
- •ПРОГРАММА ВСЕРОССИЙСКОЙ НАУЧНО-ТЕХНИЧЕСКОЙ КОНФЕРЕНЦИИ «АЭРОКОСМИЧЕСКАЯ ТЕХНИКА И ВЫСОКИЕ ТЕХНОЛОГИИ - 2003»
- •ОБЗОР ОПЕРАТИВНЫХ МЕТОДОВ НЕРАЗРУШАЮЩЕГО КОНТРОЛЯ МАШИН И КОНСТРУКЦИЙ
- •ОЦЕНКА ВЛИЯНИЯ ВОДОЕМА-НАКОПИТЕЛЯ СТОЧНЫХ ВОД ПОРОХОВОГО ПРЕДПРИЯТИЯ НА ГИДРОХИМИЧЕСКИЙ РЕЖИМ РЕКИ
- •АЭРОКОСМИЧЕСКАЯ ТЕХНИКА И ВЫСОКИЕ ТЕХНОЛОГИИ - 2003
- •НЕКОТОРЫЕ ПУТИ УЛУЧШЕНИЯ РОЗЖИГА КАМЕРЫ СГОРАНИЯ ДВИГАТЕЛЯ ПС-90А
- •ЗАКОНОМЕРНОСТИ ПРОЦЕССА РОЗЖИГА ДВИГАТЕЛЯ ПС-90А, ВЫЯВЛЕННЫЕ С ПОМОЩЬЮ БОРТОВОЙ СИСТЕМЫ КОНТРОЛЯ.
- •ИССЛЕДОВАНИЕ ПРОЧНОСТИ ПЛАСТИКА, АРМИРОВАННОГО ПОЛИЭТИЛЕНОВЫМИ ВОЛОКНАМИ, ПРИ КОМБИНИРОВАННОМ НАГРУЖЕНИИ
- •РАСЧЕТ ТЕРМОНАПРЯЖЕННОГО СОСТОЯНИЯ СОПЛОВОГО НАСАДКА ЖРД ИЗ УГЛЕРОД-УГЛЕРОДНОГО КОМПОЗИЦИОННОГО МАТЕРИАЛА
- •ТЕХНОЛОГИЯ СОЭКСТРУЗИОННОГО ПРОИЗВОДСТВА ГЕРМЕТИЗИРУЮЩЕЙ ОБОЛОЧКИ БИПЛАСТМАССОВЫХ ТРУБ
- •АНАЛИЗ РАБОТОСПОСОБНОСТИ БИПЛАСТМАССОВЫХ ТРУБ ПРИ НИЗКИХ ТЕМПЕРАТУРАХ
- •ПОЛУЧЕНИЕ ИНТЕРМЕТАЛЛИДОВ ТИТАНА Ti3Al МЕТОДОМ МЕХАНИЧЕСКОГО ЛЕГИРОВАНИЯ
- •ЭКСПЕРИМЕНТАЛЬНАЯ ОЦЕНКА ВЛИЯНИЯ ВОДНОСТРУЙНОЙ ОБРАБОТКИ НА УСТАЛОСТНУЮ ПРОЧНОСТЬ ОБРАЗЦОВ ПОЛИМЕТИЛМЕТААКРИЛАТА
- •АЭРОКОСМИЧЕСКАЯ ТЕХНИКА И ВЫСОКИЕ ТЕХНОЛОГИИ - 2003
- •МОДЕЛЬ РАСЧЕТА ДВУХФАЗНОЙ ГАЗОКАПЕЛЬНОЙ СТРУИ В КАМЕРЕ СГОРАНИЯ ЖРД
- •МОДИФИКАЦИЯ СВЯЗУЮЩЕГО НА ОСНОВЕ ДИАНОВОЙ СМОЛЫ ЭД-20 ДЛЯ ПОВЫШЕНИЯ ТЕПЛО- И ХИМИЧЕСКОЙ СТОЙКОСТИ СТЕКЛОПЛАСТИКОВЫХ ИЗДЕЛИЙ
- •ВЛИЯНИЕ РАБОТЫ СЕПАРИРУЮЩЕГО АППАРАТА НА КОМПОНЕНТНЫЙ СОСТАВ ТОПЛИВНОЙ МАССЫ, ПОЛУЧАЕМОЙ В СМЕСИТЕЛЯХ НЕПРЕРЫВНОГО ДЕЙСТВИЯ
- •ТЕХНОЛОГИЧЕСКИЕ РЕШЕНИЯ УГЛЕПЛАСТИКОВЫХ РЕШЕТЧАТЫХ СТЕРЖНЕВЫХ ЭЛЕМЕНТОВ ФЕРМЕННЫХ КОНСТРУКЦИЙ
- •ГОЛОГРАФИЧЕСКИЙ ИНТЕРФЕРОМЕТР С АВТОНОМНЫМ ОТРАЖАТЕЛЕМ В ОПОРНОМ ПУЧКЕ
- •ОПЫТ ПРИМЕНЕНИЯ ТЕРМОИНДИКАТОРНЫХ КРАСОК ПРИ ДОВОДКЕ МАЛОЭМИССИОННЫХ КАМЕР СГОРАНИЯ (МЭКС)
- •АЭРОКОСМИЧЕСКАЯ ТЕХНИКА И ВЫСОКИЕ ТЕХНОЛОГИИ - 2003
- •УСТОЙЧИВОСТЬ РАСТВОРОВ ГИПОХЛОРИТА НАТРИЯ ПРИ ХРАНЕНИИ.
