
1270
.pdfприменяемые, главным образом, для рабочих и сопловых лопаток турбин. Рабочая температура этих материалов самая высокая и дос-
тигает 1 073…1 423 К.
Химический состав исследуемых в работе сталей и сплавов приведен в табл. 5 согласно фактическому состоянию материалов по сертификатам, полученным на ОАО «Пермский моторный завод», после проверки их соответствия на образцах в центральной заводской лаборатории.
Химический состав нержавеющих хромистых жаропрочных сталей первой группы характеризуется повышенным содержанием хрома от 10 до 16 %, что обеспечивает высокую жаростойкость и жаропрочность при длительной эксплуатации при повышенных температурах в условиях контакта с кислородом и азотом воздуха.
Наличие углерода в составе сталей от 0,10 до 0,36 % обеспечивает высокую твердость и прочность, т.к. влияет на фазовые превращения и образует карбиды с вольфрамом, молибденом, ниобием. Растворяются такие карбиды только при температуре 1 423 К. В сталях имеются упрочняющие интерметаллидные фазы типа Fe2Mo, Fe2(Mo,W), называемые фазами Лавеса. Наибольшее применение для деталей компрессора нашли жаропрочные стали мартенситного класса ЭИ961Ш, ЭИ962Ш, ЭИ736Ш, ЭП517Ш, ЭП609Ш, ЭИ268 и Х12НМВФ на основе α-железа. Стали на основе γ-железа типа ЭИ481Ш (аустенитного класса) обладают более высокой жаропрочностью, т.к. содержат больше никеля, марганца, кремния, углерода, поэтому они применяются для деталей турбин. Сталь ЭИ481Ш относится к классу аустенитных сталей с карбидным упрочнением. По своей структуре эта сталь состоит из многокомпонентного аустенита и карбидов хрома Cr23C6, ванадия VC, молибдена Mo2C и пр., которые при старении после закалки выделяются из аустенита в дисперсном виде и упрочняют сталь.
51
52
Таблица 5
Химический состав исследуемых сталей и сплавов
Номер |
Марка |
|
|
|
|
|
Содержание химических элементов, % |
|
|
|
|
Твердые фазы, |
||||||
группы |
сплава |
C |
Si |
Mn |
Cr |
Ni |
Ti |
Al |
W |
Mo |
Fe |
Cu |
P |
S |
B |
V, Co |
Прочие |
включения |
|
ЭИ961Ш |
0,13 |
0,40 |
0,30 |
12,00 |
1,7 |
- |
- |
2,0 |
0,42 |
осн. |
0,13 |
0,010 |
0,010 |
- |
V 0,2 |
- |
Me3C; Mo2C; |
|
ЭИ962Ш |
0,10 |
0,40 |
0,40 |
12,00 |
1,7 |
- |
- |
1,9 |
0,50 |
осн. |
- |
0,015 |
0,015 |
- |
V 0,3 |
- |
Fe3C; Fe2V; |
|
ЭИ736Ш |
0,14 |
0,30 |
