
1270
.pdfтость меньше, чем у импортных кругов, а дисбаланс кругов колеблется от 1-го до 3-го класса. Замена импортных кругов на отечественные привела к снижению уста-лостной прочности, поэтому пришлось увеличивать число проходов до девяти для обеспечения σ–1 = 140 МПа. Высокопористые круги завода «Ильич» содержат меньшее количество пор (23 %), больше зерна (45 %) и связки
(32 %).
Круги фирмы ЭКСИ изготавливаются на Челябинском абразивном заводе по оригинальней технологии с использованием модифицированной связки и специальных наполнителей в виде стеклянных полых микросфер. В результате получается большое количество мелких пор, равномерно расположенных вокруг абразивных зерен. Технология позволяет просчитывать состав шихты и точно регулировать выходные параметры кругов по твердости и структуре. В процессе обжига кругов не происходит выгорания веществ для образования пор, и технология является экологически чистой. Данные круги испытаны в Уфе на УМПО и на ОАО «Рыбинские моторы». Удельный вес кругов – 1,71 г/см3, твердость кругов соответствует замаркированной, пористость в норме, дисбаланс, по замерам на ОАО «Пермский моторный завод», выше нормы и соответствует 3–4-му классу неуравновешенности. Этот недостаток не позволил провести производственные испытания кругов. Испытания кругов в Уфе и Рыбинске показали несколько лучшие эксплуатационные данные по износу кругов и качеству поверхностного слоя. Содержание пор в круге составляет 26 %, количество зерна – 43 %, связки – 31 %.
В МГТУ «Станкин» под руководством В.К. Старкова на базе новой технологии разработан принципиально новый вид абразивного инструмента – высокопористый инструмент с закрытой структурой, который имеет более широкие эксплуатационные возможности, чем круги с открытой структурой. Новая технология основана на применении невыгорающих порообразователей при изготовлении абразивной массы, что обеспечивает экологическую чистоту производства, позволяет использовать круги более высокой твердости, имеет высокую стабильность физико-механических свойств кругов. Производ-
331
ственные испытания данных кругов в ОАО «Пермский моторный завод» проведены при глубинном шлифовании замков лопаток из сплава ЧС70. В результате испытаний установлено: за счет уменьшения износа кругов уменьшена величина непрерывной правки кругов на 20…30 %, количество обработанных деталей увеличилось с 18 до 22 деталей, уменьшилась величина прижога на торце лопатки в 2 раза. При глубинном шлифовании «елочных» замков лопаток круги «Станкина» показали наилучшие эксплуатационные свойства по сравнению с кругами других отечественных и зарубежных фирм. Проверка лопаток на ЛЮМ-контроле показала отсутствие свечений и трещин на обработанной поверхности. Только круги «Станкина» обеспечили требуемый предел усталостной прочности 110 МПа для лопаток из нового литейного сплава ЖС26 двигателя ПС90А. Таким образом, круги производства «Экоабразив» по своим эксплуатационным данным превосходят круги фирмы «Ильич» и могут быть рекомендованы для серийного производства.
В ОАО «Пермский моторный завод» разработана технология повышения стабильности эксплуатационных свойств абразивных шлифовальных кругов за счет пропитки их специальным составом, в который входят дисульфид молибдена марки ДМ-1, жидкий бакелит марки БЖ-З, связующее фенольное порошкообразное СФП-011А и ацетон. После пропитки производится сушка и термообработка кругов при температуре 60…150 °С. В процессе термообработки происходит дополнительное укрепление связки кругов и повышение твердости кругов на 2–3 ступени. В процессе шлифования бакелитофенольная связка размягчается и создает полирующий эффект шлифования, когда зерно абразива после отрыва от основной связки удерживается еще некоторое время фенолобакелитовой связкой. Кроме того, введение порошкообразного дисульфида молибдена служит дополнительной твердой смазкой точек контакта зерна с металлом детали, что снижает тепловые и силовые нагрузки в зоне резания. В процессе пропитки ацетоновый раствор проникает глубоко в поры круга, покрывая абразивные зерна защитными пленками, что
332
также способствует снижению трения, уменьшает адгезионное взаимодействие абразивных зерен и металла деталей.
