
- •Оглавление
- •Предисловие
- •Глава 1. Общие вопросы заточки режущих инструментов
- •1.3 Заточные станки
- •1.4 Вопросы для контроля
- •Глава 2. Исследование конструкций резцов
- •2.1 Назначение, типы и конструктивные особенности
- •2.2 Конструктивные элементы резца
- •2.3 Геометрические параметры резца
- •2.4. Износ, критерий затупления и число переточек резцов
- •2.6 Вопросы для контроля
- •Глава 3. Исследование конструкций спиральных свёрл
- •3.1 Назначение, типы и конструктивные особенности
- •3.2 Методы заточки спиральных сверл
- •3.4 Вопросы для контроля
- •Глава 4. Исследование конструкций зенкеров
- •4.1 Назначение, типы и конструктивные особенности
- •4.2 Износ и затачивание зенкеров
- •4.4 Вопросы для контроля
- •5.1 Назначение, типы и конструктивные особенности
- •5.2 Выбор основных параметров
- •5.3 Износ и затачивание разверток
- •5.5 Вопросы для контроля
- •Глава 6. Исследование конструкций фрез
- •6.1 Назначение, типы и конструктивные особенности
- •6.2 Износ и восстановление фрез
- •6.3 Лабораторная работа «Конструкция фрез»
- •6.4 Вопросы для контроля
- •6.6 Вопросы для контроля
- •7.1 Исследование конструкций метчиков
- •7.1.1 Назначение, типы и конструктивные особенности
- •7.1.3 Вопросы для контроля
- •7.1.5 Вопросы для контроля
- •7.1.7 Вопросы для контроля
- •7.2 Исследование конструкций резьбонарезных головок
- •7.2.1. Назначение, типы и конструктивные особенности
- •7.2.3 Вопросы для контроля
- •Глава 8. Исследование конструкций зуборезных долбяков
- •8.1 Назначение, типы и конструктивные особенности
- •8.3 Вопросы для контроля
- •8.5 Вопросы для контроля
- •Глава 9. Исследование конструкций червячных фрез
- •9.1 Назначение, типы и конструктивные особенности
- •9.3 Вопросы для контроля
- •9.5 Вопросы для контроля
- •10.1 Назначение, типы и конструктивные особенности
- •10.3 Вопросы для контроля
- •10.5 Вопросы для контроля
- •10.7 Вопросы для контроля
- •10.9 Вопросы для контроля
- •10.11 Вопросы для контроля
- •11.1 Назначение, типы и конструктивные особенности
- •11.2 Алмазные сверла на связке «МонАлиТ»
- •11.3 Состояние рабочей поверхности сверла
- •11.4 Моделирование процесса алмазного сверления
- •11.5 Оценка режущей способности алмазных свёрл
- •11.7 Вопросы для контроля
- •12.1 Назначение и структура САПР
- •12.3 Вопросы для контроля
- •12.5 Вопросы для контроля
- •12.7 Вопросы для контроля
135
Глава 4. Исследование конструкций зенкеров
4.1 Назначение, типы и конструктивные особенности
Зенкеры относятся к режущим инструментам для получистовой и чистовой обработки отверстий, которые предварительно получены в детали тем или иным способом, например, после отливки, ковки, штамповки, сверления.
Зенкеры обеспечивают точность обрабатываемой детали с допусками по 11-12
квалитетам, при шероховатости полученной поверхности Rz = 20 – 40мкм.
В зависимости от назначения и условий обработки зенкеры имеют различные конструкции и подразделяются на следующие виды: хвостовые цельные, хвостовые сборные со вставными ножами, насадные цельные,
насадные сборные. Зенкеры изготавливают цельными из быстрорежущей стали или сборными с режущими пластинками из твёрдого сплава, напаиваемыми на корпус инструмента. Хвостовые зенкеры крепят с помощью цилиндрических или конических хвостовиков, насадные – имеют коническое посадочное отверстие и торцовую шпонку для предохранения от провёртывания в работе.
