
1270
.pdfрукции для каждого изделия по периодическому контролю сопротивления усталости как профильной части пера, так и замковой части рабочих лопаток турбин. На других предприятиях моторостроения требование проведения усталостных испытаний замковой части лопаток отсутствует из-за малого ресурса выпускаемых изделий.
Новый современный авиационный двигатель ПС90А (и его модификации) в последнее время достиг ресурса безотказной работы до 9 200 часов, поэтому обеспечению высокой надежности работы всех деталей двигателя постоянно уделяется большое внимание: в частности, введено дополнительное требование обеспечения заданной усталостной прочности замковых частей лопаток турбин, работающих в тяжелых термодинамических и вибрационных условиях. Кроме того, проведение периодических усталостных испытаний лопаток турбин позволяет судить о стабильности технологии изготовления данных деталей. Испытания проводились согласно ОСТ 1.00870–77. Доминирующими критериями при оценке прочности лопаток турбин являются уровень вибронапряжений в лопатках, замеренный на изделии, и фактический предел выносливости «елочного» замка лопатки. Предел выносливости σ–1 по «елочному» замку рабочих лопаток определяется обычно на первых ступенях турбин. Так, для лопаток изд. Д30Ф6 из сплава ЖС6УВИ допустимый предел выносливости σ–1 = 140 МПа, для лопаток изд. ПС90А из сплава ЖС26 σ–1 = 100 МПа.
Величины допустимых значений σ–1 выбираются из расчета обеспечения запаса прочности по замку в пределах нормы прочности, установленной Центральным институтом авиационного моторостроения (ЦИАМ) по результатам замера фактических максимальных вибронапряжений σmax в лопатках на изделии. Норма прочности kн определяется по формуле
kн = σ–1/σmax. |
(89) |
Кроме этого, в инструкции по усталостным испытаниям записано требование обеспечения контроля возникающих при обработке трещин методом ЛЮМ. Свечение на «елочном» профиле после обработки не допускается.
321
Усталостные испытания замков лопаток после различных видов обработки выполнялись на воздушно-пульсирующем стенде ВПС-35 по первой форме изгибных колебаний лопаток по симметричному циклу с частотой основного тона. Режим испытаний задавался и контролировался по тензорезистору № 1 и дополнительно по тензорезисторам № 2 и № 3. База испытаний – 2×106 циклов. Периодические колебания обеспечивались за счет подачи сжатого воздуха через модулирующий вращающийся диск с отверстиями. Для испытаний замков лопаток в зажимном приспособлении занижена площадка контакта на 0,9…1,0 мм по первой впадине «елочного» профиля, испытывающей максимальную нагрузку.
За предел выносливости принято максимальное напряжение, заданное по тензорезистору № 1, соответствующее наработке базы 2×106 циклов, при котором не разрушилось 6 штук лопаток. В случае разрушения хотя бы одной лопатки проводилось повторное испытание, но уже на партии из 25 лопаток. В этом случае определяется действительный предел выносливости σ–1 лопаток турбин. Если σ–1 фактически ниже допустимого, то данный технологический процесс считается нестабильным, и разрабатываются мероприятия по повышению стабильности процесса и увеличению предела усталостной прочности до необходимого значения.
Помимо дополнительных усталостных испытаний лопаток турбин в случае снижения предела усталостной прочности проводится контроль макро- и микроструктуры, остаточных напряжений и наклепа поверхностного слоя, анализ химсостава материала лопаток.
Анализ результатов исследований остаточных напряжений и наклепа позволяет судить о термодинамических процессах, происходящих в поверхностном слое обработанных деталей, и их влиянии на изменение усталостной прочности. Освоение процесса глубинного шлифования замков лопаток турбин из жаропрочных литейных сплавов ЖС6К, ЖС32, ЖС26, ЖС6УВИ, ЧС70 потребовало ряда серьезных научных исследований для решения проблемы обеспечения требуемого качества и усталостной прочности замков.
322
Простое копирование процесса глубинного шлифования, согласно разработкам и рекомендациям предыдущих исследователей, оказалось невозможным в связи с более жесткими требованиями на ОАО «Пермский моторный завод» и появлением новых сплавов типа ЖС26, ЖС32, ЧС70.
Первые же опыты по глубинному шлифованию на режимах, рекомендованных НИИД, показали, что требования по обеспечению качества и нужной усталостной прочности не выполняются. После глубинного шлифования на поверхности «елочного» профиля замков отдельных лопаток обнаружены трещины на зубьях и во впадине (рис. 170). Трещины обнаружены на некоторых «елочных» замках и после усталостных испытаний. На отдельных лопатках выявлены следы вибраций, волнистости и прижогов.
