
- •1 ЗАГАЛЬНІ ВІДОМОСТІ ПРО ПРИВОДИ
- •1.2 Огляд основних типів редукторів
- •Коефіцієнт корисної дії приводу
- •Таблиця 2.1- Значення ККД для механічних передач
- •Ланцюгова
- •Таблиця 2.2- Передаточні числа циліндричних зубчастих передач
- •(ГОСТ 2186-66)
- •Таблиця 2.3- Загальні передаточні числа двоступеневих редукторів
- •(ГОСТ 2186-66)
- •Таблиця 2.4- Передаточні числа конічних зубчастих передач
- •(ГОСТ 12289-76)
- •Таблиця 2.5- Передаточні числа черв’ячних передач (ГОСТ 2144-76)
- •Назва редуктора
- •Таблиця 2.7 - Рекомендовані значення u для різних типів редукторів
- •Тип передачі
- •Схема редуктора
- •Значення uп
- •Двоступеневий
- •циліндричний
- •редуктор
- •Розгорнута схема
- •Двоступеневий
- •співвісний редуктор
- •Двоступеневий
- •співвісний редуктор з
- •внутрішнім
- •зачепленням
- •Швидкохідна ступінь
- •Циліндрично-
- •черв’ячний редуктор
- •Продовження таблиці 2.7
- •Циліндрично-черв’ячний
- •редуктор
- •Черв’ячно-циліндричний
- •редуктор
- •Одноступеневі:
- •Таблиця 3.2 - Рекомендовані поєднання матеріалів шестірні
- •Поверхневе гартування
- •Таблиця 3.5 – Значення показників степеня кривої втоми m
- •Таблиця 3.7 - Границі витривалості зубців при згині
- •Сталі
- •Таблиця 3.16 - Коефіцієнт форми зубців YF
- •Площа
- •Таблиця 7.1 – Визначення сил в зачепленні механічних передач
- •Вид передачі
- •Значення сили, Н
- •Колова
- •Радіальна
- •Осьова
- •Колова
- •Радіальна
- •Осьова
- •Колова
- •Радіальна
- •Осьова
- •Муфта
- •Радіальна
- •Вал – шестірня
- •Вал – колеса
- •Таблиця 8.1 – Розміри проточок для різьби під круглі гайки
- •Умови роботи підшипника
- •Поля допусків
- •Таблиця 8.6 - Пластичні мастильні матеріали
- •Таблиця 8.7 – Манжети гумові армовані
- •Таблиця 9.1 - Значення коефіцієнта режиму навантаження К
- •Машини
- •L, мм не більше
- •Твердість згідно з ГОСТ 263-75, ум., од. ............…………………………...... 50—65
- •Таблиця 9.7 – Розміри і параметри муфти пружної втулково-пальцевої
- •Закінчення таблиці 9.7
- •Таблиця 9.8– Розміри (мм) пальців і втулок муфти пружної втулково-пальцевої
- •Закінчення таблиці 9.15
- •Таблиця 9.18 – Розміри і параметри ланцюгової однорядної муфти
- •Таблиця 10.11 - Зубці і вінець зірочки в поперечному перерізі
- •Параметри
- •Орієнтовні значення, мм
- •Параметри
- •Орієнтовні значення, мм
- •Розміри елементів спряжень литих корпусів, мм
- •Розміри елементів фланців литих корпусів, мм
- •Розміри гнізд підшипників і кришок, що прикручуються, мм
- •Кріплення
- •Кріплення
- •Кріплення
- •Кришки врізні, мм
- •Таблиця 10.14 - Кришка оглядового вікна
- •Таблиця 10.17 Пробки для зливу масла
- •Таблиця 10.33 Значення в’язкості масел, що рекомендуються для змащування черв’ячних передач при 1000С
- •Таблиця 10.38 - Види допусків
- •Найбільш раціонально розпочинати компонування цього редуктора з вхідного і вихідного валів. Після попереднього конструктивного оформлення підшипникових вузлів можна переходити до проміжного вала.
- •Параметри
- •Продовження таблиці 10.44
- •перетворимо нерівності (11.4), (11.5) в рівності і одержимо:
- •де Рвих – потужність на вихідному валі приводу, Вт.
- •Допустимі контактні напруження для шестірні і колеса
- •Еквівалентне число зубців шестерні і колеса
- •Допустимі контактні напруження для шестірні і колеса
- •2 ПРОЕКТУВАННЯ ПРИВОДУ
- •2.1. Вибір електродвигуна і кінематичний розрахунок приводу
- •Кутова швидкість вала електродвигуна
- •Допустимі контактні напруження для шестірні і колеса
- •2.4. Попередній розрахунок валів редуктора
- •Розрахункове значення кроку ланцюга
- •Розрахункова міжосьова відстань
- •Товщина фланців корпуса і кришки редуктора
- •Вихідний вал редуктора
- •4 ПРОЕКТУВАННЯ ПЕРЕДАЧІ
- •5.1 Вибір електродвигуна і кінематичний розрахунок приводу
- •Кутова швидкість вала електродвигуна
- •Література
- •Потуж-
- •Синхронна частота обертання, хв-1
- •Типо-
- •розмір
- •Типо-
- •розмір
- •Типо-
- •розмір
- •Типо-
- •розмір
- •Таблиця B.1 - Ланцюги типу ПРА
- •Таблиця B.2 - Ланцюги типу ПР
- •Таблиця B.3 - Ланцюги типу 2ПР
- •Таблиця B.4 - Ланцюги типу 3ПР
- •Таблиця B.5 – Ланцюги типу 4ПР
- •Таблиця B.6 – Ланцюги типу ПВ і 2ПВ
- •Таблиця В.7 – Ланцюги типу ПРИ
- •Розміри, мм
- •Розрахункові параметри
- •Особливо легка серія діаметрів 1, серія ширин 7
- •Особливо легка серія діаметрів 1, серія ширин 7
- •Легка серія діаметрів 2, серія ширин 0
- •Підшипник 315 ГОСТ 8338-75
- •Таблиця Г.2 - Кулькові підшипники радіальні дворядні сферичні
- •Легка серія
- •Легка широка серія
- •Середня серія
- •Середня широка серія
- •Підшипник 1204 ГОСТ 5720 -75
- •Кульки
- •Особливо легка серія
- •Легка серія
- •Важка серія
- •Приклад умовного позначення підшипника за ГОСТ 831 -75 з умовним позначенням 46205:
- •Підшипник 46205 ГОСТ 831-75
- •Таблиця Г.4-Роликові підшипники радіальні з короткими циліндричними роликами
- •Розміри, мм
- •Надлегка серія
- •Особливо легка серія
- •Легка широка серія
- •Середня серія
- •Середня широка серія
- •Важка серія
- •Підшипник 32315 ГОСТ 8328-75
- •Еквівалентне осьове навантаження
- •Легка серія діаметрів 2
- •Середня серія діаметрів 3
- •Важка серія діаметрів 4
- •Підшипник 8210 ГОСТ' 6874-75
- •Розміри, мм
- •Надлегка серія діаметрів 9
- •Особливо легка серія діаметрів 1
- •Легка серія діаметрів 2
- •Середня серія діаметрів 3
- •Середня широка серія діаметрів 6
- •Розміри, мм
- •Ролики
- •Розрахункові параметри
- •Підшипник 27312 ГОСТ 7260-81
- •Таблиця Д.15 – Шайби кінцеві (ГОСТ 14734-69)
- •Таблиця Д.16 – Шпильки з кінцем, що вгвинчується, довжиною
- •1d (ГОСТ 22032-76), 1,25d (ГОСТ 22034-76), 2d (ГОСТ 22038-76)
- •Таблиця Д.18 – Штифти конічні (ГОСТ 3129-70)
- •Таблиця Д.20-Збіги, проточки та фаски для метричної різьби ГОСТ 10549-80
- •Таблиця Д.23 – Кришки торцеві з отвором під манжетне ущільнення
- •(ГОСТ 18512-73)
- •Таблиця Д.26 – Кришки (торцеві та врізні) під регулювальні гвинти
- •Таблиця Д.27 – Стальні ущільнюючі шайби
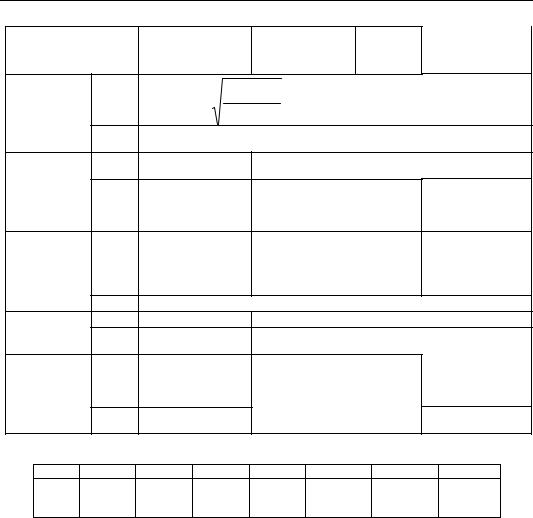
Розділ 7 |
|
|
|
|
|
|
|
|
|
|
Вали |
|
Таблиця 7.3 - Визначення розмірів ступенів валів редуктора, мм |
||||||||||||
Ступінь вала та її |
Вал – шестірня |
Вал – шестірня |
|
Вал – |
Вал – колеса |
|||||||
|
конічна |
|
циліндрична |
|
черв’як |
|||||||
параметри d, l |
|
|
|
(рис.7.4,г) |
||||||||
|
(рис.7.4,в) |
|
|
(рис.7.4,б) |
(рис.7.4,а) |
|||||||
|
|
|
|
|
|
|||||||
1 – ша |
d1 |
|
d1 |
≥ 3 16 |
10 |
3 |
T , де Т – крутний момент на валу, Нм |
|||||
під елемент |
|
|
||||||||||
відкритої |
|
|
|
πτadm |
|
|
|
|
|
|||
передачі або |
l1 |
|
l1=(0,8…1,5)d1 під зірочку; l1=(1,2…1,5)d1 –під шків |
|||||||||
півмуфту |
|
|||||||||||
l1=(1,0…1,5)d1 – під шестірню; l1=(1,0…1,5)d1 – під півмуфту |
||||||||||||
2 – га |
|
|||||||||||
d2 |
d2=d1+2t – тільки |
|
|
|
|
|
d2=d1+2t |
|
||||
під ущіль- |
під ущільнення |
|
|
|
|
|
|
|||||
|
|
|
|
|
|
|
|
|||||
нення |
|
l2 ≈ 0,6 d2 |
|
|
|
|
|
|
|
|
||
кришки з |
l2 |
– тільки |
|
|
|
l2 ≈ 1,5 d2 |
|
l2 ≈ 1,25 d2 |
||||
отвором і |
під ущільнення |
|
|
|
|
|||||||
підшипник |
|
|
|
|
|
|
|
d3=d2+3,2r ; |
|
|||
|
|
|
|
|
|
|
|
|
||||
3 – тя |
d3 |
d3=d4+3,2r мож- |
|
|
можливо d3 ≤ df1 ; |
d3=d2+3,2r |
||||||
під шестір- |
ливо d3 ≤ dfe1 |
|
|
|
при d3 > da1 |
|||||||
|
|
|
|
|
||||||||
ню, колесо |
l3 |
|
|
|
|
|
прийняти d3=da1 |
|
||||
|
l3 визначають графічно по першому етапу компоновки редуктора |
|||||||||||
4 – тя |
d4 |
d4=d5+(2…4) мм |
|
|
|
|
|
d4=d2 |
|
|||
під підшип- |
l4 |
l4 |
визначають |
|
|
l4=B – для кулькових підшипників |
||||||
ник |
|
графічно |
|
l4=Т – для роликових конічних підшипників |
||||||||
|
|
d5 |
під різьбу ви- |
|
|
|
|
|
|
d5=d3+3f; |
||
|
d5 |
|
|
|
|
|
|
ступінь можливо |
||||
5 – та |
значити в залеж- |
|
|
|
|
|
|
|||||
|
|
|
|
|
|
замінити розпір- |
||||||
опорна або |
|
ності від d2 |
|
|
Не конструюють |
|||||||
|
|
|
ною втулкою |
|||||||||
під різьбу |
|
|
|
|
|
|
|
|
|
|
||
l5 |
|
l5 ≈ 0,4d5 |
|
|
|
|
|
|
l5 визначають |
|||
|
|
|
|
|
|
|
|
|||||
|
|
|
|
|
|
|
|
графічно |
||||
|
|
|
|
|
|
|
|
|
|
|
||
Примітка: 1. Значення висоти буртика t , орієнтовні величини фаски маточини f та коор- |
||||||||||||
динати фаски підшипника r визначають в залежності від діаметра ступені d: |
||||||||||||
t |
17…24 |
25…30 |
32…40 |
42…50 |
52…60 |
|
62…70 |
71…85 |
||||
2 |
2,2 |
2,5 |
|
|
2,8 |
3 |
|
3,3 |
3,5 |
|||
r |
1,6 |
2 |
2,5 |
|
|
3 |
3 |
|
3,5 |
3,5 |
||
f |
1 |
1 |
1,2 |
|
|
1,6 |
2 |
|
2 |
2,5 |
2.Діаметр d1 вихідного кінця швидкохідного вала, що з’єднюють з двигуном за допомогою муфти, визначають за формулою d1=(0,8…1,0)dдв, де dдв, - діаметр вихідного кінця вала двигуна.
