
- •Оглавление
- •Предисловие
- •Глава 1. Общие вопросы заточки режущих инструментов
- •1.3 Заточные станки
- •1.4 Вопросы для контроля
- •Глава 2. Исследование конструкций резцов
- •2.1 Назначение, типы и конструктивные особенности
- •2.2 Конструктивные элементы резца
- •2.3 Геометрические параметры резца
- •2.4. Износ, критерий затупления и число переточек резцов
- •2.6 Вопросы для контроля
- •Глава 3. Исследование конструкций спиральных свёрл
- •3.1 Назначение, типы и конструктивные особенности
- •3.2 Методы заточки спиральных сверл
- •3.4 Вопросы для контроля
- •Глава 4. Исследование конструкций зенкеров
- •4.1 Назначение, типы и конструктивные особенности
- •4.2 Износ и затачивание зенкеров
- •4.4 Вопросы для контроля
- •5.1 Назначение, типы и конструктивные особенности
- •5.2 Выбор основных параметров
- •5.3 Износ и затачивание разверток
- •5.5 Вопросы для контроля
- •Глава 6. Исследование конструкций фрез
- •6.1 Назначение, типы и конструктивные особенности
- •6.2 Износ и восстановление фрез
- •6.3 Лабораторная работа «Конструкция фрез»
- •6.4 Вопросы для контроля
- •6.6 Вопросы для контроля
- •7.1 Исследование конструкций метчиков
- •7.1.1 Назначение, типы и конструктивные особенности
- •7.1.3 Вопросы для контроля
- •7.1.5 Вопросы для контроля
- •7.1.7 Вопросы для контроля
- •7.2 Исследование конструкций резьбонарезных головок
- •7.2.1. Назначение, типы и конструктивные особенности
- •7.2.3 Вопросы для контроля
- •Глава 8. Исследование конструкций зуборезных долбяков
- •8.1 Назначение, типы и конструктивные особенности
- •8.3 Вопросы для контроля
- •8.5 Вопросы для контроля
- •Глава 9. Исследование конструкций червячных фрез
- •9.1 Назначение, типы и конструктивные особенности
- •9.3 Вопросы для контроля
- •9.5 Вопросы для контроля
- •10.1 Назначение, типы и конструктивные особенности
- •10.3 Вопросы для контроля
- •10.5 Вопросы для контроля
- •10.7 Вопросы для контроля
- •10.9 Вопросы для контроля
- •10.11 Вопросы для контроля
- •11.1 Назначение, типы и конструктивные особенности
- •11.2 Алмазные сверла на связке «МонАлиТ»
- •11.3 Состояние рабочей поверхности сверла
- •11.4 Моделирование процесса алмазного сверления
- •11.5 Оценка режущей способности алмазных свёрл
- •11.7 Вопросы для контроля
- •12.1 Назначение и структура САПР
- •12.3 Вопросы для контроля
- •12.5 Вопросы для контроля
- •12.7 Вопросы для контроля
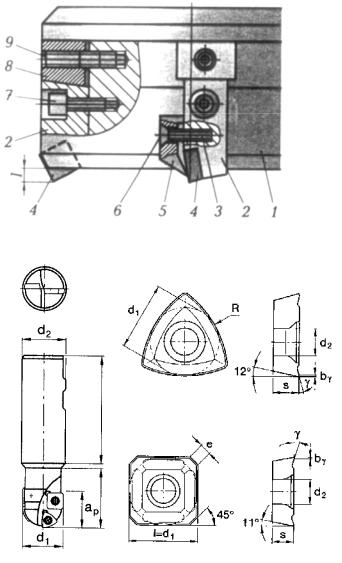
177
(рис.6.8,а). Некоторые фрезы могут работать с несколькими движениями Ds
подачи (рис.6.8, в, и, к), в том числе, с осевой подачей (рис. 6.8, в).
