
1270
.pdf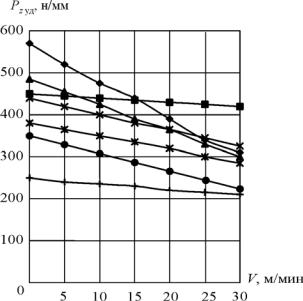
участке чистового блока на 6 %, на втором – на 25 %, а на третьем – на 27 %.
Таким образом, в процессе производственных исследований при протягивании конкретных деталей – дисков и лопаток ГТД – был подтвержден факт снижения сил резания на всех секциях многосекционных блочных протяжек с увеличением скорости резания от 0,5 до 30,0 м/мин для всех обрабатываемых материалов. На основе статистического системного анализа лабораторных и производственных исследований рассчитаны средние значения удельных сил резания qz и qy в зависимости от скорости резания V и подачи Sz. Результаты приведены в табл. 19 и на рис. 69.
Рис. 69. Влияние скорости резания V на удельную составляющую силы резания Рz уд при протягивании жаропрочных сталей ЭИ961Ш и ЭИ481Ш, деформируемых жаропрочных сплавов ЭИ787-ВД, ЭП109-ВД, ВЖ122 и литейного жаропрочного сплава ВЖЛ14 (ВК8, 0,02 мм/зуб)
ВЖЛ14,
ЭИ961Ш,
ЭИ481Ш,
ВЖ122,
ЭП109-ВД,
ЭИ787-ВД,
ВТ3-1
171
|
|
|
|
|
|
|
|
|
|
|
|
|
|
Таблица |
1 9 |
||
|
|
Значения удельных сил резания qz qy (н/мм) |
|
|
|||||||||||||
Группы |
1-я (стали жар.) |
2-я (титан. спл.) |
3-я(деф. сплавы) |
4-я (лит. сплавы) |
|||||||||||||
V, |
1,5 |
30 |
1,5 |
30 |
1,5 |
|
30 |
1,5 |
30 |
||||||||
м/мин |
|
||||||||||||||||
Sz, |
qz |
qy |
qz |
qy |
qz |
qy |
qz |
qy |
qz |
qy |
qz |
|
qy |
qz |
qy |
qz |
qy |
мм/зуб |
|
||||||||||||||||
0,01 |
404 |
192 |
415 |
170 |
202 |
202 |
196 |
190 |
372 |
209 |
291 |
140 |
444 |
185 |
296 |
130 |
|
0,03 |
479 |
255 |
447 |
234 |
274 |
226 |
240 |
214 |
511 |
279 |
349 |
186 |
612 |
250 |
423 |
180 |
|
0,05 |
510 |
281 |
472 |
250 |
350 |
240 |
315 |
235 |
622 |
360 |
510 |
215 |
620 |
256 |
459 |
194 |
|
0,10 |
550 |
310 |
500 |
269 |
500 |
280 |
440 |
247 |
800 |
620 |
740 |
320 |
665 |
280 |
580 |
240 |
3.5.Влияние режимов протягивания на характер изменения временных технологических напряжений в обрабатываемых деталях
Впроцессе протягивания деталей ГТД под действием сил резания возможно появление временных значительных растягивающих напряжений в местах крепления деталей в приспособлении. Это может привести к образованию микротрещин в поверхностном слое обрабатываемых деталей в точках крепления.