- •ИССЛЕДОВАНИЕ МЕХАНИЗМА ВЗАИМОДЕЙСТВИЯ НИЗКОМОЛЕКУЛЯРНЫХ ОРГАНИЧЕСКИХ СОЕДИНЕНИЙ С АЗИДОПЕНТОНОМ
- •ВЫСОКОЭФФЕКТИВНЫЕ ДВУХОСНОВНЫЕ БЕЗОПАСНЫЕ СОСТАВЫ ДЛЯ СТВОЛЬНЫХ СИСТЕМ
- •МОДЕЛИРОВАНИЕ ФОТОУПРУГИХ ЭФФЕКТОВ В КОНТУРЕ ВОЛОКОННО-ОПТИЧЕСКОГО ГИРОСКОПА
- •АЭРОКОСМИЧЕСКАЯ ТЕХНИКА И ВЫСОКИЕ ТЕХНОЛОГИИ - 2003
- •О ПРИМЕНЕНИИ АМОРТИЗАЦИрННЫХ УСТРОЙСТВ В РСЗО
- •ОЦЕНКА НАПРЯЖЁННО-ДЕФОРМИРОВАННОГО СОСТОЯНИЯ ИЗДЕЛИЙ ПРИ НАЛИЧИИ ПОДВИЖНОЙ ЗОНЫ КОНТАКТА
- •НОВЫЙ МЕТОД ОЦЕНКИ КОЭФФИЦИЕНТА ДИФФУЗИИ ПЕНЕТРАНТА В ПОЛИМЕРНЫХ МАТЕРИАЛАХ1
- •ОБ ОДНОМ ПОДХОДЕ ФОРМИРОВАНИЯ СЕТОК ЭЛЕМЕНТОВ ДЛЯ ЧИСЛЕННЫХ ИССЛЕДОВАНИЙ
- •АЭРОКОСМИЧЕСКАЯ ТЕХНИКА И ВЫСОКИЕ ТЕХНОЛОГИИ - 2003
- •ИССЛЕДОВАНИЕ ПРОЦЕССА МЕХАНОДЕСТРУКЦИИ В СШИТЫХ ПОЛИМЕРАХ
- •АЭРОКОСМИЧЕСКАЯ ТЕХНИКА И ВЫСОКИЕ ТЕХНОЛОГИИ - 2003
- •НАПРЯЖЕНИЯ В МЕТАЛЛЕ И АКУСТИЧЕСКИЕ МЕТОДЫ
- •МАГНИТООПТИЧЕСКИЕ СВОЙСТВА АМОРФНОЙ СТАЛИ
- •МОДЕЛИРОВАНИЕ И ОПТИМИЗАЦИЯ РЕСУРСНЫХ ИСПЫТАНИЙ ИЗДЕЛИЙ АВИАЦИОННОЙ ТЕХНИКИ В СИСТЕМЕ ИХ ЖИЗНЕННОГО ЦИКЛА
- •К ТЕОРИИ ДЕФОРМАЦИ ХАОТИЧЕСКИ АРМИРОВАННЫХ КОМПОЗИЦИОННЫХ МАТЕРИАЛОВ
- •ЗАКОНОМЕРНОСТИ ПОВРЕЖДЕНИЯ волокнистых композиционных МАТЕРИАЛОВ НА СТАДИИ РАЗУПРОЧНЕНИЯ ПРИ ОДНООСНОМ РАСТЯЖЕНИИ
- •СТАТИСТИЧЕСКАЯ ТЕОРИЯ ПЛОТНОСТИ ХАОТИЧЕСКОЙ УПАКОВКИ ЧАСТИЦ ДИСПЕРСНОГО НАПОЛНИТЕЛЯ
- •АЭРОКОСМИЧЕСКАЯ ТЕХНИКА И ВЫСОКИЕ ТЕХНОЛОГИИ - 2003
- •ПРИНЦИПЫ ТЕРМИНАЛЬНОГО НАВЕДЕНИЯ АЭРОБАЛДИСТИЧЕСКОГО ЛЕТАТЕЛЬНОГО АППАРАТА В ГОРИЗОНТАЛЬНОЙ ПЛОСКОСТИ
- •ТЕРМИНАЛЬНОЕ НАВЕДЕНИЕ АЭРОБАЛЛИСТИЧЕСКОГО ЛЕТАТЕЛЬНОГО АППАРАТА В ВЕРТИКАЛЬНОЙ ПЛОСКОСТИ
- •ККкТ0
- •СТАБИЛИЗАЦИЯ УГЛОВОГО ДВИЖЕНИЯ ЛЕТАТЕЛЬНОГО АППАРАТА КАК ЖЕСТКОГО ТВЕРДОГО ТЕЛА
- •МЕТОДЫ СТАБИЛИЗАЦИИ УПРУГИХ КОЛЕБАНИЙ КОРПУСА ЛЕТАТЕЛЬНОГО АППАРАТА
- •ОПРЕДЕЛЕНИЕ ЖЕСТКОСТИ НАГРУЖАЮЩЕЙ СИСТЕМЫ ДЛЯ ВОЛОКНИСТЫХ КОМПОЗИТОВ И ПОРИСТЫХ МАТЕРИАЛОВ ПЕРИОДИЧЕСКОЙ СТРУКТУРЫ
- •ЗАКОНОМЕРНОСТИ СЛУЧАЙНЫХ ПОЛЕЙ СТРУКТУРЫ ОДНОНАПРАВЛЕННО АРМИРОВАННЫХ ВОЛОКНИСТЫХ КОМПОЗИТОВ
- •ЧИСЛЕННОЕ МОДЕЛИРОВАНИЕ УПРАВЛЯЕМЫХ СИСТЕМ, ПРЕДСТАВЛЕННЫХ ВЕКТОРНО-МАТРИЧНЫМ УРАВНЕНИЕМ СОСТОЯНИЯ
- •СПЕЦИАЛИЗИРОВАННЫЙ ПРОГРАММНЫЙ КОМПЛЕКС ДЛЯ ОЦЕНКИ СТАБИЛЬНОСТИ ЗАРЯДОВ РДТТ
- •МОДИФИКАЦИЯ СВЯЗУЮЩЕГО НА ОСНОВЕ ДИАНОВОЙ СМОЛЫ ЭД-20 ДЛЯ ПОВЫШЕНИЯ ТЕПЛО- И ХИМИЧЕСКОЙ СТОЙКОСТИ СТЕКЛОПЛАСТИКОВЫХ ИЗДЕЛИЙ
- •ПОИСК СПОСОБОВ МОДИФИКАЦИИ ПЛЕНКИ ПТР ДЛЯ ПОВЫШЕНИЯ ХИМИЧЕСКОЙ СТОЙКОСТИ И СТОЙКОСТИ К ГИДРОАБРАЗИВНОМУ ИЗНОСУ
