
1270
.pdf3.2.2. Расчет оптимальных скоростей резания при протягивании жаропрочных сталей и сплавов аналитическим методом
Высокая трудоемкость и сложность экспериментальных исследований процесса протягивания в значительной мере определяют малоизученность и недостаточную исследованность этого одного из самых эффективных на сегодняшний день методов финишной обработки деталей из труднообрабатываемых материалов.
Вто же время появление новых труднообрабатываемых материалов или модификация применяемых требуют проведения новых или дополнительных экспериментальных исследований по определению интенсивности износа протяжек, температуры резания и оптимальных скоростей резания.
Всвязи с этим возникла настоятельная потребность разработки аналитических методов расчета оптимальных режимов протягивания для любого обрабатываемого материала. Попытки разработки таких методик производились и раньше различными исследователями, но наиболее приемлемой является методика, разработанная под руководством С.С. Силина и А.С. Кондратова.
Вданной методике использованы наши опубликованные ранее результаты экспериментальных исследований по скоростному протягиванию различных труднообрабатываемых материалов, поэтому было бы весьма интересным сравнение полученных в результате аналитического расчета данных с нашими ранее полученными экспериментальными данными для конкретных пар обрабатываемых и инструментальных материалов. Кроме того, необходимо уточнить предлагаемый расчет оптимальной скорости резания, введя дополни-
тельно расчет оптимальной температуры резания θо по полученным ранее экспериментальным зависимостям и дополнительный коэффициент обрабатываемости для различных групп обрабатываемых материалов K5. Необходимо также разработать алгоритм и программу расчета Vо для ПЭВМ.
101
Вывод расчетной формулы для определения оптимальной скорости резания при протягивании выполнен на основании известного закона сохранения энергии, представленного в виде уравнения баланса механической и тепловой энергий:
Pz V = Qд + Qс + Qи + QСОЖ , Дж/с, |
(11) |
где Pz V – общая механическая энергия, Дж/с; Qд, Qс, Qи, QСОЖ – количество тепла, уходящее из зоны резания соответственно в деталь,
стружку, инструмент и СОЖ из контактной зоны резания.
Так как попадание СОЖ на контактные поверхности зуба протяжки в момент резания ограничено, то для практических расчетов
QСОЖ не учитывается.
Для определения Qд, Qс, Qи решаются специальные тепловые задачи, в которых в качестве исходных данных используются толщина a1 и ширина b1 cреза, коэффициенты теплопроводности обрабатываемого и инструментального материалов λ, передний γ и задний α углы протяжки, коэффициент температуропроводности a, радиус округления режущей кромки ρ, температура резания Т. Все эти исходные данные формализуются в виде следующих безразмерных
критериев подобия: |
|
|||
• критерий Пекле: Pe = V a1 / a, |
(12) |
|||
• |
E = ρ1 / a1, |
(13) |
||
• |
Г = λи / λ β ε, |
(14) |
||
• |
Д = a1 / b1, |
(15) |
||
причем ε = π−ϕ−ϕ1, β = π/ 2 −α− γ, |
(16) |
|||
где β и – углы действия; φ – угол скалывания. |
|
|||
В результате расчета тепловых задач получены следующие за- |
||||
висимости: |
|
|||
|
Qc = 0,91λ b1T |
Pe0,35Е0,3 |
(17) |
|
|
|
, Дж/с, |
||
|
(sin γ)0,25 (cos α)0,15 |
102
Q = 1,85 λ b T |
Pe0,65 Е0,3 |
, Дж/с, |
(18) |
|||
|
|
|||||
c |
1 |
|
(sin γ)0,08 |
|
|
|
Q = 0,6625 λ b T |
|
Г Д0,3 Е0,165 |
, Дж/с. |
(19) |
||
|
(sin α)0,15 |
|||||
и |
1 |
|
|
|
Подставляя выражения (17), (18), (19) в уравнение теплового баланса (11), получим:
|
P |
V = 1,85λ b T |
Pe0,65 Е0,3 |
+ 0,91λ b T × |
||||||||
|
(sin γ)0,08 |
|||||||||||
|
z |
1 |
|
|
|
|
1 |
(20) |
||||
|
|
|
|
|
|
|
|
|
|
|
||
× |
|
Pe0,35 Е0,15 |
|
+ 0,6625λ b |
T |
Г Д0,3 |
Е0,165 |
. |
||||
(sin γ)0,25 (cosα)0,15 |
|
|
|
|||||||||
|
|
|
|
1 |
|
(sin α)0,15 |
||||||
Отсюда находим в общем виде: |
|
|
|
|
|
|||||||
|
|
|
Pz V |
= ψ(Рe,Е,Г,Д, |
γ,α) , |
(21) |
||||||
|
|
|
λb T |
|
||||||||
|
|
1 |
|
|
|
|
|
|
|
|
|
где ψ – безразмерная функция.
