
Biomolecular Sensing Processing and Analysis - Rashid Bashir and Steve Wereley
.pdf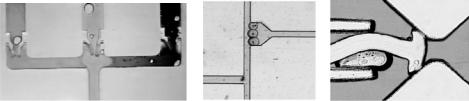
228 |
J. AURA GIMM AND DAVID J. BEEBE |
overview of materials and components, created using µFT methods, for handling fluids and carrying out processes is given in following sections.
11.3.4.1. Structural Components A typical lab-on-a-chip microsystem consists of analytical processes connected by fluidic pathways or channel networks. The channel walls also forms the skeleton of the microsystem, and are therefore fabricated from mechanically strong hydrophobic polymers. Since these materials provide the basic structure of the device, they are referred to as ‘construction materials’. Poly(iso-bornyl acrylate) and poly(bis-GMA) are the main members of this group of materials. These materials can be fabricated using liquid phase photopolymerization or laminar flow method, and display minimal change (5–10%) in volume after polymerization. Moreover, the polymerized structures show high tolerance to common organic solvents (like methanol, iso-propanol and acetone). These materials are also utilized to form ‘pillars’ or ‘posts’ that can provide mechanical support for other microfluidic components. The channel network can also be designed to function as a passive component. For example, a 3D serpentine channel network was used to improve the extent of mixing between laminar flow streams.
11.3.5. Valves
The ability to manipulate fluid flow using valves is essential in many microfluidic applications. There are two types of valves: passive valves that require no energy and active valves that use energy for operation. The type of valve used in a device depends on the amount and type of control needed for the application. Active valves often use external macroscale devices that control the actuation and provide energy. Some recent designs include an electromagnetically actuated microvalve [16] and an air-driven pressure vale [74]. Other active valve designs use energy from direct chemical to mechanical conversions or from the driving fluid, eliminating the need for external power. Rehm has demonstrated a hydrogel slug valve in which the driving force of the fluid moves a passive hydrogel slug to open or close an orifice [69]. Others have used stimuli responsive hydrogel materials that undergo volume changes through direct chemical to mechanical energy conversion. A variety of responsive hydrogel post valves [46] have been demonstrated. A responsive biomimetic hydrogel valve resembling the check valves found in veins has also been fabricated [79] as well as a hydrogel-based flow sorter device [11] that directs flow autonomously based on the pH of the stream (Figure 11.3). The hydrogel valves described here are practical due to the physics of the microscale. Since diffusion determines the
a |
b |
c |
FIGURE 11.3. Example of valves. Simple check valves (a), three hydrogel posts in swelling condition where they function as valves (b) [11], and “hammerhead” valve with spring force to physically closing the channel (c) [43].
MICROFLUIDIC TECTONICS |
229 |
response of the hydrogel, scaling effects make the hydrogel respond faster (on the order of seconds) when constructed with smaller dimensions and larger surface area to volume ratios.
Passive valves can be used to limit flow to one direction, to remove air, or to provide a temporary flow stop. Passive one-way valves (similar to the responsive bi-strip valve described above) have been constructed from both silicon and elastomers [35]. An alternative method of constructing passive valves involves the use of porous hydrophobic materials or surface treatments to create selective vents or flow stops, respectively. Vents control fluid movement by allowing air to pass but not the liquid being moved [2]. Hydrophobic surface patterning can also be used to create valve by making a section of channel hydrophobic [39].
An in situ polymerized hydrogel plug was utilized to create a ‘mobile’ valve inside a microchannel. The materials for the channel and the plug were chosen so that there is minimum adhesion between them. Upon applying high pressure, the hydrogel plug was moved in the microchannel to close specific channels. Although a high external pressure is required to move the plug, this approach gives the user freedom to open or shut channels based on the application. The deformability and mobility of hydrogel was combined to fabricate a ‘flat worm’ check-valve using µFT [43]. In this design, a hydrogel strip was anchored at one end, while the strip was free to move in and out of a constricted region or ‘valve neck’. This movement was brought about by the direction and internal pressure of the fluid stream. Thus by using responsive materials, various types of valves for can be created inside the microchannel.
