круги на бирках.
Для чистовой заточки и доводки режущих инструментов из быстрорежущих и инструментальных сталей, кроме кругов из электрокорунда,
применяют эльборовые круги.
Для чистовой заточки и доводки инструментов из инструментальных сталей применяют круги из эльбора на керамической (К) и органической (Б1,
КБ, Б156) связках. Для доводки рекомендуется в основном применять круги на органической связке.
Форму кругов из эльбора выбирают по ГОСТ 17123–79Е.
Режимы резания при заточке и доводке выбирают с условием, что на обработанной поверхности не должно получаться прижогов, трещин,
микротрещин и других дефектов; скорость круга не должна превышать максимальной скорости, допускаемой механической прочностью абразивного круга; в результате обработки должны обеспечиваться заданные параметры шероховатости обработанных поверхностей и необходимое качество режущих лезвий.
|
|
|
|
|
Таблица 1.6 |
|
Материал |
|
Материал |
Скорость |
Продольная |
Поперечная |
|
режущей части |
Обработка |
круга, |
подача, |
подача, |
||
круга |
||||||
инструмента |
|
м/с |
м/мин |
мм/дв.ход |
||
|
|
|||||
Быстрорежущая и |
Заточка |
|
|
3-6 |
0,03 – 0,05 |
|
инструментальная |
|
Электрокорунд |
20 - 25 |
|
|
|
Доводка |
1-2,5 |
0,005-0,01 |
||||
стали |
|
|
||||
|
|
|
|
|
|
|
Твердый сплав |
Заточка |
Карбид |
11-18 |
2-5 |
0,02-0,04 |
|
ВК, ТК |
кремния |
|
|
|
||
1012 |
2-5 |
0,02-0,05 |
||||
|
Рекомендуемые режимы при заточке и доводке кругами из электрокорунда и карбида кремния приведены в табл. 1.6. Рекомендуемые режимы резания при заточке и доводке твердосплавного режущего
20
инструмента алмазными кругами приведены в табл. 1.7. Рекомендации по режимам заточки и доводки режущих инструментов кругами из эльбора приведены в табл. 1.8.
|
|
|
|
|
Таблица 1.7 |
|
|
|
Режимы резания |
|
|
Операция |
Связка круга |
Скорость |
Поперечная |
|
Продольная |
круга, |
подача, |
|
подача, |
||
|
|
|
|||
|
|
м/с |
мм/дв.ход |
|
м/мин |
|
|
|
|
|
|
Заточка по пластинке из |
Органическая |
25-30 16-22 |
0,01-0,02 0,05- |
|
1,0-2,0 2,0-3,0 |
твердого сплава |
Металлическая |
|
0,08 |
|
|
Заточка совместно с |
Керамическая |
25-40 |
0,03 - 0,05 |
|
0,5-1,5 |
державкой |
|
||||
|
|
|
|
|
|
Доводка |
Органическая |
25-30 |
0,005-0,01 |
|
0,5- 1,5 |
Шлифовальные круги крепят на специальных оправках. Для предохранения кругов от повреждений и для более равномерного зажима абразивные круги закрепляют между двумя картонными прокладками толщиной
1–2мм. При креплении кругов с металлическим корпусом прокладок не применяют. При установке шлифовального круга диаметром свыше 100мм оправка вместе со шлифовальным кругом должна быть отбалансирована грузами, расположенными в кольцевых канавках на торце фланца оправки. Для защиты работающего от травм, которые могут быть вызваны разрывом круга,
необходимо применять защитные устройства – кожухи, ограждающие круг.
Таблица 1.8
Связка |
Скорость круга, |
|
Подача |
|
продольная, |
|
поперечная, |
||
м/с |
|
|||
|
м/мин |
|
мм/дв.ход |
|
|
|
|
||
Органическая |
20-30 |
0,5-1,5 |
|
0,01 – 0,03 |
Керамическая |
35-40 |
1-2 |
|
0,03– 0,08 |
Правку шлифовальных кругов производят для придания кругу требуемой геометрической формы, для устранения биения и восстановления его режущей способности. Технология правки абразивных, алмазных и эльборовых кругов приведена в [1].
После выбора, закрепления и правки шлифовального круга, установки и настройки положения обрабатываемого инструмента в приспособлении,
установленном на столе станка, а также наладки станка включают станок и
21
производят пробное касание вращающимся кругом обрабатываемой поверхности зуба инструмента. При работе на универсально-заточных станках предварительно устанавливают упоры, ограничивающие зону продольного перемещения стола.
При обработке многолезвийного инструмента (разверток, метчиков, фрез и т.п.) осуществляют пробный проход всех зубьев инструмента с целью определения наиболее выступающего зуба, с которого и следует начинать обработку. Затем перемещают стол в поперечном направлении на величину выбранной поперечной подачи и обрабатывают все зубья инструмента. Каждый зуб обрабатывают при двойном возвратно-поступательном перемещении стола.
Следующую подачу на глубину резания осуществляют после полного оборота инструмента. На универсально-заточных станках съем припуска производят при продольных возвратно-поступательных перемещениях стола. Обработку заканчивают выхаживанием без поперечной подачи. Последовательность обработки зависит от вида обрабатываемого инструмента, типа станка, способа формообразования, конструкции приспособления и т.д. В каждом конкретном случае при выполнении лабораторной работы необходимо использовать рекомендации, приводимые в руководствах по эксплуатации применяемого оборудования. Контроль точности заданных геометрических параметров, формы и расположения режущих кромок инструментов производят различными измерительными приборами и инструментами, описанными ниже.
1.2 Вспомогательные инструменты для
шлифовально-заточных и доводочных операций
1.2.1 Установка и закрепление шлифовальных кругов
При установке и закреплении шлифовальных кругов на станках необ-
ходимо учитывать, что надевание круга на шпиндель со значительным усилием недопустимо. Отверстие круга должно быть на 0,5-0,8мм больше диаметра шпинделя или буртика фланца. Если отверстие в круге меньше, чем нужно, его растачивают; если отверстие в круге велико, то шпиндель или

22
буртик фланца обёртывают лентой из бумаги, тонкого картона или резины шириной 0,8-0,9 ширины круга. Для уменьшения отверстия круга на 2-4мм его обмазывают расплавленной серой, гипсом или заливают свинцом.
Рис.1.2 Типовые случаи установки и закрепления
шлифовальных кругов на планшайбах
На рисунке 1.2а показаны установка и способы закрепления шлифовального круга плоского прямого профиля. Круг устанавливают на фланец 1 и закрепляют вторым фланцем 2. Фланец 1 закрепляется на шпиндель 3 станка. Между торцевыми поверхностями круга и фланцами устанавливают кольцевые прокладки из картона или резины.
Установка и закрепление чашечного круга (рис. 1.2в) производятся аналогично. Установка и закрепление шлифовальных кругов кольцевого типа
(рис. 1.2б и г) на фланце производятся с заливкой зазора между кругом и фланцем серой.
Диаметр крепёжных фланцев должен быть равен примерно 1/2-1/3
диаметра круга. Только для кругов малых размеров можно допускать фланцы диаметром до 1/3 диаметра круга. С внутренней стороны фланцу должны иметь выточку и соприкасаться с кругом по кольцевой поверхности шириной от 1/8 до 1/16 диаметра фланца. Кольцевые прокладки между фланцами

23
должны иметь толщину от 0,5 до 1,5мм и наружный диаметр на 4-6мм больше диаметра фланцев, имеющих одинаковый диаметр.
После центрирования круга на шпинделе производится затяжка гайки или винта ключом или отвёрткой. Установка круга на шпиндель, имеющий радиальное биение более 0,03-0,05мм, не допускается.
1.2.2 Балансировка шлифовальных кругов
Перед установкой шлифовальных кругов на станки для выполнения шлифовально-заточных операций они должны подвергаться статической или динамической балансировке [3]. Статическую балансировку осуществляют на устройствах, которые отличаются формой направляющих: ножи, призмы,
цилиндрические валики или диски (рис. 1.3).
Рис. 1.3 Устройство для статической |
Рис. 1.4 Схема статической |
балансировки |
балансировки шлифовального крута |
шлифовальных кругов |
|
Её проводят так: шлифовальный круг 1 (рисунок 1.4) предварительно закрепляют на планшайбе и устанавливают на оправку 3, которую затем располагают перпендикулярно к двум параллельным направляющим 4
балансировочного приспособления с таким расчётом, чтобы круг был равноудалён от обеих опорных поверхностей.
