
А К А Д Е М И Я Н А У К СССР
ИНСТИТУТ МАШИНОВЕДЕНИЯ ИМ. А.А. EJlABQilPADO&A^
СТАТИСТИЧЕСКИЕ
ЗАКОНОМЕРНОСТИ
МАЛОЦЩШОВОП)
РАЗРУШЕНИЯ
Ответственные редакторы:
член-корреспондент АН СССР Н.А. МАХУТОВ, доктор технических наук А.Н. РОМАНОВ
МОСКВА"НАУКА”
1989
А в т о р ы :
Н.А. Махутов, В.В. Зацаринный, Ж.Л. Базарас, Ж.М. Бледнова, М.М. Гаденин, Д.А. Гохфельд, А.В. Гурьев, М.А. Даунис,
A.Б. Злочевский, В.С. Калмуцкий, С.Ф. Кащенко, К.М. Кононов,
B.Ф. Лукьянов, В.А. Новиков, В.А. Петушков, А.Н. Романов, В.Е. Савицкий, О.С. Садаков
УДК 621.81:539.4
Статистические закономерности малоциклового разрушения / Н.А. Ма хутов, В.В. Зацаринный, Ж.Л. Базарас и др. - М.: Наука, 1989. - 252 с. - ISBN 5-02-007162-5
На основе деформационных и силовых критериев механики разрушения рассматри ваются вероятностно-статистические подходы к экспериментальной и расчетной оценке прочности, долговечности и живучести материалов, элементов конструкций и сварных соединений, подвергающихся воздействию высокого уровня циклических нагрузок и характеризующихся ограниченным ресурсом работы (104-г5« 104 циклов нагруже ния) .
Предлагаемые подходы обо сновываются экспериментальными статистическими ис следованиями, анализом закономерностей рассеяния характеристик статических и циклических свойств материалов, а также характеристик развития трещин при неодно родном напряженном состоянии (зоны концентрации, сварка, покрытия).
Рассчитана на научных и инженерно-технических работников. Табл. 40. Ил. 118. Библиогр.: 236 назв.
Рецензенты: В.П. Когаев, М.Н. Степнов
Редактор Н.Е. Миронова
On the ground of strain and stress criteria the authors present probabilistic —statistical approaches to experimental and analytical estimation of strength, durability and survival" ce of materials, structure elements and weld connections being subjected to cyclic loading
action and being characterized by a limited service life (a cycle number being equal to |
10 ~ |
5-104). |
, |
The approaches proposed are substantiated by experimental statistical investigations, ЬУ analysis of laws of static and cyclic material properties dispersion as well as of crack extension in inhomogeneous stresses state (concentration zones, welding, coatings).
The book is intended for scientific workers, engineers and other technical workers. It contains 118 illustrations, 40 tables, 236 references.
c 2040030000-493 667-89, |
KH.2. |
© Коллектив авторов, 19$9 |
|
055(02) |
89 |
|
|
ISBN 5-02-007162-5
ПРЕДИСЛОВИЕ
Научные и прикладные разработки в области малоцикловой прочности, получившие интенсивное развитие в связи с задачами интенсификации научно-технического прогресса в передовых отраслях машиностроения и новой техники, позволили к настоящему времени сформулировать ряд фундаментальных закономерностей деформирования и разрушения при ма лом числе циклов нагружения (до103 —105). Эти условия экстремального нагружения по уровню термомеханических воздействий на элементы ма шин и конструкций приводят к тому, что в локальных зонах различной протяженности возникают повторные упругопластические деформации.
Цикличность стационарного и нестационарного эксплуатационных нагру жений в сочетании с циклическими упругопластическими деформациями приводит к сложной кинетике местных напряженно-деформированных сос тояний. При этом предельные состояния по моменту образования трещин в наиболее нагруженных зонах и по стадиям их последующего развития должны рассматриваться в существенно нелинейной постановке. Темпера турно-временной фактор в еще большей степени усложняет процессы цик лического перераспределения напряжений и деформаций в местах конст руктивной концентрации и в вершине развивающихся трещин.
Критериальные характеристики образования и развития малоциклового разрушения также оказываются функционально связанными с уровнем нагружения, числом циклов, температурой, временем цикла и суммарным временем нагружения. Степень проявления нестационарности локальных напряженно-деформированных состояний в условиях воздействия указан ных конструктивных факторов находится в прямой связи с циклическими свойствами применяемых конструкционных материалов.
Обобщение результатов целого комплекса расчетных и эксперименталь ных исследований по перечисленным вопросам малоцикловой прочности, выполненных в Институте машиноведения им. А.А.Благонравова АН СССР
при взаимодействии с ведущими научными центрами страны и с промыш ленными организациями, явилось предметом серии публикаций в изда тельстве ’’Наука”: ’’Прочность при малоцикловом нагружении” (1975 г.), ’’Поля деформаций при малоцикловом нагружении” (1977 г.), ’’Прочность при изотермическом и неизотермическом малоцикловом нагружении”
(1979 |
г.), |
’’Уравнения состояния при малоцикловом нагружении” |
(1981 |
г), |
’’Прочность конструкций при малоцикловом нагружении” |
(1983 г.), ’’Механика малоциклового разрушения” (1986).
Указанные монографии отразили уровень разработок проблемы мало цикловой прочности в детерминированной постановке. Следующим этапом их развития является переход на статистические трактовки малоциклового разрушения, при которых активно используются базовые детерминирован ные закономерности прочности при малом числе циклов нагружения.
Настоящая монография содержит анализ трех основных сторон вероят ностного описания условий образования и развития разрушения: методы и средства определения статистическиххарактеристик малоцикловой усталос ти; основные закономерности и их статистические параметры при описа нии процессов деформирования и разрушения; приложения полученной исходной статистической информации к оценке прочности, живучести и ре сурса по параметру вероятностиТтовреждения.
В качестве статистического описания малоцикловой прочности прини маются деформационные критерии в кинетической постановке. При этом систематические экспериментальные исследования и статистический анализ получаемых результатов подтверждают справедливость использования лог нормальных, нормальных и усеченных распределений основных параметров кривых малоциклового деформирования и разрушения.
Принципиальное значение имеет факт связи этих распределений и пара метров с теми, которые получаются при однократном статическом нагруже нии стандартных рбразцов. В то же время при малоцикловом нагружении по сравнению со статическим существенно возрастает роль неоднородности микропластических деформаций в структурно неоднородных материалах.
К числу новых в научном отношении следует отнести данные по статис тическим закономерностям образования и развития малых и протяженных трещин в зонах концентрации напряжений. Характерными при таких усло виях оказываются процессы ускоренного роста начальных трещин и сущест венного увеличения их рассеяния. Расширение примененеия в машинострое нии упрочняющих и восстанавливающих технологий (коррозионно-стойкие и упрочняющие покрытия) с выраженной стохастичностью локальных свойств требует специальных методов исследований и анализа результатов.
Комплексные вероятностные исследования малоцикловой прочности используются как научная основа для оценки долговечности, запасов, ис ходного и остаточного ресурса элементов машин и конструкций. При та ких оценках получают отражение важные статистические конструкторские, технологические и эксплуатационные факторы — исходные механические свойства, наличие сварных соединений и их дефектность, стационарность и случайность внешних нагрузок, степень исчерпания ресурса на данной ста дии эксплуатации, приспособляемость элементов конструкций к эксплуа тационным воздействиям. Важное практическое значение имеет сопостав ление запасов (по местным деформациям и долговечности), получаемых при детерминированных и вероятностных расчетах.
Предисловие к настоящей книге написано Н.А. Махутовым, главы 1 и 2 —В.В. Зацаринным, Н.А. Махутовым, В.А. Новиковым; глава 3 —В.В. Зацаринным, В.А. Новиковым, М.А. Даунисом, Ж.Л. Базарасом; глава 4 —
A.В. Гурьевым, А.Н. Романовым, М.М. Гадениным, В.В. Зацаринным,
B.А. Новиковым, М.А. Даунисом, Ж.Л. Базарасом; глава 5 —Ж.М. Бледновой, В.В. Зацаринным, Н.А. Махутовым, В.А. Новиковым; глава 6 — В.С. Калмуцким, Ж.М. Бледновой, глава 7 - Н.А. Махутовым, Д.А. Гохфельдом, А.Б. Злочевским, О.С. Садаковым, К.М. Кононовым, В.Е. Са вицким, В.Ф. Лукьяновым, А.Н. Романовым, В.А.Петушковым, С.Ф. Ка щенко, В.А. Новиковым, В.В. Зацаринным.
Составление и подготовка материалов книги осуществлены Н.А. Маху товым и В.В. Зацаринным.
ОСНОВНЫЕ ПОЛОЖЕНИЯ СТАТИСТИЧЕСКИХ
ИДЕТЕРМИНИРОВАННЫХ ТРАКТОВОК МАЛОЦИКЛОВОГО РАЗРУШЕНИЯ
ИВЕРОЯТНОСТНЫХ ОЦЕНОК НЕСУЩЕЙ СПОСОБНОСТИ
Разработка новых машин и конструкций с высокими эксплуатационны ми характеристиками и удельными мощностями, а также необходимость снижения их металлоемкости при одновременном повышении прочности и долговечности является актуальной и сложной задачей, особенно учитывая высокую стоимость и уникальность целого ряда машин и конструкций (корпуса и роторы паровых и газовых турбин, атомные реакторы и паро генераторы, трубопроводы, ответственные элементы сварных и разъемных соединений и т.д.).
При проектировании и изготовлении таких ответственных конструкций и агрегатов, которые изначально характеризуются случайным характером изменения эксплуатационных нагрузок, большой неоднородностью механи ческих характеристик, имеющимися технологическими дефектами (микро включения, непровары, расслоения и т.д.), рассеянием характеристик проч ности и долговечности отдельных элементов, все большее распространение получают, как показано в монографии, вероятностные методы оценки прочности, надежности и ресурса.
Основанием для таких вероятностных подходов является тот факт, что процессы накопления усталостных (циклических) повреждений, приводя щие к зарождению и последующему развитию усталостных (в том числе малоцикловых) трещин, носят случайный характер.Известно, что в усло виях много- и малоцикловой усталости даже при тщательно контролируе мых условиях проведения эксперимента на практически одинаковых об разцах, изготовленных из материала одного сертификата и нагруженных в одинаковых условиях регулярными воздействиями, результаты по долго вечностям на стадиях образования трещин и разрушения, а также по дру гим параметрам (например, параметрам диаграммы усталостной трещиностойкости) имеют значительный статистический разброс. Так коэффи циенты вариации долговечности по росту усталостных трещин оказывают ся не менее 20—50%. Это указывает на сложную вероятностную природу явления усталости.
К числу основных факторов, влияющих на рассеяние долговечности и других параметров и на случайный характер накопления усталостных пов реждений. при много- и малоцикловой усталости, можно отнести ряд конструктивных, технологических, эксплуатационных и других факторов: микроструктурная неоднородность материала (наличие микротрещин, микровключений, волосовины и т.д.), технологические дефекты сварки (газовые пузыри, неметаллические включения и т.д.), состояние и чисто та обработки поверхности (шероховатость, наклеп), незначительные откло нения размеров сечений образцов, конструктивные особенности кон-
центратора напряжений, отклонения от заданных условий испытаний, мас штабный фактор, рассеяние статических и циклических свойств, а также вариация статической и циклической трещиностойкости материалов и ряд других. Поэтому для обеспечения надежности оценок прочности, долговечности и прогнозирования ресурса циклически нагруженных конструкций исследования закономерностей возникновения и развития раз рушения (трещин) целесообразно проводить в статистической постановке.
Известно, что при эксплуатации в отдельных элементах высоконагруженных конструкций энергетического, химического, металлургического и других отраслей машиностроения, работающих в условиях малоцикловых повторных нагрузок, в зонах концентрации напряжений возникают цикли ческие упругопластические деформации, приводящие к образованию и раз витию трещин (или разрушению) при суммарном числе циклов менее 104—5* 104.
Для обоснования малоцикловой прочности и ресурса указанных элемен тов конструкций в работе [1] используется детерминированный подход, в неявном виде учитывающий рассеяние свойств основного материала и сварных соединений, параметров нагружения и ряда других факторов. При этом расчет проводится по гарантированным ТУ значениям основных меха нических свойств (ОМС) с введением запасов по местным деформациям па= = 2 и долговечностям nN = 10.
Для получения уточненных вероятностных оценок малоцикловой проч ности и долговечности по условиям образования и развития трещин требу ется разработка методов, позволяющих в первую очередь учитывать рассе яние фактических ОМС материалов, являющихся в первом приближении основными характеристиками, влияющими на рассеяние циклической проч ности и долговечности при стационарном и квазистационарном нагруже ниях. Расчеты малоцикловой прочности и долговечности по фактическим, а не по гарантированным ОМС необходимы также для оценки резерва прочности элементов конструкций, что требуется при оценке их надежнос ти в эксплуатации. Применение вероятностных методов расчета позволя ет также рассматривать вопросы продления ресурса работающих конструк ций и определять уточненные и более обоснованные значения циклических запасов на стадии проектирования.
Таким образом, применение вероятностного подхода к оценке прочнос ти, живучести и ресурса требует наличия данных о рассеянии и законах распределения характеристик нагруженности (силовых и температурных воздействий), прочности, долговечности и трещиностойкости, т.е. должно базироваться на анализе и использовании совокупности статистических ха рактеристик всех расчетных параметров, определяющих случайный харак тер процессов накопления и развития усталостных повреждений.
Вероятностные подходы к оценке статической и усталостной прочности и долговечности развиваются в течение последних нескольких десятилетий. Так, статистическая теория хрупкого разрушения, разработанная В. Вейбуллом, Я.И. Френкелем и Т.А, Конторовой, затем была распространена на устглостное разрушение. Н.Н. Афанасьевым была предложена статистичес кая теория определения предела выносливости. А. Фрейдентальи Э. Гумбель рассмотрели вопросы построения вероятностных кривых усталости. Позд нее эти вопросы обобщались в работах В.В. Болотина и цр.
В работах В.В. Болотина, И.А. Биргера, В.П. Когаева иХ.Б. Кордонского процесс накопления усталостных повреждений в материале на стадии образования и при развитии трещин рассматривался как случайный во времени.
Совершенствованию вероятностных методов расчета на усталость посвя щены работы С.В. Серенсена, В.П. Когаева, М.Н. Степнова, Р.Д. Вагапова, В.С. Стреляева; в них получены экспериментальные и расчетные оценки рассеяния характеристик прочности и долговечности с обоснованием их функций распределения. Так, В.П. Когаевым и С.В. Серенсеном пред ложена теория подобия усталостного разрушения, позволившая уста новить связь между функциями распределения предела выносливости и конструктивными факторами.
Накопленный методический опыт в области многоцикловой усталости, а также последний опыт решения задач обеспечения прочности, надежности и ресурса ответственных и уникальных машин и конструкций показывает, что вероятностная оценка несущей способности конструкций узлов и агре гатов должна проводиться на всех основных этапах их создания: при проектировании новых машин, при доводке и испытаниях, в процессе экс плуатации. При этом применяемые методы определения параметров надеж ности, их точность и значимость оказываются достаточно различными.
В настоящее время наибольшее развитие получила вероятностная оцен ка прочности и ресурса для серийных и крупносерийных парков машин с большими выборками. Уникальные машины единичного и мелкосерийного производства имеют весьма ограниченный опыт их создания с применени ем вероятностных подходов. Наиболее представительная исходная инфор мация по вероятностным подходам накапливается при проведении дово дочных испытаний изделий, число которых с изменениями конструктив ных решений достигает десятков и сотен.
Вместе с тем единой системы методологических основ расчета по веро ятностным критериям и нормативных документов пока не существует.
Так, на стадии проектирования для обеспечения возможности назначе ния заданных абсолютных значений показателей надежности деталей и уз лов конструкций необходимо широкое накопление информации в различ ных направлениях: по статистике расчетных физико-механических свойств конструкционных материалов при стандартных и не стандартных испыта ниях образцов; по устойчивости геометрических форм, допусков на гео метрические размеры, состояние поверхностей, исходных дефектов, обес печиваемых используемыми технологическими процессами; по характерис тикам рассеяния параметров термомеханической нагруженности при испы таниях и в эксплуатации; по возможностям диагностики несущей способ ности изделий на разных этапах их эксплуатации.
Накопление прямой статистической информации по указанным направле ниям в сочетании и использованием теории надежности, методов математи ческой статистики и мощных ЭВМ является основным путем решения проб лемы надежности единичных и мелкосерийных уникальных установок на
стадии проектирования.
При отсутствии необходимой исходной статистической информации для прямого решения указанной проблемы следует использовать другой под ход, основанный на определении сравнительных «вероятностных характе
ристик несущей способности. Этот подход должен базироваться на унифи цированных нормативных методах определения прочности, ресурса и жи вучести в детерминированной постановке. В пределах этих методов в рас чет должны вводиться вероятностные параметры механических свойств и нагруженности, отвечающие заданными предельным состояниям, критери ям разрушения и расчетным уравнениям. Вероятностное варьирование этих параметров по специально получаемой исходной информации должно поз волять проведение сопоставимых оценок надежности по конечным веро ятностным значениям прочности, ресурса и живучести.
На стадии доводки и испытаний при ограниченном объеме исходной ин формации, получаемой в настоящее время из доводочных испытаний, осно вой определения характеристик надежности становится теория многофак торного эксперимента сложных систем с векторной интерпретацией отка зов и повреждений и с последующим моделированием возможных отказов на базе новых перспективных методов теории надежности.
При предпусковых испытаниях и в процессе эксплуатации диагностика состояния несущих элементов должна обеспечивать получение исходной ин формации по трем основным вопросам: по развитию повреждений (дефек тов, трещин); по изменению свойств материалов; по реализованным режи мам эксплутационного нагружения. Эта информация как важнейший сос тавной элемент должна входить в вероятностные расчеты надежности для последующей эксплуатации. Опыт применения таких подходов весьма ог раничен, он только накапливается в авиации, атомной энергетике.
Из изложенного следует, что задача разработки вероятностных методов расчетов надежности и несущей способности узлов и элементов конструк ций должна ставиться и осуществляться комплексно для ipex основных стадий создания установок —при проектировании, испытаниях и эксплуа тации.
В связи со сложностью разработки вероятностных подходов к оценке долговечности, прочности и ресурса материалов и конструкции обзорно рас смотрим в данной главе основные факторы, обусловливающие рассеяние характеристик усталостных свойств на стадиях зарождения и распростра нения трещин, характер статистических распределений основных механи ческих свойств материалов и статистическую оценку параметров кривых малоциклового разрушения.
1.1.Факторы, обусловливающие рассеяние долговечности
ихарактеристик развития трещин при многоцикловой усталости
Выше был перечислен ряд основных факторов, влияющих на случайный характер накопления повреждений при циклических испытаниях —метал лургические, технологические, конструкционные, эксплуатационные и др. При этом наиболее сильное влияние они оказывают на рассеяние Характе ристик усталостного разрушения элементов конструкций. К ним относятся: случайные вариации химсостава, режимов выплавки; различия в техноло гии изготовления заготовок (ковка, штамповка, литье и т-Д.)» в терми ческой и механической обработке, в том числе наклеп и качес:Гв° обработки
поверхностного слоя; концентрация напряжений и размеры поперечного сечения; характер изменения нагрузок, коррозия и т.д.
Для материала одной плавки, при условии тщательного соблюдения тех нологии изготовления образцов и проведения испытаний, рассеяние харак теристик усталости в основном определяется статистической природой са мого процесса усталости, которая связана со структурной макро- и микро неоднородностью материала. К ней относятся: различия размеров, ориен тации и формы зерен, наличие дефектов кристаллической решетки, вклю чений, многофазность состава, микронеоднородность поверхностного слоя и т.д. Кроме того, имеются случайные вариации химического состава, ре жима термообработки и т.д., например, по самой поковке.
В литературе имеется достаточно большое количество работ по экспери ментальной оценке рассеяния долговечности при испытаниях на многоцик ловую усталость. В этих работах основное внимание уделялось выбору теоретических законов, наиболее соответствующих экспериментальным функциям распределения долговечности по моменту образования трещин или окончательному разрушению.
Для многоцикловой усталости проверка экспериментальных выборок долговечности обычно проводилась на соответствие нормальному, логнор мальному и Вейбулла законам распределения. В большинстве работ [2—10
идр.] предлагается использовать логнормальный закон.
Вряде работ [2,4, 5—8] отмечалось, что рассеяние долговечности умень шается с ростом уровня напряжений. В связи с этим можно ожидать, что при малоцикловой усталости рассеяние долговечности окажется меньше, чем при многоцикловой усталости, что впоследствии подтвердилось экспе
риментально.
Для получения устойчивых оценок случайной величины по среднему значению и дисперсии, а также функции распределения важное значение имеет количество образцов, испытанных на одном уровне. В работе [5] для испытаний при изгибе с вращением образцов из алюминиевого сплава В95 показано, что среднее значение долговечности практически неизмен но (расхождение до 0,2%) для партий образцов при п = 10 и 20-26 при достаточно высоких уровнях напряжений (атах/а_ 1 более 1,5). Для дис персии влияние количества образцов было более существенно и разница достигала 15%, Авторами предложено оптимальное количество образцов в серии брать равным 20—25.
Для получения надежной оценки функций распределения случайной величины определяются доверительные интервалы, при этом необходимо учитывать рекомендации по определению минимального количества об разцов для оценки квантиля механических свойств уровня вероятности р [4? П ]. Так, при средней точности оценки квантилей уровней 1 и 99% необходимы испытания 40 образцов, при более высокой точности - до
140образцов.
Вряде работ [2—5, 7, 12] для распределения долговечностей, соответ
ствующих нормальному закону распределения логарифма случайной ве личины х = IgN, отмечено наличие как нижнего, так и верхнего порога чувствительности по циклам N0 и Nk . В этом случае случайная величина равна* = lg[(W -Ar0)/(Nfc - А^ ) ] .
Накопленные различными исследователями экспериментальные данные и опыт их статистической обработки позволили авторам работы [И] сформулировать практические рекомендации для различных видов испы таний в статистическом аспекте. Так, для длительных испытаний (много цикловая усталость, длительная прочность) рекомендуется использовать логнормальное распределение, при низких уровнях нагружения —обрат ное нормальное распределение. Распределение Вейбулла рекомендуется применять только для обработки результатов, измерений временного соп ротивления разрыву при хрупком разрушении. При этом необходимо от метить, что графически отличить логнормальное распределение от распре деления Вейбулла достаточно трудно и для этого требуются испытания иногда тысяч образцов [13].
В работах [14—20] проведена экспериментальная оценка рассеяния долговечности и скорости развития трещин. Так, в работе [14] отмеча ется значительное рассеяние скорости развития трещин dl/dN в стали 10Ni—8Со—Шо для определенных значений размаха коэффициента ин тенсивности напряжений АК. Внутрилабораторное рассеяние dl/dN обыч но относилось как 2 к 1, межлабораторное рассеяние (15 лабораторий) — как 3 к 1.
Не был выявлен какой-либо источник, явно влияющий на рассеяние dl/dN; при этом рассматривались: геометрия образца и толщина его, способ обработки данных по длинам трещин для получения их скорости, погрешности измерения длин трещин. Полученное рассеяние скорости развития трещин авторами было отнесено на счет отличий при проведении экспериментов. Однако принимая во внимание, что микроструктура ма териала изменяется случайным образом при продвижении трещины, лег ко прийти к заключению, что распространение трещины можно рассматри вать как случайный процесс [21]. На величину рассеяния скорости трещин влияет также способ обработки пар значений 1—N [16].
В работе [22] показано, что параметры уравнения Пэриса имеют рас сеяние и подчиняются нормальному закону распределения, а также имеют между собой тесную корреляционную связь. Теоретически получено, что скорость развития трещин подчиняется логнормальному закону, а при не которых предположениях это относится и к долговечности. Позднее это было подтверждено экспериментально в работах [15,17—20].
В работе [15] для пластин конечной ширины с центральной трещиной из алюминиевого сплава 2024—ТЗ получено экспериментальное рассеяние скоростей роста трещин dl/dN и проведено определение теоретических законов, аппроксимирующих экспериментальные функции распределения чисел циклов N(1) по параметру длины трещины и скорости dl/dN (ДАТ) для определенных значений АК. Для этого определяли число циклов N, соответствующее набору одних и тех же длин трещин / (164 точки изме рения) для 68 образцов, испытанных в статистическом аспекте. В работе отмечается, что при расчете скорости роста трещин dl/dN по методу се кущих погрешность значительно меньше, чем при использовании аппрок симирующих полиномов и сам процесс развития трещйны из-за его неодно родности не может быть точно описан сглаживающими функциями. Рас пределения долговечности N(1) имели по критерию согласия лучшее соот ветствие трехпараметрическому логнормальному распределению, при этом
также проверялись нормальный, двухпараметрический логнормальный, двух- и трехпараметрический Вейбулла, трех- и четырехпараметрический Гамма законы распределения. Для распределений величины dlldN(AK) все законы ’’обеспечивали удовлетворительное, но не очень хорошее соот ветствие данным”. Расчетные скорости роста трещин dl/dN, полученные
спомощью генератора случайных чисел на основе знания параметров за кона распределения величины dl/dN(AK), совпали по средним значениям
сэкспериментальными скоростями, но имели существенно меньшее рас сеяние.
Экспериментальные исследования, проведенные в работе [17], показа ли, что распределения долговечности N(1) также соответствуют логнор мальному закону. Испытания проводились на образцах из алюминиевых сплавов Д16Т (п = 43) и АМгб (п - 62), Для сплава АМгб отмечено нали чие нижнего порога чувствительности по циклам. Коэффициент вариации v для распределений N(1) составил от 26 до 13% для длин трещин от 4 до 68 мм соответственно.
В работе [18] проведены экспериментальные статистические исследо вания скорости развития трещин малой длины (от 0,06 до 0,95 мм), воз никавших на кромке отверстий под действием нагрузки, соответство вавшей спектру нагружения Для истребителя. Поскольку точная форма каждой трещины была неизвестна, ее предполагали полуэллиптической. Экспериментальная функция распределения долговечности при длине трещины 0,95 мм удовлетворительно соответствовала логнормальному распределению при проверке по критерию согласия W. Коэффициенты вариации для скорости развития малых трещин подобны коэффициентам вариации для длинных трещин, полученным в других работах (10—50%).
В работе [19] на выборке для 100 образцов из алюминиевого сплава Д16АТ получено соответствие долговечностей N0 и Np, скорости роста тре щин dl/dN(AK) и долговечности N(1) логнормальному закону распре деления.
В работах [19, 20, 23-28] рассмотрены вопросы получения расчетной оценки рассеяния скоростей развития трещин и долговечностей. Так, в работе [19] показано, что, зная статистики параметров, например урав нения Пэриса, и связь между ними можно, выбирая их значения случай ным образом (для нормального закона распределения), получить статис тические характеристики развития трещин.
В работах [20, 24] на основе экспериментальной оценки средних зна чений и дисперсий независимых параметров (распределены по нормаль ному закону) модифицированного авторами уравнения Пэриса, методом статистического моделирования получены функции распределения дол говечности N(1). Расчетные функции N(1) соответствовали эксперимен тальным функциям (объем выборки 46 образцов), имеющим соответ ствие логнормальному закону, но отмечено, что изменение, например, только длины начальной трещины и дисперсии одного из параметров мо жет привести к отличию распределения расчетной функции от логнормаль ного закона. Особенно большое отличие наблюдалось при малых (менее 0,5 мм) начальных длинах трещин усталости.
К настоящему времени предложен ряд стохастических моделей роста трещин, рассматривающих процесс распространения трещин как случай-
ный процесс [23, 25—28]. Предложенная в работе [23] вероятностная мо дель развития трещин удовлетворительно описывает экспериментальные результаты, полученные в работах [15, 19], при этом показано, что оценки параметров модели с достаточной точностью могут быть получены на че тырех тестовых образцах.
В работе [28] представлена физическая вероятностная модель, рассмат ривающая развитие трещины как процесс последовательного разрыва или восстановления атомных связей. Получена функция распределения длины трещин в терминах времени, механической работы, температуры, энергии свободной связи.
В работах [19, 29—31] определялось экспериментальное рассеяние зна чений критического коэффициента интенсивности напряжений при стати ческом нагружении Kj . Для алюминиевых сплавов Д16Т (п = 42) и АМгб (п = 62) получены в работе [30] экспериментальные функции распределе ния величины KjС удовлетворительно соответствовали по критерию сота-
сия х 2 нормальному закону распределения; рассеяние находилось на уров не рассеяния значений предела прочности оь (коэффициент вариации v составил до 5%). В работе [19] для алюминиевого сплава Д16АТ получено соответствие экспериментальных функций распределению значений Kj логнормальному закону.
В работе [29] для экспериментальных функций распределения крити ческих температур хрупкости tk0 сталей атомного энергомашиностроения получено соответствие нормальному закону распределения. Там же приве
дены температурные зависимости вязкости разрушения Kj сталей
С
15Х2МФА и 15Х2НМФА и их сварных соединений по параметру вероят ности разрушения.
В работе [31] для 11 выборок (каждая одной плавки) для значений
Kj рельсовых сталей (п = 15-^50) получено хорошее описание трехпара-
С
метрическим распределением Вейбулла. Коэффициенты вариации значе
ний величины Кт составили от 3 до 16%.
лс
Таким образом, для статистических характеристик развития много цикловых трещин выявлены следующие закономерности: эксперименталь ные функции распределения долговечности N(1) по параметру длины трещины соответствуют логнормальному закону распределения, парамет ры уравнения Пэриса являются случайными величинами и распределены по нормальному закону, экспериментальные функции распределения ве личины KJC в основном соответствуют нормальному закону. Существую
щие расчетные способы оценки рассеяния скоростей развития трещин и долговечности основываются на экспериментальных оценках рассеяния и рассматривают распространение трещины как случайный процесс; ис пользуются методы статистического моделирования.
1.2. Статистическая оценка основных механических свойств материалов
Дня оценки долговечности и ресурса элементов оборудования в вероят ностном аспекте в качестве исходных данных, кроме характеристик сопро тивления усталостному разрушению, также используется комплекс харак теристик основных механических свойств (характеристик прочности и пластичности), полученных для различных уровней вероятности. К ним относятся такие основные механические свойства (ОМС) металлов, как предел текучести (пропорциональности) а0,02» условный предел текучес ти а0>2, предел прочности obi относительное сужение фк, истинное сопро тивление разрыву Sk и показатель упрочнения т.
Знание функций распределения основных механических свойств для эксплуатационных условий нагружения (температура, скорости деформи рования, среда и т.д.) позволяют обоснованно выбирать материалы при изготовлении конструкций на основе обеспечения требуемого уровня рас четных механических характеристик с заданной вероятностью. Кроме то го, надежная статистическая оценка значений ОМС позволяет получать их минимально гарантированные значения для принятых технологий про изводства, а также сравнивать полученные экспериментальные оценки с имеющимися значениями по ТУ.
Вводя эти характеристики в уравнения малоциклового разрушения, можно получить расчетные оценки долговечности по параметру вероятнос ти разрушения (появляются трещины).
Проведенные исследования [32] также показали, что рассеяние стати ческих характеристик оказывает также существенное влияние на рассея ние параметров циклического деформирования и может в первом прибли жении описать его расчетным путем.
Надо отметить, что использование в указанных расчетах характеристик ОМС, взятых из справочников для данного материала без учета рассеяния, может привести к существенным ошибкам (см. п. 3.1). В связи с изло женным очевидно, что для надежного прогнозирования долговечности эле ментов оборудования необходимо в первую очередь располагать досто верной статистически обработанной информацией по основным механичес ким характеристикам материалов.
Рассеяние значений ОМС, подобно усталости, определяется как неодно родностью макро-и микроструктуры материала, так и отклонениями, имею щимися при изготовлении идентичных образцов и при их испытаниях. При этом для материала различных плавок колебания факторов, опреде ляющих структуру материала для установившихся заводских технологий, обычно носят случайный характер [33]. Влияние структуры материала, качества подготовки поверхности образцов и других факторов при ста тическом растяжении менее существенно, более просты и условия про ведения эксперимента. В связи с этим рассеяние значений ОМС меньше, чем долговечности при усталостных испытаниях. Исследования в этом на правлении выполнены достаточно большим количеством авторов.
В более ранних работах [34—37] обычно использовался нормальный закон распределения ОМС. Проверка нормальности в этих работах про водилась обычно на достаточно большом количестве значений ОМС, полу
ченных в основном в заводских условиях, с использованием гистограмм, иногда показателей асимметрии и эксцесса.
В ряде более поздних работ [29, 38—42 и др.] для проверки соответ ствия экспериментальных функций распределения ОМС теоретическим законам кроме графического анализа использовались критерии согласия X2, X и со2 (см. п. 2.2). При этом расширилось количество проверяемых теоретических законов: нормальный, логнормальный, усеченный нор мальный, Вейбулла и др. В большинстве рабог [29, 38, 41, 42] получено удовлетворительное соответствие нормальному закону распределения.
В работе [39] по критерию согласия х 2 проверялись нормальный, лог нормальный и трехпараметрический Вейбулла законы распределения для значений ОМС o0t2 и оъ конструкционных сталей 3, 30, 35, 45 и 40Х. По лучено лучшее соответствие трехпараметрическому распределению Вей булла.
Поскольку существует нижний предел значений ОМС, появляющийся при их браковке по ТУ, в работе [40] предлагается использовать усечен ный слева нормальный закон распределения. Показано, что при неболь шой степени усечения (параметр усечения с менее 10%) различие средне го арифметического х и среднего квадратичного отклонения s для обо их законов незначительно (< 2%). Оценка минимального значения выбор ки при уровне вероятности Р = 0,01% по нормальному закону занижена на 5—25% по сравнению с оценкой по усеченному нормальному закону и идет в запас прочности, но это не позволяет полностью использовать в расчетах прочностные свойства стали.
Анализ экспериментальных функций распределения ОМС сталей энер гомашиностроения проводился в работах [29, 32, 37,41, 42 и др.],
В большинстве работ принят нормальный закон распределения. В рабо те [42] предлагается отдать предпочтение логнормальному закону, ввиду того что для него коэффициент вариации v был получен меньше, чем для двух других проверявшихся законов (нормального и Вейбулла).
В работах [29, 42] выполнена статистическая обработка характерис тик механических свойств основного материала и его сварных соедине ний, применяемых для корпусов аппаратов ВВЭР-440 и ВВЭР-1000, а также корпусов парогенераторов. Так, в работе [29] проводилась проверка на соответствие нормальному, логнормальному, Вейбулла и экспоненциаль ному законам распределения по критериям согласия х 2»X и со2, при этом количество значений случайной величины в выборке составляло более 50.
Для экспериментальных функций распределения ОМС сталей 22К, 10ГН2МФА (корпуса парогенераторов), 15Х2МФА и 15Х2НМФА (кор пуса ВВЭР) и их сварных соединений для нормальной и эксплуатацион ной температуры 350 °С получено лучшее соответствие нормальному рас пределению. Причем для двух последних сталей ввиду значительного отли чия поковок по габаритам и по дисперсии механических свойств для стали одной марки и категории прочности выборки были разделены на четыре группы: фланец, обечайка патрубковой зоны, обечайка и днище.
В целом можно отметить, что в большинстве работ основные механичес кие свойства довольно хорошо аппроксимируются теоретическим зако ном нормального распределения, хотя методические указания [11] пред лагают в определенных случаях регламентировать его применение (напри-
14
мер, при значении коэффициента вариации v не превосходящем 0,20). Для значений ОМС в работе [11] рекомендуется применять логнормаль ное распределение.
Далее в работе (см. п. 3.1) проведена проверка по критериям согласия X, со2 и W экспериментальных функций распределения ОМС корпусных сталей атомного машиностроения Х18Н9 и 15Х2НМФА при нормальной и эксплуатационных температурах на соответствие нормальному, лог нормальному, бейбулла и экспоненциальному законам распределения с помощью составленной программы расчета на ЭВМ (см. п. 2.2). Предва рительный графический анализ показал возможность использования двух параметрических распределений ввиду отсутствия явно выраженных поро гов чувствительности. При этом число значений случайной величины в вы борке было относительно небольшое и составляло от 30 до 80 (см. п. 3.1). Трехпараметрические распределения использовались для анализа завод ских данных ОМС (п - 137), определение нижних порогов осуществля лось графическим способом.
