
- •Оглавление
- •Предисловие
- •Глава 1. Общие вопросы заточки режущих инструментов
- •1.3 Заточные станки
- •1.4 Вопросы для контроля
- •Глава 2. Исследование конструкций резцов
- •2.1 Назначение, типы и конструктивные особенности
- •2.2 Конструктивные элементы резца
- •2.3 Геометрические параметры резца
- •2.4. Износ, критерий затупления и число переточек резцов
- •2.6 Вопросы для контроля
- •Глава 3. Исследование конструкций спиральных свёрл
- •3.1 Назначение, типы и конструктивные особенности
- •3.2 Методы заточки спиральных сверл
- •3.4 Вопросы для контроля
- •Глава 4. Исследование конструкций зенкеров
- •4.1 Назначение, типы и конструктивные особенности
- •4.2 Износ и затачивание зенкеров
- •4.4 Вопросы для контроля
- •5.1 Назначение, типы и конструктивные особенности
- •5.2 Выбор основных параметров
- •5.3 Износ и затачивание разверток
- •5.5 Вопросы для контроля
- •Глава 6. Исследование конструкций фрез
- •6.1 Назначение, типы и конструктивные особенности
- •6.2 Износ и восстановление фрез
- •6.3 Лабораторная работа «Конструкция фрез»
- •6.4 Вопросы для контроля
- •6.6 Вопросы для контроля
- •7.1 Исследование конструкций метчиков
- •7.1.1 Назначение, типы и конструктивные особенности
- •7.1.3 Вопросы для контроля
- •7.1.5 Вопросы для контроля
- •7.1.7 Вопросы для контроля
- •7.2 Исследование конструкций резьбонарезных головок
- •7.2.1. Назначение, типы и конструктивные особенности
- •7.2.3 Вопросы для контроля
- •Глава 8. Исследование конструкций зуборезных долбяков
- •8.1 Назначение, типы и конструктивные особенности
- •8.3 Вопросы для контроля
- •8.5 Вопросы для контроля
- •Глава 9. Исследование конструкций червячных фрез
- •9.1 Назначение, типы и конструктивные особенности
- •9.3 Вопросы для контроля
- •9.5 Вопросы для контроля
- •10.1 Назначение, типы и конструктивные особенности
- •10.3 Вопросы для контроля
- •10.5 Вопросы для контроля
- •10.7 Вопросы для контроля
- •10.9 Вопросы для контроля
- •10.11 Вопросы для контроля
- •11.1 Назначение, типы и конструктивные особенности
- •11.2 Алмазные сверла на связке «МонАлиТ»
- •11.3 Состояние рабочей поверхности сверла
- •11.4 Моделирование процесса алмазного сверления
- •11.5 Оценка режущей способности алмазных свёрл
- •11.7 Вопросы для контроля
- •12.1 Назначение и структура САПР
- •12.3 Вопросы для контроля
- •12.5 Вопросы для контроля
- •12.7 Вопросы для контроля
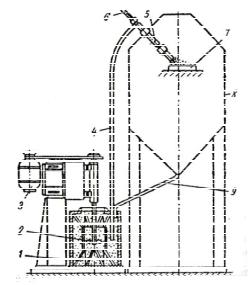
48
производить - абразивно-жидкостным полированием. Этот способ используют в основном для полирования стального инструмента, например стружечных канавок винтовых свёрл, но в некоторых случаях можно применять и для твердосплавного (очистка от грата, припоя, окалины, получение лучшего внешнего вида идр.).
Рис. 1.13 Установка для абразивно-жидкостной обработки
1-мешалка; 2-винт; 3-электродвигатель; 4-трубопровод; 5-форсунка; 6-трубопровод сжатого воздуха; 7-обрабатываемое изделие; 8-корпус установки; 9-трубопровод
На рисунке 1.13 показана схема установки для абразивно-жидкостной обработки с помощью абразивных зёрен (электрокорунд, карбид кремния)
различной зернистости, смешанных с жидкостью и подаваемых в рабочую зону под действием сжатого воздуха. В настоящее время этот способ находит всё большее применение и отличается высокой производительностью и хорошим качеством обработанной поверхности как в отношении чистоты, так и в отношении коррозиоустойчивости.
1.3 Заточные станки
Выбор заточного станка для процесса заточки (переточки) зависит от вида инструмента, его габаритных размеров, инструментального материала,
серийности изготовления инструмента и некоторых других факторов.

49
Заточные станки бывают нескольких видов – универсальные заточные станки, универсальные заточные станки с ЧПУ, специальные заточные станки,
специальные заточные станки с ЧПУ (рис.1.14).
1.3.1 Универсально-заточные станки
Универсально-заточные станки - это основной тип оборудования, ис-
пользуемого в условиях большинства инструментальных цехов, для заточки многолезвийного инструмента: сверл, зенкеров, разверток, фрез, метчиков и долбяков. На них можно затачивать также резцы, червячные фрезы, зуборезные головки и протяжки.
Рис. 1.14 Типы заточных станков
На этих станках имеется возможность выполнения операций круглого
(наружного и внутреннего), а также плоского шлифования.
