
1270
.pdf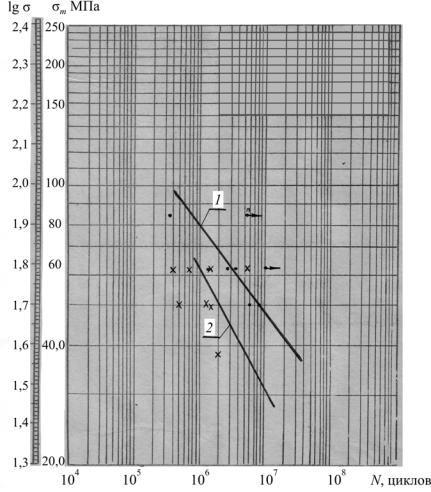
Рис. 128. Изменение предела усталостной прочности σ–1 на различной базе испытаний N циклов дисков компрессора из титанового сплава ВТЗ-1, протянутых на серийных (р) и скоростных (т) режимах:
σm = 140 МПа; 1 – группа «т»; 2 –
группа «р»
Переменные напряжения при усталостных испытаниях выдерживались в пределах 90 МПа для сечения по первой впадине замка лопатки. База испытаний составляла N = 5 107 циклов.
241
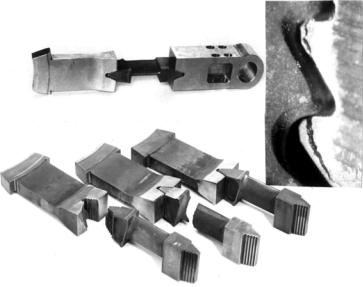
Рис. 129. Характер разрушения дисков и лопаток при совместных усталостных испытаниях замковых соединений
Разрушения при усталостных испытаниях происходили в основном по профильной части пера двухзамковых лопаток турбины. Очаги усталостных трещин на профильной части располагались, как правило, на входной кромке, долговечность профильной части составляла 2 105…5 107 циклов.
В результате сравнительных усталостных испытаний всех вышеперечисленных вариантов обработки замков лопаток и пазов в дисках не обнаружено снижения усталостной прочности при использовании методов скоростного протягивания пазов и скоростного фрезерования замков лопаток; наоборот, на ряде деталей установлено увеличение усталостной прочности от 10 до 60 %. Таким образом, применение скоростного протягивания замковых соединений дисков и лопаток компрессоров и турбин ГТД не снижает усталостной прочности этих деталей по сравнению с серийной обработкой.
242
4.6.Контрольные вопросы
1.Как влияет скорость резания на изменение шероховатости протянутой поверхности?
2.Чем объясняется горбообразный характер графика изменения шероховатости?
3.Что такое наклеп поверхности? От чего зависит его величина?
4.Каковы причины образования остаточных напряжений?
5.Каково влияние скорости резания на изменение остаточных напряжений?
6.Каково влияние режимов протягивания на изменение структуры поверхностного слоя?
7.Что такое усталостная прочность деталей?
8.Как влияют режимы резания на изменение усталостной прочности?
243
Глава 5 МЕТОДЫ ОБЕСПЕЧЕНИЯ СТАБИЛЬНОЙ РАБОТЫ
МНОГОСЕКЦИОННЫХ ТВЕРДОСПЛАВНЫХ ПРОТЯЖЕК В УСЛОВИЯХ ОПТИМАЛЬНОГО РЕЗАНИЯ
Впредыдущих главах приведены подробные доказательства преимущества процесса скоростного протягивания деталей из жаропрочных сталей и сплавов по сравнению с применяемым на производстве процессом низкоскоростного серийного протягивания. Эти исследования проводились большей частью в лабораторных условиях с применением, как правило, однозубых протяжек из быстрорежущей стали Р18 и твердого сплава ВК8.
