
1270
.pdf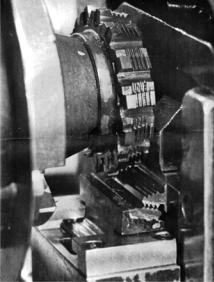
Припуск, снимаемый за один проход, составляет 1,4…1,7 мм. На ряде предприятий осуществляется операция окончательного фрезерования после предварительного фрезерования или глубинного шлифования, т.к. считается, что при фрезеровании обеспечиваются требуемое качество обработки и усталостная прочность замков лопаток.
В то же время нужно отметить, что применяемые режимы резания при фрезеровании далеки до оптимальных, а использование фрез из быстрорежущих сталей еще больше снижает режимы обработки.
В ОАО «Пермский моторный завод» проведены исследования процесса скоростного фрезерова-
ния замков турбинных лопаток сзаменой марки инструментальных материалов фрез. Исследования проводились непосредственно в условиях механического цеха на конкретных лопатках турбин из жаропрочных деформируемых сплавов ЭИ867-ВД, ЭИ787-ВД, ЭИ437БУ-ВД и литейного сплава ЖС6К на горизонтально-фрезерном станке мод. 6М83Г при попутном фрезеровании на всю глубину профиля с подачей Sz = 0,03 мм/зуб (см. рис. 166). Для обеспечения более высокой жесткости станка и попутной подачи с заданной величиной осуществлена модернизация станка.
Исследования скоростного фрезерования проводились сравнительно с применяемыми в серийных условиях низкими режимами резания и материалами фрез. Для исследования износа и стойкости фрез
311
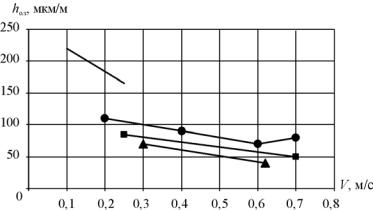
проводилось периодическое измерение фаски износа hз по задней поверхности каждого зубчика «елочной» фрезы на всех 14 зубьях. Всего проводилось 70 измерений износа hз после каждого съема фрезы.
При фрезеровании сплава ЭИ867-ВД (ХН72ВМКЮ) в серийном производстве применялись фрезы из быстрорежущей стали Р9М4К8 ЭП688. Скорость фрезерования была 0,20…0,25 м/с, что существенно ниже, чем рекомендованные НИИД режимы резания
(V = 0,5 м/с, Sz = 0,03 мм/зуб, t = 2 мм, В = 10…15 мм, z = 12 зубьев, dфр = 90 мм). Фрезерование на более низких режимах сопровождается
быстрым износом и значительной нестабильностью разброса размеров замка лопатки (до 0,08 мм вместо 0,02 мм).
Также проводились исследования фрезами из твердых сплавов ВК6М и ВРК15 на скоростях резания 24, 30, 40 м/мин. В результате исследований установлено, что наименьшую интенсивность износа hо.з.о = 73 мкм/м имеет фреза, оснащенная рениевым твердым сплавом ВРК15 при оптимальной скорости резания Vo = 30 м/мин с применением в качестве СОЖ 4 %-ной эмульсии Аквол-6 (рис. 167). Фрезерование на оптимальной скорости резания обеспечивает повышение стойкости фрез из ВРК15 в 2 раза (с 35 до 70 лопаток) по сравнению с фре-
Рис. 167. Изменения интенсивности износа фрезы при увеличении скорости фрезерования замков различных труднообрабатываемых сплавов ЖС6К,
ЭИ867-ВД,
ЭИ787-ВД,
ЭИ437БУ-ВД
312
зами из Р9М4К8Ф, более ровный и стабильный характер износа. Кроме того, с увеличением скорости резания с 12 до 30 м/мин уменьшаются усилия резания в 2–2,5 раза, что снижает степень наклепа поверхностного слоя и уменьшает погрешность геометрических параметров замков с 0,08…0,10 до 0,03 мм. При этом в поверхностном слое снижается величина максимальных растягивающих напряжений с 340 до 210 МПа, а величина шероховатости стабилизируется в пределах Ra = 0,32 мкм вместо нестабильной шероховатости Ra = 0,28…0,80 мкм при серийном фрезеровании.