6.2 Износ и восстановление фрез
Фрезы в процессе обработки изнашиваются, в основном, по задней поверхности (рис.6.9). Величина износа характеризуется шириной ленточки износа hз. Возможен также, особенно при черновом фрезеровании,
превалирующий износ по передней поверхности (в форме лунки). Возможны и другие формы износа, например, округление кромки и ее микровыкрашивания
(последнее нежелательно).
Рис. 6.6 Фреза торцовая сборная со сменной пластиной из СТМ:
1-корпус; 2 –державка; 3, 6, 7, 9 – винты; 4- режущая пластина; 5- прихват; 8 –
клин; l – вылет пластины из корпуса
(регулируемый)
Рис. 6.7 Фреза концевая со сменными пластинами: а) размеры, б) геометрия пластин
а) |
б) |
178
Восстановление работоспособности фрез осуществляют перетачиванием
зубьев, либо сменой режущих кромок путем поворота пластин или их заменой
(для сборных фрез).
6.3 Лабораторная работа «Конструкция фрез»
Цель работы – практическое изучение основных конструктивных элементов фрез различного типа. В задачи работы входит изучение методов и средств формирования производящих поверхностей фрез, на которых расположены режущие кромки зубьев, анализ их геометрических параметров, а
также изучение схем обработки различными типами фрез.
Инструменты, оборудование и приборы. Для работы используются, в
основном, стандартные фрезы: цилиндрические (рис.6.1), торцовые (рис.6.2 и 6.3), концевые (рис. 6.4 и 6.7) и другие. Для анализа геометрии фрез и измерения отдельных геометрических параметров применяют штангенциркуль,
индикаторы, различные угломеры и инструментальные микроскопы (описание и перечень приведены выше в лабораторных работах по резцам, сверлам,
зенкерам).
Методы крепления фрез и движения резания при их эксплуатации изучают на имеющихся в лаборатории станках: универсально-фрезерном и трехкоординатном вертикально-фрезерном с ЧПУ мод.24К40СФ4 (модернизированном, с числом оборотов шпинделя до 10000 в мин, N=20кВт
(рис.6.15).
Методика выполнения работы
Работа выполняется в следующей последовательности. Изучают различные типы фрез, в том числе: цилиндрические, торцовые, концевые,
фасонные и их основные элементы: рабочую часть, корпус, крепежно-
присоединительную часть. Выполняют измерение наружного диаметра D,
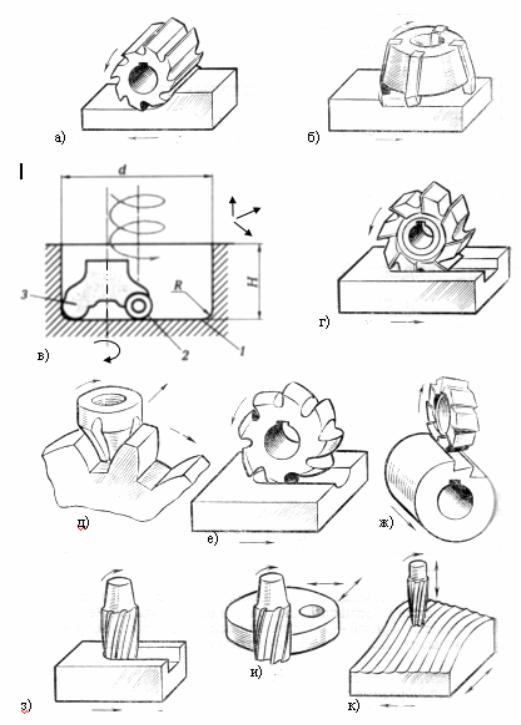
179
диаметра посадочного отверстия или хвостовика d, габаритных размеров,
рабочей части, геометрических параметров ( , , , , , 1; примеры – на рис.6.1; 6.2; 6.3).
Рис. 6.8 Типы фрез и движения резания
Выполняют эскизы фрез, на которых проставляют численные значения вышеуказанных размеров, а также число зубьев и указывают форму
180
производящей поверхности П, на которой расположены кромки фрезы
[например, цилиндрическая (рис. 6.1) или коническая (рис.6.2 и 6.3)].