3.Діаметри d2 та d4 під підшипник заокруглити до найближчого значення внутрішнього кільця підшипника.
4.Значення діаметрів (крім d2 та d4 під підшипник) заокруглити до найближчого значення із стандартного ряду (див. пояснення до формули (7.1)).
5.Довжини ділянок вала округлити до найближчого стандартного значення по ряду Ra
40:8; 8,5; 9; 9,5; 10; 10,5; 11; 11,5; 12; 13; 14; 15; 16; 17; 18; 19; 20; 21; 22; 24; 25; 26; 28; 30; 32; 34; 36; 38; 40; 42; 45; 48; 50; 53; 56; 60; 63; 67; 71; 75; 80; 85; 90; 95; 100; 105; 110; 120; 125; 130 дальше до 220 мм крок 10 мм.
6.При конструюванні валів розміри діаметрів та довжин ступенів уточнюються.
Визначення геометричних параметрів ступенів вала залежить від кількості та розмірів встановлюваних на вал деталей (див. рисунок 7.4). Проектний розрахунок ставить за мету визначити орієнтовно геометричні розміри кожної ступені вала: її діаметр d та довжину l (табл.7.3).
80
Розділ 7 |
Вали |
Вибір найбільш раціонального типу підшипника для даних умов роботи залежить від ряду факторів: типу передачі, співвідношення сил в зачепленні, частоти обертання внутрішнього кільця підшипника, терміну роботи, схеми встановлення. Попередній вибір підшипників для кожного із валів редуктора проводиться у наступному порядку:
1.У відповідності з таблицею 7.4 визначити тип і схему встановлення підшипника.
2.Вибрати типорозмір підшипників за величиною діаметра d внутріш-
нього кільця, рівного діаметру другої d2 та четвертої d4 ступенів вала під підшипники.
3.Виписати основні параметри підшипників: геометричні розміри – d,
D, B (T, c); динамічну Cr та статичну Co вантажності. Тут D – діаметр зовнішнього кільця підшипника; B – ширина кулькових підшипників; Т і с – осьові розміри роликопідшипників.
Таблиця 7.4 – Попередній вибір підшипників
Передача |
Вал |
Тип підшипника |
Схема вста- |
|
новлення |
||||
|
|
|
||
|
Шв |
При Fa/Rr≤0,25 – радіальні кулькові однорядні; |
З однією |
|
|
фіксуючою |
|||
Циліндрична |
|
при Fa/R r> 0,25 - радіально – упорні кулькові; |
опорою |
|
|
|
|||
|
При Fa/Rr≤0,25 – радіальні кулькові однорядні; |
|
||
косозуба |
Тих |
Врозпір |
||
|
при Fa/R r> 0,25 - радіально – упорні кулькові |
|||
|
|
типу 46000; роликові конічні типу 7000 |
|
|
|
|
|
|
|
|
|
Роликові конічні типу 7000 або 27000, при |
Врозпір |
|
|
|
п1<1500 об/хв |
||
|
Шв |
або |
||
Конічна |
|
Радіально - упорні кулькові типу 46000 при |
врозтяж |
|
|
|
п1≥1500 об/хв |
||
|
|
|
||
|
Тих |
Роликові конічні типу 7000 |
В розпір |
|
|
|
Радіально – упорні кулькові типу 46000; |
Врозпір або |
|
|
|
з однією |
||
|
|
роликові конічні типу 27000; |
||
|
|
фіксуючою |
||
|
|
радіальні кулькові однорядні при аw>160 мм |
||
Черв’ячна |
Шв |
опорою |
||
|
||||
|
Конічні – роликові типу 7000 або |
|
||
|
|
радіально – упорні кулькові типу 36000 |
В розпір |
|
|
|
при аw≤160 мм |
||
|
|
|
||
|
Тих |
Роликові конічні типу 7000 |
|
7.3 Перевірний розрахунок валів
Перевірний розрахунок валів на міцність виконують на спільну дію згину та кручення. При цьому розрахунок відображує різновидність циклу напружень згину та кручення, втомні характеристики матеріалів, розміри, форму, та стан поверхонь валів. Перевірний розрахунок проводять після закінчення конструктивної компоновки та встановлення основних розмірів валів (діаметрів і довжин ділянок валів, відстані між серединами опор та ін.)
Мета розрахунку – визначити коефіцієнти запасу міцності в небезпечних перерізах вала. Небезпечний переріз вала визначається наявністю джерела концентрації напружень і дії згинаючого та крутного моментів. Джере-
81
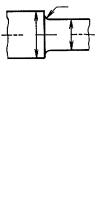
Розділ 7 |
Вали |
лами концентрації напружень можуть бути: посадка підшипника (колеса) з натягом; ступінчастий перехід між різними діаметрами; наявність шпонкового паза (шліців); наявність різьби.
Коефіцієнти запасу міцності визначається за формулою
S = |
Sσ Sτ |
, |
(7.2) |
Sσ2 + Sτ2
Розрахункове значення S повинно бути не менше від допустимого Sadm =2,0…2,5. При умові виконання спеціального розрахунку вала на жор-
сткість допускається зниження Sadm |
до 1,7. |
|
|
|
|
|
|
|
||||||||||||
Таблиця 7.5 - Значення коефіцієнтів kσ та kτ для валів з галтелями |
|
|||||||||||||||||||
|
|
|
|
|
|
|
|
|
|
|
r |
|
|
|
|
|
|
|
|
|
|
|
|
|
|
|
|
D |
|
d |
|
|
|
|
|
|
|
|
|
||
|
|
|
|
|
|
|
|
|
|
|
|
|
|
|
|
|
|
|||
D/d |
|
r/d |
|
|
|
|
|
|
|
Вали із сталі, що має σв, МПа |
|
|
|
|||||||
|
600 |
|
700 |
|
|
|
800 |
|
900 |
600 |
700 |
|
800 |
900 |
||||||
|
|
|
|
|
|
|
k |
σ |
|
|
|
|
|
k |
τ |
|
||||
|
|
0,02 |
1,96 |
|
2,08 |
|
2,20 |
|
2,35 |
1,30 |
1,35 |
|
1,41 |
1,45 |
||||||
|
|
0,04 |
1,66 |
|
1,69 |
|
1,75 |
|
1,81 |
1,20 |
1,24 |
|
1,27 |
1,29 |
||||||
До 1,1 |
|
0,06 |
1,51 |
|
1,52 |
|
1,54 |
|
1,57 |
1,16 |
1,18 |
|
1,20 |
1,23 |
||||||
|
0,08 |
1,40 |
|
1,41 |
|
1,42 |
|
1,44 |
1,12 |
1,14 |
|
1,16 |
1,18 |
|||||||
|
|
0,10 |
1,34 |
|
1,36 |
|
1,37 |
|
1,38 |
1,09 |
1,11 |
|
1,13 |
1,15 |
||||||
|
|
0,15 |
1,25 |
|
1,26 |
|
1,27 |
|
1,29 |
1,06 |
1,07 |
|
1,08 |
1,09 |
||||||
|
|
0,20 |
1,19 |
|
1,21 |
|
1,22 |
|
1,23 |
1,04 |
1,05 |
|
1,06 |
1,07 |
||||||
|
|
0,02 |
2,34 |
|
2,51 |
|
2,68 |
|
2,89 |
1,50 |
1,59 |
|
1,67 |
1,74 |
||||||
|
|
0,04 |
1,92 |
|
1,97 |
|
2,05 |
|
2,13 |
1,33 |
1,39 |
|
1,45 |
1,48 |
||||||
Більше1,1 |
|
0,06 |
1,71 |
|
1,74 |
|
1,76 |
|
1,80 |
1,26 |
1,30 |
|
1,33 |
1,37 |
||||||
|
0,08 |
1,56 |
|
1,58 |
|
1,59 |
|
1,62 |
1,18 |
1,22 |
|
1,26 |
1,30 |
|||||||
до 1,2 |
|
|
|
|
|
|||||||||||||||
|
0,10 |
1,48 |
|
1,50 |
|
1,51 |
|
1,53 |
1,16 |
1,19 |
|
1,21 |
1,24 |
|||||||
|
|
|
|
|
|
|||||||||||||||
|
|
0,15 |
1,35 |
|
1,37 |
|
1,38 |
|
1,40 |
1,10 |
1,11 |
|
1,14 |
1,16 |
||||||
|
|
0,20 |
1,27 |
|
1,29 |
|
1,30 |
|
1,32 |
1,06 |
1,08 |
|
1,10 |
1,13 |
||||||
|
|
0,02 |
2,40 |
|
2,60 |
|
2,80 |
|
3,00 |
1,70 |
1,80 |
|
1,90 |
2,00 |
||||||
|
|
0,04 |
2,00 |
|
2,10 |
|
2,15 |
|
2,25 |
1,46 |
1,53 |
|
1,60 |
1,65 |
||||||
Більше 1,2 |
|
0,06 |
1,85 |
|
1,88 |
|
1,90 |
|
1,96 |
1,35 |
1,40 |
|
1,45 |
1,50 |
||||||
|
0,08 |
1,66 |
|
1,68 |
|
1,70 |
|
1,73 |
1,25 |
1,30 |
|
1,35 |
1,40 |
|||||||
до 2 |
|
|
|
|
|
|||||||||||||||
|
0,10 |
1,57 |
|
1,59 |
|
1,61 |
|
1,63 |
1,21 |
1,25 |
|
1,28 |
1,32 |
|||||||
|
|
|
|
|
|
|||||||||||||||
|
|
0,15 |
1,41 |
|
1,43 |
|
1,45 |
|
1,47 |
1,12 |
1,15 |
|
1,18 |
1,20 |
||||||
|
|
0,20 |
1,32 |
|
1,34 |
|
1,36 |
|
1,38 |
1,07 |
1,10 |
|
1,14 |
1,16 |
||||||
У формулі (7.2) Sσ - коефіцієнт запасу міцності за нормальними на- |
||||||||||||||||||||
пруженнями |
|
|
|
|
|
|
|
σ−1 |
|
|
|
|
|
|
|
|
|
|||
|
|
|
Sσ |
= |
|
|
|
|
|
|
|
, |
|
|
|
|
(7.3) |
|||
|
|
|
|
kσ |
|
|
σ |
|
+ψ |
|
σ |
|
|
|
|
|
||||
|
|
|
|