0,40 |
14,00 |
3,1 |
- |
- |
1,9 |
- |
осн. |
- |
- |
- |
0,004 |
V 0,2 |
- |
Fe2(Mo,W); |
I |
ЭИ517Ш |
0,15 |
0,40 |
0,60 |
12,00 |
1,8 |
- |
- |
0,8 |
1,50 |
осн. |
- |
- |
- |
- |
V 0,2 |
Nb 0,3 |
Me23C6; |
|
ЭП609Ш |
0,07 |
0,60 |
0,70 |
11,00 |
1,6 |
- |
- |
- |
0,40 |
осн. |
- |
- |
- |
- |
V 0,2 |
Nb 0,1 |
Nb(CN); |
|
ЭИ268 |
0,15 |
0,60 |
0,60 |
16,60 |
2,1 |
- |
- |
- |
- |
осн. |
- |
0,010 |
0,015 |
- |
- |
Nb 0,1 |
V(CN); |
|
Х12НМВФ |
0,15 |
– |
0,30 |
12,20 |
0,8 |
0,2 |
- |
0,9 |
- |
осн. |
- |
0,010 |
0,010 |
- |
- |
- |
VC |
|
ЭИ481Ш |
0,36 |
0,70 |
8,40 |
12,60 |
8,6 |
- |
- |
- |
1,20 |
осн. |
- |
0,010 |
0,010 |
- |
V 1,3 |
Nb 0,3 |
|
|
ВТ3-1 |
|
|
|
|
|
|
|
|
|
|
|
|
|
|
|
H2 0,015 |
|
|
0,10 |
0,35 |
- |
1,82 |
- |
осн. |
6,2 |
- |
2,60 |
0,55 |
- |
- |
- |
- |
|
N2 0,05 |
Ti2ZrSi |
|
|
(α+β) |
|
O2 0,18 |
|||||||||||||||
|
|
|
|
|
|
|
|
|
|
|
|
|
|
|
|
|
||
|
|
|
|
|
|
|
|
|
|
|
|
|
|
|
|
|
Zr 0,3 |
|
|
ВТ8-М |
0,10 |
0,35 |
- |
- |
- |
осн. |
7,0 |
- |
3,40 |
0,30 |
- |
- |
- |
- |
|
Zr 0,5 |
Mo2Si2 |
|
(α+β) |
|
||||||||||||||||
|
|
|
|
|
|
|
|
|
|
|
|
|
|
|
|
|
|
|
|
|
|
|
|
|
|
|
|
|
|
|
|
|
|
|
|
H2 0,015 |
|
|
ВТ-9 (α+β) |
0,10 |
0,25 |
- |
- |
- |
осн. |
6,8 |
- |
3,50 |
0,05 |
- |
- |
- |
- |
|
N2 0,05 |
Ti5Si3 |
|
|
O2 0,15 |
||||||||||||||||
|
|
|
|
|
|
|
|
|
|
|
|
|
|
|
|
|
|
|
|
|
|
|
|
|
|
|
|
|
|
|
|
|
|
|
|
Zr 2,2 |
|
II |
|
|
|
|
|
|
|
|
|
|
|
|
|
|
|
|
H2 0,05 |
|
|
|
|
|
|
|
|
|
|
|
|
|
|
|
|
|
Nb 1,0 |
|
|
|
ВТ18У (α) |
0,06 |
0,15 |
- |
- |
- |
осн. |
7,3 |
- |
0,68 |
0,15 |
- |
- |
- |
- |
|
N2 0,04 |
TiMn |
|
|
O2 0,12 |
||||||||||||||||
|
|
|
|
|
|
|
|
|
|
|
|
|
|
|
|
|
|
|
|
|
|
|
|
|
|
|
|
|
|
|
|
|
|
|
|
Sn 2,5 |
|
|
|
|
|
|
|
|
|
|
|
|
|
|
|
|
|
|
Zr 4,0 |
|
|
|
0,10 |
0,15 |
1,50 |
- |
- |
осн. |
3,5 |
- |
- |
0,40 |
- |
- |
- |
- |
- |
H2 0,015 |
|
|
ОТ4 (α) |
N2 0,05 |
TiFe |
|||||||||||||||
|
|
|
|
|
|
|
|
|
|
|
|
|
|
|
|
|
O2 0,13 |
|
|
|
|
|
|
|
|
|
|
|
|
|
|
|
|
|
|
H2 0,01 |
|
|
ВТ20 (α) |
0,07 |
0,15 |
- |
- |
- |
осн. |
6,0 |
- |
1,0 |
0,25 |
- |
- |
- |
- |
V 2,0 |
N2 0,03 |
|
|
O2 0,15 |
|
||||||||||||||||
|
|
|
|
|
|
|
|
|
|
|
|
|
|
|
|
|
|
|
|
|
|
|
|
|
|
|
|
|
|
|
|
|
|
|
|
Zr 2,0 |
|
52

|
|
|
|
|
|
|
|
|
|
|
|
|
|
|
|
|
|
Окончание |
табл. 5 |
||
|
Номер |
Марка |
