
1270
.pdfков лопаток. В то же время в процессе маятникового шлифования на зубьях «елочного» профиля замка периодически появляются шлифовочные трещины, приводящие к браку деталей.
Одним из новых высокоэффективных процессов финишной обработки деталей машин является процесс глубинного шлифования. Под руководством С.С. Силина (г. Рыбинск) проведены сравнительные исследования процессов фрезерования и глубинного шлифования «елочных» замков турбинных лопаток. Доказано существенное преимущество глубинного шлифования перед фрезерованием по производительности (в 4 раза выше), точности и стабильности обеспечения геометрических параметров профиля.
Сравнительные исследования процессов глубинного шлифования и протягивания замков лопаток компрессора из титанового сплава ВТ3-1 провел Ю.К. Чарковский (ОАО «Рыбинские моторы»). Глубинное шлифование кругами 5ЧС 25Н М2 12 К10 с подачей детали 100 мм/мин и глубиной 1,5 мм относится по производительности к уровню глубинного шлифования сплава ЖС6К, однако уступает протягиванию. В процессе протягивания и глубинного шлифования образуются сжимающие напряжения до 80 МПа, причем разброс величин максимальных напряжений после протягивания больше, чем после глубинного шлифования. Анализ результатов исследования усталостной прочности показал, что предел усталостной прочности замков лопаток после протягивания на 8…10 % выше, чем после глубинного шлифования.
Таким образом, сравнительный анализ технической литературы и опыта моторостроительных предприятий по вопросу применяемых техпроцессов изготовления замковых соединений показал, что процесс протягивания по производительности намного опережает такие процессы, как глубинное шлифование, фрезерование и маятниковое шлифование при обеспечении требуемых параметров качества и точности обработки.
Сравнение процессов протягивания и глубинного шлифования жаропрочных сплавов на никелевой основе до сих пор не проводилось.
31
1.4. Режимы резания и режущие инструменты, применяемые при протягивании труднообрабатываемых материалов
Диски и лопатки турбины и компрессора относятся к числу наиболее нагруженных деталей, определяющих надежность и ресурс современных авиационных двигателей. Низкая стойкость режущих инструментов вносит значительную нестабильность в свойства поверхностного слоя даже в пределах небольшой партии обработанных деталей. Высокая трудоемкость процесса протягивания из-за низких скоростей резания и сложной настройки многосекционных протяжек снижает эффективность производства. Поэтому исследования проблемы оптимизации процессов протягивания, обеспечивающих более высокую и стабильную производительность, стойкость протяжек и наилучшие физико-химические свойства поверхностных слоев обработанных деталей, являются весьма актуальными задачами современного машиностроения.
Анализ литературных данных показывает, что этому вопросу уделяется недостаточное внимание. Как правило, исследования носят отрывочный несистемный характер и касаются либо анализа износоустойчивости инструментов, либо определения свойств обработанного поверхностного слоя отдельных представителей обрабатываемых материалов, либо совершенствования конструкций протяжек и протяжных станков. Недостаточно изученными являются также вопросы влияния режимов резания на силы резания и характер вызываемых ими технологических напряжений в обрабатываемых деталях. Применяемые методы и разработанные методики весьма трудоемки. Отсутствие соответствующего протяжного оборудования и применение различных методик исследований зачастую приводят к противоречивым результатам, что можно видеть в табл. 1. Некоторые исследователи рекомендуют применять при протягивании низкие скорости резания (до 3 м/мин) при использовании как быстрорежущих, так
итвердосплавных протяжек.
Вто же время Н.И. Жигалко, Н.И. Ковзель, Н.Ф. Пронкин, В.И. Белашков, А.Е. Вишняков, В.Ф. Скиженок, П.Г. Кацев и другие
32
рекомендуют для труднообрабатываемых материалов повышенные до 30…50 м/мин скорости протягивания как быстрорежущими, так и твердосплавными протяжками. Подача на зубьях протяжек рекомендуется от 0,1 мм на режущих зубьях до 0,010…0,005 мм на чистовых зубьях. Передний угол большинством авторов рекомендуется в пределах 12°…15°. Некоторые исследователи не применяют отрицательные фаски на зубьях, а другие рекомендуют их. Задний угол одни авторы рекомендуют выбирать в пределах 1,5°…3,0°, другие – в диапазоне 5°…10°.