На эскизе также указывают: тип фрезы, ее основные конструктивные характеристики (цельная, составная или сборная), марку инструментального материала (например, Р6М5).
Для сборной фрезы с СМП выполняют эскиз крепления пластин конкретной фрезы и основные элементы крепления (примерына рис.6.5 и 6.6).
На бланке (в форме рис.6.8, а –к ) для каждого вида фрезы и каждой схемы обработки указывают тип фрезы, схему фрезерования (цилиндрическое,
торцовое, встречное, попутное) и проставляют движения резания: Dr , Ds1, Ds2,
Ds3 … .
Содержание отчета
Отчет должен содержать:
1.Эскизы фрез с основными измеренными размерами и геометрическими параметрами.
2.Заполненный по форме рис.6.8 бланк.
6.4Вопросы для контроля
1.Какие конструктивные отличия имеют фрезы от других видов инструментов, - резцов; сверл; зенкеров ?
2.Какое движение называют главным при: торцовом фрезеровании; при цилиндрическом фрезеровании; при других видах фрезерования?
3.По каким признакам осуществляется классификация фрез?
4.Какие фрезы называют цельными, составными, сборными?
5.На каких станках и какими типами фрез может осуществляться обработка:
плоскости; паза; винтовой стружечной канавки цилиндрической фрезы;
181
отверстия; плоского фасонного контура; пространственного фасонного
контура?
6.Какую точность и шероховатость обеспечивает фрезерование?
7.Какие инструментальные материалы применяют для фрез?
8.Какой инструментальный материал можно использовать для торцовых фрез при обработке закаленной стали (HRC 60)?
9.Какими геометрическими параметрами характеризуются лезвия (зубья фрез):
торцовых; цилиндрических; концевых?
10. Как влияют на производительность число зубьев фрез, наружный диаметр,
частота вращения фрезы?
11.Как рассчитывают минутную подачу при фрезеровании?
12.Как осуществляется восстановление работоспособности фрез после их изнашивания?
6.5 Лабораторная работа
«Восстановление работоспособности и расчет ресурса фрез»
Цель и задачи работы. Цель работы - практическое изучение технологии восстановления фрез после их износа. В задачи работы входит: расчет ресурса фрез; изучение средств и методов восстановления работоспособности фрез после износа; контроль элементов фрез после восстановления.
Оборудование, инструменты, приборы. Для проведения работы используют: стандартные конструкции цельных и сборных фрез
(цилиндрических, концевых, торцевых); универсальный инструментальный микроскоп; угломеры; магнитные стойки с индикатором; эталоны (или прибор)
для оценки шероховатости после шлифования; фрезерный станок с ЧПУ (мод. 24К40СФ4 или иной, с малым, не более 10 мкм, биением шпинделя, рис.6.15);
шлифовально-заточной станок с ЧПУ (рис.6.12), либо универсально-заточной станок (мод. 3Д642Е или др.).
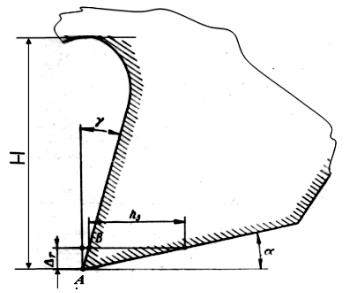
182
Методика выполнения работы
Расчет ресурса фрез. Критерии допустимого износа фрез различны
(время работы; качество обработанной поверхности; точность обработки,
величина износа и др.).
При достижении величины износа, например, по задней поверхности (hз,
рис.6.9), установленной нормативами как предельно допустимой, -
работоспособность фрезы восстанавливают. Если это невозможно (фреза полностью сточена; произошла поломка; поврежден или изношен корпус и др.), - фреза подлежит утилизации.