|
|
|
|
|
Содержание химических элементов, % |
|
|
|
|
|
Твердые фазы, |
|||||||
|
группы |
сплава |
C |
Si |
Mn |
Cr |
Ni |
Ti |
Al |
W |
Mo |
Fe |
Cu |
P |
|
S |
B |
|
V, Co |
Прочие |
включения |
|
III |
ВЖ102 |
0,09 |
0,50 |
0,60 |
15,5 |
28 |
2,2 |
0,5 |
6 |
4 |
осн. |
- |
0,008 |
|
0,007 |
- |
|
- |
- |
γ'=5 %+TiC |
|
ЭИ437-ВД |
0,05 |
0,60 |
0,40 |
17,0 |
осн. |
2,8 |
0,85 |
- |
- |
0,8 |
0,06 |
0,007 |
|
0,006 |
0,008 |
|
- |
- |
γ'=12,5 %+Tic+ |
|
|
|
|
|
+TiN+Me3B2 |
|||||||||||||||||
|
|
|
|
|
|
|
|
|
|
|
|
|
|
|
|
|
|
|
|
|
|
|
|
ЭИ787-ВД |
0,06 |
0,31 |
0,14 |
15,3 |
34,8 |
3,1 |
1,3 |
3,1 |
0,3 |
осн. |
0,01 |
0,007 |
|
0,004 |
0,005 |
|
- |
- |
γ'=23 %+TiC+ |
|
|
|
|
+Me3B |
|||||||||||||||||
|
|
|
|
|
|
|
|
|
|
|
|
|
|
|
|
|
0,01 |
|
|
|
|
|
|
ЭП109-ВД |
0,08 |
0,50 |
0,20 |
10,2 |
осн. |
- |
6,1 |
6,5 |
7,5 |
1,5 |
- |
0,01 |
|
0,008 |
|
Со 12 |
- |
γ'=38 %+Me3B |
|
|
|
ЭП742-ИД |
0,05 |
0,80 |
0,03 |
14,0 |
осн. |
2,65 |
2,7 |
- |
5,2 |
0,25 |
- |
0,008 |
|
0,007 |
0,01 |
|
Co 10,5 |
- |
γ'=33 %+TiC+ |
|
|
|
|
+Me3B |
|||||||||||||||||
|
|
|
|
|
|
|
|
|
|
|
|
|
|
|
|
|
|
|
|
|
|
|
|
ЭИ698-ВД |
0,04 |
0,40 |
0,30 |
13,9 |
осн. |
2,64 |
1,67 |
- |
2,95 |
1,0 |
0,2 |
0,01 |
|
0,005 |
0,003 |
|
V 0,3 |
Nb 3,5 |
γ'=20 %+TiC+ |
|
|
|
|
|
|
|
|
|
|
|
|
|
|
|
|
|
|
|
Co 11,0 |
Ce 0,06 |
+NbC |
|
|
ВЖ122 |
0,11 |
0,20 |
0,04 |
13,7 |
осн. |
5,0 |
3,7 |
3,0 |
4,5 |
9,5 |
0,006 |
0,01 |
|
0,01 |
0,01 |
|
V 0,3 |
Nb 3,5 |
|
|
|
|
|
Ze 0,06 |
γ'=49 % |
||||||||||||||||
|
|
|
|
Co 11,0 |
|||||||||||||||||
|
|
|
|
|
|
|
|
|
|
|
|
|
|
|
|
|
|
|
Ba 0,02 |
|
|
|
|
|
|
|
|
|
|
|
|
|
|
|
|
|
|
|
|
|
|
|
|
|
|
ЭП741-НП |
0,05 |
0,40 |
0,40 |
9,0 |
осн. |
1,7 |
5,1 |
5,5 |
3,5 |
0,5 |
- |
0,01 |
|
0,01 |
0,015 |
|
Co 16,0 |
Nb 2,5 |
γ'=40 % |
|
|
|
|
Hf 0,3 |
|||||||||||||||||
|
|
|
|
|
|
|
|
|
|
|
|
|
|
|
|
|
0,01 |
|
|
|
|
|
|
ЭК79У-ИД |
0,05 |
0,70 |
0,03 |
13,7 |
осн. |
2,62 |
2,7 |
- |
5,18 |
0,2 |
9,89 |
0,01 |
|
0,01 |
|
- |
- |
γ'=34 % |
|
|
|
ЭИ867-ВД |
0,10 |
0,40 |
0,20 |
9,5 |
осн. |
- |
4,6 |
5,5 |
11 |
3,2 |
- |
0,01 |
|
0,01 |
0,01 |
|
Co 5,5 |
Ce 0,01 |
γ'=25 % |
|
IV |
ВЖЛ-14 |
0,06 |
0,40 |
0,40 |
19,0 |
осн. |
2,8 |
1,4 |
- |
5,2 |
8,5 |
- |
0,01 |
|
0,01 |
- |
|
- |
- |
γ'=18 % |
|
|
ЖС6К |
0,15 |
0,20 |
0,20 |