По конструкции рабочей части хвостовые зенкеры аналогичны спиральным свёрлам, но не имеют поперечной режущей кромки. Число зубьев равно трём. Насадные зенкеры имеют 4 – 6 зубьев. Заднюю поверхность у цельных зенкеров делают винтовой или конической, у сборных инструментов,
оснащённых твёрдосплавными пластинами, задняя поверхность оформляется по плоскости. Стружечные канавки у зенкеров выполняют винтовыми (у
цельных зенкеров), косыми (у зенкеров со вставными ножами) и прямыми (у
зенкеров оснащённых твёрдосплавными пластинами).
Основными конструктивными элементами зенкера являются режущая и калибрующая части, число, профиль и направление стружечных канавок, углы резания, хвостовая часть. На рис. 4.1 показан хвостовой зенкер из быстрорежущей стали, имеющий винтовые передние и задние поверхности.
Хвостовые зенкеры обычно делают сварными – рабочая часть из быстрорежущей стали, хвостовик из сталей 45, 40Х, 45Х. Место сварки обычно
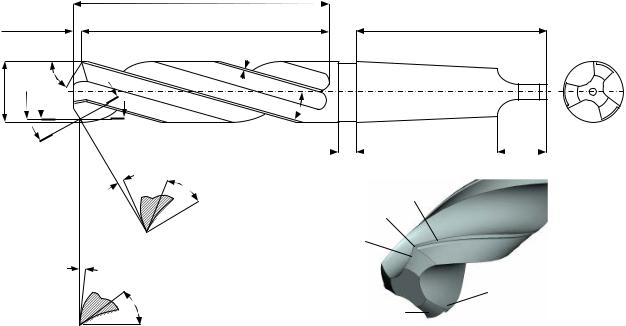
136
делают на шейке. Крутящий момент при работе инструмента передаётся с помощью конического хвостовика за счёт сил трения. Для извлечения зенкера из патрона станка служит лапка. Рабочая часть зенкера состоит из режущей и калибрующей частей.
Режущая |
Рабочая часть |
|
Калибрующая часть |
||
часть |
f
d |
di |
φ |
|
N |
|
0 |
i |
0 |
|
||
|
|
|
|
|
|
|
N |
|
|
N - N |
|
|
|
|
|
|
|
|
|
|
|
αni |
γni |
|
|
|
|
|
|
|
|
|
α0i |
0 - 0 |
|
|
|
|
|
γ0i |
|
|
Хвостовик |
ω |
|
Шейка |
Лапка |
3
5
4
1
2
Рис. 4.1. Конструкция хвостового зенкера из быстрорежущей стали
Режущая часть состоит из следующих элементов (рис. 4.1): 1 – передняя поверхность, 2 – главная задняя поверхность, 3 – вспомогательная задняя поверхность (ленточка f), 4 – главная режущая кромка, 5 – вершина зуба; и
характеризуется следующими угловыми геометрическими параметрами:
передний угол γ, задний угол α, главный угол в плане φ, угол наклона винтовой канавки ω.
Передний и задний углы зенкера задают в точке, наиболее удалённой от оси инструмента, т.е. на вершине зуба. Передний угол для обработки стали и чугуна составляет γ=6 – 12°, для обработки цветных металлов и сплавов γ=20 – 30°. Задний угол зенкера выбирают в пределах α=6 – 10°. Передний и задний углы принято определять в двух сечениях: нормальном N – N, отражающем реальные условия работы инструмента, и осевом О – О, необходимом для контроля зенкера при его изготовлении. Эти углы являются переменными по
137
длине режущей кромки инструмента. Для определения величин углов в какой-
либо i-той точке профиля зенкера используются следующие выражения:
tg oi |
|
|
di |
|
tg , |
(4.1) |
||||
|
|
|
d |
|||||||
|
|
|
|
|
|
|
|
|
|
|
tg oi |
|
|
d |
|
|
|
tg o , |
(4.2) |
||
|
di |
|
|
|||||||
|
|
|
|
|
|
|
|
|
|
|
tg ni |
|
di |
|
tg sin , |
(4.3) |
|||||
|
d |
|
||||||||
|
|
|
|
|
|
|
|
|
|
|
tg ni |
|
d |
|
|
|
tg 0 sin , |
(4.4) |
|||
di |
|
|
|
|||||||
|
|
|
|
|
|
|
|
|
|
где αoi, γoi, αni, γni, соответственно, задний и передний углы в осевом и нормальном сечениях; ω – угол наклона винтовой канавки; d, di,
соответственно, диаметры зенкера – номинальный и в текущей i-той точке.