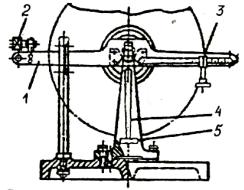
24
При этом обе направляющие должны быть одного вида. Твёрдость оправки и направляющих должна быть 50HRC, а шероховатость поверхности не ниже Ra=2,5мкм. Вследствие дисбаланса тяжёлая сторона круга окажется внизу. После остановки круга в верхнюю часть кольцевой канавки,
выполненной на боковой стороне планшайбы, устанавливают сухарь 5, который удерживается в пазу планшайбы стопорным винтом 6. После этого круг поворачивается на 90°, и если он не удерживается в состоянии безразличного равновесия, то на планшайбу устанавливают дополнительные противовесы.
Процесс балансировки продолжают до тех пор, пока шлифовальный круг не будет находиться в покое в любом положении. После правки круга балансировку необходимо повторить.
При контроле дисбаланса круг поворачивают на 90° и устанавливают груз с массой, равной допустимо неуравновешенной массе (табл. 1.9)
Рис. 1.5 Весы для статической балансировки шлифовального круга
Если под действием этого груза круг остаётся в покое или медленно опускается, то круг удовлетворяет требованиям мощности балансировки данного класса. Погрешность измерения допустимой неуравновешенности массы круга не должна превышать величины, указанной в таблице.
Для статической балансировки шлифовальных кругов диаметром 200600мм можно применять также балансировочные весы (рис. 1.5).
25
Перед началом балансировки раму 1 с помощью грузиков 2 и 3
устанавливают в нулевое положение по ватерпасу в продольном и поперечном направлениях. Шлифовальный круг вместе с фланцами монтируют на специальной оправке и устанавливают на весы. При этом балансировочные противовесы должны быть сняты с фланцев круга. Медленно вращая круг,
определяют такое его положение, которое соответствует наибольшему отклонению стрелки 4, и фиксируют это положение.
Таблица 1.9 Допустимые неуравновешенные массы круга в граммах
Мacca круга, кг |
|
Класс точности балансировки |
|
||
1 |
2 |
3 |
4 |
||
|
|||||
От 0,20 до 0,25 |
2,5 |
4,0 |
6,0 |
12,0 |
|
Св. 0,25 » 0,30 |
2,5 |
4.5 |
7,0 |
14,0 |
|
» 0,30 » 0,40 |
30, |
5,0 |
7,5 |
15,0 |
|
» 0,40 » 0,50 |
3,5 |
5,5 |
9,0 |
17,0 |
|
» 0,50 » 0,63 |
4,0 |
6,0 |
10,0 |
20,0 |
|
» 0,63 » 0,80 |
4,5 |
7,0 |
11,0 |
22,0 |
|
» 0,80 » 1,00 |
5,0 |
7,5 |
12,0 |
25,0 |
|
» 1,00 » 1,25 |
5,5 |
9,0 |
14,0 |
27,0 |
|
» 1,25 » 1,60 |
6,0 |
10,0 |
15,0 |
30,0 |
|
» 1,60» 2,00 |
7,0 |
11,0 |
17,0 |
35,0 |
|
» 2,00 » 2,50 |
7,5 |
12,0 |
20,0 |
40,0 |
|
» 2,50 » 3,00 |
9,0 |
14,0 |
22,0 |
45,0 |
|
» 3,00 » 4,00 |
10,0 |
15,0 |
25,0 |
50,0 |
|
» 4,00 » 5,00 |
11,0 |
17,0 |
27,0 |
55,0 |
|
» 5,00 » 6,30 |
12,0 |
20,0 |
30,0 |
60,0 |
|
» 6,30 » 8,00 |
14,0 |
22,0 |
35,0 |
70,0 |
|
» 8,00 » 10,00 |
15,0 |
25,0 |
40,0 |
75,0 |
С противоположной стороны круга на одинаковом расстоянии от метки размещают противовесы. Перемещая их, добиваются совмещения стрелки с нулевой отметкой шкалы 5. Шлифовальный круг при этом считается отбалансированным. Новый шлифовальный круг необходимо балансировать два раза.
Примечание. Для отрезных кругов на вулканитовой связке и армированных на бакелитовой связке допустимые неуравновешенные массы увеличиваются на 20%.
26
Имеются также механизмы и устройства, позволяющие производить балансировку круга на шлифовальном станке. Дисбаланс шлифовального круга оценивают виброметром. Динамическая балансировка кругов осуществляется на балансировочных станках ДБ 10, 9715, при этом точность балансировки высокая. Так, на станке модели 9715 она достигает 1-2,5 г*мм/кг.
|
Погрешность измерения допустимой |
|
Таблица 1.10 |
|||||
|
|
|
|
|||||
неуравновешенности массы круга (в граммах) |
|
|
||||||
Масса круга, кг |
|
|
Класс точности балансировки |
|||||
|
1 |
|
2 |
|
3 |
|
4 |
|
|
|
|
|
|
||||
От 0,20 до 0,25 |
|
0,5 |
|
0,8 |
|
1,2 |
|
2,4 |
Св. 0,25 » 0,30 |
|
0,5 |
|
0,9 |
|
1,4 |
|
2,8 |
» 0,30 » 0,40 |
|
0,6 |
|
1,0 |
|
1,5 |
|
3,0 |
» 0,40 » 0,50 |
|
0,7 |
|
1,1 |
|
1,8 |
|
3,5 |
» 0,50 » 0,63 |
|
0,8 |
|
1,2 |
|
2,0 |
|
4,0 |
» 0,63 » 0,80 |
|
0,9 |
|
1,4 |
|
2,2 |
|
4,5 |
» 0,80 » 1,00 |
|
1,0 |
|
1,5 |
|
2,4 |
|
5,0 |
» 1,00» 1,25 |
|
1,1 |
|
1,8 |
|
2,8 |
|
5,5 |
» 1,25 » 1,60 |
|
1,2 |
|
2,0 |
|
3,0 |
|
6,0 |
» 1,60» 2,00 |
|
1,4 |
|
2,2 |
|
3,5 |
|
7.0 |
» 2,00 » 2,50 |
|
1,5 |
|
2,4 |
|
4,0 |
|
8,0 |
» 2,50 » 3,00 |
|
1,8 |
|
2,8 |
|
4,5 |
|
9,0 |
» 3,00 » 4,00 |
|
2,0 |
|
3,0 |
|
5,0 |
|
10,0 |
» 4,00 » 5,00 |
|
2,2 |
|
3.5 |
|
5.5 |
|
11,0 |
1.2.3 Правка шлифовальных кругов и устройства для её выполнения
Правка инструмента для выполнения шлифовально-заточных операций осуществляется в целях придания ему режущих свойств и правильной геометрической формы. Правке подвергаются инструменты, вновь устанавливаемые на станок и затупившиеся в процессе работы. Критерием затупления инструмента является ухудшение качества обработанной поверхности, появление прижогов, вибраций, дробления и т.п. В
автоматизированном производстве правку осуществляют принудительно, через определённые интервалы времени.
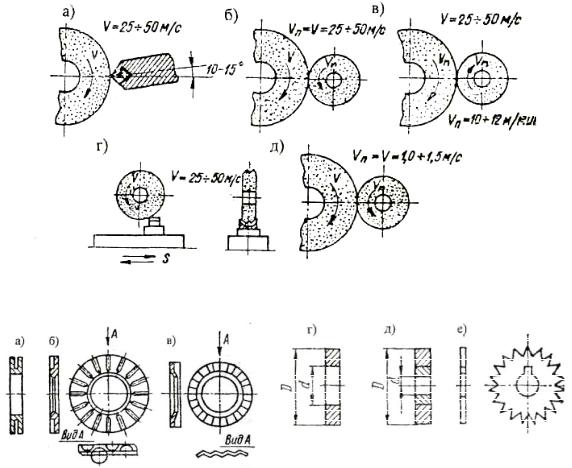
27
Наиболее распространённые методы правки приведены на рисунках
1.6 и 1.7. Правка методом обтачивания (рис.1.6а) осуществляется алмазными карандашами, иглами, алмазами в оправе (табл. 1.11).