10,5 |
осн. |
3,0 |
5,5 |
5,0 |
4,4 |
2,0 |
- |
0,01 |
|
0,01 |
0,02 |
|
Co 5,0 |
- |
γ'=53 % |
|
|
ЖС6УВИ |
0,20 |
0,10 |
0,05 |
9,5 |
осн. |
2,4 |
5,6 |
10,5 |
2,2 |
1,0 |
- |
0,01 |
|
0,01 |
0,01 |
|
Co 9,2 |
Nb 1,0 |
γ'=51 % |
|
|
ЖС26- |
0,16 |
0,25 |
- |
5,0 |
осн. |
1,1 |
6,0 |
11,5 |
1,2 |
1,0 |
- |
0,015 |
|
0,01 |
0,015 |
|
V 0,9 |
Nb 1,5 |
γ'=43 % |
|
|
ВСНК |
|
|
Co 9,0 |
||||||||||||||||
|
|
ЖС32- |
|
|
|
|
|
|
|
|
|
|
|
|
|
|
|
|
V 1,5 |
Ta 4,0 |
|
|
|
0,15 |
0,30 |
- |
5,2 |
осн. |
- |
6,0 |
9,0 |
1,2 |
1,0 |
- |
0,015 |
|
0,015 |
0,015 |
|
Nb 1,6 |
γ'=37 % |
||
|
|
ВСНК |
|
|
Co 9,2 |
Re 4,0 |
|||||||||||||||
|
|
|
|
|
|
|
|
|
|
|
|
|
|
|
|
|
0,02 |
|
|
Ce 0,025 |
|
|
|
ЧС70 |
0,11 |
0,30 |
0,30 |
15,7 |
осн. |
5,0 |
3,0 |
5,7 |
2,2 |
0,5 |
0,07 |
0,008 |
|
0,008 |
|
Co 11,5 |
Nb 0,2 |
γ'=47,5 % |
|
53 |
|
|
|
|
|
|
|
|
|
|
|
|
|
|
|
|
|
|
|
|
|
|
|
|
|
|
|
|
|
|
|
|
|
|
|
|
|
|
|
|
|
|
53 |
В состав титановых сплавов второй группы (см. табл. 5) в качестве основного легирующего элемента входит алюминий (от 3,5 до 7,3 %). Алюминий является основным упрочнителем титановых сплавов (α-стабилизатор). Кроме него вклад в повышение прочности титановых сплавов вносят молибден (0,68…3,50 %), железо (0,05…0,55 %), кремний (0,15…0,39 %) и другие элементы, которые не только упрочняют, но и гетеронизируют структуру сплавов, образуя различные интерметаллические соединения (Ti5Si3, TiMn, TiFe2 и др.). Чистый титан имеет низкую температуру начала рекристаллизации – около 763 К. Введение железа, марганца, ниобия и циркония повышает эту температуру. Легирование титановых сплавов кислородом и азотом повышают жаропрочность и температуру полиморфных превращений (α→β). Рассмотренные в работе титановые сплавы по фазовому составу можно разделить на две подгруппы: однофазные – α-сплавы (ОТ4, ВТ18У, ВТ20) и двухфазные – (α + β)-сплавы (ВТ3-1, ВТ8, ВТ9). Титановые α-сплавы имеют хорошую свариваемость, высокую пластичность, термическую стабильность, максимальное сопротивление ползучести. Поэтому титановые α-сплавы ОТ4, ВТ18У и ВТ20 применяются для сварных колец направляющих аппаратов, в которых прорезаются пазы в форме «ласточкиного хвоста» методом протягивания. Рабочие температуры спла-
ваОТ4 – 623…670 К, ау сплавов ВТ18Уи ВТ20 – 773…873 К.
