
- •1 ЗАГАЛЬНІ ВІДОМОСТІ ПРО ПРИВОДИ
- •1.2 Огляд основних типів редукторів
- •Коефіцієнт корисної дії приводу
- •Таблиця 2.1- Значення ККД для механічних передач
- •Ланцюгова
- •Таблиця 2.2- Передаточні числа циліндричних зубчастих передач
- •(ГОСТ 2186-66)
- •Таблиця 2.3- Загальні передаточні числа двоступеневих редукторів
- •(ГОСТ 2186-66)
- •Таблиця 2.4- Передаточні числа конічних зубчастих передач
- •(ГОСТ 12289-76)
- •Таблиця 2.5- Передаточні числа черв’ячних передач (ГОСТ 2144-76)
- •Назва редуктора
- •Таблиця 2.7 - Рекомендовані значення u для різних типів редукторів
- •Тип передачі
- •Схема редуктора
- •Значення uп
- •Двоступеневий
- •циліндричний
- •редуктор
- •Розгорнута схема
- •Двоступеневий
- •співвісний редуктор
- •Двоступеневий
- •співвісний редуктор з
- •внутрішнім
- •зачепленням
- •Швидкохідна ступінь
- •Циліндрично-
- •черв’ячний редуктор
- •Продовження таблиці 2.7
- •Циліндрично-черв’ячний
- •редуктор
- •Черв’ячно-циліндричний
- •редуктор
- •Одноступеневі:
- •Таблиця 3.2 - Рекомендовані поєднання матеріалів шестірні
- •Поверхневе гартування
- •Таблиця 3.5 – Значення показників степеня кривої втоми m
- •Таблиця 3.7 - Границі витривалості зубців при згині
- •Сталі
- •Таблиця 3.16 - Коефіцієнт форми зубців YF
- •Площа
- •Таблиця 7.1 – Визначення сил в зачепленні механічних передач
- •Вид передачі
- •Значення сили, Н
- •Колова
- •Радіальна
- •Осьова
- •Колова
- •Радіальна
- •Осьова
- •Колова
- •Радіальна
- •Осьова
- •Муфта
- •Радіальна
- •Вал – шестірня
- •Вал – колеса
- •Таблиця 8.1 – Розміри проточок для різьби під круглі гайки
- •Умови роботи підшипника
- •Поля допусків
- •Таблиця 8.6 - Пластичні мастильні матеріали
- •Таблиця 8.7 – Манжети гумові армовані
- •Таблиця 9.1 - Значення коефіцієнта режиму навантаження К
- •Машини
- •L, мм не більше
- •Твердість згідно з ГОСТ 263-75, ум., од. ............…………………………...... 50—65
- •Таблиця 9.7 – Розміри і параметри муфти пружної втулково-пальцевої
- •Закінчення таблиці 9.7
- •Таблиця 9.8– Розміри (мм) пальців і втулок муфти пружної втулково-пальцевої
- •Закінчення таблиці 9.15
- •Таблиця 9.18 – Розміри і параметри ланцюгової однорядної муфти
- •Таблиця 10.11 - Зубці і вінець зірочки в поперечному перерізі
- •Параметри
- •Орієнтовні значення, мм
- •Параметри
- •Орієнтовні значення, мм
- •Розміри елементів спряжень литих корпусів, мм
- •Розміри елементів фланців литих корпусів, мм
- •Розміри гнізд підшипників і кришок, що прикручуються, мм
- •Кріплення
- •Кріплення
- •Кріплення
- •Кришки врізні, мм
- •Таблиця 10.14 - Кришка оглядового вікна
- •Таблиця 10.17 Пробки для зливу масла
- •Таблиця 10.33 Значення в’язкості масел, що рекомендуються для змащування черв’ячних передач при 1000С
- •Таблиця 10.38 - Види допусків
- •Найбільш раціонально розпочинати компонування цього редуктора з вхідного і вихідного валів. Після попереднього конструктивного оформлення підшипникових вузлів можна переходити до проміжного вала.
- •Параметри
- •Продовження таблиці 10.44
- •перетворимо нерівності (11.4), (11.5) в рівності і одержимо:
- •де Рвих – потужність на вихідному валі приводу, Вт.
- •Допустимі контактні напруження для шестірні і колеса
- •Еквівалентне число зубців шестерні і колеса
- •Допустимі контактні напруження для шестірні і колеса
- •2 ПРОЕКТУВАННЯ ПРИВОДУ
- •2.1. Вибір електродвигуна і кінематичний розрахунок приводу
- •Кутова швидкість вала електродвигуна
- •Допустимі контактні напруження для шестірні і колеса
- •2.4. Попередній розрахунок валів редуктора
- •Розрахункове значення кроку ланцюга
- •Розрахункова міжосьова відстань
- •Товщина фланців корпуса і кришки редуктора
- •Вихідний вал редуктора
- •4 ПРОЕКТУВАННЯ ПЕРЕДАЧІ
- •5.1 Вибір електродвигуна і кінематичний розрахунок приводу
- •Кутова швидкість вала електродвигуна
- •Література
- •Потуж-
- •Синхронна частота обертання, хв-1
- •Типо-
- •розмір
- •Типо-
- •розмір
- •Типо-
- •розмір
- •Типо-
- •розмір
- •Таблиця B.1 - Ланцюги типу ПРА
- •Таблиця B.2 - Ланцюги типу ПР
- •Таблиця B.3 - Ланцюги типу 2ПР
- •Таблиця B.4 - Ланцюги типу 3ПР
- •Таблиця B.5 – Ланцюги типу 4ПР
- •Таблиця B.6 – Ланцюги типу ПВ і 2ПВ
- •Таблиця В.7 – Ланцюги типу ПРИ
- •Розміри, мм
- •Розрахункові параметри
- •Особливо легка серія діаметрів 1, серія ширин 7
- •Особливо легка серія діаметрів 1, серія ширин 7
- •Легка серія діаметрів 2, серія ширин 0
- •Підшипник 315 ГОСТ 8338-75
- •Таблиця Г.2 - Кулькові підшипники радіальні дворядні сферичні
- •Легка серія
- •Легка широка серія
- •Середня серія
- •Середня широка серія
- •Підшипник 1204 ГОСТ 5720 -75
- •Кульки
- •Особливо легка серія
- •Легка серія
- •Важка серія
- •Приклад умовного позначення підшипника за ГОСТ 831 -75 з умовним позначенням 46205:
- •Підшипник 46205 ГОСТ 831-75
- •Таблиця Г.4-Роликові підшипники радіальні з короткими циліндричними роликами
- •Розміри, мм
- •Надлегка серія
- •Особливо легка серія
- •Легка широка серія
- •Середня серія
- •Середня широка серія
- •Важка серія
- •Підшипник 32315 ГОСТ 8328-75
- •Еквівалентне осьове навантаження
- •Легка серія діаметрів 2
- •Середня серія діаметрів 3
- •Важка серія діаметрів 4
- •Підшипник 8210 ГОСТ' 6874-75
- •Розміри, мм
- •Надлегка серія діаметрів 9
- •Особливо легка серія діаметрів 1
- •Легка серія діаметрів 2
- •Середня серія діаметрів 3
- •Середня широка серія діаметрів 6
- •Розміри, мм
- •Ролики
- •Розрахункові параметри
- •Підшипник 27312 ГОСТ 7260-81
- •Таблиця Д.15 – Шайби кінцеві (ГОСТ 14734-69)
- •Таблиця Д.16 – Шпильки з кінцем, що вгвинчується, довжиною
- •1d (ГОСТ 22032-76), 1,25d (ГОСТ 22034-76), 2d (ГОСТ 22038-76)
- •Таблиця Д.18 – Штифти конічні (ГОСТ 3129-70)
- •Таблиця Д.20-Збіги, проточки та фаски для метричної різьби ГОСТ 10549-80
- •Таблиця Д.23 – Кришки торцеві з отвором під манжетне ущільнення
- •(ГОСТ 18512-73)
- •Таблиця Д.26 – Кришки (торцеві та врізні) під регулювальні гвинти
- •Таблиця Д.27 – Стальні ущільнюючі шайби
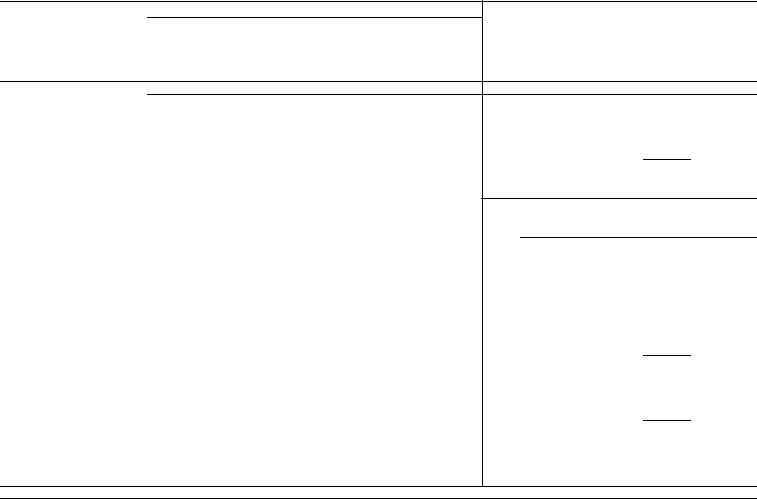
Розділ 9 |
Муфти |
Таблиця 9.18 – Розміри і параметри ланцюгової однорядної муфти
Номінальний моменткрутний Т |
d, |
|
d1, |
більшенеD, |
|
|
L, мм, не більше |
|
|
L, мм, не більше |
|
|
іРзмальнеадіваосейщення- більне-мм,,лів ше |
-оберЧастота /хв,танняоб |
|
|
|||||||
Н7 |
|
Н9 |
І |
|
ІІ |
І |
ІІ |
|
І |
ІІ |
І |
|
ІІ |
|
|
13568-75 |
|
||||||
м |
мм |
|
мм |
|
|
|
|
|
|
|
Тип |
|
|
|
|
|
|
|
|
|
Ланцюг |
|
|
|
|