Рис.1.6 Методы правки шлифовальных кругов
Рис.1.7 Диски (а- д) и звёздочки (е) для правки кругов
Алмазно-металлические карандаши, используемые для правки шлифовальных кругов выпускают: с зёрнами, расположенными цепочкой, с
зернами, расположенными слоями; с неориентированными зёрнами (рис. 1.8).
Карандаш с зёрнами алмазов, расположенных цепочкой, изготавливают из высококачественных кристаллов и широко используют при правке кругов для круглого, внутреннего, бесцентрового и фасонного шлифования.
Для правки однониточных резьбошлифовальных кругов выпускаются алмазные иглы (ГОСТ 17564-72).
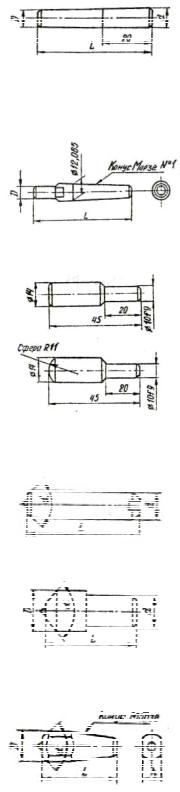
28
Таблица 1.11
Алмазные правящие инструменты
Тип, наименование, основные размеры |
|
Область применения |
|
|
||||
|
|
|
|
|
|
|
||
|
|
|
|
|
|
|
|
|
Алмазные карандаши (ГОСТ 607-80 Е) |
|
|
|
|
|
|
|
|
Исполнение А цилиндрические |
|
|
|
|
|
|
|
|
Тип 01 (с алмазами, расположенными цепочкой по оси |
|
|
|
|
|
|
|
|
карандаша) |
|
|
|
|
|
|
|
|
Тип 04 (с неориентированным расположением алмазов) |
|
|
|
|
|
|
|
|
D (h14) = 6; 8; 10мм, d (f9) = 6; 8; 10мм, L = 55; 45мм |
|
|
|
|
|
|
|
|
|
Правка |
абразивных |
кругов |
прямого |
||||
|
профиля |
на |
операциях |
|
круглого |
|||
Исполнение В с коническим корпусом |
наружного, внутреннего, бесцентрового |
|||||||
и плоского шлифования, на отдельных |
||||||||
Типы 01, 04, 02 (с алмазами, расположенными слоями) |
операциях профильного, |
резьбо- и |
||||||
D (h14) = 10; 12мм; L= 40÷70мм |
||||||||
зубошлифования, |
при |
|
которых |
|||||
|
|
|||||||
|
обработанная |
поверхность |
должна |
|||||
|
иметь шероховатость Ra<1,25мкм (при |
|||||||
|
врезном |
шлифовании) и |
Ra<0,63мкм |
|||||
|
(при шлифовании с продольной |
|||||||
|
подачей) |
|
|
|
|
|
|
|
Исполнение С ступенчатые |
|
|
|
|
|
|
|
|
Типы 02, 04, 03 (с алмазами, расположенными на |
|
|
|
|
|
|
|
|
сферической поверхности) D(hl4)=10; 12мм; L = 40-70мм |
|
|
|
|
|
|
|
|
Алмазы в оправах (ГОСТ 22908-78 Е) |
Правка |
абразивных |
кругов |
всех |
||||
|
характеристик, |
используемых |
для |
|||||
|
окончательного |
шлифования |
по- |
|||||
|
верхностей, с параметром шерохо- |
|||||||
Тип I цилиндрические |
ватости Ra > 0,2 мкм (шлифование |
|||||||
врезанием) и Ra > 0,1 мкм (шлифование |
||||||||
d(f9) = 6÷12мм; L= 0,5÷50мм; α= 90; 120°. |
||||||||
с продольной подачей) |
|
|
|
|
||||
Тип II цилиндрические с головкой |
|
|
|
|
||||
|
|
|
|
|
|
|
||
D+0,5 = 10; 12мм; d = 6; 8мм; L = 32; |
|
|
|
|
|
|
|
|
50мм; α =90; 120˚ |
|
|
|
|
|
|
|
|
Тип III с конической державкой |
|
|
|
|
|
|
|
|
D = 10,3; 12,2мм, L = 28; 32мм, h =8; 10мм; α = 90; 120°. |
|
|
|
|
|
|
|
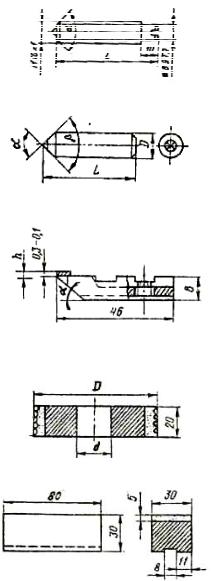
|
|
|
|
|
|
29 |
|
|
|
|
|
|
|
|
|
Тип IV с резьбовой державкой L = 36;50мм; α = 90;120˚. |
|
|
|
|
|
|
|
Алмазные иглы (ГОСТ 17564-72*) |
Правка |
|
|
однониточных |
|||
|
|
|
|||||
|
резьбошлифовальных |
кругов |
При |
||||
|
шлифовании высокоточных резьбовых |
||||||
D = 6; 8; 9,5мм; L = 35, 50мм; α = 60; 90°, β = 50, 80°. |
поверхностей |
|
|
|
|
||
|
|
|
|
|
|
||
Алмазные резцы (ГОСТ 17368-79 *Е) |
Профильная правка абразивных кругов |
||||||
на операциях круглого наружного, |
|||||||
|
|||||||
|
бесцентрового, плоского шлифования, |
||||||
|
резьбо- |
и |
|
зубошлифование |
|||
|
поверхностей |
с |
параметром |
||||
|
шероховатости |
Ra |
> 0,2 |
мкм |
|||
h-0,1 = 0,3÷1,3мм, α+1˚=28; 32; 35˚ |
(шлифование врезанием) и Ra > 0,1 мкм |
||||||
(шлифование с продольной подачей) |
|||||||
|
|||||||
Ролики алмазные прямого профиля |
|
|
|
|
|
|
|
(ГОСТ 16014-78*) |
Правка |
абразивных |
кругов |
прямого |
|||
|
профиля, используемых при обработке |
||||||
|
поверхностей |
с |
параметром |
||||
|
шероховатости R = 0,63 ÷ 1,25 мкм |
|
|||||
D (h8) = 69,85 ÷ 70,05мм; d (H6) = 19,05; 20,0мм |
|
|
|
|
|
|
|
Алмазные бруски прямого или фасонного профилей |
|
|
|
|
|
|
|
|
Правка |
абразивных |
кругов |
прямого |
|||
|
профиля или профильной правки по |
||||||
|
копиру |
на |
плоскошлифовальных |
||||
|
станках при обработке поверхностей с |
||||||
Размеры фасонных брусков определяются обрабатываемым |
Rа>1,25 мкм |
|
|
|
|
||
изделием. Алмазный слой шириной до 50мм, длиной до |
|
|
|
|
|
|
|
110мм, глубиной профиля до 20мм, радиус выпуклости R > |
|
|
|
|
|
|
|
0,1мм, радиус вогнутости R > 0,1мм |
|
|
|
|
|
|
Алмазные карандаши типов 01, 02, 03 и алмазы в оправах следует устанавливать с наклоном 10-15° в сторону вращения круга и разворачивать к направлению движения подачи. В процессе правки их необходимо поворачивать вокруг своей оси на угол 60-90°.
Карандаши типа 04 (реже 02) и алмазные иглы закрепляют без наклона к поверхности круга. Метод обтачивания используется для правки абразивных кругов, кругов из эльбора на бакелитовой и керамической связке.
Режимы правки шлифовальных кругов методом обтачивай приведены в таблице 1.12.
