
- •Оглавление
- •Предисловие
- •Глава 1. Общие вопросы заточки режущих инструментов
- •1.3 Заточные станки
- •1.4 Вопросы для контроля
- •Глава 2. Исследование конструкций резцов
- •2.1 Назначение, типы и конструктивные особенности
- •2.2 Конструктивные элементы резца
- •2.3 Геометрические параметры резца
- •2.4. Износ, критерий затупления и число переточек резцов
- •2.6 Вопросы для контроля
- •Глава 3. Исследование конструкций спиральных свёрл
- •3.1 Назначение, типы и конструктивные особенности
- •3.2 Методы заточки спиральных сверл
- •3.4 Вопросы для контроля
- •Глава 4. Исследование конструкций зенкеров
- •4.1 Назначение, типы и конструктивные особенности
- •4.2 Износ и затачивание зенкеров
- •4.4 Вопросы для контроля
- •5.1 Назначение, типы и конструктивные особенности
- •5.2 Выбор основных параметров
- •5.3 Износ и затачивание разверток
- •5.5 Вопросы для контроля
- •Глава 6. Исследование конструкций фрез
- •6.1 Назначение, типы и конструктивные особенности
- •6.2 Износ и восстановление фрез
- •6.3 Лабораторная работа «Конструкция фрез»
- •6.4 Вопросы для контроля
- •6.6 Вопросы для контроля
- •7.1 Исследование конструкций метчиков
- •7.1.1 Назначение, типы и конструктивные особенности
- •7.1.3 Вопросы для контроля
- •7.1.5 Вопросы для контроля
- •7.1.7 Вопросы для контроля
- •7.2 Исследование конструкций резьбонарезных головок
- •7.2.1. Назначение, типы и конструктивные особенности
- •7.2.3 Вопросы для контроля
- •Глава 8. Исследование конструкций зуборезных долбяков
- •8.1 Назначение, типы и конструктивные особенности
- •8.3 Вопросы для контроля
- •8.5 Вопросы для контроля
- •Глава 9. Исследование конструкций червячных фрез
- •9.1 Назначение, типы и конструктивные особенности
- •9.3 Вопросы для контроля
- •9.5 Вопросы для контроля
- •10.1 Назначение, типы и конструктивные особенности
- •10.3 Вопросы для контроля
- •10.5 Вопросы для контроля
- •10.7 Вопросы для контроля
- •10.9 Вопросы для контроля
- •10.11 Вопросы для контроля
- •11.1 Назначение, типы и конструктивные особенности
- •11.2 Алмазные сверла на связке «МонАлиТ»
- •11.3 Состояние рабочей поверхности сверла
- •11.4 Моделирование процесса алмазного сверления
- •11.5 Оценка режущей способности алмазных свёрл
- •11.7 Вопросы для контроля
- •12.1 Назначение и структура САПР
- •12.3 Вопросы для контроля
- •12.5 Вопросы для контроля
- •12.7 Вопросы для контроля
291
например, диаметром 40мм при данном способе крепления (без учета
жесткости |
системы станок–приспособление–инструмент–заготовка |
и |
влияния |
на Точность обработки режимов резания). |
|
Содержание отчета. В отчете приводят формулировку задания и цель
работы, эскиз резцовой вставки, схемы определения погрешностей позиционирования, результаты измерений (табл. 10.1), анализ полученных данных и заключение о точности установки резцовой вставки.
10.3Вопросы для контроля
1.Как настраивают базовую длину L резцовой вставки?
Варианты ответов: 1) с помощью штангенциркуля; 2) с помощью стойки с индикатором; 3) с помощью микрометра; 4) на станке по эталонной детали с помощью регулировочного винта резцовой вставки; 5) вне станка в специальном приспособлении.
2. С какой целью настраивают базовую длину L резцовой вставки вне станка?
Варианты ответов: 1) для обеспечения необходимых передних и задних углов; 2) для обеспечения заданных углов в плане; 3) для уменьшения времени замены затупившейся резцовой вставки; 4) для более надежного закрепления; 5) для уменьшения вибраций при работе.
10.4 Лабораторная работа
«Исследование влияния метода крепления и базирования многогранных
пластин на точность их установки в корпусе резца»
Одним из путей реализации быстросменной бесподналадочной замены инструмента на станках-автоматах и автоматических линиях является бесподналадочная замена многогранных твердосплавных пластин. Она осуществляется на резцах, торцовых фрезах, расточных инструментах.
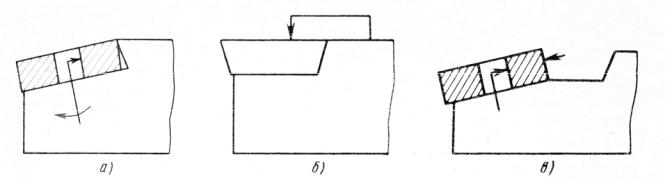
292
Достоинством данного пути является относительно небольшая затрата времени на замену изношенной и установку новой пластины. Так, по существующим нормативам время на замену многогранной пластины на инструменте составляет 0,5–1 мин, тогда как аналогичное время для замены резца в 2–4 раза больше, причем в последнем случае требуются затраты времени в 1–2 мин на настройку инструмента на размер вне станка.
Для осуществления бесподналадочной замены необходимо применять многогранные пластины точного исполнения классов допусков А и F по ГОСТ
19042–80 и методы крепления пластин, обеспечивающие их точную установку в гнезде корпуса, с базированием по боковым поверхностям и опорной поверхности. Этим условиям удовлетворяют две схемы крепления пластин,
устанавливаемые в точные пазы корпуса резца - с упором на базу (рис. 10.9, а),
например,
Рис. 10.9. Схемы крепления и базирования многогранных пластин на резцах
с помощью качающегося штифта, и креплением прихватом (рис. 10.9, б).
