
Г л ава 6
МЕТОДЫ ПОВЫШЕНИЯ УСТОЙЧИВОСТИ ХАРАКТЕРИСТИК СОПРОТИВЛЕНИЯ МАЛОЦИКЛОВОЙ УСТАЛОСТИ
6.1. Оценка параметров распределения и построение функции распределения пределов прочности материалов с покрытиями
Определение пределов прочности различных металлопокрытий, широко применяемых для повышения износостойкости и коррозионной стойкости деталей машин, сопряжено с известными экспериментальными трудностя ми. Установленные функции распределения пределов прочности компози ции сталь + покрытие (КСП) [1], учитывающие неоднородность поверх ностных и объемных дефектов в КСП, позволили предложить методику получения оценок параметров распределения пределов прочности покрытия по данным раздельного испытания образцов из материала основы и сталей с покрытиями.
Распределение, вытекающее из обобщенной теории хрупкого разруше ния [2] , применительно к КСП имеет вид
F (obK) = 1-ех р |
) |
А |
( |
°Ъп S Q 2 |
|
Ло |
|
(6.1) |
|||
где оЬк, оьо, оЬп - |
|
$С2 |
|||
соответственно пределы |
прочности КСП, материала |
||||
основы и покрытия; |
S0 i> S02 — минимальные |
прочности объемных и |
поверхностных элементов; £ с 1»*$С2 —константы, имеющие размерность напряжения; а х, а2 — любые действительные положительные числа; Ао, V0 —площадь и объем стандартного образца без покрытия; А , V —площадь и объем испытуемого образца с покрытием; F(obK) — функция распре деления КСП.
Вычисление параметров распределения пределов прочности покрытия осуществляем в следующей последовательности. Путем формальных преоб разований из (6.1) получаем
а2In(оъп - SQ2) - ot2In Sc 2 =InIn П - ^ К к ) ] exP |
Sc i ' J (6.2) |
' |
Здесь принято, что A = A 0 и V = V0 (слой покрытия весьма незначите лен). Так как параметры oci, So l , S c i материалы основы известны (их оценки легко установить из опыта), то задача определения параметров распределения оЬп покрытия а2, S02 и $сг сводится к решению системы нел чнейных уравнений
a2ln(obnj - S 02) - o t2\nSC2 = Yj\ /= 1 ,2 ,3 , |
(6.3) |
У> = In In [1 —F(aftK)] exp |
°boj - $ о \ |
(6.4) |
|
|
Sc |
Составление /-уравнений можно осуществить с помощью метода разде ляющих разбиений [3]. Для этого выбирают границы разбиений оЪ1 < < оъ2 < оьз (obKj = obQj = obn/) и подсчитывают количество m(obj) значений пределов прочности, попадающих в интервал (0, аЬ/). Отношения
v(Pbj) = m(pbj)ln |
(6.5) |
представляют собой эмпирические оценки функции распределения F(obKJ) КСП (п — общее число опытов в выборке). По назначенным границам разбиения obj с помощью оценок параметров распределения оЪо материала основы вычисляем, согласно (6.4), значения У) для системы (6.3).
Параметр распределения SQ2 находят из трансцендентного уравнения
(Ръ2 ~ S Q 2 ) = (°ьз ~ S o i)Z (9ь\ - S 0 2 ) 1 Zу |
(6.6) |
|||
где Z = (Y i~ Y2)I(YI - |
Y3) . |
|
||
Решение уравнения |
(6.6) существует в интервале 0 < SQ2 < |
оЬ1 при |
||
выполнении условия |
|
|
||
(ob2 /obi) < (аьз1°ы)г |
(6.7) |
|||
Параметры а2 и Sc 2 |
ПРИ установленном SQ 2 получают по зависимостям: |
|||
он = |
Y X - Y 2____________ |
(6-8) |
||
S0 2 ) — ]п(°Ъ 2 - $ 0 2 ) |
||||
Щ ° Ь 1 - |
|
|||
&С2 ~ |
|
° Ъ \ - $ 0 2 |
(6.9) |
|
v(Pb 1)] exp[(aftj - SQi )ISCi ] “‘} 1) 1/a’ |
||||
On{[ 1 - |
|
|||
Предложенная |
методика использовалась для определения оценок пара |
метров функции распределения и характеристик рассеяния пределов проч ности оЬп железных покрытий по данным испытания образцов из стали 30 с электролитическим железом. Прямоугольные пластинки размерами 130 X 20 X 2 мм из стали с покрытием толщиной 0,3 мм испытывались на растяжение на машине МР-0,5. Покрытия получены из сульфатного
электролита |
железнения |
при |
следующих |
режимах осаждения: Дк = |
= 1,5 кА/м2; |
Г=ЗЗЗК; рН = 0,8-Н,0. Статическая прочность стали 30 (ма |
|||
териал основы) получена |
на подобных образцах без покрытия. Предел |
|||
прочности покрытия оЬп |
(для |
сравнения) |
определяется на аналогичных |
образцах, подготовленных по следующей методике. Покрытие толщиной 0,6 мм осаждалось на одну сторону медной пластинки в соответствии с принятым режимом. После осаждения образцы зажимали в специаль ном приспособлении, исключающем их деформацию, выравнивали покры тие на выбранном участке с помощью мелкой абразивной шкурки и уда ляли медную основу.
По данным испытаний образцов из стали 30 определялись оценки пара метров распределения Вейбулла в соответствии с ГОСТ 11.007-75. В качест ве оценки параметра SQ г (минимальная прочность) принималось наимень-
Таблица 6.1
Статистические характеристики рассеяния пределов прочности КСП
Характеристика |
Биметалл |
Материал основы |
|
Покрытие |
|
|
|
опыт |
расчет |
п |
77 |
36 |
6 |
|
obj, МПа |
325 |
420 |
158 |
149 |
S(obj), МПа |
59,8 |
42 |
28,8 |
40,2 |
vx(250) |
0,1688 |
— |
— |
— |
|
|
|||
у2 (300) |
0,2857 |
— |
— |
— |
|
|
|||
у3(350) |
0,4458 |
— |
— |
— |
<*t |
— |
3,30 |
— |
1,488 |
|
|
|
|
|
SQi, МПа |
— |
294 |
— |
90 |
Scv м Па |
— |
140,5 |
— |
498 |
|
|
|
|
шее значение опытных оЬо материала основы. С помощью среднего значе ния предела прочности оЪо и среднеквадратичного отклонения S (pbo) (табл. 6.1) вычисляем отношение
vb = S(obo)l(obo - S 0 i ) = 0,333. |
(6.10) |
По полученному значению vb, согласно ГОСТ 11.007-75, находим оценку параметра формы а г = 3,30 и значение коэффициента къ = 0,897. Параметр масштаба SCi вычисляем по зависимости
$ а = (°ьо —So\)lk'b = 140,5. |
(6.11) |
Оценки параметров распределения a2, S 02 и S c 2 покрытия, вычислен ные по зависимостям (6.6), (6.8), (6.9), представлены в табл. 6.1.
Там же приведены эмпирические оценки v(obJ) функции распределения F(pьк/) Для принятых границ разбиения: оьг = 250, оЬ2 = 300, оьз = = 350 МПа.
Оценки среднего оЬп и среднеквадратичного отклонения ^(а^п) пре
делов прочности покрытия получаем по формулам |
|
|
оЬп = s02+ S |
Г(1 + 1/в „ ), |
(6.12) |
S(pbu) = |
V r(l + 2/e3) - Г2(1 + Ца2), |
(6.13) |
где Г(1 + i/oc2) —т-фуякдия*
Сравнение опытных значений пределов прочности покрытия, получен ных непосредственным испытанием образцов из покрытия, с расчетными не обнаружило статистически значимой разности. Специально проведенные исследования показали, что достаточный объем испытаний составляет n = 15-^30 образцов.
Разрушение КСП при статическом нагружении можно описать на основе принципа наибольшего дефекта [4]. Принцип наибольшего дефекта основан на допущении, что прочность элемента определяется наибольшим имеющим-
ся дефектом. Наиболее распространенными дефектами КСП являются трещины.
Имеющийся экспериментальный материал позволяет утверждать, что трещины, разных размеров распределены в КСП независимо и случайно, число трещин очень велико; плотность распределения размеров трещин имеет экспоненциальный характер. Принцип наибольшего дефекта требует также принятия следующих предложений: прочность на разрыв является линейной функцией размера самой большой трещины, какова бы ни была ее величина, и эта прочность уменьшается с увеличением размера тре щин [4]. При таких условиях распределение наибольших трещин является первым предельным распределением наибольших значений, а распределе ние прочности на разрыв —асимптотическим распределением наименьших значений [5]. В этом случае исходное распределение трещин несущественно.
Аналогичный вывод можно получить с помощью моделей наиболее слабого звена. Если предположить, что исходное распределение прочности звеньев является нормальным, то прочность биметаллического образца будет иметь распределение наименьших значений первого типа [5].
Функция распределения наименьших значений первого типа имеет вид
F(pb)= 1 - exp exp |
(6.14) |
0 < о ь <°°У (*i>0,
где «1 и и г —параметры распределения наименьшего значения. Полученный на основе принятых предположений вывод проверялся
экспериментально путем непосредственного испытания на разрыв пласти нок размером 130 X 1 0X 03 мм из нормализованной стали 30 с железным покрытием толщиной А = 0,3 мм. Рассматривались девять различных вы борок, охватывающих весь диапазон изменения технологических факторов осаждения из сульфатного электролита.
Оценка параметров распределения наименьших значений для каждой выборки из п опытов производилась по методике [6]. Для этого вначале вычисляли средние значения оЬк и среднеквадратичные отклонения S(pbK) пределов прочности КСП, а затем находили оценки параметров ах
и и i из соотношений |
|
1 l&i =S(pbK)/oNi |
(6.15) |
и l = O bK + Yjsrloti, |
(6.16) |
где YN и oN — средние и стандартные отклонения приведенных экстре мальных значений Y - &\(рЬк —и i) как функции числа наименьших зна чений N, взятых из [6, табл. 6.2.3]. Полагаем N = п, причем п —число испытанных образцов. Установленные оценки параметров для всех девяти выборок приведены в табл. 6.2.
Графическое представление вероятностей, оценивание соответствия распределения экстремальных значений первого типа экспериментальным данным с помощью оценок и #1 показали, что выбранная модель являет ся подходящей для описания выборочных совокупностей. Статистическая проверка допущения о распределении, проведенная с помощью критерия
Пирсона, количественно подтвердила вывод о том, что принятая модель
Т а б л и ца 6 2
Количество испытаний, оценки параметров распределений и результаты проверки адекватности моделей
п |
°Ь к’ МПа |
S (РЬк) » |
1/а, |
А |
Р(х*) |
/ |
X2 |
|
|||||||
|
|
МПа |
|
|
|
|
|
60 |
286,2 |
52,2 |
44,4380 |
310,7333 |
0,70 |
2 |
1,38 |
68 |
290,8 |
40,3 |
34,0544 |
309,6764 |
0,30 |
2 |
2,25 |
57 |
243,2 |
31,1 |
26,5630 |
257,8389 |
0,20-0,30 |
2 |
2,98 |
77 |
324,5 |
59,8 |
50,1909 |
352,4212 |
0,30-0,50 |
2 |
1,85 |
78 |
299,9 |
54,5 |
45,7100 |
325,3376 |
0,50-0,30 |
2 |
1,64 |
56 |
281,9 |
37,8 |
32,3187 |
299,7012 |
0,30 |
3 |
3,34 |
86 |
242,8 |
43,8 |
36,5609 |
263,2010 |
0,20-0,30 |
2 |
2,80 |
93 |
290,5 |
40,9 |
34,0096 |
309,5131 |
0,30-0,50 |
2 |
2,24 |
143 |
269,9 |
56,1 |
45,7847 |
295,7500 |
0,10-0,20 |
3 |
4,81 |
минимальных значений первого типа весьма адекватно описывала опытные данные (см. табл. 6.2).
Существенное практическое значение в испытаниях на разрыв КСП имеет распределение наименьших значений пределов прочности оЬк по всем девяти выборкам.
Согласие полученного на основе принятых предположений вывода с
данными эксперимента проверялось по следующей методике. |
|
|
1. |
Образуем вариационный ряд наименьших значений пределов проч |
|
ности биметалла оьк / по данным N= 9 выборок. |
|
|
°ъкх < °ь к 2< --- < °ъ к 9 = 130< 150< 160< 166 < 172< 180< 187 < |
||
<200 <210 МПа. |
|
|
2. Вычисляем среднее значение а йк и среднее квадратичное отклонение |
||
S(p bк ) |
для наименьших значений: оЬк = 172,7777 МПа, |
S(obK) = |
= 24,8484 МПа. |
Y = 0,4902 |
|
3. Из |
[6, табл. 6.2.3] принимаем рспомогательные значения |
и oN = 0,9288, представляющие среднее значение и среднее квадратичное отклонение величин YK (к = 1,2,.. ., 9).