- •МОДЕЛИРОВАНИЕ ОСОБЕННОСТЕЙ МЕХАНИЧЕСКОГО ПОВЕДЕНИЯ ЗЕРНИСТЫХ КОМПОЗИЦИОННЫХ МАТЕРИАЛОВ
- •ИСПОЛЬЗОВАНИЕ ОТХОДОВ ХИМИЧЕСКОГО ПРОИЗВОДСТВА ПРИ ПОЛУЧЕНИИ ОФСЕТНОЙ БУМАГИ
- •ИССЛЕДОВАНИЕ ВОЗМОЖНОСТИ ИСПОЛЬЗОВАНИЯ СКОПА ОЧИСТНЫХ СООРУЖЕНИЙ ЦБП ДЛЯ ПОЛУЧЕНИЯ КРОВЕЛЬНОГО МАТЕРИАЛА
- •АЭРОКОСМИЧЕСКАЯ ТЕХНИКА И ВЫСОКИЕ ТЕХНОЛОГИИ - 2003
- •ОБЪЕКТНАЯ КЛАССИФИКАЦИЯ НАВИГАЦИОННЫХ СИСТЕМ
- •ЭКСПЕРИМЕНТАЛЬНОЕ ИССЛЕДОВАНИЕ СВЧ ИЗМЕРИТЕЛЯ ПАРАМЕТРОВ ГАЗОВОГО ПОТОКА В ЭНЕРГЕТИЧЕСКИХ УСТАНОВКАХ
- •ИССЛЕДОВАНИЕ СИСТЕМЫ СТАРТА ПРОТИВОГРАДОВОЙ ИЗДЕЛИЯ НОВОГО ПОКОЛЕНИЯ "АЛАН"
- •ФИЗИКО-ХИМИЧЕСКИЕ ХАРАКТЕРИСТИКИ ВЗАИМОДЕЙСТВИЯ НЕПРЕДЕЛЬНОГО ОЛИГОЭФИРУРЕТАНА С ДИНИТРИЛОКСИДОМ В АКТИВНОМ ПЛАСТИФИКАТОРЕ
- •ПОСТАНОВКА И РЕШЕНИЕ ОБРАТНОЙ ГЕОМЕТРИЧЕСКОЙ ЗАДАЧИ МАГНИТОСТАТИКИ ДЛЯ МАГНИТНОЙ ДЕФЕКТОСКОПИИ
- •РЕШЕНИЕ ПРЯМОЙ ЗАДАЧИ С СИНУСОИДАЛЬНОЙ ГРАНИЦЕЙ ДЛЯ МАГНИТНОЙ ДЕФЕКТОСКОПИИ
- •КРАЕВЫЕ ЗАДАЧИ МЕХАНИКИ ЗАКРИТИЧЕСКОГО ДЕФОРМИРОВАНИЯ И РАЗРУШЕНИЯ ПОВРЕЖДЕННЫХ ТЕЛ
- •ОБНАРУЖЕНИЕ НЕИСПРАВНОСТЕЙ ДАТЧИКОВ САУ ГТД С ИСПОЛЬЗОВАНИЕМ МЕТОДА МАКСИМАЛЬНОГО ПРАВДОПОДОБИЯ
- •АНАЛИЗ ОШИБОК ВОЛОКОННО-ОПТИЧЕСКОГО ГИРОСКОПА ПРИ РАЗЛИЧНЫХ ТЕМПЕРАТУРНЫХ УСЛОВИЯХ
- •ПРОСТРАНСТВЕННЫЙ ИЗГИБ КРИВОЛИНЕЙНЫХ ТРУБ ИЗ ВОЛОКНИСТЫХ КОМПОЗИЦИОННЫХ МАТЕРИАЛОВ
- •ВЛИЯНИЕ ТЕМПЕРАТУРЫ ОКРУЖАЮЩЕЙ СРЕДЫ НА ВЫХОДНЫЕ ПАРАМЕТРЫ ИНЕРЦИАЛЬНОЙ БЕСПЛАТФОРМЕННО КУРСОВЕРТИКАЛИ
- •ПРИМЕНЕНИЕ ПОВЕРХНОСТНОГО ПЛАСТИЧЕСКОГО ДЕФОРМИРОВАНИЯ ДЛЯ ПРАВКИ ДЕТАЛЕЙ ТИПА МАЛОЖЁСТКИХ ВАЛОВ 4
- •АЭРОКОСМИЧЕСКАЯ ТЕХНИКА И ВЫСОКИЕ ТЕХНОЛОГИИ - 2003
- •О БАЛЛИСТИЧЕСКОЙ ПОГРЕШНОСТИ ОДНОРОТОРНОГО ГИРОКОМПАСА
- •НЕЛИНЕЙНЫЕ МОДЕЛИ ПРОГНОЗИРОВАНИЯ ЭФФЕКТИВНЫХ УПРУГИХ СВОЙСТВ ВЫСОКОПОРИСТЫХ композитов
- •УСТРОЙСТВО ЗАПОРНОЕ ОГНЕСТОЙКОЕ - УЗО (СПОСОБ ПЕРЕКРЫТИЯ ТРУБОПРОВОДА)
- •МЕТОДОМ ГИДРОЛИТИЧЕСКОЙ ДЕСТРУКЦИИ
- •РАЗРАБОТКА РЕЦЕПТУРЫ УНИВЕРСАЛЬНОГО МОРОЗОУСТОЙЧИВОГО ВОДОСОДЕРЖАЩЕГО ПРОМЫШЛЕННОГО ВЗРЫВЧАТОГО ВЕЩЕСТВА
- •ВЫЧИСЛИТЕЛЬНЫЙ ЭКСПЕРИМЕНТ КАК ЭЛЕМЕНТ МЕТОДИЧЕСКОГО ОБЕСПЕЧЕНИЯ ОПЫТНОГО ОПРЕДЕЛЕНИЯ НЕУПРУГИХ СВОЙСТВ МАТЕРИАЛОВ
- •ПРИМЕНЕНИЕ ЖИДКИХ КОМПОНЕНТОВ В ТРАДИЦИОННЫХ И НЕТРАДИЦИОННЫХ СХЕМАХ РАКЕТНОГО И СТВОЛЬЦОГО ВООРУЖЕНИЯ
- •АЭРОКОСМИЧЕСКАЯ ТЕХНИКА И ВЫСОКИЕ ТЕХНОЛОГИИ - 2003
- •КРАЕВАЯ ЗАДАЧА ТЕРМОЭЛЕКТРОУПРУГОСТИ ДЛЯ ПЬЕЗОКОМПОЗИТОВ
- •АЭРОКОСМИЧЕСКАЯ ТЕХНИКА И ВЫСОКИЕ ТЕХНОЛОГИИ - 2003
- •ПАРАМЕТРЫ ОРБИТЫ СПУТНИКА
- •-т = const.