Титановые (α + β)-сплавы в своей структуре содержат более 2 % стабилизаторов (молибден, кремний и др.). Они обладают меньшей термической стабильностью и жаропрочностью по сравнению с α-сплавами. Титановые сплавы ВТ3-1, ВТ8 и ВТ9 применяются в основном для штампованных лопаток и дисков компрессора, работающих до температур 723…773 °C
Обрабатываемость жаропрочных деформируемых сплавов на никелевой основе (3-я группа) в значительной мере определяется содержанием в их составе титана и алюминия, которые формируют прочностные свойства сплавов при высоких температурах.
54
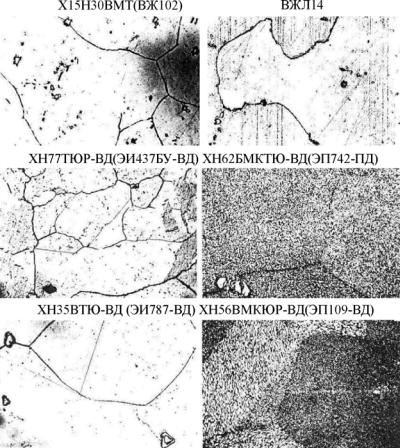
Титан и алюминий образуют с никелем твердую мелкодисперсную интерметаллидную упрочняющую γ′-фазу Ni3(Ti,Al), которая выделяется в виде твердых частиц, распределяется в сплаве
впроцессе термической обработки (рис. 6) и играет основную роль
вупрочнении жаропрочных сплавов. Повышение суммарного содержания титана с алюминием приводит к значительному увеличению
количества γ′-фазы в сплаве (табл. 6).
Рис. 6. Фотографии микроструктуры жаропрочных деформируемых сплавов
55

Таблица 6
Механические свойства исследуемых жаропрочных сталей и сплавов при нормальной температуре
Номер |
Марка |
σb, |
σ0,2, |
δ, |
Ψ, |
Qn, |
НВ, МПа, |
|
группы |
сплава |
MПа |
MПа |
% |
% |
кДж/м2 |
отп, мм |
|
|
ЭИ961Ш |
1 150 |
850 |
17 |
55 |
1 100 |
3,15 |
|
|
ЭИ962 |
650 |
750 |
19 |
50 |
1 200 |
3,10 |
|
|
ЭИ736Ш |
1 000 |
750 |
18 |
52 |
1 300 |
3,15 |
|
I |
ЭП517Ш |
1 100 |
800 |
16 |
52 |
1 000 |
3,20 |
|
ЭП609Ш |
1 200 |
750 |
14 |
64 |
1 200 |
3,60 |
||
|
14Х17Н2 |
1 100 |
850 |
10 |
40 |
2 200 |
3 300 |
|
|
Х12НМВФ |
870 |
730 |
17 |
56 |
1 400 |
2 700 |
|
|
ЭИ481Ш |
1 000 |
600 |
20 |
25 |
350 |
3 000 |
|
|
ВТ3-1 |
1 100 |
850 |
10 |
35 |
380 |
3,50 |
|
|
ВТ8М |
1 050 |
850 |
6 |
14 |
380 |
3,40 |
|
II |
ВТ9 |
1 100 |
950 |
12 |
33 |
388 |
3,30 |
|
ВТ18У |
1 100 |
950 |
8 |
19 |
350 |
3,65 |
||
|
ОТ4 |
800 |
600 |
27 |
40 |
500 |
2550 |
|
|
ВТ20 |
1 100 |
850 |
17 |
37 |
450 |
3400 |
|
|
ВЖ102 |
1 020 |
660 |
19 |
21 |
450 |
3,65 |
|
|
ЭИ787-ВД |
1 180 |
750 |
16 |
22 |
430 |
3,35 |
|
|
ЭИ437Б-ВД |
1 100 |
690 |
18 |
20 |
730 |
3,40 |
|
|
ЭП109-ВД |
1 200 |
900 |
14 |
16 |
350 |
3,25 |
|
III |
ЭП742-ПД |
1 300 |
770 |
21 |
18 |
600 |
3,30 |
|
ЭИ698-ВД |
1 210 |
800 |
28 |
36 |
500 |
3,40 |
||
|
ВЖ122(ЭП962) |
1 600 |
1 270 |
15 |
18 |
390 |
3,00 |
|
|
ЭП741-НП |
1 300 |
960 |
13 |
15 |
400 |
3,30 |
|
|
ЭК79У-ИД |
1 500 |
1 070 |
18 |
19 |
370 |
3,20 |
|
|
ЭИ867-ВД |
1 000 |
780 |
6 |
11 |
350 |
3,30 |
|
|
ВЖЛ14 |
950 |
650 |
18 |
24 |
600 |
— |
|
|
ЖС6К |
1 050 |
850 |
25 |
6,5 |
300 |
3 600 |
|
IV |
ЖС6УВИ |
1 070 |
910 |
35 |
9 |
350 |
3 550 |
|
ЖС26 |
930 |
810 |
16 |
18 |
450 |
3 500 |
||
|
||||||||
|
ЖС32 |
1 060 |
850 |
20 |
26 |
420 |
3 450 |
|
