
- •Оглавление
- •Предисловие
- •Глава 1. Общие вопросы заточки режущих инструментов
- •1.3 Заточные станки
- •1.4 Вопросы для контроля
- •Глава 2. Исследование конструкций резцов
- •2.1 Назначение, типы и конструктивные особенности
- •2.2 Конструктивные элементы резца
- •2.3 Геометрические параметры резца
- •2.4. Износ, критерий затупления и число переточек резцов
- •2.6 Вопросы для контроля
- •Глава 3. Исследование конструкций спиральных свёрл
- •3.1 Назначение, типы и конструктивные особенности
- •3.2 Методы заточки спиральных сверл
- •3.4 Вопросы для контроля
- •Глава 4. Исследование конструкций зенкеров
- •4.1 Назначение, типы и конструктивные особенности
- •4.2 Износ и затачивание зенкеров
- •4.4 Вопросы для контроля
- •5.1 Назначение, типы и конструктивные особенности
- •5.2 Выбор основных параметров
- •5.3 Износ и затачивание разверток
- •5.5 Вопросы для контроля
- •Глава 6. Исследование конструкций фрез
- •6.1 Назначение, типы и конструктивные особенности
- •6.2 Износ и восстановление фрез
- •6.3 Лабораторная работа «Конструкция фрез»
- •6.4 Вопросы для контроля
- •6.6 Вопросы для контроля
- •7.1 Исследование конструкций метчиков
- •7.1.1 Назначение, типы и конструктивные особенности
- •7.1.3 Вопросы для контроля
- •7.1.5 Вопросы для контроля
- •7.1.7 Вопросы для контроля
- •7.2 Исследование конструкций резьбонарезных головок
- •7.2.1. Назначение, типы и конструктивные особенности
- •7.2.3 Вопросы для контроля
- •Глава 8. Исследование конструкций зуборезных долбяков
- •8.1 Назначение, типы и конструктивные особенности
- •8.3 Вопросы для контроля
- •8.5 Вопросы для контроля
- •Глава 9. Исследование конструкций червячных фрез
- •9.1 Назначение, типы и конструктивные особенности
- •9.3 Вопросы для контроля
- •9.5 Вопросы для контроля
- •10.1 Назначение, типы и конструктивные особенности
- •10.3 Вопросы для контроля
- •10.5 Вопросы для контроля
- •10.7 Вопросы для контроля
- •10.9 Вопросы для контроля
- •10.11 Вопросы для контроля
- •11.1 Назначение, типы и конструктивные особенности
- •11.2 Алмазные сверла на связке «МонАлиТ»
- •11.3 Состояние рабочей поверхности сверла
- •11.4 Моделирование процесса алмазного сверления
- •11.5 Оценка режущей способности алмазных свёрл
- •11.7 Вопросы для контроля
- •12.1 Назначение и структура САПР
- •12.3 Вопросы для контроля
- •12.5 Вопросы для контроля
- •12.7 Вопросы для контроля

278
проекции нормального шага на осевую плоскость. При этом перемещение измерительного наконечника вдоль оси центров на длину трёх шагов Px3.
8. Данные всех измерений систематизируют (см. табл. 9.1) и, сравнивая полученные результаты со значениями допустимых отклонений соответствующих параметров по ГОСТ 9324 – 80, определяют, к какому классу точности относится контролируемая фреза и соответствует ли она предъявляемым требованиям.
Содержание отчёта. В отчёте приводят формулировку задания, краткую характеристику фрезы, необходимые расчёты и схемы измерений в соответствии с методикой работы, таблицу с анализом точности фрезы по исследуемым параметрам (см. табл. 9.1), заключение по работе.
9.5Вопросы для контроля
1.Какие параметры характеризуют профиль передней поверхности?
1) прямолинейность и величина переднего угла; 2) угол профиля зубьев; 3) шаг стружечных канавок; 4) передний и задний углы; 5) угол подъёма витков фрезы.