Фрезерование замков лопаток из сплава ЭИ787-ВД (ХН35ВТЮ-ВД) в серийных условиях проводилось твердосплавными «елочными» фрезами из ВК6М и ВК6ОМ на скоростях резания 15 м/мин с подачей Sz = 0,04 мм/зуб. При этом стойкость фрез составляет 25–35 лопаток при допустимом износе зубьев 0,25…0,30 мм. Низкая стойкость фрез приводила к частым переточкам и нестабильности геометрии профиля и качества поверхности. Согласно нормативам НИИД рациональной скоростью резания для фрез из ВК6М является V = 40 м/мин при Sz = 0,03 мм/зуб.
Исследования проводились фрезами из твердого сплава ВК6М диаметром 78 мм, z = 14 зубьев, γ = 0, α = 9…10°, задний угол по профильной части αп = 0…40′ на режимах V = 15 м/мин и V = 40 м/мин с подачей Sz = 0,03 мм/зуб. При фрезеровании на скорости резания 15 м/мин интенсивность износа зубьев составляла 92 мкм/м, а при скорости резания V = 40 м/мин hо.з.о = 53 мкм/м (см. рис. 167). Отмечено большое затирание на боковых режущих гранях зубцов «елочного» профиля фрез, где фактический задний угол составляет 30…40 мин. Применение в качестве СОЖ вместо эмульсии масла МР-7 позволяет уменьшить эту затертость и поднять стойкость фрез в 4–5 раз. Повышение скорости резания с 15 до 40 м/мин и замена СОЖ позволили поднять стойкость фрез с 35 до 150 штук обработанных деталей, т.е. в 4,28 раза. Производительность труда при этом повысилась в 2 раза, снизились усилия резания не менее чем в 2 раза. Стабилизировалась шероховатость по-
313
верхности замков на уровне Ra = 0,32 мкм. Степень наклепа уменьшилась c 53,0 до 16,5 %. Остаточные напряжения практически не изменяются и остаются растягивающими c уровнем 280…310 МПа на глубине 50…80 мкм, а затем переходят в сжимающие.
Фрезерование на повышенных скоростях резания с СОЖ МР-7 обеспечивает более стабильную обработку по точности с меньшим количеством подналадок. Фрезерование «елочных» замков лопаток турбин из сплава ЭИ437БУ-ВД в серийном производстве происходило
спомощью фрез, оснащенных твердым сплавом ВК6ОМ и быстрорежущей сталью Р9М4К8Ф. Скорость резания составляла 18 м/мин при подаче Sz = 0,05 мм/зуб, что существенно ниже скорости, рекомендованной НИИД (V = 36…45 м/мин при Sz = 0,03…0,04 мм/зуб).
Фрезерование на низкой скорости резания приводило к быстрому износу и большому разбросу размерных параметров замков лопаток. Для скоростного фрезерования применялись фрезы, оснащенные твердым сплавом ВРК15. Фрезерование производилось на скорости 18 м/мин фрезой из ВК6ОМ и на скорости 36 м/мин фрезой из ВРК15.
Повышение скорости фрезерования и замена марки твердого сплава позволили снизить интенсивность износа фрез с 71 до 40 мкм/м. Стойкость фрез возросла с 35 до 70 деталей. Уменьшилось выкрашивание режущих кромок зубьев фрез. Усилия резания снизились в 1,5 раза. Величина шероховатости поверхности фрезерованных замков лопаток несколько снизилась: с Ra = 0,52…0,66 мкм до Ra = 0,52…0,37 мкм при меньшем размахе варьирования. Степень наклепа практически не изменилась, а глубина наклепа снизилась
с25…30 до 15…20 мкм. Остаточные напряжения носят более благоприятный характер распределения в поверхностном слое обработанных деталей. Точность размеров замков лопаток повысилась и стала более стабильной.