- •АЭРОКОСМИЧЕСКАЯ ТЕХНИКА И ВЫСОКИЕ ТЕХНОЛОГИИ - 2003
- •УРАВНЕНИЕ ДВИЖЕНИЯ ТЕЛА С ПЕРЕМЕННОЙ МАССОЙ
- •МАТЕМАТИЧЕСКОЕ МОДЕЛИРОВАНИЕ ПРОЦЕССОВ В КАМЕРЕ ВОСПЛАМЕНЕНИЯ УСТАНОВКИ СИНТЕЗА УЛЬТРАДИСПЕРСНОГО ОКСИДА АЛЮМИНИЯ
- •РАКЕТНЫЕ ДВИГАТЕЛИ ДЛЯ ПОЛЁТА НА МАРСЕ, ИСПОЛЬЗУЮЩИЕ МАРСИАНСКИЕ ПРИРОДНЫЕ РЕСУРСЫ
- •МЕТОД РАСЧЕТА НАПРЯЖЕННОГО СОСТОЯНИЯ ПРИ ПРОКАТКЕ ПОЛОСЫ НЕСИММЕТРИЧНОГО ПРОФИЛЯ
- •ПРИМЕНЕНИЕ СОВРЕМЕННЫХ ТЕХНОЛОГИЙ АВТОМАТИЗАЦИИ ДЛЯ УПРАВЛЕНИЯ И КОНТРОЛЯ ПРОЦЕССА ИСПЫТАНИЯ ЭЛЕКТРИЧЕСКИХ МАШИН
- •МОДЕЛИРОВАНИЕ ДИАГНОСТИКИ ТРУБ ДЛЯ НЕФТЯНОЙ ПРОМЫШЛЕННОСТИ МИКРОРОБОТОМ С ДИСТАЦИОННЫМ УПРАВЛЕНИЕМ
- •МЕХАНИКА РОБОТА МАНИПУЛЯТОРА РМ - 01, ИСПОЛЬЗУЕМОГО ДЛЯ ПОГРУЗОЧНО-РАЗГРУЗОЧНЫХ РАБОТ
- •АЭРОКОСМИЧЕСКАЯ ТЕХНИКА И ВЫСОКИЕ ТЕХНОЛОГИИ - 2003
- •ВОЛОКОШШ-ОПТЙЧЕСКИЙ КАБЕЛЬ
- •АЭРОКОСМИЧЕСКАЯ ТЕХНИКА И ВЫСОКИЕ ТЕХНОЛОГИИ - 2003
- •МЕХАНИКА МЕХАНИЗМА РУЛЕВОГО УПРАВЛЕНИЯ АВТОМОБИЛЯ
- •а - и -rsinxcosS
- •АЛГОРИТМ УПРАВЛЕНИЯ МАНИПУЛЯТОРА, ИСПОЛЬЗУЕМОГО ДЛЯ ТРАНСПОРТНЫХ РАБОТ
- •МОДЕЛИРОВАНИЕ ТРЕЩИН В ДИСКАХ АВИАЦИОННЫХ ДВИГАТЕЛЕЙ МЕТОДОМ КОНЕЧНЫХ ЭЛЕМЕНТОВ В ТРЕХМЕРНОЙ ПОСТАНОВКЕ
- •УЧЕТ ВЛИЯНИЯ РАЗМЕРОВ НАЧАЛЬНОГО ДЕФЕКТА НА СКОРОСТЬ РАЗВИТИЯ ТРЕЩИН В ВЫСОКОНАГРУЖЕННЫХ ДЕТАЛЯХ ГАЗОТУРБИННЫХ ДВИГАТЕЛЕЙ
- •МОДЕЛИРОВАНИЕ НАПРЯЖЕННО-ДЕФОРМИРОВАННОГО СОСТОЯНИЯ (НДС) ЛОКАЛЬНЫХ ЗОН ДИСКОВ В УСЛОВИЯХ НЕСТАЦИОНАРНОСТИ
- •К РАЗРАБОТКЕ ЗАКОНА ИЗМЕНЕНИЯ СУММАРНОЙ СИЛЫ СОПРТИВЛЕНИЯ ОТКАТУ В ПАО
- •АЭРОКОСМИЧЕСКАЯ ТЕХНИКА И ВЫСОКИЕ ТЕХНОЛОГИИ - 2003
- •СРЕДНЕ БАЛЛИСТИЧЕСКОЕ ДАВЛЕНИЕ ПОРОХОВЫХ ГАЗОВ В КАНАЛЕ СТВОЛА
- •ТЕПЛОМАСООБМЕН ПРИ БЕЗДРЕНАЖЙОМ ХРАНЕНИИ КРИОГЕННОГО ТОПЛИВА В ШИРОКОМ ДИАПАЗОНЕ ТЕМПЕРАТУР И ДАВЛЕНИЙ
- •МАТЕМАТИЧЕСКАЯ МОДЕЛЬ ТЕПЛООБМЕНА ИЗЛУЧЕНИЕМ
- •ОПИСАНИЕ ВЯЗКОУПРУГИХ СВОЙСТВ ЭЛАСТОМЕРОВ НА ОСНОВЕ СЕГМЕНТИРОВАННЫХ ПОЛИУРЕТАНМОЧЕВИН
- •СПОСОБ И ТЕХНОЛОГИЯ АВТОМАТИЧЕСКОГО ПОЖАРОТУШЕНИЯ ДЛЯ ВЗРЫВОПОЖАРООПАСНЫХ ОБЪЕКТОВ
- •АЭРОКОСМИЧЕСКАЯ ТЕХНИКА И ВЫСОКИЕ ТЕХНОЛОГИИ - 2003
- •АТТЕСТАЦИЯ ПЕРСОНАЛА - ОДНО ИЗ ОСНОВНЫХ ЗВЕНЬЕВ СИСТЕМЫ КАЧЕСТВА
- •НОВАЯ МОДЕЛЬ УТЕЧЕК ЧЕРЕЗ ЗАЗОР НА РЕБОРДЕ ПРИ ОДНОШНЕКОВОЙ ЭКСТРУЗИИ ТЕРМОПЛАСТОВ
- •ЧИСЛЕННЫЙ АНАЛИЗ ДИНАМИЧЕСКОГО ПОВЕДЕНИЯ ГИРОЭЛЕМЕНТА КОЛЬЦЕВОГО ИНДУКЦИОННОГО ГИРОСКОПА
- •МЕТОДЫ ОСРЕДНЕНИЯ В ЗАДАЧАХ ПРОЕКТИРОВАНИЯ ЭЛЕМЕНТОВ КОНСТРУКЦИЙ АЭРОКОСМИЧЕСКОЙ ТЕХНИКИ ИЗ КОМПОЗИЦИОННЫХ МАТЕРИАЛОВ
- •ОСОБЕННОСТИ.РАЗРАБОТКИ УГЛЕРОД-УГЛЕРОДНОГО НАСАДКА ДЛЯ ЖРД.