2.При контроле профиля зубьев червячных архимедовых фрез с углом профиля зубьев 20° какое значение угла α0 из нижеприведенных надо принять для расчёта блока концевых мер?
kz
1)α0=α=20°; 2)α0=20°14'; 3)ctgα0=ctgαcosγm0; 4)ctg 0 ctg черв Pz0 ;5)α0=α-
∆α.
3. По какой поверхности перетачиваются червячные фрезы?
1) по передней и задней поверхности; 2) только по задней поверхности; 3) только по передней поверхности; 4) по передней поверхности и боковым сторонам; 5) по задней поверхности и боковым сторонам.
279
4. Затачивается червячная фреза с винтовыми стружечными канавками и углом γ=0. На какой поверхности располагаются режущие кромки фрезы?
1) эвольвентной; 2) архимедовой винтовой; 3) эвольвентной винтовой; 4) плоскости; 5) поверхности вращения.
5.Какой из указанных передних углов червячной фрезы обеспечивает при обработке наиболее точный профиль зуба колеса?
1) 15º; 2) 10º; 3) 5º; 4) 0º; 5) 8º.
6. Как устанавливается глубина резания (слой, снимаемый за 1дв.ход)
при затачивании фрезы? |
|
1) поперечным перемещением стола на круг; |
2) поперечным |
перемещением стола от круга; 3) поворотом фрезы вокруг своей оси; 4)
поворотом линейки приспособления; 5) перемещением круга к центру фрезы.
Список литературы
1.Режущий инструмент. Лабораторный практикум. Учеб. пособие для вузов по специальности «Технология машиностроения,
металлорежущие станки и инструменты» / Н.Н. Щегольков, Г.Н.
Сахаров, О.Б. Арбузов и др.; Под общ. ред. Н.Н. Щеголькова.
М.:Машиностроение, 1985 – 168с., ил.
2.Режущий инструмент: Учебник для вузов / Под редакцией С.В.
Кирсанова. М.: Машиностроение, 2007. – 512с.: ил.
3.Справочник конструктора-инструментальщика / Под общ. ред. В.А.
Гречишникова и С.В. Кирсанова. 2-е изд., перераб. и доп. – М.:
Машиностроение, 2006. – 542с.: ил.

280
Глава 10. Исследование инструментов для
автоматизированного производства
10.1 Назначение, типы и конструктивные особенности
Одним из условий эффективной эксплуатации автоматических линий,
станков с ЧПУ и автоматизированных комплексов из этих станков,
управляемых от ЭВМ, а также гибких автоматизированных систем является применение быстросменных бесподналадочных конструкций инструментов и инструментальных блоков (режущий и вспомогательный инструмент в сборе) [8, 4] .
Быстросменность инструмента обеспечивается совершенствованием методов его крепления и базирования, а также унификацией присоединительных поверхностей режущего и вспомогательного (зажимного)
инструмента с целью сокращения его номенклатуры.
Бесподналадочная замена инструмента обеспечивается наличием элементов регулирования инструмента на размер. Настройка инструмента на размер вне станка осуществляется на различных приспособлениях для настройки или путем весьма точного изготовления инструмента и режущих элементов.
В конструкциях инструментов для автоматизированного производства вопросы быстросменности и бесподналадочной замены решаются комплексно.
На станках токарной группы быстросменность обеспечивается применением резцовых вставок с регулировочными винтами (рис. 10.1, а),
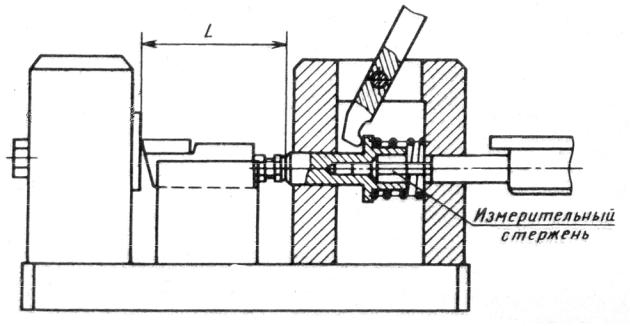
281
резцедержателей с цилиндрическим хвостовиком для станков с ЧПУ (10.1, б), с
базовой призмой для станков с ЧПУ (рис. 10.1, в), в гнездах которых устанавли-
вают резцы или другие инструменты. В данном случае резцедержавки и инструмент составляют инструментальные блоки и настройку на размер инструмента на приборах настройки проводят непосредственно в блоках.