|
|
|
|
υ |
σ |
m |
|
|
|
|
|
|||||
|
|
|
|
|
|
|
|
|
|
|
|
|
|
|||||||
|
|
|
|
|
|
kF kd |
|
|
|
|
|
|
|
|||||||
|
|
|
|
|
|
|
|
|
|
|
|
|
|
|
|
|
де σ-1 – границя витривалості сталі при симетричному циклі згину; для вуг-
82
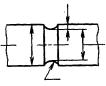
Розділ 7 |
Вали |
лецевих конструкційних сталей σ-1 0,45σВ; kσ - ефективний коефіцієнт концентрації нормальних напружень (табл.7.5…7.10); kd - масштабний фактор для нормальних напружень (табл.7.11); kF - коефіцієнт стану поверхні, що залежить від факторів, які характеризують стан поверхні: наявність корозійних пошкоджень, шорсткість поверхні, поверхневе зміцнення механічною,
термічною, хіміко-термічною обробкою, і визначається за табл.7.12; σа - амплітуда циклу нормальних напружень, яка рівна найбільшому напруженню
згину в розглядуваному перерізі; σm – середнє напруження циклу нормальних напружень;
Таблиця 7.6 - Значення коефіцієнтів kσ та kτ для валів з виточками
|
|
|
|
|
|
|
|
|
|
|
|
|
|
|
|
|
|
|
|
|
|
|
|
|
|
|
|
|
|
|
|
|
|
t |
|
|
|
|
|
|
|
||||
|
|
|
|
|
|
|
|
D |
|
|
|
d |
|
|
|
|
|
|
|
|||
|
|
|
|
|
|
|
|
|
|
|
r |
|
|
|
|
|
|
|
|
|
|
|
|
|
|
|
|
|
|
|
|
|
|
|
|
|
|
|
|
|
|
|
|||
t/r |
|
r/d |
kσ для валів із сталі, |
|
|
|
D/d |
|
r/d |
kτ для валів із сталі, |
||||||||||||
|
|
для яких σв, МПа |
|
|
|
|
|
для яких σв, МПа |
|
|||||||||||||
|
|
|
≤600 |
|
700 |
800 |
|
900 |
|
|
|
|
|
|
|
|
≤600 |
|
700 |
800 |
|
900 |
|
|
0,02 |
1,85 |
|
1,95 |
2,10 |
|
2,25 |
|
|
|
|
|
|
0,02 |
1,29 |
|
1,32 |
1,39 |
|
1,46 |
|
До |
|
0,04 |
1,80 |
|
1,85 |
2,00 |
|
2,10 |
|
|
|
До |
|
0,04 |
1,27 |
|
1,30 |
1,37 |
|
1,43 |
||
|
0,06 |
1,75 |
|
1,80 |
1,90 |
|
1,95 |
|
|
|
|
0,06 |
1,25 |
|
1,29 |
1,36 |
|
1,41 |
||||
1,1 |
|
0,08 |
1,70 |
|
1,75 |
1,80 |
|
1,90 |
|
|
|
1,1 |
|
|
0,08 |
1,21 |
|
1,25 |
1,32 |
|
1,39 |
|
|
|
0,10 |
1,65 |
|
1,70 |
1,75 |
|
1,80 |
|
|
|
|
|
|
0,10 |
1,18 |
|
1,21 |
1,29 |
|
1,32 |
|
|
|
0,15 |
1,55 |
|
1,57 |
1,60 |
|
1,65 |
|
|
|
|
|
|
0,15 |
1,14 |
|
1,18 |
1,21 |
|
1,25 |
|
Бі- |
|
0,02 |
1,89 |
|
1,99 |
2,15 |
|
2,31 |
|
|
|
Бі- |
|
0,02 |
1,37 |
|
1,41 |
1,50 |
|
1,69 |
||
льше |
|
0,04 |
1,84 |
|
1,89 |
2,05 |
|
2,15 |
|
|
|
льше |
|
0,04 |
1,35 |
|
1,37 |
1,47 |
|
1,62 |
||
1,0 |
|
0,06 |
1,78 |
|
1,84 |
1,94 |
|
1,99 |
|
|
|
1,0 |
|
|
0,06 |
1,32 |
|
1,36 |
1,46 |
|
1,52 |
|
|
0,08 |
1,73 |
|
1,78 |
1,84 |
|
1,94 |
|
|
|
|
|
0,08 |
1,27 |
|
1,32 |
1,41 |
|
1,50 |
|||
до |
|
|
|
|
|
|
до |
|
|
|
||||||||||||
|
0,10 |
1,68 |
|
1,73 |
1,78 |
|
1,84 |
|
|
|
|
0,10 |
1,23 |
|
1,27 |
1,37 |
|
1,41 |
||||
1,5 |
|
|
|
|
|
|
1,5 |
|
|
|
|
|||||||||||
|
0,15 |
1,58 |
|
1,60 |
1,63 |
|
1,68 |
|
|
|
|
|
0,15 |
1,18 |
|
1,23 |
1,27 |
|
1,37 |
|||
|
|
|
|
|
|
|
|
|
|
|
|
|||||||||||
Бі- |
|
0,02 |
1,93 |
|
2,04 |
2,20 |
|
2,37 |
|
|
|
Бі- |
|
0,02 |
1,40 |
|
1,45 |
1,55 |
|
1,65 |
||
льше |
|
0,04 |
1,87 |
|
1,93 |
2,09 |
|
2,20 |
|
|
|
льше |
|
0,04 |
1,38 |
|
1,42 |
1,52 |
|
1,60 |
||
1,5 |
|
0,06 |
1,82 |
|
1,87 |
1,98 |
|
2,04 |
|
|
|
1,5 |
|
|
0,06 |
1,35 |
|
1,40 |
1,50 |
|
1,57 |
|
|
0,08 |
1,76 |
|
1,82 |
1,87 |
|
1,98 |
|
|
|
|
|
0,08 |
1,30 |
|
1,35 |
1,45 |
|
1,55 |
|||
до |
|
|
|
|
|
|
до |
|
|
|
||||||||||||
|
0,10 |
1,71 |
|
1,76 |
1,82 |
|
1,87 |
|
|
|
|
0,10 |
1,25 |
|
1,30 |
1,40 |
|
1,45 |
||||
2,0 |
|
|
|
|
|
|
2,0 |
|
|
|
|
|||||||||||
|
0,15 |
1,60 |
|
1,62 |
1,66 |
|
1,71 |
|
|
|
|
|
0,15 |
1,20 |
|
1,25 |
1,30 |
|
1,35 |
|||
|
|
|
|
|
|
|
|
|
|
|
|
|||||||||||
|
Напруження згину змінюються за симетричним циклом і амплітуда |
|||||||||||||||||||||
цих напружень, для досліджуваного перерізу |
|
|
|
|
|
|
|
|||||||||||||||
|
|
|
|
|
|
σa |
= σ зг |
= |
|
M max |
. |
|
|
|
|
|
|
(7.4) |
||||
|
|
|
|
|
|
|
|
|
|
|
|
|
|
|||||||||
|
Середнє напруження циклу σm |
W |
|
|
|
|
|
|
|
|||||||||||||
|
(статична складова нормальних на- |
|||||||||||||||||||||
пружень) визначається осьовими силами |
|
|
|
|
|
|
|
|||||||||||||||
|
|
|
|
|
|
|
σm = |
|
Fa |
, |
|
|
|
|
|
|
|
|
(7.5) |
|||
|
|
|
|
|
|
|
|
А |
|
|
|
|
|
|
|
|
||||||
|
|
|
|
|
|
|
|
|
|
|
|
|
|
|
|
|
|
|
|
83
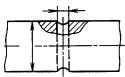
Розділ 7 |
Вали |
в іншому випадку якщо осьове навантаження Fa на вал відсутнє або порів-
няно мале, то приймають σm = 0.
Коефіцієнт, що характеризують чутливість матеріалу вала до асиметрії циклу, можна брати для сталевих валів
ψσ = 0,02 + 0,0002σ B .
Коефіцієнт запасу міцності за дотичними напруженнями:
Sτ |
= |
|
|
τ−1 |
|
|
|
(7.5) |
||
|
kτ |
τ |
|
+ψ |
|
τ |
|
|||
|
|
|
a |
τ |
m |
|||||
|
|
|
|
|||||||
|
|
|
kF kd |
|
|
|||||
|
|
|
|
|
|
|
|
|
де τ-1 – границя витривалості сталі при симетричному циклі кручення, для
конструкційних сталей приймають τ-1 0,25σВ.
Інші позначення у формулі (7.5) мають такий же зміст як і в формулі (7.3) з тою різницею, що вони відносяться до напружень кручення. Значення
kd задані в табл. 7.11, а kτ - в табл.7.5…7.10. Для згаданих вище сталей приймають ψτ = 0,5ψσ ;
Таблиця 7.7 - Значення коефіцієнтів kσ та kτ |
|
для валів з радіальними |
|
||||||||||||||||
|
|
|
|
|
отворами |
|
|
|
|
|
|
|
|
|
|
|
|
|
|
|
|
|
|
|
a |
|
|
|
|
|
|
|
|
|
|
|
|
|
|
|
|
|
|
|
d |
|
|
|
|
|
|
|
|
|
|
|
|
|
|
|
|
|
|
|
|
|
|
|
|
|
|
|
|
|
|
|
|
|
|
a/d |
|
|
|
|
kσ |
|
|
|
|
|
|
|
|
|
|
kτ |
|
||
|
|
|
Для валів із сталей, |
які мають σВ, МПа |
|
||||||||||||||
|
|
|
≤700 |
|
800 |
|
900 |
|
|
|
|
≤700 |
|
800 |
|
900 |
|||
Більше 0,05 до 0,15 |
|
|
2,0 |
|
2,02 |
|
2,12 |
|
|
|
|
1,75 |
|
1,83 |
|
1,90 |
|||
Більше 0,15 до 0,25 |
|
|
1,8 |
|
1,82 |
|
1,9 |
|
|
|
|
|
|
||||||
|
|
|
|
|
|
|
|
|
|
|
|
|
|
||||||
Примітка: Момент опору нетто: - при згині Wнетто |
|
|
πd 3 |
|
|
а |
|
|
|
||||||||||
= |
|
|
1 |
−1,54 |
|
|
; |
|
|||||||||||
32 |
|
d |
|
|
|||||||||||||||
|
πd 3 |
|
|
|
|
|
|
|
|
|
|
|
|
||||||
при крученні Wρ.нетто = |
|
а |
|
|
|
|
|
|
|
|
|
|
|
|
|
||||
16 |
1 − |
|
|
|
|
|
|
|
|
|
|
|
|
|
|
|
|||
|
|
|
|
|
|
|
|
|
|
|
|
|
|
||||||
|
|
d |
|
|
|
|
|
|
|
|
|
|
|
|
|
||||
|
|
|
|
|
|
|
|
|
|
|
|
||||||||
Амплітуду та середнє значення дотичних напружень, для валів, що |
|||||||||||||||||||
обертаються в один бік, визначають за пульсуючим циклом |
|
|
|
|
|||||||||||||||
|
|
|
τa =τm = 0,5τ = |
|
|
T |
|
, |
|
|
|
|
|
|
|
(7.6) |
|||
|
|
|
|
2Wρ |
|
|
|
|
|
|
|
||||||||
|
|
|
|
|
|
|
|
|
|
|
|
|
|
|
|
|
а для валів із змінним напрямком обертання, вказані напруження визначаються за симетричним циклом
84

Розділ 7 |
Вали |
τa =τ = |
T |
; τm = 0. |
(7.7) |
|
|||
|
Wρ |
|
У виразах для визначення амплітуд і середніх напружень осьовий W і полярний Wρ моменти опору поперечного перерізу, а також площу попереч-
ного перерізу А треба брати за фактичними розмірами перерізу.