Рис. 6.9 Схема износа фрезы по задней поверхности
Ресурс Рф фрезы - мера, характеризующая количество продукции,
обработанной за весь срок эксплуатации фрезы. Этот срок учитывает работу фрезы после всех ее переточек (или замен кромок), вплоть до утилизации:
Рф= РфТ ( 1+k ),
где РфТ - ресурс фрезы за период ее стойкости (за период работы между двумя переточками); k- количество переточек; - коэффициент (меньше 1),
учитывающий случайную убыль (поломки, выкрашивания кромок, возможное снижение стойкости после переточки).
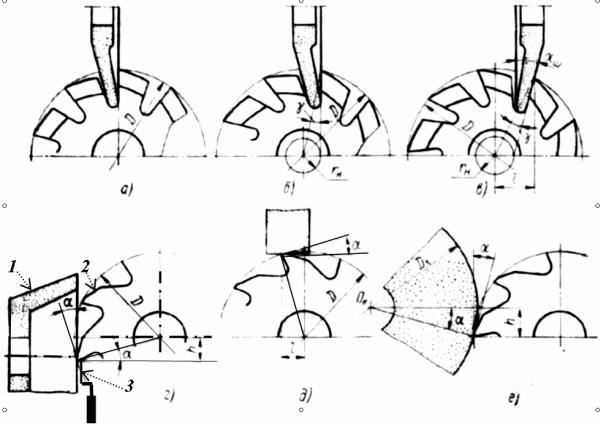
183
Рис. 6.10 Установка шлифовальных кругов при затачивании фрез
по передней (а,б,в) и по задней (г, д, е) поверхностям; г) 1- круг; 2- фреза; 3-упорка
Мера ресурса фрез может выражаться суммарной длиной (м) всех обработанных поверхностей; числом обработанных деталей данного типа (шт.),
объемом (м3) удаленного с заготовки материала и другими величинами.
Ресурс неразрывно связан с условиями эксплуатации фрез: видом и характером обработки, материалом заготовки и фрезы, режимами резания,
использованием СОЖ, жесткостью станка и инструмента, критерием допускаемого износа и его величиной, технологией восстановления инструмента после износа.
Общее число k допускаемых переточек (или, для неперетачиваемых фрез
– число замен кромок) приводится в справочной литературе [1],[4],[6] или в каталогах фирм, производителей инструмента.
Величина k может также рассчитываться, исходя из величины q
допустимого слоя стачивания при одной переточке и величины М суммарного допустимого слоя стачивания: k = M/q.
184
Число m периодов стойкости для новой фрезы составляет: m = k +1.
Для цельных фрез величина М ориентировочно принимается равной (0,3-
0,5)Н, где Н-высота зуба (рис.6.9). Для торцовых фрез с напайными твердосплавными пластинами прямоугольной формы, с длиной пластины вдоль
главной кромки lп и шириной пластины bп, величина M 0,5 bп при
перетачивании по главной задней поверхности; при перетачивании по вспомогательной задней поверхности М 0,5 lп
Величина q принимается: q r +0,1 (мм), где r = hз / (сtg - tg )
(рис.6.9); величина hз здесь принимается равной предельно допустимой и составляет для фрез из быстрорежущих сталей, при обработке конструкционных сталей:
Для цилиндрических фрез |
0,4-0,6мм; |
(0,5-0,6); |
Для торцовых |
1 -2мм; |
(1-1,2); |
Для трехсторонних |
0,4-0,6мм; |
(1 -1,2); |
Для концевых |
0,2 -0,5мм; |
(0,3-0,5). |
В скобках приведены предельные величины hз для твердосплавных фрез.
Меньшие значения hз принимаются для фрез меньшего диаметра и при повышении требований к точности и качеству обработки.
hз (сtg - tg ) Н М lп bп.
Приведем примеры расчета ресурса фрез разного типа.
Пример 1.