Сравнительные усталостные испытания 25 замков лопаток 1-й ступени двигателя Д30Ф6 из сплава ЖС6К показали, что после глубинного шлифования на режимах для 1-го прохода – Vкр = 25 м/с, t = 1,5…2,0 мм, Vдет = 100 мм/мин; для 2-го прохода – Vкр = 20 м/с,
t = 0,2 мм, Vдет = 150 мм/мин; |
для |
3-го |
прохода |
– Vкр = 30 м/с, |
t = 0,05 мм, Vдет = 200 мм/мин, |
при |
правке кругов |
с Vкр = 20 м/с, |
|
Vрол = 18 м/с, Spол = 2,0 мм/мин, |
временем |
выхаживания tвых = 5 с |
и глубиной правки hпр = 0,15 мм замки лопаток турбины имеют низкий предел выносливости σ–1 = 80 МПа вместо требуемого по инструкции 140 МПа. В то же время усталостные испытания фрезерованных лопаток подтвердили требуемый предел выносливости σ–1 = 140 МПа. В связи с этим проведен анализ возможных причин снижения σ–1, разработаны и проведены мероприятия по их устранению и стабилизации процесса.
Анализ формы расположения и микроструктуры трещин в замках лопаток показал (см. рис. 170), что большинство трещин носит усталостный характер. Часть трещин идет под углом 30° к наружной поверхности (см. рис. 170, а), а часть – в глубь металла под прямым углом (см. рис. 170, б). Обнаружены трещины и во внутренней полости замка лопатки, в алитированном слое (см. рис. 170, в) после глубинного шлифования. Причем протяженность этих трещин достигала 9…12 мм, а глубина – 0,1…0,4 мм.
323
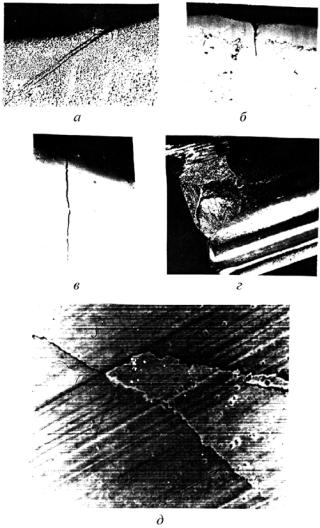
Рис. 170. Характер трещинообразования в замках лопаток турбин после глубинного шлифования: а, б, в – ×300; г – ×6; д – ×650
Излом по трещине (см. рис. 170, г) представляет собой несколько площадок усталостных внутрикристаллических сколов, расположенных под углом 45° к основанию первой впадины замка. Преиму-
324
щественное ориентирование усталостной трещины идет от основания первого зуба, далее в результате перераспределения напряжений образуются крупнокристаллические сколы. Дефектов материала в изломе не обнаружено.
Исследование поверхности первого паза замка лопатки на растровом микроскопе РЭМА-202 (см. рис. 170, д) выявило продольные риски различной ширины и глубины вдоль паза от следов зерен высокопористого шлифовального круга. Трещины в пазу местами совпадают с этими острыми глубокими рисками, а иногда идут под углом 45…60° к рискам.
Усталостные испытания замков лопаток первой ступени двигателя ПС90А из сплава ЖС26, обработанных глубинным шлифованием, также показали снижение усталостной прочности до 90 МПа вме-
сто 100…110 МПа по инструкции. Это отрицательно |
сказалось |
на проведении плановых работ по увеличению ресурса |
двигателя |
ПС90А. Ресурс двигателя был ограничен до 1 700 часов до выяснения причин снижения усталостной прочности. Поэтому проведено исследование всего комплекса технологического процесса изготовления лопаток турбин, включающего как металлургическое, так и механообрабатывающее производство. Проведено исследование влияния режимов глубинного шлифования, применяемых кругов, правящих роликов, режимов правки, качества и типа СОЖ на основные параметры качества поверхностного слоя – остаточные напряжения, наклеп и шероховатость поверхности – и на усталостную прочность замков лопаток.
Анализ остаточных напряжений в замках лопаток показал, что на всех режимах глубинного шлифования характер распределения практически одинаков, но величина и глубина распространения различная. Типовой характер распределения осевых остаточных напряжений с обеих сторон замка лопатки из сплава ЖС6УВИ представлен на рис. 171. После шлифования в тонком поверхностном слое замков на глубине 25…40 мкм наводятся сжимающие остаточные напряжения максимум 180…650 МПа на глубине 5…15 мкм. Эти напряжения переходят в небольшие растягивающие +50…+100 МПа на глубине
325
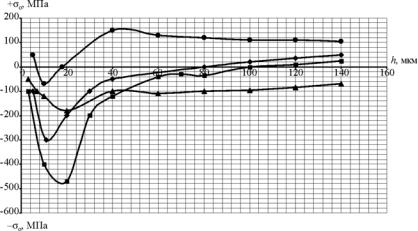
Рис. 171. Изменение остаточных напряжений по глубине поверхностного слоя после глубинного шлифования III проход, 1-я лоп. (h = 0,6 мм);
III проход, 4-я лоп.