Для исследования характера временных напряжений, возни-
кающих в пере лопатки компрессора 1 от усилия зажима Рзаж и трех радиальных сил резания от боковых протяжек 2 и 5 и подошвенной протяжки 4, закрепленных в блоке 3 (рис. 70, а) на более напряженной выходной кромке пера лопатки наклеивались тензометрические дат-
чики Д1 на спинку пера и Д2 на корытце пера (рис. 70, б). Для экспериментов отобрана партия лопаток из сплава ЭИ787-ВД, прошедших одинаковую термообработку. Включение тензодатчиков производилось по полумостовой схеме, где для компенсации температурных
ипобочных силовых деформаций подключались компенсационные тензодатчики, наклеенные на компенсационную плиту из этого же материала. Таким образом, из сигнала рабочего тензодатчика выделялась
информация только о продольном действии сил и напряжений, т.е. вдоль выходной кромки пера лопатки. Выходная кромка пера
172
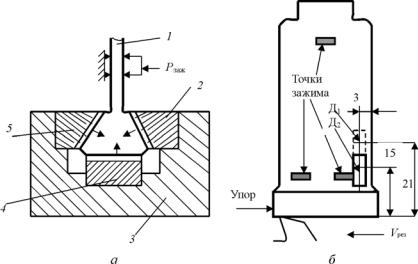
лопатки выбрана не случайно. Ее толщина обычно не превышает 1…2 мм. Именно на этой кромке пера обнаружены трещины при эксплуатации лопаток. Кроме того, при протягивании замка лопатки в этом месте по расчету возникают наибольшие технологические растягивающие напряжения.
Рис. 70. Схемы действия на перо лопатки 1 радиальных сил резания от протяжек 2, 4 и 5, входящих в блок 3 (а), и наклейки тензодатчиков Д1 и Д2 на выходную кромку пера лопатки для измерения временных напряжений при протягивании (б)
На рис. 71 показаны типичные осциллограммы записи напря-
жений в пере лопатки при |
протягивании хвостовиков лопаток |
из титанового сплава ВТ3-1 |
по обычно применяемой технологии |
(Р18, V = 2 м/мин) иприскоростномпротягивании(BК8, V = 26 м/мин). Сравнение этих осциллограмм с осциллограммами записи осевых сил резания Рz свидетельствует о непосредственном влиянии сил резания на изменение технологических напряжений σл в пере лопатки. Увеличение или уменьшение сил резания приводит к соответствующему увеличению или уменьшению напряжений в пере. Анализ показал, что на осциллограммах записи напряжений в пере лопатки
173
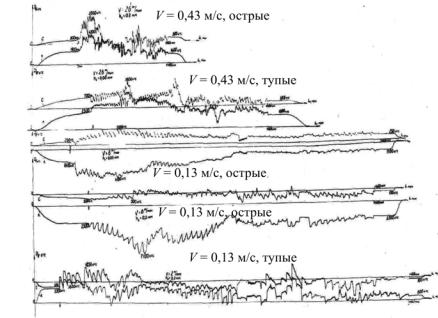
Рис. 71. Типичные осциллограммы записи временных технологических напряжений в пере лопатки из титанового сплава ВТ3-1 на различных скоростях резания при протягивании острыми и затупленными многосекционными протяжками со стороны корыта пера
и со стороны спинки пера
можно различить несколько характерных участков. Первый (начальный) участок характеризует напряжения растяжения в пере в результате зажима пера в приспособлении перед протягиванием. Последующие три-четыре участка характеризуют изменения напряжений от действия последовательно первой, второй и третьей секций протяжного блока. На последнем участке осциллограмм показано изменение напряжений в пере при разжиме детали после протягивания.
Впервые удалось проследить влияние условий зажима деталей на возникновение и изменение технологических напряжений в обрабатываемых деталях. Оказалось, что в момент зажима в пере лопатки
174
возникают напряжения даже большие по величине, чем в момент протягивания. Усилия зажима пера Рзаж, действующие на точки зажима ложементов (см. рис. 71), пытаются распрямить закрученное перо лопатки. Особенно велики эти напряжения при плохой подгонке противоположных точек зажима ложементов со стороны спинки и со стороны корыта пера лопатки.