Дисковая двуугловая (аналог – на рис.6.8,е) фреза с диаметром D = 63мм,
из стали Р6М5 (с покрытием), - при обработке конструкционных сталей с твердостью НВ 180 -200, при глубине резания t = 5мм, подаче на зуб Sz = 0,08мм, скорости резания = 40м/мин, охлаждение эмульсией,- имеет нормативный период стойкости T= 60 мин, при допустимой величине износа по задней поверхности h3= 0,7мм. Общее число переточек k = 12 (при глубине стачивания 0,35-0,4мм за одну переточку). При числе зубьев z=20, числе оборотов фрезы 202 в мин, минутная подача SM составит: sM=0,08· 202· 20= 323,2мм/мин.
185
За период стойкости Т длина пути резания L (т.е. длина обработанной поверхности заготовки, включая длину врезания и перебега) составит:
323,2 · 60 = 19392мм, т.е. ресурс Рф = 19,39 м.
При = 0,95 и k =12 :
Рф = 19,39 (1+12· 0,95) = 240,4 м.
Для расчета ресурса фрезы, выраженного количеством обработанных деталей, следует дополнительно задаться величинами: длиной детали, глубиной профиля детали, длинами врезания и перебега, числом проходов (если обработка конкретной детали осуществляется за два или более прохода).
Пример 2.
Для сборных фрез со сменной режущей частью, которую не перетачивают, например, со СМП (рис.6.4, 6.5, 6.6) ресурс фрезы определяют с учетом числа n кромок на одной пластине и с учетом общего числа N замен всего комплекта пластин.
Если ресурс одной кромки фрезы (в мин. основного времени) составляет
Рфк, то ресурс фрезы:
Рф= Рфк · · n · ( N+1) .
Двусторонняя СМП квадратной формы, установленная в корпусе фрезы,
имеет 8 кромок, т.е. n=8. Одновременно в корпусе установлено 3 пластины, а в комплекте имеется еще 15 пластин. Число возможных замен составит
N= 15/3 = 5.
При Рфк = 20 мин, = 0,9 , n=8 , N = 5 :
Рф= 20 · 0,9 · 8 · (5+1) = 864 мин.
Технология затачивания фрез
При изготовлении зубья цельных и составных фрез затачивают по передней и задней поверхностям. В сборных конструкциях фрез со СМП могут использоваться шлифованные или нешлифованные пластины. Технология затачивания оказывает большое влияние на точность и стойкость фрез.
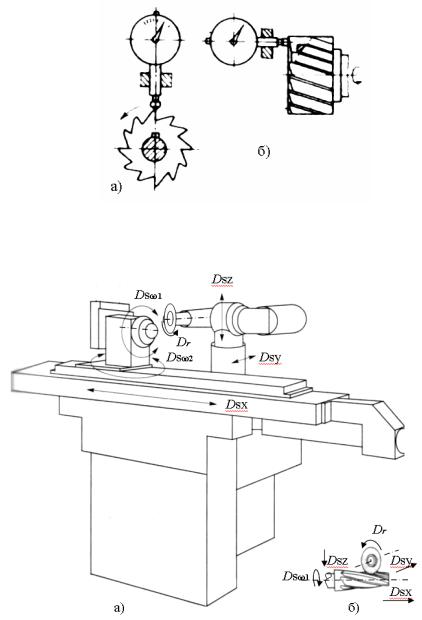
186
Затачивание новых и изношенных фрез (перетачивание) осуществляют абразивными, алмазными и эльборовыми кругами различной формы. По передней поверхности перетачивают затылованные зубья (рис.6.10, а, б, в); по задней поверхности - острозаточенные (рис.6.10, г, д, е).
После затачивания контролируется шероховатость передней и задней поверхностей (Ra = 1,2 – 0,3), геометрия (углы , , и др.), форма кромок,
радиальное (рис.6.11,а) и торцовое (рис.6.11,б) биение кромок.