11.3.6. Pumps
Pumping schemes incorporate many different physical principles [67]. The different types of pumps have drastically different features including flow rate, stability, efficiency, power consumption, and pressure head. A few examples of pumping schemes that use external control include a shape memory alloy micropump [13], a valve-less diffuser pump [3], a fixed valve pump [7] that uses piezoelectric actuation, and a self-filling pump based on printed circuit board technology [76]. Pumps can also be injection molded [15] to form inexpensive disposable pumping chambers that are externally actuated Magnetically driven pumps include a magnetically embedded silicon elastomer [41, 33], a magnetohydrodynamic micropump [45], and pumps driven by ferrofluidic movement [26, 62]. A micromotor that can valve, stir, or pump fluids was also developed that was controlled by external magnetic forces [6].
The physical processes that dominate at the microscale allow the creation of pumps that are not feasible on the macroscale. Some designs require no moving parts like a bubble pump [24] that relies on the formation of a vapor bubble in a channel, an osmotic-based pump [73], and an evaporation based pump that relies on a sorption agent to wick fluid through the channel [22]. The surface tension present in small drops of liquid can also be used to pump fluid. The passive pumping technique provides a means of moving fluid by the changes in internal pressure of liquid drops [76]. A smaller drop has a higher internal pressure than a larger drop. When a small drop is fluidically connected to a larger drop (i.e., through a microchannel), the fluid in the small drop will move towards the larger drop. In this manner, fluid can be passively pumped through microchannels simply by controlling the size of the drops on top of the microchannels.
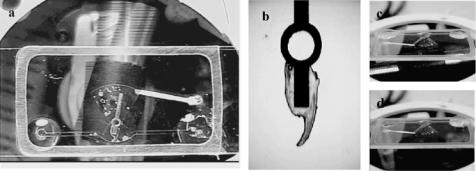
230 |
J. AURA GIMM AND DAVID J. BEEBE |
FIGURE 11.4. Ferromagnetic pump. The major components of the pump are external magnet, an actuator and microchannel (a). A closer view of the actuator that is composed of an iron bar and two separate layers of polymers
(b). The pump in action where the sizes of water drops change significantly in less than 5 seconds (c, d) [4].
Eddington et al. have demonstrated a self-regulating pump utilizing the pH responsive nature of the poly (hydroxyethyl methacrylate-acrylic acid) (HEMA-co-AA) hydrogel post where the feedback system is relayed to the responsive gel post on an orifice upstream [21]. Another recent pump is the oscillating ferromagnetic micropump that utilizes the centrifugal force (Figure 11.4) [4]. This pump relies on a magnetically driven actuator. The actuator is a direct drive as it converts the energy provided by a rotating magnetic field into linear propulsion of liquid without gears or additional parts. The volumetric flow can be easily controlled changing the spinning velocity of the external motor. Smaller micropumps and greater volumetric flow can be obtained by optimizing the geometry and position of the inlet and outlet channels.
11.3.7. Filters
In a microsystem, a filter is useful in sample preparation (e.g. remove blood cells from whole blood) and purification (e.g. chromatographic separation). Filters made of porous materials also provide a large area where surface-catalyzed reaction or detection of a sample may be carried out. Another function of a filter can be to provide docking stations to ‘hold’ a cell (e.g. ova, embryo) or other objects (e.g. bead, vesicle) in a known section of the microchannel. Using µFT methods a porous filter was prepared inside the microchannel by ‘emulsion photo-polymerization’ of a mixture consisting of monomer, porogen (e.g. water, salts), a cross-linker and a photo-initiator. By agitating the mixture, an emulsion consisting of monomer droplets was formed. Upon polymerization and further processing (e.g. drying to remove water), a contiguous polymer network surrounded by interconnected paths (pores) was formed. The size and distribution of pores, and the mechanical properties of the filter are dependent on a number of factors; including composition of pre-polymer mixture, polymerization technique and the surface energy of the channel walls. The large parameter space allows the filter property to be varied to fit the application.
