
Статистические исследования контроля качества в автоматизированных
..pdf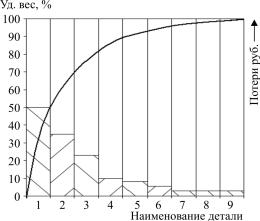
вероятности установления причин появления новых дефектов. Имея канал прямой связи, можно направлять в систему информацию об обнаруженном дефекте: наименование детали, заводской номер, технология ее изготовления, характер дефекта и условия его обнаружения. Канал обратной связи позволяет выдавать соответствующую информацию о причинах появления дефекта и о мероприятиях по его предотвращению.
Рис. 5.18. Диаграмма Парето
Используя проведенные исследования, можно выделить определяющий фактор. Так, при механической обработке таким доминирующим фактором является состояние режущего инструмента.
Для повышения оценки системы качества и получения разнородной информации, например при аудите, диаграммы Парето необходимо строить по нескольким признакам:
1)потери (затраты) времени, труда, средств;
2)себестоимость продукции (ремонта);
3)персонал.
Количество затрат, связанных с обеспечением качества продукции, в порядке возрастания можно распределить в следующей последовательности:
121
♦5…10 % – предупредительные мероприятия (анализ производственных процессов, построение системы сбора оперативной информации, определение единичных и комплексных показателей надежности и др.);
♦16…32 % – оценка качества продукции, начиная со входного контроля, проведения операционного контроля и испытаний, анализа работы контрольно-измерительной лаборатории и т.д.;
♦79…58 % – мероприятия, направленные на выявление, анализ и исправление дефектов, определение потерь от брака, затраты на замену дефектных деталей годными, организацию работы станций обслуживания и т.д.
5.6.ПОСТРОЕНИЕ ДИАГРАММЫ ПАРЕТО
ВПРОГРАММЕ «STATISTICA 8»
Используя сгруппированные по частотам (mi) и отсортированные по убыванию значения исходной выборки (приложение А – «Исходные данные»), построим диаграмму Парето в программе «STATISTICA 8» (рис. 5.21 и 5.22), например, для оборудования тепловогопункта(рис. 5.20, графа«Числодефектов» эквивалентна «mi»).
Тепловой пункт как объект управления включает в себя следующее основное оборудование (рис. 5.19): насосы отопления, насосы горячего водоснабжения (ГВС), управляющие контроллеры, частотные преобразователи, различные клапаны, датчики давления и температуры, персональный компьютер – автоматизированное рабочее место (АРМ) и др.
Алгоритм построения диаграммы Парето № 2 (см. рис. 5.22):
1.Вызвать модуль построения диаграммы: «Graphs» – «2DGraphs» – «Bar/ColumnPlots».
2.На вкладке «Quik» в качестве переменной «Variables» выбрать «Накопленная сумма дефектов, %», а также пункт – «Regular».
3.На вкладке «Options 1» в выпадающем списке «Caselabels» выбрать «Variable» – «Наименование узла».
4.Нажать кнопку «OK».
122
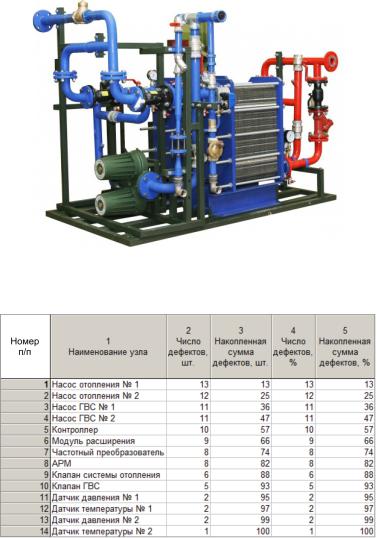
Рис. 5.19. Внешнийвид оборудования теплового пункта
Рис. 5.20. Данные диаграммы Парето, полученные на основе учётного листка
123
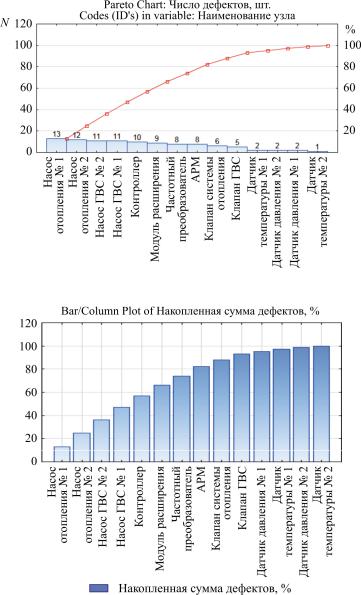
Рис. 5.21. Диаграмма Парето № 1
Рис. 5.22. Диаграмма Парето № 2
124
5.7. ДИАГРАММЫ «ПРИЧИНЫ – РЕЗУЛЬТАТ»
Причинно-следственная диаграмма (ПСД) позволяет выявить и систематизировать факторы (причины), действие которых влияет на тот или иной результат процесса, который, в свою очередь, приводит к возникновению проблемы, от решения которой зависит качество производимой продукции.