50
Благодаря достаточно большим технологическим возможностям эти станки получили широкое применение во многих отраслях промышленности для заточки инструментов с достаточной точностью с помощью универсальных и специальных приспособлений.
Основными размерами, характеризующими универсально-заточные станки, являются: наибольший размер (диаметр и длина) устанавливаемого в центровых бабках инструмента; наибольший размер шлифовального круга и мощность привода; наибольшие относительные перемещения шлифовального круга и затачиваемого инструмента; величины угловых поворотов шпинделя шлифовального круга и системы крепления инструмента.
Конструкции универсально-заточных станков отличаются большим разнообразием. Совершенствование конструкций инструментов, изменение характера требований к станкам в связи с повышением свойств инструментальных материалов (применение твердых сплавов,
минералокерамики, алмаза, нитрида бора), точности и способов заточки
(абразивная, алмазная, эльборовая, электрохимикомеханическая) повлекли за собой необходимость изменения конструкций универсально-заточных станков.
Многие годы наиболее распространенными отечественными универсально-заточными: станками были модели ЗА64 и 3641. Базовой моделью следует считать станок ЗА64, по сравнению с которым можно проследить те изменения, которые наметились и в дальнейшем были осуществлены при его модернизации.
1.Повышение жесткости шпиндельного узла за счет применения радиально-упорных шарикоподшипников, а в последствии его исполнения с постоянной гарантированной компенсацией радиального и осевого зазора с помощью цилиндрических пружин.
2.Применение в приводе шпинделя плоского бесконечного ремня из синтетических материалов, что позволило снизить вибрации системы СПИД по сравнению с клиноременной передачей.
3.Увеличение количества скоростей шпинделя шлифовального круга,
51
что позволило использовать оптимальные режимы обработки.
4.Увеличение точности отсчета поперечных подач до 0,01мм и создание механизма тонкой подачи для подвода инструмента к шлифовальному кругу.
5.Обеспечение легкости перемещений, точности основных узлов и удобства обслуживания.
6.Изготовление шпинделя шлифовального круга с внутренними конусными гнездами для установки оправок со шлифовальными кругами, что повысило жесткость и точность крепления кругов.
7.Достижение в результате таких конструктивных изменений,
возможности применения для заточки режущих инструментов кругов из алмаза и нитрида бора.
Эти направления модернизации и были заложены в конструкции новой гаммы более современных универсально-заточных станков на Витебском станкостроительном объединении, которое освоило и приступило к серийному производству новой гаммы универсально-заточных станков моделей: 3640;
ЗБ641; ЗВ641; ЗБ642; ЗВ642 и ЗБ643. Все эти станки, кроме модели 3640,
удовлетворяли требованиям для работы алмазными и абразивными кругами без охлаждения и с охлаждением (табл. 1.25).
Станки моделей 3640, ЗВ641 и ЗВ642 имели только ручное управление.
Станки моделей ЗБ641, ЗБ642 и ЗБ643 были снабжены гидроприводом и допускали следующие циклы работы: ручной при заточке инструментов небольшими партиями или при специальных работах; механизированный -
ручная поперечная подача и деление на зуб, автоматическое продольное перемещение стола; полуавтоматический - ручная поперечная подача, ав-
томатическое продольное перемещение стола и деление.
Автоматическое продольное перемещение стола обеспечивалось встроенным гидроцилиндром, автоматическое деление - специальными гидравлическими съемными приспособлениями. Автоматическая поперечная подача на станке модели ЗБ643 обеспечивалась встроенным механизмом, а на станке модели ЗБ642 – съемным (рис. 1.15). На нем использовалось
52
бесступенчатое регулирование скорости вращения шпинделя с частотой от 1300
до 6500об/мин.
