
- •Оглавление
- •Предисловие
- •Глава 1. Общие вопросы заточки режущих инструментов
- •1.3 Заточные станки
- •1.4 Вопросы для контроля
- •Глава 2. Исследование конструкций резцов
- •2.1 Назначение, типы и конструктивные особенности
- •2.2 Конструктивные элементы резца
- •2.3 Геометрические параметры резца
- •2.4. Износ, критерий затупления и число переточек резцов
- •2.6 Вопросы для контроля
- •Глава 3. Исследование конструкций спиральных свёрл
- •3.1 Назначение, типы и конструктивные особенности
- •3.2 Методы заточки спиральных сверл
- •3.4 Вопросы для контроля
- •Глава 4. Исследование конструкций зенкеров
- •4.1 Назначение, типы и конструктивные особенности
- •4.2 Износ и затачивание зенкеров
- •4.4 Вопросы для контроля
- •5.1 Назначение, типы и конструктивные особенности
- •5.2 Выбор основных параметров
- •5.3 Износ и затачивание разверток
- •5.5 Вопросы для контроля
- •Глава 6. Исследование конструкций фрез
- •6.1 Назначение, типы и конструктивные особенности
- •6.2 Износ и восстановление фрез
- •6.3 Лабораторная работа «Конструкция фрез»
- •6.4 Вопросы для контроля
- •6.6 Вопросы для контроля
- •7.1 Исследование конструкций метчиков
- •7.1.1 Назначение, типы и конструктивные особенности
- •7.1.3 Вопросы для контроля
- •7.1.5 Вопросы для контроля
- •7.1.7 Вопросы для контроля
- •7.2 Исследование конструкций резьбонарезных головок
- •7.2.1. Назначение, типы и конструктивные особенности
- •7.2.3 Вопросы для контроля
- •Глава 8. Исследование конструкций зуборезных долбяков
- •8.1 Назначение, типы и конструктивные особенности
- •8.3 Вопросы для контроля
- •8.5 Вопросы для контроля
- •Глава 9. Исследование конструкций червячных фрез
- •9.1 Назначение, типы и конструктивные особенности
- •9.3 Вопросы для контроля
- •9.5 Вопросы для контроля
- •10.1 Назначение, типы и конструктивные особенности
- •10.3 Вопросы для контроля
- •10.5 Вопросы для контроля
- •10.7 Вопросы для контроля
- •10.9 Вопросы для контроля
- •10.11 Вопросы для контроля
- •11.1 Назначение, типы и конструктивные особенности
- •11.2 Алмазные сверла на связке «МонАлиТ»
- •11.3 Состояние рабочей поверхности сверла
- •11.4 Моделирование процесса алмазного сверления
- •11.5 Оценка режущей способности алмазных свёрл
- •11.7 Вопросы для контроля
- •12.1 Назначение и структура САПР
- •12.3 Вопросы для контроля
- •12.5 Вопросы для контроля
- •12.7 Вопросы для контроля
330
зависимости коэффициента режущей способности от величины рабочей подачи
сверла, анализ полученных результатов.
11.7Вопросы для контроля
1.С каким подводом СОЖ наиболее эффективно проводить процесс обработки отверстий в деталях из хрупких неметаллических материалов алмазными кольцевыми свёрлами (без охлаждения, с наружным подводом СОЖ, с подводом СОЖ во внутреннюю полость сверла).
2.Какая форма режущей части алмазного сверл предпочтительна для обработки отверстий диаметром 1 - 5мм (кольцевая, подковообразная,
пёрочная).
3.Назовите тип связки, на которой изготавливаются алмазные кольцевые свёрла для обработки отверстий в хрупких неметаллических материалов
(органическая, металлическая или керамическая).
4.Какая относительная концентрация алмазов оптимальна для кольцевых свёрл (50%, 100%, 150% или 300%).
5.Назовите цвет жидкости, выходящей из зоны отверстия при нормальном процессе алмазного сверления стекла (белая, бесцветная, прозрачная,
темная).
Список литературы
1.Балыков А. В. Алмазное сверление отверстий в деталях из хрупких неметаллических материалов. – М.: Наука и технология, 2003, – 188 с.