По данным исследователей (табл. 1), выполнение их рекомендаций позволяет обеспечить стойкость протяжек по длине пути резания 1,5…5,0 метров (быстрорежущие протяжки) и 8…10 метров (твердосплавные протяжки).
При обработке жаропрочных литейных сплавов типа ЖС6К протягиванием рекомендуются весьма низкие скорости резания – 1,5 м/мин для быстрорежущих протяжек и 2…10 м/мин для твердосплавных протяжек.
Общий анализ работ, представленных в табл. 1, показал, что большинство работ выполнено в лабораторных условиях, на образцах обрабатываемых материалов, на станках-стендах и носит рекомендательный характер, не учитывающий конкретные производственные и технические условия, размеры и конфигурацию обрабатываемых деталей, мощность и жесткость применяемого оборудования и т.д.
С целью установления фактически применяемых режимов протягивания и глубинного шлифования проведено обследование операций обработки «елочных» замков лопаток и пазов в дисках турбин на ведущих моторостроительных заводах России и Украины. Результаты обследования, приведенные в табл. 2, показали, что протягивание пазов в дисках турбин ведется на низких скоростях резания
0,033…0,660 м/с (2…4 м/мин) с подачами 0,005…0,100 мм/зуб про-
тяжками из быстрорежущих сталей типа Р18, Р12Ф2К5М3. Передний угол у большинства протяжек – 12°…15°, а задний угол – 2°…3°. Твердосплавные протяжки практически не применяются.
33
34
|
Рекомендации различных исследователей по обработке |
Таблица 1 |
||||
|
|
|||||
|
труднообрабатываемых материалов протягиванием |
|
||||
|
|
|
|
|
|
|
|
Обрабаты- |
Вид |
Режимы |
Параметры |
|
|
Источники |
ваемый |
Примечания |
||||
обработки |
резания |
инструментов |
||||
|
материал |
|
|
|
|
|
Работы |
|
Протягива- |
V = 1,5…4 м/мин |
Р18, γ= 15°; αр* = 3°…5°; |
– |
|
М.Ф. Идзона, |
ЖС6К |
ние замков |
||||
ВИНИТИ |
|
типа «елка» |
|
αк* = 1°30'…2° |
|
|
|
|
|
|
|||
Работы |
|
Протягива- |
Vпред* = 3 м/мин |
Р18, |
Ra ≤ 1,25 мкм, |
|
В.В. Чернышева, |
|
Sz = 0,030…0,005 мм/зуб; |
||||
ЭИ929 |
ние замков |
упрочнение |
||||
М.С. Рахмаровой, |
|
типа «елка» |
Vоконч* = 1,5 м/мин |
ВК8 – чистовая; |
роликом |
|
НИАТ |
|
|
|
γ = 10°; α = 3° |
|
|
Работы |
ЭИ481 |
Протягива- |
V = 2 м/мин |
Р18, |
Ra ≤ 1,25 мкм, |
|
ЭИ617 |
Sz = 0,01…0,02 мм/зуб; |
|||||
П.Г. Балюра |
ЭИ437Б |
ние пазов |
|
γ = 10°; α = 3° |
L = 1,7–5 м |
|
|
|
|
|
|
|
|
Работы |
ВТ3-1 |
Протягива- |
Vо = 18 м/мин |
Р18, Sz = 0,07 мм/зуб; |
– |
|
В.И. Белашкова |
ВТ8 |
ние замков |
γо* = 0°; αо* = 4° |
|||
и пазов |
|
|
||||
|
|
|
|
|
||
|
|
|
|
|
|
|
Работы |