Таблица 1.25 Основные технические параметры универсально-заточных станков
Основные данные |
|
|
Модели станков |
|
|
|||
3640 |
ЗБ64П |
ЗВ641 |
ЗБ642 |
ЗВ642 |
ЗБ643 |
|||
|
|
|||||||
Класс точности |
П |
П |
П |
П |
П |
П |
||
Диаметр |
обрабатываемого |
до 100 |
до 160 |
до 160 |
до 250 |
до 250 |
до 400 |
|
инструмента, мм |
||||||||
|
|
|
|
|
|
|||
Длина |
обрабатываемого |
до 250 |
до 400 |
до 400 |
до 630 |
до 630 |
до 1000 |
|
инструмента (в центрах), мм |
||||||||
|
|
|
|
|
|
|||
|
|
|
|
|
|
|
||
Высота центров, мм |
55 |
80 |
80 |
125 |
125 |
200 |
||
Размеры стола, |
63х |
100х |
100х |
140х |
140х |
200х |
||
мм (ширина х длина) |
400 |
630 |
630 |
900 |
900 |
1400 |
||
Угол поворота стола, ° |
90 |
90 |
90 |
90 |
90 |
90 |
||
Привод продольного |
ручн. |
гидравл. |
ручн. |
гидравл. |
ручн. |
гидравл. |
||
перемещения стола |
||||||||
|
|
|
|
|
|
|||
Угол поворота шлифовальной |
- |
350 |
350 |
350 |
350 |
350 |
||
|
бабки, ° |
|||||||
|
|
|
|
|
|
|
||
Диаметр шлифовального |
до 100 |
до 150 |
до 150 |
до 200 |
до 200 |
до 250 |
||
|
круга, мм |
|||||||
|
|
|
|
|
|
|
||
|
|
2300.... |
1120.... |
1120.... |
1300... |
2240... |
1500..... |
|
Частота вращения круга, |
..10000 |
...9000 |
...9000 |
...6500 |
...5250 |
|||
...6300 |
||||||||
(6 |
(4 |
(4 |
бессту- |
бессту- |
||||
|
об/мин |
(4 сту- |
||||||
|
ступе- |
ступе- |
ступе- |
пенча- |
пенча- |
|||
|
|
пени) |
||||||
|
|
ней) |
ни) |
ни) |
тое |
тое |
||
|
|
|
||||||
Мощность привода |
0,27 |
0,56/0,7 |
0,56/0,7 |
1,5 |
1,0/0,75 |
2,2 |
||
шлифовального круга, кВт |
||||||||
|
|
|
|
|
|
|||
|
|
12мм |
|
|
|
|
|
|
Размеры |
внутренних конусов |
на- |
|
|
|
|
|
|
шлифовального шпинделя |
ружн. |
№2 |
№2 |
№3 |
№3 |
№4 |
||
(конус- |
||||||||
|
(Морзе) |
|
|
|
|
|
||
|
ность |
|
|
|
|
|
||
|
|
1:5) |
|
|
|
|
|
|
Возможность |
- |
+ |
+ |
+ |
+ |
+ |
||
работы |
алмазными кругами |
|||||||
|
|
|
|
|
|
|||
Размеры станка |
1200х |
1530х |
1530х |
2330х |
2330 |
З600х |
||
(длина х ширина х высота), |
780х |
1345х |
1345х |
1660х |
1660х |
1750х |
||
|
мм |
1550 |
1410 |
1410 |
1550 |
1550 |
1740 |
|
Масса станка, кг |
414 |
750 |
700 |
1280 |
1230 |
2500 |
Различия в конструкциях узлов станков ЗБ642, ЗВ642, ЗБ641 и ЗВ641
незначительны.
Все гидрофицированные станки имели распределительные колодки для подсоединения шлангов гидравлических приспособлений.
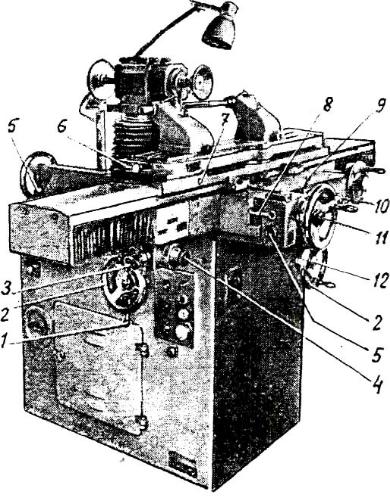
53
Впоследние годы модели универсально-заточных станков,
находящихся в эксплуатации, заметно изменилась (табл. 1.26).
Рис. 1.15 Общий вид станка модели ЗБ642 1 - рукоятка включения медленной вертикальной подачи; 2 - маховик вертикальный
подачи; 3 - распределительная колодка; 4 - кран управления; 5 - маховичок тонкой поперечной подачи; 6 - рукоятка закрепления стола; 7 - винт поворота стола; 8 - рычаг толчковый поперечной подачи; 9 - рукоятка гидравлического реверса стола; 10 - кнопка включения гидравлического перемещения стола; 11 - кнопка включения тонкой поперечной подачи; 12 - кнопка включения медленной вертикальной подачи
Универсально-заточной станок 3644 предназначен для шлифования,
заточки и доводки мелких инструментов. Станок снабжен специальным микроскопом для измерения линейных и угловых параметров и наблюдения за зоной обработки.
Универсально-заточные станки ЗВ642, ЗМ642, ЗМ642Е, ЗД642Е
предназначены для заточки и доводки разнообразного режущего инструмента. Шлифовальная бабка этих станков имеет наклон до 20°.
54
Универсально-заточные станки моделей ВЗ-318 и ВЗ-318Е,
выпускаемые в настоящее время компанией «ВИЗАС» (бывший Витебский завод заточных станков), предназначены для заточки и доводки основных видов режущих инструментов из инструментальных сталей, твердых сплавов и минералокерамики абразивными, алмазными и эльборовыми кругами. На станках возможно выполнять шлифовальные работы: круглое шлифование
(наружное и внутреннее) и плоское шлифование. Станок модели ВЗ-318Е
имеет гидрофицированный привод продольного перемещения стола и вертикальное механизированное перемещение шлифовальной головки со скоростью 390мм/мин.
1.3.2 Универсально-заточные станки с ЧПУ
Наиболее перспективным типом этого оборудования являются уни-
версально-заточные станки с ЧПУ, позволяющие значительно усовершен-
ствовать технологию заточки инструментов, повысить их стойкость и точность, что связано со снижением биения зубьев, уменьшением шероховатости заточенных поверхностей, строгой регламентацией режимов обработки и отсутствием дефектов заточки.