- •ВЕРИФИКАЦИЯ МОДЕЛИ ОПРЕДЕЛЕНИЯ КАЧЕСТВА АЭРОДИНАМИКИ СВЕРХЗВУКОВЫХ РЕШЕТОК ПРОФИЛЕЙ ТУРБИН
- •СОДОВО-НАТРОННАЯ ВАРКА ПОЛУЦЕЛЛЮЛОЗЫ С ИСПОЛЬЗОВАНИЕМ ВСПОМОГАТЕЛЬНЫХ ХИМИЧЕСКИХ ВЕЩЕСТВ
- •ВЛИЯНИЕ ВЛАГИ НА СТРУКТУРУ СЕГМЕНТИРОВАННЫХ ПОЛИУРЕТАНОВ НА ОСНОВЕ ПРОСТЫХ ОЛИГОЭФИРОВ1
- •ВЛИЯНИЕ СМЕШАННЫХ ПЛАСТИФИКАТОРОВ НА УПРУГИЕ СВОЙСТВА ПОЛИДИЕНУРЕТАНЭПОКСИДОВ1
- •КИНЕТИЧЕСКЙЕ ИССЛЕДОВАНИЯ ТЕРМОРАЗЛОЖЕНИЯ ПОЛИМЕРОВ НА БАЗЕ ТГ, ДТГ И ДТА КРИВЫХ.
- •ОПРЕДЕЛЕНИЕ МАКРОСКОПИЧЕСКИХ ХАРАКТЕРИСТИК ОПТОВОЛОКОННОГО КОНТУРА КАТУШКИ ГИРОСКОПА
- •ИЗУЧЕНИЕ МЕЖМОЛЕКУЛЯРНЫХ ВЗАИМОДЕЙСТВИЙ В ЭПОКСИДУРЕТАНСОДЕРЖАЩИХ ОЛИГОМЕРАХ
- •ИССЛЕДОВАНИЕ ДИФФУЗИОННЫХ ХАРАКТЕРИСТИК ОРГАНОПЛАСТИКОВОГО КОРПУСА РДТТ ПОСЛЕ ДЛИТЕЛЬНОГО ДЕЖУРСТВА В СОСТАВЕ РАКЕТЫ
- •АЭРОКОСМИЧЕСКАЯ ТЕХНИКА И ВЫСОКИЕ ТЕХНОЛОГИИ - 2003
- •ЭФФЕКТ ЗАКАЛКИ В H:LiNb03 ВОЛНОВОДНЫХ СЛОЯХ
- •МОДЕЛИРОВАНИЕ НЕСТАЦИОНАРНЫХ ПРОЦЕССОВ НАГРЕВА И ТЕПЛОПЕРЕДАЧИ В СТЕНКАХ КАМЕР СГОРАНИЯ ТОПЛИВА ИМПУЛЬСНЫХ ТЕПЛОВЫХ МАШИН
- •ВЛИЯНИЕ СТРУКТУРЫ ПОРОШКОВЫХ JV1ETАЛЛОКОМПОЗИТОВ НА МЕХАНИЗМ РОСТА УСТАЛОСТНЫХ ТРЕЩИН
- •СПИСОК УЧАСТНИКОВ КОНФЕРЕНЦИИ
ис с л е д о в а н и я свойств ПОРОШКОВОЙ ЦЕЛЛЮЛОЗЫ
по л у ч е н н о й из х л о п к о во й и д ре в е с н о й ц е л л ю л о л зы
МЕТОДОМ ГИДРОЛИТИЧЕСКОЙ ДЕСТРУКЦИИ
Носкова О.А., Погудина О.В Пермский государственный технический университет
Порошковая целлюлоза благодаря своим уникальным свойствам привлекает к себе внимание специалистов различных областей промышленности. На кафедре ТЦБП ПермГТУ ведутся работы по разработке способов
получения порошковой целлюлозы из разных видов волокнистого сырья и изучению свойств полученного целлюлозного порошка.
Задача данной работы состояла в изучении и сравнении свойств порошковой целлюлозы, полученной гидролизом из различного вида сырья.
В качестве исходного волокнистого сырья были использованы древесная вискозная сульфитная и хлопковая целлюлоза, в качестве гидролизующего агента —водные растворы соляной кислоты. В процессе работы были исследованы следующие свойства целлюлозы: длина волокон, выход, степень полимеризации (СП), медное число, массовая доля в целлюлозе карбонильных и карбоксильных групп, сорбционная способность по йоду' водоудержание, насыпная плотность.
Различия свойств порошковой целлюлозы, полученной из хлопковой и древесной вискозной целлюлозы, объясняются химическим составом, степенью окисления и морфологической структурой исходного волокнистого материала.
Для изучения свойств порошковой целлюлозы был проведен гидролиз волокнистого сырья (древесной сульфитной вискозной и хлопковой целлюлозы) до предельной СП по оптимальным режимам, соответственно: температура гидролиза 85 ОС и 80 ОС, концентрация соляной кислоты 4,5 % и 2,8 %.
В процессе гидролиза целлюлозы соляной кислотой по мере увеличения степени деструкции происходит разрушение волокон и образуется смесь продуктов различной длины. В результате гидролиза как хлопковой, так и древесной целлюлозы образуется целлюлозный порошок, основную долю которого составляют частицы с размером до 0,3 мм. При этом доля этих частиц в порошковой целлюлозе, полученной из хлопковой целлюлозы составляет 74,9 %, а полученной из древесной целлюлозы - 82,8 %. Возможно, такое различие объясняется более жесткими условиями получения целлюлозного порошка из древесной целлюлозы.