Фрезерование «елочных» замков лопаток турбин из литейных сплавов ЖС6К и ЖС6УВИ производилось твердосплавными фреза-
314
ми ВК6М на низкой скорости резания 5 м/мин. Рекомендуемая НИИД скорость фрезерования – 15 м/мин при использовании твердосплавных фрез. Фрезерование на низкой скорости резания приводило к быстрому износу и выкрашиванию фрез. Качество и точность обработки были весьма нестабильными.
Для скоростного фрезерования были изготовлены фрезы из сплава ВК6ОМ с мелкозернистой структурой. Перед сборкой фрез пластинки твердого сплава ВК6ОМ специальной формы 2306/1, полученные с опытного завода ВНИИТС (г. Москва), проверялись методом ЛЮМ на отсутствие трещин, термообрабатывались для выравнивания структуры и снятия внутренних напряжений. Напайка пластинок производилась методом ТВЧ латунной проволокой Л62. Охлаждение после напайки происходило в ящике с песком при температуре 433 К в течение 4 часов, а затем на воздухе. После напайки и предварительной шлифовки фрезы вновь проверялись на отсутствие трещин. Так, из 12 изготовленных фрез три были забракованы по сколам режущих кромок, а две фрезы – по микротрещинам на одной из 14 режущих пластинок.
Сравнительные исследования производились на скорости резания 5 м/мин с подачей 0,04 мм/зуб фрезой из ВК5М и на скорости резания 15 м/мин с подачей 0,03 мм/зуб фрезой из ВК6ОМ. Отмечена весьма высокая интенсивность износа фрез, превышающая более чем в два раза интенсивность износа при фрезеровании деформируемых сплавов (см. рис. 167). С увеличением скорости резания и заменой марки твердого сплава интенсивность износа уменьшилась с 210 до 165 мкм/м, т.е. в 1,3 раза. Количество обработанных лопаток между переточками увеличилось с 15–19 до 22–25 шт. Кроме того, при увеличении скорости резания снизились усилия резания в 1,5 раза, уменьшился наклеп поверхности и обеспечен более благоприятный характер распределения остаточных напряжений.
Обобщенные результаты проведенных исследований представлены на графиках hо.з = f (V) (см. рис. 167) и сведены в табл. 26. Анализ табл. 26 и графиков показал, что применение скоростных режимов
315
фрезерования наиболее существенно повышает производительность при обработке деформируемого сплава ЭИ787-ВД.
Таблица 2 6
Результаты внедрения повышенных режимов фрезерования «елочных» замков лопаток турбин из различных жаропрочных сплавов
Марка обра- |
|
Серийный режим |
|
|
Скоростной режим |
|
K* |
||||||
батываемого |
V, |
S*, |
tшт, |
Ra, |
Н, |
σоmax, |
V, |
S, |
tшт, |
Ra, |
Н, |
σо max, |
|
материала |
м/с |
мм/мин |
мин |
мкм |
% |
МПа |
м/с |
мм/мин |
мин |
мкм |
% |
МПа |
|
ЭИ867-ВД |
0,20 |
28 |
7,9 |
0,28 |
34 |
+340 |
0,50 |
52 |
6,5 |
0,32 |
28,0 |
+210 |
2,00 |
ЭИ787-ВД |
0,25 |
35 |
7,3 |
0,35 |
53 |
+310 |
0,65 |
62 |
6,3 |
0,26 |
16,5 |
+310 |
4,28 |
|
|
|
|
0,58 |
|
|
|
|
|
0,42 |
|
|
|
ЭИ437БУ-ВД |
0,31 |
55 |
6,5 |
0,52 |
4,7 |
+245 |
0,61 |
80 |
6,0 |
0,37 |
4,7 |
+150 |
2,00 |
|
|
|
|
0,66 |
|
|
|
|
|
0,52 |
|
|
|
ЖС6К |
0,09 |
14 |
10,7 |
0,82 |
48 |
+190 |
0,25 |
35 |
8,3 |
0,32 |
42,0 |
+200 |
1,30 |
0,63 |
0,63 |
* S – продольная подача детали; K – коэффициент повышения стойкости
Менее производительна обработка сплава ЖС6К. Наименьшая трудоемкость фрезерования при обработке лопаток из сплава ЭИ437БУ-ВД: tшт = 6 мин. Наибольшая трудоемкость при обработке сплава ЖС6К: tшт = 8,3 мин. Наибольшую стойкость имеют фрезы при обработке сплава ЭИ787-ВД: 150 шт. (K = 4,28), а для сплава ЖС6К – 23 шт. (K = 1,3).