|
ЧС70 |
950 |
850 |
3 |
6 |
650 |
3 600 |
|
56 |
|
|
|
|
|
|
|
По характеру упрочняющей γ′-фазы исследуемые жаропрочные сплавы можно разделить на три подгруппы.
Первая подгруппа – сплавы на железоникелевой основе. Упрочнение в этих сплавах происходит в результате выделения интерметаллидной γ′-фазы типа (Ni,Fe)3 (Al,Ti). К ним относятся ВЖ102
иЭИ787-ВД. Легирование этих сплавов титаном, алюминием, бором
имолибденом обеспечивает высокую длительную прочность. Вторая подгруппа – сплавы на никелевой основе с упрочняющей
интерметаллидной γ′-фазой типа Ni3(Al,Ti). К ним относятся из исследуемых ЭИ437БУ-ВД, ЭП742-ПД, ЭИ698-ВД, ВЖ122, ЭП741-НП, ЭК79У-ИД. Эти сплавы обладают более высокой жаропрочностью, чем сплавы на железоникелевой основе, однако содержат меньше легирующих элементов.
К третьей подгруппе относятся жаропрочные сплавы ЭП109ВД и ЭИ867-ВД, в которых отсутствуют легирование титаном и упрочнение происходит в результате выделения γ′-фазы типа Ni3Al. Характерной особенностью сплавов этой группы является пониженное содержание хрома (до 10,2 %), что компенсируется повышенным содержанием алюминия (до 6,1 %), обеспечивающим более высокие характеристики жаропрочности при 1 073 К. Обрабатываемость жаропрочных деформируемых сплавов протягиванием наименее изучена по сравнению с другими материалами. В то же время эти сплавы нашли наибольшее применение для дисков и лопаток не только турбин, но и компрессоров.
Литейные жаропрочные сплавы на никелевой основе (4-я группа обрабатываемости) отличается от деформируемых никелевых сплавов более высокой жаропрочностью при повышенных температурах (1 223…1 273 К). Объясняется это более высоким содержанием кобальта (до 11,5 %) и вольфрама (до 12 %) при высоком содержании алюминия (до 6 %) (см. табл. 5). В результате литейные сплавы имеют более высокое (до 53 %) содержание упрочняющей γ′-фазы. Поэтому эти сплавы применяются в основном для рабочих и сопловых лопаток турбин, работающих при температурах 1 273…1 473 К. Среди литейных сплавов наиболее высокой жаропрочностью обладают новые
57
сплавы ЖС26 и ЖС32, получаемые методом ВСНК – высокоскоростной направленной кристаллизацией. Сплавы ЖС26 и ЖС32 заменяют на новых двигателях сплавы ЖС6К и ЖС6УВИ с обеспечением более высокого ресурса. Для проведения лабораторных исследований процесса протягивания из исследуемых материалов изготавливались прямоугольные образцы 60×80×5 мм и 20×10×5 мм. В производственных условиях исследования проводились непосредственно при обработке деталей газотурбинных двигателей практически из всех материалов, представленных в табл. 5. Термообработка образцов и деталей из обрабатываемых сталей и сплавов проводилась согласно технологии металлургического производства, соответствующей всем техническим требованиям на изготовление деталей ГТД.