Выход порошковой целлюлозы, полученной из древесной целлюлозы, ниже, чем из хлопковой (93,7 % против 96 %). Объясняется это тем, что древесная целлюлоза содержит меньше альфа-целлюлозы, больше аморфной фракции, неустойчивой к действию кислот, и больше окисленных групп, чем хлопковая целлюлоза.
Предельная степень полимеризации порошковой целлюлозы, полученной из вискозной целлюлозы гидролизом с соляной кислотой, имеет более высокое значение, по сравнению с предельной СП, полученной из хлопкового сырья гидролизом с использованием той же кислоты (240 против 225), хотя исходная степень полимеризации вискозной целлюлозы ниже, чем у хлопковой (750 против 950).
В процессе получения волокнистой древесной целлюлозы (глубокая варка до получения мягкой целлюлозы, отбелка и облагораживание) происходит ее окисление, вследствие чего древесная целлюлоза содержит больше окисленных групп (медное число 1,18 г/100 г целлюлозы, массовая доля карбонильных и карбоксильных групп - 0,06 и 0,41 % соответственно), чем хлопковая целлюлоза (медное число 0,16 г/100 г целлюлозы, массовая доля карбонильных и карбоксильных групп 0,012 и 0,21 % соответственно). Древесная целлюлоза, содержащая больше окисленных групп, более чувствительна к действию различных реагентов, поэтому процессы деструкции и окисления в ходе гидролиза вискозной целлюлозы протекают в большей степени, т.е. больше образуется продуктов, содержащих окисленные группы. Медное число в результате гидролиза вискозной целлюлозы до предельной СП достигает 3,42 г/100 г целлюлозы, массовая доля карбонильных и карбоксильных групп соответственно - 0,41 % и 0,48 %, в то время как для хлопковой целлюлозы, гидролизованной в соляной кислоте при оптимальных условиях, эти показатели значительно ниже (соответственно - 2,58 г/100 г целлюлозы, 0,26 % и 0,24 %).
Значения показателей сорбционной и водоудерживающей способности порошковой целлюлозы, полученной в результате гидролиза древесной вискозной целлюлозы, выше, чем из хлопковой (соответственно 17,2 мг iyi г цел. и 61 % против 13,8 мг 12/1 г цел. и 40 %). Более высокие значения сорбционной способности по йоду и водоудержания целлюлозного порошка из вискозной целлюлозы связаны, возможно, с большей дефектностью кристаллитов древесной целлюлозы, что приводит к деструкции не только в доступных областях, но и на поверхности самих кристаллитов, в результате чего увеличивается доступная поверхность целлюлозного порошка
Удаление в процессе гидролиза аморфной части из волокнистого сырья приводит к образованию порошка с более высокой насыпной плотностью, по сравнению с исходной волокнистой целлюлозой. Насыпная плотность целлюлозного порошка, полученного из вискозной целлюлозы, ниже, чем из хлопковой (220 против 308 кг/м ). Повидимому, этот показатель в большей степени зависит от анизометрии частиц (отношения длины частиц к их ширине): чем больше показатель анизометрии, тем меньше насыпная плотность порошка
РАЗРАБОТКА РЕЦЕПТУРЫ УНИВЕРСАЛЬНОГО МОРОЗОУСТОЙЧИВОГО ВОДОСОДЕРЖАЩЕГО ПРОМЫШЛЕННОГО ВЗРЫВЧАТОГО ВЕЩЕСТВА
Нуруллаева Т.Э., Иванова И.П., Ибрагимов Н.Г., Ермилов А.С.
Пермский государственный технический университет, ФГУП “Научно-исследовательский институт полимерных материалов”
С целью решения проблемы утилизации разбронированных порохов и топлив, включения в производство простаивающего оборудования предприятий по производству спецтехники, а также с целью насыщения рынка промышленных взрывчатых веществ новыми высокоэффективными бризантными взрывчатыми веществами, безопасными при эксплуатации из-за низкой чувствительности к механическим воздействиям были проведены исследования по разработке водосодержащего промышленного взрывчатого вещества с высокими эксплуатационными характеристиками (диапазон эксплуатации - -40-+50°С) с использованием в качестве взрывчатого сенсибилизатора различных типов и марок порохов: измельчённых баллиститных топлив, артиллерийских порохов баллиститного и пироксилинового типов, сферических лаковых порохов.
При разработке водосодержащего взрывчатого вещества выбраны компоненты, определено их оптимальное соотношение с целью получения кислородного баланса, близкого к нулю для обеспечения максимальной реализации энергетических свойств взрывчатого материала (теплоты взрыва, идеальной работы взрыва, объёма газов) и снижения количества продуктов взрыва неполного окисления (СО, N0) для экологической безопасности, подобран эффективный гелеобразующий компонент - загуститель (водный раствор полиакриламида), определено оптимальное количество воды (14-18%), выбраны оптимальные размеры частиц активного наполнителя для обеспечения детонационных свойств взрывчатой композиции (толщина горящего свода не более 2мм), подобран структурирующий агент для загустителя, обеспечивающий высокие технологические вязкотекучие (“живучесть” массы) и физические (нерасслаиваемость и водостойкость) свойства промышленного взрывчатого вещества (сульфит натрия с бихроматом калия), изучен комплекс свойств, разработана технологическая схема изготовления промышленного взрывчатого вещества, разработано аппаратурное оформление технологического процесса изготовления.
Для возможности применения взрывчатого вещества в жёстких климатических условиях Сибири и Крайнего Севера исследования по снижению температуры замерзания до -40°С. Одним из известных путей снижения температуры замерзания водных растворов является введение в их состав криогенных добавок (антифризов). В качестве антифризов использованы в промышленном взрывчатом веществе соли щелочных и щелочноземельных металлов в сочетании с гликолями в количестве 20-30% по отношению к водному раствору окислителя - аммиачной селитры. Проведённые испытания ряда образцов показали невозможность получения требуемой морозостойкости при содержании аммиачной селитры - кристаллического полиморфного вещества - 30-50%. При уменьшении содержания аммиачной селитры до 20%, увеличении активного наполнителя - утилизируемых порохов и топлив до 50% и криогенных добавок до 15% была достигнута температура замерзания -40°С. Испытания оттермостатированных образцов при температуре -40°С в течение 24 часов укрупнённых образцов показали устойчивую и полную детонацию от штатных средств инициирования, допущенных Госгортехнадзором Российской Федерации. Морозостойкому образцу присвоен индекс “Селипор-3”
С целью расширения температурного диапазона применения промышленного взрывчатого вещества и возможности применения его в скважинах с агрессивной средой (рН=3-10,5) в состав были введены стабилизаторы химической стойкости - централит И, дифенилморфолин в количестве 0,05-0,50%.