Главный угол в плане φ оказывает прямое влияние на размеры поперечного сечения срезаемого слоя, а, следовательно, на возникающие при резании силы. Угол φ при обработке стали составляет 60°, 75° (для сквозных отверстий); при обработке чугуна – 45°, 60° (для сквозных отверстий); для глухих отверстий – φ=90°.
Угол наклона винтовых канавок зенкера ω в соответствии с формулой
(4.1) определяет передний угол в осевом сечении. Он задаётся в зависимости от обрабатываемого материала в пределах ω=10 – 30°.
Калибрующая часть обеспечивает получение требуемого размера отверстия, направление зенкера в процессе обработки и служит запасом на переточки режущей части. На калибрующей части вдоль режущей кромки оставляют ленточки шириной f=0,8 – 2,5мм в зависимости от диаметра зенкера.
Для облегчения процесса резания на калибрующей части делают обратную конусность в пределах 0,04 – 0,1мм на 100мм длины. Это утонение играет такую же роль, как и вспомогательный угол в плане φ1 у резцов.
Диаметр зенкера №1, предназначенного для обработки отверстий под последующее развёртывание, определяют с учётом припуска под развёртывание [3, 4]. Диаметр зенкера №2 (п.2 на рис. 4.2) для окончательной
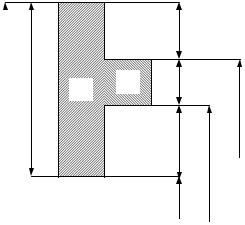
138
обработки определяют по диаметру обрабатываемого отверстия (п.1 на рис. 4.2)
с учётом припуска на отверстие, разбивки и запаса на изнашивание. На рис. 4.2
обозначено: Н – допуск на обрабатываемое отверстие, δ – допуск на изготовление зенкера, – величина разбивки отверстия, Ј – запас на износ зенкера, dн – номинальный диаметр отверстия, dmax – максимальный диаметр отверстия, d0min – минимальный диаметр зенкера, d0max – максимальный диаметр зенкера.
H |
1 |
2 |
δ |
dmax |
|
|
|
|
|
|
Ј |
|
|
|
dн |
d0max
d0min
Рис. 4.2. Схема построения допуска на наружный диаметр зенкера №2
Разбивку обычно принимают равной 0,3 – 0,4 от допуска на обрабатываемое отверстие, допуск на изготовление зенкера принимают равным
0,25 от допуска на отверстие.
4.2 Износ и затачивание зенкеров
Характер изнашивания зенкеров зависит от обрабатываемого материала.
При обработке деталей из стали для зенкеров из быстрорежущей стали критерием затупления является износ по ленточке μ (рис. 4.3а). При обработке деталей из чугуна лимитирующим износом является износ μ по уголкам (рис. 4.3б). Средние величины износа зенкеров при обработке стали μ=1,0-1,2мм, при обработке чугуна μ=0,8-1,5мм. Твердосплавные зенкеры изнашиваются главным образом по задней поверхности и уголкам. Допустимые величины
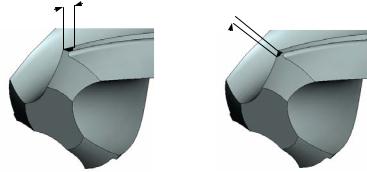
139
износа по задней поверхности для зенкеров диаметром до 20мм μ=1мм, свыше
20 до 40мм μ=1,2мм, свыше 40 до 60мм μ=1,4мм, свыше 60мм μ=1,6мм [2].