|
|
|
|
|
|
|
|
|
|
|
|
|
|
|
згідно |
|
|||||
Н, |
Гран. відх. |
|
|
І |
ІІ |
|
|
І |
|
|
ІІ |
|
|
|
|
|
|
||||||
|
|
|
|
|
|
|
|
|
|
|
ГОСТ |
|
|||||||||||
ном |
|
|
|
|
|
|
|
|
|
|
3,4 |
|
|
|
|
|
3,4 |
|
|
|
|
|
|
|
|
|
|
|
|
Виконання |
|
|
Виконання |
|
|
|
|
||||||||||
|
|
|
|
|
|
|
|
|
|
|
|
|
|
|
|||||||||
|
|
|
|
- |
|
102 |
108 |
|
80 |
102 |
- |
36 |
39 |
|
25 |
36 |
|
0,15 |
1620 |
ПР-19,5-3180 |
|
||
63 |
20, 22, 24 |
110 |
|
|
|
|
|
||||||||||||||||
25, 28 |
- |
|
122 |
128 |
|
92 |
122 |
- |
42 |
45 |
|
27 |
42 |
|
|
|
|
|
|
||||
|
|
|
|
|
|
|
|
|
|
|
|||||||||||||
|
25, 28 |
|
|
|
|
|
|
|
1380 |
|
|
||||||||||||
|
|
|
|
|
|
|
|
|
|
|
|
|
|
|
|
|
|
|
|
||||
125 |
|
30 |
125 |
- |
|
|
|
|
|
|
- |
|
|
|
|
|
|
|
|
|
|
||
|
32 |
|
|
162 |
168 |
|
124 |
162 |
|
58 |
61 |
|
39 |
58 |
|
0,20 |
|
ПР-25,4-6000 |
|
||||
|
|
|
|
|
|
|
|
|
|
|
|||||||||||||
|
35, 36 |
|
206 |
|
|
80 |
|
|
|
|
|||||||||||||
|
|
|
|
|
|
|
|
|
|
|
|||||||||||||
250 |
32, 35, 36, |
140 |
|
|
|
|
|
|
|
|
|
|
|
|
|
|
1200 |
|
|
||||
|
|
|
|
|
|
|
|
|
|
|
|
|
|
|
|
|
|
||||||
|
(38) |
|
|
|
|
|
|
|
|
|
|
|
|
|
|
|
|
|
|
||||
|
40, (42), 45 |
|
|
|
|
|
|
|
|
|
|
|
|
|
|
|
|
|
|
|
|
||
500 |
40, (42) |
200 |
278 |
|
222 |
228 |
|
172 |
222 |
|
82 |
85 |
|
57 |
82 |
|
|
|
1020 |
ПР-31,75-8850 |
|
||
45, (48), 50 |
|
|
110 |
|
|
|
|
|
|||||||||||||||
|
|
|
|
|
|
|
|
|
|
|
|
|
|
|
|
||||||||
|
(53), 55, (56) |
|
|
|
|
|
|
|
|
|
|
|
|
|
|
|
|
|
|
|
|||
|
|
|
|
|
|
|
|
|
|
|
|
|
|
|
|
|
|
|
|
|
|||
|
|
50 |
|
280 |
|
224 |
230 |
|
174 |
224 |
|
82 |
85 |
|
57 |
82 |
|
0,40 |
|
ПР-38,1-12700 |
|
||
1000 |
(53), 55, (56) |
210 |
|
|
|
|
|
780 |
|
||||||||||||||
|
|
|
|
|
|
|
|
|
|
|
|
|
|
|
|
|
|
||||||
|
60 |
|
|
|
|
|
|
|
|
|
|
|
|
|
|
|
|
|
|
||||
|
63, (65), 70 |
|
354 |
|
284 |
290 |
|
220 |
284 |
140 |
105 |
108 |
|
73 |
105 |
|
|
|
|
|
|
||
|
|
71 |
|
|
|
|
|
|
|
|
|
|
|||||||||||
|
63, (65), 70, 71 |
|
|
|
|
|
|
|
|
|
|
|
|
|
|
|
|
|
|
|
|
||
2000 |
|
(75) |
280 |
|
|
|
|
|
|
|
|
|
|
|
|
|
|
|
|
|
|
|
|
80, 85 |
|
|
|
|
|
|
|
|
|
|
|
|
|
|
|
|
|
|
|
||||
|
|
|
|
|
|
|
|
|
|
|
|
|
|
|
|
|
|
|
|
|
|||
|
|
90 |
|
424 |
|
344 |
352 |
|
272 |
344 |
170 |
130 |
134 |
|
94 |
130 |
|
0,6 |
720 |
|
|
||
|
80, (85) |
|
|
|
|
|
ПР-50,8-22680 |
|
|||||||||||||||
4000 |
|
90 |
310 |
|
|
|
|
|
|
|
|
|
|
|
|
|
|
|
|
|
|
||
|
(95) |
|
|
|
|
|
|
|
|
|
|
|
|
|
|
|
|
|
|
|
|||
|
|
100 |
|
|
|
|
|
|
|
|
|
|
|
|
|
|
|
|
|
|
|
|
|
|
(105), 110 |
|
514 |
|
424 |
432 |
|
342 |
424 |
210 |
165 |
169 |
|
124 |
165 |
|
|
|
|
|
|
||
|
100, (105), 110 |
|
|
|
|
|
|
|
|
|
|
||||||||||||
8000 |
(120) |
350 |
|
|
|
|
|
|
|
|
|
|
|
|
|
|
0,7 |
540 |
|
|
|||
|
125 |
|
|
|
|
|
|
|
|
|
|
|
|
|
|
|
|
||||||
|
(130) |
|
604 |
|
504 |
512 |
|
408 |
504 |
250 |
200 |
204 |
|
154 |
200 |
|
|
|
|
|
|
||
|
|
140 |
|
|
|
|
|
|
|
|
10. |
|
|||||||||||
|
|
|
|
|
|
|
|
|
|
|
|
|
|
|
|
|
|
|
|
|
|||
Примітки: 1. Муфти з розмірами у круглих дужках використовуються рідше; |
2. Кутове |
зміщення осей валів |
|
Число ланок ланцюга (число зубців напівмуф- ) ти
12
10
12
14
12
14
16
|
бі- |
|
h, |
Маса, кг не льше |
|
мм |
||
|
||
1,3 |
3,30 |
|
|
3,85 |
|
|
3,85 |
|
|
4,10 |
|
1,8 |
4,20 |
|
4,85 |
||
|
||
|
5,05 |
|
|
|
|
|
5,75 |
|
2,0 |
12,85 |
|
13,40 |
||
|
14,00 |
|
|
13,45 |
|
3,5 |
14,70 |
|
19,85 |
||
|
19,50 |
|
|
18,85 |
|
|
30,85 |
|
|
28,60 |
|
|
38,95 |
|
|
44,50 |
|
|
45,00 |
|
|
49,00 |
|
3,8 |
52,30 |
|
56,90 |
||
|
||
|
54,05 |
|
|
55,00 |
|
|
71,45 |
|
|
78,90 |
|
|
85,60 |
|
|
89,45 |
|
|
|
157
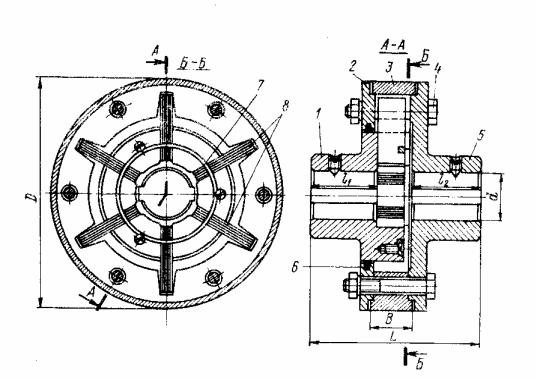
Розділ 9 |
Муфти |
Муфта має лінійну характеристику при крученні доти, поки пружина не дотикається до скосу паза. При подальшій деформації пружини характеристика муфти нелінійна. Напруження згину в пластинах пружин визначається за формулою
Рисунок 9.16 - Муфта з радіальними пластинчастими пружинами
Таблиця 9.19 – Розміри муфти з радіальними пластинчастими пружинами
Т, Н м |
nmax, хв-1 |
d, мм |
D, мм |
L, мм |
B, мм |
l1, мм |
l2, мм |
75 |
4200 |
25 |
120 |
83 |
25 |
48 |
32 |
300 |
3500 |
40 |
160 |
113 |
25 |
60 |
50 |
800 |
2100 |
55 |
200 |
143 |
30 |
80 |
60 |
2500 |
1650 |
80 |
280 |
203 |
45 |
120 |
80 |
8500 |
1250 |
120 |
360 |
283 |
55 |
160 |
120 |
17000 |
1000 |
150 |
440 |
353 |
60 |
200 |
150 |
40000 |
850 |
200 |
570 |
473 |
60 |
260 |
210 |
75000 |
800 |
250 |
640 |
543 |
65 |
300 |
240 |
σ зг = |
F2 a |
≤σ згadm , |
(9.14) |
|
W |
||||
|
|
|
де σ згadm – допустимі напруження згину для матеріалу пластин, МПа; W– мо-
158

Розділ 9 |
Муфти |
мент опору поперечного перерізу пакета пластин,мм3; а – відстань між півмуфтами у місці фіксування пружин, мм; F2 – колова сила, що діє на пакет
T2 |
|
F2 = m(R + a). |
(9.15) |
Тут Т2 – крутний момент на муфті, Нм; m – кількість пакетів; R – радіус півмуфти, де зафіксовані пакети пружин, м.
Момент опору поперечного перерізу обчислюється за формулою
W = n |
b h2 |
, |
(9.16) |
|
6 |
||||
|
|
n – кіль- |
||
де b і h – відповідно ширина і товщина одної пластини пакета, мм; |
кість пластин у пакеті; Пластини виготовляють з термооброблених сталей марок 65Г ГОСТ
105088 або 65С2А ГОСТ 4543-89.
9.4 Керовані муфти
Муфти цієї групи призначені для з'єднання і роз'єднання валів під час зупинки і роботи приводу за допомогою механізмів керування.
Кулачкова муфта. Для передачі значних моментів при нечастих включеннях і необов'язковій плавності з'єднання застосовують кулачкові або зубчасті муфти. Вони мають значно менші габаритні розміри і масу, чим фрикційні муфти, однак для їхньої роботи потрібно висока точність установки валів.
Застосовують три основні профілі кулачків: трикутний, трапецеїдальний і прямокутний (рис.9.17). Трикутний профіль (рис.9.17, а); має перевагу над іншими в легкості і швидкості включення, що обумовлено великим чис-
лом кулачків (z =15...60). Кут профілю α=300…450. Трикутний профіль застосовується в муфтах, які передають невеликі крутні моменти.
Трапецеїдальний профіль (рис.9.17, б) застосовують у муфтах, які передають великі крутні моменти при великих частотах обертання валів. Кут
профілю до осі α=3…5°, число кулачків від 3 до 15. Муфти з трапецеїдальними і трикутними профілями кулачків мають потребу в невеликому
осьовому підтисканні і після включення (якщо α > ρ, де ρ — кут тертя), тому що в них виникають осьові сили, які намагаються розсунути півмуфти.