Универсально-заточные станки с ЧПУ могут иметь от двух до семи управляемых координат (рис. 1.16).
Станки с двумя управляемыми координатами (X, А) используют для заточки передних и задних поверхностей многолезвийных инструментов цилиндрической формы с прямыми и винтовыми зубьями.
Станки с тремя управляемыми координатами (X, Z, А) позволяют за-
тачивать также зубья, расположенные на торце инструмента, в том числе и шаровой формы.
На станках с четырьмя управляемыми координатами (X, У, Z, А)
можно затачивать и инструмент конической формы.
55
На станках с пятью управляемыми координатами (X, У, Z, А, С) имеется возможность изменять положение оси затачиваемого инструмента в процессе обработки, что необходимо при заточке передних поверхностей с аксиально-
переменным шагом, а также задних поверхностей фасонного инструмента торцом круга.
Таблица 1.26 Технические характеристики универсально-заточных станков
отечественного производства последних лет
Основные данные |
3644 |
ЗД641Е |
ЗД642Е |
ЗЕ642 |
ЗМ642Е |
ВЗ-318 |
ВЗ-318Е |
|
Класс точности |
В |
П |
П |
П |
П |
В |
В |
|
Диаметр обраба- |
65 |
до 160 |
до 250 |
до 250 |
до 250 |
до 200 |
до 200 |
|
тываемого инструмента |
||||||||
(в центрах), мм |
|
|
|
|
|
|
|
|
Длина обрабатываемого |
|
|
|
|
|
|
|
|
инструмента (в центрах), |
- |
до 400 |
до 500 |
до 630 |
до 500 |
до 500 |
до 500 |
|
мм |
|
|
|
|
|
|
|
|
Высота центров, мм |
- |
80 |
125 |
125 |
125 |
100 |
100 |
|
Размеры стола, мм |
- |
400x63 |
|
900x140 |
800x140 |
|
|
|
|
|
|
|
|
|
|
|
|
Угол поворота стола, ° |
±90 |
±50 |
+ 45 |
±45 |
+45 |
+ 45 |
±45 |
|
Привод продольного |
ручной |
гидравл. |
гидравл. |
гидравл. |
гидравл. |
ручной |
гидравл. |
|
перемещения стола |
|
|
|
|
|
|
|
|
Угол поворота |
- |
+ 180 |
±180 |
± 180 |
± 180 |
+ 180 |
+ 180 |
|
шлифовальной бабки, ° |
||||||||
|
|
|
|
|
|
|
||
|
|
|
|
|
|
|
|
|
Диаметр шлифовального |
до 100 |
до 150 |
до 200 |
до 200 |
до 200 |
до 150 |
до 150 |
|
круга, мм |
|
|
|
|
|
|
|
|
Частота вращения круга, |
2800... |
2800 |
2000 |
2240.... |
2240 |
7800 |
2800.... |
|
…8000 |
....8000 |
...7000 |
6300 (4 |
6300 |
8000 |
8000 (4 |
||
мин-1 |
(4 |
(6 ступе |
(бессту- |
(4 |
(4 |
|||
|
ступени) |
ней) |
пенчато) |
ступени) |
ступени) |
ступени) |
ступени) |
|
Мощность привода |
0,55 |
0,95 |
2,2 |
1,5 |
1,5/1,1 |
0,71/0,8 |
0,71/0,8 |
|
шлифовального круга, |
||||||||
кВт |
|
|
|
|
|
5 |
5 |
|
|
|
|
|
|
|
|
||
Размер внутреннего |
|
|
|
|
|
|
|
|
конуса Морзе |
№3 |
№2 |
№3 |
№3 |
№3 |
№3 |
№3 |
|
шлифовального |
||||||||
|
|
|
|
|
|
|
||
шпинделя |
|
|
|
|
|
|
|
|
Размеры станка |
770х |
1530х |
1715х |
2330х |
1800х |
1185х |
1460х |
|
х850х |
х1345х |
х1720х |
х1660х |
х1470х |
х1195х |
х1530х |
||
(L х В х Н),мм |
||||||||
х1530 |
х1410 |
х1636 |
х1550 |
х1625 |
х1630 |
х1660 |
||
|
||||||||
Масса станка, кг |
500 |
1100 |
1500 |
1250 |
1600 |
1020 |
1150 |
На станках с пятью управляемыми координатами (X, У, Z, А, С) имеется возможность изменять положение оси затачиваемого инструмента в процессе обработки, что необходимо при заточке передних поверхностей с аксиально-

56
переменным шагом, а также задних поверхностей фасонного инструмента торцом круга.
Введение программируемого поворота шлифовальной бабки, оснащенной несколькими шлифовальными шпинделями, превращает станки с шестью управляемыми координатами (X, У, Z, А, В, С) в заточные центры,
позволяющие обрабатывать сложный многолезвийный инструмент по всем поверхностям с одной установки, что значительно повышает его точность.
Рис.1.16 Универсально-заточные станки с ЧПУ с четырьмя (а), пятью (б) и шестью (в) управляемыми координатами: X - продольное перемещение стола; Y, Z - вертикальное и поперечное перемещение шлифовальной головки; А - вращение шпинделя изделия; В - поворот шлифовальной бабки; С - поворот бабки изделия вокруг вертикальной оси.