μ
μ
а) б)
Рис. 4.3. Характер лимитирующего износа зенкеров: а – при обработке стали; б – при обработке чугуна
Для восстановления режущей способности зенкеры необходимо затачивать по задней поверхности зубьев. При затачивании снимается весь затупленный участок и для полной гарантии качества заточки – дополнительный слой толщиной 0,2мм.
Операцию затачивания можно проводить как на универсально-заточном оборудовании (станки моделей 3Д642Е, 3В642, 3А64Д и т.п.), так и специальном полуавтомате 3659А для затачивания винтовых задних поверхностей свёрл, а так же на оборудовании с ЧПУ (подробнее о заточных станках см. в гл.1, п.1.3).
При использовании универсально-заточного оборудования для установки зенкера относительно шлифовального круга необходимо специальное приспособление для затачивания винтовых поверхностей с набором сменных кулачков к нему. В случае применения полуавтомата 3659А дополнительных приспособлений не требуется, расчёт параметров установки зенкера, настройка станка и затачивание задней поверхности проводится аналогично сверлу (см.
гл.3, лабораторная работа «Изучение и исследование формообразования режущей части спиральных свёрл»).
140
4.3 Лабораторная работа
«Изучение формообразования и исследование геометрических параметров режущей части зенкеров»
Цель и задачи работы. Цель работы – практическое изучение основных конструктивных элементов зенкеров. В задачи работы входят изучение методов и средств формирования и контроля задних поверхностей зенкеров, а так же исследование их геометрических параметров.
Оборудование, инструменты и приборы. Для проведения работы требуются хвостовые зенкеры из быстрорежущей стали диаметром 20-30мм,
специальное приспособление для затачивания винтовых задних поверхностей с набором кулачков к нему, специальное приспособление для контроля, стойка с индикатором, штангенциркуль, угломер (маятниковый или универсальный).
Лабораторная работа выполняется на универсально-заточном станке (модели
3Д642Е, 3В642, 3А64Д и т.п.) при использовании шлифовального круга формы ЧК или ЧЦ из материала электрокорунд белый (24А) с зернистостью 25-40,
твёрдостью СМ1-СМ2, структурой 5-7, на керамической связке (подробнее о характеристиках шлифовального круга и его маркировке см. в гл.1, п.1.1, табл. 1.1-1.3).
Методика выполнения работы
В зависимости от износа зенкера μ и допустимой величины стачивания М определяют толщину слоя металла q, подлежащего стачиванию за одну переточку, а также общее количество возможных переточек n. Значения μ и q
приведены в таблице 4.1. Размер М у хвостовых зенкеров определяется как:
M 0,7Lраб , (4.7)
где Lраб – длина рабочей части зенкера, равная сумме длин режущей и калибрующей частей. Число переточек у хвостовых и насадных зенкеров составляет:
|
|
|
141 |
n |
M |
. |
(4.8) |
|
|||
|
q |
|
Для затачивания винтовой задней поверхности применяется специальное приспособление (рис. 4.4).