The utilization of the fabricated filter to perform biological separation was explored in preparation of whole blood samples for diagnosis studies. Separation of blood cells from whole blood is required if the diagnostic device is to assay the body fluid directly from
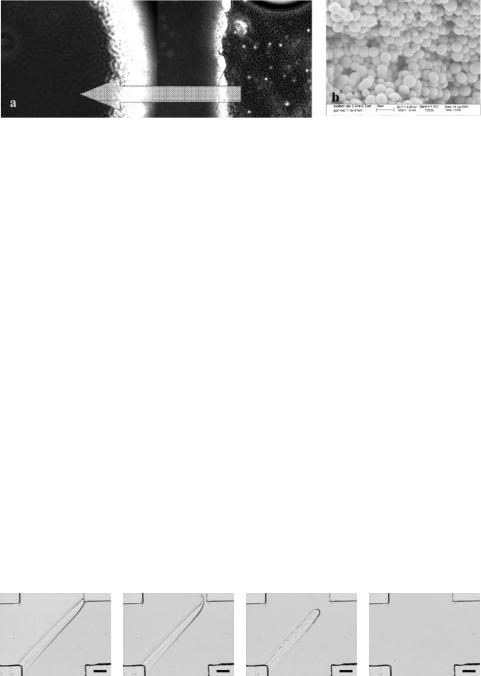
MICROFLUIDIC TECTONICS |
231 |
FIGURE 11.5. Photopolymerizable filter made with HEMA. The blood cells are separated from the serum (a) [58]. SEM image of internal filter structure (b).
the patient (or end user). The current methodology for separation is to use centrifuging techniques. However, this process is difficult for very small sample volumes (nL to a few mL) as the inertial forces diminish with reducing size. Moreover, centrifugation requires external power for operation and may be impractical in a portable diagnostic device. Separation by the porous filter was found to be as efficient as centrifuge techniques while retaining the advantage to address small volumes (Figure 11.5). A number of polymer-based monoliths that were initially targeted for capillary electrophoresis [63, 64] is being integrated into microfluidic platforms [58, 78]. Some have demonstrated novel encapsulation of proteins by functionalizing the monoliths [65].
11.3.8. Compartmentalization: “Virtual Walls”
Compartmentalization is a general term for creating compartments or separated units in a microsystem. In a broad sense, the construction of channel networks also creates compartments. Our focus is on temporary compartments, wherein the walls can be removed by an external stimulus. Temporary isolation will be important to prevent contamination from another process or reactant. The compartments can be formed either by fabricating a responsive polymeric structure or by changing the surface energy of an existing channel wall. Dissolvable physical walls have been fabricated by liquid phase photopolymerization using chemo-responsive hydrogels that contain disulfide crosslinkers (Figure 11.6) [80]. The disulfide bonds are cleaved in the presence of a reducing agent (e.g. tris (2-carboxyethyl) phosphine hydrochloride) causing the polymeric structure to dissolve away.
Since the surface energy of the channel walls can influence the flow profile inside the microchannels, by patterning hydrophobic and hydrophilic regions, temporary compartments
FIGURE 11.6. Demonstration of dissolvable hydrogels as selective sacrificial structures in microfluidic channel. The walls with disulfide crosslinkers dissolves away in presence of a reducing agent thereby controlling the direction of the flow. Scale bars 500 µm.