1.3. Статистическая оценка характеристик малоциклового разрушения
Для малоцикловой усталости в силу существенной методической слож ности имеется относительно небольшое число работ, выполненных в веро ятностной постановке [29, 42—52]. Эти работы, в основном касались воп росов экспериментальной оценки рассеяния основных механических и цик лических свойств материалов, в первую очередь долговечности по момен ту образования трещин и окончательному разрушению для условий од нородного напряженного состояния. В них также приводилось обоснова ние соответствия экспериментальных функций распределения теоретичес ким законам.
В небольшом количестве работ [41, 42, 52 и др.] приведены расчетные вероятностные оценки малоцикловой долговечности при однородном на
пряженном состоянии, полученные с учетом рассеяния |
ОМС материала |
и в ряде случаев параметров диаграмм циклического |
деформирования. |
В работах [43, 44] проведена экспериментальная статистическая оцен ка долговечности лабораторных образцов диаметром 7 и 10 мм при сим метричном жестком нагружении в условиях растяжения—сжатия, изго товленных из высокопрочных сталей НТ60 (а0>г =560 МПа, оъ = 670 МПа), НТ80 (а0>2 = 770 МПа, °ь = 840 МПа) и Нт100 (а0,2 = 1056 МПа, оь = = 1100 МПа). На каждом из уровней деформации испытывалось от 20 до 40 образцов. Анализ полученных результатов заключался в определении типа распределения долговечности при помощи графического анализа на вероятностной бумаге для нормального, логнормального и Вейбулла зако
нов распределения.
В работе [44] показано, что распределения долговечностей до образо вания микротрещин теоретически имеют форму Г-распределения, до об разования трещин N 0 - форму распределения Вейбулла и по моменту раз рушения Np - логнормальное распределение. Авторами [43, 44] по ре зультатам эксперимента принят логнормальный закон распределения дол говечностей, при этом отмечалось, что при таком относительно малом коли-
Рис. 1.1. Экспериментальные и расчетная кривые малоцикловой усталости для НТ60 1 — эксперимент, 2 —граничные точки выборки, 3 —0,0001% вероятности, 4 —раз
рушение, Npt 5 —расчетная кривая ASME, 6 —вероятность разрушения (iV0)
честве образцов его трудно отличить от распределения Вейбулла, в связи с чем логнормальный закон выбран из соображений удобства. Отмечает ся, что коэффициент вариации долговечности v для малоцикловой уста лости меньше по сравнению с коэффициентами вариации для долговеч ности, полученными при многоцикловой усталости.
|
В работе |
[43] построены также кривые малоцикловой усталости по |
|
долговечности до разрушения Np для |
различных уровней вероятности Р |
||
и |
появления |
усталостной трещины N 0 |
(рис. 1.1). Получено, что кривая |
по |
появлению усталостной трещины N 0 для Р = 0,0001% близка к двум |
кривым, составляющим соответственно 0,32 от |
долговечности N 0 и 0,58 |
от деформации еа по отношению к кривой для |
вероятности Р = 50% об |
разования трещины. Расчетная кривая малоцикловой усталости по коду ASME и кривые долговечностей N0 и Np, взятые с запасом по долговеч ности 20, находятся значительно ниже кривой 0,0001% вероятности для исследованных материалов.
В работе [45] проведена статистическая оценка долговечности Np при жестком нагружении (восемь уровней деформации) образцов из стали Х18Н10Т (объем выборки на уровне п = 60) и гибких металлических ру кавов (натурная конструкция, п = 40). Получено соответствие экспери ментальных функций распределения долговечности образцов и металлорукавов логнормальному закону распределения с нижним порогом чув ствительности по циклам. Вычисления показали равенство генеральных дисперсий и средних долговечностей материала и металлорукавов.
В работе [46] для гладких и надрезанных образцов из стали 07X16Н6
(п = 10-г 11) графически получено |
соответствие значений долговечности |
||
Np логнормальному закону распределения. |
|
|
|
На рис. 1.2, взятом из работы |
[47], показано |
рассеяние |
характерис |
тик сопротивления малоцикловой |
усталости при |
жестком |
нагружении |
Рис. 1.2. Сопротивление малоцикловой усталости трех конструкционных материалов
иих сварных соединений
а— малоуглеродистая стадо 22К, б —низколегированная сталь 15Х2МФА, в —аус тенитная сталь 08Х18НЮТ; 1‘ — основной металл, 2 —сварной шов, 3 —зона термичес
кого влияния, 4 — наплавка, 5 — среднеквадратические зависимости, 6 — границы 95% доверительного интервала
и нормальной температуре для сталей атомного энергомашиностроения 22К, 15Х2МФА и О8Х18Н10Т и их сварных соединений. На рисунке вид но, что рассеяние для сварных соединений существенно больше, чем рас сеяние для основного материала, и будет определяющим при работе эле ментов конструкций. В работе также приведены обобщающие эксперимен тальные кривые рассеяния циклической долговечности с учетом влияния эксплуатационных и технологических факторов для трех групп основных материалов — малоуглеродистых, низколегированных и аустенитных ста лей и их сварных соединений при нормальной и эксплуатационной (350 °С) температурах. Знание таких обобщенных кривых позволяет использо вать их для оценки прочности и долговечности элементов конструкций и переходить к определению кривых допускаемых напряжений. Там же приведены экспериментальные данные по сопротивлению развитию тре щин для жесткого упругопластического нагружения указанных трех групп сталей и их сварных соединений, и для каждой из групп предложены обоб щенные значения параметров уравнений типа Пэриса, записанного в вели чинах относительного размаха коэффициента интенсивности деформаций
АК1е.
В работе [48] рассмотрено влияние ряда технологических и эксплуа тационных факторов на усталостную прочность сталей 15Х2МФА и 15Х2НМФА. Отмечено, что рассеяние долговечности не превышает дву кратного от среднего значения, определенного для десяти плавок. При этом отсутствовал масштабный эффект при возникновении малоцикло вых трещин (разница в площади образцов составляла до 100 раз) для однородного и неоднородного напряженных состояний [47, 48]. В рабо тах [29, 52] приведено семейство кривых малоцикловой усталости обе их сталей по параметру вероятности разрушения Р, учитывающих внутри-
имежплавочный разброс экспериментальных данных.
Вработе [49] получено соответствие логнормальному закону для дол говечности по разрушению Np при жестком нагружении для сталей 45 и 15Х2НМФА (объем выборок п = 50 -г80), проверка проводилась по крите риям согласия х2 и X для нормального и логнормального законов рас пределения.
Таким образом, стадию возникновения усталостного повреждения в виде трещины можно определить по экспериментальным усталостным кривым, построенным по параметру вероятности разрушения (появление трещины),или с применением расчетных вероятностных кривых мало цикловой усталости. Расчетные кривые усталости могут быть построены на основе уравнений Коффина, Мэнсона, Лэнджера или их модификаций, а также по ’’Нормам расчета на прочность... ” и другим предложениям [1,42,53].
В работе [42] в условиях однородного напряженного состояния рас сматривается статистическая оценка экспериментальных и расчетных па раметров ОМС, диаграмм циклического деформирования и кривых мало цикловой усталости по моменту появления малоцикловых трещин. Резуль таты анализа экспериментальных результатов показали, что в условиях жесткого и мягкого режимов нагружений для долговечностей N 0 и Np исследуемых сталей 15Х2МФА, 45 и алюминиевого сплава Д16Т1 (объем
выборок п - 20 -г40, для стали 45 две выборки с п = 100) получено до вольно хорошее соответствие нормальному закону распределения по кри терию со2. Авторы работы [42] предлагают использовать логнормальный закон, так как он имеет меньшие значения коэффициентов вариации и, чем значения и, полученные для нормального и Вейбулла законов распре деления. Там же отмечается, что соответствие нормальному закону распре деления по критерию согласия со2 для параметров обобщенной диаграммы циклического деформирования хуже, чем для значений ОМС и долговеч ностей N 0 и Np. Для этих параметров получен существенно больший раз брос значений. Для описания параметров циклического деформирования A, A*, S T и а предлагается использовать нормальный закон, а для /3 и С — логнормальный закон распределения.
В работе [42] исследуются также корреляционные связи между значе ниями долговечности Np, параметрами циклического деформирования и значениями ОМС, полученными для одного и того же конкретного образ ца. Также приведено сопоставление экспериментальных и расчетных кри вых усталости для указанных материалов по параметру вероятности Р на основе уравнений Лэнджера, ’’Норм расчета на прочность. .. ” и других предложений (уравнения и фактический расчетно-экспериментальный материал представлен в п. 4.2).
В работе [50] на основе статистического подхода оценены критери альные уравнения Лэнджера и Мэнсона (рассмотрены результаты испы таний 41 материала — более 400 экспериментальных точек). Показана недостаточная точность этих уравнений и предложены уточненные урав нения кривой малоцикловой усталости и кривой циклического дефор мирования.
В работе [51] с целью определения констант критериального урав нения зависимости e -N p и уравнения кривой циклического деформи рования проведены испытания при жестком нагружении десяти марок чешских конструкционных сталей, каждая из нескольких плавок. На де сяти уровнях деформаций испытывалось в среднем по 50 образцов. Экс периментальные результаты рассматривались как единая статистическая совокупность, для которой получены уравнения кривых 5 и 95% вероят ности разрушения для зависимости e—Np и уравнения циклического дефор мирования. Представленные для двух уровней деформаций распределе ния амплитуды напряжения и долговечности Np подчинялись логнормаль ному закону распределения.
В целом можно отметить, что рассеяние долговечности при малоцикло вом нагружении меньше, чем для условий многоцикловой усталости.
Большинство работ, Выполненных по малоцикловой усталости в статис тическом аспекте, посвящено экспериментальной оценке функций распре деления долговечности. Для них в основном получено соответствие лог нормальному закону распределения. В работе [51] оценено рассеяние ди аграмм циклического деформирования, а в [42] - рассеяние их парамет ров. В работах [41, 42, 52] проведена расчетная оценка рассеяния долго вечности при однородном напряженном состоянии с введением в крите риальные уравнения рассеяний ОМС материала.
1.Нормы расчета на прочность элементов реакторов, парогенераторов, сосудов и трубопроводов атомных электростанций, машин и исследовательских ядерных реакторов и установок. М.: Металлургия, 1973. 408 с.
2.Степнова М.Н., Гиацинтов Е.В. Усталость легких конструкционных сплавов. Ма машино строение, 1973. 317 с.
3.Серенсен С.В.,. Степнов М.Н., Когаев В.П., Гиацинте Е.В. Исследование харак теристик выносливости конструкционных алюминиевых сплавов в связи с тех нологией их производства // Тр. МАТИ. 1958. ВБш. 35. 124 с.
4.Степнов1 М.Н. Статистические методы обработки результатов механических ис пытаний: Справочник. М.: Машиностроение, 1985. 231 с.
5.Серенсен С.В., Степнов М.Н., Когаев В.П., Гиацинте Е.В. Устойчивость функций распределения долговечности при испытании на усталость алюминиевых сплавов //
Вопросы сопротивления материалов: Тр. МАТИ. 1959. Вып. 37. С. 69-84.
в. Гиацинте Е.В., Степнова М.Н., Когаев В.П. Усталостные свойства алюминиевого сплава, применяемого для лопастей вертолетов // Исследования усталости и дли тельной статической прочности алюминиевых сплавов: Там же. 1961. Вып. 51.
С. 39-66.
7.Степнов М.Н. Линейный регрессионный анализ результатов усталостных испы таний // Конструкционная прочность легких сплавов и сталей: Там же. 1964. Вып. 61. С. 19—25.
8. |
Когаев В.П., |
Ванды шее В.П., |
Петрова И.М. Накопление усталостных поврежде |
||
|
ний |
и вероятностные методы |
расчета деталей машин на усталость при варьируе |
||
|
мых |
амплитудах |
напряжений // Прочность материалов и конструкций. Киев: |
||
|
Наук, думка, 1975. С. 26-33. |
|
|||
9. |
Freudenthal |
А.М., |
Gumbel E J. Distributions functions for predictions of fatigue life |
||
|
and fatigue strength // Intern. Conf. Fatigue Metals. L., 1956. P. 262-271. |
||||
10. |
Bastenire F. A study of scatter of fatigue test result by statistical and physical methods |
||||
|
// Fatigue of |
aircraft structure |
/ Ed. W. Barrois, E.L. Ripley. Pergamon press. 1963. |
P.53 -85 .
11.РД-50-398-83. Методические указания. Планирование механических испытаний
и статистическая обработка результатов. М.: Изд-во стандартов, 1984. 199 с.
12.Бородин Н.А., Степанов М.Н. О законе распределения предела длительной проч ности // Завод, лаб. 1970. № 3. С. 338-340.
13.Вейбулл В.А. Усталостные испытания и анализ их результатов. М.: Машинострое ние, 1964. 276 с.
14.Glark W.Gr. (Jr.), Hudak S.J. (Jr.). Variability in fatigue crack growth testing // J. Test, and Eval. 1975. Vol. 3, N 6. P. 454-476.
15.Вирклер, Хилбэри, Гоэл. Статистический характер процесса развития усталост ной трещины // Теоретические основы инженерных расчетов. М.: Мир, 1979. Т. 101, № 2. С. 46-52.
16.Betancourt Т.К., Mattews J.R. Effects of the average increment ДС on the scatter in
da/dN data and mean life cycles in HY-80 steel plate // J. Test, and Eval. 1987. Vol. 15,
N l.P . 20-29.
17.Нешпор Г.С., Армягов A.A. О распределении долговечности при испытании образ цов с усталостной трещиной // Завод, лаб. 1984. № 8. С. 70-73.
18.Hovey P.W., Gallgher J.P., Berens A.P. Estimating the statistical properties of crack growth for small cracks // Eng. Fract. Mech. 1983. Vol. 18, N 2. P. 285-294.
19.Пуш E.A. Исследование закономерностей развития усталостных трещин в листо вом металле Д16АТ в вероятностном аспекте: Автореф. дис. . . . канд. техн. наук. М., 1981. 25 с.
20.Степнов М.Н., Maxyme Н.А., Серегин А.С., Лисин А.Н. Статистические закономер ности начального развития усталостных трещин // Физ.-хим. механика материалов. 1982. №3. С. 70-74.
21.Бородачев Н.М. О характере случайного процесса распространения усталостных трещин // Пробл. прочности. 1980. № 8. С. 49-51.
22.Хазанов И.И., Полите В А . Вероятностная модель усталостной долговечности
в свете представлений линейной механики разрушения // Там же. 1977. № 2. С 10 - 15.
23.Когаев В.П., Лебединский С.Г. Вероятностная модель процесса развития усталост ной трещины // Машиноведение. 1983. № 4. С. 78-83.
24.Степнов М.Н., Махутов Н.А., Серегин А.С., Лисин А.Н. Расчет функций распреде ления долговечности элементов конструкций с трещинами // Физ.-хим. механика материалов. 1983. № 1. С. 74—77.
25. Kozin F., Bogdanoff J.L. On the probabolistic modeling of fatigue crack growth // Eng. Fract. Mech. 1983. VoL 18, N 3. P. 623-632.
26. Lin Y.K., Yang J.N. On statistical moments of fatigue crack propagation 11 Ibid. N 2
P. 243-256.
27.Ditlevsen O., OlesenR. Statistical analyses of the Virkler data on fatigue crack growth // Ibid. 1986. Vol. 25, N 2. P. 177-195.
28. Krausz A.S. The random walk theory of crack propagation // Ibid. 1979. Vol. 12, N 4.
P. 499-504.
29.Тимофеев Б .Т., Жеребенков A.C., Чернаенко T.A. Статистический подход к оценке качества и свойств сварных соединений. Л.: ЛДНТП, 1982. 23 с.
30.Нешпор Г.С., Армягов А*А. О законе рассеяния характеристик вязкости разруше ния и остаточной прочности в условиях плоского напряженного состояния // За вод. лаб. 1984. № 9. С. 70-74.
31.Тот Л., Ромвари Я., Надь Д. К вопросу применения статистических методов в ме ханике разрушения с учетом воспроизводимости результатов определения харак теристик сопротивления материалов разрушению // Пробл. прочности. 1983. №11. С. 54-59.
32.Механика малоциклового разрушения // Под ред. Н.А. Махутова, А.Н. Романо ва. М.: Наука, 1986. 264 с.
33.Меандров Л.В., Семенов Ю.Н., Перепелкин В.П. Статистический контроль метал лопроката по механическим свойствам // Завод, лаб. 1977. № 10. С. 1286-1289.
34.Кузнецов А.А., Алифанов О.М., Ветров В.И. и др. Вероятностные характеристики прочности авиационных материалов и размеров сортамента: Справочник. М.: Ма шиностроение, 1970. 568 с.
35.Осминин Э.Л., Шаталин Н.В., Жуков А.Ф., Крылов С.М. Статистический контроль механических свойств трубной заготовки // Завод, лаб. 1977. № 9. С. 1147-1148.
36.Сосновский Л.А. Статистический критерий качества материалов и методика его определения // Там же. 1973. № 12. С. 1508-1514.
37.Егоров М.Ф., Люцко Е.А. Несущая способность металлов, применяемых в изде лиях энергомашиностроения, и ее использование для оценки надежности // Тр. ЦКТИ. 1976. № 138. С. 45-49.
38.Папазова Т.М., Папазов В.В., Гудимчук В.И. Закономерности рассеивания проч ности конструкционных сталей // Вести, машиностроения. 1977. № 6. С. 40-42.
39.Беленький Д.М., Элькин А.И., Русаков А.В. Исследование распределения механи
ческих свойств и связи между ними // Пробл. прочности. 1977. № 12. С. 93-96.
40.Сосновский Л.А. О распределении характеристик механических свойств и долго вечности стали II Там же. № 5. С. 86-89.
41.Шрон Р.З., Щапова В.В. Статистический анализ распределения механических свой ств стали марок 22К и 16ГНМ в барабанах котлов высокого давления // Энерго
машиностроение. 1981. № 1. С. 35—38.
42.Базарас Ж.Л. Статистическая оценка сопротивления деформированию и разруше нию при малоцикловом нагружении: Автореф. дис. . . . канд. техн. наук. Каунас,
1983.21.
43.Iida К., Inoue Н. Life distribution and design curve in low cycle fatigue. Tokyo, 1973. 39 p. (Pap. Ship Res. Inst.; N 45).
44.Udoguchi T., Matsumura M. Statistical investigation on low cycle fatigue life of high tension steel // Proc. Intern. Conf. Mech. Behav. Materials. Kyoto, 1971. Vol. 5. P. 458470.
45.Гусенков А.П., Лукин Б.Ю. Прочность при малоцикловом нагружении гибких ме таллических рукавов II Пробл. прочности. 1972. № 1. С. 98—104.
46.Байков В.П., Мальцев В.Г., Миронов В.И. Исследование малоцикловой усталости
стали 07Х16Н6 // Там же. 1978. № 7. С. 23-24.
47.Карзов Г.П., Леонов В.П., Тимофеев Б.Т. Сварные сосуды высокого давления.
Л.: Машиностроение, 1982. 287 с.
48.Горынин И.В., Игнатова В А ., Тимофеев Б.Т., Федорова В.А. Влияние технологи ческих и эксплуатационных факторов на усталостную прочность сталей марок 15Х2МФАи 15Х2НМФА// Пробл. прочности. 1984. № 9. С. 3 -9.
49.Кочетов В.Т., Карзов Г.П., Тимофеев Б.Т., Тюнин А.А. Исследование закона рас пределения дисперсии свойств материалов при испытаниях на малоцикловую ус талость// Там же: 1978. № 11. С. 29-33.
50.Трухний А.Д., Степанов А.Д. Статистический анализ кривых малоцикловой уста лости // Машиноведение. 1978. № 4. С. 82-88.
51.Кучева Я., Толпа И., Бразда Г. Сопротивление малоцикловой усталости некоторых свариваемых конструкционных сталей // Завод, лаб. 1984. № 8. С. 79-82.
52.Звездин Ю.А., Тимофеев Б.Т., Федорова ВА ., Чернаенко Т А . Вероятностно-статио тический подход к оценке долговечности сварных узлов энергетического обору дования // Тез. докл. Всесоюз, науч.-техн. симпоз. с участием специалистов стран -
членов СЭВ (Владимир, 18-20 нояб. 1986 г.). М.: ЦП НТО Машпром, 1986. С. 7 1 - 75.
53.Прочность при малоцикловом нагружении / Под ред. С.В. Серенсена. М.: Наука, 1973. 285 с.
Г л а в а 2
МЕТОДЫ И СРЕДСТВА ИССЛЕДОВАНИЙ СОПРОТИВЛЕНИЯ МАЛОЦИКЛОВОМУ РАЗРУШЕНИЮ В СТАТИСТИЧЕСКОЙ ПОСТАНОВКЕ
2.1. Методика и аппаратура для малоцикловых испытаний в условиях нормальной и повышенной температур
Вероятностный подход к расчетно-экспериментальной оценке малоцик ловой прочности и долговечности в зонах концентрации напряжений осно вывается на разработанной методике базовых статистических малоцикло вых испытаний; статистическом анализе закономерностей образования и развития трещин в образцах с концентратором; статистическом анализе основных механических свойств (ОМС) материала с целью обоснования исходных для расчета характеристик с заданной вероятностью [1].
Для расчетной оценки рассеяния малоцикловой прочности и долговеч ности, основанной на детерминированных деформационных подходах, необходима также оценка параметров диаграмм циклического деформиро вания. Их значения определяют по результатам испытаний при однородном напряженном состоянии на гладких образцах. Представленная методика предусматривает, кроме экспериментального, также расчетное (через рас сеяние ОМС) определение параметров А, В, С, а и ft диаграмм циклическо го деформирования (см. п. 3.2).
Экспериментальная оценка рассеяния сопротивления статистическому разрушению гладких образцов и малоцикловому разрушению в зонах кон центрации напряжений проведена на двух различных по своим циклическим свойствам материалах — стабилизирующейся (упрочняющейся) стали Х18Н9 и разупрочняющейся стали 15Х2НМФА при нормальной и повышен ных (эксплуатационных) температурах 650 и 350° С соответственно.
В результате проведения испытаний при нормальных и повышенных температурах получены следующие экспериментальные рассеяния: основ ных механических свойств, долговечности по моменту появления трещин
идолговечностей, соответствующих определенным длинам, раскрытиям
искоростям развития трещин в зонах концентрации напряжений. Также были получены распределения длин, раскрытий и скоростей роста трещин по параметру долговечности и распределения скоростей роста трещин по параметру размаха коэффициента интенсивности напряжений АК.
Для статистических малоцикловых испытаний при неоднородном напря женном состоянии использовался [1] плоский образец с концентратором в виде отверстия (диаметр отверстия —7 мм, толщина образца — 6 мм,
ширина - 24 мм), теоретический коэффициент концентрации |
= 2,4 |
(рис. 2.1).
Испытания при комнатной температуре проведены на электрогидравлической установке МТС с предельным усилием 500 кН в диапазоне частот
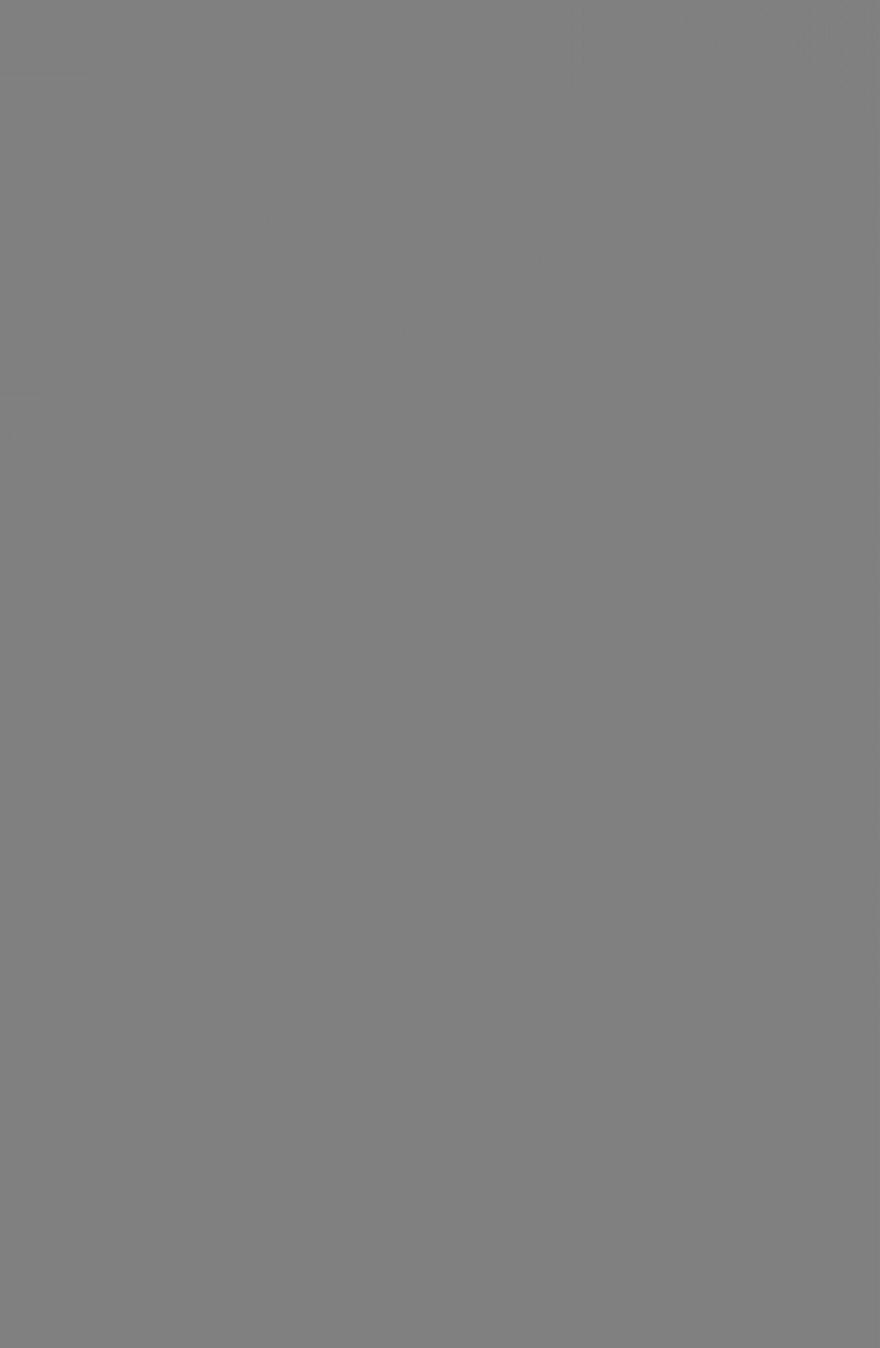
таний, при этом значения ОМС и кривые малоцикловой усталости для стали 15Х2НМФА при 350° С и для стали Х18Н9 при 650° С были получены на корсетных образцах на установке типа УМЭ-10 ТП [4]. Нагрев образцов осуществлялся пропусканием через них электрического тока.
В соответствии с используемыми для описания скоростей развития тре щин критериями линейной и нелинейной механики разрушения в экспе риментах на образцах с концентратором измерялись следующие характе ристики [5, 6]: текущая длина трещины /, перемещение берегов трещины (раскрытие) 6 в устье и на расстоянии 0,3 мм от ее вершины (Х18Н9) или непосредственно в вершине трещины (15Х2НМФА) на различных пяти ступенях нагружения в цикле —в исходном состоянии перед нагружением, при максимальных растягивающей и сжимающей нагрузках, а также при нулевой нагрузке в точках разгрузки после полуциклов растяжения и сжа тия. Используемое в дальнейшем в качестве одной из характеристик разви тия трещин амплитудное раскрытие в устье трещины 6fl определялось как разность между величинами раскрытия в устье под действием макси мальной растягивающей нагрузки и раскрытия в исходном состоянии перед началом нагружения в цикле. При записи петли гистерезиса на двухкоорди натном самописце фиксировались размахи номинального напряжения Аоп и номинальной упругопластической деформации Аеп. Моменты записи диа грамм деформирования совпадали с изменением величин / и 5.
Измерение длин и раскрытий трещин проводили оптическим способом на микроскопе типа МГ при увеличении от 55 до 120 раз (см. рис. 2.1; 2.2) только с одной стороны образца, для удобства слежения за трещинами рабочую поверхность образцов полировали. Длину трещины измеряли в полуцикле нагружения при максимальной нагрузке (с целью исключения ползучести материала во время измерений трещины нагрузка несколько снижалась —для стали Х18Н9 она составляла примерно 90% максимальной нагрузки). На одном образце в соответствии с [7] проводили не менее 15 измерений длины данной магистральной трещины и ее раскрытий.
Нагрев плоских образцов с отверстием осуществлялся при помощи компактной навесной печи с излучающими кварцевыми лампами (рис. 2.3). Печь двухсекционная, по две лампы в секции, с независимым тиристорным регулятором температуры для каждой секции. При установке секции сдви гаются по высоте до расстояния, примерно равного диаметру отверстия, и зона отверстия прогревается за счет теплопроводности. Неоднородность поля температур в зоне отверстия, где появляются трещины, не превышала ±1,5% от температуры испытаний.
На рис. 2.4 в качестве примера показано полученное по результатам измерений поле длин всех трещин, появившихся на поверхности 18 плос ких образцов из стали Х18Н9 при нормальной температуре для серии испы таний с долговечностью примерно 1000 циклов. Видно, что рост части тре щин останавливался, достигая длин 0,1—0,3 мм (штриховые линии) при одновременном выделении рядом с ними магистральных^трещин (сплош ные линии). Имея экспериментальные поля, подобные полю длин трещин /, также для амплитудных раскрытий в устье трещины 5fl и скоростей разви тия трещин dljdN графическим способом (проводя ряд горизонтальных сечений поля) получали экспериментальные функции распределения долго вечностей N по параметрам /, 8а и dljdN для всех серий испытаний сталей
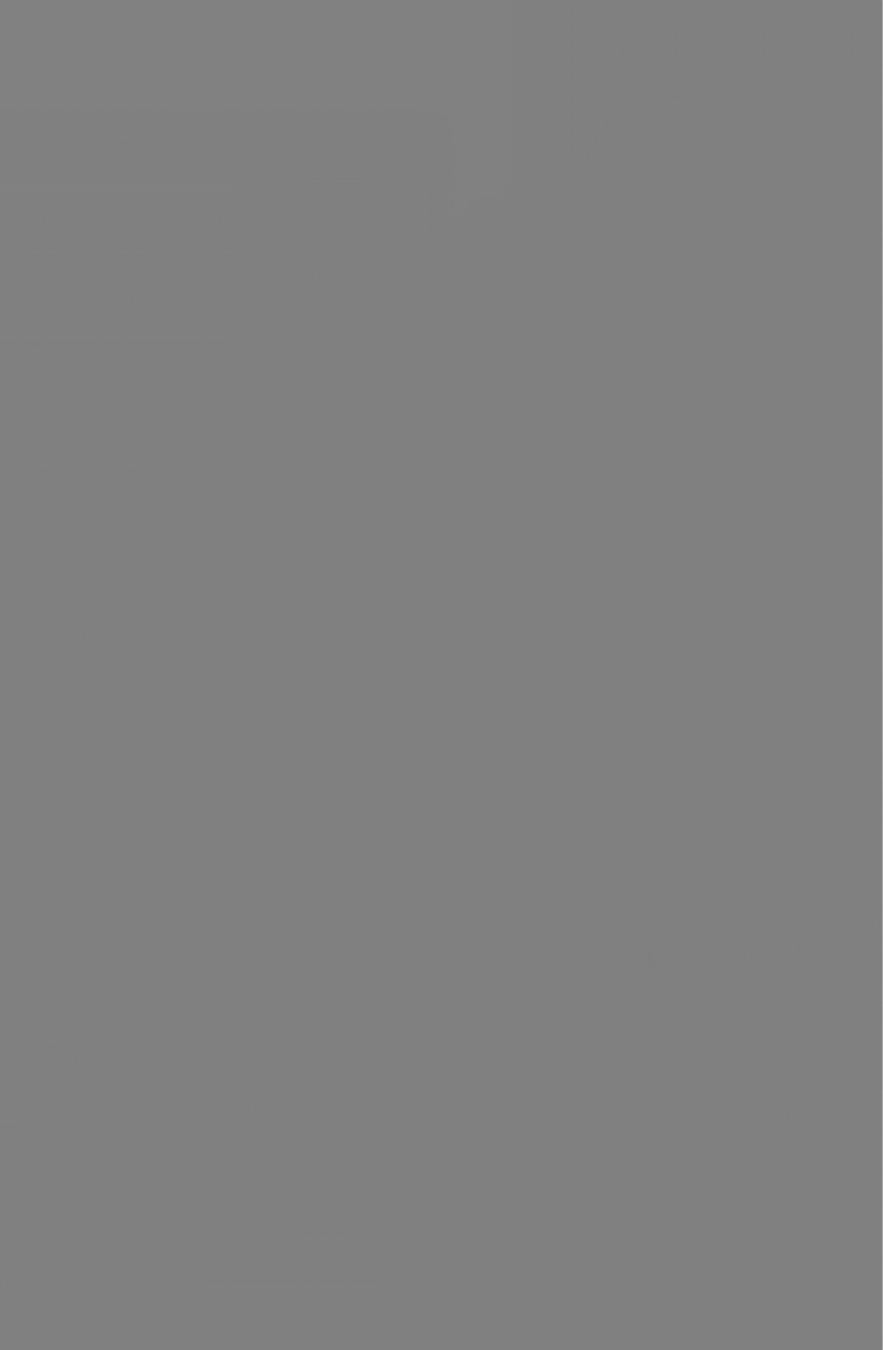
200 |
000 |
000 |
000 |
/000 |
/200 |
/000 /V |
Рис. 2.4. Экспериментальное поле длин трещин для стали Х18Н9 при нормальной тем пературе, уровень напряжений ап - 285 МПа
Х18Н9и 15Х2НМФА при нормальной и повышенных температурах. Рас пределения длин, раскрытий и скоростей роста трещин для определенной долговечности N получали, проведя ряд вертикальных сечений соответ ствующего поля.
Значения скоростей развития трещин (СРТ) получали графическим диф ференцированием лекальных кривых длин трещин для нескольких образ цов данного уровня напряжений. Затем для этих же образцов рассчитывали СРТ на ЭВМ типа СМ-4 (Фортран-IV) с помощью программы [8], исполь зующей сплайн-функции. При этом осуществлялся подбор параметров сглаживания сплайна для получения результатов, сопоставимых с резуль татами графического дифференцирования. В дальнейшем СРТ для осталь ных образцов данного уровня напряжений рассчитывалось на ЭВМ и в виде поля СРТ наносилось на графопостроителе. Аналогично с использованием той же программы аппроксимации экспериментальных данных сплайнфункциями графически строились поля длин и амплитудных раскрытий трещин в устье.
Экспериментальные функции распределения скорости роста трещин по параметру ДАТ строили по значениям скоростей, определенных методом секущих и попавших в относительно узкий интервал значений ДАТ.
Надо отметить, что на величину рассеяния скорости трещин влияет
способ обработки значений 1—N. Аппроксимация сглаживающими полино мами сужает полосу рассеяния скорости по сравнению с методом секу щих, и сам процесс развития трещин из-за его случайного характера не может быть точно описан сглаживающими функциями [9]. В упомянутой работе определялось число циклов, соответствующее набору одних и тех же длин трещин (160 точек измерения для каждого из 68 образцов, испытан ных в статистическом аспекте), и, таким образом, необходимость в по строении полей длин и скоростей трещин отпадает. Для данного случая об разцов с отверстием, когда место зарождения и направление развития тре щин четко не определены, такой способ является неприемлемым.
При использовании метода секущих рассеяние скорости зависит от величины приращения длины трещины А/ (интервала замеров значений 1—N ). Если величина А/ будет меньше, то полоса рассеяния скорости мо жет быть существенно больше, в этом случае несколько отличаться могут и средние значения скорости [10].