Преобразуем левую часть уравнения (21):
Pz V |
= |
Pz V a1 |
, |
(22) |
|
λ b T |
a c |
a b T |
|||
1 |
|
ρ |
1 1 |
|
|
где а сρ = λ; V a1 / a = Pе; сρ – удельная объемная теплоемкость обрабатываемого материала, Дж/с ; а – коэффициент температуропроводности обрабатываемого материала, м2/с.
Произведем замену выражений в (22). Обозначим V a1 / a = Pе и а1 b1 cρ T / Pz = A – энергетический критерий подобия.
Получим:
Pz V |
= |
Pe |
(23) |
|
|
|
. |
||
λ b T |
А |
|||
1 |
|
|
|
|
Подставив выражение (21) в уравнение (23), получим:
Pе/А = ψ(Ре, Е, Г, Д, γ, α,...). |
(24) |
103

Решая это уравнение относительно Ре, получим: |
|
|
|||||
|
|
Ре = ψ1(А, Е, Г, Д, γ, α,...) |
|
(25) |
|||
или |
|
|
|
|
|
|
|
|
|
V a1/a = ψ1(A, Е, Г, Д, γ, α,...), |
|
(26) |
|||
отсюда |
|
|
|
|
|
|
|
|
|
V = а / а1ψ1(А, Е, Г, Д, γ, α,...) . |
|
(27) |
|||
Для режимов оптимального резания, когда |
V = Vо; |
T = Tо; |
|||||
Pz = Pz о, получим: |
|
|
|
|
|
||
|
a |
|
a1 b1 cρ To |
|
|
|
|
Vo = |
|
ψo A = |
|
, Е, Г, Д, γ,α,... . |
(28) |
||
a1 |
Pz 0 |
||||||
|
|
|
|
|
В этом выражении оптимальная температура резания Tо находится путем расчета по найденным ранее экспериментальным зависимостям для данного обрабатываемого материала.
Выражения Рz о находим, также используя метод подобия:
Pz о = b (τρ, а1, b1, Г, Д, Е, α, γ,...). |
(29) |
После подстановки Рz в выражение (29) получим окончательно следующее выражение Vо для протягивания:
Vo = a a1
|
λρ 0,1 |
|
cρ To |
|||||||
|
|
|
|
|
|
|
|
|
|
|
|
|
|
|
|
|
|
||||
|
λ |
|
|
|
|
τρ |
||||
|
|
|
|
|
|
|
||||
|
|
|
|
|
h |
|
−3 |
K3 |
||
× 1 |
+ |
3 |
|
|
||||||
|
|
|||||||||
|
|
|
|
|
l∑ |
|
|
|
||
|
|
|
|
|
|
|
|
1,68 |
|
22 800 |
(sin α)0,1 |
|
|||
|
|
|
|
|
|
|
× |
|
ρ |
|
0,5 |
|
|
||
|
|
(1− sin γ) |
0,3 |
|
|||
|
|
1 |
|
|
(30) |
||
|
a1 |
|
|
|
|
K4 K5 , , м/мин.