2.Балыков А.В. Формообразование отверстий в деталях из неметаллических материалов алмазным инструментом. Учебное пособие, допущено (УМО АМ)
М. ИЦ ГОУ МГТУ «Станкин», 2007, - с.184 3. Балыков А.В., Липатова А.Б.Формообразование деталей из неметаллических
материалов алмазными кругами. Учебное пособие, допущено (УМО АМ) М.,
ИЦ МГТУ «СТАНКИН», 2009, – с.160

331
Глава 12. Системы автоматизированного
проектирования режущего инструмента
12.1 Назначение и структура САПР
Система автоматизированного проектирования режущего инструмента
(САПР РИ) широко применяется при проектировании объектов инструментальной техники.
САПР - человеко-машинная система объединяющая техническое,
математическое, программное и другие виды обеспечений, параметры и характеристики которых выбираются с учетом конкретных условий инженерного конструирования и проектирования [1]. Структура САПР режущего инструмента представлена на рисунке 12.1.
|
|
|
|
САПР РИ |
|
|
|
|
|
|
||||||
|
|
|
|
|
|
|||||||||||
|
|
|
|
|
|
|
|
|
|
|
|
|
|
|
|
|
|
|
Проектирующие подсистемы |
|
|
|
|
|
Обслуживающие |
подсистемы |
|
||||||
|
|
|
|
|
|
|
|
|||||||||
|
|
|
|
|
|
|
|
|
|
|
|
|
|
|
|
|
|
|
|
|
|
|
|
|
|
|
|
|
|||||
|
|
Расчет цельного РИ |
|
|
|
|
Информационно-поисковая система |
|
||||||||
|
|
|
|
|
|
|
||||||||||
|
|
|
|
|
|
|
|
|
|
|
|
|
|
|
|
|
|
|
|
|
|
|
|
|
|
|
|
|
|
||||
|
|
Расчет сборного РИ |
|
|
|
|
|
БД ГОСТ |
|
|
|
|||||
|
|
|
|
|
|
|
|
|
|
|||||||
|
|
|
|
|
|
|
|
|
|
|
|
|
|
|
||
|
|
Расчет инструмента II порядка |
|
|
|
|
|
|
|
|
|
|
|
|
||
|
|
|
|
|
|
|
|
БД НОРМАЛЬ |
|
|
|
|
||||
|
|
|
|
|
|
|
|
|
|
|
|
|
|
|||
|
|
|
|
|
|
|
|
|
|
|
|
|
||||
|
|
|
|
|
|
|
|
|
|
|
|
|
|
|
|
|
|
Проектирование приспособлений |
|
|
|
|
|
|
|
|
|
|
|||||
|
|
|
|
|
БД ранее спроектированный |
|
|
|
|
|||||||
|
|
|
|
|
|
|
|
|
|
|
|
|
||||
|
|
Проектирование ТП |
|
|
|
|
|
|
|
|
|
|
||||
|
|
|
|
|
|
|
Документирование |
|
|
|||||||
|
|
|
|
|
|
|
|
|
||||||||
|
|
|
|
|
|
|
|
|
|
|
|
|
||||
|
|
… |
|
|
|
|
||||||||||
|
|
|
|
|
|
|
|
|
|
|
||||||
|
|
|
|
|
Графика |
|
|
|||||||||
|
|
|
|
|
|
|
|
|
|
|
|
|
||||
|
|
|
|
Рис. 12.1 |
Структура САПР |
|
||||||||||
|
|
|
|
|
||||||||||||
|
|
|
|
|
Система работает следующим образом. После ввода исходных данных,
информационно-поисковая система (ИПС) в БД ГОСТ, БД НОРМАЛЬ, БД РАНЕЕ СПРОЕКТИРОВАННЫЙ, последовательно производит поиск режущего инструмента необходимого для выполнения заданной операции.
Если инструмент найден, управление передается подсистемам документирования и графики. В результате их работы конструктор получает распечатки с результатами расчета режущего инструмента и рабочий чертеж.
332
Кроме этого, на данном этапе формируется файл данных для связи с
технологической системой.
Если требуемый инструмент не найден, то возможны два варианта:
7.Поиск ближайшего типа размера инструмента с последующей корректировкой конструктивных и геометрических параметров.
8.Расчет новой конструкции при помощи одной из проектирующих подсистем [2].