Характеристики ряда моделей универсально-заточных станков с ЧПУ отечественного производства приведены в таблице 1.27.
Универсально-заточной станок с ЧПУ модели ВЗ-208ФЗ (рис. 1.17)
предназначен для заточки многолезвийного инструмента (фрез, разверток,
метчиков, плоских протяжек и др.) по передним и задним поверхностям.
Заточка ведется без охлаждения преимущественно эльборовыми и алмазными кругами. Передние и задние поверхности чаще всего затачивают с разных установок (пооперационно).
На станке затачивают инструменты с прямыми и винтовыми зубьями,
расположенными на цилиндре или конусе (рис. 1.18), а также расположенные на торце. Задние поверхности на периферии и на торце можно заточить с одной установки при использовании тороидального шлифовального круга,
установленного под углом 45°.
57
Угол поворота шлифовальной бабки ±180°. Угол поворота стола станка
±45°.
Принципиальная компоновка станка, за исключением приводов про-
граммируемых перемещений по соответствующим координатам, напоминает обычные универсально-заточные станки без систем ЧПУ.
В качестве выходных звеньев механизмов продольной, поперечной и вертикальной подач используются винтовые пары качения, собранные с предварительным натягом, а в качестве приводов - транзисторные следящие электроприводы ПРП-1 с высокомоментными двигателями постоянного тока ДК-1.
Таблица 1.27 Технические характеристики универсально-заточных станков с ЧПУ
отечественного производства
Основные данные |
|
Модели станков |
|
|||
ВЗ-208ФЗ |
ВЗ-215Ф4 |
ВЗ-409Ф4 |
ВЗ-392Ф4 |
ВЗ-417Ф4 |
||
|
||||||
Класс точности станка |
В |
В |
В |
В |
В |
|
Число управляемых осей |
4 |
5 |
5 |
5 |
5 |
|
координат |
||||||
|
|
|
|
|
||
Наибольший диаметр |
|
|
|
|
|
|
изделия, |
|
|
|
|
|
|
устанавливаемого: |
|
|
|
|
|
|
- в цанговом патроне, мм; |
- |
|
20 |
25 |
32/50 |
|
- над поворотным столом, |
до 250 |
250 |
250 |
200 |
250 |
|
мм |
|
|
|
|
|
|
Наибольшая длина |
|
|
|
|
|
|
изделия, мм, |
|
|
|
|
|
|
устанавливаемого: |
|
|
- |
- |
- |
|
- в центрах; |
до 750 |
800 |
||||
160 |
160 |
250 |
||||
- в цанговом патроне |
- |
- |
||||
|
|
|
||||
Наибольший диаметр |
до 200 |
до 200 |
200 |
150 |
150 |
|
шлифовального круга, мм |
||||||
|
|
|
|
|
||
Частота вращения |
2240...6300 |
2000... 7000 |
|
|
|
|
шлифовального |
(4 ступени) |
(бесступен- |
2000... 6000 |
2000...6000 |
2000...6000 |
|
шпинделя, об/мин |
|
чатое) |
|
|
|
|
Мощность |
|
|
|
|
|
|
электродвигателя привода |
1,5/1,1 |
3,44 |
4 |
2,2 |
7,5 |
|
шлифовального круга, кВт |
|
|
|
|
|
|
Габаритные размеры |
2360x1725х |
3000х2850х |
3000х2850х |
1500х2620х |
1920х2860х |
|
станка L х В х Н, мм |
х1600 |
х2080 |
х2080 |
х2000 |
х2000 |
|
Масса станка с отдельно |
|
|
|
|
|
|
расположенным |
2300 |
3400 |
3500 |
2000 |
2000 |
|
оборудованием, кг |
|
|
|
|
|

58
Полуавтомат оснащен системой ЧПУ типа 2С42, обеспечивающей управление по четырем координатам (из них две одновременно управляемые).
В режиме наладки с пульта системы ЧПУ можно осуществлять пере-
мещение по четырем осям координат.
Рис. 1.17 Схема универсально-заточного станка ВЗ-208ФЗ с ЧПУ: МА, Мх, My, Mz - двигатели для программируемых перемещений по соответствующим координатам.
Полуавтомат специальный шлифовально-заточной с ЧПУ модели ВЗ409Ф4 предназначен для вышлифования стружечных канавок и заточки любых режущих инструментов из быстрорежущих сталей и твердых сплавов по любым поверхностям абразивными, эльборовыми и алмазными кругами с охлаждением.
Наличие пяти управляемых осей позволяет вести обработку изделий с одного установа по всем поверхностям, что увеличивает производительность за счет сокращения вспомогательного времени, повышает точность обработки вследствие устранения погрешностей, возникающих при переустановке заготовки, и облегчает труд оператора.
Применение удлиненного фланца для шлифовальных кругов позволяет устанавливать сразу три круга, что дает возможность обрабатывать изделие поочередно разным инструментом с одного установа. На полуавтомате

59
осуществляется правка шлифовального круга и измерение параметров
обрабатываемого изделия посредством встроенного датчика фирмы
«MARPOSS».