Рис. 6.11 Схема измерения биения кромок фрезы:
а)- радиального; (б) –торцового
Рис. 6.12 Движения резания на пятикоординатном шлифовально-заточном станке с ЧПУ (а) и
схема заточки концевой конической фрезы с винтовыми зубьями по передней поверхности (б)
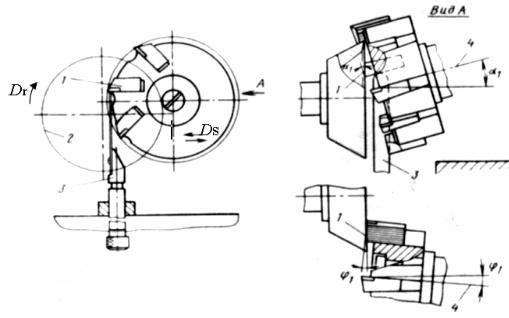
187
При контроле геометрии могут быть использованы различные методы и приборы.
Если выполнен контроль заднего угла os в осевом сечении (по двум точкам, в которых фиксируют показания индикатора) и задана ширина bn
спинки зуба в нормальном сечении (точнее, ширина участка между двумя точками в нормальном сечении задней поверхности зуба, на которой определяется задний угол), то угол рассчитывают из уравнений [5]:
=arc tg[(r-Ccos )/C sin ], где:
C=bncos /sin ; = bn sin tg /r+ , r=0,5D ,
- угловой параметр, который рассчитывается как корень уравнения: [r- (bn sin +r ctg ) tg os] sin - bn cos = 0
Рис. 6.13 Схема заточки торцовой фрезы по вспомогательной задней поверхности: 1- шлифуемая поверхность; 2- крайнее положение шлифовального круга; 3 – упорка; 4 – ось фрезы; Dr - главное движение ( вращение круга); Ds – движение продольной подачи.
Шлифование по передней и задней поверхностям зубьев некоторых типов фрез (например, концевых конических с винтовыми зубьями; борфрез)
осуществляют на многокоординатных шлифовальных станках с ЧПУ (рис. 6.12,
а, б). Такие станки обеспечивают высокое качество шлифования по всем контролируемым параметрам.

188
Рис. 6.14 Измерение биения фрезы на вертикально-фрезерном станке с ЧПУ:
а) рабочая зона станка; б) часть рабочей зоны (увеличено); 1- фреза концевая; 2-патрон; 3-
шпиндель; 4- индикатор; 5- удлинитель магнитной стойки; 6 – магнитная стойка: 7 – стол станка: 8 – рабочая часть фрезы; 9 – хвостовик фрезы; 10 – измерительный наконечник индикатора.
Например, движение подачи Dsy позволяет выдержать заданный передний
угол фрез вдоль всей ее рабочей части. Движения Ds 1 и Dsx , осуществляемые
по программе станка, позволяют получать не только винтовые зубья с
постоянным, но и с переменным осевым шагом. Это способствует
189
уменьшению вибраций фрез при обработке, а также позволяет улучшить геометрию зубьев и форму стружечных канавок фрезы.
Затачивание фрез на универсально - заточных станках осуществляют с использованием специальных приспособлений. Для торцовых фрез применяют поворотную головку (рис. 6.13), которую устанавливают на стол заточного станка.
Биение кромок фрез после затачивания (рис.6.11) измеряют в специальном устройстве, либо на станке (рис.6.14, а и б). При контроле на станке на измеренную величину биения кромок фрезы оказывает влияние также биение шпинделя станка.
Радиальное биение шпинделя составляет на станках с ЧПУ около 0,01мм
(на прецизионных высокоскоростных станках до 1 мкм и менее).
Биение хвостовых (например, концевых фрез) измеряют по хвостовику
(рис.6.14, а, б) и по кромкам (рис. 6.11).
Величина биения кромок фрез разного типа влияет на шероховатость обработанной поверхности, ее точность и на стойкость фрез. Предельная ее величина указывается в технических требованиях и составляет для фрез разного типа, размеров и исполнения 0,001 – 0,1мм. Большие величины относятся к фрезам больших диаметров и предназначенных для черновой обработки.