Прямокутний профіль (рис.9.17, в) застосовують у муфтах важко навантажених машин. Цей профіль забезпечує зчеплення півмуфт із зазором, тому погано працює при реверсивному навантаженні. Муфти важче включаються, але не вимагають постійної осьової сили притиснення і мають правильний контакт зубців по поверхні при неповному включенні муфти.
Несиметричні трикутні і трапецеїдальні профілі (рис.9.17, г, д) застосовують у муфтах для з'єднання валів з постійним напрямом обертання. Для полегшення включення муфти застосовують підрізані головки кулачків
(рис.9.17, е).
Профілі кулачків у поздовжньому перетині показані на рис.9.20, ж, з, і. Трикутний профіль має зменшену до осі муфти висоту (рис.9.20, з), тому що крок пропорційний радіусу, а профілі у всіх перетинах подібні.
159
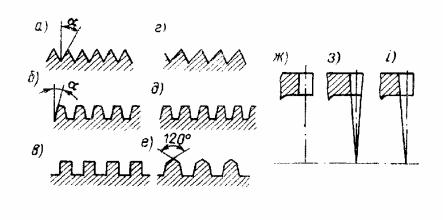
Розділ 9 |
Муфти |
Матеріал кулачкових муфт повинен забезпечувати високу твердість робочих поверхонь кулачків і посадкової поверхні рухомої півмуфти. Для півмуфт використовують сталі типу 20Х, 12ХНЗА з цементацією і гартуванням до твердості 54…60 НRС. Муфти великих розмірів виготовляють із сталі 45 або 45Л, а у відповідальних конструкціях при частих включеннях і вимиканнях - із сталі 40Х, 40ХН, 35ХГСА та ін. Робочі поверхні кулачків гартують до твердості 40…45 НRС.
Рисунок 9.17 – Профілі кулачків
Допустимі контактні напруги σНР для твердих робочих поверхонь ку-
лачків приймають: 90…120 МПа - для муфт, що включаються в стані спокою, 35…70 МПа - для муфт, що включаються на ходу. Більші значення приймають для муфт із малим числом кулачків, менші - для муфт із великим числом кулачків.
Критеріями працездатності кулачкових муфт є міцність кулачків на зминання робочих поверхонь і на згин. Кулачки зношуються при неспіввісних валах і при включенні муфти на ходу.
Контактні напруження підраховують припускаючи, що рівномірно навантажені всі кулачки
σH |
= |
2 |
Tр |
≤ σHP , |
(9.17) |
|
dcp |
z A |
|||||
|
|
|
|
де Тр - розрахунковий крутний момент; dср — середній діаметр муфти (по кулачках); А - площа проекції опорної поверхні кулачка на діаметральну площину; z - число кулачків.
Номінальне напруження згину в основі кулачків при умові, що сила прикладена до вершин кулачків,
σ зг = |
2 Тр h k |
≤ |
σ |
Т |
, |
(9.18) |
|
dcp z W |
n |
||||||
|
|
|
|
де h - висота кулачків; k - коефіцієнт нерівномірності навантаження кулачків, рівний 2...5 (менші значення - при більшій точності виготовлення і ма-
160
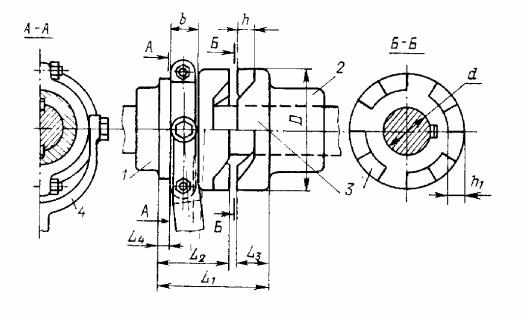
Розділ 9 |
Муфти |
лому числі кулачків і навпаки); W – осьовий момент опору перерізу основи кулачка; n – коефіцієнт безпеки, n ≥1,5.
Рисунок 9.18 - Кулачкова муфта з несиметричною трапецеїдальною формою кулачків
Таблиця 9.20 – Розміри кулачкових муфт з несиметричною трапецеїдальною формою кулачків
d |
D |
L1 |
L2 |
L3 |
L4 |
b |
h |
h1 |
|
|
|
|
мм |
|
|
|
|
25 |
76 |
146 |
95 |
45 |
10 |
18 |
19 |
16 |
30 |
90 |
172 |
105 |
60 |
12 |
18 |
20 |
18 |
35 |
102 |
184 |
115 |
62 |
12 |
18 |
22 |
20 |
45 |
114 |
204 |
128 |
66 |
12 |
18 |
25 |
22 |
50 |
128 |
222 |
140 |
72 |
12 |
18 |
25 |
22 |
55 |
140 |
235 |
150 |
76 |
12 |
18 |
25 |
22 |
60 |
152 |
242 |
160 |
82 |
20 |
18 |
30 |
25 |
70 |
165 |
274 |
175 |
88 |
20 |
18 |
32 |
30 |
75 |
178 |
286 |
188 |
92 |
20 |
24 |
35 |
32 |
На рис.9.18 зображена кулачкова муфта, яка складається з двох півмуфт 1, 2 з торцевими кулачками 3. При включенні кулачки однієї півмуфти входять у впадини другої. Включення і виключення муфти здійснюють переміщенням однієї з півмуфт вздовж вала за допомогою вилки 4.
9.5 Запобіжні муфти
Запобіжні муфти служать для запобігання деталей машин від перевантажень. Їх застосовують у машинах ударної дії у зв'язку із складністю точ-
161
Розділ 9 |
Муфти |
ного розрахунку сили удару і наявністю значних інерційних мас; у машинах, що обробляють неоднорідний матеріал з твердими включеннями (землерийні, грунтообробні, дробильні та інші машини); в автоматичних машинах у зв'язку з відсутністю постійного контролю за їхньою роботою.
Вимоги, які ставляться до запобіжних муфт:
1)надійність і безвідмовність дії;
2)точність спрацьовування, яка обумовлена здатністю роз'єднувати кінематичний ланцюг при заданому крутному моменті;
3)можливість контролю величини граничного крутного моменту;
4)здатність автоматично відновлювати свою працездатність після спрацьовування.
Муфти з руйнуючим елементом. Запобіжні елементи цих муфт найчастіше працюють на зріз; у цьому випадку їх виконують у формі циліндричних штифтів або у вигляді призматичних шпонок. Ці муфти відрізняє висока несуча здатність, простота конструкції, що й обумовило їхнє широке поширення незважаючи на ряд властивих їм недоліків:
1)поступове зниження міцності запобіжного елемента внаслідок нагромадження втомних ушкоджень;
2)зниження точності спрацьовування при числі запобіжних елементів більше одного внаслідок нерівномірного їх навантаження;
3)додаткове навантаження на вали й опори при наявності одного запобіжного елемента;
4)необхідність заміни запобіжного елемента після спрацьовування муфти, що зв'язано з зупинкою машини;
5)залежність точності спрацьовування від похибок виготовлення.
Такі муфти застосовують у машинах з рідкими випадковими перевантаженнями.
На рис.9.19, а (табл.9.21) наведена конструкція й основні розміри муфти із зрізним штифтом. Обидві півмуфти розташовані на валу 1. Півмуфта 2 з'єднана з валом шпонкою, а півмуфта 6 сидить на ньому вільно і з'єднана шпонкою з деталлю, що розташована на її маточині. Півмуфти з'єднані циліндричним штифтом 4, розташованим у втулках 3 і 5, виготовлених із сталі 40Х с наступною термообробкою до твердості 50…60 НRС.
Щоб уникнути ушкодження торців півмуфт задиркою зрізаного штифта на них передбачені кільцеві канавки шириною f і глибиною g. Для полегшення заміни штифта на зовнішню поверхню півмуфт наносять риски, при сполученні яких осі отворів втулок 3 і 5 збігаються. Замість гладких штифтів можуть застосовуватися штифти з проточкою. Як показав експеримент, вони мають більш стабільні характеристики і простіше усуваються після руйнування (задирка не виступає за межі діаметра штифта). Штифти виготовляють із сталей марок У8А, У10А або 40, 45, 50.
Величина крутного моменту, що обмежує використання муфти
Твр = А k0 σвр R , |
(9.19) |
де А – площа поперечного січення штифта (чи шпонки); k0 – коефіцієнт пропорційності (табл. 9.22);
σв – границя міцності при розтягу матеріалу запобіжного елемента; R – радіус кола, на якому розміщений запобіжний елемент.
162
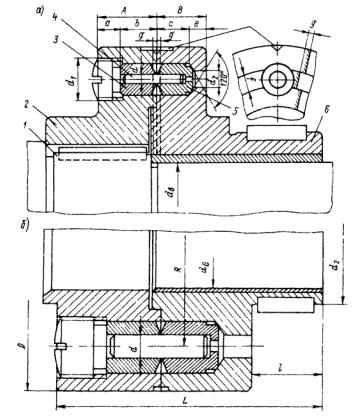
Розділ 9 |
Муфти |
Після
складання
Рисунок 9.19 – Муфта зі зрізними штифтами
Таблиця 9.21 – Розміри деталей муфт (рис.9.19,а)
Сила зрізу, |
d |
d1 |
d2 |
dв |
А |
В |
|
а |
b |
c |
e |
f |
g |
|
min, Н |
|
|
|
|
|
|
мм |
|
|
|
|
|
||
690 |
1,5 |
М16 |
5 |
10 |
22 |
16 |
|
10 |
12 |
11 |
5 |
8 |
1 |
|
1275 |
2,0 |
|||||||||||||
|
|
|
|
|
|
|
|
|
|
|
|
|||
2850 |
3,0 |
М20 |
8 |
15 |
30 |
25 |
|
12 |
18 |
17 |
8 |
10 |
1,5 |
|
5200 |
4,0 |
|
||||||||||||
8100 |
5,0 |
|
|
|
|
|
|
|
|
|
|
|
|
|
11770 |
6,0 |
М30 |
12 |
25 |
50 |
45 |
|
22 |
28 |
26 |
19 |
16 |
2 |
|
20600 |
8,0 |
|
||||||||||||
32360 |
- |
|
|
|
|
|
|
|
|
|
|
|
|
|
55000 |
13,0 |
М48 |
18 |
40 |
75 |
64 |
|
33 |
42 |
39 |
25 |
28 |
3 |
|
83400 |
16,0 |
|
||||||||||||
130000 |
20,0 |
|
|
|
|
|
|
|
|
|
|
|
|
163
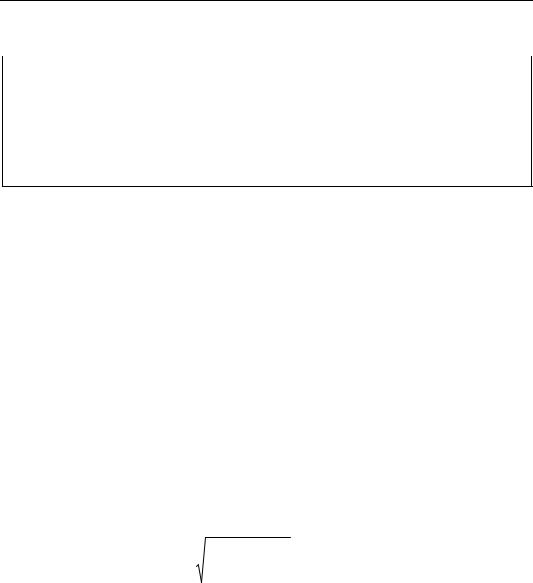
Розділ 9 Муфти
Таблиця 9.22 – Значення коефіцієнта k0 для штифтів
Діаметр |
|
|
k0 при подовженні, % |
|
|
|||||
15 |
– 20 |
22 |
– |
30 |
24 |
– |
25 |
29,9 – 31,4 |
||
штифта, мм |
||||||||||
|
|
|
|
|
|
|
|
|
||
|
|
для гладких штифтів |
|
для штифтів з V-ною канавкою |
||||||
|
|
|
|
|
|
|
|
|
|
|
2 – 3 |
0,78 |
– 0,80 |
0,80 |
– |
0,81 |
|
- |
|
- |
|
4 – 5 |
0,68 |
– 0,72 |
0,75 |
– |
0,76 |
0,86 |
– |
0,95 |
0,92 – 1,06 |
|
6 – 8 |
0,68 |
– 0,72 |
0,75 |
– |
0,78 |
0,86 |
– |
0,95 |
0,92 – 1,10 |
Примітки. Дані отримані при випробуваннях штифтів зі сталей марки У10А, 45 і 50.
