
1270
.pdfВ ходе сравнительного исследования предела изгибной прочности σb образцов различных марок твердых сплавов, проведенных на прессе Амслера, установлено, что наибольший предел изгибной прочности имеет также сплав ВК8 (рис. 16, в).
Анализ данных Г.С. Креймера показал, что предел усталостной прочности σ–1 имеет также наибольшее значение у сплава ВК8 (1 210 МПа). Твердый сплав ВК6 имеет 1 160 МПа, а сплав Т15К6 – 780 МПа. По данным Г.С. Креймера, твердый сплав ВК8 имеет также
и большее значение ударной вязкости (Qn = 0,25 кгс·м/см2), чем, например, сплав ВК6 (Qn = 0,2 кгс·м/см2) или Т15К6 (Qn = 0,05 кгс·м/см2).
Известно также, что твердый сплав ВК8 менее дефицитен, чем, например, сплав ВК10-ОМ. Кроме того, сплав ВК8 нашел широкое применение на многих машиностроительных предприятиях для изготовления резцов, фрез, зенкеров, разверток и других режущих инструментов. Отработанная в течение многих лет технология массового изготовления пластинок из этого твердого сплава, а также технологии напайки и заточки позволяют надеяться на успешное применение их и для такого сложного многозубого инструмента, как протяжки. Поэтому для проведения комплекса исследований и реализации скоростного протягивания деталей газотурбинных двигателей выбран твердый сплав ВК8.
Оптимальные геометрические параметры быстрорежущих и твердосплавных протяжек выбирались при предварительных испытаниях. Известно, что для обеспечения низкой величины шероховатости сталей 1-й группы необходимо увеличивать передний угол зубьев протяжек до 15°…20°. Задний угол необходимо также увеличивать до 5°…7°. Однако при такой геометрии уменьшается прочность режущей кромки, появляется выкрашивание и быстрый износ протяжек. Поэтому оптимальными геометрическими параметрами быстрорежущих протяжек были следующие: передний угол 12°, задний угол 3°, подача на зуб на предварительных секциях
0,06…0,10 мм, на окончательных 0,02 мм. |
|
Для сравнительных испытаний при протягивании |
деталей |
из титановых, жаропрочных деформируемых и литейных |
сплавов |
|
71 |
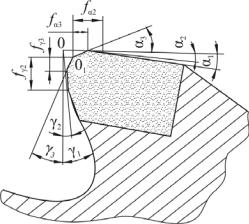
на никелевой основе быстрорежущие протяжки затачивались следующим образом: передний угол 5°, задний угол 5°, подача на зуб предварительных секций 0,06 мм, окончательных секций 0,01 мм.
Определение оптимальной геометрии твердосплавных протяжек проведены при предварительных стойкостных испытаниях при протягивании сплава ЭИ787-ВД на скорости 26 м/мин с подачей 0,06 мм/зуб, с заточкой переднего угла 20°, 15°, 10°, 0°, –5° и заднего 3°, 6°, 9°. Оценка работоспособности производилась по интенсивности выкрашивания зубьев. Наименьшее выкрашивание обнаружено у протяжек с передним углом 0° и задним углом 6°. Испытания показали также более устойчивую работу твердосплавных протяжек с фасками по передней и задней граням.
Исходя из вышеизложенного выбран следующий оптимальный вариант геометрических параметров твердосплавных протяжек (рис. 17): передний угол γ = 0°, задний угол α = 6°, ширина фасок f по передней и задней граням fα3 = fγ3 = 0,1 мм, угол заточки фасок γ3 = α3 = –5°. Для облегчения переточек введены дополнительные углы γ1 = α1 = 10° на расстоянии fα2 = fγ2 = 1…2 мм.