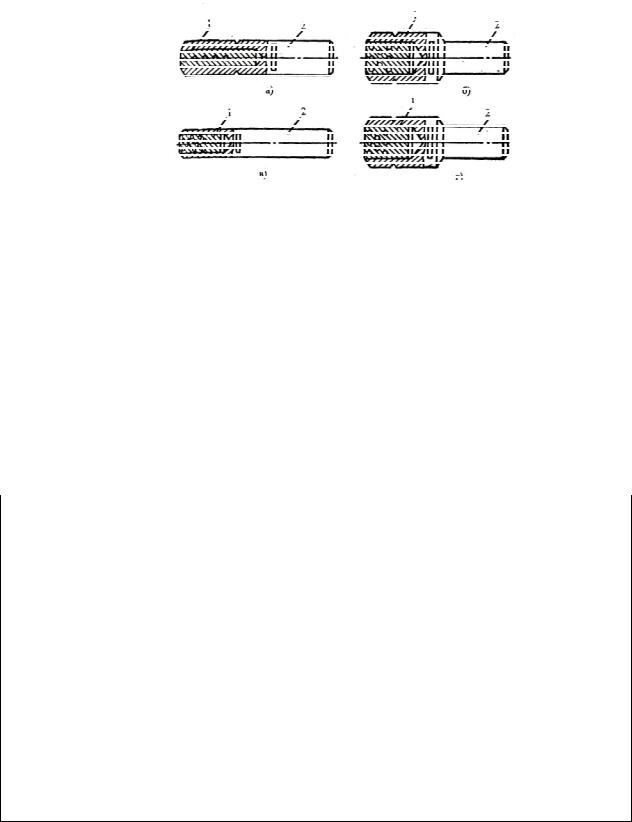
30
При правильной эксплуатации круги из эльбора и алмаза самозатачиваются. Правка применяется для устранения биения и для восстановления изношенного профиля. При правке кругов зернистостью
200/160-40/25 используют алмазные карандаши.
Рисунок 1.8 - Алмазные карандаши:
1-алмазная вставка; 2-оправка; а) с алмазами, расположенными цепочкой вдоль оси карандаша; б) с неперекрывающимися слоями алмазов; в) с перекрывающимися
слоями; г) с неориентированным расположением алмазов
Правка методом обкатывания (рис. 1.6,б) применяется при профилировании шлифовальных кругов (с прямолинейной образующей) из электрокорундов и карбида кремния.
Таблица 1.12 Режимы правки шлифовальных кругов методом обтачивания
|
|
|
Режимы правки |
|
||
|
|
|
|
Алмазно- |
||
Вид шлифования |
Шероховатость |
Алмазом |
металлическим |
|||
Ra, мкм |
|
|
карандашом |
|||
|
|
|
||||
|
|
Подача* |
Число |
Подача* |
Число |
|
|
|
проходов** |
проходов** |
|||
Круглое наружное, |
1,25 – 0,32 |
0,3/0,02 |
6/4 |
0,4/0,03 |
4/4 |
|
бесцентровое, плоское |
0,32 – 0,16 |
0,2/0,01 |
5/4 |
0,3/0,02 |
3/4 |
|
Внутреннее |
1,25 – 0,32 |
1,0/0,02 |
6/4 |
1,5/0,03 |
4/4 |
|
0,32 – 0,16 |
0,5/0,01 |
5/4 |
- |
- |
||
|
||||||
Резьбошлифование |
0,63 – 0,16 |
0,2/0,005 |
6/2 |
- |
- |
|
Шлицешлифование |
1,25 – 0,32 |
0,3/0,03 |
4/4 |
0,4/0,03 |
4/4 |
|
0,32 – 0,16 |
0,2/0,01 |
5/4 |
0,3/0,02 |
3/4 |
||
|
||||||
Профильное |
1,25 – 0,32 |
0,2/0,02 |
6/4 |
0,3/0,03 |
4/4 |
|
0,32 – 0,16 |
0,1/0,01 |
8/4 |
0,2/0,02 |
4/4 |
||
|
*В числителе указана продольная подача (м/мин). В знаменателе – поперечная подача (мм/дв.ход.)
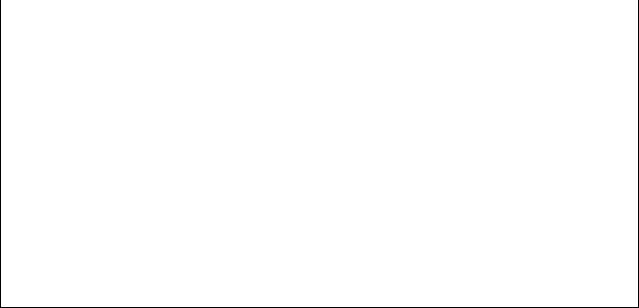
31
При правке правящий ролик устанавливается параллельно оси круга,
подвергающегося обработке, или наклоняется под некоторым углом к нему.
Наклон ролика создаёт условия для проскальзывания, при котором интенсифицируется процесс правки и осуществляется заглаживание поверхности круга. С увеличением угла возрастает износ правящего ролика.
Ролик вращается под действием сил трения между ним и кругом. Правящий инструмент имеет вид дисков, звёздочек, шарошек, абразивных кругов,
устанавливаемых на оси поодиночке или пакетом. Материал звёздочек и шарошек - закалённая сталь. Назначение - обдирочная грубая правка с поперечной подачей до 0,1мм/ход. Для правки кругов из карбида кремния твёрдостью ВТ-4Т на керамической связке применяют твердосплавные диски из твёрдого сплава ВК6. Размеры выпускаемых дисков D=40 и 60мм,
Н<3мм. Диски закрепляют на державках по два на одной оси.
Таблица 1.13 Режимы правки шлифовальных кругов методом обкатывания
|
|
Поперечная подача, |
|
|
Число проходов при |
|||||||
|
Продольная |
|
мм/дв.ход, |
|
|
|
||||||
Правящий |
при зернистости |
|
|
зернистости |
||||||||
подача, |
|
|
||||||||||
инструмент |
шлифовального круга |
|
|
|
|
|
|
|||||
м/мин |
|
|
|
|
|
|
||||||
40 |
|
25 |
|
16 |
40 |
|
25 |
|
16 |
40-16 |
||
|
|
|
|
|
||||||||
|
|
|
|
|
рабочих |
|
выхаживающ. |
|||||
|
|
|
|
|
|
|
|
|
||||
Круг из карбида |
1,0 |
0,02- |
|
0,03- |
|
0,02- |
2-3 |
|
2 |
|
2-3 |
2 |
кремния |
0,04 |
|
0,02 |
|
0,01 |
|
|
|||||
Диск |
|
0,02- |
|
0,02- |
|
0,02- |
|
|
|
|
|
|
твердосплавный |
0,5-0,1 |
|
|
2-4 |
|
2-3 |
|
2 |
2-4 |
|||
монолитный |
|
0,03 |
|
0,01 |
|
0,01 |
|
|
|
|
|
|
|
|
|
|
|
|
|
|
|
|
|
|
|
Диск стальной |
1,0-1,5 |
0,4- |
|
0,02- |
|
0,02- |
2 |
|
2 |
|
2 |
3-4 |
0,05 |
|
0,01 |
|
0,01 |
|
|
||||||
|
|
|
|
|
|
|
|
|
|
Примечание. Для интенсификации процесса правки кругами из карбида кремния ось правящего инструмента устанавливают на угол φ=8÷10˚ по отношению к оси шлифующего круга. Остальные инструменты осуществляют правку кругов при угле
φ=0÷6˚
В качестве материала дисков используют также релит (литой карбид вольфрама) в виде зёрен размером 600-1600мм, скрепленных металлической связкой. Размеры выпускаемых дисков D=40 и 75мм, Н<12мм. Диски устанавливают на державках. Правящим элементом могут быть зёрна сверхтвёрдых материалов размером 1600мм и комбинации зёрен различных

32
материалов, закрепляемых в твердосплавной или металлической связках.
Режимы правки шлифовальных кругов методом обкатки приведены в табл. 1.13.
Рис. 1.9 Приспособление для контактного обкатывания с торможением алмазных и эльборовых кругов: 1-абразивный круг; 2-кожух; 3-подшипник; 4-корпус; 5-шпиндель; 6-корпус центробежного регулятора; 7-опора; 8- колодки; 9-пружина; 10-оси колодок.
Правка методом шлифования (рис. 1.6в) - процесс обработки поверхности шлифовального круга правящим инструментом, получающим принудительное вращение подразделяется на правку с продольной подачей и правку врезанием (правка фасонных угловых поверхностей). К правящему инструменту относятся круги из карбида кремния зернистостью 125-50 на керамической связке диаметром 60-250мм, алмазные ролики из природных и синтетических алмазов, а также металлоабразивные ролики.
Режимы правки шлифовальных кругов методом шлифования приведены в табл. 1.14, а схема правки на рис.1.10. Метод обкатывания используется также
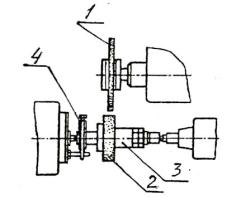
33
для правки алмазных и эльборовых кругов. Производится они с помощью приспособления для контактного обкатывания с торможением (рис.1.9).