Таблиця 9.23 – Розміри і параметри елементів муфт (рис.9.19, б)
Т |
Зрізуюча |
dв |
d |
d2 |
D |
R |
L |
l |
|
сила |
|||||||||
|
|
|
|
|
|
|
|
||
Н м |
Н |
|
|
|
мм |
|
|
|
|
30 |
690 |
25 |
1,5 |
|
|
|
|
|
|
30 |
690 |
28 |
1,5 |
45 |
100 |
35,0 |
70 |
25 |
|
50 |
1275 |
28 |
2,0 |
||||||
|
|
|
|
|
|||||
50 |
1275 |
30 |
2,0 |
|
|
|
|
|
|
155 |
2850 |
35 |
3,0 |
|
|
|
|
|
|
155 |
2850 |
40 |
3,0 |
60 |
125 |
45,0 |
100 |
30 |
|
270 |
5200 |
40 |
4,0 |
||||||
270 |
5200 |
45 |
4,0 |
|
|
|
|
|
|
430 |
8100 |
45 |
5,0 |
|
|
|
|
|
|
825 |
11770 |
50 |
6,0 |
|
|
|
|
|
|
825 |
11770 |
55 |
6,0 |
75 |
160 |
57,5 |
140 |
35 |
|
1300 |
20600 |
55 |
8,0 |
||||||
1300 |
20600 |
60 |
8,0 |
|
|
|
|
|
|
2050 |
32360 |
60 |
10,0 |
|
|
|
|
|
При проектному розрахунку визначають діаметр штифта
d = |
4 Tгр |
|
|
|
, |
(9.20) |
|
π k0 σв R |
|||
де Тгр – гранична величина моменту, при якому закінчується роботоздатність |
|||
муфти. |
|
|
|
На рис.9.19, б (табл. 9.23) наведені конструкція і основні розміри муф- |
|||
ти із зрізним штифтом. |
|
|
|
164
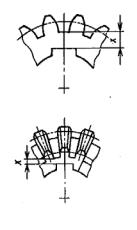
Розділ 10 |
Конструювання деталей редуктора |
10 КОНСТРУЮВАННЯ ДЕТАЛЕЙ РЕДУКТОРА
10.1 Конструювання зубчастих і черв’ячних коліс та черв’яків
Сталеві зубчасті колеса виконують точеними з круглого прокату, кованими, штампованими і литими. Спосіб виготовлення і конструкція колеса визначаються його розмірами і серійністю виробництва.
Шестірні часто виготовляють як одне ціле з валом (вал-шестірня). Цільна конструкція зменшує загальну вартість вала і шестірні, збільшує жорсткість вала, що сприятливо позначається на роботі зубчастого зачеплення, особливо при консольному розташуванні одного з коліс.
Шестірні виготовляються також знімними, якщо це виправдано конструктивно, технологічно чи економічно (наприклад, шестірня з легованої сталі, вал - з вуглецевої) і відстань х від впадини зубця до шпонкового пазу більша 2,5mt для циліндричних і 1,8me для конічних шестірень (рис.10.1).
В одиничному і дрібносерійному виробництві зубчасті колеса діаметром меншим 150 мм виконують із круглого прокату чи поковок, а заготовки коліс більшого діаметра (до 600 мм) - вільним куванням. Такі заготовки обробляються по всіх поверхнях.
У середньо-, крупносерійному і масовому виробництві при діаметрах до 600 мм колеса виготовляють переважно штампованими.
Штампування відрізняється високою продуктивністю і максимально наближують форму заготовки до форми готового колеса. Для полегшення заповнення штампа металом і звільнення його від заготовки штамп і заготовка повинні мати відповідні радіуси заокруглень і штампувальні ухили (~5°).
Внутрішня поверхня обода, зовнішня поверхня маточини, бокові поверхні диску штампованих коліс звичайно не обробляються.
Колеса великих діаметрів виготовляють литими, а в індивідуальному виробництві – зварними.
Чавунні колеса у тихохідних малонавантажених передачах виготовляють найчастіше литими. У коліс литої конструкції в дисках роблять 4...6 отворів. Отвори призначені для кріплення колеса при обробці заготовки, що дозволяє обробляти отвір під вал і зовнішню поверхню обода з однієї установки. Великі розміри отворів зменшують масу коліс.
У колесах дискової конструк-
163
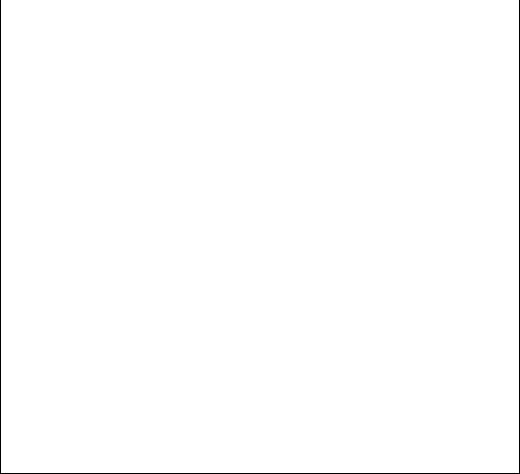
Розділ 10 |
Конструювання деталей редуктора |
ції симетричне розташування диску, щодо обода колеса, зовсім не обов'язкове. Розташування диску біля одного з торців обода дозволяє у ряді випадків істотно зменшити нерівномірність розподілу навантаження по ширині вінця, а також спрощує технологію кування колеса в однобічних підкладних штампах, а в литих колесах спрощує модель і виливки.
Виступаюча по обидва боки вінця маточина дає можливість нарізати зубці тільки на одному колесі, а маточина, що виступає лише з одного боку, дозволяє нарізати зубці на двох колесах одночасно. При однаковій довжині маточини і ширині вінця можливе одночасне нарізування зубців на декількох колесах.
У маточині литого колеса іноді для полегшення колеса проти шпонки робиться прилив, що дозволяє виготовити іншу частину маточини більш тонкою.
Таблиця 10.1 - Розміри елементів зубчастих коліс.
Параметри |
|
|
Формула |
||
|
|
|
|
||
Діаметр маточини стальних коліс |
dст ≈1,6dв |
|
|
||
Діаметр маточини чавунних коліс |
dст ≈1,8dв |
|
|
||
Довжина маточини |
lст ≈ (1,2...1,5)dв |
||||
Товщина обода циліндричних коліс (але не ме- |
δ |
|
= (2,5...4)m |
|
|
нше 8 мм) |
|
0 |
|
|
n |
Товщина обода конічних коліс (але не менше 8 |
δ |
|
= (3...4)m |
|
|
мм) |
|
0 |
|
e |
|
Товщина диска кованих коліс |
C = 0,3b2 |
|
|
||
Товщина диска штампованих коліс |
C = (0,2...0,3)b2 |
||||
Товщина диска литих коліс |
C = 0,2b2 |
|
|
||
Товщина диска конічних коліс |
C = ( 0,1...0,17 )Re |
||||
Внутрішній діаметр обода циліндричних коліс |
D0 = d f − 2δ0 |
|
|||
Внутрішній діаметр обода конічних коліс |
D0 |
= ( Re −1,25b )tgδ2 |
|||
Діаметр центрового кола |
Dотв = 0,5( D0 + dст ) |
||||
Діаметр отворів в диску (в колесах малих роз- |
dотв = 0,25( D0 − dст ) |
||||
мірів отвори не виконують) |
|||||
Товщина ребер литих коліс |
s = 0,8C |
|
|
||
Фаски зубців |
n ≈ 0,5mn |
|
|
В масовому виробництві циліндричні колеса при нарізанні зубців обробляють «пакетами» по два і більше. При цьому маточина не повинна виступати за торець вінця,
тобто lст≤ b.
Позначення: dв – діаметр вала; mn – модуль нормальний; mе – зовнішній коловий модуль; b – ширина зубчастого вінця; Re – зовнішня конусна відстань.