Рис. 17. Оптимальная схема заточки твердосплавных протяжек для обеспечения наибольшей стойкости
72
Заточка протяжек производилась на заточных станках модели 360М (модернизированных для повышения точности) алмазными кругами формы А1Т и АЧК на органической связке Б2 зернистостью АС8-АС6 со 100 %-ной концентрацией на следующих режимах: скорость круга Vкр = 25…30 м/сек, глубина шлифования
t= 0,005…0,010 мм/ход, продольная подача Sпрод = 2…3 м/мин.
2.3.Методы исследования износостойкости протяжек, температурно-силовых и адгезионных явлений процесса резания при протягивании
Исследование обрабатываемости жаропрочных сплавов проводилось путем определения закономерностей износа протяжек при различных режимах протягивания. Из всех величин, характеризующих износ, выбрана, как наиболее рациональная, ширина фаски износа по задней поверхности hз. С увеличением длины пути резания ширина фаски износа hз непрерывно и закономерно возрастает, что приводит к соответствующему изменению сил резания, параметров качества, физико-химических свойств и точности протянутой поверхности. Измерение фаски износа по задней поверхности hз производилось при помощи микроскопа МИР-2 с микронасадкой АМ9-2 с ценой деления 0,002 мкм и микроскопа ПМТ-3 при увеличении до ×300 (рис. 18). Фотографирование характера износа и разрушения кромок производилось с помощью фотоаппарата на этих микроскопах.
Измерение средней температуры контакта производилось методами естественной термопары. Тарирование естественной термопары производилось с помощью специальной тарировочной головки.
На рис. 19 и 20 представлены схемы измерения температуры резания на вертикально-протяжном станке 7Б74 с помощью естественных и искусственных термопар.
73
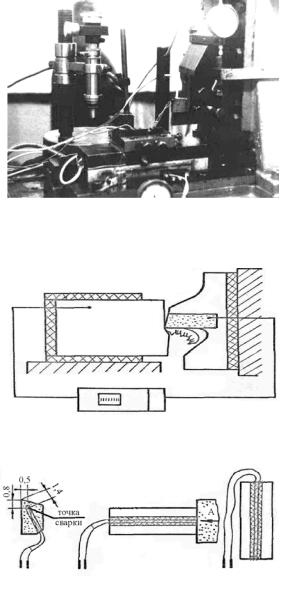
Рис. 18. Общий вид зоны протягивания, измерения износа протяжки, температуры и силы резания на скоростной установке УСП-1
Рис. 19. Схема измерения температуры резания при протягивании методом естественной термопары
Рис. 20. Схема измерения температуры резания при протягивании методом искусственных термопар
74
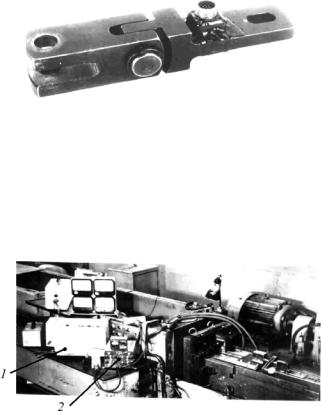
Измерение составляющих сил резания Pz и Ру в лабораторных условиях осуществлялось с помощью тензометрических датчиков, встроенных в установку УСП-1 и в зажимное приспособление на станке 7Б74. Измерение тангенциальной составляющей силы резания Рz в процессе протягивания деталей ГТД многосекционными протяжками в производственных условиях на горизонтально протяжных станках 7А540 и 7А520 проводилось с помощью специально разработанного тягового динамометра ПДМ -1 (рис. 21).
Рис. 21. Специальный тяговый динамометр ПДМ-1 для измерения силы резания в производственных условиях
На боковые поверхности динамометра ПДМ-1 наклеивались тензометрические датчики. Динамометр, рассчитанный на усилие до 100 кН, устанавливался и закреплялся между блоком протяжек и тяговым штоком гидроцилиндра горизонтально-протяжного станка. Сигналы от тензодатчиков усиливались прибором ТА-5 и записывались на пленку шлейфового осциллографа Н115 (рис. 22).