6.3. Эффективность процесса глубинного шлифования «елочных» замков турбинных лопаток
Глубинное шлифование кинематически представляет собой метод шлифования с большой глубиной резания и малой продольной подачей детали. По скорости съема металла этот метод часто превосходит другие методы абразивной и лезвийной обработки, но сохраняет при этом все преимущества шлифования, т.е. высокую геометрическую точность, малую шероховатость и т.д. Величина слоя металла, удаляемого при глубинном шлифовании за один проход, может достигать 5…10 мм, а величина продольной подачи детали
316
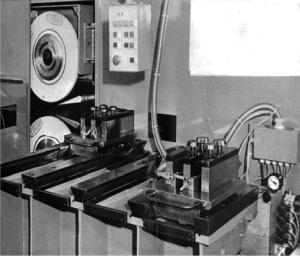
изменяется от 50 до 2 000 мм/мин и более и зависит от типа обрабатываемого материала, глубины резания, характеристики абразивного инструмента, вида СОЖ и способа ее подачи, требований к качеству обрабатываемых поверхностей.
Для глубинного шлифования применяются специальные станки, имеющие более высокую жесткость, мощность, точность, чем универсальные станки. Оснащаются эти станки многокоординатными системами ЧПУ, а также рядом систем и устройств, стабилизирующих техпроцесс. К ним относятся системы высоконапорной подачи СОЖ, охлаждения и очистки СОЖ, автоматического поддержания постоянной скорости резания, динамической балансировки и автоматической правки кругов и т.д. В настоящее время применяются станки фирмы «Элб-Шлифф» мод. SS13L (Германия) (рис. 168) и Липецкого станкозавода мод. ЛШ233. Станки фирмы «Элб-Шлифф» более надежны в работе, чем ЛШ233, особенно по системам ЧПУ. Конструкции этих станков предусматривают одновременную обработку замков четырех лопаток с двух сторон
Рис. 168. Станок SS13L для глубинного шлифования турбинной лопатки с двух сторон
317
двумя шлифовальными кругами. В результате производительность обработки замков в несколько раз выше, чем при фрезеровании или маятниковом шлифовании.
Верхний и нижний шлифовальные круги настраиваются с помощью встроенного командного компьютера и электронного пульта на нужный размер замка. Этот размер сохраняется с учетом постоянного износа кругов с помощью компьютерной системы ЧПУ. Предусмотрено попутное направление шлифования. Периодически, по мере износа кругов, предусматривается их автоматическая правка алмазным фасонным роликом, установленным на столе станка. По команде от ЧПУ к алмазному ролику подводятся последовательно верхний и нижний круги. Правка производится методом врезного шлифования с соотношением скоростей ролика Vpол и круга Vкр 0,7– 0,8. Осуществляется попутная правка. Прямым следствием обработки с большой глубиной резания является увеличенная длина дуги контакта шлифовального круга с деталью, что приводит к возрастанию мощности резания, сил резания и общей тепловой напряженности в зоне резания. Поэтому большое внимание уделяется интенсивному отводу тепла из зоны резания с помощью высоконапорной подачи CОЖ.
Вкачестве СОЖ используется 3 % раствор эмульсола «Пермол-6» производства Завода смазок и СОЖ (г. Пермь).