Таблица 1.14 Режимы правки шлифовальных кругов методом шлифования
|
Характеристика |
|
|
Режим правки |
|
||||
Правящий |
шлифовального круга |
Вид |
|
|
|||||
|
|
|
|
|
|||||
|
|
|
|
|
|
|
|
||
инструмент |
|
Степень |
|
шлифования |
Скорость |
|
Подача |
||
Зернист. |
Связка |
инстр., |
|
Прод., |
|
Попереч., |
|||
|
тв-ти |
|
|
|
|||||
|
|
|
|
м/с |
|
м/мин |
|
мм/ход |
|
|
|
|
|
|
|
|
|||
Алмазный |
40-12 |
До Т2 |
К;Б;В |
|
10,0 |
|
0,5-1,0 |
|
0,02 |
Окончательное |
|
|
0,3-0,5 |
||||||
ролик |
25-12 |
До СТ1 |
К;Б |
|
10,0 |
|
- |
|
мм/мин |
|
|
|
|
|
|
|
|
|
|
|
|
Круги из карбида кремния степени твердости: |
|
||||||
Т1-Т2 |
50-40 |
СМ2 |
К |
Предварит. |
0,5-1,0 |
|
1,0-1,5 |
|
0,05 |
ВТ1-ЧТ2 |
50-40 |
СТ1 |
К;Б |
Предварит. |
0,5-1,0 |
|
1,0-1,5 |
|
0,05 |
Более ЧТ2 |
50-40 |
СТ3 |
К;Б |
Предварит. |
0,5-1,0 |
|
1,0-1,5 |
|
0,05 |
Т1-Т2 |
40-12 |
СМ2 |
К;Б |
Окончательное |
0,5-1,0 |
|
0,5-1,0 |
|
0,03 |
ВТ1-ВТ2 |
40-12 |
СТ1 |
К;Б |
Окончательное |
0,5-1,0 |
|
0,5-1,0 |
|
0,03 |
Указанный метод находит применение при правке алмазных и эльборовых кругов. Правку кругов из эльбора и алмаза на металлической связке производят шлифованием кругами из зелёного карбида кремния.
Рис. 1.10 - Схема правки алмазного крута методом шлифования абразивным кругом:
1-алмазный или эльборовый круг; 2-абразивный круг; 3-оправка центровая; 4-хомутик
Правка методом точения с тангенциальной подачей (рис. 1.6г) аналогична правке методом обтачивания, но осуществляется брусками (прямого или фасонного профиля). При установке бруска на столе станка непосредственно за обрабатываемой заготовкой шлифовальный круг постоянно «подправляется»,
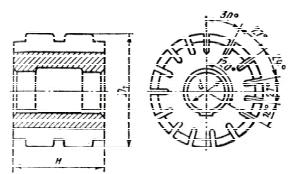
34
что позволяет получить высокое качество и точность профиля. Эльборовые круги на органической и керамической связках правятся алмазными брусками и брусками из карбида кремния; алмазные круги - брусками из зелёного карбида кремния и белого электрокорунда.
Правка методом накатывания (рис. 1.6д) на рабочую поверхность круга фасонного профиля представляет собой комбинацию пластического деформирования с дроблением зёрен и связки с уплотнением поверхности. Для накатывания используют стальные закалённые ролики из стали 45, 40Х (3133HRCэ), из сталей У8А, У10А, Р18 (61-65HRCэ), твердосплавные и алмазные ролики. Ролики должны иметь следующие размеры: D=(0,2-0,25)Dкp, высоту,
равную длине обрабатываемого профиля. В процессе правки ролик или круг принудительно вращают с окружной скоростью до 1,5м/с, поперечную подачу назначают в пределах 0,01-0,05мм/мин, после окончания профилирования целесообразно осуществить калибрование в течение 0,5-5,0мин. Правка методом накатывания получила распространение при многониточном резьбошлифовании мелкомодульного твердосплавного инструмента (долбяков шеверов, эвольвентных протяжек). Точность профиля накатанного круга может достигать: линейных размеров 0,005-0,01мм, для радиуса закругления вершины не более 0,04мм и для угловых размеров 5-10.
Рис. 1.11 Накатной ролик для правки фасонных шлифовальных кругов
На рис. 1.11 приведена конструкция накатного ролика с параллельными оси канавками неравномерного шага. Наличие канавок интенсифицирует процесс профилирования круга, а неравномерный шаг их расположения
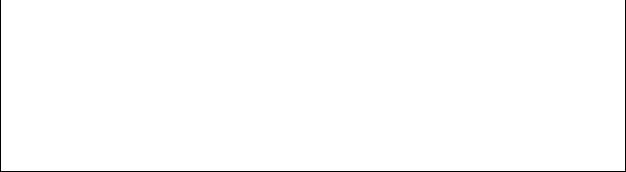
35
исключает появление на круге следов от канавок, а также биение круга после
правки.
Таблица 1.15
|
Режимы профилирования фасонных |
|
||||
|
шлифовальных кругов накатными роликами |
|
||||
|
Характеристика |
|
Режимы правки |
|||
Правящий |
шлифовального круга |
Вид |
||||
|
|
|||||
|
|
|
Попереч. |
|||
инструмент |
|
|
шлифования |
Скорость, |
||
Зернистость |
Твердость |
подача, |
||||
|
|
|
|
м/с |
мм/мин |
|
|
|
|
|
|
||
|
|
Стальной ролик твердости: |
|
|
||
HRC 30-32 |
16-40 |
М3-СМ2 |
Предварительная |
0,5 |
0,05 |
|
HRC 60-64 |
16-М20 |
М3-СТ1 |
Окончательная |
1,0-1,5 |
0,05-0,01 |
Примечание. Режимы профилирования даны для круга с керамической связкой
В таблице 1.15 приведены ориентировочные режимы профилирования кругов накатными роликами. При правке давление на круг должно составлять 8- 10*105 Па. Метод правки накатыванием применяют при многопрофильном резьбошлифовании, зубошлифовании, фасонном- и шлицешлифовании.
1.2.4Специальное приспособление дляправки шлифовального круга
На рис. 1.12 показано простое приспособление для правки шлифовального круга, обеспечивающее высокую точность. На синусной плите 1 приспособления установлено основание 2, на котором может вращаться вокруг оси 3 поворотный диск 4, несущий ползун 5. Положение ползуна 5 со стойкой 7, в которой укреплен алмазный карандаш 8, фиксируется прижимными планками 9.
Для правки круга по радиусу алмазный карандаш 8 закрепляется по специальному установочному шаблону в стойке 7, а ползун 5 устанавливается в определенное положение, фиксируемое наборам мерных плиток размером А;
набор плиток закладывается между штифтом 10 и базовой планкой 11. При заданном радиусе R профиля размер А определяется соотношением А=60±R (плюс — для выпуклого профиля, минус — для вогнутого). Правка осуществляется качательным движением диска 4 вокруг оси 3. Для правки прямолинейного профиля диск 4 с помощью фиксатора 12 устанавливается в

36
нулевое положение. Между базовой планкой магнитной плиты станка и одним из роликов 6, закрепленным на плите 1, укладывается набор мерных плиток,
соответствующий заданному углу профиля и расстоянию L между осями роликов.
Рис. 1.12 Приспособление для правки шлифовального круга
Правка осуществляется возвратно-поступательным движением алмазного карандаша.
1.2.5 Доводочные операции
Доводка является технологическим процессом финишной обработки высокоточных плоских, цилиндрических (наружных и внутренних) и фасных поверхностей, а также применяется для притирки деталей, работающих в паре
(зубчатые колёса, детали топливной и гидроаппаратуры). В результате доводки
37
получаются погрешности размеров и формы 0,5-0,1мкм и шероховатость
Ra=0,16-0,01мкм.
При доводке съем металла и формирование микрорельефа поверхности осуществляется в результате резания-царапания обрабатываемой поверхности большим количеством мельчайших абразивных частиц. В начальный период доводки, как правило, преобладает резание-царапание, а затем происходит постепенный переход к трению с пластическим деформированием металла.
Преобладание резания необходимо, когда снимается основной припуск и происходит исправление формы поверхности. На финишной стадии доводки,
когда задачей является получение малой шероховатости, необходимо преобладание трения, при котором абразивные зёрна осуществляют своеобразное выглаживание поверхности.