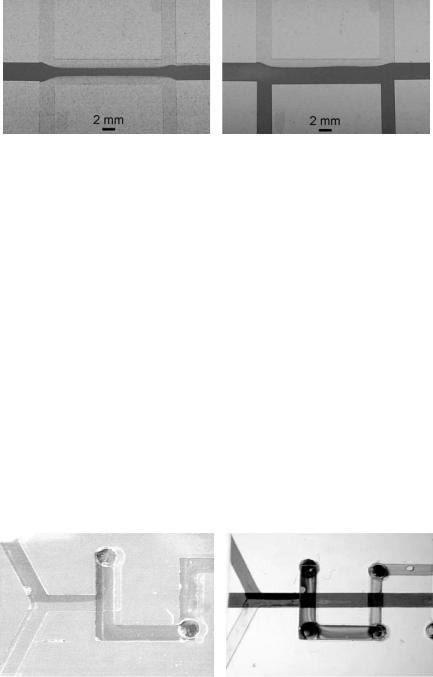
232 |
J. AURA GIMM AND DAVID J. BEEBE |
a |
b |
FIGURE 11.7. “Virtual” compartmentalization. Virtual wall compartmentalization can be achieved by multistream laminar flow surface patterning (a) or by UV photopatterning of photocleavable SAMs on glass surface (b) [81].
can be created. At low pressures, aqueous fluids are confined to hydrophilic regions, with the interfaces between the patterns acting as ‘virtual’ walls. However, the walls break down when the pressure is increased past the threshold allowing the fluid to flow throughout the channel. Such virtual walls have been realized by patterning hydrophobic regions with self-assembled monolayers (SAMs) using laminar flow method [81] or by photopatterning UV-sensitive SAMs [82] (Figure 11.7). The compartments created were removed by increasing the pressure of the fluid. The threshold pressure to break the wall is dependent on the difference of surface energies between the hydrophobic and hydrophilic adjacent regions. Multiple compartments with different threshold pressures can be created by patterning the channel walls with different surface energies.
11.3.9. Mixers
Mixing at the microscale is an ongoing challenge [40]. A unique characteristic of fluids at the microscale is the presence of laminar flow. However with laminar flow, there is no turbulence, and mixing does not readily occur. At the microscale, the channel dimensions lead to low Reynolds numbers where mixing occurs only by diffusion. Most mixers fall into two categories, active and passive. Passive mixers generally utilize set channel geometry to enhance diffusion and have the benefit of no moving parts (Figure 11.8). Active mixers
a |
b |
FIGURE 11.8. Passive chaotic mixer. Two-layer passive mixer (a) and three-layer passive mixer around another channel (the straight channel going left right) (b). Such a ‘wrap’ around a channel could be used to regulate temperature [55]. Channel width 500 µm.

MICROFLUIDIC TECTONICS |
233 |
FIGURE 11.9. Active magnetic mixer shown before mixing begins (a), during mixing (b) at a flow rate of 2 mL/min [54]. Channel width 1 mm.
generally require an external power source and moving parts to accomplish mixing. Active mixers have the advantage that the user has the ability to control if and when mixing occurs. Traditionally, active mixers have been based on MEMS technology that requires expensive fabrication techniques and cleanroom facilities. Inline magnetically actuated stirrers have been previously described in the literature using an electromagnetic micromotor [6] and micromachined mixers [48]. While these mixers show magnetic actuation using external fields, the size of the stir bar limits the effective volume that can be mixed. Recently another mixer based on magnetic actuation has also been presented [32] based on a wire placed inside tubing.
Using liquid phase photopolymerization an active, magnetically controlled micromixer can be made that is inexpensive and easy to fabricate without the need for cleanroom facilities [53]. A magnetic mixing device is made by positioning a blade inside a cavity, filling the cavity with prepolymer, and exposing the device to UV to form the channel network, followed by polymerization of a post inside the hole of the blade. The blade is actuated by a common stir-plate, giving the user a convenient method of controlling the mixing in the device (Figure 11.9). The ease of fabrication lets the user customize the mixer so that the mixer operates efficiently within the constraints of the channel network. This type of mixer has also been shown to lyse cells due to the high shear [53].