Для пропитки высокопористых кругов берут весьма мягкие круги ЗИ 29–30. За счет пропитки твердость этих кругов повышается до ЗИ 32–33, однако работают они более эффективно. Производственные испытания пропитанных кругов при глубинном шлифовании показали следующее: стойкость кругов увеличилась на 35…50 %, величина правки уменьшилась на 35 %, уменьшилась величина прижогов на торце детали, шероховатость поверхности несколько снизилась. Данным методом обработано большое количество кругов, забракованных ОТК при входном контроле по причине низкой твердости. Результаты использования этих кругов положительные.
Таким образом, выбор высококачественных кругов для глубинного шлифования является решающим фактором для обеспечения требуемого качества и усталостной прочности. Установлено, например, что увеличение зернистости кругов снижает градиент сжимающих напряжений и повышает усталостную прочность. Увеличение скорости алмазного ролика с 9 до 18 м/с при правке кругов для глубинного шлифования снижает Δσсж с –810 МПа до –320 МПа. Увеличение подачи алмазного правящего ролика с 1 до 3 мкм/10 об. кр. приводит к снижению Δσсж с 350 до 70 МПа, что также является благоприятным фактором.
Наиболее интересным и принципиально возможным является установление зависимости остаточных напряжений от глубины резания, числа проходов и порядкового номера лопатки по ходу шлифования. Эта зависимость представлена на рис. 173, где видно, что на первых проходах с большой глубиной резания h остаточные сжимающие напряжения минимальны и даже могут быть растягивающими до +150 МПа, например, у первой по ходу лопатки.
С увеличением числа проходов и снижением глубины шлифования в поверхностном слое возникают все более увеличивающиеся остаточные сжимающие напряжения, достигающие, например, на последнем – девятом – проходе величины –300…–450 МПа. Причем у первой по ходу лопатки остаточные напряжения больше, чем у четвертой. Такой характер распределения остаточных напряжений можно
333
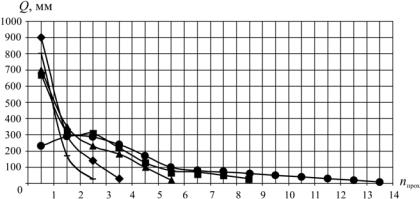
объяснить совместным воздействием силового и теплового факторов процесса шлифования. На первых проходах, когда глубина шлифования большая (tшл = 0,6…1,5 мм), превалирующее воздействие оказывает тепловой фактор. Поэтому сжимающие напряжения минимальны. При небольших глубинах шлифования на последних проходах (tшл = 0,01…0,02 мм) действие теплового фактора снижается и усиливается действие силового фактора, поэтому сжимающие напряжения увеличиваются. С увеличением износа круга действие теплового фактора усиливается, поэтому на четвертой лопатке сжимающие напряжения уменьшаются с –450 до –300 МПа по сравнению с первой лопаткой. На качество обработки влияет и жесткость системы «станок, приспособление, инструмент, деталь», качество очистки и подачи СОЖ.
Рис. 174. Характер изменения объема снимаемой стружки Q при глубинном шлифовании «елочного» профиля турбиной лопатки на различном числе проходов nпрох
14 проходов,
9 проходов,
6 проходов,
4 прохода,
3 прохода (h = 2,1; 0,2; 0,06 мм)
Проведенный анализ влияния различных параметров процесса глубинного шлифования на появление различных дефектов и снижение усталоcтной прочности замков лопаток турбин позволил наметить пути ликвидации этих дефектов и интенсифицировать этот процесс обработки.