4. |
Находим оценку 1/&1 параметра 1/OLI по уравнению |
|
||
|
1 |
S(obK) |
24,8484 |
(6.17) |
|
|
|
----------- = 26,7532. |
|
&1 |
° N |
0,9288 |
|
|
5. |
Вычисляем оценку й\ параметра по уравнению |
|
||
Mi =abK + YN ■1/о?! = 172,7777 + 0,4902-26,7532= 185,8921. |
(6.18) |
6. Осуществляем проверку адекватности модели первого предельного распределения наименьших значений оЬк путем графического представле ния вероятности, для чего последовательно выполняем следующие опера ции: 1) каждому члену ряда obKi ставится в соответствие число
(6.19)
л + 1 ’
р,%
0,95
0,90
0,00
0,70
0,50
0,30
0,09
700 720 |
700 |
750 |
790 |
ZOO |
4 rt' т а
Рис. 6.1. Распределение наименьших значений пределов проч ности ав к КСП
оценивающее отвечающую ему вероятность F (pbKi); 2) по [7, табл. IX приложений], приравнивая значения соответствующим значениям функ ции </?(—У/), определяем нормированные отклонения У*. Нормированные отклонения У* для первого типа распределения крайних членов вариа ционного ряда при отсутствии таблиц могут быть определены из соотно шения [7]
У,= 2,3026 lg(—lg JP/) + 0,83405; |
(6.20) |
3) представляем полученные данные в координатах Yj-obKi в натураль ном масштабе либо на вероятностной бумаге для распределения экстре мальных значений первого типа в координатах F(obKi) —obKi (рис. 6.1); 4) оцениваем соответствие выбранной модели экстремальных наименьших
значений первого типа с экспериментальными данными с помощью оценок |
|
л |
л |
С*1 |
ИЫх . |
|
Так как опытные точки группируются вблизи выравнивающей прямой |
У = l / c t i (o bKi — M i ) с точностью ±3%, то выбранная модель является подходящей для описания минимальных значений пределов прочности
КСП. |
Записывается функция распределения минимальных значений пре |
|
7. |
||
делов прочности биметалла в виде |
|
|
F(oЬк min) = 1 - ехр{-ехр[0,0374(аЬк- 185,8921)]}. |
(6.21) |
|
По |
графику F(obK) - o bK (см. рис. 6.1) находим, |
что минимальное |
значение предела прочности КСП при вероятности разрушения Р = 0,95 составит оЬк — 100 МПа.
Точные значения пределов прочности КСП для различных вероятностей разрушения могут быть установлены с помощью зависимости
°ьк(Р) |
l n l - l n [ l —F ( g bK)]l |
(6.22) |
Минимальное значение прочности на разрыв для вероятности разрушения Р = 0,95, установленное с помощью (6.22), равно аЬк = 106,43 МПа. Раз ность между пределом прочности obKi найденным по рис. 6.1, и точным выражением (6.22) не превышает 6%, что вполне премлемо в инженерных задачах.
62. Статистические закономерности разрушения композиции сталь + покрытие при статическом нагружении
Статистические закономерности разрушения биметалла в условиях ста тического нагружения требуют рассмотрения двух взаимосвязанных за дач: гипотетические функции распределения пределов прочности с учетом поверхностных и объемных повреждений; проявления масштабного эффек та и его связь с различными дефектами КСП.
Физико-статистический подход к выбору аппроксимирующих распре делений связан с необходимостью раздельного и совместного учета объем ных и поверхностных дефектов материала основы и покрытия. Выдвиже ние и обоснование моделей, адекватно описывающих физику протекаю щих процессов и механику разрушения, рассмотрим для каждого случая.
Наличие поверхностных и объемных дефектов говорит о том, что опыт ные данные следует объединять в две группы, каждая из которых харак теризуется своим набором параметров [4]. Если допущение о модели наислабейшего звена представляется для биметалла оправданным, то объяснением этому может послужить существование двух групп повреж дений различного характера, каждая из которых играет наиболее важную роль в определенном, отличном от других интервале напряжений. В слу чае КСП процесс разрушения может начинаться в покрытии или основе при различных уровнях напряжений и тем самым будет определяться различными повреждениями.
Дефекты, распределенные на поверхности. Рассмотрим часть поверх ности покрытия площадью А , на которой действует равномерное растя гивающее напряжение о. Предположим, что на единицу площади поверх ности приходится g(S)dS трещин, которым соответствует прочность в диапазоне от S до S + dS. Допустим, что материал покрытия имеет функ цию распределения g(S) трещин на единицу поверхности. Тогда вероят
ность разрушения бесконечно |
малой площади ЬА при напряжении < S i |
равна |
|
8* = ЬА f g(S)dS. |
(6.23) |
о |
|
Если рассмотреть тело как сплошное, состоящее из конечного числа п=А/ЬА бесконечно малых площадей, то вероятность неразрушения би металла при напряжении, меньшем или равном S i , равна [8]
1 —/>= (1 —Ьф)п = [1 - Ь А fgS (S )d S ]n. |
(6.24) |
о |
|
В пределе при ЬА -*0 вероятность разрушения при o ^ S i |
составит |
P (Si)= l - е х р [ - А f'g(S)dS]. |
(6.25) |
Предположим, что трещины разных размеров распределены в покры тии независимо и случайно: плотность распределения размеров трещин имеет экспоненциальную или степенную функцию, число трещин очень велико, прочность на разрыв является линейной функцией размера са мой большой трещины, какова бы ни была ее величина, и эта прочность уменьшается с увеличением размера трещины. При этих допущениях рас пределение трещин описывается первым предельным распределением наибольших значений, а распределение прочности на разрыв — асимпто тическим распределением наименьших значений [8].
Дефекты, распределенные по объему. В общем объеме работающих деталей объем покрытий весьма незначителен (Рджр < V ^ ) из-за ма лой толщины. Данное обстоятельство позволяет выдвинуть в первом приближении гипотезу о том, что прочность биметалла связана с дефек тами структуры, распределенными в объеме изделия. Известные работы по влиянию структуры на механические свойства материалов позволяют предположить, что распределение дефектов в объеме аналогично распре делению размеров зерен, для которых может быть принят нормальный закон [8]. Если средний размер зерна d и стандартное отклонение S(d),
то плотность дефектов P(d) |
на единицу объема, имеющих размеры от d |
||
до d + dd, находится согласно |
[8]: |
|
|
P(d) = г г |
exp |
1 |
(6.26) |
> |
|||
d 3[S(d)y/2ir |
|
2 |
|
где Р — коэффициент пропорциональности между плотностью дефектов |
|||
и плотностью распределения зерен. |
|
||
Так как напряжение разрушения а от дефекта размера d равно [8] |
|
||
о = у/паЕ/[2(1 - n 2)d}', |
|
(6.27) |
то вероятность разрушения Р(о) |
при напряжении не выше а в равномер |
|
но нагруженном объеме V биметалла будет |
|
|
- |
|
|
Р(р) = 1 —ехр - |
V S(a) |
(6.28) |
d 3 (<;)L |
/ |
В данном случае используется подход, заключающийся в выборе ба зовой величины — размера зерна Д распределение которой известно, и функциональной зависимости (627) между рассматриваемыми случай ными величинами.
Неоднородное распределение дефектов в биметалле. Прочность покры тия заметно отличается от прочности материала основы, так как роль поверхностных дефектов покрытия и внутренних повреждений материа ла основы неодинакова. Плэтому дня правильного описания явления раз рушения КСП необходимо рассматривать совместно поверхностные и объем ные дефекты. Рассматриваемый биметаллический материал представляет собой классический пример неоднородного распределения поверхностных и объемных дефектов, и, следовательно, применение обобщенной статис тической теории хрупкого разрушения в данном случае обоснованно.
Согласно [2], распределение пределов прочности Оъ материала с учетом

ob f ob f(Pb)dOb = a, + (oo |
/ А 0\ 1/т |
Г(1 + 1 lm), |
(6.32) |
- a ,) I — J |
|||
где Г (1 + 1 /т) —7-функция. |
|
|
|
Дисперсия пределов прочности S 2 (оь) КСП |
|
||
А 0 \ 21т |
|
|
|
(— ) |
[Г (1 + 2/т) —Г 2(1 + 1 /т)]. |
(6.33) |
|
Коэффициент вариации v(ob) предела прочности биметалла |
|
||
Оо - а,) (А01А)1>т у /г (1 + 2/т) —Г2(1 + 1/от) |
(6.34) |
||
и(ов) = |
|
|
|
а, + (а о -а ,)0 4 оМ )1/ т Г(1 + 1/т ) |
|
Минимальная прочность а/, определяемая экспериментально, представ ляет собой субъективную оценку, чувствительна к изменению размеров [8]. Полученную в лабораторных условиях а/ нельзя использовать в ка честве верхнего предела безопасных напряжений для натуральных эле ментов. Поэтому обычно принимают а/ = 0, тогда коэффициент вариа ции становится функцией только показателя т, который является харак теристикой материала композиции.
Формулы (6.32) и (6.33) дают количественное значение масштабно го эффекта в зависимости от площади покрытия. Предел прочности оЬ2 делали с покрытием площади А 2 может быть определен по данным лабо раторных испытаний геометрически подобных образцов с площадью по крытия А% при однородном напряженном состоянии. Различие в средней прочности равно
Оы - О ь 2 = |
[(А1/А1) 1/т- 1]Г(1 + 1/т) |
|
|
|
S(obi ) |
V r ( l |
+ 2/т) —Га(1 + 1/т ) |
’ |
(-6,35') |
где a&1, S(ob l) - |
соответственно предел |
прочности и |
среднеквадратич |
|
ное отклонение образцов с покрытием. |
|
|
||
Проектное |
напряжение ар для натурного элемента с площадью А р |
|||
при вероятности разрушения Р определится из выражения [8] |
||||
Ор1дь = [(А/Ар)Р/In 2] 1>т, |
|
(6.36) |
где оь —средняя прочность лабораторного образца с площадью А .
Таким образом, основной статистический аспект разрушения, состоя щий в увеличении вероятности разрушения с ростом площади рассматри ваемого образца, вытекает из чисто вероятностных рассуждений и требует экспериментальной проверки.
По результатам испытаний на растяжение прямоугольных пластинок размером 130 X 10 X 0,3 из стали 30 с покрытием толщиной 0,3 мм полу чена достаточно репрезентативная выборка. Для выборочной совокупнос ти рассчитывались оценки среднего db9 дисперсии S 2 (рь), коэффициента вариации v(ob) 9 асимметрии ^ b \ и эксцесса Ь2. Оценки и доверительные границы для параметров распределения (6.31) определялись по ГОСТ 11.007-75. Статистическая проверка допущения о распределении, выполнен ная с помощью критерия х >показала, что данные выборки не противоре
чат модели третьего предельного распределения для наименьших значений членов вариационного ряда. Следовательно, при использовании модели поверхностного распределения дефектов в материале покрытия стати ческая прочность КСП адекватно описывается функцией Вейбулла, которая совпадает с третьим предельным распределением для экстремальных зна чений [1].
|
МПа |
S (o b), |
v{ab) |
N/T, |
& |
|
МПа |
|
|
|
|
150 |
270 |
56,1 |
20,8 |
0,159 |
3,146 |
°о ~ аЬ |
т |
|
^ (х Ч к )} |
|
|
МПа |
|
МПа |
|
|
|
172,6 |
3,00 |
115,8 |
к = 3, |
Р = 0,30 |
|
Для экспериментальной проверки масштабного фактора испытывались на растяжение пять серий образцов из нормализованной стали 45 с покры тием из сульфатно-хлористого электролита (в каждой сёрии по 18 образ цов) . Вычислялись средние пределы прочности биметалла оъ в двух сериях и из условия Ом/obs = (As/А i ) 1/m определялся показатель степени т = 6,4187.
Зависимость среднего предела прочности оь биметалла сталь 45—элект
ролитическое покрытие от площади поверхности А |
можно представить |
формулой вида |
|
Оь = оьо [а + Ъ (А0/АУ1т ] , |
(6.37) |
где а, Ъ —эмпирические коэффициенты; А о — некоторая стандартная пло щадь; оьо — соответствующий стандартной площади поверхности предел прочности.
По данным эксперимента получено: а = 0,182, Ъ = 0,818, т = 6,4187 и о~ьо = 522 МПа для принятого А 0 = 1004,8 мм2. Сравнивая формулы (6.32) и (6.37), находим
ЬдЪо |
(6.38) |
°i ~ аоъо = 95,0 МПа, о0 —о/ = — lj~) = |
Данные сравнения (табл. 6.3) показывают удовлетворительное совпа дение опытных и расчетных оценок. Несколько меньшие значения опыт ных коэффициентов вариации по сравнению с теоретическими связаны с тем, что резко выделяющиеся экспериментальные данные предваритель но отбрасывались.
В общем объеме элемента доля покрытий незначительна. Данное обсто ятельство позволяет выдвинуть гипотезу о том, что прочность компози ции определяется дефектами, распределенными по объему. Допустим, что распределение дефектов в объеме аналогично распределению размеров зерен, для которых может быть принят нормальный закон. Наличие функ циональной связи между прочностью и размерами зерна позволило на ос нове физико-статистического подхода к выбору статистической модели на базовой величине с известным распределением заключить, что распре деление пределов прочности аь также является нормальным. Так как на-
144
Т а б л и ц а 6.3
Рабочие |
характери сти ки испы танны х образц ов и результаты сравнения |
|
||||
<*0. |
'о» |
А, |
|
СТЬ> МПа |
и (ой), % |
|
мм |
мм |
мм2 |
опыт |
расчет |
опыт |
расчет |
|
|
|
||||
25 |
125 |
9812,5 |
366 |
332,4 |
19,2 |
18,2 |
20 |
100 |
6280,0 |
392 |
363,3 |
17,4 |
18,2 |
15 |
75 |
3532,5 |
437 |
407 |
16,9 |
18,2 |
10 |
50 |
1570 |
486 |
477,8 |
14,7 |
18,2 |
8 |
40 |
1004,8 |
522 |
522 |
•15,0 |
18,2 |
пряжение разрушения о представляет собой монотонную функцию o(d) от размера зерна, то плотность распределения ip(obK) при известной/^) определяется из соотношения
<P(obK) = f[d(a)] |
bd(o) |
(6.39) |
где d (о) - функция, обратная функции o(d), подставляется в f( d ) .