11.3.9.1. Sensing Components The development of microchannels resulted in the need for sensing and measuring capabilities at the microscale. The need for sensing in microfluidics falls into two general categories.
First, one needs to measure the output of the device or system. Reducing volumes for chemical or biological assays to the microscale is of little use if there is no way to determine results quantitatively as in the macroscale. Reducing the sample size means reducing the amount of material to detect and increases the need for greater sensitivity. Creating sensors or sensing capabilities that are more responsive and smaller in size is an ongoing challenge at the microscale.
Second, one needs to measure the physics and chemistry of flow in microfluidic devices in order to understand and improve device and system designs. Quantifying both electrokinetic and pressure driven flow characteristics inside micro channels is critical to providing a basic science foundation upon which the field of microfluidics can grow [17].
234 |
J. AURA GIMM AND DAVID J. BEEBE |
Within the framework of µFT several approaches to sensing have been explored. In following sections we will focus on methods and techniques that have been developed within the framework.
11.3.10. Hydrogel as Sensors
Responsive materials, such as hydrogels, have the ability to change their properties based on environmental conditions. These materials have been explored for fabrication of microfluidic components that can function autonomously, i.e. requiring no external control.
Hydrogels have been around for about fifty years and recently, these materials are being extensively studied for use in drug delivery and as tissue scaffolds [30]. Hydrogels are a class of cross-linked polymers that have the ability to ‘absorb’ water. Responsive hydrogels can undergo phase transitions, wherein large changes in the volume can occur due to an external stimulus. The stimulus can be the presence of specific ions (e.g. pH), chemical or biological agents [56], or a change in temperature or an applied electric field [61]. The stimulus (of a responsive hydrogel) changes the polymer backbone, which then affects the movement of water and ions in and out of the polymer matrix. Two well-studied responsive hydrogels are those that are sensitive to temperature and pH changes. While in the temperature sensitive hydrogel (e.g. poly(NIPAm)), the movement of water is initiated by change in hydropathy of the backbone, in the pH sensitive hydrogel (e.g. poly(HEMA-co-AA)), the movement of water is initiated by ionization of the backbone. The time scales for the volume change will depend on the distance traveled or the initial size of the hydrogel. The change in volume can provide a mechanical force; thus transducing a chemical stimulus into a mechanical action. The factors affecting the force are the dimension of the hydrogel structure, chemical composition of the polymer matrix and the environmental conditions. Responsive hydrogels have been explored for use as sensors, or as actuators, or both. While hydrogels undergo phase transition with changes in environmental conditions, there also exist materials that can self-assemble in various geometries depending.