334
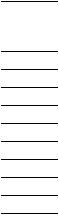
В ОАО «Пермский моторный завод» в течение 1985–1995 гг. проведен большой комплекс научно-исследовательских работ по оптимизации процесса глубинного шлифования «елочных» замков лопаток турбин различных авиационных двигателей и наземных установок из жаропрочных литейных сплавов ЖС26, ЖС32, ЧС70, ЖС6К, ЖС6УВИ, деформируемых сплавов ЭИ437БУ-ВД и ЭИ787-ВД.
Предварительные исследования показали существенное влияние на изменение σ–1 основных параметров шлифования. Как уже указывалось выше, различные параметры глубинного шлифования оказывают влияние на шероховатость, наклеп и величину градиента остаточных напряжений в тонком поверхностном слое замков лопаток, которые, в свою очередь, влияют на величину σ–1.
Первоначально отрабатывались режимы шлифования импортными высокопористыми кругами из белого электрокорунда 89А 100 G2 11 АV фирмы «Тиролит». Исследованы обычно применяемые трехпроходные режимы глубинного шлифования «елочного» профиля хвостовиков лопаток из жаропрочных никелевых сплавов ЖC6К и ЖС6УВИ с предварительной обработкой клина
(табл. 27).
Таблица 2 7
Режимы глубинного шлифования с предварительной обработкой клина
Режим |
Проход |
Скорость |
Скорость |
Глубина |
Глубина |
Предел |
Время |
круга, |
стола, |
шлифова- |
правки, |
выносливо- |
обработ- |
||
|
|
м/с |
мм/мин |
ния, мм |
мм |
сти, МПа |
ки, мин |
|
1 |
25 |
120 |
1,9…2,1 |
0,15 |
|
|
Р1 |
2 |
25 |
150 |
0,20 |
0,15 |
80 |
12,5 |
|
3 |
30 |
200 |
0,05 |
– |
|
|
|
1 |
25 |
50 |
1,9…2,1 |
0,15 |
|
|
Р2 |
2 |
25 |
150 |
0,20 |
0,15 |
90…100 |
15,0 |
|
3 |
30 |
200 |
0,05 |
– |
|
|
|
1 |
27 |
50 |
1,9…2,1 |
0,15 |
|
|
Р3 |
2 |
27 |
100 |
0,09 |
0,15 |
90 |
18,5 |
|
3 |
27 |
100 |
0,05 |
– |
|
|
|
|
|
|
|
|
|
335 |
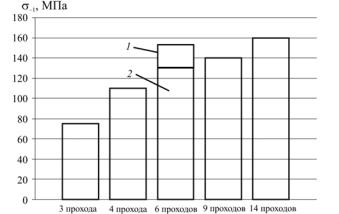
В результате экспериментов выбран режим обработки Р1, обеспечивающий требуемую геометрию «елочных» профилей, отсутствие прижогов и достаточно высокую производительность (12,5 мин на 4 одновременно обрабатываемые лопатки). По сравнению с профильным фрезерованием глубинное шлифование на режиме Р1 обеспечивает повышение производительности обработки в 3–4 раза.
Проведенные усталостные испытания показали (рис. 174), что предел выносливости «елочных» замков лопаток σ–1, обработанных методом глубинного шлифования на режиме Р1, составляет 80 МПа, что значительно меньше требуемого σ–1 = 140 МПа. С целью повышения предела выносливости замков лопаток были опробованы трехпроходные режимы глубинного шлифования с уменьшенной до 50 мм/мин подачей на первом проходе Р2 (см. табл. 28) и с уменьшенной до 100 мм/мин подачей на втором и третьем проходах Р3. При этом режим Р3 соответствует режимам обработки «елочных» профилей хвостовиков лопаток на АО «Рыбинские моторы». Анализ результатов проведенных усталостных испытаний показал, что предел выносливости замков лопаток, обработанных по режиму Р2, увеличился до 90…110 МПа, обработанных по режиму Р3 – только до 90 МПа.
Рис. 174. Гистограмма изменения предела выносливости σ–1 замков лопаток турбины, обработанных за различное число проходов при шлифовании сплавов ЖС6УВИ и ЖС6К (σ–1 ≥ 140 МПа): 1 – импортные круги;
2 – отечественные круги
336
Таким образом, путем варьирования режимов при использовании трехпроходного цикла обработки установлена возможность управления величиной усталостной прочности, однако требуемый предел выносливости σ–1 = 140 МПа для высоконагруженных лопаток обеспечить не удалось.