2.2. Методика статистической обработки экспериментальных данных
Методика статистической обработки результатов испытаний включает в себя определение предпочтительных теоретических законов и оценку их параметров для экспериментальных функций распределения ОМС мате риала и долговечности по параметру длин, раскрытий, скоростей роста тре щин, а также для ряда других полученных распределений. Это необходимо для получения значений ОМС заданного уровня вероятности и для сравне ния экспериментальных и расчетных рассеяний характеристик малоцикло вого разрушения [1].
Проверка гипотез' о виде функций распределения предварительно осу ществлялась с помощью графического метода, который заключается в нанесении значений случайной величины на вероятностную бумагу соот ветствующего теоретического закона распределения. Если эксперимен тальные точки ложатся близко и случайным образом вокруг аппроксими рующей прямой, проведенной для данного теоретического закона распре деления, то соответствующая гипотеза принимается [11, 12].
Составленные для ЭВМ типа СМ-4 графические программы позволили проводить графический анализ для нормального, логнормального, двух параметрических Вейбулла и экспоненциального законов распределений. Вначале составляется вариационный ряд из значений случайной величины:
*1 < |
Х2 < |
< * / < . < Х п_ г <Хп. |
(2.1) |
Затем для каждого члена ряда вычисляется накопленная частость |
|
||
Р(х{) |
= (/ - |
0,5)/п. |
(2.2) |
Программы обеспечивают прорисовку вероятностных сеток теорети ческих законов, нанесение на график значений случайной величины, рас четную оценку параметров теоретических законов по экспериментальной выборке и проведение аппроксимирующих прямых.
Оценка параметров указанных теоретических законов проводилась по известным формулам [11—13]. Для нормального и логнормального зако
нов значения теоретической функции распределения у - F(x) и обратной
функции х = F~l (y) |
определялисьпри помощи подпрограмм NDTR и |
NDRI соответственно |
[14]. |
Для распределения Вейбулла значений теоретической функции распре
деления F(x) равно |
|
F(Xj) = 1 - exp [-(Xj/b)c ], х > 0 , |
(2.3) |
где параметры Ъи с определялись из уравнений [15] |
|
|
(2.4) |
(2.5)
Здесь параметр с* определялся из (2.4) методом последовательных при ближений.
Для экспоненциального распределения [13] |
|
|
F(Xj) = 1 —exp [—\(Xf —в)], |
х > 0, |
(2.6) |
где |
|
|
в —Xmjn —(X —*minA0 И |
X - 1/ (X —0). |
|
После предварительного графического анализа по критериям согласия проводилась дальнейшая проверка гипотез о виде экспериментальных функций распределения. Порядок применения критериев согласия Пирсо
на х2 (и ^ |
ЮО), Колмогорова—Смирнова X |
(п > 100), Крамера—Мизеса |
со2 (п > |
50) и Шапиро—Уилка W (п < 50) |
определен в работах [11—13, |
16, 17]. Ввиду относительно малого количества значений случайной вели чины (обычно 15 < п < 50) критерий х2 в данном случае не использовал ся. В то же время в [18] указывается на возможность использования кри териев X и со2 при п > 10-^30.
Критерии согласия X и со2 используются для проверки гипотезы о со ответствии эмпирического распределения любому теоретическому рас пределению, но с заранее известными параметрами. При оценке параметров по данным самой выборки, что и имеет место в данном случае, критерии согласия X и со2 могут быть использованы для проверки на соответствие только нормальному, логнормальному и экспоненциальному теоретичес ким законам [11—13, 16]. Там же приведены критические значения ста тистик Ха и соа для указанных законов.
Критерий W является более мощным, чем соответствующие по степени убывания мощности критерия GJ2 и X, т.е. имеет меньшую вероятность принятия ложной гипотезы [17].
Критерий Колмогорова—Смирнова X основан на определении максималь ного отклонения накопленной частости от значения функции распределения
[11-13, 16]: |
|
Г |
/ - 1 |
|
D„ = |
/ |
- F(X/)], |
||
max [- |
D„ = шах |
F(x{) -------- |
||
|
n |
|
I |
n |
D„ = |
шах [Dn\ |
AT ]• |
|
(2.7) |
29
Если параметры гипотетической функции распределения заранее не известны и оцениваются по самой выборке, то для нормального или лог нормального закона
/ _ |
0,85 \ |
= $(*/)> |
(2.8) |
A i( /» - 0 ,0 1 + |
J <к, |
где Zf = (хj - X )/Sn- i , а Ф(г/) —значения функции Лапласа.
Критерий со2 определяется взвешенной суммой квадратов разностей эмпирической и теоретической функций распределения [11]:
|
оо |
|
|
со2 =п |
f [Р(х) - Fix)]2 д а * ) ] dF(x), |
(2.9) |
|
где Р(х) |
—накопленная частость P(xt ) = (/ —0,5)/л; |
F(x) —теоретичес |
|
кая функция распределения; ф [F(x)] —весовая функция. Если ф [F(x)] |
= |
||
= 1, то статистику со2 называют статистикой Смирнова, а если i//[F(дс)] |
= |
||
= ll\F(x) |
[1 —F(x)]} —статистикой Андерсона-Дарлинга. Если параметры |
гипотетической функции заранее не известны и оцениваются по выборке, то для нормального или логнормального распределения статистика Смир
нова определяется по формуле |
[11—13, 16] |
|
||
1 |
п |
[/>(*,) - |
2 |
(2.10) |
псо2 |
+ 2 |
Ф(*,)] |
||
12/2 |
i = |
1 |
|
|
Если /2со211 + — 1 < F a, то нулевая гипотеза не отбрасывается. Статис-
\2/2/
тика Андерсона—Дарлинга применяется в случаях, когда интересуются со ответствием эмпирической функции распределения теоретической в об ласти крайних значений случайной величины (на ’’хвостах” распределения). Для нормального или логнормального закона она имеет вид
гио2 = -п |
— 2 |
2 |
{P(xf) In Ф(*/) |
+ [1 —F(*/)] |
In [1 —Ф(2/)] j . |
(2.11) |
|||
|
/= |
i |
|
|
|
|
|
|
|
( 2 |
0,7 W |
3,6 |
8,0 \ |
|
|
||||
Если l nco |
—— |
/ |
111 + — |
———I < A a, то нулевая гипотеза не отбра- |
|||||
\ |
п |
\ |
п |
|
гг I |
|
|
||
сывается. |
|
|
|
|
|
|
|
|
|
Критерий Шапиро—Уилка W [И , 12, 17] предназначен для проверки |
|||||||||
гипотезы о нормальном или логнормальном распределении |
|
||||||||
W = b2/S 2, |
|
|
|
|
|
|
|
(2.12) |
|
где S 2 = |
2 (xt |
- X ) 2 и |
Ъ= |
2 |
а„_/+ |
- * ,)• |
|
||
i = i |
|
|
|
|
i = |
1 |
|
|
Значения an _ t + х берут из таблиц, и если W > Wa, то нулевая гипотеза не отбрасывается. Приближенная вероятность того, что выборка взята из нормально или логнормально распределенной совокупности, определяется по формуле [17]
( W - e |
(2.13) |
z = 7 + 77 In I -------- |
|
\ 1 - W |
|
где у у rine определяются из таблиц для соответствующего объема выборки. Программа, реализованная на ЭВМ типа СМ-4 (Фортран-IV), позволила проводить проверку гипотез о виде экспериментальных функций распреде ления ОМС сталей и значений долговечности по параметрам длин, раскры тий, скоростей роста трещин и других распределений по трем критериям согласия: Колмогорова—Смирнова X, Крамера—Мизеса со2 и Шапиро—Уил ка W. Вначале экспериментальные значения располагались в вариационный ряд, затем осуществлялись: проверка выборки на однородность по крите рию Смирнова для отбрасывания резко выделяющихся результатов [11—13], вычисление значений параметров выбранных распределений, по казателей асимметрии и эксцесса, а затем проверка по критериям согла сия на соответствие указанным четырем законам распределения. Так, по критериям согласия X, со2 и W определялись величины статистик для нор мального, логнормального и экспоненциального законов распределений. Для критерия со2 проводилось также вычисление статистик Смирнова и
Андерсона—Дарлинга.
Полученные величины статистик позволяют путем сравнения со своими критическими значениями установить соответствие нормальному, лог нормальному и экспоненциальному законам распределения и выбрать более предпочтительный из них.
Использовалась также методика, позволяющая выбрать более соответ ствующий экспериментальной выборке теоретический закон —двухпара метрическое распределение Вейбулла или логнормальное распределение. Для этого определялось отношение максимального правдоподобия и срав нивалось с критическим значением [19]
(RMLУ'" |
=(27raS2)i/2[ П |
|
xif wXxi\ b , \c*)]l ln, |
(2.14) |
|||
где |
|
i = 1 |
' |
|
|
|
|
п |
|
|
|
1 |
п |
|
|
1 |
------ |
------ |
|
||||
Sj, = - |
2 |
( ln x i - ln * ) 2, |
|
1пХ= |
- |
2 Inx, |
|
П |
i= 1 |
|
|
П |
t= 1 |
|
|
fw,{xt, |
b*;c*) = c’ ixt/b*)0* - 1 |
|
exp [-*</** ]c* |
|
|||
|
|
|
|
b |
|
|
|
Логнормальное распределение отклонялось и ему предпочиталось рас пределение Вейбулла, если (RML)lln > (RML)l^n , где критическое значе ние определялось из таблиц. Из них следует, что при уровне значимости ос = 0,1 требуется, как минимум, 35 значений случайной величины в выбор ке, чтобы сделать выбор между распределениями при мощности, равной 0,8; при а = 0,05 мощность составляет ~0,7. Для 10 < п < 20 выбрать более подходящее распределение практически уже невозможно [19, 20].
Проверка экспериментальных выборок по различным критериям согла сия X, со2 и W давала обычно сходные результаты и позволяла уточнять первоначальные более грубые оценки, сделанные графическим методом.
Графический и расчетный анализ (статистики и рассчитанные величины критериев) представлены в п. 3.1 и 5.2.
Таким образом, представленные в п. 2.1 и 2.2 методики позволяют полу чить оценку рассеяния основных механических свойств материалов и ха рактеристик образования и развития трещин малоцикловой усталости с одновременным обоснованием соответствия экспериментальных функ ций распределений теоретическим законам.
ЛИ Т Е Р А Т У Р А
1.Махутов Н А ., Зацаринный В.В., Новиков ВА . Исследование возникновения и распространения трещин малоцикловой усталости в зонах концентрации напряже ний в статистическом аспекте // Завод, лаб. 1983. № 4. С. 68-73.
2.Гусенков А.П., Зацаринный В.В. Программная установка для малоцикловых
испытаний с выдержками при повышенной температуре // Там же. 1972. № 3.
С.355-357. .
3.Серенсен С.В., Степнов М.Н., Когаев В.П., Гиацинтов Е.В. Устойчивость функций распределения долговечности при испытании на усталость алюминиевых сплавов // Вопросы сопротивления материалов: Тр. МАТИ. 1959. Вып. 37. С. 69-84.
4.Гусенков А.П., Зацаринный В.В. Установка для исследования прочности при мало цикловом нагружении в условиях повышенных температур // Завод, лаб. 1970.
№5. С. 606-609.
5.Прочность при малоцикловом нагружении / Под ред. С.В. Серенсена. М.: Наука,
1975. 285 с.
6.Романов А.Н., Махутов Н А . Исследование развития трещин при высокотемпе ратурном однократном и малоцикловом нагружении // Завод.лаб. 1978. № 1.
С. 85-91.
7.РД-50-345-82. Расчеты и испытания на прочность. Методы механических испытаний металлов. Определение характеристик трещиностойкости (вязкости разрушения) при циклическом нагружении. М.: Изд-во стандартов, 1983. 96 с.
8.Поля деформаций при малоцикловом нагружении / Под ред. С.В. Серенсена. М.: Наука, 1979. 277 с.
9.Вирклер, Хилбэри, Гоэл. Статистический характер процесса развития усталост ной трещины II Теоретические основы инженерных расчетов. М.: Мир, 1979. Т. 101, № 2. С. 46-52.
10.Betancourt Т.К., Mattews J.R. Effects of the average increment AC on the scatter in
da/dN data and mean life cycles in HY-80 steel plate // J. Test, and Eval. 1987. Vol. 15,
N l.P . 20-29.
11.Степное M.H. Статистические методы обработки результатов механических испы таний: Справочник. М.: Машиностроение, 1985. 231 с.
12.РД-50-398-83. Методические указания. Планирование механических испытаний и статистическая обработка результатов. М.: Изд-во стандартов, 1984. 199 с.
13.Айвазян С.А., Енюков И.С., Мешалкин Л.Д. Прикладная статистика. Основы моделирования и первичная обработка данных: Справ, изд. М:‘ Финансы и ста тистика, 1983. 472 с.
14.Сборник научных программ на Фортране. М.: Статистика, 1974. Вып. 1. 316 с.
15.Talrefa R. Estimation of Weibull parameters for composite material strength and fati gue life data 11 Fatigue of fibrous composite materials: ASTM STP N 723. Amer. Soc. Test, and Mater. 1981. P. 291-311.
16.Орлов А.И. Распространенная ошибка при использовании критериев Колмогоро ва и омега-квадрат // Завод.лаб. 1985. № 1. С. 60-62.
17.Хан Г., Шапиро С. Статистические модели в инженерных задачах. М.: Мир, 1969. 395 с.
18.Шеннон Р. Имитационное моделирование систем - искусство и наука. М.: Мир, 1978.418 с.
19.Dumonceaux R., Antle С.Е. Discrimination between the Log-normal and Weibull dis tributions// Technometrics. 1973. Vol. 15, N 4. P. 923-926.
20.Little R.E. Review of statistical analysis of fatigue life data using one-sided lower sta tistical tolerance limits // Statistical analyses of fatigue data: ASTM STP N 744. Amer. Soc. Test. Mater. 1981. P. 3-23.
СВЯЗЬ МЕЖДУ ХАРАКТЕРИСТИКАМИ РАССЕЯНИЯ ПАРАМЕТРОВ ДЕФОРМИРОВАНИЯ
ПРИ СТАТИЧЕСКОМ И МАЛОЦИКЛОВОМ НАГРУЖЕНИИ
3.1.Определение рассеяния основных механических свойств
икорреляционных связей между ними
Расчетные вероятностные методы оценки малоцикловой прочности и долговечности предусматривают использование в качестве исходных дан ных для расчета рассеяний фактических основных механических свойств (ОМС) материала. Это обусловливает необходимость определения для экспериментальных функций распределения ОМС предпочтительных теоре тических законов и установления корреляционных связей между самими ОМС с целью обоснования значений их с заданным уровнем вероятности.
Причинами рассеяния ОМС (а0>02, o0 2f о*,, Skf фк и 5), как и при уста лости, являются факторы, определяющие микроструктуру материала. Это металлургические факторы, начиная от состава шихты и кончая пара метрами процессов прокатки и термической обработки, колебания кото рых в рамках установленных режимов чаще всего носят случайный харак тер. В то же время рассеяние усиливается технологией изготовления образ цов и технологией проведения эксперимента. При этом получаемое рассея ние ОМС существенно меньше, чем рассеяние долговечности при малоцик ловой и многоцикловой усталости.
Статистические исследования ОМС проводятся давно и в основном сво дятся к определению предпочтительного теоретического закона распреде ления и оценке его параметров. При использовании законов нормального и логнормального распределения, а также распределения Вейбулла опреде лена предпочтительность первых двух распределений. Однако пока мало исследований по оценке уровня вероятности гарантированных технологией значений ОМС и по определению корреляционных связей между самими ОМС (см. п. 1.2).
При статическом нагружении в условиях нормальной температуры для стали 15Х2МФА испытано 160, для стали 45—220 и для алюминиевого сплава Д16Т1 — 120 образцов при скорости растяжения 33 • 1(Г4 с"1 При этом пятикратные образцы диаметром 5 мм вырезались из цилиндри ческой части и головок гладких образцов, испытанных на малоцикловую усталость. Это в дальнейшем дало возможность установить корреляцион ные связи между ОМС и долговечностями по образованию трещин N0 и окончательному разрушению Np (см. п. 4.2).
При большом числе испытаний (порядка нескольких сот) простая сово купность данных становится слишком громоздкой и мало наглядной, поэтому полученный статистический материал по механическим характе ристикам - пределы пропорциональности, текучести, прочности (<7о,02*
ао,2 > аь)> истинное сопротивление разрыву (Sk), |
относительное сужение |
|
(ф), |
равномерное сужение (фь) — подвергался дополнительной обработ |
|
ке: |
были построены статистические ряды. Для |
построения гистограмм |
весь диапазон статистического ряда разбивался на десять равных интер валов, длина которых
■*инт &шах *min)/(«—!),
где *maxH*m in” максимальное и минимальное значения механической характеристики в статистическом ряду; п —количество интервалов. Уве личение п выше 15—20 нецелесообразно даже при большом объеме ста тистических рядов, так как при этом точность статистических оценок увеличивается несущественно, а объем вычислений значительно возрастает.
Статистические ряды ОМС были представлены графически в виде гисто грамм. При этом по оси абсцисс откладывались интервалы равной длины,
ана каждом из интервалов, как на основании, строились прямоугольники
свысотой, равной плотности эмпирического распределения:
Р{ = т{/п,
где т{ —число значений случайной величины в данном интервале; п —об щее число значений случайной величины.
Анализ имеющегося статистического материала с использованием гисто граммы показал качественное его соответствие нормальному распреде лению, но для более полной количественной оценки рассчитывались ста тистические характеристики для трех часто используемых законов распре деления —нормального, логнормального и закона Вейбулла.
Для нормального и логнормального распределения определялись: сред нее арифметическое 5с, среднее квадратическое отклонение S , дисперсия А коэффициент асимметрии Sa и коэффициент вариации и.
Для распределения Вейбулла статистические характеристики опреде
лялись по зависимостям: |
|
|
|
|
х = Ъкь + с, |
|
|
|
(3.1) |
S = bkb, |
2 (х/-х)31/р- 2 |
3/2 |
(3.2) |
|
sa - f ~ |
|
|||
(х,-х)2\ |
(3.3) |
|||
[(и-1)(и-2) /= ! |
J / U - l i=1 |
i |
|
|
v = bkb/(bkb +c). |
|
|
|
|
Коэффициенты kb и gb для |
зависимостей |
(3.1) —(3.3) |
подбирались по |
полученному значению Sa из табл. 1 [1], а параметры масштаба Ъ и сдвига с определялись по зависимостям
|
с = х - Ъкъ |
при C < xmint |
Ъ = |
С = Xmin |
при C>Xmfn. |
В табл. 3.1—3.3 приведены |
статистические характеристики распределе |
ний механических величин исследованных материалов: нормального, логнормального и распределения Вейбулла. Из проведенного анализа
Статистические характеристики нормального закона распределения исследован ных механических характеристик
Характе |
|
Материал |
Количест |
X |
S |
D |
|
Sa |
|
ристика |
|
во образ |
|
|
|||||
|
|
|
цов |
|
|
|
|
|
|
<70,02* МПа |
15Х2МФА |
160 |
287 |
42 |
1764 |
|
0,080 |
0,146 |
|
|
|
45 |
220 |
325 |
52 |
2704 |
|
0,410 |
0,160 |
|
|
Д16Т1 |
й о |
292 |
40 |
1600 |
|
-0,043 |
0,136 |
а0,2> МПа |
|
15Х2МФА |
160 |
414 |
53 |
2809 |
|
0,002 |
0,128 |
|
|
45 |
220 |
325 |
52 |
2704 |
|
0,410 |
0,160 |
<7£, МПа |
|
Д16Т1 |
120 |
346 |
41 |
1681 |
|
0,011 |
0,118 |
|
15Х2МФА |
160 |
602 |
42 |
1764 |
|
-0,491 |
0,069 |
|
|
45 |
220 |
811 |
77 |
5929 |
|
-0,333 |
0,095 |
|
Sfo МПа |
Д16Т1 |
120 |
677 |
41 |
1681 |
|
-0,141 |
0,061 |
|
|
15Х2МФА |
160 |
1585 |
201 |
40401 |
0,240 |
0,127 |
||
|
45 |
220 |
1154 |
100 |
10000 |
-0,110 |
0,087 |
||
|
Д16Т1 |
120 |
793 |
52 |
2704 |
|
-0,061 |
0,066 |
|
* ,% |
|
15Х2МФА |
160 |
80,12 |
2,41 |
5,86 |
|
1,451 |
0,030 |
|
45 |
220 |
41,05 |
5,18 |
26,86 |
|
0,225 |
0,126 |
|
|
Д16Т1 |
120 |
14,59 |
2,58 |
6,64 |
|
0,529 |
0,177 |
|
|
15Х2МФА |
160 |
10,16 |
2,56 |
6,58 |
|
2,432 |
0,252 |
|
|
45 |
220 |
14,18 |
2,77 |
7,67 |
|
1,446 |
0,195 |
|
|
Д16Т1 |
120 |
12,84 |
0,71 |
0,51 |
|
0,071 |
0,055 |
|
Т а б л и ц а |
3.2 |
|
|
|
|
|
|
|
|
Статистические характеристики логнормального закона распределения исследо |
|||||||||
ванных механических характеристик |
|
|
|
|
|
||||
Характе |
Материал |
Количест |
X |
S |
D |
|
Sa |
V |
|
ристика |
во образ |
|
|||||||
|
|
|
цов |
|
|
|
|
|
|
а0,02> МПа |
15Х2МФА |
160 |
284 |
0,0649 |
0,0042 |
|
-0,301 |
0,026 |
|
|
45 |
|
220 |
321 |
0,0688 |
0,0047 |
|
0,074 |
0,027 |
|
Д16Т1 |
120 |
290 |
0,0609 |
0,0037 |
|
-0,263 |
0,025 |
|
ао,2> МПа |
15Х2МФА |
160 |
410 |
0,0571 |
0,0032 |
|
-0,299 |
0,022 |
|
|
45 |
|
220 |
321 |
0,0688 |
0,0047 |
|
0,073 |
0,027 |
оъ, МПа |
Д16Т1 |
120 |
343 |
0,0513 |
0,0026 |
|
0,117 |
0,020 |
|
15Х2МФА |
160 |
600 |
0,0315 |
0,0009 |
|
-0,828 |
0,011 |
||
|
45 |
|
220 |
806 |
0,0423 |
0,0018 |
|
-0,558 |
0,015 |
|
Д16Т1 |
120 |
676 |
0,0267 |
0,0007 |
|
-0,308 |
0,009 |
|
Sfo МПа |
|
|
• |
|
|||||
15Х2МФА |
160 |
1571 |
0,0551 |
0,0030 |
--0,033 |
0,017 |
|||
|
45 |
|
220 |
1149 |
0,0381 |
0,0014 |
--0,278 |
0,012 |
|
|
Д16Т1 |
120 |
791 |
0,0287 |
0,0008 |
--0,218 |
0,010 |
||
*,% |
15Х2МФА |
160 |
80,03 |
0,0129 |
0,0002 |
|
1,186 |
0,007 |
|
45 |
|
220 |
40,68 |
0,0548 |
0,0029 |
|
0,045 |
0,034 |
|
Д16Т1 |
120 |
14,36 |
0,0754 |
0,0057 |
|
0,168 |
0,065 |
||
15Х2МФА |
160 |
9,90 |
0,0945 |
0,0089 |
|
0,995 |
0,095 |
||
45 |
|
220 |
13,92 |
0,0807 |
0,0065 |
|
0,258 |
0,071 |
|
Д16Т1 |
120 |
12,82 |
0,0241 |
0,0006 --0,168 |
0,022 |
Статистические характеристики закона распределения Вейбулла исследованных механических характеристик
Характерис |
Материал |
Количество |
X |
S |
Sa |
и |
тика |
|
образцов |
|
|
|
|
а0,02» МПа |
15Х2МФА |
160 |
287 |
42 |
0,081 |
0,146 |
|
45 |
220 |
325 |
52- |
0,419 |
0,159 |
|
Д16Т1 |
120 |
292 |
40 |
-0,043 |
0,138 |
а0,2» МПа |
15Х2МФА |
160 |
414 |
53 |
0,002 |
0,129 |
|
45 |
220 |
325 |
52 |
0,418 |
0,159 |
|
Д16Т1 |
120 |
346 |
41 |
.0,023 |
0,117 |
МПа |
15Х2МФА |
160 |
602 |
42 |
-0,499 |
0,070 |
|
45 |
220 |
811 |
77 |
-0,340 |
0,095 |
|
Д16Т1 |
120 |
677 |
41 |
-0,142 |
0,061 |
Sfo МПа |
15Х2МФА |
160 |
1585 |
201 |
0,246 |
0,127 |
|
45 |
220 |
1154 |
100 |
-0,112 |
0,087 |
|
Д16Т1 |
120 |
793 |
52 |
-0,062 |
0,066 |
ф,% |
15Х2МФА |
160 |
79,60 |
2,42 |
1,478 |
0,032 |
|
45 |
220 |
41,05 |
5,18 |
0,228 |
0,126 |
|
Д16Т1 |
120 |
14,59 |
2,58 |
0,542 |
0,177 |
Фь>% |
15Х2МФА |
160 |
8,19 |
2,56 |
0,248 |
0,313 |
|
45 |
220 |
12,75 |
2,77 |
1,466 |
0,217 |
|
Д16Т1 |
120 |
12,80 |
0,71 |
0,073 |
0,056 |
результатов (см. табл. 3.1—3.3) и соответствующих гистограмм было установлено, что средние арифметические значения, определенные по гистограммам, довольно близки к расчетным. Большинство механичес ких характеристик имеют значительный коэффициент асимметрии, что наблюдалось и по гистограммам. Максимальный коэффициент асимметрии наблюдается у ф и фь.
По-видимому, одним из основных показателей разброса механических характеристик является коэффициент вариации, который для большинства их принимает минимальное значение при использовании логнормального распределения. Это подтверждает предпочтительность логнормального распределения по сравнению с нормальным и распределением Вейбулла. Необходимо отметить, что как коэффициент вариации, так и другие ста тистические параметры для законов Вейбулла и нормального распределе ния мало отличаются, что, кстати, отмечено и другими авторами при огра ниченном объеме выборки.
Необходимо отметить, что в п. 2.2 приведена методика, позволяющая оценить параметры распределения Вейбулла при помощи расчетов на ЭВМ. Эта методика позволяет также определить предпочтительный теоретичес кий закон на основе расчета по критериям согласия X, со2 и W.
Известно, что выборочные характеристики являются надежными коли чественными оценками лишь при большом объеме выборки. При ограни ченных объемах испытаний необходимо указать степень точности и надеж-
Т а б л и ц а З А
Результаты расчета нормированных механических характеристик
Характеристика |
15Х2МФА |
45 |
Д16Т1 |
а0,02* МПа |
228 |
253 |
235 |
а0,2» МПа |
339 |
253 |
288 |
<7£, МПа |
542 |
703 |
618 |
Sfa МПа |
1302 |
1014 |
719 |
V', % |
76,72 |
33,79 |
10,90 |
Фь* % |
6,58 |
10,30 |
11,82 |
|
ности оценок. Представление об уровне точности и надежности оценок дают доверительные интервалы, определяемые по зависимости
х |
S |
х + |
S |
< а < |
, ty |
||
|
у /п -Г ty> |
|
у/п=т |
где t7i |
и ty2 — квантили |
нормального распределения, определяемые по |
заданным значениям доверительной вероятности у\ и у2 и к = п—1.
При вероятностных расчетах прочности и долговечности элементов конструкций для повышения их надежности целесообразнее пользоваться не выборочными значениями механических характеристик, а значениями границ доверительных интервалов, в частности, выборочное среднее зна чение механической характеристики заменить нижней границей довери тельного интервала, а выборочное среднее квадратическое отклонение — верхней границей доверительного интервала.
Часто при конструировании используются стандартные значения меха нических характеристик без учета имеющегося внутриплавочного и межплавочного разброса этих характеристик, что иногда может привести к существенному отклонению от истинной прочности и долговечности конструкции. С целью выяснения этой погрешности для имеющихся ста тистических рядов по известной стандартной методике определяли вели чины нормированных механических характеристик, которые сопостав ляли со стандартными значениями и математическими средними для иссле дованных материалов. Для обеспечения надежного запаса прочности норми рование механических характеристик провели снизу, а расчетные значения норм определяли с использованием вариационного ряда, упорядоченного по возрастающей переменной величине. При этом расчетные значения норм определяли по зависимости
с0 =х - kiS.
Значения толерантного множителя к\ зависят от объема выборки и для исследованных материалов составляли: 1,41 для стали 15Х2МФА; 1,40 для стали 45 и 1,43 для алюминиевого сплава Д16Т1.
Результаты расчета нормированных механических характеристик при ведены в табл. 3.4. Нормированные механические характеристики, рас-
Рис. 3.1. Функции распределения пределов пропорциональности, текучести и прочности а — сталь 15Х2МФА, б — сталь 45, в — алюминиевый сплав Д16Т1; 1 — aofo2» 2 ~
°0,2> 3 — оb‘t здесь и на рис. 3.2: / —нормированная величина, II —справочная
считанные по изложенной методике, обеспечивают требуемый ГОСТом уровень надежности.
Совместно с нормированными справочными механическими характе ристиками на рис. 3.1 и 3.2 в координатах вероятность события—механи ческая характеристика для логнормального распределения представлены все экспериментальные данные исследованных механических характе ристик.
Как следует из рис. 3.1 и 3.2, совокупность экспериментальных данных для всех механических характеристик на вероятностной бумаге логнор мального распределения представляется прямыми, что является подтверж дением соответствия этих величин логнормальному распределению.
Известно, что при расчете параметров диаграмм деформирования и долговечности в основном используются характеристики ОМС ао,2> Оь и Ф- Эти характеристики обычно приводятся и в справочной литературе. Сопоставление экспериментальных данных, нормированных и справочных характеристик ао,2»°ъ и Ф>приведенное на рис. 3.1 и 3.2, позволяет заклю чить, что справочные характеристики плохо соответствуют эксперименталь ным данным. Например, справочные характеристики предела текучести 0о,2 для всех исследованных материалов дают значительную вероятность: для стали 15Х2МФА —74%, для стали 45—62%, для сплава Д16Т1 —90%. Аналогичная картина наблюдается и у предела прочности оъ для стали 15Х2МФА, а для стали 45 и алюминиевого сплава Д16Т1 справочные дан ные соответствуют вероятности ниже 1%. Для относительного сужения ф справочная величина для стали 15Х2МФА составляет 0,0003% вероятности, для стали 45 соответствует экспериментальным данным, т.е. 50%.
Zi
Lr c
г]
# о/
|
ft] |
|
|
I N |
|
|
W |
|
|
I |
n |
|
1 |
и |
|
' |
и |
|
/ |
1 |
|
.t . |
|
•• |
|
|
и1 JUJ |
||
/ |
.1 |
|
j-1J J ____ |
||
f |
8 Г0 2 P S '* |
|
Рис. 3.2. Функции распределения истинного сопротивления разрыву |
(£*), относитель |
|
ного (ф) и равномерного сужения (ф^) |
|
|
1 —алюминиевый сплав Д16Т1, 2 —сталь 45, 3 —сталь 15Х2МФА |
|
|
Поскольку относительное сужение ф используется как основная харак теристика при оценке малоцикловой долговечности, то применение для стали 15Х2МФА справочной величины ф = 50%, составляющей для нашего материала 0,0003% вероятности, дает большой запас по сравнению с факти ческой долговечностью. Для стали 45 справочная величина ф =40%, состав ляющая для экспериментальных данных 95% вероятности, не обеспечивает достаточного уровня надежности. В табл. 3.4 и на рис. 3.1 и 3.2 приведены полученные на основе экспериментальных данных нормированные харак теристики, которые во всех случаях дают удовлетворительный результат, так как их вероятности ниже 50 и выше 1—5%, но необходимо иметь в виду, что здесь не учитывается межплавочный разброс.
Таким образом, из проведенного сопоставления справочных характе ристик с данными вариационного ряда для исследованных материалов следует, что использование справочных механических характеристик для расчетов малоцикловой прочности и долговечности деталей и конструк тивных элементов недопустимо, так как может привести к существенным отклонениям от реальной картины.
Большое влияние на экспериментальные результаты при малоцикловом нагружении оказывает разброс диаграмм статического деформирования. Анализ огибающих диаграмм статического деформирования, построенных с использованием крайних значений статистических рядов о0 02, сг0|2>°ь> еп еъ в координатах о—е и а-ё, показал, что на результаты малоцикло-
wл \J Af
вых испытаний оказывает влияние способ задания уровня нагружения и применяемые координаты. Для жесткого нагружения влияние координат несущественно, но мягкое нагружение в абсолютных координатах о-е практически трудно реализовать из-за большого разброса деформаций при заданных о. Например, для стали 15Х2МФА при уровне нагружения о = 400 МПа деформация может меняться от 0,2 до 4,5%, при о= 450 МПа — от 0,2 до 11,5%, при о= 500 М П а- от 0,2% до бесконечности. При приме нении относительных координат а—ё~разброс значений деформации суще-_ ственно снижается, что и определяет предпочтительность координат а—е для мягкого нагружения.
Проведены также оценки рассеяния ОМС для корпусных сталей атомно го энергомашиностроения Х18Н9 и 15Х2НМФА при нормальной и эксплуа тационных температурах —650 и 350 °С.
На рис. 3.3 показаны экспериментальные функции распределения ОМС стали 15Х2НМФА при нормальной температуре для материала с дополни тельным отпуском (620 °С —25 ч + 650 °С —17 ч), ориентированным на штатную термообработку корпуса энергетического аппарата при сборке. На рис. 3.3 видно, что значения ОМС удовлетворительно аппроксимируются прямыми, проведенными в предположении нормального закона распреде ления.
Сопоставление статистически обработанных ОМС с гарантированными
(заводскими) минимальными |
свойствами |
для значений, равных о^° = |
= 560 МПа, о^°2 = 450 МПа, |
=55% |
и б20 = 15%, показывает, что |
аппроксимирующие прямые распределений ОМС пересекают уровень тре бований ТУ при значениях вероятности, значительно меньших 1%. В табл. 3.5 приведены значения статистик х, S n_ i и и, а также значения приближенной вероятности Pw того, что выборка соответствует нормаль ному или логнормальному закону при проверке по критерию согласия W.
На рис. 3.4, a- в показаны экспериментальные функции распределения ОМС стали 15Х2НМФА (с дополнительным отпуском) при температуре
350° С и проверка их на |
соответствие нормальному, логнормальному |
и двухпараметрическому' |
Вейбулла законам распределения. Значения |
статистик % S n_ ь v и вероятности Pw (%) представлены в табл. 3.6.
Из рисунков следует, что экспериментальные функции распределения лучше соответствуют нормальному и логнормальному законам распределе ния, соответствие ОМС при повышенной температуре закону распределе ния Вейбулла неудовлетворительное. Анализ по критерию согласия W (см. табл. 3.5 и 3.6) показывает, что соответствие функций распределения значений о0 2 и оь нормальному и логнормальному законам составляет от 3 до 25% при нормальной температуре и от 1 до 4% при повышенной температуре. Соответствие распределений величины а0 02 обоим законам распределения на уровне 28—45%. Остальные функции распределений ОМС (фк, S k, б^) имеют более высокое соответствие (до 99%) (за исключением функций для фк при нормальной температуре и наличии дополнительной термообработки, где соответствие 4—5%).
