
- •Foreword
- •Foreword to First Edition
- •Contributors
- •Preface
- •A.1 Piezoelectric Materials
- •A.3 Optical Fiber Sensors
- •A.4 Electrorheological Fluids
- •A.5 Magnetostrictive Materials
- •A.6 Micro-Electro-Mechanical Systems
- •A.7 Comparison Of Actuators
- •References
- •Index
- •1. Introduction and Overview
- •1.1 General
- •1.3 High-Performance Fiber Composite Concepts
- •1.4 Fiber Reinforcements
- •1.5 Matrices
- •References
- •Bibliography
- •2. Basic Principles of Fiber Composite Materials
- •2.1 Introduction to Fiber Composite Systems
- •2.3 Micromechanics
- •2.4 Elastic Constants
- •2.5 Micromechanics Approach to Strength
- •2.6 Simple Estimate of Compressive Strength
- •References
- •3. Fibers for Polymer-Matrix Composites
- •3.1 Overview
- •3.3 Carbon Fibers
- •3.4 Boron Fibers
- •3.5 Silicon Carbide
- •3.6 Aramid Fibers
- •3.7 Orientated Polyethylene Fibers
- •3.8 Dry Fiber Forms
- •References
- •4. Polymeric Matrix Materials
- •4.1 Introduction
- •4.2 Thermoset and Thermoplastic Polymer Matrix Materials
- •4.3 Thermosetting Resin Systems
- •4.4 Thermoplastic Systems
- •References
- •5. Component Form and Manufacture
- •5.1 Introduction
- •5.2 Outline of General Laminating Procedures
- •5.5 Filament Winding
- •5.7 Process Modelling
- •5.8 Tooling
- •References
- •6. Structural Analysis
- •6.1 Overview
- •6.2 Laminate Theory
- •6.3 Stress Concentration and Edge Effects
- •6.4 Failure Theories
- •6.7 Buckling
- •6.8 Summary
- •References
- •7. Mechanical Property Measurement
- •7.1 Introduction
- •7.2 Coupon Tests
- •7.3 Laboratory Simulation of Environmental Effects
- •7.4 Measurement of Residual Strength
- •7.5 Measurement of Interlaminar Fracture Energy
- •References
- •8. Properties of Composite Systems
- •8.1 Introduction
- •8.3 Boron Fiber Composite Systems
- •8.4 Aramid Fiber Composite Systems
- •8.6 Properties of Laminates
- •References
- •9. Joining of Composite Structures
- •9.1 Introduction
- •9.2 Comparison Between Mechanically Fastened and Adhesively Bonded Joints
- •9.3 Adhesively Bonded Joints
- •9.4 Mechanically Fastened Joints
- •References
- •10. Repair Technology
- •10.1 Introduction
- •10.2 Assessment of the Need to Repair
- •10.3 Classification of Types of Structure
- •10.4 Repair Requirements
- •10.6 Patch Repairs: General Considerations
- •10.7 Bonded Patch Repairs
- •10.9 Application Technology: In Situ Repairs
- •10.10 Bolted Repairs
- •References
- •11. Quality Assurance
- •11.1 Introduction
- •11.2 Quality Control
- •11.3 Cure Monitoring
- •References
- •12. Aircraft Applications and Design Issues
- •12.1 Overview
- •12.2 Applications of Glass-Fiber Composites
- •12.3 Current Applications
- •12.4 Design Considerations
- •12.7 A Value Engineering Approach to the Use of Composite Materials
- •12.8 Conclusion
- •References
- •13. Airworthiness Considerations For Airframe Structures
- •13.1 Overview
- •13.2 Certification of Airframe Structures
- •13.3 The Development of Design Allowables
- •13.4 Demonstration of Static Strength
- •13.5 Demonstration of Fatigue Strength
- •13.6 Demonstration of Damage Tolerance
- •13.7 Assessment of the Impact Damage Threat
- •References
- •14. Three-Dimensionally Reinforced Preforms and Composites
- •14.1 Introduction
- •14.2 Stitching
- •14.3 Z-Pinning
- •14.6 Knitting
- •14.8 Conclusion
- •References
- •15. Smart Structures
- •15.1 Introduction
- •15.2 Engineering Approaches
- •15.3 Selected Applications and Demonstrators
- •References
- •16. Knowledge-Based Engineering, Computer-Aided Design, and Finite Element Analysis
- •16.2 Finite Element Modelling of Composite Structures
- •16.3 Finite Element Solution Process
- •16.4 Element Types
- •16.5 Finite Element Modelling of Composite Structures
- •16.6 Implementation
- •References
566 COMPOSITEMATERIALS FOR AIRCRAFT STRUCTURES
interaction between bending and torsion when the shear center is offset from the centroid of the section. In addition, local buckling modes involving the buckling of the flanges and web of the beam will be predicted, in addition to the global modes of Euler beam buckling when a buckling analysis is executed. However, the model cannot predict the detailed stress and strain distribution at the intersection of the web and flanges. I f details of stress and strain are required at this intersection, a three-dimensional brick analysis is required, as indicated in the Figure.