ВТ8 |
Протягива- |
Vпред = 15…20 м/мин |
Р18, |
|
|
А.Е. Вишнякова |
ВТ9 |
ние замков |
Vоконч = 30 м/мин |
Sz = 0,01…0,2 мм/зуб; |
– |
|
|
ВТ4 |
и пазов |
|
αо > 1°30' |
|
|
34 |
|
|
|
|
|
|
Работы |
Нержа- |
|
Vпред = 5…10 м/мин |
|
|
|
веющие |
|
γ = 15°; α = 1°…2° |
– |
||
|
Г.И. Грановского |
|
Vоконч = 1 м/мин |
|||
|
стали |
|
|
|
||
|
Работы |
|
|
|
Р18Ф2К8М, |
|
|
20Х13 |
Протягива- |
V = 30 м/мин |
Sz = 0,05 мм/зуб; γ = 10°; |
|
|
|
В.Ф. Скиженка |
– |
||||
|
15Х11МФ |
ние замков |
V = 35 м/мин |
α = 3°; ВК8, выкрашива- |
||
|
В.Д. Лемешонка |
|
|
|
ниеSz = 0,04…0,06 мм/зуб |
|
|
|
|
|
|
|
|
|
|
|
|
VР18 = 18…30 м/мин |
ВК6М, ВК8; |
|
|
Работы |
ВТ8 |
Протягива- |
Sz = 0,04…0,06 мм/зуб; |
– |
|
|
|
ние наруж- |
VВК = 18…30 м/мин |
γ = 5°…10°; α = 4°…6° |
|
|
|
П.Г. Кацева |
|
|
|
||
|
ЖС6К |
ное |
VВК = 7…10 м/мин |
ВК15, ВК8; γ = 5°; |
– |
|
|
|
|||||
|
|
|
α = 7°…10° |
|||
|
|
|
|
|
|
|
|
|
ЭИ617 |
Протягива- |
Vпред = 3 м/мин |
Р18, |
|
|
Работы |
ЭИ481 |
ние наруж- |
Sz = 0,005…0,030 мм/зуб; |
Ra = 0,32…0,63 мкм |
|
|
Н.Ф. Пронкин |
ЭИ437 |
ное |
Vоконч = 1,5 м/мин |
ВК8, γ = 10°…15°; |
|
|
|
ЖС6К |
|
α = 1,5°…3,0° |
|
|
|
|
|
|
|
||
|
|
|
Протягива- |
VР18 = 10…15 м/мин |
Р18, Р9М4К8 γ = 10°; |
|
|
Работы |
ЭИ415 |
ние наруж- |
VР9М4К8 = 28…32 м/мин |
α= 4°…6°; Т14К8 γ= 10°; |
– |
|
|
ное |
VТ14К8 = 35…45 м/мин |
α = 3°…4°; fз = 0,1; |
|
|
|
Н.И. Жигалко |
|
Sz = 0,05 мм/зуб |
fп = 0,2 мм; γф = –10° |
|
|
|
|
|
|
|||
|
Н.И. Ковзелья |
|
Протягива- |
VР6М5 = 25…35 м/мин |
γ = 10°; α = 4°…6°; |
|
|
и др. |
2Х13 |
γ = 10°; α = 3°…4°; |
|
||
|
|
(ЭЖ2) |
ние наруж- |
VТ14К8 = 30…50 м/мин |
fп = 0,2 мм; fз = 0,1; |
– |
|
|
|
ное |
Sz = 0,05 мм/зуб |
γф = –10° |
|
35 |
|
|
|
|
|
|
|
|
|
|
|
35 |
|
|
|
|
|
|
|
36
Окончание табл. 1
Источники |
Обрабаты- |
Вид |
Режимы |
Параметры |
Примечания |
|
ваемый |
||||||
обработки |
резания |
инструментов |
||||
|
материал |
|
|
|
|
|
|
ЭИ752 |
Протягива- |
VР9М4К8 = 12…20 м/мин |
γ = 10°; α = 4°…6°; |
|
|
|
(3Х19Н9М |
ние наруж- |
VТ14К8 = 25…40 м/мин |
γ = 10°; α = 5°; |
– |
|
|
fп = 0,2 мм; fз = 0,1; |
|||||
|
ВБТ) |
ное |
Sz = 0,05 мм/зуб |
γф = –5° |
|
|
|
|
|
|
|
||
|
ВТ8 |
Протягива- |
VВК6М = 25…40 м/мин |
γ = 10°; α = 3°…4°; |
tшт = 0,7 мин |
|
|
ние наруж- |
Sz = 0,05 мм/зуб |
fп = 0,2 мм; fз = 0,1; |
tшт = 0,32 мин |
||
|
|
ное |
γф = 5° |
(твердый сплав) |
||
|
|
|
||||
|
|
Протягива- |
VВК8 = 2…10 м/мин |
γ = 5°; α = 70°; |
tшт = 2 мин |
|
|
ЖСК6 |
ние наруж- |
VР9М4К8 = 1,5 м/мин |
fп = 0,2 мм; fз = 0,1; |
tшт = 0,7 мин |
|
|
|