В процессе доводки происходит образование оксидных плёнок и адсорбционных слоев на металлической поверхности, снижающих её прочность и способность противостоять разрушению. Поэтому для повышения химической активности абразивных паст и суспензий вводят такие вещества,
как олеиновая кислота, стеарин и др. Процесс доводки протекает в условиях граничного трения, когда поверхности притира и обрабатываемой заготовки разделяет тонкий граничный слой смазки. Поэтому для улучшения смазывающих свойств доводочных смесей в них вводят масла или жиры животного происхождения, добиваясь оптимальной вязкости доводочной смеси.
По способу подачи доводочной смеси различают доводку с непрерывной её подачей и с периодическим дозированным нанесением смеси на притир. В
первом случае суспензия или жидкая паста непрерывно перемешиваются и подаются на рабочую поверхность притира. Непрерывную подачу абразивной смеси применяют на предварительных операциях, где требования к точности и шероховатости поверхности не высоки.
При доводке с периодическим нанесением пасты на притир необходимо вмешательство оператора или создание специальных дозирующих устройств.
38
Абразивными пастами называются смеси абразивных материалов с неабразивными различной густоты, начиная от совершенно жидких и вплоть до брикетированных в довольно твёрдые тела нужной формы и размеров.
Изготовление абразивных паст производится из готовых составных частей путём смешивания их в надлежащих весовых (или объёмных)
количествах. Свойства пасты зависят от её состава, вследствие чего основами характеристиками паст следует считать:
1)абразивный материал;
2)зернистость;
3)состав неабразивных материалов;
4)концентрацию, т. е. процентное содержание абразивного материала в пасте;
5)консистенцию, т. е. густоту пасты.
Ассортимент применяемых на практике паст для различных операций доводки и полирования чрезвычайно широк и не стандартизован. Это обусловлено тем, что из-за простоты процесса получения пасты потребители сами изготовляют её применительно к особенностям выполняемых операций.
Жидкие пасты хранят в жестяных банках, мазеобразные (дорогие сорта) в
тюбиках, а из твёрдых чаще отливают конические или трапецеидальные брикеты.
Для доводки используют микропорошки, из различных абразивных материалов: электрокорунда нормального, белого, карбида кремния зелёного,
карбида титана, карбида бора, оксида алюминия (глинозём), оксида хрома; а
также из сверхтвёрдых материалов: алмаза, нитрида бора (эльбора, кубонита,
гексанита-А).
В таблице 1.16 приведены значения шероховатости, получаемые на различных операциях, в зависимости от зернистости используемых порошков.
Как видно из таблицы, для операций доводки, притирки и отделочной обработки используют порошки с зернистостью от 6-5(50-40) до МЗ-М1(3/2-
39
2/1) соответственно для абразивных, алмазных материалов. При этом обеспечивается шероховатость поверхности Ra от 0,4-0,2 до 0,04-0,02мкм.
По результатам обработки доводочные операции можно разделить на грубые (точность 3-5 мкм, шероховатость Ra=0,16-0,32мкм), чистовые
(точность 1-2 мкм, шероховатость Ra=0,08-0,16мкм) и тонкие (точность 0,1- 0,5мкм, шероховатость R3=0,01-0,04мкм). Строгая последовательность и постепенность выполнения операций являются основой рациональной технологии доводки.
Таблица 1.16 Выбор зернистости абразивного порошка в зависимости от требований к
шероховатости обработанной поверхности и вида операции
Зернистость порошка |
Шероховатость |
|
|||
|
Алмазного, |
обработанной |
Вид операции |
||
Абразивного |
эльборового, |
поверхности |
|||
|
|||||
|
кубонитового |
Ra, мкм |
|
||
200-100 |
- |
12,5 … 6,3 |
Обдирка и зачистка отливок, |
||
поковок, крупных штампованных |
|||||
|
|
|
|
заготовок |
|
80-50 |
- |
3…3,2 |
Предварительное плоское |
||
шлифование торцом круга, отрезные |
|||||
|
|
|
|
работы |
|
40-25 |
- |
2,5 |
… 1,6 |
Предварительное шлифование и |
|
заточка, правка алмазных кругов |
|||||
|
|
|
|
||
20-12 |
160/125-100/80 |
1,6 |
… 0,8 |
Предварительное шлифование, |
|
заточка |
|||||
|
|
|
|
||
10-8 |
80/63-63/50 |
0,8 |
… 0,4 |
Окончательное шлифование и |
|
заточка твердосплавного |
|||||
|
|
|
|
инструмента |
|
6-5 |
50/40 |
0,4 |
… 0,2 |
Отделочное шлифование, доводка, |
|
резьбошлифование |
|||||
|
|
|
|
||
М40М28 |
40/28 – 28/20 |
0,2 |
… 0,1 |
Суперфиниширование, доводка, |
|
притирка |
|||||
|
|
|
|
||
М20 – М10 |
20/14 – 10/7 |
0,1 … 0,05 |
Доводка, притирка, отделочная |
||
обработка |
|||||
|
|
|
|
||
М7-М5 |
7/5 – 5/3 |
0,05 |
… 0,04 |
Отделочная обработка |
|
М3 – М1 |
3/2 – 2/1 |
0,04 |
… 0,02 |
Отделочная обработка |
В качестве неабразивных материалов в состав входят такие компоненты,
как олеиновая кислота, парафин, стеарин, керосин, масло (касторовое, костное,
говяжий жир). Содержание абразива в грубых и средних пастах составляет 5080%, в тонких пастах 15-20%. При доводке пасты могут быть разбавлены до требуемой консистенции керосином или маслами (велоситом, вазелиновым,
касторовым и др.).
40
Для доводки используют также абразивные суспензии, в которых абразив
(не более 10% по массе) находится в жидкой среде во взвешенном состоянии. В
качестве жидкой среды используют керосино-масляную смесь с добавкой 3-5%
олеиновой кислоты. При обработке неметаллов применяют водные суспензии.
По применению доводочных смесей из различных абразивных материалов можно использовать следующие общие рекомендации. Для доводки изделий из термически обработанных сталей следует использовать смеси на основе электрокорундовых порошков. При доводке изделий из особо твёрдых неметаллических материалов (керамики) применяют порошки карбида бора,
которые используют также при доводке высокотвёрдых стальных изделий
(например, калибров). Применение алмазных и эльборовых порошков и паст наиболее эффективно при доводке изделий из высокотвёрдых закалённых сталей (инструментальных, быстрорежущих), твёрдых сплавов, режущей керамики.
Используя современное доводочное оборудование и технологическую оснастку, можно обеспечить с большой степенью точности постоянство режимов доводки: скорости, давления, времени, а также постоянство условий подачи абразивной смеси (её количество и периодичность дозировки).
Притиры. Наибольшее распространение в промышленности получили чугунные притиры. Чугун сочетает ряд свойств, делающих его наилучшим притирочным материалом: высокую износостойкость, необходимую для сохранения точной формы; специфическую структуру, в которой наряду с участками высокой твёрдости (цементит) имеются мягкие участки (феррит), а
также наличие графитовых включений, улучшающих условия трения. Лучших результатов при доводке достигают при использовании перлитного чугуна,
причем чем мельче применяемый абразив, тем более тонкопластичную структуру должен иметь чугун. Твёрдость перлитного чугуна должна быть НВ=150-200. Наиболее благоприятной формой графитовых включений является пластинчатая, а также шаровидная (в модифицированном чугуне).
41
При доводке высокоточных отверстий иногда применяют разрезные притиры из мягкой стали. Притиры для доводки отверстий должны иметь точность формы в продольном и поперечном сечениях в пределах 0,005мм;
биение притира на оправке не должно превышать 0,01мм. Для восстановления
точности изношенных притиров применяют контрпритиры-втулки.
Производительность и качество доводки зависят от величины припуска,
количества доводочных операций и режимов обработки. Как правило, доводку
выполняют после шлифования. Припуск при односторонней доводке: |
|
h = k (Rz + Δ), |
(1.1) |
а при плоскопараллельной и доводке поверхностей вращения: |
|
h = k (2Rz + Δ), |
(1.2) |
где k=1,2-1,5- коэффициент запаса, учитывающий наличие на поверхности отдельных грубых рисок, царапин и других дефектов; Rz - высота неровностей шлифованной поверхности после шлифования.