При растяжении критическое значение нормального растягивающего напряжения оЬи, при котором происходит разрушение образца, связано
с упругими постоянными, поверхностной энергией у |
и величиной зерна |
d зависимостью Холла—Петча [9] |
|
аЬи = а0 + Kd 1/2, |
(6.40) |
где
K = (6nyG/l - д ) 1/2.
Величина о0 представляет собой* сопротивление движению дислока ций, зависит от содержания примесей, температуры деформации, но не зависит от приложенных напряжений; G —модуль сдвига; д —коэффи циент Пуассона; d —средний размер зерна; а0 и К —постоянные для дан ного сплава и условий деформирования.
Обратная функция оЬи (d) имеет вид
d = К 2/(оЬи - а0)2. |
(6.41) |
Закон распределения напряжения разрушения, полученный методом
преобразования случайных величин, согласно (6.39), имеет вид f
2К 2 |
1 |
К 2 - d {аЬи - ff0)2 |
,(6.42) |
f(0 bu) |
Р _ 2 |
S(d)(abu - a 0)2 J |
|
y/2nS(d) (аЬи - сто)3 |
|
где d и S(d) —соответственно среднее значение размера зерна и его сред неквадратичное отклонение.
Среднее значение предела прочности КСП равно
- |
;оо |
2К 2аЬи |
1 |
К 2 - d ( o bu -Qo) |
|
о |
V2VS(d)(abu - a 0)2 |
exp |
S(d)(obu - a 0)2 } |
|
2 |
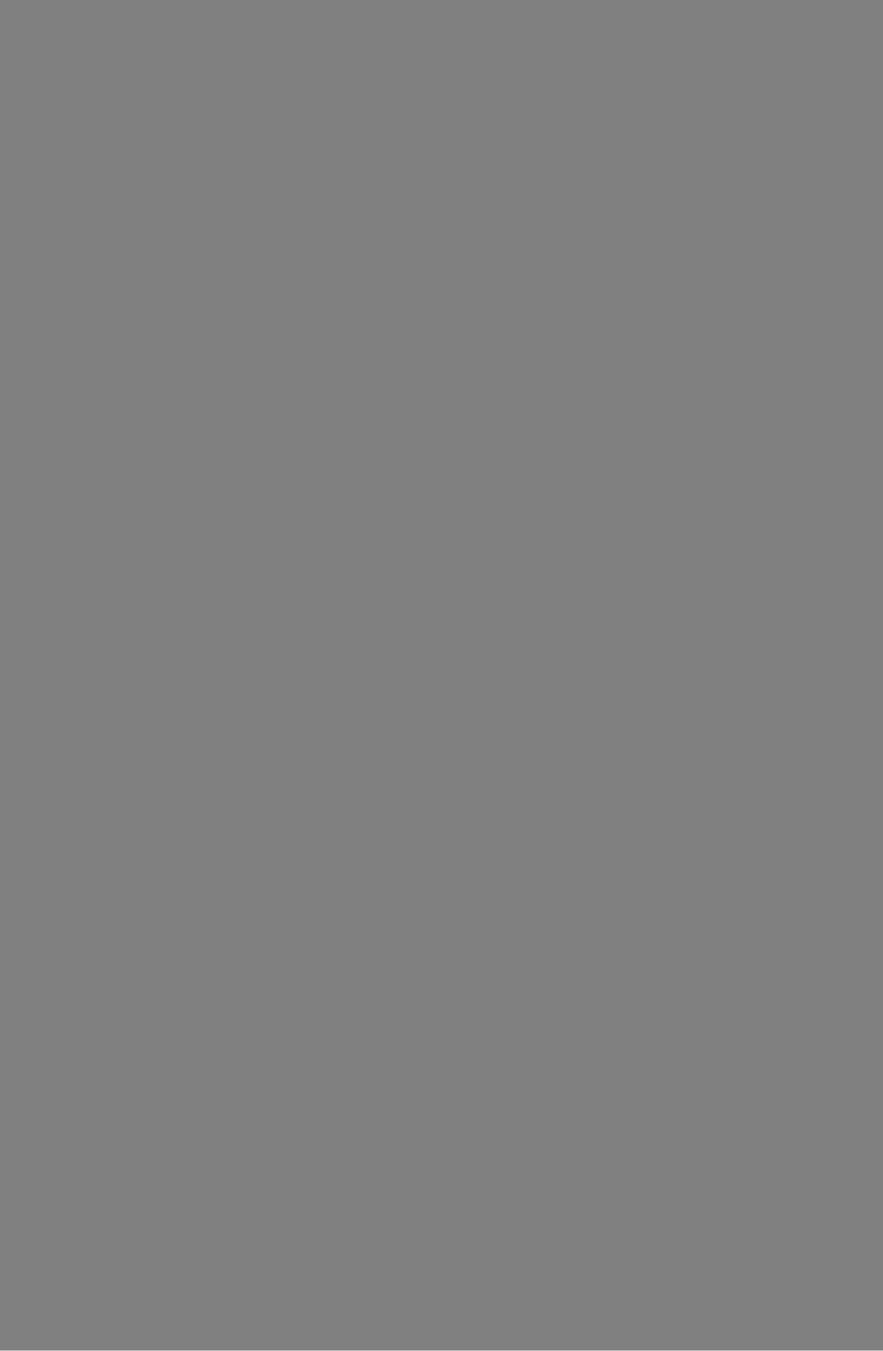
ценная точка достаточно близко расположена к координатам нормального распределения. Однако построение области рассеяния оценок Ь\ и Ьг показало, что наряду с нормальным должны быть рассмотрены и другие гипотетические законы распределения. Окончательное решение о выборе аппроксимирующего распределения, осуществленное с помощью х2-кри терия, показало, что нет оснований отвергать допущение о нормальности распределения предела прочности биметаллических образцов (х2 = 2,25 < < Хтабл = 3,36 при к = 4) и Р > 0,50.
Доверительные интервалы для среднего значения и среднеквадратич ного отклонения пределов прочности КСП соответственно равны:
Р 1261 < дьК < 279 МПа} =0,95,
Р \ 49,7 < S (o bK)< 62,5 МПа! =0,95.
Проверка |
других распределений |
дала значения х 2-критерия |
меньше |
критического (Р<0,05). |
|
|
|
Статистическим анализом данных |
испытаний (см. табл. 6.3) |
получен |
|
конкретный |
вид функций (6.44) для изделий из нормализованной стали |
||
45 с железным покрытием |
|
|
|
дь (V) = 609,1 - 55,2 Vin VIVo, |
|
(6.45) |
|
где VQ —объем зерна поликристалла. |
|
|
6.2.2. Функция распределения при совместном учете поверхностных и объемных дефектов
Наличие поверхностных и объемных дефектов, неоднородно распреде ленных в композиции, предлагается учитывать согласно обобщенной тео рии хрупкого разрушения [2] • Обобщенное распределение применительно
к КСП преобразуется в (6.1). |
|
|
||||
Зависимость |
(6.1) получена из распределения (6.29) путем представле |
|||||
ния объема V КСП в виде объема материала основы V\ и поверхностного |
||||||
слоя у _ |
у = у п. Допустим, что в объеме V\ материала основы параметра |
|||||
ми |
распределения являются 5oi> *^ci и a i* а в объеме покрытия |
5о2> |
||||
Sc 2 |
и |
Так как поверхностный слой покрытия весьма тонок, то |
Vn, |
|||
и можно принять Vi = V. |
|
|
||||
Распределение |
(6.1) |
позволяет описать двойственный |
характер |
масш |
||
табного |
эффекта. Среднее значение предела прочности |
КСП при |
*S*o i = |
|||
= S02 =S0 находим из соотношения [2] |
|
|
||||
obK =So+ sci ( у ) |
7exp ( - «Л - W *' )du, |
|
(6.46) |
/ У \ 1,а* (Оьо- S o )
(6.47)
\ V 0 J |
Sci |
Интеграл (6.47) выражается непосредственно через табулированные, функции только при ах = = & [2]. Тогда среднее значение предела проч-
Т а б л и ц а 6.4
Сравнение расчетных и опытных значений средних пределов прочности КСП
А, м м 2 |
|
Расчетный оЬк, МПа |
Опытный |
|
К, м м 3 |
ос= 3,30 |
а = 6,42 |
оЬк, МПа |
|
|
|
|
||
9812 |
6 1 3 2 8 |
251 |
326 |
* 332 |
6280 |
3 1 4 0 0 |
289 |
380 |
363 |
3532 |
13427 |
352 |
423 |
437 |
1570 |
3925 |
476 |
494 |
478 |
1005 |
2 0 1 2 |
586 |
541 |
522 |
ности изделия с покрытием объемом V и поверхностью А получаем из
°Ьк “ So + Sc i |
A |
Vo |
Г (1 + 1/ос). |
(6.48) |
1 + -------- |
||||
|
А о |
V |
|
|
По зависимости |
(6.48) определяли средние значения пределов прочнос |
ти образцов с покрытием различных диаметров и поверхностью рабочей части. Проверка показала удовлетворительное совпадение (ошибка б < < 5%) расчетных и опытных значений средних пределов прочности КСП (табл. 6.4) при использовании в качестве параметра выборочной оценки (а = 6,42), полученной по данным испытания биметаллических образцов.
Расчет |
по оценке параметра распределения оьо стальных образцов |
(а = |
= 3,30) |
нецелесообразен, так как ошибка прогноза растет с увеличением |
|
диаметра и в рассматриваемых пределах превышает 20%. |
|
|
Функция распределения F(obK) может быть также определена |
с уче |
том полученных закономерностей при раздельном рассмотрении поверх ностных и объемных дефектов.
Веростность того, что местный предел прочности ни в одной точке по верхности А не будет превзойден, равна
Г _ |
А_ |
т |
|
(6.49) |
|||
Л ( а ь ) = е х р - |
А 0 \ а 0 - a, J |
||
L |
|
Аналогична вероятность того, что это не произойдет ни в одной точке объема V элемента
V °ь |
1 |
Г |
J_ |
/ |
°b - °Ь0 |
\ 21 dob. |
(6.50) |
Pi(ob) = 1 — |
exp |
||||||
Vo |
S(pbQ)s/T%7 |
Г |
2 |
\ |
S(ob0) |
/ J |
|
Искомая функция распределения номинальных пределов прочности биметалла определяется по формуле
^ ( а ь к ) = 1 - Л ( а * ) Л ( а ь). |
(6.51) |
С учетом соотношения между вероятностью неразрушения и нормиро ванной нормально распределенной случайной величиной zp выражению (6.50) можно придать следующий вид:
Т а б л и ц а 6.5 Расчетные и опытные характеристики рассеяния покрытия
т |
ov |
°о ~ °V |
|
Расчетные |
|
Опытные |
|
|
|
|
|
|
|||
|
МПа |
МПа |
аЬп* |
s(< W - |
U(<W |
°bie |
S (<*Ьп)> |
|
|
|
МПа |
МПа |
|
МПа |
МПа |
4,034 |
108 |
209 |
111 |
9,5 |
0,278 |
131 |
23,8 |
1,510 |
146 |
318 |
187 |
27,6 |
0,674 |
158 |
28,8 |
2,812 |
0 |
381 |
7,4 |
3,8 |
0,385 |
10,6 |
14,1 |
1,755 |
148 |
235 |
168 |
18,5 |
0,426 |
150 |
30,9 |
Г |
/ |
°Ъп |
°ьо ~ °ъо |
|
Р ( ° Ь к ) = 1 “ ехР[ |
\ |
О0 — Oj |
S(obо) |
(6.52) |
где оьо, S(ob0) —соответственно среднее значение и среднеквадратичное отклонение предела прочности оьо металла основы; Ф - нормированная функция Лапласа.
Среднее значение пределов прочности КСП можно устанавливать по за висимости
оо |
[-(“ |
)'][■-ейг)] |
|
|
|
|
°ь к = / о&ехр |
|
|
dob. |
(6.53) |
||
о |
|
|
|
|
|
|
Функция распределения |
(6.52) может быть использована для установ |
|||||
ления характеристик рассеяния покрытия. Из (6.52) |
получаем уравнение |
|||||
|
|
1 - 0 \ °ьо - °ьо |
] |
|
||
т In (оЬп —О/) —т In (а0 —о{) - lnln |
L S(obo) |
|
(6.54) |
|||
|
|
1 |
- Р ( ° Ь к ) |
|
|
|
которое является исходным при определении параметров распределения поверхностных слоев. Используя метод разделяющих разбиений можно составить и решить систему нелинейных уравнений
m ^n (°bnj ~ o i) - m \n (p 0 - о{)= Yj\ / = 1,2,3, (6.55) где
1 —<t>[(ob0 — obo)/S(obo)]
Yj - InIn |
1 |
~ F (o bK) |
|
|
|
|
|
||
Минимальная |
прочность |
поверхностных элементов определяется |
||
из трансцендентного |
уравнения (6.6). Решением уравнения |
(6.55) |
||
относительно параметров т и о0 получены следующие формулы: |
|
|||
т = ______ °ь 1 — °Ь2_______ |
(6.56) |
|||
ln(aftl - |
oi)-\n{ob2 - |
огУ |
|
°bl — Ol |
(6.57) |
1 —Ф[(Ры — Оьо)/3(°ьо)] | \ 1/m |
|
1 v(Pb 1) |
I/ |
где ab l, ob2, a&3 - выбранные границы разбиения; v(pbj) - эмпиричес кая оценка функции распределения F(obK) биметалла.