164
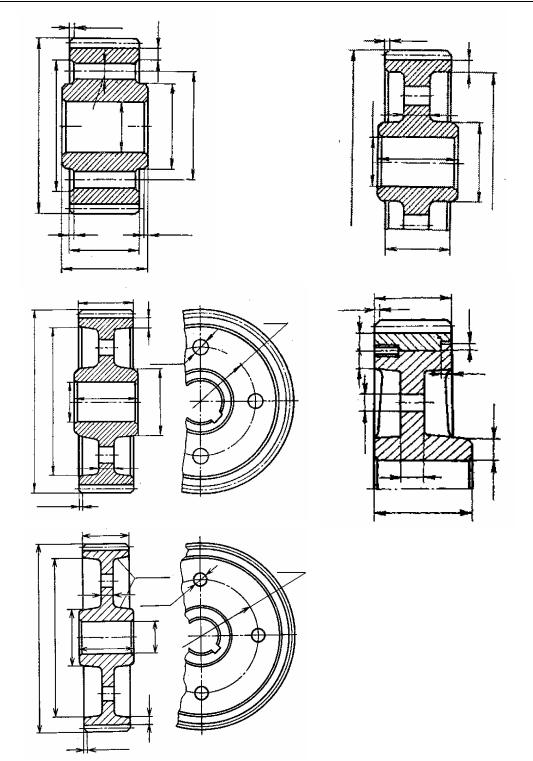
Розділ 10
n× 450 |
o |
|
δ |
a |
o |
отв |
в |
ст |
oтв |
d |
D |
d |
d |
d |
D |
|
|
3…5 мм |
2×450 |
|
|
b |
а) |
|
|
lст |
|
|
|
b |
o |
|
|
|
|
|
|
|
δ |
|
|
|
dотв |
a |
o в |
lст |
ст |
|
|||
d |
D d |
|
d |
|
|
С |
|
|
n× 450 |
|
в) |
|
|
b |
|
|
|
С |
1:20 |
|
|
dотв |
|
|
|
|
|
|
a o ст |
|
в |
d D d |
lст |
d |
|
|
|
|
|
|
|
|
o |
|
|
|
δ |
|
|
n× 450 |
|
Dотв
Dотв
г)
Конструювання деталей редуктора
|
n× 450 |
|
o |
|
|
|
δ |
в |
|
С |
o |
|
D |
||
d |
|
|
|
a |
lст |
|
ст |
|
|
||
d |
|
|
d |
|
b |
|
б) |
|
|
|
|
n× 450 |
b |
|
|
|
|
|
|
|
|
|
t |
o |
|
|
|
δ |
|
|
|
S |
|
|
h |
|
|
|
|
|
|
|
ст |
|
|
|
δ |
ст |
|
|
|
d |
|
|
|
|
С |
|
в |
|
|
|
|
|
|
|
d |
д) |
lст |
|
|
Рисунок 10.2- Циліндричні зубчасті колеса:
а- коване колесо при d ≤ 150 мм;
б- коване колесо при d ≥ 150 мм; в – штамповане колесо;
г – лите колесо при d ≤ 600 мм; д – бандажоване колесо
при d ≥ 500 мм.
165
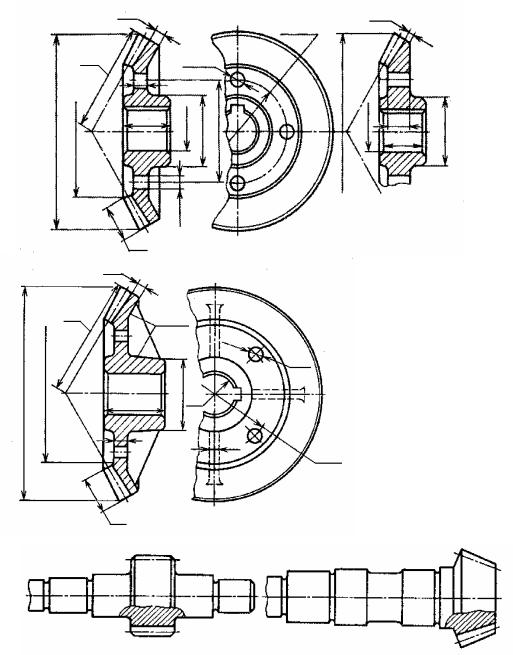
Розділ 10 |
Конструювання деталей редуктора |
δо
Re
С
ae |
0 |
d |
D |
b
δо
Re
ae |
0 |
|
d |
D |
lст |
|
|
С
b
а)
dотв |
|
|
в |
ст |
отв |
d d D |
||
отв |
|
|
d |
|
|
а) |
|
|
1:20 |
|
|
ст |
dв |
|
d |
|
S
в)
δо
Dот
dae
в |
С |
ст |
|
||
d |
|
d |
б)
dотв
Dотв
Рисунок 10.3 -Конічні зубчасті колеса:
а – штамповані при dae ≤ 500 мм;
б– ковані при dae ≤ 500 мм;
в– литі при dae > 300 мм.
б)
Рисунок 10.4 - Вали-шестірні: а – циліндрична; б – конічна
166
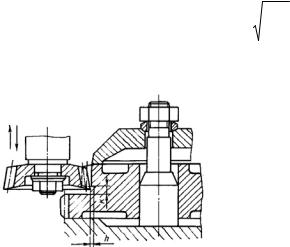
Розділ 10 |
Конструювання деталей редуктора |
При діаметрах d ≥ 500 мм важко навантажені колеса можуть виконуватися бандажними. Бандаж (обід) виконується з легованої сталі, центр – із дешевої вуглецевої сталі литим чи зварним, а також - литим чавунним (рис.10.2,д). Товщина бандажу (мм) по впадинах зубців:
при z<150.
|
|
|
δ0 |
= ( 2,4m +10 ) |
|
|
z |
, |
|
|
(10.1) |
||||
|
при z >150 |
150 |
|
|
|||||||||||
|
|
|
|
|
|
|
|
|
|
|
|||||
|
δ0 |
= 0,016d +10 . |
|
|
|
|
|
|
|
(10.2) |
|||||
|
|
|
|
|
|
|
|
|
|
||||||
|
|
|
|
|
|
|
|
Товщина ободу центра колеса s δ0 . |
|||||||
|
|
|
|
|
Розміри буртика h і t приймаються як для |
||||||||||
|
|
|
|
|
черв'ячних коліс (див. рис.10.7). |
||||||||||
|
|
|
|
|
|
|
|
Діаметр |
стопорних гвинтів dгв= |
||||||
|
|
|
|
|
(0,5...0,6)δ0 , довжина lгв |
≤ 3dгв. |
|||||||||
|
|
|
|
|
|
|
|
Вінці коліс внутрішнього зачеплення |
|||||||
|
|
|
|
|
і блок шестірні обробляються довб’яками |
||||||||||
|
|
|
|
|
(рис.10.5). Глибина канавки для виходу |
||||||||||
|
|
|
|
|
довб’яка h=(1...2) мм. Ширина канавки |
||||||||||
|
|
|
|
|
вибирається за табл.10.2. На довбальних |
||||||||||
|
|
|
|
|
верстатах обробляються |
також шевронні |
|||||||||
Рисунок 10.5 - Спосіб закріплення |
колеса з мінімальною шириною канавки |
||||||||||||||
блока циліндричних коліс на зубо- |
між півшевронами (ширина канавки – див. |
||||||||||||||
|
довбальному верстаті |
табл. 10.2). |
|
|
|
|
|
||||||||
|
Таблиця 10.2 - Ширина канавки k, мм, для виходу довб’яка |
||||||||||||||
|
β0 |
|
|
|
|
|
|
m, мм |
|
|
|
|
|
||
|
|
1,5 |
2…3 |
4 |
|
|
|
|
5...6 |
|
8 |
|
10 |
|
|
|
|
|
|
|
|
|
|
|
|
||||||
|
|
|
|
|
|
|
|
|
|
|
|
|
|
|
|
|
0 |
|
5 |
6 |
7 |
|
|
|
|
8 |
|
10 |
|
11 |
|
|
15 |
|
5,5 |
7 |
8,5 |
|
|
10 |
|
12 |
|
15 |
|
||
|
23 |
|
6,5 |
8 |
10 |
|
|
12 |
|
15 |
|
18 |
|
||
|
30 |
|
7,5 |
10 |
12 |
|
|
15 |
|
18 |
|
22 |
|
Найбільш розповсюдженим і продуктивним є нарізування зубців чер- в'ячною фрезою. Ширина канавки між півшевронами шевронного колеса при нарізуванні зубців черв'ячною фрезою визначається за табл.10.3.
Таблиця 10.3 - Ширина канавки k, мм для виходу черв’ячної фрези
|
|
|
|
|
|
|
|
mn, |
|
β0 |
|
mn, |
|
β0 |
|
мм |
20 |
30 |
40 |
мм |
20 |
30 |
40 |
|
|
||||||
|
|
|
|
|
|
|
|
2 |
28 |
32 |
35 |
5 |
52 |
58 |
63 |
2,5 |
32 |
37 |
40 |
6 |
60 |
67 |
72 |
3,0 |
36 |
42 |
45 |
7 |
68 |
75 |
82 |
3,5 |
40 |
47 |
50 |
8 |
75 |
82 |
90 |
4 |
46 |
52 |
55 |
10 |
90 |
100 |
108 |
167
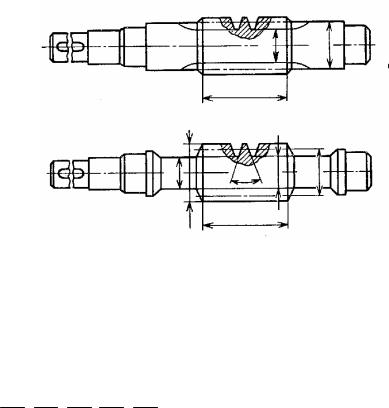
Розділ 10 |
Конструювання деталей редуктора |
Витки черв’яків виконують у більшості випадків за одне ціле з валом (рис. 10.6): фрезеруванням при d0 > df1 чи нарізанням на токарних станках при d0 < df1, чим забезпечується вільний вихід різця.
Черв'ячні колеса для економії кольорових металів виконують із бронзовим вінцем і чавунним чи (рідше) сталевим центром.
f1 |
0 |
d |
d |
b1
a)
d0
da1
400
b1
df1
d1
б)
Рисунок 10.6 - Черв’яки:
а – з фрезерованими витками; б – з витками, нарізаними на токарному верстаті.
Для коліс невеликих і середніх діаметрів найбільш часто застосовується бандажна конструкція, у якій бронзовий обід сідає на колісний центр по посадці з гарантованим натягом. Конструкція цього з'єднання показана на рис.10.7. Для з'єднання обода і колісного центра застосовують посадки
Hp67 , Hr67 , Hs67 , Hs77 , Hs78 .
При нагріванні до високої температури посадка може ослабнути внаслідок розходження в коефіцієнтах лінійного розширення бронзи і чавуну. Для запобігання взаємного окружного й осьового зсуву вінця і маточини їх з'єднують гвинтами по поверхнях рознімання. Як правило, використовують стандартні гвинти із шестигранною головкою, їх сильно затягують. Після затягування зайву частину гвинтів зрізають, а ту частину що залишилася закернують у декількох місцях. При свердлінні отворів під гвинти у площині спряження двох деталей, свердло веде в бік менш твердої деталі. Для усунення цього, центр отвору зміщують у бік більш твердої деталі. При чавунному центрі такий зсув можна не робити. Посадочну поверхню виконують з упорним буртиком або без нього. Щоб уникнути центрування по двох поверхнях діаметр розточки у вінці під буртик повинен бути на 0,5...1 мм більшим діаметра буртика центра колеса. Розміри, буртика: h = (0,15…0,2)b2, t=0,1b2. У з'єднанні без буртика гвинти ставлять із двох сторін у шаховому порядку.