На основании ПСД качественно проводится анализ появления причин, приводящих к возникновению проблем. Поэтому ее целесообразно строить на начальной стадии анализируемого процесса.
После этого, используя диаграммы Парето, корреляционный, дисперсионный анализ, выявляют степень влияния этих причин. Контрольный листок, диаграмма разброса, регрессионный анализ, графики и прочее позволяют оценить характер влияния. Затем разрабатывают мероприятия, на основании которых принимаются решения по устранению или уменьшению влияния причин отступлений от технических условий.
Результат действия системы факторов и причин влияет на качество изделий в ходе реализации технологического процесса, совокупность которых можно охарактеризовать как взаимодействие 4М. Результат действия этих причинных факторов, характеризующий зависимость между процессом (4М) и качеством, можно представить в графическом виде (рис. 5.23).
Если результат процесса оказался неудовлетворительным, то это свидетельствует об отклонении процесса в какой-то точке от заданных условий. Поэтому необходимо поддерживать в процессе производства заданные условия, что будет гарантировать обеспечение формирования заданного качества. Учитывая, что показатели качества, как правило, выражаются заданными параметрами, то производя обработку статистических данных, можно осуществлять контроль и предсказыватьрезультатпроцессадлязаданныхусловийработы.
Поэтому для производства изделий высокого качества необходимо поставить в соответствие различные факторы производства
125
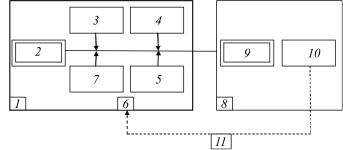
Рис. 5.23. Причинно-следственная диаграмма:
1 – система причинных факторов; 2 – основные факторы производства; 3 – материалы; 4 – оборудование, включая инструменты; 5 – методы операций; 6 – процесс (4М); 7 – оператор; 8 – следствие; 9 – характеристики качества; 10 – данные; 11 – процесс контролируется качеством
наиболее важным показателям качества. Среди факторов необходимо выделить те, которые наиболее значимо отрицательно влияют на результат качества. После этого необходимо разработать программу действий по исключению (уменьшению) таких факторов правильно подобранными мероприятиями, разработанными на основе причин- но-следственной диаграммы.
Объектом исследования с помощью ПСД может быть проблема (например, неудовлетворенность потребителей) или результат поиска (например, полная удовлетворенность потребителей). Второй вариант наиболее предпочтительный, так как позволяет выявить наиболее эффективные подходы к достижению цели.
Схемы, характеризующие зависимость между полученными результатами и причинами, воздействующими на эти результаты, именуются диаграммами «причины – результат». Диаграмма «причины – результат» имеет «хребет», большие, средние и малые «кости», она напоминает по форме рыбу и поэтому называется схемой «рыбий скелет» (рис. 5.24). Диаграмма «причины – результат» – весьма эффективное средство выявления главных причин.
126
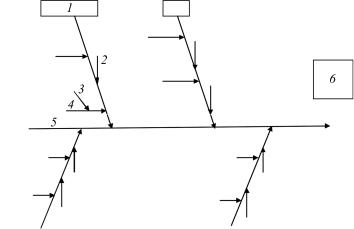
Рис. 5.24. Форма диаграммы «причины – результат» (диаграмма К. Ишикавы): 1 – факторы (причины); 2 – большая «кость»; 3 – малая «кость»; 4 – средняя «кость»; 5 – «хребет»; 6 – характеристика (результат)
Пример 5.9. Проанализируем затраты на контроль качества на основе ПСД.
Контроль качества производимых продуктов начинается на этапе разработки изделия и направлен на удовлетворение требований потребителя. Достижение этой цели всегда связано с ростом затрат на контроль качества, хотя эти затраты и стремятся уменьшить.
Для анализа затрат, связанных с контролем качества, на первом этапе анализа составляли диаграмму «причины – результат»
(рис. 5.25).