В целом можно отметить, что проведенная с использованием различных критериев согласия X, со2 и W статистическая обработка ОМС стали XI8Н9 при нормальной температуре [2], температуре 650° С и стали 15Х2НМФА при нормальной и повышенной температуре показывает в большинстве
=/s%
Я М |
/707 |
SA |
Рис. 3.3. Функции распределения основных механических свойств стали |
15Х2НМФА при нормальной температуре |
1 - 6 , 2 - ог0(02, 3 - ст0>2, 4 - о ь, 5 - ф к, б - Sk |
|
Статистические характеристики основных механических свойств стали 15Х2НМФА при нормальной температуре
Параметр |
|
|
Напряжение» МПа |
|
|
распределе- |
|
|
|
|
|
ния |
ао,оз |
*8сто,0 2 |
a0,2 |
teCTo,2 |
аЪ |
Без дополни*гельной термообработки
|
|
n = 30 |
|
п = 31 |
|
п = 31 |
X |
646,75 |
2,8102 |
697,81 |
2,8435 |
791,13 |
2,8982 |
s n - 1 |
31,50 |
0,0211 |
24,59 |
0,0152 |
22,10 |
0,0121 |
v = S „ _ i / x |
0,0487 |
0,0075 |
0,0352 |
0,0053 |
0,0279 |
0,0042 |
p w |
38,2 |
43,6 |
2,9 |
4,0 |
12,9 |
17,4 |
|
|
С дополнительной термообработкой |
|
|||
|
|
п = 30 |
|
п = 30 |
|
п = 30 |
X |
558,47 |
2,7467 |
581,35 |
2,7641 |
689,74 |
2,8386 |
Sn-1 |
20,73 |
0,0160 |
22,13 |
0,0164 |
18,35 |
0,0115 |
v = Sn - l l X |
0,0371 |
0,0058 |
0,0381 |
0,0059 |
0,0266 |
0,0041 |
PW |
28,1 |
38,1 |
7,6 |
и д |
20,3 |
24,8 |
Т а б л и ц а 3.6
Статистические характеристики основных механических свойств стали 15Х2НМФА (с дополнительной термообработкой) при температуре 350° С
Параметр |
|
Напряжение, МПа |
|
|
распределения |
a0,0 2 |
te<*0,02 |
а0,2 |
tea0,2 |
|
||||
|
п = 39 |
|
|
п = 38 |
|
1 |
2,6357 |
|
1 |
X |
433,37 |
438,78 |
2,6839 |
|
s n - l |
31,87 |
0,0319 |
28,67 |
0,0252 |
V |
0,0735 |
0,0121 |
0,0593 |
0,0094 |
PW |
39,1 |
44,9 |
1,3 |
3,6 |
случаев удовлетворительное соответствие их функций распределений, особенно для характеристик пластичности, нормальному и логнормаль ному законам распределений. При этом во всех случаях логнормальный закон был предпочтительнее распределений Вейбулла, а соответствие экспо ненциальному закону практически отсутствовало.
Принятие гипотезы о нормальном или логнормальном законе распреде ления ОМС сталей 15Х2НМФА и Х18Н9 позволило использовать расчетные значения ОМС для заданных уровней вероятности Р для проведения вероят ностных расчетов по моменту образования и при развитии малоцикловых
Напряжение, МПа |
|
Пластичность, % |
|
||
Sk |
•в*к |
Ф |
lgФ |
6 |
lgб |
|
|
Без дополнительной термообработки |
|
||
л = 28 |
|
|
л = 29 |
Л = 29 |
|
1682,2 |
3,2257 |
74,707 |
1,8733 |
21,040 |
1,3228 |
52,75 |
0,0138 |
0,888 |
0,0052 |
0,717 |
0,0148 |
0,0314 |
0,0043 |
0,0119 |
0,0028 |
0,0341 |
0,0112 |
31,6 |
23,3 |
46,4 |
56,4 |
98,1 |
99,0 |
|
|
С дополнительной термообработкой |
|
||
л = 31 |
|
|
л = 31 |
|
л = 31 |
1647,7 |
3,2167 |
78,306 |
1,8937 |
23,631 |
1,3728 |
42,47 |
0,0112 |
0,788 |
0,0044 |
1,242 |
0,0229 |
0,0258 |
0,0035 |
0,0101 |
0,0023 |
0,0526 |
0,0167 |
48,0 |
45,8 |
3,8 |
4,3 |
31,2 |
27,8 |
|
Напряжение, МПа |
|
Пластичность, % |
||
аь > |
lgаь |
Sk |
*gSk |
|
|
л = 38 |
|
П - 41 |
|
|
л = 41 |
1 |
|
" "1 |
3,0525 |
66,594 |
1 |
594,99 |
2,7742 |
1131,5 |
1,8233 |
||
23,87 |
0,0171 |
81,87 |
0,0317 |
1,668 |
0,0109 |
0,0401 |
0,0062 |
0,0724 |
0,0104 |
0,0250 |
0,0059 |
1,9 |
3,9 |
99,0 |
92,5 |
81,1 |
81,3 |
трещин (см. гл. 4 и 5). При этом оказалось также необходимым учитывать возможные зависимости между самими ОМС.
Для определения характера и степени зависимости ОМС друг от друга проведена оценка параметров эмпирической линии регрессии двух случай ных величин, имеющих нормальное распределение, и оценка значений коэффициента корреляции г. Для этого на ЭВМ типа СМ-4 (Фортран-IV) составлена программа расчета параметров линейной регрессии и коэффи циента корреляции; графическая часть программы обеспечивает нанесение экспериментальных значений ОМС на график и проведение линии регрессии.
200 |
400 |
000 |
|
^0,02 f **0,2 ' ^0 ’ М 0а;рл |
•/Ъ\% |
Рис. 3.4. Функции распределения основных механических свойств стали 15Х2НМФА при температуре 350 ° С
а — логнормальное распределение, б — нормальное распределение, в — распреде ление Вейбулла; Г — <*0,02» 2 —^о,2» 3 — 4 — ф 5 — Sk
На рис. 3.5 показаны характерные зависимости между ОМС стали 15Х2НМФА (с дополнительной термообработкой) при нормальной темпера туре. Из рисунка следует, что увеличению прочностных характеристик ста ли а0,2 и Оъ соответствует уменьшение ее пластичности фк, при этом значе ния величины г имеют величину порядка 0,8, что свидетельствует о доволь-
но тесной корреляционной связи между указанными величинами. При уве личении значений S k и S k/ob возрастает и пластичность, при этом значения величины г составляют соответственно 0,3 и 0,9. Расчетные значения отно шения S,fc/ab, принятые равными 1 + 1,40* (штриховая линия), имеют меньшую среднюю величину и меньшее рассеяние, чем экспериментальные.
Для значений ОМС стали 15Х2НМФА при температуре 350 ° С характер зависимостей между ОМС тот же, но значения величины г существенно меньше: о0 2-ф к, г = 0,30; оь-ф к, г = 0,25; Як-ф к, г = 0,40; 8 к!оь-ф к, г = 0,59. ’
На рис. 3.6 для стали Х18Н9 при температуре 650 °С показаны характер ные зависимости между ОМС. Расчетные значения S k/ob = 0,8 + 2,060 ^ [3] (штриховая линия) имеют меньшее рассеяние, чем экспериментальные.
Для данных объемов выборок (п > 30) значимые значения коэффициента корреляции г соответствуют г > 0,4 [4]. В целом же г принимает значения и меньше 0,4, обычно изменяясь от 0,3 до 0,8.
Таким образом, для вероятностного расчета долговечностей по образо ванию и развитию трещин в данных случаях можно принять, что увеличе нию значений величины фк и S k соответствует уменьшение значений осталь ных ОМС. При этом необходима оценка принятого допущения, что можно сделать путем сравнения такого расчета с расчетом долговечностей по кон кретным значениям ОМС для каждого образца статистической серии (см.
п.4.3).
Вцелом можно отметить, что коэффициенты вариации значений ОМС (для нормального закона) для сталей Х18Н9 и 15Х2НМФА при нормаль
ных и повышенных температурах для материала одной плавки изменялись в пределах: 2,8-10,3% (а0>2); 2,5-4,0 (ай); 2,5-12,5 (Sk); 1,0-4,2% (фк), при этом их значения были максимальными для стали Х18Н9 при
SK/^S
Рис. 3.5. Зависимости между основными механическими свойствами стали 15Х2НМФА при нормальной температуре
температуре 650 °С. Проведенный по критериям согласия X, cJ2 и W расчет ный анализ для обеих сталей позволяет принять нормальный или логнор мальный закон их распределения. Установление зависимостей между ОМС позволило определить табличные значения ОМС заданного уровня вероят ности. Достоверность использования табличных значений ОМС необходимо проверять расчетами малоцикловой долговечности по конкретным значе ниям ОМС для каждого образца статистической серии (для данного мате риала и температуры).
3.2. Учет рассеяния параметров циклического деформирования и их связь с ОМС материала
Одной из основных характеристик материалов, определяющих эксплуа тационную надежность конструкций, является сопротивление циклическо му деформированию. Известно, что диаграммы циклического деформиро вания, как и диаграммы статического нагружения, чувствительны к вариа циям химического состава, термообработке, поверхностному наклепу, условиям нагружения и другим факторам. В результате наблюдается суще ственный разброс характеристик циклического деформирования, во мно-
Рис. 3.6. Зависимости между основными механическими свойствами ста ли Х18Н9 при температуре 650 ° С
гих случаях значительно превышающий разброс ОМС. Расчеты сопротивле ния малоцикловому деформированию проводятся с использованием пара метров диаграмм циклического деформирования, но статистическая оценка этих параметров пока никем не проводилась.
В настоящей работе статистической оценке подвергались параметры (А, А а, /3, С и 5 Г), используемые при аналитическом описании диаграмм циклического деформирования. В первую очередь по той же методике, как и для ОМС, были построены гистограммы и установлено, что вид гистограмм в основном зависит от объема выборки и с ее увеличением гистограммы для большинства параметров по своей форме приближают ся к нормальному распределению.
Расчет статистических характеристик (среднего арифметического, сред него квадратического отклонения, дисперсии, коэффициентов асимметрии и вариации) проводился для распределения Вейбулла, нормального и лог нормального распределений. Анализ статистических характеристик показал, что коэффициент вариации для параметров А, А *, S T и а принимает мини мальное значение при применении нормального, а для параметров /3 и С — логнормального распределения. Статистические характеристики закона Вей булла мало отличаются от характеристик нормального распределения. Следует отметить, что коэффициент вариации нормального распределения
4% щ я
з з
зз
70
50
30
70
7
0,7
0,02 |
$50 7,00 |
0,25 0f50 Q75 ос 0,75 |
7,25 |
7,75 5^ |
0 |
4±> А2
Рис. 3.7. Функции распределения параметров диаграмм циклического деформиро вания
а: 1 — |
A lt 2 — А2; а, б |
— алюминиевый сплав Д16Т1, <Г0 = 1,15; в: 1 — сталь 45, |
2 — сталь |
15Х2МФА, 3 — |
алюминиевый сплав Д16Т1; г, д — сталь 15Х2МФА: 1 — |
а0 = 1,00, 2 - а0 = 1,12, 3 - а0 = 1,25
циклических параметров А, А * явно зависит от уровня нагружения и умень шается с его возрастанием. Это объясняется меньшей стабильностью диа грамм исходного и первого полуциклов нагружения на начальных стадиях деформирования.
Графический анализ экспериментальных значений параметров цикличе ского деформирования на вероятностной сетке нормального и логнормаль ного законов также подтвердил их соответствие указанным теоретическим законам (рис. 3.7), гдеЛь А 2 —экспериментальные значения параметра А циклической диаграммы, определенные как показано ниже.
Сопоставление статистических характеристик параметров диаграмм
циклического упругопластического нагружения и механических харак теристик показало более существенный разброс диаграмм циклического деформирования. Отсюда следует, что диаграммы циклического деформи рования более чувствительны к вариациям химического состава, условиям термической технологической обработки и эксперимента.
В связи с использованием для расчета параметров диаграмм цикличе
ского деформирования статических характеристик |
[5] большой |
интерес |
|
представляет |
исследование корреляционных связей |
между N0, Np и ф\ |
|
Фъ> ао,2’ аь> |
Ф(Ро,г1аь)> А> С> S T и Ф‘>ао,2» °ь> ^ ( ао,2/аь); |
а также |
между А*—А и о0 2 , аь, аь/а0 2.
Анализ корреляционных .связей между параметрами диаграмм цикличе ского деформировния и механическими характеристиками показал, что коэффициенты корреляции близки к единице. Применение для расчетов модифицированной пластичности ф (о0 2/оь) несколько уменьшает коэф фициенты корреляции по сравнению с коэффициентами для ф. Например, параметры At С, S т для стали 15Х2МФА и параметр С для стали 45 хуже коррелируют с ф(о021°ь)т всех уровнях нагружения. Использование соотношения оь/о0 2 для большинства уровней нагружения всех материа лов увеличивает коэффициент корреляции по сравнению с другими меха ническими характеристиками.
Таким образом, проведенные исследования указывают на довольно тес ную корреляционную связь между механическими характеристиками
ипараметрами циклического деформирования, что подтверждает правиль ность и физический смысл математических зависимостей, предложенных разными авторами для описания процесса малоциклового деформирования
иразрушения как при мягком, так и при жестком нагружении.
Расчетная оценка рассеяния долговечностей по моменту образования тре щин N0 при мягком нагружении для однородного напряженного состояния [6] показала, что использование вероятностных значений параметров диаграммы циклического деформирования приводит к противоречивым результатам, например более высокое значение долговечности N0 — для меньшего уровня вероятности Р для стали 15Х2МФА и др. Поэтому в даль нейшем расчеты по определению N0 проводили с использованием средне арифметических значений параметров диаграммы циклического деформи рования.
В связи с изложенным было принято целесообразным проводить оценку экспериментального разброса параметров диаграмм циклического дефор мирования сталей Х18Н9 и 15Х2НМФА расчетным способом путем учета рассеяния ОМС. При этом расчетное рассеяние параметров сравнивалось с их экспериментальными значениями, полученными на основе единичных ис пытаний на различных уровнях нагружения.
В работе [7 ] предложены зависимости, связывающие параметры диа грамм циклического деформирования и ОМС. Так, параметр А, характе ризующий сопротивление деформированию в первом полуцикле нагруже ния, определяется по формуле
(3.4)
где КА —коэффициент, принимаемый для широкого класса сталей равным
70*- а
5
/о' |
|
|
|
|
5 |
A |
A |
i |
|
|
|
|||
70l |
1 ■ »!«■■■ |
— * |
ч |
* 7 -“ |
..1.1 |
70г |
1_L_L |
||
|
S 70' |
5 |
О л |
Рис. 3.8. Экспериментальные (точки) и расчетные (линии) значения параметров А и а диаграмм циклического деформирования стали Х18Н9 при нормальной темпе ратуре (а-в)
0,16. При этом за относительную ширину петли в первом полуцикле 5 ^
при экспериментальном определении параметра А \ |
принимается значение, |
||
определяемое продлением прямой, |
|
описывающей |
зависимость 5 ^ —А, |
на первый полуцикл нагружения к = |
1 |
(рис. 3.8, а). Здесь и в дальнейшем |
индекс Р означает, что указанная характеристика может быть определена для заданного уровня вероятности Р (экспериментально или расчетным путем).
Если определять величину непосредственно по первому полуциклу (из диаграмм циклического деформирования), то получаются существен
но большие (меньшие) значения параметра |
(Л2), и его значение в этом |
случае приближенно равно [8] |
|
Агр =0,7 + 0 , 5 ^ - |
(3.5) |
°ь
Параметры а и /3, определяющие соответственно интенсивность цикличе ского упрочнения и разупрочнения, равны:
С
(3.6)
где Кв —коэффициент, равный 3 • 10“3 Параметр С обобщенной диаграммы деформирования определяется вы
ражением
ср = Kc i 1 Т 7 "Т ~2)> |
(3-7) |
где Кс —коэффициент, равный 1,5 |
1СГ3 |
На рис. 3.8, а при нормальной температуре показана зависимость отно сительной ширины петли 5 ^ от количества полуциклов к. Эксперимен тальные и расчетные рассеяния параметра А (величины А г и А 2) представ лены на рис. 3.8, б. Экспериментальные значения параметра Л2 обозначены точками 7, 2; точками 2 обозначены те значения Аг, для которых имеются значения А%, определенные экспериментально и обозначенные точками
3—9. Из рисунка следует, |
что для значений е ^ > 1 0 соответствие расчету |
наблюдается только для |
экспериментальных значений А \. Разброс экспе |
риментальных значений А \ и А^ существенно больше, чем расчетное рассея ние, обусловленное вероятностными значениями отношения о0 2/оь (3.4) и (3.5).
Расчетные значения параметра а представлены на рис. 3.8, в в виде линий.
При |
этом значение |
коэффициента Кв в формуле (3.6) принято равным |
15 |
10"3 вместо Кв |
= 3 • 10"3. |
На рис. 3.9, а для стали 15Х2НМФА (с исходной термообработкой) при нормальной температуре показан экспериментальный разброс параметров А \(1 ) и А 2 (2). Там же нанесены расчетные рассеяния параметра А \ при КА = 0,16 (сплошные линии) и при КА = 0,08 (штриховые линии). Экспе риментальный разброс значений параметра А \ и здесь больше расчетного рассеяния и в основном охватывается расчетным при значениях КА = = 0,08-Ю,16.
На рис. 3.9, б показаны экспериментальные и расчетные значения пара метра р. При расчете величины 0 в соответствии с (3.7) коэффициент Кс принят равным 1,5 • 10”3 Экспериментальный разброс величины 0 больше расчетного при малых значениях величины ё ^
Аналогичные выводы можно сделать для стали 15Х2НМФА (с дополни тельной термообработкой) при температуре 350°С (см. рис. 3.9, в, г). При этом экспериментальный разброс значений параметра А \ в основном охватывается расчетным при значениях КА, изменяющихся от 0,16 (сплош ные линии) до 0,3 (штриховые линии).
В целом можно отметить, что для сталей Х18Н9 и 15Х2НМФА при нор мальной и повышенных температурах (650 и 350 °С соответственно), в первом приближении возможно описание экспериментального разброса параметров циклической диаграммы А, а и (3 расчетным путем (через
? - 1 L e 2
0 |
5 _ |
e° |
^T |
* |
1 |
Рис. Э.9. Экспериментальные (точки) и расчетные (линии) значения параметров А и р диаграмм циклического деформирования стали 15Х2НМФА при нормальной тем пературе {а, б) и 350 °С (в, г)
рассеяние |
ОМС). Рекомендованные в [7] значения коэффициентов Кл = |
= 0,16, Кв |
= 3 10_3 и Кс = 1,5 10~3 необходимо уточнять для данного |
материала и температуры по результатам эксперимента. В этом случае существенное отличие получено только для значений коэффициента КА . Проведенная в дальнейшем оценка влияния экспериментально полученных значений Кл = 0,08 и 0,3 на расчетную долговечность по моменту образо вания трещин N0 в зонах концентрации (см. п. 4.4) показала, что суще ственное влияние имеется только для стали Х18Н9 при температуре 650 °С. В остальных случаях значение коэффициента КА можно принять равным 0,16.
ЛИ Т Е Р А Т У Р А
1.ГОСТ 11007-75. Правила определения оценок и доверительных границ для пара метров распределения Вейбулла. М.: Изд-во стандартов, 1976. 31 с.
2.Механика малоциклового разрушения / Под ред. Н.А. Махутова, А.Н- Романова. М.: Наука, 1986. 264 с.
3.Золотаревский В.С. Механические испытания и свойства металлов. М.: Металлур гия, 1974. 304 с.
4.Джонсон Н., Лион Ф. Статистика и планирование эксперимента в технике и науке. М.: Мир, 1980. 510 с.
5.Дауни с М.С. Функциональные связи между циклическими и механическими харак теристиками в условиях малоциклового нагружения // Материалы конф. ’’Развитие технических наук в республике и использование их результатов”. Сопротивление материалов. Вильнюс: РИСО Минвуза ЛитССР, 1979, С. 42-44.
6.Базарас Ж.Л. Статистическая оценка сопротивления деформированию и разруше нию при малоцикловом нагружении: Автореф. дис. канд. техн. наук. Каунас, 1983. 21 с.
7.Махутов Н.А. Деформационные критерии разрушения и расчет элементов кон струкций на прочность М.: Машиностроение, 1981. 272 с.
8.Прочность при малоцикловом нагружении / Под ред. С.В. Серенсена. М.: Наука, 1975. 285 с.
Г л а в а 4
ОСОБЕННОСТИ КРИВЫХ МАЛОЦИКЛОВОЙ УСТАЛОСТИ ПРИ ЖЕСТКОМ И МЯГКОМ НАГРУЖЕНИИ ПО ПАРАМЕТРУ ВЕРОЯТНОСТИ РАЗРУШЕНИЯ
С УЧЕТОМ МИКРО- И МАКРОНЕОДНОРОДНОСТЕЙ РАСПРЕДЕЛЕНИЯ ДЕФОРМАЦИЙ
4.1. Микронеоднородность деформаций при статических и циклических нагружениях
Микронеоднородность пластических деформаций, связанная со структу рой металлов, при однократном и циклическом нагружениях определяет целый ряд особенностей макродеформирования [1—4]. К их числу отно сятся: изменение формы поперечных сечений образцов (эллиптичность при исходном круговом сечении) , потеря устойчивости пластических деформа ций и шейкообразование, изменение скоростей циклической ползучести, развитие линий Чернова—Людерса, начального участка кривой неупругого макродеформирования в связи с эффектами деформационного старения.
Металлы и сплавы являются поликристаллическими телами, состоящими из большого числа различно ориентированных кристаллов (зерен), нераз рывно связанных между собой по границам. Каждый монокристалл ани зотропен по своей природе, и его физико-механические свойства в большей или меньшей степени зависят от направления (ориентировки). Деформа ционные процессы, протекающие в поликристалле под нагрузкой, гораздо сложнее, чем у монокристаллов, и характеризуются высокой степенью микронеоднородности развития деформаций по элементам структуры. Ка жущийся внешне хаотическим процесс микронеоднородного деформирова ния подчинен достаточно строгим закономерностям и для конкретной структуры металла, сложившейся в ходе кристаллизации и предваритель ной обработки. Поэтому анализ деформационного поведения микроэле ментов сплава необходимо вести с привлечением статистических методов и вероятностного анализа, а для выяснения чрезвычайно сложной картины формирования широкого комплекса механических свойств поликристаллического материала (т.е. макрообъема) необходимо знание напряженного и деформированного состояния по микроскопически малым областям, а также установление закономерностей распределения микронеоднородных деформаций в объеме групп зерен, отдельных зерен и их частей. При этом необходимо учитывать, что на микроуровне каждый микрообъем нахо дится в общем случае в объемном напряженном состоянии, вид которого меняется от точки к точке, даже при внешнем (макроскопическом) линей ном напряженном состоянии.
На базе формирующейся упругопластической неоднородной внутризеренной деформации устанавливается сложная картина микронеоднород ного течения поликристалла. Решающее значение в формировании устой чивого поля микронеоднородной деформации играют границы зерен, вбли зи которых и возникают наиболее часто зоны повышенной и уменьшенной
Рис. 4.1. Распределение микронеодно-
родной |
деформации |
(а) |
вдоль |
ре |
||
перной |
линии |
(база |
10 |
мкм) |
(б) |
|
для |
поликристаллического |
материала |
||||
a-Ti |
|
|
|
|
|
|
А, |
В |
— зерна; 1—3 — локальные |
||||
деформации по |
реперным |
точкам |
1 — |
|||
13; 4, 5 |
— локальные деформации по |
|||||
промежуточным наколам |
|
|
n/ i e
Рис. 4.2. Зависимость изменения коэф фициентов концентрации локальных деформаций по ферриту от содержа ния (в %) структурных составляю щих
1 —феррит, 2 —перлит
/00 |
SO |
20 О |
деформации, определяя ее микроконцентрацию. Границы зерен проявляют двойственное значение, с одной стороны, в качестве ’’стопоров” для разви тия макродеформации, с другой —в роли микроконцентраторов локальных деформаций и напряжений. Уверенное определение локальных деформаций может проводиться на базах в 5—8 раз меньше структурного элемента — размера зерна, что позволяет определять не только зеренную, но и внутризеренную неоднородность деформаций (рис. 4.1).
Оценочной характеристикой микронеоднородной (в пределах зерен) деформации является коэффициент концентрации локальных деформаций
Кце |
~~ |
(4.1) |
где е/ |
—относительная деформация z-го локального участка; |
еср — сред |
няя деформация (макродеформация) по т микроучасткам, входящих в рассмотрение (т > 10СК-200). При больших степенях деформации целесооб
разно вычислять истинные деформации е* = 1п(////,0) . |
|
|
|
По данным экспериментов |
[5], величина К^е для |
углеродистых |
сталей |
(термообработка—нормализация) систематически |
возрастает с |
ростом |
|
структурной неоднородности |
содержания углерода в стали —от |
1,8 для |
армко-железа до 4,2 для стали У7. Для двух- и многофазных сплавов сле дует производить раздельное определение коэффициентов концентрации
локальной деформации с целью выделения опасных элементов структуры, по которым возможно преждевременное исчерпание ресурса пластичности (в особенности при циклических нагружениях) и развитие микротрещин.
На рис. 4.2 приведены графики изменения коэффициента концентрации локальной деформации, определенные отдельно для ферритных и перлит ных зерен (от армко-железа до стали У8), доля содержания феррита в ко торых изменяется от 100 до 0%, а перлита —от 0 до 100%.
С увеличением доли прочной составляющей в стали (перлита) уровень микронеоднородности деформации неуклонно растет, что отражает роль увеличивающейся стесненности деформации по разнородным элементам структуры.
При малоцикловых нагружениях общие закономерности развития микронеоднородных пластических деформаций остаются такими же, как и при статических нагружениях. Однако при знакосимметричных нагружениях прослеживается обратимость локальных деформаций в полуциклах растя жения и сжатия [6]. Слабые элементы структуры, усиленно деформирую щиеся в полуцикле растяжения, остаются такими же и в полуцикле сжатия (рис. 4.3), хотя после разгрузки результирующая пластическая деформация по ним в пределах точности эксперимента равна нулю.
Распределение очагов повышенной и уменьшенной локальной деформа ции, установившееся в первом полуцикле, как правило, сохраняется в пос ледующих циклах растяжения (сжатия) до момента образования микротрещиньь
Появление микротрещин неизбежно ведет к нарушению стабильности микронеоднородного деформирования [7].
Процесс повреждения металла, связанный с зарождением и развитием трещин, можно разделить на три основные периода. В первом проходят процессы интенсификации деформаций по слабым микрообластям в со ответствии с присущими данной структуре материала закономерностями микронеоднородного деформирования, чем подготавливаются условия для развития микротрещин. Заканчивается данный подготовительный период лавинно нарастающим образованием разрозненных трещин, в большинстве не выходящих за размеры зерна. Такие повреждения для материала еще не являются опасными и практически не отражаются на статических характе- - ристиках. Во втором периоде превалирующим становится рост микротре щин в микронеоднородно деформирующейся среде. Условия слияния и продвижения трещин становятся зависимыми от направления встречаю щихся трещин и границ зерен. Это облегчает или затрудняет их дальнейшее развитие, пока они не перерастут в магистральную макротрещину со своим законом продвижения.
При прочих равных условиях можно ожидать, что более благоприятным для малоцикловой прочности является уменьшение неоднородности распре деления микродеформаций по структуре металла. На рис. 4.4 приведены графики распределения локальных деформаций на поверхности образца по длине реперной линии (база 20 мкм) для сплава ВТ-6 в исходном состоя нии и после поверхностного пластического деформирования (ППД) обкат кой роликами (по результатам автора и В.П. Тарасова). Коэффициент кон центрации локальных деформаций К'це для образцов, обработанных ППД, уменьшается почти в 2 раза (от 3 до 1,5), что ведет к увеличению долго-
Рис. 4.3. Графики распределе ния микронеоднородной де формации по длине реперной линии (база 10 мкм) в пер вом (д), втором (б) цикле растяжения-сжатия и их сум марная деформация в ^разгру женном состоянии (в)
Амплитуды циклических де формаций еа = ± 1%
Рис. 4.4. Распределение микро неоднородной деформации для образцов из титанового спла ва ВТ-6 с исходным состояни ем поверхности (а) и обрабо танных ППД (б) при степенях накопленной пластической де формации
1 - 3%, 2 - 6, 3 - 9%
200 000 000 000 /000 /200 £,мхм
Рис. 4.4
вечности (на верхнем плато кривой малоцикловой усталости) более чем
в10 раз.
Вобласти многоцикловой усталости основной причиной повышения цик
лической прочности при ППД считается наведение в поверхностном слое благоприятной эпюры сжимающих напряжений. При малоцикловых нагру жениях, особенно при больших перегрузках, когда имеются пластические деформации, роль остаточных напряжений снижается.
4.2. Статистические закономерности неоднородности деформаций и трещинообразования
Анализ условий образования разрушения при циклическом упругоплас тическом деформировании показывает, что в большинстве случаев моменту образования макротрещины длиной 0,5—2 мм, которую принято считать за критерий достижения разрушающего числа циклов [8], предшествует пе риод, когда на поверхности образца в различных зонах его рабочей базы в условиях однородного напряженного состояния образуются вначале отдельные, длиной 50—100 мкм, а затем рассредоточенные по значитель ной части поверхности, зачастую сливающиеся друг с другом микротрещи ны (рис. 4.5). Эти микротрещины, развиваясь в процессе деформирования, в конечном итоге вырастают в магистральную макротрещину, которая и обусловливает разрушение образца [9].
Наблюдения, проведенные за условиями и характером образования рас средоточенных микротрещин, показали, что их количество находится в корреляционной зависимости от характера разрушения. Так, в случаях выраженного квазистатического разрушения, когда число циклов до разру шения составляет величину до 10—20, микротрещины практически отсутст вуют, а процесс разрушения образца сосредоточивается в шейке. В области смешанного характера разрушений при Np = 30СН400 циклов, когда для всех рассматривавшихся форм циклов мягкого режима нагружения (треу гольной, трапецеидальной, двухчастотной) наблюдался смешанный характер разрушения с образованием определенной степени утонения шейки и уста лостной макротрещины, плотность количества трещин на единицу поверх ности образца в близлежащей к месту разрушения зоне оказалась макси мальной и для рассматриваемой в качестве примера стали Х18Н10Т, испы танной при 6505 С, составила величину 150—200 на 100 мм2 при их средней длине около 300—400 мкм. С ростом числа циклов до разрушения, что соответствует уменьшению величины циклической упругопластической деформации, как плотность образования, так и средняя длина рассредото ченных микротрещин несколько падает. Статистическая обработка разме ров образовавшихся к моменту разрушения образцов рассредоточенных по их поверхности трещин показала, что в целом для всего исследованного
диапазона долговечностей (до Np = 4 • 103 цикл) и рассмотренных режимов нагружения статистический ряд их длин в каждом отдельном случае описы вается нормальным законом распределения [10].
Рассмотренный характер образования отдельных рассредоточенных по поверхности образца микротрещин в процессе циклического упругопласти ческого деформирования может быть связан с известным и исследованным фактором неоднородности развития как циклических, так и односторонне накапливаемых местных пластических деформаций на различных участках рабочей базы образца [11, 12]. При этом установлено, что расположение участков с различным уровнем развивающихся в них деформаций носит случайный характер, а сами величины этих местных деформаций описыва ются нормальным законом распределения со средней величиной, в каче стве которой в данном случае выступает математическое ожидание, равное полной деформации, измеряемой интегрально на всей рабочей базе образца.
Проведенные в этих экспериментах измерения и наблюдения показали,


были наибольшими при растяжении. С ростом числа циклов нагружения происходит некоторое перераспределение местных деформаций между отдельными участками, однако зоны с повышенным уровнем деформации остаются. Аналогичным образом развиваются и односторонне накапливае мые пластические деформации, также обнаруживая с ростом числа циклов нагружения участки с сохранением повышенного уровня деформации, накопленной в сторону растяжения.
Средние значения пластических деформаций (циклических и односторон не накопленных), полученные суммированием по отдельным участкам, равным 0,5 и 5 мм, практически совпадают с величинами деформаций, определенных на базе 40 мм. Если охарактеризовать неоднородность как циклической, так и односторонне накопленной пластической деформации в цикле соответственно коэффициентами макронеоднородности цикличес
кой § и односторонне |
накопленной К ^е пластической деформации, опре |
|
деляемыми как |
|
|
“ ^/шах/^ |
и |
Кце — ^’шах/^» |
где 6imax — максимальная местная пластическая деформация в цикле; eimsix — максимальная местная односторонне накопленная деформация; 5 и ё~—соответственно их средние значения,то можно видеть (см.рис. 4,6,б), что наибольшая относительная неоднородность имеет место в первые (кро ме исходного) циклы нагружения, когда материал сильно упрочнен и уровни средних деформаций невелики. С увеличением числа циклов, а так же величины средних деформаций (как циклических, так и односторонне накопленных) коэффициенты неоднородности уменьшаются, стремясь к одному и тому же значению, которое при дальнейшем нагружении изменя ется незначительно, вплоть до появления микротрещин.
Полученные результаты измерения местных деформаций на отдельных (0,5 мм) участках базы образца представляют собой статистически предста вительный объем данных и могут быть обработаны с использованием со ответствующих вероятностных представлений. Осуществление такой обра ботки показало, что совокупность местных пластических деформаций отдельных участков базы образца подчиняется с достоверностью по крите рию Колмогорова в 99% нормальному закону распределения и математи ческое ожидание при этом равно соответствующей средней деформации.
На рис. 4.7 представлены кривые накопленной вероятности распределе ния местных циклических 5* и односторонне накопленных е* деформа ций. Видно, что с увеличением уровня средней деформации при нагружении в нулевом полуцикле увеличивается и значение среднего квадратичного отклонения величин местных деформаций (рис. 4.8, а ) , характеризующего наклон Кривых накопленной вероятности.
При Изменении знака нагружения (полуцикл сжатия, k = 1) рассеяние местных деформаций существенно уменьшается, и, как видно на рис. 4.7, наклон Кривой накопленной вероятности местных деформаций уменьша ется. При этом среднеквадратичное отклонение также резко уменьшается (см. рис. 4.8, а). С увеличением количества циклов нагружения рассеяние как в поцуцикле растяжения, так и в полуцикле сжатия уменьшается, а за тем стабилизируется и в конечном счете оказывается одинаковым для по-
О)
го
Рис. 4.7
Рис. 4.7. Кривые накопленной вероятности распределения местных циклических (j) и односторонне накапливаемых (б) пластических деформаций при циклическом де формировании образца из стали Х18Н10Т
луциклов растяжения и сжатия. Для испытанной стали Х18Н10Т стадия стабилизации наступила для выбранного уровня напряжений (оа = = 420 МПа, Np = 750 цикл) уже к 50-му циклу нагружения.
Для односторонне накопленных местных деформаций (см. рис. 4.7, б) рост числа циклов нагружения хотя и сопровождается некоторым уменьше нием рассеяния, однако оно не столь ярко выражено, как для местных цик лических деформаций, среднеквадратичное отклонение s е и коэффициент вариации v е стабилизируются уже к 10-му циклу нагружения, имея близ кое значения как для полуциклов растяжения, так и сжатия. Но следует иметь в виду, что в этом случае для стали Х18Н10Т практически не наблю далось накопления средних деформаций в сторону растяжения, и даже име ло место после 1-го цикла нагружения до 20-го цикла некоторое накопле ние деформаций в сторону сжатия на базе их измерения.
Если принять во внимание, что случайными величинами в нашем рас смотрении являются местные циклическая б/ и односторонне накапливае мая е/ пластические деформации, a Up , s и а —соответственно заданный
U(e>
Рис. 4.8. Изменение параметров нормального закона распределения величин местных циклических (а) и односторонне накапливаемых (б) пластических деформаций
Полуцикл: 1 —растяжения, 2 —сжатия
квантиль, среднее квадратичное отклонение и математическое ожидание данной совокупности, то с учетом, что а = 5 или а =~ё, упомянутые коэф фициенты неоднородности деформаций могут быть охарактеризованы как
K*ns = PpSs + 5)1 S И К*це = (Upse +ё)/ё.
Количественный анализ указанных преобразований показал, что наилуч шее соответствие величины рассматриваемых коэффициентов, определен ных по конкретным значениям средних и экстремальных местных деформа ций и с использованием приведенных статистических характеристик, име ет место при значении квантиля Up = 2,79, т.е. при вероятности р = 99,73%, соответствующей трем стандартным отклонениям.
В связи с известными представлениями, что деформационная неодно родность материала обусловливается его структурной неоднородностью, а последняя может быть охарактеризована данными о микротвердости на отдельных локальных участках образца, были выполнены соответствующие измерения микротвердости по образующим рабочей базы образца с шагом не более 0,5 мм и предпринята попытка установления корреляционной свя-
зи между данными о неравномерности развития локальных деформаций и неравномерности локальной микротвердости.