Таблиця 7.8 - Значення коефіцієнтів kσ та kτ для валів з однією шпонковою канавкою
|
|
|
|
|
|
|
|
|
|
|
|
|
|
b |
|
|
|
|
|
|
|
|
|
|
|
|
|
|
|||
|
|
|
|
|
|
|
|
|
|
1 |
|
|
|
|
|
|
|
|
|
|
|
|
|
|
|
|
|
|
|
||
|
|
|
|
|
|
|
|
|
|
|
|
t |
|
|
|
|
|
|
|
|
|
|
|
|
|
|
|
|
|
|
|
|
|
|
|
|
|
|
|
|
|
|
|
|
|
|
d |
|
|
|
|
|
|
|
|
|
|
|
|
|
|
||
|
|
|
|
|
|
|
|
|
|
|
|
|
|
|
|
|
|
|
|
|
|
|
|
|
|
|
|||||
|
|
|
|
|
|
|
|
|
σВ, МПа |
|
|
|
|
|
|
|
|
Примітка: |
|
2 |
|
||||||||||
Коефіцієнти |
|
|
|
|
|
|
|
|
|
|
|
|
|
|
|
|
3 |
|
|
|
|
|
|||||||||
|
|
|
|
|
|
|
|
|
|
|
|
|
|
|
|
|
|
|
|
|
|
|
|
|
|
||||||
|
|
|
|
|
|
|
|
|
|
|
|
|
|
|
|
|
|
|
Wнетто = πd |
|
− |
bt1 (d −t1 ) |
|
||||||||
|
|
|
|
|
600 |
|
700 |
|
800 |
|
|
900 |
|
|
|||||||||||||||||
|
|
|
|
|
|
|
|
|
|
|
|||||||||||||||||||||
|
|
|
|
|
|
|
|
|
|
|
|
|
|
|
|
|
|
|
|
|
|
|
32 |
|
|
|
2d |
|
|
||
|
kσ |
|
1,6 |
|
1,75 |
|
1,80 |
|
|
1,90 |
|
|
|
|
|
|
|
; |
|
|
|
(d − t |
)2 |
|
|||||||
|
|
|
|
|
|
|
|
|
|
|
|
|
|
|
|
|
|
|
|
|
|
|
πd 3 |
|
bt |
1 |
|
||||
|
|
|
|
|
|
|
|
|
|
|
|
|
|
|
|
|
|
|
|
|
|
|
|
|
|||||||
|
kτ |
|
1,5 |
|
1,6 |
|
1,7 |
|
|
1,90 |
|
Wρ.нетто = |
|
16 |
− |
|
1 |
|
|||||||||||||
|
|
|
|
|
|
|
|
|
|
|
|||||||||||||||||||||
|
|
|
|
|
|
|
|
|
|
|
|
|
|
|
|
|
|
|
|
|
|
|
|
|
|
|
2d |
|
|
||
Таблиця 7.9 - Значення коефіцієнтів kσ |
та kτ для шліцьових ділянок вала |
|
|
||||||||||||||||||||||||||||
|
|
Шліци |
|
|
|
|
|
|
|
|
|
|
|
|
|
σВ, МПа |
|
|
|
|
|
|
|
|
|
||||||
|
|
|
|
|
|
|
600 |
|
700 |
|
|
|
800 |
|
|
|
|
|
900 |
|
|
||||||||||
|
|
|
|
|
|
|
|
|
|
|
|
|
|
|
|
|
|
|
|
||||||||||||
Прямі |
|
|
kσ |
|
|
|
|
1,55 |
|
1,60 |
|
|
|
1,65 |
|
|
|
|
|
1,70 |
|
|
|||||||||
|
|
kτ |
|
|
|
|
2,35 |
|
2,45 |
|
|
|
2,55 |
|
|
|
|
|
2,65 |
|
|
||||||||||
|
|
|
|
|
|
|
|
|
|
|
|
|
|
|
|
|
|
|
|||||||||||||
Евольвентні |
|
|
kσ |
|
|
|
|
1,55 |
|
1,60 |
|
|
|
1,65 |
|
|
|
|
|
1,70 |
|
|
|||||||||
|
|
kτ |
|
|
|
|
1,46 |
|
1,49 |
|
|
|
1,52 |
|
|
|
|
|
1,55 |
|
|
||||||||||
|
|
|
|
|
|
|
|
|
|
|
|
|
|
|
|
|
|
|
|||||||||||||
Таблиця 7.10 - Значення kσ/kd |
для валів із напресованими деталями при |
|
|
||||||||||||||||||||||||||||
|
|
|
|
|
|
тиску запресовування більше 20 МПа |
|
|
|
|
|
|
|
|
|||||||||||||||||
d, мм |
|
|
|
|
σВ, МПа |
|
|
|
|
|
|
|
|
|
|
|
|
Примітка |
|
|
|
|
|
|
|||||||
|
600 |
|
|
700 |
|
|
800 |
|
|
900 |
|
|
|
|
|
|
|
|
|
|
|
|
|
|
|
||||||
|
|
|
|
|
|
|
|
|
|
|
|
|
|
|
|
|
|
|
|
|
|
|
|
|
|||||||
14 |
|
2,0 |
|
|
2,3 |
|
|
2,6 |
|
|
3,0 |
|
|
1.Для дотичних напружень |
|
|
|
|
|||||||||||||
22 |
|
2,35 |
|
2,6 |
|
|
3,0 |
|
|
3,4 |
|
|
|
kτ |
= 0,6 |
kσ |
+ 0,4 |
|
|
|
|
|
|
|
|
|
|||||
30 |
|
2,6 |
|
|
2,8 |
|
|
3,3 |
|
|
3,8 |
|
|
|
|
|
|
|
|
|
|
|
|||||||||
|
|
|
|
|
|
|
|
kd |
|
|
kd |
|
|
|
|
|
|
|
|
|
|||||||||||
40 |
|
2,7 |
|
|
3,2 |
|
|
3,65 |
|
|
4,0 |
|
|
|
|
|
|
|
|
|
|
|
|
||||||||
|
|
|
|
|
|
|
2.Якщо тиск запресовування 10…20МПа |
||||||||||||||||||||||||
50 |
|
3,3 |
|
|
3,6 |
|
|
4,0 |
|
|
4,5 |
|
|
значення kσ/kd зменшити на 5…15% |
|
|
85
Розділ 7 |
Вали |
Таблиця 7.11 – Значення kd
Матеріал вала |
|
|
|
|
|
|
|
Діаметр вала d, мм |
|
|
|
|||||
|
20 |
|
30 |
|
40 |
|
50 |
70 |
|
100 |
200 |
|||||
|
|
|
|
|
|
|||||||||||
Вуглецева сталь σВ=400…500 МПа |
0,92 |
|
0,88 |
|
0,85 |
|
0,82 |
0,76 |
|
0,70 |
0,63 |
|||||
|
|
|
|
|
|
|
|
|
|
|
|
|
|
|
|
|
Вуглецева сталь σВ=500…600 МПа |
0,89 |
|
0,85 |
|
0,81 |
|
0,78 |
0,73 |
|
0,68 |
0,61 |
|||||
|
|
|
|
|
|
|
|
|
|
|
|
|
|
|
|
|
Легована сталь σВ=800…1200 МПа |
0,86 |
|
0,81 |
|
0,77 |
|
0,74 |
0,69 |
|
0,65 |
0,59 |
|||||
|
|
|
|
|
|
|
|
|
|
|
|
|
|
|
|
|
Таблиця 7.12 – Значення коефіцієнта kF |
|
|
|
|
|
|
|
|
|
|
|
|
||||
Вид обробки |
|
|
Границя міцності,σB , МПа |
|
|
|
||||||||||
поверхні |
|
|
|
|
|
|
|
|
|
|
|
|
|
|
|
|
400 |
|
600 |
|
|
800 |
|
1000 |
|
1200 |
|
1400 |
|||||
|
|
|
|
|
|
|
||||||||||
Полірування |
1,0 |
|
1,0 |
|
|
1,0 |
|
1,0 |
|
1,0 |
|
|
1,0 |
|||
Шліфування |
0,97 |
|
0,95 |
|
|
0,93 |
|
0,90 |
|
0,87 |
|
0,85 |
||||
Тонке точіння |
0,94 |
|
0,90 |
|
|
0,86 |
|
0,80 |
|
0,75 |
|
0,70 |
||||
Грубе точіння |
0,90 |
|
0,84 |
|
|
0,78 |
|
0,72 |
|
0,65 |
|
0,60 |
Якщо в розглядуваному перерізі є декілька концентраторів напружень, то враховують той для якого відношення kσ kτ більше.
7.4 Конструювання валів
Для редукторів загального призначення рекомендують виконувати прості за конструкцією гладкі вали однакового номінального діаметра по всій довжині. Для забезпечення необхідних посадок деталей відповідні ділянки вала повинні мати передбачені відхилення. Але, якщо місця посадок віддалені від кінця вала, то встановлення деталей утруднюється. Тому для спрощення складання та демонтажу вузла вала, заміни підшипників та інших монтованих деталей, вали виконують ступінчастими. Приклад такої конструкції показано на рис.7.5. На ділянках вала, що призначені для нерухомих посадок деталей, вказують відхилення розмірів вала типу s6, u7, r6 та n6 із скосами для полегшення монтажу. Розміри скосів і фасок,(місця I та II), в залежності від діаметра прилягаючої ділянки вала, наведені в табл.7.13.
Таблиця 7.13 – Розміри фасок і скосів на валах
Позначення скосів |
|
Діаметр вала, d, мм |
|
||
і фасок |
|
|
|
|
|
15…30 |
30…45 |
45…70 |
70…100 |
100…150 |
|
с, мм |
1,5 |
2,5 |
2,5 |
3,0 |
4,0 |
а, мм |
2 |
3 |
5 |
5 |
8 |
α, град. |
30 |
30 |
30 |
30 |
10 |
Для щільного прилягання торців деталей до виступів вала в місці переходу III роблять галтелі радіусом r в залежності від діаметра d1 (табл.7.14)
В місцях переходу від d до D, якщо деталі в цьому місці не встанов-
люють, передбачають галтелі з радіусом заокруглення R≈0,4(D-d).
Правий кінець вала довжиною l однакового номінального діаметра
86
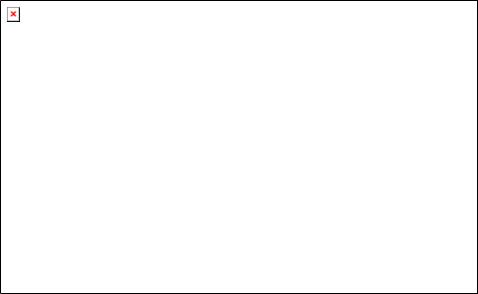
Розділ 7 |
Вали |
d2=d3 має на ділянці довжиною l1 відхилення k6 для посадки муфти або шківа. Ділянка що розміщена правіше, на якій не встановлюється деталь, виконується з відхиленням h11. Це дозволяє зменшити кількість ступенів вала.
Таблиця 7.14 – Розміри галтелі залежно від діаметра вала
Позначення галтелі |
|
Діаметр вала, d1, мм |
|
||
і фаски |
15…30 |
30…45 |
45…70 |
70…100 |
100…150 |
r, мм |
1,0 |
1,0 |
1,5 |
2,0 |
2,5 |
с, мм |
1,5 |
2,0 |
2,5 |
3,0 |
4,0 |
II
d2 k6
I
III |
|
r |
l |
|
l1 |
||
|
|
|
|
D |
2 |
|
h11 |
d |
|
d |
|
|
|
|
3 |
r6 |
|
r6 |
1 |
|
1 |
d |
|
d |
I |
II |
III |
a |
c×450 |
r |
|
|
|
|
D c |
|
α |
|
1 |
|
|
d |
|
Рисунок 7.5 – Конструкція вала редуктора |
|
a
I
Конструкція ступенів вала залежить від типу і розмірів встановлених на них деталей (зубчастих і черв’ячних коліс, підшипників, муфт, зірочок, шківів) і способу закріплення цих деталей в діаметральному і осьовому напрямках (див. рис.10.56….10.73). При розбиранні конструкції вала враховують технологію складання і розбирання передач, механічну обробку, втомну міцність і розхід матеріалу при виготовленні. Діаметральне закріплення коліс, елементів відкритих передач, муфт і підшипників здійснюється посадками, шпонковими з’єднаннями і з’єднанням з натягом.
Нижче розглядаються рекомендації з конструювання посадочних поверхонь ступенів валів, з’єднаних між собою перехідними ділянками
(рис.7.6…7.10).
Вихідний кінець вала може бути конічним або циліндричним (рис.7.6). Посадка на конус має ряд переваг: легко збираються і знімаються деталі , висока точність базування, можливість створити будь-який натяг. У редукторах рівнозначно застосовують циліндричні і конічні кінці. Діаметр вихідного кінця d1 визначають із умови міцності вала на кручення.