Достоинством двух последних резцедержавок является возможность применения стандартных конструкций инструмента. Быстросменность и бесподналадочная замена осевого инструмента обеспечивается применением цилиндрических хвостовиков, с передачей крутящего момента с помощью шпонки и регулированием на размер либо с помощью регулировочного винта,
что требует изготовление специального инструмента (рис. 10.1, г) либо упорной гайкой, когда применяется стандартный инструмент (рис. 10.1, д). На рис. 10.1,
д инструмент с конусом Морзе устанавливают в переходную втулку с цилиндрической наружной поверхностью. Втулка со стороны инструмента имеет резьбу, на которую навинчивается регулировочная гайка. Передача крутящего момента осуществляется шпонкой. Скос на цилиндрическом хвостовике с помощью винта 1 (рис. 10.1, г) обеспечивает
Рис. 10.2. Приспособление для настройки длины резца вне станка
отсутствие перемещения инструмента при выводе его из изделия. На рис. 10.2
показано приспособление для настройки резцов на размер вне станка.

282
Индикатор приспособления настраивают по эталону. Точность размерной настройки инструментов δΗ определяется суммарным влиянием элементарных погрешностей эталона δЭ, погрешностью регулирования инструмента при настройке δР и погрешностью установки на станке δУ.
При определении погрешности бесподналадочной замены [11] отдельные погрешности суммируются как случайные величины с введением коэффициента k = 1,2;
Н 1,2 Н2 |
Р2 У2 |
(10.1) |
Погрешность |
бесподналадочной замены не |
определяет точность |
обработки, которая зависит также от жесткости технологической системы станок – приспособление – инструмент – заготовка и режимов резания.
Одним из основных требований к автоматизированному многономенклатурному, часто сменяемому производству в современных условиях является его гибкость, позволяющая предприятиям в нужный момент за короткий срок переходить на выпуск новой или более совершенной продукции. Это требование может быть удовлетворено применением станков с ЧПУ, станочных модулей робот – станок с ЧПУ и автоматизированных комплексов из станков с ЧПУ, управляемых от ЭВМ.
Такое производство требует соответствующего гибкого ин-
струментального обеспечения, позволяющего обрабатывать любые поверхности минимально возможной номенклатурой режущего и вспомогательного (зажимного) инструмента, обеспечивающей его автоматическую бесподналадочную замену с заданной точностью. Решение данной задачи достигается применением системы вспомогательного инструмента для станков с ЧПУ, которая устанавливает номенклатуру и основные размеры. Система вспомогательного инструмента регламентирована руководящим техническим материалом РТМ2 П10-2–79, разработанным ЭНИМС и ВНИИ, и устанавливает при подсистемы: вспомогательного инструмента для станков с ЧПУ сверлильно-расточной и фрезерной групп,
вспомогательного инструмента с цилиндрическим хвостовиком для станков с
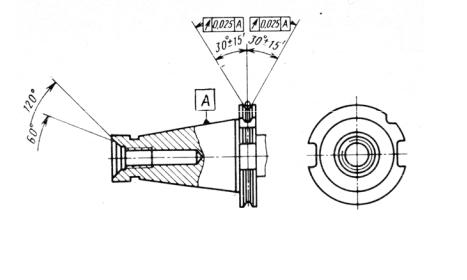
283
ЧПУ токарной группы, вспомогательного инструмента с базирующей призмой для станков с ЧПУ токарной группы.