Измерения выполнялись на микротвердомере типа ПМТ-3 с нагрузкой на индентор в различных сериях этих измерений в диапазоне от 10 до 200 гс, а статистическая обработка этих данных и по величинам диагоналей отпе чатков (рис. 4.9, а) и по вычисленным значениям микротвердости (рис. 4.9, 6) показала, что они, так же как и рассмотренные данные о неоднород ности развития местных деформаций, подчиняются нормальному закону распределения. При этом было отмечено, что параметры нормального зако на распределения микротвердости изменяются немонотонно в зависимости от уровня нагрузки на индентор и от значения микротвердости (см. рис. 4.9). С увеличением нагрузки среднее квадратичное отклонение возрас тает, достигая максимума при нагрузке 100 гс, а затем убывает, стремясь к некоторому постоянному значению.
Относительное рассеяние (коэффициент вариации vHм) также изменя ется не монотонно. При нагрузках до 50 гс его значение убывает, что свя зано с увеличением точности измерения диагонали отпечатка, а существен ный разброс при малых нагрузках на индентор, например при 10 гс, объяс няется в основном сравнительно большой абсолютной погрешностью изме рения при малом абсолютном значении размера диагонали. Повышение наг рузки сопровождается увеличением коэффициента вариации, который дос тигает экстремального значения лри нагрузке 100 гс, а затем с ее дальней шим ростом падает, стремясь, так же как и среднеквадратичное отклоне ние, к некоторому устойчивому значению.
В зависимости от микротвердости, абсолютное значение которой опреде
ляется |
нагрузкой на индентор Р и диагональю отпечатка /, параметры |
SH и VH |
также изменяются немонотонно (см. рис. 4.9): коэффициент |
вариации уменьшается, а среднеквадратичное отклонение возрастает с
увеличением |
микротвердости приблизительно |
до |
2 103 МПа, а за |
|
тем |
s# и VH резко возрастают до значения |
микротвердости 2,15 |
||
103 |
МПа, |
соответствующей нагрузке на индентор |
100 гс, и в дальней |
шем снова падают.
Известно, что для измерения микронеоднородности структуры сталей оптимальной нагрузкой на индентор является нагрузка в 100 гс, которая обеспечивает достаточно высокую точность измерения диагонали на прибо ре ПМТ-3. Увеличение нагрузки приводит ко все большему усреднению ре зультатов, поскольку при больших нагрузках происходит сильное упрочне ние составляющих, имеющих низкую прочность и высокую пластичность, в результате рассеяние результатов уменьшается, и абсолютное значение мик ротвердости стремится к некоторому постоянному значению.
Введение в рассмотрение по аналогии с коэффициентами неоднородности деформаций понятий коэффициентов неоднородности структуры материа ла с использованием рассматриваемых характеристик диагоналей отпечат ков / и микротвердости Я д в виде /£д/ = ^тгх/Т и К Нц = ЯД/Я Д1позволяет провести соответствующие рассмотрения с использованием этих характе ристик. В указанных выражениях //тах иЯ мт|П— соответственно макси мальный размер диагонали отпечатка и минимальное значение микротвер дости; I и Яд —средние значения отпечатков и микротвердости (соответст-
\zoo
0 0 L,MKM
Рис. 4.9. Кривые накопленной вероятности распределения величин диагоналей отпечат ков (д) и микротвердости (б) на локальных участках базы образца Х18Н10Т, а также изменение параметров нормального закона распределения микротвердости (в) при различных уровнях нагрузки на индентор

/000 /500 2000 / / # , 51(1CL
~S0 |
I |
_1 |
PflC |
/00 |
/50 |
||
Рис. 4.9 (окончание) |
|
|
|
вующие математические ожидания I { |
и Hpi) . Причем коэффициенты неод |
нородности структуры по диагоналям, так же как и коэффициенты неодно родности деформаций, рассматриваются при положительных квантилях, а коэффициенты неоднородности структуры по измеренным значениям микротвердости рассматриваются при отрицательных значениях квантилей, поскольку наибольшую деформацию испытывают участки с наименьшей микротвердостью.
Если по аналогии с расчетными коэффициентами неоднородности дефор
маций К *М5 и К*це ввести расчетные коэффициенты неоднородности |
ве |
личин диагоналей отпечатков K*pi и микротвердости К*н ,то они также |
мо |
гут быть вычислены через параметры нормального закона распределения соответствующих величин в виде
к*ц1 = (Up S, + Ш * я м = НрЦНр + Up sHt) ,
где / и Нр — средние значения размеров диагоналей отпечатков и микро твердости; Sj и s# —среднеквадратичные отклонения совокупностей изме-
ренных значений. Коэффициент неоднородности микротвердости при этом по указанным соображениям рассматривается с отрицательными значения ми квантиля Up. Результаты вычислений этих коэффициентов показали, что наилучшее их соответствие значениям Крд и Кце с погрешностью не более 8% через их среднее значение К ^ е имеет место при Up = —2,79.
Таким образом, коэффициенты неоднородности циклической Кр& и на копленной Кре пластической деформации на стабилизированном участке процесса деформирования могут оцениваться по результатам измерения микротвердости через коэффициент неоднородности микротвердости
гг
Известно, что условием макроразрушения при малоцикловом нагруже нии является достижение уровнем суммарного повреждения критической величины, принимаемой равной d = 1,0 в соответствии с критериальным уравнением [14, 15] типа
N P |
1 |
Np |
е |
d = / |
------------ dn + |
/ |
--------- dn, |
о |
N [ea(и)] |
о |
ек |
где еа —уругопластическая деформация в цикле, складывающаяся из упру гой и пластической составляющих: еа = 5 + еу .
В общем случае при расчетах по данному уравнению используются сред ние значения деформационных характеристик 6 и е, измеряемых на всей базе образца, и предельное состояние определяется моментом образования магистральной трещины. Если неоднородность развития местных деформа ций охарактеризовать соответствующими коэффициентами неоднородности циклической и односторонне накопленной деформации Кр§ и Кре, являю щимися своеобразными коэффициентами концентрации местной деформа
ции по сравнению |
со средней, то величины соответственно циклической |
и односторонне |
накопленной пластических деформаций на отдельном |
участке ’’преимущественного” деформирования могут быть вычислены как 5/тах =Кр5 £ и eimax =Креё, где 8 и F — средние величины соответст вующих деформаций. Полученные таким образом деформационные харак теристики могут быть заложены в расчет, и в результате при решении при веденного критериального уравнения относительно числа циклов до разру шения Np будет вычислена долговечность до образования предельного сос тояния (микротрещины) на локальном участке образца с повышенной де формационной способностью.
С целью экспериментальной проверки такого предположения были про ведены испытания стали Х18Н10Т при мягком нагружении с трапецеидаль ной формой цикла при t = 650°С и аатах = 180МПа. На полирован ной поверхности образца по его образующей наносились риски с шагом 0,5 мм, по которым в процессе эксперимента с помощью металлографичес кого микроскопа, расположенного на крыше камеры испытательной уста новки, проводились измерения местных деформаций с наблюдением и фо торегистрацией поверхности образца. Полученные при этом результаты по казали, что характеры развития местной циклической 5/ и односторонне
накопленной |
пластических деформаций на отдельном участке, на кото |
||
ром |
в процессе нагружения была обнаружена трещина, и соответствую |
||
щих |
средних |
деформационных |
параметров 5 и е подобны между собой |
(рис. 4.10,а). |
|
|
|
Значения коэффициентов Кц5 |
и Кре для рассматриваемого участка (рис. |
4.10, б) после изменения в первых циклах в дальнейшем стабилизируются, несколько увеличиваясь, как и величины местных деформаций, лишь после образования на нем трещины (рис. 4.11), размер которой к моменту окон
чательного разрушения образца достигал / = 300 |
мкм. |
|
||
Вычисленное в этом случае число циклов |
до образования трещины |
|||
для рассматриваемого эксперимента с использованием |
полученных мест |
|||
ных значений |
иХде, а |
также кинетики |
средних |
деформаций (см. |
рис. 4.10) составляет NTp = |
1780 циклов, в то |
время как в действитель- |
Рис. 4.10. Кинетика средних (/) и местных (2) циклических (/) и односторонне на капливаемых (2) пластических деформаций (я), а также коэффициентов их неодно родности {б) при мягком режиме нагружения с выдержками образца из стали
Х18Н10Т
t = 650 °С, аа = 180 МПа, т = 5 мин
ности рассматриваемая трещина была обнаружена на 2000 цикле, когда ее размер составлял / ^ 90 мкм.
Таким образом, видно, что критериальная зависимость с использованием коэффициентов неоднородности местных деформаций позволяет доста точно удовлетворительно описать процесс возникновения трещин на отдель ных участках базы образца за соответствующее время до окончательного разрушения, которое в данном эксперименте произошло при Np3=2077 цик лов, а расчет дает Np = 2164 циклов. Рассматриваемая трещина, зарегистри рованная в зоне измерении местных деформаций, не развилась до магист ральной. Последняя образовалась на другом участке образца, находив шемся вне поля измерения локальных деформаций.
Таким образом, как следует из рассмотренных данных, рассредоточен ное образование микро- и макротрещин при циклическом упругопласти ческом деформировании может быть связано со структурной неоднород ностью материала, обусловливающей, в свою очередь, неоднородность развития местных циклических деформаций на различных его участках, величины которых подчиняются нормальному закону распределения. Для учета этой структурной неоднородности материала при оценке цикличес кой прочности образцов и элементов конструкций могут вводиться коэф фициенты неоднородности циклической и односторонне накопленной де формаций, определяемые по статистическим параметрам распределения со ответствующих величин или другим косвенным методом, в качестве ко-
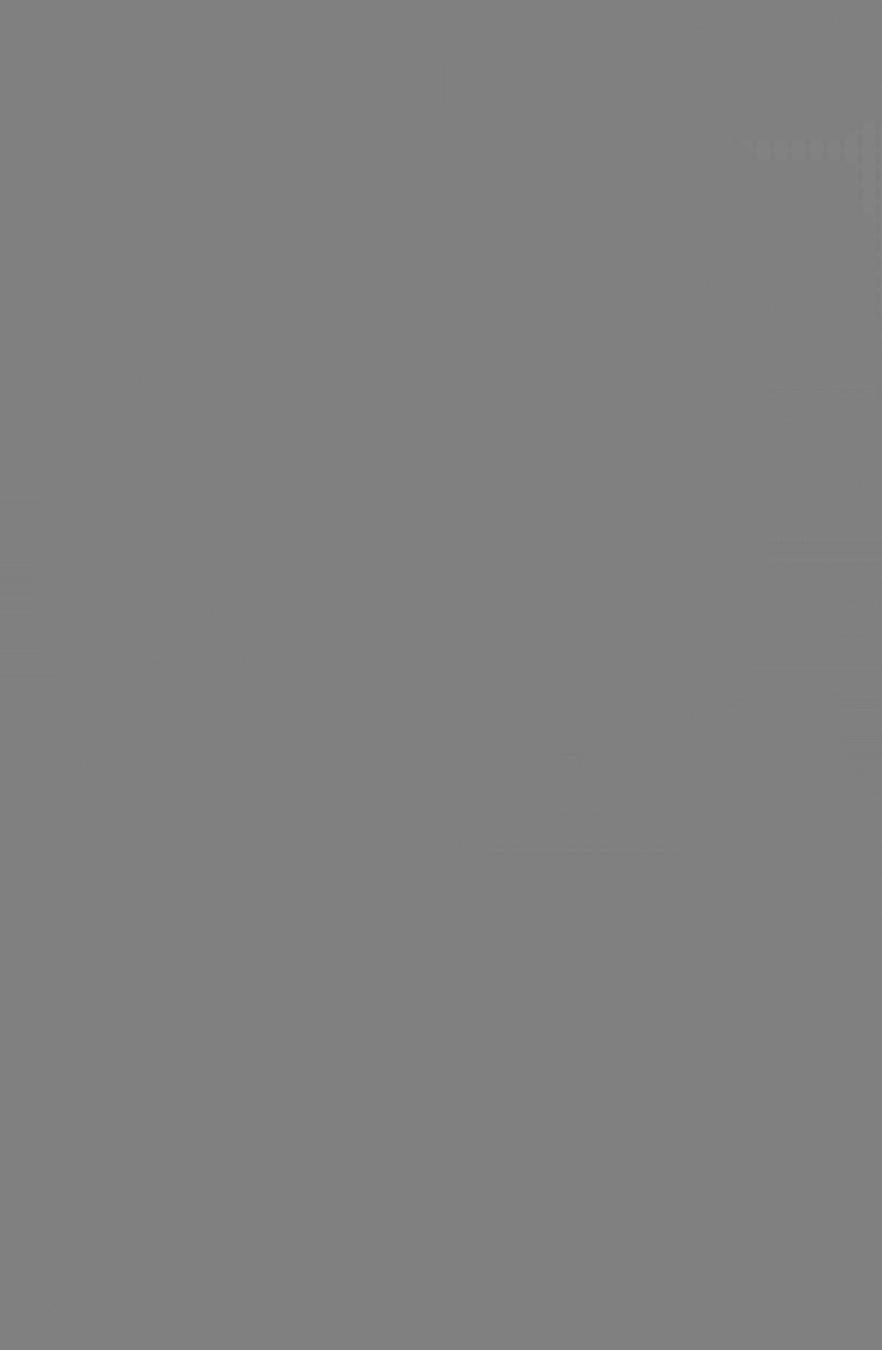
4 3 .Рассеяние малоцикловой долговечности
при однородном напряженном состоянии
Из обзора научных работ (см. п. 1.3) следует, что основное количество исследований, посвященных статистической оценке результатов малоцикло вых испытаний проведено для условий однородного напряженного состоя ния . В основном они касаются вопросов оценки рассеяния долговечности до появления усталостной трещины, до достижения трещиной определен ной длины или до окончательного разрушения. И лишь в отдельных рабо тах рассматривается статистическая оценка диаграмм циклического упру гопластического деформирования или параметров этих диаграмм и прово дится расчетное определение рассеяния долговечности с введением в крите риальные уравнения рассеяния ОМС материала.
При статистической оценке малоцикловой долговечности до появления усталостной трещины N 0 и разрушения Np в проведенных работах в основ ном проверялось соответствие результатов исследований нормальному, лог нормальному распределениям и распределению Вейбулла [16—18] и др. В работе [16] с целью надежной статистической оценки характеристик сопротивления малоцикловой усталости определение законов распределе ния ОМС и характеристик малоцикловой усталости (деформационных и прочностных) делалось для контрастных по своим циклическим свойст вам материалов (упрочняющихся —алюминиевый сплав Д16Т1, разупрочняющйхся —низколегированная сталь 15Х2МФА, стабильных —среднеугле родистая сталь 45).
Как и следовало ожидать, разброс результатов при оценке по коэффи циенту вариации для малоцикловой усталости меньше по сравнению с раз бросом при многоцикловой усталости. Выявлено [16] , что при жестком нагружении коэффициент вариации не зависит от уровня нагружения, а при мягком нагружении этот коэффициент растет с увеличением уровня для ясех исследованных материалов. По-видимому, как считает автор ра боты [16] , это является следствием изменения формы диаграммы цикли ческого деформирования,т.е. наличием повышенных вариаций ширины пет ли упругопластического гистерезиса при возрастании уровня нагружения по сравнению с аналогичными вариациями при более низких уровнях, что и вед$т к возрастанию разброса долговечности.
При обработке результатов с использованием нормального и логнор мального распределений для некоторых материалов наблюдался нижний порог Чувствительности. Проверка соответствия экспериментальных дан ных определенному закону распределения проводилась, как и в большинст ве работ по многоцикловой усталости, с использованием графического представления результатов на вероятностной бумаге, построения гисто грамм 1 критериев согласия (со2) , а также сопоставления основных статис тических параметров: коэффициентов вариаций, асимметрий и эксцесса для нормального и логнормального распределений.
Анализ гистограмм для мягкого и жесткого нагружений показал, что для всех исследованных материалов и уровней нагружения существует положительная асимметрия, а с увеличением выборки вид гистограммы приближается к нормальному распределению. Статистический анализ рас сеяния долговечности показал значительно меньший разброс долговечности по сравнению с разбросом параметров диаграмм циклического деформиро
вания. Увеличение объема выборки как при мягком, так и при жестком нагружении ведет к более четкому соответствию статистического ряда нормальному распределению. Однако из анализа статистических характе ристик для трех законов распределений долговечности признано необходи мым пользоваться логнормальным законом распределения.
В работе [16] также было проведено определение корреляционных свя зей между ОМС материалов и параметрами малоцикловой усталости (дол говечностью N 0, Np, параметрами циклического деформирования) , позво ляющих повысить надежность построения кривых малоцикловой усталос ти с использованием механических характеристик. Получена значимая корреляционная связь.
Из анализа результатов расчета коэффициентов корреляции следует, что долговечность N 0 и Np при жестком нагружении хорошо, почти прямоли нейно коррелировала с механическими характеристиками для исследован ных материалов, но наилучшая корреляция получена у стали 15Х2МФА с о0у2 и 5 Л,у стали 45 —с ф ,о02 и Sk , а у алюминиевого сплава Д16Т1 — с оь . Интересно отметить,что для сталей 15Х2МФА и 45 применение множи теля о0 2/оь У Ф незначительно увеличивает, а у сплава Д16Т1 уменьшает коэффициент корреляции между N 0, Np и Ф(Ро,г1°ъ)-
При мягком нагружении корреляционная связь между Np и механичес кими характеристиками почти прямолинейная. Особенно тесно долговеч ность коррелирует с ф.
Для определения возможной величины рассеяния результатов испыта ний, а также оценки уровня вероятности полученных кривых малоцикло вой усталости В.В. Ларионовым и В.В. Евдокимовым были проведены испытания большого числа образцов (20 штук на один уровень напряже ния) из стали 16Г2АФ на трех уровнях напряжений. Образцы изготав ливали из листового проката толщиной 16 мм и имели ширину рабочей части 80 мм.
Результаты испытаний приведены на рис. 4.12. Видно,что с повышением уровня напряжения (рис. 4.12,я)рассеяние долговечностей (в отличие от [16]) уменьшается, поскольку имеет место переход от чисто усталостных разруше ний, связанных слокальными разрушениями в неблагоприятно ориентирован ных зернах металла, к малоцикловым, определяющимся макропластическими деформациями значительных объемов, величины которых контролируют ся в процессе испытаний. Так, при уровне напряжений о = 300 МПа макси мальная разница в долговечностях составила 7,5 раза, а при о = 500 МПа — 32 раза.
Статистическая обработка полученных результатов показала, что имеет мес то логнормальный закон распределения (см. рис. 4.12,в) , а также позволи ла получить кривые усталости в зависимости от заданной вероятности раз рушения. На рис. 4.12,5 в качестве примера приведены кривые мапоцикловой усталости стали 16Г2АФ для вероятности разрушения 50, 30 и 5%. На рис. 4.12, а показана кривая усталости, полученная ранее на ограничен ном числе образцов. Видно, что эта кривая, полученная испытаниями одно го образца на каждом из порядка 10 уровней напряжений, примерно соот ветствует кривой 50%-ной вероятности разрушения.
В работе [16] и других наряду с экспериментальными кривыми усталос ти материалов по параметру вероятности Р получена и их расчетная оцен-
|
|
|
|
|
|
<>,ша |
|
|
|
ш |
а |
— |
|
|
|
ш |
|
|
|
SOO |
|
|
|
/ |
\ \ |
|
|
||
|
' ч |
&»• |
|
|
500 |
Р5Х£ |
|
|
|
ООО |
|
\ |
|
|
ООО |
|
|
||
|
4 4* |
> |
nr-Si7 |
|
|||||
зоо |
|
|
|
JOO |
|
% |
|
||
|
|
|
|
|
|
|
|
|
|
|
|
|
|
|
|
|
|
J |
ь |
zoo/ и -------------- „ |
|
|
|
|
200 з |
|
|| С |
I |
|
|
Г |
4 0 0 0 |
4 |
|
|||||
//7J 2 4 0 0 /0 *2 0 0070s Z |
70s Z |
0 0070 Z V0070s Z 000A7 |
Рис. 4.12. Сопротивление малоцикло вой усталости стали 16Г2АФ
а — кривая малоцикловой усталос ти и экспериментальные точки по дол говечности для трех серий испытаний; б — кривые малоцикловой усталости по параметру вероятности разруше ния, в — функции распределения ма лоцикловой долговечности для различ ных уровней нагружения
ка на основе ряда известных в литературе уравнений кривой малоцикловой усталости — уравнений Коффина, Мэнсона, Лэнджера, их модификаций, норм прочности и других предложений [1, 19—22]. Систематические иссле дования по построению расчетных вероятностных кривых малоцикловой усталости в научной литературе пока отсутствуют.
Уравнение Коффина определяет зависимости долговечности при жест ком нагружении от размаха пластической деформации ер в цикле
m |
1 |
1 |
(42) |
ep N m * |
- I n ------ - |
||
р |
2 |
1 - ф |
v ' |
В работе |
[16] |
использовалось |
модифицированное уравнение Коффина |
e N « 'P * C lp . |
|
(4.3), |
В отличие от зависимости Коффина а1р < т и С1р < Сф. Константы ос1р и С\р Предварительно можно определить по механическим свойствам материала:
ао,2 |
100 |
а 1р = 0,17 + 0,55 ф ------, |
С1р = 0,75 а 1р In — ----- — |
оь |
100 — \рк |
Степенные уравнения Мэнсона и Лэнджера наиболее широко применяют ся для описания кривых сопротивления разрушению при циклическом на гружении и выражают связь мжду полной упругопластической деформа цией е =* ер + еу и числом циклов до разрушения. Для случая нагружения
с заданными амплитудами деформаций при симметричном цикле они име ют следующий вид:
|
1 / |
|
100 |
\ |
0’6 |
0Ь |
|
|
еа = |
- ( i n |
------------ ) |
N ~ 0,6 |
ь уу — 0,12 |
(4.4) |
|||
+ 1,75----- iV0 |
||||||||
|
2 |
\ |
100 -— фк / |
|
Е |
|
||
еа = |
1 |
|
1 |
1п- |
100 |
0,4 <>ъ |
(4,5), |
|
- |
|
N т |
|
+ |
||||
|
4 |
|
|
100- ф к |
|
|
где N —число циклов до разрушения; Е — модуль продольной упругости, МПа; фк —относительное сужение площади поперечного сечения образца при статическом растяжении; оъ — предел прочности при статическом рас тяжении; т —постоянная,зависящая от свойств материала.
Уравнение кривой циклического разрушения при асимметричном цикле жесткого нагружения в величинах условных упругих напряжений (о* =еаЕ ) имеет вид [19]
|
Е |
100 |
Оа = |
In |
(46) |
4 N m(l +r*)/( 1 - г * ) |
№ - ф к |
+ l + ( ^ - i K ) ( l + г • ) / ( ! - Г •) ’
где г* — коэффициент асимметрии цикла деформации (г* = emin/emax); а_ 1 —значение предела выносливости (МПа) на базе N 0 = 10б.
Для аналитического описания кривой усталости при симметричном
мягком нагружении может быть использована зависимость |
|
|||
е(о) = |
1 |
100 |
|
(4.7) |
In |
100 - |
фь |
||
|
N m 1 |
|
||
где |
—исходная деформация нулевого полуцикла нагружения; т х — |
|||
константа материала, |
зависящая от его механических характеристик; |
Фь —равномерное сужение поперечного сечения (при напряжениях, равных пределу прочности).
В случае асимметричного цикла напряжений г уравнение принимает
вид [19] |
|
|
|
АЕ |
1 - г |
100 |
(43) |
о * = ----------------------- In |
----------------- + |
||
2 |
2 |
1 0 0 -i|/6 |
|
+__________f - i _________
1 +(0 - i / a b)(l+ r)/(l - r )
Для условий симметричного нагружения заданными деформациями для расчетной кривой использовалось также расчетное уравнение из новых
норм прочности |
|
|
|
0,5 In [1/(1 |
-* * )] |
(4.9) |
|
(4Л00,5 |
E(4N) 0,05 |
||
|
Располагая на основе статистической обработки кривыми распределения ОМС материалов при соответствующих температурах и вводя в указанное
/02 2 |
¥ 6 S /0 J 2 |
¥ S 0 Г0 ¥ 2 0Q |
Рис, 4.13. Сопоставление расчетных вероятностных кривых (сплошные линии) мало цикловой усталости при жестком нагружении с экспериментальными (пунктир) для стали 15Х2МФА
Расчет по зависим ости: а — (4 .5) , б — (4.9) , в — (4.3)
уравнение определенные вероятностные значения этих характеристик получаем расчетные кривые малоцикловой усталости, соответствующие различной вероятности разрушения.
По зависимостям (4 3 ), (4 3 ), (4.9) были построены кривые мало цикловой усталости 1, 10, 30, 50, 70, 90 и 99% вероятности разрушения с использованием вероятностных значений а0>2, оь, фк и етв координатах logё"0 —logN0 и loge0 —logN0 для сталей 15Х2МФА и 45.
На рис. 4.13 приведено сопоставление вероятностных расчетных и экспе-
Рис. 4.14. Сопоставление расчетных вероятностных кривых малоцикловой усталос
ти |
жесткого нагружения с экспериментальными |
(пунктир) |
для стали |
15Х2МФА |
||||
|
1, 1' - расчет |
по |
зависи м ости |
(4 .5 ); |
2, 2' - (4 .9) ; 3 , 3 ' - |
(4 .3) ; 1 - |
3 - расчет |
|
с |
использован и ем |
норм и рован н ы х характери сти к; |
l ' —З' — расчет с исп ользован и ем |
|||||
справочны х данны х; |
4 — расчет |
(4 .5) с |
прим енением пе = 2 ; |
5 — расчет с прим ене |
||||
нием Лдг = 10 по (4 .5) |
|
|
|
|
|
|
риментальных кривых малоцикловой усталости по уравнениям (4.3), (4.5), (4.9) для стали 15Х2МФА при жестком нагружении. Из рис.4.13,а,б
следует, что |
угол наклона ширины полос разброса экспериментальных |
и расчетных |
кривых примерно сопоставимы для зависимостей (4.5) и |
(4.9), однако экспериментальные кривые расположены ниже расчетных. Расчетные кривые, построенные по зависимости (4 3 ), целиком попадают в зону экспериментальных (см. рис. 4.13, в) ,но сопоставление делает за труднительным ’’обратное” расположение расчетных вероятностных кри вых в области долговечностей N 0 > 200 + 400 циклов, которое вызывает ся особенностями расчета вероятностных значений констант а и С. Такое же сопоставление расчетных и экспериментальных кривых жесткого нагруже ния для стали 45 показало, что в этом случае экспериментальные кривые расположены выше расчетных, но расчет по зависимости (4.3) лучше соот ветствует эксперименту.
Аналогичная картина наблюдается и при сопоставлении расчетных и экс периментальных кривых малоцикловой усталости в абсолютных коорди натах loge0-logA^0.
На рис. 4.14 для стали 15Х2МФА сопоставлены экспериментальные кривые малоцикловой усталости 1, 50 и 99% вероятности разрушения с расчетными, построенными по зависимостям (4.5) и (43) с использова нием нормированных механических характеристик, определенных по изло женной методике (см. п. 3.1), справочных механических характеристик и кривых малоцикловой усталости, определенных с использованием при меняемых коэффициентов запаса nN = 10 по циклам и пе = 2 по деформа циям. При построении последних использовались кривые, построенные по нормированным характеристикам и зависимости (4.5).
Как следует из рис. 4.14, для стали 15Х2МФА кривые малоцикловой усталости, построенные по нормированным механическим характеристи кам, проходят выше экспериментальной кривой 99% вероятности разру шения. Те же кривые, построенные с использованием справочных механи ческих характеристик, расположены в полосе долговечностей между кри выми 1 и 50%. Этого и следовало ожидать, так как нормированное значе ние ф = 76,72% для стали 15Х2МФА превышает экспериментальное значение и соответствует ему при вероятности 15%, а справочное ф = 50% соответст вует вероятности 0,0003% экспериментального ф. Из-за такого ’’высокого” расположения расчетных кривых малоцикловой усталости по отношению к экспериментальным также довольно высоко проходят кривые, построен ные с использованием коэффициентов запаса = 10 и пе = 2 .___
Для стали 45 расчетные кривые, построенные с использованием как нор мированных, так и справочных механических характеристик,расположены значительно ниже экспериментальных.
Попытки в [16] оценить расчетным путем экспериментальные кривые малоцикловой усталости при мягком нагружении дали удовлетворитель ные результаты только для области усталостного разрушения. Для допол нительного обоснования методик оценки рассеяния характеристик мало циклового разрушения в зонах концентрации для сталей Х18Н9 (серии со средней долговечностью 3 - 102 и 104 циклов) и 15Х2НМФА (1,5 • 103 циклов) при нормальной температуре проведен анализ зависимостей между ОМС и экспериментальными (N3Kcn) долговечностями до образования трещин N 0, окончательного разрушения Np и развития трещины A N = = Np — N 0. Анализ проводился по конкретным ОМС (статические микро образцы из недеформированной части образца с концентратором) и долго вечностям для каждого образца статистической серии.
Для зависимостей ob- N 3Kcn (N0, AN, Np) , для стали 15Х2НМФА и (7^—Арцсч (A/Q, AN, Np\ Фк~Мрасч для стали Х18Н9 для имеющихся объемов выборок (обычно п = 20) полученные значения г являлись значи мыми и по абсолютной величине г изменялись от 03 до 0,8. В остальных случаях получены значения г обычно менее 0,4. Это указываете частности, на то, что при малоцикловом нагружении определяющей оказывается связь между комплексами ОМС и долговечностью, а не связь между отдельными ОМС и долговечностью.
Проведенный в работе [16] анализ по сопоставлению расчетных и экспе риментальных вероятностных кривых малоцикловой усталости показыва ет при принятых в работе допущениях, что построение кривых малоцикло вой усталости по общим аналитическим зависимостям в отдельных случаях может привести к существенным погрешностям. В связи с этим при таких расчетах необходимо иметь хотя бы экспериментальную кривую 50% ве роятности разрушения. В дальнейшем необходимо продолжение системати ческих экспериментальных вероятностно-статистических исследований по малоцикловой усталости и уточнение расчетных подходов для оценки рассеяния характеристик разрушения как при однородном, так и неодно родном напряженном состояниях.
4 4 . Экспериментальная и расчетная оценки малоцикловой долговечности в зонах концентрации напряжений
по параметру вероятности появления трещины
Выше были рассмотрены имеющиеся работы по оценке рассеяния долго вечности при малоцикловой усталости. При-этом практически все работы являются экспериментальными и выполнены для условий однородного напряженного состояния на стадии образования трещины или для оконча тельного разрушения.
Для неоднородного напряженного состояния исследования по экспери ментальной и расчетной вероятностной оценке характеристик малоцикло вой усталости и механики малоциклового разрушения в литературе практи чески отсутствуют. Для получения таких оценок в данной главе и в п. 5.2 приведены результаты систематических малоцикловых испытаний в статис тической постановке, выполненных в ИМАШ АН СССР по методике, изло женной в п. 2.1 для сталей Х18Н9 и 15Х2НМФА при нормальной и повышен ных (эксплуатационных) температурах. Получены экспериментальные и расчетные оценки рассеяния скоростей и долговечности по моменту обра зования трещин и долговечности при развитии трещин по параметрам их длин, раскрытий и скоростей роста. Проведено обоснование соответ ствия их экспериментальных функций распределения теоретическим за конам.
Графический и расчетный анализ (статистики и рассчитанные величины критериев) представлены в п. 5.2.
Стадия развития трещин от зон концентрации напряжений при малоцик ловой усталости может составлять значительную часть от общей долговеч ности и быть сопоставимой со стадией момента образования трещин.
На рис. 4.15 показаны кривые малоцикловой усталости в зависимости от заданной вероятности разрушения для плоского образца с отверстием из стали Х18Н9 при нормальной температуре (по результатам испытаний 65 образцов) [23]. Одиночные малоцикловые испытания показаны точка ми 1, а средние значения долговечностей в каждой из трех серий (пример но по 20 образцов в серии) показаны точками 2. Штриховыми линиями нанесено семейство кривых усталости по моменту образования трещин N 0 длиной 0,3 мм в диапазоне вероятностей 1—99%, сплошными линиями по казан момент разрушения Np для уровней вероятности Р, равных 1,50 и 99%. Видно, что экспериментальные точки по разрушению в основном хорошо описываются кривой 50%-ной вероятности разрушения, а все поле разброса данных укладывается в диапазоне от 1 до 99% вероятности.
Количественные данные по вариации долговечностей N 0 и Np в соот ветствующем диапазоне вероятностей Р, а также вариации долговечностей от 1% вероятности образования трещин N0 до 99% вероятности разруше ния Np представлены в табл. 4.1 и составляют от 2,5 до 43 раз, что прибли женно учитывается в нормативных документах [19,24] запасами по долго вечности, равными 10—20 при использовании минимальных (гарантирован ных по ТУ) характеристик основных механических свойств.
Для получения расчетной оценки рассеяния долговечности по моменту образования трещин N 0 при номинальном мягком нагружении проводился расчет по деформационному критерию разрушения с введением в него
78
Af/fa
ж
270 ^ ----------- |
L- J |
70s |
s |
70¥-------/7,цам |
^ |
s |
Рйс. 4.15. Экспериментальные кривые малоцикловой усталости по параметру вероят ности Р для образцов с концентратором (аа - 2,4) для стали Х18Н9 при нормаль ной температуре
вероятностных характеристк ОМС [23, 25, 26]. При этом определение количества циклов до появления трещин N 0 в зоне концентрации проводи лось по уравнению типа Лэнджера для кривой усталости из норм прочности для условий жесткого нагружения [19]
In |
1 |
(4.10) |
|
4N ? U + (1 +/■•)/(!- г*) ’ |
1 - ф к |
1 + ( o _ i/f f b ) ( l + /••)/(! - г*) ’
где Е — модуль продольной упругости, МПа; фк — относительное сужение площади поперечного сечения образца при статическом растяжении; а_ i — предел выносливости гладкого образца при циклическом растяжении—
Т а б л и ц а 4.1.
Диапазоны изменения долговечностей при статистических испытаниях стали Х18Н9 при нормальной температуре
У ровень напряже- |
Вариации долговечностей в диапазоне вероятн ости |
||
ни я оп, МПа |
(1 * 99)%ЛГ„ |
(1 -5- 99)%Np |
1%ЛГ0 Ч- 99%Np |
|
|||
350 |
2,85 |
2,53 |
3,69 |
285 |
3,82 |
2,76 |
4,78 |
228 |
3,16 |
2,71 |
3,45 |
сжатии, МПа; оь — предел прочности при статическом растяжении, МПа; т6о — показатель степени; г* — коэффициент асимметрии местных дефор
маций; Од —условное упругое напряжение, равное произведению местной деформации (упругой или упругопластической) на модуль продольной упругости (а^ = еЕ). Индекс р здесь и далее означает, что данная величи на определяется уровнем вероятности Р значений ОМС.
Расчет по схеме жесткого нагружения в зоне концентрации является приближением имевшегося в эксперименте режима мягкого нагружения по номинальным напряжениям. В связи с этим проводилась оценка долго вечности N 0 в зоне концентрации и для условий мягкого нагружения по зависимости из норм прочности [19]. Это в первую очередь необходимо для стали 15Х2НМФА, являющейся циклически разупрочняющейся.