Причинно-следственная диаграмма строится на основе максимального числа факторов, характеризующих характеристику исследуемого объекта, значение которой превышает предельные допустимые значения. При исследовании причин появления такого явления могут привлекаться специалисты, не имеющие прямого отношения к работе, так как они могут способствовать выявлению причин отклонения характеристики от заданных значений и дать
127
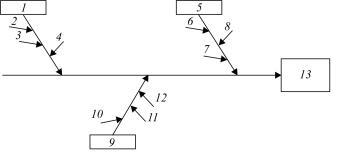
необходимые рекомендации по их устранению. В этом случае наиболее эффективным методом является групповой метод анализа «мозговой штурм».
Рис. 5.25. Диаграмма «причины– результат» для анализапричин, вызывающих ростзатрат наконтроль качества: 1 – расходынапрофилактику брака; 2 – расходынаразработку правил контроля: 3 – расходынаобучение персонала, контролирующегокачество; 4 – поверкакалибров иизмерительных инструментов; 5 – расходы наужесточениеконтроля; 6 – увеличениерасходов наремонтизмерительныхустройств; 7 – увеличениерасходов насоставителей программы испытанийиконтроля; 8 – увеличение расходов на испытателей; 9 – расходы набрак; 10 – много возвратов; 11 – многопеределок; 12 – много рекламаций; 13 – ростзатратнаконтролькачества
Исходя из опыта применения ПСД, можно перечислить рекомендации по их совершенствованию:
1.При рассмотрении проблемы следует принимать во внимание как внутренние, так и внешние факторы. При рассмотрении со- циально-экономических проблем необходимо учитывать экономическую ситуацию в стране, на мировом рынке, налоговую политику государства, региональные особенности и т.п.
2.Каждое предложение, способствующее выявлению факторов и причин, приводящих к возникновению проблемы, должно вноситься в определенное место ПСД, предлагаемое автором идеи. Остальные участники «мозгового штурма» могут предлагать свои идеи. В этом случае выбор окончательного решения определяется большинством голосов.
128
3.Окончательный вариант разработки ПСД анализируется всеми членами команды. При необходимости возможна консультация с профильными специалистами, не участвующими в «мозговом штурме». Появившиеся проблемы и предложения обсуждают через 1…3 дня всеми членами команды.
4.Важная для организации проблема (повышение качества продукции, стабилизация технологического процесса и т.п.) может обсуждаться в коллективе организации.
5.При разработке ПСД в команду следует включить работников, непосредственных исполнителей работ, знающих не только внутренние проблемы производства, но и тех, кто может предложить эффективные пути решения проблем: операторы и наладчики оборудования, контролеры, технологи, специалисты финансовых служб и др.
В японском промышленном стандарте (JIS) на терминологию
вобласти контроля качества дано следующее определение диаграммы: диаграмма причин и результатов – диаграмма, которая показывает отношение между показателями качества и воздействующими на него факторами.
5.8. ПОСТРОЕНИЕ ПРИЧИННО-СЛЕДСТВЕННОЙ ДИАГРАММЫ В ПРОГРАММЕ «STATISTICA 8»
В качестве примера для построения причинно-следственной диаграммы (ПСД) рассмотрим влияние на выходную скорость колёсной роботизированной платформы различных факторов, представленных на рис. 5.26, б.
При составлении диаграммы «причины – результат» для анализа причин, влияющих на выходную скорость колёсной роботизированной платформы, необходимо учесть как внутренние, так и внешние факторы, среди которых можно выделить следующие: сцепление, механическая часть, электрическая часть и управляющие сигналы.
129
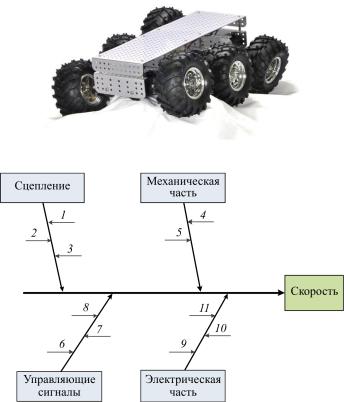
а
б
Рис. 5.26. Причинно-следственная диаграмма роботизированной платформы: а – внешний вид; б – причинно-следственная диаграмма
Опишем параметры, формализующие основные факторы
(см. рис. 5.26):
1.Коэффициент трения рабочей поверхности колёс.
2.Коэффициент трения покрытия.
3.Угол наклона роботизированной платформы относительно линии горизонта.
4.Соответствие состояния платформы стандарту.
130