Вреальных условиях производства применяются в основном многозубые многосекционные блочные протяжки, имеющие различ-
ные подачи Sz от 0,12 до 0,01 мм/зуб на зубьях и движущиеся обычно на весьма низких скоростях резания: 0,5…2,0 м/мин, далеких от оптимальных значений. В процессе резания на каждой секции протяжек действуют переменные значения температур и сил резания, зависящие от режимов резания, геометрии протяжек и других факторов. В свою очередь, изменяющиеся параметры процесса резания вызывают соответствующие изменения износостойкости протяжек, параметров качества обработки и технологических напряжений в обрабатываемых деталях. Поэтому при протягивании многосекционными протяжками необходимо назначать такие условия резания, которые обеспечивали бы высокую производительность и высокую стойкость всех протяжек, входящих в блок, при соблюдении требуемого качества обработки. Определение же оптимальных режимов для каждой секции протяжек, а тем более для каждого зуба требует значительных по трудоемкости экспериментальных исследований или приближенных расчетов различными аналитическими методами. Поэтому разработка ускоренных методов экспериментального и аналитического определения оптимальных режимов протягивания является весьма важной для реализация процесса более интенсивного скоростного протягивания деталей ГТД.
244
Значительным препятствием к внедрению процессов скоростного протягивания замковых соединений дисков, лопаток турбин
икомпрессоров твердосплавными многосекционными протяжками является фактор хрупкого разрушения зубьев протяжек. Изучение процессов адгезионного взаимодействия обрабатываемых и инструментальных материалов, термодинамических условий входа и выхода зубьев протяжек из обрабатываемых деталей позволяет научно обоснованно оценить причины хрупкого разрушения твердосплавных протяжек и разработать эффективные методы повышения стабильности и надежности их работы.
5.1.Особенности износа и хрупкого разрушения твердосплавных протяжек
Всвязи с применением в качестве режущей части протяжек твердых сплавов вместо быстрорежущих сталей возникло несколько серьезных проблем по обеспечению высокой стойкости, надежности
истабильности их работы. Обнаружено, что при протягивании на раз-
личных режимах резания износ протяжек происходит в основном в виде хрупкого разрушения режущих кромок твердосплавных зубьев. Типичный характер выкрашивания и разрушения режущих кромок твердосплавных протяжек показан на рис. 130.
Появление выкрашиваний на режущих зубьях протяжек приводит к резкому увеличению нагрузки на последующих зубьях и их разрушению. Постепенно происходит лавинообразное разрушение всех последующих режущих и чистовых зубьев протяжек, что вызывает значительное ухудшение шероховатости и точности протягиваемых поверхностей деталей.
Наиболее крупные выкрашивания протяжек обнаружены при низких скоростях резания. С увеличением скорости резания до оптимальных значений уровень выкрашиваний снижается, а при дальнейшем увеличении вновь увеличивается. Установлено, что одной из причин разрушения (поломок) твердосплавных зубьев протяжек является недостаточная жecткoсть системы «станок, приспособление,
245
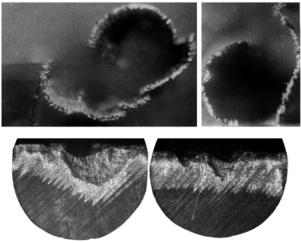
Рис. 130. Типичный характер сцепления стружки
сзубом протяжки, выкрашивания и разрушения режущих кромок твердосплавных протяжек при удалении стружки
инструмент, деталь». С целью повышения жесткости этой системы увеличены габаритные размеры корпусов протяжек, блоков, адапторов, повышена жесткость крепления деталей в приспособлении. В результате значительно снизилась поломка режущих зубьев, однако выкрашивание отдельных зубьев все же наблюдалось. Не все зубья твердосплавной протяжки изнашиваются одинаково. Есть зубья с выкрашиванием, а есть на этой же протяжке зубья и без выкрашивания, с износом.
Можно предположить, что причинами выкрашивания отдельных зубьев протяжек, помимо сложных термодинамических процессов в зоне резания, является нестабильность физикохимических свойств самых твердосплавных пластинок даже в пределах одной изготовленной партии.