о* |
O L \ - A E 1 - r 0 |
I n |
1 |
(4.11) |
-------------------2 N™°» 2 |
+ |
|||
|
1 - |
Фь |
|
_________0-1____________
1 +(ог_ 1/аг>)(1 + ra)/( 1 - г а) ’
где аа —теоретический коэффициент концентрации напряжений; А —пара метр диаграммы циклического деформирования; га — коэффициент асим метрии местных напряжений; фь — равномерное относительное сужение площади поперечного сечения образца при статическом растяжении. Равно мерное сужение фь можно определить по формуле [27]
1 — а 0,2 !°Ь
Фьр =Фк
Skl°b —а 0 ,2 1°Ъ
Значение показателя maQ определяется выражением
1 - г а
то0р
2
Показатель асимметрии местных напряжений г - равен
|
|
о"(0) |
о ( 1 ) |
г- = |
m in |
—S |
|
и ш ах |
° ш ах |
||
°Р |
ш ах |
Ош ах |
В формулах (4.10) и (4.11) значение предела выносливости о _ г опре деляется выражениями:
° - 1р =(0,54 —2 • 10"4 оь)оъ |
при оъ > 7 0 0 МПа, |
||
° - 1р =0,4 оъ |
при |
аь <700МПа. |
|
Значения показателя те^ в формуле (4.10) равны |
|||
т0() =0,5 |
при |
400 МПа < о ь < 700 МПа, |
|
ир |
|
|
|
те0р = 0,36 + 2 10’4 оъ при |
700МПа < о ь < 1200 МПа. |
Условные упругие напряжения а* и коэффициент асимметрии опреде
ляли по методике, изложенной в [27] |
|
|||||
|
ё (1) Е |
|
ё (о) |
- ё (1) |
|
|
°а. |
шах |
|
сшах |
max |
|
|
|
г; |
= |
» ( 0 ) |
|
||
|
|
|
|
max |
|
|
? (0) |
_g(°>jr<0>. |
-О ) |
= |
(1)„(1) |
9 |
|
стахр |
п |
е 9 |
та хр |
сп |
||
где |
|
^тах ~ номинальные и максимальные местные дефор |
мации в нулевом и первом полуциклах деформирования; К ^ и А*1* - коэффициенты концентрации деформаций. При этом предполагалось, что
величина деформации в первом полуцикле e'^Vx W1я обеих сталей опре деляется для диаграммы циклического деформирования, стабилизирован ной в первом и последующих полуциклах.
Учет кинетики деформаций в каждом полуцикле нагружения в случае разупрочнения материала для стали типа 15Х2НМФА (15Х2МФА) пока зал [27] изменение N 0 в меньшую сторону на 15—35% по сравнению с рас четом только для нулевого и первого полуциклов деформирования (схе ма жесткого нагружения). Там же показано, что образование трещин в зонах концентрации при симметричном цикле номинальных напряжений, меньших единицы, для разупрочняющихся сталей связано с накоплением в основном усталостных поверждений. Предположение о жестком дефор мировании в зонах концентрации с учетом кинетики деформаций только в нулевом и первом полуциклах для циклически разупрочняющихся мате риалов дает завышение расчетной долговечности. Для цикличности упроч няющихся сталей это предположение приводит к появлению дополнитель ного запаса прочности и не влияет на его величину для циклически ста бильных сталей.
В таком расчете предполагается значение относительного циклического предела текучести по циклам S ty принимать постоянным для материала и
равным и определять из эксперимента по первому полуциклу дефор мирования для условии однородного напряженного состояния.
При степенной аппроксимации диаграмм деформирования величина коэффициентов концентрации деформаций Ке и концентрации напряже ний Ка определяется по зависимости Нейбера, модифицированной Н.А. Ма-
хутовым [27]:
2
_________<*(71 +т________________ |
|
- |
(4.12) |
|
Ос^ j n ( l - m ) [ l - ( a n - l / a a ) ] / ( l + m ) |
ПРИ |
° п ^ 9 |
||
|
к е =
ер
|
|
1 - т |
|
1+т |
д-1+т |
|
ист |
и п |
яг |
-т)[ 1 - (оп - l/aCT)]/(l + т > |
2т
а1 +т
~чл(1-т)[1-(<7„-1/аст)т/(1 + т)
(<Хо°п)
при а „ < 1 , |
(4.13) |
при Оп > 1, |
(4.14) |
6. Зек. 1830 |
81 |
Кгг |
а 2т f (l +m) |
при Оп < 1. |
------------------------ ----- --------------- =----------------------- |
||
°Р |
^ ( 1 - т ) / ( 1 + т ) / а о ря ^ п ( 1 - т ) [ 1-(<тл -1/с«а ) ] т / ( 1 + т ) |
|
|
п |
|
(4.15) Здесь т — характеристика упрочнения материала при степенной аппрокси мации диаграммы деформирования, определяемая для нулевого или к-то полуцикла нагружения; п —показатель степени, обычно равный 0,5.
Показатель упрочнения в нулевом т (0)р и к-м полуцикле т (к)р при нормальной температуре может быть определен через значения ОМС и пара метры диаграммы деформирования по формулам [27]
/п. |
|
л пс |
lg(Sk/o0'2) |
|
(4.16) |
|
т(0)р |
= 0,75- |
1 |
|
|
||
|
|
lg |
In |
1 |
-ФкJ |
|
|
|
|
||||
|
|
o0t2/E + 0,2 |
- |
1 - 1 |
||
|
|
1(Г2 |
|
|
||
|
|
|
2 |
■?(0)m(0) |
|
|
m(k)p |
= |
[ |
|
|
|
при S T =£2. |
|
|
,» ) » ( • ) + |
^ (? < ° > |
- |
e«»m <°>) F(fc)l |
|
|
|
lg, |
||||
|
|
О J * |
|
ST |
|
J |
Для зон концентрации напряжений величину т (к) определяют по этой же формуле при замене величины относительной номинальной деформа ции ~ё£°) на величину относительной максимальной местной деформа-
Ц истах'
Функция F(k)p для упрочняющихся материалов равна [28]
т р = !/**> |
(4.17) |
где а — параметр обобщенной диаграммы деформирования. Функция F(k) для разупрочняющихся материалов определяется выражением [28]
Нк)р = ех р [Ц (* -1)], |
(4.18) |
где 0 —параметр обобщенной диаграммы деформирования.
Расчетная оценка рассеяния указанных параметров проводилась по формулам п. 3.2.
Таким образом, проведя статистическую обработку результатов ста тических испытаний и располагая экспериментальными функциями рас пределения ОМС (<*0,02» 0о,2» оь, и S k), можно, используя изложен ную методику, рассчитать по формулам (4.10) и (4.11) число циклов до появления трещины N 0 для заданного уровня вероятности Р. Кроме того, также учитывалась степень зависимости ОМС друг от друга.
Значения ОМС обеих сталей в предположении их соответствия нормаль ному закону распределения для нормальной и повышенных температур представлены в табл. 4.2. При этом в расчет также вводилось рассеяние величины модуля упругости (обычно 3S n _ i = 104 МПа).
Результаты расчета по моменту образования трещин N 0 для стали Х18Н9 при нормальной температуре по уравнению для жесткого нагружения представлены на рис. 4.16. Для проверки соответствия расчетных и экспе риментальных результатов проведено несколько вариантов расчета [25,
82
Т а б л и ц а 4.2
Значения основных механических свойств сталей Х18Н9 и 15Х2НМФА при нор мальной и повышенных температурах для различных уровней вероятности Р
р,% |
|
|
Прочностные ОМС, МПа |
|
Пластич |
|
|
|
|
|
|
ность, % |
|
|
а0,02 |
а0,2 |
°Ъ |
Sk |
Е ■10'* |
Фк |
|
|
|
Х18Н9, 20° С |
|
|
|
1 |
163 |
249 |
723 |
1 754 |
19 220 |
68,73 |
50 |
186 |
267 |
682 |
1 902 |
20 000 |
72,44 |
99 |
209 |
285 |
641 |
2 050 |
20 780 |
76,15 |
Х18Н9, 650° С
1
50
99
—
—
—
113 |
273 |
914 |
14 300 |
75,58 |
149 |
301 |
708 |
15 500 |
68,85 |
185 |
328 |
502 |
16 700 |
62,12 |
|
|
15Х2НМФА (с исходной т/о) * 20 ° С |
|
|
||
1 |
574 |
634 |
740 |
1 562 |
20 225 |
76,78 |
50 |
647 |
698 |
791 |
1 679 |
21 000 |
74,71 |
99 |
720 |
762 |
842 |
1 796 |
21 775 |
72,64 |
|
|
15Х2НМФА (с дополнительной т /о ), 350 °С |
|
|||
1 |
359 |
417 |
540 |
1 322 |
18 225 |
70,47 |
50 |
433 |
484 |
595 |
1 131 |
19 000 |
66,59 |
99 |
507 |
551 |
650 |
940 |
19 775 |
62,71 |
*Т/о —термическая обработка.
26, 29], при этом полученная величина N 0 для условий мягкого нагруже ния в зоне концентрации много больше, чем для условий жесткого нагру жения. Полученные коэффициенты вариации v для условных расчетных распределений сравнимы с экспериментальными.
Расчетные варианты 7, 2 и 3 (см. рис. 4.16) отличаются друг от друга способом получения значений а0 02 и (расчетное или эксперименталь ное). Так для варианта 1 обе величины экспериментальные (значения пре дела текучести а0>02 определялись с допуском 0,02% на пластическую де формацию). Для варианта 2 обе величины расчетные, значения величин ао,02 H S* определялись по формулам [27,30]
|
|
|
_1____ |
|
|
а0,2 |
|
]Т |
(4.19) |
а0,02. |
10- 2 +ст0>2)",(0) |
|
||
_(Е 0,2 |
|
|
||
Sk = a*(0,8 + 2,06^)(X 18H 9), |
Sk = аь{1 + 1,4фк) (15Х2НМФА). |
|||
|
|
|
|
(4.20) |
Для варианта 3 значения ст002 |
— расчетные, значения S k — экспери |
|||
ментальные. Вариант |
4 является |
оценкой корректности расчетов типа |
Рис. 4.16. Экспериментальные и расчетные функции распределения долговечности по моменту образования трещин N 0 для стали Х18Н9 при нормальной температуре
1—3. Для этого варианта значения ОМС те же, что и для варианта 7, но они брались из эксперимента для данного конкретного образца, а не из экспе риментальных функций распределения ОМС для одинаковых уровнений вероятности Р. При этом коэффициент вариации v для варианта 4 сопоста вим со значением для варианта 1. Это позволяет сделать вывод о возмож ности использования расчетов типа вариантов 1—3 вместо расчетов по конкретным статическим свойствам образцов.
Для вариантов 1—4 значения показателя упрочнения в к-м полуцикле т (к) вычислялись при значениях функции F{k) = 1 и коэффициенте КА =
=0,16 в формуле для А. Для варианта 5 способ получения значений а002
иS k тот же, что и для варианта 2 (расчетный), однако значения F(k) вычис
лялись по формуле (4.17). При этом значение количества полуциклов к в этой формуле принималось равным количеству полуциклов для поло вины экспериментальной долговечности N 03ксп, взятой равной среднему значению долговечности для каждого уровня нагружения.
Объемное напряженное состояние, возникающее при циклическом де формировании из-за стеснения деформаций в зоне концентрации образ ца, учитывалось в расчете, согласно [27], путем уменьшения номинальных напряжений и располагаемой пластичности материала. Так, в случае мак симальной объемности (условия плоской деформации) усредненные вели чины второго и третьего относительных главных напряжений, отнесенные
к первому главному напряжению по нетто-сечению образца, равны а2 = = 0,14 и а3 = 0,07. Тогда коэффициент повышения первого главного на-
пряжения в зоне концентрации за счет объемности равен
ё(°)
^lmax
шах |
j W |
= у / 2 /[ (1 - а 2 ш а х ) 2 + (<*2шах ^З ш а х ) + ( ша х |
|
u max |
|
(4.21)
Коэффициент снижения предельных пластических деформаций в зоне концентрации De max, в свою очередь, равен
кр
Dб шах |
|
(4.22) |
Л п а х О |
Сг2шах |
^ З ш а х ) |
где кр = 0,8 1,2._ |
|
_ |
При величинах о2 = 0,14 и а3 = 0,07 значения/тах и Demjlx составляют: / max = М15, Demах = 0,89 при кр = 1,2. Эти значения величин принима лись для уровней напряжений оп равных 350 и 285 МПа. Для уровня напря жений оп = 228 МПа принято / тах = 1,08, £>втах = 0,97. Для условий плоского напряженного состояния можно принять / тах = 1,066, Demax =
= 0,99 (рг =0,14, о3 =0).
На рис. 4.16 кривая 2 1 соответствует расчету по варианту 2 без учета объемности. Как следует из рисунка, учет объемности увеличивает долго вечность N о, несмотря на уменьшение располагаемой пластичности. Кривая 211 соответствует расчету по варианту 2 для условия плоского напряжен ного состояния, которому при имеющихся диаметре отверстия и толщине (d = 7 мм, h = 6 мм) должно соответствовать напряженное состояние образца.
На рис. 4.16 видно, что расчет долговечности по вариантам 1-5 дает подобные результаты. Ближе всего к эксперименту (по среднему значе нию) лежат расчеты по вариантам 1 и 4. Приближенный учет поцикловой кинетики упрочнения материала (вариант 5) по сравнению с вариантом 2 несколько увеличивает долговечность и уменьшает коэффициент вариа ции у. Однако все варианты (1-5) дают результаты не в запас прочности. Использование зависимостей Нейбера для определения значений коэффи циентов концентрации упругопластических напряжений и деформаций вместо формул (4.12) —(4.15) общей картины существенно не меняет (см. рис. 4.16, кривые 2IV ).
Одной из возможных причин расхождения эксперимента и расчета яв ляется неучет неоднородности распределения максимальных локальных циклических пластических деформаций стали Х18Н9. В соответствии с работой [12] коэффициент макронеоднородности циклической пластичес кой деформации Ке можно принять равным 1,35 и соответственно увели чить значение условного упругого напряжения в формуле (4.10).
При использовании в расчете значения Ке = 1,35 (вариант 2111) получе ны значения долговечности А^0 до 2,5 раз меньшие, чем по варианту 211 Другой причиной расхождения результатов может быть то, что, по дан ным работы [31], при местных относительных упругих напряжениях в зоне концентрации о > 3,0 расчеты по зависимостям Г. Нейбера и Н.А. Махутова [27] приводят к систематическому и существенному снижению де
формаций по сравнению с расчетом по методу конечных элементов (МКЭ). В дальнейшем, при увеличении величины о , результаты расчета деформа ций по зависимостям Н.А. Махутова приближаются к результатам, полу ченным по МКЭ. Из рис. 4.16 следует, что при увеличении нагрузок рас
хождение экспериментальных и |
расчетных |
значений долговечности N 0 |
|
сначала возрастает (серия |
103 |
циклов), а |
затем уменьшается (серия |
300 циклов), что соответствует указанному выводу работы [31]! |
|||
Коэффициент вариации |
долговечности v |
по появлению трещины JV0 |
в зависимости от уровня нагружения изменяется от 2,5 до 7% для расчет ных вариантов и от 2,5 до 4,5% по результатам эксперимента для логнор мального закона распределения. При этом ближе всего к эксперименталь ному оказался коэффициент вариации для расчета по вариантам 3 и 5. Можно отметить также уменьшение коэффициентов вариации с увеличе нием долговечности.
Расчетная и экспериментальная оценки рассеяния долговечности N 0 в зоне концентрации напряжений для стали 15Х2НМФА (с исходной термо обработкой) при нормальной температуре показаны на рис. 4.17.
В связи с тем, что сталь 15Х2НМФА. является циклически разупрочняющейся, была использована приближенная схема расчета, по которой
для |
относительных номинальных напряжений оп < 1 принималось, |
что |
||
величина относительного |
циклического предела текучести S ^ |
= 2, |
а в |
|
зоне |
концентрации S ^ |
=1,5 (значению, наблюдавшемуся для |
однород |
ного напряженного состояния при упругопластическом деформировании). Расчетная деформация в первом полуцикле деформирования определялась с учетом разупрочнения материала путем замены в функции F(k) первого полуцикла на полуцикл к, соответствующий половине значения экспери ментальной долговечности N 0. Значение коэффициента кА в формуле (3.4) принималось 0,16. Кривая 1 соответствует расчету по уравнению мяг кого нагружения (4.11) без учета объемности, кривая 2 —с учетом объем ности для условий плоской деформации; кривая 3 соответствует расчету по уравнению жесткого нагружения (4.10) без учета объемности, кри вая 4 — с учетом объемности для условий плоской деформации. При рас чете значения величин ОМС а0 2 и S k определялись по формулам (4.19) и (4.20).
Штриховыми линиями на рис. 4.17 показаны расчетные значения N 0, полученные с учетом зависимости экспериментальных значений Аоэксп от уровня вероятности Р, т.е. значения функции F(k) в этом случае вычис лялись для чисел полуциклов к, определяемях не 50%-ной средней экспе риментальной долговечностью А^0эксп, а долговечностью УУ0эксП = / ( / >), зависящей от уровня вероятности.
В расчетах по формулам мягкого (4.11) и жесткого (4.10) нагружений при определении показателей степени mOQ и т€о величина показателя асим
метрии местных напряжений га при к = А^0эксп была приравнена значению га при к - 1, а значения величины те для разных уровней вероятности принимались равными ее значению при Р = 50%.
Из рис. 4.17 следует, что расчетные значения долговечности N6Q для стали 15Х2НМФА при нормальной температуре для условий жесткого на гружения в зоне концентрации соответствуют экспериментальным, для
/0* |
10 2 |
/0 J |
/Уд, ЦИКЛ |
Рис. 4.17. Экспериментальные и расчетные функции распределения долговечности по моменту образования трещин N 0 для стали 15Х2НМФА при нормальной температуре
Обозначения в тексте
условии мягкого нагружения получаются существенно меньшие долговеч ности Na .
Для стали 15Х2НМФА при температуре 350 С (с дополнительной термо обработкой) расчет долговечности по моменту появления трещин N 0 показан на рис. 4.18. Так же как и при нормальной температуре, расчет проводился по нулевому и первому полуциклам деформирования, при этом деформация первого полуцикла определялась с учетом разупрочнения материала для числа полуциклов к, равного половине экспериментальной долговечности N 03Kcn. Использовалась та же приближенная схема расче та с упругим номинальным деформированием в первом и нулевом полуциклах, по которой при оп < 1 величина S fr = 2 для номинальных деформа ций первого полуцикла и S*T = 1,7 в зоне концентрации.
При расчетё использовались значения кратковременных ОМС при 350°,
так |
как |
до 400° С для стали 15Х2НМФА деформации ползучести можно |
не |
учитывать [32]. В отличие от расчета при нормальной температуре в |
|
формулу |
(4.16) вместо коэффициента 0,75 вводится величина 1—0,3 ф*к. |
На рис. 4.18 кривая 1 соответствует расчету по уравнению мягкого на гружения без учета объемности; кривая 2 — с учетом объемности для условий плоской деформации; кривые 3 и 4 получены по уравнению жест кого нагружения соответственно без учета объемности и с учетом ее для условий плоской деформации. При этом расчет проводился по варианту типа 2, т.е. значения величин ОМС и $к пРинимались расчетными по формулам (4.19) и (4.20). Значение коэффициента кА в формуле (3.4) принято равным 0,16. Штрихпунктирными линиями показаны расчетные
Рис. 4.18. Экспериментальные и расчетные функции распределения долговечности по моменту образования трещин N 0 для стали 15Х2НМФА при температуре 350 ° С
Обозначения в тексте
значения N 0i полученные при учете зависимости N оэксп от уровня вероят ности Р.
В целом можно отметить, что для расчета долговечности N 0 для стали 15Х2НМФА при нормальной и повышенной температурах эксперимент соответствует расчету по варианту 2 в предложении жесткого нагружения в зоне концентрации. При учете кинетики деформаций в нулевом и первом полуцикле, определенной с учетом разупрочнения материала, расчетные значения долговечности N€Q незначительно отличаются от эксперименталь ных значений. При этом для величин номинальных напряжений аном < 1 можно принять значение кА равным 0,16. Значения величин а0>02 и $ к можно определять указанным расчетным способом.
При расчете долговечности N 0 для стали Х18Н9 при 650 °С не обходимо учитывать наличие деформаций ползучести и изменение во времени ха- • рактеристик основных механических свойств.
Влияние температур и времени деформирования г учитывается введе нием в уравнение типа Лэнджера характеристик а ^ , и 5^т , зависящих от времени. Эти зависимости аппроксимируются степенными уравнениями
[32], в которые входит эквивалентное время ползучести: |
|
°ьт = °ь0<7оЛ\Г |
(4.23) |
|
Yko VO 1 4 |
» |
(4.24) |
|
|
|
(4.25) |
где T0 - |
время испытаний до разрушения при кратковременном |
стати |
|
ческом |
нагружении |
(т0 « 0,05 ч для пластичных сталей); т0ъ и т ^к - |
параметры кривой длительной прочности и пластичности стали, зависящие от температуры. Для аустенитных сталей типа 18-8 при 650 °С в соответст
вии с работой [32] для времен г, составляющих 104-5 |
104 |
ч, та |
= |
|
= 0,1119тФк =0,128-^0,178. |
|
и ф*к |
* |
|
Если для рассматриваемого ресурса т, известны величины |
|
, т0 |
||
таь = |
lg (^ 04 f.)/lg(T*/ro)- |
|
|
|
щ к = |
ы ф !со1'Р1.Ш(т.1то)- |
|
|
|
Подобным образом учитывается влияние температуры и времени нагру жения на остальные характеристики, используемые для расчета по моменту
образования трещины ао,02т >°о,2Т»S \ 7 , ф*Ьт, что позволяет в дальнейшем определить параметры диаграмм циклического деформирования А*, С\ , В \ , т\ (к) и величину коэффициентов концентрации напряжений и дефор маций К*6т и К*от [32].
При симметричном цикле в условиях мягкого нагружения и высоких температур напряжения изменяются непропорционально деформациям. Для определения эквивалентного (по повреждаемости от ползучести) вре мени цикла тцэ и эквивалентного времени ползучести т следует учитывать скорость деформирования и нагружения в полуциклах растяжения и сжа тия, различную чувствительность материалов к выдержкам при растяже нии, а также соотношение времен выдержки и полуцикле растяжения и сжатия [32].
По результатам эксперимента получено эквивалентное время ползу чести (в ч ):
^ —^цэ^Оэксп — 1»51.
Проведенные испытания на длительную прочность стали Х18Н9 данной плавки при 650 °С позволили уточнить значения показателей степени m0b>
тфк и mSk в уравнениях (4.23) —(4.25). Они |
оказались соответственно |
|||||
равны: 0,098; |
0,0107 и 0,0838. Уточненное значение |
показателя степени |
||||
Шфк оказалось меньше рекомендованного в работе [32] |
от 12 до 17 раз. |
|||||
Это говорит о необходимости экспериментального уточнения этих |
показа |
|||||
телей для конкретного исследуемого материала. |
|
|
|
|
||
При испытаниях получены кривые |
длительной прочности, |
пластич |
||||
ности и величина рассеяния долговечности для |
18 образцов (серия) при |
|||||
уровне напряжений адл = 110 МПа (рис. 4.19, |
точки |
4) |
со следующими |
|||
выборочными |
средними значениями: долговечности "г |
= |
1409 ч, пластич |
|||
ности ~ф*к = 61,7%, истинного сопротивления разрыву S kr |
= 299 МПа, где |
|||||
SkT. = сгдл/(1 |
— ФkTf )• На рисунке |
также показана |
граница разброса |
Рис. 4.19. Изменение пластичности фк при испытании на длительную прочность для сталей Х18Н9 и Х18Н10Т при 650 ° С
1 — сталь Х18Н10Т; 2 — сталь Х18Н9; 3 —то же, длительное статическое растяжеиие; 4 — то же, серия 18 образцов из данной плавки; 5 —то же, две плавки, ЦКТИ
±3S„_i для кратковременных значений пластичности фк и длительных
значений ф*кт.
Таким образом, уравнение кривой по моменту образования трещин с учетом влияния высоких температур, времени процесса деформирова ния или времени выдержки в цикле тъ для жесткого нагружения может быть записано в следующем виде:
E f |
In |
|
1 |
оа* |
|
+ |
|
1 +Ге |
|
То |
|
+ ------- |
|
1 - |
( •^О^цэ |
1 - г е |
|||
1 + _______°J-\____________ |
(4.26) |
||
1 +ге |
|||
°ь а [то/(М0 |
7-цэ)] |
m ° b |
1 - Г е |
Уменьшенные с учетом эквивалентного времени ползучести г = 1,51 ч значения ОМС стали Х18Н9 при 650°С позволяют рассчитать по изложен
ной методике долговечность по |
моменту появления трещины N 0. Значе |
||
ние относительного циклического предела текучести |
полагалось по |
||
стоянным и равным |
= 2 |
(по результатам эксперимента при одно |
родном напряженном состоянии).
На рис. 4.20 показаны экспериментальные и расчетные значения долго вечности N 0i полученные в предположении жесткого нагружения в зоне концентрации (при расчете по уравнению мягкого нагружения значения долговечности N0 в данном случае получаются много больше).
Расчетные условные распределения долговечности N 0 получены с учетом упрочнения материала для к = N 03Kcn = 650 циклов, при этом значения величин "00,027 и S \ T - расчетные, где S \ T =о*Ьт(0,8 + 2,06i//*T). Кри вые 2 и 2Гсоответствуют расчету без учета объемности и с учетом ее для
условий |
плоской деформации соответственно |
(/тах = 1,115, DemBX = |
|
= 0,89), |
значение коэффициента кА |
= 0,16. Кривые 1 и I 1 (те же условия |
|
объемности) получены для расчета |
по ОМС |
для данного конкретного |
|
образца. |
|
|
Из рис. 4.20 видно, что вместо расчетов типа 1 можно использовать расчеты типа 2; в целом для стали Х18Н9 при 650 °С расчеты дают значе ния долговечности N0 не в запас прочности. Так же как и для расчетов при нормальной температуре, возможными причинами являются неучет неоднородности циклической пластической деформации и систематическое завышение расчетной долговечности N 0 при высоких уровнях местных относительных упругих напряжений (а > 3,0) [12, 31]. Для расчета по варианту 2п с введением коэффициента неоднородности циклической пластической деформации Ке = 1,35 [12] значения долговечности N0 меньше до 2,5 раз по сравнению со значениями, полученными по вариан ту 2'
Для выяснения степени влияния рассеяния отдельных характеристик ОМС (а0>2, фу оь) на рассеяние расчетной долговечности N0 для стали Х18Н9 при нормальной температуре (рп = 285 МПа —долговечность 103 цикл.) и температуре 650 °С и стали 15Х2НМФА при 350 °С были прове дены соответствующие расчетные оценки. Использовался вариант расче та типа 2. При этом значения ОМС материала o0t2,o b и фк условно пред-
полагались независимыми и поочередно вводились в расчет с величиной
среднеквадратического отклонения S n_ i, равной 0,5 |
или 1,5 |
от экспе |
|
риментального |
условно принятого за единицу. |
Значения |
же S n_ i |
двух других статистических характеристик принимались равными еди нице.
Получено, что по уменьшению степени влияния на рассеяние расчет
ной |
долговечности N 0 рассеяние ОМС распределилось следующим обра |
зом: |
для обеих сталей для условий жесткого нагружения в зоне концен |
трации — в порядке о0 2 , Фк и °ъ> ДЛЯ мягкого нагружения для стали 15Х2НМФА при 350 ”С - аь, ст0>2, Фк при о„ < 1 и а0,2, оь, фк при а„ > 1.
В целом можно отметить, что расчетные оценки рассеяния долговеч ности по моменту образования трещин N0 для условий жесткого нагруже ния в зоне концентрации для обеих сталей при нормальной и повышенных температурах в основном удовлетворительно соответствуют эксперимен тальным величинам рассеяния. Расчет долговечности N 0 проводился по нулевому и первому полуциклам деформирования и в дальнейшем ма териал считался или стабилизировавшимся, или вместо первого полуцикла для приближенного учета кинетики деформаций в расчет через функцию числа полуциклов F(k) вводился к-й полуцикл для к =N03KCTl. При этом полагалось, что величина S ^ равна .
Изложенная методика, основанная на деформационном критерии мало циклового разрушения, позволяет получить расчетные оценки рассеяния долговечности N 0 при наличии экспериментальных рассеяний ОМС мате риала. При проведении расчетов также необходимо учитывать степень и вид зависимости значений ОМС друг от друга. При этом расчетные оценки N 0, полученные по значениям ОМС для конкретных образцов серии, в основном удовлетворительно соответствуют расчетным оценкам, полу ченным по значениям ОМС из экспериментальных функций их распределе ния при одинаковом уровне Р, если увеличению прочностных свойств ма териала о0 2 и оъ соответствует уменьшение пластичности (при этом значения величин o0f02 и $к принимаются расчетными по приведенным формулам).
Необходимо отметить, что при использовании зависимостей Нейбера вместо формул (4.10) и (4.11) получены меньшие наклоны расчетных кривых долговечности N 0 (см. рис. 4.16). Учет объемности напряженного состояния в зоне концентрации приводит для сталей Х18Н9 и 15Х2НМФА к увеличению значений расчетной долговечности N 0 до двух раз по срав нению с расчетами без учета объемности.
Рекомендованное в работе [27] значение кл = 0,16 можно использо вать для стали Х18Н9 при нормальной температуре и для стали 15Х2НМФА для нормальной и повышенной температур (при расчете N0 по уравнению
жесткого нагружения), |
что дает результаты, |
сравнимые с экспери |
ментальными. |
|
|
Учет неоднородности |
циклических пластических деформаций для стали |
Х18Н9 при нормальной и повышенных температурах позволяет сущест венно (до 2,5 раз) уменьшить расхождение расчетных и эксперименталь ных значений долговечности N 0 для уровня вероятности Р = 1%.
1.Прочность при малоцикловом нагружении / Под ред. С.В. Серенсена. М.: Наука, 1975. 285 с.
2.Стрижало В.А. Циклическая прочность и ползучесть металлов при малоцикловом нагружении в условиях низких и высоких температур. Киев: Наук, думка, 1978. 238 с.
3.Гурьев А.В., Кондратьев О.В. Закономерности пластической деформации углеро дистых сталей при малоцикловом нагружении // Тез. докл. и сообщ. V Всесоюз. симпоз. ’’Малоцикловая усталость — критерии разрушения и структура материа лов” (Волгоград, сент. 1987 г .) . Волгоград: ДТНТО, 1987. Ч. 1. С. 22-24.
4.Гурьев А.В., Савкин А.Н. Роль микропластических деформаций в развитии уста лостных повреждений в металлах // Механическая усталость металлов: (Материа лы VI междунар. коллоквиума). Киев: Наук, думка, 1983. С. 122-129.
5.Гурьев А.В., Кукса Л.В. О роли микронеоднородной деформации в разрушении и
формировании пластических свойств двухфазных поликристаллических спла вов II Физ. и хим. обраб. материалов. 1968. № 4. С. 97-103.
6. Гурьев А.В., Ми шарев Г.М., Хесин ЮМ- Об обратимости пластической деформа ции при повторно-переменных нагружениях // Металловедение и прочность мате риалов: Тр. Волгоград, политех, ин-та. 1970. Т. 2. С. 62-70.
7. Микроструктурные вопросы развития трещин малоциклового разрушения / А.В. Гурьев, Б.Б. Чечулин, Ю.Д. Хесин, Е.П. Богданов, А.С. Столярчук // Тез. докл. и сообщ. IV Всесоюз. симпоз. ’’Малоцикловая усталость - механика раз рушения, живучесть и материалоемкость конструкций” (Краснодар, сент. 1983г.). М.: ЦП НТО Машпром, 1983. Вып. 1. С. 137—142.
8.Методы испытаний при малоцикловом нагружении. Методические указания. Научно-техническое сотрудничество стран - членов СЭВ. М.: МЦНТИ, 1986. 88 с.
9.Романов А.Н., Гаденин М.М. Особенности рассредоточенного трещинообразования
всвязи с неоднородностью развития деформаций при малоцикловом нагружении II Структурные факторы малоциклового разрушения металлов. М.: Наука, 1977. С. 39-50.
10.Романов А.Н., Гаденин ММ. Неоднородность развития пластических деформаций
при малоцикловом нагружении и методы их измерения // Температурная микро скопия металлов и сплавов. М.: Наука, 1974. С. 62-68.
11.Водопьянов В.И., Гурьев А.В. Закономерность микр ©неоднородного развития пластической деформации в поликристаллических сплавах // Тр. Волгоград, поли техи. ин-та, 1973. Вып. 3. С. 5-16.
12.Серенсен С.В., Романов А.Н., Гаденин ММ. Влияние структурной неоднородности на развитие пластической деформации при малоцикловом нагружении // Струк турные факторы малоциклового разрушения металлов. М.: Наука, 1977. С. 22—38.
13.Романов А.Н.. Гаденин М.М., Юнин ВМ. Высокотемпературные вакуумные про граммные установки для исследования процессов малоциклового разрушения. //
Температурная микроскопия металлов и сплавов. М.: Наука, 1974. С. 13-19.
14.Махутов Н .А .В оробьев А.З., Гаденин ММ. и др. Прочность конструкций при малоцикловом нагружении. М.: Наука, 1983. 272 с.
15.Расчеты прочности элементов конструкций при малоцикловом нагружении. Мето дические указания. Научно-техническое сотрудничество стран - членов СЭВ. М.: МЦНТИ, 1987. 42 с.
16.Базарас Ж.Л. Статистические оценки сопротивления деформированию и разруше нию при малоцикловом нагружении: Автореф. дис.. . . канд. техн. наук. Каунас, 1983. 21 с.
17.Гусенков А.П., Лукин Б.Ю. Прочность при малоцикловом нагружении гибких металлических рукавов // Пробл. прочности. 1972. № 1. С. 98-104.
18.Iida К., Inoue Н. Life distribution and design curve in low cycle fatigue. Tokyo, 1973.
39 p. (Pap. Ship Res. Inst.; N 45).
19. Нормы расчета на прочность элементов реакторов, парогенераторов, сосудов и трубопроводов атомных электростанций, опытных и исследовательских ядерных реакторов и установок. М.: Металлургия, 1973. 408 с.
20.Трухний А .Д ., Степанов А.Д. Статистический анализ кривых малоцикловой уста лости II Машиноведение. 1978. № 4. С. 82-88.
21.Шрон Р.З., Щапова В.В. Статистический анализ распределения механических свойств стали марок 22К и 16ГНМ в барабанах котлов высокого давления // Энергома
шиностроение. 1981. № 1. С. 35-38.
22. Звездин Ю.А., Тимофеев Б.Т., Федорова В.А., Чернаенко Т.А. Вероятностно-ста тистический подход к оценке долговечности сварных узлов энергетического обо рудования II Тез. докл. Всесоюз. науч.-техн. сим поз. с участием специалистов стран - членов СЭВ (Владимир. 18-20 нояб. 1986 г.). М.: ЦП НТО Машпром, 1986. С. 71-75.
23.Махутов Н.£., Зацаринный В.В., Новиков В.А. Исследование возникновения и распространения трещин малоцикловой усталости в зонах концентрации напряже
ний в статистическом аспекте // Завод, лаб. 1983. № 4. С. 68-73.
24.ASME boiler and pressure vessel code, Sec. Ill // Appendices, 1986. Div. 1. 663 p.
25.Махутов H.A., Зацаринный В.В., Новиков В А. Особенности статистических подхо дов к оценке малоцикловой прочности и долговечности // Надежность и долго вечность машин и сооружений. Киев: Наук, думка. 1984. Вып. 6. С. 42-51.
26.Механика малоциклового разрушения / Под ред. Н.А. Махутова, А.Н. Романова. М.: Наука, 1986. 264 с.
27.Махутов Н.А. Деформационные критерии разрушения и расчет элементов кон струкций на прочность. М.: Машиностроение, 1981. 272 с.
28.Гусенков А.П. Прочность при изотермическом и неизотермическом нагружении. М.: Наука, 1979. 295 с.
29.Махутов Н.А., Зацаринный В.В., Новиков В.А. Оценка малоцикловой долговеч
ности в зонах концентрации с учетом рассеяния статических и циклических свойств // Усталость материалов и конструкций: Тр. Междунар. конф. стран —чле нов СЭВ. Прага, 1984. Т. 1. С. 197-204.
30.Золотаревский В.С. Механические испытания и свойства металлов. М.: Металлур гия, 1974. 304 с.
31.Гусенков А.П., Хорошилов В.Н., Котов П.И. и др. Интерполяционные подходы к расчету упругопластических деформаций в локальных зонах элементов конструк ций в связи с оценкой малоцикловой прочности // Машиноведение. 1986. № 6. С. 66-75.