Якщо вал з’єднується з двигуном через муфту, то діаметр d1 немає відрізнятись від діаметра вала двигуна більше ніж на 20%. При виконанні цієї
87
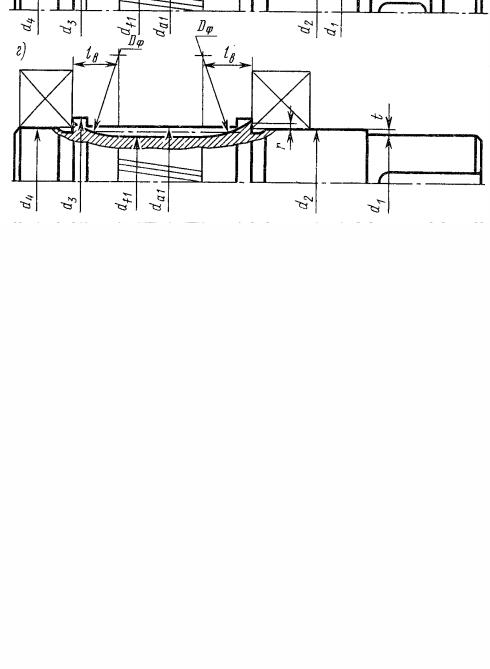
Розділ 7 |
Вали |
а)
б)
в)
г)
Рисунок 7.6 – Конструкція вала – шестірні циліндричної:
а) - df1>d3; б) - df1<d3; в) – dа1=d3; г) - dа1<d3 ;
88
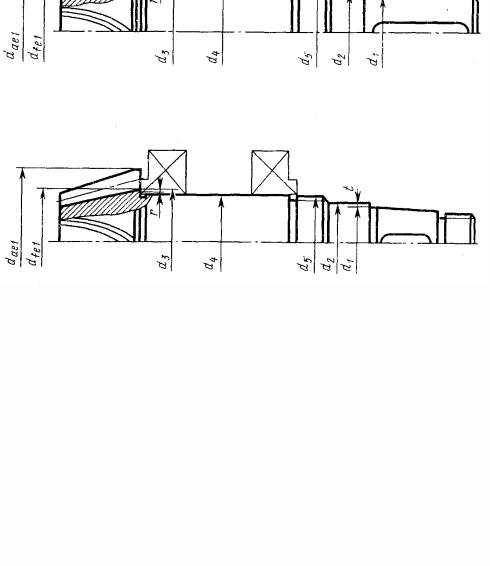
Розділ 7 |
Вали |
а)
б)
в)
Рисунок 7.7 – Конструкція вала – шестірні конічної:
а) - dfe1>d3; б) - dfe1<d3; в) – dfe1=d3;
89
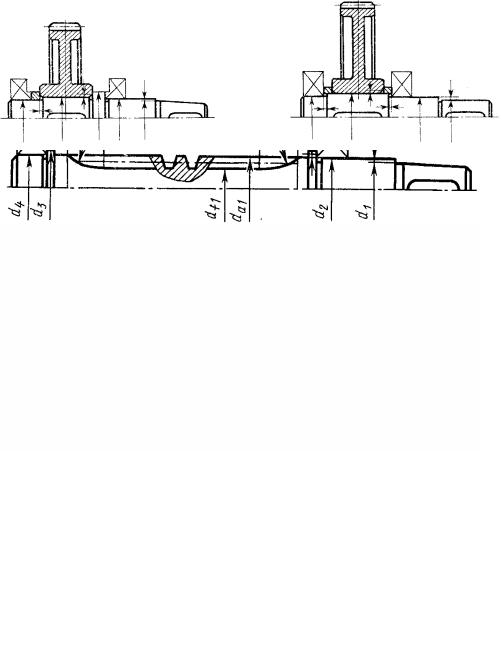
Розділ 7 |
Вали |
а)
б)
в)
Рисунок 7.8 – Конструкція черв’ячного вала:
а) - df1>d3; б) - df1=d3; в) – dа1<d3; df1<d3.
|
|
|
|
а) |
|
|
|
|
б) |
|
c |
|
|
t |
|
|
|
c |
t |
|
f |
|
|
|
|
f |
|
||
4 |
3 |
5 |
2 |
1 |
4 |
3 |
|
2 |
1 |
d |
d |
d |
d |
d |
d |
d |
|
d |
d |
|
|
|
|
|
|
|
|
|
|
Рисунок 7.9 – Конструкція тихохідного вала:
а) – з 5 – ю ділянкою (розпірна втулка на 4 – й ступені) ; б) – без 5 – ї ділянки.
90
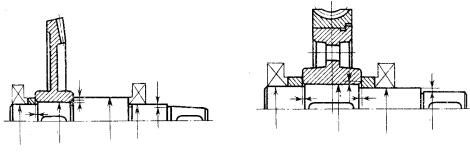
Розділ 7 |
Вали |
|
|
|
а) |
|
|
|
|
б |
) |
|
f |
|
|
|
|
|
|
t |
|
|
|
|
t |
|
f |
c |
|
|
|
|
c |
|
|
|
4 |
3 |
2 |
1 |
|
4 |
3 |
5 |
2 |
1 |
|
||||
d |
d |
d |
d d |
d |
d |
d |
d |
|
|
|
|
|
|
|
|
|
|
|
|
Рисунок 7.10 – Конструкція тихохідного вала:
а– з 5 – ю ділянкою (розпірна втулка на 4 – й ступені) ;
б– без 5–ї ділянки (розпірні втулки на 2-й й 3-й ділянках).
умови з’єднання валів можна забезпечити стандартною муфтою.
Для полегшення встановлення деталі на вихідний кінець вала на його торці передбачають фаску.
Діаметр другої ступені d2 відповідає діаметру внутрішнього кільця підшипника (див. табл.7.3). А довжина залежить від осьових розмірів деталей, які входять в комплект підшипникового вузла.
Діаметр третьої ділянки вала визначається за рекомендаціями наведеними у табл.7.3. Довжина ділянки може бути більшою за довжину маточини колеса, і тоді для фіксації колеса використовують втулки (рис.7.9,б, рис.7.10,б). Рівноцінним є варіант з використанням однієї втулки і бурта (п’ята ділянка) (рис.7.9, а і рис.7.10, а).
Конструкція 3-ї ділянки вала-шестірні циліндричної передачі і валачерв’яка залежить від величини передаточного числа u передачі і міжосьової
відстані aw . При невеликому u і відносно великому aw отримаємо d3<df1 (рис.7.6,а, рис.7.8,а); при великому u і відносно малому aw буде d3>df1, і то-
ді конструкцію третьої ділянки вала оформляють як показано на одному із варіантів рис.7.6 і рис.7.8. У випадку коли зовнішній діаметр шестірні (черв’яка) виявиться меншим за d3, третю ділянку вала обточують під діаметр dа1. При цьому необхідно передбачити місце для виходу фрези, навіть якщо це буде упорний буртик для підшипника.
У конічній передачі при великому передаточному числі u (u>3,15) шестірня виходить малих розмірів, і тоді d3>dfе1. У таких випадках не вдається забезпечити упорний буртик і його конструюють аналогічно рис.7.7,в.
Четверта ділянка вала, під підшипником, по діаметру відповідає другій ділянці, а її довжина залежить від осьових розмірів деталей підшипникового вузла із сторони глухої кришки.
Для швидкохідного вала конічного редуктора (рис.7.7) на четвертій ділянці встановлюються обидва підшипники. Довжина ділянки визначається геометрично ескізною компоновкою.
П’ята ділянка на тихохідних валах запобігає осьовому зміщенню колеса (рис.7.9, а і рис.7.10, а). У черв’ячних і циліндричних редукторах часто
91
Розділ 7 |
Вали |
Робоче Креслення вала рис.7.11
92
Розділ 7 |
Вали |
замість п’ятої ділянки тихохідного вала встановлюють розпірні втулки
(рис.7.9, б і рис.7.10, б).
Приклад виконання робочого креслення ступінчастого вала приведено на рис.7.11.
7.5 Шпонкові та шліцьові з’єднання
Для з’єднання вала з деталями, що передають обертання, часто вико-
ристовують призматичні шпонки (табл.7.12) із сталі, яка має σВ≥600МПа, наприклад, із сталі 45, Ст 6.
Довжину шпонки призначають із стандартного ряду таким чином, щоб вона була меншою від довжини маточини (приблизно на 5…10 мм). Напруження зминання вузьких граней шпонки не повинно перевищувати допустимого, тобто повинна виконуватись умова
σ зм = |
F |
≤ σ змadm |
(7.8) |
|
|||
|
Aзм |
|
де F=2T/d; Т –крутний момент, Н мм; d – діаметр вала в місці встановлення
шпонки; площа зминання Азм=(h-t1)lр; lр – робоча довжина шпонки: для шпонки з плоскими торцями lр=l, для шпонки із заокругленими торцями lр=l-b; при сталевій маточині і спокійному навантаженні допустиме напру-
ження на зминання σ змadm ≤100МПа; при коливаннях навантаження це зна-
чення слід зменшити на 20…25%, при ударному навантаженні – на 40…50%; при встановленні на вал чавунних деталей приведені значення
σзмadm зменшують вдвічі.
Зврахуванням приведених вище значень F та Азм формулу (7.8) можна записати у наступному виді:
σ |
|
= |
|
|
2Т |
≤σ adm |
(7.9) |
|
dl |
|
(h −t ) |
||||
|
зм |
|
p |
зм |
|
||
|
|
|
|
1 |
|
|
Якщо при перевірці шпонки σзм виявиться значно меншим від σ змadm , то
можна вибрати шпонку меншого перерізу – як для вала попереднього діапазону діаметрів, але обов’язково перевірити її на зминання.
Якщо ж σзм виявиться більшим від σ змadm , то допускається встановлення
двох шпонок під кутом 1800 (передбачають, що кожна шпонка сприймає половину навантаження), однак раціонально перейти до шліцьового з’єднання.
Для відносно тонких валів (діаметром приблизно до 44 мм) допускається встановлення сегментних шпонок (табл.7.16).
З’єднання перевіряють на зминання
σ |
|
= |
|
|
2Т |
|
≤σ adm |
(7.10) |
|
dl |
(h −t ) |
||||||
|
зм |
|
зм |
|
||||
а шпонку – на зріз |
|
|
|
|
|
1 |
|
|
|
|
|
|
2Т |
|
|
|
|
|
τзр |
= |
|
≤τзмadm |
(7.11) |
|||
|
d l b |
|||||||
|
|
|
|
|
|
|
93
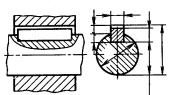
Розділ 7 |
Вали |
Значення σ змadm |
такі ж, як і для призматичних шпонок; τзмadm ≈0,6σ змadm . |
||||||||||
Таблиця 8.15 – Шпонки призматичні (ГОСТ 23360-78) |
|
||||||||||
|
|
|
|
|
|
|
|
|
|
|
|
|
|
|
|
2 |
b |
|
|
|
|
|
|
|
|
|
|
|
t |
|
|
|
|
|
|
|
|
|
|
|
d |
|
2 |
|
|
|
|
|
|
|
|
|
|
|
-t |
|
|
||
|
|
|
|
1 |
|
|
d |
|
|
||
|
|
|
|
|
t |
|
|
|
|
|
|
|
|
|
|
|
|
|
1 |
|
|
|
|
|
|
|
|
|
|
|
-t |
|
|
||
|
|
|
|
|
|
|
d |
|
|||
|
|
|
|
Розміри, мм |
|
|
|
|
|
||
Діаметр |
|
Переріз |
|
Глибина паза |
|
Фаска |
|||||
вала, d |
|
шпонки |
|
вала, t1 |
|
втулки, t2 |
|
s × 450 |
|||
|
|
b×h |
|
|
|
|
|
|
|
|
|
Більше 10 до 12 |
|
4×4 |
|
2,5 |
|
|
1,8 |
|
0,08-0,16 |
||
Більше 12 до 17 |
|
5×5 |
|
3,0 |
|
|
2,3 |
|
0,16-0,25 |
||
Більше 17 до 22 |
|
6×6 |
|
3,5 |
|
|
2,8 |
|
|||
Більше 22 до 30 |
|
8×7 |
|
4,0 |
|
|
3,3 |
|
|
||
Більше 30 до 38 |
|
10×8 |
|
5,0 |
|
|
3,3 |
|
|
||
Більше 38 до 44 |
|
12×8 |
|
5,0 |
|
|
3,3 |
|
0,25-0,40 |
||
Більше 44 до 50 |
|
14×9 |
|
5,5 |
|
|
3,8 |
|
|||
Більше 50 до 58 |
|
16×10 |
|
6,0 |
|
|
4,3 |
|
|
||
Більше 58 до 65 |
|
18×11 |
|
7,0 |
|
|
4,4 |
|
|
||
Більше 65 до 75 |
|
20×12 |
|
7,5 |
|
|
4,9 |
|
|
||
Більше 75 до 85 |
|
22×14 |
|
9,0 |
|
|
5,4 |
|
0,40-0,60 |
||
Більше 85 до 95 |
|
25×14 |
|
9,0 |
|
|
5,4 |
|
|||
|
|
|
|
|
|
||||||
Більше 95 до 110 |
|
28×16 |
|
10,0 |
|
|
6,4 |
|
|
||
Примітка: 1.Довжину шпонки вибирають із ряду: 6; 8; 10; 12; 14; 16; 18; 20; 25; 28; 32; 36; |
|||||||||||
40; 45; 50; 56; 63; 70; 80; 90; 100; 110; 125; 140; 160; 180; 200…(до 500). |
|
||||||||||
2. Матеріал шпонок – сталь з границею міцності не менше 590 МПа. |
|
||||||||||
3. Приклади умовного позначення шпонок виконання 1, переріз b×h=20×12, |
|
||||||||||
довжина 90 мм |
Шпонка 20×12×90 ГОСТ 23360 -78 |
|
|||||||||
Те ж, виконання 2 |
|
||||||||||
Шпонка 2 - 20×12×90 ГОСТ 23360 -78 |
|
||||||||||
|
|
|
|||||||||
|
|
|
|
|
|
|
|
|
|
|
|
94
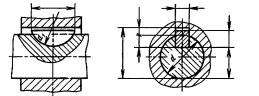
Розділ 7 |
Вали |
Таблиця 8.16 – Шпонки сегментні (ГОСТ 24071-80) |
|
|
Розміри, мм |
||||||
|
|
|
|
l |
b |
h |
|
|
|
|
|
|
|
2 |
|
|
|
|
|
|
|
|
|
d+t |
|
|
t |
|
|
|
|
|
|
|
|
|
1 |
|
|
|
|
|
|
|
|
|
d- |
|
|
|
|
|
|
|
|
|
|
|
|
Діаметр |
|
|
Розміри |
Глибина паза |
|
||||
вала d |
|
|
Фаска |
||||||
|
|
шпонки |
|
|
|
|
|||
Більше |
|
До |
|
вала t1 |
|
втулки t2 |
s × 450 |
||
|
|
b×h×l |
|
|
|||||
10 |
|
12 |
3×6,5×16 |
5,3 |
|
1,4 |
|
0,08-0,16 |
|
12 |
|
14 |
4×6,5×16 |
5,0 |
|
1,8 |
|
|
|
14 |
|
16 |
4×7,5×19 |
6,0 |
|
1,8 |
|
|
|
16 |
|
18 |
5×6,5×16 |
4,5 |
|
2,3 |
|
0,16-0,25 |
|
18 |
|
20 |
5×7×19 |
5,5 |
|
2,3 |
|
||
20 |
|
22 |
5×9×22 |
7,0 |
|
2,3 |
|
|
|
22 |
|
25 |
6×9×22 |
6,5 |
|
2,8 |
|
|
|
25 |
|
28 |
6×10×25 |
7,5 |
|
2,8 |
|
|
|
28 |
|
32 |
8×11×28 |
8,0 |
|
3,3 |
|
0,25-0,40 |
|
32 |
|
38 |
10×13×32 |
10,0 |
|
3,3 |
|
||
|
|
|
|
||||||
Примітка: |
1.Матеріал |
шпонок – сталь з границею міцності σВ ≥59 0МПа. |
|
||||||
2. В залежності від прийнятої бази обробки на робочому кресленні вказують розмір t1 для |
|||||||||
вала (віддають перевагу) d - t1, для втулки – розмір d + t2. |
|
|
|
Шліцьові з’єднання надійніші від шпонкових, особливо при змінних навантаженнях. В цих з’єднаннях досягається більш точне центрування деталей на валі, а розподіл навантаження між шліцами полегшує переміщення рухомих деталей вздовж вала.