На двух предприятиях отрасли начато промышленное производство промышленного взрывчатого вещества “Селипор-3”, проведены приёмочные испытания в натурных условиях гранитных карьеров СУ74 г. Екатеринбурга и “Микашевичи” республика Беларусь.
Результаты испытаний показали высокую работоспособность промышленного взрывчатого вещества “Селипор-3” на гранитах, гранитодиоритах и диоритах со степенью крепости пород / = 16-20 по шкале Протодьяконова, а также надёжность срабатывания в обводнённых скважинах от штатных средств инициирования.
п о
МАТЕМАТИЧЕСКОЕ ПРОГНОЗИРОВАНИЕ ЭКВИВАЛЕНТНЫХ ТЕМПЕРАТУР ЭКСПЛУАТАЦИИ ИЗДЕЛИЙ В УСЛОВИЯХ ПРЯМОГО ВОЗДЕЙСТВИЯ СОЛНЕЧНОГО ИЗЛУЧЕНИЯ
Одинцов Ю.Т., Мальцев КС.
ФГУП «Научно-исследовательский институт полимерных материалов», г. Пермь
К настоящему времени имеется значительный статистический материал (ГОСТ 16350-80, ГОСТ 2448282 и т.д.) о температурных условиях для большинства районов Земного шара. Эти данные с помощью ГОСТ 9.707-81 позволяют прогнозировать эквивалентные температуры изделий при хранении их под навесом. Однако различные машины и оборудование эксплуатируются в наземных условиях на открытом воздухе. При этом они подвергаются неблагоприятному воздействию климатических факторов (суточных и годовых изменений температур, солнечной радиации и т.д.). В результате воздействия климатических факторов ухудшаются свойства конструкционных материалов машин и снижаются сроки их служебной пригодности.
В предлагаемой работе с помощью численного конечноэлементного моделирования прогнозируется тепловое состояние многослойного изделия цилиндрической формы, подвергаемого в условиях эксплуатации прямому воздействию солнечного излучения. При расчете теплового состояния изделия учитываются следующие компоненты солнечного излучения: радиационный, конвективный и лучистый тепловые потоки и тепловой поток от земной поверхности. Задача решается при граничных условиях 2- го рода.
Привязка к условиям эксплуатации в конкретном географическом регионе осуществляется выбором соответствующих параметров граничных условий - ходом температуры окружающей среды, интенсивностью и продолжительностью солнечного излучения. Информация о температуре окружающей среды определена по ГОСТ 24482-82. Приход солнечной энергии на поверхность изделия рассчитывался
сприменением приведенных в работе [1] соотношений и зависимостей, учитывающих географическую координату (широту) размещения изделия, суточное склонение и ход солнца, пространственную ориентацию составляющих поверхность изделия конечных элементов.
На основе описанного алгоритма разработана вычислительная программа TeSunRad, позволяющая определять тепловое состояние во времени в любой точке поперечного сечения изделий, эксплуатируемых в естественных климатических условиях стран с жарким сухим тропическим климатом
сучетом воздействия прямого солнечного излучения. Конечной целью выполняемых расчетов, наряду с оценками теплового состояния, является получение информации типа температура-время ее действия в элементах за полный годовой цикл эксплуатации изделий в форме и объеме, достаточном для решения задачи прогноза сохраняемости характеристик принятыми на практике методами, например, по
изложенной в ГОСТ 9.707-81 процедуре.
Список литературы
1 Даффи Дж. А., Бекман У.А. Тепловые процессы с использованием солнечной энергии. М: Мир.- 1977.-420с.
ш
ОЦЕНКА СТЕПЕНИ ВЛИЯНИЯ ФОРМЫ ГОЛОВНОЙ ЧАСТИ НА ПРОЦЕСС ПРОНИКАНИЯ В ПЕСОК СНАРЯДОВ
С НЕТРАДИЦИОННЫМИ МАССОВЫМИ ХАРАКТЕРИСТИКАМИ
Ожиганов И.А.
Пермский государственный технический университет
Известно, что форма головной части (ГЧ) проникающего в преграду снаряда существенно влияет на дальность проникания. Так, в /1/ влияние головной части описывается коэффициентом X в формуле дальности проникания. Значения коэффициента меняются от 0,56 для тупого снаряда до 1,32 для конической ГЧ длиной в 3 калибра.
С целью оценки степени влияние формы головной части на процесс проникания в песок снарядов нетрадиционных массовых характеристик был реализован план экспериментов по построению регрессионной модели второго порядка. В качестве независимых исследуемых факторов, определяющих дальность проникания, были приняты: а) х х - масса снаряда т; б) х2 - начальная скорость v0; в) х3 - угол полураствора конуса р. Априори допуская нелинейность зависимости дальности проникания от различных факторов, был выбран квази-Д-оптимальный симметричный план Песочинского /2/, обеспечивающий наименьший объем эллипсоида рассеяния оценок коэффициентов.
При реализации плана кодированные значения факторов варьировались на трех уровнях: -1, 0, +1. Представлялось необходимым реальные интервалы варьирования факторов установить достаточно широкими с целью захватить большую область исследования, однако препятствием к расширению интервалов варьирования являлись возможности экспериментальной базы, в частности, по максимальной дальности проникания. Ограничения по максимальной дальности определяли выбор наиболее "напряженной" точки эксперимента - с максимальной массой и максимальной начальной скоростью. Масса снаряда в экспериментах изменялась в интервале от 0,3 до 1,5 кг (коэффициент массы Ст = 24.. 123 кг/дм^), начальная скорость от 50 до 100 м/с, угол полураствора конуса головной части снаряда Р от
30° до 90°. План экспериментов состоял из 13 опытов с дублированием. В результате расчетов коэффициентов модели, оценки их значимости по 5% уровню получена зависимость дальности проникания в рассматриваемом интервале изменения факторов.