32.Махутов Н.А. Кинетика развития малоциклового разрушения при повышенных температурах // Исследования малоцикловой прочности при высоких температу рах. М.: Наука, 1975. С. 99-123.
33.Погребняк Я.Я. Исследование циклической ползучести сталей Х18Н9 и Х18Н9Т: Автореф. дис. . . . канд. техн. наук. Рига, 1975. 30 с.
Г л а в а 5
СТАТИСТИЧЕСКИЕ ЗАКОНОМЕРНОСТИ ОБРАЗОВАНИЯ И РАЗВИТИЯ ТРЕЩИН МАЛОЦИКЛОВОЙ УСТАЛОСТИ
5.1. Образование и развитие трещин в материалах с дефектами типа пор и включений
Методы расчета инженерных задач основаны, как правило, на детерми нированном подходе к оценке долговечности. На практике часто прихо дится сталкиваться с изменением свойств, что и является главной причиной статистического разброса, наблюдаемого при испытании на усталость. С точки зрения надежности это явление имеет важное значение.
В большинстве современных вероятностных подходов учитывается глав ным образом случайность параметров нагружения, свойства материала, ха рактеризующие долговечность до разрушения и до образования трещины определенной величины, трактуются либо как константы, либо как слу чайные переменные с малыми коэффициентами вариации.
Имеется небольшое число работ, в которых предпринята попытка вве дения статистических характеристик в инженерные методы расчета. В ра боте [и с целью получения расчетной оценки рассеяния долговечностей по моменту образования трещин проводится расчет по деформационному кри терию [2] с введением в него вероятностных характеристик основных ме ханических свойств материала [3].
Процесс возникновения трещин, происходящий за счет накопления пов реждений, и последующее разрушение зависят от ряда конструктивных, технологических и эксплуатационных факторов. Количество, размеры и конфигурация появляющихся усталостных трещин не могут быть опреде лены однозначно и зависят от размеров и формы детали, величины ампли туды напряжения и условий воздействия среды. Но даже для одинаковых, тщательно контролируемых условий эксперимента [4, 5] коэффициент ва риации долговечности по росту усталостных трещин достигает 20%. Поэто му можно считать, что долговечность как по моменту зарождения трещины, так и по моменту разрушения имеет сложную вероятностную природу. Для обеспечения надежности работы конструкций и прогнозирования их долго вечности целесообразно проводить исследования закономерностей возник новения и роста трещин в статистической постановке.
При коррозионно-усталостном нагружении циклическая долговечность в большей степени определяется зарождением и ростом множества мелких трещин и их слиянием. Микродефекты, являющиеся потенциальным источ ником зарождения трещин, распределены по поверхности независимо и случайно. Плотность распределения дефектов имеет экспоненциальную или степенную функцию [6].
Усталостную долговечность материала можно теоретически рассчитать,
если знать статистическое распределение дефектов и их чувствительность к разрушению [7, 8]. Для оценки чувствительности к разрушению важным является выяснение распределения усталостных трещин по форме и разме рам на различной стадии повреждаемости. В качестве одного из определя ющих параметров может быть принят корень квадратный из площади де фекта, спроектированного на направление, перпендикулярное направлению максимального напряжения (y/F) .
Исследование особенностей зарождения многочисленных трещин как на воздухе, так и при воздействии 3%-ного водного раствора NaCl проводили на плоских образцах из стали 45 размером 5X10 мм. Испытания проходили в условиях жесткого нагружения при симметричном чистом изгибе [9]. В ходе исследования методами металлографии определяли плотность и рас пределение трещин на поверхности, их размеры и конфигурацию в продоль ном и поперечном сечениях при определенном числе циклов нагружения и проводили анализ распределения дефектов по параметру глубины, раскры тия и
Исследование формирования дефектов при коррозионно-усталостном нагружении показало, что форма и конфигурация реальных дефектов слож ны и разнообразны, большая часть их трехмерна. На поверхности образца размером в продольном сечении 5X20 мм образуется от 30 до 200 трещин различных размеров в зависимости от амплитуды деформации, условий испытания и числа циклов нагружения.
Анализ соотношения длины /. глубины h и раскрытия 5 дефектов пока зал, что эти соотношения колеблются в пределах Л//= 0,1-К,5 и h/5 =
= 0,2^5, причем при значениях длин трещин более 300 мкм соотношение h/l приобретает устойчивое значение, приблизительно равное 0,4—0,7.
На рис. 5.1 представлено изменение y/F в зависимости от глубины трещи ны при амплитуде деформации 0,15%. При малых амплитудах деформации 0,13—0,15% происходит множественное образование усталостных трещин, что облегчает возможность их слияния и способствует снижению цикли ческой долговечности. Сравнение разуплотнений в процессе циклического деформирования на воздухе и в среде показало, что при испытании на воз духе при больших амплитудах деформации зарождается большее количество трещин, которые растут независимо.
В процессе исследования определялись функции распределения размеров трещин при долговечности составляющей (0,6—0,9) Np по параметру глу бины, раскрытия и yJF (рис. 5.2). Оценка параметров распределения осно вывается на известных методиках статистической обработки [10, 11]. Гра фическое представление функции распределения и статистическая проверка гипотез с помощью ^критерия показали, что могут быть приняты в ка честве статистической модели логарифмически нормальное распределение и распределение Вейбулла—Гнеденко [10], но последнее менее удовлетво рительно описывает результаты опытов при больших размерах трещин.
В работах [7, 8] при определении распределения циклической долговеч ности при напряжениях, близких к пределу выносливости, для описания распределения числа дефектов использовано /3-распределение, а дла описа ния усталостной долговечности материала с одним дефектом —трехпара метрическое распределение Вейбулла. При этом не учитывается материал и условия испытания.
Рис. 5.2. Экспериментальные функции распределения размеров дефектов, образовав шихся в результате циклического деформирования по параметру v/F* (7), раскрытия б (2) и глубины h (3) на стали 45 после испытания в растворе NaCl при еа = 0,15%
Точки относятся к \J~F
Металлографические исследования показали, что форма трещин в попе речном сечении близка к полуэллипсу, вытянутому вдоль поперечного се чения образца, В поперечном сечении трещины имеют треугольную, трапе циевидную или полуэллиптическую формы. Таким образом, в процессе цик лического деформирования образуются объемные дефекты, которые мож но рассматривать как поверхностные поры.
В связи с обоснованием критериев безопасности и ресурса циклически нагруженных деталей целесообразно применение различных моделей к оценке долговечности и разрушения на стадии зарождения и распростране ния трещин. С целью моделирования процесса разрушения материалов с поверхностными дефектами в виде пор производились испытания образ цов с искусственными дефектами в виде лунок различных размеров.
Испытания материалов с дефектами производились на образцах из ста ли 45, стали 08Х18Н10Т и меди М-1 в условиях симметричного чистого из гиба по методике [9]. Дефекты в виде лунок различных размеров выпол нены с помощью обычного или лазерного сверления и имитируют поверх ностные поры (рис. 5.3). В целях исключения влияния наклепа, изменяю щего условия зарождения трещины, сверление производили в несколько этапов. При изготовлении лунок лазерным сверлением образцы подверга ли нормализации. Расстояние между дефектами было выбрано таким обра зом, что распространение трещин от дефектов можно считать независимым. Эффект влияния трещин друг на друга проявлялся только при достижении одной из трещин размера, равного ширине образца. В этом случае рост тре щин от других дефектов практически прекращался.
При проведении испытаний на усталость на образцах, имеющих три ис-

Рис. 5.4. Кривая малоцикловой усталости стали 45 с искусственным дефектом d = = 0,5 мм, h = 0,5 мм для различных вероятностей разрушения
дом с последующей фрактографией. В образцах с искусственными дефекта ми усталостные трещины образовывались почти симметрично с двух сторон каждого дефекта. Под длиной трещины понимали длину с учетом засвер ленного отверстия.
Вероятностный подход к оценке долговечности вызывает необходи мость изучения закономерностей распределения характеристик усталост ных свойств на стадии зарождения и распространения трещин. По данным о распредлении долговечности до разрушения строили кривые малоцикловой усталости для различных вероятностей разрушения (рис. 5.4) и функции распределения долговечности до разрушения при фиксированной длине трещины. Для определения рассеянияхарактеристик определялись выбороч ные статистики; среднее арифметическое^, среднее квадратическое откло нение 5, коэффициент вариации v =S/X. Значения выборочных статистик для стали 45 с искусственными дефектами разных размеров приед =0,3% приведены в табл. 5.1.
На рис. 5.5 приведен полигон накопленных частот длин трещин сц дефек тов диаметром 0,5 мм при различных значениях долговечности.
Параметры логарифмически нормального распределения (М — матема тическое ожидание и S —среднее квадратическое отклонение) зависят от отношения N/Npy где Np —долговечность до разрушения образца без искус ственных дефектов (рис. 5.6). На начальной стадии роста трещины среднее квадратическое отклонение достигает 20%, а к моменту разрушения 7—10%. Опыты показали, что амплитуда деформации незначительно влияет на за висимость параметров распределения от относительной долговечности. За висимость параметров распределения от относительной долговечности N/Np
описывается уравнениями
М= Aln(N/Np) +В, |
(5.1) |
S = С + DN/Np, |
(5.2) |
где А, В, С, D —эмпирические коэффициенты, зависящие от размера дефек-
Т а б л и ц а 5.1 Выборочные статистики для образцов из стали 45 с искусственными дефектами
Д мм |
N |
|
S |
v = S/X |
No/Np |
|
1.0 |
N 0 |
2,7272 |
0a225 |
0,0570 |
0,0625 |
|
|
|
|
|
|
||
|
Np |
3,9337 |
0,150 |
0,0380 |
|
|
|
|
2,8877 |
0,187 |
0,0640 |
|
|
0,7 |
N p |
4,0250 |
0,094 |
0,0235 |
0,0729 |
|
|
|
|||||
0,5 |
N 0 |
3,092 |
0,1462 |
0,0473 |
0,0952 |
|
Np |
4,1140 |
|
|
|||
|
0,0768 |
0,0187 |
|
|||
0,3 |
No |
3,3080 |
0,075 |
0,0231 |
0,135 |
|
|
4,1765 |
0,133 |
|
|||
|
Np |
0,0319 |
|
|||
0,2 |
No |
3,6045 |
0,125 |
0,0346 |
0,230 |
|
|
4,2425 |
|
|
|||
|
Np |
0,156 |
0,037 |
|
||
0,1 |
No |
3,6973 |
0,151 |
0,041 |
0,254 |
|
|
4,2919 |
0,130 |
0,0305 |
|||
|
Np |
|
||||
Без от- |
No |
4,0303 |
0,0947 |
0,0235 |
0,537 |
|
верстия |
Np |
4,3003 |
0,0731 |
0,017 |
||
|
та: А = 1,23 ехр(—0,97 \/*Р), 5 = 0,88 ехр ( - 0 ,3 6 \^ ), С = 0,305 —0 ,1 3 \^ , D =0,186 + 0,21 \ / F
Опыты проводились на образцах с тремя искусственными дефектами, расположенными по оси на равных расстояниях друг от друга. Несмотря на то что трещины развивались приблизительно симметрично от каждого де фекта, скорость распространения их от каждого дефекта .различна. Вероят ность разрушения для этого случая может быть определена на основании установленного экспериментально распределения длин трещин при задан ной долговечности.
Для расчета вероятности разрушения образца с тремя дефектами необхо димо вычислить тройной интеграл
/шах |
/щах *тах |
|
|
Щ ь к, / э ) = / Л х / Д , Их ( М /2 ( / а ) / э ( / з ) Л 3 , |
( 5 . 3 ) |
||
0 |
0 |
0 |
|
где / 1 (/) —плотность логнормального распределения с определенными ра нее (5.1), (5.2) параметрами, / тах — максимальная длина трещины, при которой происходит разрушение образца.

/ 2 J 0 S 0 7 0 0 imaK 10
Рис. 5.7. Расчетная функция распределения максимальных длин трещин на образцах
с искусственными дефектами d = 0,5 мм, h = 0,5 мм при еа |
= 0,3%, полученная мето |
|||||
дом Монте-Карло |
|
|
|
|
|
|
При N ю |
' Л |
\'7 |
1 4 |
2\ |
3’ 4 ~ 4’ 5 ~ 5> 6 - 6>7 - |
7, 8 - 8, 9 - 9 ,10 - 10, |
11 - 11,12 — |
12,1 3 - |
13, |
- 1 4 |
|
|
Al
ZH'
7 |
3 |
/ / |
73 |
rs A7-70 |
Рис. 5.8. Зависимость долговечности от N/ F H
y/tT для образцов из стали 45 с искусствен
ными дефектами d = 0,4 мм при различных соотношениях hjd
Рис. 5.9. Кривые скорости роста трещин для |
|
|
|
||||||
стал i 45 |
с |
искусственными |
дефектами |
диа |
|
|
|
||
метр эм |
0,4 |
мм при различных значениях hjd |
0 70 |
|
|
||||
hid: |
1 |
- |
0,5; 2 - 1,5; 3 - |
2,5; 4 - 1; |
5 - |
70 |
2 0 J 0 |
||
|
|||||||||
2,0; 6 -1 2 |
|
|
|
4 |
|||||
|
|
|
|
|
|
К1 0777а \777Г |
определить вероятность разрушения при заданном числе циклов нагруже ния и вероятность образования максимальной длины трещины при задан ной долговечности.
С целью изучения общих закономерностей повреждения и разрушения материалов с дефектами решалась задача определения циклической дол говечности в зависимости от формы и абсолютных размеров дефекта.
Для оценки влияния формы дефекта проводились опыты на образцах с искусственными дефектами при различных отношениях Л/d. В качестве параметра, определяющего влияние дефекта на долговечность, принима лись d , \/F y3vV . Анализ показал, что долговечность до разрушения имеет приблизительно одинаковую корреляцию с yJF и 3yjv (рис. 5.8). Но в свя зи со сложностью определения объема реального дефекта в качестве опре деляющего параметра выбран \ ^ . На рис. 5.8 приведено изменение долго вечности до зарождения трещины / = 0,1 мм и до разрушения в зависи мости от отношения h/d при d = 0,4 мм. Как видно на рисунке, зарожде ние трещины в меньшей степени зависит от соотношения h/d, чем окон чательное разрушение.
Изучение поверхности излома образцов с дефектами при различном от ношении h/d показало, что распространение трещины происходит по полуэллипсам и соотношение полуосей эллипса зависитот соотношения h/d. Очевидно, скорость распространения трещины уменьшается в середине об разца, т.е. в середине образца создаются условия, задерживающие ее рас пространение.
На рис. 5.9 показана кривая скорости роста трещин для образцов с раз личными значениями h/d ; точки — экспериментально наблюдаемая ско рость роста трещины и ее аппроксимация законом Пэриса в зависимости от
АК
dl |
(5.4) |
— = САКт . |
|
dN |
|
Для каждой отдельной трещины закон роста трещины аппроксимирован методом наименьших квадратов. Из рисунка следует, что закон Пэриса за вышает скорость роста трещины при низких значениях А К . Это приводит к заниженной оценке усталостной долговечности для трещин, начинающих расти при низких АК. Экспериментальные данные хорошо совпадают с кривой за исключением самых коротких трещин. Значения коэффициен тов уравнения Пэриса (5.4) следующие:
h/d |
\/7 t мм |
т |
С -106 |
h/d |
\/ F , ш |
т |
С • Ю6 |
0,56 |
0,20 |
1,527 |
6,72 |
5,00 |
0,88 |
2,104 |
88,4 |
1,00 |
3,37 |
2,233 |
65,5 |
6,25 |
0,99 |
2,146 |
77,6 |
1,50 |
0,46 |
2,382 |
35,1 |
7,50 |
0,09 |
2,164 |
77,0 |
2,00 |
0,55 |
2,236 |
54,9 |
8,75 |
U 7 |
2,650 |
20,0 |
2,50 |
0,61 |
2,157 |
70,8 |
10,00 |
1,26 |
1,926 |
22,5 |
3,00 |
0,68 |
2,170 |
69,2 |
11,25 |
1,33 |
2,279 |
63,4 |
4,00 |
0,79 |
2,274 |
53,9 |
12,00 |
1,41 |
2,460 |
32,0 |
Исследование влияния абсолютных размеров дефектов d и h на цикли ческую долговечность производилось на основе многофакторного регрес сионного анализа с использованием униформ-ротабельных планов второ го порядка [12]. Для получения математической модели использовали раз ложение неизвестной функции долговечности в ряд Тейлора. По данным эксперимента определялись выборочные коэффициенты регрессии. Модель, построенная по результатам эксперимента, имеет вид
* = 0о + 0 1 * ! + 0 2 * 2 + 0 1 2 * 1 * 2 + 011*1* + 0 2 2 * ! . |
(5.5) |
Для вычисления коэффициентов модели применялся метод наименьших квадратов. По данным регрессионного анализа устанавливали значимость коэффициентов регрессии, адекватность математической модели, диспер сию предсказанного значения выхода, доверительные интервалы для значе ния выхода. Значимость коэффициентов уравнения определяли по крите рию Стьюдента, а адекватность —по критерию Фишера.
При планировании эксперимента приняты следующие интервалы варьи рования: d = Xi = 0,1-И,0 мм; h =Х2 = 0,1 -=-1,0 мм. Значения коэффициен тов уравнения (5.5) в натуральном виде для стали 45 следующие:
efl, % |
|
Pi |
0а |
01 а |
01, |
0 аа |
||
0,2 |
157 201 |
- 7 6 |
7 4 5 |
- 2 6 5 |
283 |
20 000 |
3 0 0 5 0 |
163 780 |
0,3 |
3 4 1 9 1 |
- 1 4 |
453 |
- 4 4 |
517 |
5 200 |
4 4 9 2 |
23 445 |
0,4 |
16 891 |
- 1 5 |
953 |
- 2 6 |
319 |
781 |
12 947 |
19 077 |
Ранжирование коэффициентов уравнения в кодированном виде по сте пени их влияния показало, что коэффициенты при смешанных членах сос тавляют около 10% от коэффициента при ATlf т.е. соотношение глубины и диаметра значительно меньше влияет на долговечность, чем абсолютные размеры дефекта (рис. 5.10).
Для оценки циклической долговечности материала с дефектами необхо димо учесть влияние формы и размера дефекта и концентрацию напряже ний, вызванную дефектом.
Точный анализ концентрации напряжений для всех реальных случаев невозможен. На практике используются решения для типовых концентра торов напряжений, для которых значения коэффициентов концентрации определены достаточно полно и надежно [13]. В литературе приводятся данные по влиянию дефектов и включений [2, 14, 15] на концентрацию нап ряжений и методы расчетно-экспериментальной оценки долговечности на стадии разрушения с использованием результатов анализа напряженнодеформированного состояния в вершине трещины. Действительные коэф фициенты концентрации напряжений и деформаций могут быть вычислены по формуле Н.А. Махутова [2] при знании теоретических коэффициентов концентрации.
Теоретически учесть одновременно влияние концентрации напряжений, формы и размера дефекта трудно. Поэтому о влиянии дефектов на долго вечность при малоцикловом нагружении можно судить по эффективным коэффициентам концентрации, определяемым экспериментально.
Эффективные коэффициенты концентрации напряжений и деформаций при малоцикловом нагружении могут быть определены по кривым мало-
Рис. 5.10. Диаграмма долговечности образцов из стали 45 при еа = 0,3% в зависимости от абсолютных размеров дефекта
Л, мм: 1 — 1; |
2 — 0,7; 5 —0,5; 4 —0,3; 5 —0,2; 6 —0,1; d, мм: 7 —1; 8 —0,7; |
9 - 0,5; 10 - 0,3; |
11 - 0,2; 12 - 0,1 |
цикловой усталости (рис. 5.11, а, б)
K<JM = ON/ONKf Кем = |
(5.6) |
где а#, е w —амплитуда напряжения и деформации гладкого образца при определенной циклической долговечности; о^к , е # к —амплитуда напря
жений и деформаций образца с концентратором напряжений; Ка , К€ — эффективные коэффициенты концентрации напряжений и деформации
при малоцикловом |
нагружении. |
Вводя понятие эффективного коэффициента концентрации энергии |
|
Кх = К„мКем |
(5.7) |
в предложенный ранее энергетический критерий [16], будем иметь |
|
Къ WNP = a Q, |
(5.8) |
где W —энергия, затраченная на деформацию образца, определяемая по пет-
ле механического гистерезиса; Q —энергоемкость материала, Q ц fTsCpd Г+
т
+ L ; а —коэффициент термомеханической активности; р —постоянная. Значения эффективных коэффициентов концентрации напряжений, де формаций и энергий для материалов с дефектами приведены в табл. 5.2. Для проведения прочностных расчетов с учетом кинетики циклического упругопластического деформирования необходимо иметь не только уста лостную кривую по моменту разрушения, но и кривую, полученную из ус ловия появления повреждений заранее установленной величины. Такие кри вые поврежденности можно использовать для оценки времени, необхо-
105
Рис. 5.11. Кривые малоцикловой усталости стали 45 с искусственными дефектами
При d, м м : 1 , 1 ' - 1; 2, |
2* - 0,7; 3 , З1 — 0,5; 4, 4 - 0,3; 5, 5' - 0,2; 6 — без де |
ф ектов; I — разруш ен и е,// |
—повреждение |
димого для полного разрушения детали, в которой обнаружена усталостная трещина.
Потребность в определении длительности стадии распространения трещин обусловлена тем обстоятельством, что в ряде случаев период развития трещин составляет значительную долю полной долговечности. Так, зарож дение и распространение макротрещины на гладких образцах происходит в последние 30% долговечности. При наличии концентрации напряжений на развитие усталостной трещины может понадобиться до 90—95% общего числа циклов. Для исследованных размеров дефектов период роста трещи-
Т а б л и ц а 5.2
Эффективные коэффициенты концентрации^дпя материалов с дефектами
F |
Сталь |
45 |
|
Сталь 08Х18Н10Т |
|
Медь М-1 |
|
||
■J , |
|
|
|
|
|
|
|
|
|
е |
|
|
* 2 |
|
К* |
* 2 |
|
|
* 2 |
|
|
|
|
|
к ы |
||||
|
|
|
|
ем |
|
||||
0 ,9 2 |
1,05 |
1,33 |
1,40 |
1,20 |
1,82 |
2,18 |
1,22 |
1,69 |
2,09 |
0,65 |
1,04 |
1,24 |
1,29 |
U 4 |
1,43 |
1,63 |
1,17 |
1,40 |
1,64 |
0 ,4 6 |
1,03 |
1,16 |
1,19 |
1,12 |
1,36 |
1,55 |
1,13 |
1,29 |
1,46 |
0 ,2 8 |
1,02 |
1,09 |
1,11 |
1,10 |
1,34 |
1,47 |
1,09 |
1,22 |
1,33 |
0,23 |
1,01 |
1,08 |
1,09 |
1,06 |
1,18 |
1,25 |
1,05 |
1,13 |
1,19 |
0 ,1 8 |
1,01 |
1,7 |
1,08 |
1,05 |
1,18 |
1,24 |
— |
— |
— |
|
|
|
|
|
|
|
|||
0 ,4 6 * |
— |
— |
— |
1,12 |
1,21 |
1,36 |
1,10 |
1,24 |
1,36 |
0 ,5 5 * |
— |
— |
— |
— |
— |
— |
1,02 |
1,09 |
1,12 |
|
|
|
|
||||||
0 ,1 5 * |
1,02 |
1,03 |
1,05 |
1,00 |
1,02 |
1,02 1,00 |
1,02 |
1,02 |
|
0 ,1 1 * |
1,00 |
1,03 |
1,03 |
1,00 |
1,02 |
1,02 |
1,00 |
1,02 |
1,02 |
0 ,0 8 * |
1,01 |
1,02 |
1,03 |
1,00 |
1,02 |
1,02 |
1,00 |
1,02 |
1,02 |
*Искусственные дефекты выполнены лазерным сверлением.
ны составляет для стали 457V0 = (0,75-Ю,95) Npt для стали 08Х18Н10Т N0 = = (0,7-Ю,9) Np и для меди М-1 N0 = (0,7-Ю,8) Np, причем с увеличением ам плитуды напряжения N0/Np снижается. Анализ зависимости N0/Np от ампли туды деформации показывает, что для всех размеров дефектов в диапазо не исследованных амплитуд деформации это отношение меняется в преде лах 0,05—0,3. Отмечается тенденция снижения отношения N0/Np с увеличе нием размера дефекта.
Существование этой тенденции объясняется тем, что с уменьшением раз мера дефекта соотношение между числом циклов до зарождения трещи ны N0 и числом циклов до разрушения Np растет в пользу Л^, так как фак торы, определяющие условия зарождения трещины, более зависимы от раз мера дефекта, чем факторы, определяющие скорость роста трещины. Связь между числом циклов до разрушенияNp и число циклов до зарождения тре щины определяется зависимостью
N c = A 0N£,
где А 0 и п — коэффициенты.
Значения коэффициентов А 0 и п приведены в табл. 5.3.
Статистическая обработка экспериментальных данных позволила предло жить для определения долговечности при малоцикловом нагружении в за висимости от размера дефекта при определенной деформации следующую зависимость:
N m Fy / r = Gp, |
(5.9) |
где mF и Gp —коэффициенты.
Значения mF и GF приведены в табл. 5.3.
Большинство испытанных образцов как гладких, так и с искусственны-
Т а б л и ц а 5.3
Значения ко эф ф и ц и ен то в д л я различны х ам п ли туд д еф орм ац и и
еа,% |
Разрушение |
|
Зарождение трещин |
А 0 |
|
|||
|
тр |
cF |
|
|
|
|
|
|
|
|
mF0 |
CF 0 |
|
|
|||
0,2 |
2,99 |
1,6810,э |
1,52 |
1,5 |
• 10‘ |
559 |
0,49 |
|
0,3 |
2,87 |
2,77 |
- 1 0 “ |
1,33 |
5,8 |
• 103 |
543 |
0,44 |
0,4 |
2,78 |
5,09 |
10’ |
1,72 |
7,4 |
• 10* |
123 |
0,62 |
ми дефектами имели нераспространяющиеся трещины. В некоторых слу чаях, что особенно характерно для меди, нераспространяющиеся трещины обнаружены не только на краю дефекта, но и на поверхности, далеко от искусственного дефекта. При испытании на малых амплитудах деформа ций наблюдается мцогоочаговость усталостного разрушения. Зачастую тре щины образуются вне зоны концентрации напряжений. Незначительная часть трещин продолжает расти и, сливаясь, образует магистральную тре щину. Остальные трещины, достигнув определенного размера, не растут. Опасными являются трещины, размеры которых превышают размеры нераспросграняющихся трещин. Обнаруженный наибольший размер нераспространяющейся трещины для меди составляет 340 мкм, дня стали 08Х18Н10Т —210 мкм, для стали 50—170 мкм.
В настоящее время считается установленным факт существования безо пасного размера дефекта при испытании на пределе усталости. Значение безопасного размера дефекта колеблется по данным разных авторов в пределах от 2 до 700 мкм [17—20]. Опыты показали, что существует по верхностная дефектность оптимальной величины, которая не приводит к снижению циклической долговечности при малоцикловом нагружении.
На рис. 5.12 показана зависимость долговечности от размера дефекта дня различных уровней деформации для стали 45. Анализ этих зависимостей позволил определить критический размер дефекта, не оказывающего влия ния на долговечность при малоцикловом нагружении.
При низких уровнях напряжений на меди и стали 45 наблюдается образо вание вторичных трещин. Зарождение этих трещин идет независимо от мо мента и места зарождения первой трещины. Видимо, информация о зарож дении вторичных трещин характеризует материал. Отношение NQ/NP (где N0 — долговечность до образования вторичных трещин) колеблется в пределах 0,85—0,92. Разницу между N Q H N0, очевидно, можно рассматри вать как не реализованный прочностной резерв. Именно этот диапазон дол говечности следует считать наиболее целесообразным для проведения вос становительных обработок, позволяющих наиболее полно реализовать прочностные свойства металлов.
Таким образом, статистические испытания на малоцикловую усталость с использованием образцов, имеющих дефекты с одинаковой чувствитель ностью к разрушению, позволили определить количественные закономер ности зарождения и распространения трещин в поврежденном металле.
Рис. 5 .1 2 . Зави си м ость долговечности от разм ера д еф екта д л я стали 45
1 — разрушение, 2 —повреждение
5.2. Расчетная оценка рассеяния скорости и долговечности при развитии малоцикловых трещин
Для разработки уточненных методов вероятностной оценки несущей способности и живучести элементов конструкций с трещинами и для обос нования возможности получения таких оценок расчетным способом необ ходимы широкие исследования для получения экспериментальных оценок рассения характеристик малоциклового разрушения сталей различных классов. Экспериментальные и расчетные статистические оценки характе ристик образования и развития малоцикловых трещин в зонах концентра ции напряжений, как уже отмечалось, в литературе практически отсут ствуют.
На основе проведенных исследований статистических закономерностей образования и развития трещин в зонах концентрации рассматриваются разработанные расчетно-экспериментальные методы оценки рассеяния характеристик малоциклового разрушения-рассеяния скоростей при обра зовании и развитии и долговечностей при развитии малоцикловых трещин. Экспериментальная и расчетная оценка долговечности по параметру вероят ности образования трещин рассматривалась в п. 4.4.
Экспериментальные функции распределения чисел циклов до образо
вания трещин N0i до разрушения Np, а также до достижения трещинами определенных длин Щ7), амплитудных раскрытий в устье N(8a) и ско
ростей |
роста N(dljdN) для сталей Х18Н9 и 15Х2НМФА при нормальной |
[1, 3] |
и повышенных температурах (650 и 350 °С соответственно) прове |
рялись на соответствие четырем теоретическим законам распределения (нормальному, логнормальному, двухпараметрическим Вейбулла и экспо ненциальному) по методике, изложенной в п. 2.2. При этом для первона чальной проверки указанных гипотез вначале использовался приближен ный графический метод, а затем проводился расчетный анализ по крите риям согласия X, со2 и W.
Результаты графического и расчетного анализов, проведенные в рабо те [1] для сталей Х18Н9 и 15Х2НМФА при нормальной температуре, пока зали удовлетворительное соответствие распределений величинN(j),N(8a) и N(dl/dN) обеих сталей нормальному или логнормальному законам рас пределений. При этом нормальный закон обычно лучше соответствовал опытным данным на стадии образования трещин (соответствие ему со ставило по критерию W для стали Х18Н9 30—95% против 15—50% для лог нормальному закона).
На стадии развития трещин, ближе к моменту разрушения, вследствие повышения ’’расслоения” данных в выборках (см. рис. 2.4, сталь Х18Н9) повышалась относительная роль логнормального закона (5—50% против 10—40% для нормального закона). При этом по мере развития трещин общее соответствие обоим законам постепенно ухудшалось (до уровня 5—50%). В момент разрушения значения величины к р имели достаточно вы сокое соответствие обоим законам (40—95%). В связи с этим ближе к мо менту разрушения экспериментальные выборки стали составлять только из разрушающих трещин (по одной трещине максимальной длины для каждого образца статистической серии).
Аналогичный характер изменения функций распределения величин N(1), N(8а) и N(dl/dN) с числом циклов нагружения наблюдался и для стали 15Х2НМФА с исходной термообработкой.
На рис. 5.13, a- в и 5.14, a- в для стали 15Х2НМФА (с дополнительной термообработкой) при 350° С показаны результаты графического анали за на соответствие некоторых выборочных распределений чисел циклов по параметрам / и dl/dN нормальному, логнормальному и Вейбулла зако нам распределения. Из рисунков следует удовлетворительное соответ ствие эмпирических распределений нормальному и логнормальному зако нам распределений, обычно с предпочтением логнормальному законам. Соответствие экспоненциальному закону отсутстввало. При этом соот ветствие закону Вейбулла в большинстве случаев хуже, чем логнормаль ному закону.
Проведенный по критериям согласия расчетный анализ подтверждает этот вывод. Так, соответствие по критерию согласия W составило: для
---------- *—
Рис. 5 .1 3 . Экспериментальные функции распределения чисел циклов N (I) по парамет ру длины трещины
Здесь и на рис. 5.14 распределение: а —логнормальное, б —нормальное, в —Вей булла; при/, мм: 2 - 0 ,1 ; 2 - 0,2; 3 - 0,5; 4 - 2,0; 5 - 3 ,0
нормального закона 11—88% (N (f))f 19—49% (W(5fl) ) , 19—97% (N(dl/dN)); для логнормального закона 35—52% (N(J)), 36—76% (А/(5Д)), 61—99%
(N (dU АО).
На рис. |
5.15, а -г и 5.16, а-г для стали Х18Н9 при температуре 650 С |
в качестве |
примера показано графическое соответствие экспериментальных |
распределений чисел циклов N(1) и N(dl/dN) нормальному, логнормально му, двухпараметрическим Вейбулла и экспоненциальному законам распре деления. На рисунках видно, что для перечисленных величин наблюдается удовлетворительное соответствие логнормальному, нормальному и Вей булла законам распределения и плохое соответствие экспоненциальному закону. При этом предпочтительным является логнормальный закон, что подтверждается расчетным анализом по критериям согласия X, со2 и W (табл. 5.4). Так, соответствие по критерию Wсоставило: для нормального закона 10-50% (АГ(/)), 40-90% (N(8a)), 18-60% (N(dl/dN)); для лог нормального закона 14—74% 38—99% (N(5fl)),3 1 —93% (N(dl/dN)). Закон Вейбулла везде хуже соответствовал экспериментальным распреде лениям, чем логнормальный закон.
Распределения длин трещин /(АО, амплитудных раскрытий в устье Sa(N) и скоростей роста dljdN (N) для определенных чисел циклов Допо лучали, проводя ряд вертикальных сечений соответствующих полей, пред ставляющих зависимость данной характеристики трещины от числа циклов нагружения N (см. рис. 2.4).
В качестве примера на рис. 5.17, а, б показаны результаты графического анализа на соответствие эмпирических распределений долговечностей / (N) для стали Х18Н9 при нормальной температуре нормальному и логнор мальному законам. На рисунке видно более явное наличие порогов, не смотря на обычно меньшее число значений случайной величины, попадаю щее в выборку по сравнению с прежними распределениями величин N(f), N(8a) и N(dl/dN). Наличие порогов определило и более худшее соответ ствие проверямым теоретическим законам. Так, для стали Х18Н9 при нор мальной температуре (/(АО) и стали 15Х2НМФА при температуре 350°С (5e (N)) соответствие п.о критерию согласия W составило: для нормаль ного закона 0—17% (/(АО), 0—21% (5Л(А0), для логнормального закона 2—35% (/(АО), 21—98% (6fl(A0). При этом распределение Вейбулла было менее предпочтительным по сравнению с логнормальным распределением.
На рис. 5.18, а, б для стали 15Х2НМФА при 350 °С показано соответ ствие экспериментальных функций распределения dljdN (ДК) скоростей роста трещин dN/dl, попадающих в узкий интервал (ширина интервала АК составляла 3,1 МПа • для определенных средних значений величин \gAK логнормальному и Вейбулла законам распределения. Анализ по критериям согласия показал лучшее соответствие логнормальному закону. Затем по степени убывания соответствия располагались закон Вейбулла, экспоненциальный и нормальный законы распределения.