168
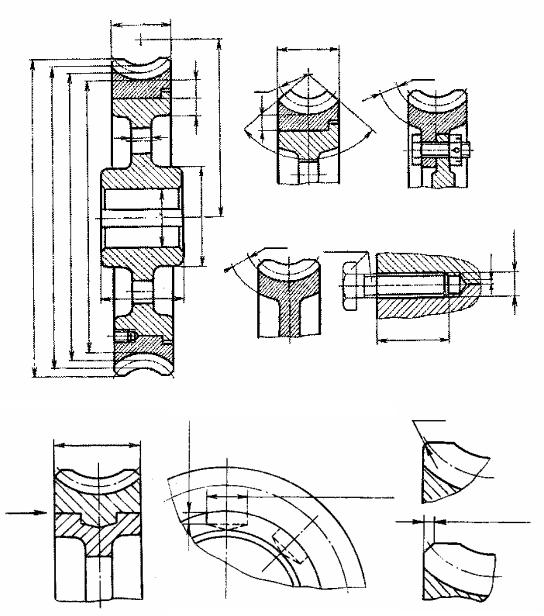
Розділ 10 |
Конструювання деталей редуктора |
b2
δ2 δ1
C
аw
ам2 а2 2 f2 |
в |
ст |
d d d d |
d |
d |
b2
δ1
d1/2
δ1
2γ
б) в)
δ1 Спиляти
lгвинта
t |
гвинта |
d |
|
а) |
|
г) |
д) |
|
(0,3…0,4)b |
A |
0,5m |
|
b2 |
|
|||
|
|
d=(0,4…0,5)b |
ж) |
|
A |
|
|
||
|
|
|
0,5m×450 |
|
|
|
|
|
з)
е)
Рисунок 10.7 - Конструкція черв’ячних коліс:
а– з напресованим і фіксованим гвинтом вінцем; б – з напресованим вінцем;
в– з прикрученим вінцем; г – суцільнолите черв’ячне колесо; д – фіксація вінця;
е– біметалічна конструкція черв’ячного колеса; ж – закруглення зубця колеса;
з– фаска зубців колеса.
169
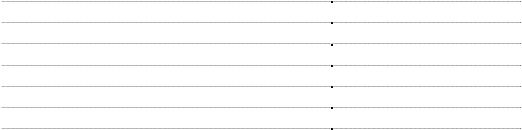
Розділ 10 |
Конструювання деталей редуктора |
Кількість гвинтів від трьох до восьми з кожної сторони вінця. |
Рекомендова- |
||||||||
ні товщини вінця наведені в табл.10.4. Діаметр гвинтів dв |
= (1,2. ..1,5)m. |
||||||||
Довжина гвинтів lв = (2...3)dв. |
|
|
|
|
|
|
|
|
|
Таблиця 10.4 - Розміри елементів черв’ячних коліс |
|
|
|
|
|
|
|
|
|
Параметри |
|
|
|
Формула |
|
|
|
||
|
|
|
|
|
|||||
Діаметр маточини колеса |
dст ≈ (1,6...1,8)dв |
|
|
|
|||||
Довжина маточини колеса |
lст ≈ (1,2...1,7)dв |
|
|
|
|||||
Товщина вінця колеса при: |
δ1 = 3,5m |
|
|
|
|
|
|||
m = 1,5 мм; |
|
|
|
|
|
||||
m = 2 мм; |
δ1 = 3,2m |
|
|
|
|
|
|||
m = 2,5 мм; |
δ1 = 3m |
|
|
|
|
|
|||
m = 3 мм; |
δ1 = 2,8m |
|
|
|
|
|
|||
m = 4 мм; |
δ1 = 2,5m |
|
|
|
|
|
|||
m = 5 мм; |
δ1 = 2,4m |
|
|
|
|
|
|||
m > 6 мм |
δ1 = 2,1m |
|
|
|
|
|
|||
Товщина обода центра |
δ2 |
=δ1 |
|
|
|
|
|
||
Товщина диска колеса |
C = 0,25b2 |
|
|
|
|
|
|||
Внутрішній діаметр обода колеса |
D0 |
= d f 2 − 4δ1 |
|
|
|
|
|||
Діаметр центрового кола |
Dотв = 0,5(D0 + dст ) |
|
|
||||||
Діаметр отворів у диску (в колесах малих розмірів |
d |
|
|
= 0,25(D |
|
− d |
|
) |
|
отвори не виконують) |
|
отв |
|
0 |
|
ст |
|
|
У колесах великих діаметрів (dам2 ≥ 400 мм) вінець ставлять на болтах для отворів з-під розверстки (рис.10.7,в). У серійному і масовому виробництві застосовують біметалічну конструкцію (рис.10.7, е), у якій вінець відлитий у форму з попередньо вставленим у неї центром. Кути по краях зубців притупляють фаскою або округленням (рис.10.7, ж, з).
Часто торці зубців оформляють відповідно до кута обхвату 2γ (рис.10.7, б). При цьому зменшується можливість поломки зубця при зсуві плями контакту до одного з торців. Конструкція центра виконується аналогічно конструкції литих зубчастих коліс. Робочі креслення зубчастих і черв’ячних коліс зображені на рис.10.8…10.13.
10.2 Конструювання шківів пасових передач та зірочок ланцюгових передач
Шківи плоскопасових передач. При коловій швидкості υ ≤ 15 м/с
шківи виготовляють з чавуну СЧ15, для υ =15…30 м/с – із СЧ20. При великих швидкостях, внаслідок дії відцентрових сил, міцність чавуну недостатня. Якщо швидкість менша 45 м/с, застосовують сталеві шківи марки 25Л.
170
Розділ 10 |
Конструювання деталей редуктора |
Частіше шківи виготовляються литими, а при малих діаметрах - точеними.
Рисунок 10.8
171
Розділ 10 |
Конструювання деталей редуктора |
Рисунок 10.9
172
Розділ 10 |
Конструювання деталей редуктора |
Рисунок 10.10
173
Розділ 10 |
Конструювання деталей редуктора |
Рисунок 10.11
174
Розділ 10 |
Конструювання деталей редуктора |
Рисунок 10.12
175
Розділ 10 |
Конструювання деталей редуктора |
Рисунок 8.13
176
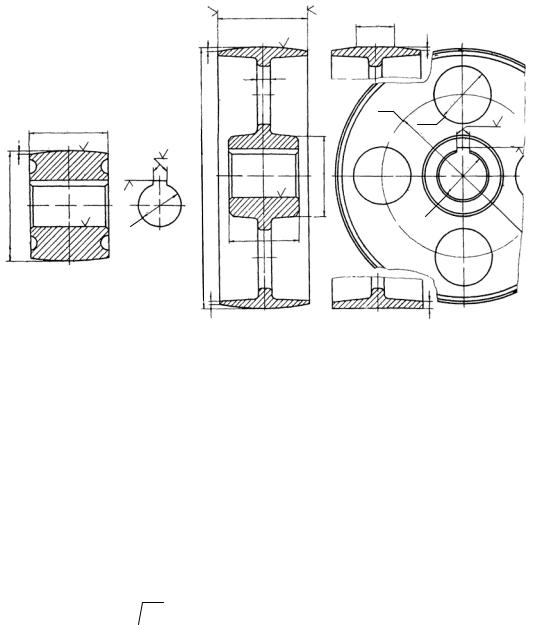
Розділ 10 |
Конструювання деталей редуктора |
Стандарт ГОСТ 17383-73 регламентує три види конструктивного виконання робочої поверхні ободу шківа: опуклий (рис.10.14, а, б); циліндричний (рис.10.14, б); циліндричний з подвійною конусністю (рис.10.14. г). Там же наведені значення стріли опуклості h (табл.10.5).
h
dP
|
|
|
6,3 |
В |
|
6,3 |
≤0,4В |
|
||
|
|
|
|
|
|
|
|
|||
|
|
|
h |
|
0,4 |
|
|
h |
|
|
|
|
|
|
|
|
|
|
|||
|
|
|
|
|
δ |
|
|
|
|
|
|
|
|
|
|
|
г) |
do |
|
||
|
|
|
|
|
|
|
3,2 |
|||
B |
|
|
|
|
|
|
|
dотв |
||
|
|
|
|
|
|
|
|
|
|
|
0,4 |
|
|
3,2 |
|
|
|
|
|
|
|
|
|
|
|
|
|
|
|
|
6,3 |
|
|
|
|
|
|
|
|
|
|
|
|
|
|
|
|
|
|
м |
|
|
|
|
|
|
|
|
|
|
d |
|
|
|
|
|
6,3 |
|
|
0,8 |
|
|
|
|
|
|
|
p |
|
|
|
|
|
|
|
||
|
|
|
d |
|
|
|
|
d |
|
|
0,8 |
d |
|
|
|
|
|
|
|
||
|
|
|
|
|
|
|
|
lС
а)
e |
h |
б) в)
Рисунок 10.14 – Конструкції ободу шківів:
а, б – опуклий; в – циліндричний; г – з подвійною конусністю
Опуклість робочої поверхні ободу запобігає сповзанню паса. Опуклість переважно роблять на більшому шківі, тому що напруження від згину паса менші, ніж на малому шківі. При u = 1 робиться опуклим ведений шків, а при υ > 25 м/с опуклими мають бути обидва шківи. За конструкцією литі і точені шківи виконуються монолітними (рис.10.14, а), з диском (рис.10.14, б), із спицями. Якщо висока точність монтажу передачі не може бути забезпечена, для попередження сповзання паса застосовують шківи з ребордою.
У дисках передбачають отвори для кріплення шківа при обробці, полегшення транспортування та зменшення маси, а також для виходу ливарних газів (для литих конструкцій).
Шківи із спицями використовують при коловій швидкості υ < 25 м/с і dP > 300 мм, у випадку більшої швидкості застосовують шківи з диском.
Число спиць можна визначити розрахунковим шляхом:
zc = d p
6,5 ,
де dp – розрахунковий діаметр шківа, мм.