Проведенный статистический анализ напряжений, возникающих в пере лопатки при зажиме, показал, что распределение величин технологических напряжений при зажиме подчиняется нормальному закону распределения. Уравнение графика распределения напряжений при зажиме лопатки в приспособлении имеет вид
f (σ) = 15 10−4 exp[−7 10−6 (σл −59,1)], |
(64) |
где σл – переменное случайное напряжение в пере лопатки. Построенные графики экспериментального и расчетного рас-
пределения напряжений σл свидетельствуют о близком совпадении значений. Стабильная работа зажимного устройства позволяет более объективно сравнивать напряжения в пере, возникающие при потягивании замков лопаток на различных режимах. В результате анализа работы зажимных приспособлений удалось внести некоторые изменения в конструкцию и снизить величину напряжений растяжения в пере лопатки. В дальнейшем было предложено применить заливку пера лопаток в специальную капсулу легкоплавким сплавом и зажим производить по наружной поверхности капсулы. Из осциллограмм напряжений в пере лопаток при протягивании замков на последующих участках после зажима (см. рис. 62) видно, что наибольшие растягивающие напряжения (106 Мпа) зафиксированы на участке первой секции затупленных протяжек при обработке по серийному варианту (Р18, 2 м/мин).
В сумме с напряжениями от зажима лопатки общее максимальное растягивающее напряжение в пере достигает 229 МПа.
На рис. 72 представлены графики зависимости средних значений напряжений в пере лопаток σл от скорости резания при протяги-
175

Рис. 72. Влияние изменения скорости протягивания V на величину средних растягивающих напряжений σл, возникающих на выходной кромке пера лопаток при протягивании хвостовиков лопаток острыми и затупившимися протяжками (ЭИ787-ВД, ВК8)
hз = 0,04 мм,
hз = 0,2 мм
вании лопаток из сплава ЭИ787-ВД. С увеличением скорости резания с 2 до 26 м/мин σл уменьшается с 44 до 39 МПа при использовании острых протяжек, т.е. на 13 %. При затуплении протяжек до hз = 0,2 мм напряжение σл увеличивается на 40…50 %. Однако с увеличением скорости резания с 2 до 26 м/мин σл также уменьшается с 60 до 43 МПа, т.е. на 40 %. Следовательно, обработка замков лопаток из жаропрочных сплавов на оптимальных режимах резания обеспечивает снижение вредных растягивающих технологических напряжений, вероятность появления микротрещин в пере лопаток и более высокую надежность обрабатываемых деталей.
176
3.6.Контрольные вопросы
1.Как изменяются прочностные и пластические свойства металлов с увеличением температуры испытаний?
2.Что такое «провал пластичности» металла и как использовать его для оптимизации процесса резания?
3.Каковы особенности появления теплоты при протягивании многозубым инструментом?
4.В чем заключаются особенность моделирования тепловых процессов численным методом?
5.В чем заключаются особенности расчета оптимальной температуры резания?
6.Что представляет собой метод математического планирования экспериментов при определении оптимальных условий протягивания?
7.Как влияет скорость резания на изменение усилий резания при протягивании?
8.Как влияет геометрия протяжек на силы резания?
9.Как усадка стружки зависит от технологических параметров протягивания?
10.Почему возникают напряжения в деталях в момент протя-
гивания?
177
Глава 4 ВЛИЯНИЕ РЕЖИМОВ ПРОТЯГИВАНИЯ И ГЕОМЕТРИИ
ПРОТЯЖЕК НА ФОРМИРОВАНИЕ ОСНОВНЫХ ПАРАМЕТРОВ КАЧЕСТВА ПОВЕРХНОСТНОГО СЛОЯ
ИУСТАЛОСТНУЮ ПРОЧНОСТЬ ДЕТАЛЕЙ ИЗ РАЗЛИЧНЫХ СТАЛЕЙ И СПЛАВОВ
Впредыдущей главе установлены основные закономерности влияния режимов резания на износ протяжек, температуру и силы резания, процесс стружкообразования. В свою очередь изменение этих параметров влияет на напряженное состояние детали в процессе резания, на изменение таких параметров физико-химического состояния поверхностного слоя, как величина шероховатости, глубина
истепень наклепа, величина и характер распределения остаточных напряжений, структурно-фазовые превращения, химсостав и др.
Формирующийся в процессе резания поверхностный слой обрабатываемых деталей оказывает существенное влияние на их эксплуатационные свойства. Обеспечение высокой усталостной и длительной прочности, термоусталости, износоустойчивости, коррозионной стойкости и других эксплуатационных требований к деталям ГТД может быть достигнуто и технологическими методами, т.е. назначением соответствующих режимов резания.