На рисунке показана зависимость коэффициента формы головной части, определяемого как отношение дальностей проникания снаряда с произвольным углом ГЧ и снаряда с базовой формой ГЧ. В качестве базовой формы ГЧ
выбрана тупая ГЧ (угол полураствора конуса ГЧ р=90°). |
|
На графике обозначено: 1 |
эксперименты со |
снарядами Ст = 24 кг/дм3; 2,3 - эксперименты со снарядами Ст = 123 кг/дм3 (начальная скорость 50 и 100 м/с); 4 зависимость для конической ГЧ /1/; 5 зависимость для оживальной ГЧ /1/ (пересчитаны к базовой форме ГЧ).
Для классических снарядов (коэффициент массы Ст до 24 кг/дм3) можно отметить, что значения коэффициента формы ГЧ близки к предложенным в /1/, хотя зависимость
(в калибрах) имеет иной характер. Для тяжелых снарядов с Ст = 123 кг/дм3 в исследуемом диапазоне скоростей влияние формы
головной части несущественно (кривые 2, 3).1
1.Yuong C.W Depth Prediction for Earth-Penetrations Projectiles. - J.Soil Mech. And Found.Dev.ASCE 1969, СМ3, p.80.
2.Новик Ф.С., Арсов Я.Б. Оптимизация процессов технологии металлов методами планировани экспериментов. - М.: «Машиностроение», 1980, 304 с.
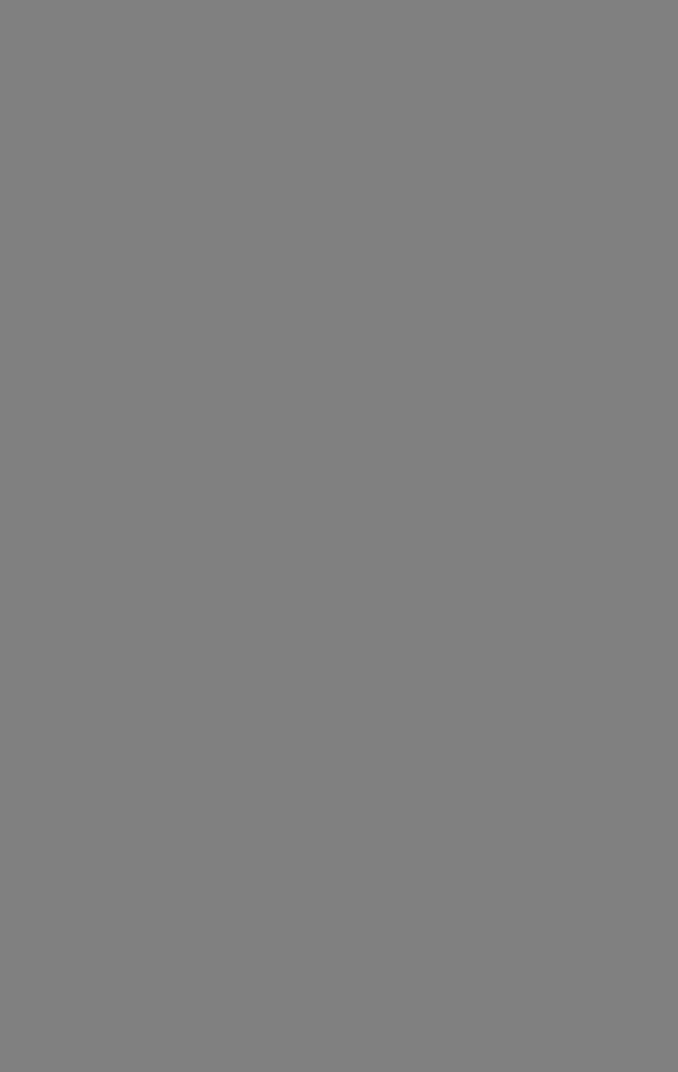
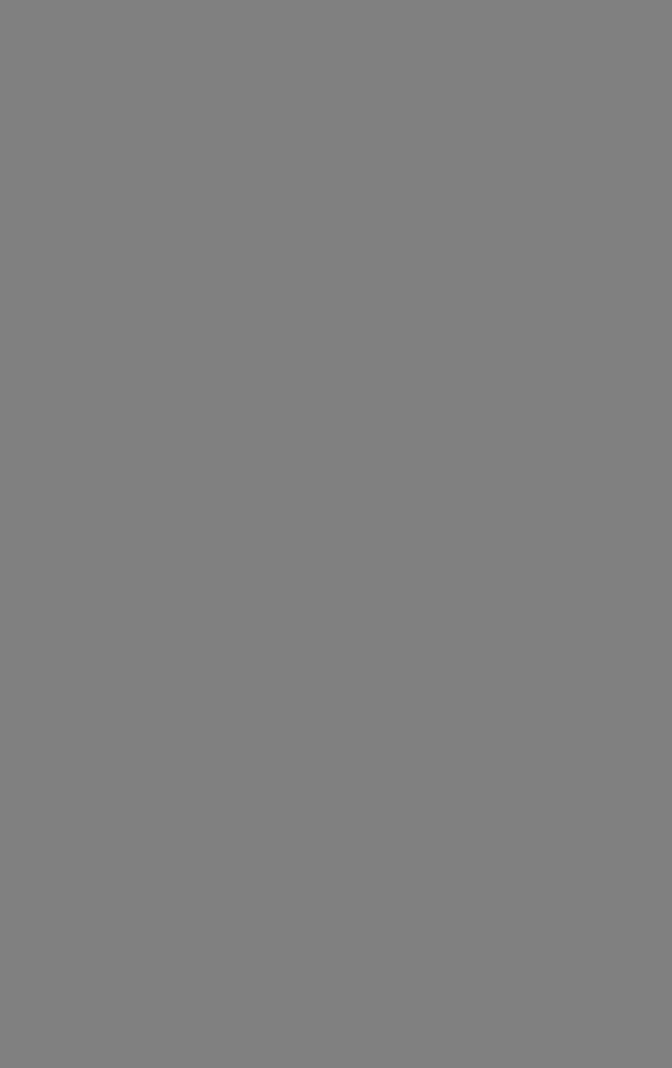