Рис. 1.18 - Заточка многолезвийного инструмента на универсально-заточном станке с ЧПУ: а - конической концевой фрезы по передней поверхности винтового зуба тарельчатым кругом; б - цилиндрической концевой фрезы по задней поверхности винтового и торцового
зубьев тороидальным кругом; в - концевой фрезы со сферическим концом по задней поверхности винтового и радиусного зубьев тороидальным кругом, г -плоской протяжки по задней поверхности гаечным кругом; д – метчика по задней поверхности режущей части кругом прямого профиля (затачивание заборного конуса).
Применение устройства ЧПУ SINUMERIK 810D и вентильных двигателей производства фирмы SIEMENS (Германия), гарантирует высокое качество управления и обеспечивает надежную работу станка.
Устройство ЧПУ SINUMERIK 810D дает возможность осуществлять любое движение с использованием линейной, круговой, винтовой и сплайновой интерполяции; характеризуется свободным программированием и позволяет вести управление от ЭВМ высшего ранга.
Диапазон контурной скорости 0,01...6м/мин. Дискретность задания перемещений: линейных 0,001мм, угловых 0,001°.
Наибольшее продольное перемещение (координата X - стол) - 400мм;
наибольшее вертикальное перемещение шлифовальной головки (координата У
- колонна) - 285мм; наибольшее поперечное перемещение (координата Z -
каретка поперечная) - 210мм; наибольший угол поворота стола в
60
горизонтальной плоскости (координата В – стол поворотный) - 200°;
наибольший угол поворота шпинделя бабки изделия (координата А),°, не ограничено.
Шлифовально-заточной полуавтомат с ЧПУ модели ВЗ-392Ф4
предназначен для заточки и шлифовки стружечных канавок различных режущих инструментов из быстрорежущих сталей и твердых сплавов по любым поверхностям абразивными, эльборовыми и алмазными кругами с охлаждением. Станок имеет компактную конструкцию с закрытой кожухом зону обработки. Доступ с трех сторон.
Полуавтомат имеет программное управление по пяти осям. Система управления SINUMERIK фирмы SIEMENS позволяет обрабатывать самые сложные профили инструмента при малом времени наладки и простом обслуживании.
Бабка изделия (оси Z, А и С). Бабка изделия (ось А) смонтирована на поворотном столе (ось С), узел поворота которого закреплен на поперечных салазках (ось Z). Высокопрецизионные червячные зацепления и подшипники позволяют осуществлять точное деление изделия и его разворот относительно двух взаимно перпендикулярных осей.
Шлифовальная бабка (оси X, У) – смонтирована на вертикальном ползуне
(У), который перемещается по колонне, установленной на продольных,
салазках (X).
Все перемещения по линейным координатам осуществляются в беззазорных направляющих линейного перемещения через высокоточные предварительно натянутые ходовые пары винт-гайка качения. Движение по осям производится от вентильных двигателей.
Система управления SINUMERIK фирмы SIEMENS характеризуются сложными перемещениями с высокими динамическими параметрами; воз-
можностью любого движения, как линейного, кругового или онлайнового, так и свободно задаваемого математическими функциями; удобным диалогом, в
61
котором система управления опрашивает оператора; свободным управлением;
управлением системой через персональный компьютер.
Пределы контурной скорости 0,01...6м/мин. Дискретность задания перемещений: линейных 0,001мм, угловых 0,001°.
Наибольшее перемещение по координатам: продольное (координата X) - 200мм; вертикальное (координата У) - 175мм; поперечное (координата Z) - 200мм; поворот шпинделя бабки изделий вокруг горизонтальной оси
(координата А) - не ограничено; поворот бабки изделия вокруг вертикальной оси (координата С) - 200°.
Число управляемых координат 5, из них одновременно 5.
Полуавтомат шлифовально-заточной с ЧПУ модели ВЗ-417Ф4 - пред-
ставляет собой широкоуниверсальный шлифовально-заточной станок с ЧПУ и предназначен для вышлифовки стружечных канавок с любыми параметрами.
На всех видах режущего инструмента из быстрорежущих ста лей и твердых сплавов, а также заточки всех видов инструмента по любым поверхностям абразивными, алмазными и эльборовыми шлифовальными кругами с охлаждением и без него.
Устройство ЧПУ SINUMERIK 840D производства фирмы SIEMENS (Германия) характеризуется: высокоточными и высокодинамичными пе-
ремещениями; возможностью осуществления любого движения с исполь-
зованием линейной, круговой, винтовой, сплайновой и полиномной интер-
поляции; свободным программированием; возможностью управления в диалоговом режиме; возможностью управления посредством персонального компьютера.
Перемещения по осям осуществляются вентильными двигателями с цифровым управлением производства фирмы SIEMENS.
Полуавтомат имеет гидрофицированный зажим-разжим заготовок в шпинделе бабки изделия и шлифовального круга в шлифовальной бабке.
62
Перемещения по осям X, У, Z осуществляются по шариковым линейным направляющим качения фирмы NSK, сочетающим в себе легкость хода,
высокую точность и жесткость.