I f the structure is comprised of beams which are slender and transfer load by axial, bending and torsional components, then rod and beam elements can be used. The success of the analysis, summarized in Section 16.3 for the rod element, depends on the definition of the effective stiffness components.
16.6 Implementation
Once the details o f how the composite material will be modelled have been resolved, the full power of the finite element analysis becomes available. The finite element method can be applied to structures of arbitrary shape and can include advanced applications including:
•Non-linear analysis for post-buckling behavior modes of failure, and ultimate collapse
•Static or dynamic solutions, including crash simulation
•Optimization.
16.6.1Post-Buckling Performance and Stiffener Separation
Local failure of composite components has been discussed in Chapter 6. However, failure of structural assemblies was not considered. The analysis of these structures and the prediction of failure rely on finite element analysis.
For example, composite structures are often composed of assemblies of stiffened plates. Local buckling can be allowed to occur below the ultimate failure load in these stiffened structures so long as the residual strength of the structure is sufficient to carry the applied loads. Analysis is required to predict the post-buckling behavior as well as ensuring that buckling does not trigger separation of the stiffeners that would lead to a significant loss of strength. A geometric non-linear analysis is required to predict the post-buckling behavior of the panel shown in Figure 16.13b, and a fracture mechanics approach is used to predict growth of a disbond between the panel and the stiffener.8 The initial disbond weakens the panel and is introduced into the analysis to prove its damage tolerance.
The analysis8 is based on plate elements in a commercial finite element system.9 The panel and stiffener have been modelled separately and connected by
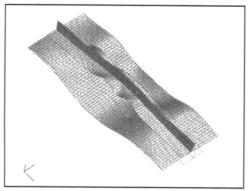
KNOWLEDGE-BASEDENGINEERING,CAD,AND FEA |
567 |
||
Stringer |
~11~./Stringer web |
|
|
flange |
|
|
|
Skin |
Iii |
Stringer flange |
|
_ _ ~ n _ _ ° _ d a l s : : : n : o d a |
a) Modelling using plates and |
||
'rigid elements |
|
||
|
; |
plane |
|
b) Post-buckling deformation
""~'"7"7"'i"'T' "
Fig. 16.13 Finite element analysis of stiffener separation.
rigid links. The rigid links are removed to model the area affected by the disbond. A virtual crack extension procedure is used to determine the energy release rate in modes I and II crack extension and predict growth of the disbond. Studies were completed to determine the buckling loads and the post-buckling behavior of a damaged panel in an empennage structure, the critical length of the disbond, and the residual strength of the damaged panel.
568COMPOSITE MATERIALS FOR AIRCRAFT STRUCTURES
16.7DesignOptimization
The combination of knowledge-based systems and optimization algorithms allow an automated design process to include both performance and cost objectives in the design analysis. For example, the structure in Figure 16.3 was subject to an optimization process searching for a design that combined low weight and low manufacturing cost. 1° The structural performance under pressure loads is controlled by ply orientation in the laminate, by the thickness of the panels, and by the geometry, thickness, location, and shape of the stiffening members. All can be varied in a finite element model to satisfy strength, stiffness, and buckling requirements.
Procedures available in commercial finite element systems 11 include a topology optimization system, 12to identify the principle structural members, and a parametric design algorithm that allows variables in the optimization algorithm to include dimensions such as the location of the stiffening members. Successful applications of these algorithms ~° do not necessarily require an automated process; rather, the algorithms can be used to guide the evolution of the design and help the design team to evaluate a number of different design options in a concurrent engineering approach. As the design evolves, so does understanding of the load paths in the structure and the redundancy that provides damage tolerance, often a primary design requirement.