Системы инструментальной оснастки предназначены для компоновки функциональных единиц – инструментальных блоков (комбинаций режущего и вспомогательного инструмента), каждый из которых предназначен для выполнения конкретного технологического перехода обработки заданной детали на конкретном станке. Для снижения затрат на вспомогательный ин-
струмент и для удобства эксплуатации важным условием эффективности подсистемы вспомогательного инструмента является его минимальное количество, обеспечивающее возможность закрепления максимально возможного числа инструментов различных типов и размеров. Эта задача достигается унификацией конструктивных элементов вспомогательного инструмента. Важным фактором унификации инструментальной оснастки является принятие единых исполнений присоединительных поверхностей инструмента и станков. С этой целью разработаны хвостовики инструментов с конусом 7:24 для станков с ЧПУ (ГОСТ 25827–83). Рекомендуется использовать хвостовики с конусом 40 и 50.
Для станков классов точности Η и Π степень точности хвостовиков АТ5,
для станков точности В и А – АТ4.
Рис. 10.3. Хвостовики вспомогательного инструмента для станков с ЧПУ сверлильно-расточной и фрезерной групп
Конструкция хвостовиков по ОСТ2 П14-2–78 показана на рис. 10.3.
Унифицированы также цилиндрические хвостовики инструментов (рис. 10.4).
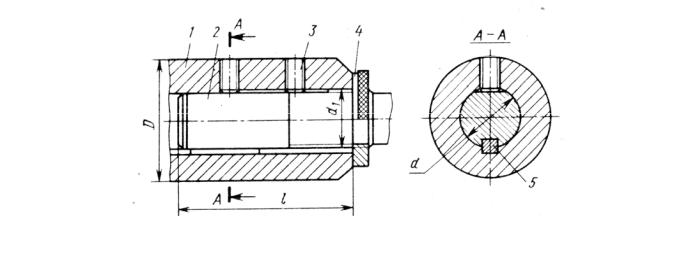
284
На хвостовиках предусмотрена трапецеидальная резьба для регулирования вылета инструмента относительно переходных втулок с помощью упорных гаек.
На рис. 10.5 показана подсистема вспомогательного инструмента для станков с ЧПУ сверлильно-расточной и фрезерной групп. Биение присоединительных поверхностей для инструмента в переходных втулках и оправках относительно конусов 7:24 установлено 0,01мм. Точность изготовления цилиндрических поверхностей установлена с отклонением по Н6
и h6 и параметром шероховатости Ra = 0,32 – 1,25 мкм по ГОСТ 2789–73.
Соединение цилиндрических поверхностей инструмента с переходными втулками и с закреплением цилиндрического хвостовика инструмента двумя болтами называется цилиндрическим соединением с односторонним натягом.
Рис.10.4.ЦилиндрическийхвостовиквспомогательногоинструментадлястанковсЧПУ: 1-переходнаядержавка;2-цилиндрическийхвостовик;3-зажимнойвинт;4-регулировочнаягайка;5-шпонка
В инструментальных блоках, устанавливаемых в шпинделе станка,
биение режущих кромок инструментов не должно превышать следующих
величин:
Инструмент |
Биение, мм |
Сверла с цилиндрическим хвостовиком диаметром 6–18мм……………… 0,056 Сверла с коническим хвостовиком диаметром 18–30мм………………….. 0,071 Зенкера и развертки диаметрами, мм:
до 50 …………………………………………………………………………… 0,062 до 120 ………………………………………………………………………….. 0,071
Расточные оправки для получистовой обработки отверстий диаметром
22-180 …………………………………………………………………………..0,030