Каждая из применяемых инструментальных оправок может нести три шлифовальных круга одновременно.
На станке предусмотрена возможность установки автоматического измерительного устройства производства фирмы MARPOSS, а также высокоэффективной и надежной системы подачи и очистки СОЖ производства фирмы SOMERMEYER и HKS, дающей возможность резко повысить интенсивность обработки заготовок при сохранении качества и точности изделий.
Оригинальная конструкция ограждения дает возможность при хорошей герметичности и обзоре зоны резания иметь удобный доступ к рабочим органам полуавтомата для обслуживания и настройки.
Возможность одновременного управляемого интерполируемого перемещения по пяти осям позволяет вести обработку изделия с одного установа по всем поверхностям.
Пределы контурной скорости на полуавтомате 0,01-6м/мин.
Дискретность задания перемещений: линейных 0,001мм; угловых 0,01°.
Наибольшее перемещение по координатам: X (продольное перемещение)
-400мм; У (вертикальное перемещение) - 210мм; Z (поперечное перемещение)
-320мм; А (поворот шпинделя бабки изделия) - не ограничено; В (поворот стола) ± 100°.
Компоновка полуавтомата удобная и позволяет рационально использовать все его рабочее пространство.
Быстрое развитие заточных станков с ЧПУ создает предпосылки для включения участка централизованной заточки инструмента в состав ГПС, с
управлением от центральной ЭВМ. Для встроенного в ГПС заточного участка должны использоваться девятикоординатные заточные станки с ЧПУ, у
которых помимо координат, имеющихся у шестикоординатных станков X, У, Z,
63
А, В, С, должны быть еще две координаты W, V - поступательных перемещений крестового суппорта поворотной части бабки изделия и одна координата D поворота (наклона) шлифовального круга в вертикальной плоскости. При точной настройке абсолютных нулевых точек по каждой из координат можно по программе, переданной от центральной ЭВМ в УЧПУ станка, точно привести шлифовальный круг в исходное положение и провести необходимую заточку или вышлифовывание канавок инструментов,
используемых для обработки деталей в ГПС. Результаты автоматического измерения заточенного инструмента передаются в центральную ЭВМ и используются для введения коррекции в программу многооперационного станка при работе этим инструментом.
1.3.3 Специальные заточные станки
Поскольку все режущие инструменты имеют высокую твердость, не-
обходимую для выполнения процесса обработки, то точность их размеров и
шероховатость рабочих поверхностей обеспечивается на шлифовально-
заточных операциях. Наличие на инструментах сложных поверхностей требует в ряде случаев применения специальных станков и приспособлений.
При сравнительно небольших партиях изделий, что характерно для инструментальных цехов, не представляется возможным широко использовать
в них высокопроизводительные специальные шлифовальные и за
точные станки. В связи с этим заточные участки машиностроительных
предприятий |
комплектуются чаще всего универсальным |
оборудованием, |
на котором |
используются специальные приспособления, |
вспомогательный |
и мерительный инструменты.
На специализированных станках производится заточка инструмента,
как правило, одного вида. Специализированные заточные станки высоко-
производительны и обеспечивают более точную обработку затачиваемых поверхностей инструмента. Однако их применение целесообразно, если станок загружен не менее чем на 50% рабочего времени или когда необходимая
64
точность инструмента не может быть достигнута на универсальном оборудовании. Особенно это касается инструментов, используемых на автоматических линиях, многоцелевых станках и станках с ЧГГУ, работающих в составе ГПМ, ГПУ и ГПЦ.
Для заточки резцов используют также специализированные станки.
Станок ЗД625 применяют для предварительной абразивной заточки твердосплавных и быстрорежущих резцов торцом чашечного или сегментного круга.
Станок ЗВ622Д предназначен для чистовой заточки и доводки твер-
досплавных и быстрорежущих резцов алмазными и эльборовыми кругами.
Резец, лежащий на наклонном столе в незакрепленном состоянии, затачивают вручную.
Заточный станок модели ЗБ632В для заточки и доводки резцов вручную -
двухсторонний, оснащен приспособлениями для заточки передней поверхности резцов, образования стружколомающих порожков и канавок. Алмазные или абразивные круги устанавливают на концах шпинделя, служащего валом электродвигателя.
Станок 3629Р применяют для заточки твердосплавных и быстрорежущих резцов (резьбовых и галтельных) по главной, вспомогательной и переходной
(радиусной) кромкам. Заточка производится торцом алмазного круга на металлической связке с электроэрозионной правкой и охлаждением.
Продольная подача механизирована. Настройку производят с помощью микрометрических упоров, шкал и лимбов, обеспечивающих точность ус-
тановки по линейным и угловым размерам, соответственно, ±0,01мм и ±10. Для ориентации резца и совмещения плоскости круга с осью поворота суппорта используют микроскоп.