Однако, в ряде случаев применяют крепления пластин с помощью клина (рис. 10.9, в, ГОСТ 21151–75). Данная конструкция не обеспечивает точного базирования пластин и не может использоваться для их бесподналадочной замены.
Цель и задачи работы. Цель работы – исследовать влияние метода крепления и базирования многогранных твердосплавных пластин на размеры резца по длине и определить схему крепления, обеспечивающую возможность бесподналадочной замены многогранных пластин на инструментах.
Выполнение работы позволяет объективно оценить методы крепления

293
многогранных пластин на инструментах с точки зрения пригодности для при-
менения в автоматизированном производстве.
Необходимое оборудование, инструменты и приборы. Для выполнения работы необходимы: 1) приспособление для размерной настройки резцов вне станка с эталоном; 2) резцы, оснащенные квадратными пластинами твердого сплава с базированием пластин по схемам, показанным на рис. 10.9, а, в оди-
накового размера, с одинаковыми углами в плане и регулировочными винтами; 3) две многогранные твердосплавные пластины классов допусков А или F по ГОСТ 19042–80, указанные на рис. 10.10.
Рис. 10.10. Основные размеры квадрат ной многогранной пластины
Методика выполнения работы. 1. Многогранные пластины измеряют микрометром по ширине квадрата d, толщине S и диагонали К (см. рис. 10.10).
Результаты измерений записывают. Допустимые предельные отклонения конструктивных параметров рассматриваемых пластин приведены в табл. 10.2.
Таблица 10.2
|
Классы |
|
Предельные отклонения, мм, для параметров |
|
||||
|
допусков |
|
т |
|
d |
|
s |
|
|
А |
|
±0,005 |
|
±0,025 |
|
±0,025 |
|
|
F |
|
±0,005 |
|
±0,013 |
|
±0,025 |
|
|
Μ |
|
±0,08…0,18 |
|
±0,05…0,13 |
|
±0,13 |
|
|
U |
|
±0,13…0,38 |
|
±0,08…0,25 |
|
±0,13 |
|
2. |
По эталону |
устанавливают |
нулевое |
показание индикатора |
приспособления для размерной настройки резцов.
294
3.Резец 1 с креплением пластины по рис. 10.9,а с первой пластиной настраивают в приспособлении на размер L с точностью ± 0,01мм. Показание индикатора записывают.
4.На резце 1 первую пластину поворачивают и закрепляют 3 раза.
После каждого поворота измеряют на приспособлении размер резца и записывают показания индикатора (при неизменной настройке резца и приспособления). Разность показаний индикатора представляет собой погрешность размерной настройки после поворота пластины.
|
|
|
|
|
|
|
Таблица 10.3 |
|
|
|
|
|
|
|
|
|
|
№ |
|
|
|
|
|
Измеряемый или рассчитываемый параметр |
|
Полученное |
|
|
|
|
|
|
значение |
||
|
|
|
|
|
Формула для расчета |
|
||
|
|
|
|
|
|
|
параметра, мм |
|
|
|
|
|
|
|
|
|
|
|
|
|
|
|
|
|||
1 |
Размеры первой пластины (см. рис. 10.10) : dl ; kl ; s1; |
|
|
|||||
|
m |
k1 |
d1 |
|
|
|
|
|
|
|
|
|
|
||||
|
1 |
|
|
2 |
|
|
|
|
2 |
|
|
|
|
|
|
|
|
Размеры второй пластины: d2 ; k2 ; s2 ; |
|
|
||||||
|
m |
k2 |
d2 |
|
|
|
||
|
|
|
|
|
||||
|
2 |
|
|
2 |
|
|
|
|
|
|
|
|
|
|
|
|
|
3 |
Погрешность эталона δЭ = L - Lф |
|
|
|||||
4 |
Показание индикатора настроечного приспособления для резца 1 с первой |
|
|
|||||
|
пластиной: δ111 |
|
|
|||||
5 |
То же после поворота и закрепления пластины δ112 ;δ113 ;δ114 |
|
|
|||||
6 |
Показание индикатора настроечного приспособления для резца 1 со второй |
|
|
|||||
|
пластиной: δ121 |
|
|
|||||
7 |
То же после поворота и закрепления пластины: δ122 ; δ123 ; δ124 |
|
|
|||||
8 |
Параметры, аналогичные п. 4 ... 6 для резца 2: δ211; δ212; δ213; δ214; δ221; |
|
|
|||||
|
δ222; |
δ223; δ224 |
|
|
||||
9 |
Погрешность длины резца 1 после поворота первой пластины: |
|
|
|||||
|
δ1п = δllmaxδ11min |
|
|
|||||
10 |
Погрешность длины резца 1 после замены первой пластины на вторую |
|
|
|||||
|
δ13 = δ12max - δllmin |
|
|
|||||
11 |
Погрешность длины резца 2 после поворота первой пластины: |
|
|
|||||
|
δ2п = δ 21max - δ 21min |
|
|
|||||
12 |
Погрешность длины резца 2 после замены первой пластины на вторую: |
|
|
|||||
|
δ23 = δ22max - δ21min |
|
|
|||||
|
|
|
|
|
|
|
|
|
5. На |
резец |
1 устанавливают и |
закрепляют |
вторую |
пластину. |
||
При неизменной |
настройке приспособления |
и |
резца записывают |
||||
показание |
индикатора. |
Индикатор |
покажет |
погрешность |
размер |
ной настройки при замене пластин классов допусков А или F.
6. Действия, аналогичные п. 3–5 повторяют для резца 2, оснащенного последовательно обеими пластинами.