104
В полученном выражении (30) помимо известных введены следующие условные обозначения: ρ – радиус округления режущей кромки, мм; l∑ – суммарная длина работающих участков зуба протяжки по его периметру, мм; λ, λρ – коэффициенты теплопроводности обрабатываемого и инструментального материалов, Вт/(м К); сρ – удельная объемная теплоемкость обрабатываемого материала, Дж/(м3 К); а – коэффициент температуропроводности обрабатываемого материала, м2/с; τρ – сопротивление обрабатываемого материала пластическому сдвигу, МПа; а1 – толщина среза или подача на зуб протяжки (Sz), мм/зуб; K3 – коэффициент, учитывающий влияние СОЖ на увеличение Vо. Если СОЖ не используется, K3 = 1. Если применяется СОЖ на водной основе, K3 = 1,05; если СОЖ на масляной основе, K3 = 1,15; K4 – коэффициент, учитывающий влияние применяемого защитного покрытия на процесс протягивания. Если покрытие не используется, то K4 = 1, если оно используется, то K4 выбирается из табл. 9 в зависимости от номера группы обрабатываемости и характеристики покрытия; K5 – коэффициент, учитывающий влияние на процесс протягивания обрабатываемости данного материала резанием. Для материалов первой группы K5 = 0,5, для второй – K5 = 1, для третьей – K5 = 0,85, для четвертой – K5 = 0,3; m1 – коэффициент пропорциональности между τρ и σb.
Таблица 9
Выбор коэффициента K4
Покрытие |
1-я группа |
2-я группа |
3-я группа |
4-я группа |
TiC |
1,01…1,05 |
— |
— |
— |
TiN |
1,05…1,10 |
— |
1,01 |
— |
(Ti-Cr)N |
1,10 |
— |
1,05 |
1,01 |
TiC-Al2O3-TiN |
1,15 |
— |
1,10 |
1,10 |
(Nb-Zr)N |
1,15 |
1,10 |
1,10 |
1,10 |
TiC-Al2O3 |
1,10…1,15 |
1,00 |
1,05 |
1,05 |
105
Для упрощения записи формулы (30) и составления программы для ПЭВМ обозначим отдельные функциональные блоки выражения в виде следующих коэффициентов:
|
|
λρ 0,1 |
cρ To |
1,68 |
|
|
|
||||||||
K = |
|
|
|
|
|
|
|
|
|
, |
(31) |
||||
|
|
|
|
|
|||||||||||
|
|
λ |
|
|
τρ |
|
|
|
|
||||||
|
|
|
|
|
|
|
|
|
|
||||||
K |
= |
|
|
22 800 (sin α)0,1 |
|
, |
(32) |
||||||||
|
|
ρ |
0,5 |
|
|
|
|
|
|
|
|||||
1 |
|
|
(1− sin γ)0,3 |
|
|
|
|||||||||
|
|
|
|
1 |
|
|
|
|
|
||||||
|
|
|
a1 |
|
|
|
|
|
|
|
|
|
|
||
|
|
|
K2 |
= |
|
+ |
|
h −3 |
|
|
|
|
|||
|
|
|
1 |
|
з |
. |
|
|
|
(33) |
|||||
|
|
|
|
|
|
|
|
||||||||
|
|
|
|
|
|
|
|
|
lΣ |
|
|
|
|
Для фасонных протяжек l∑ = b n, где b – длина работающего участка элемента фасонного профиля на зубе протяжки, мм; n – число элементов фасонного профиля на зубе протяжки.