Большой вклад в изучение состояния поверхностного слоя внесли такие ученые, как В.А. Кривоухов, А.И. Каширин, М.О. Якобсон, П.Е. Дьяченко, А.И. Исаев, А.А. Маталин, А.Д. Макаров, В.С. Мухин, Л.С. Мурашкин, И.В. Дунин-Барковский, Б.С. Балакшин, И.А. Биргер, Б.А. Кравченко, А.М. Сулима, В.К. Старков и др.
Исследованию влияния режимов резания при протягивании различных материалов на состояние протянутого поверхностного слоя большое внимание уделено в работах А.В. Щеголева, Г.И. Грановского, Д.К. Маргулиса, П.Г. Кацева, Н.Ф. Пронкина, Н.И. Жигалко, Г. Опитца, М. Шутте и др.
Исследования параметров поверхностного слоя после протягивания на повышенных скоростях резания проводили Н.И. Жигалко,
178
Н.И. Ковзель, А.Е. Вишняков, В.А. Ведмедовский, В.И. Белашков
идр. Эти исследования носили разрозненный отрывочный характер, касающийся отдельных марок обрабатываемых материалов. Исследования усталостной прочности деталей после протягивания практически не проводились. Многие исследования проводились только
влабораторных условиях на строгальных станках и станках-стендах на образцах материалов. Поэтому весьма актуальным является установление закономерностей влияния режимов протягивания на основные параметры качества обработки, усталостную прочность образцов
иконкретных деталей из различных труднообрабатываемых материалов, обработанных непосредственно в производственных условиях механического цеха.
4.1.Влияние режимов протягивания
игеометрии протяжек на формирование шероховатости протянутой поверхности
Шероховатость поверхности согласно ГОСТ 2789–73 – это совокупность микронеровностей поверхности с относительно малыми шагами на базовой длине. Чаще всего шероховатость поверхности представляет собой следы механической обработки деталей. При протягивании шероховатость поверхности – это следы режущих и калибрующих зубьев протяжек, искаженные в результате термопластической деформации и сопутствующей процессу резания вибрации системы «станок, приспособление, инструмент, деталь». Величина шероховатости является обычно определяющим технологическим критерием процесса протягивания.
Исследование влияния режимов резания и геометрии протяжек на изменение шероховатости обработанной поверхности проводилось при протягивании как образцов в лабораторных условиях, так и конкретных деталей-дисков и лопаток ГТД в производственных условиях. Согласно ТУ чаще всего необходимо обеспечить при протягивании деталей ГТД шероховатость Ra ≤ 1, 25 мкм.
Общий характер влияния скорости резания V на изменение шероховатости поверхности Ra при протягивании в лабораторных ус-
179
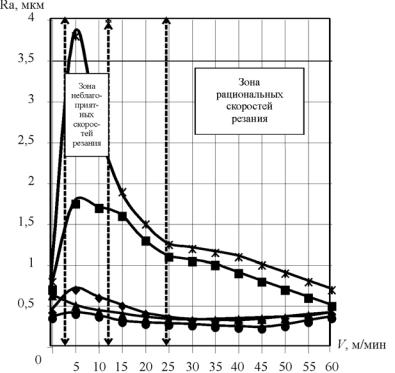
ловиях образцов из стали ЭП517Ш, жаропрочного деформируемого сплава ЭИ787-ВД, титанового сплава ВТ3-1 и литейного жаропрочного сплава ВЖЛ14 изображен на рис. 73. На графиках Ra = f (V) имеется две характерные зоны изменения шероховатости. Первая зона – зона неблагоприятных скоростей от 2,5 до 12,0 м/мин. Вторая зона – назовем ее зоной рациональных скоростей резания – находится в диапазоне от 24 м/мин и выше.
Рис. 73. Влияние скорости резания V на шероховатость протянутой поверхности Ra различных сталей и сплавов ВЖЛ14,
ВТ3-1,
ЭИ787-ВД,
ЭП517Ш,
ЭП517Ш (0,1 мм/зуб)
Применяемые на производстве скорости резания находятся на графиках левее зон неблагоприятных скоростей. Для всех обраба-
180