Затылованные зубья с плоскими передними поверхностями перетачивают торцом шлифовального круга (рис.6.10, а и б); при наличии переднего угла 0 (или <0 ) смещение rп торца круга относительно оси фрезы рассчитывают: rп = 0,5 D sin (рис.6.10, б).
Винтовые передние поверхности перетачивают конической поверхностью шлифовального круга (рис.6.10, в); при этом ось круга разворачивают относительно нормали к оси фрезы приблизительно на угол наклона винтовой линии зуба (рис. 6.12, б).
Затачивание зубьев острозаточенных фрез по задней поверхности может осуществляться торцом шлифовального круга (рис. 6.10,г); вершина зуба при
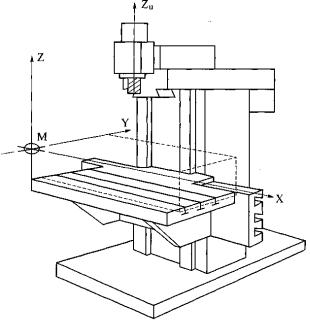
190
этом устанавливается ниже горизонтальной осевой плоскости фрезы на величину h:
h = 0,5 Dр sin , где - задний угол фрезы в ее торцевом сечении; Dр –
расчетный диаметр фрезы, равный фактическому (с учетом предыдущих перетачиваний) наружному диаметру фрезы.
На станках с ЧПУ (рис. 6.12, а) величина h устанавливается предварительной настройкой, путем поворота инструментального шпинделя
(движение Ds ) и перемещением стола станка относительно шлифовального круга вдоль оси x (движение Dsx).
Рис. 6.15 Трехкоординатный вертикальнофрезерный станок с ЧПУ: Zи – ось шпинделя (ось фрезы); X, У, Z – оси координат движений подач
(Dsx, Dsy, Dsz); т.М – базовая точка отсчета координат; Ф – концевая фреза.
На универсально-заточном станке (мод. 3Д642Е и др.) величина h
устанавливается с помощью приспособлений с упоркой (рис.6.10, г).
Настройка приспособления осуществляется так же, как при затачивании развертки по задней поверхности (см. гл.5):
- на стол станка устанавливают штангенрейсмус; в центрах станка закрепляют цилиндрическую оправку с диаметром dо;
191
- снимают оправку со станка, сдвигают планку штангенрейсмуса вниз на величину
(0,5 dо +h); после этого на шкале штангенрейсмуса должно быть показание,
равное:
Но - (0,5 dо +h), где h – расчетная величина смещения зуба фрезы
(рис.6.10,г); в таком положении закрепляют планку штангенрейсмуса;
-устанавливают фрезу на станке (насадную – на оправке в центрах; закрепляют центра);
-вертикальным перемещением стола станка устанавливают в определенное положение шлифовальный круг относительно фрезы; примерное положение круга показано на рис. 6.10,г; ось круга не обязательно проходит ниже линии центров на величину h , возможны разные варианты установки с учетом длины фрезы;
-шпиндель шлифовального круга разворачивают на 2-30 вокруг вертикальной оси, чтобы торец круга не был параллелен оси фрезы; направление вращение круга должно быть таким, чтобы силы резания при шлифовании прижимали зуб фрезы к упорке;
-упорку 3 (рис.6.10,г) устанавливают так, чтобы ее верхний конец упирался в планку штангенрейсмуса; в таком положении ее закрепляют, верхний край упорки расположен ниже линии центров (оси фрезы) на величину h;
-прижимают переднюю грань зуба фрезы к упорке, делают пробные проходы с одновременной ручной поперечной подачей стола с фрезой (до «искры», т.е. до касания зуба с кругом);
-устанавливают ограничители хода при продольной (вдоль оси фрезы) подаче стола станка, обеспечивая возможность шлифования зуба по всей длине;
-сообщают поперечную подачу (перпендикулярно оси фрезы) столу станка на глубину резания первого прохода;
-шлифуют последовательно все зубья фрезы;
-выполняют шлифование зубьев второго, третьего… окончательного прохода.