ное |
|
γф = 5° |
(твердый сплав) |
|
НИИТ Авто- |
IV группа |
Протягива- |
|
|
|
|
пром: Режимы |
Vпред = 8…10 м/мин |
|
|
|||
обрабаты- |
Sz = 0,005…0,1 мм/зуб |
– |
||||
резания метал- |
ваемости. |
ние наруж- |
Vоконч = 2…4 м/мин |
|||
лов, 4 изд. Спра- |
НВ 277–321 |
ное |
|
|
|
|
вочник, 1995 г. |
|
|
|
|
||
|
|
|
|
|
||
|
|
|
|
|
|
* Vпред – предварительная скорость протягивания; Vоконч – окончательная скорость протягивания; αр – задний угол режущего зуба; αк – задний угол калибрующего зуба; γо – передний угол оптимальный; αо – задний угол оптимальный.
36
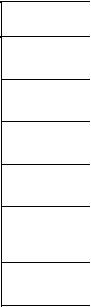
Таблица 2
Фактические режимы обработки пазов в дисках турбин на моторостроительных предприятиях
Предприятие |
Обрабатываемый |
Вид |
Инструментальные |
Режимы |
γ, град. |
α, град. |
Примечание |
|
|
материал |
обработки |
материалы |
резания |
|
|
|
|
ММПО |
|
|
|
|
|
|
|
|
ЭП742-ИД, |
Протягивание |
Р12Ф2К5М3 |
Vp = 3 м/мин, |
|
|
Стойкость |
||
им. Чернышева |
ЭП741-ИД |
пазов |
HRC 65…67 |
Sz = 0,025…0,05 |
10 |
3 |
||
1…2 м |
||||||||
(г. Москва) |
диски турбин |
блоками |
Р18 |
мм/зуб |
|
|
||
|
|
|
||||||
МППО «Салют» |
ЭП742-ИД |
Протягивание |
|
V = 1,6…1,8 м/мин, |
|
|
Стойкость |
|
пазов |
Р18, Р12Ф2М3 |
Sz = 0,02…0,05 |
15 |
1,5…5,0 |
||||
(г. Москва) |
диски турбин |
1,5…2,0 м |
||||||
АО «Мотор |
|
блоками |
|
мм/зуб |
|
|
|
|
ЭП742 |
Протягивание |
Р18 хвостовые |
V = 1,0…1,5 м/мин, |
|
|
Стойкость |
||
Сич» (Украина, |
диски турбин |
Sz = 0,02…0,10 |
15 |
2…4 |
1,5…2,0 м |
|||
г. Запорожье) |
HB302–398 |
пазов |
протяжки 11 шт. |
мм/зуб |
|
|
(1 диск ) |
|
|
|
|
|
|||||
АО «ОМПО» |
ЭП742-ИД |
Протягивание |
|
V = 1,8…2 м/мин, |
|
|
Стойкость |
|
Р18 |
Sz=0,02…0,065 |
12…15 |
2…3 |
|||||
(г. Омск) |
диски турбин |
пазов |
|
мм/зуб |
|
|
1,5…3,0 м |
|
|
|
|
|
|
|
|
||
АО «Металли- |
ЭП428, |
|
|
V = 2…4 м/мин, |
|
|
Станок |
|
|
|
|
|
2МП-301, |
||||
ческий завод» |
15Х11МФ-Ш |
Протягивание |
Р18, Р6М5 |
Sz = 0,02…0,20 |
15 |
3 |
||
стойкость |
||||||||
(г. С.-Петербург) |
диски турбин |
пазов |
|
мм/зуб |
|
|
||
|
|
|
2…3 м |
|||||
|
|
|
|
|
|
|
||
НПО «Сатурн» |
ВЖ122 |
Протягивание |
Р12Ф2К5М3, |
V = 1,2…4,5 м/мин, |
|
|
Стойкость |
|
пазов, 3-зубая |
HRC = 68…69, |
Sz = 0,01…0,04 |
3…1,5 |
2…3 |
98 пазов |
|||
(г. Москва) |
диски турбин |
|||||||
|
|
«елка» |
3 блока |
мм/зуб |
|
|
(1 диск) |
37
37