В результате подстановки этих коэффициентов общая расчетная формула оптимальной скорости резания выглядит следующим образом:
V = |
a |
K K K |
|
K |
|
K |
|
K |
. |
(34) |
|
2 |
3 |
4 |
|||||||
o |
1 |
|
|
5 |
|
|
||||
|
a1 |
|
|
|
|
|
|
|
|
Для вычисления величины оптимальных скоростей разработана программа для ПЭВМ, блок-схема алгоритма расчета которой представлена на рис. 33. На рис. 34 приведены графики изменения оптимальной скорости резания, рассчитанной на ПЭВМ для различных труднообрабатываемых материалов в зависимости от изменения подачи Sz. Наибольшая величина оптимальных скоростей резания наблюдается при протягивании титанового сплава ВТ3-1, а наименьшая – при протягивании жаропрочного литейного сплава ЖС6К. Сравнение расчетных и экспериментальных данных (табл. 10) показало их достаточно хорошую сходимость.
106
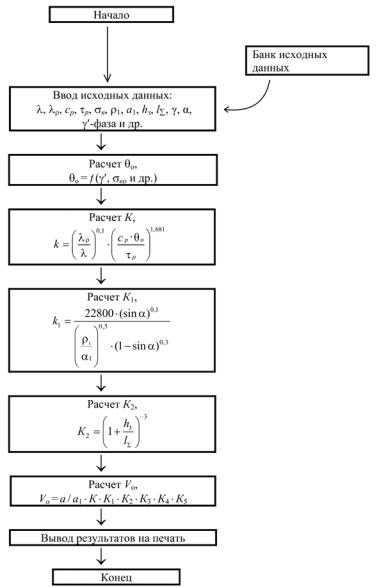
Рис. 33. Блок-схема алгоритма расчета оптимальной скорости резания Vo для протягивания различных сталей и сплавов
107
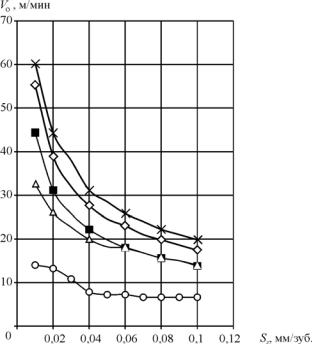
Рис. 34. Результаты расчета влияния подачи Sz на величину оптимальной скорости резания Vo для различных сталей и сплавов
ЭИ437БУ-ВД,
ЭИ787-ВД,
ЭИ736Ш,
ВТ3-1,
ЖС6К
В результате анализа математических расчетов оптимальных скоростей и температур резания для всех групп труднообрабатываемых материалов установлено, что уровни оптимальных скоростей протягивания лежат на один-два порядка выше уровня скоростей, рекомендуемых справочной литературой и применяемых на практике. Поэтому для практического подтверждения теоретических исследований необходимо провести глубокие и тщательные экспериментальные исследования процесса протягивания труднообрабатываемых материалов как в лабораторных условиях (на образцах), так и в производственных (на конкретных обрабатываемых деталях).
108
Таблица 1 0
Сравнение расчетных и экспериментальных значений оптимальной скорости резания Vо для различных сталей и сплавов протяжками ВК8
Подача, |
Значения Vо, м/с, расчетное/экспериментальное |
||||
мм/зуб, |
ЭИ787-ВД |
ЭИ736Ш |
ВТ3-1 |
ЭИ437БУ-ВД |
ЖС6К |
Sz |
|
|
|
|
|
0,010 |
0,74/0,56 |
0,56/0,42 |
1,05/1,05 |
0,92/0,84 |
0,24/0,14 |
0,015 |
0,60/0,49 |
0,50/0,35 |
0,86/0,86 |
0,75/0,74 |
0,23/0,12 |
0,020 |
0,52/0,45 |
0,45/0,31 |
0,74/0,75 |
0,65/0,67 |
0,22/0,11 |
0,025 |
0,47/0,42 |
0,42/0,28 |
0,66/0,68 |
0,58/0,63 |
0,20/0,11 |
0,030 |
0,43/0,40 |
0,40/0,25 |
0,60/0,62 |
0,53/0,64 |
0,18/0,10 |
0,040 |
0,37/0,36 |
0,35/0,22 |
0,52/0,54 |
0,46/0,55 |
0,13/0,09 |
0,045 |
0,35/0,35 |
0,34/0,21 |
0,49/0,52 |
0,44/0,52 |
0,13/0,09 |
0,050 |
0,33/0,34 |
0,32/0,20 |
0,47/0,47 |
0,41/0,51 |
0,12/0,09 |
0,055 |
0,32/0,33 |
0,31/0,19 |
0,45/0,47 |
0,39/0,50 |
0,12/0,08 |
0,060 |
0,30/0,32 |
0,30/0,18 |
0,43/0,45 |
0,38/0,47 |
0,12/0,08 |
0,065 |
0,29/0,31 |
0,29/0,18 |
0,41/0,43 |
0,36/0,46 |
0,12/0,08 |
0,070 |
0,28/0,31 |