В табл.7.17 наведені розміри прямобічних шліцьових з’єднань, а в табл.7.18 – розміри евольвентних шліцьових з’єднань.
Вибране з’єднання перевіряють на міцність проти зминання
σ зм ≈ |
Т |
≤ σ змadm . |
(7.12) |
|
0,75zAзмRср |
||||
|
|
|
Тут Т – крутний момент, Нмм; коефіцієнт 0,75 введений для врахування нерівномірності розподілу навантаження між шліцами; Rср=0,25(D+d); z – кількість шліців; Азм – розрахункова площа зминання, мм2.
D − d |
|
|
||
Азм= |
|
− 2 f l , |
(7.13) |
|
2 |
||||
|
|
|
||
де l – довжина маточини. |
|
|
|
95
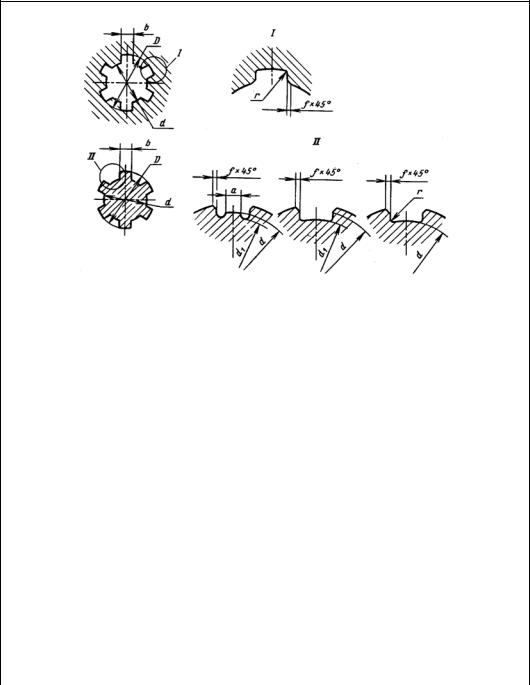
Розділ 7 |
Вали |
Таблиця 8.17 - З’єднання шліцьові прямобічні (ГОСТ 1139 – 80)
Виконання А Виконання В Виконання С
|
|
|
Розміри, мм |
|
|
|
||
Число |
d |
D |
b |
d1 |
a |
f |
r, не |
|
зубців z |
не менше |
більше |
||||||
|
|
|
|
|||||
1 |
2 |
3 |
4 |
5 |
6 |
7 |
8 |
|
|
|
|
Легка |
серія |
|
|
|
|
|
23 |
26 |
6 |
22,1 |
3,54 |
|
|
|
6 |
26 |
30 |
6 |
24,6 |
3,85 |
0,3 |
0,2 |
|
|
28 |
32 |
7 |
26,7 |
4,03 |
|
|
|
|
32 |
36 |
6 |
30,4 |
2,71 |
|
|
|
8 |
36 |
40 |
7 |
34,5 |
3,46 |
0,4 |
0,3 |
|
42 |
46 |
8 |
40,4 |
5,03 |
||||
|
|
|
||||||
|
46 |
50 |
9 |
44,6 |
5,75 |
|
|
|
|
52 |
58 |
10 |
49,7 |
4,89 |
|
|
|
|
56 |
62 |
10 |
53,6 |
6,38 |
|
|
|
8 |
62 |
68 |
12 |
59,8 |
7,31 |
0,5 |
0,5 |
|
72 |
78 |
12 |
69,6 |
8,45 |
||||
|
|
|
||||||
|
82 |
88 |
12 |
79,3 |
8,62 |
|
|
|
|
92 |
98 |
14 |
89,4 |
10,08 |
|
|
|
|
|
|
Середня |
серія |
|
|
|
|
|
16 |
20 |
4 |
14,5 |
- |
|
|
|
6 |
18 |
22 |
5 |
16,7 |
- |
0,3 |
0,2 |
|
21 |
25 |
5 |
19,5 |
1,95 |
||||
|
|
|
||||||
|
23 |
28 |
6 |
21,3 |
2,34 |
|
|
|
6 |
26 |
32 |
6 |
23,4 |
1,65 |
0,4 |
0,3 |
|
28 |
34 |
7 |
25,9 |
1,70 |
||||
|
|
|
96
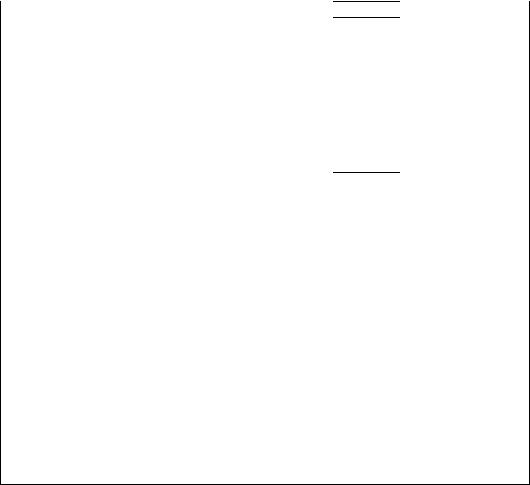
Розділ 7 |
Вали |
Закінчення табл.8.17
1 |
2 |
3 |
|
4 |
5 |
6 |
|
7 |
8 |
|||
8 |
32 |
38 |
|
6 |
29,4 |
- |
|
0,4 |
0,3 |
|||
36 |
42 |
|
7 |
33,5 |
1,02 |
|
||||||
|
42 |
48 |
|
8 |
39,5 |
2,57 |
|
|
|
|
||
|
46 |
54 |
|
9 |
42,7 |
- |
|
|
|
|
||
8 |
52 |
60 |
|
10 |
48,7 |
2,44 |
|
0,5 |
0,5 |
|||
56 |
65 |
|
10 |
52,2 |
2,50 |
|
||||||
|
|
|
|
|
|
|||||||
|
62 |
72 |
|
12 |
57,8 |
2,60 |
|
|
|
|
||
|
72 |
82 |
|
12 |
67,4 |
- |
|
|
|
|
||
10 |
82 |
92 |
|
12 |
77,1 |
3,0 |
|
0,5 |
0,5 |
|||
|
92 |
102 |
|
14 |
87,3 |
4,5 |
|
|
|
|
||
|
|
|
|
|
Важка |
серія |
|
|
|
|
|
|
z |
d |
|
D |
|
b |
a1 |
|
|
f |
|
r |
|
|
16 |
|
20 |
|
2,5 |
14,1 |
|
|
|
|
|
|
10 |
18 |
|
23 |
|
3,0 |
15,6 |
|
|
0,3 |
|
|
0,2 |
21 |
|
26 |
|
3,0 |
18,5 |
|
|
|
|
|||
|
|
|
|
|
|
|
|
|
||||
|
23 |
|
29 |
|
4,0 |
20,3 |
|
|
|
|
|
|
|
26 |
|
32 |
|
4,0 |
23,0 |
|
|
|
|
|
|
10 |
28 |
|
35 |
|
4,0 |
25,4 |
|
|
|
|
|
|
32 |
|
40 |
|
5,0 |
28,0 |
|
|
0,4 |
|
|
0,3 |
|
|
36 |
|
45 |
|
5,0 |
31,3 |
|
|
|
|
|
|
|
42 |
|
52 |
|
6,0 |
36,9 |
|
|
|
|
|
|
10 |
46 |
|
56 |
|
7,0 |
40,9 |
|
|
|
|
|
|
|
52 |
|
60 |
|
5,0 |
47,0 |
|
|
|
|
|
|
16 |
56 |
|
65 |
|
5,0 |
50,6 |
|
|
0,5 |
|
|
0,5 |
62 |
|
72 |
|
6,0 |
56,1 |
|
|
|
|
|||
|
|
|
|
|
|
|
||||||
|
72 |
|
82 |
|
7,0 |
65,9 |
|
|
|
|
|
|
20 |
82 |
|
92 |
|
6,0 |
75,6 |
|
|
|
|
|
|
92 |
|
102 |
|
7,0 |
85,5 |
|
|
|
|
|
|
|
|
|
|
|
|
|
|
|
|
Примітка: Виконання А дано для виготовлення валів з’єднань легкої та середньої серій методом обкатування. Вали з’єднань важкої серії методом обкатування не виготовляють.
Допустиме напруження σ змadm для поверхонь шліців, які не підлягають спеціальній термічній обробці, приймають:
-при спокійному навантаженні і нерухомому з’єднанні σ змadm =100 МПа;
-при рухомому з’єднанні не під навантаженням σ змadm =40 МПа;
- при змінному навантаженні σ змadm зменшують на 30-50% в залежності від інтенсивності ударів.
Якщо поверхні шліців термічно оброблені, то значення σ змadm збільшу-
ють на 40…50%.
Перевірку на міцність евольвентних шліцьових з’єднань на зминання виконують за формулою (7.12), де Азм≈0,8тl; т – модуль зубців;
Rср≈(Dа+dа).
