
- •Оглавление
- •Предисловие
- •Глава 1. Общие вопросы заточки режущих инструментов
- •1.3 Заточные станки
- •1.4 Вопросы для контроля
- •Глава 2. Исследование конструкций резцов
- •2.1 Назначение, типы и конструктивные особенности
- •2.2 Конструктивные элементы резца
- •2.3 Геометрические параметры резца
- •2.4. Износ, критерий затупления и число переточек резцов
- •2.6 Вопросы для контроля
- •Глава 3. Исследование конструкций спиральных свёрл
- •3.1 Назначение, типы и конструктивные особенности
- •3.2 Методы заточки спиральных сверл
- •3.4 Вопросы для контроля
- •Глава 4. Исследование конструкций зенкеров
- •4.1 Назначение, типы и конструктивные особенности
- •4.2 Износ и затачивание зенкеров
- •4.4 Вопросы для контроля
- •5.1 Назначение, типы и конструктивные особенности
- •5.2 Выбор основных параметров
- •5.3 Износ и затачивание разверток
- •5.5 Вопросы для контроля
- •Глава 6. Исследование конструкций фрез
- •6.1 Назначение, типы и конструктивные особенности
- •6.2 Износ и восстановление фрез
- •6.3 Лабораторная работа «Конструкция фрез»
- •6.4 Вопросы для контроля
- •6.6 Вопросы для контроля
- •7.1 Исследование конструкций метчиков
- •7.1.1 Назначение, типы и конструктивные особенности
- •7.1.3 Вопросы для контроля
- •7.1.5 Вопросы для контроля
- •7.1.7 Вопросы для контроля
- •7.2 Исследование конструкций резьбонарезных головок
- •7.2.1. Назначение, типы и конструктивные особенности
- •7.2.3 Вопросы для контроля
- •Глава 8. Исследование конструкций зуборезных долбяков
- •8.1 Назначение, типы и конструктивные особенности
- •8.3 Вопросы для контроля
- •8.5 Вопросы для контроля
- •Глава 9. Исследование конструкций червячных фрез
- •9.1 Назначение, типы и конструктивные особенности
- •9.3 Вопросы для контроля
- •9.5 Вопросы для контроля
- •10.1 Назначение, типы и конструктивные особенности
- •10.3 Вопросы для контроля
- •10.5 Вопросы для контроля
- •10.7 Вопросы для контроля
- •10.9 Вопросы для контроля
- •10.11 Вопросы для контроля
- •11.1 Назначение, типы и конструктивные особенности
- •11.2 Алмазные сверла на связке «МонАлиТ»
- •11.3 Состояние рабочей поверхности сверла
- •11.4 Моделирование процесса алмазного сверления
- •11.5 Оценка режущей способности алмазных свёрл
- •11.7 Вопросы для контроля
- •12.1 Назначение и структура САПР
- •12.3 Вопросы для контроля
- •12.5 Вопросы для контроля
- •12.7 Вопросы для контроля
301
где А1 = 160 : 100= 1,6.
10.Действия, аналогичные п. 9, выполняют с контрольными оправками
№5 и 6.
На основании п. 9–10 определяют влияние точности изготовления инструмента с цилиндрическим хвостовиком на точность их позиционирования.
По результатам работы (п. 5 – 7 и 9 – 11) делают вывод о влиянии конструкции хвостовиков инструмента (конус Морзе или цилиндрические поверхности) на точность позиционирования инструмента.
11.Запись и обработку полученных данных производят в соответствии
стабл. 10.4.
Содержание отчета. В отчете приводят эскизы переходной втулки, контрольных оправок № 1–3, державки, контрольных оправок № 4–6, схемы измерений, запись результатов работы с необходимыми расчетами (табл. 10.4) и заключение о влиянии конструкции и точности изготовления хвостовиков режущего и вспомогательного инструмента на точность позиционирования.
Указать, для каких видов инструмента можно рекомендовать конструкции и точность изготовления исследованных хвостовиков.
10.7 Вопросы для контроля
1. Какие элементы конструкции инструментальных блоков влияют на точность позиционирования инструмента?
Варианты ответов: 1) номинальные размеры хвостовиков с конусом 7 :
24; 2) номинальные размеры конусов Морзе; 3) номинальные размеры цилиндрических хвостовиков; 4) вылет режущего инструмента относительно торца вспомогательного инструмента; 5) точность изготовления присоединительных поверхностей режущего и вспомогательного инструмента.
302
2. При какой степени точности конусов Морзе обеспечивается
минимальное биение режущих кромок инструмента в инструментальном
блоке?