Проектирующие подсистемы разрабатываются на основе поэлементного метода [3]. Для расчета, в данном случае, необходимо определится с комплектом основных и дополнительных исходных данных, которые зависят от размеров обрабатываемой детали (основные) и требований конструктора
(дополнительные) к проектируемому режущему инструменту. Они могут совпадать с данными введенными в ИПС. В результате работы проектирующей подсистемы конструктор получает рабочий чертеж инструмента, который может корректировать, как при помощи дополнительных исходных данных, так и посредством графических подсистем (например T-flex). При необходимости результаты расчета могут бать занесены в базу данных ранее спроектированного режущего инструмента.
Следует отметить, что серийность производства мало влияет на структуру проектирующей подсистемы и учитывается при разработки методики.
При выборе или разработке системы автоматизированного проектирования технологических процессов этому фактору уделяется особое внимание. Так, при массовом производстве целесообразно использовать не параметрический подход, при серийном блочно-модульный, а при единичном производстве необходимо применять алгоритмизированные параметрические системы технологического проектирования.
Данный комплекс лабораторных работ рассчитан на изучение ПМК применяемых для разработки технологических процессов серийного производства (на примере «СИТЕПП»).
333
СИТЕПП - это программно-методический комплекс, представляющий собой гибкий инструментарий создания интегрированных систем проектирования техпроцессов и оснастки, баз данных, справочников и т.д.,
обеспечивающий комплексную конструкторско-технологическую подготовку машиностроительных производств на единой программно-методической платформе.
Система технологической подготовки производства СИТЕПП предназначена для разработки технологической документации изготовления изделий машиностроения в условиях мелкосерийного и серийного производства, а также для создания файлов для смежных подсистем конструкторской и технологической подготовки производств, разработки управляющих программ для станков с ЧПУ и систем управления производством.
Система СИТЕПП состоит из базового модуля (ядра системы) и
расчетных приложений. Ядро системы обеспечивает взаимосвязь между расчетными приложениями и позволяет создавать технологическую документацию изготовления изделия для всех основных машиностроительных переделов (методов обработки).
Компьютерная система, безусловно, не в состоянии заменить квалифицированного технолога. Поэтому СИТЕПП создана как средство, не подменяющее технолога, а существенно ускоряющее и упрощающее проектирование технологий, расчет параметров технологических процессов,
формирование текстов переходов, выбор необходимой оснастки и инструментов, формирование документации и операционных эскизов.
В лабораторной работе применен так называемый блочно-модульный принцип построения параметрических техпроцессов для серийного и мелкосерийного производства. Он заключается в следующем: каждый модуль состоит из двух блоков: конструкторского и технологического, которые соединены между собой посредством набора параметров средствами ПМК СИТЕПП (обычно этими параметрами является результат работы
334
конструкторской подсистемы). Другими словами, каждой конструкции инструмента соответствует свой технологический процесс. Таким образом,
алгоритмизация происходит на уровне технологических процессов, а не на уровне операций. Такой подход позволяет упростить освоение данной системы технологического проектирования, а также процесс написания и корректировки техпроцессов. Например, для создания нового и корректировки используемого техпроцесса можно применить операцию из уже существующих техпроцессов,
причем полностью, не меняя марки оборудования, типажа режущего и мерительного инструмента и т.д. Также есть возможность подключения заводских таблиц норм времени к конкретным операциям, поэтому машинное время корректировать не обязательно, что позволит упростить его расчет.
Особенностью построения данного вида техпроцессов в СИТЕПП по сравнению с другими системами является то, что не требуется искать критериев выбора операций, так как техпроцесс жестко связан с конструкцией посредством внутренних связей ПМК. Также к преимуществам относится то,
что данной системой может пользоваться как опытный, так и начинающий технолог или просто оператор. Одним из недостатков является увеличение объема работы при создании баз данных.
12.2 Лабораторная работа
«Разработка технологических процессов изготовления режущего инструмента на персональном компьютере (на базе ПМК СИТЕПП)»
Цели и задачи работы. Целью работы является изучение процесса разработки технологического процесса изготовление режущего инструмента и создание технологической документации при помощи ПМК «СИТЕПП» в
условиях серийного производства.