|
|
|
|
|
|
Таблица 4.1 |
Диаметр зенкера |
|
|
Обрабатываемый материал |
|||
|
Чугун |
|
Сталь |
|||
d,мм |
|
|
|
|
|
|
Износ |
|
Стачивание |
Износ |
|
Стачивание |
|
|
μ,мм |
|
q,мм |
μ,мм |
|
q,мм |
До 6 |
0,5 |
|
0,8 |
0,6 |
|
1,0 |
Свыше 6 до 10 |
0,6 |
|
0,9 |
0,8 |
|
1,1 |
Свыше 10 до 15 |
0,7 |
|
1,0 |
0,9 |
|
1,3 |
Свыше 15 до 20 |
0,8 |
|
1,2 |
1,0 |
|
1,5 |
Свыше 20 до 25 |
0,9 |
|
1,4 |
1,2 |
|
1,7 |
Свыше 25 |
1,0 |
|
1,6 |
1,4 |
|
2,0 |
Зенкер, установленный в приспособлении, совершает относительно шлифовального круга винтовое движение (DS2, DS3), создаваемое кулачком 1,
имеющим торцовую винтовую поверхность определённого шага. При повороте маховика 4 зенкер начинает вращаться (DS2). Упор 3, закреплённый в корпусе приспособления, скользя по винтовой поверхности кулачка 1, заставляет зенкер, преодолевая сопротивление пружины 2, перемещаться в осевом направлении (DS3). В результате сочетания этих движений (вращательного DS2 и
поступательного DS3) задние поверхности зенкера в процессе затачивания приобретают винтовую форму. Группу движений DS2 и DS3 называют движениями формообразования.
Шлифовальный круг, вращаясь вокруг своей оси, создаёт главное движение резания DR, поперечное перемещение стола станка обеспечивает движение подачи DS1 на глубину резания. Группу движений DR и DS1 называют движениями резания.
Подвод зенкера к шлифовальному кругу и отвод его по окончании обработки производится поперечным перемещением стола станка с помощью вспомогательного движения DS4.
Для получения необходимой величины задних углов у зенкера в приспособление (рис. 4.4) следует установить кулачок из комплекта с
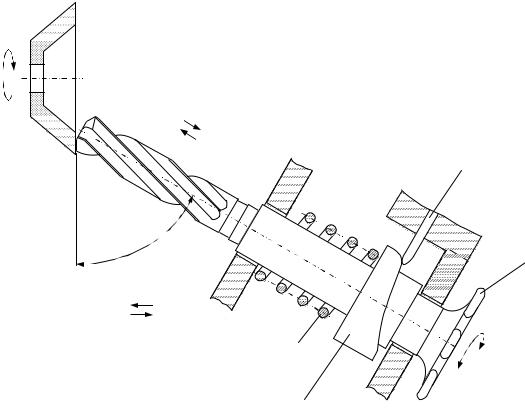
142
определённым шагом винтовой поверхности. Величина шага (в мм)
определяется по формуле:
P d |
tg n |
, |
(4.5) |
|
|||
|
sin |
|
где d – диаметр зенкера; αn – задний угол зенкера в нормальном сечении,
который требуется получить в результате заточки; φ – главный угол в плане.
Если задний угол зенкера задан в осевом сечении (α0), то его значение в нормальном сечении находят как:
tg n tg 0 sin . |
(4.6) |
DS1
DR
DS3
3
φ
4
DS4
2
DS2
1
Рис. 4.4. Схема формообразования винтовых задних поверхностей зенкера
Шаги винтовых поверхностей сменных кулачков из комплекта приспособления равны 5, 7, 9, 13, 17мм. По полученному (4.5) результату выбирают кулачок с шагом винтовой поверхности, наиболее близким к расчётному и устанавливают его в приспособление.

143
Поворотом верхней части приспособления вокруг вертикальной оси устанавливают требуемую величину угла в плане φ (рис. 4.4). Отсчёт
необходимого значения φ производят по лимбу на приспособлении.
1 |
2 |
а |
|
|
V |
|
Б |
0 - 0 (развёрнуто на плоскость) a
l |
i |
γ0i=ωi |
|
||
|
|
i’ |
|
α0i |
|
|
0 - 0 |
|
|
|
i |
|
|
|
α0i |
γ0i |
Б (увеличено) |
|
|
τ |
|
|
i |
|
|
|
|
i |
|
0 |
0 |
ρ |
|
|
|
|
i’ |
|
|
|
ρ |
Рис. 4.5. Схема измерения заднего угла зенкера: 1 – индикатор; 2 – диск для отсчёта угла поворота
При помощи маховика поперечной подачи стола медленно подводят зенкер к торцу шлифовального круга (не касаясь его) и при помощи упора на приспособлении устанавливают режущую кромку так, чтобы она полностью
144
провёртывалась относительно шлифовального круга, а последний не касался,
при этом, следующего зуба зенкера.