11.3.11. Sensors That Change Shape
The phase transition in a responsive hydrogel is brought about by changes in specific groups on the polymer backbone. In pH responsive hydrogel, this change is the ionization of a chemical group (e.g. carboxylic acid, amine) (Figure 11.10). Another way to engineer responsiveness is to incorporate cross-linker that can be cleaved by chemical or enzymatic reactions; resulting in volume change or disintegration of the hydrogel. Yu et al. have demonstrated a chemo-responsive hydrogel in the µFT platform. The cross-linker (N, N’- cystamine-bisacrylamide) contains disulphide bonds, which was broken in the presence of a reducing agent (e.g. dithiothritol); leading to disintegration or ‘dissolving’ of the hydrogel [80]. Yet another way to realize detection (as a structural change) is to create hydrogels where the matrix is held by specific interaction. For example, Miyata and coworkers have developed a bio-responsive hydrogel where the cross-links are formed by antigen-antibody interaction. In the presence of a free antigen, the cross-links are ‘dissolved’, resulting in volumetric expansion of the structure, and thus recognition of the specific antigen. The selectivity of detection thus depends on the type of cross-linker and the sensitivity will depend on the density of the cross-linker in the polymer matrix. The disappearance or volume
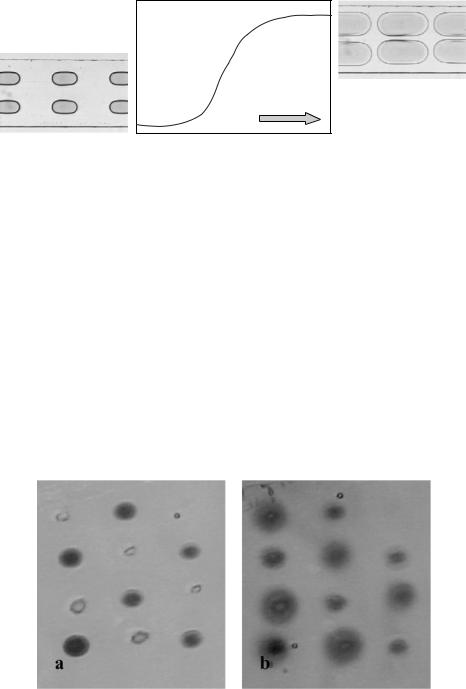
MICROFLUIDIC TECTONICS |
235 |
Normalized
Volume
pH
FIGURE 11.10. pH-sensitive hydrogel sensors. Typical volume change seen with pH responsive hydrogels like HEMA-AA (2-hydroxyethyl methacrylate—acrylic acid). Channel width 1 mm.
change in the hydrogel sensor can be easily visualized without other instrumentation. An unaided human eye can detect the disappearance of a 100 um circle or a few 10’s of µm change in diameter of a post within a microchannel. Alternatively, the action (dissolution or volume change) can be used to trigger a color producing reaction.
11.3.12. Sensors That Change Color
Color change is easily perceived by the human eye and this simple detection mechanism can be exploited by entrapping ion-sensitive dyes in a hydrogel matrix. Both the dye and the hydrogel have a specific response function to the local environment, changes in which are reflected in the color and size of the readout structure. A combinatorial readout display consisting of a layout of different dyes was fabricated using liquid phase photopolymerization, and tested to display pH changes inside the microchannel (Figure 11.11) [57]. The basic colorimetric format was extended to include biomolecule detection and chemical reactions by entrapping proteins in the polymer (unpublished). One advantage of using the
FIGURE 11.11. Colorimetric pH-sensitive readouts. Combinatorial pH sensor with alternate patterns of Congo Red and Phenophthalein dyes immobilized in hydrogel mix, in acidic solution (a) or in basic solution (b) [57].
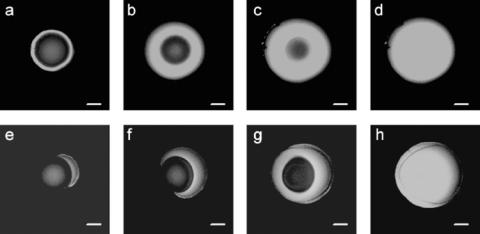
236 |
J. AURA GIMM AND DAVID J. BEEBE |
dye-immobilized-gel construct is that the high volume support of the hydrogel provides sufficient color signal intensity to allow perception by the naked eye, unlike surface immobilized dyes that typically require optical/electronic detection due to low intensities. The wide availability of dyes sensitive to both chemical and biological agents will allow extension of this idea to many applications such as rapid screening of combinatorial libraries. Moreover, polymer matrices responsive to other stimuli like temperature can be chosen to provide readouts that are sensitive to multiple parameters.