Якщо zс<3, то шків виготовляється з диском. Якщо zс>3, то кількість спиць округлюється до найближчого парного числа. Вісь шпонкової канавки
177
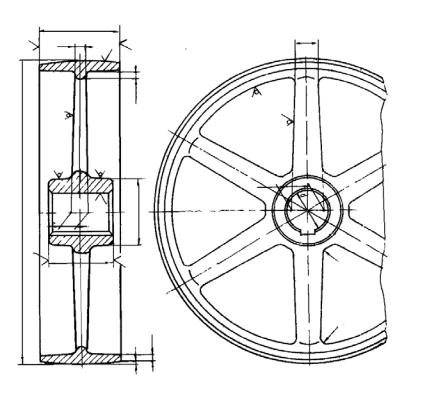
Розділ 10 |
Конструювання деталей редуктора |
Таблиця 10.5 - Діаметри шківів і стріла опуклості, мм (ГОСТ 17383-73)
Зовнішній діаметр |
40 |
45 |
50 |
56 |
|
63 |
71 |
80 |
|
90 |
100 |
112 |
125 |
140 |
|
Відхилення |
±0,5 |
± |
0,6 |
± |
0,8 |
± |
1,0 |
|
|
±1,2 |
|
± |
1,6 |
||
Зовнішній діаметр |
140 |
160 |
180 |
200 |
|
224 |
250 |
280 |
|
315 |
355 |
400 |
450 |
500 |
|
Відхилення |
±1,6 |
|
|
±2,0 |
|
|
± |
2,5 |
|
|
±3,2 |
|
|
±4,0 |
|
Зовнішній діаметр |
560 |
630 |
710 |
800 |
|
900 |
1000 |
1120 |
1250 |
1400 |
1600 |
1800 |
2000 |
||
Відхилення |
|
±5,0 |
|
|
|
±6,3 |
|
|
|
±7,1 |
|
|
±8,0 |
|
|
Ширина В |
|
|
|
|
Відхилення |
|
|
Стріла опуклості обода, h |
|||||||
40 |
|
|
|
|
|
|
|
|
|
|
|
|
1 |
|
|
50 |
|
|
|
|
|
± 1 |
|
|
|
|
|
|
|
||
63 |
|
|
|
|
|
|
|
|
|
|
|
|
|
||
71 |
|
|
|
|
|
|
|
|
|
|
|
|
1,5 |
|
|
80 |
|
|
|
|
|
|
|
|
|
|
|
|
|
|
|
100 |
|
|
|
|
± 1,5 |
|
|
|
|
|
|
|
|
||
125 |
|
|
|
|
|
|
|
|
|
2 |
|
|
|||
140 |
|
|
|
|
|
|
|
|
|
|
|
|
|
|
|
|
|
|
|
|
|
|
|
|
|
|
|
|
|
|
|
160 |
|
|
|
|
|
|
|
|
|
|
|
|
|
|
|
200 |
|
|
|
|
|
± 2 |
|
|
|
|
|
2,5 |
|
|
|
224 |
|
|
|
|
|
|
|
|
|
|
|
|
|||
|
|
|
|
|
|
|
|
|
|
|
|
|
|
|
|
250 |
|
|
|
|
|
|
|
|
|
|
|
|
|
|
|
315 |
|
|
|
|
|
± 3 |
|
|
|
|
|
3 |
|
|
|
355 |
|
|
|
|
|
|
|
|
|
|
|
|
|||
|
|
|
|
|
|
|
|
|
|
|
|
|
|
|
6,3
dP
6,3
|
В |
с0 |
а0 |
6,3 |
|
|
0,4 |
|
|
S |
|
|
|
с |
3,2 |
М |
|
а |
d |
|
|
|
|
lМ |
6,3 |
R |
|
|
|
|
|
R0 |
|
|
e |
h
Рисунок 10.15 – Конструкція шківів із спицями
178

Розділ 10 |
Конструювання деталей редуктора |
в маточині шківа повинна збігатися з подовжньою віссю спиці.
Переріз спиці береться еліптичним, причому велика вісь еліпса с лежить у площині обертання шківа і відкладається в місці перетинання спиці з діаметральною площиною шківа. Менша вісь еліпса а переважно приймається на 60% менше с, тобто a =0,4с. Спиці працюють на згин, як консольні балки, які навантажені зосередженою силою Ft, (у даному випадку - це колова сила, прикладена на розрахунковому діаметрі dp ). Шуканий вираз для визначення с з умови міцності на згин, (з врахуванням деяких умовностей,
прийнятих у розрахунку), має вигляд: |
||||||
с ≥ 3 40F d |
p |
(z |
c |
σ |
HF |
), |
t |
|
|
|
де Ft - колова сила, в Н; (Ft = 2Т/dp, Т – крутний момент на валу шківа);
σHF =30...40 МПа – допустимі напруження згину для сірих чавунів СЧ15 і
СЧ20; для вуглецевих сталей можна прийняти σHF =70...90 МПа. Розрахункове с округлюється до цілого числа в мм. Від діаметральної площини до обода шківа згинаючий момент, створюваний на спиці коловою силою Ft зменшується, тому переріз спиці в цьому напрямку звужується. У поздовжньому напрямку спиця викреслюється так, що її перетин із зовнішнім
колом обода дає розмір осі еліпса с0 ≈ 0,8с. Менша вісь еліпса тут приймається а0=0,4с0.
У шківах, при ширині ободу В ≤ 300 мм, спиці розташовуються в один ряд, у більш широких шківах у два ряди. При зовнішньому діаметрі dP>500мм і серійному виробництві застосовуються зварні шківи з прокату та штампованих елементів, які працюють при швидкості до 60 м/с.
Геометричні розміри елементів шківа визначають за такими залежнос-
тями:
Товщина ободу біля краю
e = 0,005d p + 3 - для литих шківів;
e = 0,004(b + 0,5d p )+ 4 - для зварних,
де b і dp — відповідно ширина паса та розрахунковий діаметр шківа, мм. Висота ребра у литих шківів (рис. 10.15)
s = e + 0,02B .
Діаметр маточини шківів всіх типів d м = (1,8...2,0)d ,
де d - діаметр вала.
Довжина маточини для шківів при однорядному розташуванні спиць
lм = (1,5...2,0)d .
Радіуси спряження спиці біля маточини і з ободом (рис.10.15) дорівнюють відповідно R = 0,8а і R0 =0,8a0, а, а0 — розміри перерізу спиці, що визначаються при розрахунку на міцність.
Діаметр кола розташування отворів у шківах з диском d0 = 0,5(d p − 2e + d м ).
Діаметр отвору у диску шківа dотв 0,35[d p − (2e + dM )].
Товщина диска δ=(0,25... 0,3)d, але не менше 8 мм.
179

Розділ 10 |
Конструювання деталей редуктора |
Граничні відхилення розрахункового діаметру шківів згідно з ГОСТ13383-73 подані у табл. 10.5. Не вказані граничні відхилення оброблених не спряжених поверхонь: отворів - по Н14, валів - по h14, решти - по js16. Норми радіального та торцевого биття ободу шківа наведені у табл.10.6.
Таблиця 10.6 - Радіальні і торцеві биття ободу шківа
Радіальне биття |
|
Торцеве биття |
|
Діаметр dp, мм |
Биття, мкм |
Діаметр dp, мм |
Биття, мкм |
50…120 |
40 |
60…160 |
40 |
120 …260 |
50 |
160…400 |
60 |
260… 500 |
60 |
400…1000 |
100 |
500… 800 |
80 |
|
|
Шківи, що працюють при швидкості υ >5 м/с, мають бути статично сбалансовані.
Рекомендовані діаметри розточок маточини та її довжина для кожного розміру шківа наведені у ГОСТ 17383 -73.
Граничні відхилення довжини маточини з конічним посадковим отвором не більше Н13. Шорсткість робочої поверхні ободу немає перевищувати Rа=0,2...0,4 мкм, її бажано полірувати. Посадковий отвір під вал повинен мати шорсткість не вище Rа = 0,8...1,6 мкм, решта оброблених поверхонь Rа=6,3 мкм, необроблені литі поверхні - Rа =100 мкм. Необроблені поверхні шківів мають бути пофарбовані.
При шпонковому з'єднанні і циліндричному з’єднанні маточини з валом призначають такі посадки: при нереверсивному спокійному наванта-
женні - Hk67 ; при нереверсивному навантаженні з помірними поштовхами та
ударами - Hm67 ; при реверсивному навантаженні з великими поштовхами та
Hp67 . \
Осьова фіксація шківа виконується стопорними гвинтами або торцевими шайбами.
Шківи клинопасових передач. Матеріали для виготовлення шківів такі ж, як для шківів плоскопасових передач. Розміри профілю канавок литих та точених шківів клинопасових передач наведені у табл.10.8. Конструктивно литі і точені шківи виконуються монолітними (рис.10.16, а), з диском або із спицями (рис.10.16, б). Область застосування клинопасових шківів різних типів наведено в табл.10.7
Робочі поверхні канавок повинні мати шорсткість не більше Ra=0,4 мкм, а при малих діаметрах шківів не більше Ra = 0,2 мкм. Робочі поверхні бажано полірувати. Зовнішній діаметр і ширина ободу клинопасових шківів відповідно
de = d p + 2b , В = (z −1)e + 2 f .
180
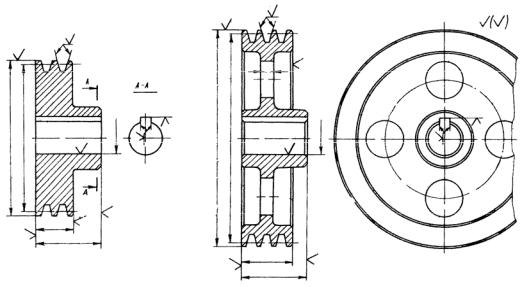
Розділ 10 |
Конструювання деталей редуктора |
Розміри решти конструктивних елементів (не стандартизовані): товщина ободу чавунного шківа
S = Sчав = (0,8...0,9)h ;
товщина ободу стального шківа
S = Sст = 0,8Sчав ;
товщина диска
δ = (1,2...1,3)S ;
діаметри технологічних отворів в диску
d0 = (0,7...0,8) (d0 − d м ),
дени.d0 = dp - 2 (h + S) – внутрішній діаметр обода шківа; dм – діаметр маточи-
6,3
de dМ
6,3
0,4
0,8
lМ |
|
6,3 |
|
В |
|
|
|
а)
6,3
d |
3,2 |
6,3 |
|
d d |
|||
|
|
e |
М |
6,3
6,3
0,4
δ |
6,3 |
|
0,8 |
d |
|
lМ |
6,3 |
|
В |
||
|
б)
80
6,3
3,2
Рисунок 10. 16– Конструкція шківів клинопасових передач
Таблиця 10.7 - Границі розрахункових діаметрів і число канавок клинопасових шківів різних типів (ГОСТ 20889-80 і ГОСТ 20897-80)
Переріз паса |
Розрахункові діаметри шківів dр, мм |
Кількість |
|||
монолітний |
з диском |
зі спицями |
канавок |
||
|
|||||
Z |
50…90 |
80…160 |
≥ 180 |
1…4 |
|
А |
90…100 |
112…200 |
≥ 224 |
1…6 |
|
В |
- |
125…250 |
≥ 280 |
1…7 |
|
С |
- |
200…355 |
≥ 400 |
1…8 |
|
D |
- |
315…400 |
≥ 450 |
1…8 |
181
Розділ 10 |
Конструювання деталей редуктора |
Таблиця 10.8
182
Розділ 10 |
Конструювання деталей редуктора |
Конструктивні параметри шківів (розміри спиць, маточини, число спиць) визначаються, як і для шківів плоскопасових передач.