97
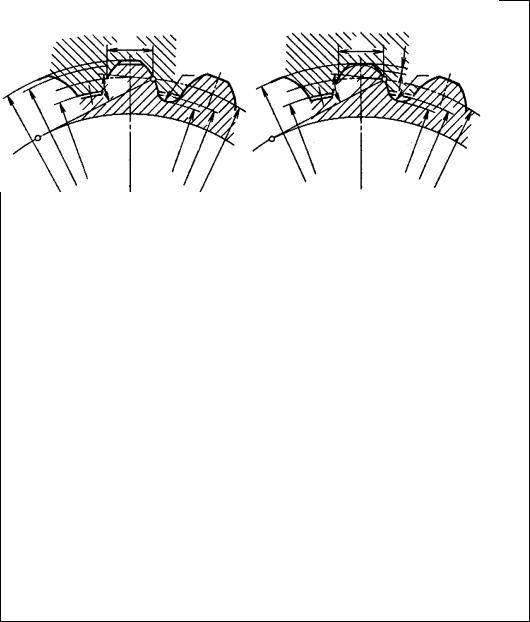
Розділ 7 |
Вали |
Таблиця 8.18 - З’єднання шліцьові евольвентні (ГОСТ 6033-80)
|
|
|
|
Центрування по S |
|
|
|
|
|
|
Центрування по D |
|
|
|||||||
|
|
|
|
|
S |
|
|
|
|
|
|
|
|
S |
ρ |
|
|
|||
|
|
|
|
|
|
|
|
|
|
|
|
|
|
|
|
|
|
|||
|
|
|
|
|
α |
|
R |
|
|
|
|
|
|
|
|
R |
|
|
||
|
|
|
|
|
|
|
|
|
|
|
|
α |
|
|
|
|
|
|||
|
|
da |
Da |
df |
df |
|
|
|
|
D |
|
|
df df |
|
|
|||||
|
|
Df |
|
|
|
|
|
|
d |
|
|
|
Da |
|
|
|
d |
|
|
|
|
|
|
|
|
|
|
|
|
|
|
|
|
|
|
|
|
||||
|
|
|
|
|
|
|
|
|
|
|
|
|
|
|
|
|
|
|
||
|
|
|
|
|
|
|
|
|
|
Розміри, мм |
|
|
|
|
|
|
|
|
||
|
D |
|
|
|
Модуль, т |
|
|
|
|
D |
|
|
Модуль, т |
|
|
|||||
|
|
0,8 |
|
1,25 |
|
|
2 |
|
|
3 |
|
|
2 |
|
3 |
|
5 |
|
||
|
|
|
|
|
Число |
зубців z |
|
|
|
|
|
|
Число зубців z |
|
|
|||||
10 |
|
11 |
|
|
|
|
|
|
|
|
|
60 |
|
28 |
|
18 |
|
|
|
|
12 |
|
13 |
|
|
|
|
|
|
|
|
|
65 |
|
31 |
|
20 |
|
|
|
|
15 |
|
17 |
|
|
|
|
|
|
|
|
|
70 |
|
34 |
|
22 |
|
|
|
|
17 |
|
20 |
|
12 |
|
|
|
|
|
|
|
75 |
|
36 |
|
24 |
|
|
|
|
20 |
|
23 |
|
14 |
|
|
|
|
|
|
|
80 |
|
38 |
|
25 |
|
|
|
|
25 |
|
30 |
|
18 |
|
|
|
|
|
|
|
85 |
|
|
|
27 |
|
15 |
|
|
30 |
|
36 |
|
20 |
|
|
|
|
|
|
|
90 |
|
|
|
28 |
|
16 |
|
|
35 |
|
|
|
26 |
|
|
16 |
|
|
|
|
95 |
|
|
|
30 |
|
17 |
|
|
40 |
|
|
|
30 |
|
|
18 |
|
|
|
|
100 |
|
|
|
32 |
|
18 |
|
|
45 |
|
|
|
34 |
|
|
21 |
|
|
|
|
|
|
|
|
|
|
|
|
|
50 |
|
|
|
38 |
|
|
24 |
|
|
|
|
|
|
|
|
|
|
|
|
|
55 |
|
|
|
|
|
|
26 |
|
|
17 |
|
|
|
|
|
|
|
|
|
|
Примітка: 1. В таблиці наведені номінальні діаметри D із першого ряду – в інтервалі від |
||||||||||||||||||||
10 до 100мм; відповідно значення модулів також із першого ряду |
в інтервалі від 0,8 до |
5мм. В ГОСТ 6033-80 інтервал діаметрів від 4 до 500 мм, інтервал модулів від 0,5 до
10мм.
2. Числа зубців z наведені в таблиці тільки ті, які відмічено в стандарті у першому ряді. 3. Діаметр ділильного кола d=mz; діаметр кола впадин втулки: при плоскій формі дна Df=D; при заокругленій Df=D+0,44m; діаметр кола вершин зубців втулки Dа=D-2m; діаметр кола впадин вала: при плоскій формі дна df=D -2,2m; при заокругленій df=D -2,76m; діаметр кола вершин зубців вала: при центруванні по ширині зубця dа=D-0,2m; при
центруванні по зовнішньому діаметру dа=D; R=0,47m; α=300.
98
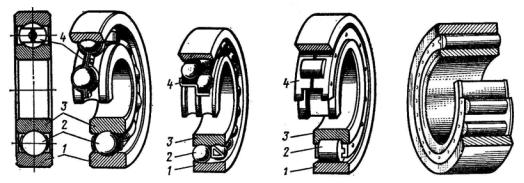
Розділ 8 |
Опори валів |
8 ОПОРИ ВАЛІВ
8.1 Загальні відомості
Підшипники кочення – це елементи опор осей і валів та інших деталей, що працюють на принципі тертя кочення.
Підшипники кочення (рис.8.1) складаються із : зовнішнього 1 і внутрішнього 3 кілець , тіл кочення — кульок або роликів 2, які котяться по бігових доріжках кілець на певній відстані один від одного, і сепаратора 4. Відносне обертання внутрішнього кільця відносно зовнішнього забезпечується за рахунок тіл кочення між кільцями. Сепаратор розділяє тіла кочення і утримує їх на однаковій відстані.
а) |
б) |
а) |
б) |
Рисунок 8.1- Підшипники кулькові |
Рисунок 8.2 – Підшипники роликові |
Кільця і тіла кочення виготовляють із підшипникової сталі з високим вмістом хрому (ШХ6, ШХ15, ШХ20СГ) та інших легованих сталей, наприклад сталі 12Х2Н4А, 18ХГТ. Сепаратор виготовляють із сталей Ст1; Ст2, а також з латуні, бронзи, капрону, текстоліту, металопластмас, фторопласту з металевими і неметалевими наповнювачами.
99
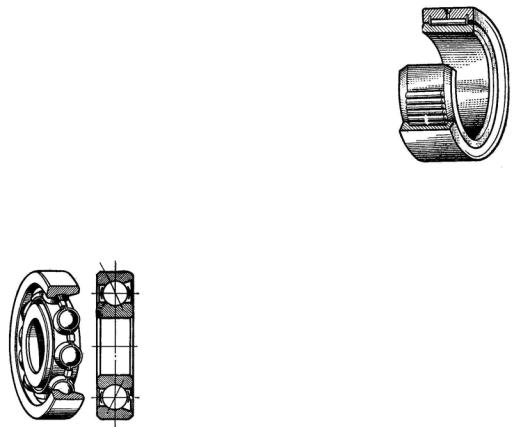
Розділ 8 |
Опори валів |
8.2 Конструкції і класифікація підшипників кочення
Підшипники кочення поділяються за такими ознаками:
– за формою тіл кочення підшипники бувають - кулькові і роликові (з циліндричними, конічними, бочкоподібними, голчастими й витими роликами);
–за числом рядів тіл кочення – однорядні, дворядні, чотирирядні;
–за способом компенсації перекосів вала -
несамоустановні та самоустановні сферичні.
– за радіальними розмірами підшипники кочення з одним і тим же внутрішнім діаметром поділяють на 5
серій діаметрів (надлегка, особливо легка, легка, середня та важка) і на 5 серій ширини (особливо вузька, вузька, нормальна широка, широка, особлива широка).
- за напрямом сприйманого навантаження підшипники кочення поділяються на – радіальні (здатні сприймати радіальне навантаження); радіально-упорні (здатні сприймати радіальне та осьове навантаження); упорні (здатні сприймати тільки осьове навантаження); упорно-радіальні (сприймають значне осьове і незначне радіальне навантаження).
Коротко розглянемо найпоширеніші стандартні підшипники кочення.
Радіальні однорядні кулькові підшипники (рис.8.1, а) можуть сприймати ра-
діальне і незначне осьове навантаження. Набули най-
αбільшого поширення в машинобудуванні. Витримують великі кутові швидкості вала (особливо з сепараторами з кольорових металів) і допускають перекіс кілець до 10'. Найдешевші з підшипників кочення ра-
діальні роликопідшипники з короткими (рис.8.2,а) і
довгими (не стандартизовані, рис.8.2,б) циліндричними роликами сприймають тільки радіальне навантаження (якщо є борти на кільцях, то можуть сприймати незначне осьове навантаження). Навантажувальна здатність цих підшипників значно більша, ніж куль-
кових, однак вони не допускають перекосу кілець, оскільки ролики починають працювати кромками й підшипники швидко виходять з ладу. Роликові підшипники з витими роликами сприймають радіальне на-
вантаження при невисоких кутових швидкостях. Застосовують при ударних навантаженнях (удари пом'якшуються податливістю витих роликів). Не потребують високої точності монтажу і спеціального захисту від забруднень.
100
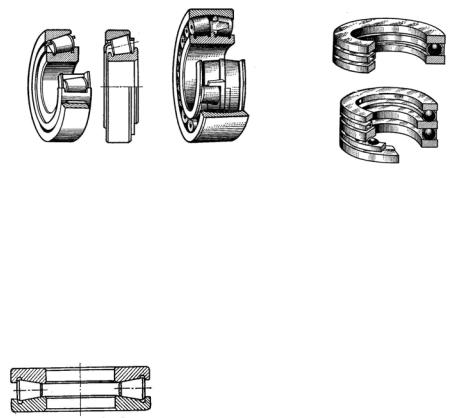
Розділ 8 |
Опори валів |
Голчасті підшипники (рис.8.3) мають ролики з відношенням довжини до діаметра (4...10). Можуть працювати при значних радіальних навантаженнях, витримують ударні навантаження при невисоких кутових швидкостях. Не допускають осьового навантаження і перекосу кілець. Ці підшипни-
а)
а) |
б) |
б) |
|
Рисунок 8.6 – Підшипники |
|||
Рисунок 8.5 – Підшипники |
|||
радіально–упорні роликові |
упорні кулькові |
ки застосовують у карданних шарнірах, двигунах і коробках передач мотоциклів, автомобілів і тракторів, в опорах кривошипно-повзунних і кулісних механізмів. Радіально-упорні кулькові підшипники (рис.8.4) застосовують у підшипникових вузлах, які сприймають разом радіальні й осьові навантаження. Радіальна вантажопідйомність цих підшипників на З0... ...40 % більша, ніж у радіальних однорядних кулькових підшипниках. їх застосовують при середніх і високих кутових швидкостях і безударних навантаженнях. Кульковий радіально-упорний підшипник може сприймати осьове навантаження тільки в одному напрямі. Конічні роликові підшипники
(рис.8.5) також призначені для сприймання радіального й осьового навантажень. Порівняно з радіально-упорними кульковими підшипниками мають більшу вантажопідйомність, відзнача-
ються можливістю роздільного монтажу внут- Рисунок 8.7 рішнього (разом з роликами і сепараторами) і
зовнішнього кілець, а також властивістю сприймати невеликі ударні навантаження. Недоліком цих підшипників є велика чутливість до неспіввісності та відносного перекосу кілець. Кулькові
(рис.8.1,б) і роликові дворядні (рис.8.5,б) сферичні самоустановні підшип-
ники мають підвищену вантажопідйомність порівняно з однорядними. Допускають перекіс кілець до 2° і тому їх можна застосовувати для валів зниженої жорсткості, а також у тих випадках, коли співвісність посадочних місць не гарантовано.
101

Розділ 8 |
Опори валів |
Упорні кулькові і роликові підшипники (рис.8.6, 8.7) призначені для сприймання тільки осьового навантаження, їх установлюють в парі з радіальними кульковими або роликопідшипниками, які центрують вісь вала й обмежують його переміщення в радіальному напрямі. Зображений на рис.8.6,б подвійний упорний кульковий підшипник призначений для сприймання двостороннього осьового навантаження. На рис.8.8 зображено: а - упорно-радіальний кульковий, б - упорно-радіальний з сферичними роликами. Ці підшипники можуть сприймати значні осьові навантаження і частково радіальні, не вимагаючи установлювати поруч радіальні підшипники.
а) |
α |
б) |
|
Рисунок 8.8 |
|||
|
|
Усі підшипники кочення мають умовне позначення, яке складається з ряду цифр. Дві перші цифри, рахуючи справа, показують умовно діаметр внутрішнього кільця підшипника. Для визначення діаметра внутрішнього кільця в міліметрах треба останні дві цифри його умовного позначення помножити на 5.
Третя цифра праворуч умовного позначення показує серію підшипника: особливо легка – 1; легка – 2; середня – 3; важка – 4 і т. д.
Четверта цифра праворуч означає тип підшипника: 0 – радіальний кульковий однорядний; 1 - радіальний кульковий дворядний сферичний; 2 - радіальний із короткими циліндричними роликами; 3 - радіальний роликовий дворядний сферичний; 4 – голчастий; 5 – роликовий із витими роликами; 6 – радіально-упорний кульковий; 7 – роликовий конічний; 8 – упорний кульковий; 9 – упорний роликовий.