192
При наличии на фрезе винтовых зубьев с углом наклона (см.рис.6.2)
дополнительно учитывают направление продольной подачи; оно выбирается таким, чтобы при продольном перемещении фрезы относительно круга в
процессе шлифования фреза получала вращательное движение от упорки.
Расчет суммарной (при всех проходах ) глубины q снимаемого слоя приведен выше (cм. расчет ресурса фрезы). Общее число проходов при затачивании
одного зуба фрезы рассчитывают:
припуск пр на предварительные проходы: пр = q - чист, где чист –
припуск на чистовые проходы и доводку (если она выполняется). чист =
(1…3) tчист + 0,005мм, т.е. число чистовых проходов 1..3; 0,005мм – припуск
на доводку. Ориентировочно tчист = 0,01 – 0,02мм; число предварительных проходов равно пр/tпр, где tпр = 0,02 – 0,08; (tпр и tчист - поперечная подача в мм/дв.ход на предварительных и чистовых проходах соответственно);
сумма предварительных, чистовых проходов и прохода на доводку и выхаживание (выхаживание осуществляют с нулевой глубиной резания) дает общее число проходов.
Продольная подача принимается в пределах 0,5 – 6м/мин (меньшие значения - для доводки и при чистовых проходах, а также при ручной подаче и при меньших размерах фрез). Более точные рекомендации приводятся выше ( в
разделе «Общие рекомендации») и учитывают марку круга и материал фрез.
Для затачивания фрез из быстрорежущих сталей используются круги из
электрокорунда и эльборовые; скорость резания = 20-30 м/c.
Для затачивания твердосплавных фрез применяют алмазные круги ( =
25-40 м/c), а также круги из карбида кремния ( = 10-18) м/c.
После затачивания производится контроль параметров, перечисленных
выше (см. рис.6.11; 6.14). |
|
Затачивание зубьев торцовых фрез по задней поверхности |
на |
универсальнозаточном станке осуществляют торцом круга с использованием поворотной головки, в которой закрепляется фреза (насадная – с помощью оправки) (рис. 6.13).
193
Затачиваемый зуб 1 фрезы упирается свей передней поверхностью в упорку 3.
На рис.6.13 показана установка фрезы при затачивании вспомогательной задней поверхности: фреза разворачивается в двух плоскостях относительно торца круга 2 на углы 1 и 1. После затачивания формируется вспомогательная задняя поверхность и вспомогательная кромка АС (см. рис. 6.2).
Размер q общего снимаемого при затачивании слоя (см.рис.6.9), глубину t (поперечную подачу Sпоп), общее число проходов рассчитывают по методике,
приведенной выше для цилиндрических фрез. Марку круга, продольную подачу Sпр, скорость резания - назначают в соответствии с общими рекомендациями.
После затачивания производят контроль геометрических параметров
(углов , , , 1 и 1) радиального (рис.6.11,а) и торцового (рис.6.11,б) биения кромок. Фиксируют общее биение кромок (разницу между максимальным и минимальным показаниями индикатора за оборот фрезы) и биение соседних зубьев. Результаты контрольных измерений заносят в протокол.
Содержание отчета
Отчет должен содержать:
1. Расчет ресурса фрезы заданного типа.
Исходные данные включают: тип фрезы, диаметр D, число зубьев, эскиз зуба и износа (пример – на рис.6.9); способ восстановления (перетачивание,
либо поворот и смена пластин); коэффициент .
Для перетачиваемых фрез - величины: hз , , , Н, М; для напайных твердосплавных напайных пластин (перетачиваемых), а также размеры пластины: длина lп, ширина bп .
Для неперетачиваемых с СМП - величины n, N, Рфк .
По методике, приведенной выше (п. 6.4.3.1) производится расчет Рфк.
Исходные данные, расчет и полученный результат заносятся в отчет.