Допуски на відстань між віссю крайньої канавки і торцем шківа, а також на відстань між осями канавок приведені в табл.10.8.
Граничні відхилення діаметрів dр до 500 мм - по b11; понад 500 мм - по d11. Діаметр dр визначають одним із двох методів: за допомогою глибиноміра і за допомогою двох циліндричних роликів (див. мал. до табл.10.7). При вимірюванні глибиноміром повинен бути також знайдений, як допоміжний параметр, діаметр dе . Діаметри роликів, що рекомендуються d, і вимірювальні розміри x і К шківів для клинових пасів наведені в табл.10.8. Припустима різниця в розмірах канавок К одного й того самого шківа для клинових пасів не повинна перевищувати: для січень Z, А, В – 0,2 мм; для перерізу С –
0,3 мм.
Граничні відхилення зовнішніх діаметрів dе - h11. Невказані граничні відхилення вільних оброблюваних поверхонь: по Н14, валів - по h14, інші - по js16. Граничне відхилення довжини маточини з конічним посадковим отвором не повинне бути більше h13. Граничні відхилення кута канавки для механічно оброблених шківів не повинні бути більше 10 - для пасів перерізу Z, А, В; 30' - для типів пасів С, D, E, ЕO .
Биття конусної робочої поверхні канавки шківа на кожні 100 мм діаметра, заміряне перпендикулярно до утворюючого конуса, не повинне бути більше 0,2 мм при частоті обертання шківа до 8 с-1; 0,15 мм - при частоті обертання шківа 8...16 с-1; 0,10 мм - при частоті обертання шківа більше 16с-1. Радіальні і торцеві биття обода шківа приведені в табл.10.9.
Таблиця 10.9 - Радіальні і торцеві биття ободу шківа
|
|
Радіальне биття |
|
|
|
Торцеве биття |
|
|
Діаметр dp, мм |
Биття, мкм |
|
Діаметр dp, мм |
Биття, мкм |
||
Понад |
50 до 120 |
100 |
Понад |
60 до 160 |
100 |
||
» |
120 |
» 260 |
120 |
» |
160 |
» 400 |
160 |
» |
260 |
» 500 |
160 |
» |
400 |
» 1000 |
250 |
» |
500 |
» 800 |
200 |
|
|
|
|
Внутрішній отвір маточини під вал повинен мати шорсткість не більше Ra=2,5 мкм, інші оброблені поверхні (зовнішній діаметр, торці обода і маточини) - Ra = 6,3 мкм, необроблені литі поверхні - Ra = 400. Неопрацьовані поверхні шківа повинні бути пофарбовані.
Зірочки ланцюгових передач. За призначенням зірочки поділяються на ведучі, ведені та допоміжні (натяжні, відтяжні, обвідні). За конструктивним виконанням розрізняють зірочки зі спицями, без спиць, суцільні, складніі: з диска та маточини (рис.10.17).
Основні елементи зірочок (маточина, диск, вінець) проектуються так само, як аналогічні елементи зубчастих коліс та шківів. Конструкцію зірочок розробляють поряд з конструкцією інших елементів передачі з врахуванням стандарту на профіль зубців і поперечний переріз вінця. У табл.10.11 значення Dc і r4 обрані так, щоб бічні пластини ланцюга не заважали роликам вільно розміщатися в западинах зубців.
183
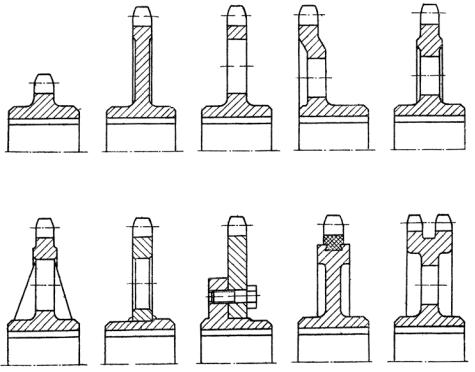
Розділ 10 |
Конструювання деталей редуктора |
а) |
б) |
в) |
г) |
д) |
е) |
ж) |
з) |
к) |
л) |
Рисунок 10.17 – Зірочки ланцюгових передач:
а – монолітні; б, в, г, д – з диском; е – із спицями; ж – зварні; з – складені; к – із зубчастим вінцем з пластмаси; л – з диском для дворядних ланцюгів
Ту чи іншу форму поперечного перерізу обода (див. табл.10.11) вибирають в залежності від співвідношення товщини b1 і діаметра De, а також від способу одержання заготовки. Наприклад, при малому b1 і великому De застосовують форму, зображену на мал.10.17, д, інакше зірочка вийде у вигляді тонкого диску і може вібрувати в осьовому напрямку. При великому b1 і порівняно малому De вигідна форма на мал.10.17, б, що дозволяє заощаджувати метал. Форма на мал.10.17, ж, доцільна при виготовленні зірочки з листа методом зварювання. В інших частинах конструкція зірочки проста. Вона подібна конструкції зубчастих коліс чи шківів. Конструкція на рис.10.17, з є кращою для діаметрів понад 200 мм, коли маточина може бути виконана з чавуну. Крім того, при зношуванні зубців, тут можна замінити тільки обід.
Ступінь шорсткості для бічних поверхонь зубів – Ra6,3, профілю Ra1,25…3,2. Шорсткість інших поверхонь за звичайними нормами. Посадка на вал не нижче 6-го квалітету точності.
Матеріал - сталь 15, 20 з цементацією вінця і гартуванням до 52…60 НRСэ; сталь 40, 45 і 40Л, 45Л з твердістю поверхневого шару вінця 40…50 НRСэ; чавун марки не нижче СЧ18 з термообробкою вінця до 360…430 НВ.
184
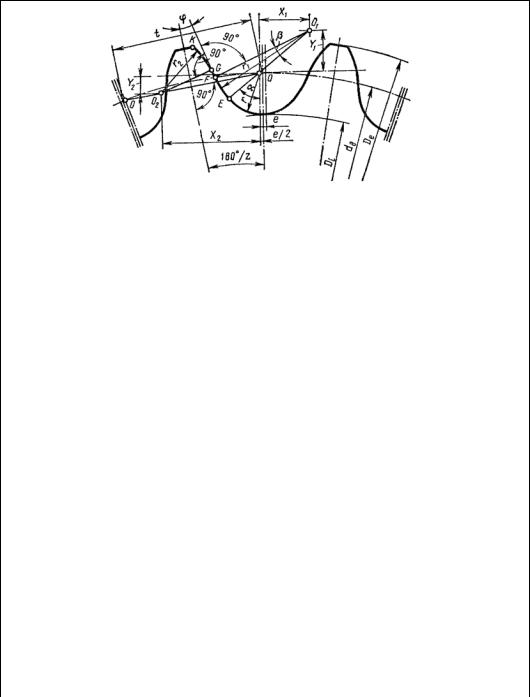
Розділ 10 |
Конструювання деталей редуктора |
Таблиця 10.10 - Метод розрахунку і побудова профілю зубців зірочок для привідних роликових і втулкових ланцюгів
Профіль зубців зі зміщенням центрів дуг впадин
Параметри |
Розрахункові формули |
||||||||||||||||||
Крок ланцюга t |
|
Згідно розрахунку |
|
||||||||||||||||
Діаметр ролика ланцюга (для втулкових |
Розміри згідно стандартів на ланцюг |
||||||||||||||||||
ланцюгів – діаметр втулки) D |
|||||||||||||||||||
|
|
|
|
|
|
|
|
|
|
|
|
|
|
|
|
|
|
||
Число зубців зірочки z |
|
Згідно розрахунку |
|
||||||||||||||||
|
|
|
dд |
= |
|
|
|
t |
|
|
|
|
|
|
|
|
|||
Діаметр ділильного кола dд |
|
|
|
1800 |
|
|
|
|
|||||||||||
|
|
|
|
sin |
|
|
|
|
|||||||||||
|
|
|
|
|
|
|
|
|
z |
|
|
|
|
|
|
||||
|
|
|
|
|
|
|
|
|
|
|
|
|
|
|
|
|
|||
|
|
|
|
|
|
|
|
|
|
1800 |
|||||||||
Діаметр кола виступів De |
D |
e |
= t |
K |
+ ctg |
|
|
|
|
|
|
|
|
||||||
|
|
|
|
|
|
|
|||||||||||||
|
|
|
|
|
|
|
|
|
|
|
|
z |
|
||||||
|
|
|
|
|
|
|
|
|
|
|
|
|
|
||||||
Діаметр кола впадин Dі |
|
|
Di = dд −2r |
|
|||||||||||||||
Найбільша хорда (для контролю зірочок з |
Lx = dд cos |
95 |
0 |
|
−2r |
||||||||||||||
непарним числом зубців) Lx |
|
|
|
|
|
|
|
||||||||||||
|
|
|
z |
|
|||||||||||||||
|
|
|
|
|
|
|
|
|
|
|
|
|
|
|
|
||||
Радіус впадин r |
r = 0,5025D + 0,05 мм |
||||||||||||||||||
Радіус спряження r1 |
r1 = 0,08D + r =1,3025D +0,05 мм |
||||||||||||||||||
Радіус головки зуба r2 |
r2 = D(1,24 cosϕ +0,8 cos β −1,3025 ) −0,05 мм |
||||||||||||||||||
Половина кута впадини α |
|
|
α = 550 − |
60 |
|
|
|
|
|
||||||||||
|
|
|
z |
|
|||||||||||||||
|
|
|
|
|
|
|
|
|
|
|
|
|
|||||||
Кут спряження β |
|
|
β =180 − |
600 |
|
|
|||||||||||||
|
|
|
я |
|
|||||||||||||||
|
|
|
|
|
|
|
|
|
|
|
|
|
|||||||
Половина кута зуба ϕ |
ϕ =170 − |
640 |
|
= 900 − |
1800 |
−(α + β) |
|||||||||||||
я |
|
|
|
|
я |
||||||||||||||
|
|
|
|
|
|
|
|
|
|
|
|
|
|
||||||
Пряма ділянка профілю FG |
FG = D(1,24 sinϕ −0,8 sin β) |
||||||||||||||||||
Відстань від центра дуги впадини до |
|
|
OO2 |
=1,24D |
|
||||||||||||||
центра головки зуба ОО2 |
|
|
|
|
|
|
|
|
|
|
|
|
|
|
|
|
|
|
|
Зміщення центрів дуг впадини е |
|
|
|
|
e = 0,03t |
|
|
|
|
|
|
185