Для глубинного шлифования разработаны специальные высокопористые шлифовальные круги диаметром 450…500 мм (рис. 169). Образование пор в кругах производится в процессе изготовления за счет выгорания или выплавления специальных поробразователей.
Впорах круга при глубинном шлифовании размещаются стружка и шлам, которые затем вымываются наружу высоконапорной струей СОЖ и под действием центробежной силы при вращении кругов.
Профилирование и восстановление режущей способности производится правящим алмазным роликом. При изготовлении роликов предъявляются высокие требования к точности корпуса, посадочных отверстий, наружного профиля. Так, биение торцев корпуса наружного диаметра профиля допускается в пределах 0,002…0,005 мм.
318
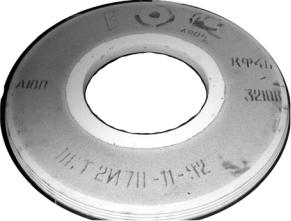
Рис. 169. Шлифовальный высокопористый круг после обработки замка лопатки
Стойкость правящих роликов зависит от метода изготовления применяемых искусственных или естественных алмазов, режимов правки и др. Ролики изготавливаются на специальном участке инструментального цеха.
Для контроля твердости покупных высокопористых кругов совместно с ВНИИАШ (г. С.-Петербург) разработан прибор «Звук- 202-02», который измеряет частоту собственных колебаний кругов, возбуждаемых ударом (молотком).
Возникающие свободные колебания воспринимаются датчиком (микрофоном), усиливаются и поступают на систему фильтров. Из спектра частот выделяется сигнал частотой, соответствующей выбранному виду шлифовального круга. Полученное значение измеряется частотомером и выводится на цифровое табло. Разработана таблица звуковых индексов, где определенному диапазону частот соответствует свой звуковой индекс.
Данный прибор позволяет точнее и быстрее, чем с помощью пескоструйного прибора, определять твердость шлифовальных кругов и обеспечивает 100 %-ный контроль вновь поступающих кругов.
319
В результате имеется возможность подбирать круги с заданными фи- зико-механическими свойствами для конкретных операций шлифования, а также не допускать на ответственные операции круги с повышенной или пониженной твердостью.
Анализ литературных данных показал, что и теоретические данные, и практика заводов рекомендуют применять число проходов шлифовального круга 2–3, скорость круга – 20…30 м/с, скорость движения детали – от 50 до 200 мм/мин, общий снимаемый припуск – 2…3 мм без предварительной подготовки клина и 0,3…1,5 мм – при подготовке клина замка лопатки. Направление шлифования попутное.
Правка кругов |
производится |
алмазными |
роликами отечественного |
и импортного |
производства |
зернистости |
400/315–630/500 обычно |
из синтетических алмазов марок АС65Т, АС82Т, АС132Т на следую-
щих режимах: Vкр = 25 м/с, Vрол = 20 м/с, подача круга на ролик 2 мкм/ об. кр. при непрерывной правке, время выхаживания 5…7 с.
Вкачестве режущего инструмента применяются высокопористые круги импортного и отечественного производства из электрокорунда белого типа 24А, зернистости 10–12, твердости ВМ1-ВМ2 (звуковой индекс ЗИ 31–34), 10–12-й структуры, на керамической связке типа К5ПГ с порообразователями из перлита (П) или фруктовой косточки (КФ) с размером зерен порошка в среднем 400 мкм. Круги должны выполняться с точностью класса А и иметь первый класс неуравновешенности.
Основной критерий при оптимизации процесса глубинного шлифования на ОАО «Пермский моторный завод» – это требование обеспечения установленного предела усталостной прочности обработанных деталей при хорошей производительности обработки, высоком качестве и точности деталей.
Вто же время в рассмотренных рекомендациях НИИД, НПО «Сатурн» (ОАО «Рыбинские моторы»), РГАТА отсутствуют мероприятия по обеспечению требуемой усталостной прочности замка лопатки турбины. Для реализации этого условия по требованию конструкторов и представителей заказчика разработаны специальные инст-
320