Оборудование, инструменты и приборы. Персональные компьютеры,
оснащенные специализированным программным обеспечением (клиентом работы с базой «СИТЕПП», t-flex CAD).
335
Методика выполнения работы. Для выполнения лабораторной работы необходимо знать основные сведения о режущем инструменте,
конструкционных особенностях и технологии изготовления. В качестве примера рассмотрим вариант разработки технологического процесса изготовления зенкера.
Зенкеры относятся к режущим инструментам, применяемым для получистовой и чистовой обработки отверстий, которые предварительно получены в детали тем или иным способом, например, после отливки, ковки,
штамповки, сверления. Зенкеры обеспечивают точность обрабатываемой детали с допусками по 11-12 квалитетам, при шероховатости полученной поверхности Rz = 20 - 40мкм.
В зависимости от назначения и условий обработки зенкеры имеют различные конструкции и подразделяются на следующие виды: хвостовые цельные, хвостовые сборные со вставными ножами, насадные цельные,
насадные сборные. Зенкеры изготавливают цельными из быстрорежущей стали или сборными с режущими пластинками из твёрдого сплава, напаиваемыми на корпус инструмента. Хвостовые зенкеры крепят с помощью цилиндрических или конических хвостовиков, насадные - имеют коническое посадочное отверстие и торцовую шпонку для предохранения от привертывания в работе.
По конструкции рабочей части хвостовые зенкеры аналогичны спиральным свёрлам, но не имеют поперечной режущей кромки. Число зубьев равно трём. Насадные зенкеры имеют 4-6 зубьев. Заднюю поверхность у цельных зенкеров делают винтовой или конической, у сборных инструментов,
оснащённых твердосплавными пластинами, задняя поверхность оформляется по плоскости. Стружечные канавки у зенкеров выполняют винтовыми (у
цельных зенкеров), косыми (у зенкеров со вставными ножами) и прямыми (у
зенкеров оснащённых твердосплавными пластинами).
Основными конструктивными элементами зенкера являются режущая и калибрующая части, число, профиль и направление стружечных канавок, углы резания, хвостовая часть. На рисунке 12.2 показан хвостовой зенкер из
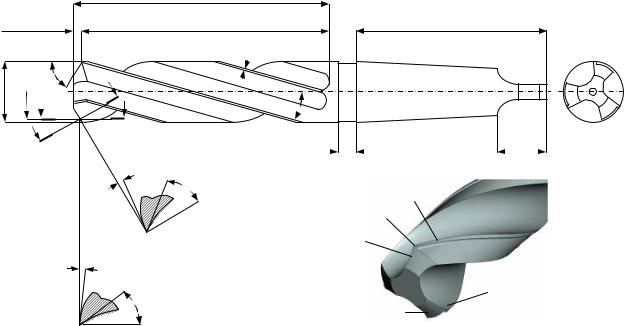
336
быстрорежущей стали, имеющий винтовые передние и задние поверхности.
Хвостовые зенкеры обычно делают сварными - рабочая часть из быстрорежущей стали, хвостовик из сталей 45, 40Х, 45Х. Место сварки обычно делают на шейке. Крутящий момент при работе инструмента передаётся с помощью конического хвостовика за счёт сил трения. Для извлечения зенкера из патрона станка служит лапка. Рабочая часть зенкера состоит из режущей и калибрующей частей.
Режущая |
Рабочая часть |
|
Калибрующая часть |
||
часть |
f
d |
di |
φ |
|
N |
|
0 |
i |
0 |
|
||
|
|
|
|
|
|
|
N |
|
|
N - N |
|
|
|
|
|
|
|
|
|
|
|
αni |
γni |
|
|
|
|
|
|
|
|
|
α0i |
0 - 0 |
|
|
|
|
|
γ0i |
|
|
Хвостовик |
ω |
|
Шейка |
Лапка |
3
5
4
1
2
Рис. 12.2 Эскиз зенкера
Режущая часть состоит из следующих элементов (рис 12.2): 1 - передняя поверхность, 2 - главная задняя поверхность, 3 - вспомогательная задняя поверхность (ленточка f), 4 - главная режущая кромка, 5 - вершина зуба; и
характеризуется следующими угловыми геометрическими параметрами:
передний угол γ, задний угол α, главный угол в плане ω [4].