Доводку производят в несколько последовательных операций, число которых зависит от требований к точности и шероховатости обрабатываемой поверхности таблица 1.17. Для обеспечения стабильности процесса доводки рассеяние размеров партии заготовок не должно превышать 0,2-0,3 величины припуска. Это достигается путём селекции заготовок. Основными факторами,
определяющими режим доводки, являются: давление на площадь контакта притир-заготовка; скорость рабочего движения и время доводки.
При обработке заготовок из закалённых сталей оптимальные значения давления на предварительных операциях составляют 1 2*105Па, на окон-
чательных операциях 0,5 1,0*105Па. При высокой скорости доводки (до
100м/мин). На предварительных операциях давление может быть снижено до
0,5 0,7*105Па и до 0,2 0,5*105Па на окончательных. Цикл доводки можно осуществить как с постоянным давлением, так и с изменением давления во время операции. В последнем случае вначале работают с большим давлением,
обеспечивая интенсивность съёма металла, а в конце операции уменьшают давление для достижения необходимой шероховатости поверхности.
42
Скорость рабочего движения на предварительных доводочных операциях
40-120м/мин; окончательная доводка производится при скорости 15-30м/мин,
прецизионная доводка при скорости 5-10м/мин. При доводке не происходит каких-либо фазовых изменений в поверхностном слое металла, так как тепловыделение, а следовательно, и температура поверхностного слоя в процессе обработки незначительны. Доводка создаёт некоторый наклёп
(упрочнение) в поверхностном слое металла. Степень наклёпа достигает 2030%, глубина упрочнённого слоя не превышает 10мкм. В поверхностном слое металла после доводки образуются остаточные напряжения сжатия, величина которых составляет 20 40*105Па, а глубина напряженного слоя не превышает
7-10мкм.
При доводке свободным абразивом происходит интенсивное шаржирование поверхностного слоя абразивными частицами. Интенсивность шаржирования зависит от твёрдости обрабатываемого материала, давления и времени доводки.
Таблица 2.9 Количество доводочных операций и припуски на доводку
Требуемая |
Требуемая |
Количество |
Припуск на |
||
шероховатость Ra, |
|||||
точность, мкм |
операций |
доводку, мм |
|||
мкм |
|||||
|
|
|
|
||
3,0 – 0,5 |
0,16 |
1 |
0,03 |
– 0,05 |
|
1,0 – 2,0 |
0,08 |
1 |
0,03 |
– 0,05 |
|
2 |
0,005 – 0,01 |
||||
|
|
||||
|
|
1 |
0,03 |
– 0,05 |
|
0,2 – 0,5 |
0,04 |
2 |
0,005 – 0,01 |
||
|
|
3 |
0,002 |
– 0,003 |
|
|
|
1 |
0,03 |
– 0,05 |
|
0,1 – 0,3 |
0,01 – 0,02 |
2 |
0,005 – 0,01 |
||
3 |
0,002 |
– 0,003 |
|||
|
|
||||
|
|
4 |
0,0005 – 0,001 |
Для доводки стального и в отдельных случаях твердосплавного инструмента используют пасты ГОИ, представляющие собой окись хрома,
приготовленную из хромпика с серой и добавкой жировой части, силикагеля и керосина. Пасты ГОИ выпускают в виде круглых тюбиков, на этикетках которых указаны сорт и полирующая способность пасты, зависящая от
43
размеров зёрен. Полирующая (или шлифующая) способность пасты ГОИ определяется толщиной слоя, снимаемого настой с пластины из закалённой стали размером 35x9мм при доводке её на плоском чугунном притире размером
400x400мм после 100 движений, соответствующих 40м пути.
Состав и содержание составляющих пасты ГОИ |
Таблица 1.18 |
|||
|
||||
трёх её основных сортов |
|
|||
Наименование основных частей |
Содержание составляющих в % в пастах |
|||
Грубой |
Средней |
|
тонкой |
|
|
|
|||
Окись хрома (прокаленная) |
88 |
79 |
|
74 |
Стеарин |
10 |
15 |
|
20 |
Олеиновая кислота |
- |
2 |
|
2 |
Силикагель |
- |
1,8 |
|
1,8 |
Сода двууглекислая |
- |
0,2 |
|
0,2 |
Керосин |
2 |
2 |
|
2 |
Разные растворимые соли |
|
Следы |
|
|
Посторонние включения |
|
Не допускаются |
|
Пасты ГОИ изготавливают трёх основных сортов: грубая, средняя и тонкая. Состав их указан в таблице 1.18. Три сорта этой пасты химико-
механического действия применяют в зависимости от требований к шероховатости обрабатываемых поверхностей. В таблице 1.19 указана производственно-техническая характеристика паст ГОИ.
Таблица 1.19 Производственно-техническая характеристика паст ГОИ
Производственно- |
|
Показатели для паст |
|
|
техническая |
Грубой |
Средней |
Тонкой |
|
характеристика |
||||
|
|
|
||
Полирующая или |
|
|
|
|
шлифующая |
18 – 40 |
8 – 17 |
1 – 7 |
|
способность |
||||
|
|
|
||
(зернистость) в мкм |
|
|
|
|
Размер тюбика в мм: |
35-38 |
25-27 |
20-22 |
|
диаметр |
||||
высота |
48-52 |
48-52 |
48-52 |
|
Цвет |
Темно-зеленый |
Темно-зеленый |
Светло-зеленый |
|
(почти черный) |
||||
|
|
|
||
|
Обдирочная работа, |
|
|
|
|
выравнивание |
Доводочные работы, |
Окончательная доводка, |
|
Применение |
поверхностей, снятие |
|||
снятие штрихов после |
изготовление шлифов, |
|||
грубых царапин (часто |
||||
|
грубой пасты |
полирование |
||
|
применяется вместо |
|||
|
|
|
||
|
шабрения) |
|
|
|
Качество поверхности |
Матовая поверхность |
Полузеркальная |
Зеркальная поверхность |
|
после обработки |
поверхность без |
|||
без резких царапин |
оптической точности |
|||
пастой ГОИ |
заметных царапин |
|||
|
|
44
Кроме паст ГОИ для доводки инструмента из инструментальных сталей и оснащённого твёрдым сплавом и минералокерамикой применяют пасты, состав и назначение которых указаны в таблице 1.20.
Полировальные пасты, предназначенные преимущественно для получения хорошей чистоты поверхности под хромирование и другие виды антикоррозионного или декоративного покрытия, указаны в таблице 1.21.
В качестве абразивов для изготовления доводочных паст ИПМ АН Украины были предложены порошки карбидотитана (полученного по специальной технологии – самораспространяющегося высокотемпературного синтеза-СВС) и гексанита-А.
При изготовлении паст из этих материалов в состав композиции входят:
классифицированные по зернистости порошки, связующие и поверхностно-
активные вещества (в качестве которых используют натуральные и синтетические жирные кислоты и их производные - мыла, воски, спирты; а
также различные углеводороды, гликоли и их производные, полимеры и др.).
Составы паст и соотношение компонентов зависят от конкретных условий их применения.
Выпускаются пасты на жировой и водорастворимой основах в мазеобразном (расфасованные в тубы) и твёрдом состоянии (в виде карандашей).
Содержание порошков гексанита-А или карбида титана в пастах колеблется в широких пределах от 5-10 до 30-70мас.%. Условное обозначение паст из микропорошка карбида титана зернистостью 10/7 при нормальной концентрации: КТ 10/7 НОМ. Применение паст на основе этих материалов позволяет повысить в 1,5-2 раза производительность труда на доводочных операциях; уменьшить шероховатость обработанных поверхностей; увеличить в 1,5 раза стойкость инструмента; а также снизить степень шаржирования абразива в обработанную поверхность.
По доводке мерительного инструмента (калибров, концевых мер)
применение паст КТ по сравнению с алмазными и абразивными пастами ГОИ
45
соответствующей зернистости позволило повысить производительность до
двух раз.