16.7.1 Cost Estimates for Design Optimization
The design of weight-effective aerospace structures can no longer guarantee the success of the product. Manufacturers need to verify that their products are an optimal tradeoff between minimum weight, cost, and risk, all within a time frame that meets time-to-market needs. Costs here are taken to mean whole-of-life costs including manufacturing, operation, and maintenance costs. Optimization of these objectives must be carried out in the conceptual design phase because, once the design concept is fixed, up to 80% of the whole-of-life costs will also be fixed. 13 Further detail design alterations may not produce substantial reductions in manufacturing cost or reduce the requirements for through life support.
Implementation of CAE gives the designer the opportunity to enhance the understanding of the functionality of the design and to determine the primary drivers for cost and weight. Preliminary cost estimates for setting cost and weight targets can be based on $/kg and $ / m 2 parameters, validated using data from completed projects. These estimates can be enhanced by identifying cost drivers that represent the complexity of the design, ensuring the cost estimate is not simply proportional to weight or size. 14
As the design evolves, these cost estimates cannot reflect the effect of detailed design changes on cost. In the final stages of the design, the cost will rise as weight is removed from the structure. One approach to estimating cost is based on the Process Costing Analysis Database (1992-1997). 15This approach separates a
KNOWLEDGE-BASED ENGINEERING, CAD, AND FEA |
569 |
manufacturing process into discrete steps and identifies the parameters from which manufacturing time can be estimated. For example, the time required for a non-destructive inspection can be related to the length of a joint that is to be inspected for defects. Cost estimates follow by applying an appropriate hourly rate for the cost of labor.
Design and analysis of efficient composite structures is a complex process. Successful exploitation of these materials will depend on the efficient use of the latest CAE and KBE tools.
References
~CATIA Proprietary Software, Dassault Systems, www.catia.com.
2ICAD Proprietary Software, Knowledge Technologies International. www.ktiworld.
c o m
3young, W. C., Roark's Formulas for Stress and Strain, 7th ed., McGraw-Hill, 2000. 4Cook, R. D., Finite Element Modeling for Stress Analysis, Wiley, 1995.
5Adams, V., and Askenazi, A., Building Better Products with Finite Element Analysis,
Onward Press, 1999.
6Matthews, F. L., Davies, G. A. O., Hitchings, D., and Soutis, C., Finite Element Modeling of Composite Materials and Structures, Woodhead Publishing, 2000.
7Tan, P., Tong, L., and Steven, G., "Micromechanics Models for the Elastic Constants and Failure Strengths of Plain Weave Composites," Composite Structures, Vol. 47, 1999, pp. 797-804.
Syap, J., Scott, M., Thomson, R., and Hachenberg, D., The Analysis of Skin-to-Stiffener Debonding in Composite Aerospace Structures, ICCS-11, Monash Univ., Melbourne, Australia, Nov. 2001.
9MSC.NASTRAN Proprietary software of the MacNeal Schwendler Corporation, www.msc.com.
l°Raju, J., "A Conceptual Design and Cost Optimization Methodology," Proceedings of the 44th AIAA/ASME/ASCE/AHS Structures, Structural Dynamics and Materials Conference, April 2003.
11ANSYS Proprietary software of Swanson Analysis Inc, www.ansys.com. 12Bendsoe, M., Diaz, A., and Kikuchi, N., "Topology and Generalised Layout
Optimization of Elastic Structures" Topology Design of Structures, edited by M. P. Bendsoe and C. A. Mota Soares, Kluwer Academic Publishers, Netherlands, pp. 159-205.
13Wang, K., Kelly, D., Dutton, S., "Multi-objective Optimisation of Composite Aerospace Structures," Composite Structures, 2002, pp. 141-148.
14Hinrichsen, J., "A380---Flagship Aircraft for the New Century," SAMPE Journal, Vol. 38, No. 3, 2002, pp. 8-12.
]SGutowski, T. G., Neoh, E. T., and Polgar, K. C., Adaptive Frameworkfor Estimating Fabrication Time of Advanced Composite Manufacturing Processes, Technical Report, Laboratory for Manufacturing and Productivity, Massachusetts Institute of Technology, Cambridge, MA, 1995.