При этом установлена весьма низкая стойкость протяжек от 1 до 3 м протянутой поверхности. Причиной низкой стойкости протяжек является обычно быстрый износ зубьев и связанное с этим ухудшение геометрических параметров, увеличение высоты микронеровностей, появление рисок и надиров на протянутой поверхности. Практически обработать протягиванием более одного диска из сплавов ЭП741-НП, ЭП742-ИД, ВЖ122 при указанных режимах невозможно. Вместе с тем отмечается, что другие методы механической обработки «елочных» пазов в дисках турбин, кроме протягивания, не применяются, несмотря на значительную сложность и высокую трудоемкость изготовления «елочных» профильных протяжек. Изготовлением протяжек занимаются инструментальные цеха моторостроительных предприятий. Технология изготовления протяжек на большинстве предприятий одинакова.
Протягивание пазов в дисках турбин производится преимущественно на горизонтально-протяжных станках типа 7А540 и СПС40, имеющих диапазон рабочих скоростей от 1 до 6 м/мин. Таким образом, скоростное протягивание пазов в дисках турбин не применяется.
Вопросы обеспечения качества и усталостной прочности замковых соединений неразрывно связаны с вопросами повышения эффективности самих операций механообработки, обеспечения более высокой стойкости режущих инструментов и, следовательно, более стабильной обработки. С появлением новых газотурбинных двигателей, имеющих более высокие эксплуатационные параметры, задачи механообработки еще более осложняются из-за повышения требований к точности, качеству изготовления, усложнения конструкций деталей, появления еще более труднообрабатываемых материалов.
Задачи повышения производительности, качества обработки, повышения стойкости режущих инструментов при механической обработке резанием решались многими учеными в нашей стране и за рубежом путем замены быстрорежущих лезвийных инструментов на твердосплавные и перехода на более высокий диапазон скоростей резания. Наиболее многочисленные исследования проведены для таких процессов, как точение и фрезерование.
38
Втабл. 3 приведены рекомендации ведущих ученых по обработке точением и фрезерованием деталей из различных жаропрочных сталей
исплавов. Анализ этой таблицы показывает, что при точении и фрезеровании уровень применяемых скоростей резания находится в диапазоне 15…50 м/мин, т.е. на целый порядок выше скоростей резания, применяемых при протягивании аналогичных материалов. В качестве инструментальных материалов для резцов и фрез рекомендуются преимущественно твердые сплавы вольфрамокобальтовой группы ВК6М, ВК8, ВК10-ОМ и др. Можно отметить, что различным маркам инструментальных и обрабатываемых материалов соответствуют и различные по величине оптимальные скорости резания.