Предложенная методика использовалась для установления оценок па раметров функции распределения покрытий и определения характерис тик рассеяния КСП для четырех выборочных совокупностей. В расчетах приняты (по данным испытаний) характеристики стали 30 (материала основы): оьо = 420 МПа и S(ob0) = 42 МПа. Полученые, согласно соот ношениям (6.6) и (6.56), (6.57), оценки параметров распределения пок рытия, а также вычисленные средние значения дЬп, среднеквадратичные отклонения S(obn) и коэффициенты вариации v (оЬп) приведены в табл. 6.5.
Сравнение опытных значений пределов прочности покрытия, получен ных непосредственным испытанием образцов из покрытия (см. табл. 6.5) с расчетными, не обнаружило статистически значимого различия для рас смотренной модели распределения объемных повреждений.
6.2.3. Учет рассеяния характеристик временного сопротивления при статистическом растяжении сталей с покрытиями
Исследованиями многократно доказано, что технологические факторы нанесения покрытий оказывают существенное влияние на статическую проч ность КСП. Описание этого влияния может быть адекватно осуществлено с помощью статистической модели второго порядка [12]
к |
к |
к |
(6.58) |
оь =Ь0 + 2 |
Ъ(х{ + 2 |
ЪцХ/ + 2 ЪиХ{Хи |
|
i= i |
/ = 1 |
/ < / |
|
где X/ — рецептурно-технологические факторы, управляющие прочностью КСП и включенные в модель (общее число факторов к)\ Ь0, £/,£//»£// - выборочные коэффициенты регрессии.
Проверка исходных предпосылок регрессионного анализа показала, что при построении модели типа (6.58) можно встретить два случая: оценки
дисперсии S 2 (оь) однородны во всем диапазоне изменения |
технологи |
ческих факторов Х(\ обнаруживается некоторая тенденция в |
изменении |
оценок дисперсии S 2 (оъ) в зависимости от аргументов X/.
Рассмотрим методические аспекты установления оценок дисперсии пре делов прочности КСП для каждого из перечисленных случаев.
Оценки дисперсии однородны. Оценка дисперсии предсказанного значе ния S 2 (оь) для модели (6.59) определяется на основе общей теории оши
бок функций случайных величин как |
|
|
|
|
|||
S \ S b)= |
3 ( |
- ^ |
\ . S 2( ^ + 2 E COV( M |
/ ) ( - ^ ) |
( т г - ) |
’ <6-59) |
|
|
/ - о\ |
bbj |
/о |
\ bbi |
/о |
\ Эbj ) о |
|
где cov (b{bj) —ковариации коэффициентов b{ nbj.
Выражение (6,59) правомерно в силу того, что оценки коэффициентов регрессии —случайные величины с дисперсиями S 2 (b0) , S 2 (&,), S 2 (Ьц) и S 2 (Ьу) ,поэтому
5 2(aft) = 5 2(6o)+ 2 S 2(bt) x j + 2 |
S 2(bi,)xj xj |
+ 2 S 2{bu)x,f + |
|
i = 0 |
i < / |
|
i = l |
+ 22cov(Z>,-Z>/) X/Xj + . . . + 2 |
2 cov(Z>,-/ |
bsj)x2xf |
(6.60) |
|
i <j |
|
|
Для наиболее распространенных симметричных планов эксперимента второго порядка [13] линейные эффекты Ь( и эффекты взаимодействия by определяются с постоянными дисперсиями и независимо, т,е.
соу(Ь{ bj) = cov (by biK) = cov(b0bi) =cov (b0by) = cov(Z?/ bJK) = 0,
и формула (6,60) упрощается
S 2(ab) = S 2(b0) + S 2(bi) 2 xj +S2(bif) |
2 |
+ S2(Z>„) 2 x f + |
|||
|
/=1 |
|
/< / |
|
1= 1 |
к |
|
к |
|
|
(6.61) |
+ 2cov(Z><>£//) 2 |
х 0Х/ + 2cov(bubjj) 2 |
X/X?. |
|
||
/ = l |
|
/ < / |
|
|
|
Анализ (6,61) показывает, что |
точность расчетов по |
полиномиальной |
|||
модели, характеризуемая S 2 (оь), |
зависит от трех параметров: точности |
||||
эксперимента (5Э), |
координат точки предсказания |
(.х 1р, , |
. , ,х кр), влия |
ющих нелинейно (каждая координата входит как х*/р и х?р,и свойств пла на эксперимента, связанных с координатами точек, в которых ставился эк сперимент через матрицу ошибок (или ковариационная матрица).
Оценки коэффициентов регрессии определяются с дисперсиями и ко
вариациями: |
|
|
|
|
|
S 2(bo) = т г |
S i |
S 2(bi) = - - Г - s b |
|
|
|
N |
|
|
JVX; |
|
|
N |
s i , |
c - d |
e2 . |
(6.62) |
|
S \b i,) = |
S 2(bti) = |
*^э > |
|||
NK3 |
|
N |
|
|
|
соv(b0bu) = - — |
S i , |
|
d |
|
|
cov(bu bfj) = ~ — S i , |
|
||||
|
N |
|
|
N |
|
где N — число |
опытов |
плана эксперимента. При дублировании опытов в |
|||
каждой строке плана эксперимента Si надо делить не на N, а на |
N |
||||
2 пи. |
|||||
|
|
|
|
|
и = 1 |
Внедиагональные элементы ковариационной матрицы определяются
через четные моменты плана эксперимента Х г Д з Л |
по формулам [14]: |
к\1 |
|
а = -------------------------г—+ 1, |
|
Х4 —Х3 + к\з —к\ 2 |
|
ь= ----- ------------ тгг- , |
(6-63) |
Х4 —Х3 + к\з —к\ 2 |
|
Л4 —Х3 |
|
|
|
|
|
|
_ |
Хз - х | |
|
|
|
|
|
(X4 —X3) (X4 —X3 + k \ 3 —ЛЛ2) |
|
|
||||
где |
|
|
|
|
|
|
X2 = |
N |
N |
дмд:-м / |
N |
лм, |
|
N " 1 2 |
x 2u = 2 |
2 |
|
|||
|
м = 1 |
u = 1 |
|
и = 1 |
|
|
|
N |
|
N |
|
N |
|
\ 3 = N -' 2 |
(x*x/)u = |
2 nu(x jx f)u l 2 лм, |
(6.64) |
|||
|
u = 1 |
w= 1 |
|
U= 1 |
|
|
X4 = |
N |
N |
nu x?u l |
N |
лм. |
|
iV“1 2 |
x?M = 2 |
2 |
|
|||
|
И= 1 |
li = 1 |
|
M= 1 |
|
|
Вторая часть формул (6,64) используется при дублировании опытов в каждой точке плана эксперимента.
Оценки дисперсии неоднородны. Данные эксперимента показывают, что
дисперсия предела прочности S 2 ([аь) является функцией координатных точек плана эксперимента. В этом случае предполагают, что величина услов ной дисперсии предела прочности пропорциональна некоторой функции h2 (*/) от технологических факторов X/, т.е.
S 2(bb) = o2h2{x,), |
(6.65) |
где о2 — постоянная составляющая условной дисперсии, определяемая из соотношения [12]
1 |
ЛГ |
|
(6.66) |
о2 = --------- |
2 (ти/ —1) оо,52(а&), |
|
|
п - N |
/= 1 |
|
|
где N —число различных фиксированных значений переменных X/; |
— |
||
количество наблюдений в каждом опыте плана эксперимента; |
п —общее |
||
число опытов; |
—’’веса” условных дисперсий. |
|
|
Вид неизвестной функции h2 (х/) можно устанавливать |
с помощью |
метода наименьших квадратов. Для этого дисперсии (или среднеквадра тичные отклонения) в каждой строке плана эксперимента рассматриваются как параметры оптимизации и рассчитываются оценки коэффициентов регрессии модели вида (6.58).
Рассмотрим применение описанного подхода к задаче определения дис
персии S 2 (рь) предела прочности композиции сталь 30 + электролитичес кое железо. В план эксперимента для описания влияния технологических факторов на прочность композиции включались два наиболее значимых фактора: температура электролита и рабочая плотность тока х2.
Среднеквадратичные отклонения рассматривались как выходы D-опти мального плана и рассчитывались оценки коэффициентов регрессии. Урав нение регрессии, адекватно описывающее область экспериментирования, после удаления незначимых коэффициентов имеет вид
h2(х/) = 50,12 + 9,55 x t —2,32 х2 - 4 ,7 8 х 2. |
(6.67) |
Таблица 6.6.
Определение постоянной составляющей условной^ дисперсии
S2(ab) |
**(ч> |
“>i= 1M*2(*I) |
S2(a6)(mf— 1) |
CJ |
mi |
|
,- s 2 (ob)lh2(xi) |
||||
2724,84 |
52,0 |
0,019 |
3054,55 |
52,46 |
60 |
1624,08 |
37,5 |
0,027 |
2937,96 |
43,40 |
68 |
967,21 |
32,1 |
0,031 |
1679,08 |
30,18 |
57 |
3576,04 |
55,8 |
0,018 |
4982,02 |
64,14 |
77 |
2970,25 |
58,7 |
0,017 |
3888,06 |
50;56 |
78 |
1428,84 |
39,6 |
0,025 |
1964,66 |
36,08 |
56 |
1918,84 |
43,0 |
0,023 |
3751,33 |
44,69 |
86 |
1672,81 |
47,7 |
0,021 |
3231,87 |
35,02 |
93 |
3147,21 |
50,1 |
0,020 |
9315,74 |
62,85 |
149 |
С у м м а |
|
|
34805,27 |
|
724 |
Определение постоянной составляющей условной дисперсии показано в табл. 6.6. Величина совместной оценки условной дисперсии, вычисленной по зависимости (6.66) при N= 9, оказалась равной &2 =48,6787. Тогда ве личину условной дисперсии S 2 (оь) зависимой переменной предела проч ности КСП можно определить из выражения
S 2(ab) = b2h2(xi) = 48,68 (50,12 + 9,55*! - 2?>2хг - 4,78x1). |
(6.68) |
||
Проверка |
однородности нормированных |
дисперсий S 2 (ob)/h2 (х,) |
|
показала, что нуль-гипотеза может быть принята. |
|
||
Рассеяние |
пределов прочности натурных |
биметаллических |
элементов |
может быть получено с использованием методов линеаризации и статис тических испытаний (метод Монте-Карло).
Расчетная формула для дисперсии пределов прочности S2 (<?&) натурных элементов при использовании метода линеаризации получается из выраже
ния для масштабного эффекта с помощью закона сложения ошибок |
|
||
= (^Г)о |
+ 2 .'=! (^Г) 0 ( ‘ |
) 0 Г“ °Х( °Xf |
(6'69) |
Например, при использовании зависимости (6.37) из предположения независимости случайных величин оьо, А 0, А, т и постоянства а и Ъ по лучим
5 2(аь) = |
О- |
|
а Ъо |
Метод статистических испытаний позволяет решить задачу определения закона распределения предела прочности натурных биметиллических эле ментов по известным или предварительно оцененным тем или иным спо собом законам распределения случайных величин оьо, А о, А и т. Допус тим, что о Ьо>А 0 и А имеют нормальное распределение, а параметр т — равномерный закон распределения с параметрами Д»Mi- Чтобы получить случайную величину mUJ равномерно распределенную в интервале (м>Мi)>
используется преобразование |
|
|
ти(рo,Mi) = (Mi -Мо)Л„ +ц0, |
|
(6.71) |
где R u — случайная величина, равномерно |
распределенная в |
интервале |
(0, 1). |
|
|
Аналогично случайные величины (айо)^ , |
04о)лг и Q4)w» |
имеющие |
нормальные распределения с параметрами: оЬо, 5 (aft0), Л0, S (Ло) и А, S (А), находятся как
iPbo)N = °Ьо + R N S(°bo)> |
(6.72) |
(AO)N = А о +Rpj S(A0), |
|
(Л )д г = A +RM S(A), |
|
где Rtf — случайная величина из нормально распределенной совокупности с параметрами д = 0 и о = 1,
Идея метода заключается в следующем, С помощью зависимостей (6,71) и (6.72) получаем случайные величины (ob0) Ni, (А 0) щ , 04)м»:по которым рассчитывают предел прочности obj натурной детали согласно (6.72). В результате получают одну ’’реализацию” случайного явления. Произведя такое моделирование многократно (п раз), устанавливают мно жество ’’реализаций” случайной величины предела прочности натурного биметаллического элемента — вариационный ряд, который обрабатывают обычными статистическими методами. Приближенное число испытаний при моделировании методом Монте-Карло находится по формуле [11]
|
(6.73) |
где Z i- a j2 — квантиль |
нормированного нормального распределения; |
(1 —а/2) — вероятность |
(доверительный уровень) того, что оценка х ма |
тематического ожидания не будет отличаться от истинного значения д боль ше чем на ± е; е — максимально допустимая ошибка при оценке д; о9— первоначальная ошибка среднего квадратичного отклонения.
Рассмотренные статистические особенности механического поведения материалов с покрытиями приобретают существенное значение при цик лическом нагружении, когда на ранних стадиях нагружения возникает об разование систем микротрещин в поверхностных слоях. Учитывая взаимо связь характеристик статической и циклической прочности (см. гл. 3 и 4), приведенные данные по распределению характеристик статической проч ности можно вводить в уравнение кривых малоциклового разрушения.