Расточные оправки для чистовой обработки отверстий диаметрами, мм: 25-80……………………………………………………………………………. 0,005 80–180………………………………………………...…………………………0,010
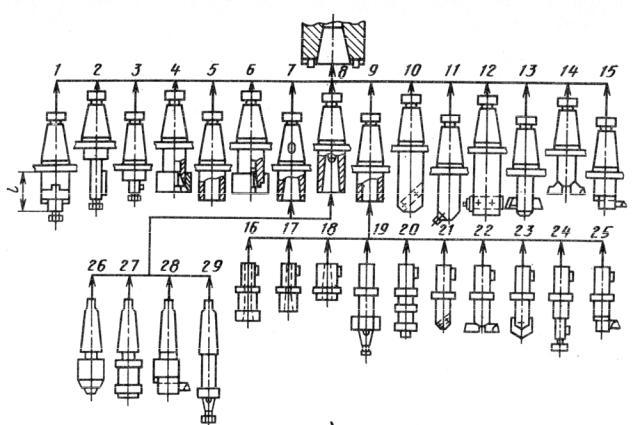
285
Рис. 10.5. Подсистема вспомогательного инструмента для станков с ЧПУ сверлильнорасточной и фрезерной групп: 1– оправка с конусом 7 : 24 для насадных фрез с поперечной шпонкой; 2 – оправка с конусом 7 : 24 для насадных торцовых фрез с продольной шпонкой; 3, 4 – патроны с конусом 7 : 24 цанговые и диапазоном зажима 20–40мм; 5 – переходные втулки с конусом 7 ; 24 для концевых фрез; 6 –цанговые патроны с конусом 7 : 24 и диапазоном зажима 5 – 20мм; 7 – переходные втулки с конусом 7 : 24 для инструмента с конусом Морзе и лапкой; 8 – переходные втулки с конусом 7 ; 24 для инструмента с конусом Морзе и резьбовым отверстием; 9 –державки с конусом 7 : 24 для регулируемых патронов, втулок и оправок; 10 –расточные оправки с конусом 7 : 24 для получистового растачивания; 11 –расточные оправки с конусом 7 : 24 для чистового растачивания; 12 –сборные оправки с конусом 7 : 24 для чистового растачивания; 13 –оправки с конусом 7 : 24 для подрезных пластин; 14 –расточные двузубые головки с конусом 7 : 24; 15 –расточные универсальные головки с конусом 7 : 24; 16–цанговые регулируемые патроны с диапазоном зажима 5– 25мм; 17– универсальные регулируемые втулки с внутренним конусом Морзе; 18– регулируемые длинные втулки с внутренним конусом Морзе; 19 – регулируемые оправки для насадных зенкеров и разверток; 20 –регулируемые резьбонарезные патроны; 21 – регулируемые оправки для получистового растачивания; 22– регулируемые расточные двухзубые оправки; 23 –регулируемые оправки для крепления пластин перовых сверл; 24 – регулируемые оправки для дисковых фрез; 25 –регулируемые расточные патроны; 26 – сверлильные трехкулачковые патроны без ключа; 27 – резьбонарезные патроны с конусом Морзе; 28 – расточные патроны с конусом Морзе; 24 – оправки с конусом Морзе для насадных зенкеров и разверток
Статическая точность (точность позиционирования) инструментальных блоков зависит от конструкции и точности изготовления присоединительных поверхностей режущего и вспомогательного инструмента. Установлено, что
286
наибольшую точность обеспечивают цилиндрические присоединительные поверхности с минимальными зазорами, а наименьшую – поверхности, вы-
полненные в виде конусов Морзе.
Разработана методика расчета точности позиционирования, учитывает конструкцию и точность изготовления присоединительных поверхностей режущего и вспомогательного инструмента.
Точность обработки зависит также от деформации инструментальных блоков. Погрешности, вызванные деформацией инструментальных блоков,
могут составлять до 60% погрешности обработки. Деформация инструментальных блоков оценивается допустимой податливостью, т.е.
величиной деформации блока, мкм, в точке приложения силы в 1 Ньютон.