Сформулированное в 1961 г. А.Д. Макаровым положение (закон) о постоянстве оптимальной температуры резания для конкретной пары инструментального и обрабатываемого материала позволило с научных позиций назначать оптимальные скорости резания. Это положение неоднократно было подтверждено различными исследователями при продольном и торцевом точении, растачивании, сверлении, нарезании резьбы, фрезеровании цилиндрическими, торцевыми и концевыми фрезами, зубофрезеровании.
Вто же время имеются весьма ограниченные сведения о теплофизической природе взаимодействия инструментальных и обрабаты-
ваемых материалов при протягивании. Особенно мало сведений по протягиванию жаропрочных сплавов на никелевой основе. Это объясняется весьма высокой трудоемкостью проведения стойкостных опытов, отсутствием протяжных станков с широким диапазонам рабочих скоростей, необходимых для оптимизации, отсутствием достаточного опыта по изготовлению и эксплуатации дорогостоящих твердосплавных протяжек. Только решив все эти задачи вместе, комплексно, можно переходить к вопросам оптимизации процессов протягивания жаропрочных сплавов.
39

40
Таблица 3
Рекомендации по обработке жаропрочных сталей и сплавов точением и фрезерованием (чистовая обработка)
Источники |
Вид |
Обрабатываемые |
Инструментальные |
Скорость |
Подача, |
Глубина |
γ,○ |
α,○ |
|
обработки |
материалы |
материалы |
резания, |
мм/об; |
резания, |
град. |
град. |
||
|
м/мин |
мм/зуб |
мм |
||||||
|
|
|
|
|
|
|
|
|
|
|
|
ЭИ961 |
|
104…85 |
|
|
16…5 |
8 |
|
|
Точение |
ХН177ТЮР |
ВК6М ВК6ОМ |
|
|
||||
Работы |
58…21 |
0,02…0,06 |
0,2 |
0…5 |
15…10 |
||||
Я.Л. Гуревича |
|
ЖС6К |
ВК3М |
138…78 |
|
|
5 |
15 |
|
|
ВТ3-1 |
|
|
|
|||||
и др. |
|
|
|
|
|
|
|
||
|
|
|
|
|
|
|
|
||
Торцевое |
ХН35ВТЮ |
ВК6М |
32…49 |
0,03…0,10 |
3,0 |
5…8 |
15 |
||
|
|||||||||
|
фрезерование |
ВТ3-1 |
66…54 |
–5 |
|||||
|
|
|
|
|
|
|
|
|
|
|
|
14Х17Н2 |
Т15К6 |
|
|
|
|
|
|
|
|
ХН51ВМТЮ |
180 |
0,09 |
0,5 |
|
|
||
|
Точение |
ВК6М |
10 |
10 |
|||||
Работы |
КФР |
35…30 |
0,084 |
1,0 |
|||||
|
ВК6М |
|
|
||||||
А.Д. Макарова |
|
ХН77ТЮР |
|
|
|
|
|
||
|
|
|
|
|
|
|
|||
и др. |
Торцевое |
ХН51ВМТЮ |
ВК8 |
30 |
0,084 |
|
5 |
|
|
|
КФР |
|
|
0,5 |
10 |
||||
|
фрезерование |
|
|
0,05 |
–8 |
||||
|
ЖС6К |
ВК8 |
21,5 |
|
|
||||
|
|
|
|
|
|
||||
|
|
|
|
|
|
|
|
|
|
Работы |
Получистовое |
|
|
|
|
|
|
|
|
Н.Г. Петрухи |
ХН77ТЮР |
ВК8 |
27 |
0,15 |
1,5 |
10 |
15 |
||
и др. |
точение |
|
|
|
|
|
|
|
|
|
|
|
|
|
|
|
|
||
|
|
|
|
|
|
|
|
|
Стойкость, мин
30
60
18 000 hз = 0,25 мм
1 000
hз = 0,15 мм
–
60
40