Для повышения устойчивости характеристик сопротивления разрушению используются различные методы [15] — термообработка, поверхностное пластическое деформирование, обработка в азотоводородной плазме тлею щего разряда.
ЛИ Т Е Р А Т У Р А
1.Калмуцкий В.С. Вероятностно-статистические закономерности повреждения и разру шения сталей с покрытиями: Автореф. дис.. . . д-ратехн, наук. М„ 1984. 37 с.
2.Болотин В.В. Статистические методы в строительной механике. М.: Стройиздат, 1966, 279 с.
3.Герцбах И.Б., Кордонский Х.Б. Модели отказов. М,: Сов. радио, 1966. 16Ь с.
4.Разрушение. Математические основы теории разрушения / Под ред. Г. Либовица. М.: Мир, 1975. Т. 2. 764 с.
5.Капур К., Ламберсон Л. Надежность и проектирование систем. М.: Мир, 1980. 604с.
6.Гумбель Э. Статистика экстремальных значений, М.: Мир, 1965. 450 с.
7.Смирнов Н.В., Дунин-Борковский И.В. Курс теории вероятности и математичес кой статистики для технических приложений, М.: Наука, 1969. 512 с,
8.Арёон А. Статистические аспекты разрушения // Разрушение и усталость / Под ред. Л. Браутмана. М.: Мир, 1978. С. 166-205.
9- Физическое металловедение / Под ред. Р. Кана, М,: Мир, 1968. Выл, 3. 484 с.
10.Фридман Я.Б. Механические свойства металлов. М,: Машиностроение, 1974. Ч. 1. 472 с.
11.Хан Г., Шапиро С. Статистические модели в инженерных задачах. М,: Мир, 1969. 396 с.
12.Калмуцкий В.С. Анализ и оптимизация качества материалов. Кишинев: Штиница, 1978. 160 с.
13.Вознесенский В.А. Статистические методы планирования эксперимента в технико экономических исследованиях, М,: Финансы и статистика, 1981. 263 с.
14.Нови к Ф.С., Арсов Я.Б. Оптимизация процессов технологии металлов методами планирования экспериментов. М.: Машиностроение; София: Техника, 1980, 304 с.
15.Чаевский М.И., Бледнова Ж.М. Коррозионно-механическая повреждаемость и пути повышения коррозионно-усталостной прочности // Тез. докл. Всесоюз. науч.-техн, симпоз. ’’Нормирование и прочность высоконагруженных машин” . М,: ЦП НТО Машпром, 1986, С, 206-210,
УЧЕТ РАССЕЯНИЯ РАСЧЕТНЫХ ПАРАМЕТРОВ ПРИ ОЦЕНКЕ ДОЛГОВЕЧНОСТИ ЭЛЕМЕНТОВ КОНСТРУКЦИЙ
7.1. Общие положения по статистической прочности и долговечности
Сопротивление деформациям и разрушению элементов машин и конст рукций при малоцикловом нагружении в детерминированной и статисти ческой постановке определяется кинетикой напряженно-деформированных состояний и критериальными характеристиками предельных состояний. Эти два основных типа состояний существенно зависят от статических и циклических свойств применяемых конструкционных материалов [1—3] (см. гл. 1—4):
{ea(aa,7a)l |
= f(E , ат,т, |
, aa,N, t, г) , |
(7.1) |
|
|
Oj* |
|
\N0,Nr\ =f[ea(oa, ya),ek (ak ,y k), t, r ] , |
(7.2) |
||
где ea , oa , 7a |
—амплитудные значения местных деформаций |
(напряжений |
или энергий); от —предел текучести материала; m —показатель упрочне ния в упругопластической области; оп — номинальное напряжение; % — теоретический коэффициент концентрации напряжений; N —число циклов нагружения; t — температура; т —время цикла; N0,N T —долговечность на стадии образования и развития трещин; ек —характеристика предельной пластичности (прочности или энергии).
Статические или циклические свойства материалов определяются их хи мическим составом и структурой. С учетом особенностей проявления состава и структуры при малоцикловом нагружении конструкционные металлические материалы можно условно разделить на две основные группы — структурно-однородные и структурно-неоднородные. Для боль шого числа несущих элементов машин и конструкций характерно приме нение структурно-однородных материалов (заготовки в виде листового проката, прутков, поковок из заданной стали или сплава). В этом случае необходимая вариация механических свойств (Е, от , т, ек) достигается, как правило, легированием и термообработками, а одна из наиболее важ ных величин оТ оказывается связанной с величиной зерна d по известному степенному уравнению Петча—Холла. Циклические свойства материалов, входящие в неявном виде в уравнение (7.1), зависят от исходных свойств при статическом нагружении (см. гл. 1—3):
[А, С(В)\ = ( - ^ - , е„
\0Ь
где А — параметр диаграммы деформирования в первом полуцикле нагру-
156
женин; С(В) —характеристики циклического разупрочнения (упрочнения); оъ, еь —напряжение и деформация предела прочности. Температурный t и временной т факторы входят в уравнения (7.1) и (7.2) через экспонен циальные и степенные функции.
Однако для структурно-однородных материалов важное значение имеют три типа неоднородности распределения локальных механических свойств (см. гл. 4). Первый из них определяет неравномерность распределения местных деформаций по зернам и группам зерен, вызывая неравномерное возникновение систем микротрещин на поверхности образцов и деталей. Второй тип неоднородности связан с повышенной величиной локальных деформаций в тонких поверхностных слоях (толщиной до 0,1—0,2 мм); образование остаточных напряжений в этих слоях в большой степени ска зывается на эффекте Баушингера и на возможности резкого увеличения долговечности N0 путем последовательного удаления в процессе цикличес кого нагружения наиболее повреждаемых поверхностных слоев. К третье му типу неоднородности следует отнести макронеоднородность по сече нию, обусловленную процессами кристаллизации, прокатки, термообработ ки. Для широко применяемых конструкционных сталей базовые харак теристики механических свойств связаны с размером сечений F уравне ниями степенного вида
1 а о ,2 1°ь>ек\ = /(^го/7г),
где F 0 —поперечное сечение стандартного образца.
Структурная неоднородность материалов в макрообъемах создается при следующих технологических процессах: сварка, наплавка, плакирова ние, поверхностное или объемное пластическое деформирование, обработка импульсами электрического тока, взрывная обработка, химико-термичес кая обработка, ионно-плазменная, гальваническая и др.
При названных видах обработок возникают неоднородные структурные состояния как по поперечным сечениям F, так и по длине L рассматривае мого элемента.
Решение задач малоцикловой прочности и ресурса для таких элемен тов должно производится на базе двух основных положений: для соот ветствующих зон элементов со своими локальными механическими свой ствами можно использовать уравнения (7.1) и (7.2); для переходных зон должно быть учтено возникновение дополнительных напряжений и де формаций, обусловленных совместностью их деформирования.
Последний фактор может анализироваться на базе решения нелинейных краевых задач и может быть сведен к изменению величин через коэффи циенты контактного упрочнения КК (для сварных соединений, биметал лов) через интенсивности напряжений а/ и деформаций в/ или через коэф фициенты / повышения главных напряжений:
ат= отКк; I=o°i/oi,
где От — предел текучести в зоне с неоднородными свойствами с учетом объемности напряженного состояния; о?, ai — первое главное напряже ние при объемном и линейном напряженном состоянии.Предельная пластич ность е% при объемном напряженном состоянии определяется коэффициен
том De снижения пластичности
в% = K D &к D e —e jc (P i/ o Cp ) K f ) , |
(7 *3) |
где оср — среднее напряжение (аср = оi + а2 + о3); |
KD —характеристика |
материала (А^ = 0,8 -Н ,2), |
|
В структурно-однородных и неоднородных металлических материалах (см, гл, 4- 6) при их изготовлении, при изготовлении и эксплуатации машин и конструкций возможно образование микро- и макродефектов (трещины, расслоения, поры, включения), Эти дефекты создают высокую концентрацию локальных деформаций еа тах и напряжений aflmax
{ max i °а max \ =f(ea, oa,l0, (o„laT) ,m, N, t, r), |
(7.4) |
где /о —начальный размер дефекта.
При этом предельные деформации в зонах дефектов можно оценивать по уравнениям (7,2) и (7.3),
В соответствии с данными экспериментов и расчетного анализа при вяз ких состояниях материалов при определении величин NT по уравнению (7.2) следует учитывать размеры дефектов /0 > 0,5 -М мм. При этом ки нетические уравнения для скорости трещины dl/dN имеют степенной вид
dN =f(AKle,e°k JoX |
(7.5) |
где AKie — размах коэффициента интенсивности деформаций, зависящий от /о, оп/от , N , t, т,т. Количественные зависимости основных механичес ких свойств (Е, оТ, т, ек) от химического состава и структуры материалов позволяют вести по заданной вероятности расчетный анализ прочности и ресурса машин и конструкций при малоцикловом нагружении на различ ных стадиях их создания и эксплуатации. В качестве исходных определяю щих конструктивных и эксплуатационных факторов при Этом оказываются статистические данные о параметрах O„ , OL0 , F, t, т, N, /0.
Совместное решение систем уравнений (7.1)—(7.5) Позволяет опреде лить два основных этапа: по местным деформациям пе и по долговечности nN. Обеспечение указанных запасов достигается всеми указанными харак теристиками механических свойств и эксплуатационной нагруженности. Наиболее эффективное значение при этом имеет рациональный выбор конструкционных материалов и технологий изготовления. Основой такого выбора являются указанные критериальные уравнения и уравнения сос тояния для малоциклового нагружения.
12 . Учет статистики свойств при расчетах сосудов давления
В соответствии с нормами прочности выбор основных размеров сосуда проводится на основе оценки статической прочности При номинальной нагрузке.
При этом за допускаемое статическое номинальное Напряжение [а#] принимается минимальнее из двух значений:
[°н\ = Оо^/«о,2 . или [ан ] =0*ь 1пь , |
(7.6) |
Значения ОМС и запасов статической |
прочности д л я |
стали Х 18Н 9 |
при норм аль |
||
ной тем п ературе |
|
|
|
|
|
р,% |
”0,2р |
пьР |
(**0,2* МПа |
а&, МПа |
|
|
|
|
|
|
|
50* |
1,5 |
2,6 |
266,6 |
681,5 |
72,44 |
1 |
1,34 |
2,37 |
241,1 |
625,7 |
67,40 |
0,5 |
1,33 |
2,35 |
237,9 |
620,2 |
66,91 |
0,1 |
1,30 |
2,31 |
232,7 |
609,1 |
65,90 |
Нормы |
1,5 |
2,6 |
220,0 |
500,0 |
55,0 |
прочности |
|
|
|
|
|
*Без доверительного интервала.
где п02 = 1,5 и пь = 2,6, а значения о ^2 и °ъ принимаются равными гаран тированным по ТУ для данного диапазона температур.
При проведении расчета с учетом рассеяния фактических свойств ма териала можно оценить резерв прочности материала. При этом возможна менее консервативная оценка допускаемых напряжений. Тогда значения
запасов статической |
прочности для различных уровней вероятности Р |
с учетом величины доверительных интервалов будут следующие: |
|
Я р ” п * Р т jn^ m ax > |
(7*7) |
где x Pmin — нижняя односторонняя доверительная граница квантиля уров ня Р; х тах — максимальное значение среднего арифметического; п — запас дляР = 50%.
Величину xPmin для нормального закона можно оценить по зависи мостям, приведенным в работе [4]:
S
* P m i n = * + ' l - 0 [ « “ I ->У/П2р]
(где ty (k9ri) — квантиль уровня у = 1 —/3 центрального распределения Стьюдента с к = п — 1 степенями свободы и параметром нецентральности и = \Jnzp9n —число значений случайной величины) или приближенно [5]:
Хр min “ *min — z p 5max >
где x min —минимальное значение среднего арифметического; zp —кван тили уровня Р; 5max —максимальное значение среднеквадратичного откло нения с учетом величины доверительных интервалов.
Без учета величины доверительных интервалов значение запаса стати стической прочности определяется по формуле
np = nxpfx.
В качестве примера в табл. 7.1 приведены значения запасов п0 2 и пъ для заданных уровней вероятности Р, определенные для одной плавки стали Х18Н9 при комнатной температуре с учетом 98% доверительных интервалов для значений основных механических свойств (ОМС). Число значений случайной величины в выборке составляло 50 < п < 80.
Т а б л и ц а 1 2
Значения запасов по величине условного упругого напряжения a j для расчета долговечности по уравнению жесткого нагружения
р,%
|
102 цикл |
10э цикл |
104 цикл |
од |
1,61 |
1,62 |
1,66 |
од |
1,66 |
1,67 |
1,70 |
1 |
1,69 |
1,70 |
1,72 |
50 |
|
2,0 |
|
Из таблицы видно, что значения запасов п0 2 и пь, вычисленные с учетом рассеяния ОМС, имеют определенный резерв при уровнях вероятности Р выше 0 ,1%.
Аналогично можно определить значения циклических запасов прочности па и долговечности nN для однородного напряженного состояния для заданного уровня вероятности Р с учетом величины доверительных ин тервалов:
п Ор ~ п а ^apmin/^amax > nN р ~ > (7*8)
где П 0 = 2 И nN = 10.
В табл. 7.2 приведены значения циклических запасов по напряжениям п0р стали Х18Н9 при комнатной температуре, полученные расчетным путем по уравнению жесткого нагружения норм прочности с введением в уравнение рассеяния значений фактических ОМС оь и фк (при расчете принят симметричный цикл деформаций, г* = —1). При этом полагалось, что минимальным значениям оь соответствует минимальная пластичность фк. Указанное сочетание дает меньшие величины запасов. Вводимые в рас чет значения ОМС определены с учетом 98% доверительных интервалов.