В настоящее время практически отсутствуют стандартные методы контроля пластин твердого сплава с целью их отбраковки. По-
246
этому при изготовлении твердосплавных протяжек могут быть установлены пластинки с различными прочностными и другими характеристиками.
Указанное предположение проверялось путем определения изгибной прочности твердого сплава и отбраковки пластин по величине магнитной проницаемости, а также при стойкостных испытаниях протяжек.
Для эксперимента взята партия из 200 пластинок из твердого сплава ВК8 (форма № 2405) Кировоградского комбината твердых сплавов. По паспортным данным, средняя изгибная прочность пластинок в партии – 1 630 МПа. Определение фактического предела прочности пластинок производилось на прессе Амслера при нагрузке 1,5…2,5 кН. В результате проверки установлено, что предел прочности на изгиб σизг для различных пластинок в партии колеблется от 1 132 до 2 240 МПа со средним значением 1 540 МПа.
Проверка магнитной проницаемости, проведенная на приборе ИОТС-21 (см. рис. 16), показала, что пластинки также имеют широкий разброс значений магнитной проницаемости от 3 до 28 делений милливольтметра. Причем определено, что меньшим значениям магнитной проницаемости соответствовала и меньшая прочность твердого сплава σизг.
Для установления связи между пределом изгибной прочности и стойкостью протяжек проведены стойкостные испытания пластинок, для которых затем определялся предел прочности на изгиб. Испытания проводились при протягивании сплава ЭИ787-ВД на скорости резания 26 м/мин с подачей 0,02 мм/зуб. Статистическая обработка данных, полученных методом наименьших квадратов, выявила прямолинейную корреляцию между стойкостью протяжек L и пределом прочности на изгиб σизг в виде
L = 0,12σизг – 0,36, м. |
(65) |
Вычисленный коэффициент α = 0,95 характеризует достаточно высокую корреляцию между стойкостью инструмента и пределом прочности твердого сплава. Отбраковка пластин с низкой σизг обеспечивает более высокую стойкость протяжек.
247
Дополнительным методом решения проблемы стабилизации режущих свойств твердого сплава в пределах одной партии является введение специальной термообработки твердого сплава по авторскому свидетельству № 360151, включающей отжиг на следующих режимах: нагрев со скоростью 120…150 °С в час до температуры 820…850 °С, выдержка 25…35 мин, охлаждение в печи со скоростью 50…75 °С в час, затем на воздухе, и нормализацию при температуре 900 °С. Время нагрева при нормализации – 16…25 с.
Для термообработки и последующих сравнительных испытаний взято еще 200 пластинок из той же партии твердого сплава ВК8. До и после отжига пластинок проведена проверка магнитной проницаемости. В результате установлено, что после отжига среднее значение показаний прибора ИОТС-21 увеличилось с 18 делений милливольтметра до 24, после нормализации пластинок показания прибора – еще до 40 делений.
Ранее было установлено, что чем больше показания прибора ИОТС-21, тем выше изгибная прочность и стойкость протяжек. Таким образом, можно предположить, что дополнительная термообработка позволяет повысить изгибную прочность твердосплавных пластинок и снизить вероятность появления выкрашиваний и поломок протяжек.
Проверка изгибной прочности пластинок после термообработки показала, что разброс значений σизг в партии уменьшился и составил 1 633…1 940 МПа со средним значением 1 719 МПа. В результате применения термообработки удалось повысить σизг на 11,6 % и обеспечить более стабильные свойства пластинок.
Стойкостные испытания твердосплавных многозубых секционных протяжек с отобранными на приборе ИОТС-21 и термообработанными пластинками при протягивании замков лопаток из жаропрочного сплава ЭИ787-ВД показали увеличение стойкости в 1,5–2 раза и уменьшение вероятности выкрашиваний и поломок зубьев.