Механические свойства обрабатываемых материалов, полученные в результате термической обработки, приведены в табл. 6.
Анализ табл. 6 показывает, что среди исследуемых материалов наибольшей прочностью (до σb = 1 600 МПа) обладают жаропрочные деформируемые сплавы на никелевой основе (III группа). Наиболее пластичные материалы – жаропрочные хромистые стали (I группа), имеющие относительное удлинение до 20 %, относительное сужение до 64 %. Наименьшей ударной вязкостью Qn и пластичностью обладают титановые сплавы (II группа) и литейные жаропрочные сплавы на никелевой основе (IV группа).
2.2. Модернизация протяжного оборудования, разработка конструкций и выбор рациональных марок материалов протяжек для решения задач оптимизации
Экспериментальные исследования проводились в лабораторных и производственных условиях. Для лабораторных исследований спроектирована и изготовлена специальная установка скоростного протягивания модели УСП-1 (рис. 7) с диапазоном скоростей от 1,0…60,0 м/мин и модернизирован вертикально-протяжной станок мод. 7Б74 (рис. 8, а) с диапазоном скоростей 1,5…30,0 м/мин. Протягивались моделированными протяжками образцы из жаропрочных сталей и сплавов.
58
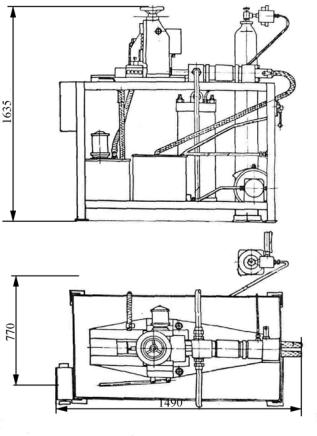
Рис. 7. Принципиальная схема скоростной установки УСП-1
Производственные исследования производились в условиях механических цехов ОАО «Пермский моторный завод» при протягивании конкретных деталей газотурбинных двигателей многосекционными протяжками на модернизированных горизонтально-протяжных станках мод. 7А540 (рис. 8, б) в диапазоне скоростей от 1 до 30 м/мин. Все используемые при исследовании станки имели гидравлический привод. Для обеспечения высоких скоростей резания на установке УСП-1 (рис. 7) установлен гидроусилитель, в котором обеспечивается
59
высокое давление за счет подачи сжатого инертного газа азота, находящегося в специальном баллоне. В установке имеются встроенные тензометрические датчики для замера осевой и радиальной сил резания, а также устройство для мгновенной остановки процесса резания при получении корней стружек.
Для осуществления исследования износа протяжек, силы и температуры резания при протягивании на повышенных скоростях резания разработана и осуществлена модернизация гидропривода применяемых в протяжных станках мод. 7Б74 и 7А540 (рис. 8, а, б). Это оказалось намного дешевле, быстрее и выгоднее (особенно в настоящий момент), чем приобретение новых специальных скоростных станков.
Первоначально было рассмотрено несколько вариантов модернизации протяжных станков. Первый вариант разработан в СКБ ПС (г. Минск). Повышение рабочих скоростей протягивания достигается путем установки дополнительного гидронасоса. При такой модернизации сохраняется тяговое усилие, однако конструкция гидропривода усложняется в два раза, значительно увеличиваются габариты станка, усложняется настройка, регулировка и ремонт гидропривода.
Второй вариант модернизации разработан на Запорожском моторостроительном заводе. Увеличение скоростей протягивания достигается путем изготовления нового штока главного гидроцилиндра с увеличенным в 1,5 раза диаметром при сохранении размеров гидроцилиндра. Недостатком данной схемы модернизации является неустойчивая работа гидропривода из-за повышенных кавитационных явлений в гидросистеме в момент рабочего хода протяжки.
Наиболее приемлемым вариантом оказалась схема модернизации за счет изготовления нового гидроцилиндра с меньшим внутренним диаметром Дц и нового поршня с уменьшенным диаметром и с прежним диаметром штока Дш (рис. 9). Конструктивные особенности модернизированных протяжных станков приведены в табл. 7.
60