Величины запасов по допускаемому числу циклов nN дая долговечно сти Ne0, примерно равной 103 циклам (qj = 2000 МПа/, составили 6,21, 6,66 и 6,88 для уровней вероятности 0,1,0,5 и 1% соответственно.
Из изложенного следует, что при расчете с использованием фактических; значений ОМС требуемого уровня вероятности Р (например, Р = 0,1%) для данной плавки стали Х18Н9 при нормальной температуре имеется определенный резерв по уровню допустимых условных упругих напря жений и допустимых чисел циклов нагружения по сравнению с расчетом по фактическим средним значениям ОМС с использованием нормативных запасов 2 и 10. Поскольку нормативный расчет проводится для гаранти рованных по ТУ значений ОМС (минимальных), то получаемые величины допускаемых условных упругих напряжений будут ниже и являются в дан ном случае более консервативными.
На основе разработанных расчетно-экспериментальных методов и их
программных реализаций для зон концентрации |
(см. гл. 2; 3; п. 4.3; |
п. 5.2) в качестве примера приведен модельный |
расчет рассеяния долго |
вечности по моменту образования и при развитии малоцикловых трещин
Рис. 7.1. Экспериментальные функции распределения основных механических свойств стали 15Х2НМФА при температуре 350 °С (заводские данные)
до разрушения с учетом межплавочного рассеяния ОМС для сосуда из стали 15Х2НМФА в зоне патрубка при эксплуатационной температуре 350 °С.
Оценка межплавочного рассеяния ОМС получена по заводским данным для семи корпусов сосуда (число значений случайной величины в выборке составляло 140 шт.).
На рис. 7.1 показаны результаты графического анализа функций рас-
11. Зак. 1830 |
161 |
|
Значения расчетной долговечности по моменту появления трещин N € Q и значения условного упругого напряжения о£ для стали 15Х2НМФА при 350 °С для раз личных уровней вероятности значений ОМС (заводские данные) и нагрузки
Уровень |
Интенсивность номинальных напряжений а/ном »МПа |
|||
вероятности |
267,2 |
302,4 |
337,6 |
|
ОМС,% |
||||
|
i> = 1 |
Р = 5 0 |
Р -9 9 |
|
99 |
27739* |
15847 |
9826 |
|
452,3 |
549,0 |
655,6 |
||
|
||||
50 |
15881 |
9262 |
5786 |
|
485,4 |
592,8 |
712,6 |
||
|
||||
1 |
7637 |
4500 |
2820 |
|
524,1 |
644,8 |
780,9 |
||
|
*В числителе —NеО, цикл; в знаменателе —аар* МПа.
пределения величин а0(2, obi фк и 5, они аппроксимированы прямыми, проведенными для логнормального (д) и Вейбулла (б) законов распреде ления. Из рисунка следует, что соответствие распределений а0 2И °ь обоим законам неудовлетворительное. Распределение величин фк и б соответ ствует закону Вейбулла (кроме трех-четырех значений малого уровня вероятности). После определения графическим способом нижних порогов [4] получено удовлетворительное соответствие величин а0 2 и оь лог нормального закону (значения статистик расчетного анализа по критериям согласия X и со2 меньше критических значений для уровня значимости а =0,15).
Диаметр сосуда равен 920 мм, толщина стенки 52 мм, значения ОМС понимались с учетом толщины стенки [6], что в первом приближении учитывает влияние масштабного эффекта при малоцикловой усталости
идает консервативный результат, так как по оценкам приводит к сниже нию долговечности примерно в 2 раза. Имеющиеся литературные данные показывают слабое проявление масштабного эффекта. Так для образцов без концентратора увеличение объема деформируемого металла до 100 раз
ииспытания крупногабаритных образцов с концентратором показали слабое снижение долговечности по сравнению с лабораторными образца ми [7]. Аналогичные результаты получены для образцов с высокой сте пенью концентрации — резьбовыми соединениями М2СН-М110 из сталей
25Х1МФ и 38ХНЗМФА [8], но при этом размер пластических зон отно сительно диаметра шпилек невелик.
Для сосуда у патрубка теоретический коэффициент концентрации коль цевых напряжений принят 3,23, меридиональных —1,34. При эксплуатации сосуда, нагруженного внутренним пульсирующим давлением, для ста ционарного режима нагружения имеется разброс максимальных значений давления. Принято, что интенсивность номинальных напряжений сосуда °iooc изменяется п0 нормальному закону распределения с коэффициентом
Рис. 1,2. Зависимости между основными механическими свойствами стали 15Х2НМФА при температуре 350 °С (термообработка совместно с деталью)
а - г - 0,43; б - 0,37; в - 0,92; г - 0,22
вариаций Vo , ^ = 5%. Среднее значение а,- примем равным 302,4 МПа (табл. 7.3). "ом
Параметры диаграммы циклического деформирования А, а, /3, С и В определялись расчетным путем (см. гл. 3). Расчет осуществлялся по нуле вому полуциклу деформирования и первому полуциклу, который опреде лялся с учетом разупрочнения.
В табл. 7.3 приведены значения расчетной долговечности для различной вероятности (.Р) по моменту появления трещин Ne0 и значения условного упругого напряжения о}, полученные для условий жесткого нагружения в зоне концентрации с учетом межплавочного рассеяния ОМС и указанного рассеяния нагрузки.
Расчет проводился по табличным значениям ОМС для температуры 350 °С, полученным для предпочтительных теоретических законов и с уче том корреляционных связей меяоду отдельными ОМС (рис. 7.2).
На рисунке видно, что увеличению прочности материала соответствует уменьшение его пластичности. Значения коэффициента корреляции были значимыми и составляли примерно от 0,3 до 0,9. В дальнейшем досто-
Рис. 7.3» Расчетные функции распределения долговечности по моменту образования трещин N0 для сосуда из стали 15Х2НМФА у патрубка при температуре 350 °С
верность таких расчетов циклической долговечности оценивалась расче том по конкретным значениям ОМС каждого образца статистической серии.
На рис. 7.3 показаны расчетные функции распределения долговечности по моменту появления трещин N0 и окончательному разрушению Np при постоянной номинальной нагрузке 0/сос = 337,6 МПа (для уровня вероят ности Р = 99%). Кривая 1 соответствует значениям долговечности Ne0 для сосуда для условий жесткого нагружения в зоне концентрации, кривая 2 — Na0 для условий мягкого нагружения. При этом полагалось, что увели чению прочности стали соответствует уменьшение пластичности (кривые сдвинуты на порядок влево). Кривые 1* и 2* получены для условий жест кого и мягкого нагружения в зоне концентрации соответственно, но уве личению прочности соответствует увеличение пластичности. Кривая 3 рассчитана по значения ОМС для конкретных образцов, для сравнения на рис. 73 нанесена часть кривой 1.
Из рисунка следует, что расчет по варианту 3 лучы^ соответствует ва рианту 2, при этом расчет по варианту 1 приводит к Несколько большей долговечности. Здесь показаны также значения долговечности Np (кр. 4 и .4 ) . Расчет по варианту I 1дает консервативные результаты.
'На рис. 7.3 условно для уровня вероятности Р = 0,1% показаны расчет ные значения долговечностей N eQ и Np ( точки / и // соответственно), полученные для значений ОМС, взятых по ТУ. На рисунке видно, что рас-
164
четные значения долговечности, полученные по рассмотренным вариантам
1—4 для |
ОМС сосуда и экстраполированные на уровень вероятности |
Р = 0,2%, |
больше, чем значения долговечности, полученные по ТУ. |
Кривые малоцикловой усталости по моменту появления трещины Ne0, полученные по уравнению жесткого нагружения с учетом межплавочного рассеяния ОМС и рассеяния нагрузки, показаны на рис. 7.4. Значения долговечности Ne0, полученные при одинаковой номинальной нагрузке а ном (Р = 99%), обозначены точками. Там же приведены кривая долго вечности Ne0, полученная для ОМС по ТУ, и кривые с нормативными запасами па = 2и nN = 10, полученные относительно кривой при Р = 50%.
Значение запасов |
относительно средних значений величин |
и |
Ne0 |
||
равны |
|
|
|
|
|
% |
= 2 о*р/о*, |
nNp = ЮNe0p/Ne0> |
|
|
|
где о%р и N e0 |
— значения о£ и Ne0 по параметру вероятности Р; |
о£ и |
|||
N |
— средние |
значения; 2 и 10 —нормативные запасы. По результатам |
расчета и рис. 7.4 можно полечить,что значения запасов па и nN относитель но средних значений и Ne0 более 1,5 и 5 соответственно для уровня вероятности Р более 0,2%.
Значения запасов п0 и nN относительно значений о$ и Ne0, полученных через ОМС по ТУ, будут более 2 и 10 соответственно при вероятности более 0,2%.
На рис. 15 показано сопоставление функций плотности вероятностей действующих номинальных нагрузок и величин о0 2 и оь при условии нормального закона их распределения. Используя понятие гарантии неразрушения по Н.С. Стрелецкому, можно получить характеристику безопас ности 7 по А.Р. Ржаницыну [9], функция неразрушаемости ф равна:
Ф = О; |
— On 2 у |
Ф“ О; |
- On о |
|||
Г |
* Н О М |
U *Z ’ |
|
* Н О М |
|
U »Z 7 |
|
1 |
X - |
1 |
|
|
(7.9) |
|
|
|
|
|
|
|
|
v4> |
N/ U о Х2 + |
U а, |
|
|
|
|
|
|
|
‘ Н О М |
|
|
Р ( _ ) = 1 _ Ф ( 7 ), |
|
|
|
|
||
X |
—^0,2/ ^I*HOM ”” ^ |
|
» 7<7Q,2 — |
Уоь “ 8,57. |
||
Вероятность разрушения Р ( - ) |
для 7= 5 будет 3 • 10“7 [10], для величин |
|||||
ао,2 и оъ значения Р ( - ) |
будут еще меньше. |
|||||
Запасы статической |
прочности naQ и паь по нормам равны 1,5 и 2,6 |
|||||
соответственно. Запасы |
статической |
прочности для уровня вероятности |
||||
Р = 50% составляют: пао |
= 1,63 и п0ь = 1,88, т.е. нормативные условия |
для величины оь не выполняются, но вероятность разрушения Р (-) доста точно мала и составляет менее 3 • 10“7
Таким образом, для сосуда из стали 15Х2НМФА долговечности N e0 и Np , полученные с использованием значений ОМС по ТУ, соответствуют экстраполированным значениям расчетной долговечности для уровня Р менее 0,2% (см. рис. 7.3). Запасы статической прочности относительно величин (*0,2 и оь довольно велики, и вероятность разрушения составила менее 3 • 10"7
6^,Af/7a
Рис. 7.4. Расчетные кривые малоцикловой долговечности по образованию трещин N0 для сосуда из стали 15Х2НМФА в месте его соединения с патрубком, полученные с учетом межплавочного рассеяния ОМС и рассеяния нагрузки
Г ( * ц г ) Г Ш
УМУ
Ш <>; МЛа
Рис. 7.5. Сопоставление функций плотности для распределений номинальной нагруз ки аном и величин а0>2 и аь
С учетом проведенного анализа запасов па и nN (см. рис. 7.4) в данном случае подтверждается достаточность нормативных значений запасов, и можно считать обоснованным продление ресурса на малоцикловую уста лость для рассмотренного сосуда из стали 15Х2НМФА в зоне патрубка или назначить менее консервативные запасы при его проектировании.
7.3.Рассеяние характеристик прочности, долговечности
итрещиностойкосги элементов со сварными соединениями
7.3.1.Статистические характеристики сопротивления малоцикловому разрушению элементов сварных конструкций
При проектировании ответственных сооружений широкое распростра нение получают вероятностные методы оценки прочности и ресурса кон струкций из-за случайного характера изменения эксплуатационных нагру зок и рассеяния характеристик прочности и долговечности элементов конструкций. Особенно это относится к сварным конструкциям, так как сварные швы практически невозможно изготовить бездефектными, а дли
тельность стадии роста трещины в них составляет существенную долю в общей долговечности.
Исследованию зависимости рассеяния долговечности от характерных переменных параметров (оа ,\g N p, АК) посвящены работы [11 —17 и др.]. В монографии [12] предложена методика определения параметров диа граммы циклического деформирования и рассеяния этих параметров для выполнения вероятностных расчетов долговечности. В этих работах экспе риментальные исследования обычно проводились на гладких образцах или на образцах с типовым геометрическим концентратором. Для сварных соединений количество факторов, влияющих на рассеяние параметров прочности, больше, чем для гладких образцов и образцов с геометрическим концентратором, и основные из этих факторов трудно контролировать. В то же время мало исследований о рассеянии параметров прочности, долговечности и трещиностойкости сварных соединений (особенно в кор розионной среде и для алюминиевых сплавов) [7,18,19].
В данном параграфе для сварных стыковых соединений листов алюми |
|
ниевых сплавов выполнены исследования рассеяния характеристик стати |
|
ческой прочности оР{ и 5р/, долговечности |
lgNPji скорости роста трещин, |
а также параметров кривых усталости и |
кинетических диаграмм уста |
лостного разрушения (КДУР); п,С ,р,К fS.