Таблица 1.10 Состав и назначение паст для доводки режущих инструментов
Характеристика пасты |
Компоненты |
Примечание |
||
Наименование |
Содержание, |
|||
|
% |
|
||
|
|
|
||
|
Для инструмента из сталей |
|
||
|
Электрокорунд, |
60 |
|
|
Твердая |
корунд или карбид |
|
|
|
(брикетизированная) |
кремния |
|
Для предварительной |
|
химико-механического |
Стеарин или |
35 |
доводки |
|
воздействия |
парафин |
|
|
|
|
Олеиновая кислота |
5 |
|
|
Твердая |
Электрокорунд или |
70 |
Преимущественно для |
|
(брикетизированная), |
корунд |
|
||
|
инструментов из |
|||
химико-механического |
Парафин |
28 |
||
быстрорежущей стали |
||||
воздействия |
Олеиновая кислота |
2 |
||
|
||||
|
Карбид кремния |
35 |
|
|
|
зеленый (или |
|
|
|
Мазеобразная |
черный) |
|
Для доводки и |
|
Мыло зеленое |
22 |
полирования |
||
|
||||
|
Воск технический |
10 |
|
|
|
Вода |
33 |
|
|
Для инструмента, оснащенного твердым сплавом и металлокерамикой |
||||
|
Карбид кремния |
58-59 |
|
|
Мазеобразная, |
зеленый |
|
Для доводки |
|
механического |
Вазелин |
38-39 |
||
(малопроизводительна) |
||||
воздействия |
технический |
|
||
|
|
|||
|
Парафин |
2-3 |
|
|
Твердая, механического |
Карбид бора или |
85 |
Для доводки и |
|
порошок В-1 |
|
полирования |
||
действия |
|
|||
Парафин |
15 |
(высокопроизводительна) |
||
|
||||
Твердая, механического |
Карбид бора |
85 |
Для доводки и |
|
Парафин |
13 |
полирования |
||
действия |
||||
Олеиновая кислота |
2 |
(высокопроизводительна) |
||
|
Доводка (притирка) с использованием паст производится с помощью чугунных притиров (материал СЧ18), на поверхность которых равномерно наносится слой пасты ~ 100мг. Удельное давление не должно превышать
0,75*105 Па, продолжительность доводки (притирки) составляет 5-6 мин, так как по истечении этого времени зерна измельчаются и производительность резко падает. Скорость вращения (движения) притира при механической обработке должна составить 5-10м/мин.
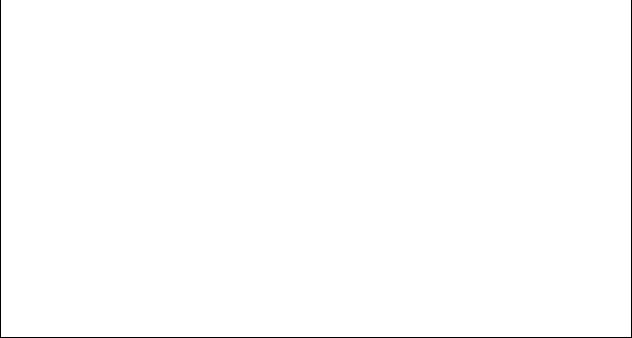
46
Таблица 1.21 Составные части паст (по массе) для различных видов обработки
|
Окончательное |
Предварительное полирование |
|
Тонкое |
||||
|
полирование |
полирование |
||||||
|
|
|
|
|||||
Наименование |
|
Цветных металлов |
Сильнорежущей пастой |
Слаборежущей пастой |
Под хромирование |
I стадии |
|
II стадии |
составных |
Стали |
|
||||||
частей |
|
|||||||
|
|
|||||||
|
|
|
|
|
|
|
|
|
Олеин |
12 |
1 |
20 |
- |
- |
- |
|
- |
Стеарин |
2-6 |
3 |
15 |
1 |
1-0 |
- |
|
- |
Парафин |
- |
- |
6 |
- |
- |
1 |
|
- |
Воск пчелиный |
- |
- |
- |
1 |
1-2 |
- |
|
1 |
Говяжье сало |
- |
2 |
- |
- |
- |
1,5 |
|
25 |
Абразив |
1 |
13 |
35-40 |
До 5 |
5-8 |
12 |
|
1 |
(1) |
(1) |
(2) |
(3) |
(4) |
(5) |
|
(5) |
|
|
|
Условные обозначения абразива: – венская известь; (2) – окись железа; (3) – окись хрома;
(4) – окись алюминия; (5) – наждачная пыль
Рекомендации по выбору зернистости применяемой пасты в зависимости от вида обработки и требуемой шероховатости приведены в таблице 1.22.
Наиболее эффективно применение рассмотренных паст КТ и из гексанита-А на доводке о полировании деталей авиационной техники,
прецизионных подшипников, запорно-тормозной аппаратуры, узлов пневмоприводов (кранов, вентилей, клапанов), а также инструментальной оснастки. Тубы с пастами рекомендуется хранить при температуре от -10 до
+25 °С. Алмазные микропорошки, на основе которых изготовляют и выпускают алмазные доводочные пасты, получили широкое распространение на доводочных операциях.
|
|
|
Таблица 1.22 |
|
Рекомендации по выбору зернистости пасты |
||||
Вид обработки |
Зернистость пасты |
Шероховатость поверхности Ra, мкм |
||
До обработки |
После обработки |
|||
|
|
|||
Черновая доводка |
160/125 – 50/40 |
1,5 |
0,32 |
|
Получистовая |
60/40 – 14/10 |
0,2 |
0,1 |
|
доводка |
||||
|
|
|
||
Чистовая доводка |
14/10 – 3/2 |
0,063 |
0,032 |
|
Полирование |
3/2 – 1/0 |
0,025 |
0,01 |
47
Данные о концентрации и работоспособности алмазных паст нормальной
(Н) и повышенной (ПО) абразивной способности приведены в таблице 1.23.
|
|
|
Алмазные пасты (ГОСТ 16877-71) |
|
Таблица 1.23 |
|||||||
|
|
|
|
|
|
|
||||||
|
Концентрация |
Количество |
|
Концентрация |
|
Количество |
||||||
|
алмазов в |
|
|
|||||||||
|
алмазов, % по |
|
алмазов, % по |
|
алмазов в 1г |
|||||||
Зернистость |
1г пасты, |
Зернистость |
|
|||||||||
|
|
массе |
карат |
|
массе |
|
|
пасты, карат |
||||
|
|
|
|
|
|
|
|
|
|
|
||
|
Н |
|
П |
Н |
П |
|
Н |
|
П |
|
Н |
П |
60/40 |
10 |
|
20 |
0,5 |
1,0 |
7/5 |
3 |
|
6 |
|
0,15 |
0,3 |
40/28 |
7 |
|
14 |
0,35 |
0,7 |
5/3 |
2 |
|
4 |
|
0,1 |
0,2 |
28/20 |
7 |
|
14 |
0,35 |
0,7 |
3/2 |
2 |
|
4 |
|
0,1 |
0,2 |
20/14 |
5 |
|
10 |
0,25 |
0,5 |
2/1 |
1 |
|
2 |
|
0,05 |
0,1 |
14/10 |
5 |
|
10 |
0,25 |
0,5 |
1/0 |
1 |
|
2 |
|
0,05 |
0,1 |
В таблице 1.24 приведены некоторые данные об алмазных пастах. |
|
|
Алмазные пасты (ГОСТ 16877-71) |
Таблица 1.24 |
||
|
|
|||
Обрабатываемый |
|
Пасты с алмазами |
|
|
материал |
АСМ40 |
АСМ20 |
АСМ3 |
АСМ2 |
Сталь: |
|
|
|
|
инструментальная |
0,02 |
0,018 |
0,021 |
0,020 |
быстрорежущая |
0,028 |
0,024 |
0,026 |
0,026 |
Твердый сплав |
0,024 |
0,022 |
0,025 |
0,025 |
После доводки (притирки) изделия необходимо тщательно очистить от шаржированного абразива. В качестве разбавителей паст на жировой основе рекомендуется использовать машинное и авиационное масло, керосин, бензин; а
паст на водорастворимой основе - спирт или воду. Очистку обработанных деталей, работающих в узлах трения (плунжерные пары), проводят в таком порядке: протирание ветошью с последующей промывкой в бензине (для паст с жировой основой), мягкой щёткой; окончательная промывка в 1%-м растворе кальцинированной соды с помощью ультра звука (для чего используется ультразвуковой низкочастотный диспергатор типа УЗДН-1). Акустическая мощность экспоненциального излучения 75Вт/см2, резонансная частота 22кГц,
продолжительность 3мин.
Помимо указанных способов доводки и полирования неукреплёнными абразивными зёрнами, доводку и полирование некоторых инструментов можно