Рис. 22. Общий вид измерения и записи силы резания при протягивании замков лопаток на горизонтальнопротяжном станке мод. 7А540: 1 – осциллограф Н115, 2 – усилитель ТА-5
75
Тарировка динамометра производилась при растяжении на прессе Амслера с усилием до 120 кН. Конструкция динамометра обеспечивает надежную работу в производственных условиях на длительное время и не оказывает влияния на качество протягиваемых деталей. Запись температуры и сил резания на осциллограф является вынужденной мерой из-за быстротечности процесса резания при протягивании.
2.4.Особенности методики исследования основных параметров качества поверхностного слоя
иусталостной прочности протягиваемых деталей
влабораторных и производственных условиях
Измерение технологических напряжений, возникающих при протягивании в деталях, а также определение усталостной прочности деталей производилось с помощью тензометрических датчиков, наклеенных на самые опасные с точки зрения трещинообразования поверхности деталей.
Контроль шероховатости протянутых поверхностей образцов производился с помощью микроскопа МИС-11 непосредственно на установке УСП-1. Шероховатость обработанных поверхностей деталей измерялась на вырезанных образцах при помощи профило- графа-профилометра мод. 201 и прибора Н133.
Для измерения глубины и степени наклепа протянутых поверхностей использовался микроскоп ПМТ-З и метод косых шлифов. Измерение величины и характера распределения остаточных напряжений по глубине поверхностного слоя производилось на вырезанных из деталей прямоугольных образцах с помощью прибора ПИОН-2 при травлении поверхностного слоя по методу Н.Н. Давиденкова. Усталостные испытания деталей производились на различных вибродинамических стендах типа ВЭДС-200А. Анализ микроструктуры материалов и процессов стружкообразования производился с помощью металлографического микроскопа МИМ-7. Для измерения тангенциальной
76
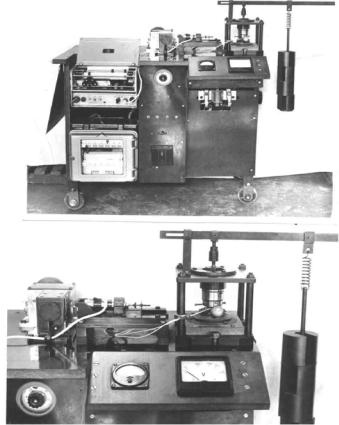
прочности адгезионных связей между инструментальным и обрабатываемым материалами использовался адгезиомер УОМИМ-1 (рис. 23). Исследование дефектов поверхностного слоя обработанных деталей и характера износа зубьев протяжек производилось с помощью электронного микроскопа ЭМВ-100Л. Исследование изменений поверхностного слоя деталей как следствия адгезионных явлений
Рис. 23. Общий вид адгезиомера УОМИМ -1 для исследования адгезионных явлений, имитирующих процесс резания
при протягивании
77
между обрабатываемым и инструментальным материалами, производилось с помощью рентгеноспектрального химического анализа на установке МАР-2. Фиксация быстропротекающих процессов стружкообразования производилась с помощью скоростной кинокамеры СКС-1М. Использовались методы математической статистики и планирования экспериментов. Математические расчеты производилась с помощью ПЭВМ.
2.5.Контрольные вопросы
1.Почему некоторые материалы называются труднообрабатываемыми?
2.На какие группы разделены все труднообрабатываемые материалы?
3.Как изменяются прочностные и пластические свойства материалов с увеличением температуры испытаний на растяжение?
4.Какие методы модернизации протяжного оборудования вы
знаете?
5.В чем суть метода измерения износа инструмента?
6.Какова методика выбора оптимальной марки инструментального материала для протяжек?
7.Рациональная геометрия зуба твердосплавной протяжки.
8.Какие методы измерения температуры резания вам известны?
9.Какие методы измерения силы резания вам известны?
10.Какие методы исследования адгезионных явлений в зоне резания вам известны?
11.Какие методы исследования параметров качества поверхностного слоя вам известны?