Методика исследований. Материалами для испытаний были сплав АМг-61 и сплав повышенной прочности системы Al-41g —Zn. Сварка листов сплава системы А1—Mg—Zn выполнялась сварочной проволокой из сплава АМг-61 (мягкая прослойка), по линии сплавления накладывались дополнительно технологические валики без присадки. Термообработка соединений после сварки не проводилась. Статические и усталостные испытания проводились на стандартных образцах, вырезанных из предварительно сваренных пла стин, толщина листов 4—10 мм; из тех же листов были изготовлены глад кие образцы и образцы с концентратором в виде свободного и заполненно го заклепкой отверстия (рис. 7.6).
Усталостные испытания по исследованию рассеяния долговечности и параметров крцвых усталости проводились при мягком нагружении на переменное растяжение по пульсирующему циклу R = 0 с частотой 0,25 Гц, база испытаний 1 • 105 циклов, количество образцов на одну кривую уста лости 12—50 шт., количество испытанных на одном уровне образцов 4—10 шт (до 30 шт.) . Испытания проводились в воздухе ц 3%-ном растворе поваренной соли. Коррозионная среда подводилась к образцу с помощью ванночки из оргстекла, укрепляемой на образце. Некоторые пластины перед разрезкой на образцы выдерживались в 3%-ном растворе без на пряжения в течение 6 мес.
Исследования рассеяния скорости роста усталостных трещин (РУТ) и параметров КДУР (а также влияющих на них факторов) проводились на плоских образцах с центральным надрезом [19].
Образцы изготовлялись из листов, плит, прессованных панелей и про филей, вырезанных вдоль и поперек направления проката (прессования). Ширина образцов В составляла 140 и 300 мм, толщина t была 3—50 мм.
Центральный надрез был выполнен в виде отверстия диаметром D - 12 мм с боковыми надрезами глубиной /н = 3 мм, перпендикулярными продоль-
Я-ft
/ г
'Vi |
ш т |
Рис* 7.6, Образцы для статических и усталостных испытаний 1—6 —типы образцов
|
/ |
|
|
J0 |
а |
|
|
|
|
|
|
|
/ |
£ |
|
|
|
|
/ |
1 |
_ |
|
|
|
/ |
/ " к |
|
||
- |
' |
1 L/ |
|
|
|
/ |
V L**1 ) |
1 |
- ~ 8 H 4 |
||
|
/ |
|
9 ^ |
|
|
|
1 |
|
|
L |
|
Рис. 7*7. Образцы для исследования скорости роста усталостных трещин в сварном стыковом соединении
Центральный надрез: а —на оси шва, б —на линии сплавления
ной оси образца (рис. 7.7). Угол между поверхностями бокового надреза 30°, радиус в вершине надреза —0,1 мм.
Образцы (см. рис. 7.7) для исследования скорости РУТ в сварных соеди нениях и рассеяния параметров КДУР основных зон сварного соединения изготовляли из предварительно сваренных пластин 800X800X10 мм. Усиление шва сфрезеровывали заподлицо с основным металлом. Зону шва полировали до зеркальной поверхности. Вершины боковых надрезов располагались по оси шва, по линии сплавления и в основном металле на расстоянии 150 мм от оси шва. Испытания проводили на переменное растя жение при мягком нагружении на универсальной испытательной машине ГРМ-1 в воздухе и 3%-ном растворе поваренной соли, частота нагружения 10 Гц, коэффициент асимметрии R = 0,12-ь0,8. Перед коррозионно-уста лостными испытаниями поверхность образца в исследуемой зоне обезжи ривали ацетоном и спиртом. Коррозионная среда подводилась к образцу с помощью емкости из полиэтиленовой пленки. Наблюдение за распростра нением усталостных и коррозионно-усталостных трещин и измерение их длины на обеих поверхностях в процессе испытаний без остановки испы тательной машины производили с помощью микроскопной приставки МПБ-2 с ценой деления 0,05 мм и базой 6,5 мм. Для расширения диапазона применимости МПБ-2 на большие длины трещин 2/ = 50-^200 мм на обеих
поверхностях образца в сторону от вершин инициирующих надрезов нано сили бритвой риски на расстоянии 5 мм друг от друга.
При обработке результатов испытаний применяли методики статисти ческой обработки данных механических испытаний [4]. Для каждой вы борки вычисляли: среднеарифметическое Зс, среднеквадратическое откло нение (CKO) S , коэффициент вариации и. Приближенная проверка эмпи рических функций распределения выполнялась графическим методом. Проверка однородности выборки проводилась по критерию Груббса. Статистическая проверка гипотезы согласия опытного распределения с нормальным законом проводилась по критериям Пирсона (х^) и Кол могорова-Смирнова (X) для большой выборки и по критерию Шапиро — Уилка для малых выборок.
Выявление в процессе проверки на однородность резко выделяющихся низких результатов еще не означало обязательного исключения их из выборки, а лишь сигнализировало о необходимости более тщательного
обследования этого сварного |
соединения для отыскания объективной при |
чины резкого снижения исследуемой характеристики. |
|
Статистическая обработка |
результатов усталостных испытаний для |
определения уравнения кривой усталости в виде |
|
lgNp = IgA - mlgffmax |
(7.10) |
проводилась по методу [21 ] (А, т —параметры кривой усталости). Статические испытания. На рис. 1& и 7.9 показаны экспериментальные
распределения величин разрушающего напряжения и относительного удли нения сварных стыковых соединений листов из сплава АМг-61 и сплава системы А1—Mg—Zn, Они удовлетворительно аппроксимируются прямыми линиями в предположении нормального закона распределения. В табл. 7.4 приведены параметры распределений. Из таблицы следует, что СКО разрушающих напряжений сварных стыковых соединений равны S = 30-^36 МПа, а коэффициенты вариации v = 8,2-М 1,2%. Коэффициент вариации относительного удлинения более чем в 3 раза превышает коэф фициент вариации разрушающего напряжения.
Полученные характеристики рассеяния ор сварных соединений из сплава А1—Mg—Zn в 1,5—2 раза выше характеристик рассеяния оь сплава В-95Т, приведенных в работе [20], а дня сварных соединений сплава АМг-61 характеристики рассеяния в 3—4 раза выше рассеяния оъ сплава АМг-бМ, приведенного в [20].
В табл. 7.4 приведены результаты испытаний 203 стандартных образцов сварного стыкового соединения сплава АМг-61, изготовленных из листов толщиной 4—10 мм разных плавок, сварка выполнялась большим количе ством сварщиков в разных условиях Значение нижнего одностороннего
толерантного предела ор при р = у= |
0,95 будет равно ~*260 МПаи ниже при |
|
нимаемого при |
проектировании |
значения разрушающего напряжения |
ор = Коь = 300 |
МПа. |
рассеяния механических характеристик |
Для изучения |
причин высокого |
были дополнительно проанализированы испытания 37 стандартных образ цов стыкового сварного соединения сплава АМг-61. Образцы вырезали из одной сваренной. по типовой технологии пластины толщиной 5 мм. Ре-

I_____ I_____I |
I_______ |
|
2 |
6 / 0 |
/0 {4)0,°/o |
Рис, 7.8, Распределения значений разрушающих напряжений образцов сварных сты ковы х соединений сплава АМг-61, толщина листа 5 м м
1— 3 —типы разрушений (рис. 7.10) , £ —для всех разрушений образцов
Рис. 7.9, Распределения значений разрушающих напряжений (7) и относительного удлинения (77) образцов сварных стыковых соединений сплава А1—Mg—Zn
2— 4 —зоны разрушения (рис. 7.11)
зультаты этих испытаний приведены на рис. 7.8 и в табл. 7.4. Обследование образцов после испытаний выявило наличие трех характерных типов разру шения (см. рис. 7.10), и результаты испытаний были разделены соответст венно на три выборки.
На рис. 7.8 показаны экспериментальные распределения разрушающих напряжений для каждого типа разрушения. Они удовлетворительно согла суются с нормальным законом распределения. Полученные для этих выбо-
Т а б л и ц а 7.4 Параметры распределения статической прочности и пластичности образцов сварных сты ковы х соединений
|
|
АМг-61 |
|
Al-M g-Zn |
Характеристики |
4—10/203* |
5/37 |
|
4/34 |
|
|
°р , МПа |
Ор, МПа |
ь,% |
JC |
318 |
325 |
392 |
7.6 |
S |
30 |
36 |
32 |
2,2 |
и, % |
9,4 |
11,2 |
8,2 |
29,0 |
•В числителе —толщина, мм; в знаменателе —количество, шт.
Рис. 7.10. Характерные типы статического разрушения сварных стыковых соединений сплава АМг-61 (толщина 5 мм)
Обозначения те же, что на рис. 7.8
Рис. 7.11. Характерные зоны статического разрушения сварных стыковых соедине ний сплава А1—M g-Zn (толщина 4 мм)
Обозначения те же, что на рис. 7.9
рок значения СКО равны 13—25 МПа, что в 1,5—2,8 раза меньше значения, полученного для выборки из всех 37 образцов. Большие значения рассея ния соответствуют выборке с меньшей прочностью —третьему типу разру шения. Для сварных соединений, разрушившихся по третьему типу, харак терны большие значения несоосности (до 2,5 мм), усиления шва (до 12,5 мм) и объема наплавленного металла, а также резкий переход от шва к листу. Исключение этих дефектов при изготовлении конструкции приведет к существенному снижению рассеяния прочности и заметному уве личению ор и в конечном итоге к увеличению надежности конструк
ции.
На рис. 7.9 и в табл. 7.4 приведены результаты испытаний 34 образцов сварного стыкового соединения листов одной плавки сплава повышенной прочности системы А1—Mg—Zn (см. рис. 7.6, 3), Эти соединения являются соединениями с мягкой прослойкой, включающей металл шва из АМг-61 и разулрочненный металл зоны термического влияния.
Обследование образцов после испытаний выявило наличие четырех ха рактерных зон разрушения (рис. 7.11), и результаты испытаний были раз делены на соответствующие выборки. Экспериментальные распределения (см. рис. 7.9) разрушающих напряжений для каждого типа разрушения удовлетворительно, но хуже, чем на рис. 7.8, согласуются с нормальным законом распределения. Полученные для этих выборок значения СКО равны 8—26 МПа. Улучшение контроля формы шва в сварных соединениях с мягкой прослойкой, особенно при снятии усиления с одной стороны, позволяет избежать разрушения по мягкой прослойке (зоны 1 и 2), умень шить рассеяние и увеличить прочность сварного соединения с мягкой про слойкой. Причиной повышенного рассеяния механических характеристик сварных соединений являются дефекты сварных швов.
Дефекты сварных швов, оцененных в сварных пластинах даже баллом 3, случайно попадая при раскрое пластин в один-два образца, могут вызвать резкое снижение прочности и пластичности при испытаниях этих образцов. Если этот дефект пропускается применяемой методикой контроля качест ва изготовления или допускается соответствующими техническими требо ваниями и документами, то резко выделяющийся в малой выборке низкий результат не должен исключаться из рассмотрения. Статистический подход к назначению величины коэффициента прочности в формуле ор =коь явля ется действенным инструментом для улучшения качества изготовления и повышения культуры производства.
max*МЛа
Рис, 7,12, Кривая усталости сварного стыкового соедине ния (тип 1 )
Рис, 7,13, Зависимость между относительным удлинением и числом циклов до разрушения, образцы типа 1
Усталостные испытания. Результаты усталостных испытаний сварных стыковых соединений листов толщиной 4—8 мм сплава АМг-61 трех плавок приведены на рис. 7.12. Для этих же образцов на рис. 7.13 приведена зависи мость относительного удлинения от числа циклов до разрушения. Приведен ные на рис. 7.12 результаты можно считать типовыми для всех стыковых сварных соединений сплава АМг-61, так как эти образцы изготовлялись из листов нескольких плавок, а сварку выполняли разные сварщики по ти повой технологии в течение примерно 3 лет.
Рис, 7.14. Основные типы ( 1 —3 ) усталостных изломов
6
2
/2 7 * Л9 ' Л ?2 /2 7 * /2 7 * |
7/р |
Рис. 7.15. Кривые усталости образцов сплава А1—M g-Zn |
|
Обозначения те же, что на рис. 7.6; |
2 ' — коррозионно |
усталостные испытания образцов типа 2 |
|
Кривая усталости omfiX-N p в двойных логарифмических координатах в интервале долговечности от одного цикла до 1 • 105 циклов состоит из двух участков —левого пологого и правого крутого. Такой же вид име ет и зависимость 8-N p . В исследованном диапазоне Np наблюдаются два ти па разрушения —квазистатическое и усталостное и три вида изломов. Пе релом кривых усталости связан с переходом характера разрушения от ква зистатического к усталостному. Разрушение сварных соединений происхо дило по линии сплавления.
Основные типы изломов приведены на рис. 7.14. У типа 1 практически отсутствует усталостная зона. Он наблюдается в диапазоне максимальных напряжений цикла от ~ ор до а0>2 и даже 0,8aof2Типы изломов 2 и 3 имеют четкую усталостную зону и наблюдаются при сгтах < 1 8 0 МПа. При этом тип 2 наблюдается существенно реже, чем 3.
При статистической обработке результатов испытаний и определении
параметров уравнения (7.10) кривой усталости нельзя объединять экспери ментальные данные, относящиеся к разным участкам кривой усталости. Поэтому уже при планировании эксперимента целесообразно оценить ожи даемые значения координат точки перелома кривой усталости.