(h = 0,6 мм); IX проход, 4-я лоп. (h = 0,1 мм);
IX проход, 1-я лоп. (h = 0,1 мм)
25…40 мкм. После механической обработки лопатки турбин проходят термообработку в виде отжига для снятия напряжений. После отжига величина остаточных напряжений уменьшается до –20…– 150 МПа.
Для повышения усталостной прочности замков лопаток турбин после глубинного шлифования и отжига предложено ввести дополнительную операцию обдувки замков стальными микрошариками на специальной дробеметной установке. В результате остаточные напряжения сжатия вновь возросли и составили для 3-минутного времени упрочнения –280…–400 МПа, а для 15-минутного времени упрочнения –310…–600 МПа. Глубина залегания сжимающих напряжений возросла до 50…80 мкм, после чего остаточные напряжения переходят в растягивающие: до +80…+200 МПа на глубине 140 мкм. Анализ глубины и степени наклепа показал, что после глубинного шлифования глубина наклепа h составляет 20…30 мкм, а степень наклепа Н = 19…24 %, после
326
отжига |
h = 9…14 мкм, Н = 5…20 %, после |
упрочнения |
h = 10…20 мкм, Н = 14,1 %. |
|
|
Сравнительное исследование усталостной прочности замков |
||
лопаток |
и образцов-имитаторов «елочного» замка |
из сплава |
ЖС6УВИ, проведенное как в ОАО «Пермский моторный завод», так и в ЦИАМе при нормальной (293 К) и рабочей (923…973 К) температурах, показало, что упрочнение микрошариками повышает предел выносливости на 25…60 % по сравнению с неупрочненными деталями. В результате упрочнения предел выносливости σ–1 повысился до 110…120 МПа, что было еще недостаточно для серийного производства лопаток из сплава ЖС6УВИ. Поэтому проведено дополнительное исследование процесса глубинного шлифования.
Статистический анализ максимальной величины сжимающих остаточных напряжений, возникающих на различных режимах глубинного шлифования, и последующих результатов усталостных испытаний показал, что величина предела выносливости σ–1 в значительной степени зависит от величины градиента сжимающих напряжений в весьма тонком поверхностном слое от 2 до 10 мкм. Установлено, что чем больше величина градиента изменения Δσсж, тем меньше предел выносливости σ–1. Оптимальной величиной градиента сжимающих остаточных напряжений, обеспечивающих σ–1 = 140 МПа, является Δσсж = 200…300 МПа, не более. При увеличении Δσсж более 300…400 МПа предел выносливости замков лопаток снижается относительно требуемого. Так, например, после усталостных испытаний были определены остаточные напряжения на замках лопаток, выдержавших и не выдержавших требуемый предел выносливости. На лопатках, выдержавших σ–1 = 140 МПа, Δσсж = 300 МПа, а на лопатках, не выдержавших испытание, Δσсж = 500 МПа на глубине 5…10 мкм.
Следует отметить, что аналогичные результаты по снижению усталостной прочности замков лопаток после глубинного шлифования по сравнению с фрезерованием были обнаружены Н.С. Рыкуновым при проведении исследований на Уфимском МПО. Возможной причиной снижения усталостной прочности могут быть длинные про-
327
дольные глубокие риски от абразивных зерен шлифовальных кругов. По сравнению с фрезой, имеющей наружный диаметр 70…90 мм, диаметр шлифовального круга обычно 450…500 мм. Поэтому длина дуги контакта шлифовального круга в несколько раз больше, чем у фрезы. После фрезерования на поверхности замков видны короткие, 2…5 мм, риски, имеющие ровные края и небольшую глубину.
На поверхности замков, обработанных глубинным шлифованием, видны длинные продольные риски различных размеров и глубины. Края их острые, рваные, с выдавленными заусенцами. В самих рисках видны следы адгезионного взаимодействия металла, налипшего на зерно, и металла детали. На профилограмме шероховатости после глубинного шлифования можно видеть большое различие по высоте, глубине, остроте впадин микронеровностей. Такой неоднородный, случайный характер распределения микронеровностей можно объяснить, во-первых, врезным характером правки кругов алмазными роликами, имеющими достаточно крупную зернистость алмазных зерен – 300…500 мкм. Во-вторых, неравномерная шероховатость объясняется врезным характером шлифования и применением весьма мягких высокопористых шлифовальных кругов. Наличие крупных пор в круге и их низкая твердость приводят к большей неравномерности распределения режущих зерен на периферии круга как по высоте, так по ширине обрабатываемого профиля. В результате на периферии круга имеются абразивные режущие зерна, выступающие на 2…5 мкм, а также режущие зерна, выступающие на 1…2 мкм. Причем расположение этих зерен носит случайный, хаотический характер. После правки и при затуплении круга характер случайного распределения зерен может полностью измениться.