248
Для объяснения эффекта повышения стойкости протяжек после термообработки проведен сравнительный анализ твердосплавных пластинок до и после термообработки. Для этого пластинки твердого сплава подвергнуты визуальному осмотру, замеру твердости по шкале Роквелла, определен их удельный вес и исследована микроструктура.
Визуальный осмотр не выявил каких-либо дефектов в материале твердого сплава. Твердость материала пластин измерялась в пяти точках, и определялось ее среднее значение. Результаты измерений твердости пластинок находились в пределах HRC 89…90 ед. Удельный вес не изменился. Изломы пластин имеют нормальную структуру. Существенных различий в пористости не обнаружено.
Определение величины зерна WC-фазы производилось при рассмотрении микроструктуры измерением на микроскопе МИМ-7 по 100 зерен при увеличении до 1 500 раз. В результате установлено, что после термообработки в твердом сплаве увеличивается содержание мелкого зерна с 78 до 87 % по сравнению с исходной структурой.
Таким образом, повышение стойкости твердосплавных пластин после дополнительной термообработки можно объяснить тем, что при нагревании пластин ВК8 до 800…900 °С происходит измельчение величины зерна карбида вольфрама, распад твердого раствора цементирующей фазы, повышение пластичности и вязкости сплава, уменьшение остаточных напряжений. В результате значительно снижается вероятность трещинообразования при пайке, заточке в процессе эксплуатации твердосплавных пластин.
Отбраковка пластинок твердого сплава для протяжек с помощью прибора ИОТС-21 и последующая дополнительная термообработка не исключают все же вероятности появления выкрашивания зубьев протяжек. Поэтому для выявления возможных трещин в твердом сплаве введен дополнительный контроль методом цветной дефектоскопии ЛЮМ-1 до пайки пластинок и после заточки.
Анализ работы твердосплавных протяжек показал, что выкрашивание может появиться на зубьях уже после первого реза.
249
При рассмотрении зубьев вновь изготовленных многосекционных протяжек обнаружена значительная шероховатость режущих кромок, что, безусловно, может быть одной из причин начала появления микротрещин в твердом сплаве и последующего интенсивного выкрашивания. Поэтому эффективным средством борьбы с выкрашиваниями режущих кромок является заточка и доводка фасок на передней и задней гранях по схеме, указанной на рис. 17. Доводка фасок на режущих кромках обеспечивает ровную кромку с небольшой шероховатостью и отсутствием значительных концентраторов напряжений (рис. 131). Наличие концентраторов напряжений ускоряет образование макро- и микротрещин, направленных перпендикулярно режущей кромке. При смене тепловых нагрузок и ударном воздействии эти трещины развиваются и переходят на заднюю грань зуба, что и приводит к выкрaшивaнию режущих кромок. Это наглядно можно видеть на фотографиях последовательного износа протяжек, где острозаточенные протяжки (см. рис. 131, а) имеют значительные сколы и выкрашивания, а протяжки с фасками (рис. 131, б) имеют ровную, без выкрашиваний режущую кромку.
Приведенная методика повышения стойкости твердосплавных протяжек, т.е. отбраковка, термообработка, заточка и доводка фасок, весьма эффективна, но только для небольших подач при небольшой длине пути резания. С увеличением подачи Sz более 0,05…0,06 мм/зуб и длины пути резания выкрашивание и сколы все же имеют место, в особенности при протягивании наиболее высокопрочных сталей и сплавов практически на всех скоростях резания в большей или меньшей степени. Это можно видеть на фото хрупкого разрушения протяжек из ВК8 при протягивании наиболее высокопрочного сплава ЭП109-ВД с подачей Sz = 0,06 мм/зуб. Уже через 40 резов происходит практически полное разрушение режущих кромок протяжек, как на скорости 2 м/мин, так и на скорости 20 м/мин. На контактных поверхностях имеются значительные следы адгезионного взаимодействия с обрабатываемым металлом. По-видимому, при протягивании –
250