Дальнейшие эксперименты показали (табл. 28), что наиболее эффективным путем повышения предела выносливости «елочных» замков лопаток и сохранения требуемой производительности является плавное снижение глубины шлифования по проходам за счет увеличения числа проходов с одновременным повышением скорости стола. Уменьшение глубины шлифования tшл снижает усилия резания Рz и Ру, а увеличение скорости детали способствует некоторому возрастанию температуры в зоне резания. В результате происходит снижение действия силового фактора на формирование высокого градиента сжимающих напряжений в тонком (5…10 мкм) поверхностном слое. Так, при снижении глубины шлифования с 0,60 до 0,02 мм усилие резания Ру уменьшается с 720 до 200 кН при скорости детали 100 мм/мин. При скорости детали 500 мм/мин это снижение еще больше – с 850 до 190 кН. Увеличение скорости детали с 100 до 500 мм/мин при глубине окончательного шлифования приводит к увеличению средней температуры контакта с 300 до 500 °С, что снижает градиент высоких сжимающих напряжений и создает более благоприятный для усталостной прочности характер их распределения по глубине поверхностного слоя.
Анализ изменения шероховатости показал, что с увеличением V cо 100 до 2000 мм/мин величина микронеровностей Ra увеличивается с 0,53 до 0,83 мкм, что не должно сказаться существенно на снижении σ–1. С увеличением скорости детали степень наклепа увеличивается незначительно с 35 до 42 %, а глубина наклепа не изменяется. В связи с этим при оптимизации процесса были опробованы режимы с увеличенным числом проходов (см. табл. 27).
337
Таблица 2 8
Режимы глубинного шлифования без предварительной обработки клина
|
Фирма- |
Но- |
Скорость |
Скорость |
Глубина |
Предел |
Время |
Ре- |
мер |
вынос- |
обра- |
||||
жим |
изготовитель |
про- |
круга, |
стола, |
шлифования, |
ливости, |
ботки, |
|
круга |
хода |
м/с |
мм/мин |
мм |
МПа |
мин |
|
|
|
|
|
|||
Р4 |
«Тиролит» |
1, 2 |
20…25 |
250…300 |
0,70…2,20 |
150 |
14 |
3, 4 |
20 |
300 |
0,30…0,45 |
||||
|
|
5, 6 |
20…25 |
300 |
0,025…0,125 |
|
|
Р5 |
«Ильич» |
1–3 |
25 |
250…350 |
0,50…1,80 |
160 |
15 |
4–6 |
20 |
350 |
0,15…0,40 |
||||
|
|
7–9 |
20…25 |
350 |
0,02…0,08 |
|
|
Р6 |
«Ильич» |
1–3 |
25 |
500 |
0,50…1,80 |
160 |
12 |
4–6 |
20 |
500 |
0,15…0,40 |
||||
|
|
7–9 |
20…25 |
500 |
|
|
|
Примечание: СОЖ 3…8 %, эмульсия «Аквол-6».
При использовании импортных кругов лучшие результаты были получены на шестипроходном шлифовании Р4 без предварительной обработки клина хвостовика лопаток. При использовании трехпроходного режима обе плоскости клина хвостовика обычно предварительно шлифуются с обеспечением припуска по вершинам «елочного» профиля в пределах 0,25…0,35 мм. При исключении предварительного шлифования припуск по вершинам «елочного» профиля составляет 1…2 мм.
Усталостные испытания лопаток, обработанных кругами фирмы «Тиролит» на шестипроходных режимах глубинного шлифования Р4 с тремя правками, показали, что предел выносливости замков лопаток составляет 150 МПа, что вполне удовлетворяет техническим требованиям.