11.3.13. Cell-gel Sensors
Cells respond to various types of stimuli—physical forces, temperature, and chemical and biological molecules. Cells are being explored as potential biosensors for the recognition of pathogens. However, using cells comes with a cost, maintenance of appropriate environments and supply of nutrients. To produce sensors that have the similar capability as the cells, “artificial cells” have been developed in the µFT platform by overlaying a monolayer of amphiphilic molecules around a responsive hydrogel [44]. The lipid molecules protect the hydrogel from external environment in a cell-like manner. When the monolayer is disrupted due to mechanical stress or chemical molecules; the hydrogel is exposed to the environment (Figure 11.12). If the environment favors phase transition or a color change, a response can be detected. The cell-gel system can be modified to detect specific molecules by embedding surface receptors in the lipid layer so that upon recognition, the monolayer is disrupted. As the lipid layer and the hydrogel are responsive to different stimuli, cell-gel sensors are activated only in the presence of both stimuli. This mechanism may help ensure that there are minimal false positives. Moreover, this construct provides with a large parameter space, as various combinations of the stimuli-sensitive materials can be engineered into the component. A similar mechanism can be found in many biological processes, where at least two
FIGURE 11.12. Effect of lipid modification on µgel sensor. The presence of elevated pH solution is signaled by an increase in fluorescence emission. With an unmodified µgel, the expansion starts at the exterior of the gel (a), and moves inward (b, c, d). In contrast, when lipid-modified µgel, permeation began in a localized site (e) and spread asymmetrically (f, g, h). Scale bar 200 µm.
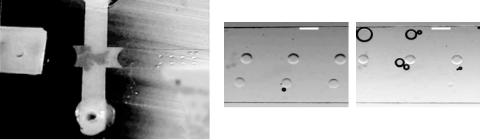
MICROFLUIDIC TECTONICS |
237 |
50 |
50 |
0 |
0 |
|
|
m |
m |
b |
c |
a
FIGURE 11.13. Liposome sensor relay. Functionalized liposomes are captured by the emulsion filter. Normal and responsive gel posts are seen down stream (a). As liposomes were lysed upstream the responsive gel posts with disulfide crosslinkers dissolve away (b, c after 14 minutes) [25]. Channel width approximately 2 mm.
signals are required to elicit a response. For example, T-cells (in the immune system) require recognition of two signals simultaneously to activate it against tumor or virus-infected cells.
11.3.14. Liposome Sensor
Relying completely on the responsive hydrogel can limit the types of signals and molecules that may be detected. For each type of signal, the raw materials for the hydrogel must be created individually, which can be both difficult and time-consuming. A more efficient method would be to use a ‘signal transfer’ mechanism commonly seen in signaling cascades of biological systems. This mechanism allows for the sensitivity of one interaction to initiate a common cascade; and in most cases, the signal is amplified during the transfer. For example, in cells, while there are various receptors in the cell membrane that are sensitive to specific molecules, the binding event is relayed to the nucleus via a common kinase pathway. A similar strategy has been developed using the µFT platform, wherein functional liposomes (lipid vesicles) were used in conjugation with a responsive hydrogel (Figure 11.13). The liposome contained the stimulus for the hydrogel and was held by a porous filter, upstream from the hydrogel. In the presence of an external signal (chemical or biological), specific reactions were initiated at the surface of the liposome, leading to its lysis and subsequent spilling of the contents, thus relaying the signal to the hydrogel [25].
11.3.15. E-gel
The volume change of a hydrogel under the influence of electricity has been reported previously, however their application for use in microfluidic systems has only been recently investigated. Although one of the main advantages of hydrogel actuators is their ability to change volume without electronic controls, it would be shortsighted to entirely dismiss electronics integrated with hydrogels due to the ubiquitous nature of electronics. By coupling simple electronic circuits with hydrogel actuators, we can combine the main advantages of both platforms such as ease of fabrication with precise control over system performance. Bassetti et al. demonstrated the use of square voltage waveforms with varying pulse widths to precisely control the volume of a poly(HEMA-AA) hydrogel actuator (Bassetti, Submitted) as shown in Figure 11.14. The voltages used for the study were low (5-12 V) and could be easily integrated into a microfluidic system.