0,28/0,17 |
0,40/0,42 |
0,35/0,46 |
0,11/0,08 |
0,075 |
0,27/0,30 |
0,27/0,16 |
0,38/0,40 |
0,34/0,45 |
0,11/0,08 |
0,080 |
0,26/0,29 |
0,26/0,16 |
0,37/0,39 |
0,33/0,43 |
0,11/0,07 |
0,085 |
0,25/0,29 |
0,26/0,15 |
0,36/0,38 |
0,32/0,42 |
0,11/0,07 |
0,090 |
0,25/0,28 |
0,25/0,15 |
0,35/0,37 |
0,31/0,42 |
0,11/0,07 |
0,095 |
0,24/0,28 |
0,25/0,15 |
0,34/0,36 |
0,30/0,41 |
0,11/0,07 |
0,100 |
0,23/0,27 |
0,24/0,14 |
0,33/0,35 |
0,29/0,40 |
0,11/0,07 |
3.3. Экспериментальное определение оптимальных режимов резания при протягивании труднообрабатываемых сталей и сплавов
Оптимизация процессов обработки на металлорежущих станках при экспериментальных исследованиях может быть осуществлена только на основе глубокого и тщательного изучения физической сущности явлений, сопровождающих процесс резания и основных закономерностей износа инструмента, как главного фактора, влияющего на точность, производительность и качество обработки.
109
Известно, что одной из важнейших характеристик процесса резания является температура резания (средняя температура контакта), которая оказывает решающее влияние на весь комплекс явлений, сопутствующих процессу резания и на физико-химические свойства поверхностного слоя деталей. В свою очередь наибольшее влияние на интенсивность износа и температуру резания оказывает скорость резания, которая определяет также и производительность процесса резания. Зависимость между скоростью резания V при протягивании различных материалов, стойкостью Тмин и толщиной среза а принято выражать формулой степенного вида:
V = |
|
C |
, м/мин. |
(35) |
|
T m |
|
ay |
|||
|
|
|
|
||
|
мин |
|
|
|
Исследования, проведенные в последнее время, показывают, что такие формулы справедливы лишь для узкого диапазона скоростей резания. При изменении скорости резания в широком диапазоне эта зависимость имеет сложный экстремальный характер. В связи с этим проведено исследование изменения интенсивности износа зубьев протяжек и температуры резания при протягивании жаропрочных сталей и сплавов в широком диапазоне скоростей резания (от 1,5 до 60,0 м/мин) и подач (от 0,01 до 0,15 мм/зуб).
На рис. 35 приведены графики износа протяжек при протягивании жаропрочного сплава ЭИ787-ВД на различных скоростях резания, типичные для протягивания различных типов сталей и сплавов. Особенностью этих графиков является отсутствие периода приработки, т.к. по задней и передней граням заранее образованы фаски 0,08…0,10 мм. Такая геометрия зубьев позволяет устранить влияние качества заточки передней и задней граней зубьев на величину приработочного износа зубьев и начать стойкостные испытания любой протяжки при одинаковых условиях. Кроме того, образование фасок по передней и задней граням путем доводки устраняет дефекты на режущей кромке, образующиеся при заточке, и снижает вероятность появления выкрашивания режущей кромки в период приработки.
110