Варианты ответов: 1) АТ5; 2) АТ6; 3) АТ7; 4) ΛΤ8; 5) АТ9.
10.8 Лабораторная работа
«Исследование влияния конструкций и точности изготовления присоединительных поверхностей режущего и вспомогательного инструмента на податливость инструментальных блоков»
Работа направлена на изучение эксплуатационных возможностей вспомогательного инструмента и раскрывает качественные и количественные характеристики податливости инструментальных блоков.
В работе изучается податливость инструментальных блоков и инструмента с коническими и цилиндрическими хвостовиками в зависимости от точности их изготовления.
Погрешности размеров деталей, вызываемые деформацией инструментальных блоков, составляют более половины суммарной погрешности обработки, поэтому жесткость (или обратная ее величина – податливость) инструментальных блоков является важнейшей характеристикой качества вспомогательного инструмента.
Вспомогательный инструмент, как элемент технологической оснастки,
под действием сил резания испытывает деформацию двух видов: объемную деформацию деталей (изгиб, кручение) и деформацию контактных поверхностей (смещение· на краю стыков и поворот осей контактных поверхностей) в местах соединений. Первый вид деформаций определяется по формулам курса "Сопротивление материалов". Контактная жесткость также определяет величину деформации в месте приложения сил и зависит от конструкции и точности изготовления присоединительных поверхностей.

303
Контактную деформацию в местах стыка под действием силы Р,
приложенной на расстоянии L от конца стыка, определяют по формуле
y = δ0+θ L, |
(10.5) |
где δ0–смещение на краю стыка в результате контактной податливости; θ – угол поворота в стыке.
Для расчета величин δ0 и θ имеются формулы, учитывающие конструкцию, размеры присоединительных поверхностей и величину действующих сил. Однако формулы не учитывают точность изготовления присоединительных поверхностей и вследствие этого дают значительно
заниженную величину контактных деформаций. |
|
||||||
Вследствие |
незначительной величины δ0 |
ею часто пренебрегают. В |
|||||
этом случае контактная деформация: |
|
||||||
y = θ L, |
|
|
|
(10.6) |
|||
Для хвостовиков с конусами Морзе угол |
|
||||||
|
0,2P 2 |
2L 1 ; |
(10.7) |
||||
|
|
|
|
||||
|
|
|
D |
|
|
|
|
|
|
|
|
|
|
|
|
4 |
1 |
; |
|
(10.8) |
|||
|
|
||||||
|
|
13D3 |
|
|
|
|
где Ρ – приложенная сила; L – расстояние от точки приложения силы до торца соединения; D – номинальный диаметр конуса Морзе на торце стыка.
Величина деформации блока зависит от числа присоединительных поверхностей и может быть рассчитана как сумма объемных и контактных деформаций по формуле
n1 |
3 |
n2 |
|
|
yб |
PLi |
ili; |
(10.9) |
|
3El |
||||
1 |
1 |
|
||
|
i |
|
|
Где п1 –число элементов инструментального блока, подвергающихся объемной деформации; п2 – число стыков в блоке; Li – длина элементов блока с объемной деформацией; li – длина элементов блока с контактной

304
деформацией; Ρ – нагружающая сила; Ε – модуль продольной упругости, Ε =
2,1 ·102 ГПа; li,- – осевой момент инерции рассматриваемого сечения блока.
Податливость инструментального блока П yб ; (мкм/Н).
P
Цель и задачи работы. Цель работы – исследование влияния конструкции и точности изготовления присоединительных поверхностей инструментальных блоков на их податливость. В задачу работы входит определение податливости инструментальных блоков и углов поворота элементов блока с конусом Морзе и цилиндрическим соединением различной точности изготовления.
Необходимое оборудование, инструменты и приборы:
1.Горизонтально-фрезерный станок 6Р82 (6Р82Г) или другой модели, оснащенный шпинделем с внутренним конусом 50.
2.Переходная втулка с конусом 7 : 24 для инструментов с конусом Морзе и лапкой.
3.Три контрольные цилиндрические оправки №№ 1, 2, 3 диаметром 23,9мм с конусом Морзе 3 и лапкой. Общая длина оправки 225мм. Биение цилиндрической части оправки относительно конуса Морзе не более 0,01мм.
Степени точности конусов Морзе у оправок № 1 - АТ6; № 2 - АТ7 и № 3-АТ8.
4.Державка с конусом 50 для регулируемых патронов втулок и оправок с цилиндрическим отверстием диаметром 36мм.