Рассмотрим этот вопрос подробнее. На рис. 7.15 приведены результаты усталостных испытаний образцов типов 2, 4—6 (см. рис. 7.6) в воздухе и коррозионной среде. Левый участок кривой усталости гладких образцов более пологий, чем у образцов с типовыми концентраторами. Наклон правых участков кривых усталости практически постоянен дня всех рас смотренных типов образцов сплава, т.е. показатель степени уравнения вто рых участков кривых малоцикловой усталости можно считать одинаковым дня всех рассмотренных типовых конструктивных элементов.
Координаты точек перелома кривых усталости для Р = 50% рассмотрен ных типов образцов лежат в диапазоне:
^шах “ (0,97“ 0,86) (7р , |
(7.11) |
Np = (0,5-г5) . Ю3 |
|
большие значения соответствуют гладким образцам. Показатели степени в полученных уравнениях вторых участков этих кривых усталости образ цов типа 6 семи алюминиевых сплавов находятся в диапазоне т = 3,8-г8,9. Зависимость т от предела прочности сплавов имеет выпуклую форму и аппроксимируется следующим выражением:
m = —92,1 + 0,477 — 5,61 10"4о£ (7.12)
(оъ имеет размерность МПа).
Можно считать, что при малоцикловом нагружении диапазон рассеяния показателя степени т дня заданного уровня вероятности и дня других ти повых элементов конструкций не будет выходить из указанного диапазона.
Зависимость СКО логарифмов чисел циклов до разрушения от lgN р дня сварных стыковых соединений (тип 1) сплава ПМг-61 толщиной 4 и 8 мм приведены на рис. 7.16. Аналогичные данные дня образцов типов 2—5 спла ва А1—Mg—Zn толщиной 4 мм приведены на рис. 7.17. Экспериментальные распределения чисел циклов до разрушения удовлетворительно согласу ются с логнормальным законом распределения (рис. 7.18). Дня спла ва АМг-61 в диапазоне Np = 1 • 103-H • Ю5 и amax = 12(Н250 МПа, соответ ствующих второму участку кривой усталости, полученные значения СКО всех выборок находятся в диапазоне 0,22—0,38 и группируются около значения S = 0,28. Можно считать, что дня второго участка кривой усталос ти S = const. При значениях Ар и атах, соответствующих первому (полого му) участку кривой усталости, наблюдается резкое увеличение S. Следо вательно, значения S на участках кривой усталости пропорциональны показателю степени в уравнении (7.10).
В общем выражении долговечности с учетом двух стадий разрушения
Ар = А0 + Атр, |
(7ЛЗ) |
где А0 — число циклов до образования трещины; |
—число циклов |
на стадии роста трещины (живучесть); дня первого участка,видимо, имеет место неравенство А0 А ^ , в отдельных случаях дня некоторых образ цов (при наличии дефектов) получаем А0 « 0, т.е. Ар ~ А ^ . Увели-
174
Рис. 7Л6. Зависимость CKO логарифма чисел циклов до разрушения от IgAJ, для сплава АМг>61
Рис, 7Л 7. Зависимость СКО логарифмов чисел циклов до разрушения от IgAJ, для
сплава А1—Mg—Zn
1 - тип 4\ 2 - тип 2; 3 - тип 2 в коррозионной среде; 4 - тип 5; 5 - тип 3\ 6 - тип 3 в коррозионной среде; I—IJI —зоны с характерными значениями S
Pt 0/*
Рис. 7Л8, Экспериментальное рас пределение логарифмов чисел цик лов до разрушения образцов ти па 5, сплав Al-M g-Zn (оттх = = 220 МПа)
чение рассеяния Np при переходе в многоцикловую область (на третьем участке кривой усталости) отмечено в работах [15,17].
На полученных для вторых участков кривых усталости зависимостях S —\gN можно выделить три зоны значений S. В первую зону вошли глад кие образцы и образцы с отверстием, т.е. СКО не зависит от коэффициента концентрации. Полученные для этих образцов значения S ~ 0,03"г0,08 удов летворительно согласуются со значениями, полученными для аналогичных
образцов в работах [15,17].
Во вторую зону со значениями S 0,13"»"0,26 входят сварные стыковые соединения, испытанные в воздухе. Третью зону со значениями S —0,26"H),33 составляют СКО сварных соединений, испытанных в коррозионной среде.
Рис, 7,19, Влияние относительной площади несплавления в корне шва (а) и остаточ ной погиби (б) на долговечность сварных соединений сплава АМг-61
При а, МПа: а. 1 - 60±30, 2 - 60±15; б. 1 - 140±70, 2 - 80±40
Таким образом, для сварных стыковых соединений значения CKO \gNp в несколько раз выше, чем для образцов с типовым_концентратором в виде отверстия. Коррозионная среда не только снижает Npи значения ограничен ных пределов выносливости, но и в 1,3-Ь2 раза увеличивает CKO lgNp.
Главной причиной большого рассеяния чисел циклов до разрушения сварных соединений алюминиевых сплавов являются дефекты сварных швов и особенности сварки как метода соединения. Несплавления, остаточ ная погибь могут в несколько десятков раз снизить долговечность сварного соединения (рис. 7.19). Усталостная трещина всегда возникает на вогнутой поверхности. Наиболее опасны приповерхностные дефекты, особенно в свар ных соединениях со снятием усиления шва. Влияние этих дефектов увели чивается с уменьшением напряжений цикла нагружения.
Усталостная зона в изломе (см. рис. 7.14) имеет форму, близкую к поло вине или четверти эллипса. Ее площадь возрастает с уменьшением атах. От ношение полуосей эллипса для изломов типа 2 равно 0,5—0,25, а дпа изло мов типа 3 — 0,3—0,1; с уменьшением атах это отношение уменьшается.
Для изломов типа 2 твердость металла вблизи зоны разрушения практи чески постоянная, а у изломов типа 3 наблюдается увеличение твердости у торца, где расположена зона долома (рис. 7.20). С приближением к зоне разрушения твердость по длине образцов возрастает. При amax < a0j2 не отмечено заметного увеличения твердости вблизи зоны разрушения. Но при amax > а0:2 для сварных соединений сплава АМг-61 твердость в зо не разрушения возрастает с увеличением атах (рис. 7.21). Отмечено увели чение в 1^ раза твердости в зоне разрушения по сравнению с исходной твердостью (до усталостных испытаний). Рассеяние твердости в зоне разру шения испытанных образцов сварных соединений значительно ниже рассея ния их долговечности. Выполненные исследования не позволили установить простые зависимости между рассеянием Np сварных соединений и формой изломов, ростом и рассеянием твердости в зоне разрушения.
Исследование кинетики усталостного разрушения. Усталостные трещи ны у вершин боковых надрезов возникают быстро, особенно в металле

Рис. 7.20. Изменение твердости по ширине и длине образца после усталостных испытаний (сплав АМг-61)
(HRV)f/HRV
Рис, 7.21. Зависимость твердости сплава |
I----- 1 |
71 |
I |
АМг-61 от максимального напряжения цик |
|||
ла нагружения |
0 0f 5 |
7,0 |
7,5 |
**max /^of2
сварного шва. Они устойчиво развиваются даже при а=20±10 МПа. Кор розионная среда резко снижает число циклов N0 на прорастание трещин на 1 мм из вершины надреза. С уменьшением напряжения значения N0 увеличиваются интенсивнее Л ^, а коэффициент живучести /3 -N ^/N p уменьшается от 0,98 до 0,75. Рассеяние N0 больше рассеяния Л^,. Пара метры уравнения (7.10) применительно к N0 для исследованных сплавов и острого надреза равны т - 3,1 4-4,0 и А = 6,94-7,2, меньшие значения соот ветствуют высокопрочным сплавам. Эти значения т в 1,14-1,5 раза меньше значений, приведенных для вторых участков кривых малоцикловой уста
лости. |
|
|
Результаты исследования скорости dl/dN распространения |
усталостных |
|
трещин |
(РУТ) были представлены в виде степенной зависимости от КИН |
|
в форме Пэриса с модификацией по [19]: |
|
|
<Л_ |
1 |
(7.14) |
<т |
С(АК)п |
|
(1 - ю р |
|
где п, С,р —параметры, определяемые из эксперимента.
В общем случае КДУР состоит из трех участков. Для крайних участков 1, 3 характерно повышенное рассеяние скоростей РУТ и параметров урав нения (7.14). Например, приведенные в табл. 7.5 статистические характе ристики параметров п2 и п3 показывают, что для образцов сплава АМг-61 В - t = 300 10 мм коэффициент вариации пъ в ~ 2,5 раза больше коэффи циента вариации п2, а последний в 1,3 раза меньше значения этой характе ристики для высокопрочного сплава. Средний участок КДУР заканчивается при достижении трещиной длины чисто усталостной зоны 2ls . В этих точ ках значения скорости РУТ для всех исследованных полуфабрикатов и сплавов и R =0,124-0,8 расположены в узком диапазоне (2—4)10~3 мм/цикл. Переход от второго участка КДУР к третьему происходит при значениях
12. Зак. 1830 |
177 |
Статистические характеристики |
параметров |
КДУР, образцы |
продольные |
|
{В = 100 мм, f = 10 мм) |
|
|
|
|
Сплав |
Параметр КДУР |
X |
S |
V, % |
АМг-61 |
П7 |
2,20 |
0,12 |
5,5 |
А1—Mg-Zn |
пз |
5,85 |
0,72 |
12,3 |
П2 |
2,54 |
0,18 |
7,1 |
^тах/ао,2> равных ~ 1,3 для |
высокопрочных сплавов и |
3,3 для сплава |
АМг-61. Отношение значений показателя степени в (7.14) |
для третьего и |
|
второго участков КДУР равно л2/из = 1,5-гЗ,0. |
|
|
Получено приблизительно |
10-кратное рассеяние значений скорости РУТ |
|
на втором участке КДУР для всех испытанных образцов |
(рис. 7.22). Рас |
смотрим причины такого рассеяния. Скорость РУТ возрастает с увеличени ем Ощах при равных АК и R = const. При этом п2 не изменяется (рис. 7.23). Отмечено четырехкратное возрастание скорости РУТ. Чем меньше толщина листа, тем при меньших отах начинает сказьюаться это влияние. Такой эф фект связан, видимо, с возникновением поперечных сжимающих деформа ций при растяжении образца. При статических испытаниях потеря устойчи вости берегов трещин у аналогичных образцов происходила при
о« 0,8(///)2Я
Сростом атах уменьшается протяженность второго участка, уменьшается длина 21s , но возрастает соответствующий ей K/s .
Увеличение коэффициента асимметрии при равных размахах КИН сдви гает КДУР в область больших скоростей РУТ при постоянном значении п2 (рис. 7.24). Статистические характеристики параметра р для второго участ
ка |
КДУР равны: р = 1,46, s = 0,44 для высокопрочного сплава |
и р - |
= |
1,08, s =0,14 для сплава АМг-61. |
|
|
Увеличение толщины образцов вызывает увеличение п2, п3, 2ls и |
умень |
шение С2 (рис. 7.25). Наибольшие достигнутые средние значения показа теля степени п2 равны 2,5 и 3,1 для сплава А1—Mg—Zn и АМг-61 соответст венно. С уменьшением ширины образцов возрастает скорость РУТ и увели чивается рассеяние параметров КДУР.
Анизотропия скорости РУТ и параметров КДУР коррелирует с анизотро пией механических характеристик. У сплава АМг-61 она более заметна. У продольных образцов 2ls значительно больше, чем у поперечных.
Коррозионная среда резко сокращает длительность стадии образования трещины и в несколько раз увеличивает скорость РУТ на первом участ ке КДУР. С ростом длины трещины влияние коррозионной среды умень шается. На втором участке КДУР скорость РУТ в 1,6—23 раза больше, чем на воздухе.
Типовые КДУР для сварного стыкового соединения листов сплава АМг-61 приведены на рис. 7.26. Для металла шва и металла у линии сплав ления они имеют такую же форму, как и для основного металла.
Характерной особенностью КДУР сварного стыкового соединения листов сплава АМг-61 является то, что вторые участки этих диаграмм для металла
dl/dtf; лглг/и,икл
77“Е —
/ 0' |
к ° ++( |
— |
|
|
В * * А |
х |
ллЛп |
/0
/0
-------------------- ^ Ь |
р |
' |
)
Л
•
•
<3
/ 0'
-------------------------------L - |
I |
Aft, МЛа /м
Рис» 1 2 2 , Зависимость скорости РУТ от размаха КИН для сплава АМг-61 Точки — результаты испытания образцов
dl/d07 лглг/цикл
а Н7 МЛа
Рис. 7*23. Влияние максимального напряжения о ,,^ цикла нагружения на скорость РУТ и параметры КДУР (АМг-61, В • t ~ 300 • 4 мм, R —1/3)
При ота х , МПа: 1 - 45, 2 - 60, 3 - 80, 4 - 100, 5 - 13S
основных зон сварного соединения параллельны между собой (рис 7 26)
нем1И^ п * Пара^ |
Т |
В |
УЧЭСТКа КДУР "РЕДОНЫ в табл. 7.6 В послед- |
чески чиаии ЭТ° И |
18 |
ИЦЫ Даны Результаты проверки гипотезы о статисти |
чески значимом различии величин конкретного параметра КДУР основ30HwCBaPHoro соединения.Статистический анализ показал,
a nnvL ИЧИ6 значении паРаметра п2 всех зон статистически незначимо, а Другие параметры отличаются значимо. Параметр л2 для всех зон сварно-
го соединения при испытаниях в воздухе и коррозионной среде одинаков, его статистические характеристики: п 2 = 2,3; s = 0,05. Следовательно, можчитать, что для сварного соединения сплава АМг-61 этот параметр ма-