Дополнительно были проведены исследования качества поверхностного слоя «елочного» профиля хвостовиков лопаток непосредственно после глубинного шлифования на режиме Р4, после от-
338
жига при температуре 960 °С в среде аргона, предусмотренного технологией, а также после профильного фрезерования.
Анализ полученных результатов показал, что в поверхностном слое после глубинного шлифования залегают сжимающие напряжения с максимальной величиной 140…330 МПа на глубине 10…20 мкм, переходящие на глубине 35…45 мкм в растягивающие величиной до 80…160 МПа. После отжига в среде аргона, предусмотренного технологией, глубина залегания сжимающих напряжений снижается до 20 мкм, а их максимальная величина – до 100 МПа. Шероховатость «елочного» профиля по параметру Ra составляет 0,4…0,5 мкм.
В связи с этим на станках SS13L был внедрен процесс шестипроходного глубинного шлифования на режиме Р4 (см. табл. 28) «елочных» профилей хвостовиков лопаток из никелевых сплавов ЖС6УВИ и ЖC6К импортными кругами. Цикл обработки составил 14 минут (на 4 лопатки), что привело к снижению трудоемкости в 4,5 раза по сравнению с фрезерованием, высвободилось 16 фрезерных станков, 22 фрезеровщика.
Ввиду того, что импортные круги, поставленные вместе со станками фирмой «Элб-Шлифф», закончились, проведены работы по внедрению отечественных высокопористых кругов. Были испытаны высокопористые круги завода «Ильич» 1 500×20…25×203, 25А 10П 31…32 12 К5/П40-15.
В результате испытаний установлено, что лопатки, прошлифованные этими кругами на шестипроходном режиме Р4, имели предел выносливости только 130 МПа, что меньше допустимого. Снижение предела выносливости «елочных» замков лопаток при использовании отечественных кругов, в отличие от импортных, может быть объяснено большим ростом сил резания в зоне шлифования, что, повидимому, связано с меньшей (в 1,5 раза) пористостью кругов, худшим качеством зерна и связки, неравномерностью их распределения в круге и большим дисбалансом. Так, токовая нагрузка электродвигателей при использовании отечественных кругов возрастает по срав-
339
нению с импортными на 8…15 %, причем большее возрастание наблюдается при шлифовании четвертой лопатки, что указывает на более интенсивное затупление (засаливание) отечественных кругов.
При использовании более мягких отечественных кругов характеристики 25А 10П 29…30 12 К5/П40-15 не удалось обеспечить требуемую точность «елочного» профиля ввиду катастрофически быстрого осыпания кругов. С целью обеспечения требуемого предела выносливости лопаток при шлифовании отечественными кругами с характеристиками 25А 10П 31…32 12 К5/П40-15 выбран наиболее рациональный режим девятипроходного шлифования Р5 с четырьмя правками, приведенный в табл. 27. При шлифовании «елочных» профилей на девятипроходном режиме Р5 предел выносливости «елочных» замков лопаток достигает 160 МПа.
За счет применения большого числа проходов, более высокой скорости стола и уменьшения глубины шлифования устранено интенсивное засаливание кругов, что приводит к идентичному качеству всех прошлифованных лопаток. Время цикла при шлифовании «елочных» профилей отечественными кругами на девятипроходном режиме Р5 составило 15 мин (на 4 лопатки), что позволило внедрить отечественные круги вместо импортных практически без потери производительности.
Отработанный режим девятипроходного глубинного шлифования Р5 (см. табл. 27) обеспечивает высокое качество поверхностного слоя и высокую надежность «елочных» хвостовиков только при использовании кругов в узком диапазоне твердости (ЗИ 31–32). При использовании более твердых кругов характеристики (ЗИ 33–34) на режиме Р5 предел выносливости «елочных» замков лопаток составлял только 130 МПа, что меньше требуемого. Причина снижения предела выносливости в данном случае заключается в повышенной засаливаемости более твердых кругов.
С целью уменьшения засаливаемости кругов с ЗИ 33–34 был отработан режим Р6 с повышенной до 500 мм/мин скоростью стола
340