П’ята і шоста цифри праворуч характеризують конструктивні особливості підшипника (вводяться не для всіх підшипників).
Сьома цифра характеризує серію підшипника за шириною.
Клас точності вказують зліва від позначення через дефіс. Наприклад, 5-206, де 5 – клас точності, а 206 – умовне позначення радіального кулькового підшипника легкої серії.
Підшипники кочення поділяють на п’ять класів точності (ГОСТ 52089) і позначаються цифрами: 0; 6; 5; 4; і 2 (у порядку зростання точності). Точність розповсюджується на діаметри кілець і їх ширину. Для валів і осей загального призначення використовують підшипники кочення нормальної точності класу 0.
102
Розділ 8 |
Опори валів |
Основні розміри найбільш розповсюджених типів підшипників наведені у додатку Г. До таких розмірів належать внутрішній діаметр d, зовнішній діаметр D і ширина підшипника В. В упорних кулькових підшипниках ширину характеризує розмір Н, а в радіально-упорних роликових підшипниках найбільшу ширину визначає розмір Т.
8.3 Вимоги до конструкції опор валів з підшипниками кочення
Під час конструювання підшипникових вузлів беруть до уваги призначення механізму, умови його монтажу і експлуатації, величину і напрям експлуатаційних навантажень підшипників, необхідний ресурс, частоти обертання, температурні умови і стан зовнішнього середовища, а також загальну компоновку механізму і технологічні можливості його виготовлення. Всі ці фактори визначають не тільки конструкцію опори, типи використаних підшипників і спряжених з ними деталей, але й систему ущільнень та змащування, а також точність виготовлення окремих деталей.
Найбільш загальними вимогами до опор з підшипниками кочення є забезпечення співвісності посадочних поверхонь під підшипники, належна жорсткість деталей підшипникового вузла і умови правильного монтажу і демонтажу опор.
Співвісність посадочних поверхонь під підшипники вимагає забезпечення повної збіжності осей посадочних шийок валів і отворів корпусів після монтажу. Якщо не вжито заходів для компенсації можливих конструктивних чи технологічних дефектів, що спричиняють похибки у співвісності, робота підшипникової опори буде ненормальною внаслідок перекосу кілець і перевантаження тіл кочення.
Основні способи забезпечення співвісності: а) розташування підшипникових опор у спільному корпусі або фіксація окремих корпусів опор на спільній основі з розточуванням отворів під зовнішні кільця підшипників за один прохід різального інструмента; б) остаточна обробка посадочних поверхонь на валах за одне встановлення на верстаті; в) застосування в опорах самоустановних сферичних кулькових чи роликових підшипників для багатоопорних і податливих валів.
Жорсткість деталей підшипникового вузла досягається за умови виконання таких вимог: а) розміри спряжених з підшипниками деталей повинні бути такими, щоб під дією експлуатаційних навантажень вони не деформувались і не спотворювали свою геометричну форму; б) навантаження, що діють на опору, не повинні спричинювати відхилення від співвісності посадочних поверхонь; в) висота і площа опорних поверхонь бортів на валах і в корпусах повинна бути достатньою для сприйняття осьових зусиль без деформацій; г) торцеві кришки для фіксації підшипників в осьовому напрямку
103
Розділ 8 |
Опори валів |
повинні мати достатню жорсткість для уникнення деформацій, що можуть спотворити нормальне положення підшипника.
Умови правильного монтажу і демонтажу опор з підшипниками кочення: а) наявність відповідних фасок на поверхнях шийок валів і в розточках корпусів; б) можливість застосування відповідних пристроїв для напресування і випресування підшипників; в) забезпечення технологічності монтажу всіх деталей опори з можливістю регулювання зубчастих зачеплень й інших елементів, а також зазорів в самих підшипниках.
8.4 Конструкції опор валів механічних передач
Вали зубчастих передач здебільшого розташовують в опорах з підшипниками кочення. Залежно від того, яке співвідношення радіальних і осьових зусиль, що діють на вали, використовують як радіальні, так і радіальноупорні підшипники.
Узубчастих передачах прямозубих або косозубих з малим кутом нахилу зубців і відносно малою відстанню між опорами використовують радіальні кулькові підшипники (рис.8.9, а). Для того, щоб уникнути защемлення тіл кочення від температурних деформацій, передбачається зазор а = 0,2...0,4 мм. Цей зазор регулюють за допомогою мірних прокладок (b) між корпусом
інакладними кришками підшипників. Така конструкція досить проста, оскільки отвори у корпусі можна виконати без бортиків наскрізною розточкою за одну установку, що забезпечує високу точність посадочних гнізд під підшипники. Крім того, в опорах зменшується кількість деталей і зручно виконувати монтаж і регулювання осьового зазору.
Конструкцію опор вала за рис.8.9, б застосовують у разі значної відстані між опорами. Тут права опора вала фіксована, а ліва — плаваюча. Осьовий зазор с повинен бути в межах 2...3 мм, щоб уникнути защемлення підшипників при температурних перепадах.
Узубчастих передачах з шевронними колесами або здвоєними косозубими, що утворюють шеврон, осьові зусилля на опори відсутні. Однак через неточності виготовлення і складання може відбуватись нерівномірне навантаження півшевронів за умови жорсткої осьової фіксації двох валів. Щоб уникнути такого явища, один із валів (переважно швидкохідний) роблять плаваючим в осьовому напрямі. Цього досягають використанням в опорах вала радіальних підшипників з короткими циліндричними роликами без бортів на зовнішньому кільці. Конструкція опор плаваючого вала показана на рис.8.9, в. У випадку недостатньо жорстких валів доцільно використовувати радіальні сферичні кулькові підшипники (рис.8.9, г).
Узубчастих передачах косозубих, конічних або черв'ячних на вали можуть діяти значні осьові навантаження. В таких випадках в опори валів
104
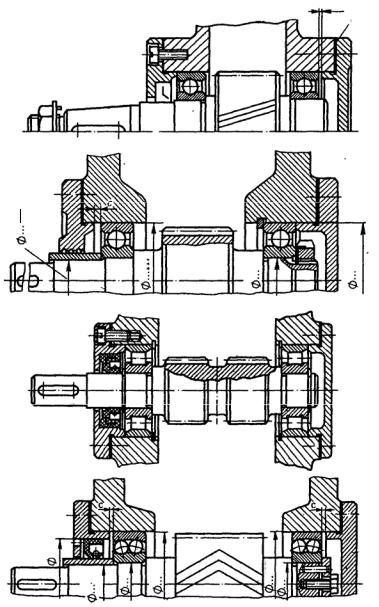
Розділ 8 |
Опори валів |
а)
H8 h8
б)
в)
а
b
H8 |
k6 |
H7 |
|
h7 |
г)
|
k6 |
H7 |
H7 k6 |
|
H8 |
h8 |
Рисунок 8.9 – Конструкції опор валів з радіальними підшипниками
105
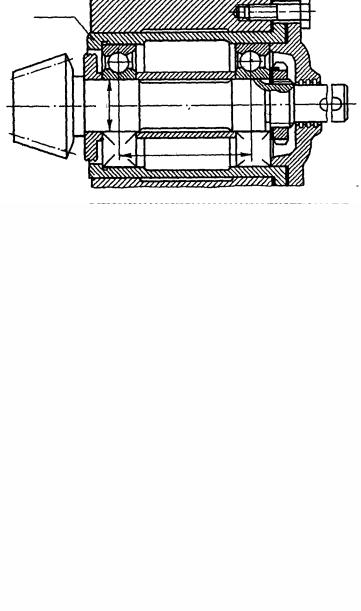
Розділ 8 |
Опори валів |
а) L
а l а
H7
б)
d |
m6 |
l<(8…10)d
стакан
в)
d
l<(8…10)d
Рисунок 8.10 – Конструкції опор валів з радіальноупорними підшипниками
106
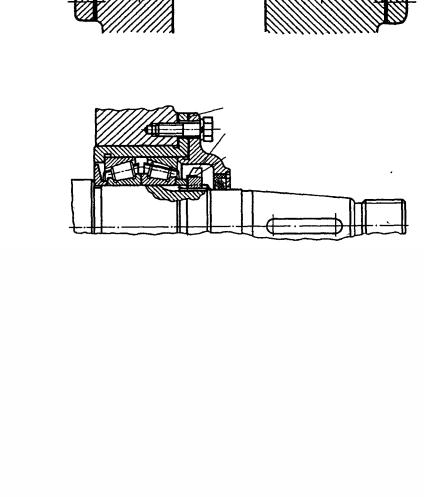
Розділ 8 |
Опори валів |
Дистанційне кільце
Стакан
а)
l>(8…10)d
b
1
б) |
2 |
|
Рисунок 8.11 – Конструкції опор валів з двома кульковими і роликовими радіально-упорними підшипниками
107
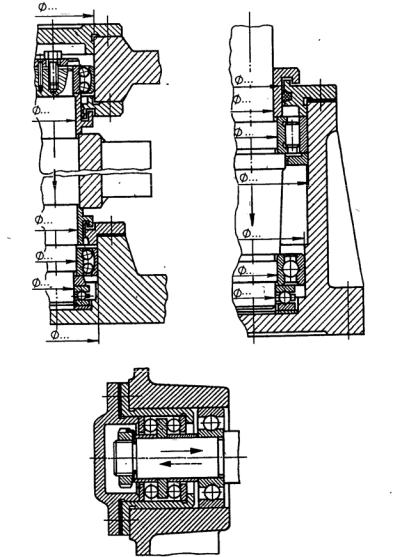
Розділ 8 |
Опори валів |
H7
H7
H8
h8
а)
H8
h8
k6
s6
H7
h11
H8
h8
k6
б)
H17
Fa
H17
k6
s6
Fa |
в) |
Рисунок 8.12 – Конструкції опор валів з упорними підшипниками
108
Розділ 8 |
Опори валів |
встановлюють радіально-упорні кулькові (рис.8.10,а) або кулькові (рис.8.10,б) підшипники за умови, що відношення відстані між опорами до діаметра вала не перевищує 8. Зображені на рис.8.10 конструкції опор валів досить прості, але вимагають ретельного регулювання осьових зазорів у підшипниках в необхідних межах як під час складання опор, так і під час експлуатації. Температурні видовження вала ні в якому разі не мають повністю вибирати осьові зазори. В опорах валів (рис.8.10) осьові зазори регулюються комплектом металевих прокладок завтовшки 0,05...0,2 мм, що встановлюються між корпусом і кришками підшипників.
Для валів, що мають значну відстань між опорами і навантажені значними осьовими силами, часто використовують комбіновані опори. В одній опорі (більш навантаженій) розташовують два радіально-упорні підшипники для сприйняття радіального навантаження і двостороннього осьового навантаження, а в іншій - один радіальний плаваючий підшипник для сприйняття тільки радіального навантаження (рис.8.11, а). Для вільного осьового переміщення зовнішнього кільця плаваючого підшипника в корпусі необхідно передбачити його відповідну посадку з зазором. В такій конструктивній схемі опор валів можуть використовуватись радіально-упорні підшипники як кулькові (рис.8.11, а), так і роликові конічні (рис.8.11, б). В останньому варіанті слід звернути увагу на закріплення внутрішніх кілець конічних роликових підшипників гайкою на валу. Тут потрібна додаткова втулка між торцем внутрішнього кільця підшипника і гайкою 1 із стопорною шайбою 2 для того, щоб забезпечити зазор між сепаратором підшипника і шайбою.
Регулювання осьових зазорів радіально-упорних підшипників в опорах за рис.8.11 здійснюється набором прокладок (b) під кришками. Тут же для встановлення зовнішніх кілець підшипників у корпусі передбачені додаткові перехідні втулки (стакани). Ці втулки поставлені з метою спрощення технології механічної обробки посадочних гнізд у корпусі.
Конструктивні особливості опор вертикальних валів з використанням радіальних і одинарних упорних підшипників подані на рис.8.12, а,б. Тут на вали діє односторонньо направлена осьова сила Fa. У випадку можливої двосторонньої дії осьової сили опора вала зі здвоєним упорним і радіальним підшипниками може мати конструкцію, яка наведена на рис.8.12, в.
8.5 Деталі кріплення підшипників кочення в опорах
Деякі способи закріплення підшипників кочення в опорах валів показані на рис.8.13 і 8.14. Найбільш надійним способом кріплення підшипника на валу є спосіб з використанням спеціальної шліцьової гайки, яка нагвинчується на різьбову ділянку вала (рис.8.13, г). Гайка фіксується від самовідгвинчування спеціальною стопорною шайбою (табл.Д.13). Різьбова ділянка
109