Разработка технологического процесса изготовления режущего инструмента в ПМК СИТЕПП происходит следующим способом. Перед созданием нового проекта необходимо разработать технологический процесс изготовления зенкера [5] и определить, какую информацию он будет содержать,
например:
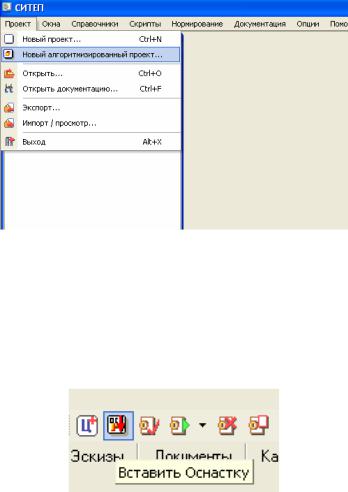
337
1.Наименование операций и переходов;
2.Наименование оборудования;
3.Наименование оснастки;
4.Режущий, измерительный и вспомогательный инструмент;
5.Режимы резания;
6.Операционные эскизы.
Создание проекта происходит в несколько этапов.
Этап 1. Вызовите программу СИТЕПП. Во вкладке «проект» выберите команду «Создайте новый алгоритмизированный проект». (рис. 12.3)
Рис. 12.3 Создание нового проекта
Этап 2. Добавьте в созданный проект оснастку с помощью соответствующей кнопки на панели инструментов (рис 12.4).
Рис. 12.4 Панель инструментов
В строке «Группа» в атрибутах напишите наименование оснастки
(например, зенкер).
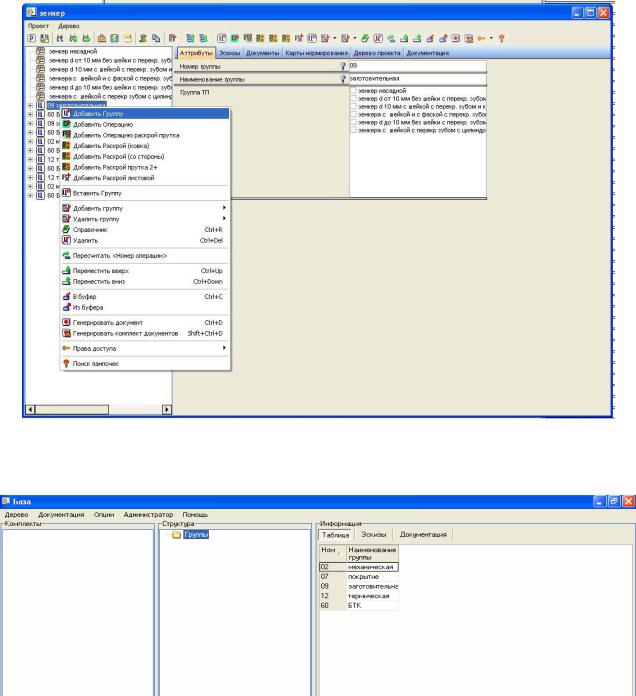
338
Этап 3. Для созданной оснастки выберите необходимые операции из базы данных (нажатием клавишей мышки вызовите контекстное меню
«Добавить группу» (рис 12.5, 12.6).
Рис. 12.5 Добавление группы
Рис.12.6 Окно «База»
Этап 4 Для каждой группы (механическая, покрытие, заготовительная,
термическая или БТК) определите нужное количество операций. Добавьте их в
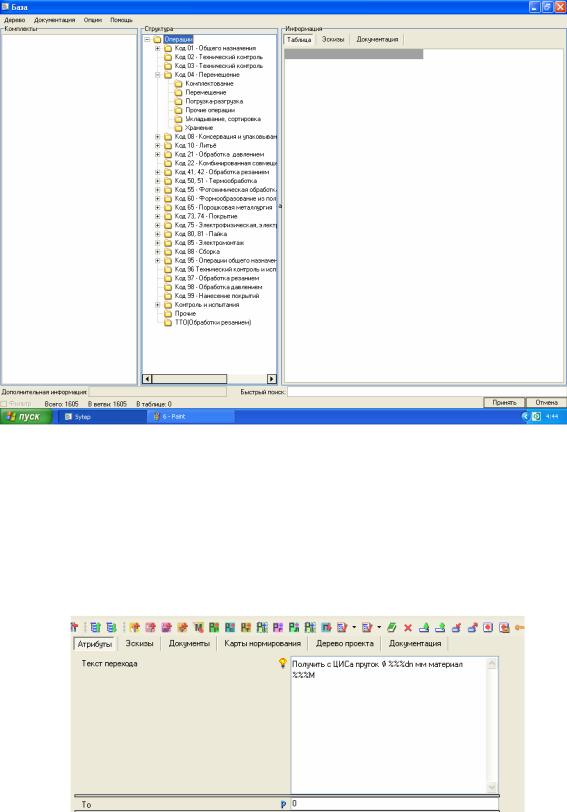
339
соответствующие группы так, как рассмотрено выше (с помощью вызова контекстного меню) (рис 12.7).