Включают вращение шлифовального круга. Скорость круга должна находиться в пределах 20–25м/с (для инструмента из быстрорежущей стали), и 10–18м/с (для твёрдосплавных зенкеров). Подводят заднюю поверхность одного из зубьев зенкера к шлифовальному кругу, определяя момент соприкосновения по искре [1]. Вращением маховика поперечной подачи стола передвигают зенкер в сторону шлифовального круга на глубину резания t=0,02– 0,04мм, отсчитывая величину перемещения по лимбу на корпусе маховика поперечной подачи, и производят затачивание последовательно всех зубьев.
Эта операция повторяется до тех пор, пока не будет снят весь изношенный участок величиной q, подлежащей стачиванию за одну переточку,
со всех зубьев. Число этих повторений (проходов) можно определить, разделив q на t, и умножив результат на количество зубьев.
По завершении обработки зенкер отводят от шлифовального круга,
останавливают вращение круга и вынимают заточенный инструмент из приспособления.
После затачивания измеряют задний угол, главный угол в плане и биение режущих кромок. Для этого зенкер закрепляют в приспособлении для контроля
(рис. 4.5), затем к его задней поверхности устанавливают с натягом измерительный наконечник индикатора 1.
Точку контакта i измерительного наконечника располагают на задней поверхности как можно ближе к режущей кромке и наружному диаметру зенкера. В этом положении индикатор 1 устанавливают на ноль. Затем поворачивают зенкер вокруг оси на угол τ=10–15°, отсчитывая его по шкале 2
приспособления. При повороте зенкера по стрелке V на угол τ, измерительный наконечник индикатора 1 переместится по дуге l радиуса ρ из точки i в точку i’
на величину а. Для определения осевого заднего угла развернём на плоскость режущий клин в осевом сечении 0 – 0 (рис. 4.5). Тогда угол α0 определим
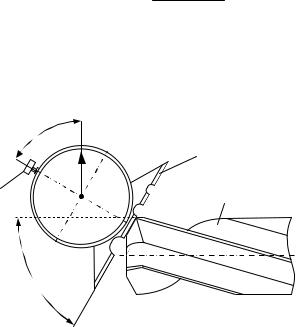
145
разделив величину a на длину дуги l=ρτ. После преобразований, с учётом перевода угла τ из градусов в радианы, окончательно получим:
tg 0 |
|
a |
, |
(4.9) |
0,01745 |
где а – показания индикатора, мм; ρ – радиус, мм (расстояние от оси зенкера до точки контакта с измерительным наконечником); τ – угол поворота зенкера, °.
φ
|
1 |
3 |
2 |
|
φ
Рис. 4.6. Измерение главного угла в плане Главный угол в плане φ можно измерить маятниковым или
универсальным угломерами. При использовании маятникового угломера
(подробнее о работе прибора см. в гл.5, рис. 5.17) зенкер закрепляют в приспособлении для контроля (рис. 4.5). Измерительную линейку угломера 1
совмещают с главной режущей кромкой зенкера 2 (рис. 4.6) так, чтобы они касались друг друга без просвета, и, удерживая прибор в этом положении,
зажимают кнопку 3 на корпусе угломера. После того как стрелка на индикаторе угломера перестанет колебаться, кнопку отпускают и отмечают показания индикатора. В случае применения универсального угломера определение угла φ осуществляется аналогично сверлу (см. гл. 3, рис. 3.25а).
Допустимое отклонение измеренных углов от заданного значения – ±2°.
Контроль биения (δ) режущих кромок производится также с помощью приспособления (рис. 4.5) с индикатором закреплённым на стойке. Биение,
измеренное по нормали к режущим кромкам, не должно превышать: для