78
Глава 3 ИССЛЕДОВАНИЕ ФИЗИЧЕСКИХ ЯВЛЕНИЙ ПРОЦЕССА РЕЗАНИЯ И УСТАНОВЛЕНИЕ
ОПТИМАЛЬНЫХ РЕЖИМОВ ПРОТЯГИВАНИЯ ДЛЯ РАЗЛИЧНЫХ ГРУПП ТРУДНООБРАБАТЫВАЕМЫХ СТАЛЕЙ И СПЛАВОВ
3.1. Установление наиболее благоприятных температурных зон резания с позиции снижения прочностных
ипластических свойств сталей
исплавов при их нагреве
При рассмотрении вопросов трения и износа режущих инструментов необходимо иметь представление о прочностных и пластических изменениях в контактных слоях трущихся пар. Последнее в значительной степени зависит от температуры этих слоев, микроструктуры металла и характера взаимодействия дислокаций с элементами этой структуры.
Исследования процессов резания жаропрочных сталей и сплавов при точении и фрезеровании твердосплавными режущими инструментами, проведенные различными авторами, показывают, что температура в зоне резания достигает 973…1 273 К.
Несмотря на то, что время контакта стружки с инструментом измеряется тысячными долями секунды, а скорость нагрева при резании составляет 106 град/с, металлографический анализ зоны трения показывает, что в ряде случаев успевает происходить фазовое превращение в контактных слоях.
На первом этапе исследований процесса протягивания было предположено, что при протягивании с увеличением скорости резания и ростом температуры резания существует вполне определенное термодинамическое состояние зоны резания каждого режущего элемента многозубой протяжки, при котором могут наблюдаться наиболее благоприятные параметры износа протяжек и качества обработ-
79
ки. Это состояние определяется характерной для данной пары температурой инструментального и обрабатываемого резания, называемой
вдальнейшем оптимальной.
Сцелью определения влияния температуры на основные механические свойства исследуемых обрабатываемых материалов проводились испытания при одноосном растяжении круглых стандартных образцов на прессе Амслера с записью кривой деформации в диапазоне температур 293…1 273 К. На рис. 24, 25, 26, 27 приведены графики изменения механических свойств жаропрочных сталей и сплавов в зависимости от температуры испытаний.
Анализ данных, приведенных на этих графиках показывает, что изменение прочностных и пластических свойств различных сталей и сплавов носит сложный характер, имеющий свои особенности для каждой группы обрабатываемых материалов. Общей закономерностью для всех испытанных сталей и сплавов является снижение прочностных свойств с увеличением температуры испытаний. Причем для жаропрочных сталей ЭИ481Ш и ЭИ961Ш (см. рис. 24, а, б)
предел прочности σb резко уменьшается при невысоких температурах нагрева 600…800 К до 400…600 МПа с первоначальных значений 1 000…1 200 МПа при комнатной температуре, т.е. в 2–2,5 раза.
Аналогичное резкое снижение прочности выявлено у титановых сплавов ВТ3-1 и ВТ18У (см. рис. 25, а, б). При увеличении температуры испытания до 800…850 К предел прочности снижается с 1 000…1 100 МПа до 500…800 МПа (особенно резко для сплавов ВТ3-1 и ВТ8М), т.е. в 1,2–2 раза.
Жаропрочные деформируемые сплавы на железоникелевой основе ВЖ102 и ЭИ787 имеют тенденцию резкого снижения прочности при несколько большей температуре испытаний (порядка 873…973 К) (см. рис. 26, а, б). При этих температурах предел прочности снижает-
ся с 1 100…1 200 МПа до 800…900 МПа, т.е. на 20…30 %.
Жаропрочные деформируемые сплавы на никелевой основе ЭП109-ВД, ЭП742-ПД, ЭИ437БУ-ВД и ВЖ122 сохраняют повышенную прочность 900…1 400 МПа до температуры испытания 973 К.
80