Рис. 12.7 Заполнение групп операциями
Этап 5. Для каждой операции составьте необходимое количество переходов, добавьте их и сформулируйте текст перехода в соответствующем атрибуте (рис 12.8).
Рис. 12.8 Вкладка «Атрибуты»
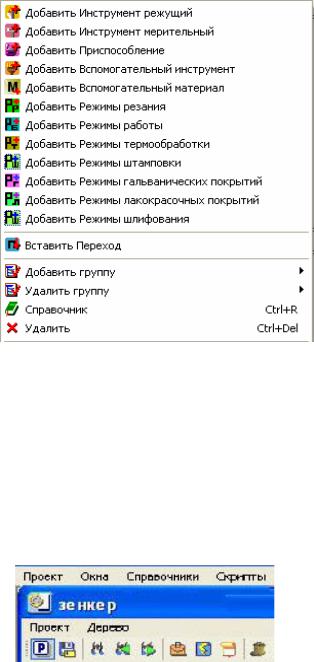
340
Впереходах отметьте шифр инструкции, оборудование, приспособления
ивспомогательные инструменты, необходимые для изготовления вашего инструмента (рис 12.9).
Рис. 12.9 Контекстное меню перехода
Этап 6. Для разработанного техпроцесса составьте список параметров,
используемых в операционных переходах. При зависимости одних параметров от других (например, длины Конуса Морзе от его номера) необходимо составить программу по расчету (рис 12.10,12.11).
Рис. 12.10 Кнопка «Параметры проекта»
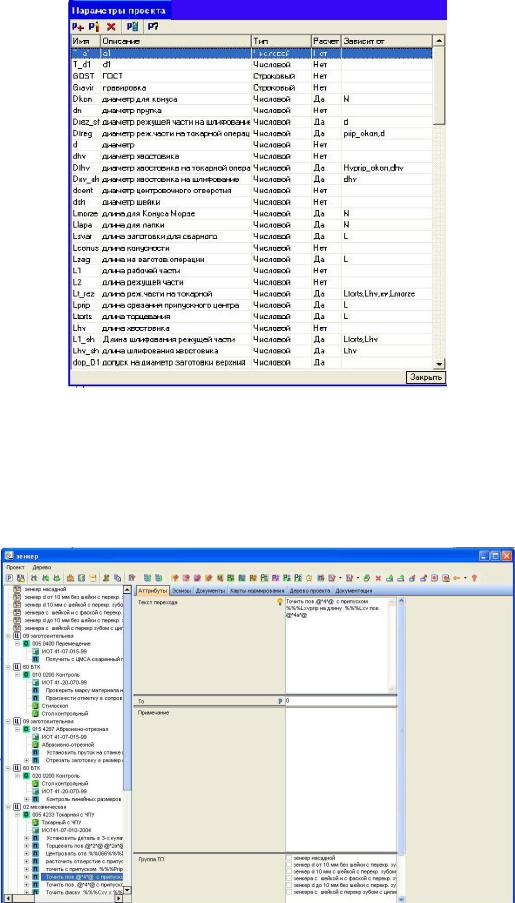
341
Рис. 12.11 Диалоговое окно «Параметры проекта»
Этап 7. После завершения ввода параметров сгенерируйте
технологических процесс и распечатайте документацию (рис. 12.12 ).
Рис. 12.12 Пример готового технологического процесса