Допустимая податливость для некоторых видов инструмента имеет следующие значения:
Инструмент
Допустимая податливость, мкм/Н
Сверла диаметром, мм
6–18 ………………………………………………………………………0,286 18–30……………………………………………………………………...0,172
Расточные оправки для получистовой обработки отверстий диаметрами, мм:
40-80 ………………………………………………………..…………… 0,150
80-180 ………………………………………………………..………….. 0,108
Расточные оправки для чистовой обработки отверстий диаметрами, мм:
40-80 ……………………………………………..……………………… 0,118
80-180 …………………………………………..……………………….. 0,072
Инструментальные блоки испытывают деформацию двух видов:
деформацию деталей (изгиб, скручивание) и деформацию контактных поверхностей элементов блока в местах соединений. Деформации первого вида противостоит объемная жесткость, а деформации второго вида – контактная жесткость. Объемная жесткость определяется по формулам сопротивления материалов. Контактная жесткость, влияющая на величину деформации блока в месте приложения силы, зависит от величины и направления действующих сил,
конструкции и точности изготовления сопряженных поверхностей.
287
Методы расчета податливости инструментальных блоков, учитывающие
конструкцию и точность изготовления присоединительных поверхностей
режущего и вспомогательного инструмента, разработаны.
10.2 Лабораторная работа
«Исследование погрешности установки резцов,
настраиваемых на размер вне станка»
Лабораторная работа направлена на изучение одной из систематических постоянных погрешностей обработки, зависящей от точности расположения вершины резца относительно оси изделия. Эта погрешность проявляется за период стойкости резца до его замены и зависит от погрешности эталона, по которому настраивается приспособление для размерной настройки резца,
погрешности настройки резца на размер и погрешности, возникающей при установке резца в резцедержавке. Первые две погрешности устанавливают измерением эталона и точностью настройки резца. Последняя погрешность может быть определена экспериментально и зависит от конструкции и точности изготовления резцедержавки и способа крепления резца.
В данной работе точность установки определяется для резцовых вставок,
устанавливаемых в закрытый паз резцедержавки и закрепляемых клином.
Цель и задачи работы. Цель работы – исследование конструкции и точности позиционирования быстросменных резцов, настраиваемых на размер вне станка. В задачи работы входят изучение конструкции приспособления для размерной настройки резцов и приобретение навыков работы на нем, изучение индикаторного приспособления для изменения точности позиционирования,
анализ погрешностей позиционирования и обработка полученных данных.
Необходимое оборудование, инструменты и приборы. Для выполнения работы необходимы: приспособления для настройки резца на размер вне станка; эталон к указанному приспособлению для установки нулевого показания индикатора с маркировкой номинального и фактического размера

288
длины; индикаторное приспособление для измерения точности позиционирова-
ния резца; резцовая вставка с винтом для настройки длины L, оснащенная многогранной твердосплавной пластиной. Для выполнения лабораторной работы можно использовать резцовую вставку для контурного точения с механическим креплением трехгранных твердосплавных пластин (рис. 10.6).
Рис. 10.7. Эталон
Рис. 10.6. Резцовая вставка
Методика выполнения работы
1. Настраивают длину L резцовой вставки (рис. 10.6) в приспособлении для настройки резцов вне станка. Схема приспособления показана на рис. 10.2.
Нулевое показание индикатора устанавливают по эталону с номинальной длиной L. Фактическую длину эталона Lф маркируют на одной из боковых сторон. Эскиз эталона показан на рис. 10.7. Эталон изготовляют из стали 40Х,
термически обработанной до твердости HRC 50–55 с точностью ± 0,01мм. Реко-
мендуемое сечение эталона 25 х 30мм. По эталону устанавливают нулевое показание шкалы индикатора приспособления. Натяг индикатора делают около одного миллиметра. Записывают фактический размер эталона и показание индикатора.
Затем устанавливают в приспособление резцовую вставку и настраивают ее на длину L с точностью ± 0,01мм. Записывают действительный размер резца,
равный фактической длине эталона ± показание индикатора.