При проведении усталостных испытаний эти концентраторы могут быть очагами зарождения усталостных трещин, что подтверждается характером расположения усталостных трещин во впадинах «елочных» замков и в радиусе перехода к торцу замка. Очень часто трещины располагаются в продольном направлении, совпадая с глубокими рисками от шлифования.
328
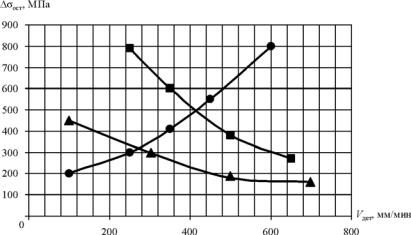
Проведено исследование влияния различных параметров глубинного шлифования на величину градиента остаточных сжимающих напряжений. На рис. 172 приведена зависимость Δσсж от изменения скорости детали Vдет, твердости применяемых кругов ЗИ и величины концентрации СОЖ эмульсии «Пермол-6».
Рис. 172. Влияние скорости подачи детали Vдет, концентрации СОЖ КСОЖ, твердости кругов ЗИ на градиент сжимающих остаточных напряжений Δσост после глубинного шлифования замков лопаток турбины
ЗИ,
Vдет,
КСОЖ
Установлено, что с увеличением скорости детали Vдет (подачи
стола) Δσсж уменьшается с 750 МПа при Vдет = 250 мм/мин до 270 МПа при Vдет = 290 мм/мин при одинаковых других условиях шлифования. Увеличение концентрации СОЖ с 1 до 7 % приводит
к снижению Δσсж от 450 до 150 МПа.
Установлено существенное влияние на градиент остаточных сжимающих напряжений основных параметров и качества применяемых высокопористых кругов. С увеличением твердости кругов
сЗИ 31 до ЗИ 41 градиент остаточных напряжений резко возрастает
с200 до 800 МПа. Именно это явилось, по-видимому, одной из причин нестабильности процесса глубинного шлифования, случайного характера снижения усталостной прочности на отдельных замках
329
лопаток турбин после глубинного шлифования. Дело в том, что абразивный завод «Ильич» (г. С.-Петербург) выпускал высокопористые круги с широким диапазоном звуковых индексов: от ЗИ 29 до ЗИ 45 в одной партии кругов исходя из специфики своего производства, а по условиям технологии требовались круги ЗИ 31–32. Поэтому на операцию глубинного шлифования могли попасть более твердые круги ЗИ 34–35, которые создавали более высокий градиент Δσсж
иснижали предел выносливости.
Всвязи с недостаточным качеством отечественных высокопористых кругов на ОАО «Пермский моторный завод» введен 100 %-ный контроль твердости, пористости, дисбаланса покупных кругов с отбраковкой негодных.
Проведен анализ качества и эксплуатационных параметров высокопористых шлифовальных кругов фирмы «Тиролит» (Австрия), кругов с порообразователями – перлит (П) и фруктовая косточка (КФ), кругов фирмы ЭКСИ (г. Курган) и фирмы «Экоабразив» («Станкин», г. Москва). Кроме того, проведено исследование работоспособности кругов, пропитанных спецсоставом на ацетоновой основе с дисульфидом молибдена.
Круги фирмы «Тиролит» (Австрия) были получены вместе с импортными станками мод. SS13L фирмы «Элб-Шлифф» в количестве 1 500 шт. Проверка твердости, пористости, дисбаланса показала высокие параметры качества: твердость на всех кругах в пределах одного звукового индекса ЗИ 32, пористость в норме, дисбаланс соответствует первому классу. Отмечены высокая равномерность расположения пор в круге, более чистое белое зерно электрокорунда. Содержание пор в круге – 33 %, зерна – 39 %, связки – 28 %. Удельный вес 1,55 г/см3. Глубинное шлифование замков лопаток этими кругами на шести проходах обеспечивает требуемый предел выносливости σ–1 = 140 МПа при градиенте Δσсж = –200…–300 МПа.
Отечественные круги фирмы «Ильич» с выгорающими порообразователями (П и КФ) значительно уступают импортным кругам по показателям качества и эксплуатационным свойствам. Абразивные зерна имеют сероватый цвет, поры различных размеров расположены весьма неравномерно в теле круга (особенное КФ), порис-
330