На станке модели 3622 можно производить заточку резцов, оснащенных пластинками из твердого сплава, быстрорежущей стали и сверхтвердых материалов. На этом станке резцы затачиваются и доводятся по задним
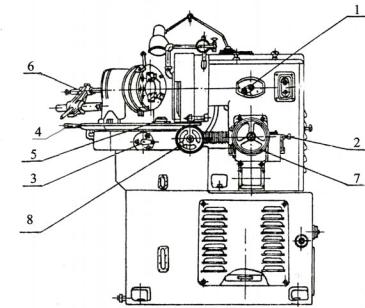
65
поверхностям торцом алмазного и эльборового круга. Возможна заточка резцов по передней поверхности кругом прямого профиля.
Общий вид заточного специального станка для заточки сверл и зенкеров
(полуавтомат 3659А) представлен на рис. 1.19
Рис. 1.19 Общий вид станка 3659А для заточки сверл и зенкеров
Настройку станка для заточки производят в следующей последовательности: рукояткой 1 (рис. 1.19) настраивают величину заднего угла; рукояткой 2 устанавливают подачу на одно перо инструмента, а
рукояткой 3 заданное количество зубьев. Рукояткой 4 поворачивают верхнюю часть каретки в положение, соответствующее углу при вершине 2φ
затачиваемого инструмента по шкале 5; рукояткой 6 закрепляют задний центр инструмента; маховичок 7 поворачивают на 40° и тем самым включают вращение патрона, планетарное и осевое перемещение заточного круга;
маховичком 7 при дальнейшем повороте устанавливают необходимую величину слоя металла, снимаемого с инструмента; маховичком 8 подводят инструмент к заточному кругу; рукоятку 2 нажимают в осевом направлении и тем самым включают автоматическую подачу; по окончании цикла маховичок 7
автоматически возвращается в исходное положение; при этом инструмент отводится от круга, и вращение патрона прекращается.
66
1.3.4 Специальные заточные станки с ЧПУ
Наиболее ярким представителем этого типа станка являются станки для заточки червячных фрез.
Фрезы с винтовой передней поверхностью затачивают конической по-
верхностью круга методом многопроходной обработки, причем на станках без программного управления, деление осуществляют после каждого двойного хода круга по канавке, а круговая подача на глубину шлифования производится после полного поворота фрезы. Таким образом, для снятия припуска требуется несколько оборотов фрезы. После съема основной части припуска обычно производят правку круга с компенсацией его износа. Заточку заканчивают одним - тремя выхаживающими оборотами фрезы.
На станках с ЧПУ деление производится после съема всего припуска с обрабатываемого зуба, а круговая подача идет периодически после каждого одинарного или двойного хода. Следовательно, весь припуск снимается за один оборот фрезы. Второй оборот используется для выхаживания. Однооборотная заточка повышает производительность обработки в 1,5...2 раза.
При заточке червячных фрез на станках с микропроцессорным управ-
лением можно осуществить наиболее рациональный в заданных условиях цикл обработки.
Червячные фрезы с прямыми канавками затачивают торцом шлифо-
вального круга тарельчатой формы с заборным конусом (для фрез классов точности В и С) или с острой кромкой (для фрез классов А и АА) методом глубинного шлифования. Заточку производят эльборовыми (для фрез из быстрорежущей стали) и алмазными (для твердосплавных зубьев) кругами.
Глубинная заточка эльборовым кругом на керамической связке (ЛП-12СТ1-СТ2
ОП9; 100-150%) производится со скоростью круга 22...25м/с, скоростью продольной подачи и подачей на глубину шлифования соответственно
0,6м/мин и 0,5мм при предварительной заточке и 0,2м/мин и 0,1...0,3мм при окончательной заточке, СОЖ (Укринол-14 с химически активными
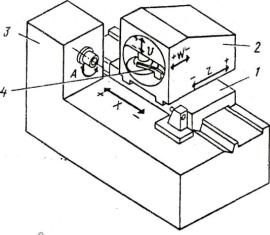
67
присадками) с подачей около 100л/мин. Глубинный метод заточки алмазным кругом на металлической связке (АС4 125/100 Ml-01 100%) производится со скоростью круга 18...20м/с, скоростью продольной подачи 0,3м/мин и подачей на глубину шлифования 0,2.. .0,4мм. СОЖ и ее подача такие же.
Полуавтомат моделей ЗВ663ВФЗ предназначен для заточки (в условиях единичного и мелкосерийного производства) червячных фрез по передней поверхности. На полуавтоматах можно затачивать дисковые модульные и резьбовые фрезы, а также другие многолезвийные инструменты с равномерно расположенными по окружности стружечными канавками.
Полуавтомат имеет пять координат (рис.1.20): X - продольное переме-
щение шлифовальной головки 2; А - вращение шпинделя бабки 3 изделия; U и W - соответственно вертикальное и горизонтальное перемещение алмаза,
предназначенного для правки конической боковой поверхности шлифовального круга с углом профиля 20° по специальной кривой.
Рис. 1.20 Система координат полуавтомата модели ЗВ663ВФЗ для заточки червячных фрез
Дискретность перемещений по координатам X, Z, U и W составляет
0,001мм, по координате А - 0,001°. Вертикальное перемещение алмаза обеспечивается с достаточной степенью точности качательным движением рычага 4, несущего алмаз и приводимого во вращение от механизма с дис-
ковым кулачком и цилиндрическим толкателем (эквидистанта к профилю