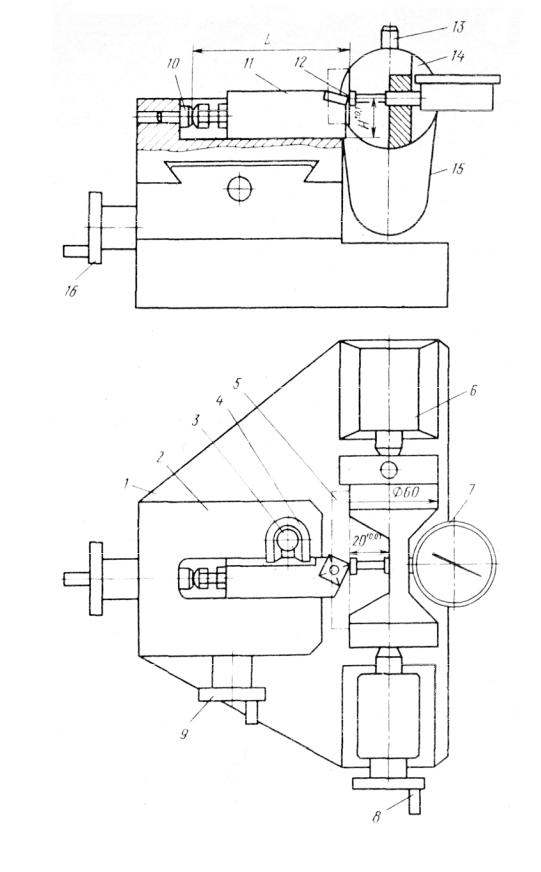
289
2. Погрешность установки резцовой вставки определяют специальным
контрольным индикаторным приспособлением (рис. 10.8).
Рис. 10.8. Схема индикаторного приспособления для исследования точности
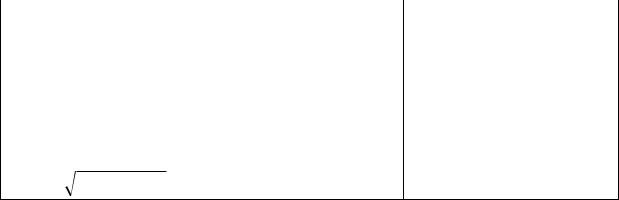
290
На плите 1 приспособления установлены центровые бабки 6 и
резцедержавка 2 с упором 10. Резцовую вставку 11, настроенную на размер,
устанавливают в гнездо резцедержавки до упора и закрепляют клином 4 с
помощью винта 3. Вершина 12 резца должна располагаться на линии центров приспособления с допуском ±0,1мм. В центровых бабках устанавливают оправку 14 с индикатором с плоским наконечником и ценой деления 0,002мм.
Ось индикатора с точностью 0,01мм должна пересекать ось оправки 14.
Нулевое показание индикатора при натяге 1мм обеспечивают с помощью планки 5. Противовес 15 обеспечивает горизонтальное расположение индикатора. Оправку затягивают рукояткой 8. Рукоятками поперечного 16 и
продольного 9 перемещения резцедержавки вершину резца устанавливают в середину плоского наконечника так, чтобы шкала индикатора 7 показывала нулевое положение. Покачиванием рукоятки 13 на противовесе, жестко соединенном с оправкой 14, добиваются минимального показания индикатора.
Это показание принимают за нулевое.
3.Открепляют, снимают и вновь устанавливают резец. Аналогично п. 2
определяют минимальное показание индикатора и записывают его. Данную операцию повторяют 8–10 раз с записью показаний индикатора. Максимальное показание индикатора при многократных установках определяет погрешность установки резца, настроенного на размер вне станка.
|
Таблица 10.1 |
Измеряемый или рассчитываемый параметр |
Полученное значение |
Формула для расчета |
параметра, мм |
Погрешность эталона δэ = L - Lф |
|
Показание индикатора приспособления после настройки |
|
резца на размер δр |
|
Показания индикатора контрольного приспособления |
|
при повторных установках и закреплениях резца – бу1; |
|
бу2, ..., бу10 |
|
Погрешность позиционирования (настройки) |
|
Н 1,2 Н2 Р2 У2
Запись и обработку полученных данных производят в соответствии с табл.
10.1. По данным табл. 10.1 определяют точность обработки (квалитет) детали,