5.Три контрольные цилиндрические оправки №№ 4, 5 и 6 диаметром 23,9мм с цилиндрическим хвостовиком диаметром 36мм и длиной 116мм. Общая длина оправки 225мм.
Биение диаметра 23,9мм относительно хвостовика должно быть не
более 0,01мм. Размеры диаметров хвостовиков: для оправки № 4 –36 00,,0102 мм,
для оправки № 5 –36 00,,0304 мм и для оправки № 6 – 36 00,,0607 мм.
6.Индикаторы со стойками (2 шт.) и ценой деления 0,002мм.
7.Динамометр марки ДОС М31 или другой, обеспечивающий контроль
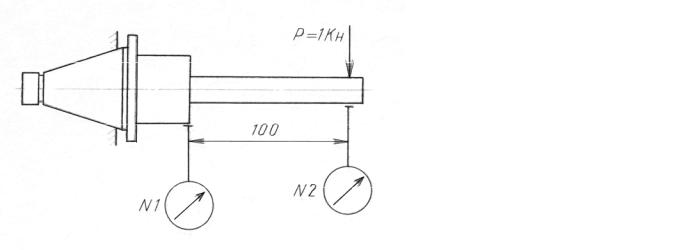
305
приложения силы 1 кН.
8.Стойка для установки динамометра, закрепляемая на столе станка.
Методика выполнения работы. Работу выполняют на фрезерном станке, в шпинделе которого устанавливают инструментальные блоки, состоящие из переходных втулок или державок и цилиндрических контрольных оправок с присоединительными поверхностями в виде конуса Морзе или цилиндрической поверхности с различной точностью изготовления. Оправки при помощи динамометра нагружаются силой в 1 кН, приложенной на расстоянии 100мм от торца переходной втулки или державки. Величина деформации блока у торца переходной втулки и на контрольной оправке в сечении приложения силы измеряется индикатором. Величина перекосов в стыках получается как разность расчетной объемной и фактической деформаций, измеренных индикаторами. Схема нагружения блока приведена на рис. 10.12.
Рис. 10.12. Схема нагружения блока с цилиндрической оправкой
Обозначим показания индикатора № 1, установленного на торце переходной втулки, δΒ, а показание индикатора № 2 на оправке – δ0 . Показание индикатора № 1 является результатом объемной деформации переходной втулки и перекоса ее оси в месте стыка конусов 7 : 24 шпинделя и оправки от действия силы Р. Индикатор № 2 показывает суммарную деформацию инструментального блока, которая включает объемные и контактные деформации контрольной цилиндрической оправки и переходной втулки. Перекос оси контрольной оправки на 1мм ее длины:
306
|
|
|
|
|
|
|
|
Pl |
|
|
|
|
|
0 |
|
|
|
|
|
|
|
|
|
|
||||||||
|
|
|
|
B |
|
|
|
|||
|
|
|
|
|
|
|
|
3EJ |
(10.10) |
|
|
|
|
|
|
100 |
|
|
|||
|
|
|
|
|
|
|
|
|
Порядок выполнения работы:
1.С хобота станка снимают кронштейн с подшипниками и сдвигают его в направлении шпинделя в крайнее положение.
2.В шпинделе станка устанавливают переходную втулку с конусом 7 : 24 и затягивают ее.
3.В переходную втулку устанавливают контрольную цилиндрическую оправку № 1.
4.Устанавливают стойку с динамометром так, чтобы точка приложения силы находилась на расстоянии 100мм от торца оправки (см. рис. 10.12).
5.Устанавливают стойки с индикаторами так, чтобы их наконечники находились на торце переходной оправки (индикатор № 1) и на контрольной оправке в сечении приложения силы. Наконечники индикаторов плоские. Индикаторы устанавливают в диаметральной горизонтальной плоскости блока.
6.Динамометром нагружают блок силой Р=1кН. Снимают показания индикаторов.
7.Последовательно в переходную оправку устанавливают контрольные оправки № 2 и 3, нагружают их и снимают показания индикаторов.
8.В шпинделе станка устанавливают и затягивают державку с конусом 50.
9.Последовательно в державку устанавливают контрольные оправки № 4–6. Устанавливают индикаторы № 1, 2, динамометр и нагружают блок силой
1кН. Снимают показания индикаторов для каждой из оправок.
10.Запись и обработку полученных данных производят в соответствии с табл. 10.5.
По данным табл. 10.5 определяют влияние конструкции и точности изготовления присоединительных поверхностей режущего и вспомогательного инструмента на податливость инструментальных блоков.