В целом по результатам графического и расчетного анализов по крите-
Рис. 5 .1 4 . Э ксп ерим ентальн ы е |
ф ун кц и и распределения чисел ц и к ло в N {dljdN) по |
п арам етру ско р о сти роста трещ |
ин |
При dljdN, мм/цикл: 1 - 10"9, 2 - 5 • 10"9, 3 - 10“2, 4 - 3 • 10"2
в°/о |
|
|
|
|
оо |
|
|
|
|
0 5 |
|
|
|
|
00 |
|
|
|
|
50 |
|
|
|
|
20 |
|
|
|
|
5 |
|
|
|
|
/ |
|
|
|
|
О,Г |
ООО |
/ООО |
|
цикл |
500 |
|
|||
/>% |
|
|
|
|
50,0 |
|
|
|
|
50 |
|
|
|
|
0 5 |
|
|
|
|
50 |
|
|
|
|
50 |
|
|
|
|
20 |
|
|
|
|
5 |
|
|
|
|
7 |
|
|
|
|
О,/ |
/ООО |
7000 |
/ООО |
U,UM |
5 0 0 |
Рис. 5.15. Экспериментальные функции распределения чисел циклов N(1) по парамет ру длины трещины
Здесь и на рис. 5.16 распределение: а —логнормальное, б —нормальное, в — Вейбулла, г - экспоненциальное; при /, мм: 1 - 0,2; 2 - 0,5; 3 - 1 ; 4 - 2 ; 5 - 4
риям согласия можно отметить, что экспериментальные функции распре деления характеристик малоциклового разрушения N (t)yN(ba) uN(dlldN) для сталей Х18Н9 и 15Х2НМФА при нормальной и повышенной температу рах удовлетворительно соответствует нормальному и логнормальному за конам с предпочтением нормальному закону на стадии образования трещин (обычное соответствие обоим законам по критерию W составило 20-80%); на стадии развития трещин лучшее соответствие наблюдалось для логнор мального закона; соответствие закону распределения Вейбулла за редким исключением хуже, чем логнормальному закону, а соответствие экспонен циальному закону практически отсутствует.
114
Р,в/о
Распределения величин l(N), 8а (М) и dl/dN(N) имеют более выраженные пороги, чем распределения N(l), N(8a) и N(dlldN), и соответственно худшее соответствие теоретическим законам распределения; лучшее соответ ствие установлено для логнормального закона (10—30% по критерию М/ ), соответствие нормальному и экспоненциальному законам слабое.
Распределения величин dl/dN(АК) в большинстве случаев имели удовле творительное соответствие логнормальному и экспоненциальному законам (кроме значений для стали 15Х2НМФА при нормальной температуре), при этом экспоненциальный закон часто был предпочтительнее логнормаль ного; соответсвие закону распределения Вейбулла было в основном хуже, чем логнормальному закону; соответствие нормальному отсутствовало.
В разработанном экспериментальном методе оценки рассеяния долго вечности по моменту образования трещин N0 и по параметру ее длины N(f)> а также скоростей роста трещин в зонах концентрации анализиро-
Pf °/o
Рис. 5.16. Экспериментальные функции распределения чисел циклов N(dl/dN) по па раметру скорости развития трещин
При dl JdN, мм/цикл: 1 - 0,0003; 2 - 0,001; 3 - 0,003; 4 - 0 ,0 1 ; 5 - 0,03
вались экспериментальные выборки, как правило объемом от 15 до 50 (средние значения 20—30).
Экспериментальные значения скоростей развития трещин и соответ ствующие им размахи коэффициента интенсивности напряжений АК опре делялись с помощью программы расчета на ЭВМ (Фортран-IV) по ниже изложенному алгоритму; графическая часть программы обеспечивала построение зависимости dl jdN—AK.
В соответствии с работой [21] скорости развития трещин определяются по формуле
^• _ h+ 1 ~ U
dN |
Ni+ l- N i |
и вычисляются для среднего значения длины трещины /* = (/, + х+ lt)l2.
Размах коэффициента интенсивности напряжений АК (условный для малоциклового нагружения) определяется выражением
ще АОп — размах номинальных напряжений в брутто-сечении образца
(принято Аоп = 2оап)\ |
f u = y j sec [эт(d + 2lf)/2b] - |
поправка Феддерсена |
на ширину Ъ образца |
[22]; / 2/ — поправка Бови |
на наличие отверстия |
диаметром d для двух сквозных радиальных трещин, обычно функция задается таблично [23].
Табличные значения функции Бови аппроксимировались полиномом, предложенным Ю.А. Свирским [24]:
f |
2i = 1,0008 - 0,23312z/ + 7,4652z*—30,117zf + |
|
+ 65,402z*- 63,834z*+ 23,703z^, |
(5.10) |
|
где |
z,= 1/(1 + ifi/d). |
|
Результаты статистической обработки распределений чисел циклов N по пара
метрам длины трещины N(J), амплитудного |
раскрытия трещины в устье N (6Д) |
|||||
и скорости роста трещины N(dl/dN) для стали Х18Н9 при температуре 650 С |
||||||
Параметр рас |
N(1 =0,3 мм) |
|
lgN |
Щ = 1 мм) |
|
IgW |
пределения |
п - |
3t |
|
л = 28 |
|
|
|
|
|
|
|||
|
|
1 |
|
----------------------- 1 |
|
1 |
X |
--------------------------- |
|
838.6 |
|
827,2 |
|
650,6 |
' |
634,6 |
|
|||
$п- 1 |
146,3 |
|
0,0989 |
139.6 |
|
0,0736 |
V |
0,225 |
|
0,0353 |
0,166 |
|
0,0252 |
р„,% |
48,5 |
|
73,3 |
30,1 |
|
26,5 |
Параметр рас |
N(6a = 0,05 мм) |
|
lgN |
ЛГ(6а = 0,3 мм) |
|
lgIV |
пределения |
|
|
|
|
|
|
|
п = 30 |
|
я = 16 |
|
|
|
|
---------------------------- |
1----------------------- |
|
------------ - |
i |
’ |
X |
803,4 |
|
791,0 |
984,8 |
|
975,5 |
1 |
140,5 |
|
0,0789 |
139,2 |
|
0,0616 |
и |
0,175 |
|
0,0272 |
0,141 |
|
0,0206 |
Pw, % |
66,5 |
|
38,8 |
41,7 |
|
47,5 |
В работе [1] приведены экспериментальные скорости развития трещин dljdN и расчетные значения скоростей для стали Х18Н9 для нормальной температуры для серии с долговечностью 103 циклов по уравнению Фор мэна (рис. 5.19, а, кривая 7).
dl _ ААКВ
dN ~ (1 - R) К, - А К
где А и В — параметры; R —коэффициент асимметрии, принят равным нулю; Xj — критическое значение коэффициента интенсивности напря
жений, значение которого по результатам эксперимента условно принято
100 |
МПа • >/м (по данным работы |
[25] значение Кг для стали Х18Н9 |
|
при |
20 ° С равно 120 МПа • |
• |
° |
При длинах трещин менее 1 мм наблюдалось увеличение разброса данных
и повышенное |
значение |
экспериментальных скоростей роста трещин |
по сравнению с |
расчетным |
(см. рис. 5.19, д, кр. 7). Там же приведены при |
меры расчета скоростей роста трещин малой длины с использованием кон цепции предела трещинностойкости 1С [26, 27]
h = Кс<р(Г)= Кс ■Ф с/аь\
h = «с у/ 1 - (ос1оь)п\
где Кс — критический коэффициент интенсивности напряжений; ос —кри тическое напряжение, обычно определяемое экспериментально, в данном случае определялось расчетом по методике, изложенной в работе [28]; оъ — предел прочности. Этот расчет представлен на рис. 5.19, а (кр. 2 и 5
= 2 мм) |
|
lgN |
|
N P |
lgN p |
N ( 6 a = 0,01мм) |
lg$a |
|||||
л = 16 |
|
|
|
п = 16 |
|
|
л = 25 |
|
|
|||
909,3 |
1 |
|
|
|
1 |
|
|
--------------------- и |
613,4 |
|||
|
895,9 |
|
1009,4 |
|
1000,4 |
628,4 |
|
|||||
162,8 |
|
|
0,0770 |
|
141,0 |
|
|
0,0599 |
141,1 |
|
0,0978 |
|
0,179 |
|
|
0,0261 |
|
0,140 |
|
|
0,0200 |
0,225 |
|
0,0351 |
|
17,0 |
|
|
26,1 |
|
9,8 |
|
|
14,3 |
89,4 |
|
99,9 |
|
Nldl/rlN = I O ' 3 |
|
|
|
|
|
|
|
lg N |
1 |
- |
м м \ |
|
М М |
\ |
l g # |
л г (< я /^ л г = 1 0 -1 - |
^ - |
) |
Nidl/dN =3-10“®--------- | |
IgW |
|||||
\ |
ЦИКЛ |
J |
1 |
ЦИКЛ |
/ |
|
1 |
ц и к л у |
||||
|
л = 23 |
|
|
|
л = |
28 |
|
|
л = |
14 |
|
|
669,7 |
|
|
653,0 |
|
917,6 |
|
|
905,6 |
1003,6 |
|
994,4 |
|
155,2 |
|
|
0,0998 |
|
152,4 |
|
|
0,0716 |
140,1 |
|
0,0613 |
|
0,232 |
|
|
0,0355 |
|
0,166 |
|
|
0,0242 |
0,140 |
|
0,0204 |
|
47,8 |
|
|
93,0 |
|
18,5 |
|
|
31,8 |
58,9 |
|
60,7 |
для п = 4 и п = 2 соответственно). Из рисунка следует, что использование величины 1С вместо Кс позволяет лучше описать повышенную скорость роста трещин малой длины.
Представленные данные в явном виде не содержат статистические ха рактеристики циклического разрушения. Однако рассеяние скоростей роста трещин на начальном и последующем участках их развития может определяться статистическими характеристиками критического коэффи циента интенсивности напряжений KCi параметров А и Д которые, в свою очередь, связаны с основными механическими свойствами материала.
Там же [1] по результатам сравнения экспериментальных скоростей развития трещин для стали Х18Н9 при малоцикловом нагружении с расчет ными значениями скоростей, полученными по уравнению Пэриса для усло вий многоциклового нагружения:
— =сАКт, |
(5.11) |
<Ш |
|
показано, что в силу повышенных пластических деформаций в зонах тре щин различие экспериментальных и расчетных скоростей составляет до 1,5 порядков и зависит от уровня нагружения. В уравнении (5.11) принято /я = 3,53; с = 0,941 1(Г4; АК = Аопу/тгГ-/, кН/мм3^2,Я = -1 [15].
В связи с этим анализ закономерностей развития трещин должен осу ществляться не в величинах коэффициентов интенсивности напряжении, а в величинах коэффициентов интенсивности деформаций. При этом особен ности кинетических кривых в области малых длин трещин следует связы вать с анализом накопления повреждений в зонах концентрации к моменту образования трещины.
f - i 1 l I I \* 0 )
Рис. 5.17. Экспериментальные функции распределения длин трещин / (N) по парамет ру числа циклов
Здесь и на рис. 5.18 распределение: а — логнормальное, б —нормальное; при N , цикл: 1 —700, 2 — 800, 3 —900, 4 — 1000
Уравнение для скорости роста трещины, согласно [2], в величинах коэффициентов интенсивности деформаций можно записать в виде
dl |
= С ^ К ^ О |
(5.12) |
|
dN |
|||
a ie |
|
или в более общей форме для номинальных напряжений ниже предела текучести
120
Lg dl/dM j ш /цанл
//7 ' |
7/7 |
|
|
lg dl/d/7, мм/цикл |
|
|
|
Рис. 5.18. Экспериментальные функции распределения |
скорости |
развития трещин |
|
dl jdN (ДК) по параметру размаха коэффициента интенсивности напряжений |
|||
При lg Д К , МПа *у/м: 1 - 1,60; 2 - 1,70; 3 - 1,85; |
4 - |
1,90; 5 - |
1,95 |
dl
= caAKt 1f {г/Г)' |
(5.13) |
dN
1 - y
где размах коэффициента интенсивности деформаций АК1е выражен через размах условного коэффициента интенсивности напряжений АКг Величина
122
di/d/V, мм/цалл |
di/d/V,мм/цалл |
|
- а |
/, |
|
|
||
|
/ / |
|
2 |
/ Ш |
|
y . |
||
7df |
If • |
|
• / / |
||
— |
Yf+* |
|
5 |
||
x • |
||
|
2 |
|
|
|
|
|
• |
70'2 |
|
|
|
|
|
• |
— |
|
|
|
• |
|
|
|
|
|
|
|
||
5 |
|
|
|
|
|
|
■м |
|
• |
• |
|||
|
|
• |
||||
2 |
|
• |
|
• |
• |
|
|
|
X |
|
|
||
7 0 * |
, |
• |
& |
- Л \ |
. * 5 ^ |
|
- |
|
|
• |
t v |
||
|
= |
2 , |
|
|
||
0 |
|
|
|
|
||
— |
• |
* |
|
JГ* |
|
|
|
- |
. t |
|
|
||
|
|
• ^ |
• |
••S' |
|
|
|
|
*■ |
|
|||
TV 0005г |
• |
|
4 |
f0\,2 |
||
|
ф |
|||||
70 |
|
7,25 |
7,05 |
|
||
|
|
|
|
|
i |
A J |
• |
• |
|
|
|
• |
||
|
|
• « |
J S 9 • |
|
|
\• * • / t |
P |
• |
|
||
|
|
; |
! 5 £ . P |
• |
|
|
|
лл |
|
• |
|
|
|
7 |
4 |
|
|
|
|
|
|
||
' |
|
• / |
• |
|
|
|
j / |
« |
|
|
|
|
|
|
V |
■ |
|
w |
• • |
• |
|
|
0,57,0 |
i,MM |
|
_ _ L _ L —L |
r |
/f Z5 |
7,05 |
7,05 t |
|
|
IgA /f, ш |
а ^ л Г |
Рис. 5.19. Экспериментальное и расчетное рассеяния скорости развития трещин от концентратора для стали Х18Н9 при нормальной тем
пературе а = 285 МПа; количество образцов —10
Ук = 2 Р ^ ПРИ номинальных упругопластических деформациях [2]
1 — т ( к )
|
|
М , * ' |
(5.14) |
где |
|
|
|
|
2 -0 ,5 [1 - |
т(к)\( 1 - Sn) |
|
к е |
1 + |
т(к) |
|
|
|
Показатель упрочнения материала в к-м полуцикле определяется через максимальную деформацию в зоне трещины ef по формуле [2]
т{к)р = lge™/lg |
А |
1 |
)F(k) |
(5.15) |
где функция F (k )p = exp [с(е . —1) —для разупрочняющегося материала; F (к)р ~ 1 —для упрочняющегося и стабильного материалов.
В зоне трещины максимальная относительная разрушающая деформация
равна |
|
|
De |
ес> |
(5.16) |
е |
||
I |
|
|
где 6с _ относительная разрушающая деформация гладкого образца: |
|
|
1 |
1 |
(5.17) |
= — |
In ------ |
е Т
Величина^в формуле (5.12) равнаСа = 1/2этё*.
В соответствии с работой [2] коэффициент снижения предельных пласти ческих деформаций De и коэффициент повышения первого главного напря жения / в зоне трещины за счет возникновения объемности напряженного состояния для плоского напряженного состояния равны: De = 0,610, / = = 1,10; для плоской деформации Д, = 0,209,7= 2,49.
Рассеяние расчетных значений скоростей роста трещин определялось введением в уравнения (5.12) —(5.16) рассеяния основных механических свойств для уровней вероятностей 1, 50 и 99% [1]. При этом в расчетах для обеих сталей при нормальной и повышенной температурах были ис пользованы следующие допущения:относительный циклический предел текучести постоянен и равен S ^ = 2 ; коэффициент асимметрии номинальных напряжений R =-1, т.е. S n = 2оп и Sn = оп\ коэффициенты
параметров |
диаграммы |
циклического |
деформирования брались, к ж |
ре |
||||
комендуется |
в |
работе |
[2], т.е. |
КА |
= |
0,16 — в формуле (3.4), Кв |
= |
|
= 3 10"3 |
— |
в |
(3.6), |
Кс = 1,5 |
10“3 |
- |
в (3.7); значения величин ОМС |
°о 02 и $ к принимались расчетными по (4.19) и (4.20) соответственно. Результаты расчета [1] для стали Х18Н9 при нормальной температуре,
проведенные для значений ОМС при разных уровнях вероятности Р, пока заны на рис. 5.19, б. Расчет проводили для условий плоской деформации (кр. 2) и плоского напряженного состояния (кр. 3). Там же приведены примеры расчета скоростей роста малых упругопластических трещин, имею щих большее экспериментальное рассеяние скоростей по сравнению с рас-
124
Ьд d d/l / л 7г л г /ц и м
gl d d/l |
A л г j/м |
/ц и л /7 |
Рис. 5.20. Экспериментальное и расчетное рассеяния скорости развития трещин от концентратора для стали 15Х2НМФА при нор
мальной температуре (а) и 350 ° С (б) |
|
й: а = 527 МПа, л = 21; б: а = 391 МПа, |
= 19 |
четным, путем учета повреждаемости материала в зоне концентратора к моменту образования трещин. При этом анализ повреждаемости материа ла вблизи отверстия к моменту образования трещин N0 проводился при помощи расчета на ЭВМ плоской задачи по МКЭ [1].
Скорректированное таким образом значение еу дало увеличение расчет
ной скорости роста трещины dl/dN при длинах трещин менее 1 мм (см. рис. 5.19, б’ кр. 4 - Р= 1 и 99%).
Подобный учет повреждаемости материала вблизи отверстия к моменту появления трещин N0 проводился также по зависимостям, описанным
в п. 4.4. Для этого из теоретического решения в рядах Хоуланда (для |
|
d/b = 0,3), приведенного в работе [29], определялось изменение теорети |
|
ческого |
коэффициента концентрации упругого напряжения аа по нетто- |
сечению |
образца пластины с отверстием. Затем по формулам (4.10) — |
(4.18) определялось значение долговечности N0 (К = N0 эксп), которому |
для элемента на кромке отверстия присваивалось повреждение, равное единице. При этом проводили расчет по нулевому и первому полуциклам деформирования и для них определяли накопленное усталостное повреж дение. Далее находились значения N0 для точек по нетто-сечению образца и соответствующие им повреждения (уменьшение максимальной отно сительной разрушающей деформации ё~Л. Результаты расчета показаны на рис. 5.19, б (кр. 5 - Р - 1, 50 и 99%).
Расчетные скорости |
роста трещин при значениях Кл , определенных |
|
из эксперимента |
при |
однородном напряженном состоянии для стали |
15Х2НМФА (Кл |
= 0,08 |
для нормальной температуры и 0,3 для 350° С) |
слабо отличаются |
от расчетных значений скоростей при КА = 0,16. Для |
стали Х18Н9 при 650 °С влияние значений КА существенно, в связи с этим проводилось два варианта расчетов —при КА = 0,16 и 0,08.
На рис. 5.20, а показаны результаты расчета скорости развития трещин и ее рассеяния для стали 15Х2НМФА при нормальной температуре с исход ной термообработкой, проведенного для значений ОМС при условии вероят ности Р, равных 1, 50 и 99%. Расчет проводился для условий плоской дефор мации (кр. 1) и плоского напряженного состояния (кр. 2). Значения функ ции f (г/0, так же как и для стали Х18Н9 при 20 °С, в данном случае можно не учитывать. Из рисунка следует, что экспериментальные значения ско ростей роста трещин соответствуют расчетным значениям, полученным для условий плоской деформации, что при толщине образца, равной 6 мм, согласуется с результатами [2]. Экспериментальное рассеяние скоростей роста трещин длиной менее 1 мм существенно больше расчетного рассея ния и имеет большее среднее значение. Учет повреждаемости материала вблизи отверстия по изложенной методике (по изменению а по неттосечению образца) приводит к повышению расчетных скоростей роста тре щин.
Результаты такого расчета показаны на рис. 5.20, а, где кр. 4 соответ ствует расчету долговечности в зоне концентрации по уравнениям для жесткого нагружения, кр. 3 — по уравнениям для мягкого нагружения. При этом кр. 3 соответствует принятая в расчете объемность 0%, а кр. 4 — объемность 11,5%. Получено слабое влияние объемности при расчетах для условий жесткого или мягкого разрушения. На рисунке видно, что кр. 3 и 4 охватывают группу точек, выделяющуюся из массива других то-
125
126
а
7,0
\\ 54i 1________ |
■ h |
|
j |
ж |
|
|
|
|
7 ^ X J { г м |
_ |
f |
||
/% y L O |
/ А |
у |
7 • |
|
|
•• / |
1 |
||
5 Q S \ t*1[£ |
& |
/ |
|
2,0
3,0
'■ k j p |
/,,0 1 S.0 |
¥.0 |
0,0 1,мм |
2 , М М |
~ V \ / \ |
K L |
• |
и . |
|
|
__ _ J ___ |
|
||
|
7 0 |
Lgj/t', Ш а |
Ш |
|
|
|
Рис. 5.21. Экспериментальное и расчетное рассеяния скорости развития трещин от концентратора для стали Х18Н9 при тем пературе 650 ° С (ст = 158 МПа, п = 16)
При Кд: а —0,16; б — 0,08
чек. Эти выделяющиеся точки в эксперименте соответствовали трещинам, которые вышли изнутри образца и становились сквозными трещинами малой длины (от 0,2 до 1 мм). Трещины длиной от 0,05 до 0,4 мм в основ ном являлись угловыми и имели более низкую, чем сквозные, величину размаха коэффициента интенсивности напряжений АК. При определении экспериментальных значений АКе в расчете скоростей роста трещин это не учитывалось и все трещины считались сквозными.
На рис. 5.20, б показаны результаты расчета скорости развития трещин для стали 15Х2НМФА при температуре 350° С (с дополнительной термо обработкой), проведенного для значений ОМС уровней вероятности Р, равных 1, 50 и 99% [30]. Расчетные кр. 1 соответствуют условиям плоской деформации, кр. 2 —условиям плоского напряженного состояния, значе ния функции f(r/f) в расчете не учитывались. Расчетные значения скорости несимметричны, так как для уровня вероятности Р = 1% номинальные на пряжения S n > 1, а для Р - 50 и 99% S n < 1 до длины трещин примерно 1,5 мм. Кривые 3 соответствуют расчету с учетом повреждаемости мате риала по изложенной методике для условий мягкого нагружения с объем ностью, равной 0%, а кр. 4 —расчету для условий жесткого нагружения с объемностью 11,5%.
Результаты расчета скорости развития трещин для стали Х18Н9 при температуре 650° С для различных уровней вероятности Р (1, 50 и 99%) значений ОМС и при КА = 0,16 показаны на рис. 5.21, а [30]. Расчетные кр. 1 соответствуют условиям плоской деформации, кр. 2 — условиям плоского напряженного состояния. Так же как и при расчете по моменту появления трещины N0 (п. 4.4), в данном случае принимались допущения, что параметр циклической диаграммы С является функцией отношения
кратковременных значений величин ОМС cfQ2Q и а*0; |
параметр А = |
||||
= / К |
2т/а ьт)* |
Значения величин огЬт, |
определялась с учетом экви |
||
валентного времени ползучести к |
моменту образования трещин N0 и т = |
||||
= 1,51 ч, а значение величины |
в первом приближении принято рав |
||||
ным |
значению ofQ2Q. Значение $*Кт — экспериментальное; |
принято, что |
|||
возрастанию S fK |
соответствует |
уменьшение |
(проверено расчетом |
скорости роста трещин по значениям ОМС для конкретных образцов).
В расчете учитывалось также упрочнение материала. Кривые 3 соответ ствуют расчету с учетом предварительно накопленной повреждаемости материала по изложенной методике. Учет эквивалентного времени пол зучести т, соответствующего различным длинам трещин, например, для т = 2 ч, дает в данном случае незначительное увеличение скорости роста трещин.
На рис. 5.21, б показана расчетная скорость развития трещины при значении коэффициента КА = 0,08. Видно, что величина параметра диа граммы циклического деформирования А оказывает довольно существен ное влияние на скорость роста трещин и расчет лучше соответствует экспе рименту.
Определение расчетных скоростей развития трещин, удовлетворительно описывающих их экспериментальные значения, позволяет в качестве сле
дующего шага перейти к расчетам |
долговечности |
по развитию тре |
щин и сравнить результаты расчетов |
с фактическими |
долговечностями |
по разным стадиям разрушения. |
|
|
Расчетная оценка рассеяния долговечности по развитию трещин прово дилась при помощи численного интегрирования скорости трещин по ме тоду Уэддла [31]. Значение долговечности, соответствующее прорастанию трещины по длине /, определялось по формуле
|
|
1 - |
A k ] Ki f ( r / l f |
|
AN = N(t) - |
N0 = |
i |
l |
|
f -------------------------- — dl « |
|
|||
|
|
c;AK]Ki f ( r / i f |
|
|
i |
1 |
dl. |
|
|
f — |
2 |
|
(5.18) |
|
l<>AK |
|
|
||
|
|
|
||
|
Ie |
|
|
|
где AKJe при 5 „ тек |
> 1, |
|
|
|
|
1 - |
m (к) |
2 - 0 , 5 [ l - m ( t ) ] ( l - i „ |
тек ) |
|
m ( k ) [ l + m ( k )] |
|||
AKJe = S Птек |
|
1 + m (к) |
(5.19) |
Величина S n — переменное номинальное напряжение в нетто-сечении
Т 0 1C
образца, изменяющееся вследствие развития трещин, для трещины длиной / (для образца шириной Ъс отверстием диаметра d)
'п тек |
= s„ нетто 0 1 _ |
[21/(Ь - |
d )]' |
|
|||
Тогда |
|
|
|
|
2[1 - m(fc)] |
|
|
|
|
|
|
|
|
||
|
|
|
|
m(fc)[ l+m(fc)l |
|
||
N. - N 0 = 2nel |
S „ |
|
|
|
|||
* |
u |
|
f |
"нетто 0 |
|
|
|
|
|
|
|
|
2[ l-m(fc)] |
|
|
|
|
|
|
|
m(k)[ 1 |
+ m(k)] |
X |
|
|
|
21 |
|
|
|
|
|
|
|
|
|
|
|
|
|
|
Ф - d ) |
|
|
2 - 0 ,5 [ 1 - ш ( Л ) ] ( 1 - 5 Птек) |
||
|
|
|
|
|
|
— 2 |
|
|
|
|
|
7T(d+ 21) |
1 + m(k) |
||
|
|
|
\ [ Ъ |
/200] |
|||
Х[УПй |
|
|
|
|
dl |
||
|
|
V tf/jec |
2b |
||||
брутто |
|
sec |
|
||||
|
|
|
|
|
|
|
(5.20) |
где /2 (z) |
|
—аппроксимирующий полином функции Бови, который опреде |
лялся по формуле (5.10); z = 1/(1 + 2l/d).
На рис. 5.22 и 5.23 показаны экспериментальные и условные расчетные
830
|
|
|
7 |
0 |
ff |
/д З |
(в) и 15Х2НМФА (б) |
п ри н о р м а д м ^ ^ м п е ^ а ^ Г 0* расПределения Долговечности |
по парам етру д ли н ы трещ ин ы N(1) сталей Х18Н9 |
||||
в! ° = 285 МШ> " |
= ‘ 8: * ' = 527 МП“' « “ |
I - 0.1; , - 0.5; 3 - |
1.0; 4 - |
2.0; |
5 - |
3.0 |
129
ё
|
0 0 0 |
7 0 0 0 |
2 П 0 Щ N,цикл |
5 0 0 |
7 0 0 |
1 0 3 |
Щ И , ц и к л |
*“?• 5^ |
3 . Экспериментальные и расчетные функции распределения долговечности по параметру длины трещины N(1) сталей 15Х2НМФА |
||||||
W и л18Н9 (о) при повышенных температурах |
|
|
|
|
|
||
a : f |
- 350 |
С; при/, мм: 1 - 0,1; 2 - 0,5; 3 - |
2,0; 4 - 3,0; б: t = 650°С; |
при /, мм: 1 - |
0,2; 2 - 0,5; 3 - |
1,0; 4 - |
2,0; 5 - 4,0 |
распределения чисел циклов N (/) по достижению трещиной определенной длины (пунктир) для сталей Х18Н9 и 15Х2НМФА при нормальной и по вышенных температурах. Сплошными линиями показаны распределения N(l0), от которых начиналось интегрирование. Интервал интегрирования везде выбирался от 0,5 до / мм, для стали 15Х2НМФА при нормальной температуре —от 1,0 мм, так как при длине примерно 0,5—1 мм трещины обычно уже были сквозными и имели экспериментальные значения скоростей роста, сравнимые с расчетными. Для стали Х18Н9 при 650 °С величина коэффициента Кл принята 0,08, в остальных расчетных случаях КА =0,16.
Из рисунков видно, что наклоны расчетных линий подобны экспери ментальным, однако расчетные линии дают в основном несколько завы шенные долговечности, т.е. расчет идет не в запас. Исключение составляет область малых вероятностей Р, где расчетные долговечности обычно мень ше или близки к экспериментальным. Излому расчетных линий N(f) на гра
фиках обычно соответствует переход значений величины S п |
< 1 к значе- |
||
ниям, большим единицы |
(см. рис. 5.23, а); если Sn |
> 1 - |
сразу, с ма- |
лых трещин или £„тек < |
1 —на всем интервале интегрирования, то расчет |
ная линия является близкой к прямой (см. рис. 5.22, а, б).
В целом можно отметить, что экспериментальное рассеяние скоростей роста малоцикловых трещин обеих сталей удовлетворительно соответ ствует расчетному рассеянию, несколько превышая его для трещин малой длины по своей величине и по средним значениям. Использование концеп ции предела трещиностойкости 1Спозволяет улучшить соответствие расчет ных и экспериментальных скоростей роста трещин малой длины. Учет накопления повреждений в зоне концентрации напряжений к моменту образования трещин повышает расчетную скорость трещин малой длины для расчетов в величинах коэффициентов интенсивности деформаций
LKIe.
Расчетные значения условных распределении чисел циклов N(t) по до стижению трещиной определенной длины удовлетворительно соответ ствуют экспериментальным распределениям в области малых уровней вероятности Р.
В соответствии с [1, 2] на стадии развития трещин величины запасов по предельным нагрузкам пр и долговечности nN в зависимости от типа конструкции и условий эксплуатации выбирают не ниже, чем на стадии образования трещин, т.е. nN = 3-Н0. Величины запаса щ на стадии роста трещины принимают равными 2—5. Величины запасов пр nN uNi равны:
пр р = Pp/P°t nN p =Np/Nэ, nt = 1С/Р,
где Рр — предельная нагрузка на стадии развития трещин при числе циклов эксплуатации N =А^; Np —число циклов развития трещины до образования разрушения при эксплуатационных нагрузках Р=РЭ; 1С — критическая
длина трещины; / э —длина трещины при Р - Р эили N = N э.
Так, для стали 15Х2НМФА при нормальной и повышенной температурах
рассеяние долговечности по параметру длины трещины N(1) |
для экспери |
ментальных и расчетных оценок имеет значения запасов nN^ |
(относитель |
но средних величин N(t), уменьшенных в соответствии с нормативным коэффициентом nN в 10 раз) более пяти для уровня вероятности Р = 1% (см. рис. 5.22, 5^5.23, а). При этом запас nN(i) определялся по формуле
= nNN([)p/N(f), где Идг = 10.
ЛИ Т Е Р А Т У Р А
1.Механика малоциклового нагружения / Под ред. Н.А. Махутова, А.Н. Романова. М.: Наука, 1986. 264 с.
2.Махутов Н.А. Деформационные критерии разрушения и расчет элементов кон
струкции на прочность. М. : Машиностроение, 1981. 272 с.
3.Махутов Н.А., Зацаринный В.В., Новиков В.А. Особенности статистических под ходов к оценке малоцикловой прочности и долговечности // Надежность и долго вечность машин и сооружений. Киев: Наук, думка, 1984. Вып. 6. С. 42-51.
4.Вирклер, Хилбери, Гоэл. Статистический характер процесса развития усталостной трещины II Теорет. основы инж. расчетов. 1979. № 2. С. 46-53.
5.Ортиз К. Стохастическая модель скорости роста усталостной трещины // Конструи рование и технология машиностроения. 1987. № 1. С. 15-24.
6.Финкель В.М. Физические основы торможения разрушению. М.: Металлургия,
1977. 360 с.
6.Сакаи Т. Теоретическое рассмотрение распределений усталостной долговечности металлических материалов с учетом распределения дефектов // Нихон к икай
гаккаиромбунсю. А. 1982. Т. 48, №425. С. 11—20 (Наяп. яз.).
8. Танака Ц., Сакаи Т., Окада К. Статистические исследования распределения уста лостных долговечностей, основанные на объединении трещин, образующихся из поверхностных дефектов // Там же. 1984. Т. 50, № 458. С. 1166—1172 (На яп.
я з.).
9.Бледнова Ж.М. Методика определения характеристик циклического упругопласти ческого деформирования в условиях воздействия агрессивных сред // Тез. докл. и сообщ. V Всесоюз. симпоз. ’’Малоцикловая усталость - критерии разрушения и структура материалов” (Волгоград, сент. 1987 г.). Волгоград: ДТНТО, 1987. Ч. 2. С. 211-213.
10.Степнов М.Н. Статистические методы обработки результатов механических испы таний. М.: Машиностроение, 1985. 229 с.
11.Степнов М.Н. Статистическая обработка результатов механических испытаний. М.:‘ Машиностроение, 1972. 232 с.
12.Налимов В.В., Чернова Н.А, Статистические методы планирования экстремальных экспериментов. М.: Наука, 1965. 338 с.
13.Петерсон Р. Коэффициенты концентрации напряжений. М.: Мир, 1977. 302 с.
14.Панасюк В.В., Стадник М.М., Силованюк В.И Концентрация напряжений в трех мерных телах с тонкими включениями. Киев: Наук, думка, 1986. 213 с.
15. Карзов Г.П., Леонов В.П., Тимофеев Б.Т. Сварные сосуды высокого давления.
Л: Машиностроение, 1982. 287 с.
16.Бледнова Ж.М. Восстановление сплошности селективным осаждением легирую щего компонента из жидкой фазы // Сопротивление материалов в агрессивных средах. Краснодар: Политехи, ин^г, 1986. С. 28-49.
17.Трощенко В.Т., Покровский В.В., Прокопенко А.В. Трещиностойкость металлов при циклическом нагружении. Киев: Наук, думка, 1987. 251 с.
18.Кудрявцев ИИ. Нераспространяющиеся усталостные трещины. М.: Машинострое ние, 1982. 174 с.
19. Murakami Y.t Endo |
Т. Effects of small defects on fatigue strength of metals // Intern, |
i J. Fat. 1980. Vol. 2, |
N 1. P. 23-30. |
20.Murakami Y., Endo M. Quantitative evaluation of fatigue strength of metals containing various small defects or cracks// Eng. Fract. Mech. 1983. Vol. 17, N 1. P. 1-15.
21.РД-50-345-82. Расчеты и испытания на прочность. Методы механических испыта ний металлов. Определение характеристик трещиностойкости (вязкости разру шения) при циклическом нагружении. М.: Изд-во стандартов, 1983. 96 с.
22.Б роек Д. Основы механики разрушения. М.: Высш. шк., 1980. 368 с.
23.Bowie O.L. Analysis of an infinite plate containing radial cracks originating at the boun dary of an internal hole // J. Math, and Phys. 1956. Vol. 25. P. 60—71.
24. Доценко A.M., Городниченко В.И. О погрешности измерения длины трещины фольговыми датчиками трещины и методики их учета при анализе результатов испытаний материалов на трещиностойкость // Пробл. прочности. 1984. №5.
С.119-124.
25.Atanasiu N.E., Irimescu B.R. Fatigue crack propagation and treshold of type 304L
austenite stainless steel // Mechanical behaviour of materials-IV (ICM 4). 1984. Vol. 2.
P.841-847.
26.Морозов E.M. Расчет на прочность при наличии трещин // Прочность материалов
иконструкций. Киев: Наук, думка, 1975. С. 323-333.
27.Маркочев В.М., Морозов Е Ж Предел трещиностойкости в системе критериев прочности тел с трещинами // Исследование хрупкой прочности строительных металлических конструкций. М.: ЦНИИПСК. 1982. С. 102-112.
28.Маркочев ВЖ. Расчет на прочность при наличии трещин // Пробл. прочности.
1980. № 1. С. 3 -6 .
29. Савин Г.Н. Распределение напряжений около отверстий. Киев: Наук, думка, 1968.
887с.
30.Махутов Н.А., Зацаринный В.В., Новиков В.А. Влияние повышенных температур на характеристики деформирования и на развитие малоцикловых трещин в кор пусных сталях // Тез. докл. и сообщ. V Всесоюз. симпоз. ’’Малоцикловая уста лость - критерии разрушения и структуры материалов” (Волгоград, сент. 1987 г .). Волгоград: ДТНТО, 1987. Ч. 2. С. 116-118 а.
31.Ламуатье Ж.П. Упражнения по программированию на Фортране-IV. М.: Мир, 1978.
162с.